品质管理-G8D资料精编版
品质管理8D实战案例培训资料8D实施方法PPT78页

了解問題
1、成立小組
2.清楚 描述問題
3.执行和确认 临时措施
识別可能原因
选择最有可能 的原因
5、确定及 验证纠正措施
6、执行永久 纠正措施
最有可能的原因 是否是根本原因
7、避免再发生
识別可能的 解决方案
8、恭贺小組
6
1D (Use Team Approach )—— 成立小组
小组成员具备工艺/产品的知识,有配给的时间并授予了权限 ,同时应具有所要求的能解决问题和实施纠正措施的技术素质。 小组必须有一个指导和小组长。
31
D6、验证纠正措施
1. 换完电线后,至今尚没有发现连接点松动的迹象。 2. 断开电流接触器的电路进行试验,一旦电压不正常,转子 将自动停止工作,直至没电镀的产品从线上取下。 以上工作,小组共同进行了验证,并提请顾客事先的批准。
32
D7、防止再发生的措施
❖电镀工作指导书被修改增加了如下内容: 1)当生产线不正常停止时,操作者不仅要挑选出缺陷产品 ,而且要在工作记录记下数量及当班QC的名字。 2)在电镀线在每天早上启动前,电流接触器的连接点和电 线必须检查。以上,由杨星在12月15日完成。 ❖开发一个包括每天需检查事项的检查清单,例如生产线停 止,不管缺陷产品是否被挑选,制造部和QA需进行审核。 ❖ 依次类推,如果有类似问题,该小组负责纠正并采取适 当的预防措施。
4
何謂8D
• 此方式須通过“8D 报告”。 • 所谓“八个步骤”,其每个步骤意义及其流程请参
阅附图.该图虽已列出解决问题的各个步骤,但各 个步骤的先后順序可视问题的困难度及复杂程度 而异,不必拘泥于图示順序.且问题解决经过应有书 面记录. • 如:某一问题发生及团队组成时,可能制造人员已 经先行采取临时对策,惟其永久解决方案,则可能尚 需小组人员的共同参与,经多方研讨后才能产生。
品质管理工具8D手法.上课讲义

8-D手法Corrective Actions Procedure8-Discipline Approach矫正措施—— 8-D手法一. What is "8-D"?(什么是 8-D?8-D : A systematic approach utilized for true root cause finding & problem solving.. 8-D: 是一个用于探索原因、解决问题的系统化流程。
Discipline 1. Use Team Approach 组建团队Discipline 2. Describe The Problem 描述问题Discipline 3. Immediate Corrective Actions 紧急对策Discipline 4. Seek The Root Cause 根本原因Discipline 5. Permanent Corrective Actions 永久改善措施Discipline 6. Verification Of Effectiveness 效果确认Discipline 7. Preventive Actions 防止复发Discipline 8. Congratulate Your Team, Case Close 祝贺结案二.When shall 8-D be used? 何时用8-D?Supplier's quality performance consistently exceeds the agreed goal.当供应商品质持续超出要求的目标时。
Supplier meets the agreed goal, but one failure symptom concentrates more than 2%.当单一不良现象达到2%,即使总体质量水平满足要求。
A defect occurred that should have been contained within the supplier's process.供应商制程不良导致品质异常。
{品质管理八D方法}8D管理模式讲义ppt54页

• 以5WHY 深入追蹤直到分析出真正原因 (ROOT CAUSE)
• 儘可能以實際模擬的方式+數據圖表驗證真 正的原因.
Page 35 of 111
常用原因解析手法
魚骨圖
MATERIAL(因 1)
8D 的本質: 問題解決程序
當我們觀察到 或發現………時
這現象是否正常 跟標準或目標比較的差 異(偏離程度) 其差異是否不該在
為什麼會發生異常 ?
如何改善異常 ? 如何控制發生異 常的 原因 ?
現
象
確認並定義問題
例如: 人員出勤率93%
WHAT, WHEN, WHERE, WHO, WHY,
HOW, HOW MUCH
時間 地點 產品類型 作業人員 原材料 機器 方法 相關條件 環境 計劃
Page 32 of 111
D3:Develop Containment Action (暫時改善措施)
• 以 P-D-C-A 循環的方法暫時執行.執行過 程中要確認ICA的效果(例如PPM顯著降 低,CPK, YIELD顯著提升, 避免問題再 發生,直到永久改善行動完成為止就可以 功成身退.
Page 19 of 111
PDCA 與 SDCA
屬於兵力的提昇 (提昇製程的能力)
AP CD
AP CD
AS CD
AS CD
屬於兵力的維持 (將製程穩定化)Page 20 of 111
PDCA , CA-PDCA 與 SDCA
AP CD
AS CD
(+)
GAP
Analysis
质量管理G8D作成要领说明
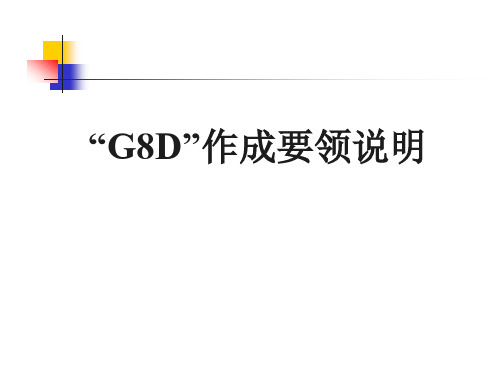
被充分地评审和修订?
2、是否对类似产品或工艺进行了措施的水平
展开?
注意:增加过程检验或作一个单独的审核,不
能算作是预防措施。Fra bibliotek有效率 实施日 %: 期:
预防措 预防措 施的有 施的实 效性 施日期
“G8D”的作成要领
D8-受表彰的小组和个人
总结小组在问题解决过程中的经验,对小组及 小组成员的贡献进行表彰。
产品或工艺名称:
公司或部门:
指发生问题的产品或涉及 指发生问题的供应商名称或及其部
的加工过程
门
“G8D”的作成要领
D0-现象:
指问题的定义和清晰/量化的描述
D0-应急反应活动:
有效率%: 实施日期:
为了不影响顾客生产,对采取的应急措施 应急措施的 应急措施
的有效性进行验证后而采取的应急活动,有效性
报告人 时间
有效率 %:
永久措 施的有 效性
实施日 期:
永久措 施的实 施日期
“G8D”的作成要领
D7-预防措施
再发防止
对相关的文件进行修订,以防止该问题及类似
问题的再发。如有必要,建议从体系或系统的
角度着手改进(包括方针、惯例、程序文件、
流程等) 。
(标准化)
采取预防措施时,通常考虑以下方面:
1、PFMEA、控制计划及相关的过程表单是否
1、是否识别出了可接受的根本原因? 2、每一个根本原因对发生本次问题的贡献率有多大? 3、找到的原因在工艺上认可了吗? 4、找到的原因在体系/体制上认可了吗?
影响比 例%
每一个根 本原因的 贡献率
“G8D”的作成要领
D5/D6-永久性的纠正措施
针对D4的根本原因(发生/流出)确定永久性的纠 正措施并进行验证。在制定永久性的纠正措施时, 应考虑以下方面:
{品质管理八D方法}品质改善8D程序手法概述PPT64页
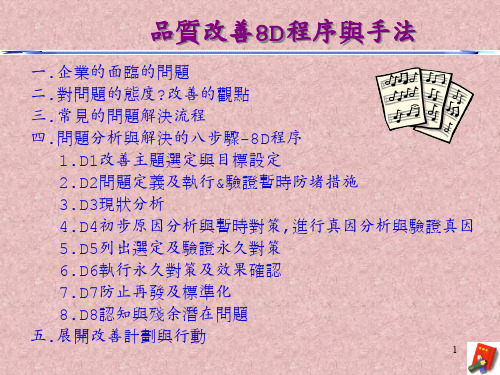
依據整體經營需求望展開
-- 生產各類目標
-- 品質各類目標
-- 財務各類目標
-- 采購與原物料各類目標
-- 營業各類目標
-- 產品(研究)開發各類目標
來自外部顧客要求
來自內部顧客要求
同業(競爭者)產品或技術標竿比較
同業(競爭者)管理水準標竿比較
異業管理水準標竿比較
來自持續不斷改善動機
品質改善8D程序與手法
一.企業的面臨的問題
二.對問題的態度?改善的觀點
三.常見的問題解決流程
四.問題分析與解決的八步驟-8D程序
1.D1改善主題選定與目標設定
2.D2問題定義及執行&驗證暫時防堵措施
3.D3現狀分析
4.D4初步原因分析與暫時對策,進行真因分析與驗證真因
5.D5列出選定及驗證永久對策
6.D6執行永久對策及效果確認
人員能力 不足問題
業績衰退 問題
人員流動 性問題
營業毛利 少
品 質 改 善 8D 程 序
無法因應 企業整體資 環境能力 源無效能
生產效率 員工士氣問
問題
題
易生產問 開發時效問
題
題
缺乏管理 組織活力不
能力
足問題
新產品缺 產品缺乏競
乏
爭力
9
企業面臨的問題
三.貴公司現存在的問題
• VOQ進料檢驗單位
• • •
企業面臨的問題
b.問題的種類與結構(形態)
問題結構有如冰山
現象(可感覺.可衡量
)
處置
一次因 (近因)
治標
品 質 改 善 8D 程 序
n次因 (根因)
治本
G8D

●
有必要时需要邀请其它相关部门,如:客户,供应链等
Schneider Electric
-SSIC 2012
9
团队要求
●
Team Approach
● 跨部门团队 – 由与此问题有关的部门成员组成
工艺工程师,质量工程师,维修工程师,IE工程师,等.
● 多学科团队 – 由不同领域的成员组成
● 工程人员,市场人员,客户服务,制造作业员,财务人员,等
比较好的做法 : 良品与不良品的比对通常可以清楚的描述问题.
Schneider Electric
-SSIC 2012
15
问题:
早晨开车去上班
车在上坏掉了
“为什么是我?!“
Schneider Electric
-SSIC 2012
16
问题描述方法
问题描述方法
1. 用数据说话:
问题 答案 (以车坏在路上为例子) 为什么很重要 定义研究对象
确定优先解决的问题
2. 提供良品与不良品的直观比较: 3. 尽量详细/直接.
Schneider Electric -SSIC 2012 18
以车坏在路上为例 » 合适的问题描述
今天早晨在我开车去上班的路上,车在半路熄火;导致我不能按时上班;没有人 员受伤。
Schneider Electric
-SSIC 2012
●
●
选定合适的统计工具。
如果是重复发生,需要先前的改善措施进行检查。
Schneider Electric
-SSIC 2012
13
定义问题现状
规则 : 要包含:- What, When Where, Who, Why and 2How (How bad is the problem/How it was detected ?).
{品质管理八D方法}8D和质量工具
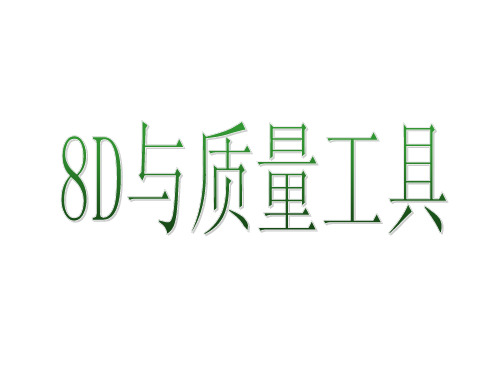
解决收集数据的问题,
提供记录相关问题的记录格式
1199
查检表的作业流程
明确目的
当前的问题:如顾客抱怨、合格率水平、质量损失率、返 工返修、设备故障率等。因此, 必需把握現状与使用的目的
拟定查检項目
从因果图中选择当前影响不合格的潜在原因作为查检项 目,以4—6项为宜
确定抽样方案
全检、抽检
确定查检方法
解决问题的途径之一
22
8D QC工具
8D是解决问题的八个步骤,它系统性根本性地 研究、分析和解决不符合问题,并防止其再发生, 是一种结构化的工作流程。
8D研究的对象:是已发生的不符合——体系、产品或过程。
系统性:研究与问题所关联的各个分支,解决的是系统偏差的问题;
是一项团队的活动。
根本性:研究发生问题的根源,不仅要解决问题的表观,更注重分析造
2211
层別法
层別法就是针对班组不同、作业员不同、工艺方法不 同、設備不同、原材料批次等生产要素所收集的数据,按 照它們共同的特征加以分类、统计的一种分析方法。也 就是为了区別各种不同原因对结果的影响,而以个別原 因为主,分別统计分析的一种方法。
解决数据的分类问题 为设计查检表提供依据
原材料进货质量信息统计分层: 交检数、验收合格数(递交合格率)、验收不合格数、使 用不合格数、偏差使用数(应列入使用不合格数的分项)、 退货数、质量特性的分类。
判断不合格的基准、检测与判定方法、查检时间和地点、
查检活动责任人等
设计查检表
数据记录格式
实施查检
对记录的数据可应用柏拉图确定主要原因
2200
# # # 工件不合格查检表
#### #### 表面不良 砂眼 加工不良 气孔 其他 缺陷合计数 不合格工件数
G8D管理要求

长安福特马自达
Changan Ford Mazda
2. G8D 针对CFMANJ的管理流程 G 8 D H a n d lin g
QR/QM
Proc e ss 以精立业 以质取胜
Warranty
STA Team
Supplier Adaption G8D
注意事项:
<14 days
Supplier Submit G8D to STA
- 问题会再次发生 - 增加工作量 - 恶化关系 - 增加成本
长安福特马自达
Changan Ford Mazda
以精立业 以质取胜
STA Team
Thanks!
流出 Escape
与完成检验、检查相关的
检查文件是否有检查项目,检查频 次/检查方法是否有效/ 是否实施 根本原因的推导:建议使用相关工具, Date Efficiency Percent Implemented 如:鱼骨图,5Why等。 根本原因的验证:最佳的是能够再现问 题的发生与消失。 有效率% 实施日期
有效率% 实施日期 Efficiency Percent Implemented Date 临时措施需要迅速并且验证有效性,确
保不会引入新问题。如改变零件状态, 需要得到PD方面的认可,提Alert/偏差 申请有效性及有无再发
验证Verification / Validation:
长安福特马自达
Changan Ford Mazda
人、机、料、法、环
D4-根本原因Root Cause
3.2 G8D 填写要点
层次上升 文件、程序、规定
以精立业 以质取胜
STA Team
影响比例%Affect Percent
质量管理8D报告培训经典教材含案例分析

常用方法
1.对操作员现场询问 2.现场观察 3.模拟试验
4.DOE试验
5.异常记录
四. 8D步骤—D4原因分析
5-Why 分 当析一个原因被发现时,不停地问为什么、为什么、为什么、
为什么、为什么,一直到无法拆解下去 。
TOYOTA 5-Why?
1W
WHY 问题
2W
WHY 中间原因
3W
WHY 中间原因
单击添加副标题
8D报告培训教材 (经典)
Possible
课堂纪律
一.手机请关机或调成静音。 二.请保持课堂安静,请勿交头接耳或大声讲话。 三.如有问题请会后交流 。
目录
CONTENT
01 什么是8D 单击此处添加正文
03 何时采用8D 单击此处添加正文
05 8D改善案例 单击此处添加正文
02 为什么要推行8D 单击此处添加正文
什么是问题???
问期题望
期望 目标
现实
四. 8D步骤—D2问题描述
问题描述方法:5W/2H
WHO
5W2H 谁
WHAT
什么
WHEN WHERE WHY HOW
何时 何地 为什么 怎么样
解释 识别那一个客户(内/外部)在抱怨 问题的症状,无法用文字描述清楚的,借助 于数字或图片将问题表达清楚
记入问题发生的日期 记入问题发生的场所 识别已知的解释 在什么的模式或状态这问题会发生
HOW MUCH
什么程度 问题发生的程度、量
13
需要考虑的问题:
一.防止继续产生不良品 (减少不良品产生)。
二.减小产生的不良和后续 可能产生不良对客户的影 响。
定义、验证和执行临时控制行动,保证在 永久纠正措施实施前,将问题与内外部顾 客隔离。
品质部培训8D课程PPT培训课件

实施永久措施
总结词
制定并实施永久措施,从根本上解决问题, 防止问题再次发生。
详细描述
在8D方法实施流程中,实施永久措施是为 了从根本上解决问题,防止问题再次发生。 这些措施应该是经过深思熟虑和充分验证的, 具有长期性和稳定性。在实施永久措施的过 程中,团队需要密切关注措施的效果,及时 调整和完善,以确保问题得到彻底解决。
详细描述
在8D方法实施流程中,实施临时措施是为了控制问题的进一步发展,减轻其对产品、过程和客户的影 响。这些措施通常是紧急的、临时的,旨在稳定局势,为后续的深入分析和改进提供基础。
确定并验证根本原因
总结词
深入分析问题,找出根本原因,为制定 永久措施提供依据。
VS
详细描述
在8D方法实施流程中,确定并验证根本 原因是关键的一步。团队需要运用科学的 方法和工具,对问题的根本原因进行深入 分析,并对其进行验证。只有确定了问题 的根本原因,才能制定出有效的永久措施 ,从根本上解决问题。
04
8D方法应用案例分析
应用案例一:汽车行业中的8D方法应用
总结词
广泛采用、标准化流程
VS
详细描述
汽车行业是8D方法应用最为广泛的领域 之一。各大汽车制造商采用8D方法来解 决生产过程中出现的各种质量问题,确保 产品的一致性和可靠性。通过标准化流程 ,8D方法在汽车行业中实现了高效的问 题解决和持续的质量改进。
02
8D方法实施流程
成立专项团队
总结词
组建跨部门、跨领域的团队,确保问题解决的有效性和效率。
详细描述
在8D方法实施流程中,第一步是成立一个由不同部门和领域专家组成的专项团 队,以确保问题解决的全面性和专业性。这个团队应该具备丰富的经验和技能, 能够针对不同的问题进行深入分析和有效解决。
{品质管理八D方法}8DTRAINING培训讲义PPT85页

8D 步驟
D0
准备
D1
建立团队
D2
问题描述
D3
制定实施临时措施(ICA)
D4
确定根本原因和失控点
D5
选择并验证PCA
D6
实施并确认PCA
D7
防止再发生
D8
认可贡献、庆祝胜利
D2 目的
• 通过下面的技术描述内部/外部问题
问题陈述——第二步
• 一旦确定了对象和缺陷,第二步就是问“为什 么缺陷发生在这个对象身上?”
• 精炼陈述为了
– 努力集中于只有一个根本原因的简单问题 – 利用现有的数据尽可能地接近根本原因 – 检查问题的根因是否未知
• 一遍一遍重复“为什么缺陷发生在这个对象身 上?”称为重复为什么
– 连续询问直至无答案为止
8D
2008-2-27
什么是8D?
8D(8 Disciplines of Problem Solving),是解决问题的8个步 骤,是在问题原因不确定时,运 用特定的系统过程推动问题的根 本解决。
8D 步驟
D0
准备
D1
建立团队
D2
问题描述
D3
制定实施临时措施(A)
D4
确定根本原因和失控点
• 职责类别:
– 组长 – 时间管理 – 板书 – 记录
组长
• 小组管理者 • 小组发言人 • 与小组一起工作,设定目标和任务 • 收集并概括成员的意见 • 指导使用8D方法 • 集中关注会议的目的和议程 • 可以向小组提供各种信息 • 指导确定结论 • 概括结论 • 成立子组 • 参加讨论时放弃领导的 角色
品质管理八D方法8D报告起源及运用ppt47页
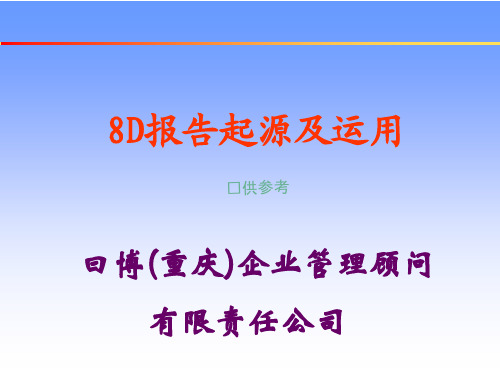
紧急反应计划可能很难用测量验证,因为它是以常 识为基础。例如,如果将受到影响的产品停止发运, 那么顾客就不会再经历症状。
1D现象描述和准备
紧急反应计划的执行和证实: 选择和验证并执行了紧急反应计划后,必须证 实紧急反应计划能够起作用。证实就是提供正 在进行中的证据证明紧急反应计划达到了目的 并且没有引起新的问供题参考。 到达顾客前的证实: 试验 检测 观察 关于产品和过程的检测 顾客证实包括顾客反馈。
6D 预防措施(管理、技术) 修改必需的系统包括政策、程序、图纸等 来防止同一或相似问题的再发生。
7D责任落实和表彰 供参考 落实相关供应商、内部责任人的责任,并 根据情况表彰小组和个人的贡献。
8D关闭确认和总结。 总结本次改进活动过程中的经验,找出遗 留问题。
1D需填写的内容
表头内容: 主题 产品型号/过程名称 状态:开发、样件供、参小考 批、批量等 重要度 公司或部门 小组或负责人 启用日期
3D 开发临时纠正措施
第三步:执行临时纠正措施 执行临时纠正措施的重要部分是计划怎样执行临时纠 正措施。
第四步:证实临时纠正措施 执行临时纠正措施后,需要进行证实。证实用来证明 临时纠正措施满足要求供并参且考没有产生新的问题。 证实有两种形式: 到达顾客前证实。在暴露给顾客前和成功验证之后, 证明行动在起作用的证实。包括试验、观测、和其 它质量检测。 顾客证实。来自于顾客的证明临时纠正措施正在起 作用的证实。
1D需填写的内容
1D: 现象(事实) 发生件数(故障件与总数的比例) 发生的状况(发生场所如山区平地海边、季
节、使用状况、是否新供的参产考品等) 应急反映计划 实施人/日期 确认及有效性检查 检查人/日期
1D现象描述和准备
为什么准确描述和准备8D过程
三现五原则G8D品质保全讲义

一:無科學根據DATA 無科學根據
疑 問 點:常發生的直覺判斷
焊接強度不足→對策:焊道加長2mm 正確嗎? 2mm。 ~焊接強度不足→對策:焊道加長2mm。正確嗎? 模溫不足變形→對策:模溫提高10 沒問題嗎? 10° ~模溫不足變形→對策:模溫提高10°。沒問題嗎?
思
考:加長2mm、提高10°C如何得到的? 加長2mm、提高10° 如何得到的? 2mm 10
品質研習講義 品質研習講義
1.三現五原則 1.三現五原則 2 . G8D .品質保全 3 .品質保全
前
背景: 一.背景:
言
1.品質為企業生存之基本條件 1.品質為企業生存之基本條件 2.品質經常發生不良 品質經常發生不良, 2.品質經常發生不良,品質損失大 3.品質不良 品質不良, 3.品質不良,操作者認為是品管部門的責任 4.SY品質目標 品質目標100PPM↓ 4.SY品質目標100PPM↓ 5.不良解析經常未能找出真因 5.不良解析經常未能找出真因
為 什 麼 之
五 層 左前座椅椅背 前/後升降連桿 原圖規格設定 分 晃動大 與滑板 ASSY 寬鬆 析 搭配間隙大
1
2
3
4
5
識別記號
責任單位
組立日期
引擎號碼
* 請 於 94 年 5 月 4 日 下 13 時 30 分 NY 會 議 室 參 加
對 策 報 告 . 請 先 向 廠 部 市 主 管 報 告
三現五原則
市怨編號 反應單位 反應者 K0504001 廠異編號 張 木 信 主管 管制單位 品 質 檢 查 課 承辦者 尤 宏 文 主管 游 家 齊 製 品 NY 技 術 反應日期 94 年 04 月 22 日 課 對策 單位 4PTD 指派對策者 PL
- 1、下载文档前请自行甄别文档内容的完整性,平台不提供额外的编辑、内容补充、找答案等附加服务。
- 2、"仅部分预览"的文档,不可在线预览部分如存在完整性等问题,可反馈申请退款(可完整预览的文档不适用该条件!)。
- 3、如文档侵犯您的权益,请联系客服反馈,我们会尽快为您处理(人工客服工作时间:9:00-18:30)。
G8DG8D概述G8D是福特标准化的解决问题的方法。
它由8个步骤和1个准备步骤组成,这些步骤分别协助G8D团队成员以客观的角度来确定、定义和解决问题并防止类似的问题再发生。
在开始我们的讲解之前,我想先谈谈以下两点:1.问题还是机会?在每一个问题的背面都隐藏着它的反面-机会,关键是我们能否去除它的伪装,找到机会--无名我想负责跟踪质量的每个人都可能碰到过这样的情况:出了个质量问题,你一看,咿……这个问题我们在去年或者以前不是解决过了吗?为什么现在又出来了?如果这种事情,很不幸发生在你们的身上的话,我可以想象你们会有多恼火,一次又一次花费大量的精力在相同的问题上。
因此,从系统上评估影响并从根本上解决问题在长远来说,提供了节省时间、金钱和资源的机会。
但是能否把握这种机会的前提是:我们是否知道真正的问题所在。
2.问题的认识不管露在水上的冰山一角有多大,80%仍然是在水面之下,问题也是一样。
不管从表面上看来,问题有多严重或者压力有多大,它仅仅是问题的表象。
表象可能小到只是个小缺陷,也可能大到停产、召回。
这里提到的冰山一角,其实就是二八原则,通过对20%的表象的研究,找到机会,解决80%的问题。
以上是我觉得大家对问题应该持有的态度。
G8D的背景和优点1987年,福特汽车公司开始部署8D,解决内部过程中和在其整个北美一级供应商的问题。
由于它纳入了朱兰,戴明等的思想,此后不久,获得世界范围的承认和执行。
1995年,福特汽车组建跨组织的指导小组,将该过程进行标准化并建立起全球G8D数据库系统,以避免不同区域及国家的差异。
G8D集合了团队工作、经验学习、鱼骨刺图、头脑风暴、FMEA等各种工具,因此不仅仅是现在大家对其比较单薄的认识,我会在后续给大家一一展示,目前大家所接触到得G8D,只是G8D的思路和方法,并没有机会进入到FORD的数据库系统,使用G8D软件在数据库中查询、更新和提交。
综上,归纳G8D作用如下1.G8D是一种标准化的解决问题的方法,2.G8D是QS 9000, ISO 9000等其它标准的一部分,3.G8D给福特,或者广泛点来说-质量人,提供了一种共通的语言D0 准备G8D1.为什么要为G8D过程作准备G8D的过程是很精深的,前面已经提到部分工具,后续还会继续介绍。
可能涉及大量的时间、人员和资源(通常来说,1个标准的G8D,需要90天的时间)。
如果使用不适当(并不是所有的问题都适合采用G8D)将会浪费更多的时间、人力和相关的资源。
D0帮助你把焦点放在真正需要采用G8D解决的问题上,以便有效的地使用资源。
2.D0需要做什么采取紧急响应措施ERA(Emergency Response Action)确定是否适合采用G8D0.1 ERA定义3.紧急响应措施ERA(Emergency Response Action)定义:紧急响应措施(ERA)确认G8D是否必要时或之前所采取的措施,目的在于保护顾客及相关的各方不受故障现象影响。
那么谁是顾客?谁又是相关的各方呢?顾客是指经历故障现象的一个人、组织或驾驶员;受影响的各方是指将被故障现象影响的人、组织或驾驶员。
例如:一个驾驶员由于空调问题将车开来维修,驾驶员就是顾客;处理空调保修的服务人员是相关的各方。
思考题:一个驾驶员载着他的朋友一起,由于空调问题,将车开来到4S店来找维修人员维修,请问,在此案例中,谁是顾客,谁是受影响的各方?细化:当现场发生问题时,顾客反馈给你的可能就是一个故障现象,例如:车门打不开,空调不制冷、零件装不上。
什么原因,它们不知道,甚至并不知道是不是你的零件的问题。
你不能要求你的顾客跟你清楚你们自己零件一样了解你的零件。
因此,你需要时间去了解更多的信息或者再做相关的初步调查。
而在你调查这段时间里面,怎么样来保证说不合格的件不流出到底最终顾客手上,造成影响,你需要采取措施。
因此,ERA有以下特点:ERA是基于你手头现有的信息而制定的措施ERA可能是大到影响停止所有发运,也可能是小到什么都不用做ERA可能是须立即执行的措施——你不必花太多时间去研究应急措施ERA不一定是必需的,根据问题的严重性和顾客的影响来决定是否需要ERAERA是在成立G8D小组之前实施的,通常由监督人(对问题负责并有权解决的人)决定是否执行ERA。
有时,ERA可能在量化数据收到前执行。
在任何情况下都需要评估是否需要ERA。
有时需要不止一个ERA来完全保护我们的顾客。
例如,一个ERA用来保护顾客,另一个用来保护他们免受第一个ERA带来的副作用。
0.2 通常的ERA有哪些1.停产(停产了,当然没有不合格件流出了,自然不会对顾客和相关的各方产生影响)2.挑选(挑出合格件,不让不合格件流出)3.停止发货、换货、紧急空运物料、100%检查等等例如一个水坝有一个小洞正在漏水,一个小孩看见后立即用自己的手指塞住水坝上的洞,从而挽救了整个村子。
ERA就是:小孩用手指塞住水坝上的洞,阻止水的流出0.3 ERA的实施和确认实施ERA后,必须确认ERA能够起作用。
提供证据证明ERA达到了目的并且没有引起新的问题。
验证主要分成两块,到达顾客前的验证和顾客之后的确认。
到达顾客前的验证主要是用来确定我们的产品是否符合设计的要求,主要方式是:1)测试;2)检测;3)观察;4)关于产品和过程的质量检查顾客确认为顾客反馈,主要是用来确定采取ERA的件之后,原来的故障现象是否已经消除。
通常使用Paynter 图可以用来确认ERA。
例如:有个零件,顾客反馈非常难装配,由于涉及到几个相关零件,而暂时也不知道哪个零件不合格,那么为了满足生产,可能ERA就是对其中的某个零件进行扩孔,如从∮10改到∮12,那么在选择和验证该ERA的时候,可能就需要考虑扩孔后对强度、装配定位等等是否有影响,并通过相关的实验、或CAE分析、或者借鉴以前的经验进行验证,如无风险,可采取。
那么采取之后,也就是实施之后,到达顾客前,我们当然需要通过检测等方式去测量我们的∮10孔是否改到∮12,而不是∮11或者∮13,要不然不进行测量,直接送到顾客,又发现装配不上,这个时候不仅没有起到作用反而误导了大家,时间也白白浪费掉了,更谈不上支持生产了.OK,如果扩孔后没问题,那么零件给了顾客之后,顾客使用新零件装配,是否还存在难装配这样一个故障现象?如果没有的话,那就是ERA确认有效;当然,中间还会涉及到以下几点,因情况不同,但需要注意:1.ERA理论上要求在24小时内实施;2.如果真的从∮10改到∮12,那么需要顾客的确认;3)ERA的件需要考虑增加标识,以进行区分。
综上:我们可以看出,ERA主要针对的是顾客经历的故障现象的消除。
前面也讲到了,在D0阶段,我们只接到了顾客的抱怨,并不知道故障现象之后的问题是什么,更谈不上原因的分析了。
而由于顾客生产的压力等各种原因,时间紧急,又不能给顾客造成损失,因此我们采取ERA,让他们不再受这种故障现象的困扰。
给我们腾出时间,去找问题和分析原因,进行后续工作。
但要强调的一点就是:不要以为有了ERA,顾客没有抱怨了,我们就可以高枕无忧,或者舒缓后续的工作。
前面ERA的细化中提到:通常由监督人(对问题负责并有权解决的人)决定是否执行ERA。
有时,ERA可能在量化数据收到前执行,然后再看看ERA通常的方式。
为什么要有监督人或公司高层来决定是否适合采用ERA?我们可以看到ERA通常会有比较大的影响,或者涉及到额外费用、人力和资源的投入,是不经济的,所以我们要做的就是尽快进行后续工作,缩短ERA的时间。
由于8# sky66666 提到不清楚怎么样使用Paynter图来确认ERA。
我结合上面的举例,简单说明下:从附件简示图上可以看出,实施之后,故障现象消除,确认有效。
0.4 G8D的适用标准以上我们讲解了D0中的ERA,那么还有一个重点就是判断是否采用G8D这种方法来解决问题。
那么在列出具体的判定标准之前,为便于后续大家的理解,我想先跟大家明确一个概念:故障现象和问题。
0.5 故障现象和问题什么是故障现象,什么是问题,我想大家听起来都觉得可以理解,但是在实际操作中却又非常容易混淆,因此会通过比较详细的例子来给大家建立一个比较深的印象。
下面给出故障现象和问题的定义;1.故障现象是指可测量的事件或效果(它们必须是顾客体验到的)。
它表示一个或多个问题存在。
2.问题是指同期望有偏差或任何由未知原因引起的有害的后果。
3.故障现象是问题的显示4.G8D过程区别了故障现象和问题。
适用标准的大部分是故障现象。
没有故障现象,不会知道有问题。
例如在水坝漏水的案例中:现象是水坝漏水,问题就是水坝上有小洞。
思考题:下面冰激凌的故事是来自本论坛上,在此对原作者表示感谢,在此引用只是想大家能够更好的理解故障现象和问题。
希望大家能够在看完这个小故事后,回帖告诉我,你们觉得在此案例中,什么是故障现象,什么是问题?香草冰激凌的故事这是一个发生在美国通用汽车的客户与该公司客服部间的真实故事。
有一天美国通用汽车公司的庞帝雅克(Pontiac)部门收到一封客户抱怨信,上面是这样写的∶“这是我为了同一件事第二次写信给你,我不会怪你们为什么没有回信给我,因为我也觉得这样别人会认为我疯了,但这的确是一个事实。
”“我们家有一个传统的习惯,就是我们每天在吃完晚餐后,都会以冰淇淋来当我们的饭后甜点。
由于冰淇淋的口味很多,所以我们家每天在饭后才投票决定要吃哪一种口味,等大家决定后我就会开车去买。
”“但自从最近我买了一部新的庞帝雅克后,在我去买冰淇淋的这段路程问题就发生了。
”“你知道吗?每当我买的冰淇淋是香草口味时,我从店里出来车子就发不动。
但如果我买的是其它的口味,车子发动就顺得很。
为什么这部庞帝雅克当我买了香草冰淇淋它就发不动,而我不管什么时候买其它口味的冰淇淋,它就一尾活龙?为什么?为什么?”事实上庞帝雅克的总经理对这封信还真的心存怀疑,但他还是派了一位工程师去查看究竟。
当工程师去找这位仁兄时,很惊讶的发现这封信是出之于一位事业成功、乐观、且受过高等教育的人。
工程师安排与这位仁兄的见面时间刚好是在用完晚餐的时间,两人于是一个箭步跃上车,往冰淇淋店开去。
当他们买好香草冰淇淋回到车上后,车子果然发不动了。
这位工程师之后又依约来了三个晚上。
第一晚,巧克力冰淇淋,车子没事;第二晚,草莓冰淇淋,车子也没事;第三晚,香草冰淇淋,车子发不动。
这位思考有逻辑的工程师,到目前还是死不相信这位仁兄的车子对香草过敏。
因此,他仍然不放弃继续安排相同的行程,希望能够将这个问题解决。
工程师开始记下从开始到现在所发生的种种详细资料,如时间、车子使用油的种类、车子开出及开回的时间……,根据资料显示他有了一个结论,这位仁兄买香草冰淇淋所花的时间比其它口味的要少。