刀具加工深度与工件最小(内)R角参考值
刀具合理几何参数的选择
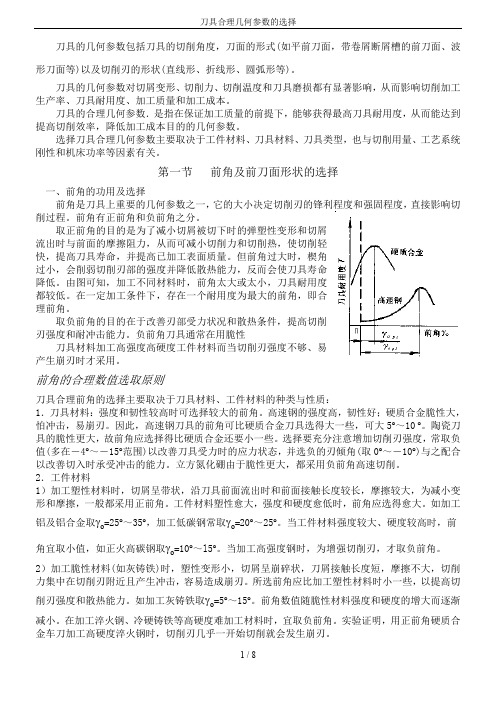
刀具的几何参数包括刀具的切削角度,刀面的形式(如平前刀面,带卷屑断屑槽的前刀面、波形刀面等)以及切削刃的形状(直线形、折线形、圆弧形等)。
刀具的几何参数对切屑变形、切削力、切削温度和刀具磨损都有显著影响,从而影响切削加工生产率、刀具耐用度、加工质量和加工成本。
刀具的合理几何参数.是指在保证加工质量的前提下,能够获得最高刀具耐用度,从而能达到提高切削效率,降低加工成本目的的几何参数。
选择刀具合理几何参数主要取决于工件材料、刀具材料、刀具类型,也与切削用量、工艺系统刚性和机床功率等因素有关。
第一节前角及前刀面形状的选择一、前角的功用及选择前角是刀具上重要的几何参数之一,它的大小决定切削刃的锋利程度和强固程度,直接影响切削过程。
前角有正前角和负前角之分。
取正前角的目的是为了减小切屑被切下时的弹塑性变形和切屑流出时与前面的摩擦阻力,从而可减小切削力和切削热,使切削轻快,提高刀具寿命,并提高已加工表面质量。
但前角过大时,楔角过小,会削弱切削刃部的强度并降低散热能力,反而会使刀具寿命降低。
由图可知,加工不同材料时,前角太大或太小,刀具耐用度都较低。
在一定加工条件下,存在一个耐用度为最大的前角,即合理前角。
取负前角的目的在于改善刃部受力状况和散热条件,提高切削刃强度和耐冲击能力。
负前角刀具通常在用脆性刀具材料加工高强度高硬度工件材料而当切削刃强度不够、易产生崩刃时才采用。
前角的合理数值选取原则刀具合理前角的选择主要取决于刀具材料、工件材料的种类与性质:1.刀具材料:强度和韧性较高时可选择较大的前角。
高速钢的强度高,韧性好;硬质合金脆性大,怕冲击,易崩刃。
因此,高速钢刀具的前角可比硬质合金刀具选得大一些,可大5°~10°。
陶瓷刀具的脆性更大,故前角应选择得比硬质合金还要小一些。
选择要充分注意增加切削刃强度,常取负值(多在-4°~-15°范围)以改善刀具受力时的应力状态,并选负的刃倾角(取0°~-10°)与之配合以改善切入时承受冲击的能力。
切削用量及刀具几何角度的选择汇总

第五十四页
二、选取切削用量的原则 1.切削深度ap的选取原则
切削深度应尽可能大,尽量减少走刀次数。
2.进给量f 的选取原则 ⑴粗加工时,在工艺系统刚度和强度允许时,尽量选较 大值;
⑵精加工、半精加工一般选较小值。
3.切削速度v 的选取原则 (1)粗加工时,应选较低的切削速度,精加工时选择较高 的切削速度; (2)加工材料强度硬度较高时,选较低的切削速度,反之取
刀尖是刀具强度和散热 条件都很差的地方。切削过
程中,刀尖切削温度较高, 非常容易磨损,因此增强刀 尖,可以提高刀具耐用度。 刀尖对已加工表面粗糙度有 很大影响。
第三十六页
5.4 过渡刃与修光刃参数的选择
一、过渡刃及其参数选择 ⑴外圆车刀过渡刃参数:
过渡刃偏角
rs
1 2
r
过渡刃长度
bs=0.5~2mm
第五十二页
3.切削用量对切削加工生产率的影响
切削机动时间:
tm(nsL f)(ahp)1d0wv0L f0ahp(min
第五十三页
机动时间:tmnsLf
hdw L h(min
ap 10v00 f ap
刀具耐用度:
t
vn
Ct fp
aqp
➢ 提高v,刀具耐用度下降,辅助时间增加,效率降低; ➢ 减小ap ,走刀次数增加,效率降低。 因此,应先取大的切削深度,然后选取合理的切削速度。
⑷影响各切削分力的比值及切削过程的平稳性。 ①车外圆时,当刃倾角由正变负时,吃刀抗力Fy增大; ②刃倾角越大,参加工作的切削刃越长,使切削平稳。
第四十八页
刃倾角的选择原则:P74
1)粗加工λS< 0(保护刀尖),精加工λS> 0(使Fy小些) 2)断续切削:λS< 0(保护刀尖) 3)工件σb、HB大:λS< 0(保护刀尖) 4)系统刚性差:λS> 0(使Fy小些) 5)微量切削:λS取大值(使刀具实际刃口半径↓)
刀具几何参数和切削用量的合理选择

加工条件:工艺系统刚性差时,易出现振
动,应选取较小的后角αo;加工表面质量要求 较高时,为减轻刀具与工件之间的摩擦,应选
取较大的后角αo;尺寸精度要求较高时,应选 取较小的后角αo,以减小刀具的径向磨损值NB 值,如下图所示。
硬质合金车刀合理后角的参考值如下表所示。
② 后角αo的选择
切削厚度hD:粗加工时,切削厚度hD较大,要 求切削刃坚固,应选取较小的后角αo。精加工时, 切削厚度hD较小,磨损主要发生在后刀面上,为降 低磨损,应选取较大的后角αo。
工件材料:工件材料强度和硬度较高时,为提
高切削刃强度,应选取较小的后角αo;工件材料软、 塑性大时,后刀面磨损严重,应选取较大的后角αo; 工件材料脆性较大时,载荷集中在切削刃处,为提
负前角双面型:该形式的刀具使刀具的重磨次数 增加,最大程度地减少了前刀面和后刀面的磨损。同 时负前角的倒棱应有足够的宽度,以确保切屑沿该棱 面流出。
(3)倒棱
倒棱是增强切削刃强度的一种措施。在用脆性大 的刀具材料粗加工或断续切削时,磨倒棱能够减小刀 具崩刃,显著提高刀具耐用度(可提高1~5倍)。
倒棱宽度br1不可太大,以便切屑能沿前刀面 流出。br1的取值与进给量f有关,常取br1≈ (0.3~0.8)f。其中,精加工时取小值,粗加工
② 前角γo的选择
工件材料:工件材料的强度、硬度较低,塑
性较好时,应选取较大的前角γo;工件材料脆性较 大时应选取较小的前角γo;工件材料强度、硬度较 高时,应选取较小的前角γo,甚至负前角。
刀具材料:刀具材料的强度和韧度高时,如高 速钢,可选取较大的前角γo;反之,刀具材料的强度 和韧度差时,如硬质合金,应选取较小的前角γo。
刀具几何参数的合理选择

15
三、前角的选择 3.前刀面的型式 3.前刀面的型式 3)正前角曲面带倒棱型:这种型式是在平面带 正前角曲面带倒棱型: 倒棱的基础上,前刀面上又磨出一个曲面, 倒棱的基础上,前刀面上又磨出一个曲面,称 为卷屑槽或月牙槽。 为卷屑槽或月牙槽。常用于粗加工或精加工塑 性材料的刀具。 性材料的刀具。
16
34
八、切削液 1.切削液的作用 1.切削液的作用 2)切削液的润滑作用 2)切削液的润滑作用 减小摩擦角并减小切屑与前刀面之间 的摩擦因数和摩擦力;增大剪切角, 的摩擦因数和摩擦力;增大剪切角,减小 切削变形从而使切削力减小, 切削变形从而使切削力减小,切削功率降 低;由于降低了切削区的温度,致使刀具 由于降低了切削区的温度, 磨损减小,刀具耐用度提高; 磨损减小,刀具耐用度提高;使积屑瘤不 易产生,提高已加工表面的质量。 易产生,提高已加工表面的质量。
22
精车 10~12 ~ 6~8 ~ 6~8 ~
四、后角的选择 3.后刀面的形式 3.后刀面的形式
23
五、主偏角的的选择 1. 主偏角的功用 主偏角κr影响切削分力的大小; 主偏角 影响切削分力的大小;影响加工表 影响切削分力的大小 面粗糙度值的大小;主偏角影响刀具耐用度; 面粗糙度值的大小;主偏角影响刀具耐用度;影 响工件表面形状。 响工件表面形状。
31
七、刃倾角的选择 1.刃倾角的功用 控制切削刃在切入和切出时的平稳性; 3)控制切削刃在切入和切出时的平稳性; 4)控制背向力Fp和进给力Fƒ的比值。 控制背向力F 和进给力F 的比值。 2.刃倾角的选择 刃倾角的合理数值与正、负号, 刃倾角的合理数值与正、负号,主要根据加 工性质选取。粗加工λ 保护刀尖), ),精 工性质选取。粗加工λS <0(保护刀尖),精 加工λs λs> 小些);断续切削: );断续切削 加工λs> 0(使FP小些);断续切削:λS <0 保护刀尖);工件σ HB大 );工件 (保护刀尖);工件σb、HB大:λS <0(保护 刀尖);系统刚性差: );系统刚性差 小些); 刀尖);系统刚性差:λS >0(使FP小些); 微量切削: 取大值(使刀具实际刃口半径↓ 微量切削:λS取大值(使刀具实际刃口半径↓) 32
刀具切削部分几何参数的选择
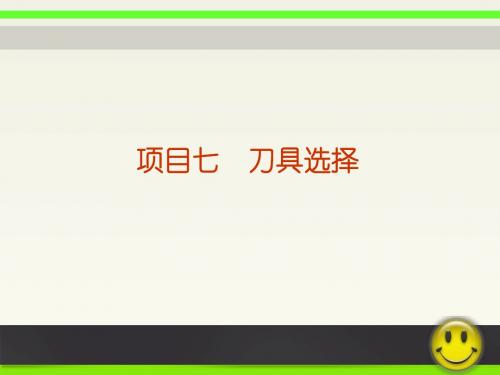
Kr ’
3.影响已加工表面质量
减小Kr进可以使工件表面残留面积高度减小, 从而使已加工表面粗糙度值减小。
4.影响断屑效果、排屑方向
增大Kr会使hD增厚,bD减小,有利于切屑折断, 有利于孔加工刀具使切屑沿轴向顺利流出。
二、合理主偏角的选择原则
粗加工时, 硬质合金车刀一般选用较大 的主偏角(Kr=60~75),以利于减少振
切削刃强度及抗冲击能力 增加,且有一定的减压和 消振作用。
适用于陶瓷等脆性材料刀具。
后角及后面形状的选择
后角的作用主要
1) 减小主后刀面与工件之间的摩擦,提高已加工表 面质量和延长刀具寿命; 2) 配合前角调整切削刃和刀头部分锋利程度、强度和 散热条件; 3) 小后角车刀在特定的条件下可抑制切削时的振动。
主偏角减小,则刀尖角r增大,
使刀尖强度提高,散热体积增大。 主偏角较小的刀具在切入时,最 先与工件接触处是远离刀尖的地 方,因而可减少因切入冲击造成 的刀尖损坏。
2.影响切削分力比值及切削层单位面积切削力
当Kr减小时,由于hD 减小,变形系数增大, 使切削层单位面积切削力 Ff 有所增大;在ap和f相同时, 使切削功率有所增加。但 Kr1 更主要的是会使背向力Fp Kr2 增大,容易引起工艺系统 振动。当工艺系统刚度不 足时,会使刀具寿命降低。
动、断屑和采用较大的切削深度。 加工硬度高的材料,如冷硬铸铁和淬硬钢 时,在系统刚性好,切削深度不大时.取
较小的主偏角(Kr=10~30),以利于提
高刀具耐用度。
工艺系统刚性较好时,取较小的主偏角可 提高刀具耐用度;刚性不足,加车削细长
轴时,应取大的主偏角,可取Kr=90~93,
以减小背向力ap,减少振动。 需要从中间切入及仿形加工的车刀,应取 较大主偏角; 车阶梯轴则需用Kr=90的偏刀;
10第十章 刀具合理几何参数的选择

Rm a x
ctgkr
f
ctgkr'
(4)主偏角和副偏角共同决定了刀尖角,直接 影响刀尖的强度、导热面积和容热体积。
(5)副偏角过小会增加副切削刃的工作长 度,增大副后刀面与已加工表面的摩擦,易引 起系统振动,反而增大表面粗糙度。
(6)切断刀、锯片刀和槽铣刀等,为了保 证刀头强度和重磨后刀头宽度变化较小,只能 取很小的副偏角(1°-2°)。
合理选择主偏角的原则: 主要看工艺系统的刚性如何。 系统刚性好,不易产生变形和振动,则主偏角
可取小值; 若系统刚性差(如切削细长轴),则宜取大值。
二、修光刃
1、位置:副切削刃处
k
' r
00
2、作用:
降低表面粗糙度
3、几何尺寸
修光刃长度:
b' (1.2 ~ 1.5) f或(4 ~ 6)f
2、合理几何参数: 保证加工质量的同时,获得最高的刀具耐用
度,从而达到提高切削效率或降低生产成本目的 的几何参数。 一般原则: (1)考虑工件材料、刀具材料及刀具类型; (2)考虑刀具各几何参数间的相互关系; (3)考虑具体加工条件; (4)考虑刀具锋利性与强度的关系。
二、前角及前刀面形状的选择
高强钢、高锰钢、淬硬钢
s 20 0 ~ 30 0
s 30 0 ~ 450
第五节 先进刀具介绍
一、750大切深强力外圆车刀 二、750银白屑外圆车刀 三、900机夹不锈钢定前角车刀 四、910机夹不重磨按钮式车
一、750大切深强力切削车刀
车刀工作图: 反映刀具角度及各
结构尺寸。
工作长度 4、影响切削分力
1、控制切屑流向
s 00 切屑沿垂直切削刃的方向流出
模具设计标准
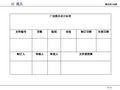
+0.00-+ 0.2 ⊥≦0.1
+1 --+3 ⊥≦1
+0.00-+0.1 ⊥≦0.08
1000以上
以上尺寸仅供参考;
参考值变 形量
调质的材料变形值为1000MM变形6-8MM 煅件的材料变形值为1000MM变形为0.3-0.5MM 热处理的材料变形值为1000为2-3MM 第6页
GC 模具
模胚
所有模芯的XY都以XY基准角单边碰数;Z对底面为O;模芯上面的小镶件,Z同 样对底为0;
五.其他小工件,如斜顶,行位,小镶件等 按照2D图纸标数为基准;特别的工件特别对待; 六.注意;为了检测模芯及模胚的垂直度,所有操作人员应引起高度重视, 基准边垂直度高度200以内公差0.02MM以内,高度200-400以内公差0.0 3MM以内。如超出公差范围必须请示部门经理。操作人员在检测好侧面 的垂直度后,应再检测验证一下平面的误差;特别是慢走丝;第8页GC 模具吊环模具设计标准
第9页
GC 模具
运水
模具设计标准
字休大小:小于500的模具8MM,大于500的模具10MM,深0.3 注意事项:
1:每条运水都需要有进出标识,模具小于500的由钳工用字码打字。 模具大于500的用晒纹晒字。 2:文字标识统一加工在运水下方,下方没位置的时候可放在上方或左右两边
第13页
GC 模具
倒角
模具设计标准
当分型面有尖角时,做渐 变R角过渡
第14页
GC 模具
运水与堵头
模具设计标准
所有模具注意此处的距 离,确保堵头能安装。 (PT1/4”保证有15mm,PT1 /8”保证有10mm,少于上 面尺寸需在评审时提出 确认
刀具的标注角度技术总结

刀具的标注角度技术总结1.750 内孔车刀几何角度:主偏角Kr=750,副偏角Kr′=150,前角γ0=100,后角α0=80,副后角α0′=80,刃倾角λs=50答案:2.75外圆车刀几何角度:主偏角Kr=75,副偏角Kr=15,前角γ0=10,0 0 10 0 后角α0=80,副后角α01=80,刃倾角λs=-50答案:3.600 内孔车刀几何角度:主偏角Kr=600,副偏角Kr′=150,前角γ0=100 后角α0=80,副后角α0′=80,刃倾角λs=-50答案:,4.900 外圆车刀几何角度:主偏角Kr=900,副偏角Kr′=150,前角γ0=100 后角α0=80,副后角α0′=80,刃倾角λs=50答案:5.450 内孔车刀几何角度:主偏角Kr=450,副偏角Kr1=150,,前角γ0 0 100=10,后角α0=10,副后角α0=10,刃倾角λs=-50答案:6.450 端面车刀几何角度:主偏角Kr=450,副偏角Kr′=450,前角γ0=50 后角α0=80,副后角α0′=80,刃倾角λs=50答案:,篇二:刀具角度标注参考系刀具标注角度参考系设计制造测量角度时的基准(1)基面Pr: 通过主切削刃上选定点,垂直于该点切削速度方向的平面。
(2)切削平面Ps:通过主切削刃上选定点,与主切削刃相切,且垂直于该点基面的平面。
(3)切削刃剖平面正交平面Po:通过主切削刃上选定点,垂直于基面和切削平面的平面。
正交平面参考系:基面、切削平面和正交平面组成标注刀具角度的正交平面参考系。
法平面Pn :过切削刃上选定点并垂直于主切削刃的平面进给平面Pf :垂直于基面平行于进给方向的平面切深平面Pp :垂直基面和假定工作平面的平面篇三:刀具标注角度2)后角αo -- 后刀面与切削平面之间的夹角。
若通过选定点的切削平面位于楔形刀体的实体之外,后角为正值;反之为负值。
3)楔角βo -- 前刀面与主后刀面之间的夹角。
刀具角度选择
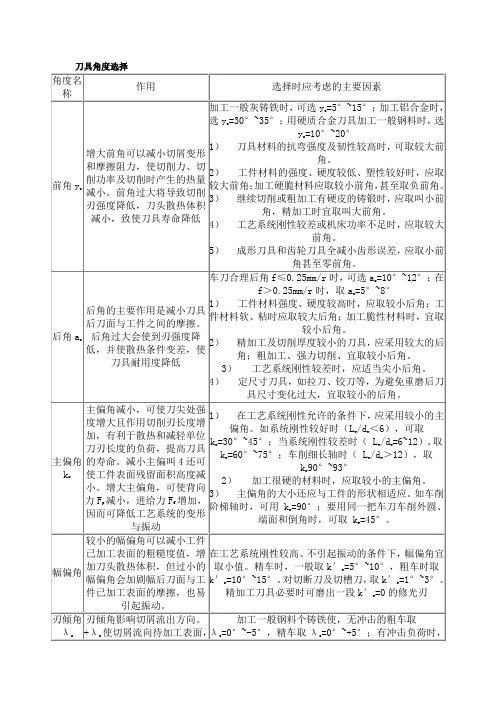
后角的主要作用是减小刀具后刀面与工件之间的摩擦。后角过大会使到刃强度降低,并使散热条件变差,使刀具耐用度降低
车刀合理后角f≤0.25mm/r时,可选ao=10°~12°;在f>0.25mm/r时,取ao=5°~8°
1) 工件材料强度、硬度较高时,应取较小后角;工件材料软、粘时应取较大后角;加工脆性材料时,宜取较小后角。
1)前刀面Ay—切下的切屑沿其流出的表面。
2)主后刀面Aa—与工件上过渡表面相对的表面。
3)副后刀面A'a—与工件上已加工表面相对的的表面。
4)主切削刀S—前刀面与主后刀面的交线,它承担主要切削工作。
5)副切削刃S'—前刀面与副后刀面的交线,它协同主切削刃完成切削工作,并最终形成已加工表面。
6)刀尖—主切削刃与副切削刃连接处的那部分切削刃。
刀具角度选择
角度名称
作用
选择时应考虑的主要因素
前角yo
增大前角可以减小切屑变形和摩擦阻力,使切削力、切削功率及切削时产生的热量减小。前角过大将导致切削刃强度降低,刀头散热体积减小,致使刀具寿命降低
加工一般灰铸铁时,可选yo=5°~15°;加工铝合金时,选yo=30°~35°;用硬质合金刀具加工一般钢料时,选yo=10°~20°
2) 精加工及切削厚度较小的刀具,应采用较大的后角;粗加工、强力切削、宜取较小后角。
3) 工艺系统刚性较差时,应适当尖小后角。
4) 定尺寸刀具,如拉刀、铰刀等,为避免重磨后刀具尺寸变化过大,宜取较小的后角。
主偏角kr
主偏角减小,可使刀尖处强度增大且作用切削刃长度增加,有利于散热和减轻单位刀刃长度的负荷,提高刀具的寿命。减小主偏叫4还可使工件表面残留面积高度减小。增大主偏角,可使背向力Fp减小,进给力Ff增加,因而可降低工艺系统的变形与振动
刀具参数设置

一:1)铣削刀具的选用:加工曲面类零件时,为了保证刀具切削刃与加工轮廓在切削点相切,而避免刀刃与工件轮廓发生干涉,一般采用球头刀,粗加工用两刃铣刀,半精加工和精加工用四刃铣刀;铣较大平面时,为了提高生产效率和提高加工表面粗糙度,一般采用刀片镶嵌式盘形铣刀;铣小平面或台阶面时一般采用通用铣刀;铣键槽时,为了保证槽的尺寸精度、一般用两刃键槽铣刀;2)孔加工刀具的选用:数控机床孔加工一般无钻模,由于钻头的刚性和切削条件差,选用钻头直径D应满足L/D≤5(L为钻孔深度)的条件;钻孔前先用中心钻定位,保证孔加工的定位精度;精绞前可选用浮动绞刀,绞孔前孔口要倒角;镗孔时应尽量选用对称的多刃镗刀头进行切削,以平衡镗削振动;尽量选择较粗和较短的刀杆,以减少切削振动。
在经济型数控加工中,由于刀具的刃磨、测量和更换多为人工手动进行,占用辅助时间较长,因此,必须合理安排刀具的排列顺序。
一般应遵循以下原则:①尽量减少刀具数量;②一把刀具装夹后,应完成其所能进行的所有加工部位;③粗精加工的刀具应分开使用,即使是相同尺寸规格的刀具;④先铣后钻;⑤先进行曲面精加工,后进行二维轮廓精加工;⑥在可能的情况下,应尽可能利用数控机床的自动换刀功能,以提高生产效率等。
另外,刀具的耐用度和精度与刀具价格关系极大,必须引起注意的是,在大多数情况下,选择好的刀具虽然增加了刀具成本,但由此带来的加工质量和加工效率的提高,则可以使整个加工成本大大降低。
总之,根据被加工工件材料的热处理状态、切削性能及加工余量,选择刚性好,耐用度高的铣刀,是充分发挥数控铣床的生产效率和获得满意的加工质量的前提。
二、切削用量的确定数控编程时,编程人员必须确定每道工序的切削用量,并以指令的形式写入程序中。
切削用量包括切削速度、背吃刀量或侧吃刀量及进给速度等。
对于不同的加工方法,需要选用不同的切削用量。
切削用量的选择原则是:保证零件加工精度和表面粗糙度,充分发挥刀具切削性能,保证合理的刀具耐用度并充分发挥机床的性能,最大限度地提高生产率,降低成本。
CNC铣床刀具知识
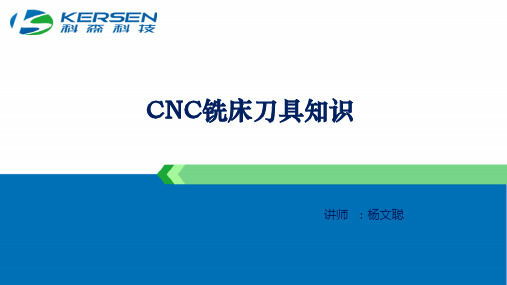
4.3、刀具使用常识(刃数与切削关系)
容屑空间
2刃 过中心切削
3刃 过中心切削
4刃 过中心切削
6刃 过中心切削
8刃 过中心切削
表面光洁度
4.4刀具使用常识(刀具选用)
加工形式 单刃
2刃
3刃
T型刀
燕尾刀
仿型刀
2.4、刀具材料(钻头、牙刀、铰刀)
整体常规刀具: 特点 1. 因钻头、铰刀、牙刀都为孔加工用刀,故分为一类 2. 钻头一般 分为定点钻(90°钻角)、钻头(118°钻角)两种 3. 铰刀为节省加工时间,现常见为钻、铰组合刀具 4. 牙刀分为铣削牙刀(3mm以上)、挤压牙刀(3mm以下)
6.2、刀具设计(T型刀具)
1、如图加工T槽,T槽切深1.09mm,T槽宽度为2mm,R角为4.1; 2、先确定直径部分,刀具R角需小于产品R角并尽量接近,故选 择D8的直径,切深1.09, 故有效切深直径为1.09*2=2.18,避位单边至少0.3mm,故脖子避位尺寸为8-2.180.3*2=5.22,可定为5mm,脖子长度大于产品最高点即可; 3、非标刀具设计首先确定最大直径小于等于产品拐角直径,脖子侧向避位一般最小要 大于0.1mm,脖子直径一般为大于等于刀具直径的1/3,超过1/3部分需评估刀具寿命;
刃数 螺旋角 前角 径向后角与轴向后角 芯厚 刃带形式 (精加工刀具/粗加工刀具)
主要影响:
表面光洁度,容屑空间,槽直线度 表面光洁度,排屑性能 ,切削力 切削刃强度 , 切削力, 切屑流方向
表面光洁度,刀具使用寿命 径向强度,切屑空间 , 表面光洁度,荷载,谐振, 切削力
4.1、刀具使用常识(刀柄)
刀具及切削参数选择

⒈ 粗车
⑴选择切削深度:由已知条件得单边余量Z=3mm,故取ap=3mm ⑵选择进给量:有查表5-5(《金属切削原理与刀具》)知,f=0.4mm/r ⑶选择切削速度:工件材料为合金结构钢,由表5-10(同上)知,ap=3mm, f=0.4mm/r时,Vc=70m/min,可保证T=60min
⑷确认机床主轴转速 s=1000Vc/π dw=891.7(r/min) ⑸由机床(C620)参数查表知,实际主轴转速为800r/min,故实际的切削速度
----刘睿、蔡波
校 核
精 加 工
切削液的选择
用改变外部条件来影响和改善切削过程是提高产品质量和生产 率的有效措施之一,其中应用最广泛的是合理选择和使用切削液。 切削液主要通过冷却和润滑作用来改善切削过程,它一方面吸 收并带走大量切削热,起到冷却作用,另一方面它能渗入到刀具与零 件和切削的接触面,形成润滑膜,有效地减小摩擦;切削液还可以一 起清洗和防锈的作用。合理地选择切削液,可以降低切削一力和切削 温度,提高刀具耐用度和加工质量。 粗加工时,切削用;量大,切削热多,应选以冷却为主的切削 液。水溶性切削液具有良好的冷却。清洗作用,也可选择离子型切削 液或3~5%乳化液,刀具的材料是硬质合金钢,耐热性较好,一般不 用切削液。若使用切削液,应注意连续、充分浇注,以免因冷热不均 产生热应里而导致刀具损坏。 精加工时,切削液的主要作用是减小工件表面粗糙度值和提高 加工精度,应选用具有良好润滑性能的切削液。可选切削油或浓度较 高的乳化液。因为精加工在高速下运转,可选用5%乳化液
----小组讨论
刀具选择理由: 金刚石立方氮化硼价格较昂贵,从经济角度来看不可取; 陶瓷虽然有高的耐热性,与金属亲和里小,加工表面质量好, 但强度韧性低,脆性大,导热能力低,易破裂; 硬质合金钢中钨钴类不加工钢,排除钨钛类; 由于切屑呈带状,切削较平稳,而YT15适合于半精加工
不同直径刀具能加工深度及建议“设计倒R角”参数

说明:在不影响“产品和模具的结构和强度”情况下,“面与面相交倒R角尽量倒 大点。以利于提升CNC加工效率。加工钢材为一般预硬钢HCR≤38度。加工淬火料 时深度要同比减少25%。 刀具直径 ¢1毫米 ¢2毫米 ¢3毫米 ¢4毫米 ¢5毫米 ¢6毫米 ¢8毫米 ¢10毫米 ¢12毫米 ¢16毫米 ¢17毫米 ¢20毫米 ¢21毫米 ¢25毫米 ¢32毫米 ¢40毫米 ¢50毫米 ¢63毫米 最佳加工深度 ≤3毫米 ≤6毫米 ≤15毫米 ≤20毫米 ≤25毫米 ≤30毫米 ≤40毫米 ≤50毫米 ≤60毫米 ≤80毫米 ≤90毫米 ≤100毫米 ≤100毫米 ≤125毫米 ≤160毫米 ≤170毫米 ≤250毫米 ≤300毫米 最佳加工R角 R≥0.55毫米 R≥1.1毫米 R≥1.6毫米 R≥2.1毫米 R≥2.6毫米 R≥3.5毫米 R≥4.5毫米 R≥5.5毫米 R≥6.5毫米 R≥8.5毫米 R≥10毫米 R≥11毫米 R≥11毫米 R≥14毫米 R≥17毫米 R≥22毫米 R≥27毫米 R≥35毫米
ቤተ መጻሕፍቲ ባይዱ
收藏!刀具5个角度选择基础
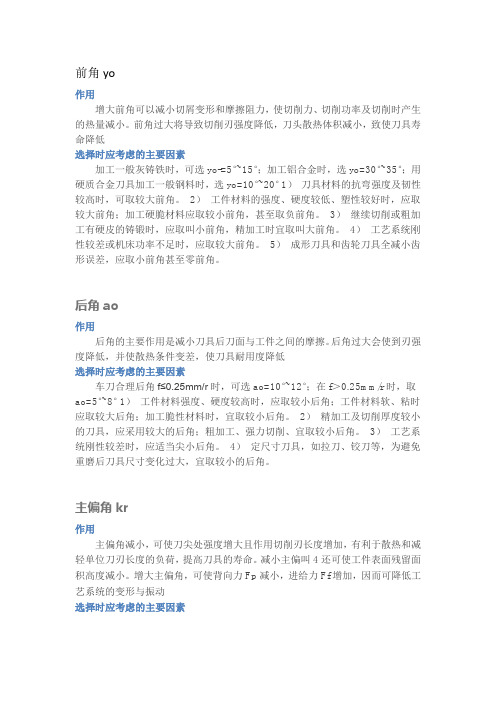
前角yo作用增大前角可以减小切屑变形和摩擦阻力,使切削力、切削功率及切削时产生的热量减小。
前角过大将导致切削刃强度降低,刀头散热体积减小,致使刀具寿命降低选择时应考虑的主要因素加工一般灰铸铁时,可选yo-=5°~15°;加工铝合金时,选yo=30°~35°;用硬质合金刀具加工一般钢料时,选yo=10°~20° 1)刀具材料的抗弯强度及韧性较高时,可取较大前角。
2)工件材料的强度、硬度较低、塑性较好时,应取较大前角;加工硬脆材料应取较小前角,甚至取负前角。
3)继续切削或粗加工有硬皮的铸锻时,应取叫小前角,精加工时宜取叫大前角。
4)工艺系统刚性较差或机床功率不足时,应取较大前角。
5)成形刀具和齿轮刀具全减小齿形误差,应取小前角甚至零前角。
后角ao作用后角的主要作用是减小刀具后刀面与工件之间的摩擦。
后角过大会使到刃强度降低,并使散热条件变差,使刀具耐用度降低选择时应考虑的主要因素车刀合理后角f≤0.25mm/r时,可选ao=10°~12°;在f>0.25mm/r时,取ao=5°~8° 1)工件材料强度、硬度较高时,应取较小后角;工件材料软、粘时应取较大后角;加工脆性材料时,宜取较小后角。
2)精加工及切削厚度较小的刀具,应采用较大的后角;粗加工、强力切削、宜取较小后角。
3)工艺系统刚性较差时,应适当尖小后角。
4)定尺寸刀具,如拉刀、铰刀等,为避免重磨后刀具尺寸变化过大,宜取较小的后角。
主偏角kr作用主偏角减小,可使刀尖处强度增大且作用切削刃长度增加,有利于散热和减轻单位刀刃长度的负荷,提高刀具的寿命。
减小主偏叫4还可使工件表面残留面积高度减小。
增大主偏角,可使背向力Fp减小,进给力Ff增加,因而可降低工艺系统的变形与振动选择时应考虑的主要因素1)在工艺系统刚性允许的条件下,应采用较小的主偏角。
如系统刚性较好时(Lw/dw<6),可取kr=30°~45°;当系统刚性较差时(Lw/dw=6~12),取kr=60°~75°;车削细长轴时(Lw/dw>12),取kr90°~93°2)加工很硬的材料时,应取较小的主偏角。
刀具角度对加工的影响
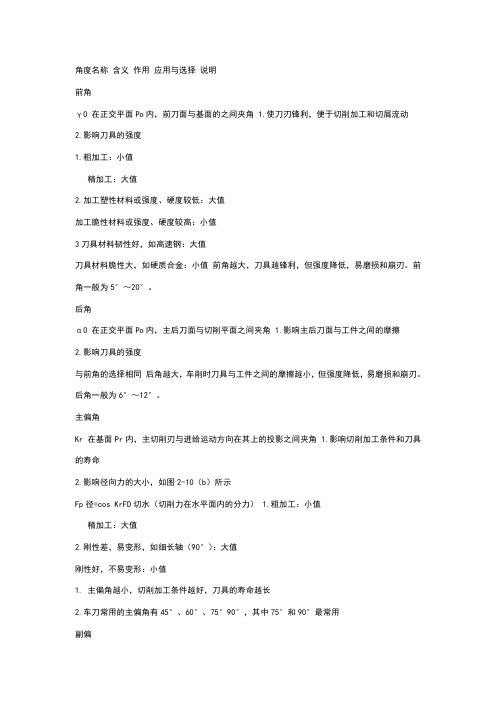
角度名称含义作用应用与选择说明前角γ0 在正交平面Po内,前刀面与基面的之间夹角 1.使刀刃锋利,便于切削加工和切屑流动2.影响刀具的强度1.粗加工:小值精加工:大值2.加工塑性材料或强度、硬度较低:大值加工脆性材料或强度、硬度较高:小值3刀具材料韧性好,如高速钢:大值刀具材料脆性大,如硬质合金:小值前角越大,刀具越锋利,但强度降低,易磨损和崩刃。
前角一般为5°~20°。
后角α0 在正交平面Po内,主后刀面与切削平面之间夹角 1.影响主后刀面与工件之间的摩擦2.影响刀具的强度与前角的选择相同后角越大,车削时刀具与工件之间的摩擦越小,但强度降低,易磨损和崩刃。
后角一般为6°~12°。
主偏角Kr 在基面Pr内,主切削刃与进给运动方向在其上的投影之间夹角 1.影响切削加工条件和刀具的寿命2.影响径向力的大小,如图2-10(b)所示Fp径=cos KrFD切水(切削力在水平面内的分力) 1.粗加工:小值精加工:大值2.刚性差,易变形,如细长轴(90°):大值刚性好,不易变形:小值1. 主偏角越小,切削加工条件越好,刀具的寿命越长2.车刀常用的主偏角有45°、60°、75°90°,其中75°和90°最常用副偏角Krˊ 在基面Pr内,副切削刃与进给运动反方向在其上的投影之间夹角 1.主要影响加工表面的粗糙度,如图2-10(c)所示2.影响副切削刃与已加工表面之间的摩擦和刀具的强度 1.粗加工:大值(与副偏角选择相反)精加工:小值1. 副偏角越小,残留面积和振动越小,加工表面的粗糙度越低,表面质量越高。
但过小会增加刀具与工件的摩擦,另外,刀具的强度降低2.副偏角一般为5°~15°刃倾角λs 切削平面Ps内,主切削刃在其上的投影与基面之间夹角 1.主要控制切屑的流动方向2.影响刀尖的强度 1.粗加工:λs<0精加工:λs≥0(防止切屑划伤工件) 1. λs<0时,刀尖处于主切削刃的最低点,刀尖强度高,切屑流向已加工表面;λs>0时,刀尖处于主切削刃的最高点,刀尖强度低,切屑流向待加工表面2. λs一般为-5°~+5°。