催化裂化过程中骨架异构化反应的研究__催化裂化工艺过程中骨架异构化反应的表征及其
催化裂化技术

催化裂化原料 催化裂化原料分为馏分油和渣油两大类。
1、Distillate Oil(馏分油)
(1)直馏重馏分油(350~500℃)
大多数直馏重馏分含芳烃较少,容易裂化,轻油收率较高, 是理想的催化裂化原料。
(2)热加工产物:焦化蜡油、减粘裂化馏出油等。
其中烯烃、芳烃含量较多,转化率低、生焦率高。不单独
• 5.正碳离子将H+ 还给催化剂,本身变成烯烃,反应中止。
催化裂化催化剂
一、催化裂化剂的种类、组成和结构
工业上使用的裂化催化剂归纳起来有三大类:
1、天然白土催化剂
催化裂化装置最初使用的经处理的天然白土,其主要活性 组分是硅酸铝。
2、无定型硅酸铝催化剂
天然白土被人工合成硅酸铝所取代。
• 无定型硅酸铝催化剂 • 硅酸铝的主要成分是氧化硅和氧化铝,合成硅酸铝依铝含量的不同又分 为低铝(含Al2O310%~13%)和高铝(含Al2O3约25%)二种。其催化剂 按颗粒大小又分为小球状(直径在3~6mm)和微球状(直径在40~80)。 • Al2O3、SiO2及少量水分是必要的活性组分,而其它组分是在催化剂的制 备过程中残留下来的极少量的杂质。合成硅酸铝是由Na2SiO3和Al2(SO4)3 溶液按一定的比例配合而成凝胶,再经水洗、过滤、成型、干燥、活化 而制成的。硅酸铝催化剂的表面具有酸性,并形成许多酸性中心,催化 剂的活性就来源于这些酸性中心,即催化剂的活性中心。
在全世界催化裂化装置的总加工能力中,提升管催化
裂化已占绝大多数。
流程图画面
催化裂化化学反应原理
• 一、单体烃催化裂化的化学反应 • (一)烷烃 • 烷烃主要发生分解反应,分解成较小分子的烷烃和烯烃, 烷烃分解时多从中间的C—C键处断裂,分子越大越容易 断裂
炼油催化裂化过程中的异构化反应机理研究

炼油催化裂化过程中的异构化反应机理研究炼油催化裂化是一种常用的石油加工技术,通过将高分子量的石油原料在催化剂的作用下,裂解为低分子量的烃类产品。
在这个过程中,异构化反应机理起到了重要的作用。
本文将对炼油催化裂化过程中的异构化反应机理进行研究。
异构化反应是石油加工过程中常见的反应之一,它可以将直链烃转化为支链烃。
这种转化可以提高燃料的辛烷值并减少芳香烃的生成,从而提高产物的燃油质量。
在炼油催化裂化过程中,异构化反应通常发生在裂化转化反应的早期阶段。
研究表明,催化剂种类、反应温度、反应压力等因素都会对异构化反应的机理产生影响。
首先,催化剂选择是影响异构化反应机理的关键因素之一。
不同类型的催化剂具有不同的酸碱性质和活性中心,可以选择性地促进异构化反应的发生。
例如,铂族催化剂在中等温度下可以有效催化异构化反应。
其次,反应温度对异构化反应机理有直接影响。
在较低温度下,异构化反应速率较慢,产物中直链和支链烃的比例较大。
而在高温下,异构化反应速率增加,支链烃生成的比例也随之增加。
此外,反应压力也会影响异构化反应的进行。
在适当的压力下,反应速率加快,支链烃的生成得到增强。
但是过高的压力可能会导致副反应的发生,影响异构化反应的选择性。
炼油催化裂化过程中异构化反应的机理主要包括分子取代、脱氢和重排等步骤。
其中分子取代是异构化反应的关键步骤之一,它涉及到直链烃分子与催化剂表面活性中心的吸附和解离。
脱氢步骤是异构化反应中的重要步骤之一,通过脱除烃分子中的氢原子,形成双键结构,使分子结构发生变化。
重排步骤则是在分子取代和脱氢过程中发生的,通过一系列的内部迁移和断裂重组,使烃分子的碳链结构发生变化,生成支链烃。
异构化反应机理的研究不仅可以帮助我们更好地理解炼油催化裂化过程中的反应规律,还可以指导工业生产中的改进和优化。
通过选择合适的催化剂和反应条件,可以提高炼油催化裂化过程中异构化反应的效率和选择性,从而获得更高质量的燃料产品。
石油炼制名词解释

名词解释:1.催化裂化:催化裂化是在0.1~0.3MPa、500℃左右的温度及催化剂作用下,重质原料油发生以裂解为主的一系列化学反应,转化为气体、汽油、柴油、油浆及焦炭的工艺过程。
2.催化剂活性:催化剂的活性就是能加快反应速度的性能。
3.二次燃烧:由过剩O2含量太高,再生器密相床烧焦产生的CO在稀相段或集气室燃烧,放出大量热量而烧坏设备。
4氢转移反应:某烃分子上的氢脱下来立即加到另一烯烃分子上使之饱和的反应。
5碳堆积:再生器烧焦能力低或供氧不足,反应生成的焦炭烧为完全,使催化剂活性及选择性下降,又至使反应时生焦量增大,再生器烧焦更不完全,这样造成恶性循环,使催化剂上焦炭迅速增大,这就是碳堆积。
简答题1.简述催化裂化的化学反应分解反应、异构化反应,氢转移反应,烷基化反应,芳构化反应,烷基化反应、生焦反应2.列出芳烃转化的催化剂种类有酸性催化剂和固体酸,固体酸又分为浸附在适当载体上的质子酸;浸附在适当酸性卤化物,混合氧化物催化剂,贵金属-氧化硅-氧化铝催化剂;分子筛催化剂3.C8芳烃异构化反应所用的催化剂无定型SiO2-Al2O3催化剂,负载型铂催化剂。
ZSM催化剂,HF-BF3催化剂4.简述目前工业上分离对二甲苯的方法?答:深冷结晶法,络合分离法,吸附分离法5.简述开发芳烃转化工艺的原因不同来源的各种芳烃馏分组成是不同的,能得到各种芳烃的产量也不同,因此如果仅从这里取得芳烃,必然导致供需矛盾,所以用该工艺调节芳烃产量为什么催化裂化产物中少C1、C2,多C3、C4?正碳离子分解时不生成<C3、C4的更小正碳离子。
为什么催化裂化产物中多异构烃?伯、仲正碳离子稳定性差,易转化为叔正碳离子。
为什么催化裂化产物中多β烯烃?伯正碳离子易转为仲正碳离子,放出H+形成β烯烃。
催化裂化的原料和产品有什么特点?答:主要原料有:直馏馏分油、常压渣油、脱沥青油、焦化蜡油、减压渣油等。
主要产品有液化气、汽油、柴油、油浆等。
催化裂化原理

4
4.1 概述
二、催化裂化的发展历程 催化裂化自1936年实现工业化至今经历了四个阶段: 固定床、移动床、流化床和提升管。
Fixed Bed
Moving Bed
5
4.1 概述
Fluid Bed
Lift Pipe
在全世界催化裂化装置的总加工能力中,提升管催化
裂化已占绝大多数。
6
4.1 概述
三、催化裂化主要发展方向 1、加工重质原料
25
4.3 烃类的催化裂化反应
H C H 3CC H 3
+
H + (C at.)+C H 3C HC H 3
思考1:为什么催化裂化产物中少C1、C2,多C3、C4? 正碳离子分解时不生成<C3、C4的更小正碳离子。 思考2:为什么催化裂化产物中多异构烃?
伯、仲正碳离子稳定性差,易转化为叔正碳离子。
20
4.3 烃类的催化裂化反应
2、正碳离子机理
以正n-C16H32来说明。 (1)生成正碳离子
正n-C16H32得到一个H+,生成正碳离子。如
H
H
n -C 5 H 1 1CC 1 0 H 2 0+H + n -C 5 H 1 1CC 1 0 H 2 1
+
(2)β断裂
大正碳离子不稳定,容易在β位置上断裂,生成一个烯
若正碳离子为伯正碳离子,易变成仲碳离子,再进行β 断裂,甚至异构化为叔正碳离子,再进行β断裂。
22
4.3 烃类的催化裂化反应
C H 2C 8H 17 +
C H 3C HC 7H 16 +
C H 3C HC H 2+C H 2C 5H 11 +
催化裂化工艺流程及主要设备

2023催化裂化工艺流程及主要设备pptcontents •概述•催化裂化工艺流程•催化裂化主要设备•工艺特点和操作规程•安全与环保•常见故障及排除方法•发展方向和新技术应用目录01概述催化裂化是一种将重质烃类转化为轻质烃类和液化气的过程,是石油化工中重要的二次加工手段之一。
催化裂化工艺主要采用流化床反应器,催化剂作为床层中的介质,在适宜的温度、压力和空速条件下进行反应。
催化裂化基本概念1催化裂化主要设备23流化床反应器是催化裂化的主要设备之一,分为单器、双器和多器系统。
反应器再生器是催化裂化中的重要设备,用于烧去催化剂表面的积炭,恢复催化剂活性。
再生器旋风分离器用于将反应和再生两个工艺流程分开,同时将催化剂从反应器物料中分离出来。
旋风分离器催化裂化工艺流程简介原料油进入反应器,在适宜的温度、压力和空速条件下进行反应。
分离出的催化剂进入再生器,烧去积炭恢复活性。
反应后的物料进入旋风分离器,将催化剂从物料中分离出来。
再生后的催化剂回到反应器物料中,继续参与反应。
02催化裂化工艺流程原料油缓冲在催化裂化工艺中,原料油首先需要进入缓冲罐,进行初步的脱水和脱盐处理。
原料油加热原料油通过加热炉加热到一定温度,以便能够进行催化裂化反应。
原料预处理催化裂化主要流程加热后的原料油被送到催化裂化反应器中,同时加入催化剂。
进料在催化裂化反应器中,原料油在催化剂的作用下发生裂化反应,生成轻质油品和小分子烃类。
裂化反应裂化反应后的油气和催化剂分离,油气进入分馏塔进行分离。
催化剂分离分离后的催化剂进入再生器烧焦再生,循环使用。
催化剂循环油气在分馏塔中根据沸点不同,分离成不同沸点的油品,如汽油、柴油和重油。
油品分馏分离出的油品通过一系列精制过程,如脱硫、脱氮、脱氧等处理,提高油品质量。
油品精制催化裂化过程中产生的气体,通过压缩、冷却和分离等步骤,得到液态烃和干气。
气体分离经过处理的油品和气体分别进入相应的储罐或装置进行储存或进一步加工。
催化裂化机理及特点

催化裂化机理及特点催化裂化是一种通过加热和催化剂的作用将长链烃分子裂解为短链烃分子的重要工艺。
催化裂化机理及特点主要包括以下几个方面:一、催化裂化机理1.构造反应:长链烃分子在裂化过程中首先发生构造反应,通过裂解碳-碳键,形成相对较短的碳链碳烃和烯烃。
2.重排反应:长链烃分子中的骨架碳骨架会经历一系列重排反应,使得产物中更多的是相对稳定的异构体和环状化合物。
3.脱氢反应:重排反应过程中,长链分子中的烃基可能失去氢原子,从而形成烯烃,增加了催化裂化的产物中烯烃的含量。
4.脱氢裂解反应:在高温高压下,部分碳链碳烃可以发生脱氢裂解反应,形成更短的链长烃烃烃烃、烯烃和芳香烃。
二、催化裂化特点1.催化裂化具有高选择性:在催化剂的影响下,催化裂化反应主要发生在长链烃分子中的弱键和缺陷位置,使得产物中的碳链长度相对较短,同时产生更多的异构体和环状化合物。
2.催化裂化反应速度快:催化剂的存在提高了反应活性,使得裂化反应可以在相对低的温度和压力下进行,加快了反应速度。
3.催化裂化可以产生高附加值的产品:催化裂化使得重质燃料油转化为轻质烃类产品,其中包括汽油、炼厂气、润滑油基础油等,这些产品有较高的附加值。
4.催化裂化可以降低能源消耗:通过催化裂化将重质原油转化为较轻质产品,如汽油和炼厂气,不仅提供了更多的高附加值产品,还减少了对原油的需求,降低了能源消耗。
5.催化裂化可以调节产品分布:通过不同的催化剂组合和反应条件,可以调节催化裂化产物的碳链长度分布,以满足市场需求,提高产品经济效益。
总之,催化裂化是一种高效、高选择性的炼油工艺,通过加热和催化剂的作用,将长链烃分子裂解为短链烃分子,产生高附加值产品,并降低能源消耗。
催化裂化机理和特点的深入研究对于提高炼油工艺的效率和降低能源消耗具有重要意义。
(完整)催化裂化的装置简介及工艺流程
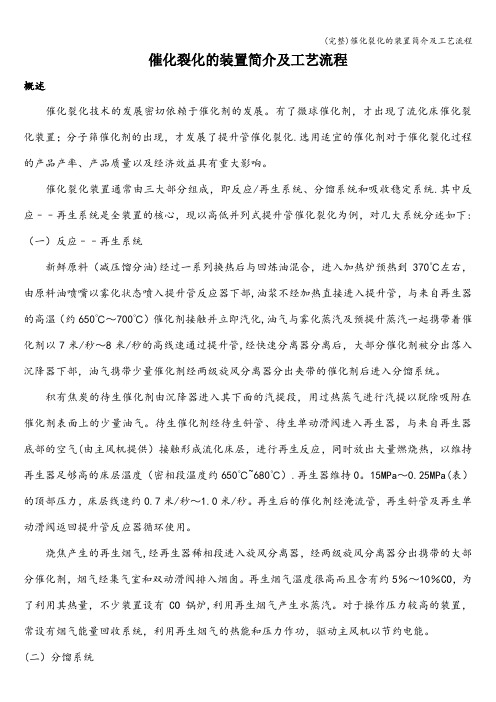
催化裂化的装置简介及工艺流程概述催化裂化技术的发展密切依赖于催化剂的发展。
有了微球催化剂,才出现了流化床催化裂化装置;分子筛催化剂的出现,才发展了提升管催化裂化.选用适宜的催化剂对于催化裂化过程的产品产率、产品质量以及经济效益具有重大影响。
催化裂化装置通常由三大部分组成,即反应/再生系统、分馏系统和吸收稳定系统.其中反应––再生系统是全装置的核心,现以高低并列式提升管催化裂化为例,对几大系统分述如下:(一)反应––再生系统新鲜原料(减压馏分油)经过一系列换热后与回炼油混合,进入加热炉预热到370℃左右,由原料油喷嘴以雾化状态喷入提升管反应器下部,油浆不经加热直接进入提升管,与来自再生器的高温(约650℃~700℃)催化剂接触并立即汽化,油气与雾化蒸汽及预提升蒸汽一起携带着催化剂以7米/秒~8米/秒的高线速通过提升管,经快速分离器分离后,大部分催化剂被分出落入沉降器下部,油气携带少量催化剂经两级旋风分离器分出夹带的催化剂后进入分馏系统。
积有焦炭的待生催化剂由沉降器进入其下面的汽提段,用过热蒸气进行汽提以脱除吸附在催化剂表面上的少量油气。
待生催化剂经待生斜管、待生单动滑阀进入再生器,与来自再生器底部的空气(由主风机提供)接触形成流化床层,进行再生反应,同时放出大量燃烧热,以维持再生器足够高的床层温度(密相段温度约650℃~680℃).再生器维持0。
15MPa~0.25MPa(表)的顶部压力,床层线速约0.7米/秒~1.0米/秒。
再生后的催化剂经淹流管,再生斜管及再生单动滑阀返回提升管反应器循环使用。
烧焦产生的再生烟气,经再生器稀相段进入旋风分离器,经两级旋风分离器分出携带的大部分催化剂,烟气经集气室和双动滑阀排入烟囱。
再生烟气温度很高而且含有约5%~10%CO,为了利用其热量,不少装置设有CO锅炉,利用再生烟气产生水蒸汽。
对于操作压力较高的装置,常设有烟气能量回收系统,利用再生烟气的热能和压力作功,驱动主风机以节约电能。
石油化工重油催化裂化工艺技术

石油化工重油催化裂化工艺技术石油化工重油催化裂化工艺技术是一种将重油转化为轻质油和化学品的过程。
该过程主要利用催化剂的作用,在高温高压条件下,使重油的大分子裂解成小分子,同时发生异构化、芳构化和氢转移等反应,以获得更多的轻质油和化学品。
催化剂的选择:催化剂是该技术的核心,其选择对产品的质量和产量有着至关重要的影响。
目前,常用的催化剂包括酸性催化剂、金属催化剂和金属氧化物催化剂等。
工艺条件的控制:工艺条件包括反应温度、压力、空速等,这些因素对产品的质量和产量都有着极大的影响。
因此,精确控制这些工艺条件是重油催化裂化工艺技术成功应用的关键。
产品的质量和性能:重油催化裂化工艺技术生产的产品具有高辛烷值、低硫含量等特点,被广泛应用于汽油、柴油、航空煤油等领域。
在应用方面,石油化工重油催化裂化工艺技术适用于不同类型重油,如减压渣油、催化裂化残渣油、脱沥青油等。
对于不同工业应用,可根据实际需求选择合适的工艺技术。
例如,对于生产高质量汽油和柴油的需求,可以选择更为精细的催化剂和严格的工艺条件;对于生产高附加值化学品的需求,则可以通过调整工艺流程和催化剂类型来增加化学品产量。
虽然石油化工重油催化裂化工艺技术在提高石油利用率、生产高质量石油化工产品方面具有重要作用,但也面临着一些挑战。
催化剂的活性、选择性和稳定性是该技术的关键,而目前催化剂的研究与开发尚存在诸多困难。
重油催化裂化过程中产生的固体废物和废气等对环境造成了严重影响,亟需解决。
由于重油资源的有限性,需要进一步探索和研发更为高效、环保的石油化工技术,以适应未来可持续发展的需要。
石油化工重油催化裂化工艺技术在石油化工产业中具有重要地位。
随着经济的发展和科技的进步,该技术将不断完善和优化,提高石油利用率和生产效率,同时注重环保和可持续发展。
未来,需要加强催化剂的研发与优化,减少环境污染,提高技术的绿色性和可持续性。
应积极探索新的石油化工技术,以应对全球能源危机和环境问题的挑战。
2020年中国石油大学北京网络学院 石油加工工程-第二阶段在线作业 参考答案

B、正碳离子、正碳离子
C、自由基、正碳离子
D、正碳离子、自由基
我的答案:B 此题得分:0.0分
19.(2.5分) 下面__不是烷烃热反应的规律。
A、C-C键比C-H键更容易断裂
B、长链烷烃容易从中间断裂
C、随分子量增大裂解易进行
D、正构烷烃比异构烷烃更易于断裂
我的答案:D 此题得分:2.5分
正确
错误
我的答案:正确此题得分:2.5分
23.(2.5分) 焦化可加工各种渣油,且工艺简单,是最理想的渣油轻质化过程。
正确
错误
我的答案:错误此题得分:2.5分
24.(2.5分) 流化焦化的生焦率比延迟焦化的高。
正确
错误
我的答案:错误此题得分:2.5分
25.(2.5分) 烃类在催化裂化过程中会发生分解反应、异构化反应、氢转移、芳构化反应和缩合生焦反应,其中分解反应是催化裂化的特有反应。
正确
错误
我的答案:正确此题得分:2.5分
29.(2.5分) 稠环芳香烃最容易在裂化催化剂上吸附。
正确
错误
我的答案:正确此题得分:2.5分
30.(2.5分) 烷烃在裂化催化剂上不易吸附,因此不是良好的裂化组分。
正确
错误
我的答案:错误此题得分:2.5分
31.(2.5分) 炼厂中的蒸馏操作可以归纳为闪蒸、简单蒸馏和精馏三种基本类型。
中国石油大学北京网络学院
石油加工工程-第二阶段在线作业
参考答案
1.(2.5分) 催化裂化装置一般由三个部分组成,即:反应-再生系统、分馏系统、吸收-稳定系统,其中__是催化裂化装置的核心。
A、反应-再生系统
B、分馏系统
催化裂化培训讲义1反应机理

3)环烷烃:分解反应、异构化反应、氢转 移反应
4)芳香烃:脱烷基反应、侧链异构化(3 个C以上)、多环缩合反应
2021/9/27
26
3.2 化学反应的特点
1)烷烃断键在正构中间,异构在叔C原 子的ß键。
2)烯烃很活波,反应速率快,催化主要 反应。
(1)经过半个多世纪的发展,工艺技术已非常 成熟 (2)能最大量生产高RON汽油组分与低碳烯烃 (3)原料适应性较广(从VGO、CGO、DAO到AR、 VR)
2021/9/27
7
(4) 反应转化深度较高,轻油及LPG收率较高 (5)装置压力等级不高,操作条件相对缓和, 投资较省 (相对加氢裂化)
(6)LPG中含有大量低分子烯烃,利用价值非 常高,能生产出高附加值产品
3 )焦炭 焦炭产率5-10%。 焦炭分为:催化碳、附加焦碳、可汽提焦、污染
焦
2021/9/27
18
2.2.2 催化裂化原料和产品特点
原料
products dry gas LPG gasoline LCO
LCO
m% H%
C1~C2 Light cycle
oil
轻<5循环油19,~2即3 催化柴油
C3~C4
分解反应速率2倍烷烃,规律与烷烃相 似,
2021/9/27
27
异构有骨架异构、双键位移异构、几何 异构三种。
氢转移造成汽油饱和和催化剂失活。氢 转移反应比分解反应慢的多。低温高活 性有利于氢转移反应,高温相对抑止氢 转移,生产高辛烷值汽油。
芳构化主要是脱氢形成。
2021/9/27
28
3)环烷烃断键成烯烃和断侧链叔C原子的ß键, 速率较快。氢转移生成大环和芳烃。
催化裂化工艺介绍

1.0催化裂化催化裂化是原料油在酸性催化剂存在下,在500C左右、1X 105〜3X 105Pa 下发生裂解,生成轻质油、气体和焦炭的过程。
催化裂化是现代化炼油厂用来改质重质瓦斯油和渣油的核心技术,是炼厂获取经济效益的重要手段。
催化裂化的石油炼制工艺目的:1)提高原油加工深度,得到更多数量的轻质油产品;2)增加品种,提高产品质量。
催化裂化是炼油工业中最重要的一种二次加工工艺,是重油轻质化和改质的重要手段之一,已成为当今石油炼制的核心工艺之一。
1.1催化裂化的发展概况催化裂化的发展经历了四个阶段:固定床、移动床、流化床和提升管。
见下图:在全世界催化裂化装置的总加工能力中,提升管催化裂化已占绝大多数。
1.2 催化裂化的原料和产品1.2.0原料催化裂化的原料围广泛,可分为馏分油和渣油两大类。
馏分油主要是直馏减压馏分油(VGO),馏程350-500 E,也包括少量的二次加工重馏分油如焦化蜡油等,以此种原料进行催化裂化称为馏分油催化裂化。
渣油主要是减压渣油、脱沥青的减压渣油、加氢处理重油等。
渣油都是以一定的比例掺入到减压馏分油中进行加工,其掺入的比例主要受制于原料的金属含量和残炭值。
对于一些金属含量低的石蜡基原有也可以直接用常压重油为原料。
当减压馏分油中掺入渣油使通称为RFCC。
以此种原料进行催化裂化称为重油催化裂化。
1.2.1产品催化裂化的产品包括气体、液体和焦炭。
1、气体在一般工业条件下,气体产率约为10%-20%,其中含干气和液化气。
2、液体产物1)汽油,汽油产率约为30%-60%;这类汽油安定性较好。
2)柴油,柴油产率约为0-40%;因含较多芳烃,所有十六烷值较低,由重油催化裂化得到的柴油的十六烷值更低,这类柴油需经加氢处理。
3)重柴油(回炼油),可以返回到反应器,已提高轻质油收率,不回炼时就以重柴油产品出装置,也可作为商品燃料油的调和组分。
4)油浆,油浆产率约为5%-10%,从催化裂化分馏塔底得到的渣油,含少量催化剂细粉,可以送回反应器回炼以回收催化剂。
催化裂化的工艺特点及基本原理
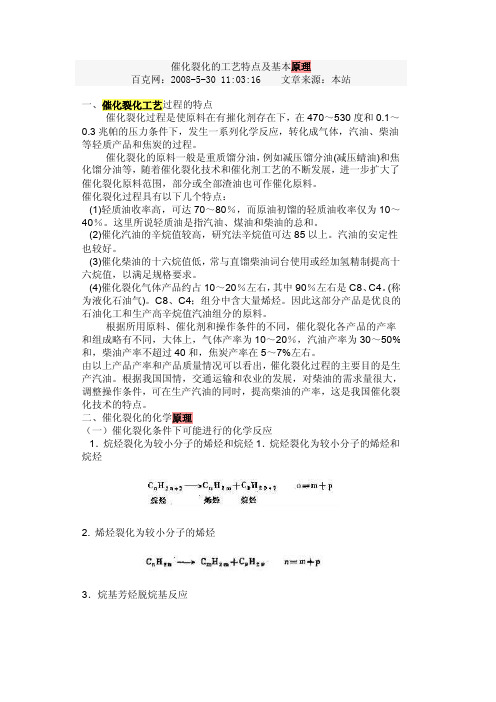
催化裂化的工艺特点及基本原理百克网:2008-5-30 11:03:16 文章来源:本站一、催化裂化工艺过程的特点催化裂化过程是使原料在有摧化剂存在下,在470~530度和0.1~0.3兆帕的压力条件下,发生一系列化学反应,转化成气体,汽油、柴油等轻质产品和焦炭的过程。
催化裂化的原料一般是重质馏分油,例如减压馏分油(减压蜻油)和焦化馏分油等,随着催化裂化技术和催化剂工艺的不断发展,进一步扩大了催化裂化原料范围,部分或全部渣油也可作催化原料。
催化裂化过程具有以下几个特点:(1)轻质油收率高,可达70~80%,而原油初馏的轻质油收率仅为10~40%。
这里所说轻质油是指汽油、煤油和柴油的总和。
(2)催化汽油的辛烷值较高,研究法辛烷值可达85以上。
汽油的安定性也较好。
(3)催化柴油的十六烷值低,常与直馏柴油词台使用或经加氢精制提高十六烷值,以满足规格要求。
(4)催化裂化气体产品约占10~20%左右,其中90%左右是C8、C4。
(称为液化石油气)。
C8、C4;组分中含大量烯烃。
因此这部分产品是优良的石油化工和生产高辛烷值汽油组分的原料。
根据所用原料、催化剂和操作条件的不同,催化裂化各产品的产率和组成略有不同,大体上,气体产率为10~20%,汽油产率为30~50%和,柴油产率不超过40和,焦炭产率在5~7%左右。
由以上产品产率和产品质量情况可以看出,催化裂化过程的主要目的是生产汽油。
根据我国国情,交通运输和农业的发展,对柴油的需求量很大,调整操作条件,可在生产汽油的同时,提高柴油的产率,这是我国催化裂化技术的特点。
二、催化裂化的化学原理(一)催化裂化条件下可能进行的化学反应1.烷烃裂化为较小分子的烯烃和烷烃1.烷烃裂化为较小分子的烯烃和烷烃2. 烯烃裂化为较小分子的烯烃3.烷基芳烃脱烷基反应4.烷基芳烃侧链断裂5.环烷烃裂化为烯烃假如环烷烃中仅有单环,则环不打开:6.氢转移反应如:环烷烃+烯烃→芳香烃+烷烃7.异构化反应:烷烃→异构烷烃烯烃→异构烯烃8.芳构化反应烯烃环化脱氢生成芳香烃,如:9.缩合反应单环芳烃可缩台成稠环芳烃,最后可缩合成焦炭,并放出氢气,使烯烃饱和。
催化裂化反应机理研究进展及实践应用

催化裂化反应机理研究进展及实践应用一、内容描述随着全球能源需求的不断增长和环境保护要求的日益严格,石油化工行业正面临着巨大的压力和挑战。
为了提高石油加工效率,降低生产成本,实现可持续发展,催化裂化技术作为一种重要的石油加工方法,得到了广泛的关注和研究。
本文将对催化裂化反应机理的研究进展进行概述,并结合实际应用案例,探讨催化裂化技术的发展趋势和前景。
首先本文将介绍催化裂化的基本原理和过程,催化裂化是一种在催化剂的作用下,通过加热、高压等条件使原油中的烃类分子断裂成更小分子的过程。
这一过程中涉及到多种反应类型,如氢转移反应、异构化反应、芳构化反应等。
了解这些反应类型及其动力学特性对于优化催化裂化工艺具有重要意义。
其次本文将重点介绍催化裂化反应机理的研究进展,近年来随着科学技术的不断发展,催化裂化反应机理的研究取得了显著成果。
研究人员通过对实验数据和理论模型的分析,揭示了催化裂化反应中的各种关键因素及其相互作用规律。
例如催化剂的选择和性能、反应温度和压力、进料组成和结构等都对催化裂化反应的速率和选择性产生重要影响。
此外研究人员还发现了一些新的催化裂化反应途径和机制,为优化催化裂化工艺提供了理论指导。
本文将结合实际应用案例,探讨催化裂化技术的发展趋势和前景。
随着环保法规的不断完善和技术水平的提高,催化裂化技术在国内外得到了广泛应用。
例如中国石化、中国石油等国内大型石油化工企业已经在催化裂化领域取得了一系列重要突破,实现了高效、低排放的生产目标。
未来催化裂化技术将继续向高性能、高选择性和低能耗方向发展,为全球石油化工行业的发展做出更大贡献。
1. 催化裂化反应技术的重要性和应用领域提高原油利用率:CFCC技术可以将原油中的长链烃类分子分解为较短的烃类分子,从而提高原油的加工效率和利用率。
这对于资源有限的国家和地区具有重要意义,可以降低对进口原油的依赖,减少能源消耗。
降低生产成本:CFCC技术具有较高的转化率和选择性,可以有效地去除原油中的杂质和有害物质,提高产品的质量。
催化裂化(分析的很全面)
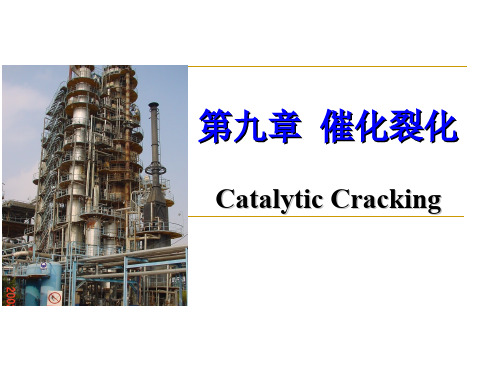
第九章 催化裂化
Catalytic Cracking
第一节 概述
燃料生产中一个重要的问题
如何将原油中的重质馏分油甚至渣油转化成轻
质燃料产品
重质油轻质化
从大分子分解为较小的分子
主要依靠分解反应(热反应和催化反应)
从低 H/C 的组成转化成较高 H/C 的组成
脱 碳(溶剂脱沥青、催化裂化、焦炭化等) 加 氢(加氢裂化)
变)
提高催化剂的活性还有利于促进氢转移反应和异
构化反应,对提高产品质量有利。
催化剂的活性取决于它的结构和组成。
② 活性和催化剂表面上的积炭有关
催化剂表面积炭量↗,活性↙ 。 单位催化剂上焦炭沉积量主要与催化剂在反应器内
的停留时间有关。
催化剂上的焦炭含量还与剂油比有关
③ 剂油比, C/O
一、催化裂化的原料和产品
催化裂化是目前石油炼制工业中最重要的二次加工过
程,也是重油轻质化的核心工艺 ,是提高原油加工深 度、增加轻质油收率的重要手段。
催化裂化原料:重质馏分油 ( 减压馏分油、焦化馏分
油 ) 、常压重油、减渣 ( 掺一部分馏分油 ) 、脱沥青 油。 主要控制指标:金属含量和残碳值
催化裂化技术今后的发展方向: ① 加工重质原料 ② 降低能耗 ③ 减少环境污染 ④ 适应多种生产需要的催化剂和工艺 ⑤ 过程模拟和计算机应用
第二节 石油烃类的催化裂化反应
一、单体烃的催化裂化反应
1 .各类单体烃的裂化反应
(1). 烷 烃
烷烃主要发生分解反应,例如 :
C16H34
+ C8H16 C8H18
催化裂化工艺培训(1)
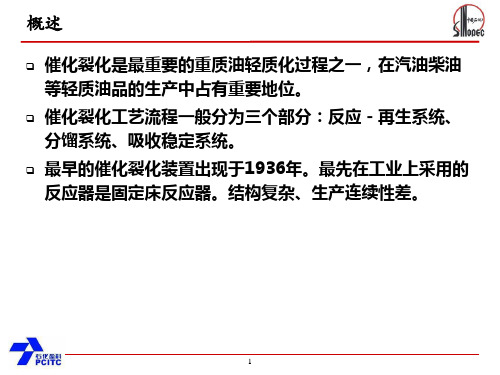
K -301 D -201 D -201 原料油缓冲 罐
32
富气压缩 机
D -302 稳定塔顶回 流罐
分馏塔顶油气 分离器 C - 301 吸收塔 A- 301 A ~ D C - 3
FIQ -30404
FT
干气至双脱
C - 101 反应沉降器 C -202 A 轻柴油汽提 塔
23 22 41 36
催化剂组成及结构:主要活性成分为硅酸铝。天然活性白 土和人工合成硅酸铝都是无定型硅酸铝,分子筛催化剂是 具有固顶晶格结构的硅酸铝盐,具有稳定均以的孔结构。 分子筛根据晶体结构不同分为不同的类型,用于催化裂化 的分子筛主要是Y型分子筛。
7
催化剂
催化剂性能:活性、稳定性(催化剂再生) 选择性(汽油产率)
1
30 25
C - 202 B 轻柴油汽提 塔
3 2 1
1
P - 306 A/ B
D - 301 气压机出口冷 凝罐
1
P - 303 A/ B E -201 A ~ D P - 207 A / B E - 207 A~ D P -201 A / B P - 304 A/ B E- 305 A / B E -302 A /B E -303 A / B E -308 A /B A - 302 A ~ D
催化剂在催化裂化发展中起着重要作用。催化剂的发展主 要经历了活性白土、硅酸铝、分子筛等几个阶段。催化剂 的活性、选择性的提高以及稳定性的增强,促进了催化装 置流程设备的革新和提升管技术的发展,还促进了再生技 术的迅速发展。
2
原料及产品
原料:重质馏分油,主要是直馏减压馏分油(VGO),也包 括焦化重馏分油(CGO,通常须加氢精制),原料重要质量 指标有密度、残碳、硫含量、氮含量、重金属含量等。 产品:气体(10-20%)、催化汽油(30-60%)研究法 辛烷值约在80-90,安定性也较好、催化柴油(0-40%含 有较多芳烃,十六烷值低,安定性较差)、重质油(回炼 油)及焦炭(5-7%,结焦在催化剂表面,只能用空气烧 去不能作为产品分离)。
催化裂化装置提高丙烯收率的操作优化

催化裂化装置提高丙烯收率的操作优化摘要:丙烯是一种重要的石油化工产品,广泛用于聚合物制造、化学合成和其他工业应用。
催化裂化装置是生产丙烯的主要工艺单元之一。
提高丙烯收率对于降低生产成本、提高利润至关重要。
因此,本文主要就如何提高催化裂化装置丙烯收率进行探讨,并提出一系列操作优化策略,旨在实现更高的丙烯产量。
关键词:催化裂化装置;反应条件;丙烯收率;操作优化前言催化裂化装置是石油炼制工业中的重要组成部分,其主要功能是将重负荷的石油馏分分解成更有价值的产品,其中包括丙烯这一关键化学品。
丙烯是一种广泛应用于化工行业的重要原料,用于生产塑料、合成橡胶、燃料添加剂等众多产品。
因此,提高催化裂化装置丙烯的收率对于提高炼油厂的盈利能力和资源利用效率至关重要。
一、操作优化1 反应条件优化反应条件优化是提高催化裂化装置丙烯收率的关键,尤其是反应温度的控制。
催化裂化过程中主要发生裂化反应、氢转移反应、异构化反应和芳构化反应,其中裂化反应和芳构化反应是吸热反应,而氢转移反应和异构化反应是放热反应。
所以随着反应温度的升高,有利于裂化反应的发生,丙烯的产率会逐步提高。
丁烯是非稳定的二次产物,正、异丁烯间的异构反应有利于异丁烯生成,而氢转移反应不利于异丁烯保留。
反应温度较高时,氢转移反应的比重大,异丁烯转化率较高,异丁烯含量下降。
而在高温度的区间内,热裂化反应的比重大,抑制了氢转移反应的发生,异丁烯转化率较低,异丁烯含量增加,这就造成了异丁烯含量先减少后增加的现象。
当反应温度较高时以后,反丁烯-2、顺丁烯-2的生成量和消耗量达到短期平衡。
另外汽油中的烯烃和芳烃是辛烷值较高的组分,提高反应温度后,有利于裂化反应的发生,烯烃和芳烃温度对汽油成分以及辛烷值的影响的生成增加。
同时,消耗烯烃的氢转移反应为放热反应,提高反应温度相当于抑制氢转移,因此提高了裂化反应与氢转移反应比,从而,汽油中烯烃的体积分数和辛烷值都有一定程度的上升。
但是当反应温度达到某一平衡点后,芳烃的生成量不会随着温度的升高而增加,甚至有所减少。
我国催化裂化工艺技术进展

我国催化裂化工艺技术进展一、本文概述催化裂化(FCC)作为一种重要的石油加工技术,在我国石油工业中占据着举足轻重的地位。
随着科技的不断进步和环保要求的日益严格,我国催化裂化工艺技术也在持续发展和创新。
本文旨在全面概述我国催化裂化工艺技术的最新进展,包括技术原理、工艺流程、催化剂研发、设备改进以及环保措施等方面的内容。
通过对这些方面的深入探讨,本文旨在展示我国催化裂化工艺技术在提高石油资源利用效率、促进石油工业可持续发展以及减少环境污染等方面的积极贡献。
本文还将对催化裂化工艺技术的发展趋势进行展望,以期为相关领域的科研人员和企业提供有益的参考和借鉴。
二、催化裂化工艺技术的基本原理催化裂化(Catalytic Cracking)是一种重要的石油加工过程,主要目的是将重质烃类转化为更有价值的轻质产品,如汽油、煤油和柴油等。
其基本原理是利用催化剂加速烃类分子在高温高压环境下的热裂解反应,使长链烃类断裂成较短的链烃,从而改善产品的品质和产量。
催化裂化工艺主要包括热裂化和催化裂化两个阶段。
热裂化是在没有催化剂的情况下,通过高温使烃类分子发生热裂解,生成较小的烃分子。
然而,这个过程的选择性较差,会产生大量的裂化气和焦炭,导致产品收率较低。
催化裂化则是在热裂化的基础上引入催化剂,通过催化剂的选择性吸附和表面酸性,使得烃类分子在较低的温度下就能发生裂解,同时提高裂解的选择性和产品的收率。
催化剂的活性、选择性和稳定性对催化裂化过程的影响至关重要。
在催化裂化过程中,烃类分子首先被催化剂表面的酸性位点吸附,然后在催化剂的作用下发生裂解反应。
生成的较小烃分子随后从催化剂表面脱附,进入气相,最后通过冷凝和分离得到所需的产品。
随着科技的不断进步,我国的催化裂化工艺技术也在不断发展。
新型的催化剂、反应器和工艺条件的优化等技术的发展,使得催化裂化过程的效率和选择性得到了显著提高,为我国石油工业的发展做出了重要贡献。
三、我国催化裂化工艺技术的现状我国催化裂化工艺技术自上世纪五十年代引进至今,经历了从引进消化到自主创新的发展历程,目前已经形成了具有自主知识产权的催化裂化工艺技术体系。
催化裂解工艺(DCC)

催化裂解工艺(DCC)1.工艺原理:催化裂解工艺(DCC)是以重质油为原料、利用择形催化反应制取气体烯烃的新技术。
其中催化裂解Ⅰ型(DCC-Ⅰ)以生产最大量丙烯为主要目的,催化裂解Ⅱ型(DCC-Ⅱ)以生产最大量异丁烯和异戊烯、兼产丙烯和高辛烷值优质汽油为目的。
它们所加工的原料可以是蜡油、蜡油掺渣油或二次加工油以及常压渣油,实现了炼油工艺向石油化工的延伸,开创了一条以重质油为原料直接制取低碳烯烃的新途径,达到国际先进水平。
由于目的产品不同,DCC-Ⅰ和DCC-Ⅱ两者采用的反应器型式、催化剂类型和工艺操作条件都不相同,其差别列于表1。
从表1可见,DCC-Ⅱ的反应时间、反应温度、剂油比及注水量均低于DCC-Ⅰ。
表1:DCC-Ⅰ和DCC-Ⅱ工艺的主要差别DCC-ⅠDCC-Ⅱ反应器型式提升管十床层提升管催化剂CRP CIP反应温度,℃540-580500-530剂油比9-156-9注水量,m%15-256-10产品分布,m%H2~C211.91 5.59C3~C442.2234.49C5+汽油26.6039.00柴油 6.609.77重油 6.07 5.84焦炭 6.00 4.31损失0.60 1.00合计100.00100.00烯烃产率,m%丙烯21.0314.29总丁烯14.0314.65异丁烯 5.13 6.13总戊烯--9.77异戊烯-- 6.77异丁烯/总丁烯0.360.42异戊烯/总戊烯--0.69汽油性质RONC99.396.4MONC84.782.5催化裂解利用择形催化反应原理,将重质原料油选择性裂化成低碳气体烯烃,其丙烯产率是常规FCC的3倍以上。
异丁烯和异戊烯产率也达到FCC的3倍以上。
催化裂解工艺开辟了一条制取低碳烃的新途径。
1.1催化裂解的一般特点①催化裂解是碳正离子反应机理和自由基反应机理共同作用的结果,其裂解气体产物中乙烯所占的比例要大于催化裂化气体产物中乙烯的比例。
②在一定程度上,催化裂解可以看作是高深度的催化裂化,其气体产率远大于催化裂化,液体产物中芳烃含量很高。
- 1、下载文档前请自行甄别文档内容的完整性,平台不提供额外的编辑、内容补充、找答案等附加服务。
- 2、"仅部分预览"的文档,不可在线预览部分如存在完整性等问题,可反馈申请退款(可完整预览的文档不适用该条件!)。
- 3、如文档侵犯您的权益,请联系客服反馈,我们会尽快为您处理(人工客服工作时间:9:00-18:30)。
石油学报(石油加工)2004年10月 ACTA PETROLE I SINICA(PETROLEUM PROCESS ING SECTION) 第20卷第5期文章编号:1001 8719(2004)05 0020 07催化裂化过程中骨架异构化反应的研究.催化裂化工艺过程中骨架异构化反应的表征及其特点SKELETAL IS OMERIZATION REACTION IN CATALYTIC CRACKING.C haracterization and Performances of Skeletal Isomerization Reaction in C atalytic C racking Processes高永灿GAO Yong can(中国石油化工股份有限公司石油化工科学研究院,北京100083)(Rese ar c h Institute of Petroleu m Processing,SINOPE,Beij ing100083,China)摘要:在提升管催化裂化装置(Riser unit,RU)中,以中间基的中东混合油的加氢脱硫常压渣油(DSAR)和石蜡基的减压蜡油(V GO)掺减压渣油(V R)构成的混合油(70%大庆VG O掺混30%大庆VR,质量分数)为催化进料,研究了DCC(Deep catalytic cracking) 和 、常规FCC(Fluid catalytic cracking)和M IP(M aximizing iso paraffin)4种工艺中骨架异构化反应的特点、裂化气组分和汽油馏分支链度的表征及其间的关联性。
结果表明,裂化气中C4组分支链度指数B G1和B G2(B G,Deg ree of branching for cracked gas,B G1为(异丁烷+异丁烯)与(正丁烷+正丁烯)的产率(质量分数)之比,B G2为异丁烷与正丁烷的产率(质量分数)之比)与汽油馏分支链度指数(B N,Degree of branching for naphtha,汽油馏分中异构烷烃与正构烷烃的产率(质量分数)之比)有良好的关联性。
DCC、常规F CC和M IP工艺产品汽油馏分支链度、汽油馏分中异构烷烃含量以及汽油馏分中相同碳原子数烷烃的支链度等,均按DCC <DCC <FCC<M IP的顺序递增。
上述4种工艺汽油馏分中C6烃和C9烃的烷烃组分的支链度均最高,为两个峰值点,但其汽油馏分中烷烃的支链度峰谷点不同,DCC工艺汽油馏分中C7烃的烷烃组分支链度最低,常规FCC和M IP工艺汽油馏分中C8烃的烷烃组分支链度最低。
关 键 词:催化裂化;催化裂解;异构化;支链化;汽油;裂化气;异构烷烃中图分类号:T E624.4 文献标识码:AAbstract:Characterization and performances of skeletal isomerization reaction in different catalytic cracking processes including DCC (Deep catalytic cracking for m ax imizing propylene),DCC (Deep catalytic cracking for maximizing propylene and iso olefin),conventional FCC(Fluidized catalytic cracking for gasoline w ith high octane number),M IP(Maximizing iso paraffin forg asoline w ith higher iso paraffin content)w ere studied on RU(Riser unit)pilot plant withintermediate base DSAR(H ydrodesulfurization atmospheric resid from mid east crude oil)and paraffinic base(70%(mass percent)Daqing VGO mixed w ith30%(m ass percent)Daqing VR) feedstocks.B G1and B G2(B G,Degree of branching for cracked gas,characterized by mass fraction ratios of B G1=(y(i butane+i butene)/y(n butane+n butene)),and B G2=y(i butane)/y(n butane))show ed good correlations w ith B N(Degree of branching for naphtha,characterized by mass fraction ratios of B N=y(i paraffin)/y(n paraffin)).Degree of branching for naphtha B N, iso paraffin content in naphtha and degree of branching for paraffin w ith same number of carbon atoms in naphtha in different processes are all in the order of DCC <DCC <FCC<M IP.The degree of branching for paraffin in naphtha fraction in these processes show ed tw o m ax imum at C6收稿日期:2003 09 28基金项目:国家重点基础项目(973)基金资助(G2000048001)and C 9,and the minimum appeared at C 7for DCC process and C 8for both conventional FCC and M IP processes.Key words:catalytic cracking;deep catalytic cracking;isomerization;branching;gasoline;cracked g as;iso paraffin骨架异构化反应是催化裂化过程中重要的二次反应之一,涉及到正碳离子的氢转移反应[1]。
反应生成的叔碳离子可以从催化剂上脱附生成异构烯烃,或通过吸附负氢离子反应生成异构烷烃,或大分子叔碳离子继续进行裂化链传递反应。
因此,骨架异构反应决定着反应产物的支链度。
O Connor 等[2]提出用汽油馏分中C 6异构烷烃与C 6正构烷烃的质量比(m (i C 6)/m (n C 6))来表征汽油馏分的支链度(Degree of branching)。
而有关用裂化气中的组分来表征催化过程中骨架异构化反应的程度,以及裂化气组分支链度与汽油馏分支链度之间关系的研究报道仍较少。
笔者通过提升管催化裂化中型试验装置(Riser unit,RU ),研究了中国石油化工股份有限公司石油化工科学研究院(简称石科院)开发的利用催化裂化过程生产低碳烯烃的催化裂解技术(DCC,Deep catalytic cracking)、利用催化裂化过程生产富含异构烷烃清洁汽油的催化技术(M IP,M ax im izing iso paraffins)和常规催化裂化工艺中骨架异构化反应的特点及表征方式。
1 实验部分1.1 原料油实验中采用了两种不同类型的原料油:中间基的中东混合油的加氢脱硫常压渣油(DSAR)和石蜡基的减压蜡油(VGO)掺减压渣油(VR)构成的混合油(70%大庆VGO 掺混30%大庆VR,质量分数),其主要性质列于表1。
DSAR 原料油主要应用于DCC 工艺与常规FCC 工艺的对比研究,石蜡基原料油用于常规FCC 工艺与M IP 工艺的对比研究。
表1 原料油性质Table 1 Feedstock propertiesFeedstockProcess (20 )/g cm -3Refracti veindex (70 )Pour poi nt/ w (CCR)1)/%w /%CHSN w / g g -1Ni V DSARDCC ,DCC ,FCC 0.9211 1.498012 4.2387.2112.100.470.12 5.49.870%Daqi ng VGO+ 30%Daqi ng VRM IP,FCC0.89051.4798492.9486.4813.180.150.192.9<0.11)CCR Conradson carbon residue1.2 催化剂实验中不同工艺分别采用各自专用的催化剂,催化剂的主要性质列于表2。
M MC 2、M MC 1和HGY 2000R 分别为DCC 、DCC 和FCC 工艺的专用催化剂,MLC 500作为FCC 和M IP 工艺的实验用催化剂。
根据原料油的不同性质,实验前对不同工艺的专用催化剂,分别采用不同的预处理来模拟工业平衡剂的性能。
M MC 2、M MC 1和H GY 2000R 催化剂的预处理:采用环烷酸镍和环烷酸钒浸渍催化剂,经烘干、焙烧处理后,在790 、90%(体积分数)水蒸气和10%(体积分数)空气混合气氛下老化14h,再以柴油为进料油在RU 装置上对老化剂进行24~48h 的反应、再生连续催化减活。
M LC 500催化剂的预处理则仅在800 、100%(体积分数)水蒸气的气氛下老化12h 。
21第5期 催化裂化过程中骨架异构化反应的研究表2 催化剂性质Table 2 Catalyst propertiesCatalyst Process Activecom ponent w /%Al 2O 3Na 2O S g 1)/m 2 g -1V P 2)/ml g -13)/g cm -34)/%0~40 m 0~149 mw / g g -1Ni V M M C 1DCC M FI+Y zeolite 48.70.102300.290.7515.392.233003000M M C 2DCC M FI+Y zeolite50.10.052040.280.7915.890.533003100HGY 2000R FCC Y zeolite 50.50.172510.190.7113.692.030004000M LC 500FCC,M IPY zeoli te/M FI+Y zeolite51.20.321470.180.7022.490.0--1) Surface area;2) Pore volume;3) Apparent bulk density;4) Particle size distribution1.3 实验装置及产物组成分析对应于不同的催化裂化工艺,采用配有不同反应器模式的提升管催化裂化反应装置(RU),其简明流程见图1。