铝合金薄壁壳体焊接件缺陷分析与控制
铝及铝合金焊接常见缺陷和防止措施12招!

铝及铝合金焊接常见缺陷和防止措施12招!铝及铝合金焊丝的选择主要根据母材的种类,对接头抗裂性能、力学性能及耐蚀性等方面的要求综合考虑。
有时当某项成为主要矛盾时,则选择焊丝就着重从解决这个主要矛盾入手,兼顾其它方面要求。
一般情况下,焊接铝及铝合金都采用与母材成分相同或相近牌号的焊丝,这样可以获得较好的耐蚀性;但焊接热裂倾向大的热处理强化铝合金时,选择焊丝主要从解决抗裂性入手,这时焊丝的成分与母材的差别就很大。
常见缺陷(焊接问题)及防止措施1、烧穿产生原因:a、热输入量过大;b、坡口加工不当,焊件装配间隙过大;c、点固焊时焊点间距过大,焊接过程中产生较大的变形量。
防止措施:a、适当减小焊接电流、电弧电压,提高焊接速度;b、大钝边尺寸,减小根部间隙;c、适当减小点固焊时焊点间距。
2、气孔产生原因:a、母材或焊丝上有油、锈、污、垢等;b、焊接场地空气流动大,不利于气体保护;c、焊接电弧过长,降低气体保护效果;d、喷嘴与工件距离过大,气体保护效果降低;e、焊接参数选择不当;f、重复起弧处产生气孔;g、保护气体纯度低,气体保护效果差;h、周围环境空气湿度大。
防止措施:a、焊前仔细清理焊丝、焊件表面的油、污、锈、垢和氧化膜,采用含脱氧剂较高的焊丝;b、合理选择焊接场所;c、适当减小电弧长度;d、保持喷嘴与焊件之间的合理距离范围;e、尽量选择较粗的焊丝,同时增加工件坡口的钝边厚度,一方面可以允许使用大电流,微信公众号:焊王,另一方面也使焊缝金属中焊丝比例下降,这对降低气孔率是行之有效的;f、尽量不要在同一部位重复起弧,需要重复起弧时要对起弧处进行打磨或刮除;一道焊缝一旦起弧要尽量焊长些,不要随意断弧,以减少接头量,在接头处需要有一定焊缝重叠区;g、换保护气体;h、检查气流大小;i、预热母材;j、检查是否有漏气现象和气管损坏现象;k、在空气湿度较低时焊接,或采用加热系统。
3、电弧不稳产生原因:电源线连接、污物或者有风。
铝合金焊接常见缺陷及解决措施

铝合金焊接常见缺陷及解决措施一、强的氧化能力铝与氧的亲和力很强,在空气中极易与氧结合生成致密而结实的AL2O3薄膜,厚度约为0.1μm,熔点高达2050℃,远远超过铝及铝合金的熔点,而且密度很大,约为铝的1.4倍。
在焊接过程中,氧化铝薄膜会阻碍金属之间的良好结合,并易造成夹渣。
氧化膜还会吸附水分,焊接时会促使焊缝生成气孔。
这些缺陷,都会降低焊接接头的性能。
为了保证焊接质量,焊前必须严格清理焊件表面的氧化物,并防止在焊接过程中再氧化,对熔化金属和处于高温下的金属进行有效的保护,这是铝及铝合金焊接的一个重要特点。
具体的保护措施是:1、焊前用机械或化学方法清除工件坡口及周围部分和焊丝表面的氧化物;2、焊接过程中要采用合格的保护气体进行保护;3、在气焊时,采用熔剂,在焊接过程中不断用焊丝挑破熔池表面的氧化膜。
二、铝的热导率和比热大,导热快尽管铝及铝合金的熔点远比钢低,但是铝及铝合金的导热系数、比热容都很大,比钢大一倍多,在焊接过程中大量的热能被迅速传导到基体金属内部,为了获得高质量的焊接接头,必须采用能量集中、功率大的热源,有时需采用预热等工艺措施,才能实现熔焊过程。
三、线膨胀系数大铝及铝合金的线膨胀系数约为钢的2倍,凝固时体积收缩率达6.5%-6.6%,因此易产生焊接变形。
防止变形的有效措施是除了选择合理的工艺参数和焊接顺序外,采用适宜的焊接工装也是非常重要的,焊接薄板时尤其如此。
另外,某些铝及铝合金焊接时,在焊缝金属中形成结晶裂纹的倾向性和在热影响区形成液化裂纹的倾向性均较大,往往由于过大的内应力而在脆性温度区间内产生热裂纹。
这是铝合金,尤其是高强铝合金焊接时最常见的严重缺陷之一。
在实际焊接现场中防止这类裂纹的措施主要是改进接头设计,选择合理的焊接工艺参数和焊接顺序,采用适应母材特点的焊接填充材料等。
四、容易形成气孔焊接接头中的气孔是铝及铝合金焊接时极易产生的缺陷,尤其是纯铝和防锈铝的焊接。
氢是铝及铝合金焊接时产生气孔的主要原因,这已为实践所证明。
铝合金板焊缝表面缺陷原因分析

铝合金板焊缝表面缺陷原因分析利用光学显微镜和扫描电镜对用5B06- O合金焊丝焊接后产生的焊缝表面缺陷进行了分析;确认焊缝表面的夹杂物为MgO焊渣,其产生原因是焊接时保护气体流量不足或焊接现场环境不好造成的。
某型号舱体的贮箱壳体与连接环之间采用氦-氩混合气体保护的钨极自动氩弧焊机焊接,焊丝采用东北轻合金有限责任公司(以下简称东轻公司)生产的5B06-O(LFl4M)合金直径为2mm的线材。
在进行焊接试验时,焊缝上出现黑色和黄色的夹杂物,用户认为是焊丝存在质量问题。
东轻公司对此缺陷进行了分析研究。
1 用户焊接试验的方法焊接设备:POLYSOUDE 750PC型全自动氩弧焊机;保护气体:氦-氩混合气体;焊接用试板:2.5mm厚5A06-O铝合金板;焊丝:Φ2mm的5B06-O合金线材;环境温度:27℃;相对湿度:小于55%。
2 缺陷的组织特征2.1 缺陷的宏观特征用户对两块试板进行了焊接试验,第一块试板焊缝的宏观表面组织如图1所示,焊缝外观光滑无异物,为正常的氩弧焊焊缝。
第二块试板焊缝的宏观表面组织如图2所示,焊缝上存在大量的黄色夹杂物和少量的黑色夹杂物,夹杂物浮在焊缝表面,有的呈突起状,有的呈凹陷状。
图1 焊缝表面无夹杂物的试板图2 焊缝表面有夹杂物的试板2.2 缺陷的扫描电镜分析结果缺陷处的扫描电镜照片如图3所示。
对图3中的黑色夹杂物和黄色夹杂物分别进行了能谱成分分析,结果如图4、5。
从图4、5得知,夹杂物主要是由Mg 和O组成:黑色夹杂物中ω(Mg)=41.79%,ω(O)=36.04%;黄色夹杂物中ω(Mg)=55.89%,ω(O)=37.80%。
这说明夹杂物的产生原因是由于焊接时性质活泼的Mg元素与O元素发生反应形成MgO焊渣。
图3 扫描电镜下缺陷处形貌3 焊丝的显微组织对用户提出质量异议的焊丝进行了化学成分分析(表1)。
结果表明焊丝的化学成分符合GB/T3190-1996《变形铝及铝合金化学成分》的规定。
铝合金焊接常见缺陷的产生原因及质量控制分析

铝合金焊接常见缺陷的产生原因及质量控制分析摘要:铝合金材料在现代装备制造业中应用广泛,铝合金材料的可焊性较差,焊接过程中会出现很多缺陷,主要是气孔和裂纹较多。
分析了铝合金焊接过程中造成气孔和裂纹的因素,提出减少气孔和裂纹的质量控制措施。
关键词:铝合金;焊缝;缺陷;措施1 焊接性能简介(1)氧化能力强。
Al与O2在空气中结合生成致密的Al2O3薄膜,厚度约为0.1μm,熔点高达2050℃,密度大,在焊接过程中氧化膜会阻碍金属之间的良好结合,并且容易造成夹渣,氧化膜还会吸附水分,焊接时易生成焊缝气孔。
(2)铝的比热大,导热速度快。
因导热快,散热也快,焊接一般采用能量集中功率大的焊接热源,有时还需预热,才能获得高质量的焊接接头。
(3)线膨胀系数大。
铝及铝合金线膨胀系数大,金属凝固时体积收缩率也大,易产生焊接变形。
(4)容易形成气孔。
H2是铝及铝合金焊接时产生气孔的主要原因,H2主要来源于焊接材料(母材、焊丝、保护气体)吸附的水分。
(5)合金元素蒸发和烧损。
铝合金的某些合金元素,在高温下容易蒸发烧损,从而改变了焊缝金属的化学成份,降低了焊接接头的性能。
(6)铝及铝合金熔化时无色泽变化。
铝及铝合金焊接时,由固态转变为液态时,没有明显的颜色变化,给焊接操作带来一定困难。
2 TIG焊常见缺陷及防止措施铝及铝合金TIG焊的各种缺陷,既有与其他电弧焊相同的,也有一些是其特有的。
铝及铝合金TIG焊的焊接质量与焊前准备情况、保护气体纯度、焊接参数的正确性、电极材料的质量、操作技术的熟练程度、焊接电源等因素有关。
其常见缺陷产生原因及对策阐述如下。
2.1气孔在焊接过程中,熔池中的气体未在金属凝固前逸出,残存于焊缝中的空穴被称为气孔。
气孔是比较多见的焊接缺陷,在焊缝的各个位置都可能发现气孔。
铝合金焊接时生成气孔的气体主要是氢气,氢气主要来自电弧周围的空气,母材和焊丝表面的杂质,如油污,水分等的分解燃烧。
气孔是铝合金焊接时最容易出现的一种体积型缺陷,气孔的存在减少了焊缝的受力截面,有些针形气孔会使焊缝疏松,从而降低了接头的强度,还有就是降低了焊缝的力学性能。
铝合金焊接缺陷的分析与研究

铝合金焊接缺陷的分析与研究铝合金焊接具有密度低、耐腐蚀以及良好的导热性和导电性等特点,在机械、航空以及电子产业中都有广泛的应用。
但是,铝合金焊接也存在着裂纹和气孔等多种缺陷。
本文针对这些缺陷产生的原因进行了分析和探讨,并针对特定的缺陷提出了具体的防止对策。
在机械制造行业中,焊接加工是一种应用广泛的加工方式,它不仅强度可靠,节省材料,还能加工出其它加工方式难以完成的产品。
在焊接中,铝合金焊接具有耐腐蚀、比强度高以及良好的导热性和导电性。
这些特点使铝合金焊接在机械、电力以及轨道车辆等多个领域中得到了广泛的应用。
但是在铝合金焊接中也存在着裂纹、气孔以及咬边等各种缺陷,这对焊接产品的质量产生了严重的威胁。
本文从铝合金的性能和焊接特性出发,对铝合金焊接存在的缺陷进行分析和介绍,并针对性的提出防止对策。
铝合金的性能及其焊接特性铝合金中的铝是一种轻金属,它的密度非常小,利用它来焊接成的产品重量低,这在航天航空以及交通轨道等领域具有重要的意义。
铝合金的耐腐蚀非常好,不容易受到环境的侵蚀,同时它的比强度也高,焊接成的产品质量好。
铝合金的导电导热性能好,在低温下也能保持良好的机械性能。
目前焊接所用铝合金用的比较多的是铝锰合金和铝镁合金两类。
在航天航空等重要领域也会用到比强度和比刚度高的铝铜合金和铝锂合金。
这些铝合金主要具有以下一些焊接特性。
第一,铝合金的氧化能力特别强,在焊接过程中会生成氧化薄膜。
第二,铝合金具有高导电性和导热率,不会因局部过热产生内应力,但也因此所需能量更多。
第三,线膨胀系数和凝固体积收缩率比较大,容易形成热裂纹。
第四,焊接时铝合金没有具体的颜色变化,这给焊接者的观察工作带来困难。
第五,铝合金在高温中容易吸入气体,在焊接过程中会形成气孔。
铝合金焊接常见缺陷分析及研究因为铝合金自身存在的一些焊接特性,以及其它各种原因,在铝合金焊接中容易出现裂纹、气孔、焊缝成型不良以及咬边等多种缺陷。
下面本文将针对各个缺陷产生的原因进行分析,再提出具体的防止对策。
铝合金焊接缺陷分析及预防

铝合金焊接缺陷分析及预防铝合金焊接缺陷分析及预防1、焊缝尺寸不符合要求主要是指焊缝宽窄不一、高低不平、余高不足或过高等。
焊缝尺寸过小会降低焊接接头的强度;尺寸过大将增加结构的应力和变形,造成应力集中,还增加焊接工作量。
焊接坡口角度不当或装配间隙不均匀,焊接电流过大或过小,运条方式或速度及焊角角度不当等均会造成焊缝尺寸不符合要求。
2、咬边由于焊接参数选择不当,或操作工艺不正确,沿焊趾的母材部位产生的沟槽或凹陷即为咬边。
咬边使母材金属的有效截面减小,减弱了焊接接头的强度,而且在咬边处易引起应力集中,承载后有可能造成在咬边处产生裂纹,甚至引起结构的破坏。
产生咬边的原因主要有操作方式不当,焊接规范选择不正确,如焊接电流过大、电弧过长、焊条角度不当等。
咬边超过允许值应予以补焊。
3、焊瘤焊接过程中,熔化的金属流淌到焊缝之外未熔化的母材上,所形成的金属瘤即为焊瘤。
焊瘤不仅影响焊缝外表的美观,而且焊瘤下面常有未焊透缺陷,易造成应力集中。
对于管道接头来说,管道内部的焊瘤还会使管内的有效面积减小,严重时使管内产生堵塞。
焊瘤常在立焊和仰焊时产生,焊缝间隙过大,焊条角度和运条方法不正确、焊条质量不好、焊接电流过大或焊接速度太慢等均可引起焊瘤的产生。
4、烧穿焊接过程中,熔化的金属自坡口背面流出,形成穿孔的缺陷称为烧穿。
烧穿常发生于打底焊道的焊接过程中。
发生烧穿,焊接过程不能继续进行,是一种不能允许存在的焊接缺陷。
造成烧穿的主要原因是焊接电流太大焊接速度过低、坡口和间隙太大或钝边太薄以及操作不当等。
为了防止烧穿,要正确设计焊接坡口尺寸,确保装配质量,选用适当的焊接工艺参数。
单面焊接可采用加铜板或焊剂垫等办法防止熔化金属下塌及烧穿。
手工电弧焊接薄板时,可采用跳弧焊接法或续灭弧焊接法。
5、未焊透焊接时接头根部未完全熔透的现象称为未焊透,未焊透常出现在单面焊的根部和双面焊的中部。
未焊透不仅使焊接接头的机械性能降低,而且在未焊透处的缺口和端部形成应力集中点,承载后会引起裂纹。
铝合金焊接工艺与焊接缺陷分析研究

铝合金焊接工艺与焊接缺陷分析研究铝合金是一种广泛应用的材料,它具有轻便、韧性好、耐腐蚀、导热性能良好等优点。
因此,在工业生产中,铝合金焊接工艺已经成为一项非常重要的工艺。
然而,铝合金焊接过程中常常会出现一些焊接缺陷,这些缺陷不仅会影响焊缝的强度和密封性,还可能导致零件失效。
因此,对于铝合金焊接工艺及其缺陷的研究,具有重要的理论和实际意义。
一、铝合金焊接工艺铝合金的焊接工艺一般包括氩弧焊、气保焊、激光焊等。
在氩弧焊中,需要用到直流电源和氩气,焊接过程中,要使用直流电流,以避免交流电的电流变换所引起的电弧不稳定现象;氩气的主要作用是保护焊缝,防止氧气和氮气等对焊缝的污染。
在气保焊中,需要用到氩气和焊丝,焊接过程中,将焊丝通过喷嘴弯折加热熔化,再加上氩气的保护,形成焊缝。
在激光焊中,激光束要通过透镜进行聚焦,然后聚焦在铝合金材料表面,使其熔化,然后快速冷却,形成焊缝。
二、焊接缺陷焊接缺陷是指在焊接过程中产生的不良现象和局部缺陷,这些缺陷会对焊缝的性能造成不良影响。
铝合金焊接缺陷的种类繁多,包括气孔、夹杂、缩孔、裂纹等。
其中最常见的缺陷是气孔和夹杂。
气孔是指焊缝中存在的气体孔洞,它们会使焊缝的密封性和强度下降。
气孔产生的原因主要有气体包裹在熔池中、杂质对焊接过程的干扰、焊接材料不洁净等。
避免气孔的产生,需要保证焊接过程中气体环境的洁净度,对焊接材料进行充分的清洗处理,以及控制焊接电流的大小。
夹杂是指焊缝内或焊接金属与基板间存在的杂质或氧化物,它们会降低焊缝的耐腐蚀性、密封性和力学性能。
夹杂的产生主要与材料的质量和焊接过程中的干扰有关。
避免夹杂的方法包括对焊接材料进行充分的清洗、使用适当的焊接参数以及控制焊接过程中的干扰因素。
三、焊接缺陷的分析及处理方法对于铝合金焊接中出现的缺陷,需要开展全面的分析,确定其产生的原因,然后针对性地采取相应的处理方法。
1. 气孔的分析及处理方法气孔是铝合金焊接中常见的焊接缺陷,其处理方法主要有以下几种:(1)采用合适的焊接工艺参数进行焊接,如控制焊接电流、预热温度等。
常见铝合金焊接缺陷及检验方法
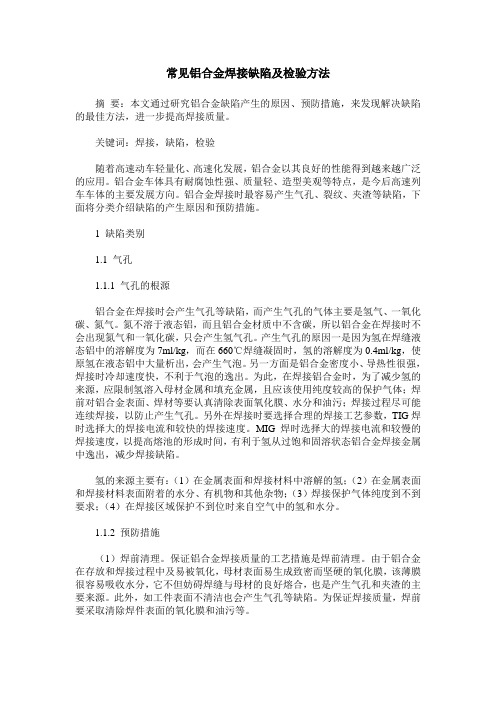
常见铝合金焊接缺陷及检验方法摘要:本文通过研究铝合金缺陷产生的原因、预防措施,来发现解决缺陷的最佳方法,进一步提高焊接质量。
关键词:焊接,缺陷,检验随着高速动车轻量化、高速化发展,铝合金以其良好的性能得到越来越广泛的应用。
铝合金车体具有耐腐蚀性强、质量轻、造型美观等特点,是今后高速列车车体的主要发展方向。
铝合金焊接时最容易产生气孔、裂纹、夹渣等缺陷,下面将分类介绍缺陷的产生原因和预防措施。
1 缺陷类别1.1 气孔1.1.1 气孔的根源铝合金在焊接时会产生气孔等缺陷,而产生气孔的气体主要是氢气、一氧化碳、氮气。
氮不溶于液态铝,而且铝合金材质中不含碳,所以铝合金在焊接时不会出现氮气和一氧化碳,只会产生氢气孔。
产生气孔的原因一是因为氢在焊缝液态铝中的溶解度为7ml/kg,而在660℃焊缝凝固时,氢的溶解度为0.4ml/kg,使原氢在液态铝中大量析出,会产生气泡。
另一方面是铝合金密度小、导热性很强,焊接时冷却速度快,不利于气泡的逸出。
为此,在焊接铝合金时,为了减少氢的来源,应限制氢溶入母材金属和填充金属,且应该使用纯度较高的保护气体;焊前对铝合金表面、焊材等要认真清除表面氧化膜、水分和油污;焊接过程尽可能连续焊接,以防止产生气孔。
另外在焊接时要选择合理的焊接工艺参数,TIG焊时选择大的焊接电流和较快的焊接速度。
MIG焊时选择大的焊接电流和较慢的焊接速度,以提高熔池的形成时间,有利于氢从过饱和固溶状态铝合金焊接金属中逸出,减少焊接缺陷。
氢的来源主要有:(1)在金属表面和焊接材料中溶解的氢;(2)在金属表面和焊接材料表面附着的水分、有机物和其他杂物;(3)焊接保护气体纯度到不到要求;(4)在焊接区域保护不到位时来自空气中的氢和水分。
1.1.2 预防措施(1)焊前清理。
保证铝合金焊接质量的工艺措施是焊前清理。
由于铝合金在存放和焊接过程中及易被氧化,母材表面易生成致密而坚硬的氧化膜,该薄膜很容易吸收水分,它不但妨碍焊缝与母材的良好熔合,也是产生气孔和夹渣的主要来源。
铝及铝合金焊接常见缺陷和防止措施

C】尽量在不引起气流絮乱的地方进行焊接
四焊缝成型差
产生原因
A】焊缝规范选择不当
B】焊枪角度选择不正确
C】焊工操作不熟练
生的原因
A】热输入量过大
B】坡口加工不当,焊件装配间隙过大
C】点固焊时焊点间距过大,焊接过程中产生了较大的变形量
防护措施
A】适当减小焊接电流,电弧电压,提高焊接速度
B】大钝边尺寸,减小根部间隙
C】适当减小点固焊时焊点间隙
二气孔
A】母材或焊丝上有油,锈,污垢等
B】焊接场地空气流动大,不利于气体保护
铝及铝合金焊丝的选择主要根据母材的种类,对接头的抗裂性能,力学性能及耐腐蚀
等方面的要求的综合因素考虑。有时当某项成为主要矛盾时,则选择焊丝时主要从考虑解决主要矛盾入手,兼顾其它方面要求。一般情况下,焊接铝及铝合金都采用于母材成分相同或相近牌号的焊丝进行焊接,这样才能获得较好的耐腐蚀性,但焊接热裂倾向的热处理强化铝合金时,选择焊丝时主要从抗裂性入手,这是焊丝的成分与母材的差别就很大。
C】焊接电弧过长,降低气体保护效果
D】喷嘴与工件距离过大,气体保护效果降低
E】焊接参数选择不当
F】重复起弧出产生气孔
G】保护气纯度低,气体保护效果差
H】周围环境空气湿度大
防护措施
与产生原因之间的做适当检查,并且适当的调试电流,电弧
三电弧不稳
产生原因:电源线连接,污物或者有风
防止措施
A】检查所有导电部分并使其表面保持清洁
铝焊常见缺陷及原因

铝焊常见缺陷原因及措施(一)焊接缺陷种类常见的缺陷主要有焊缝成形差、裂纹、气孔、烧穿,未焊透、未熔合、夹渣等。
1、焊缝成形差产生原因:焊接规范选择不当;焊枪角度不正确;焊工操作不熟练;导电嘴孔径太大;焊接电弧没有严格对准坡口中心;焊丝、焊件及保护气体中含有水分。
焊缝成形差主要表现在焊缝波纹不美观,且不光亮;焊缝弯曲不直,宽窄不一,接头太多;焊缝中心突起,两边平坦或凹陷;焊缝满溢等。
2、气孔产生原因:氩气纯度低或氩气管路内有水分、漏气等;焊丝或母材坡口附近焊前未清理干净或清理后又被污物、水分等沾污;焊接电流和焊速过大或过小;熔池保护欠佳,电弧不稳,电弧过长,钨极伸出过长等。
焊接时熔池中的气孔在凝固时未能逸出而留下来所形成的空穴称为气孔。
在MIG焊接过程中,气孔是不可避免的,只能尽量减少它的存在。
在培训的过程中,仰角焊、立向上焊气孔倾向尤为明显,根据DIN30042标准规定,单个气孔的直径最大不能超过0.25α(α为板厚),密集气孔的单个直径最大不超过0.25+0.01α(α为板厚)。
氢是铝及铝合金熔化焊产生气孔的主要原因。
氮不溶于液态铝,铝又不含碳,因此铝合金中不会产生氮气孔和一氧化碳气孔;氧和铝有很大的亲和力,总是以氧化铝的形式存在,所以也不会产生氧气孔;氢在高温时大量的溶于液态铝,但几乎不溶于固态铝,所以在凝固点溶于液体中的氢几乎全部析出,形成气泡。
但铝和铝合金的比重轻,气泡在熔池中的上升的速度较慢,加上铝的导热能力强凝固,不利于气泡的浮出,故铝和铝合金易产生气孔,氢气孔在焊缝内部一般呈白亮光洁状。
氢的来源比较多,主要来自弧柱气氛中的水、焊丝以及母材所吸附水分对焊缝气孔的产生常常占有突出的地位。
厂房空气中的湿度也影响弧柱气氛。
MIG焊接时,焊是以细小熔滴形式通过弧柱而落入熔池的,由于弧柱温度最高,熔滴比表面积很大,故有利于熔滴金属吸收氢,产生气孔的倾向也更大些。
弧柱中的氢之所以能够形成气,与它在铝合金中的溶解度变化有。
铝及铝合金焊接中常见焊接缺陷及其对策

铝及铝合金焊接中常见焊接缺陷及其对策摘要:铝及铝合金的应用范围随着社会经济的发展在不断扩大,在轨道交通、建筑、桥梁、船舶中都有被应用。
又随着近些年来更高效率和更高想能的焊接技术的推广,铝及铝合金被运用得越来越广泛,相应的技术也得到了一定的发展。
不过,在铝及铝合金的实际运用过程中,由于其存在着容易氧化、熔点低、导热性高、热容量大以及膨胀系数大的特点,也给其焊接工艺造成了一定的影响,容易出现一些焊接缺陷。
本文主要对铝及铝合金焊接中的常见缺陷进行分析,并提出相应的解决措施。
希望能够对铝及铝合金的焊接行业有所帮助,提高焊接效率与焊接质量。
关键词:铝及铝合金;焊接缺陷;对策引言:铝及铝合金耐腐性较好,并且轻度较高,还具有导电性以及导电性好的特点,因此,铝及铝合金在工业中得到了广泛应用。
因此,相关焊接人员在进行铝及铝合金焊接时,对其性能、焊接方式、焊接材料、焊接缺陷等都需要有充分的把握。
只有对相应的焊接知识熟练掌握之后才能够更好的开展铝及铝合金的焊接工作。
1铝及铝合金的焊接性能要想充分掌握铝及铝合金的焊接技巧,就需要对其的焊接性能有所掌握。
铝及铝合金具有以下焊接性能:1)比热大、导热快。
由于铝及铝合金导热较快,其散热速度也相对较快,在进行焊接工作时,一般使用功率较大的焊接热源,有时候焊接热源的热度不够,还需要对热源进行预热。
2)膨胀系数大。
由于具有膨胀系数大的特点,在焊接之后,金属凝固后的收缩率也较大。
因此,在焊接中容易出现变形的情况。
3)容易形成气孔。
氢气是铝及铝合金焊接时容易出现气孔的主要原因,其中主要来自于焊接材料中含有的水分。
2铝及铝合金中常见焊接缺陷铝及铝合金在我国工业中被应用得十分广泛,虽具有许多的优势,但是也有一些常见的焊接缺陷,要想提高铝及铝合金的焊接效率和焊接质量,就需要对相应的焊接缺陷进行充分的把握,在把握相应焊接缺陷的基础上,再提出相应的解决措施。
铝及铝合金焊接中的常见缺陷主要有裂纹、凹陷、烧穿、气孔凹陷等,以下是对这些缺陷的分点阐述。
铝合金焊接7类缺陷及防止措施(超实用)

铝合金焊接7类缺陷及防止措施(超实用)1、焊接气孔焊接时,熔池中的气泡在凝固时未能逸出而残留下来所形成的孔穴。
产生原因:1) 母材或焊丝材料表面有油污、氧化膜清理不干净,或清理后未及时焊接。
2) 保护气体纯度不够高,保护效果差。
3) 供气系统不干燥,或漏气漏水。
4) 焊接工艺参数选择不当。
5) 焊接过程气体保护不良,焊接速度过快。
防止措施:1) 焊前彻底清理焊缝区和焊丝。
2) 采用合格的保护气体,纯度应符合规范。
3) 供气系统保持干燥,防止漏气漏水。
4) 焊接工艺参数选择要合理。
5) 注意保持焊炬、焊丝和工件间的准确位置,焊炬应尽量垂直于工件;尽量采用短弧施焊,喷嘴离工件距离应控制在10~15 mm;焊炬应做匀速直线运动,钨极应对准焊缝中心,往复匀速送丝;焊接现场要有挡风设施,不能有风流动,焊件应进行适当预热;注意引弧和收弧质量。
2、未焊透、未熔合焊接时未完全熔透的现象,称为未焊透。
焊接时焊道与母材或焊道与焊道之间未完全熔化结合的部分,称为未熔合。
产生原因:1) 焊接电流控制过小,电弧过长,焊接速度过快,预热温度低。
2) 焊缝间隙过小,钝边过大,坡口角度过小。
3) 焊件表面及焊接层面间的氧化物清除不干净。
4) 操作技术不熟练,不能把握送丝的良好时机。
防止措施:1) 选择正确的焊接电流参数。
厚板焊接时,焊前进行工件预热80~120 ℃,使工件温度达到焊接要求。
2) 选择合适的焊接接头间隙和坡口角度。
3) 加强焊件表面及焊接层面间氧化物的清理工作。
4) 强化焊接操作技术,应正确判断坡口或焊层表面的熔化情况,采用大电流(一般应使焊部位在电弧引燃后5 s 之内能获得一定大小干净明亮的熔池,此时可加丝焊接)快速焊和快送少加焊丝的方法,精心施焊,可避免未焊透和未熔合现象的发生。
3、咬边焊接后,母材与焊缝边沿交界处的凹陷沟槽称为咬边。
产生原因:1) 焊接工艺参数过大,焊接电流太大,电弧电压太高,热输入量过大。
铝合金焊接缺陷及控制

铝合金焊接缺陷及控制摘要铝合金密度低,强度大,大量应用于高速列车的车体制造。
但铝合金焊接时变形大,易产生气孔、裂纹等缺陷,因此需要采取相应的措施来有效地控制铝合金焊接缺陷,保证高速列车的制造质量。
关键词:铝合金氧化膜气孔裂纹变形夹渣未焊透前言目前铝合金作为大众化的金属材料被广泛的应用于各个行业,它具有密度低、强度高、挤压性及焊接性能良好、回收利用率高等多优越特点,也批量应用于铁道车辆制造业。
高速动车在速度提高的同时也要求车体具有更高的承载强度,因此必须提高铝合金焊接质量,有效地控制缺陷的产生,达到设计要求。
1.铝合金的性能纯铝是银白色的轻金属,密度2.7g/cm³,约为钢的1/3(钢的密度为7.87g/cm³),导电率较高,仅次于金、银、铜居第4位。
热导率比钢大两倍左右,熔点为658℃,加热溶化时无明显颜色变化,具有面心立方结构,无同素异构转变。
塑性和冷、热、压力加工性能好,但强度低(只有90 MPa左右)。
纯铝的化学活泼性强,与空气接触时,就会在其表面生成一层致密的氧化膜(主成分是Al2O3)薄膜,这层氧化膜可防止冷的硝酸及醋酸的腐蚀,但在碱类和含有氯离子的盐类溶液中被迅速破坏而引起强烈腐蚀。
纯铝中随着杂质的增加,其强度增加,而塑性、导电性和耐蚀性下降。
铝合金是在纯铝中加入合金元素如镁、锰、硅、铜、锌等后获得不同性能的金属材料。
2.应用于结构件的铝合金简介目前利用于铁道车辆的铝合金主要由5000系列、6000系列,7000系列。
[Al- Mg合金-5000系]:由于Mg的增加直接影响其机械性能,能增加抗拉强度。
含有低Mg的合金主要利用于装饰材料、建筑材料。
含有 2.5%Mg的合金具有较好的耐蚀性、加工性、耐海水性、焊接性,则主要利用于车辆、船舶的制造。
[Al- Mg-Si合金-6000系]:主要含有Mg、Si金属,是热处理强化性铝合金。
此系列合金具有优良的挤压性,因此制造型材非常有利,且具有良好的耐蚀性、焊接性、具有较高的强度,则广泛利用于铁道车辆、船舶、建筑用窗框、土木结构材料的制造。
铝合金焊接常见缺陷和防治措施

铝及铝合金焊丝的选择主要根据母材的种类,对接头抗裂性能、力学性能及耐蚀性等方面的要求综合考虑。
有时当某项成为主要矛盾时,则选择焊丝就着重从解决这个主要矛盾入手,兼顾其它方面要求。
一般情况下,焊接铝及铝合金都采用与母材成分相同或相近牌号的焊丝,这样可以获得较好的耐蚀性;但焊接热裂倾向大的热处理强化铝合金时,选择焊丝主要从解决抗裂性入手,这时焊丝的成分与母材的差别就很大。
常见缺陷(焊接问题)及防止措施1、烧穿产生原因:a、热输入量过大;b、坡口加工不当,焊件装配间隙过大;c、点固焊时焊点间距过大,焊接过程中产生较大的变形量。
防止措施:a、适当减小焊接电流、电弧电压,提高焊接速度;b、大钝边尺寸,减小根部间隙;c、适当减小点固焊时焊点间距。
2、气孔产生原因:a、母材或焊丝上有油、锈、污、垢等;b、焊接场地空气流动大,不利于气体保护;c、焊接电弧过长,降低气体保护效果;d、喷嘴与工件距离过大,气体保护效果降低;e、焊接参数选择不当;f、重复起弧处产生气孔;g、保护气体纯度低,气体保护效果差;h、周围环境空气湿度大。
防止措施:a、焊前仔细清理焊丝、焊件表面的油、污、锈、垢和氧化膜,采用含脱氧剂较高的焊丝;b、合理选择焊接场所;c、适当减小电弧长度;d、保持喷嘴与焊件之间的合理距离范围;e、尽量选择较粗的焊丝,同时增加工件坡口的钝边厚度,一方面可以允许使用大电流,微信公众号:焊王,另一方面也使焊缝金属中焊丝比例下降,这对降低气孔率是行之有效的;f、尽量不要在同一部位重复起弧,需要重复起弧时要对起弧处进行打磨或刮除;一道焊缝一旦起弧要尽量焊长些,不要随意断弧,以减少接头量,在接头处需要有一定焊缝重叠区;g、换保护气体;h、检查气流大小;i、预热母材;j、检查是否有漏气现象和气管损坏现象;k、在空气湿度较低时焊接,或采用加热系统。
3、电弧不稳产生原因:电源线连接、污物或者有风。
防止措施:a、检查所有导电部分并使表面保持清洁;b、将接头处的脏物清除掉;c、尽量不要在能引起气流紊乱的地方进行焊接。
第七章铝及铝合金常见焊接缺陷、原因分析和控制规则
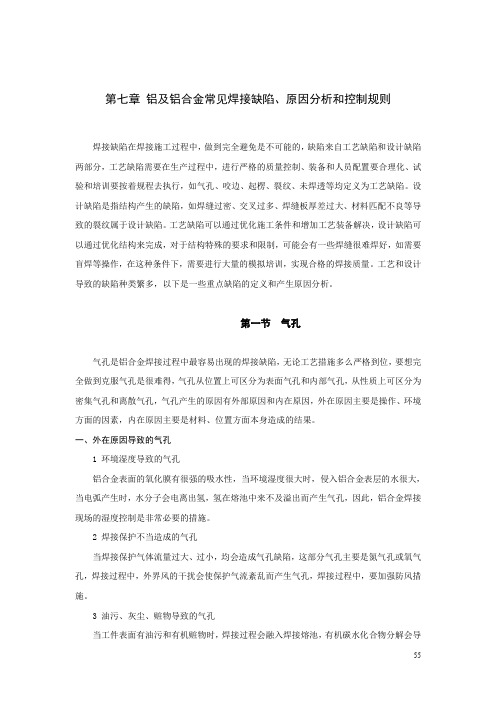
第七章铝及铝合金常见焊接缺陷、原因分析和控制规则焊接缺陷在焊接施工过程中,做到完全避免是不可能的,缺陷来自工艺缺陷和设计缺陷两部分,工艺缺陷需要在生产过程中,进行严格的质量控制、装备和人员配置要合理化、试验和培训要按着规程去执行,如气孔、咬边、起楞、裂纹、未焊透等均定义为工艺缺陷。
设计缺陷是指结构产生的缺陷,如焊缝过密、交叉过多、焊缝板厚差过大、材料匹配不良等导致的裂纹属于设计缺陷。
工艺缺陷可以通过优化施工条件和增加工艺装备解决,设计缺陷可以通过优化结构来完成,对于结构特殊的要求和限制,可能会有一些焊缝很难焊好,如需要盲焊等操作,在这种条件下,需要进行大量的模拟培训,实现合格的焊接质量。
工艺和设计导致的缺陷种类繁多,以下是一些重点缺陷的定义和产生原因分析。
第一节气孔气孔是铝合金焊接过程中最容易出现的焊接缺陷,无论工艺措施多么严格到位,要想完全做到克服气孔是很难得,气孔从位置上可区分为表面气孔和内部气孔,从性质上可区分为密集气孔和离散气孔,气孔产生的原因有外部原因和内在原因,外在原因主要是操作、环境方面的因素,内在原因主要是材料、位置方面本身造成的结果。
一、外在原因导致的气孔1 环境湿度导致的气孔铝合金表面的氧化膜有很强的吸水性,当环境湿度很大时,侵入铝合金表层的水很大,当电弧产生时,水分子会电离出氢,氢在熔池中来不及溢出而产生气孔,因此,铝合金焊接现场的湿度控制是非常必要的措施。
2 焊接保护不当造成的气孔当焊接保护气体流量过大、过小,均会造成气孔缺陷,这部分气孔主要是氮气孔或氧气孔,焊接过程中,外界风的干扰会使保护气流紊乱而产生气孔,焊接过程中,要加强防风措施。
3 油污、灰尘、赃物导致的气孔当工件表面有油污和有机赃物时,焊接过程会融入焊接熔池,有机碳水化合物分解会导致气孔产生。
4 操作不当导致的气孔当焊接前倾角度过小或操作不稳,均会导致焊接气孔的产生,在焊接培训过程中,焊接操作避免气孔的技能需要必备的。
铝合金焊接常见缺陷的产生原因及质量控制措施

(5)补 焊结 束 ቤተ መጻሕፍቲ ባይዱ ,应 等 到 自然 冷却 至 5O。以下 ,再 喷 涂渗 透剂 ,否 则易 造成 补焊 区产生 冷 却 裂纹 。对 于 裂 纹 的修 补 ,要 彻底 把 缺 陷清 除掉 以后 ,按 照工 艺 文 件 的要 求 进 行 补 焊 。
效 的方法 ,能 够最 大限 度 的在 焊接 时让气 孔 逸 出。 1_5 气 孔 的 去 除 及 修 补
气 孔 的 修 补应 根据 图纸 、执行 标 准 、工 艺 文 件规 定 的 级 别 判 断 是 否 超 标 ,超 标 的 ,要 打 磨 去 掉 。对 于 超 标 严 重 的 气 孔 ,应 挖 开 完 全 去 除 后 进 行 补 焊 。 打 磨 去 掉 缺 陷 时 应 注 意 打 磨 的深 度 .切 勿 为 追 求 缺 陷 的 消 除 而 造 成 打 磨 过 度 ,补 焊 时 非 无 损 检 测 人 员 不 要 白行 进 行 渗 透 探 伤 , 以 防 止 操 作 方 法 不 当 引 起 缺 陷 开 口堵 塞 ,降 低 缺 陷 检 出 率 ,造 成 质 量 隐 患 。
MIG焊 [J].焊 接 ,2008(9):33—35. [2]周 万 胜 ,姚 君 山 .铝 及 铝 合 金 的 焊 接 [M].北 京 :机 械 工 业 出 版 社 ,
2006.
[3]黄 旺福 ,黄 金 刚.铝 及 铝 合 金 焊 接 指 南 [M].长 沙 :湖 南 科 学 技 术 出 版 社 ,2004.
计 在 应 力 集 中处 。 (2)利 用 衰减 控 制 降 低 冷却 速度 ,适 当的 填 充 弧
铝焊常见缺陷原因

铝焊常见缺陷原因及措施(一)焊接缺陷种类常见的缺陷主要有焊缝成形差、裂纹、气孔、烧穿,未焊透、未熔合、夹渣等。
1、焊缝成形差产生原因:焊接规范选择不当;焊枪角度不正确;焊工操作不熟练;导电嘴孔径太大;焊接电弧没有严格对准坡口中心;焊丝、焊件及保护气体中含有水分。
焊缝成形差主要表现在焊缝波纹不美观,且不光亮;焊缝弯曲不直,宽窄不一,接头太多;焊缝中心突起,两边平坦或凹陷;焊缝满溢等。
2、气孔产生原因:氩气纯度低或氩气管路内有水分、漏气等;焊丝或母材坡口附近焊前未清理干净或清理后又被污物、水分等沾污;焊接电流和焊速过大或过小;熔池保护欠佳,电弧不稳,电弧过长,钨极伸出过长等。
焊接时熔池中的气孔在凝固时未能逸出而留下来所形成的空穴称为气孔。
在MIG焊接过程中,气孔是不可避免的,只能尽量减少它的存在。
在培训的过程中,仰角焊、立向上焊气孔倾向尤为明显,根据DIN30042标准规定,单个气孔的直径最大不能超过0.25α(α为板厚),密集气孔的单个直径最大不超过0.25+0.01α(α为板厚)。
氢是铝及铝合金熔化焊产生气孔的主要原因。
氮不溶于液态铝,铝又不含碳,因此铝合金中不会产生氮气孔和一氧化碳气孔;氧和铝有很大的亲和力,总是以氧化铝的形式存在,所以也不会产生氧气孔;氢在高温时大量的溶于液态铝,但几乎不溶于固态铝,所以在凝固点溶于液体中的氢几乎全部析出,形成气泡。
但铝和铝合金的比重轻,气泡在熔池中的上升的速度较慢,加上铝的导热能力强凝固,不利于气泡的浮出,故铝和铝合金易产生气孔,氢气孔在焊缝内部一般呈白亮光洁状。
氢的来源比较多,主要来自弧柱气氛中的水、焊丝以及母材所吸附水分对焊缝气孔的产生常常占有突出的地位。
厂房空气中的湿度也影响弧柱气氛。
MIG焊接时,焊是以细小熔滴形式通过弧柱而落入熔池的,由于弧柱温度最高,熔滴比表面积很大,故有利于熔滴金属吸收氢,产生气孔的倾向也更大些。
弧柱中的氢之所以能够形成气,与它在铝合金中的溶解度变化有。
铝合金材料主要缺陷与质量控制技术

铝合金材料主要缺陷与质量控制技术铝合金材料,这个名字一听就感觉高大上,对吧?在我们的日常生活中,铝合金可谓无处不在。
想想你手里的手机壳、汽车的车身,甚至是窗户框,基本都离不开这玩意儿。
不过,铝合金这货也有点小脾气,偶尔会出现一些缺陷,让人抓狂。
今天就跟大家聊聊铝合金的主要缺陷和怎么控制这些缺陷,保证我们用得放心,真是让人心里踏实啊。
说到铝合金的缺陷,第一时间浮现在脑海里的就是“气泡”。
没错,就像泡沫咖啡里那些可爱的小泡泡,听起来挺可爱的,但在铝合金里就没那么好玩了。
气泡一旦出现,铝合金的强度可就下降了,真是让人心痛。
你想想,买了个贵重的东西,结果里面藏着泡泡,简直就是“里外不是人”啊。
怎么控制呢?在铝合金的铸造过程中,控制好温度和压力,像对待自己家小猫一样细心,避免空气混入,这样就能减少气泡的出现。
再说说“夹杂物”,这可不是什么小东西,而是铝合金里的“坏蛋”。
这些夹杂物可能是其他金属、氧化物或者杂质,影响铝合金的性能。
就好比你吃饭时碰到一根头发,心里那个别扭,完全影响了食欲。
铝合金如果有夹杂物,强度和韧性肯定大打折扣。
怎么解决呢?那就是要在铝的冶炼过程中精益求精,彻底清除掉那些“不速之客”,让铝合金能够以最完美的姿态展现。
还有一种情况,就是“裂纹”。
别以为裂纹就小,小裂纹能让你哭得稀里哗啦。
铝合金在焊接或冷却过程中,温度变化太快,就容易产生裂纹。
就像我们在寒冷的冬天里突然去洗冷水澡,瞬间让你受不了。
而铝合金一旦有了裂纹,强度直线下降,简直就是一颗定时炸弹。
对此,焊接时保持温度均匀,真是至关重要,像是在煮面,水开得太快面条容易烂,慢慢来,才能保证铝合金的稳定。
要聊聊“腐蚀”。
铝合金虽然说是个强壮的家伙,但也经不起风吹雨打,长时间暴露在潮湿环境中,表面就容易出现腐蚀。
这就像你不小心把香水喷在白衬衫上,时间长了,衣服就留下了难以洗掉的痕迹。
铝合金的表面处理就显得尤为重要,铝合金表面涂层和阳极氧化,可以有效防止腐蚀,让它在各种环境中都能“游刃有余”。
铝焊常见缺陷及原因

铝焊常见缺陷及原因第一篇:铝焊常见缺陷及原因铝焊常见缺陷原因及措施(一)焊接缺陷种类常见的缺陷主要有焊缝成形差、裂纹、气孔、烧穿,未焊透、未熔合、夹渣等。
1、焊缝成形差产生原因:焊接规范选择不当;焊枪角度不正确;焊工操作不熟练;导电嘴孔径太大;焊接电弧没有严格对准坡口中心;焊丝、焊件及保护气体中含有水分。
焊缝成形差主要表现在焊缝波纹不美观,且不光亮;焊缝弯曲不直,宽窄不一,接头太多;焊缝中心突起,两边平坦或凹陷;焊缝满溢等。
2、气孔产生原因:氩气纯度低或氩气管路内有水分、漏气等;焊丝或母材坡口附近焊前未清理干净或清理后又被污物、水分等沾污;焊接电流和焊速过大或过小;熔池保护欠佳,电弧不稳,电弧过长,钨极伸出过长等。
焊接时熔池中的气孔在凝固时未能逸出而留下来所形成的空穴称为气孔。
在MIG焊接过程中,气孔是不可避免的,只能尽量减少它的存在。
在培训的过程中,仰角焊、立向上焊气孔倾向尤为明显,根据DIN30042标准规定,单个气孔的直径最大不能超过0.25α(α为板厚),密集气孔的单个直径最大不超过0.25+0.01α(α为板厚)。
氢是铝及铝合金熔化焊产生气孔的主要原因。
氮不溶于液态铝,铝又不含碳,因此铝合金中不会产生氮气孔和一氧化碳气孔;氧和铝有很大的亲和力,总是以氧化铝的形式存在,所以也不会产生氧气孔;氢在高温时大量的溶于液态铝,但几乎不溶于固态铝,所以在凝固点溶于液体中的氢几乎全部析出,形成气泡。
但铝和铝合金的比重轻,气泡在熔池中的上升的速度较慢,加上铝的导热能力强凝固,不利于气泡的浮出,故铝和铝合金易产生气孔,氢气孔在焊缝内部一般呈白亮光洁状。
氢的来源比较多,主要来自弧柱气氛中的水、焊丝以及母材所吸附水分对焊缝气孔的产生常常占有突出的地位。
厂房空气中的湿度也影响弧柱气氛。
MIG焊接时,焊是以细小熔滴形式通过弧柱而落入熔池的,由于弧柱温度最高,熔滴比表面积很大,故有利于熔滴金属吸收氢,产生气孔的倾向也更大些。
- 1、下载文档前请自行甄别文档内容的完整性,平台不提供额外的编辑、内容补充、找答案等附加服务。
- 2、"仅部分预览"的文档,不可在线预览部分如存在完整性等问题,可反馈申请退款(可完整预览的文档不适用该条件!)。
- 3、如文档侵犯您的权益,请联系客服反馈,我们会尽快为您处理(人工客服工作时间:9:00-18:30)。
¨ 检查/ f 易 发 现 壳 体 内
集 中 的地 方 , 日 该 安 装 支座
部 的 焊 缝 外 观缺 陷 ,即 使 增 加 x 射线 枪 测 ,也 会 因 角接 焊 缝 往 拐 们处x 线 成像I 什仃 嘘 影 ,也 难以【 l : 圳 角接 焊 缝 的 内 、 外部 缺
图2 典型 圆筒形 薄壁壳体焊接件
应力 ( 有 拉 力 、 应 力 、 剪切
成 力 、弯 曲应 力和 复 合应 力 ) ;
气动 载 荷 、撤 动 戴 倚 川 卜 ,
安 装 支 座 焊 缝 处 承我 的 度 远 低
量 发现 :裂 纹 源 区2 3 mm范 围 内
( 约 占焊 缝 全 3 % )存 在 未 焊
控 制 气 孔 、央 淹 缺 陷 于 f f 施 :① 要 保 证 母材 、焊 、 火 焊 前 消 理 干 净 。 ②仔 储 J 川 转} f 、 f 避 免 次 污染 , 要求的仃仃 f } 时 I 内 完 成 焊 接 。 ③ 焊 接 电 流 j 焊接速7 蒸 适中。冈此 , I 验 j , I :
为避 免 弁 】 接 焊 缝 产生 的 应 力
严格 控 制钨 极 污 染焊 缝 的 情 况 ,
集『 l I 造 成疲 劳 裂纹 ,将 安 装 支座
的 纰 成 零 件 连 接 形 式 优 化 虹改 , 女 ¨ I 割2 b 所, J 。
仍 现 亮点 缺 陷 , 此 ,排 除 火
焊按接 头强罔3 是 在科研 生产 试验 中 ,
通 过低 倍 金 相 枪 查 发 现 的铝 合 金 角焊 缝 缺 陷 。 外 , 们焊 缝 的 质 量 J - 检 性
,
4 . 焊接参 数优化
将 角焊 的 构 设 优 化 成 对 焊 后 ,在 生 产 I I 1 叮 彳 丁 t 效控 焊 什 的 末焊 透 等 外 观 缺 陷 , l i ,似
测 分 析 亮 点 缺 的 化 。 成 分 为 Al 1 0 , ,Al O 的密度约 为 合 材 料的4 倍, 亮 点 为 高 密 度 分 析 戚J I ^ I I ・
3 . 焊接结构 设计优化
l 冬 J 2 a 所 永 的 安 装 支 的 仪需
火 l 缺 。
。
状 不 眦 则 的 单 个 也点 状 暗 点 , 导致
. 个 成链
行 中 川时 承 受 着 气 动 载 荷 和
振 动载 苘 ,焊 缝 处承 受 气动 载 荷 J : 的: 矩 、 剪 力和 拉 力 。据 此 分 析 得 到 陔安 装 史庸 断 裂 失 效 原
合格 。呔 ¨ ‘
装,
造过程中无f 中压 工 序 ,因 角按
并『 I _ 易j 进行I _ 】 } 见 榆 杏 肢 x射 线 榆 洲 发 现焊 接 缺 1 ; f ; ,进 ・ 步 保证
并
对 按 接 头 相 比 , 其 焊 缝
干其材料安全疲劳} 及 ,满 疲 劳 强 度 要求 。
易 产 乍 未 焊 透 、 气 扎 、 夹渣 等 缺
透缺陷 ( 图l d ) ,焊缝 熔 透 区 宽度为1 . 2 ~1 . 4 mm,熔 透 深 度 为 母 材厚 度6 0 % ̄ 7 0 %,未 发 现其 他 1 人 】 邴缺 。 术焊 透 不 仅 严 影 响
钨 缺 陷 的可 能 。 进 一步 采 川 金十 l I 瞍s EM 枪
逐 渐 扩 展 , 当利 余 部 分 强 度 足 f I l f ,最 终 导致 安装 支座 断 裂 。
体优 化 办案 女 ¨ 下: ( 1 )改 进 后 的 【 端盖 L j 巾 部 简 的 连 接 采 用 l 6 颗 4 mm ̄ O 1 ] 钉铆接 , , 式, 改 进 前 的 内 角接
焊接形式卡 H 比 ,消 除 _ r 焊 接 缺 陷 等/ f 利 祟 对连 接 性 能 的影 响 。 ( 2 )改进 后 的 【 } l 郝 圃 简 下 端 连 接 采用 对 接 焊 接 方 式 , 改进 n 外 角按 焊 接 形 式 相 比 , 焊接 1 : 艺操 作 到 较 人提 高 ,
将 个 部 分 经 简 钣 金 工 艺成 肜 的 薄 板 材焊 接而 成 ,这 种 角按
, 式 r l ; J : t  ̄ 接结 构 出然 降 低 了工 艺 难度和制造成本 ( 不 采 川 整 件棒 科 或 板 料 机 加 ,大 火 节 省 r材 料 费 川 ,也 / f 采用 州 I 压结 构 件组
T
域 变 形 严 重 ,为 瞬 断 区域 ;下 部 2 / 3区域 为 裂 纹 扩 展 域 , 采 用 低 倍金 栩 观 察 裂 纹 扩 展 区域 ,发 现 典 裂 纹 源 宏 观 形 貌 :断 口较
l 技 术 研 究 与 应 用
r
为 坦 ,许可观察到断裂之后的
色销 合 金 磨 损 产物 ,如 1 b 所
中 的暗 点 为典 的 . 个 ( 4 L 成链 状 气孔 缺 陷 , 凭经 岭 初 步 削断 l 式 验
此 , I
特 定 的 承 载 环 境
亮 点 为 灾钨 缺 ,
为: 卜 端 与简 体 外 角按 焊 缝 的 爪焊 透 缺 陷 造 成 焊 接 结 构 力
粜r l I ' 谚 裂纹 , 交变 载 倚 作 用下 产 生 疲 后 交 变载 荷 作 用 卜
永 。进 一 步通 过 S E M观 察 ,可 见 敛 密 的 疲 劳 条带 ( 见 1 C ), 此 推 断 该断 r 】 为疲 劳 断 口。 针 对 裂 纹 源 区 检 测 焊 缝 质
●■■l
】
I
( r J ) 构 优 化
( b )
f J & f 匕 J l t