轧机伺服液压系统
偏八辊轧机液压伺服系统调试与改进

统压力和杆腔的 背压调整适 当,作液压 自身负载控
制 。压 下 液压 缸 上 下 运 动数 次 ,确 认 是 否满 足 位 置
的主要原因。找 出原 因后笔者首先提 出将底座与卷
取机的滚动摩擦副改为滑动摩擦导轨 ,在底座侧受
滤要求特 别严格 。在调试前必须对各路管道及系统
回路 进行 清洁 度 循 环 清 洗处 理 ,油 液 清 洁 度必 须 达
f l j NA S 1 6 3 8 5 ~6 级 ,相 当于q S O 4 4 0 6 标准2 0 / 1 8 级要
求。
状态 ,利 用动态调试 仪器和微机在线调试 ,测试 出 系统的特性 ,进一步校正参数 ,确定满足设计要求
盘车 ,转动灵活、无卡 阻现象后点动电动机确认 方
向 无 误 再 进 入 循 环 泵 及 主 泵 的 调 试 。 ④ 启 动 液 压 泵 ,将 液 压 系统 压 力 调 整 N o . 5 MP a ,拧 松 相 关 排
3 . 现场改进措 施
生 产过 程 中出现 开卷 机 纠 偏 系 统液 压 缸 外 泄 漏 和 工作 辊 夹 紧 不稳 定 问题 ,具体 改进 措 施如 下 : ( I )EP C  ̄ q 偏 系 统 的 伺 服 液 压 缸 使 用一 段 时
处理板、电源板 、编程器板等组成 ,输入板共有 1 4 块 ,用于接收继 电器和光 电管来的信号。输 出板有 2块 ,1 1 2 个直流输 出点,7 2 个交流输出点 ,整机
约4 0 8 个 点 ,控 制 四个 动 力头 上 、 下左 右移 动 及 工 作 台前 后 移 动 ,该 系统 应 用极 不 广 泛 。为 此 ,我 厂 与 北 京机 床 研 究 所 下 属 机 电公 司 合作 对 K2 4 数 控 装
四辊轧机液压压下装置液压系统设计
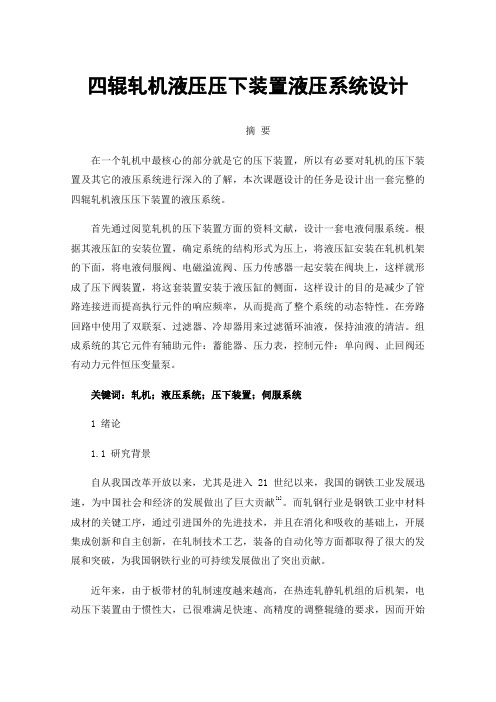
四辊轧机液压压下装置液压系统设计摘要在一个轧机中最核心的部分就是它的压下装置,所以有必要对轧机的压下装置及其它的液压系统进行深入的了解,本次课题设计的任务是设计出一套完整的四辊轧机液压压下装置的液压系统。
首先通过阅览轧机的压下装置方面的资料文献,设计一套电液伺服系统。
根据其液压缸的安装位置,确定系统的结构形式为压上,将液压缸安装在轧机机架的下面,将电液伺服阀、电磁溢流阀、压力传感器一起安装在阀块上,这样就形成了压下阀装置,将这套装置安装于液压缸的侧面,这样设计的目的是减少了管路连接进而提高执行元件的响应频率,从而提高了整个系统的动态特性。
在旁路回路中使用了双联泵、过滤器、冷却器用来过滤循环油液,保持油液的清洁。
组成系统的其它元件有辅助元件:蓄能器、压力表,控制元件:单向阀、止回阀还有动力元件恒压变量泵。
关键词:轧机;液压系统;压下装置;伺服系统1 绪论1.1 研究背景自从我国改革开放以来,尤其是进入21世纪以来,我国的钢铁工业发展迅速,为中国社会和经济的发展做出了巨大贡献[1]。
而轧钢行业是钢铁工业中材料成材的关键工序,通过引进国外的先进技术,并且在消化和吸收的基础上,开展集成创新和自主创新,在轧制技术工艺,装备的自动化等方面都取得了很大的发展和突破,为我国钢铁行业的可持续发展做出了突出贡献。
近年来,由于板带材的轧制速度越来越高,在热连轧静轧机组的后机架,电动压下装置由于惯性大,已很难满足快速、高精度的调整辊缝的要求,因而开始采用电动压下与液压压下相结合的压下方式[2]。
在现代化的冷连轧机组中,几乎已全部采用液压压下装置。
1.3 本课题主要研究内容本课题主要是设计一套四辊轧机压下装置的液压系统,以前冷轧机的压下装置是靠大功率电动机带动牌坊顶部的蜗轮蜗杆和压下螺丝来实现的,自从采用液压技术后,轧制速度提高了10倍以上,精度也大大提高了。
采用液压压下系统的轧机一旦发现误差,能以极短的时间调整辊缝。
所以有必要对轧机液压压下装置进行研究,具体内容如下:(1)首先查阅轧机压下装置液压系统方面的相关资料,了解压下装置的工作原理并对组成压下装置液压系统中的电液伺服阀有一定了解,伺服阀是液压系统中最关键的元件,是液压系统同电气系统的连接元件。
浅谈伺服阀在轧机液压系统的使用与维护
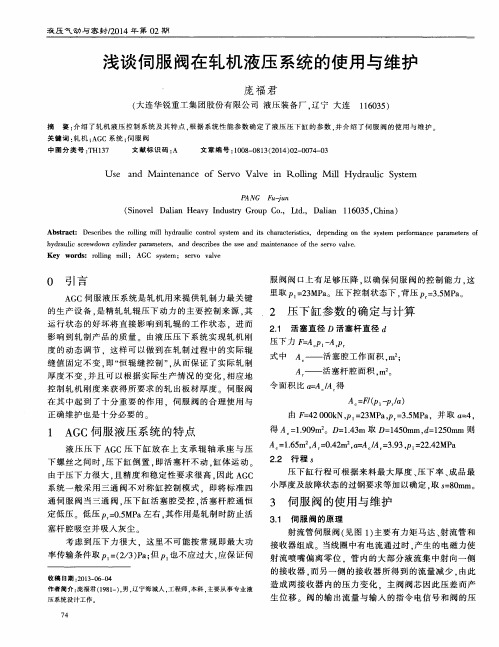
1 AG C伺 服 液 压 系 统 的特 点
液压压下 A G C压 下 缸 放 在 上 支 承 辊 轴 承 座 与 压
下螺 丝 之 间时 , 压 下 缸倒 置 , 即活 塞杆 不 动 , 缸 体 运动 。 由于 压下 力很 大 . 且 精 度 和稳 定性 要求 很 高 . 因此 AG C 系统 一 般采 用 三通 阀不 对 称缸 控 制模 式 .即将标 准 四 通 伺 服 阀 当三 通 阀 . 压下 缸 活 塞 腔受 控 . 活 塞 杆 腔通 恒
0 引 言
A G C伺服 液 压 系统 是轧 机 用来 提供 轧 制力 最 关键 的生 产设 备 . 是 精 轧 轧辊 压 下 动力 的主要 控 制来 源 . 其 运 行 状 态 的好 坏将 直 接 影 响到 轧 辊 的工 作 状 态 .进 而 影 响 到 轧制 产 品 的质 量 由液 压 压下 系 统 实现 轧 机 刚 度 的动 态调 节 .这 样 可 以做 到 在 轧制 过 程 中的实 际 辊 缝 值 固定 不 变 . 即“ 恒 辊 缝控 制 ” . 从 而保 证 了实 际轧 制 厚 度 不变 . 并 且 可 以 根据 实 际 生产 情 况 的变 化 . 相 应 地 控 制 轧机 刚度来 获 得 所 要求 的轧 出板 材 厚 度 伺 服 阀 在 其 中起 到 了十分 重 要 的作 用 .伺 服 阀 的合 理使 用 与 正 确维 护 也是 十分 必要 的。
式中
Hale Waihona Puke A — — 活塞 腔 工作 面积 , m z ;
A —— 活塞杆 腔 面积 。 m z 。
冷带轧机液压压下伺服系统模型算法控制应用研究
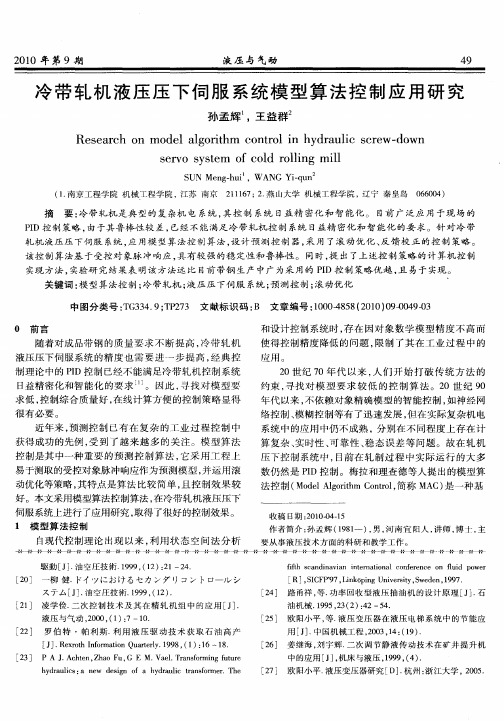
2 0世纪 7 0年代 以 来 , 们 开 始 打 破 传 统 方 法 的 人 约束 , 找 对 模 型要 求 较 低 的控 制 算 法 。2 寻 O世 纪 9 O 年代 以来 , 依赖 对 象精确 模 型 的智能 控制 , 不 如神 经 网 络控 制 、 模糊 控制 等有 了迅 速 发展 , 但在 实 际复杂 机 电 系统 中的应 用 中仍不 成熟 ,分别 在 不 同程度 上 存 在计
收 稿 日期 :000 —5 2 1 - 1 4
作者简介 : 孟辉 (9 1 )男 , 南宦 阳人 , 师 , 十 , 孙 18 ~ , 河 讲 博 主
自现 代控 制理 论 出现 以来 , 用 状 态 空 间 法分 析 利
驱 勤 [ ] 油 空 压 技 衍 .9 9 ( 2 :1 4 J. 19 , 1 ) 2 —2 .
21 0 0年 第 9期
液 压 与 气动
4 9
冷 带 轧 机 液 压 压 下 伺 服 系 统 模 型 算 法 控 制 应 用 研 究
孙 孟 辉 王 益 群 ,
Re e r h o d l ag rt m o to n h d a l c e d wn s a c n mo e l o i h c n r li y r u i s r w— o c
s r o s se o o d r li g mi e v y t m f c l o l l n l
S UN n — u .W ANG — u Me g h i Yiq n
( . 京 工 程 学 院 机 械 工 程 学 院 ,江 苏 南 京 1南
2 16 ; . 山 大学 机 械 工程 学 院 , 宁 秦 皇 岛 1 17 2 燕 辽
油 机 械 .9 5 2 ( )4 5 . 19 ,3 2 :2— 4
轧机AGC液压系统

轧机AGC液压系统、弯辊抽动伺服液压系统,活套液压控制系统,助卷辊液压系统,卷筒液压系统、侧导板液压系统、轧机AWC液压系统等等。
主要维护原则钢铁冶金液压系统泵站集中,元件种类多,要求的精度也有不同,设备属于大型复杂的生产线,可靠性要求高,加之连续作业往往没有足够检修时间对液压系统进行维护保养。
这就决定生产线的液压系统故障多而复杂,排除难度大任务重。
液压事故诊断的基本要求:正确、精确、简洁、快速、超前。
诊断技术发展,不解体化、高精度化、智能化、网络化。
液压系统出现故障时不易找出原因、排查困难,现将在工作中积累的一些经验和方法归纳,以供参考。
一是排除法,一样一样的排除,二是经验法,对生产现场很了解,对出问题的地方也有经常性的,很快就能找到出问题原因。
三是综合法,排除法和经验都一起来诊断事故,效果好更好些。
对于一般的原则:先排除外围在处理内部,伺服系统先电器后机械最后是液压。
一、望:看到什么。
1、看系统的配置是否正常,包括:泵、阀、执行元件、工作油液、滤油器、散热器等;2、看速度(流量):看执行机构运动速度是否有异常现象;3、看压力:看液压系统中各测压点的压力值大小及波动;4、看油液:观察油液容量是否合适,是否清洁,有无变质,油中是否有泡等;5、看泄漏:看液压管道各接头处、阀板结合处、液压缸端盖处、液压泵轴伸出处是否有渗漏、滴漏和油垢现象。
二、闻:听到什么。
1、听噪声:判断听到的声音是否属于噪声,噪声的源头在哪,是液压泵、马达、阀等液压件还是系统的管路或与元件连接的工作机构。
2、听冲击声:听系统的冲击声是否属于正常。
冲击声的时间:液压阀换向时冲击,还是莫名地发声。
冲击声的规律性:有节奏还是无规律。
3、听泄漏声:听油路内是否有细微不断的声音。
4、听敲打声:听液压件运转时是否有敲打声。
5、听相关人员反映。
三、摸:感觉到什么。
1、摸温升:用手摸运动部件表面,检查是否发热。
2、摸振动:感觉是否有振动现象。
3、摸爬行:感觉运动件有无“爬行”现象。
热轧生产线上伺服系统的应用与维护

热轧生产线上伺服系统的应用与维护热轧厂生产的过程中,轧机系统作为其核心设备,有着重要的作用。
伺服系统是轧机的控制大脑,伺服系统分散到轧机的各个部位,有利于热轧生产线的稳定和安全。
通过对热轧生产线的伺服系统进行研究,分析其生产中的运行情况,找出存在的问题以及原因,采取有效的实施方案,从多个层面保证伺服控制系统的稳定和精确。
文章对热轧生产上的伺服系统的应用和维护进行探究,以供参考。
标签:热轧生产线;伺服系统;应用;维护液压伺服系统的控制精度高,反应速度快,并且系统具有非常大的刚性,在船舶、航空以及冶金等行业普遍的应用。
同时伺服阀对油液的污染具有非常强的敏感度,精度要求非常高,在使用和维护的过程中存在一定的难度。
在热轧生产的过程中,伺服系统会出现不正常工作的情况,需要对其进行分析,了解不正常工作的原因,提出相应的解决方案,保证热轧生产安全、稳定的开展。
1 热轧生产线上伺服系统存在的问题和原因(1)伺服系统不动作。
此种问题主要的表现是现场无动作,可以通过以下几点检查进行故障的处理。
首先,电气专业人员对伺服阀的给定电压进行检查,是否能够到达伺服阀,中间线路的绝缘性是否存在降低的情况,伺服阀的插头位置是否存在虚接、断线以及脱焊的情况。
在检查时,可以通过程序中的伺服阀进行测量验证或者借助伺服阀测试台开展检查工作。
其次,机械专业检查人员检查在检修和维护的过程中,进出油口是否存在接反情况。
如果上述检查正常,可以进行先导级或者过滤器的检查,是否存在堵塞的情况。
最后,对阀芯进行检查,是否存在卡死的情况。
(2)伺服阀存在固定输出但是出现失控情况。
此种问题通常的表现是电气输出是正常的,但是伺服阀的动作和电气不成对应关系,或者出现来回的波动。
伺服阀出现此种故障的原因有以下几点:前置级堵死或者喷嘴被堵塞等,阀芯被卡住,阀体、阀套出现变形的情况,导致伺服系统出现波动。
过滤器如果出现堵塞的情况,也会造成伺服阀输出出现失控的情况。
轧机的液压压下装置

轧机的液压压下装置液压压下装置是轧机中非常重要的组成部分,它主要用于在轧制过程中对轧辊进行压下,以使金属材料在轧制过程中得到良好的形状和尺寸。
液压压下装置一般由液压系统、主缸、液压缸、液压管路等部分组成。
下面将从这几个方面对液压压下装置作详细介绍。
一、液压系统液压系统是液压压下装置中最为核心的部分,它主要由油箱、油泵、阀门和油管等组成。
油箱主要用于储存液压油,并且在油箱中放置油滤器和油温计等,以确保液压系统中的油液清洁和温度适宜。
油泵的作用是将液压油从油箱中抽出并送入液压缸内,从而使液压缸对轧辊进行压下。
油泵一般有液压柱塞泵、液压齿轮泵和液压叶片泵等几种类型。
阀门主要用于控制液压系统中的液压油流动方向、流量和压力等参数,以实现对液压压下装置的控制。
油管主要用于将液压系统中的液压油输送到液压缸中,并且使液压油在液压缸内进行压力传递。
二、主缸主缸是液压压下装置中的一个重要部件,它主要由液压缸筒、活塞、活塞杆、活塞密封等组成。
液压缸筒一般由优质的合金钢材料制造而成,并且经过热处理和精密加工等工艺,以确保其具有足够的强度和刚性。
活塞是主缸内部的运动部件,它的作用是在液压压下装置工作时对轧辊进行压下,从而使金属材料在轧制过程中得到压制和塑性变形。
活塞杆是连接活塞和液压缸筒的部件,它的结构要求具有足够的强度和刚性,以承受液压压下装置工作时产生的巨大作用力。
活塞密封是主缸内部的关键部件,它的作用是防止液压缸内的液压油泄漏,并且保证液压系统的密封性和工作可靠性。
四、液压管路液压管路是液压压下装置中非常重要的部分,它主要由液压管、接头、接头密封等组成。
液压管一般由优质的碳钢管或不锈钢管制造而成,并经过加工和抛光等工艺,以确保其具有足够的强度和耐腐蚀性。
接头主要用于连接液压管和液压缸、液压泵、阀门等部件,使液压油能够顺畅流动。
接头密封一般采用油封圈、O型圈等密封件,它的作用是防止液压管路中的液压油泄漏,并且保持液压系统的密封性和工作可靠性。
中板轧机HGC伺服液压缸的结构设计

中板轧机 HGC伺服液压缸的结构设计现代的热轧生产线中配置了许多不同的液压系统,液压油缸作为液压系统的执行机构也被大量使用。
根据热轧生产线设备配置不同所用液压油缸的数量、种类和型式而有所差异,按照油缸所使用的部位不同来分就有几十种之多。
其中就有许多液压伺服系统中使用的液压缸,一般称为伺服液压缸。
由于设备结构参数以及控制要求的不同,对伺服液压缸的要求也不一样,不同系统伺服液压缸的组成、结构、规格、材料都不尽相同,所以基本上都是非标设计。
伺服液压系统是液压技术的高精尖领域,其伺服液压缸与普通液压缸的设计及参数要求有许多不同之处,它是为控制设计的,更看重动态性能。
在伺服系统中它会直接影响了系统的动态响应,控制精度,稳定性等等。
具体来讲,伺服油缸与传统油缸以下不同:在功用方面:传动液压缸作为动执行元件,用于驱动工作负载,实现工作循环运动,满足常规运动速度及平稳性要求;伺服液压缸作为控制执行元件用于高频下驱动负工作负载,实现高精度、高响应伺服控制。
在强度及结构方面:1.强度传动液压缸满足工作压力和冲击压力下工作要求;伺服液压缸满足工作压力和高频冲击压力下工作要求,因此其厚度尺寸往往是超过正常的强度设计计算值,偏于安全,即比普通液压缸的壁厚要失。
2.刚度传动液压缸一般无特别要求;伺服液压缸要求高刚度,即活塞杆的细长比要很小,否则执行元件的唱有频率念下降得承出下降很多,,缸的底座不仅能够满足支承缸的受力要求,3.稳定性传动液压缸满足压杆稳妥定性要求;伺服液压缸满足压杆高稳定性要求。
4.导向传动液压缸要求有良好的导问性能,满足重载或偏载要求;伺服液压缸要求有良好的导向性能,满足高频下的重载、偏载要求。
5.连接间隙传动液压缸连接部位配合良好无较大间隙;伺服液压缸连接部位配合优良,不允许存在游隙。
6.缓冲传动液压缸高速运动时应能满足在行程终点时缓冲;伺服液压缸不碰缸底不需要考虑缓冲装置。
7.安装传动液压缸只需考虑缸体与机座、活塞杆与工作机构的连接;伺服液压缸除了考虑缸体与机座、活塞杆与工作机构的连接,还要考虑传感器及伺服控制阀组的安装。
可逆式轧机液压伺服系统污染及控制

( agS a o n te Co, t. tpCo ln l t 1T n h nI nadSel .Ld Sr l Rol gPa ; r i d i n 2He B i n ryS ucs c pt nT c n lg ae ) i e E eg o re Ocu a o eh oo Acd my i y
6 0高压 液压 系统工 作原 理 图如 图 l 示 . 图看 1 所 从 出在 线过 滤器 精度 是 3x t m。循 环 过滤器 精度 是 1 t 0x m。 从过 滤器精 度看应能 满足该 系统工作 要求 , 但设 备经 过
一
排查 , 确定该 系统 的污染 源主要来 自以下几个 方面 。
Ab t a t i p p ra a y e h o re a d c n r l f o lt n o e e sn l h d a l ev y tm, mp a ie h s e t l y o n s r c : s a e n l s st e s u c n o t l i n r v ri g mi y r u i s ro s s Th o op uo l c e e h sz st e e s n i i fma - at a e n n p l t n r b i st e cr u ain f t t n wh c n e s n b e a d i g t r mak b ee e to r d ci n g me t ol i , e u l h i lt l a i ih u r a o a l, n es e r a l f c n p o u t o u o d c o ir o t o Ke o d : S u c f ol t n yW r s o r e o l i ; C n o ; R t r l o lt i r t P u o otl r e u n Oi C mpe e F l ae t
轧机液压系统故障攻关及国产化改造

图2 P 2 尘 圈 T防
A3
2 液 压 系 统对 密封 的影 响 .
Al d
伺服液压缸 的有杆腔压力为系统压力 ,中间无控制 阀, 当液压杆无负载 时,有杆腔始终保持约3 M a 0 P 的高压 ,对密 封元件 影响极 大。 由于缸外杂质 的侵入 ,使O — 型杆 封 MS S 磨损 ,造成密封 圈无压侧被挤出定位槽 ,进而迅速损坏 。
试制过程 中 , 计将精度 等级 d7 提高到6 , 合此 液 设 a级 级 结
压缸 的工况 ,对活塞杆 的不 圆度 、不柱度均要求 ≤00 rm。 .1 a 缸筒 表 面活 塞 杆表 面 粗糙 度 R ≤02 m,缸筒 材 质 选 用 a .
油缸缸体
4 G M 锻件 ,活 塞杆材质选用4 C 锻件调质处 理 ,外表 面 2rn 0r
2 工况分析 . 在轧制过程 中,水平 伺服液 压缸用 于调整上 、下水平
中标 号2 5 0 所示) ,该 防尘圈 由一个带 有密封 刃 口和 防尘刃 口的P F 异形 圈和二 个用作 预加载元 件 的O 圈组成 的双 TE 形 唇 口防尘 圈 ( 如图2 所示) ,材料是P F / 铜复合材料 ,具 T E青
3 MP ,可调整压 力至2 M a 0 a 0 P ,因此所选三通减 压阀能满足 使 用要求 。预计将有 杆腔压力 降至9 P ,同步在T S Ma C 系统 ( 电气 控制程 序) 中 以计算 轧制 力为结 果 的相关参 数 作修 改 ,具体计算 如下 。
受力分析见图3 。
A。
尘 刃 口
1 密封损坏原 因分析 .
对 损坏 的伺 服液压缸解 体发现 ,防尘 圈 、密封 圈定位
槽 及导 向环 内均堆满 粉末状污物 ,甚 至部 分导 向环 出现非
650单机架可逆冷轧机AGC液压伺服系统设计毕业论文
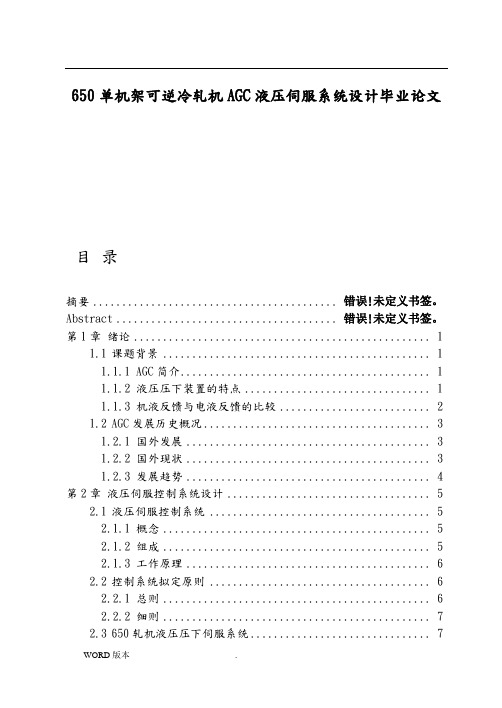
3.3液压泵的选择13
3.3.1主泵——轴向柱塞泵13
3.3.2辅泵——叶片泵14
3.4电机的选择15
3.5阀类元件的选择15
3.5.1减压阀15
3.5.2电磁溢流阀15
3.5.3单向阀16
3.5.4电磁换向阀16
3.5.5电磁水阀16
3.5.6截止阀16
3.6液压附件的选择16
电液反馈式的主要优点是系统的惯性小,反应灵敏。随着电液伺服阀的可靠性的提高和自动控制技术的日益发展,采用这种形式的液压压下轧机逐渐增多。
液压压下装置的可靠性主要取决于液压元件和控制系统的可靠性。液压压下装置要求较高的备品制造精度和设备维护水平以及可靠的自动化系统。
钢铁工业迅速发展的今天,钢材市场的竞争愈演愈烈。随着国民经济的高速发展,科学技术不断进步,汽车、机械制造、电器和电子行业对板带材的质量提出了更高的要求。对于板带钢来说,如何生产出厚度、宽度、板形、板凸度、平面形状等指标都符合实际需要的产品是关键的技术所在。
3.6.1蓄能器16
3.6.2过滤器18
3.6.3温度计19
3.6.4电加热器19
3.6.5液位计20
3.6.6减震喉20
3.6.7橡胶接管20
3.6.8测压排气接头20
3.6.9压力表20
3.6.10冷却器20
3.6.11安全截止阀块21
3.6.12位置传感器22
3.6.13压力传感器22
3.6.14压力继电器22
1.
近年来,国外在板形和板厚等控制技术方面取得了许多新的进展。
国外早在五十年代就开始在电动机械压下轧机上采用AGC控制技术以提高带材纵向厚度精度。国外轧机的厚度控制应用于电动机械轧机和液压轧机、冷轧机和热轧机、连轧机和单机架轧机。近30年来,国外轧机的装备水平发展很快。在冷带轧机上广发利用液压压下、液压弯辊、厚度自动控制、板形控制和计算机控制等技术,在新技术运用方面均已采用液压AGC系统与计算机控制相结合的DCS,装设了测量精度高的三测仪表(测厚、测压、测),且装设了板形检测装置。人工智能(AI)技术已经广泛应用 ,包括模糊控制(FZ)、专家系统( ES)和人工神经元网络(ANN)技术在 AGC系统中的应用,已经取得了巨大成果和经济效益。
轧机AGC液压系统常见故障及处理

轧机AGC系统故障及处理河北邯钢冷轧薄板有限公司目前拥有一条1550单机架六辊可逆轧机,设计年产量20万吨,轧机采用液压压上方式,实现AGC自动控制,本文主要结合在实际生产中出现的故障进行分析和总结。
1 AGC系统原理AGC系统又称为自动辊缝控制系统(automatic roll gauge control),AGC系统在轧机应用领域中的工作原理是当轧机的轧制力发生变化就会实现轧机的自动补偿和调整动作,用测厚仪测得板材实际厚度与给定厚度比较,将偏差以电压的形式通过伺服阀达到控制液压缸的动作,调整轧机的轧辊辊缝,从而使出口板厚恒定,保证产品的目标厚度,同板差、异板差达到性能指标要求。
该轧机有2个压上缸,分别位于操作侧和驱动侧,每个压上缸各有1个压力传感器、伺服阀和电磁溢流阀。
伺服阀的供油管路前后各有1个液控单向阀。
压上缸压上时2个单向阀处于开通状态,电磁溢流阀做溢流阀用(压上缸的进油口压力大于调定压力时溢流)。
压上缸下降时电磁溢流阀换向进行卸荷,液控单向阀关闭油路对伺服阀进行保护。
2 AGC系统故障分析及处理2.1两侧AGC液压缸从快抬位置(228mm)快速上升到10mm辊缝位置的过程中,一侧无动作导致倾斜超限。
可能引起该现象的原因有:2.1.1电磁溢流阀阀芯卡死,一直在进行卸荷。
判断是否卡死的依据有电磁溢流阀是否异常发热和是否有卸荷的声音。
处理方法--更换电磁溢流阀,需要注意的是更换完成后需要调节新阀至指定的溢流压力值;2.1.2 伺服阀航空插头里的信号线发生脱落,表现为伺服阀给定值和反馈值相差超过5%,处理方法更换航空插头;2.1.3 伺服阀内泄严重,更换伺服阀;2.2 换辊后在校辊过程中到轧制力差清零步骤时,两侧液压缸位置倾斜大于0.7mm报警无法正常校辊,可能的原因有:2.2.1 中间辊或工作辊安装偏差大。
通过观察在压上至标定轧制力过程中轧制力和两侧AGC缸位置变化,如位置变化同步,完成后轧制力差大于200KN,处理方法换辊;或者压力传感器异常,更换压力传感器;2.2.2 如AGC缸位置变化不同步,观察哪一侧与辊缝变化相差大,更换伺服阀此外在生产中还出现过因伺服阀零位磨损较大引起的液压缸轻微跳动、电磁溢流阀插头虚接引起的液压缸卡顿等现象。
轧机的液压润滑系统及其管理

设备管理轧机的液压润滑系统及其管理宋春阳(常德中联重科液压有限公司,湖南 常德 415001)摘 要:液压润滑系统是轧机的重要组成部分,其性能的优劣对轧机的性能有着重要的影响,对各个系统进行了介绍并对系统运行中的注意事项进行了总结。
关键词:轧机;液压润滑系统;板形;生产效率液压润滑系统是轧机的重要组成部分,液压系统用于控制轧机中液压执行元件的动作,润滑系统用于实现关键部件的润滑,液压润滑系统性能的优劣对轧机的性能有着重要的影响,工作不好的系统将导致整台轧机不能正常运行。
文章分系统进行介绍并结合实际对液压润滑系统运行中的注意事项进行了总结。
1液压系统液压系统用于控制轧机中所有液压执行元件的动作,根据执行元件工作压力的高低及对油品的要求分为两个系统:高压伺服系统和低压系统。
1.1高压伺服系统高压伺服系统用于控制轧机中AGC液压压下油缸、工作辊弯辊油缸、中间辊弯辊油缸和横移油缸及支承辊平衡油缸。
AGC液压压下部分用于控制AGC液压压下油缸以实现轧机的辊缝给定与控制,其与测厚仪及压下油缸装置构成轧机的辊缝闭环控制,对轧机的性能有着极大的影响,直接决定带材的厚差质量。
液压弯辊、横移控制系统用于工作辊弯辊、中间辊弯辊控制及中间辊的横移控制。
其中操作侧工作辊弯辊、传动侧工作辊弯辊及中间辊弯辊用于轧机带材板形的手动给定控制,以达到控制带材板形的目的。
中间辊横移系统用于轧制前,根据来料宽度情况预设定中间辊的位置,轧制时确保中间辊的位置保持不变。
这几个系统属于板形控制部分,决定着成品带材的板形质量。
支承辊平衡用于平衡上支承辊的重量以消除轧制过程中上支撑辊重量对轧制的影响。
高压伺服系统工作压力高,且使用伺服阀及比例阀较多,故要求较高,油液清洁度要求6级及以上,同时要求压力波动小,目前国内生产元件性能不易达到,故多采用进口件。
1.2低压系统低压系统用于对全机组中普通的液压油缸及液压马达进行传动和控制。
其根据轧机中普通油缸及液压马达的数量有着众多的控制回路,每个回路实现一个机械执行机构动作的控制。
综合实训--六辊板带可逆冷轧机液压伺服控制系统

1150mm六辊板带可逆冷轧机液压伺服控制系统目录目录第1章绪论 (1)1.1轧机位置控制系统发展情况 (1)1.1.1 液压位置控制系统发展情况 (1)1.1.2 控制理论及技术的发展 (1)1.2国内外研究情况简介 (6)1.2.1 国外概况 (6)1.2.2 国内概况 (7)第2章液压系统原理的设计 (8)2.1技术及工艺要求 (8)2.1.1 系统的要求 (8)第3章液压伺服控制系统设计 (9)3.1液压伺服板厚控制的基本原理 (9)3.2轧机数字闭环厚度控制 (10)1.1 轧机位置控制系统发展情况:第一种是手动压下调节板厚。
最早的轧机是靠手动调节压下螺丝来进行辊缝调节的。
这种调节方式仅能设定原始辊缝,无法达到厚度控制精度的要求,因而在板带轧机上已经基本不再采用。
第二种是电动压下调节板厚。
手动压下的调节方式缺点很多,所以在电机出现之后,人们就将它用到轧机上.不仅采用电机驱动,而且压下调节也采用电动方式,由电机通过减速装置驱动压下螺丝来设定原始辊缝。
这种调节方式一般不能在线调节,无法保证严格的厚度精度,因而目前只在开坯和厚板轧机上使用,板带轧机上很少用。
第三种是液压压下调节板厚。
1.1.1液压位置控制系统发展情况:(1)是电—液双压下系统调节装置。
电—液双压下系统也是由粗调和精调两部分组成的,其中粗调部分就是一般的电动压下装置,用它来设定原始辊缝。
精调部分采用液压系统,其具体结构方式有多种。
如用液压缸推动扇形齿轮以带动压下螺丝以及将液压缸直接放在轴承座与压下螺丝或压下横粱之间等方式。
这种调节方式的精调系统较为灵活,调节精度高。
特别是这种系统的粗调系统可以是一般的电动压下,因而这种方式特别适用于对旧轧机的改造,目前仍在采用。
(2)是全液压压下调节装置。
全液压压下的厚度调节系统取消了传统的压下螺丝,用液压缸直接压下,这种厚度调节方式结构简单,灵敏度高,能够满足很严格的厚度精度要求.并可根据需要,改变轧机的当量刚度,是现代化轧机上普遍采用的厚度调节方式。
液压伺服系统电液伺服系统课件
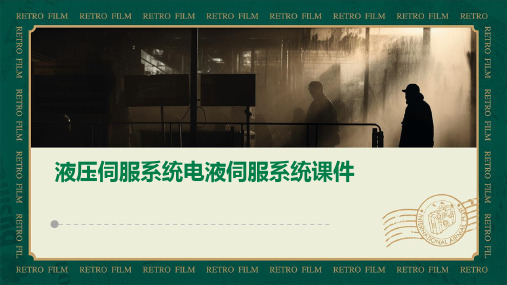
随着科技的不断发展,液压伺服系统也在不断创新和完善。未来,液压伺服系统将朝着智能化、数字 化、网络化方向发展,实现更高效、更精准的控制。同时,液压伺服系统还将更加注重环保和节能, 推动绿色制造和可持续发展。
02 电液伺服系统基础知识
电液转换元件
01
02
03
伺服阀
将电气信号转换为液压流 量或压力,实现液压执行 机构的精确控制。
速度同步
采用液压伺服系统实现多工位、多执行机构的速 度同步,优化生产流程。
航空航天领域中的应用
飞机起落架收放系统
通过电液伺服系统实现飞机起落架的平稳收放,确保飞行安全。
发动机推力控制
利用液压伺服系统对航空发动机进行精确的推力控制,提高飞行 性能。
飞行姿态调整
采用电液伺服系统实现飞行姿态的快速、精确调整,满足复杂飞 行需求。
仿真分析
在系统模型的基础上,进行仿真分析,包括系统动态响应、控制精度、稳定性等方面的评估,以验证设计的合理性。
优化设计
根据仿真分析结果,对系统进行优化设计,包括调整元件参数、改进控制策略等,以提高系统性能。
04 电液伺服系统实现技术
硬件平台搭建
控制器选择
根据系统需求,选用合适的控制器,如PLC、DSP等,确保控制精 度和实时性。
元件选型与计算
元件选型
根据规格书要求,选择合适的液压泵 、马达、阀等元件,确保系统性能达 标。
元件计算
对所选元件进行详细的计算和分析, 包括流量、压力、功率等参数,确保 元件之间的匹配性和系统的稳定性。
系统仿真与优化
系统建模
利用AMESim、MATLAB/Simulink等仿真软件,建立液压伺服系统的数学模型,为后续仿真分析提供基础。
铸轧机液压系统使用说明书
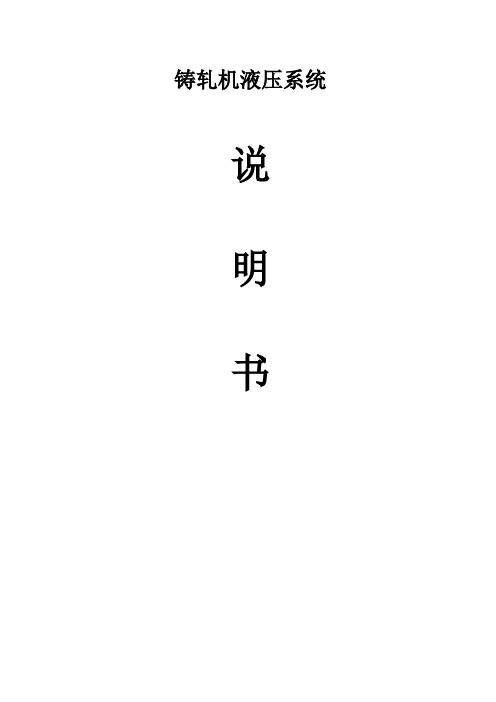
四、液压系统技术参数:
1、高压泵组工作压力:P=31Mpa;额定压泵组(1)大泵工作压力:P=4Mpa;额定流量:Q=98L/min
改正油泵旋转方向
油泵过度发热
油泵磨损或损坏
修理或换新
油的粘度过低
使用推荐粘度的液压油
冷却不足或冷却中断
改进调整冷却系统,使冷却水畅通
附表:液压传动系统常见故障及排除方法
故障
产生的原因
消除办法
油泵转速过低或动力功率低
皮带打滑,联轴器或电动机有故障
消除故障
从高压侧到回油侧的漏损
压力调整错误
消除故障
安全阀不关闭,存在脏东西或零件磨损
铸轧机液压系统
说
明
书
一、概述
本液压系统由压上泵组、中压泵组、阀台、自循环过滤冷却系统、高位油箱和底盘组成一个整体结构。
1、由2台柱塞泵组为压上油缸提供流量为15L/min,压力为31MPa的高压液压源。
2、由2台叶片泵组为控制阀台提供流量分别为98L/min、26L/min和压力分别为4Mpa、10Mpa中压液压源。
2、油泵启动时,必须处于卸荷(低压)状态,启动5秒后油泵方可加载。
3、油温控制:
当油温低于20℃时,油温开关发信号,接通加热器。
4、液位控制:液位开关用于油箱高低液位时报警,液位极低时报警并停止所有油泵。
5、滤油控制:当滤油器堵塞时,压差发讯器应发出信号,通知操作人员更换或清洗滤芯。过滤精度:回油口处20μ、循环过滤20μ。
▲注意维修保养和安全操作记录,无特殊障碍不要随便装拆液压元件。建议新液压油使用半年后更换一次,以后每隔一年更换一次,以保证系统的正常运行。
轧机压下大型伺服液压缸测试系统加载机架有限元模态分析

连杆小头衬套过盈联接 的有 限元计算和试验测试表 明 , 本 文所述 的连杆小头衬套孔位置综合误差纠正方法可行。 按这种纠 正方法 已完成 2 0余件连杆的修理 ,装机使用未发现异常情况 。 0 实际应用情况表明 , 该纠正方法对恢复连杆小头衬套孔位置综合 精度简单 、 有效 , 可在其它内燃机连杆修理中推广应用 。
★ 来稿 日期 :00 0— 1 ★基金项 目: 21—53 科技部科技人员服务企业行动项 目(Q 09 J002 , S 20GE 02 )湖北省教育厅青年科 学基金 (2O 103 , Q 06 10 ) 武汉科技大学冶金装备及其控制教育部 重点实验室开放基金重点资助项 目(09 0 ) 20B 1
有限元模 态分析 木
黄 富碹 陈新元 陈奎 生 陈 忱 。 (武 汉科技 大学 冶 金装备 及其控 制省部 共建教育 部重点 实验室 , ’ 武汉 40 8 ) 30 1
(武钢集团国际经济贸易总公司, 武汉 4 0 8 ) 30 1
F nt l me tmo a a y i ft e r ln i h d a l e v — yid r ii ee e n d I an lss o ol g m l y r u i s r o c l e h i l c n
a dcnrlWu a 3 0 C ia n ot , h n4 0 8 , hn ) o 1 ( nen t n l cn mi & Ta igC roai , gn ru , h n4 0 8 , hn ) 2 t ai a E oo c I r 0 rdn op rt n Wu agG op Wu a 3 0 C ia o 1
微 电子 以及计算 机辅助测试技术 , 能对缸直径 1 0 r 以下 的 60 m a 各类 伺服液压缸进行检验 , 其系统原理图如 图 1 所示 。
液压伺服系统的计算

APC系统的操纵模式及工作参数的运算项目内容
操纵模式
由于压下力专门大,且精度和稳固性要求专门高,因此APC系统一样采纳三通阀—不对称缸操纵模式,即用标准四通伺服阀当三通阀用,压下缸活塞腔受控,活塞杆腔通恒定低压。
低压Pr的作用是轧制时Pr=0.5MPa左右,防止活塞杆腔空吸并吸入灰尘;换辊时使Pr=3MPa左右用于快速提升压下缸。
压下缸放在上支承辊轴承座与压下螺丝(或牌坊顶面)之间时,压下缸倒置,即活塞杆不动,缸体运动。
系统供油压
力Ps
因压下力专门大,为幸免压下缸尺寸、伺服阀流量和供油系统
参数尺寸过大,拟取经济压力;考虑液压元件及伺服阀的额定
压力系列,并考虑到可靠性和爱护水平,取Ps=28MPa
负载压力PL
考虑到压下力专门大,那个地点不可能按常规即最大功率传输
条件取P
L
=(2/3)Ps;但PL也不应过大,
应保证伺服阀阀口上有足够压降,以确保伺服阀的操纵能力,
那个地点取P
L
=23MPa
背压Pr 压下操纵状态取Pr=0.5MPa。