脱硫石灰石密度与重量百分比关系
石灰石石膏湿法脱硫工艺脱硫效率影响因素
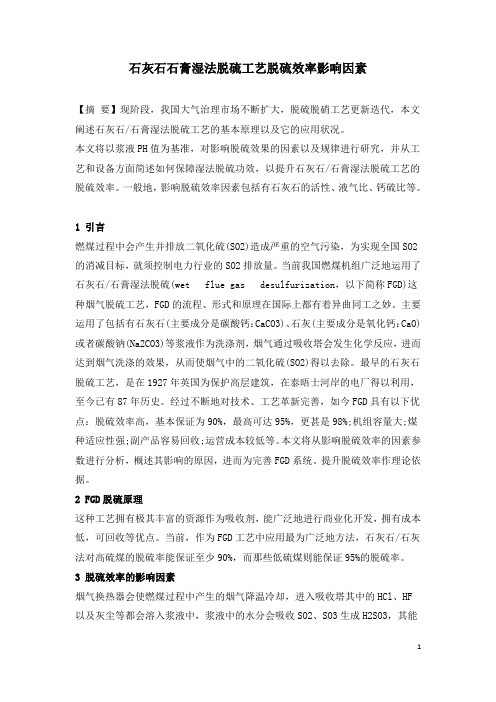
石灰石石膏湿法脱硫工艺脱硫效率影响因素【摘要】现阶段,我国大气治理市场不断扩大,脱硫脱硝工艺更新迭代,本文阐述石灰石/石膏湿法脱硫工艺的基本原理以及它的应用状况。
本文将以浆液PH值为基准,对影响脱硫效果的因素以及规律进行研究,并从工艺和设备方面简述如何保障湿法脱硫功效,以提升石灰石/石膏湿法脱硫工艺的脱硫效率。
一般地,影响脱硫效率因素包括有石灰石的活性、液气比、钙硫比等。
1 引言燃煤过程中会产生并排放二氧化硫(SO2)造成严重的空气污染,为实现全国SO2的消减目标,就须控制电力行业的SO2排放量。
当前我国燃煤机组广泛地运用了石灰石/石膏湿法脱硫(wet flue gas desulfurization,以下简称FGD)这种烟气脱硫工艺,FGD的流程、形式和原理在国际上都有着异曲同工之妙。
主要运用了包括有石灰石(主要成分是碳酸钙:CaCO3)、石灰(主要成分是氧化钙:CaO)或者碳酸钠(Na2CO3)等浆液作为洗涤剂,烟气通过吸收塔会发生化学反应,进而达到烟气洗涤的效果,从而使烟气中的二氧化硫(SO2)得以去除。
最早的石灰石脱硫工艺,是在1927年英国为保护高层建筑,在泰晤士河岸的电厂得以利用,至今已有87年历史。
经过不断地对技术、工艺革新完善,如今FGD具有以下优点:脱硫效率高,基本保证为90%,最高可达95%,更甚是98%;机组容量大;煤种适应性强;副产品容易回收;运营成本较低等。
本文将从影响脱硫效率的因素参数进行分析,概述其影响的原因,进而为完善FGD系统、提升脱硫效率作理论依据。
2 FGD脱硫原理这种工艺拥有极其丰富的资源作为吸收剂,能广泛地进行商业化开发,拥有成本低,可回收等优点。
当前,作为FGD工艺中应用最为广泛地方法,石灰石/石灰法对高硫煤的脱硫率能保证至少90%,而那些低硫煤则能保证95%的脱硫率。
3 脱硫效率的影响因素烟气换热器会使燃煤过程中产生的烟气降温冷却,进入吸收塔其中的HCl、HF以及灰尘等都会溶入浆液中,浆液中的水分会吸收SO2、SO3生成H2SO3,其能分解H+和HSO3-,与浆液中的CaCO3发生水反应生成二水石膏,使得浆液的PH 值发生变化。
电厂脱硫石灰石粉标准
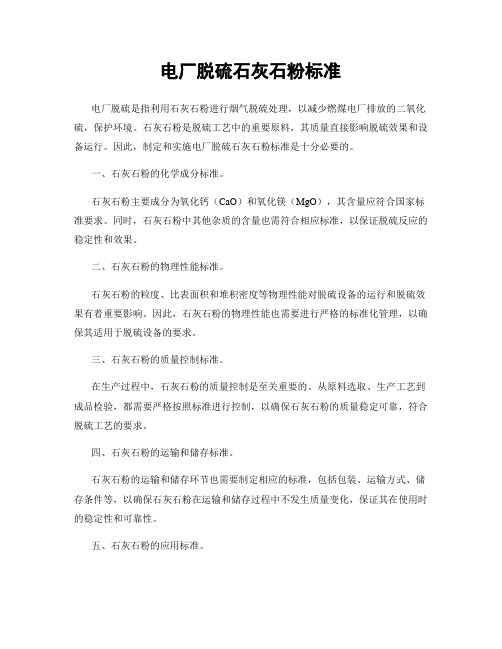
电厂脱硫石灰石粉标准电厂脱硫是指利用石灰石粉进行烟气脱硫处理,以减少燃煤电厂排放的二氧化硫,保护环境。
石灰石粉是脱硫工艺中的重要原料,其质量直接影响脱硫效果和设备运行。
因此,制定和实施电厂脱硫石灰石粉标准是十分必要的。
一、石灰石粉的化学成分标准。
石灰石粉主要成分为氧化钙(CaO)和氧化镁(MgO),其含量应符合国家标准要求。
同时,石灰石粉中其他杂质的含量也需符合相应标准,以保证脱硫反应的稳定性和效果。
二、石灰石粉的物理性能标准。
石灰石粉的粒度、比表面积和堆积密度等物理性能对脱硫设备的运行和脱硫效果有着重要影响。
因此,石灰石粉的物理性能也需要进行严格的标准化管理,以确保其适用于脱硫设备的要求。
三、石灰石粉的质量控制标准。
在生产过程中,石灰石粉的质量控制是至关重要的。
从原料选取、生产工艺到成品检验,都需要严格按照标准进行控制,以确保石灰石粉的质量稳定可靠,符合脱硫工艺的要求。
四、石灰石粉的运输和储存标准。
石灰石粉的运输和储存环节也需要制定相应的标准,包括包装、运输方式、储存条件等,以确保石灰石粉在运输和储存过程中不发生质量变化,保证其在使用时的稳定性和可靠性。
五、石灰石粉的应用标准。
石灰石粉在脱硫工艺中的应用也需要制定相应的标准,包括投加比例、投加方式、投加位置等,以确保石灰石粉能够发挥最佳的脱硫效果,同时减少对环境和设备的影响。
六、石灰石粉的监测和评价标准。
为了确保电厂脱硫工艺的稳定运行,还需要制定相应的石灰石粉监测和评价标准,包括对石灰石粉质量和使用效果进行定期监测和评价,及时发现问题并进行调整和改进。
总结,电厂脱硫石灰石粉标准的制定和实施,对于保障脱硫工艺的稳定运行和脱硫效果的达标具有重要意义。
只有严格按照标准要求进行生产、运输、储存和应用,才能确保石灰石粉的质量稳定可靠,为电厂脱硫工作提供可靠的保障。
石灰石石膏湿法脱硫计算
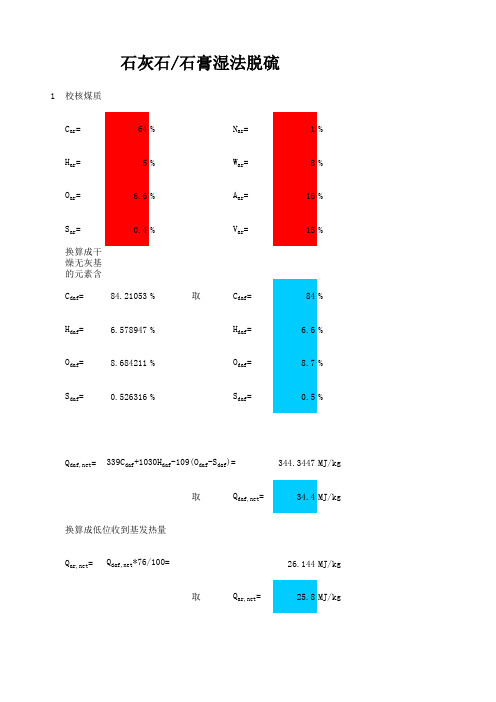
2S Y *106 = Qs
取
CSO2=
851.0638 mg/m³ 852 mg/m³
SO2浓度的校准
基准氧含量为
CSO2,at4.6% =
CSO2,at4.6% =
C * CC CC SO2 ,at4.6%
O2 ,air O2 ,air
O2 ,4.6% O2 ,6%
931.52 mg/m³ 取
CSO2,at4.6% =
mgypsum=
1466.4 kg/h
取
mgypsum=
1466 kg/h
mwater=mfrom,absorbor-mgypsum=
9814 kg/h
Vfrom,absorbor=
m from,absorbor
=
s
取
Vfrom,absorbor=
10.45412 m³/h 10.45 m³/h
18 石灰石浆液供给
mhydrocyclone,underflow s,hydrocyclone,underflow
=
2400 kg/h 1.721664 m³/h
取
Vhydrocyclone,underflow=
1.72 m³/h
17.5 吸收塔来石膏浆液计算
mfrom,absorbor=mhydrocyclone,underflow+mhydeocyclone,overfloe
0.077
mwater,vapourised=
21200 kg/h
V m water,saturation
water,vapourised water,saturation
=
取
Vwater,saturation=
石灰石-石膏湿法脱硫系统的设计计算.

石灰石-石膏湿法脱硫系统设计(内部资料)编制:xxxxx环境保护有限公司2014年8月1.石灰石-石膏法主要特点(1)脱硫效率高,脱硫后烟气中二氧化硫、烟尘大大减少,脱硫效率高达95%以上。
(2)技术成熟,运行可靠性高。
国外火电厂湿法脱硫装置的投资效率一般可达98%以上,特别是新建的大机组采用湿法脱硫工艺,使用寿命长,可取得良好的投资效益。
(3)对燃料变化的适应范围宽,煤种适应性强。
无论是含硫量大于3%的高硫燃料,还是含硫量小于1%的低硫燃料,湿法脱硫工艺都能适应。
(4)吸收剂资源丰富,价格便宜。
石灰石资源丰富,分布很广,价格也比其它吸收剂便宜。
(5)脱硫副产物便于综合利用。
副产物石膏的纯度可达到90%,是很好的建材原料。
(6)技术进步快。
近年来国外对石灰石-石膏湿法工艺进行了深入的研究与不断改进,可望使该工艺占地面积较大、造价较高的问题逐步得到妥善解决。
(7)占地面积大,一次性建设投资相对较大。
2.反应原理(1)吸收剂的反应购买回来石灰石粉(CaCO3)由石灰石粉仓投加到制浆池,石灰石粉与水结合生成脱硫浆液。
(2)吸收反应烟气与喷嘴喷出的循环浆液在吸收塔内有效接触,循环浆液吸收大部分SO2,反应如下:SO2(气)+H2O→H2SO3(吸收)H2SO3→H+ +HSO3-H+ +CaCO3→ Ca2+ +HCO3-(溶解)Ca2+ +HSO3-+2H2O→ CaSO3·2H2O+H+ (结晶)H+ +HCO3-→H2CO3(中和)H2CO3→CO2+H2O总反应式:SO2+CaCO3+2H2O→CaSO3·2H2O+CO2(3)氧化反应一部分HSO3-在吸收塔喷淋区被烟气中的氧所氧化,其它的HSO3-在反应池中被氧化空气完全氧化并结晶,反应如下:CaSO3+1/2O2→CaSO4(氧化)CaSO4+2H2O→CaSO4·2H2O(结晶)(4)其他污染物烟气中的其他污染物如SO 3、Cl -、F -和尘都被循环浆液吸收和捕集。
电厂脱硫石灰石用量计算公式
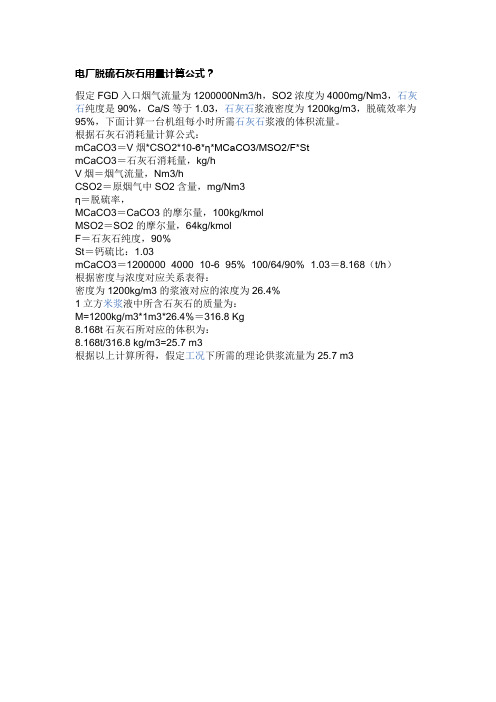
电厂脱硫石灰石用量计算公式?
假定FGD入口烟气流量为1200000Nm3/h,SO2浓度为4000mg/Nm3,石灰石纯度是90%,Ca/S等于1.03,石灰石浆液密度为1200kg/m3,脱硫效率为95%,下面计算一台机组每小时所需石灰石浆液的体积流量。
根据石灰石消耗量计算公式:
mCaCO3=V烟*CSO2*10-6*η*MCaCO3/MSO2/F*St
mCaCO3=石灰石消耗量,kg/h
V烟=烟气流量,Nm3/h
CSO2=原烟气中SO2含量,mg/Nm3
η=脱硫率,
MCaCO3=CaCO3的摩尔量,100kg/kmol
MSO2=SO2的摩尔量,64kg/kmol
F=石灰石纯度,90%
St=钙硫比:1.03
mCaCO3=1200000×4000×10-6×95%×100/64/90%×1.03=8.168(t/h)
根据密度与浓度对应关系表得:
密度为1200kg/m3的浆液对应的浓度为26.4%
1立方米浆液中所含石灰石的质量为:
M=1200kg/m3*1m3*26.4%=316.8 Kg
8.168t石灰石所对应的体积为:
8.168t/316.8 kg/m3=25.7 m3
根据以上计算所得,假定工况下所需的理论供浆流量为25.7 m3。
石灰石湿法脱硫浆液密度控制范围

石灰石湿法脱硫工艺是一种常用的烟气脱硫方法,其脱硫效率高、操作稳定、设备耐腐蚀等特点使其成为工业上广泛应用的脱硫技术之一。
在石灰石湿法脱硫中,脱硫浆液密度是一个重要的操作参数,对保证脱硫效率、减少能耗、延长设备寿命具有重要作用。
本篇文章将围绕石灰石湿法脱硫浆液密度控制范围展开详细的讨论。
一、脱硫工艺概述石灰石湿法脱硫是将石灰石石灰化后与烟气中的二氧化硫进行化学反应,生成硫酸钙或碳酸钙,并将其分离出烟气,从而达到脱硫的目的。
其脱硫过程可以分为石灰石石灰化、吸收反应、浆液处理等几个步骤。
在整个脱硫过程中,脱硫浆液密度是一个需要被精确控制的操作参数。
二、脱硫浆液密度的作用1. 影响脱硫效率:脱硫反应的进行需要一定的时间和一定的条件,而脱硫浆液的密度会影响反应的进行速率,进而影响脱硫效率。
2. 影响设备运行稳定性:脱硫塔内的浆液密度过高或过低都会影响设备的运行稳定性,甚至导致设备堵塞或浆液泵的运行不稳定。
3. 影响原料消耗:脱硫时消耗的原料主要是石灰石,而脱硫浆液密度的不合适会导致原料的浪费,增加脱硫成本。
三、脱硫浆液密度的控制范围1. 过高的浆液密度:当脱硫浆液密度过高时,会导致吸收塔内的浆液循环困难,甚至发生黏结与结垢,影响脱硫效率。
应控制脱硫浆液的密度不得高于1.35g/cm³。
2. 过低的浆液密度:脱硫浆液密度过低将导致溶液中的固体物质质量分数下降,反应物含量下降,降低脱硫效果,还将影响设备的正常运行。
脱硫浆液密度不应低于1.15g/cm³。
四、脱硫浆液密度控制的方法1. 控制石灰石浆液比例:通过调节石灰石与水的比例,来控制脱硫浆液的密度。
一般来说,增加水量可以降低密度,而增加石灰石的用量可以提高密度。
2. 合理控制搅拌时间:在制备脱硫浆液过程中,通过合理的搅拌时间可以保证悬浮在水中的石灰石颗粒均匀分散,从而影响脱硫浆液的密度。
3. 控制配料温度:在配料时控制水温和石灰石温度,可以影响脱硫浆液的密度。
脱硫系统设计-石灰石 - 石膏湿法脱硫

脱硫系统设计---- 石灰石 - 石膏湿法脱硫1 脱硫系统设计的初始条件在进行脱硫系统设计时,所需要的初始条件一般有以下几个:(1)处理烟气量,单位:m3/h或Nm3/h;(2)进气温度,单位:℃;(3)SO2初始浓度,单位:mg/m3或mg/Nm3;(4)SO2排放浓度, 单位:mg/m3或mg/Nm3;2 初始条件参数的确定2.1 处理风量的确定处理烟气量的大小是设计脱硫系统的关键,一般处理烟气量由业主方给出或从除尘器尾部引风机风量大小去确定。
处理风量还存在标况状态(Nm3/h)和工况状态(m3/h)的换算,换算采用理想气体状态方程:PV = nRT(P、n、R均为定值)V1/T1=V2/T2V1: mg/Nm3,T1:273K; V2: mg/m3,T2:t+273K(t为进气温度);怀化骏泰提供的是工况烟气量是300000m3/h,烟气温度150℃,经上述公式转换得出标况烟气量193600 Nm3/h(液气比计算用标况烟气量)2.2 进气温度的确定进气温度为经过除尘后进入脱硫塔的烟气温度值,进气温度大小关系到脱硫系统烟气量的换算和初始SO2浓度换算。
2.3 SO2初始浓度的确定SO2初始浓度一般由业主方给出,并且由此计算脱硫系统中各项设备参数,也是系统选择液气比的重要依据。
SO2初始量计算公式如下:S+O2→SO232 64C SO2=2×B×S ar/100×ηso2/100×109C SO2-SO2初始量,mg; B-锅炉BMCR负荷时的燃煤量,t/h;S ar-燃料的含S率,%;ηso2-煤中S变成SO2的转化率,%,一般取0.85;怀化骏泰提供的是4000 mg/Nm32.4 SO2排放浓度的确定一般根据所在地区环保标准确定。
二氧化硫排放限值与烧煤、油、气有关,与新建或改造锅炉有关,与地区有关,设计之前需要查看当地环保排放标准。
按照国家标准,污染物排放浓度需按公式折算为基准氧含量排放浓度,所以实测的排放浓度还需要经过折算,燃煤锅炉按基准含氧量O2=6%进行折算,c = c’× (21 - O2) / (21 - O2’)式中c –大气污染物基准氧含量排放浓度 , mg/m3;c’—实测的大气污染物排放浓度, mg/m3; 38 mg/m3O2’-- 实测的含氧量 ,%; 15%O2 -- 基准含氧量 ,%; 6%计算: SO2浓度(6%O2)=38×(21-6)/(21-15)=95mg/m3,结果也是与在线监测值相符根据在线监测电脑上显示实测的大气污染物排放浓度, 实测的含氧量,我们可以自己计算出折算值.当然电脑上也给我们自动折算并且给出了折算值,但是这个值怎么来的,我们需要知道,怀化骏泰的排放浓度是100mg/ m3,折算值,不是实测值,3 脱硫系统的设计计算3.1 参数定义(1)液气比(L/G ):即单位时间内浆液喷淋量和单位时间内流经吸收塔的烟气量之比.单位为L/m3;)/3()/(h m h L 的湿烟气体积流量单位时间内吸收塔入口单位时间内浆液喷淋量液气比石灰石法液气比范围在8l/m3-25l/m3之间,一般认为12.2就可以了(液气比超过某个值后,脱硫效率的提高非常缓慢,而且提高液气比将使浆液循环泵的流量增大,增加循环泵的设备费用,塔釜的体积增大.增大脱硫塔制造成本,同时还会提高吸收塔的压降,加大增压风机的功率及设备费用)通过液气比可以计算出循环浆液量Q 循 = 12.2 × 193600 / 1000 = 2362 m3/h(2)钙硫比(Ca/S ):理论上脱除1mol 的S 需要1mol 的Ca ,但在实际反应设备中,反应条件并不处于理想状态,一般需要增加脱硫剂的量来保证一定的脱硫效率,因此引入了Ca/S 的概念。
脱硫石灰石耗量分析

湿法脱硫系统石灰石耗量分析经过“十一五”的大力推进,烟气脱硫技术已在我国活力发电行业得到了广泛的应用,对于脱硫系统的研究也日渐深入细致,在“十二五”大力倡导节能减排的背景下,通过运行优化,实现脱硫系统的经济运行,就成了目前的一个重要研究领域I 。
石灰石是脱硫反应的吸收剂,耗量较大,是脱硫系统运行成本的主要组成部分,石灰石耗量与设计值发生较大偏差,不仅会直接造成脱硫运行成本的攀升,而且也会对吸收塔浆液品质、脱水系统运行工况等产生一定影响,因此石灰石耗量分析也就成为了石灰石.石膏脱硫系统节能优化运行的要重点研究的问题。
为了分析实际运行中石灰石耗量偏差情况,找出影响石灰石消耗量的主要因素,进而提高石灰石在脱硫反应中的利用率,降低运行成本,因此在某2×600 Mw 机组配套脱硫系统上进行了石灰石耗量分析的相关试验。
1 石灰石耗量计算理论上,石灰石中所含的有效脱硫成分,即CaCO,在脱硫反应中与烟气中的SO:按照理论钙硫比发生反应,因此理论石灰石耗量是指脱硫系统在设计Ca/S比条件下,按照脱除SO2量计算得出的所需石灰石量。
计算公式如下:M~:—Qsnd~(C—sl-Cs2)××⋯ l000000 64式中:Mcaco3——理论石灰石耗量,kg/ll;Q5 d——标干烟气量, Nm ha(6%02); csl一一原烟气s02浓度,mg/Nm (6%02);Cs2一一净烟气SO2浓度,mg/Nm (6%O2);收稿日期:2012.12-10戴新(1970一),男,高级工程师。
丰镇,012100n一一石灰石纯度,试验期间为89.4%;——设计钙硫比, 1.03。
实际脱硫反应中,由于石灰石反应活性、杂质含量等因素影响,石灰石实际耗量会与理论值存在一定偏差,通常实际石灰石消耗量是通过实际脱硫反应中投加到吸收塔内的石灰石浆液量和浆液密度计算得出,计算公式如下:M c 川式中:^ aCO3——实际石灰石耗量,kg/h; P ——石灰石密度,P =2.6 g/cm ;P ——石灰石浆液密度,g/cm ;——每小时石灰石浆液量,m /h。
脱硫用石灰石粉标准
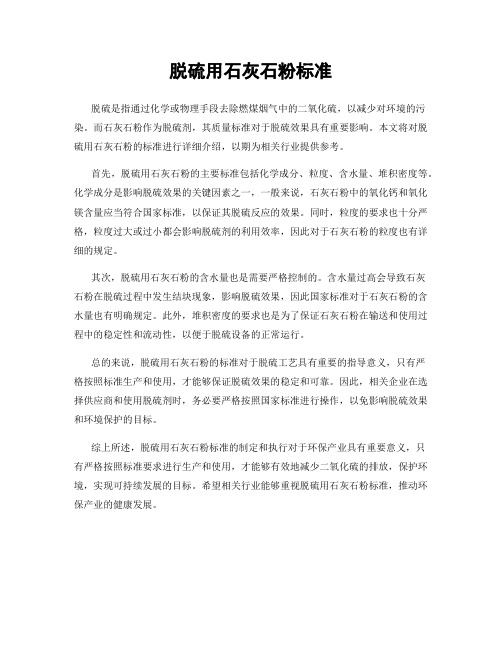
脱硫用石灰石粉标准
脱硫是指通过化学或物理手段去除燃煤烟气中的二氧化硫,以减少对环境的污染。
而石灰石粉作为脱硫剂,其质量标准对于脱硫效果具有重要影响。
本文将对脱硫用石灰石粉的标准进行详细介绍,以期为相关行业提供参考。
首先,脱硫用石灰石粉的主要标准包括化学成分、粒度、含水量、堆积密度等。
化学成分是影响脱硫效果的关键因素之一,一般来说,石灰石粉中的氧化钙和氧化镁含量应当符合国家标准,以保证其脱硫反应的效果。
同时,粒度的要求也十分严格,粒度过大或过小都会影响脱硫剂的利用效率,因此对于石灰石粉的粒度也有详细的规定。
其次,脱硫用石灰石粉的含水量也是需要严格控制的。
含水量过高会导致石灰
石粉在脱硫过程中发生结块现象,影响脱硫效果,因此国家标准对于石灰石粉的含水量也有明确规定。
此外,堆积密度的要求也是为了保证石灰石粉在输送和使用过程中的稳定性和流动性,以便于脱硫设备的正常运行。
总的来说,脱硫用石灰石粉的标准对于脱硫工艺具有重要的指导意义,只有严
格按照标准生产和使用,才能够保证脱硫效果的稳定和可靠。
因此,相关企业在选择供应商和使用脱硫剂时,务必要严格按照国家标准进行操作,以免影响脱硫效果和环境保护的目标。
综上所述,脱硫用石灰石粉标准的制定和执行对于环保产业具有重要意义,只
有严格按照标准要求进行生产和使用,才能够有效地减少二氧化硫的排放,保护环境,实现可持续发展的目标。
希望相关行业能够重视脱硫用石灰石粉标准,推动环保产业的健康发展。
脱硝尿素脱硫石灰石耗量简易计算方法

输入数据
序号
参数
单位
数值
备注
1 干标况烟气量 Nm3/h 2 NOX初始浓度 mg/Nm3
3
NOX脱除率
%
4
NSR氨氮比
5 烟气中氧含量 %
1000000 200 80 2 7
标况、干基、6%O2 标况、干基、6%O2
SNCR脱硝一般设计12
实际氧量
计算数据
1 NOX折算浓度 mg/Nm3
Nm3/h mg/Nm3
%
1000000 200 80
标况、干基、6%O2 标况、干基、6%O2
氨逃逸
ppm
3
设计一般不大于3
烟气中含氧量 %
7
实际氧量
计算数据
烟气中NOx含量 mg/Nm3
187
烟气中NO含量 mg/Nm3
116
烟气中NO2含量 mg/Nm3
9
实际氧,干基 实际氧,干基 实际氧,干基
200
煤含硫量
%
0.5
SO2去除效率
Ca/S 石灰石纯度 (CaCO3) 石灰石浆液密度
%
% kg/m3
95 1.05 95 1250
设计一般为1.02-1.05
石膏含水率
%
15
石膏纯度
%
90
计算数据
S02去除量 石灰石消耗量
kg/h kg/h
1710 2953
液消耗量 m3/h
12
单台锅炉,以煤量计算
石膏产量
kg/h
6007 单台锅炉,以煤量计算
注:绿色区域为输入值,红色区域为输出值
S02排放浓度 mg/Nm3
100
(整理)脱硫石灰石耗量分析
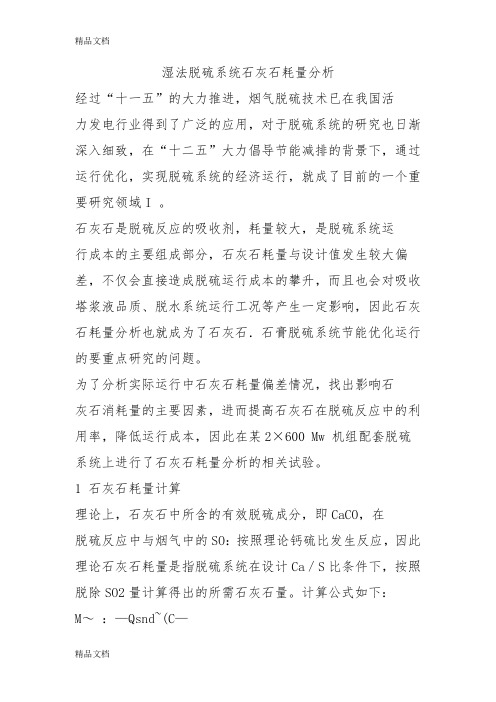
湿法脱硫系统石灰石耗量分析经过“十一五”的大力推进,烟气脱硫技术已在我国活力发电行业得到了广泛的应用,对于脱硫系统的研究也日渐深入细致,在“十二五”大力倡导节能减排的背景下,通过运行优化,实现脱硫系统的经济运行,就成了目前的一个重要研究领域I 。
石灰石是脱硫反应的吸收剂,耗量较大,是脱硫系统运行成本的主要组成部分,石灰石耗量与设计值发生较大偏差,不仅会直接造成脱硫运行成本的攀升,而且也会对吸收塔浆液品质、脱水系统运行工况等产生一定影响,因此石灰石耗量分析也就成为了石灰石.石膏脱硫系统节能优化运行的要重点研究的问题。
为了分析实际运行中石灰石耗量偏差情况,找出影响石灰石消耗量的主要因素,进而提高石灰石在脱硫反应中的利用率,降低运行成本,因此在某2×600 Mw 机组配套脱硫系统上进行了石灰石耗量分析的相关试验。
1 石灰石耗量计算理论上,石灰石中所含的有效脱硫成分,即CaCO,在脱硫反应中与烟气中的SO:按照理论钙硫比发生反应,因此理论石灰石耗量是指脱硫系统在设计Ca/S比条件下,按照脱除SO2量计算得出的所需石灰石量。
计算公式如下:M~:—Qsnd~(C—sl-Cs2)××⋯ l000000 64式中:Mcaco3——理论石灰石耗量,kg/ll;Q5 d——标干烟气量, Nm ha(6%02); csl一一原烟气s02浓度,mg/Nm (6%02);Cs2一一净烟气SO2浓度,mg/Nm (6%O2);收稿日期:2012.12-10戴新(1970一),男,高级工程师。
丰镇,012100n一一石灰石纯度,试验期间为89.4%;——设计钙硫比, 1.03。
实际脱硫反应中,由于石灰石反应活性、杂质含量等因素影响,石灰石实际耗量会与理论值存在一定偏差,通常实际石灰石消耗量是通过实际脱硫反应中投加到吸收塔内的石灰石浆液量和浆液密度计算得出,计算公式如下:M c 川式中:^ aCO3——实际石灰石耗量,kg/h; P ——石灰石密度,P =2.6 g/cm ;P ——石灰石浆液密度,g/cm ;——每小时石灰石浆液量,m /h。
脱硫系统石灰石浆液流量实例计算

某电厂的一台300MW机组,其锅炉脱硫装置的入口烟气流量为1070659Nm 3/h,进口烟气氧量为6%,SO 2浓度为1985mg/Nm 3,石灰石纯度是92%,Ca/S等于1.03,石灰石浆液密度为1230kg/m 3,脱硫效率为91%,试计算该脱硫装置每小时所需石灰石浆液的质量流量和体积流量各是多少? 解:根据石灰石消耗量计算公式:332226,10CaCO CaCO RG SO rawgas SO R t SO M m V c F M η−=××××÷×S式中:3CaCO m =石灰石消耗量,kg/hRG V =烟气流量:1070659Nm 3/h2,SO rawgas c =原烟气中SO 2含量:1985mg/Nm32SO η=脱硫率,91%3CaCO M =CaCO 3的摩尔量,100.09kg/kmol2SO M =SO 2的摩尔量,64.06kg/kmolR F =石灰石纯度,92%S t =钙硫比:1.0336100107065919851091%92% 1.0364−=××××÷×CaCO m=2125.2581×0.91×1.5625÷0.92×1.03=3.3832(t/h)根据密度与含固量的换算公式1211100%11S S ρωρ−=×−式中:ω=质量分数(含固量),%1S ρ=石灰石的浆液密度,kg/m 32S ρ=石灰石的密度,取2.71×103 kg/m 311 1.23100%11 2.71ω−=×− =10.813100%10.369−×−=0.2964×100%=29.64(%)根据石灰石浆液的质量流量计算公式: 33CaCO suspension CaCO m m c =式中:suspension m =石灰石浆液质量流量,t/h 3CaCO m =石灰石消耗量,t/h 3CaCO c =石灰石浆液的含固量,% 3.383229.64%= suspension m=11.4143(t/h)石灰石浆液的体积流量计算公式 suspension suspension suspensionm V ρ=式中:suspension V =石灰石浆液体积流量,m 3/h suspension m =石灰石浆液质量流量,kg/h suspension ρ=石灰石浆液的密度,kg/m 33311.4143101.2310×=× suspension V=9.2799(m 3/h)。
脱硫系统采用石灰石粉经济性分析

采用石灰石粉作为吸收剂的经济性分析张江1. 情况简介我公司脱硫系统吸收剂原设计采用直径小于20mm的石灰石,经湿式球磨机研磨达到250目通过率大于90%、含固率25%的石灰石浆液。
两座吸收塔最大石灰石消耗量为10.3t/h,脱硫系统设计含硫量为0.67%,实际燃用煤种含硫量为0.52%,实际双塔消耗石灰石量为110-120t/天。
设1座混凝土石灰石储仓,储仓的总容量按2台锅炉在BMCR工况运行3天(日利用20 h 计)的石灰石耗量设计,有效容积为460m3。
经调研:大唐盘电公司因石灰石质量较差曾发生影响脱硫效率的问题,已将吸收剂改为石灰石粉,外购石灰石粉采取罐车运输,使用事故浆液箱作为石灰石粉混合箱,增加2台浆液输送泵实现向石灰石浆液箱供浆;大唐盘电公司原湿式球磨机浆液制备系统处于备用保养状态,计划占用一座灰库作为石灰石粉事故储仓。
国华浙能公司脱硫系统为干式球磨机石灰石粉制备系统,单台吸收塔区域设计有日石灰石粉储仓及2台浆液输送泵,石灰石粉运输采取罐车装载,满足脱硫系统运行需要。
2. 系统改造初步方案在现有石灰石料仓西侧增设石灰石粉仓,底部设浆液箱及2台浆液输送泵。
按2台锅炉在BMCR工况运行3天(日利用20 h 计)的石灰石粉耗量设计,两座吸收塔最大石灰石消耗量为10.3t/h,石灰石粉堆积密度按1.1 t/ m3计算,需要增加容积560m3石灰石粉仓(底部设置气化装置)、增加两台给料机、粉仓顶部设置布袋除尘器。
外购的石灰石粉由封闭式罐车运输,使用罐车自带气源将石灰石粉送入石灰石粉仓。
通过粉仓底部电动给料机、落粉管进入浆液箱,按加水搅拌后,通过浆液循环泵输送至浆液供应箱,供脱硫系统运行消耗。
电动给料机出力按15t/h考虑,浆液混配箱有效容积需达到75 m3,混配箱实际容积需达到90 m3,(直径5.4米,高4米),两座吸收塔最大石灰石消耗量为10.3t/h,按20h计算,需配置浆液206吨,每日混配箱系统需运行14小时,(目前实际日消耗石灰石120吨,每日混配箱系统需运行8小时。
烟气脱硫石灰石粉国标

烟气脱硫石灰石粉国标全文共四篇示例,供读者参考第一篇示例:烟气脱硫石灰石粉是一种用于烟气脱硫的环保材料,其国家标准在我国环保产业发展中起着重要作用。
为了更好地了解烟气脱硫石灰石粉国标的相关内容,我们有必要对其进行详细的介绍。
一、烟气脱硫石灰石粉的定义烟气脱硫石灰石粉是指将石灰石煅烧或熟料石灰石粉碎后,通过搅拌、磨砂机等特殊工艺制得的石灰石粉。
该产品主要用于烟气脱硫,是一种环保材料。
烟气脱硫石灰石粉的国标为GB/T 19001-2016《烟气脱硫石灰石粉》。
该标准规定了烟气脱硫石灰石粉的技术要求、试验方法、检验规则、标志、包装、运输和贮存等内容,是我国对该产品的标准化要求。
根据国家标准,烟气脱硫石灰石粉的技术要求主要包括以下内容:1.化学成分:烟气脱硫石灰石粉的主要成分为氧化钙和氧化镁,其含量应符合标准规定,以确保产品的质量。
2.物理性能:烟气脱硫石灰石粉的颗粒大小、比表面积、堆积密度等物理性能应符合标准规定,以确保产品在脱硫过程中的有效性。
烟气脱硫石灰石粉主要用于火电厂、水泥厂、钢铁厂等工业企业的烟气脱硫设备中,通过喷射或浆液混合的方式,将石灰石粉与烟气中的氧化硫等有害气体进行化学反应,从而达到脱硫的目的。
烟气脱硫石灰石粉可以有效降低烟气中的二氧化硫排放,减少大气污染,保护环境。
该产品还可以提高工业生产的效率,降低能源消耗和生产成本,促进企业的可持续发展。
烟气脱硫石灰石粉国标的制定为我国环保产业的发展提供了重要的支持,为石灰石粉行业标准化、规范化提供了有效的指导。
我们有信心相信,在政府、企业和社会的共同努力下,烟气脱硫石灰石粉将在环保领域取得更大的成就,为我国环境保护事业作出更大的贡献。
【结束】第二篇示例:烟气脱硫石灰石粉是一种用于烟气脱硫的材料,是石灰石经过加工而得到的一种粉状物质。
在煤热电厂、钢铁厂等工业生产过程中,燃烧煤炭会产生二氧化硫等有害气体,烟气脱硫就是通过将石灰石粉喷入烟气中,与二氧化硫发生反应,从而达到减少大气污染的目的。
电厂脱硫石灰石用量计算公式
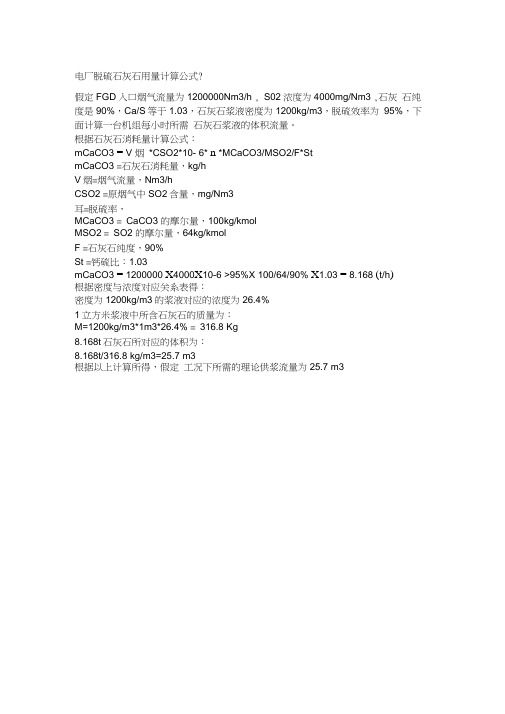
电厂脱硫石灰石用量计算公式?
假定FGD入口烟气流量为1200000Nm3/h , S02浓度为4000mg/Nm3 ,石灰石纯度是90%,Ca/S等于1.03,石灰石浆液密度为1200kg/m3,脱硫效率为95%,下面计算一台机组每小时所需石灰石浆液的体积流量。
根据石灰石消耗量计算公式:
mCaCO3 = V 烟*CSO2*10- 6* n *MCaCO3/MSO2/F*St
mCaCO3 =石灰石消耗量,kg/h
V烟=烟气流量,Nm3/h
CSO2 =原烟气中SO2含量,mg/Nm3
耳=脱硫率,
MCaCO3 = CaCO3 的摩尔量,100kg/kmol
MSO2 = SO2 的摩尔量,64kg/kmol
F =石灰石纯度,90%
St =钙硫比:1.03
mCaCO3 = 1200000 X4000X10-6 >95%X 100/64/90% X1.03 = 8.168 (t/h)
根据密度与浓度对应关系表得:
密度为1200kg/m3的浆液对应的浓度为26.4%
1立方米浆液中所含石灰石的质量为:
M=1200kg/m3*1m3*26.4% = 316.8 Kg
8.168t石灰石所对应的体积为:
8.168t/316.8 kg/m3=25.7 m3
根据以上计算所得,假定工况下所需的理论供浆流量为25.7 m3。
电厂脱硫用石灰石标准

电厂脱硫用石灰石标准电厂脱硫是指利用石灰石等原料制备石灰乳,通过喷射或浆液法将石灰乳喷入烟气中,与烟气中的二氧化硫发生化学反应,将二氧化硫转化为硫酸盐,达到减少大气污染的目的。
在电厂脱硫工艺中,石灰石的质量和标准对脱硫效果起着至关重要的作用。
本文将介绍电厂脱硫用石灰石的标准及相关要求。
首先,电厂脱硫用石灰石应符合国家相关标准,包括石灰石的化学成分、颗粒大小、含水量、堆积密度等指标。
其中,化学成分是石灰石的重要特征之一,主要包括钙含量、镁含量、硅含量等。
合格的石灰石应具有较高的钙含量,低的镁含量和硅含量,以保证脱硫反应的高效进行。
此外,石灰石的颗粒大小和含水量也直接影响着脱硫工艺的稳定性和效果,因此在选用石灰石时需严格按照标准要求进行筛选和检测。
其次,电厂脱硫用石灰石的标准还包括了石灰石的采购、储存和使用等方面的要求。
在采购环节,应选择具有生产许可证和质量合格证明的正规生产厂家,避免购买劣质产品影响脱硫效果。
在储存和使用过程中,石灰石应储存在干燥通风的库房内,避免受潮结块影响使用效果。
同时,在投入脱硫系统前,需对石灰石进行颗粒破碎和筛分,确保颗粒大小符合要求,以保证脱硫工艺的稳定运行。
最后,电厂脱硫用石灰石的标准也涉及了脱硫工艺中的操作和管理要求。
在脱硫系统运行中,需定期对石灰石投加量、浆液浓度、喷射均匀性等进行监测和调整,保证脱硫效果达到设计要求。
同时,对石灰石的消耗量和脱硫效率进行统计分析,及时发现和解决问题,确保脱硫系统的稳定运行。
总的来说,电厂脱硫用石灰石标准的制定和执行对于保障电厂脱硫工艺的稳定运行和脱硫效果的达标具有重要意义。
只有严格按照标准要求选择、采购、储存和使用石灰石,才能确保脱硫工艺的高效、稳定运行,减少大气污染,保护环境。
石灰石-石膏湿法脱硫化学分析

c = 样品经清洗和40℃干燥后的玻璃坩埚重量(g)
(c – b)
含固量% = ------------------- ·100%
a
注:砂芯坩锅用毕即用1:1盐酸煮洗。酸洗后的坩埚一定要清洗
干净后方可再次使用,避免因酸残留在坩埚内与石灰、石膏内的
CaCO3反应,影响后续试验的准确性。检验坩埚是否清洗干净的
3、灰化,灼烧。
用低温烘去水分,不要使滤纸着火,反复灼烧时间
应控制15分钟左右。
下一节
2021/3/27
CHENLI
14
重量分析法
(1)重量分析法的原理 (2)重量分析法的过程和对沉淀的要求 (3)影响沉淀溶解度的因素 (4)影响沉淀纯度的因素 (5)沉淀条件的选择
2021/3/27
CHENLI
2021/3/27
CHENLI
11
4.1 石膏和浆液中硫酸盐(SO3)含量分析
高氯酸钡滴定法
亚硫酸盐被H2O2氧化,主要阳离子用离子交换树 脂除去,生成的硫酸根用高氯酸钡进行滴定,指示剂 为磺酸-Ⅲ,溶液颜色从紫色变为淡篮色。测定值为总 硫酸盐,包括亚硫酸盐转化的,亚硫酸盐SO2用碘定量 法测定,并在转化为SO3后减去。
2021/3/27
CHENLI
13
试验过程中的注意点
重量分析法的注意点:
1、获取大的晶形沉淀,减小沉淀开始时的硫酸钡相对 过饱和度。总得可归纳为:热、稀,慢,不断搅拌, 过量的沉淀剂(过量20~30%)及陈化。
2、过滤洗涤中防止样品损失。
如选用慢速定量滤纸以及在洗涤沉淀时,可用带橡
皮管的玻棒擦洗烧杯,后用热蒸馏水洗涤至无氯离子 为止。
尽可能获得颗粒大的晶形沉淀,它的表面积小,吸附杂质少,易于过滤 和洗涤。
脱硫石灰石浆液、石膏成分分析法

1 吸收塔(石膏)浆液分析对于湿法脱硫而言,脱硫反应存在最佳反应pH 值。
同时为防止系统结垢,应控制浆液pH 和密度在指定范围。
氯离子含量是浆液吸收倍率的反应,同时也是防止系统腐蚀的重要控制指标。
1.1 pH打开pH 测定仪预热半小时,用标准缓冲液进行定位,清洗电极后测定浆液pH ,记录pH 值和浆液温度。
1.2 密度洗净并恒重比重瓶,带塞称量。
用新煮沸并冷却至20℃的蒸馏水注满比重瓶,不得带入气泡,装好后立即浸入20±0.1℃的恒温水浴中,20min 后取出,用滤纸除去溢出毛细管的水,擦干后立即称量。
将比重瓶里的水倒出,洗净、干燥、称量。
以试样代替水测试。
021ρρ⨯=m m 式中:ρ-密度,g/cm 3ρ0-在20℃时蒸馏水的密度,g/cm 3m 1-充满比重瓶所需试样的质量,gm 2-充满比重瓶所需水的质量,g1.3 亚硫酸根含量在250ml 三角烧瓶中加入1ml0.1mol/LI 2标准溶液和约10ml 去离子水,吸取10ml 浆液,加入其中。
滴加1+1的硫酸,混合均匀,在暗处静置5分钟。
再加入100ml 去离子水,用0.1N 硫代硫酸钠标准溶液滴定至溶液为淡黄色,加入2ml 淀粉溶液,再继续滴定至蓝色消失。
()3221112100080V C V C V X ⨯⨯⨯⨯-⨯= 式中:X 1-浆液中亚硫酸根含量,mg/LV 1-碘标准溶液加入量,mlC 1-碘标准溶液浓度,mol/LV 2-硫代硫酸钠标准溶液耗量,mlC 2-硫代硫酸钠标准溶液浓度,mol/LV 3-吸取浆液体积,ml1.4 碳酸根含量取10ml 浆液,加入1ml30%的双氧水,2分钟后加入10ml1.0mol/LHCl 标准溶液和20ml 去离子水,在50~70℃放置约5min 。
滴加2滴酚酞指示剂,用1.0NNaOH 标准溶液滴定至溶液由无色刚好变为红色终点。
()3221121000100V C V C V X ⨯⨯⨯⨯-⨯= 式中:X -浆液中碳酸盐含量,mg/mlV 1-HCl 标准溶液加入量,mlC 1-HCl 标准溶液浓度,mol/LV 2-NaOH 标准溶液加入量,mlC 2-NaOH 标准溶液浓度,mol/LV 3-吸取浆液体积,ml1.5 氯离子含量取100ml 试样至于250ml 锥形瓶中,调整pH 至酚酞指示剂红色刚好消失,加入1ml 铬酸钾指示剂,用硝酸银标准溶液滴定至橙色,记录硝酸银标准溶液的耗量a 。