关于加工深度的精确控制- MasterCAM
mastercam精加工的用法
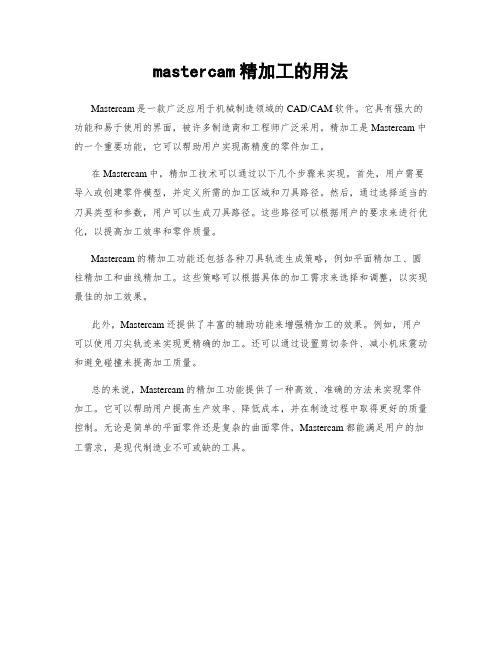
mastercam精加工的用法
Mastercam是一款广泛应用于机械制造领域的CAD/CAM软件。
它具有强大的功能和易于使用的界面,被许多制造商和工程师广泛采用。
精加工是Mastercam中的一个重要功能,它可以帮助用户实现高精度的零件加工。
在Mastercam中,精加工技术可以通过以下几个步骤来实现。
首先,用户需要导入或创建零件模型,并定义所需的加工区域和刀具路径。
然后,通过选择适当的刀具类型和参数,用户可以生成刀具路径。
这些路径可以根据用户的要求来进行优化,以提高加工效率和零件质量。
Mastercam的精加工功能还包括各种刀具轨迹生成策略,例如平面精加工、圆柱精加工和曲线精加工。
这些策略可以根据具体的加工需求来选择和调整,以实现最佳的加工效果。
此外,Mastercam还提供了丰富的辅助功能来增强精加工的效果。
例如,用户可以使用刀尖轨迹来实现更精确的加工。
还可以通过设置剪切条件、减小机床震动和避免碰撞来提高加工质量。
总的来说,Mastercam的精加工功能提供了一种高效、准确的方法来实现零件加工。
它可以帮助用户提高生产效率、降低成本,并在制造过程中取得更好的质量控制。
无论是简单的平面零件还是复杂的曲面零件,Mastercam都能满足用户的加工需求,是现代制造业不可或缺的工具。
Mastercam加工方法总结

需要选择螺旋进刀的方式进行铣削 注意选择合适的字体 注意选择合适的字体 如果余量较小,可不必有进行粗加工 如果余量较小,可不必有进行粗加工 1、可以选定角度范围进行加工 2、如果余量较小,可不必有进行粗加工
对选定范围进行曲面加工 利用Z方向的间距对加工精度进行控制 利用角度范围对加工区域进行控制 合理设置角度增量
注意事项
单向铣削有利于提高加工质量,双向铣削有利于提高工作效率
设置好合理的切削深度
1、加工内、外轮廓时要将串连方向和补偿方向结合起来考虑 2、加工内轮廓时要设置进/退刀向量 3、加工内、外轮廓要用控制器补偿
1、使用岛屿深度挖槽时,要打开岛屿上方的预留量,这样岛屿 上方铣削整个区域,岛屿下方则可以绕开岛屿。 2、加工内、外轮廓时要将串连方向和补偿方向结合起来考虑。 3、要设置进/退刀向量
扫描面 (2.5D)
钻孔
全圆铣削 挖槽 外形铣削加工 等高(粗)+挖槽(精) 挖槽(粗)+挖槽(精)
等高/挖槽(粗)+浅平面
可以利用循环指令进行孔的 加工 对圆孔进行铣削加工 可以刻阳文和阴文 沿字体轮廓线的加工 对选定范围进行平面加工 对选定范围进行平面加工
加工平缓曲面
等高/挖槽(粗)+环绕等距 加工平缓曲面
类型
表面 平面
轮廓
加工方法 面铣 挖槽
外形铣削加工
Mastercam加工方法总结
加工特点 可以选择一个或多个封闭区 域进行加工 可以对某个封闭区域进行平 面加工
可以进行内、外轮廓的加工
2D加工
沟槽
挖槽
可以对个封闭区域进行挖槽 加工并允许挖槽区域存在岛 屿
孔 圆孔 刻字
MasterCAM外形铣削主要参数的设置方法

MasterCAM外形铣削主要参数的设置方法前言MasterCAM是一款常用的CAM软件,具有强大的功能及灵活的操作性,被广泛应用于机械制造行业。
在进行外形铣削时,合理设置参数是非常重要的,这样可以提高加工效率,保证加工质量。
本文将介绍MasterCAM外形铣削的主要参数设置方法及其影响。
外形铣削的基本概念外形铣削是制造业中常见的一种加工方式。
其基本原理是通过旋转的铣刀在工件表面上进行铣削,移除必要的材料来得到所需的形状。
在MasterCAM中,外形铣削是通过面铣削操作完成的。
在进行外形铣削时,需要考虑铣削方向、铣削深度、刀具直径以及进给速度等参数的设置,以确保加工效果。
外形铣削参数的设置方法铣削方向铣削方向是外形铣削的一个重要参数。
在MasterCAM中,铣削方向分为水平铣削、垂直铣削和多轴旋转三种方式。
选择不同的铣削方向对加工效果有很大的影响。
•水平铣削:水平铣削适用于平整的工件表面,切削刃与工件平面垂直。
这种方式可以使刀具的切入力最小,因此切削效果好,同时也可以提高加工精度和表面平整度。
•垂直铣削:垂直铣削适用于工件边缘或轮廓,铣刀切削方向垂直于工件表面。
这种方式可以保证切削力的均匀分布,同时也有利于加工较深的凸起形状。
•多轴旋转:在MasterCAM中,可以使用多轴旋转的方式进行铣削。
该方式可以实现任意角度的铣削,适用于加工形状较为复杂的工件。
铣削深度铣削深度表示铣刀在一次铣削过程中所能切削的最大深度。
通常情况下,铣削深度应该尽可能大,以提高加工效率。
但是,在考虑铣削深度时也需要考虑切削力和表面质量的影响。
如果铣削深度过大,可能会导致刀具过度磨损、加工精度下降和表面效果下降等问题。
刀具直径刀具直径是外形铣削的一个重要参数,通常情况下,刀具直径越大,铣削效率越高,加工精度越高。
但是,在选择刀具直径时也需要考虑工件的几何形状以及加工深度和切削质量等因素。
进给速度进给速度是铣削过程中切削刃移动的速度,是外形铣削的另一重要参数。
mastercam精加工的用法

mastercam精加工的用法摘要:一、Mastercam 简介二、Mastercam 精加工概述三、Mastercam 精加工的步骤1.准备工作2.精加工轮廓3.精加工策略选择4.刀具路径规划5.刀具补偿与加工仿真四、Mastercam 精加工应用实例五、总结与展望正文:Mastercam 是一款广泛应用于数控加工领域的CAM 软件,它提供了强大的加工功能,可以帮助用户轻松实现各种零件的加工。
其中,Mastercam 精加工是实现高精度加工的重要手段。
Mastercam 精加工主要通过对零件的精确尺寸、形状和表面质量的追求,实现对复杂零件的高精度加工。
它包括一系列精加工策略,如等高精加工、等距精加工、螺旋精加工等,这些策略可以根据加工零件的特点和需求进行选择。
在Mastercam 中进行精加工的具体步骤如下:1.准备工作:首先,用户需要创建或导入零件模型,并设置加工的刀具、机床和加工参数等相关信息。
2.精加工轮廓:在Mastercam 中,用户可以通过绘制、编辑或导入轮廓的方式,定义精加工的轮廓。
这一步骤对于实现高精度加工至关重要。
3.精加工策略选择:根据加工零件的特点和需求,用户需要选择合适的精加工策略。
例如,对于需要保证加工表面质量的零件,可以选择等高精加工;对于需要提高加工效率的零件,可以选择等距精加工。
4.刀具路径规划:在Mastercam 中,用户可以根据加工策略和轮廓信息,规划刀具的路径。
这一步骤直接影响到加工过程的顺利进行和加工质量。
5.刀具补偿与加工仿真:为了保证加工过程中刀具的稳定性和安全性,Mastercam 提供了刀具补偿功能。
此外,用户还可以通过加工仿真功能,预览加工过程,以检查刀具路径的正确性和安全性。
在实际应用中,Mastercam 精加工被广泛应用于各种高精度零件的加工,如手机壳、模具等。
通过合理地运用Mastercam 精加工功能,用户可以大大提高加工效率,降低加工成本,提高零件的加工质量。
MasterCAM

ExperienceIM· 49 ·在进行MasterCAM 模拟加工时,需对各参数进行设置,正确设置刀具参数、加工参数除了要具备数控编程知识外,还需具备一定的数控加工工艺知识,结合实际加工经验进行各参数的设置,编出合理的数控加工程序。
下面以MasterCAM 外形铣削加工刀具参数、加工参数的设置方法为例论述。
一、外形铣削刀具参数设置方法1.刀具的选择在数控加工中,刀具的选择直接关系到加工精度的高低、加工表面质量的优劣和加工效率的高低。
选用合适的刀具并使用合理的切削参数,将可以使数控加工以最低的加工成本、最短的加工时间达到最佳的加工质量。
铣削平面、曲面的刀具主要有平刀(平底刀、端铣刀)、圆鼻刀(牛鼻刀、圆角刀)和球刀(球头刀、R 刀)等刀具。
(1)平刀(平底刀、端铣刀):在粗加工和精加工时都可使用。
平刀主要用于粗加工、平面精加工、外形精加工和清角加工。
使用平刀加工要注意刀尖很容易磨损,可能会影响加工精度。
(2)圆鼻刀(牛鼻刀、圆角刀):主要用于模坯粗加工、平面精加工和侧面精加工,适合于加工硬度较高的材料。
常用圆鼻刀圆角半径为0.2mm ~6mm。
在加工时应该优先选用圆鼻刀。
(3)球刀(球头刀、R 刀):主要用于曲面的粗、精加工,由于球头刀的端部切削速度为零。
因此,为了保证加工速度,一般采用的切削行距都很密。
2.刀具参数设置在MasterCAM 中,刀具参数主要有刀具号码、刀具直径、刀角半径、主轴转速、下刀速率和提刀速率等参数(图1)。
刀具参数的设置应根据机床、夹具、刀具和工件的刚度以及机床功率来确定。
(1)刀具号码:用来指示要换上加工中心刀库中的第几号刀,NC 程序中M06换刀指令指示的刀具号与此号码相对应。
对于数控铣床来说,此号码无意义。
(2)刀具直径:粗加工时,应根据工件结构和特点选择直径较大的刀具,以提高加工效率。
而精加工时则应根据轮廓的最小圆角,选择小于圆角的刀具,以提高加工表面的精度和质量。
mastercam精加工的用法

mastercam精加工的用法Mastercam是一款广泛应用于机械加工领域的计算机辅助设计与计算机辅助制造(CAD/CAM)软件。
它提供了丰富的功能和工具,可以用于各种精加工任务。
本文将详细介绍Mastercam在精加工中的用法。
首先,Mastercam可以用于多轴加工。
它支持多种坐标系,包括三轴、四轴、五轴甚至六轴。
这意味着Mastercam可以同时控制多个运动轴,实现复杂的立体加工。
对于复杂的零件,多轴加工可以大大提高加工效率和精度。
其次,Mastercam提供了强大的刀具路径生成功能。
在进行精加工时,刀具路径的选择非常重要,它直接影响到加工的质量和效率。
Mastercam可以根据用户设定的工艺参数和材料特性,自动生成最佳的刀具路径。
刀具路径可以根据不同的加工需求进行优化,例如最小化切削时间、最大限度减小切屑堆积等。
此外,Mastercam还提供了切削力仿真功能,可以模拟刀具切削时的受力情况,帮助用户评估加工过程中的切削负载,进一步优化刀具路径。
Mastercam还具备自动化编程能力,可以提高编程效率和准确度。
通过Mastercam的智能化编程功能,用户只需要输入简单的几何形状和加工参数,软件就可以自动生成完整的加工程序。
这样,即使没有编程经验的用户也能快速、准确地生成加工代码。
此外,Mastercam还支持与其他CAD软件的无缝集成,可以直接导入CAD模型进行加工,大大节省了时间和人力资源。
除了上述功能,Mastercam还提供了许多其他的辅助工具,用于解决各种精加工中的难题。
例如,Mastercam可以用于刀具半径校正,保证加工结果的精度。
它还提供了高级的切割功能,可以实现复杂的形状加工。
此外,Mastercam还支持实时仿真和碰撞检测,可以在加工之前检查加工过程中是否存在碰撞问题,避免设备受损。
总之,Mastercam是一款功能强大、易于使用的精加工软件。
它提供了多轴加工、刀具路径生成、自动化编程等众多功能,可以帮助用户实现高质量、高效率的精加工。
mastercam啄钻参数

Mastercam 啄钻参数简介Mastercam 是一款广泛应用于机械加工领域的计算机辅助设计与计算机辅助制造(CAD/CAM)软件。
它提供了丰富的功能和工具,可以帮助用户完成从设计到加工的全过程。
在 Mastercam 中,啄钻是一种常见的钻孔加工方式,它可以快速、高效地完成对工件的钻孔操作。
本文将详细介绍 Mastercam 中的啄钻参数设置,包括啄钻类型、切削参数、进给速率、刀具选择等内容。
通过合理设置这些参数,可以提高钻孔加工的质量和效率。
啄钻类型Mastercam 提供了多种啄钻类型,用户可以根据具体的加工要求选择适合的类型。
1.点动啄钻:点动啄钻是最简单的钻孔方式,刀具在钻孔点上下作简单的进退运动。
这种方式适用于钻孔深度较浅且孔径较小的情况。
2.螺旋啄钻:螺旋啄钻是一种将刀具沿着螺旋路径下钻的方式。
它可以提高切削效率,减少切削力,适用于钻孔深度较大的情况。
3.斜喂啄钻:斜喂啄钻是一种将刀具在钻孔过程中斜向进给的方式。
它可以减少切削力,提高切削效率,适用于钻孔深度较大且孔径较小的情况。
4.自定义啄钻:Mastercam 还提供了自定义啄钻的功能,用户可以根据具体需求自定义刀具路径和进给方式。
切削参数在进行啄钻加工时,合理设置切削参数对于加工质量和效率都非常重要。
1.切削速度:切削速度是指刀具每分钟旋转的圈数。
切削速度的选择要根据被加工材料的硬度和刀具的材质来确定。
通常情况下,硬度较高的材料需要较低的切削速度。
2.进给速率:进给速率是指刀具每分钟在工件上移动的距离。
进给速率的选择要考虑到切削速度、材料硬度和刀具的刃数等因素。
合理的进给速率可以保证加工效率和加工质量的平衡。
3.切削深度:切削深度是指每次刀具下钻的距离。
切削深度的选择要根据被加工材料的硬度、刀具的强度和工件的要求来确定。
较大的切削深度可以提高加工效率,但也会增加切削力和刀具的磨损。
4.切削冷却:在钻孔加工过程中,切削冷却非常重要。
mastercam精加工的用法
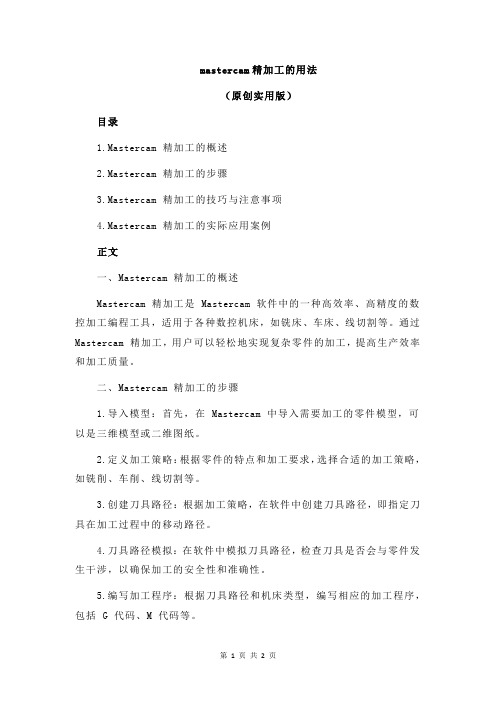
mastercam精加工的用法(原创实用版)目录1.Mastercam 精加工的概述2.Mastercam 精加工的步骤3.Mastercam 精加工的技巧与注意事项4.Mastercam 精加工的实际应用案例正文一、Mastercam 精加工的概述Mastercam 精加工是 Mastercam 软件中的一种高效率、高精度的数控加工编程工具,适用于各种数控机床,如铣床、车床、线切割等。
通过Mastercam 精加工,用户可以轻松地实现复杂零件的加工,提高生产效率和加工质量。
二、Mastercam 精加工的步骤1.导入模型:首先,在 Mastercam 中导入需要加工的零件模型,可以是三维模型或二维图纸。
2.定义加工策略:根据零件的特点和加工要求,选择合适的加工策略,如铣削、车削、线切割等。
3.创建刀具路径:根据加工策略,在软件中创建刀具路径,即指定刀具在加工过程中的移动路径。
4.刀具路径模拟:在软件中模拟刀具路径,检查刀具是否会与零件发生干涉,以确保加工的安全性和准确性。
5.编写加工程序:根据刀具路径和机床类型,编写相应的加工程序,包括 G 代码、M 代码等。
6.传输加工程序:将编写好的加工程序传输到数控机床,进行实际加工。
三、Mastercam 精加工的技巧与注意事项1.选择合适的刀具:根据加工材料和加工工艺要求,选择合适的刀具类型、尺寸和材料。
2.合理设置加工参数:根据加工工艺和机床性能,合理设置加工速度、进给速度、刀具补偿等参数,以保证加工效率和加工质量。
3.刀具路径模拟:在编写加工程序前,一定要进行刀具路径模拟,以避免刀具与零件发生干涉,导致加工失败或损坏设备。
4.加工过程中的监控:在实际加工过程中,要密切关注加工过程,如有异常情况,应立即停止加工,检查原因并采取相应措施。
四、Mastercam 精加工的实际应用案例假设有一个复杂的三维零件,需要进行铣削加工。
首先,在 Mastercam 中导入该零件的三维模型,然后选择铣削加工策略,创建刀具路径。
基于MasterCAM软件的选刀及高度方向精度控制研究

删
P i n g 币 n g
u & h o u V o c a t i o n a l T e c h n o l o g y C o l l e g e E l e c t r o n i c s& I n J b r ma t i o n , K a i l i , G u i z h o u 5 5 6 0 0 0 , C h i n a )
Ba s e d o n Ma s t e r CAM s o f t wa r e t o o l s e l e c t i o n a n d p r e c i s i o n c o n t r o l 0 f t h e
h e i g h t d i r e c t i o n
Ab s t r a c t :T h e s t u d y s t u d y b a s e d o n t h e Ma s t e r CAM s o f t w a r e t o o l s e l e c t i o n a n d p r e c i s i o n c o n t r o l o f t h e h e i g h t d i — r e c t i o n .T o o l s e l e c t i o n a n d p r e c i s i o n c o n t r o l i n h e i g h t d i r e c t i o n ma d e Ma s t e r C AM s o f t wa r e a s t h e p r i ma r y me a n s o f r e — s e a r c h ,a n a l y s e d a n d o v e r v i e w Ma s t e r CAM s o f t wa r e ,e x p l o r e d p r e c i s i o n c o n t r o l f o r t o o l s e l e c t i o n a n d p r e c i s i o n c o n t r o l o f h i g h d i r e c t i o n .a n a l y z e d t h e i mp o  ̄ a n c e o f t h e a c c u r a c y c o n t r o l b e t we e n t h a t t w o .I n t h i s p a p e  ̄ Ma s t e r CAM s o f t w a r e p r o —
Master CAM

第1章Mastercam基本操作31出最佳的加工边界曲线。
(6)构建刀具路径限制边界。
对于规划的加工区域,需要使用边界来限制加工范围的,先构建出边界曲线。
4.加工参数设置参数设置可视为对工艺分析和规划的具体实施,它构成了利用CAD/CAM软件进行NC编程的主要操作内容,直接影响NC程序的生成质量。
参数设置的内容较多,其中:Mastercam数控加工实例教程32(1)切削方式设置用于指定刀轨的类型及相关参数。
2)加工对象设置是指用户通过交互手段选择被加工的几何体或其中的加工分区、毛坯、避让区域等。
(3)刀具及机械参数设置是针对每个加工工序选择适合的加工刀具并在CAD/CAM软件中设置相应的机械参数,包括主轴转速、切削进给、切削液控制等。
()加工程序参数设置包括对进退刀位置及方式、切削用量、行间距、加工余量、安全高度等。
这是C A M软件参数设置中最主要的一部分内容。
5.生成刀具路径在完成参数设置后,即可将设置结果提交给CAD/CAM系统进行刀轨的计算。
这一过第1章Mastercam基本操作33程是由CAD/CAM软件自动完成的。
6.刀具路径检验为确保程序的安全性,必须对生成的刀轨进行检查校验,检查有无明显刀具路径、有无过切或者加工不到位,同时检查是否会发生与工件及夹具的干涉。
校验的方式有:(1)直接查看。
通过对视角的转换、旋转、放大、平移直接查看生成的刀具路径,适于观察其切削范围有无越界及有无明显异常的刀具轨迹。
(2)手工检查。
对刀具轨迹进行逐步观察。
(3)实体模拟切削,进行仿真加工。
直接在计算机屏幕上观察加工效果,这个加工过程与实际机床加工十分类似。
对检查中发现问题的程序,应调整参数设置重新进行计算,再作检验。
7.后处理后处理实际上是一个文本编辑处理过程,其作用是将计算出的刀轨(刀位运动轨迹)以规定的标准格式转化为NC代码并输出保存。
在后处理生成数控程序之后,还需要检查这个程序文件,特别对程序头及程序尾部分的语句进行检查,如有必要可以修改。
Mastercam编程参数设置的含义和应用
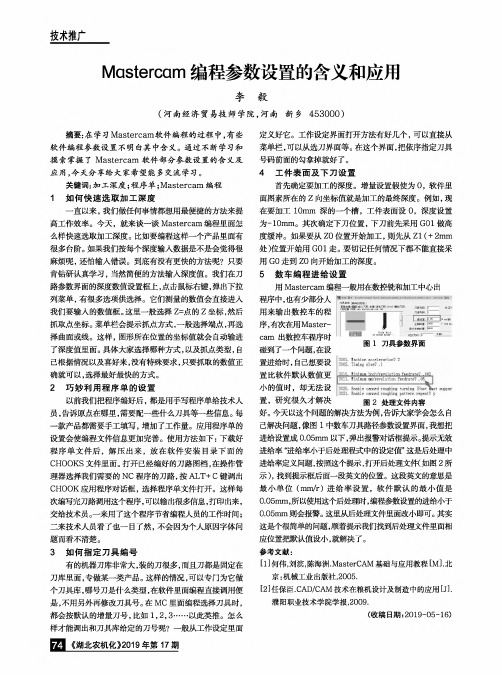
技术推广Mastercam编程参数设置的含义和应用李毅(河南经济贸易技师学院,河南新乡453000)摘要:在学习Mastercam软件编程的过程中,有些软件编程参数设置不明白其中含义。
通过不断学习和摸索掌握了Mastercam软件部分参数设置的含义及应用,今天分享给大家希望能多交流学习。
关键词:加工深度;程序单;Mastercam编程1如何快速选取加工深度一直以来,我们做任何事情都想用最便捷的方法来提高工作效率。
今天,就来谈一谈Mastercam编程里面怎么样快速选取加工深度。
比如要编程这样一个产品里面有很多台阶。
如果我们按每个深度输入数据是不是会觉得很麻烦呢,还怕输入错误。
到底有没有更快的方法呢?只要肯钻研认真学习,当然简便的方法输入深度值。
我们在刀路参数界面的深度数值设置框上,点击鼠标右键,弹出下拉列菜单,有很多选项供选择。
它们测量的数值会直接进入我们要输入的数值框。
这里一般选择Z=点的Z坐标,然后抓取点坐标。
菜讎会际抓点方式,一般选择端点,再选择曲面或线。
这样,图形所在位置的坐标值就会自动输进了深度值里面。
具体大家选择哪种方式,以及抓点类型,自己根据情况以及喜好来,没有特殊要求,只要抓取的数应确就可以,选择最好最快的方式。
2巧妙利用程序单的设置以前我们把程序编好后,都是用手写程序单给技术人员,告诉原点在哪里,需要配一些什么刀具等一些信息。
每一款产品都需要手工填写,增加了工作量。
应用程序单的设置会使编程文件信息更加完善。
使用方法如下:下载好程序单文件后,解压出来,放在软件安装目录下面的CHOOKS文件里面。
打开已经编好的刀路图档,在操作管理器选择我们需要的NC程序的刀路,按ALT+C键调出CHOOK应用程序对话框,选择程序单文件打开。
这样每次编写完刀路调用这个程序,可以输出很多信息,打印出来,交给技术员。
一来用了这个程序节省编程人员的工作时间;二来技术人员看了也一目了然,不会因为个人原因字体问题而看不清楚。
MasterCAM参数设置里各种深度的含义
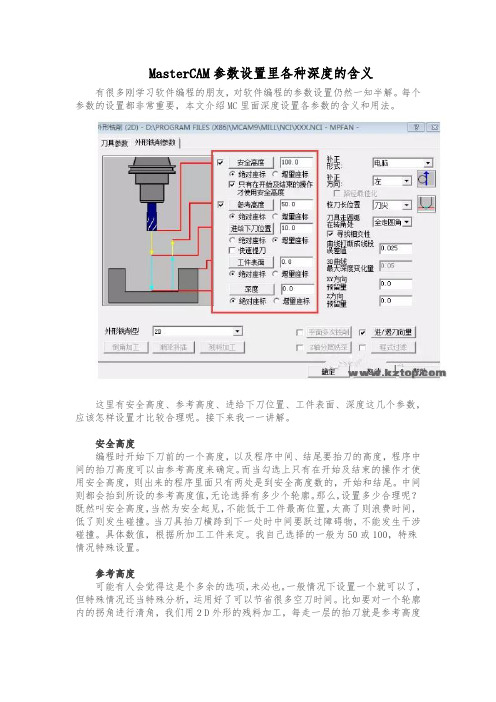
MasterCAM参数设置里各种深度的含义有很多刚学习软件编程的朋友,对软件编程的参数设置仍然一知半解。
每个参数的设置都非常重要,本文介绍MC里面深度设置各参数的含义和用法。
这里有安全高度、参考高度、进给下刀位置、工件表面、深度这几个参数,应该怎样设置才比较合理呢。
接下来我一一讲解。
安全高度编程时开始下刀前的一个高度,以及程序中间、结尾要抬刀的高度,程序中间的抬刀高度可以由参考高度来确定。
而当勾选上只有在开始及结束的操作才使用安全高度,则出来的程序里面只有两处是到安全高度数的,开始和结尾。
中间则都会抬到所设的参考高度值,无论选择有多少个轮廓。
那么,设置多少合理呢?既然叫安全高度,当然为安全起见,不能低于工件最高位置,太高了则浪费时间,低了则发生碰撞。
当刀具抬刀横跨到下一处时中间要跃过障碍物,不能发生干涉碰撞。
具体数值,根据所加工工件来定。
我自己选择的一般为50或100,特殊情况特殊设置。
参考高度可能有人会觉得这是个多余的选项,未必也。
一般情况下设置一个就可以了,但特殊情况还当特殊分析,运用好了可以节省很多空刀时间。
比如要对一个轮廓内的拐角进行清角,我们用2D外形的残料加工,每走一层的抬刀就是参考高度值,如果不设参考就要抬到安全高度了。
还有在钻孔设置的参考值为R平面值。
这里我使用的清角程序,同时设置了安全高度和参考高度,矮的黄色线抬刀为参考高度,高的黄色线抬刀为安全高度。
进给下刀位置在下刀前我们都会给一个小小的走G01的高度缓冲。
比如说我要从Z0位置开始加工,会从Z1位置开始用G01走。
当然你也可以直接以G0的速度走到Z向下刀深度,具体操作方法是:将进给下刀位置设增量0,任何情况下都直接G0走到Z向开始加工深度。
特殊情况特殊对待,一般情况下会设置,我给的数值在1-3这个范围。
图中的Z2就是设置的进给下刀位置。
工件表面开始加工的深度深度最终要加工的深度,就是我们铣下去的深度。
如果我们选择增量设置0的话,加工到的最终深度会是软件里面图素所在的Z向坐标值。
数控加工中Mastercam编程过程和加工特点

第18卷第2期2006年6月武汉工程职业技术学院学报Journal of Wuhan Eng ineer ing InstiuteV ol.18N o.2June.2006数控加工中M astercam编程过程和加工特点郑何敏(杭州职业技术学院 浙江杭州:310000)摘 要 M astercam具有强大的计算机辅助设计及制造(CAD/CAM)功能,是目前广泛使用的计算机辅助设计及制造软件。
主要介绍了Mastercam软件在数控加工中的编程过程、加工方式及特点。
关键词 数控加工 CAD CAM中图分类号:T P391.7 文献标识码:A 文章编号:1671 3524(2006)02 0017 03CAD(计算机辅助设计)和CAM(计算机辅助制造)已经显示出了其巨大潜力,在机械制造工业方面已经占据了主导地位。
使用CAD/CAM系统产生的CNC程序代码可以替代传统的手工程序制作。
Mastercam具有强大的计算机辅助设计和计算机辅助制造功能,集工件的二维几何图形设计、三维曲面设计、刀具路径模拟、加工实体模拟等功能于一身,并提供友好的人机交互,是目前广泛使用的计算机辅助设计和计算机辅助制造软件。
1 数控加工中的Mastercam编程过程1.1 模型建立随着现代数控编程软件技术的飞速发展,零件的模型能否正确建立已经成为CAM能否顺利进行的关键。
M astercam作为专业的CAM软件,它强大的功能就在于拥有丰富的数据交换接口,对于各种类型的前端造型(包括ASCII、DXF、IGES、STL、VDA、SAT、DWG、NFL等),均可通过Conv eners 命令将其转换为M astercam格式,用作CAM中的零件模型。
此外,Mastercam自己也具有独立的几何造型模块,可以独立完成二维、三维的各种实体、曲面(包括复杂的举升实体、扫描实体、举升曲面、昆式曲面等)的造型,还可以完成实体取壳、曲面熔接的操作。
mastercam 切削参数
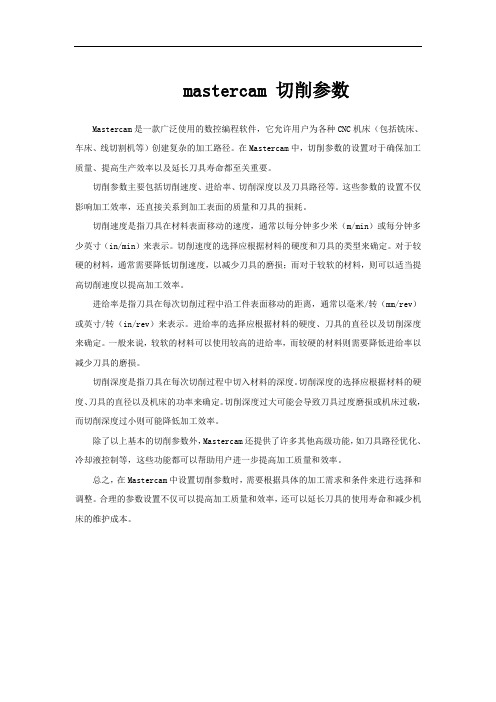
mastercam 切削参数Mastercam是一款广泛使用的数控编程软件,它允许用户为各种CNC机床(包括铣床、车床、线切割机等)创建复杂的加工路径。
在Mastercam中,切削参数的设置对于确保加工质量、提高生产效率以及延长刀具寿命都至关重要。
切削参数主要包括切削速度、进给率、切削深度以及刀具路径等。
这些参数的设置不仅影响加工效率,还直接关系到加工表面的质量和刀具的损耗。
切削速度是指刀具在材料表面移动的速度,通常以每分钟多少米(m/min)或每分钟多少英寸(in/min)来表示。
切削速度的选择应根据材料的硬度和刀具的类型来确定。
对于较硬的材料,通常需要降低切削速度,以减少刀具的磨损;而对于较软的材料,则可以适当提高切削速度以提高加工效率。
进给率是指刀具在每次切削过程中沿工件表面移动的距离,通常以毫米/转(mm/rev)或英寸/转(in/rev)来表示。
进给率的选择应根据材料的硬度、刀具的直径以及切削深度来确定。
一般来说,较软的材料可以使用较高的进给率,而较硬的材料则需要降低进给率以减少刀具的磨损。
切削深度是指刀具在每次切削过程中切入材料的深度。
切削深度的选择应根据材料的硬度、刀具的直径以及机床的功率来确定。
切削深度过大可能会导致刀具过度磨损或机床过载,而切削深度过小则可能降低加工效率。
除了以上基本的切削参数外,Mastercam还提供了许多其他高级功能,如刀具路径优化、冷却液控制等,这些功能都可以帮助用户进一步提高加工质量和效率。
总之,在Mastercam中设置切削参数时,需要根据具体的加工需求和条件来进行选择和调整。
合理的参数设置不仅可以提高加工质量和效率,还可以延长刀具的使用寿命和减少机床的维护成本。
mastercam后处理入门与应用实例精析

一、Mastercam后处理的基本概念Mastercam是一款广泛应用于制造行业的CAD/CAM软件,它具备强大的后处理功能,可以将CAM系统生成的刀具轨迹数据转换为特定数控机床可以识别和执行的G代码。
Mastercam后处理的作用是非常重要的,它直接影响着数控机床加工过程的精度和效率。
二、Mastercam后处理的原理Mastercam后处理的原理是将CAM系统生成的刀具轨迹数据转换为数控机床可以识别和执行的G代码。
该过程涉及到对加工参数、刀具信息、切削参数等进行处理和优化,同时还需要考虑不同数控机床的特性和加工方式,确保生成的G代码能够精准地控制数控机床进行加工。
三、Mastercam后处理的基本流程1. 导入CAM系统生成的刀具轨迹数据;2. 设置加工参数、刀具信息、切削参数等;3. 选择数控机床类型和加工方式;4. 进行后处理优化和修正;5. 生成数控机床可以识别和执行的G代码。
四、Mastercam后处理的应用实例以CNC铣床加工为例,介绍Mastercam后处理的具体应用实例:1. 导入CAM系统生成的刀具轨迹数据,包括刀具路径、进给速度、切削深度等;2. 设置加工参数,如切削速度、进给速度、切削深度等;3. 针对不同的零件形状和加工要求,选择合适的刀具信息和切削参数;4. 根据数控铣床的特性和加工方式,进行后处理优化和修正;5. 生成数控铣床可以识别和执行的G代码,并进行仿真验证。
五、Mastercam后处理的优势与局限1. 优势: Mastercam后处理可以根据不同数控机床的特性和加工方式进行优化,确保生成的G代码能够精准地控制数控机床进行加工。
2. 局限: Mastercam后处理也存在一些局限,如在处理复杂曲面加工时需要额外的修正和优化,以确保刀具轨迹的精度和平滑性。
六、Mastercam后处理的发展趋势随着制造业的发展和数控技术的不断进步,Mastercam后处理也在不断发展和完善。
mastercam精加工的用法

Mastercam精加工的用法1. 简介Mastercam是一款用于计算机辅助制造(CAM)的软件,它主要用于工业制造中的数控加工。
Mastercam精加工是其中的一个功能模块,它提供了一系列工具和功能,帮助用户进行高精度的加工操作。
2. Mastercam精加工的特点Mastercam精加工具有以下几个特点: - 高精度:Mastercam精加工提供了各种高精度的加工工具和算法,可以实现微米级的加工精度。
- 多轴加工:Mastercam精加工支持多轴加工,可以在多个坐标轴上进行同时加工,提高生产效率。
- 多种加工策略:Mastercam精加工提供了多种加工策略,包括等高线加工、平面加工、曲面加工等,可以根据不同的加工需求选择合适的策略。
- 自动化操作:Mastercam精加工具有自动化操作的功能,可以根据用户设定的参数自动进行加工操作,减少人工干预。
- 可视化界面:Mastercam精加工提供了直观的可视化界面,用户可以通过图形界面进行操作,方便快捷。
3. Mastercam精加工的使用步骤使用Mastercam精加工进行加工操作的步骤如下: 1. 导入CAD模型:首先,需要将需要加工的CAD模型导入Mastercam软件中。
可以使用Mastercam提供的导入功能,支持多种CAD文件格式。
2. 创建加工路径:根据加工需求,使用Mastercam的工具和功能创建加工路径。
可以选择合适的加工策略,设置加工参数,生成加工路径。
3. 优化加工路径:对生成的加工路径进行优化,可以通过调整刀具路径、减少切削次数等方式,提高加工效率和质量。
4. 模拟验证:使用Mastercam提供的模拟功能,对加工路径进行验证。
可以通过模拟操作来检查加工路径是否正确,避免出现错误。
5. 导出G代码:完成加工路径的设置和验证后,可以导出G代码,用于数控机床进行实际加工操作。
4. Mastercam精加工的应用领域Mastercam精加工广泛应用于工业制造领域,特别是需要高精度加工的行业,例如航空航天、汽车制造、模具制造等。
关于加工深度的精确控制- MasterCAM

加工面余量5,最大下切步距10,顶部切削调整量0.2,其它切削(底部和临界深度处)调整量0.2,等高刀路第一刀深度Z4.8最后一刀深度-54.8实际进刀量9.933切削深度用相对深度,MC系统计算加工深度时自动包含加工面余量,自动侦测所选择加工面的最高点和最低点。
第一刀的计算:最高点-顶部调整+加工余量(0-0.2+5=4.8);最后一刀的计算:最低点+底部调整量+加工余量(-60+0.2+5=-54.8)实际进刀量:总切削量:切削的最高点-最低点,(非曲面最高点,最低点)切削次数:总切削量除最大进刀量往上取整,实际进刀量=总切削量/切削次数"总切削量:4.8-(-54.8)=59.6;切削次数:59.6/10=5.96,向上取整为6实际进刀量:59.6/6=9.9333333ADJUSTMENT TO TOP CUT:顶面切削调整量又有种译法叫第一刀的相对位置。
设置第一刀与工件顶面的距离。
当数值为正时,向下调整。
当数值为负时,向上调整。
ADJUSTMENT TO OTHER CUTS:其它(底面和各临界面)切削调整量又译作其它切削预留量,设置最后一刀和工件底部的距离,各临界刀路和各临界深度的距离。
正值向上调整,负值向下调整。
第一刀的切削位置由工件的顶面,顶面切削调整量,加工面余量3个参数决定最后一刀的切削位置由工件的底面,其它(底面和各临界深度)切削调整量,加工面余量3个参数决定。
各临界深度的切削位置由各临界深度,其它(底面和各临界深度)切削调整量,加工面余量3个参数决定。
第一刀的切削位置的特例。
当ADJUSTMENT TO TOP CUT为负时,如-1。
顶面为0,加工面余量为0.5。
由于加工面余量为0.5,在Z1.5处,刀路怎么走都不会过切,或者说系统无法在该深度确定刀路,故实际第一刀不会在Z1.5处。
只是系统计算总切削量的最高点在Z1.5,1.5减去一个下切步距(Z向进刀量)若〈0.5,则该处为第一刀处。
mastercam轨迹自动同步功能介绍

mastercam轨迹自动同步功能介绍Mastercam是一种先进的机器编程软件,它可以帮助制造商在CNC机床上自动化地创建和编辑轨迹。
它的轨迹自动同步功能可以帮助用户更轻松地进行编程和操作,提高生产效率和精度。
轨迹自动同步是Mastercam中的一项重要功能,它可以根据用户的需求自动调整和优化轨迹。
这个功能可以帮助用户减少编程和操作的时间,提高生产效率。
在传统的编程中,用户需要手动调整和修改每个轨迹的参数和属性,这样很容易出错并且耗时耗力。
而有了轨迹自动同步功能,用户只需要设置一次,系统就会自动根据用户的需求进行调整和优化,大大简化了编程的过程。
轨迹自动同步功能可以根据用户的需求自动调整轨迹的速度、加工深度和切削方向等参数。
用户只需要输入所需的参数,系统就会根据这些参数自动调整轨迹,以确保最佳的加工效果和质量。
此外,轨迹自动同步功能还可以根据用户的机床和刀具参数进行优化,以确保加工的准确性和稳定性。
除了自动调整轨迹参数,轨迹自动同步功能还可以自动同步轨迹之间的关系。
在传统的编程中,用户需要手动调整和修改每个轨迹之间的关系,以确保它们按照正确的顺序执行。
而有了轨迹自动同步功能,用户只需要设置好每个轨迹的顺序,系统就会自动根据这些顺序进行同步,确保它们按照正确的顺序执行。
这样可以避免轨迹之间的冲突和错误,提高加工的效率和质量。
轨迹自动同步功能还可以帮助用户更好地控制CNC机床的运动。
在传统的编程中,用户需要手动调整和修改每个轨迹的运动方式和路径,以确保它们按照预期的方式运动。
而有了轨迹自动同步功能,用户只需要设置好每个轨迹的运动方式和路径,系统就会自动根据这些设置进行同步,确保机床按照预期的方式运动。
这样可以避免机床的误差和偏差,提高加工的精度和稳定性。
Mastercam的轨迹自动同步功能可以帮助制造商更轻松地进行编程和操作,提高生产效率和精度。
它的自动调整和优化功能可以减少编程和操作的时间,提高生产效率。
- 1、下载文档前请自行甄别文档内容的完整性,平台不提供额外的编辑、内容补充、找答案等附加服务。
- 2、"仅部分预览"的文档,不可在线预览部分如存在完整性等问题,可反馈申请退款(可完整预览的文档不适用该条件!)。
- 3、如文档侵犯您的权益,请联系客服反馈,我们会尽快为您处理(人工客服工作时间:9:00-18:30)。
加工面余量5,最大下切步距10,顶部切削调整量0.2,
其它切削(底部和临界深度处)调整量0.2,
等高刀路
第一刀深度Z4.8
最后一刀深度-54.8
实际进刀量9.933
切削深度用相对深度,MC系统计算加工深度时自动包含加工面余量,自动侦测所选择加工面的最高点和最低点。
第一刀的计算:最高点-顶部调整+加工余量(0-0.2+5=4.8);
最后一刀的计算:最低点+底部调整量+加工余量(-60+0.2+5=-54.8)
实际进刀量:总切削量:切削的最高点-最低点,(非曲面最高点,最低点)
切削次数:总切削量除最大进刀量往上取整,
实际进刀量=总切削量/切削次数"
总切削量:4.8-(-54.8)=59.6;
切削次数:59.6/10=5.96,向上取整为6
实际进刀量:59.6/6=9.9333333
ADJUSTMENT TO TOP CUT:顶面切削调整量
又有种译法叫第一刀的相对位置。
设置第一刀与工件顶面的距离。
当数值为正时,向下调整。
当数值为负时,向上调整。
ADJUSTMENT TO OTHER CUTS:其它(底面和各临界面)切削调整量
又译作其它切削预留量,设置最后一刀和工件底部的距离,各临界刀路和各临界深度的距离。
正值向上调整,负值向下调整。
第一刀的切削位置由工件的顶面,顶面切削调整量,加工面余量3个参数决定
最后一刀的切削位置由工件的底面,其它(底面和各临界深度)切削调整量,加工面余量3个参数决定。
各临界深度的切削位置由各临界深度,其它(底面和各临界深度)切削调整量,加工面余量3个参数决定。
第一刀的切削位置的特例。
当ADJUSTMENT TO TOP CUT为负时,如-1。
顶面为0,加工面余量为0.5。
由于加工面余量为0.5,在Z1.5处,刀路怎么走都不会过切,或者说系统无法在该深度确定刀路,
故实际第一刀不会在Z1.5处。
只是系统计算总切削量的最高点在Z1.5,1.5减去一个下切步距(Z向进刀量)
若〈0.5,则该处为第一刀处。
若〉或= 0.5,则再继续向下偏下切步距,直至低于0.5,该处才是第一刀
的位置
所以第一刀深度一定是小于加工面余量的
NOTE:DRIVE STOCK IS INCLUDED IN。
注:加工面余量包含在里面,
在用相对深度控制加工深度时,系统是自动计算加工面余量在加工深度里的,不能
更改。
而用绝对深度控制加工深度时,该项有复选框是可以取舍的。