注射模温度控制系统
注射模标准模架由哪几部分组成
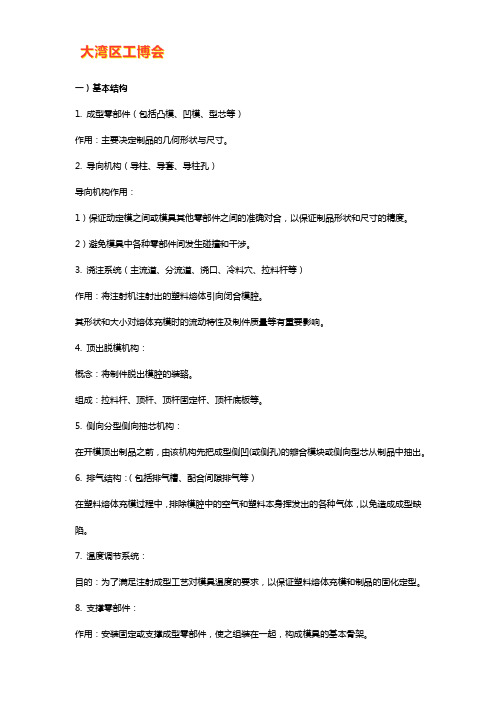
一)基本结构1. 成型零部件(包括凸模、凹模、型芯等)作用:主要决定制品的几何形状与尺寸。
2. 导向机构(导柱、导套、导柱孔)导向机构作用:1)保证动定模之间或模具其他零部件之间的准确对合,以保证制品形状和尺寸的精度。
2)避免模具中各种零部件间发生碰撞和干涉。
3. 浇注系统(主流道、分流道、浇口、冷料穴、拉料杆等)作用:将注射机注射出的塑料熔体引向闭合模腔。
其形状和大小对熔体充模时的流动特性及制件质量等有重要影响。
4. 顶出脱模机构:概念:将制件脱出模腔的装臵。
组成:拉料杆、顶杆、顶杆固定杆、顶杆底板等。
5. 侧向分型侧向抽芯机构:在开模顶出制品之前,由该机构先把成型侧凹(或侧孔)的瓣合模块或侧向型芯从制品中抽出。
6. 排气结构:(包括排气槽、配合间隙排气等)在塑料熔体充模过程中,排除模腔中的空气和塑料本身挥发出的各种气体,以免造成成型缺陷。
7. 温度调节系统:目的:为了满足注射成型工艺对模具温度的要求,以保证塑料熔体充模和制品的固化定型。
8. 支撑零部件:作用:安装固定或支撑成型零部件,使之组装在一起,构成模具的基本骨架。
注射模机构类型很多,但无论何种结构的模具,其主要有以下几种零件构成:一.成形零件成形零部件包括定模型腔、动模型腔和型芯等零件。
在注塑时,这类零件直接接触塑料,以成形制品,其精度要求较高,是注射模的核心零件。
1.定模型腔定模型腔又称凹模,主要成形塑件的外部形状。
2.动模型腔动模型腔又称凸模,主要成形塑件的内部形状。
3.型芯型芯一般固定在动模上,主要成形型孔及特殊形状的凹、凸;类塑件。
二.浇注系统零件浇注系统零件主要包括定位圈、浇口套等零件。
主要作用是将注射机料桶内的熔融塑料填充到模具型腔内,并起传递注射压力作用。
1.浇口套浇口套为组成塑料注入模具时需通过的主要通道零件,一般嵌镶在定模上。
2.定位圈是模具安装在注射定模板上时,决定注射机喷嘴口与浇口套相互位置的定位装置。
三.脱模系统零件注射模的脱模机构,是由推出塑件所需的全部结构零件组成,如顶杆、顶杆垫板、顶杆固定板等零件。
注射模具调温系统设计
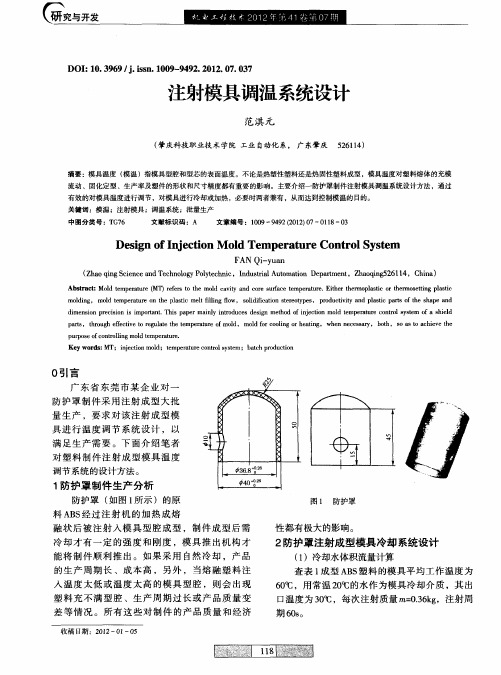
8
l 0 1 2
16 . 6
12 . 3 11 .0
5 ×I . 0
62×I . 74 1- .X 0 3
l 5
2 O 2 5
08 . 7
06 .6 05 3
.
9 ×l | . 旷 2
1 .Xl 24 0 1 .X 55 l 0
洼:在 R=00 及水温 1℃的条件下。(e e100 O R 为雷诺准数)
modn lig, mod tmp rt r n te pa t l fl n o l e eaue o h lsi meti l g f w, sldf ain see tp s p o u t i n l t at fte s p n c i l oiic to troy e , rd ci t a d pa i p rso h ha e a d i vy s c
f ~
一 — 一 一 .
丫
一
冕
代人式 ()得 : 1
V: n mAh
一
_●
03 . 6×6 0×35×1 . 0
寺
命 寺
图2 定模板冷却水道
6 c t ) 6x 0 4 8( — O o / 2一 0 0 x 70 2) p 一 10 1 3
准角 7 O
t — 冷却 水 出 口温 度 ,3% ; l — 0
— —
奇 命
一
一
。 。 令
' 一一
Ah 从熔 融状 态 的塑料 进人 型腔 时 的温度 到 一 塑 料 冷 却 脱 模 温 度 为 止 ,塑料 所 放 出 的热 焓 量 ,
A h=35 1 /g .x 0Jk 。
A s at l e eaue( ) eest emo ai n oesr c e p rtr. i e emolsi o hr oet gpat b t c:Mo t r d mprtr MT rfr t l cvt a dcr uf etm eaue Et rt r pat rte stn l i oh d y a h h c m i s c
基于PLC与HMI的高光注射模温控制系统

50 0 ) 106
【 摘要】 根据 高光注射成型原 理和模具温度动态控制要求 , 研制 以P C为控制核心的模 具 L
温度控制 系统 , 以实现 高光注射模 温度 的快速 准确 实时控制 ; 利用人机界 面技 术, 实现 了
Hale Waihona Puke 注射工艺全过程 的实时监控 , 障生产 系统 的稳 定性 、 保 可靠性 和 易操作性 , 实际应 用 中 在
t mp r t r c n r l y tm w t L a t e o e wa d v l p d e e a u e o to s s e i P C s h c r s e eo e .T e a i a d a c r t h h r p d n c u a e
、
 ̄
[ 李庆寿主编 2 】
.
机床 夹具设计 【 . M] 机械工业 出版社 .19 . 98
采用普通车床利用四爪卡盘校 能 较难 甚 至 慨 4 ~ 大 0 8 正 9 件 夹紧安装工件方法加工 保证 无法保证 6mn 0i
、
[ 国家机械工业委员会统编 . 3 ] 镗铣工工 艺学 [ .机械工业 M】
取得 了明显效 益 。
关键词 : 高光注射 ; 模具温控 系统;L ; P C 触摸屏 中图分类号:Q 2 . ; G 5 T 30 6T 69 6 文献标识码 : B 文章编号 :0 2 0 — 2 0 2 2 1— 10— 0
De eo m e to o d Te e a u e Co t olr S se v lp n fM l mp r t r n r l y tm e
机, 为缩短成型时间 , 满足成型要求 , 研制高光注射温
而高光注射技术则采用一种动态模温控制方式 ,
注射模工作原理
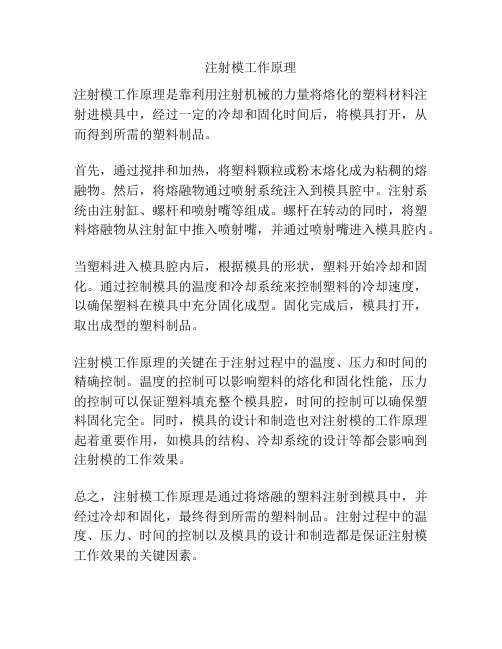
注射模工作原理
注射模工作原理是靠利用注射机械的力量将熔化的塑料材料注射进模具中,经过一定的冷却和固化时间后,将模具打开,从而得到所需的塑料制品。
首先,通过搅拌和加热,将塑料颗粒或粉末熔化成为粘稠的熔融物。
然后,将熔融物通过喷射系统注入到模具腔中。
注射系统由注射缸、螺杆和喷射嘴等组成。
螺杆在转动的同时,将塑料熔融物从注射缸中推入喷射嘴,并通过喷射嘴进入模具腔内。
当塑料进入模具腔内后,根据模具的形状,塑料开始冷却和固化。
通过控制模具的温度和冷却系统来控制塑料的冷却速度,以确保塑料在模具中充分固化成型。
固化完成后,模具打开,取出成型的塑料制品。
注射模工作原理的关键在于注射过程中的温度、压力和时间的精确控制。
温度的控制可以影响塑料的熔化和固化性能,压力的控制可以保证塑料填充整个模具腔,时间的控制可以确保塑料固化完全。
同时,模具的设计和制造也对注射模的工作原理起着重要作用,如模具的结构、冷却系统的设计等都会影响到注射模的工作效果。
总之,注射模工作原理是通过将熔融的塑料注射到模具中,并经过冷却和固化,最终得到所需的塑料制品。
注射过程中的温度、压力、时间的控制以及模具的设计和制造都是保证注射模工作效果的关键因素。
基于改进CMAC网络的注塑模温度控制

第2 5卷第 5期
v0 _5. I2 No. 5
西 华 大 学 学 报 ・ 自 然 科 学 版
J un l f h aUnv ri ・Nau a ce c o r a u ie s y o Xi t t r l in e S
20 0 6年 9月
由于计算机的响应速度远大 于温度的变化速度 , 所 以负 责检 测模具 不 同部位 温度 的几个 热 电偶可 以同
时通 过不 同继 电器接 在 同一个 A 9 D55的输人 口上 , 这样 可 以只用一 路 A/ D分 时检测 几路 热 电偶 , 约 节
成本 。量程 为 0~4 0 的 K 型V级的模拟信号输 出。由于温度和电压值是非 线性的, 热电偶输出的 mV级信号必须经 A 5 5 D 9 进 行线性 化 、 端 补 偿 和 信 号 放 大 , 送 到 AD 70 冷 再 7 1 A 71 D 70把 模 拟 信 号 转 换 为 数 字 信 号 再 送 人 AT 9 5 单 片机 的输人 口 , 而 完成 整 个 温度 信 号 8C 1 从
度 _ 。导热 油循环 系 统 除模 具 外 , 他 部 件都 进 行 5 J 其 隔热 保温 处理 。高 温 油 泵将 导 热 油 吸人 循 环 通 路 。
摘
要: 精密 注塑机模具 温度控 制的效果 直接影 响注 塑制品 的质量 , 为提高模 具温度控 制 的实时性 、 确性 , 精
采用改进 的 C C控制算 法 , 8 C 1单 片机为控 制器 , MA 以 95 利用 高温 导热 油的循 环实 现模 具 温度 的控 制。改进 的 C C神经网络利用 激活单元 先前学习次数作为可信 度 , MA 其误差校正值与激活单元先前学习次数 的负 k次方成 比
10模具设计-第十章--温度调节系统PPT课件

10 . 1 模具温度及塑料成型温度关系
2)对于粘度高、流动性差的塑料,例如聚碳酸酯、聚砜、 聚甲醛、聚苯醚和氟塑料等,为了提高充型性能,考虑到 成型工艺要求较高的模具温度,必须设置加热装置对模具 进行加热。
3)一般需要用常温水或冷水对模具冷却,而对于高粘流温度 和高熔点的塑料,可用温水进行模温控制。
在模具中设置温度调节系统的目的:
就是要通过控制模具温度,使模塑成型具有良好的产品质
量和较高的生产率。
模具温度的调节是指对模具进行冷却或加热,必要时两者
兼有,从而达到控制模温的目的。
4
10 . 1 模具温度及塑料成型温度关系
注射入模具中的热塑性熔融树脂,必须在模具内冷却固化才 能成为塑件,所以模具温度必须低于模具内熔融树脂的温度, 即达到θg(玻璃化温度)以下的某一温度范围,由于树脂本身 的性能特点不同,不同的塑料要求有不同的模具温度。
3
第十章 温度调节系统
模具温度及其调节的重要性
2.模具温度对成型周期的影响
缩短模塑成型周期就是提高模塑效率。
缩短成型周期关键在于缩短冷却硬化时间,而缩短冷却时 问,可通过调节塑料和模具的温差,在保证制件质量和成 型工艺顺利进行的前提下,降低模具温度有利于缩短冷却 时间,提高生产效率。 缩短成型周期→缩短冷却硬化时间→调节塑料和模具的温差→保证 质量前提下降低模具温度→缩短冷却时间,提高生产效率
4)对于模温要求在90℃以上的,必须对模具加热。 对于流程长、壁厚较小的塑件,或者粘流温度(或熔点)虽 不高但成型面积很大的塑件,为了保证塑料熔体在充模过 程中不至温降太大而影响充型,可设置加热装置对模具进 行预热。 对于小型薄壁塑件,且成型工艺要求模温不太高时,可以 不设置冷却装置而靠自然冷却。
塑料注射模具冷却系统的设计
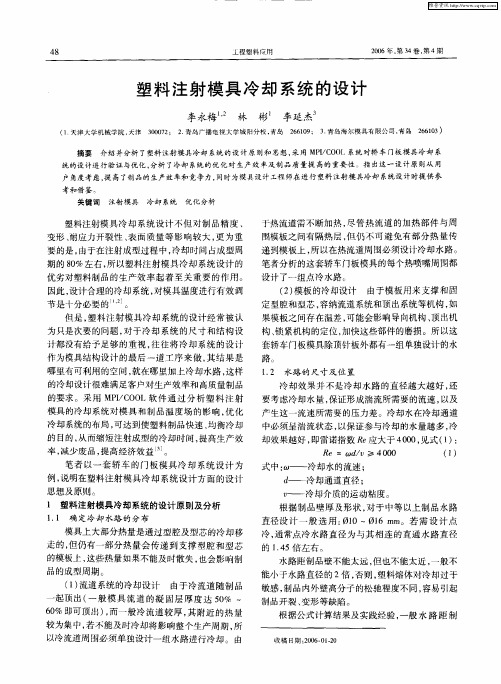
起顶 出 ( 般 模 具 流 道 的凝 固层 厚 度 达 5 % 一 0
6 % 即可顶 出 )而 一 般 冷 流道 较 厚 , 附近 的热 量 0 , 其 较 为集 中 , 不 能及 时 冷却将 影 响 整个生 产周 期 , 若 所
根据公式计算结果及实践经验 , 一般 水 路 距 制
收稿 日期 :0 6 O 一0 2 0 一 l2
要考ቤተ መጻሕፍቲ ባይዱ冷却水量 , 保证形成湍流所需要的流速 , 以及
产 生这 一流 速所 需 要 的压 力 差 。冷却 水在 冷却 通 道
中必须呈湍流状态 , 以保证参与冷却的水量越多, 冷 却效果越好 , 即雷诺指数 应大于 4 o , oO 见式 ( ) 1:
Re = ∞d v≥ 40 0 / 0 () 1
摘要 介 绍并分析 了塑料 注射模具 冷却 系统的设 计原 则和 思想 , 采用 MP/ O L系统对轿 车 门板模 具冷却 系 IC O
统 的设计进行验 证与优化 , 分析 了冷却 系统 的优 化 对生产 效率 及制 品质量提 高的重要性 指 出这一设计 原则从 用
户角度考虑, 提高了制品的生产效率和竞争力, 同时为模具设计工程师在进行塑料注射模具冷却 系统设计时提供参
直径设计 一般 选 用: 0~1 6m/ l 3 / 1 1 。若 需 设计 点 冷, 通常点冷水路直径为与其相连的直通水路直径
的 i4 . 5倍 左右 。
模具上大部分热量是通过型腔及型芯的冷却移
走的 , 但仍有一部分热量会传递到支撑型腔和型芯
的模板 上 , 些热 量 如果 不能及 时散 失 , 会影 响制 这 也
图 2 型芯冷却系统不意图 ( 7组 回路 )
度 为 20C, 腔温 度为 4  ̄ 3 ̄ 型 0C。基于 上述设 计 原则 ,
注射模具的基本结构与分类

三、带活动镶件的注射模
1-定模板 2-导柱 3活动镶件 4-型芯 5动模板 6-动模垫板 7-垫板 8-弹簧 9-推 杆 10-推杆固定板 11-推板 12-动模座板
四、带有侧向抽芯的注射模
1-楔紧块 2-斜导柱 3-侧型芯滑块 4-型 芯 5-型芯固定板 6动模垫板 7-垫块 8动模座板 9-推板 10-推杆固定板 11推杆 12-拉料杆 13导柱 14-动模板 15浇口套 16-定模座板 17定位圈
四、自动脱螺纹的注射模
1-螺纹型芯 2-模脚 3动模垫板 4-定距螺钉 5-动模板 6-衬套 7定 模板 8-注射机开合模 丝杠
工作原理:
塑件带有内螺纹或外螺纹须自动脱模时,在 模具中需要设置可以旋转的螺纹型芯或者型环。 通过注射机的往复运动或旋转运动,或者设置专 门的驱动(如电动机或液压马达等)和传动机构, 带动螺纹型芯者型环转动,使塑件脱出。 开模时,A-A面先分开,同时,螺纹型芯1在 随着注射机开合模丝杆8的后退中自动旋转,此时, 螺纹塑件由于定模板7的止转作用并不移动,仍留 在型腔内。当A-A面分开一段距离,即螺纹型芯1 在塑件内还有最后一牙时,定距螺钉4拉动动模板 5,使模具沿B-B打开,此时,塑件随型芯一道离 开定模型腔,然后从B-B分型面两侧的空间取出。
六、推出机构设在定模一侧的注射模
1-动模座板 2-垫板 3-定模垫板 4-成型 镶件 5、7-螺钉 6动 模板 8-脱模板 9-拉 板 10-定模板 11-定 模座板 12型芯 13导 柱
工作原理:
为便于注射机锁模系统的顶出装置工作,模 具开模后,塑件一般留在动模一侧,模具脱模机 构也设置在动模一侧。有时由于塑件的特殊要求 或者形状的限制,开模后塑件可能留在定模一侧, 这时就需要在定模一侧设置脱模机构。定模一侧 的脱模机构一般是采用拉板、拉杆或者链条与动 模相连。。 开模后,塑件紧包在凸模11 上,塑件留在了 定模一侧,当动模左移一定距离,拉板8 通过定 距螺钉6 带动推件板7 将塑件从凸模中脱出。
注射模的典型结构与分类

注射模的典型结构与分类1 . 1 注射模的典型结构注射模的基本结构是由动模和定模两大部分组成。
动模安装在注射机的移动模板上,定模安装在注射机的固定模板上。
注射时,动模与定模闭合构成型腔和浇注系统,开模时,动模与定模分离,通过脱模机构推出塑件。
根据模具中各个部件的作用,注射模具可以细分为以下几个部分。
( l )成型部分。
直接成型塑件的部分通常由凸模(成型塑件内表面)、凹模(成型塑件外表面)、型芯或成型杆、镶块,以及螺纹型芯和螺纹型环等组成。
( 2 )浇注系统.是指将塑料熔体由注射机喷嘴引向闭合型腔的流动流道.通常,浇注系统由主流道、分流道、浇口和冷料井组成。
( 3 )导向机构。
导向机构保证合模时动模和定模准确对合,以保证塑件的形状和尺寸精度,避免模具中其他零件(经常是凸模)发生碰撞和干涉。
导向机构分为导柱导向机构和锥面定位导向机构。
对于深腔、薄壁、精度要求较高的塑件,除了导柱导向外,经常还采用内外锥面定位导向机构。
在大中型注射模具的脱模机构中,为了保证在脱模过程脱模装置不因为变形歪斜而影响脱模,经常设置导向零件。
( 4 )脱模机构。
是指开模时将塑件和浇注系统凝料从模具中推出,实现脱禅的装置,常用的脱模机构有推杆、推管和推件板等。
( 5 )侧向分型抽芯机构。
带有内外侧孔、侧凹或侧凸的塑件,需要有侧向型芯或侧向成型块来成型,在开模推出塑件之前,模具必须先进行侧向分型,抽出侧向型芯或脱开侧向成型块,塑件才能顺利脱模。
负责完成上述功能的机构,称为侧向分型抽芯机构。
( 6 )温度调节系统。
为了满足注射成型工艺对模具温度的要求,模具一般设有冷却和加热系统。
冷却系统一般在模具内开设冷却水道,外部用橡皮软管连接。
加热装置则在模具内或模具四周设置电热元件、热水(油)或蒸汽等具有加热结构的板件。
模具中是开设冷却还是加热装置,需要根据塑料种类和成型工艺来确定。
( 7 )排气系统.注射充模时,为了塑料熔体的顺利进人,需要将型腔内的原有空气和注射成型过程中塑料本身挥发出来的气体排出模外,常在模具分型面处开设几条排气槽。
注塑成型模具的温度控制
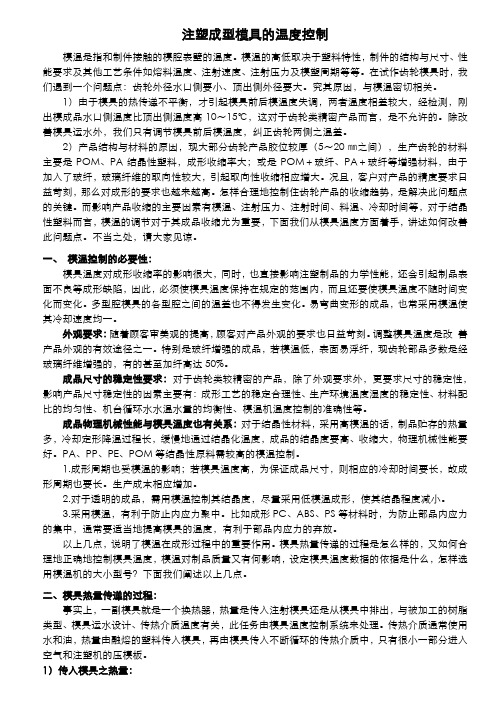
注塑成型模具的温度控制模温是指和制件接触的模腔表壁的温度。
模温的高低取决于塑料特性,制件的结构与尺寸、性能要求及其他工艺条件如熔料温度、注射速度、注射压力及模塑周期等等。
在试作齿轮模具时,我们遇到一个问题点:齿轮外径水口侧要小、顶出侧外径要大。
究其原因,与模温密切相关。
1)由于模具的热传递不平衡,才引起模具前后模温度失调,两者温度相差较大,经检测,刚出模成品水口侧温度比顶出侧温度高10~15℃,这对于齿轮类精密产品而言,是不允许的。
除改善模具运水外,我们只有调节模具前后模温度,纠正齿轮两侧之温差。
2)产品结构与材料的原因,现大部分齿轮产品胶位较厚(5~20㎜之间),生产齿轮的材料主要是POM、PA结晶性塑料,成形收缩率大;或是POM+玻纤、PA+玻纤等增强材料,由于加入了玻纤,玻璃纤维的取向性较大,引起取向性收缩相应增大。
况且,客户对产品的精度要求日益苛刻,那么对成形的要求也越来越高。
怎样合理地控制住齿轮产品的收缩趋势,是解决此问题点的关键。
而影响产品收缩的主要因素有模温、注射压力、注射时间、料温、冷却时间等,对于结晶性塑料而言,模温的调节对于其成品收缩尤为重要,下面我们从模具温度方面着手,讲述如何改善此问题点。
不当之处,请大家见谅。
一、模温控制的必要性:模具温度对成形收缩率的影响很大,同时,也直接影响注塑制品的力学性能,还会引起制品表面不良等成形缺陷,因此,必须使模具温度保持在规定的范围内,而且还要使模具温度不随时间变化而变化。
多型腔模具的各型腔之间的温差也不得发生变化。
易弯曲变形的成品,也常采用模温使其冷却速度均一。
外观要求:随着顾客审美观的提高,顾客对产品外观的要求也日益苛刻。
调整模具温度是改善产品外观的有效途径之一。
特别是玻纤增强的成品,若模温低,表面易浮纤,现齿轮部品多数是经玻璃纤维增强的,有的甚至加纤高达50%。
成品尺寸的稳定性要求:对于齿轮类较精密的产品,除了外观要求外,更要求尺寸的稳定性,影响产品尺寸稳定性的因素主要有:成形工艺的稳定合理性、生产环境温度湿度的稳定性、材料配比的均匀性、机台循环水水温水量的均衡性、模温机温度控制的准确性等。
注塑模具温控机工作原理_概述说明以及解释
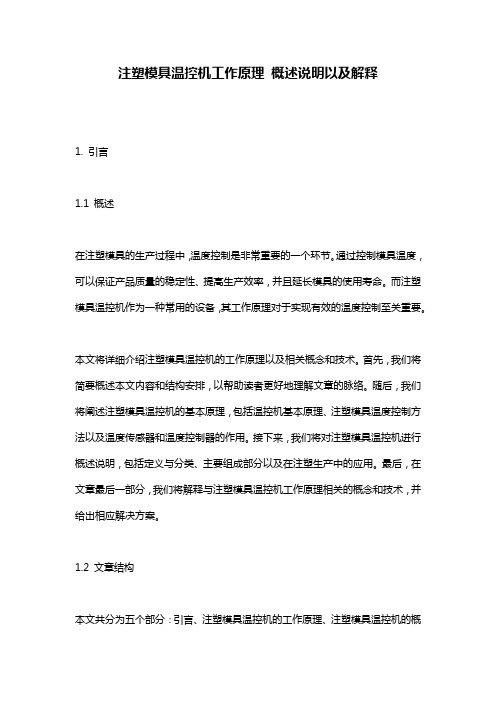
注塑模具温控机工作原理概述说明以及解释1. 引言1.1 概述在注塑模具的生产过程中,温度控制是非常重要的一个环节。
通过控制模具温度,可以保证产品质量的稳定性、提高生产效率,并且延长模具的使用寿命。
而注塑模具温控机作为一种常用的设备,其工作原理对于实现有效的温度控制至关重要。
本文将详细介绍注塑模具温控机的工作原理以及相关概念和技术。
首先,我们将简要概述本文内容和结构安排,以帮助读者更好地理解文章的脉络。
随后,我们将阐述注塑模具温控机的基本原理,包括温控机基本原理、注塑模具温度控制方法以及温度传感器和温度控制器的作用。
接下来,我们将对注塑模具温控机进行概述说明,包括定义与分类、主要组成部分以及在注塑生产中的应用。
最后,在文章最后一部分,我们将解释与注塑模具温控机工作原理相关的概念和技术,并给出相应解决方案。
1.2 文章结构本文共分为五个部分:引言、注塑模具温控机的工作原理、注塑模具温控机的概述说明、解释注塑模具温控机工作原理相关概念及技术以及结论。
下面将逐一介绍每个部分的内容。
1. 引言: 本部分将对文章进行概述,包括引言部分的概述、文章结构和目的。
2. 注塑模具温控机的工作原理: 本部分将详细介绍注塑模具温控机的工作原理,包括温控机基本原理、注塑模具温度控制方法以及温度传感器和温度控制器的作用。
3. 注塑模具温控机的概述说明: 本部分将对注塑模具温控机进行概述说明,包括定义与分类、主要组成部分以及在注塑生产中的应用。
4. 解释注塑模具温控机工作原理相关概念及技术: 本部分将对与注塑模具温控机工作原理相关的概念和技术进行解释,并给出相应解决方案。
主要包括控制回路原理及其调节方法、模具热平衡流程及关键参数介绍以及温度场分布与优化调节问题解决方案。
5. 结论: 本部分将总结模具温控机的工作原理重要性,并对模具温控机工作原理的理解进行总结。
最后,我们还将展望未来模具温控机领域的发展方向。
1.3 目的本文的目的在于详细介绍注塑模具温控机的工作原理、概述说明和相关概念及技术。
模具冷却系统
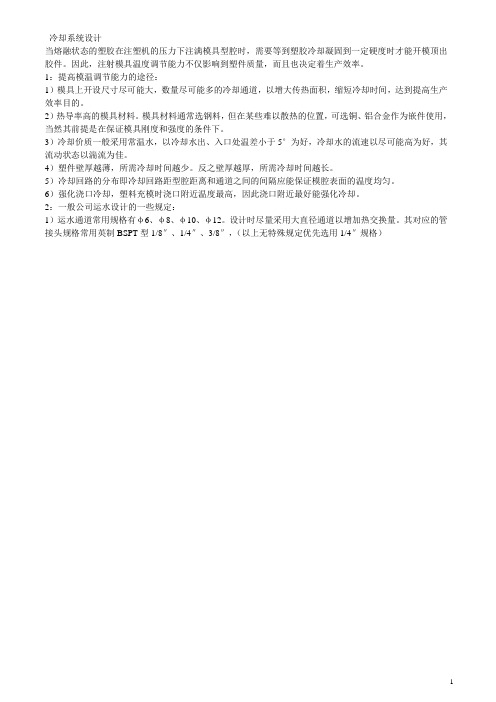
冷却系统设计
当熔融状态的塑胶在注塑机的压力下注满模具型腔时,需要等到塑胶冷却凝固到一定硬度时才能开模顶出胶件。
因此,注射模具温度调节能力不仅影响到塑件质量,而且也决定着生产效率。
1:提高模温调节能力的途径:
1)模具上开设尺寸尽可能大,数量尽可能多的冷却通道,以增大传热面积,缩短冷却时间,达到提高生产效率目的。
2)热导率高的模具材料。
模具材料通常选钢料,但在某些难以散热的位置,可选铜、铝合金作为嵌件使用,当然其前提是在保证模具刚度和强度的条件下。
3)冷却价质一般采用常温水,以冷却水出、入口处温差小于5°为好,冷却水的流速以尽可能高为好,其流动状态以湍流为佳。
4)塑件壁厚越薄,所需冷却时间越少。
反之壁厚越厚,所需冷却时间越长。
5)冷却回路的分布即冷却回路距型腔距离和通道之间的间隔应能保证模腔表面的温度均匀。
6)强化浇口冷却,塑料充模时浇口附近温度最高,因此浇口附近最好能强化冷却。
2:一般公司运水设计的一些规定:
1)运水通道常用规格有φ6、φ8、φ10、φ12。
设计时尽量采用大直径通道以增加热交换量。
其对应的管接头规格常用英制BSPT型1/8″、1/4″、3/8″,(以上无特殊规定优先选用1/4″规格)
1。
注塑机结构分析及其工作原理
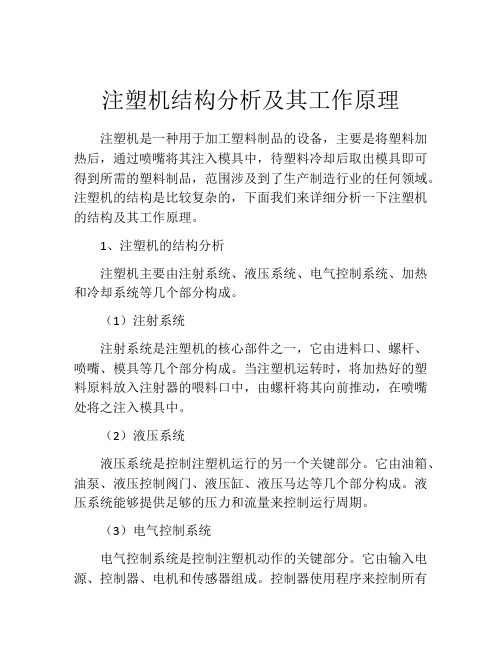
注塑机结构分析及其工作原理注塑机是一种用于加工塑料制品的设备,主要是将塑料加热后,通过喷嘴将其注入模具中,待塑料冷却后取出模具即可得到所需的塑料制品,范围涉及到了生产制造行业的任何领域。
注塑机的结构是比较复杂的,下面我们来详细分析一下注塑机的结构及其工作原理。
1、注塑机的结构分析注塑机主要由注射系统、液压系统、电气控制系统、加热和冷却系统等几个部分构成。
(1)注射系统注射系统是注塑机的核心部件之一,它由进料口、螺杆、喷嘴、模具等几个部分构成。
当注塑机运转时,将加热好的塑料原料放入注射器的喂料口中,由螺杆将其向前推动,在喷嘴处将之注入模具中。
(2)液压系统液压系统是控制注塑机运行的另一个关键部分。
它由油箱、油泵、液压控制阀门、液压缸、液压马达等几个部分构成。
液压系统能够提供足够的压力和流量来控制运行周期。
(3)电气控制系统电气控制系统是控制注塑机动作的关键部分。
它由输入电源、控制器、电机和传感器组成。
控制器使用程序来控制所有的电机、马达、油压和喷嘴等部件的行动,以实现所需的注塑周期。
(4)加热和冷却系统加热和冷却系统用来控制注射模具中的温度。
这些系统包括供热器、温度传感器、加热棒、制冷机、温度控制模块等几个部分。
2、注塑机的工作原理注塑机的工作原理是将塑料原料加热到一定程度,然后使用注塑机中的喷嘴将其注入模具中,在模具中待其冷却后取出模具就可以得到所需的塑料制品。
当运行注塑机时,首先将塑料颗粒放入注塑机的喂料口中,然后螺杆开始将原料推进注塑器。
当塑料原料被加热到一定程度,它就会变软,这时螺杆会将它从注射器喷出,注入到模具中。
当塑料在模具中冷却时,它会沿着模具的轮廓缩小,这样就能够得到所需的塑料制品。
对于注塑机中的液压系统,有几个东西需要注意,例如:注塑机的频率和压力要由控制器控制。
必须使用正确的油量,以确保注塑机顺利运行。
注塑机应定期进行检查和维修。
总之,注塑机通过组合多个部分来实现加工塑料制品的目标。
热流道结构知识点总结

热流道结构知识点总结热流道结构在塑料注射成型过程中扮演着重要的角色,它可以帮助提高注射成型的效率和质量。
本文将会总结热流道结构的相关知识点,包括热流道系统的基本原理、组成部分、优点和缺点、应用范围等内容。
一、热流道系统的基本原理热流道系统是一种在注射模具中用于传送加热的热载体,保持塑料材料在注射成型过程中的流动状态,以保证产品的成型质量和提高生产效率。
热流道系统的基本原理包括:1. 热载体传导热量:热流道系统中通常采用热载体(如热油、热水)传导热量,将热能传递到模具的热流道中,使塑料材料在注射成型过程中能够始终保持在合适的流动状态。
2. 控制模具温度:通过控制热载体的温度和流量,可以实现对注射模具中的温度进行精确的控制。
这样可以避免塑料材料在成型过程中受温度变化的影响,保证产品的尺寸稳定性和表面质量。
3. 优化成型条件:热流道系统可以根据不同的产品形状和材料特性,灵活调节模具中不同部位的温度,以实现最佳的注射成型效果。
二、热流道系统的组成部分热流道系统由多个组成部分组成,主要包括热流道控制器、加热装置、温度探测器、热流道喉口等。
1. 热流道控制器:负责对热流道系统的温度、压力等参数进行实时监控和调节,以确保注射成型过程中的稳定性和一致性。
2. 加热装置:通常采用电加热或加热用的热管,通过对热载体进行加热,传递热能到热流道系统中。
3. 温度探测器:用于监测热流道系统中的温度变化,反馈给热流道控制器,以实现自动调节和控制。
4. 热流道喉口:负责将加热好的热载体传递到模具的热流道中,为塑料材料提供适宜的加热条件。
三、热流道系统的优点和缺点热流道系统相比传统的冷流道系统具有许多优点,但也存在一些缺点。
1. 优点:(1)节能减耗:热流道系统采用热载体传导热量,可以有效减少注射成型过程中的能耗,提高生产效率。
(2)减少生产环境污染:热流道系统可以降低产品的废料率,提高成型质量,减少生产环境的污染。
(3)提高产品质量:热流道系统可以精确控制模具中不同部位的温度,保证产品的尺寸稳定性和表面质量。
注塑成型工艺注射模温度调节系统
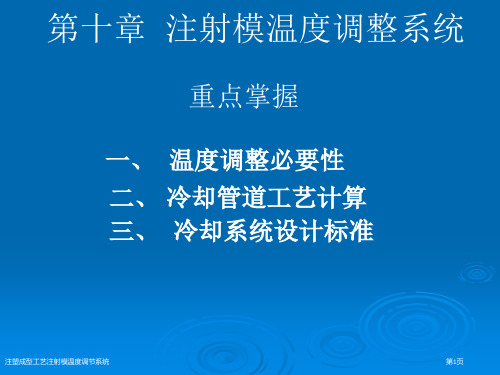
(10-18)
式中 W——单位时间内注入型腔中塑料质量,kg/h;
N——每小时注射次数; G——每次塑料注射量,kg;
Q1——单位质量塑料制件从熔体进入型腔开始到冷却结束时所
放出热量,kJ/kg;又称为单位热流量之差或热焓之差。
对于一些塑料,可从图10-2中得到不一样温度下热焓量,
第十章 注射模温度调整系统
重点掌握
一、 温度调整必要性 二、 冷却管道工艺计算 三、 冷却系统设计标准
注塑成型工艺注射模温度调节系统
第1页
第一节 温度调整必要性
一、温度调整对塑件质量影响
1.变形
模具温度稳定,冷却速度均衡,可减小塑件变形。 对壁厚不一致和形状复杂塑件,经常会出现因收缩不均 匀而产生翘曲变形情况。故须采取适当冷却系统,使模 具凹模与型芯各个部位温度基本保持一致,方便型腔内 塑料熔体能同时凝固。
Q1——单位重量塑件在凝固时所放出热量,kJ/kg; ρ——冷却介质密度,kg/m3;
c1——冷却介质比热容,kJ/(kg·℃);
θ1——冷却介质出口温度,℃;
θ2——冷却介质进口温度,℃。
注塑成型工艺注射模温度调节系统
第15页
Q1可表示为
Q1 c2 3 4 u (10-13)
式中 c2——塑料比热容,kJ/(kg·℃); θ3、θ4——分别为塑料熔体温度和推出前塑件温度,℃;
A——冷却介质传热面积,m2;
Δθ——模具温度与冷却介质温度之间差值,℃;
t——冷却时间,s。
式(10—1)知,当所需传递热量Q不变时,可经过以下
三条路径来缩短冷却时间。
注塑成型工艺注射模温度调节系统
第6页
1.提升传热膜系数
- 1、下载文档前请自行甄别文档内容的完整性,平台不提供额外的编辑、内容补充、找答案等附加服务。
- 2、"仅部分预览"的文档,不可在线预览部分如存在完整性等问题,可反馈申请退款(可完整预览的文档不适用该条件!)。
- 3、如文档侵犯您的权益,请联系客服反馈,我们会尽快为您处理(人工客服工作时间:9:00-18:30)。
注射模温度控制系统
–在注射成型中,注射模的温度对于塑料熔体的流动充模、固化成型、生产效率以及塑件的形状和尺寸精度都有重要影响,而恰当均匀的模具温度则必须由模内的温度调节系统进行控制。
–在注射模中设置温度调节系统的目的,就是要通过控制模具温度,使注射成型具有良好的制品质量和较高的生产效率。
l对热固性塑料的模塑成型,必须对模具采取加热措施。
l需要指出,模具中设置温度调节系统后,会给注射成型生产带来一些问题:
l例如,采用冷却水调节控制模温时,大气中的水分容易凝聚在型腔表壁而影响制品的表面质量。
l再如,采用加热措施调节控制模温时,模温升高以后,模内一些采用间隙配合的滑动零件将会有所膨胀,于是,预留的配合间隙将会减小或者消失,从而导致这些零件的运动发生故障。
l因此,在设计模具和温度调节系统时,对于诸如此类的问题,均要想办法加以预防。
a)层流Re<2000~2300b)紊流Re>4000
l实验证明,湍流的冷却效果比层流的好得多;l据资料表明,在湍流下的热传递比层流高10~20倍。
“同心层绝热体”,妨碍散热传热效果明显增强
l 为了使冷却水处于湍流状态(Re >6000),无论多大的模具,水孔直径不能大于14mm ,否则,冷却水难以成为湍流状态,从而降低热交换率。
l 一般水孔的直径可以根据塑件的平均壁厚来确定。
e d R υρη=塑件平均壁厚,mm
22~44~6冷却水孔直径,mm 8~1010~1210~14
冷却回路设置的基本原则
1.冷却水道应尽量多、截面尺寸应尽量大
2.冷却水道应尽量接近模腔表壁且彼此到模腔表壁的距
离应尽量相等
3.冷却水路的入口应靠近浇口部位
4.冷却水路的出、入口温差应尽量小
5.冷却水路应沿着塑料收缩的方向设置
6.冷却水道的布排应尽可能与制品形状保持一致
7.细长型凸模可采用喷射式水路或间接冷却法
8.其它注意事项
1. 冷却水道应尽量多、截面尺寸应尽量大
2. 冷却水道应尽量接近模腔表壁,并且彼此到模腔表壁的距离应尽量相等
l一般冷却水孔边至型腔表面的距离应大于10 mm,常用12~15 mm。
3. 浇口处应加强冷却
侧浇口点浇口
直接浇口
4. 冷却水路的出、入口温差应尽量小
5. 冷却水路应沿着塑料收缩的方向设置
6.其它注意事项
①冷却水道应尽量避免接近制品容易出现熔接痕的部位,
以防止熔接不牢降低制品强度。
②冷却水道的截面积应能保证水流呈湍流状态(紊流状
态),因此,直径一般不小于8mm,这主要从加工及保证水流的湍流状态等考虑;
③冷却水流不能穿过镶拼模块的接缝,否则将产生漏水;
④冷却水路中不要有死角,以防冷却水回流影响冷却效果;
⑤从减小压力损失的观点出发,冷却水路的总长度不要过
大,一般不要超过1200~1500mm。
二)常见冷却系统的结构
1. 直流式和直流循环式
–特点:
Ø结构简单,加工方便
Ø但模具冷却不均匀
2. 循环式
间隙循环式:冷却效
果好,但出入口数量较多,加工费时密封圈堵塞
连续循环式:只有一个入口和出口,冷却效果稍差,适于中小型型芯和型腔
冷却零件系统(运水零件)
喉嘴(Nipple)
40
方法(二)﹕二層運水
預壓20%
–特点:
3. 喷流式
Ø结构简单,成本较低,冷却效果较好
管子
4. 隔板式–特点:
Ø加工麻烦,隔板与孔配合要求高,否则隔板易转动而达不到要求。
隔板
5. 特深型腔塑件的冷却–特点:
Ø冷却效果特别好
7. 间接冷却
铍铜型芯
铍铜杆
镶件
带有Be-Cu镶件的模具(便于散热)
Cavity Cooling water line
Baffle(夹片、运Core Cooling water line
水井)。