宁钢高炉槽下料斗秤改造
2号高炉槽下皮带秤误差的日常检测及处理
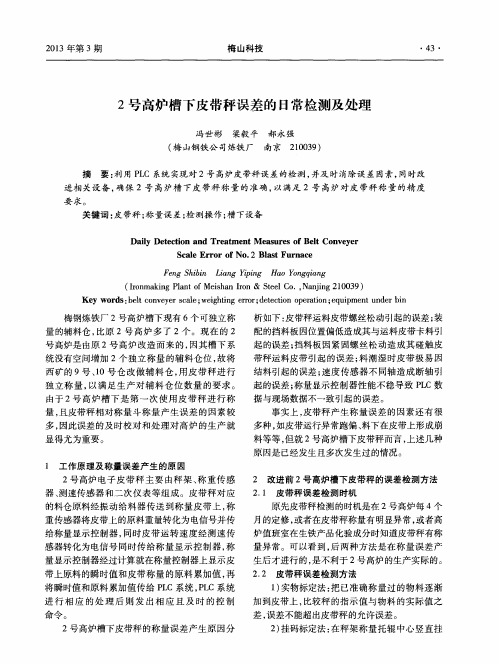
梅 钢炼 铁厂 2号 高炉槽 下 现有 6个 可独立 称
析如 下 : 皮 带秤 运料 皮带 螺丝 松动 引起 的误差 ; 装 配 的挡料板 因位 置偏 低造 成其 与运料 皮 带卡料 引 起 的误 差 ; 挡料 板 因 紧 固螺 丝 松 动 造 成其 碰 触 皮 带 秤运 料皮 带 引起 的误 差 ; 料 潮 湿 时皮 带 极 易 因
显得 尤为 重要 。
1 工作 原理及 称 量误 差产 生 的原 因
结料引起的误差 ; 速度传感器不同轴造成断轴引 起 的误 差 ; 称量显 示控 制 器性 能 不 稳 导致 P L C数
据 与 现场数 据不 一致 引起 的误 差 。
事实上 , 皮带秤产生称量误差 的因素还有很 多种 , 如皮 带运行 异 常跑偏 、 料 下在皮 带上 形成 崩 料等等 , 但就 2 号高炉槽下皮带秤而言 , 上述几种
量的辅料仓 , 比原 2号高炉多 了 2个。现在的 2
号 高炉是 由原 2号 高 炉 改 造 而来 的 , 因其 槽 下 系 统 没有 空 间增 加 2个 独 立称 量 的辅 料 仓 位 , 故 将
西矿的 9 号、 1 0号仓改做辅料仓 , 用皮带秤进行 独立称量 , 以满足生产对辅料仓位数量 的要 求。 由于 2 号 高炉槽 下是第一 次使用皮带秤进 行称 量, 且皮带秤相对称量斗称量产生误差 的因素较 多, 因此 误差 的及 时 校 对 和 处理 对 高炉 的生 产 就
2 ) 挂 码标 定法 : 在 秤 架称 量 托 辊 中心 竖 直 挂
2号高炉槽下皮带秤 的称量误差产生原因分
・
4 4・
梅 山科 技
2 0 1 3年第 3期
一
定 量 的标准 砝码 代替 皮带 上料 , 启动 皮带 , 比较 3 ) 链 码标 定法 : 把 已知重 量 的链 码 ( 或链 条 、
高炉槽下称重PLC自动计量系统技术改造及研究
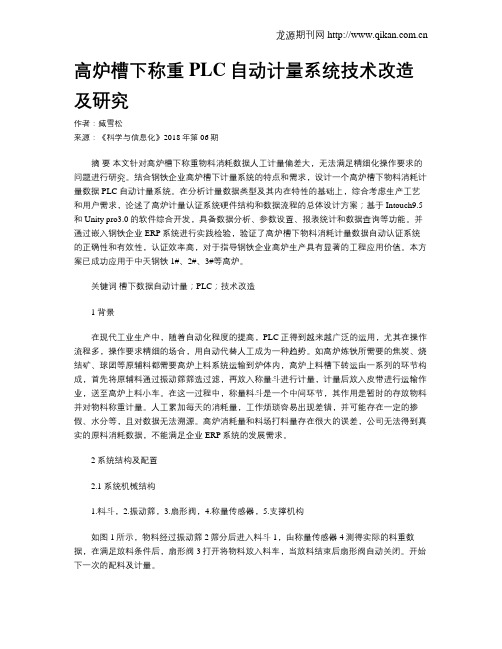
高炉槽下称重PLC自动计量系统技术改造及研究作者:臧雪松来源:《科学与信息化》2018年第06期摘要本文针对高炉槽下称重物料消耗数据人工计量偏差大,无法满足精细化操作要求的问题进行研究。
结合钢铁企业高炉槽下计量系统的特点和需求,设计一个高炉槽下物料消耗计量数据PLC自动计量系统。
在分析计量数据类型及其内在特性的基础上,综合考虑生产工艺和用户需求,论述了高炉计量认证系统硬件结构和数据流程的总体设计方案;基于Intouch9.5和Unity pro3.0的软件综合开发,具备数据分析、参数设置、报表统计和数据查询等功能。
并通过嵌入钢铁企业ERP系统进行实践检验,验证了高炉槽下物料消耗计量数据自动认证系统的正确性和有效性,认证效率高,对于指导钢铁企业高炉生产具有显著的工程应用价值。
本方案已成功应用于中天钢铁1#、2#、3#等高炉。
关键词槽下数据自动计量;PLC;技术改造1 背景在现代工业生产中,随着自动化程度的提高,PLC正得到越来越广泛的运用,尤其在操作流程多,操作要求精细的场合,用自动代替人工成为一种趋势。
如高炉炼铁所需要的焦炭、烧结矿、球团等原辅料都需要高炉上料系统运输到炉体内,高炉上料槽下转运由一系列的环节构成,首先将原辅料通过振动筛筛选过滤,再放入称量斗进行计量,计量后放入皮带进行运输作业,送至高炉上料小车。
在这一过程中,称量料斗是一个中间环节,其作用是暂时的存放物料并对物料称重计量。
人工累加每天的消耗量,工作烦琐容易出现差错,并可能存在一定的掺假、水分等,且对数据无法溯源。
高炉消耗量和料场打料量存在很大的误差,公司无法得到真实的原料消耗数据,不能满足企业ERP系统的发展需求。
2 系统结构及配置2.1 系统机械结构1.料斗,2.振动筛,3.扇形阀,4.称量传感器,5.支撑机构如图1所示,物料经过振动筛2筛分后进入料斗1,由称量传感器4测得实际的料重数据,在满足放料条件后,扇形阀3打开将物料放入料车,当放料结束后扇形阀自动关闭。
宣钢4#高炉槽下电子称重系统改造

导, 作 用 于受力 部分 即重量 传感 器上 产生 信号 , 这 就
要求 杠 杆 的 主要 部 位 “ 刀 刃” 处 必须保 持稳定 、 准
确, 不 能 积尘 且 无锈 、 无损 , 但 因长 期使 用 加 之 现场 粉 尘浓 度 大 , 刀 刃处 经 常 出现 积 尘 、 锈蚀 等 问题 , 造
新 的称量 系统 也 由机 械 和 电气 两 大 部 分 组 成 。
如图 1 所示 , 机 械部 分抛弃 了原 来 的机械 杠杆 , 每 台
秤 由 4个 重量 传 感 器直 接 受 力 于秤 斗 , 传 感器 上 端
固定 于支 架 , 下 端连 在秤 斗上 , 这样 称斗及 斗 中原 料
的重量 直接作 用 于 传感 器 上 , 消 除 了机 械 杠杆 式 称 量 系统所 存在 的 固有故 障 , 简 化 了秤体结 构 。 同时 , 秤 斗 四周增加 了一 定 的高度 , 扩大 了容量 , 量 程 也相 应 增大 , 适合 于 大料批装 料要 求 。其工 作过 程 : 给料 机 把原 料 放 入秤 斗 , 总体 重量 直 接 作用 于 4个 称重
选 型 和 设 备 调试 过 程 。 改 造 后 , 称重系统计量准确 、 稳定性好 , 为 高 炉 顺 行 提 供 了有 力 保 障 。
关键词 : 高炉 ; 电子称重系统 ; 改 造 中图分类号 : T F 3 2 1 . 2 文 献标 识 码 : B 文 章编 号 : 1 0 0 6— 5 0 0 8 ( 2 0 1 5 ) 0 5— 0 0 6 0— 0 4
0 7 5 1 0 0 )
Ab s t r a c t:Th e e l e c t r i c we i g hi n g s ys t e m u n d e r t h e g r o ov e of b l a s t f u na r c e No. 4 o f Xua n S t e l i s r e f o r me d t o s o l v e i t s pr o bl e ms :b a d s t a b i l i t y a nd i n a c c u r a t e me a s u r i n g. I t i s i nt r od u c e d i n d e t a i l t he p l a n, e q u i p me n t s e — l e c t i o n,a n d d e b ug gi n g p r o c e s s . Af t e r r e f o r ma t i o n t h e s y s t e m i s a c c u r a t e a nd s t e a d y, g ua r a n t e e s t h e s mo ot h o p e r a t i o n o f bl a s t f u r na c e. Ke y W o r ds :b l a s t f u na r c e;e l e c t r i c we i gh i n g s y s t e m ;r e f o r ma t i o n
浅谈分厂渣罐车新增电子秤的改造

浅谈分厂渣罐车新增电子秤的改造摘要:通过对《国务院关于钢铁行业化解过剩产能实现脱困发展的意见》以及《“十三五”钢铁工业调整升级规划》的解读,发展绿色循环经济已经成为国家钢铁战略的必然方向。
工业转型升级和绿色发展对资源综合利用提出了更高的要求,环境保护法治化越来越严格。
本着“提升企业素质和增强持续发展能力”等发展理念,为进一步建立完善公司生产全流程、管理全方位、红渣不出厂门,进一步提升钢渣的再利用。
结合目前公司推进的智能制造,促进生产的安全转型升级。
结合企业发展愿景,经过分厂领导及技术人员论证,针对分厂高温、高湿的接渣平车处增加无线式电子秤,取代了以往的凭经验生产,能做到每一罐的钢渣是精确的,渣罐的容积率能合理最大限度的利用,后期的热焖处理打水量有数据支撑,减少了吨水消耗。
关键词:接渣平车电子秤高温无线传送一、改造前状况江阴兴澄特种钢铁有限公司综合利用分厂于2021年4月投产,由中冶节能设计,当时接渣平车上没有设计电子秤,所有落料的接渣全部有工人观察及凭经验,每罐的接渣量误差可以达到五吨之内,有时为了多积料,需将平车带着渣罐往返开出来观察是否还能再多积一点料,对生产节奏及后续的热焖工艺打水量带来很大的影响。
为改善目前的现状,完善工艺要求,需在渣罐车上安装一套电子传感器,主要是为能满足生产过程中对渣罐的计量,来达到生产工艺上的要求。
二、渣罐车电子秤的基本要求:结合现有设备的实际情况,要求在改造渣罐车电子秤时,具体要求为:2.1、称量方式:车载电子秤形式。
2.2、最大称量范围:90t2.3、称量数据:稳定、可靠。
2.4、改造后的渣罐车电子秤满足现场综合精度:±0.5%的工艺要求。
2.5、保证设备安装电子秤后不影响设备的正常运行。
平车支架可以承重100吨重量。
2.6、为满足生产现场实际情况电子秤必须为耐高温+200~+250℃之内正常工作,允许过载300%,抗侧向力100%,允许偏载100%等要求。
高炉炉顶改造方案

1高炉炉顶改造案及配套系统情况(讨论)一、1#高炉炉顶改造案1、考虑斜桥角度不变,斜桥上部炉顶部位弯轨折点标高不变,降低高炉煤气封头高度794 mm,使炉顶大法兰和受料斗上沿距离为87 94mm。
2、在炉顶大法兰和受料斗上沿距离为8794 mm围布置受料斗、料罐、气密箱、布料器等装置,料罐有效容积为12m3。
3、溜槽长度1800mm,溜槽垂直高度下沿和炉吼钢砖上沿距离为335mm。
4、现有炉顶放散阀平台+47.415m提高为+47.50m,平台加大重新制作现有炉顶天轮标高+44.295m,提高为+45.015m。
(保留利用天轮平台)现有平台+39.400 m、+35.030 m、+33.000 m、+36.160 m、+27.200 m(炉顶大平台)、+24.3 m废除制作新平台+25.0 m、+31.360 m、+34.560 m、+41.00 m、+51.50m。
5、高炉煤气封头降低高度后,煤气封头角度变为48度,煤气封头角度变小后,不再能承载煤气上升管等的重力,将煤气上升管等的重力,由炉体承重转移至25.0 m平台,煤气导出管上装膨胀节(为防止煤气上升管等的重力传递到煤气封头上,钢和公司炼铁厂均装设有膨胀节)。
6、除煤气导出管和煤气上升管对接部分改造外,其它煤气上升管和下降管尽可能利用现有、不做变动。
对煤气封头到煤气下降管部分做喷涂。
#二、煤气二次均压目前1#450高炉系统煤气加压机能力小,勉强维持现有干除尘需要,考虑两个案。
1、2#450高炉系统煤气加压机能力富余,所以在2 #450高炉系统煤气加压机后的管道上设置两个阀门,实现分别用于对两座高炉炉顶进行二次均压。
2、将现有1#450高炉煤气加压机(型号不变)由3m3/min,加大为15 m3/min。
三、氮气系统2#450高炉系统(炉顶和风机)目前使用量约为250m3/h,两座高炉则为500 m3/h,留有余地应按600 m3/h考虑,选择以下其中一个案。
称量料斗的改进措施

分析 以上三点不足 , 问题均 围绕着不 需要更 换 的移动除尘罩和上部直段而产生 , 因此要想缩 短 检修 时 间 , 只移 动需要 更 换 的部 分是 最佳 选 择 。但是 , 需要更换部分 的下部锥体段却无法整 4 改进效 果 体移动。如果把锥体段改为几个部件拼接 而成 , 改进后维护和检修耗时 、 所需机具及人工大 即可实现在现有条件下方便 移出和移人 , 最后决 幅减 少 , 见表 1 。 定对 锥体 化整 为零 。 表 1 维护检修耗时对比 改进后 的锥体段 由4 J  ̄ 组成 , 每两片都采用螺 栓连接 , 组装成为立体的锥体段。这样一来 , 无须 移 动 笨 重 的除 尘 罩 和 上 部 直 段 , 整个 过 程 只 需 电 动扳手拆装螺栓 即可 。不仅降低 了检修难度 , 而 且大大缩短 了检修工期。 在 可 行 性方 面 , 改 进 前后 最 大 不 同之 处 在 于 , 锥体段的4 片采 用 现场 拼装 代替 了预先 焊接 , 因此 以下 两方 面需 要考 虑 : ( 1 ) 螺 栓 强 度 。假 设 本 体 和 物 料 的所 受 重 力 值得一提 的是 , 改进后 的锥体段 , 任何一面均 为 G, 本 体 与水 平 面 夹角 为 , 则 螺 栓所 受 拉力 为 可 以单独更换 。不仅降低 了成本 , 而且避免 了整 F 1 =G C O S , 剪力 为 F 2 =G s i n 。 体更换所带来的长时间停机。 因此 , 选 用满 足要 求 的螺栓 即可保 证 其 强 度 。锥体段 自重 5 . 6 t , 装料上 限为 1 5 t , 合计重量约 5 结 束语 2 1 t , 查 图 纸 可 知 约 为 5 6 。 ( 为 方 便计 算 以 6 0 。 通过称量 斗锥体段结构的改进 , 改变了之前 计) 。每 棱边 设 置 8 个 螺栓 , 一 共 有 螺栓 3 2 个 。故 整体进出的检修方法 , 简化 了锥体段检修流程 , 使 理 论 上单个 螺栓 最 大受力 为 : 得后续 维护更加便捷 。 目前工业生产 中 , 料斗使 拉力 F l =G C O S = 3 2 1 6 N 用 比较普遍 , 大多存在更换难度大和耗时长 的难 剪力 F : =G s i n = 5 5 7 0 N 题, 本改进具有一定借鉴意义。 ( 2 0 1 3 - 0 4 - 1 2 收稿 ) 根据机械设计手册高强度六角头螺栓技术条
高炉焦炭秤技改实践
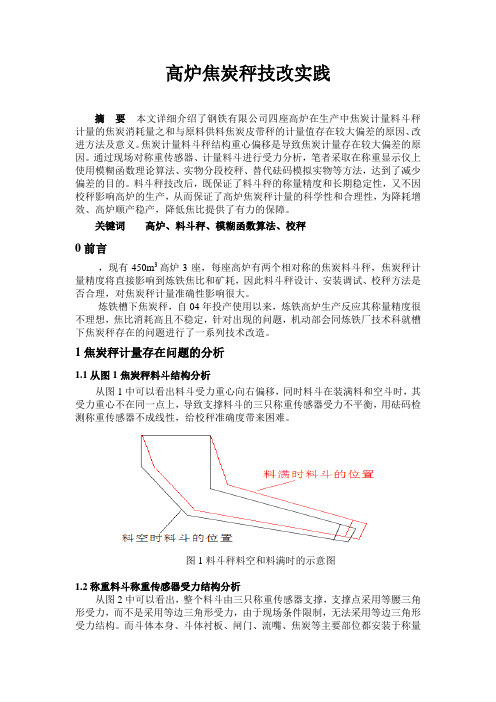
高炉焦炭秤技改实践摘要本文详细介绍了钢铁有限公司四座高炉在生产中焦炭计量料斗秤计量的焦炭消耗量之和与原料供料焦炭皮带秤的计量值存在较大偏差的原因、改进方法及意义。
焦炭计量料斗秤结构重心偏移是导致焦炭计量存在较大偏差的原因。
通过现场对称重传感器、计量料斗进行受力分析,笔者采取在称重显示仪上使用模糊函数理论算法、实物分段校秤、替代砝码模拟实物等方法,达到了减少偏差的目的。
料斗秤技改后,既保证了料斗秤的称量精度和长期稳定性,又不因校秤影响高炉的生产,从而保证了高炉焦炭秤计量的科学性和合理性,为降耗增效、高炉顺产稳产,降低焦比提供了有力的保障。
关键词高炉、料斗秤、模糊函数算法、校秤0前言,现有450m3高炉3座,每座高炉有两个相对称的焦炭料斗秤,焦炭秤计量精度将直接影响到炼铁焦比和矿耗,因此料斗秤设计、安装调试、校秤方法是否合理,对焦炭秤计量准确性影响很大。
炼铁槽下焦炭秤,自04年投产使用以来,炼铁高炉生产反应其称量精度很不理想,焦比消耗高且不稳定,针对出现的问题,机动部会同炼铁厂技术科就槽下焦炭秤存在的问题进行了一系列技术改造。
1焦炭秤计量存在问题的分析1.1从图1焦炭秤料斗结构分析从图1中可以看出料斗受力重心向右偏移,同时料斗在装满料和空斗时,其受力重心不在同一点上,导致支撑料斗的三只称重传感器受力不平衡,用砝码检测称重传感器不成线性,给校秤准确度带来困难。
图1料斗秤料空和料满时的示意图1.2称重料斗称重传感器受力结构分析从图2中可以看出,整个料斗由三只称重传感器支撑,支撑点采用等腰三角形受力,而不是采用等边三角形受力,由于现场条件限制,无法采用等边三角形受力结构。
而斗体本身、斗体衬板、闸门、流嘴、焦炭等主要部位都安装于称量斗前部分,使整个都斗的前部重量大于后半部分重量,造成三只称重传感器受力输出偏差较大。
1.3用测力计校秤方法不合理图2 称重传感器测力计受力简图从图2中可以看出,一只称重传感器一侧采用两个测力计施压校秤,而两只称重传感器一侧采用一个测力计施压校秤,很明显,在校秤过程中,每个测力计施加同样的压力,但每只传感器所输出的mv信号不一致,且偏差超过正常校秤范围,消除偏差难度大。
烧结机配料秤改造

烧结机配料秤改造郑丹君① 王宏 张军(宁波钢铁有限公司炼铁厂 浙江宁波315807)摘 要 为了维持烧结作业区烧结机配料秤配料精度。
逐一排查了配料秤如皮带跑偏、托辊积料、皮带积料等故障,并对皮带称进行一系列改良改造。
结果表明,改造后,秤的精度误差达到了允许范围之内,降低了故障率,满足了生产工艺的需求,保证了烧结矿的质量。
关键词 烧结 配料秤 误差 精度中图法分类号 TG8 TF325.1 文献标识码 BDoi:10 3969/j issn 1001-1269 2023 06 024ImprovingofthePrecisionofBatchingScaleofSinteringMachineZhengDanjun WangHong ZhangJun(NingboIron&SteelCo.,Ltd.,Ningbo315807)ABSTRACT Inordertomaintainthebatchingaccuracyofthesinteringmachinebatchingscaleinthesinteringoperationarea.Thefaultsofthebatchingscalessuchasbeltmistracking,idleraccumulation,beltaccumulation,etc.werecheckedonebyone,andaseriesofimprovementsandtransformationswerecarriedoutonthebeltscale.Theresultsshowthatafterthetransformation,theaccuracyerrorofthescalereachestheallowablerange,whichreducesthefailurerate,meetstheneedsoftheproductionprocess,andensuresthequalityofthesinter.KEYWORDS Sintering Batchingscale Error Precision1 前言宁波钢铁有限公司1#烧结机设计430m2,年产烧结矿443万t/a,于2006年6月投产。
高炉矿槽称重传感器的安装调试关键技术

37INSTALLATION2024.1赖志成(上海南汇建工建设(集团)有限公司 上海 201206)摘 要:本文以沙钢2#1080m ³高炉矿槽系统为例,详细介绍了称重传感器的安装与调试过程,包括称重传感器的安装要点、电气系统回路调试、称重传感器的系统标定、称重传感器使用故障及排查等。
保证了称重传感器的安装质量,减少了检修率,使矿槽系统顺利运行。
关键词:称重传感器 回路调试 系统标定 信号中图分类号:TH707 文献标识码:B 文章编号:1002-3607(2024)01-0037-03高炉矿槽称重传感器的安装调试关键技术近年来,随着科学技术的迅速发展,传感器的应用越来越广泛,对传感器的精确度要求越来越高。
在现代化的工业生产过程中,往往缺少不了传感器的辅助,尤其是在工艺性设备自动化生产过程中的各个参量,要使用各种传感器进行感应和转换,使工艺设备在自动化生产的过程中处于正常状态,并生产出达到质量要求的产品。
称重传感器以其较高的测量精确度及较大的称量范围在现代冶金行业的物位测控中得到了广泛的应用,在施工过程中,合理的称重传感器安装与调试是其发挥作用的基础[1]。
1 工程概况沙钢2#小高炉大修项目位于张家港市锦丰镇现沙钢厂内江堤东路以南,占地面积约为43,800m 2。
工程拟将原2#380m³高炉拆除,在原高炉地块处新建2#1080m³高炉。
高炉矿槽系统长70.85m,宽18.00m,高33.00m。
主要包括机械化运输系统、料仓,给料、筛分、称量设备、皮带输送机及焦丁回收设施等。
采用分散筛分、分散称量的工艺方式,所有入炉料均在槽下筛分、称量。
本工程结构类型以钢结构为主,主控制室、水泵房等为土建结构,包含大量的机电安装工程。
项目工期紧、任务重,在保证施工质量的前提下使用简单、实用、有效的施工方法能大大节省工期,为项目的如期交付打下 基础。
2 工程重点和难点施工环境复杂。
项目位于原有厂区内,临近有原料及烧结系统,在日常施工中,空气中的粉煤灰含量较大。
高炉槽下配料秤数字化控制的实现
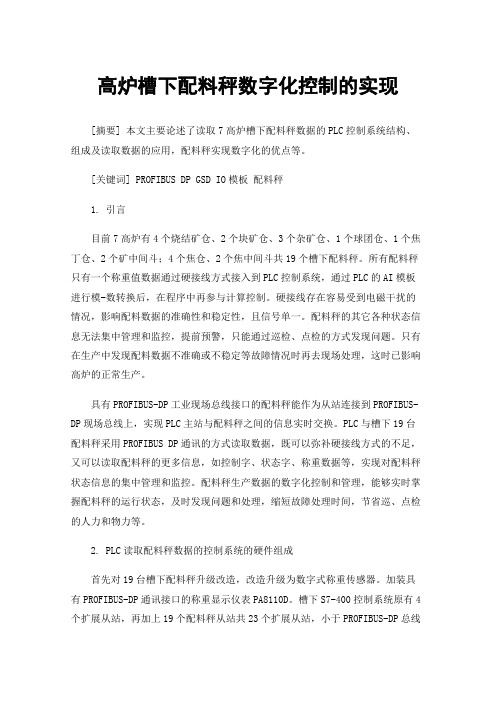
高炉槽下配料秤数字化控制的实现[摘要] 本文主要论述了读取7高炉槽下配料秤数据的PLC控制系统结构、组成及读取数据的应用,配料秤实现数字化的优点等。
[关键词] PROFIBUS DP GSD IO模板配料秤1. 引言目前7高炉有4个烧结矿仓、2个块矿仓、3个杂矿仓、1个球团仓、1个焦丁仓、2个矿中间斗;4个焦仓、2个焦中间斗共19个槽下配料秤。
所有配料秤只有一个称重值数据通过硬接线方式接入到PLC控制系统,通过PLC的AI模板进行模-数转换后,在程序中再参与计算控制。
硬接线存在容易受到电磁干扰的情况,影响配料数据的准确性和稳定性,且信号单一。
配料秤的其它各种状态信息无法集中管理和监控,提前预警,只能通过巡检、点检的方式发现问题。
只有在生产中发现配料数据不准确或不稳定等故障情况时再去现场处理,这时已影响高炉的正常生产。
具有PROFIBUS-DP工业现场总线接口的配料秤能作为从站连接到PROFIBUS-DP现场总线上,实现PLC主站与配料秤之间的信息实时交换。
PLC与槽下19台配料秤采用PROFIBUS DP通讯的方式读取数据,既可以弥补硬接线方式的不足,又可以读取配料秤的更多信息,如控制字、状态字、称重数据等,实现对配料秤状态信息的集中管理和监控。
配料秤生产数据的数字化控制和管理,能够实时掌握配料秤的运行状态,及时发现问题和处理,缩短故障处理时间,节省巡、点检的人力和物力等。
2. PLC读取配料秤数据的控制系统的硬件组成首先对19台槽下配料秤升级改造,改造升级为数字式称重传感器。
加装具有PROFIBUS-DP通讯接口的称重显示仪表PA8110D。
槽下S7-400控制系统原有4个扩展从站,再加上19个配料秤从站共23个扩展从站,小于PROFIBUS-DP总线扩展总站数32个,所以可以通过7高炉槽下S7-400 PLC控制系统的PROFIBUS-DP总线扩展完成配料秤的数据读取和控制,CPU通过PROFIBUS-DP 总线读取配料秤数据,PROFIBUS-DP数据通讯线通过单模光耦模块、光缆与槽下配料秤连接。
宁波钢铁有限公司高炉槽上小车自动加料的应用
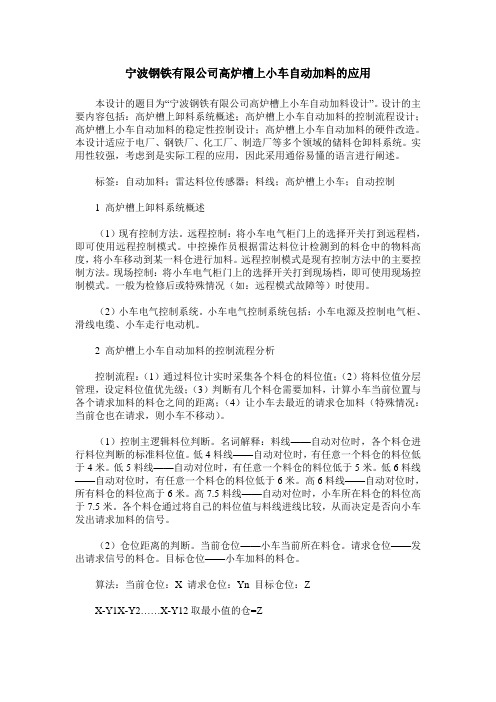
宁波钢铁有限公司高炉槽上小车自动加料的应用本设计的题目为“宁波钢铁有限公司高炉槽上小车自动加料设计”。
设计的主要内容包括:高炉槽上卸料系统概述;高炉槽上小车自动加料的控制流程设计;高炉槽上小车自动加料的稳定性控制设计;高炉槽上小车自动加料的硬件改造。
本设计适应于电厂、钢铁厂、化工厂、制造厂等多个领域的储料仓卸料系统。
实用性较强,考虑到是实际工程的应用,因此采用通俗易懂的语言进行阐述。
标签:自动加料;雷达料位传感器;料线;高炉槽上小车;自动控制1 高炉槽上卸料系统概述(1)现有控制方法。
远程控制:将小车电气柜门上的选择开关打到远程档,即可使用远程控制模式。
中控操作员根据雷达料位计检测到的料仓中的物料高度,将小车移动到某一料仓进行加料。
远程控制模式是现有控制方法中的主要控制方法。
现场控制:将小车电气柜门上的选择开关打到现场档,即可使用现场控制模式。
一般为检修后或特殊情况(如:远程模式故障等)时使用。
(2)小车电气控制系统。
小车电气控制系统包括:小车电源及控制电气柜、滑线电缆、小车走行电动机。
2 高炉槽上小车自动加料的控制流程分析控制流程:(1)通过料位计实时采集各个料仓的料位值;(2)将料位值分层管理,设定料位值优先级;(3)判断有几个料仓需要加料,计算小车当前位置与各个请求加料的料仓之间的距离;(4)让小车去最近的请求仓加料(特殊情况:当前仓也在请求,则小车不移动)。
(1)控制主逻辑料位判断。
名词解释:料线——自动对位时,各个料仓进行料位判断的标准料位值。
低4料线——自动对位时,有任意一个料仓的料位低于4米。
低5料线——自动对位时,有任意一个料仓的料位低于5米。
低6料线——自动对位时,有任意一个料仓的料位低于6米。
高6料线——自动对位时,所有料仓的料位高于6米。
高7.5料线——自动对位时,小车所在料仓的料位高于7.5米。
各个料仓通过将自己的料位值与料线进线比较,从而决定是否向小车发出请求加料的信号。
槽下计量系统改造

槽下计量系统改造本文以串行通信为例,介绍计算机与槽下称重显示表进行通信的软件架构体系;并以RS232串行通信标准,实现了数据自动采集处理的VF串行通信。
一.引言随着冶金行业竞争越来越强,成本问题显得越来越突出,炼铁成本更是是我们萍钢公司成本最关键的环节,它的成本也是最难控制的,作为服务于炼铁的单位计控,就是要将所有的计量设备做准,槽下计量就是关系到每个高炉成本数据的关键所在,具体体现在秤的准确性和上料采集系统的准确性两个方面,目前秤的精度经过定时校验等手段基本能控制在0.5%左右,应该可以说是没问题,现在关键是上料系统的PLC数据处理系统误差很大,它受工艺影响,如上料延时时间和提前量、下料延时时间和料空设定量、下料口关闭后的密封状况、模拟电流经过几个环节的误差情况、手自动操作的误操作等等诸多因素很难做准。
这次改造的目的就是撇开这些因素单独上一套计量数据采集系统来尽量保证其计量的准确性,从而保证这些数据能准确客观地反映炼铁的生产指标和成本核算。
二、思路首先不能采用4-20mA模拟信号传输,而采用RS-232C串行口传输方式,这样显示表显示得数据就和电脑上显示的一摸一样,没有了传输环节的误差;其次用软件来判断上料和下料开始及结束,这样就撇开了上料延时时间和提前量、下料延时时间和料空设定量、下料口关闭后的密封状况等工况的影响及手自动误操作的影响。
三、系统硬件组成及工作原理系统硬件:由一台计算机、MOXA多串口卡C320Turbo和MOXA扩展卡(含CPU卡)、YH3120G显示表三部分组成,通过RS232串行端口进行通讯。
工作原理:槽下秤YH3120G表连续不断地将动态称量数据连接到MOXA 扩展卡,经过CPU转换成数据总线信号,再通过C320Turbo多串口卡传到计算机,最后通过完善的计量软件进行采集和处理。
计算机以定时中断的方式读取数据,进行分析、处理、转换后将净重数据显示在第二窗口并保存整个称量过程的开始上料时间、上料结束时间、毛重值、开始放料时间、下料结束时间、皮重值及计算出的净重值等。
1#高炉槽下系统改造
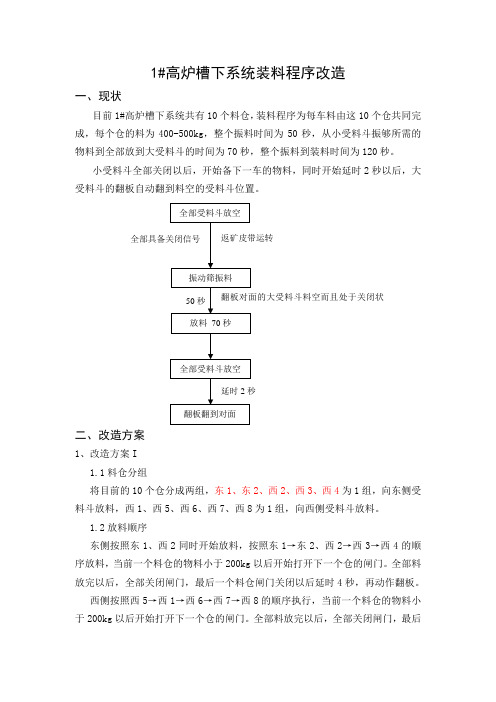
1#高炉槽下系统装料程序改造一、现状目前1#高炉槽下系统共有10个料仓,装料程序为每车料由这10个仓共同完成,每个仓的料为400-500kg,整个振料时间为50秒,从小受料斗振够所需的物料到全部放到大受料斗的时间为70秒,整个振料到装料时间为120秒。
小受料斗全部关闭以后,开始备下一车的物料,同时开始延时2秒以后,大受料斗的翻板自动翻到料空的受料斗位置。
二、改造方案1、改造方案I1.1料仓分组将目前的10个仓分成两组,东1、东2、西2、西3、西4为1组,向东侧受料斗放料,西1、西5、西6、西7、西8为1组,向西侧受料斗放料。
1.2放料顺序东侧按照东1、西2同时开始放料,按照东1→东2、西2→西3→西4的顺序放料,当前一个料仓的物料小于200kg以后开始打开下一个仓的闸门。
全部料放完以后,全部关闭闸门,最后一个料仓闸门关闭以后延时4秒,再动作翻板。
西侧按照西5→西1→西6→西7→西8的顺序执行,当前一个料仓的物料小于200kg以后开始打开下一个仓的闸门。
全部料放完以后,全部关闭闸门,最后一个料仓闸门关闭以后延时4秒,再动作翻板。
1.3料种的放置东2、西1为球团矿其余仓为烧结矿2、改造方案II放弃槽下翻板的功能,将其固定到中间位置。
1.1料仓分组将目前的10个仓分成两组,东1、东2为1组,向东侧受料斗放料,西1、——西8为1组,向西侧受料斗放料。
1.2放料顺序东侧按照东1→东2的顺序放料,当前一个料仓的物料小于200kg以后开始打开下一个仓的闸门。
西侧按照西1→西8的顺序执行,当前一个料仓的物料小于200kg以后开始打开下一个仓的闸门。
1.3料种的放置西2、西3为球团矿,其余仓为烧结矿。
东侧2个仓需要振够1车料,全部为烧结矿矿、西侧8个仓振1车料,球团矿为两车料的球团矿。
3、改造要求3.1两种方案都需要提高物料的仓口流速,要求各仓备料的时间控制到75秒以内,向大秤量斗的放料时间控制到55秒以内,这样包括放料以后的延时(5秒)在内,备两车料的时间为195秒,备两车料可以节约45秒。
- 1、下载文档前请自行甄别文档内容的完整性,平台不提供额外的编辑、内容补充、找答案等附加服务。
- 2、"仅部分预览"的文档,不可在线预览部分如存在完整性等问题,可反馈申请退款(可完整预览的文档不适用该条件!)。
- 3、如文档侵犯您的权益,请联系客服反馈,我们会尽快为您处理(人工客服工作时间:9:00-18:30)。
衡 往往 也 选用 此 结 构 的传 感 器 , 除精 度 高外 , 它 最 大 的优 点是 当料 斗 因基 座 振 动 等水 平 外 力 作用 消 失后, 由于钢 球 的 回位 和 限位 作用 , 不会 发 生料 斗
锈 和球碗 被粉尘 填满 而影 响 回位 , 钢球 和球 碗外 在 设 计专用 硅橡胶 制作 的波纹 套罩 住 , 并用 黄油 涂抹
槽秤 、 4台焦炭秤 、 1台焦 丁秤 。原 设 计 要 求称 量 精
度为 ±1 O ,0 9年 9月公 司提 出槽 下 配 料 称 量 .% 20
系统改 作炼 铁厂 高 炉铁水 成 本 核算 使 用 , 要求 称 量
精度要 求 达 到 ±0 5 。为 此 , 高槽 下 秤 称 量 精 .% 提 度成 为铁前 计量 的首要任 务 。
以 内的 目标 。
关键 词 : 下 系统 ; 斗秤 ; 量精度 ; 槽 料 称 改造
0 H 吾 I J
3 前期 安装 不规 范 , ) 称量 斗 和 混凝 土 边框 有 碰
擦 现象 , 使二 次仪 表信 号输 出线 性受 到影 响 。
4 现场 称量 斗周 围防护 不 到位 , 落 物料 清 理 ) 散 不及 时 , 造成 积料 或卡 料现 象 , 得称 量不稳 定 。 使
称重 传感 器选 型 。采 用 钢 球 承 载 桥 式 称 重 传
感 器 (Z C L—Y B一7—5 1/ 5 ) 替 换 目前 使 用 的 / 0 1 t来 双球 面 承载 的柱 式 传 感 器 ( Z C L—Y B一5 1/ 5 ) /0 1 t。 因该 传感 器 的弹性 体部 位 为工 字 剪切 梁 结构 , 有 具
21 月 三 0 年8 第 期 1
全
5 3
宁 钢 高 炉 槽 下 料 斗 秤 改 造
袁 小钟 王伟 同
3 50 ) 187 ( 波钢铁 有 限公 司炼铁 厂 宁 波 宁
摘
要 : 号 高 炉槽 下 系统 原设 计 1 1 7台料 斗秤 , 因设 计 、 装 、 安 维护 等 各种 原 因 , 量过 程 无 法达到 成 本核 称 算要 求 的称 量精度 。通过称 重 传感 器重 新选 型 、 重控 制 器更 换 , 称 实现料 斗 秤 称 重精 度 在 ±0 5 . %
冶全
良好 的抗侧 向力作 用及 加载 位置 变化 影 响小 , 测量 精 度高 、 动态性 能好 的特点 。精度 要求 很 高 的汽 车
21 月 三 0 年8 第 期 1
器处 于精确 的测 量位 置 和Leabharlann 斗 四 周存 在 预 留的 间
隙 。考虑 到炼铁槽 下环 境粉 尘较 多 , 防止钢 球生 为
积 量 比较 , 而在 称 量过程 中发现 问题 。 从 选 型参数 和 功能 如表 1 。
之 上 , 旦 振 动筛 启 动 运 行 , 称 量 斗 壳 体 造 成 冲 一 对
击 , 而使传感 器 受外 力作 用 , 响称 量精 度 。 从 影
2 经 常性 受振动 筛 的 冲击或 干 扰 , ) 引起 称 重传 感 器偏 移 , 致每 次 物 料 放 空后 , 秤 底 值 变 化不 导 空 同 , 大偏移 3( 最 t去除料 斗 积料 因素 ) 。
相 对 固定 的位置 。
从 投产 开始 运行 到 问题 提 出 , 后 2年多 的时 前 间 内 , 产 工 艺 根 据 报 表上 数 据 统 计 及 理 论分 析 , 生
始终认 为称 量不 准 , 为 动 态运 行 误 差 超 ±2 0 , 认 .%
而设备 人员 通过 定期对 料 斗秤 校 准 情况 看 , 度 达 精 到要 求 , 为查 明偏 差原 因 , 现场 环 境 、 对 秤体 结 构 等
5除尘 管 道 软 连 接 不 合 理 , 且 容 易 积料 , ) 并 如
积 料 长 时 问不 清 理 , 个 软 连 接 和管 道 连 成 一 体 , 整 对称 量斗 产生 额外作 用 力 。 6 由于 Se es 0 ) i n 0系歹 L m 4 UP C接受 工 业 标 准 信 号( 4~2 ) , 于 4 A时 , L 0 mA 低 m P C还 是 按 照 4 A处 m
进行 重 点查 看 、 据记 录 、 数 综合 分 析 得 出 , 成 运 行 造 过 程 中超差 的原 因有 以下 几个 方面 : 1振 动筛 底座 没有 固定 , ) 自然 地 放在 承 重 轨 道
2 称 重仪 表 模 拟 量 输 出信 号 ( ) 4~2 ) A具 有 Om 6 A信 号作 为 零 点 功 能 , 秤 重 量 具 有 累计 功 能 , m 且 实 现空仓 负 值 数 据 有 效 及 上 位 机 累 积 量 和仪 表 累
宁波 钢铁有 限公 司 1 高 炉 2 0 号 0 7年 5月 1日 投产 , 设计 炉容 20 m , 产 铁 水 2 0万 t所 用 原 50 3 年 0 ,
燃料 包 括烧 结 矿 、 矿 、 团 、 炭 等 几 大 类 , 下 块 球 焦 槽 配料称 量 系 统共 设 1 7台静 态料 斗秤 , 中 1 其 2台矿
钢 球 以防生锈 。
单 向移 位 现象 , 即具 有 自复位 性 能 , 终保 证传 感 始
表 1 称 量 系统 选型参数
称量 仪 表选 型 。原 使 用 济 南 金 钟 BQ一30 S 19 型 二次显 示 仪 表 , 仪 表 基 本 功 能 :R 该 S一22 3C一
理, 即秤体 值 为负值 时 ,L P C显 示仍 为零 。
2 解 决 方 案 及 措 施
2 1 称 量 系统选 型 .
l 现 状 分 析
1 1 原料 斗秤 运行 情况 .
依 据 现场 对称量 装 置 的分析 情 况 , 量 系 统重 称
新 选 型 , 型要 求 : 选 1称 重传 感 器 除满 足 温 度 、 度 、 尘 等环 境 ) 湿 粉 因素 外 , 须 具 有 自复位 性 能 , 得 称 重 前 后都 在 必 使