第4章 型铣和深度加工轮廓
4、外形轮廓铣削加工

顺铣
铣刀与工件接触部位的旋转方向 与工件进给方向相同。
二、工艺知识
逆铣
铣刀与工件接触部位的旋转方向 与工件进给方向相反。
顺铣特点:顺铣时,铣刀刀刃的切削厚度由最大到零, 不存在滑行现象,刀具磨损较小,工件冷硬程度较 轻。垂直分力Fv向下,对工件有一个压紧作用,有 利于工件的装夹。但是水平分力Fh方向与工件进给 方向相同,不利于消除工件台丝杆和螺母间的间隙, 切削时振动大。但其表面光洁度较好,适合精加工。
的终点坐标值; (2)通过G00或G01运动指令建立刀具半径补偿。 (3)D为刀具半径补偿代号地址字,后面一般用两
位数字表示代号。刀具半径值用CRT/MDI方式输入。
❖G41为左偏刀具半径补偿,定义为假设工件不动, 沿刀具运动方向向前看,刀具在零件左侧的刀具半 径补偿,见下图:
❖G42为右偏刀具半径补偿,定义为假设工件不动, 沿刀具运动方向向前看,刀具在零件右侧的刀具半 径补偿,见下图:
①切削深度t:为了保证零件的加工精度和表面粗糙 度, 一般应留一定的余量进行精加工。数控机床的精加工余量 可略小于普通机床。
②切削宽度b:一般b与刀具直径d成正比,与切削深度成 反比。经济型数控机床的加工过程中,一般b的取值范围 为:b=(0.6~0.9)d。
③切削速度v:v的选择主要取决于刀具耐用度。另外, 切削速度与加工材料也有很大关系。
❖以G42为例,刀具半径补偿建立的过程如下图:
注意:
1)建立补偿的程序段,必须是在补偿平面 内不为零的直线移动。
2)建立补偿的程序段,一般应在切入工件 之前完成。
2.取消刀具半径补偿(G40)
❖ 指令格式:
G 40
G
G
00 01
X X
第4章 数控铣削 外轮廓、凸模的加工

变斜角类零件—飞机上的变斜角梁椽条
3.立体曲面类零件(用软件编程) 加工面为空间曲面的零件称为曲面类零件。 这类零件的特点是:一是加工面不能展开成平面,二是 加工面与加工刀具始终为点接触。这类零件在数控铣床加 工中也较为常见,通常采用两轴半联动数控铣床加工精度 要求不高的曲面;精度要求高的曲面需用三轴联动数控铣 床加工,若曲面周围有干涉表面,需用四轴甚至五轴联动数 控铣床加工.
铸铁
π
平口台虎钳装夹工件
铣削用自定心三爪卡盘
铣削用四爪卡盘
万能分度头及其装夹示例
找正定位块后,工件靠紧 定位块用压板装夹工件
直接找正后用压板装夹工件
(b)一面两销定位后夹紧工件
数控铣床坐标系
刀具远离工件的方向为正方向
为 正 为正
一般X轴在水平方向
机床坐标系
4坐标联动数控铣床: 机床主轴可以绕X、Y、Z三个坐标 轴和其其中一个轴作数控摆角联动加工
5坐标联动数控铣床: 机床主轴可以绕X、Y、Z三个坐标 轴和其其中两个轴作数控摆角联动加工
经济型数控铣床
数 控 铣 床 按 数 控 系 统 功 能 分 类
经济型数控铣床一般是在普通立式铣床或卧式铣床 的基础上改造而来的,采用经济型数控系统,成本 低,机床功能较少,主轴转速和进给速度不高,主 要用于精度不高的简单平面或曲面零件加工,如图 5-7所示。
数 控 铣 床 按 数 控 系 统 功 能 图5-7 经济型数控铣床 分 类
图5-8 全功能型数控铣床
图5-9 高速铣削数控铣床
数控铣床主要加工对象
1.平面类零件(主要用手工编程)2.变斜角类零件(用软件编程) 3.立体曲面类零件(用软件编程)
1.平面类零件(主要用手工编程) 指加工面平行或垂直于水平面,以及 较复杂典型平面类零件 加工面与水平面夹角为一定值的零件。 目前数控铣床加工的绝大多数零件属 于平面类零件。这类零件的特点是:加 工面为平面或加工面可以展开为平面。 这类零件的数控铣削相对比较简单,用 三坐标数控铣床的两轴联动就可以加工 出来。
《数控铣床编程与操作项目教程(第3版)》教学课件—04轮廓加工
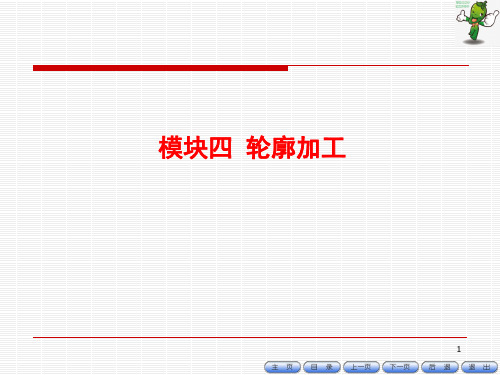
数控系统
公制
英制
法那克系统
G21
G20
西门子系统
G71
G70
4
法那克系统与西门子系统公、英制尺寸输入编程示例
法那克系统
西门子系统
含义说明
N10 G20
N10 G0 G70 X10 Y30 开始输入英制尺寸
模块四 轮廓加工
1
课题1 平面加工
[学习目标]
1.知识目标 ①了解平面铣刀的选用; ②了解公、英制尺寸设定指令; ③掌握进给速度单位设定指令(G94、G95); ④掌握平面铣削工艺的制定及编程方法。 2.技能目标 ①掌握平面铣削方法; ②掌握平面质量控制方法。
2
图4-1-1 零件图
图4-1-2三维效果图
8
(3)每分钟进给量与每转进给量关系 F=nf F:每分钟进给量, n:主轴转速, f :每转进给量
例:每转进给量为0.15mm/r,主轴转速为1000r/min, 每分钟进给量:F=nf=0.15×1000=150 (mm/min)。 (4)指令使用说明 1)数控车床中常默认G95有效,数控铣床中常默认G94有效。 2)G95指令只有在主轴为旋转轴时才有意义。 3)G94、G95更换时要求写入一个新的地址F。 4)G94、G95均为模态有效指令。
24
五、零件检测与评分 六、加工结束、清理机床
25
[资料链接]
数控铣床(加工中心)夹具选择主要考虑产品的生产批量、生 产效率、质量保证及经济性, 在产量小或研制时,应尽量采用组合夹具或通用夹具; 小批量或成批生产时可考虑采用专用夹具; 生产批量较大时,可考虑采用多工位夹具或气动、液压夹具。
数控铣工实训课件-轮廓加工

轮廓加工
4.1.2任务实施
一、工艺分析
1.技术要求分析 该零件为模具镶件,其120*120尺寸及公差由坯料制造时保证。成 形部分即台阶尺寸精度要求较高,且成形尺寸只许正差,这是为后续 工序钳工修正和抛光留量。因此,在编程、加工或机床调整时保证本 工序加工出工件的最大极限尺寸 2.确定加工方案 工件的铣削过程分为三个阶段进行,即加工工艺路线为:粗铣——半 精铣——精铣。
第 8 / 30页
轮廓加工
2.坐标系的确定 编程时选择G54作为工件坐标系,坐标系原点设在工件上 表面几何中心处,即,Φ80圆台圆心。如图4-1-5 b所示。 3.数值计算 由确定的进给路线可知,以刀具中心为基准按轮廓编程, 起刀点均设在X-120.0,Y-120.0,Z100.0处。则三个铣削 过程在XY平面内的有关节点计算如下: 铣平面:行切,每刀沿X方向的切削宽度设为20mm。 切入点坐标:X-40.0 -X=60.0-20.0=40.0
第 18 / 30页
轮廓加工
2.刀具长度补偿指令G43、G44、G49
G43、G44指令是指令机床数控系统在刀具长度的方向的坐标轴上加一个刀 具长度差值或减一个刀具长度差值,编程时使用G43、G44指令必须与具有 直线运动指令配合使用,G43、G44指令才能有效。 指令编程格式: (G17/G18/G19) G01/G00 G43 X Y Z H ; (G17/G18/G19) G01/G00 G44 X Y Z H ; 在G17后的刀具长度补偿指令,只能将刀具长度的补偿值补偿到Z轴。 在G18后的刀具长度补偿指令,只能将刀具长度的补偿值补偿到Y轴。 在G19后的刀具长度补偿指令,只能将刀具长度的补偿值补偿到X轴。
精铣方台轮廓;
轮廓、型腔的铣削加工

实训项目四轮廓、型腔的铣削加工实训目的与要求:1.利用基本指令对轮廓、型腔进行编程、加工;2.掌握用半径补偿功能进行轮廓、型腔的编程、加工;3.合理安排工艺进行零件的加工。
课题一轮廓的铣削加工模块一不带半径补偿的轮廓加工一、编程实例编写如图4-1所示零件加工程序,毛坯尺寸120×800×20,工件材料45号钢。
图4-1 不带半径补偿的轮廓加工二、相关知识点(一)工艺部分1.夹具及刀具选用本例夹具可选规格136mm的机用平口虎钳。
加工外轮廓刀具可选用φ16mm的立铣刀;为提高内壁加工质量,不直接用φ12的键槽铣刀,而是采用φ10mm的键槽铣刀加工腰圆型槽。
刀具切削参数如表4-1所示。
表4–1 刀具与切削用量2.(1)加工路线的确定原则在数控加工中,刀具刀位点相对于零件运动的轨迹称为加工路线。
加工路线的确定与工件的加工精度和表面粗糙度直接相关,其确定原则如下:①加工路线应保证被加工零件的精度和表面粗糙度,且效率较高。
②使数值计算简便,以减少编程工作量。
③应使加工路线最短,这样既可减少程序段,又可减少空刀时间。
④加工路线还应根据工件的加工余量和机床、刀具的刚度等具体情况确定。
(2)切入、切出方法选择采用立铣刀铣削外轮廓侧面时,铣刀在切入和切出零件时,应沿与零件轮廓曲线相切的切线或切弧上切向切入、切向切出(图4-2中A-B-C-B-D)零件表面,而不应沿法向直接切入零件,以避免加工表面产生刀痕,保证零件轮廓光滑。
铣削内轮廓侧面时,一般较难从轮廓曲线的切线方向切入、切出,这样应在区域相对较大的地方,用切弧切向切入和切向切出(图4-3中A-B-C-B-D)的方法进行。
图4-2 外轮廓切线(弧)切入切出图4-3 内轮廓切弧切入切出(3)凹槽切削方法选择加工凹槽切削方法有三种,即行切法(图4-4a)、环切法(图4-4b)和先行切最后环切法(图4-4c)。
三种方案中,a图方案最差(左、右侧面留有残料);c图方案最好。
深度轮廓铣用法

深度轮廓铣用法
1.刀具选择和参数设置:首先,需要创建并选择一把合适的刀具,然后设置刀具的具体参数。
2.陡峭区域加工:当设置为“仅陡峭的”时,只有陡峭度大于指定陡峭“角度”的区域才会被加工,非陡峭区域则不加工。
3.合并距离:这个参数用于将小于指定距离的切削移动的结束点连接起来,以消除不必要的刀具退刀。
当部件表面陡峭度变化较多,或者在非常接近指定的陡峭角度时,陡峭度的微小变化引起退刀,以及在表面间存在小的间隙时,应用合并距离可以减少退刀。
当生成的刀轨有较多的很接近的退刀与进刀路径时,可以将合并距离稍稍改大点。
4.最小切削长度:这个参数用于消除小于指定值的刀轨段。
5.切削层设置:使用“切削层:最优化”选项,系统将根据不同的陡峭程序来设置切削层,使加工后的表面残余相对一致。
此外,深度轮廓铣的进刀方式也有多种选择,例如沿部件斜进刀、光顺进刀等,这些进刀方式的选择会对加工效果和痕迹产生一定影响。
UG NX 8.0数控加工基础教程第4章 型腔铣

行设置。
3.生成型腔铣操作刀具路径 在型腔铣操作对话框中指定了所有参数后,单击对话框底部的“生 成刀具路径”图标 ,即可生成刀具路径。单击“确定”按钮保存生成的 刀具路径,完成型腔铣操作的创建。
4.3.2创建型腔铣一般步骤 创建型腔铣操作时,需首先定义要加工的零件几何体,然后根据零件的形状
指定合适的切削方式,再设置必要的加工参数,最后生成刀具路径,并对生
样做的话),这样就可以省去先创建整个零件的刀具路径,然后使用修剪功能
对刀具路径进行进一步编辑的操作。
4.修剪边界
修剪边界可用于将刀具路径包含在特定的区域 内,通过把裁减侧指定为内部或外部(对于闭合 边界),或指定为左侧或右侧(对于开放边界), 可以定义要从操作中排除的切削区域的面积。在 修剪几何定义时,还可以在切削参数对话框中指
4.5型腔铣的工艺参数设置
型腔铣应用非常广泛,如何确定型腔铣的加工工艺参数成为一
个很关键的问题。如果选择不当,不但会影响所加工零件的尺寸 精度,还会给数控机床带来不必要的损坏。
4.5.1型腔铣切削层设定型腔是水平切削操作,每一层刀轨都在同一平面上。 可以单独指定切削平面,切削平面决定刀具的背吃刀量。切 削层的参数包括总深度和每层深度间距。 在设置型腔铣参数时,切削层是为型腔铣操作指定型 腔铣平面,直接决定选项加工的成败和优劣。 在指定了部件几何体后,“切削层”按钮将被激活。 单击“型腔铣”对话框中的“刀轨设置”选项组的“切削层” 按钮 ,NX将弹出“切削层”对话框。
4.6.1 工艺分析及加工步骤 型腔铣分步完成倒圆角和凸台圆弧粗加工,加工出模型外形的大致轮
廓,然后进行等高轮廓铣加工8个凸台圆弧部分。
1.型腔铣 对模型进行开粗加工,选用D20R3的端铣刀,部件余量为1mm。 2.对模型进行粗加工 铣去上一次剩余的材料,型腔铣或剩余 铣。选用D10R1端铣刀,部件余量为 1mm。 3.对模型进行拐角粗加工 选用D4的球头铣刀,部件余量为1mm。 4.对模型的顶面和底面进行光底精加工 选用D15R0的端铣刀,壁余量为1mm, 部件余量为0。 5.等高轮廓铣 对模型型面进行精加工。选用D1.75的球铣刀,部件余量为0mm。
第4章 型腔铣

4.修剪边界
修剪边界可用于将刀具路径包含在特定的区域 内,通过把裁减侧指定为内部或外部(对于闭合 边界),或指定为左侧或右侧(对于开放边界), 可以定义要从操作中排除的切削区域的面积。在 修剪几何定义时,还可以在切削参数对话框中指 定一个修剪余量,控制刀具与修剪几何体的距离。 刀具在运动时总位于修剪几何上,也就是刀具中 心沿刀轴方向与修剪边界重合,不能指定刀具与 修建几何相切。在“型腔铣”对话框中单击“指 定修剪边界”图标 ,弹出 “修剪边界”对话框。 可以选择平面、曲线或通过点连成直线来定义修 剪区域。以下根据面边界,曲线和点方法分别加 以说明。
在设置型腔铣参数时,切削层是为型腔铣操作指定型腔 铣平面,直接决定选项加工的成败和优劣。
在指定了部件几何体后,“切削层”按钮将被激活。单 击“型腔铣”对话框中的“刀轨设置”选项组的“切削层” 按钮 ,NX将弹出“切削层”对话框。
4.5.2 设置型腔铣切削参数
与平面铣相比,型腔铣主要增加了延伸刀轨、空间范围、容错加工、防止底 切等等选项,这些选项分别位于 “策略”、“余量”和“更多”选项卡上面。
创建方法
设置粗加工参数
(6) 创建工序 单击“创建工序”按钮,弹出“创建工序”对话框。
创建工序对话框
在弹出的“型腔铣”对话框中,根据加工要求和零件特点,在“刀轨设置”、 “机床控制”等选项组进行工艺设置,然后单击“生成” 按钮,将生成刀具路径, 并单击“确认刀轨”按钮 ,,以实体方式进行加工切削仿真。经过验证如果刀具 路径没有问题,即可进行相应的后处理,生成加工代码。
型腔铣操作对话框中的创建几何体图标包括:指定部件,指定毛坯 ,指定 毛坯 ,指定切削区域和指定修剪边界 。可分别定义零件几何体、毛坯几何体、 检查几何体、切削区域和修剪几何体。选择这些几何体,可定义和修改型腔铣 操作的加工区域。零件几何体、毛坯几何体和检查几何体的定义方法与平面铣 相同。在这里只介绍前面没有叙述过的切削区域和修剪几何。
数控加工工艺与编程第4章习题答案
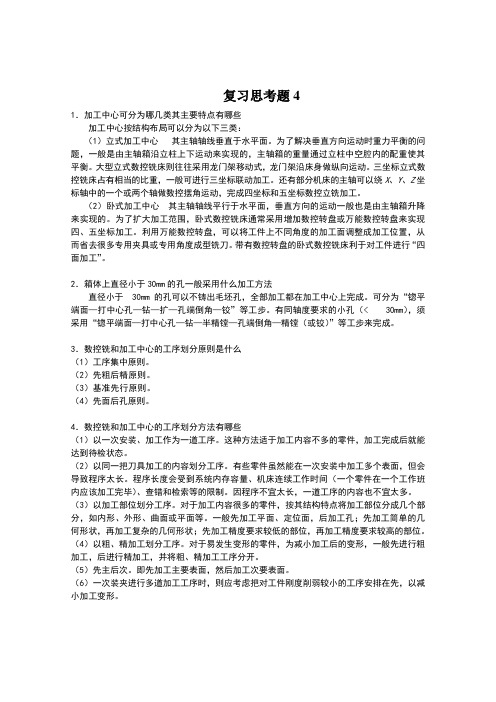
复习思考题41.加工中心可分为哪几类其主要特点有哪些加工中心按结构布局可以分为以下三类:(1)立式加工中心其主轴轴线垂直于水平面。
为了解决垂直方向运动时重力平衡的问题,一般是由主轴箱沿立柱上下运动来实现的,主轴箱的重量通过立柱中空腔内的配重使其平衡。
大型立式数控铣床则往往采用龙门架移动式,龙门架沿床身做纵向运动。
三坐标立式数控铣床占有相当的比重,一般可进行三坐标联动加工。
还有部分机床的主轴可以绕X、Y、Z坐标轴中的一个或两个轴做数控摆角运动,完成四坐标和五坐标数控立铣加工。
(2)卧式加工中心其主轴轴线平行于水平面,垂直方向的运动一般也是由主轴箱升降来实现的。
为了扩大加工范围,卧式数控铣床通常采用增加数控转盘或万能数控转盘来实现四、五坐标加工。
利用万能数控转盘,可以将工件上不同角度的加工面调整成加工位置,从而省去很多专用夹具或专用角度成型铣刀。
带有数控转盘的卧式数控铣床利于对工件进行“四面加工”。
2.箱体上直径小于30mm的孔一般采用什么加工方法直径小于30mm的孔可以不铸出毛坯孔,全部加工都在加工中心上完成。
可分为“锪平端面—打中心孔—钻—扩—孔端倒角—铰”等工步。
有同轴度要求的小孔(<30mm),须采用“锪平端面—打中心孔—钻—半精镗—孔端倒角—精镗(或铰)”等工步来完成。
3.数控铣和加工中心的工序划分原则是什么(1)工序集中原则。
(2)先粗后精原则。
(3)基准先行原则。
(4)先面后孔原则。
4.数控铣和加工中心的工序划分方法有哪些(1)以一次安装、加工作为一道工序。
这种方法适于加工内容不多的零件,加工完成后就能达到待检状态。
(2)以同一把刀具加工的内容划分工序。
有些零件虽然能在一次安装中加工多个表面,但会导致程序太长。
程序长度会受到系统内存容量、机床连续工作时间(一个零件在一个工作班内应该加工完毕)、查错和检索等的限制。
因程序不宜太长,一道工序的内容也不宜太多。
(3)以加工部位划分工序。
30第4章型腔铣和深度加工轮廓铣

图4-1 玩具支架的前模型腔
图4-2 凹形模型零件
4.2 型腔铣的参数设置
【型腔铣】的主界面如图4-3所示,最关键的参数是切削层、切削区域,以及IPW(残留毛坯)的应用型 腔铣的加工原理是在刀轨路径的同一高度内完成一层切削,当遇到曲面时将会绕过,再下降一个高度进行下一层
的切削,系统按照零件在不同深度的截面形状计算各层的道路轨迹,如图4-4所示。
第4章 型腔铣和深度加工轮廓铣
4.1 型腔铣的概述
型腔铣主要用于工件的粗加工,快速去除余量 ,可加工不同形状的模型,也可进行工件的半精加 工和部分精加工。型腔铣的操作原理是通过计算毛 坯除去工件后剩下的材料来产生刀轨,所以只需要 定义工件和毛坯即可计算刀轨轨迹,使用方便且智 能化程度高。
4.1.1 型腔铣与平面铣的比较
步骤09:修改【切削模式】为【跟随周边】选项。如图4-26所示
4.2.2 切削区域
/轮廓线裁剪 在【切削参数】对话框中,可以在【空间氛围】选择卡中将【修剪方式】设定为【轮廓线】,则系统利用工件几何体最大轮 廓线决定切削范围,刀具可以定位到从这个范围偏置一个刀具半径的位置,如图4-8所示。 /参考刀具 在【切削参数】对话框的【空间氛围】选项卡中,可以设定参考刀具,如图设定此参数来创建清角刀轨,在对话框右边有产 生的刀轨示意。还可设置【重叠距离】对刀轨进行进一步的控制,如图4-9所示。
/陡峭角度 此参数限定加工区域的陡峭程度,而非陡峭面采取另外的加工方式,两者结合,达到对工件完整光 顺精加工的目的,如图4-13所示。
图4-12 【深度加工轮廓】主界面
图4-13 【刀轨设置】参数
4.3
深度加工轮廓铣操作
/混合切削模式 当每层的导轨没有封闭时,单向切削模式会生成许多提刀,采用混合切削模式避免提刀,可以提高加 工效率,使刀轨更为美观,如图4-14所示。
数控加工工艺与编程(程俊兰)第4章 习题答案

复习思考题41.加工中心可分为哪几类?其主要特点有哪些?加工中心按结构布局可以分为以下三类:(1)立式加工中心其主轴轴线垂直于水平面。
为了解决垂直方向运动时重力平衡的问题,一般是由主轴箱沿立柱上下运动来实现的,主轴箱的重量通过立柱中空腔内的配重使其平衡。
大型立式数控铣床则往往采用龙门架移动式,龙门架沿床身做纵向运动。
三坐标立式数控铣床占有相当的比重,一般可进行三坐标联动加工。
还有部分机床的主轴可以绕X、Y、Z坐标轴中的一个或两个轴做数控摆角运动,完成四坐标和五坐标数控立铣加工。
(2)卧式加工中心其主轴轴线平行于水平面,垂直方向的运动一般也是由主轴箱升降来实现的。
为了扩大加工范围,卧式数控铣床通常采用增加数控转盘或万能数控转盘来实现四、五坐标加工。
利用万能数控转盘,可以将工件上不同角度的加工面调整成加工位置,从而省去很多专用夹具或专用角度成型铣刀。
带有数控转盘的卧式数控铣床利于对工件进行“四面加工”。
2.箱体上直径小于30mm的孔一般采用什么加工方法?直径小于φ30mm的孔可以不铸出毛坯孔,全部加工都在加工中心上完成。
可分为“锪平端面—打中心孔—钻—扩—孔端倒角—铰”等工步。
有同轴度要求的小孔(< φ30mm),须采用“锪平端面—打中心孔—钻—半精镗—孔端倒角—精镗(或铰)”等工步来完成。
3.数控铣和加工中心的工序划分原则是什么?(1)工序集中原则。
(2)先粗后精原则。
(3)基准先行原则。
(4)先面后孔原则。
4.数控铣和加工中心的工序划分方法有哪些?(1)以一次安装、加工作为一道工序。
这种方法适于加工内容不多的零件,加工完成后就能达到待检状态。
(2)以同一把刀具加工的内容划分工序。
有些零件虽然能在一次安装中加工多个表面,但会导致程序太长。
程序长度会受到系统内存容量、机床连续工作时间(一个零件在一个工作班内应该加工完毕)、查错和检索等的限制。
因程序不宜太长,一道工序的内容也不宜太多。
(3)以加工部位划分工序。
最新全套 MasterCAM第四章 挖槽类零件加工编程范例和参数设定
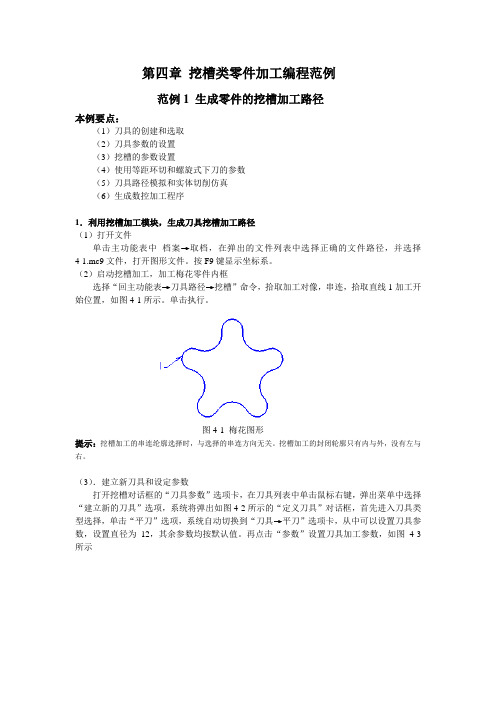
第四章挖槽类零件加工编程范例范例1 生成零件的挖槽加工路径本例要点:(1)刀具的创建和选取(2)刀具参数的设置(3)挖槽的参数设置(4)使用等距环切和螺旋式下刀的参数(5)刀具路径模拟和实体切削仿真(6)生成数控加工程序1.利用挖槽加工模块,生成刀具挖槽加工路径(1)打开文件单击主功能表中档案→取档,在弹出的文件列表中选择正确的文件路径,并选择4-1.mc9文件,打开图形文件。
按F9键显示坐标系。
(2)启动挖槽加工,加工梅花零件内框选择“回主功能表→刀具路径→挖槽”命令,拾取加工对像,串连,拾取直线1加工开始位置,如图4-1所示。
单击执行。
图4-1 梅花图形提示:挖槽加工的串连纶廓选择时,与选择的串连方向无关。
挖槽加工的封闭轮廓只有内与外,没有左与右。
(3).建立新刀具和设定参数打开挖槽对话框的“刀具参数”选项卡,在刀具列表中单击鼠标右键,弹出菜单中选择“建立新的刀具”选项,系统将弹出如图4-2所示的“定义刀具”对话框,首先进入刀具类型选择,单击“平刀”选项,系统自动切换到“刀具→平刀”选项卡,从中可以设置刀具参数,设置直径为12,其余参数均按默认值。
再点击“参数”设置刀具加工参数,如图4-3所示图4-2 选择刀具形式图4-3 设置刀具参数点击“工作设定”弹出“工作设定”视窗,进给率的计算选择为依照刀具。
确定在“挖槽”视窗中,选择“挖槽参数”选项卡,设置XY方向预留量设为0,由于零件上表面的Z=0,故设置进给下刀位置为3.0和参考高度设置为30.0,加工深度按零件要求设为-10。
注意绝对坐标和增量坐标的选择,参数设置如图4-4所示。
图4-4 挖槽参数设置分层铣深参数。
在“Z轴分层铣深”前打勾,单击“Z轴分层铣深”按钮,打开“Z 轴分层铣深设定”对话框,如图4-5所示,设置分层铣深参数。
最大粗切量为0.5mm;精铣次数为0;其余参数按照默认值单击“确定”按钮返回到外形铣削参数对话框。
图4-5 Z轴分层铣深参数在“挖槽”视窗中,选择“粗切精修参数”选项卡,选用“等距环切”加工方法,切削间距为刀具直径的80%(切削间距(距离)计算方法是:{刀具直径-刀R角*2}*80%。
30第4章型腔铣和深度加工轮廓铣

显示 可重新显示范围以作为视觉参考。
插入范围 删除当前范围
图4-5 【切削层】对话框
图4-6 自动形成切削层图例
4.1.2 切削层
2.用户定义切削层 允许用户通过定义每个新范围的底 面来创建范围,通过选择面定义的范围 将保持与部件的关联性,但不会检测新 的水平表面。 3.单个切削层 根据部件和毛坯几何体设置一个切 削范围,如图4-7所示。在单个切削层中 只能修改顶层和底层。
部件几何体
毛坯几何体
图4-3 【型腔铣】对话框
图4-4 【型腔铣】的几何体
4.2.1 切削层
切削层为型腔铣操作指定切削平面。切削层由切削深度范围和每层深度来定义。一个范围有两个垂直于刀轨矢 量的小平面来定义,可以同时定义多个切削范围。每个切削范围可以根据部件几何体的形状确定切削层的切削深度, 各个切削范围都可以独立地设定各自的均匀深度。
第4章 型腔铣和深度加工轮廓铣
4.1 型腔铣的概述
型腔铣主要用于工件的粗加工,快速去除余量 ,可加工不同形状的模型,也可进行工件的半精加 工和部分精加工。型腔铣的操作原理是通过计算毛 坯除去工件后剩下的材料来产生刀轨,所以只需要 定义工件和毛坯即可计算刀轨轨迹,使用方便且智 能化程度高。
4.1.1 型腔铣与平面铣的比较
顶部:从第一个切削范围的顶部开始测量范围深度值。
范围顶部:从当前突出显示的范围的顶部开始测量范围深度值。
范围底部:从当前突出显示的范围的底部开始测量范围深度。也可
使用滑尺来修改范围底部的位置。
WCS原点:从工作坐标系原点处开始测量范围深度值。
信息
在单独的窗口中显示关于该范围的详细说明。
当前范围底面深度
图4-1 玩具支架的前模型腔
UG操作子类型
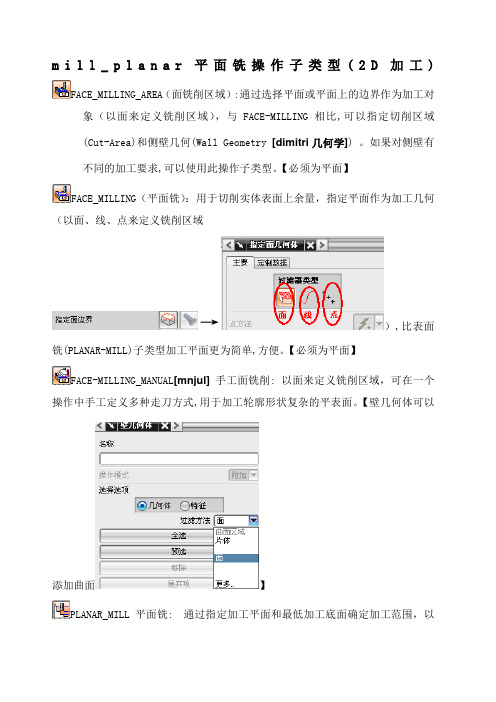
m i l l_p l a n a r平面铣操作子类型(2D加工) FACE_MILLING_AREA(面铣削区域):通过选择平面或平面上的边界作为加工对象(以面来定义铣削区域),与FACE-MILLING 相比,可以指定切削区域(Cut-Area)和侧壁几何(Wall Geometry[dimitri几何学]) 。
如果对侧壁有不同的加工要求,可以使用此操作子类型。
【必须为平面】FACE_MILLING(平面铣):用于切削实体表面上余量,指定平面作为加工几何(以面、线、点来定义铣削区域→),比表面铣(PLANAR-MILL)子类型加工平面更为简单,方便。
【必须为平面】FACE-MILLING_MANUAL[mnjul]手工面铣削: 以面来定义铣削区域,可在一个操作中手工定义多种走刀方式,用于加工轮廓形状复杂的平表面。
【壁几何体可以添加曲面】PLANAR_MILL平面铣:通过指定加工平面和最低加工底面确定加工范围,以面、线、点来定义铣削区域,可以修剪、检测几何体,是平面铣的基本形式, 其他平面铣操作子类型可以理解为此种形式的特例。
PLANAR_PROFILE平面轮廓加工:没有切削方法选择,只用于平面轮廓加工(用于光侧或清根)。
profile [prufail]ROUGH_FOLLOW跟随零件粗加工:跟随零件轮廓走刀,其默认的切削方式为跟随零件走刀(Follow Part),主要用于挖腔粗加工。
rough [rf]ROUGH_ZIGZAG往复粗加工:往复式走刀, 其默认的切削方式为往复式走刀(ZigZag) ,可用于挖槽粗加工或铣平面。
ROUGH_ZIG单向粗加工:单向走刀, 其默认的切削方式为单向轮廓走刀(Zig with Contour) ,可保持单纯的顺铣或逆铣加工。
CLEANUP_CORNERS清理拐角(清角):清除上一步平面加工未清除的余量(即光底),清理拐角,其默认的切削方式为跟随零件走刀(Follow Part) ,使用此操作子类型可清理内拐角的残余材料(2D残料加工)。
数控铣床知识--轮廓加工(PPT 54张)

★
掌握内轮廓铣 削的加工工艺 的设计方法
掌握内轮廓铣
削的编程方法
26
任务二【知识准备】
一 二
三
内轮廓的加工工艺 螺旋类加工
子程序
27
任务二 【知识准备】
一、内轮廓的加工工艺
1.加工内轮廓时的Z向进刀方式
(1)垂直切深进刀 (2)在工艺孔中进刀
(3)三轴联动斜线进刀
(4)三轴联动螺旋线进刀
28
任务二 【知识准备】
6
任务一 【技能目标】
●
●
掌握外轮廓铣削的编程方法 掌握刀具半径补偿的基本概念 能熟练运用刀具半径补偿进行编程
●
●
了解数控铣削加工阶段的划分方法
7
任务一【知识准备】
一 二 三 四 五 六
数控铣削加工工序的划分 铣削内外轮廓的进给路线 数控加工工艺文件 手工编程中基点的计算 指令介绍 刀具半径补偿
掌握可转位刀片的刀尖圆弧半径与表面粗糙度的关系
掌握子程序的应用方法
40
●
任务三 【知识准备】
一 二 三
机夹可转位刀片及代码 极坐标与柱面坐标 坐标变换
41
任务三 【知识准备】
一、机夹可转位刀片及代码
1.可转位刀片的表示方法
可转位刀片十个号位表示的内容
加工
工艺系统
11 12
35
任务二 【任务实施】
表3.21 表面粗糙度影响因素分析
影响因素 装夹与校正
序号 1 3
产生原因 工件装夹不牢固,加工过程中产生振动 刀具磨损后没有及时修磨 刀具刚度差,刀具加工过程中产生振动 主偏角、副偏角及刀尖圆弧半径选择不当
刀具
4 5
6
4轮廓铣削
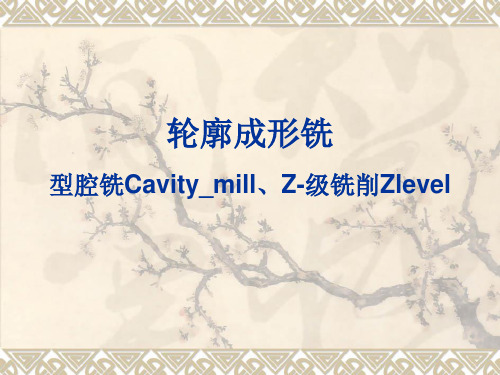
➢注意:若没有定义毛坯几何体时, 如果修剪方式为无,将不能生成刀具 路径,此时系统将提示在没有岛的周 围定义要切削的材料;若设置为轮廓 线或者外部边,则可以生成刀具路径。
❖ 单步向上:指定控制切削层数的值。 ❖ 最大切削宽度:是刀具可切削的最大宽度
(俯视刀轴时)。如果比刀具半径小,则刀 具的底部中央位置有一个未切削部分。对于 对中切削刀具,将最大切削宽度设为50%或 更高,以使切削量达到最大。对非对中切削 刀具,设置为50%以下。
3.1 插铣刀轨设置
❖ 点:该选项用来设置预钻孔进刀点和切削区 域起点。
➢ 等高轮廓铣、清根加工、角落粗铣等操作是轮廓铣中常用的 铣削方式。
➢ 轮廓铣操作可移除平面层中的大量材料,由于在铣削后会残 留余料,因此轮廓铣最常用于在精加工操作之前对材料进行 粗铣。
轮廓成形铣概述
➢ 轮廓铣的加工过程与平面铣类似,都是用平面的切削层(垂 直于刀轴)去除大量材料。
➢ 二者不同的是定义几何体的方法,平面铣使用边界定义加工 几何体,而轮廓铣可以使用边界、面、曲线和实体,并且常 用实体来定义模具的型腔和型芯。
3.2 插铣粗加工设置
❖ 用于粗加工的插削几何体与型腔铣非常相似, 支持部件、毛坯、检查、切削区域和修剪几 何体;
❖ 使用指定的切削区域、切削区域之上的毛坯 量和切削区域延伸量,以便确定要切削的量;
❖ 使用插削层对话框确定插削层,与切削层 (单个范围)类似。
❖ 毛坯不是粗加工操作所必须的。如果型腔是 封闭的并且没有毛坯,则从假定的毛坯顶部 开始插入。
第四章-型腔铣加工
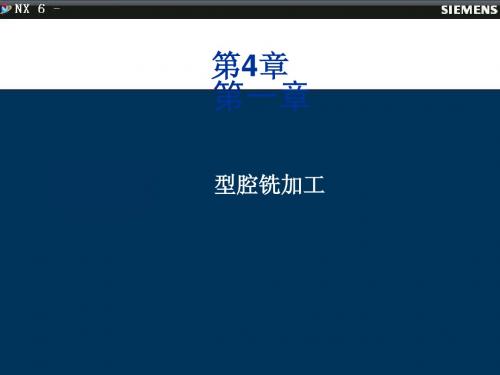
处理中的工件: 当希望在生成刀轨时考虑先前操作 剩余的材料时,可在操作中使用 IPW。 使用3D:用于在同一几何体组中 使用先前操作的3D IPW几何体。 使用基于层的:基于层的IPW使用 先前操作中的2D切削区域来确定 和加工剩余材料。基于层的IPW可 以高效地切削先前操作中留下的拐 角和阶梯面。当加工简单部件时, 刀轨处理时间较3D IPW显著减少; 加工大型的复杂部件时,所需时间 更是大大减少。
切削参数
在边上延伸 使用 “在边上延伸”来 加工部件周围多余的铸 件材料。还可以使用它 在刀轨刀路的起点和终 点添加切削运动,以确 保刀具平滑地进入和退 出部件。 刀路将以相切 的方式在切削区域的所 有外部边缘上向外延伸, 如图所示。
修剪由: 可以使系统在没有明 确定义毛坯几何体的 情况下识别出型芯部 件的毛坯几何体。
等高轮廓铣
等高轮廓铣加工的设计目的工只能切削部件的陡峭区域 或整个部件。除了部件几何体,还可以将切削区域几何体指 定为部件几何体的子集,以限制要切削的区域。如果没有定 义任何切削区域几何体,则系统将整个部件几何体当作切削 区域。在生成刀轨的过程中,系统将跟踪该几何体,需要时 检测部件几何体的陡峭区域,对跟踪形状进行排序,识别要 加工的切削区域,以及在所有切削层都不过切部件的情况下 对这些区域进行切削。 等高轮廓铣的一个重要功能就是能够指定陡角,以区分陡峭 与非陡峭区域。将陡角切换为“开”时,只有陡峭度大于指 定陡角的区域才执行轮廓铣。将陡角切换为“关”时,系统 将对整个部件执行轮廓铣。
设置加工环境
打开软件,调入需要加工的产品模型,然后 进入加工模块,如果该产品模型是第一次进 入加工模块,系统将会弹出“加工环境设置” 对话框,在“CAM会话设置”列表中选择 “cam_general”,在“要创建的CAM设置” 列表中选择“mill_contour”进入初始化。
- 1、下载文档前请自行甄别文档内容的完整性,平台不提供额外的编辑、内容补充、找答案等附加服务。
- 2、"仅部分预览"的文档,不可在线预览部分如存在完整性等问题,可反馈申请退款(可完整预览的文档不适用该条件!)。
- 3、如文档侵犯您的权益,请联系客服反馈,我们会尽快为您处理(人工客服工作时间:9:00-18:30)。
第4章型腔铣和深度加工轮廓学习提示:型腔铣主要用于工件的粗加工,快速去除毛坯余量,可加工平面铣无法加工的零件形状,一般包括带拔模角度的零件侧壁和带曲面的零件等。
本章介绍型腔铣的加工特点、型腔铣的适用范围,与深度加工轮廓铣的异同;重点介绍型腔铣和深度加工轮廓的参数设置,包括切削层、切削参数、处理中的工件(IPW)等。
最后通过实例来说明型腔铣和深度加工轮廓铣操作的运用。
技能目标:了解型腔铣和深度加工轮廓的应用范围,掌握设置切削层、切削参数的方法,掌握型腔铣和深度加工轮廓铣操作的设置方法。
4.1 型腔铣基础理论型腔铣主要用于工件的粗加工,快速去除毛坯余量,可加工平面铣无法加工的零件形状,一般包括带拔模角度的零件侧壁和带曲面的零件等。
型腔铣的操作原理是通过计算毛坯除去工件后剩下的材料来产生刀轨,所以只需要定义工件和毛坯即可计算刀位轨迹,使用方便且智能化程度高。
本章将先介绍型腔铣的基本设置,再通过实例说明型腔铣的应用思路。
4.1.1 型腔铣与平面铣的比较型腔铣与平面铣操作都是在水平切削层上创建的刀位轨迹,用来去除工件上的材料余量。
大部分情况下,特别是粗加工,型腔铣可以替代平面铣,但平面铣也有它独特的优势。
下面对型腔铣和平面铣进行比较。
1. 相同点(1)型腔铣与平面铣刀具轴都垂直于切削层平面。
(2)型腔铣与平面铣的大部分参数基本相同,如切削方式、进刀和退刀、控制点、切削参数选项,拐角控制选项等。
2. 不同点(1)定义工件和毛坯的几何体类型不同,平面铣使用边界,型腔铣大部分使用实体,也可使用小平面和边界。
(2)切削深度的定义不同,平面铣通过指定的边界和底面的高度差来定义总的切削深度。
型腔铣是通过毛坯几何体和零件几何体来定义切削深度。
4.1.2 型腔铣的适用范围型腔铣的适用范围很广泛,可加工的工件侧壁可垂直或不垂直,底面或顶面可为平面或曲面如模具的型芯和型腔等。
可用于大部分的粗加工,直壁或斜度不大的侧壁的精加工,通过限定高度值,只作一层切削,型腔铣也可用于平面的精加工以及清角加工等。
适用于型腔铣的工件类型有如图4-1和图4-2所示。
图4-1打印机盖板的后模型腔图4-2 塑料前模型芯4.1.3 型腔铣的参数设置型腔铣创建操作的主界面如图4-3所示,型腔铣最关键的参数是切削层、切削区域,以及IPW(残留毛坯)的应用。
本节先介绍型腔铣的加工原理,然后对型腔铣的参数设置作讲解。
图4-3 【型腔铣】对话框型腔铣的加工原理是在刀具路径的同一高度内完成一层切削,当遇到曲面时将会绕过,再下降一个高度进行下一层的切削,系统按照零件在不同深度的截面形状计算各层的道路轨迹。
如图4-4所示的零件,分4层切削,在不同的层里,道路轨迹也有所不同。
1. 切削层切削层是为型腔铣操作指定切削平面。
切削层由切削深度范围和每层深度来定义。
一个范围由两个垂直于刀轴矢量的小平面来定义,同时可以定义多个切削范围。
每个切削范围可以根据部件几何体的形状确定切削层的切削深度,各个切削范围都可以独立地设定各自的均匀深度。
图4-4 【型腔铣】的切削层在【型腔铣】对话框下【刀轨设置】选项中单击【切削层】按钮,打开【切削层】对话框,如图4-5所示。
在【切削层】对话框中,型腔铣操作提供了全面、灵活的方法对切削范围、切削深度进行调整。
下面讲解切削层中的各个选项的理解和用法。
图4-5【切削层】对话框(1)自动生成切削层自动生成将范围设置为与任何水平平面对齐,这些是部件的关键深度。
只要没有添加或修改局部范围,切削层将保持与部件的关联性,系统将检测部件上的新的水平表面,并添加关键层与之匹配。
选择这种方式时系统会自动寻找部件中垂直于刀轴矢量的平面。
在两平面之间定义一个切削范围,并且在两个平面上生成一种较大的三角形平面之间表示一个切削层,每两个小三角形平面之间表示范围内的切削深度,如图4-6所示。
图4-6 自动生成切削层图例◆仅在底部范围在【切削层】对话框中选择“仅在底部范围”复选框时,则在绘图区只保留关键切削层,如图4-7所示,该参数设定只加工关键切削层的深度,即只加工工件存在平面区域的深度,该参数常用于精加工。
◆切削深度切削深度可分为总的切削深度和每一刀的深度,每一刀的深度可以定义为全局切削深度和某个切削范围内的局部削深度。
如图4-8所示。
图4-7 仅在底部切削的切削层图4-8 切削深度◆当前范围信息向上和向下箭头:使用向上和向下箭头从各个范围中进行选择。
图形区域中突出显示的范围(以选择颜色显示)是当前的活动范围。
其他范围将以部件颜色显示。
当突出显示每个范围时,该范围的编号和层将显示在上/下箭头的上方,【范围深度】文本框中将显示该范围当前的深度值。
◆插入范围使用【插入范围】可在当前的范围下添加一个新范围。
◆编辑当前范围使用“编辑当前范围”可修改当前范围。
◆删除当前范围使用【删除当前范围】可删除当前的范围。
当删除一个范围时,所删除范围之下的一个范围将会进行扩展以自顶向下填充缝隙。
如果删除仅有的一个范围时,系统将恢复默认的切削范围,该范围将从整个切削体积的顶部延伸至底部。
◆测量开始位置顶层:从第一个切削范围的顶部开始测量范围深度值。
范围顶部:从当前突出显示的范围的顶部开始测量范围深度值。
范围底部:从当前突出显示的范围的底部开始测量范围深度值。
也可使用滑尺来修改范围底部的位置。
WCS原点:从工作坐标系原点处开始测量范围深度值。
◆信息在单独的窗口中显示关于该范围的详细说明。
◆显示可重新显示范围以作为视觉参考。
(2)用户定义切削层允许用户通过定义每个新范围的底面来创建范围,通过选择面定义的范围将保持与部件的关联性。
但不会检测新的水平表面。
(3)单个切削层根据部件和毛坯几何体设置一个切削范围,如图4-9所示。
在单个切削层中只能修改顶层和底层。
图4-9 单个切削层图例2. 切削区域型腔铣操作提供了多种方式来控制切削区域。
下面对5种切削区域定义方式分别进行介绍。
◆检查几何体与平面铣类似,型腔铣的检查几何体用于指定不允许刀具切削的部位,如压板、虎钳等,不同之处是腔铣可用实体等几何对象定义任何形状的检查几何体。
可以用片体、实体、表面、曲线定义检查几何体。
◆修剪边界修剪边界用于修剪刀位轨迹,去除修剪边界内侧或外侧的刀轨,必须是封闭边界。
◆切削区域切削区域用于创建局部刀具路径。
可以选择部件表面的某个面或面域作为切削区域,而不选择整个部件,这样就可以省去先创建整个部件的刀具路径,然后使用修剪功能对刀路径进行进一步编辑的操作。
当切削区域限制在较大部件的较小区域中时,切削区域还可以减小系统计算路径的时间。
◆轮廓线裁剪在【切削参数】对话框中,当打开容错加工时,可以在【空间范围】选项卡中将【修剪由】设定为“轮廓线”,则系统利用工件几何体最大轮廓线决定切削范围,刀具可以定位到从这个范围偏置一个刀具半径的位置,如图4-10所示。
图4-10 【切削参数】对话框◆参考刀具在【切削参数】对话框的【空间范围】选项卡中,可以设定参考刀具,如图4-11所示,设定此参数常来创建清角刀轨,在对话框右边有产生的刀轨示意。
还可设【重叠距离】,对刀轨进行进一步的控制。
图4-11 【空间范围】对话框3. 处理中的工件(IPW)IPW就是In Process Workpiece,是指工序件的意思。
该选项主要用于二次开粗,是型腔铣中非常重要的一个选项。
处理中的工件(IPW)也就是操作完成后保留的材料,该选项可用的当前输出操作(IPW)的状态,包括3个选项。
“无”、“使用3D”和“使用基于层的”如图4-12所示。
图4-12处理中的工件选项图4-13“无”处理中的工件◆无:该选项是指在操作中不使用处理中的工件。
也就是直接使用几何体父节点组中指的毛坯几何体作为毛坯来进行切削,不能使用当前操作加工后的剩余材料作为当前操作的毛坯几何体,如图4-13所示。
◆使用3D:该选项是使用小平面几何体来表示剩余材料。
选择该选项,可以将前一操作加工后剩余的材料作为当前操作的毛坯几何体,避免再次切削已经切削过的区域,如图4-14所示。
图4-14使用3D处中的工件图4-15使用基于层的选项工程提示:在使用3D选项时,必须在选择的父节点中已经指定了毛坯几何体,否则在创建刀具路径时弹出警告对话框。
提示几何体绷带没有定义毛坯几何体,不能生成刀具路径。
使用基于层:该选项和“使用3D”类似,也是使用先前操作后的剩余材料作为当前操作的毛坯几何体并且使用先前操作的刀轴矢量,操作都必须位于同一几何父节点组内。
使用该选项可以高效地切削先前操作中留下的弯角和阶梯面,如图4-15所示。
工程提示:在二次开粗时:如果当前操作使用的刀具和先前操作的刀具不一样,建议“使用3D”选项;如果当前操作使用的刀具和先前刀具一样,只是改变了步进距离或切削浓度,建议选择“使用基于层”选项。
在定义IPW时,【空间范围】对话框会出现【最小移除材料】文本框,最小移除材料厚度值是在部件余量上附加的余量,使生成的处理中的工件比实际加大后的工序件稍大一点。
如图4-16所示。
比如当前操作指定的部件余量是0.5mm,而最小移除材料厚度值是0.2mm,生成的处理中的工件的余量是0.7mm。
可以理解为,前一个IPW的余量在0.7以上的区域才能被本操作加工到。
内图4-16 最小移除材料IPW可以成功执行的条件是,在使用之前的所有操作都必须有同一个几何体组之下,且全部操作已生成。
工程提示:IPW常用于半精加工,清除前一把刀具铣不到的角落和无法下刀的区域。
优先使用“跟随工件”的切削方式,生成的刀轨安全高效,智能化程度高。
4.1.4 深度加工轮廓操作深度加工轮廓铣操作是型腔铣的特例,经常应用到陡峭曲面的精加工和半精加工,相对于型腔铣的“配置文件”方式,增加了一些特定的参数,如陡峭角度、混合切削模式、层间过渡、层间剖切等,其主界面如图4-17所示:图4-17 深度加工轮廓(ZLEVEL-PROFILE)主界面现对深度加工轮廓操作与型腔铣操作的区别,分别介绍如下。
(1)陡峭角度此参数限定被加工区域的陡峭程度,而非陡峭面采用另外的加工方式,两者结合,达到对工件完整光顺精加工的目的。
参数设定如图4-18所示。
(2)混合切削模式当每层的刀轨没有封闭时,单向切削模式会产生许多提刀,采用混合切削模式避免提刀,可以提高加工效率,使刀轨更为美观。
参数设定如图4-19所示。
图4-18“陡峭角度”参数图4-19“混合”切削参数(3)层间过渡提供了2种层到层之间的过渡方法,其中“直接对部件进刀”避免了提刀,使得产生的刀轨更为精简。
参数设定如图4-20所示。
图4-20 【层到层】参数(4)层间剖切设定层间切削的步距和最大移动距离,可以实现在进行深度轮廓加工时,对非陡峭面进行均匀加工。
参数设定如图4-21所示。