内饰材料标准
汽车内饰物燃烧标准

汽车内饰件阻燃标准等级汽车内饰阻燃标准主要由国家或汽车制造商发布,其中大部分标准的测试方法都是比较接近,主要关注内饰材料的易燃性和燃烧速率,只要不超过一定的燃烧速率(一般为102mm/min)时,都是允许在汽车内使用的。
取样测试的部位为汽车内暴露面向下13mm内的单层或者复合层材料,若每层可以分离则需要单独测试。
内饰材料燃烧标准GB8410 - 汽车内饰材料的燃烧特性。
GB8410标准规定了汽车内饰材料水平火钳特性的技术要求及试验方法。
GB8410标准适用于汽车内饰材料水平燃烧特性的评定。
内饰材料不燃烧、可以燃烧但燃烧速度不大于100mm/min、火焰在60s内自行熄灭且燃烧距离不大于50mm。
燃烧速度:测得的燃烧距离与燃烧此距离所用时间的比值,单位为毫米每分钟(mm/min)。
从保证乘员安全的角度来讲,不燃烧当然是最好,而燃烧速度能够靠材料本身保证在一定的范围之内,也可以为乘员提供一定的生存时间和逃生的时间。
在实际的试验操作过程中,是以在规定时间内不能引燃或在第一个标志柱之前自行熄灭的视为不燃烧。
汽车内饰材料阻燃标准FMVSS302主要适用于汽车内饰材料的阻燃测试,UL94是广泛适用于塑料材料的阻燃测试。
针对产品用途范围不一样,且测试方法和要求也不一样。
不易燃。
医用防护服采用不易燃材料,并且离开火焰后燃烧不大于5s,该项目可以采用ZYYQ阻燃性能测试仪设备进行测试,ZYYQ阻燃性能测试仪智能化程度高,符合国家标准GB/T5455-1997《纺织品燃烧性能试验垂直法》,可用于有阻燃要求的服装织物、装饰织物、帐篷织物等阻燃性能的测定。
阻燃海绵由于含可燃的碳氢链段、密度小、比表面积大,未经阻燃处理的聚氨酯海绵是可燃物,遇火会燃烧并分解,产生大量的烟雾,给灭火带来困难。
特别是聚氨酯软泡开孔率较高,可燃成分多,燃烧时由于较高的空气流通性而源源不断地供给氧气,易燃且不易自熄。
聚氨酯海绵的许多应用领域非常广泛,如建筑材料、床垫、家具、保温材料、汽车座垫及内饰材料等,都需达到阻燃要求。
nes m0094标准

NES M0094标准是关于汽车内饰可燃烧性能的测试标准。
它用于评估汽车内部组件在遇到火源时的燃烧行为和释放有害气体的能力。
该标准规定了测试方法、设备、样品准备和试验程序,以确保汽车内饰材料具有足够的阻燃性能和低烟释放能力。
根据NES M0094标准,汽车内饰材料需要满足以下要求:
1. 燃烧速度:内饰材料需要以适当的速度燃烧,以减少火势在车辆内的蔓延。
2. 烟雾释放:内饰材料不应释放过多的有害烟雾和气体,以减少对乘客和驾驶员的危害。
3. 毒性:内饰材料不应释放有毒物质,以确保乘客和驾驶员的安全。
NES M0094标准是针对汽车制造商和内饰材料供应商的测试要求,以确保汽车内部组件的安全性和可靠性。
通过遵守该标准,可以减少火灾对乘客和驾驶员的危害,并提高车辆的整体安全性。
汽车voc国标
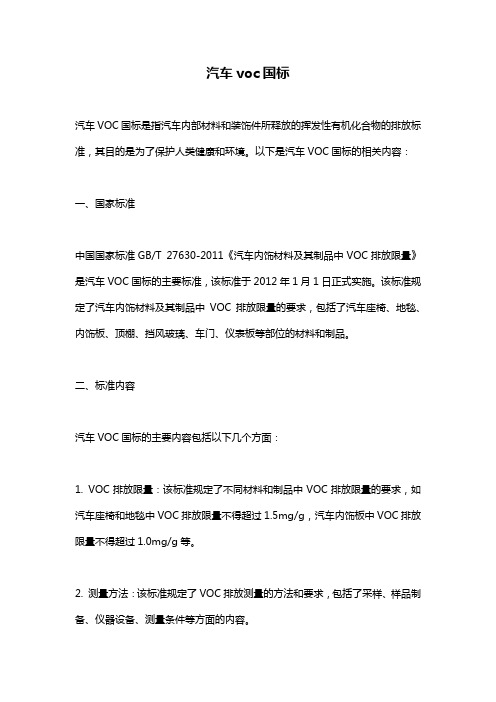
汽车voc国标
汽车VOC国标是指汽车内部材料和装饰件所释放的挥发性有机化合物的排放标准,其目的是为了保护人类健康和环境。
以下是汽车VOC国标的相关内容:
一、国家标准
中国国家标准GB/T 27630-2011《汽车内饰材料及其制品中VOC排放限量》是汽车VOC国标的主要标准,该标准于2012年1月1日正式实施。
该标准规定了汽车内饰材料及其制品中VOC排放限量的要求,包括了汽车座椅、地毯、内饰板、顶棚、挡风玻璃、车门、仪表板等部位的材料和制品。
二、标准内容
汽车VOC国标的主要内容包括以下几个方面:
1. VOC排放限量:该标准规定了不同材料和制品中VOC排放限量的要求,如汽车座椅和地毯中VOC排放限量不得超过1.5mg/g,汽车内饰板中VOC排放限量不得超过1.0mg/g等。
2. 测量方法:该标准规定了VOC排放测量的方法和要求,包括了采样、样品制备、仪器设备、测量条件等方面的内容。
3. 适用范围:该标准适用于所有汽车内饰材料及其制品的生产、销售和使用。
4. 标识要求:该标准规定了符合要求的汽车内饰材料和制品应当标注“符合GB/T 27630-2011标准要求”。
三、实施效果
自2012年1月1日起,汽车内饰材料和制品必须符合GB/T 27630-2011标准要求才能够生产、销售和使用。
该标准的实施对于保护人类健康和环境具有重要意义,可以有效降低汽车内部VOC排放量,减少空气污染和有害物质对人体的危害。
同时,该标准的实施也促进了汽车内饰材料和制品的技术升级和产业升级,提高了汽车内饰材料和制品的安全性和环保性。
汽车内饰件3c认证标准

汽车内饰件3c认证标准汽车内饰件3C认证标准。
随着汽车产业的快速发展,汽车内饰件的安全性和质量成为消费者关注的焦点。
为了保障汽车内饰件的安全性和质量,我国对汽车内饰件实施了3C认证标准。
首先,汽车内饰件3C认证标准对产品的材料和工艺提出了严格要求。
汽车内饰件必须采用符合国家标准的环保材料,以确保产品在使用过程中不会对人体健康造成危害。
同时,汽车内饰件的生产工艺必须符合相关标准,确保产品的质量稳定可靠。
其次,汽车内饰件3C认证标准对产品的功能和性能进行了严格检测。
汽车内饰件在通过3C认证之前,需要经过一系列的功能和性能测试,包括产品的耐磨性、耐高温性、阻燃性等方面的测试,以确保产品在使用过程中能够满足消费者的需求,并具有良好的安全性能。
另外,汽车内饰件3C认证标准对产品的外观和标识也有一定的要求。
汽车内饰件在通过3C认证之后,需要在产品上标注3C认证标志,以便消费者在购买时能够识别出符合国家标准的产品。
同时,产品的外观也需要符合相关的美学要求,以提升产品的整体质感和品质感。
总的来说,汽车内饰件3C认证标准的实施,对提升汽车内饰件的质量和安全性起到了积极的作用。
通过严格的认证标准和检测流程,可以有效地杜绝一些质量不合格的产品流入市场,保障消费者的权益。
同时,也可以促进汽车内饰件行业的健康发展,推动企业不断提升产品质量和技术水平。
在未来,随着汽车产业的不断发展和消费者对汽车内饰件质量和安全性的要求不断提高,汽车内饰件3C认证标准也将不断完善和提升,以适应市场的需求和发展。
相信通过3C认证标准的不断完善和执行,汽车内饰件的质量和安全性将会得到进一步提升,为消费者提供更加优质的产品和服务。
一文读懂:汽车内饰部件的选材及特点
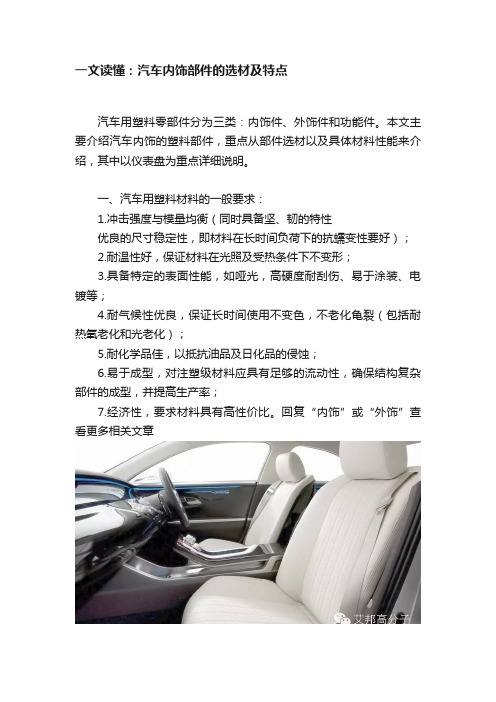
一文读懂:汽车内饰部件的选材及特点汽车用塑料零部件分为三类:内饰件、外饰件和功能件。
本文主要介绍汽车内饰的塑料部件,重点从部件选材以及具体材料性能来介绍,其中以仪表盘为重点详细说明。
一、汽车用塑料材料的一般要求:1.冲击强度与模量均衡(同时具备坚、韧的特性优良的尺寸稳定性,即材料在长时间负荷下的抗蠕变性要好);2.耐温性好,保证材料在光照及受热条件下不变形;3.具备特定的表面性能,如哑光,高硬度耐刮伤、易于涂装、电镀等;4.耐气候性优良,保证长时间使用不变色,不老化龟裂(包括耐热氧老化和光老化);5.耐化学品佳,以抵抗油品及日化品的侵蚀;6.易于成型,对注塑级材料应具有足够的流动性,确保结构复杂部件的成型,并提高生产率;7.经济性,要求材料具有高性价比。
回复“内饰”或“外饰”查看更多相关文章汽车内部对内饰材料的要求耐热性:因夏季常时间光照,车厢内温度比较高,要求内饰件材料具有高耐热性耐老化性:包括热氧老化和光老化,防止部件老化变色、劣化 气味性:为了驾乘人员的身体健康,材料应确保低挥发性、低气味哑光性:为确保驾驶安全,选用哑光材料或哑光皮纹二、具体汽车塑料内饰部件的选材1.仪表板:仪表板(instrument panel ) 驾驶室中安装各种指示仪表和点火开关等的一个总成,它装在仪表嵌板上,或者作为附件装在转向管柱上。
回复“内饰”或“外饰”查看更多相关文章仪表盘项目 硬质仪表板软质仪表板骨架 表皮制造方法 注塑成型, 表面可以注塑成型 (1)搪塑(2)吸塑喷漆处理使用材料PP+TALC, PC/ABS PC/ABS. PPO, (1)PVC 搪塑粉(2)PVC/ABS 片材外观 外观良好 外观良好外观良好手感 手感差 手感良好手感较好制造成本低 高适用车型经济型 中高级轿车2.硬质仪表板车型大众POLO, CADDY,GOL :PP+EPDM+T10, PP+EPDM+T20 CITROEN(雪铁龙):ELYSEE,富康:PP+EPDM+T15NISSAN (东风日产)SUNNY :PP+EPDM+T20FORD(长安福特)嘉年华:PP+EPDM+T25GMSAIL (雪佛兰):PP+EPDM+GB253.硬质仪表板材料组分PP:共聚聚丙烯,高结晶聚丙烯滑石粉:超细滑石粉,提供刚性和耐热性EPDM/POE:提供韧性助剂:耐候,耐划伤,长期热稳定4.聚丙烯仪表板材料典型性能性能单位 范围 含义 MFR g/10min 7-20流动性密度 g/cm3 1.0-1.18 15-25%矿物填充拉伸强度 M Pa >19 强度伸长率 % 40缺口冲击强度 KJ/m2 15-30(23℃)韧性弯曲模量 M Pa1500-2500 刚性弯曲强度 M Pa>25 HDT(0.45 MPa) ℃>105 耐热性能 5.软质仪表板制作过程6.仪表板骨架热固性材料-木粉板:SMC/BMC ,VW 车型,卡车,大中型客车热塑性材料-PC-GF ,SMA-GF ,PPO :目前多数轿车采用 LFT-PP 新型材料,性价比高:FORD 福克斯,VW 斯柯达7.仪表板附件杂物盒:PP ,或者ABS副仪表板:PP+EPDM+TALC出风口-耐冷热交变:ABS, PC/ABS饰框-电镀,仿木处理:ABS, PC/ABS注:仪表板特殊要求HDT温度高(1.8MPa):≥100℃可冷凝挥发物含量低:(SAEJ1756)≤2mg低光泽:光泽度≤4 (60°)其他内饰材料选材1.立柱前立柱,中立柱上部,后立柱:PP,PP+TALC中立柱下部:韧性要求高,与仪表板材料一致其他要求:落锤冲击韧性断裂。
大众内饰件标准

大众内饰件标准一、引言大众内饰件标准是指大众汽车公司对其车辆内部零部件的设计、制造和安装提出的要求和规范。
内饰件是指车辆内部的各种装饰和功能性配件,如座椅、仪表盘、中控台、车门饰板等。
这些内饰件不仅影响了车辆的外观美观,还关系到车内乘坐者的舒适度和安全性。
因此,大众对内饰件的标准要求非常严格。
二、座椅座椅是车辆内饰件中最重要的部分之一,大众对座椅的标准有以下要求:1. 座椅材料必须符合相关的环保法规,不得含有有害物质;2. 座椅的设计和制造必须符合人体工程学原理,能够提供舒适的乘坐体验;3. 座椅的安装必须牢固可靠,不得出现松动或异响;4. 座椅的调节功能必须灵活方便,能够满足不同乘坐者的需求。
三、仪表盘仪表盘是车辆内饰件中的重要组成部分,大众对仪表盘的标准有以下要求:1. 仪表盘的材料必须具有一定的防火性能,能够在发生事故时有效防止火灾蔓延;2. 仪表盘上的仪表和控制按钮必须布局合理、易于操作,乘坐者能够方便地获取所需的信息和进行操作;3. 仪表盘的造型和颜色要与车辆整体风格相协调,给人以美观的感觉;4. 仪表盘的安装必须牢固可靠,不得出现松动或异响。
四、中控台中控台是车辆内饰件中的重要部分,大众对中控台的标准有以下要求:1. 中控台的布局和设计必须符合人体工程学原理,能够方便乘坐者进行各种操作;2. 中控台上的控制按钮和显示屏幕必须布局合理、易于操作,乘坐者能够方便地控制车辆各项功能;3. 中控台的材料和装饰必须符合环保要求,并且能够与车辆整体风格相协调;4. 中控台的安装必须牢固可靠,不得出现松动或异响。
五、车门饰板车门饰板是车辆内饰件中的重要组成部分,大众对车门饰板的标准有以下要求:1. 车门饰板的材料必须具有一定的防火性能,能够在发生火灾时有效防止蔓延;2. 车门饰板的造型和颜色要与车辆整体风格相协调,给人以美观的感觉;3. 车门饰板的安装必须牢固可靠,不得出现松动或异响;4. 车门饰板上的开关和储物空间必须布局合理、易于操作,乘坐者能够方便地存放和取出物品。
汽车内饰件国家标准
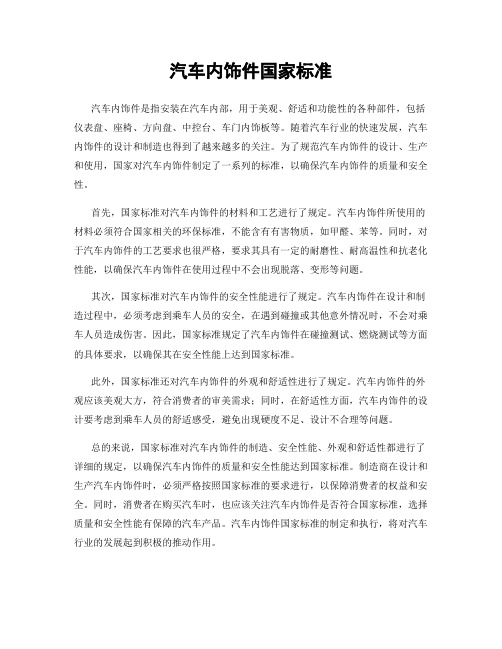
汽车内饰件国家标准汽车内饰件是指安装在汽车内部,用于美观、舒适和功能性的各种部件,包括仪表盘、座椅、方向盘、中控台、车门内饰板等。
随着汽车行业的快速发展,汽车内饰件的设计和制造也得到了越来越多的关注。
为了规范汽车内饰件的设计、生产和使用,国家对汽车内饰件制定了一系列的标准,以确保汽车内饰件的质量和安全性。
首先,国家标准对汽车内饰件的材料和工艺进行了规定。
汽车内饰件所使用的材料必须符合国家相关的环保标准,不能含有有害物质,如甲醛、苯等。
同时,对于汽车内饰件的工艺要求也很严格,要求其具有一定的耐磨性、耐高温性和抗老化性能,以确保汽车内饰件在使用过程中不会出现脱落、变形等问题。
其次,国家标准对汽车内饰件的安全性能进行了规定。
汽车内饰件在设计和制造过程中,必须考虑到乘车人员的安全,在遇到碰撞或其他意外情况时,不会对乘车人员造成伤害。
因此,国家标准规定了汽车内饰件在碰撞测试、燃烧测试等方面的具体要求,以确保其在安全性能上达到国家标准。
此外,国家标准还对汽车内饰件的外观和舒适性进行了规定。
汽车内饰件的外观应该美观大方,符合消费者的审美需求;同时,在舒适性方面,汽车内饰件的设计要考虑到乘车人员的舒适感受,避免出现硬度不足、设计不合理等问题。
总的来说,国家标准对汽车内饰件的制造、安全性能、外观和舒适性都进行了详细的规定,以确保汽车内饰件的质量和安全性能达到国家标准。
制造商在设计和生产汽车内饰件时,必须严格按照国家标准的要求进行,以保障消费者的权益和安全。
同时,消费者在购买汽车时,也应该关注汽车内饰件是否符合国家标准,选择质量和安全性能有保障的汽车产品。
汽车内饰件国家标准的制定和执行,将对汽车行业的发展起到积极的推动作用。
汽车内饰选材定义指南

汽车内饰选材定义指南内饰篇内饰件的一般要求:有足够的抗刮擦性能,以免表面受尖硬物体刮磨出现划痕;具有一定的抗蚀性、耐温、在长期光照下不变色;满足表面不反光(低光泽)、无异味、长时间高温环境无小分子物质析出、不产生致使车玻璃变模糊的物质、阻燃性好等要求仪表板篇1.通常仪表板选材考虑的因素:1)本体材料要有足够的刚性,据分析多款车型总结,弹性模量≥1900Mpa才可满足其刚性要求。
因为仪表板上有许多安装件,如烟灰缸、手套箱、杂物箱、通风口等。
由于仪表板经常被太阳直射,因此高温下的负载能力也是考查仪表板材料的一个重要指标2)仪表板要有足够的韧性,一般来说冲击强度≥18KJ/M2,因为在一些碰撞时仪表板能够吸收一些能量,降低对乘客的伤害。
除此之外还要考虑材料的低温冲击韧性3)高温稳定性:仪表板太阳直射部位温度可高达110℃,在110℃/24h下,仪表板本体不出现变形、翘曲及影响外观的表面现象出现4)低温稳定性:在-40℃/24h条件下,仪表板本体不出现翘曲、轮廓和曲面歪斜以及影响外观表面的现象出现5)耐光照色牢度:氙灯照射5个周期(约250h)后,灰度等级≥4级,表面不能有影响外观的现象发生,不能有增塑剂渗出6)气味性、有机物挥发、甲醛含量、重金属等必须满足相关法规要求。
气味性暂时可参考大众公司的企业标准进行定义7)燃烧性:内饰件燃烧性能为强检项目,按照GB8410试验方法,要求≤100mm/min 8)仪表板表皮环保要求:目前趋势TPO代替PVC表皮综合上述诸多因素,从材料和成型工艺分为硬质和软质两种,硬质仪表台外观质量很难达到较高水平,容易出现缩瘪、熔接痕。
目前国内仪表板常用材料为:本体材料:PP+EPDM-T20、ABS、PC+ABS、PP+GF30+T30麻纤维等几种仪表板材料的优缺点比较如下:软质仪表台:骨架+缓冲发泡层+表皮真空吸附表皮:桑塔纳搪塑表皮:与真空吸附法相比,表皮无应力,无开裂,尺寸稳定厚度均匀,表皮纹理清晰,接近天然皮革,能制造表面形状复杂的仪表台,耐候性方面搪塑PVC 表皮要优于PVC/ABS拉伸表皮2.中控面板材料:1)一般需喷亚光漆或仿桃木处理2)刚性要好,尺寸稳定性好。
GB8410-2006汽车内饰标准
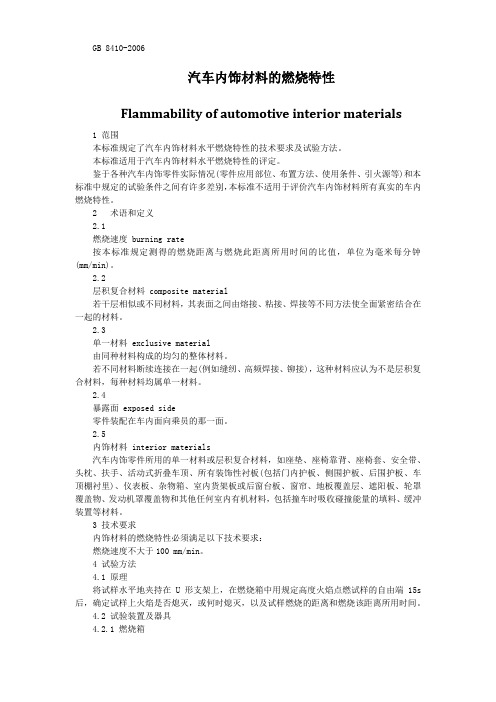
GB 8410-2006汽车内饰材料的燃烧特性Flammability of automotive interior materials1 范围本标准规定了汽车内饰材料水平燃烧特性的技术要求及试验方法。
本标准适用于汽车内饰材料水平燃烧特性的评定。
鉴于各种汽车内饰零件实际情况(零件应用部位、布置方法、使用条件、引火源等)和本标准中规定的试验条件之间有许多差别,本标准不适用于评价汽车内饰材料所有真实的车内燃烧特性。
2 术语和定义2.1燃烧速度 burning rate按本标准规定测得的燃烧距离与燃烧此距离所用时间的比值,单位为毫米每分钟(mm/min)。
2.2层积复合材料 composite material若干层相似或不同材料,其表面之间由熔接、粘接、焊接等不同方法使全面紧密结合在一起的材料。
2.3单一材料 exclusive material由同种材料构成的均匀的整体材料。
若不同材料断续连接在一起(例如缝纫、高频焊接、铆接),这种材料应认为不是层积复合材料,每种材料均属单一材料。
2.4暴露面 exposed side零件装配在车内面向乘员的那一面。
2.5内饰材料 interior materials汽车内饰零件所用的单一材料或层积复合材料,如座垫、座椅靠背、座椅套、安全带、头枕、扶手、活动式折叠车顶、所有装饰性衬板(包括门内护板、侧围护板、后围护板、车顶棚衬里)、仪表板、杂物箱、室内货架板或后窗台板、窗帘、地板覆盖层、遮阳板、轮罩覆盖物、发动机罩覆盖物和其他任何室内有机材料,包括撞车时吸收碰撞能量的填料、缓冲装置等材料。
3 技术要求内饰材料的燃烧特性必须满足以下技术要求:燃烧速度不大于100 mm/min。
4 试验方法4.1 原理将试样水平地夹持在U形支架上,在燃烧箱中用规定高度火焰点燃试样的自由端15s 后,确定试样上火焰是否熄灭,或何时熄灭,以及试样燃烧的距离和燃烧该距离所用时间。
4.2 试验装置及器具4.2.1 燃烧箱燃烧箱用钢板制成,结构示意图见图1,尺寸见图2。
汽车内饰材料voc测试标准
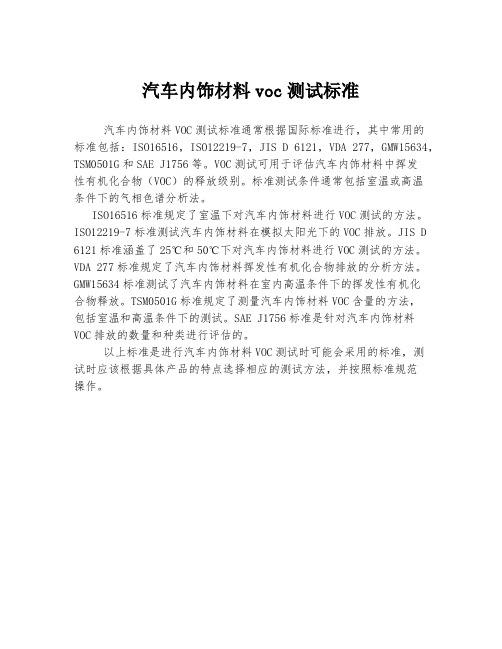
汽车内饰材料voc测试标准
汽车内饰材料VOC测试标准通常根据国际标准进行,其中常用的
标准包括:ISO16516,ISO12219-7,JIS D 6121,VDA 277,GMW15634,TSM0501G和SAE J1756等。
VOC测试可用于评估汽车内饰材料中挥发
性有机化合物(VOC)的释放级别。
标准测试条件通常包括室温或高温
条件下的气相色谱分析法。
ISO16516标准规定了室温下对汽车内饰材料进行VOC测试的方法。
ISO12219-7标准测试汽车内饰材料在模拟太阳光下的VOC排放。
JIS D 6121标准涵盖了25℃和50℃下对汽车内饰材料进行VOC测试的方法。
VDA 277标准规定了汽车内饰材料挥发性有机化合物排放的分析方法。
GMW15634标准测试了汽车内饰材料在室内高温条件下的挥发性有机化
合物释放。
TSM0501G标准规定了测量汽车内饰材料VOC含量的方法,
包括室温和高温条件下的测试。
SAE J1756标准是针对汽车内饰材料VOC排放的数量和种类进行评估的。
以上标准是进行汽车内饰材料VOC测试时可能会采用的标准,测
试时应该根据具体产品的特点选择相应的测试方法,并按照标准规范
操作。
内饰相关质量检验标准

车内空气中有机物浓度要求(东风日产乘用车公司)序号项目浓度要求(mg/m3 )1 苯≤0.112 甲苯≤1.103 二甲苯≤1.504 乙苯≤1.505 苯乙烯≤0.266 甲醛≤0.107 乙醛≤0.058 丙烯醛≤0.05检验方法:1.车内空气中有机物的浓度检测按 HJ/T400-2022 的规定进行。
实施采样时,在HJ/T400-2022 规定的环境条件下,受检车辆处于静止状态,车辆门、窗和乘员舱进风口风门均处于关闭状态,发动机和空调等设备不工作。
2.对可能影响检测结果的其他条件(如汽车出厂时的内饰状态改变与否、出厂与检测的间隔时间等),可由相关方商议约定。
内饰材料:汽车内饰零件所用的单一材料或者层积复合材料,如座垫、座椅靠背、座椅套、安全带、头枕、扶手、活动式折叠车顶、所有装饰性衬板(包括门内护板、侧围护板、后围护板、车顶棚衬里)、仪表板、杂物箱、室内货架板或者后窗台板、窗帘、底板覆盖层、遮阳板、轮罩覆盖物、发动机罩覆盖物和其他任何室内有机物,包括装车时吸收碰撞能量的填料、缓冲装置等材料。
技术要求内饰材料的燃烧特性必须满足以下技术要求:燃烧速度不大于 100mm/min。
内饰材料燃烧特性取样要求:标准试样形状和尺寸见下图,试样的厚度为零件厚度,但不超过 13mm。
以不同种类材料进行燃烧性能比较时,试样必须具有相同尺寸(长、宽、高),通常取样时必须使试样沿全长有相同的横截面。
当零件的形状和尺寸不足以制成规定尺寸的标准试样时,则应保证下列最小尺寸试样,但要记录。
a)如果零件宽度介于 3mm~60mm,长度应至少为 356mm。
在这种情况下试样要尽量做成接近零件的宽度。
b)如果零件宽度大于 60mm,长度应至少为 138mm。
此时,可能的燃烧距离相当于从第一标线到火焰熄灭时的距离或者从第一标线开始至试样末端的距离。
c)如果零件宽度介于 3mm~60mm,且长度小于 356mm 或者零件宽度大于 60mm,长度小于 138mm,则不能按 GB 8410 标准试验。
汽车内外饰常用材料性能工艺介绍

汽车内外饰常用材料性能工艺介绍一、汽车内饰常用材料:1.皮革:皮革是最常见的汽车内饰材料之一,具有高级、豪华的外观,舒适的手感和耐久性。
它通常用于座椅、方向盘、仪表板等部位。
2.布料:布料是一种经济实惠、舒适的汽车内饰材料,常用于座椅和内饰的软包装上。
布料可以根据需要选择不同的纤维材料,如棉、尼龙、聚酯等。
3.仿制品:仿制品是一种模仿真皮材料的材质,其外观和性能类似于皮革,但价格更加经济实惠。
它常用于经济型和中低端汽车的内饰。
4.木质饰条:木材是一种常用的内饰材料,给人一种天然、优雅的感觉,常用于中高档车型。
木质饰板可采用真正的木材,也可以是木纹贴皮。
5.塑料:塑料是汽车内饰中最常用的材料之一,具有轻质、易加工、成本低等优点。
塑料可以用于制造方向盘、仪表台、门板等部位。
二、常见材料性能特点:1.耐磨性:汽车内饰材料应具备较高的耐磨性,以便经受长时间使用和摩擦带来的损耗。
2.耐温性:汽车内饰材料应能在不同温度下保持其原有性能和外观,避免因温度变化而产生变形或老化。
3.耐光性:汽车内饰材料需具备一定的耐光性,以避免日晒引起的褪色和变黄。
4.防火性:汽车内饰材料应具备良好的防火性能,以防止火灾蔓延和乘员伤害。
5.舒适性:汽车内饰材料应具有良好的舒适性,如皮革应具备透气性、柔软性和温暖感。
三、常用工艺介绍:1.缝制工艺:汽车座椅和方向盘通常采用缝制工艺,通过缝纫机将材料缝合在一起,增强强度和美观度。
2.焊接工艺:汽车门板、天花板等部位通常采用焊接工艺,通过高温或超声波将材料焊接在一起,使其变得坚固和耐用。
3.粘接工艺:汽车内饰中的一些部件,如仪表板、中控台等,通常采用粘接工艺,使用胶水或胶带将材料固定在一起。
4.喷涂工艺:汽车内饰中的木质饰板或塑料件通常需要进行喷漆处理,以增强其外观和质感。
5.凹凸工艺:汽车内饰中的一些部位,如方向盘和座椅的凸起部分,通常采用凹凸工艺,通过加厚或加填料实现。
6.热压工艺:汽车内饰中的一些部位,如座椅头枕和方向盘,通常采用热压工艺,将材料进行热压成型,增加强度和稳定性。
长安汽车内外饰用聚丙烯材料技术规范

长安汽车内外饰用聚丙烯材料技术规范一、材料选型与物性要求1.1材料选用1.2物性要求聚丙烯材料的物性要求如下:(1) 密度:0.90g/cm³~0.91g/cm³,符合汽车内外饰件的轻量化设计要求。
(2) 熔体流动速率(MFR):6g/10min~15g/10min,适中的MFR,能够保证注塑成型的流动性。
(3)拉伸强度:≥25MPa,保证饰件具有足够的强度和刚性。
(4)弯曲强度:≥30MPa,保证饰件在使用过程中不易断裂。
(5)冲击强度:≥15kJ/m²,确保饰件在碰撞等情况下具有良好的抗冲击性能。
(6)耐候性:符合汽车内外饰件的使用寿命要求,能够长期抵御阳光、雨水和气候变化的侵蚀。
(7)表面质量:材料表面光洁,无明显的气泡、砂眼、线条和划痕等缺陷。
二、材料加工工艺2.1原料处理选择优质的聚丙烯原料,进行干燥处理,确保材料中的水分和杂质含量符合要求,避免在注塑过程中产生气泡和其他缺陷。
2.2注塑成型(1)模具设计:根据饰件的几何形状和尺寸要求,设计合适的注塑模具,确保饰件的精度和质量。
(2)注塑参数:根据材料的熔体流动速率和机械性能,合理设置注塑机的注射压力、注射速度和保压时间等参数。
(3)模温控制:通过模具的温控系统,控制模具温度在适宜的范围内,以保证注塑成型的质量和效率。
(4)除露处理:针对饰件表面的毛刺和射孔等缺陷,进行除露处理,使其表面光滑、平整。
三、饰件的表面处理3.1表面涂装内饰件和特定外饰件需要进行涂装处理,以增强材料的耐候性、防刮擦性和装饰效果。
(1)底涂:采用特定底漆,提高饰件表面的附着力和耐候性。
(2)面涂:采用特定面漆,实现饰件的装饰效果,如金属光泽、亚光和哑光等。
(3)清漆:在面漆干燥后,涂覆透明清漆,增加饰件的光泽度和耐污性。
3.2表面处理部分外饰件需要进行表面处理,以达到特定的效果和要求。
(1)喷砂:通过喷砂处理,增加饰件的粗糙度和防滑性能。
汽车内饰材料标准
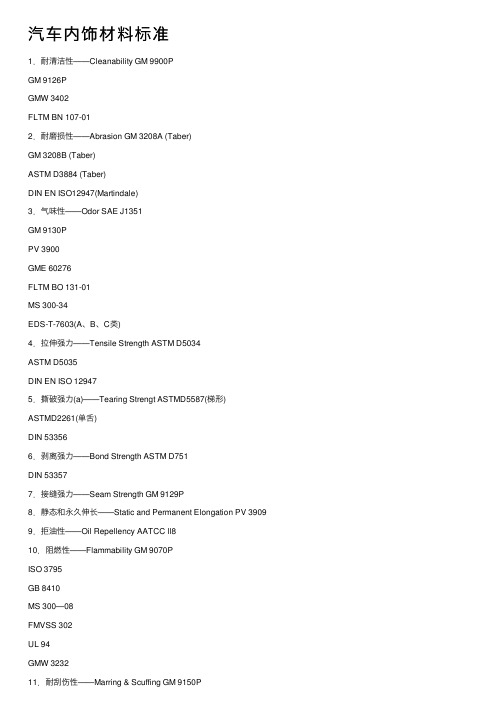
汽车内饰材料标准1.耐清洁性——Cleanability GM 9900PGM 9126PGMW 3402FLTM BN 107-012.耐磨损性——Abrasion GM 3208A (Taber)GM 3208B (Taber)ASTM D3884 (Taber)DIN EN ISO12947(Martindale)3.⽓味性——Odor SAE J1351GM 9130PPV 3900GME 60276FLTM BO 131-01MS 300-34EDS-T-7603(A、B、C类)4.拉伸强⼒——Tensile Strength ASTM D5034ASTM D5035DIN EN ISO 129475.撕破强⼒(a)——Tearing Strengt ASTMD5587(梯形)ASTMD2261(单⾆)DIN 533566.剥离强⼒——Bond Strength ASTM D751DIN 533577.接缝强⼒——Seam Strength GM 9129P8.静态和永久伸长——Static and Permanent Elongation PV 3909 9.拒油性——Oil Repellency AATCC ll810.阻燃性——Flammability GM 9070PISO 3795GB 8410MS 300—08FMVSS 302UL 94GMW 323211.耐刮伤性——Marring & Scuffing GM 9150P12.透⽓性——Air Permeability GB/T 5453ISO 923713.防霉性——Resistance to Mildew GM 9128P(14天)14.尺⼨稳定性——Dimensional Stability SAE J883GM 9452PGM 9452P & GM 950515.⽔解稳定性——Hydrolic Stabilit GM 9231P(168⼩时)16.排⽔性——Water Repellency GM 9317P17.柔韧性——Pliability GM 9664P18.抗起球性——Resistance to Pilling GM 3347PASTM D3512GM 9652PASTM D497019.耐⽔斑、盐渍性——Water Spotting,Salt GM 9133P20.耐汗渍⾊牢度——Colorfastness to Perspiration FLTM BI 113-0622.抗汗性——Resistance to Perspiration GM 9240P23.耐⽔⾊牢度——Dye Stability AA TCC 10724.耐摩擦⾊牢度——Colorfastness to Rubbing AATCC 8FLTM BN 107-0125.拉伸回复性能——Recoverability SAE J85526.SO2点蚀法——Resistance to SO2 GM 9736P27.有机化合物挥发(苯、甲苯、⼆甲苯等)——Benzene、Methylbenzene、Xylene,etc.Head-Space-GC/MS28.总碳挥发——VOC PV 3341TS INT 2029.甲醛含量——Formaldehyde Content PV 3925GME 6027130.重⾦属含量——Heavy Metal GB/F l7593(游离量)31.重⾦属含量(总量法Pb Hg Cd)——Heavy Metal (Total Method)EPA 3050B(产品为塑料件/及其涂层)32.六价铬——Cr6+ GB 746733.氙弧加速⽼化及耐光⾊牢度——Acceleration Aging(Xenon Lamp) & Colorfastness to light SAE J1885SAE J1960GMW 3414PV 390234.纤维降解——Fiber Degradation GM 9771P 35.循环⽼化——Cycle Aging GM 9200P 36.雾化——Fogging SAE J 1756。
lv216-2标准

lv216-2标准
LV216-2标准是指汽车内饰材料的阻燃性能测试标准,是为了保障汽车乘客的
安全而设立的。
在汽车行驶过程中,各种原因可能引发火灾,而阻燃性能良好的内饰材料能够有效减少火灾事故的发生,保护乘客的生命安全。
LV216-2标准要求内饰材料在受到明火烧灼后,其自燃时间应该不超过60秒,并且火焰蔓延的速度应该尽可能地慢,以便乘客有足够的时间逃生。
此外,内饰材料在燃烧的过程中,不能产生大量的有毒气体,以免危害乘客的健康。
LV216-2标准的实施对汽车制造商提出了更高的要求,他们需要选择符合标准
的阻燃材料,严格把控生产过程,确保每一款车型的内饰都符合标准要求。
虽然这增加了汽车生产成本,但却换来了乘客生命安全的保障,是一种值得的投资。
除了汽车制造商,消费者在购车时也应该重视车辆的内饰阻燃性能。
可以通过查看汽车的阻燃性能测试报告,或者询问销售人员来了解车辆的安全性能。
选择通过了LV216-2标准测试的车型,可以更好地保护自己和乘客的安全。
然而,LV216-2标准并不是唯一的阻燃性能测试标准,还有其他一些国际标准
如ISO 3795等。
因此,汽车制造商和消费者在选择阻燃材料时,也需要考虑不同
标准之间的差异,以确保所选材料符合当地法律法规的要求。
总的来说,LV216-2标准的实施提高了汽车内饰材料的阻燃性能,为乘客的生
命安全提供了更好的保障。
汽车制造商和消费者都应该重视这一标准,选择符合要求的阻燃材料,共同营造一个更加安全的出行环境。
希望随着科技的不断进步,汽车的阻燃性能能够得到进一步提升,让每一位乘客都能够安心出行。
内饰材料的性能评价和优化

内饰材料的性能评价和优化一、引言内饰材料是指汽车内部的各种装饰和实用材料,例如座椅、仪表板、门板、内饰踏板等。
这些材料的性能直接影响到汽车的舒适性、安全性和乘坐体验。
因此,对内饰材料的性能评价和优化是汽车设计和生产中非常重要的一环。
二、内饰材料的性能评价1. 耐久性内饰材料要经受长期使用的考验,所以其耐久性是非常重要的指标。
耐久性与材料的化学稳定性、机械强度和抗磨损性等有关。
常用的测试方法包括模拟使用实验、抗磨损实验、耐老化实验等。
2. 可靠性内饰材料的可靠性与其使用寿命和安全性密切相关。
可靠性评价主要考虑材料在极端使用条件下的表现,如高、低温环境、高湿度、紫外线照射等。
测试方法包括高低温循环测试、湿热试验、紫外线照射测试等。
3. 舒适性舒适性是内饰材料的一个重要性能指标,其直接关系到驾乘者的体验和健康。
舒适性评估主要包括对材料的温度、湿度、通风、噪音等影响的评估。
测试方法包括温湿度测试、电机噪声测试、通风评估等。
4. 环境友好性内饰材料的环境友好性评价主要考虑材料对环境的影响。
评估指标包括有毒物质析出量、挥发性有机物排放量、可分解性等。
测试方法包括有毒物质析出测试、挥发性有机物测试、可分解性测试等。
三、内饰材料的优化1. 材料性能的综合考虑内饰材料的性能指标较多,优化时要综合考虑。
例如耐久性好但环境友好性差的材料并不是最佳选择,而是需要在多方面考虑后做出选择。
2. 纳米技术的应用纳米技术的应用对于内饰材料的优化有着显著的影响。
例如,将纳米颗粒添加到材料中可以增强其力学性能,提高材料的耐久度和舒适性。
3. 生态材料的使用生态材料的使用是内饰材料优化的一个趋势。
这些材料具有环保、无毒、低挥发性等特点,可以有效降低材料对环境的影响,提高材料的环保性。
4. 智能化设计随着技术的不断发展,智能化的设计和材料的结合也成为了内饰材料优化的方向之一。
例如将智能材料与座椅相结合,使座椅可以自动感知驾乘者的姿态和需要,提高驾乘者的舒适度。
汽车内饰材料安全标准评价、测试与解决方案

汽车内饰材料平安标准评价、测试及解决方案随着汽车工业的迅猛开展,人们停留在车内的时间越来越长,车内的环境质量将更大限度地影响着人们的安康,也因此越来越受到关注。
车内环境质量的重要污染源是汽车内饰材料,这主要是由纺织品、皮革和塑料等汽车内饰材料在生产加工时残留的有机溶剂造成的,包括苯、甲醛、二甲苯等挥发性有机物,这种原因引起的污染在刚购置的新车中尤其突出。
本文针对汽车内饰材料的平安性能,从车内环境质量控制的几个方面阐述了汽车内饰材料环保平安性能评价指标、相关标准和测试方法,以及车内污染物来源和应对措施。
一、汽车内饰材料平安性能评价指标现有的汽车内饰材料平安性能评价指标主要有雾化值阻燃性、气味、甲醛含量、挥发性有机物散发气体。
国内由于没有适用的车内环境污染物控制标准,一些企业对车内环境污染没有引起足够的重视并未采取相应的措施。
缺乏标准限值的污染物,如多环芳烃等致癌物质将很有可能造成污染物“黑洞〞。
因此,加强对车内环境的监视和检测,增加车内污染物的监测工程,制定车内污染物限值,以客观反映车内空气质量状况,推动车内环境污染的防治,保障消费者的身心安康已迫在眉睫。
1.1 车内空气质量评价(1〕车内空气污染物的来源车内污染物一是来源于汽车主体材料中所含有害物质的释放;二是来源于车内装饰材料中所含有害物质的释放;三是来源于外界污染物的进入;四是来源于车内驾乘人员的生活习惯。
汽车主体用塑料、橡胶和化学纤维等高分子物质中未参加聚合的小分子物质如苯乙烯、醋酸乙烯、丙烯、酚醛类及聚合度较小的分子的释放;车内装饰材料自身及其使用的各种胶粘剂中都会含有污染物并造成车内空气的二次污染,污染物主要有甲醛、苯、甲苯、氯仿、丙酮、二甲苯、烯烃、氯代烃和芳香烃等;外界污染物主要有一氧化碳、碳氢化合物、氢氧化物等,汽车尾气及车内空调蒸发器长期使用后管道内积累的污染物也会进入车内;驾乘人员为改善新车的气味所喷的空气清新剂、甲醛去除剂、车用香料等也是车内空气的二次污染源,驾乘人员在车内吸烟也会增加挥发性有害物质和尘埃之类的空气污染物水平。
汽车内饰选材定义指南

汽车内饰选材定义指南
汽车内饰选材定义指南
内饰篇
内饰件的一般要求:
有足够的抗刮擦性能,以免表面受尖硬物体刮磨出现划痕;具有一定的抗蚀性、耐温、在长期光照下不变色;
满足表面不反光(低光泽)、无异味、长时间高温环境无小分子物质析出、不产生致使车玻璃变模糊的物质、阻燃性好等要求仪表板篇
1.通常仪表板选材考虑的因素:
1)本体材料要有足够的刚性,据分析多款车型总结,弹性模量≥1900Mpa才可满足其刚性要求。
因为仪表板上有许多安装件,如烟灰缸、手套箱、杂物箱、通风口等。
由于仪表板经常被太阳直射,因此高温下的负载能力也是考查仪表板材料的一个重要指标
2)仪表板要有足够的韧性,一般来说冲击强度≥18KJ/M2,因为在一些碰撞时仪表板能够吸收一些能量,降低对乘客的伤害。
除此之外还要考虑材料的低温冲击韧性
3)高温稳定性:仪表板太阳直射部位温度可高达110℃,在110℃/24h下,仪表板本体不出现变形、翘曲及影响外观的表面现象
出现
4)低温稳定性:在-40℃/24h条件下,仪表板本体不出现翘曲、轮廓和曲面歪斜以及影响外观表面的现象出现
5)耐光照色牢度:氙灯照射5个周期(约250h)后,灰度等级≥4级,表面不能有影响外观的现象发生,不能有增塑剂渗出6)气味性、有机物挥发、甲醛含量、重金属等必须满足相关法规要求。
气味性暂时可参考大众公司的企业标准进行定义
7)燃烧性:内饰件燃烧性能为强检项目,按照GB8410试验方法,要求≤100mm/min 8)仪表板表皮环保要求:目前趋势TPO代替PVC 表皮
综合上述诸多因素,从材料和成型工艺分为硬质和软质两种,硬质仪表台外观质量很难达到较高水平,容易出现缩瘪、熔接痕。
- 1、下载文档前请自行甄别文档内容的完整性,平台不提供额外的编辑、内容补充、找答案等附加服务。
- 2、"仅部分预览"的文档,不可在线预览部分如存在完整性等问题,可反馈申请退款(可完整预览的文档不适用该条件!)。
- 3、如文档侵犯您的权益,请联系客服反馈,我们会尽快为您处理(人工客服工作时间:9:00-18:30)。
内饰材料内饰件仿木1.产品功能:提高美观度、增强硬度、提高饰件的耐用性。
2.应用的材料:本体(一般是ABS)+双组份色漆+水转印+清漆3.产品生产工艺:转印膜的印刷→转印工件的预处理→喷底漆→流平→烘干→上架→转印膜的延展→转印膜的活化→转印→水洗→烘干→画膜→喷清漆保护→烘干(表面并不是十分好的,可能会进行一些抛光处理)。
4.产品的性能要求:①产品本身的物理机械性能(ABS材料本身的比重、模塑收缩率、拉伸强度、弯曲强度、弯曲模量、洛氏硬度、伸长率、缺口冲击强度等)②水转印后需要检测其附着性能、耐磨性能、镜面光泽度、漆膜厚度、PH值(补充其具体数值)5.产品检验:底漆出现颗粒(研磨)、底漆喷涂失败(研磨后重新喷涂)、转印出现气泡及白点(修补)成品后基本上靠的是目测为主,看看是否出现颗粒、花纹缺失、花纹错位、花纹不清晰、划痕、色差等。
6.产品开发周期:产品开发一般有两种形式:1.包含ABS本体的模具开发(数据扫描→点云处理→ABS本体设计→转印膜设计→样品试制→试装验证→模具开发→模具件。
这过程需要45天)2.不包含ABS本体的开发即主机厂提供零部件,工厂进行水转印加工(转印膜设计→样品试制→试装验证,这过程需要30天)7.价格测算:特定规格制具面积×制具单价/产品面积(即一个制具能转印多少个产品),制具的单价为280/m2(生晖价格)坐垫1.产品功能:保护汽车原装座椅的皮套不被损坏、方便清洗、美观车内装饰、增加成员乘坐舒适性。
2.产品应用材料:传统的竹编或草质坐垫、亚麻坐垫、冰丝、水牛皮、仿皮、超纤、羊毛座垫。
(以前还有陶瓷、石头、玻璃,不过现在基本上在市面上见不到)传统的竹编或草质坐垫:现竹编或草质的坐垫增加了一些图案,使其变得精美细腻,这种坐垫的优势就是价格低廉,乘坐清凉,但是使用寿命比较短,一般只有一年多。
亚麻坐垫:采用纯天然材料制成(现市面上多采用以亚麻纱与棉纱混纺为主),具有防水作用,并具有耐摩擦、耐高温、散热快等优点。
它的装饰性和舒适性都很强,具有良好的透气性。
常温下使用,人体的实感温度可以下降3~4摄氏度。
冰丝坐垫:冰丝汽车坐垫是由天然棉皮经科学提炼而成,具有良好的透气性能,能自动调节湿度,日照升温慢等特点。
冰丝汽车坐垫还有防霉、防虫、防静电等效果。
水牛皮:水牛皮坐垫具有温凉、透气、防菌等特点,适合高档轿车使用。
日常保存应放在通风干燥处,天气晴朗的时候,在通风阴凉处多多晾晒,切勿在阳光下曝晒。
仿皮:强度高,薄而有弹性,柔软滑润,透气透水性好,并可防水;低温下仍具有较好的抗张强度和曲扰强度,有较好的耐光老化性和耐水解稳定性;耐磨,外观和性能均接近天然皮革,易洗涤去污,易缝制;表面光滑紧密,可进行多种表面处理及染色,品种多样。
羊毛垫:其手感好,不易掉毛,毛茸茸、蓬松松的,一看就觉得有股暖意,提高汽车内饰档次,彰显个性。
3.产品生产工艺:不同的材料其加工工艺不一致竹编或草质坐垫:竹材(草质材料)预处理→竹材手工或机器编织→图案绘制亚麻坐垫:亚麻纱线→半成品填芯辫→按经纬及图案机器编织→修边跟缝边冰丝坐垫:冰丝→半成品填芯辫→按经纬及图案机器编织→修边跟缝边水牛皮:裁剪→缝制→缝制填充物→粘合→缝边仿皮:裁剪→缝制→缝制填充物→粘合→缝边羊毛垫:熟皮→染色→钉制→裁剪→熨烫→上布4.产品性能要求:按纺织产品性能要求,甲醛含量/(mg/kg)≤75,PH值4.0~8.5,染色牢度(耐水、耐酸汗渍、耐干摩擦)≥3级,无异味,禁用可分解致癌芳香胺染料。
甲醛含量的测定按GB/T 2912.1执行,PH值的测定按GB/T 7573执行,耐水色牢度的测定按GB/T 5713执行,耐酸碱汗渍色牢度的测定按GB/T 3922执行,耐干摩擦色牢度的测定按GB/T 3920执行。
5.产品检验:基本靠目测、触摸、嗅觉,检测是否有线头,缝纫线是否整齐,是否有褶皱,是否有刺激性气味。
6.产品开发周期;一周7.产品价格测算:因为不同的花纹,采用的加工工艺会有差距,所以无法进行价格测算尾箱垫1.产品功能:保证尾箱垫的洁净美观,耐脏,拆卸方便,容易清洗。
2.产品材料应用:现用的材料有几种,即其结构形式不一样.①仿皮+无纺布+海绵+EV A(XPE)发泡+麻布;(XPE比EV A产品稍贵,其强度、韧性、抗卷曲柔韧性比EV A好,但是拒水性不如EV A,EV A有耐水性、耐腐蚀性、加工性、防震动性、保温性、隔音性,XPE有绝热性、缓冲性、吸音性、成型性、无毒、无味、耐药品性、耐油、耐酸、耐卤性。
)②EV A(XPE)+麻布;立体成型,轻便且防水性能好,价格便宜,但是有异味,最好放置一段时间再装配,容易出现折痕。
③PE:立体成型,轻便防水性能好,无异味,但是价格较贵。
④橡胶TPO:立体盆型高边、轻便、防水性好、无味;但是容易损坏,怕尖硬物。
3.产品生产工艺:①EV A(XPE)热压成型(铁模)→仿皮裁剪→仿皮缝接→粘贴成型→缝边(一般应用EV A 或XPE这两种材料的产品不可避免的应用到胶水粘贴,都有刺激性气味存在)②EV A(XPE)热压成型→粘贴成型→缝边(一般应用EV A或XPE这两种材料的产品不可避免的应用到胶水粘贴,都有刺激性气味存在)③PE颗粒→热熔→板材→热压(木模)→修边④橡胶TPO颗粒→热熔→板材→热压(木模)→修边4.产品性能要求:按纺织产品性能要求,甲醛含量/(mg/kg)≤75,PH值4.0~8.5,染色牢度(耐水、耐酸汗渍、耐干摩擦)≥3级,无异味,禁用可分解致癌芳香胺染料。
甲醛含量的测定按GB/T 2912.1执行,PH值的测定按GB/T 7573执行,耐水色牢度的测定按GB/T 5713执行,耐酸碱汗渍色牢度的测定按GB/T 3922执行,耐干摩擦色牢度的测定按GB/T 3920执行。
(外观性、燃烧特性、耐热性、耐水性、耐潮湿性)5.产品检验:基本靠目测、触摸、嗅觉,检测是否有线头,缝纫线是否整齐,是否有褶皱,是否有刺激性气味。
6.产品开发周期:5天7.产品价格测算:按所用面料及面积算,PVC(PU)+EV A(XPE)+麻布,90~140元;EVA(XPE)麻布,20~30元;橡胶TPO,110~130元;PE,110~130元脚垫1.产品功能:具有吸水、防尘、防污、隔音、保护原车地毯的一种环保汽车内用品。
可以有效防止鞋底残留的水分、赃物造成与离合器、制动器和油门间的滑动,避免安全隐患,降低内饰被污染和损坏的可能性。
2.产品材料应用:常用的有以下种类:化纤脚垫、.亚麻脚垫、.PVC脚垫、.橡胶脚垫、.呢绒脚垫、.皮革脚垫化纤脚垫(针刺脚垫):麻布+化纤面料+EV A(XPE)优点:汽车厂唯一选用原装配套材质脚垫,有良好的耐蛀、耐腐蚀性能,是环保产品,选料讲究,美观高档。
能将吸水、吸尘、去污、隔音、保护主机毯等功能发挥至极点。
亚麻脚垫:亚麻优点是价格便宜。
缺点是:摸上去比较软,清洗后容易起毛,而且清洗几次之后会变形,导致脚踩上去脚垫表面深陷下去,影响舒适性,为避免滑动建议经常更换。
pvc脚垫(塑料脚垫):PVC 优点:是容易清洗。
缺点:冬天容易变硬,会滑动,部分产品原材料质量不可控,味道重(可能会放邻苯二甲酸二脂的稳定剂,会渗出,有毒)丝圈脚垫:PVC 丝圈脚垫采用当前比较新颖的制作工艺,加入了独特的丝圈植入技术,其特殊的丝圈结构,在实际使用中有着安全舒适,耐脏易洗等特点。
丝圈脚垫的喷丝有韧性,有光泽,手感柔软,背面均匀分布防滑软钉,能有效抓车地板,即使折叠按压后也能迅速反弹,无折痕。
使用寿命一般为两到三年。
橡胶脚垫:橡胶橡胶脚垫跟塑料脚垫一样,清洗都很方便。
橡胶质地脚垫在高温情况下容易变形,而且味道比较重。
.呢绒脚垫:有绒质和纯羊毛两种。
手工产品,价格一般较高,不容易打理。
皮革脚垫:PU皮+EV A(XPE)+麻布例如立体脚垫,清洗方便,缺点是不吸水、吸尘,隔音不好。
3.产品生产工艺:化纤脚垫:裁绒→底布和栽绒粘接→平整毯面→毯面印花亚麻脚垫:亚麻纱线→半成品填芯辫→按经纬及图案机器编织→修边跟缝边pvc脚垫:PVC粒料→熔化→热压成型丝圈脚垫:PVC粒料→熔化→压底面片→喷丝→高温粘合→裁剪→热压成型→修边橡胶脚垫:硫化成型→橡胶处理剂处理→粘贴双面胶→冲压成型呢绒脚垫:绒料裁剪→缝制→修边皮革脚垫:XPE(EV A)热压成型→仿皮裁剪→仿皮缝制→填充物缝制→XPE、仿皮、海绵等粘贴→缝边4.产品的性能要求:按纺织产品性能要求,甲醛含量/(mg/kg)≤75,PH值4.0~8.5,染色牢度(耐水、耐酸汗渍、耐干摩擦)≥3级,无异味,禁用可分解致癌芳香胺染料。
甲醛含量的测定按GB/T 2912.1执行,PH值的测定按GB/T 7573执行,耐水色牢度的测定按GB/T 5713执行,耐酸碱汗渍色牢度的测定按GB/T 3922执行,耐干摩擦色牢度的测定按GB/T 3920执行。
5.产品检验:检测尺寸、检测是否有毛边、是否有色差、是否有异物、是否粘贴牢固6.产品开发周期:两周7.产品价格测算:丝圈地毯1.产品功能:丝圈脚垫采用当前比较新颖的制作工艺,加入了独特的丝圈植入技术,其特殊的丝圈结构,在实际使用中有着安全舒适,耐脏易洗等特点。
丝圈脚垫的喷丝有韧性,有光泽,手感柔软,背面均匀分布防滑软钉,能有效抓车地板,即使折叠按压后也能迅速反弹,无折痕。
使用寿命一般为两到三年。
2.应用的材料:PVC3.产品生产工艺:PVC粒料→熔化→压底面片→喷丝→高温粘合→裁剪→冲压成型→修边4.产品性能要求:气味性检测、物理机械性能(如拉伸强度、弯曲强度、伸长率等)(补充具体数值)5.产品检验:基本靠肉眼判断,检测外观尺寸,检查其粘合程度、喷丝是否均匀、喷丝平面是否平整。
6.产品开发周期:10天(测量数据→模具开发→产品试样)。
注:模具为铝模7.价格测算:按产品面积跟产品厚度计算(一般一套5座产品都是200~300/套)大包围脚垫(立体地毯)1.产品功能:大包围脚垫采用高边设计,能全方位保护原车绒布,保护范围较大,固定紧密,而且还采用原车防滑设计,能让脚垫不会发生走位、打滑等情况,底部的水分不容易挥发,夏天会出现霉变等问题。
2.产品材料应用:仿皮(PU/PVC)+海绵+XPE(EV A)+填充物+麻布3.产品生产工艺:XPE(EV A)热压成型→仿皮裁剪→仿皮缝制→填充物缝制→XPE、仿皮、海绵等粘贴→缝边(一般应用EV A或XPE这两种材料的产品不可避免的应用到胶水粘贴,都有刺激性气味存在)4.产品性能要求:按纺织产品性能要求,甲醛含量/(mg/kg)≤75,PH值4.0~8.5,染色牢度(耐水、耐酸汗渍、耐干摩擦)≥3级,无异味,禁用可分解致癌芳香胺染料。