表面有微结构的硅片键合技术
MEMS工艺体硅微加工工艺

MEMS工艺体硅微加工工艺1. 简介MEMS(Micro-Electro-Mechanical Systems),即微电子机械系统,是一种集成了电子、机械和光学等技术的微型设备。
MEMS工艺体硅微加工工艺是MEMS制造中最常用的一种工艺。
本文将介绍MEMS工艺体硅微加工的基本原理、工序以及常见的应用领域。
2. 工艺原理MEMS工艺体硅微加工工艺以单晶硅片作为主要材料,通过一系列的加工工序,制造出具有复杂结构和微尺寸的器件。
其工艺原理主要包括以下几个方面:2.1 单晶硅片制备单晶硅片是MEMS工艺体硅微加工的基础材料。
通过化学气相沉积(CVD)或磁控溅射等方法,在硅熔体中生长出单晶硅片。
然后,通过切割和抛光等工艺,将单晶硅片制备成规定尺寸和厚度的硅衬底。
2.2 光刻工艺光刻工艺是MEMS工艺体硅微加工中的重要步骤。
首先,将光刻胶覆盖在硅片表面。
然后,使用掩膜板,通过紫外光照射,使光刻胶发生化学反应,形成图案。
接着,将硅片浸泡在显影液中,去除未曝光的光刻胶。
最后,通过加热或暴露于紫外光下,固化已经显影的光刻胶。
2.3 甜蜜刻蚀甜蜜刻蚀是MEMS工艺体硅微加工中的关键步骤。
将制备好的硅片放置在刻蚀室中,通过控制刻蚀气体的流量、温度和压力等参数,使硅片表面发生化学刻蚀。
根据刻蚀深度和刻蚀特性的要求,可以选择不同的刻蚀方法,如湿法刻蚀、干法刻蚀等。
2.4 互连与封装互连与封装是MEMS工艺体硅微加工的最后环节。
通过金属薄膜沉积、光刻和腐蚀等工艺,将金属导线、引线等结构制作在硅片上,并与芯片上的电极进行连接。
同时,为了保护MEMS器件免受机械损伤和环境腐蚀,常常需要对其进行封装,通常采用薄膜封装或微结构封装等方法。
3. 工序流程MEMS工艺体硅微加工的工序流程会因具体的器件设计和制造要求而有所差异。
下面是一个典型的MEMS工艺体硅微加工的工序流程:1.单晶硅制备:通过CVD或磁控溅射等方法,制备出单晶硅片。
SOI的简介及其制备技术
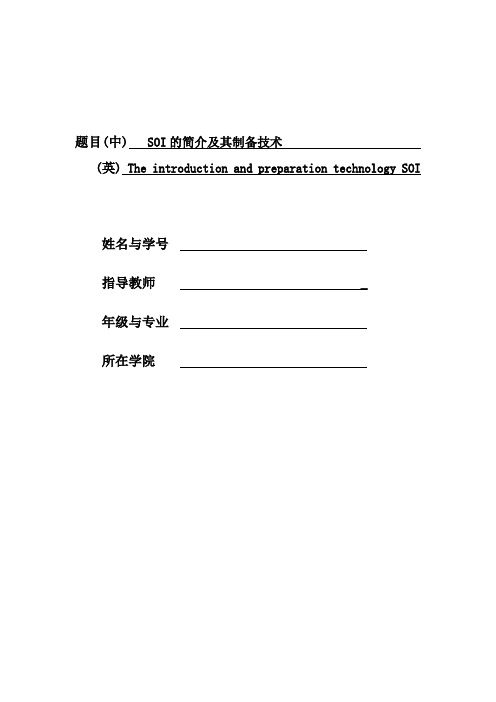
题目(中) SOI的简介及其制备技术(英) The introduction and preparation technology SOI姓名与学号指导教师 _年级与专业所在学院SOI的简介及其制备技术[摘要]SOI材料被誉为“二十一世纪硅集成电路技术”的基础,他可以消除或者减轻体硅中的体效应、寄生效应以及小尺寸效应等,在超大规模集成电路、光电子等领域有广阔的应用前景。
介绍了主要隔离、智能隔离、硅片玻璃以及外延层转移等集中主要的制备SOI材料的方法以及近期相关的研究成果。
本文将以初学者为对象,简单地介绍SOI极其制备技术。
[关键词] SOI 硅材料多孔硅多晶硅键合技术[正文]SOI简介SOI,全称:Silicon-On-Insulator,即绝缘衬底上的硅,也称为绝缘体上的硅。
SOI技术是在顶层硅和背衬底之间引入了一层埋氧化层,是一种具有独特的“Si/绝缘层/Si”三层结构的新型硅基半导体材料。
它通过绝缘埋层(通常)实现了器件和衬底的全介质隔离。
为SiO2下面就SOI的发展、优点、分类以及发展前景进行简单介绍。
虽然SOI技术出现了很久,但是取得突破性进展是在20世纪80年代后期。
以SOI材料具有了体硅等其他硅材料所无法比拟的优点:1)速度高----全耗尽SOI器件具有迁移率高、跨导大、寄生电容小等优点使SOI CMOS 具有极高的速度特性。
2)功耗低----全耗尽SOI器件漏电流小,静态功耗小;结电容与连线电容均很小,动态功耗小。
3)集成密度高----SOI采用介质隔离,不需要制备体硅CMOS电路的阱等复杂隔离工艺,器件最小间隔仅取决于光刻和刻蚀技术的限制。
4)成本低----SOI技术除了衬底材料成本高于硅材料外,其他成本均低于体硅。
SOI CMOS 的制造工艺比体硅至少少3块掩模板,减少13~20%的工序。
5)抗辐照特性好---全介质隔离结构,彻底消除体硅电路中的闩锁效应。
且具有极小的结面积,因此具有非常好的抗软失效,瞬时辐照和单粒子翻转能力。
键合技术
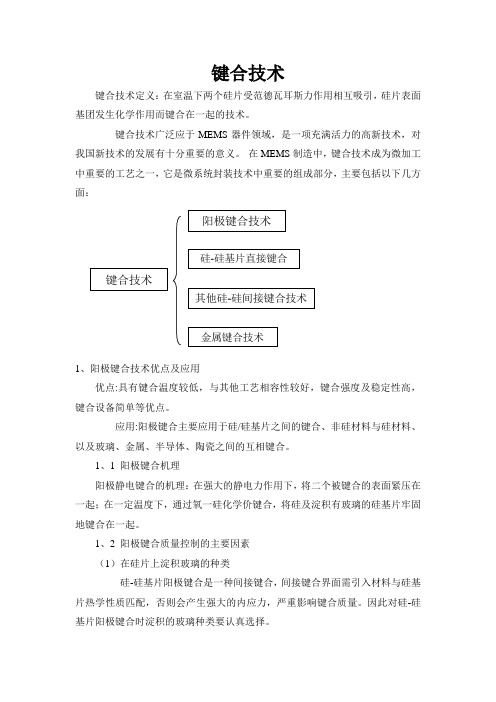
键合技术键合技术定义:在室温下两个硅片受范德瓦耳斯力作用相互吸引,硅片表面基团发生化学作用而键合在一起的技术。
键合技术广泛应于MEMS 器件领域,是一项充满活力的高新技术,对我国新技术的发展有十分重要的意义。
在MEMS 制造中,键合技术成为微加工中重要的工艺之一,它是微系统封装技术中重要的组成部分,主要包括以下几方面:1、阳极键合技术优点及应用优点:具有键合温度较低,与其他工艺相容性较好,键合强度及稳定性高,键合设备简单等优点。
应用:阳极键合主要应用于硅/硅基片之间的键合、非硅材料与硅材料、以及玻璃、金属、半导体、陶瓷之间的互相键合。
1、1 阳极键合机理阳极静电键合的机理:在强大的静电力作用下,将二个被键合的表面紧压在一起;在一定温度下,通过氧一硅化学价键合,将硅及淀积有玻璃的硅基片牢固地键合在一起。
1、2 阳极键合质量控制的主要因素(1)在硅片上淀积玻璃的种类硅-硅基片阳极键合是一种间接键合,间接键合界面需引入材料与硅基片热学性质匹配,否则会产生强大的内应力,严重影响键合质量。
因此对硅-硅基片阳极键合时淀积的玻璃种类要认真选择。
(2)高质量的硅基片准备工艺为了提高硅-硅阳极键合的质量,硅基片表面必须保持清洁,无有机残留物污染,无任何微小颗粒,表面平整度高。
为确保硅基片平整,光滑,表面绝对清洁,为此要采用合适的抛光工艺,然后施以适当的清洗工艺。
清洗结束后,应立刻进行配对键合,以免长期搁置产生表面污染。
(3)控制阳极键合工艺参数保证键合质量阳极键合的主要工艺参数:键合温度,施加的直流电压。
为了使玻璃层内的导电钠离子迁移,以建立必要的静电场。
普遍认为键合温度控制在200℃- 500℃较适宜。
推荐的施加电压一般在20V-1000V之间,其范围较宽,具体视玻璃材料性质及所选的键合温度来决定。
1、3 阳极键合技术的应用硅/硅阳极键合的许多实例是在微电子器件中制造SOI结构,此处介绍一种具体工艺流程,如图1-1所示。
硅玻璃键合

硅玻璃键合
硅玻璃键合,也称为硅键合,是一种常见的表面粘接技术,常用于制造微流体芯片、传感器、光学器件等。
硅玻璃键合的过程是将两个或多个硅材料通过高温和高压的作用下,使其表面接触并形成互连,然后再降温固化。
硅材料的表面会发生物理和化学反应,形成强固的键合。
硅玻璃键合的优点包括:
1. 高强度:硅玻璃键合可以提供非常强的结合力,使得连接的器件更加稳固可靠。
2. 适用范围广:硅玻璃键合可以被应用于多种材料的连接,包括硅、玻璃、陶瓷等。
3. 良好的热稳定性:硅玻璃键合可以承受高温环境,具有较好的热稳定性。
4. 高精度:硅玻璃键合可以实现微米级别的精度,非常适合微观器件的制造。
然而,硅玻璃键合也存在一些限制和挑战:
1. 成本较高:硅玻璃键合的设备和材料成本较高,不适合大批量生产。
2. 对表面精度要求高:硅玻璃键合需要较高的表面精度,因此在制造过程中需要进行精密加工和清洁处理。
3. 对温度环境敏感:硅玻璃键合的过程需要较高的温度和压力,因此对工艺条件要求较为严格。
总体来说,硅玻璃键合是一种重要的微纳技术,具有广泛的应
用前景和潜力,但在实际应用中需要克服一些技术难题,才能更好地发挥其优势。
硅玻璃键合
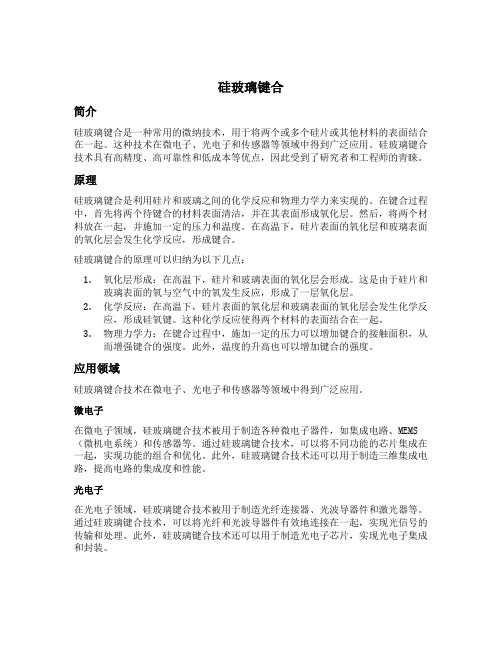
硅玻璃键合简介硅玻璃键合是一种常用的微纳技术,用于将两个或多个硅片或其他材料的表面结合在一起。
这种技术在微电子、光电子和传感器等领域中得到广泛应用。
硅玻璃键合技术具有高精度、高可靠性和低成本等优点,因此受到了研究者和工程师的青睐。
原理硅玻璃键合是利用硅片和玻璃之间的化学反应和物理力学力来实现的。
在键合过程中,首先将两个待键合的材料表面清洁,并在其表面形成氧化层。
然后,将两个材料放在一起,并施加一定的压力和温度。
在高温下,硅片表面的氧化层和玻璃表面的氧化层会发生化学反应,形成键合。
硅玻璃键合的原理可以归纳为以下几点:1.氧化层形成:在高温下,硅片和玻璃表面的氧化层会形成。
这是由于硅片和玻璃表面的氧与空气中的氧发生反应,形成了一层氧化层。
2.化学反应:在高温下,硅片表面的氧化层和玻璃表面的氧化层会发生化学反应,形成硅氧键。
这种化学反应使得两个材料的表面结合在一起。
3.物理力学力:在键合过程中,施加一定的压力可以增加键合的接触面积,从而增强键合的强度。
此外,温度的升高也可以增加键合的强度。
应用领域硅玻璃键合技术在微电子、光电子和传感器等领域中得到广泛应用。
微电子在微电子领域,硅玻璃键合技术被用于制造各种微电子器件,如集成电路、MEMS (微机电系统)和传感器等。
通过硅玻璃键合技术,可以将不同功能的芯片集成在一起,实现功能的组合和优化。
此外,硅玻璃键合技术还可以用于制造三维集成电路,提高电路的集成度和性能。
光电子在光电子领域,硅玻璃键合技术被用于制造光纤连接器、光波导器件和激光器等。
通过硅玻璃键合技术,可以将光纤和光波导器件有效地连接在一起,实现光信号的传输和处理。
此外,硅玻璃键合技术还可以用于制造光电子芯片,实现光电子集成和封装。
传感器在传感器领域,硅玻璃键合技术被用于制造各种传感器,如压力传感器、温度传感器和加速度传感器等。
通过硅玻璃键合技术,可以将传感器的敏感部分和电子部分有效地连接在一起,实现信号的采集和处理。
MEMS加工工艺及表面加工

这里e+表示空穴,即Si得到空穴后从原子升 到氧化态
腐蚀液中的水解离发生下述反应 H2O=(OH)-+H+
17
Si2+与(OH)-结合,成为:
Si2++2(OH)-——>Si(OH)2
接着Si(OH)2放出H2并形成SiO2,即:
Si(OH)2——> SiO2+H2
44
体与表面微机械技术的比较
表面微机械加工技术
45
硅园片 淀积结构层 刻蚀结构层 淀积牺牲层
刻蚀牺牲层 淀积结构层
刻蚀结构层 释放结构
46
• 微加工过程都是在硅片表面的一些薄膜上进行的, 形成的是各种表面微结构,又称牺牲层腐蚀技术。 • 特点:在薄膜淀积的基础上,利用光刻,刻蚀等 IC常用工艺制备多层膜微结构,最终利用不同材料 在同一腐蚀液中腐蚀速率的巨大差异,选择性的腐 蚀去掉结构层之间的牺牲层材料,从而形成由结构 层材料组成的空腔或悬空及可动结构。
SFx+ F
Deep reactiveion etching ~1995
Surface micromachining
~1986
LIGA ~1978
4
MEMS加工技术的种类
硅微机械加工工艺:体硅工艺和表面牺牲层工艺
美国为代表,伴随硅固态传感器的研究、开发而在集成电路平面 加工工艺基础上发展起来的三维加工技术。具有批量生产,成本 低、加工技术可从IC成熟工艺转化且易于与电路集成
• 优点:与常规IC工艺兼容性好; 器件可做得很小
• 缺点:这种技术本身属于二维平面工艺,它限 制了设计的灵活性。
47
48
关键技术
牺牲层技术 薄膜应力控制技术 防粘连技术
硅熔融键合-概述说明以及解释

硅熔融键合-概述说明以及解释1.引言1.1 概述硅熔融键合是一种重要的微纳加工技术,通过将两个硅片在高温下加热至熔点,使它们在接触面上形成均匀的液态硅层,然后在一定压力下使它们融合连接。
这种技术可以实现高精度、高强度的硅片接合,被广泛应用于半导体行业、光电子领域、微机电系统等领域。
本文将从硅熔融键合的定义与原理、应用领域、优势与挑战等方面进行深入探讨,旨在全面了解这一技术的重要性及其未来发展前景。
硅熔融键合作为一种具有巨大潜力的微纳加工技术,对提升微纳器件的性能和功能具有重要意义。
1.2 文章结构本文主要分为引言、正文和结论三部分。
在引言部分中,将概述硅熔融键合的基本概念及其在工程领域中的重要性,介绍文章的结构以及写作目的。
在正文部分,将详细介绍硅熔融键合的定义与原理,探讨其在各个应用领域的具体应用情况,以及分析其在工程领域中的优势和挑战。
在结论部分,将对硅熔融键合的重要性进行总结,展望其未来的发展前景,同时进行对整篇文章的总结,并给出结语。
通过以上结构,将全面解释硅熔融键合的相关内容,为读者提供更深入的了解。
1.3 目的本文旨在深入探讨硅熔融键合技术的相关知识,从而全面了解其定义、原理、应用领域、优势和挑战。
通过对硅熔融键合进行系统性的分析和总结,旨在揭示其在现代科技领域中的重要性和发展潜力。
同时,希望能够引起读者对硅熔融键合技术的关注,促进其在不同领域的应用和推广。
通过本文的阐述,读者可以更深入地了解硅熔融键合技术的价值和意义,为相关领域的研究和实践提供参考和启发。
2.正文2.1 硅熔融键合的定义与原理硅熔融键合是一种常用于微纳加工领域的关键工艺,其原理主要基于高温下硅材料的表面发生熔融并在处理压力的作用下形成键合。
在硅熔融键合过程中,通常需要在高温(约1000C)下将两个硅片表面对接,然后通过施加压力使其发生熔融,随后在一定的时间内保持恒定的温度和压力,使两个硅片的分子结构相互融合,形成牢固的键合。
多层硅片混合键合

多层硅片混合键合一、概述多层硅片混合键合是一种新型的三维集成技术,它可以将不同芯片的多个层次集成在一起,从而实现更高的功能集成度和更小的尺寸。
该技术主要包括两个步骤:先将不同芯片分别制备好,然后将它们通过键合工艺粘合在一起。
二、多层硅片混合键合的优点1. 提高了芯片的功能集成度由于多层硅片混合键合可以将不同芯片的多个层次集成在一起,因此可以实现更高的功能集成度。
这意味着我们可以在一个芯片上实现更多的功能,从而减少了系统中所需的组件数量和尺寸。
2. 提高了系统性能由于多层硅片混合键合可以将不同芯片粘合在一起,因此可以减少电路之间的连接长度和阻抗,从而提高了系统性能。
此外,由于所有组件都被封装在同一个硅片中,因此还可以减少电磁干扰和噪声。
3. 减小了系统尺寸由于多层硅片混合键合可以实现更高的功能集成度,并且减少了电路之间的连接长度和阻抗,因此可以减小系统的尺寸。
这对于一些需要小型化的应用非常有用。
三、多层硅片混合键合的制备工艺1. 制备芯片多层硅片混合键合的第一步是制备芯片。
由于不同芯片可能具有不同的材料和工艺要求,因此制备芯片的方法也各不相同。
一般来说,我们可以通过晶圆加工、薄膜沉积、光刻等技术来制备芯片。
2. 键合工艺多层硅片混合键合的第二步是键合工艺。
在这个步骤中,我们需要将两个或多个芯片粘合在一起。
目前,常用的键合技术包括:(1)焊接键合:利用高温下两个金属表面之间产生的化学反应使其结合。
(2)压力键合:利用高压将两个材料压在一起,从而实现粘结。
(3)电子束焊接:利用电子束将两个材料熔化并粘结在一起。
(4)激光焊接:利用激光将两个材料熔化并粘结在一起。
四、多层硅片混合键合的应用领域多层硅片混合键合技术已经被广泛应用于各种领域,包括:1. 通信多层硅片混合键合技术可以用于制备高性能的光电集成芯片,从而实现更快速、更稳定的通信。
2. 生物医学多层硅片混合键合技术可以用于制备微型生物芯片,并且可以将不同的生物传感器集成在一起,从而实现对不同生物分子的检测和分析。
硅硅直接键合工艺

硅硅直接键合工艺
硅硅直接键合工艺是一种新型的半导体封装技术,它通过将芯片直接键合到基板上,从而实现了更高的集成度和更小的封装尺寸。
这种技术具有许多优点,例如高可靠性、低成本、高效率等,因此在半导体行业中得到了广泛的应用。
硅硅直接键合工艺的原理是利用金属键合技术将芯片直接键合到基板上。
这种技术可以在不使用任何粘合剂的情况下实现芯片和基板的键合,从而避免了粘合剂可能带来的问题。
此外,硅硅直接键合工艺还可以实现多芯片的键合,从而实现更高的集成度和更小的封装尺寸。
硅硅直接键合工艺的优点主要包括以下几个方面:
1. 高可靠性。
硅硅直接键合工艺可以避免粘合剂可能带来的问题,从而提高了封装的可靠性。
2. 低成本。
硅硅直接键合工艺不需要使用粘合剂,从而降低了封装的成本。
3. 高效率。
硅硅直接键合工艺可以实现多芯片的键合,从而提高了封装的效率。
4. 更高的集成度。
硅硅直接键合工艺可以实现更高的集成度,从而实
现更小的封装尺寸。
硅硅直接键合工艺在半导体行业中得到了广泛的应用。
例如,在微处
理器、存储器、传感器等领域中,硅硅直接键合工艺都得到了广泛的
应用。
此外,硅硅直接键合工艺还可以用于制造MEMS(微机电系统)器件、光电子器件等。
总之,硅硅直接键合工艺是一种新型的半导体封装技术,它具有许多
优点,例如高可靠性、低成本、高效率等。
随着半导体技术的不断发展,硅硅直接键合工艺将会得到更广泛的应用。
键合技术在电子器件制造中的应用
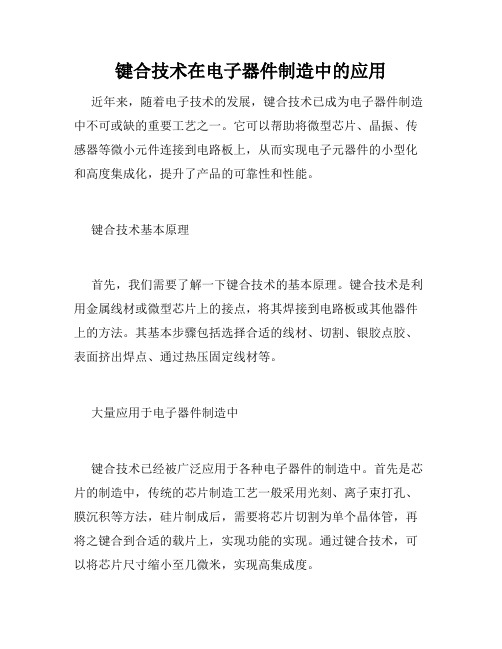
键合技术在电子器件制造中的应用近年来,随着电子技术的发展,键合技术已成为电子器件制造中不可或缺的重要工艺之一。
它可以帮助将微型芯片、晶振、传感器等微小元件连接到电路板上,从而实现电子元器件的小型化和高度集成化,提升了产品的可靠性和性能。
键合技术基本原理首先,我们需要了解一下键合技术的基本原理。
键合技术是利用金属线材或微型芯片上的接点,将其焊接到电路板或其他器件上的方法。
其基本步骤包括选择合适的线材、切割、银胶点胶、表面挤出焊点、通过热压固定线材等。
大量应用于电子器件制造中键合技术已经被广泛应用于各种电子器件的制造中。
首先是芯片的制造中,传统的芯片制造工艺一般采用光刻、离子束打孔、膜沉积等方法,硅片制成后,需要将芯片切割为单个晶体管,再将之键合到合适的载片上,实现功能的实现。
通过键合技术,可以将芯片尺寸缩小至几微米,实现高集成度。
其次是微型化的传感器的制造中,如光纤光栅传感器、湿度传感器、加速度传感器等。
这些微型传感器仅仅有几毫米或者几米的尺寸,而其功能和性能非常优异,很多时候,它们需要采用键合技术来实现和载片的连接,从而更好的实现信号的传输和检测。
最后是晶体振荡器的制造中。
晶体振荡器是一种产生高频信号的微小元件,其通过石英晶体材料生产较高频率的电脉冲,而其在电子产品的制造中扮演着非常重要的角色。
晶体振荡器需要将线材焊接到片上,通过表面挤出焊点等键合工艺实现,从而确保其在电子产品中的高可靠性、高稳定性及高精度。
发展趋势随着电子产品小型化和多功能化的趋势日益流行,人们对电子器件的形态、性能和特性都有了更高的要求。
因此,未来的键合技术应不仅能满足在尺寸、密度和性能方面的要求,同时也必须更高效、更环保。
例如,人们正在研究采用更环保的焊接技术,如无铅焊接,来替代传统的焊接技术,从而在保证电子器件性能的同时,保护生态环境。
此外,随着5G技术的发展,越来越多的电子器件需要频率越来越高,这也对键合技术提出了新的更高要求。
waferbonding工艺

waferbonding工艺Wafer bonding工艺是半导体工业中的一项重要技术,它是把两个或多个半导体片子(wafer)粘合在一起,从而形成一个更加复杂的结构,同时实现不同材料之间的接口整合。
Wafer bonding工艺常常被用于开发新型器件,例如MEMS(微机电系统)、功率半导体器件和光电器件等。
Wafer bonding可分为分子键合、压合键合和焊接键合三种类型。
分子键合利用分子间吸引力粘合SiO2表面,一般使用的技术有Anodic Bonding(阳极键合)和Thermal Compression Bonding(热压键合)。
压合键合是通过施加压力的方式使两片wafer复合在一起,本质上来说就是利用高压力形成键合。
最后,焊接键合需要一定的加热或电极反应,将氧化物等杂质去除,然后进行焊接,同时合成一种新的化合物来实现键合。
其中,阳极键合常常被用于制备MEMS器件。
该技术的基本思路是利用正电荷引导SiO2离子到带负电的Si片子上,形成一个氧化物层,从而形成粘合。
它具有低时间成本、能够实现低压键合、低温度等优点。
除了阳极键合,还有Eutectic Bonding。
这种方式需要提前制造出某种薄膜,通过在火炬中快速加热,并在特定条件下液化形成短暂的液面,从而实现两片wafer纵向复合的过程。
另一方面,拉伸键合存在的问题是不可逆性和固态扩散造成的不稳定性。
所以我们需要采取合适的方式进行实验室操作,同时采用机器视觉方法观测这种键合的可靠性,以确保其质量。
总之,Wafer bonding工艺是半导体行业不可或缺的技术之一。
它有着多种实现方式,应用广泛。
而对于不同种类的材料配对,也需要对相应的键合方式进行选择。
同时,为保证其质量稳定,还需要对它进行适当的监控和测试,从而对其进行优化和改进,以满足未来的生产需要。
半导体硅片发展历程、常见形态及SOI硅片的4种制备技术?

半导体硅片发展历程、常见形态及SOI硅片的4种制备技术?硅材料根据晶胞的排列方式不同,分为单晶硅和多晶硅。
单晶硅和多晶硅最大的区别是单晶硅的晶胞排是有序的,而多晶硅是无序的。
在制造方法方面,多晶硅一般是直接把硅料倒入坩埚中融化,然后再冷却而成。
单晶硅是通过拉单晶的方式形成晶棒(直拉法)。
在物理性质方面,两种硅的特性相差较大。
单晶硅导电能力强,光电转换效率高,单晶硅光电转换效率一般在 17%~25%左右,多晶硅效率在 15%以下。
光伏硅片:由于光电效应,且单晶硅优势明显,所以人们使用硅片完成太阳能到电能的转换。
在光伏领域使用的一般为圆角方形的单晶硅电池片。
价格较便宜的电多晶硅片也有使用,但转换效率较低。
由于光伏硅片对纯度、曲翘度等参数要求较低,所制造过程相对简单。
以单晶硅电池片为例,第一步是切方磨圆,先按照尺寸要求将单晶硅棒切割成方棒,然后将方棒的四角磨圆。
第二步是酸洗,主要是为了除去单晶方棒的表面杂质。
第三步是切片,先将清洗完毕后的方棒与工板粘贴。
然后将工板放在切片机上,按照已经设定好的工艺参数进行切割。
最后将单晶硅片清洗干净监测表面光滑度,电阻率等参数。
半导体硅片:半导体硅片比光伏硅片的要求更高。
首先,半导体行业使用的硅片全部为单晶硅,目的是为了保证硅片每个位臵的相同电学特性。
在形状和尺寸上,光伏用单晶硅片是正方形,主要有边长125mm,150mm,156mm 的种类。
而半导体用单晶硅片是圆型,硅片直径有 150mm(6 寸晶圆),200mm(8 寸晶圆)和 300mm (12 寸晶圆)尺寸。
在纯度方面,光伏用单晶硅片的纯度要求硅含量为4N-6N 之间(99.99%-99.9999%),但是半导体用单晶硅片在9N(99.9999999%)-11N(99.999999999%)左右,纯度要求最低是光伏单晶硅片的1000 倍。
在外观方面,半导体用硅片在表面的平整度,光滑度和洁净程度要比光伏用硅片的要求高。
硅硅直接键合的理论及工艺研究
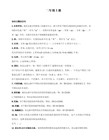
图2.4图2—5同),如图2—6所示,设单个硅片的厚度为“,表面起伏高度为2^,凹部为一圆9合界面的电流传输特性。
因此控制氧化层厚度在2nm以下也是关键技术之一。
图2.10用TEM方法观测的退火到950℃的亲水键合片同时,氧化层的存在导致键合片中杂质扩散行为不同与半导体的正常扩散。
键合工艺控制的主要目的要保证界面杂质扩散特性。
由于键合界面晶格中断会产生一定的缺陷,从而降低少子寿命增大漏电流。
因此为保证后续器件的性能,杂质要有一定扩散,以使键合界面位于重掺杂区。
但如果杂质扩散太深,杂质分布将明显偏离突变PN结,I区串联电阻增大,使电子器件性能降低。
因此,需要通过键合片退火温度和时间控制,通过工艺优化,达到产品要求。
14键合片中空洞。
通过软件处理可进行空洞面积测量,图像保存及有关分析功能的应用。
图3.4为用超声波显微镜检测硅硅键合片中的空洞图象。
此方法分辨率比较高,虽然所用到的系统比X射线的系统便宜,但还是相当昂贵,而且成像时间较长;最重要的一点是它必须将待测样品放在液体中扫描观测,因此在预键合阶段不能使用此方法检测空洞,这很大程度上限制了它在键合片上的应用。
图3.3超声波探测示意图1.)输入脒冲2.)输出端3.)rf转换器4.)相匹配的电路网5)zn0换能器6.)xy扫描器7)蓝宝石捧(11km,s)8.)超声探头9.)相匹配的涂层10.)去离子水(15km,s)1l1硅键台片样品图3-4硅键合片空洞超声波检测照片3.1.3红外透射检测法[4】红外透射检测方法(IR检测法)是在检测键合片空洞时最常用的方法,它是一种实时监控的探测方法。
图3.5为键合片界面空洞IR探测系统框图。
由于红外光在硅键合片界面空洞与硅材料之间的透射率不同,当一定强度的红外平行光线从键合片一面垂直入射到键合片表面时,在键合片另一面红外摄像仪将收集到该硅键合片透射的红外光,最后成像于监视器上,就可观察到硅键合片中空洞的大小、形状。
硅片键合技术2024

引言概述:硅片键合技术(二)是针对硅片键合方法的深入探讨。
本文将从硅片键合技术的原理和应用、不同类型的硅片键合方法、硅片键合的优缺点、硅片键合的应用前景以及未来发展方向等五个大点展开论述。
本文旨在对硅片键合技术进行全面分析,以期读者对该技术有更加深入的了解。
正文内容:1.硅片键合技术的原理和应用1.1硅片键合技术的基本原理1.2硅片键合技术的应用领域1.3硅片键合技术在集成电路封装中的应用2.不同类型的硅片键合方法2.1硅硅键合方法2.2硅玻璃键合方法2.3硅金属键合方法2.4硅聚合物键合方法2.5硅其他材料键合方法3.硅片键合的优缺点3.1硅片键合的优点3.2硅片键合的缺点4.硅片键合的应用前景4.1硅片键合在集成电路封装中的应用前景4.2硅片键合在MEMS器件制造中的应用前景4.3硅片键合在光电子器件制造中的应用前景5.硅片键合技术的未来发展方向5.1硅片键合技术的改进和创新5.2硅片键合技术与其他相关技术的融合5.3硅片键合技术的工艺设备和工艺流程的改进总结:硅片键合技术作为一种关键的封装技术,在集成电路、MEMS器件和光电子器件等领域具有广泛的应用前景。
通过深入探讨硅片键合技术的原理和应用、不同类型的键合方法、优缺点以及未来的发展方向,可以发现该技术在解决器件封装和组装过程中的问题方面具备许多优势。
硅片键合技术仍然存在一些挑战,需要不断改进和创新。
未来,随着工艺设备和工艺流程的进一步改进以及与其他相关技术的融合,硅片键合技术将迎来更加广阔的发展前景。
希望本文能够对读者对硅片键合技术有更加深入的了解,并为相关领域的研究和应用提供一定的参考价值。
单晶硅阳极键合
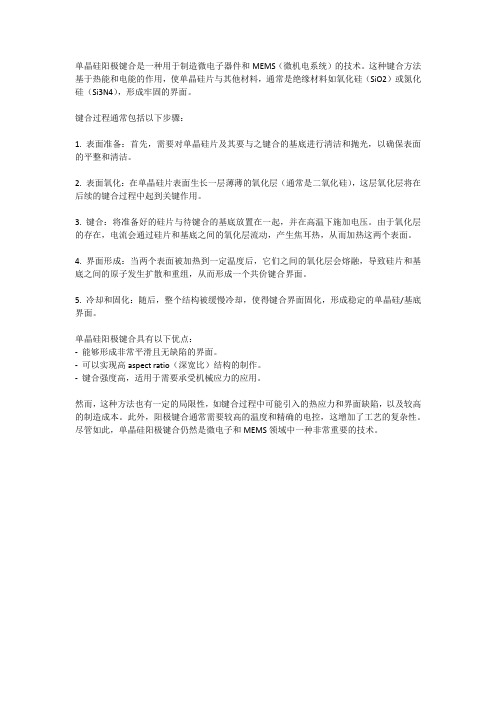
单晶硅阳极键合是一种用于制造微电子器件和MEMS(微机电系统)的技术。
这种键合方法基于热能和电能的作用,使单晶硅片与其他材料,通常是绝缘材料如氧化硅(SiO2)或氮化硅(Si3N4),形成牢固的界面。
键合过程通常包括以下步骤:
1. 表面准备:首先,需要对单晶硅片及其要与之键合的基底进行清洁和抛光,以确保表面的平整和清洁。
2. 表面氧化:在单晶硅片表面生长一层薄薄的氧化层(通常是二氧化硅),这层氧化层将在后续的键合过程中起到关键作用。
3. 键合:将准备好的硅片与待键合的基底放置在一起,并在高温下施加电压。
由于氧化层的存在,电流会通过硅片和基底之间的氧化层流动,产生焦耳热,从而加热这两个表面。
4. 界面形成:当两个表面被加热到一定温度后,它们之间的氧化层会熔融,导致硅片和基底之间的原子发生扩散和重组,从而形成一个共价键合界面。
5. 冷却和固化:随后,整个结构被缓慢冷却,使得键合界面固化,形成稳定的单晶硅/基底界面。
单晶硅阳极键合具有以下优点:
-能够形成非常平滑且无缺陷的界面。
-可以实现高aspect ratio(深宽比)结构的制作。
-键合强度高,适用于需要承受机械应力的应用。
然而,这种方法也有一定的局限性,如键合过程中可能引入的热应力和界面缺陷,以及较高的制造成本。
此外,阳极键合通常需要较高的温度和精确的电控,这增加了工艺的复杂性。
尽管如此,单晶硅阳极键合仍然是微电子和MEMS领域中一种非常重要的技术。
MEMS键合工艺简介
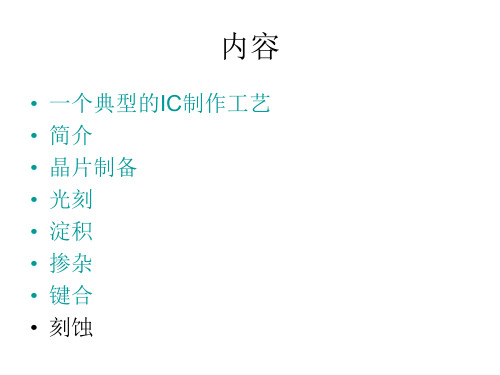
工艺及参数影响
• 表面处理的作用:吸附OH根很关键 NH4OH、H2SO4、等离子体处理 • 温度的影响; • 与温度有关的孔洞;沾污碳氢化合物随温度生高 (200~800度)释放产生孔洞,大于1100高温退 火或先800度退火处理可消除 • 键合强度:随温度生高增加 • 界面氧化层的稳定:三种机制解释 • 表面平整度: • 沾污粒子:1微米粒子产生4.2mm孔洞 足够清洗、超净环境、平整表面、高温处理、 低温键合:在小于500度下完成键合
内容
• • • • • • • • 一个典型的IC制作工艺 简介 晶片制备 光刻 淀积 掺杂 键合 刻蚀
键合
键合
键合工艺
键合:静电键合、热键合、“复合”键合 键合的目的是通过外界作用将多个基片“粘接”
பைடு நூலகம்
不同的键合方式,键合原理不同
静电键合
静电键合:Wallis和Pomerantz于1969年提出,静电键合可把金属、 合金、半导体与玻璃键合 原理: • 硼硅玻璃、磷硅玻璃在一定 温度下软化,行为类似电解 质,外加电压下,正离子 (Na)向阴极漂移,在阳极形成空间电荷区, 外加电压落于空间电荷区,漂移停止 • 如硅接阳极,玻璃接阴极,硅玻璃接触, 在界面形成的负空间电荷区与硅发生化学 反应,形成化学键Si-O-Si,完成键合 • 可通过检测电流监测键合 是否完成
复合键合
“复合”键合 原理利用中间层之间的反应完成键合 • 带硅化物的键合:NiSi,PtSi,TiSi2等 • 金硅键合:利用金硅互熔点低的特点(400度左右) • 非晶硅
金硅共晶键合
键合技术比较
键合对准
键合质量检测
红外检测
划片
SEM观察
静电键合
工艺及工艺参数的影响
几种主要的键合方法
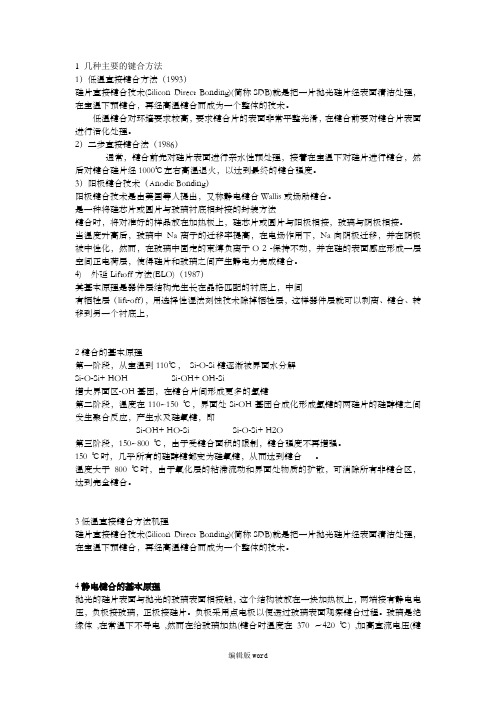
1 几种主要的键合方法1)低温直接键合方法(1993)硅片直接键合技术(Silicon Direct Bonding)(简称SDB)就是把一片抛光硅片经表面清洁处理,在室温下预键合,再经高温键合而成为一个整体的技术。
低温键合对环境要求较高,要求键合片的表面非常平整光滑,在键合前要对键合片表面进行活化处理。
2)二步直接键合法(1986)通常,键合前先对硅片表面进行亲水性预处理,接着在室温下对硅片进行键合,然后对键合硅片经1000℃左右高温退火,以达到最终的键合强度。
3)阳极键合技术(Anodic Bonding)阳极键合技术是由美国等人提出,又称静电键合Wallis或场助键合。
是一种将硅芯片或圆片与玻璃衬底相封接的封装方法键合时,将对准好的样品放在加热板上,硅芯片或圆片与阳极相接,玻璃与阴极相接。
当温度升高后,玻璃中Na离子的迁移率提高,在电场作用下,Na向阴极迁移,并在阴极被中性化,然而,在玻璃中固定的束缚负离子O 2 -保持不动,并在硅的表面感应形成一层空间正电荷层,使得硅片和玻璃之间产生静电力完成键合。
4) 外延Liftoff方法(ELO)(1987)其基本原理是器件层结构先生长在晶格匹配的衬底上,中间有牺牲层(lift-off),用选择性湿法刻蚀技术除掉牺牲层,这样器件层就可以剥离、键合、转移到另一个衬底上,2键合的基本原理第一阶段,从室温到110℃,Si-O-Si键逐渐被界面水分解Si-O-Si+ HOH Si-OH+ OH-Si增大界面区-OH基团,在键合片间形成更多的氢键第二阶段,温度在110~150 ℃,界面处Si-OH基团合成化形成氢键的两硅片的硅醇键之间发生聚合反应,产生水及硅氧键,即Si-OH+ HO-Si Si-O-Si+ H2O第三阶段,150~800 ℃,由于受键合面积的限制,键合强度不再增强。
150 ℃时,几乎所有的硅醇键都变为硅氧键,从而达到键合。
温度大于800 ℃时,由于氧化层的粘滞流动和界面处物质的扩散,可消除所有非键合区,达到完全键合。
键合技术概述

引言概述在现代电子技术领域,键合技术是一项关键技术,广泛应用于集成电路、光电子器件、微电子封装等领域。
键合技术的目的是将两个或多个物体通过键合技术放置在一起,以实现电子设备的电连接、信号传递和机械强度的提供。
本文将深入探讨键合技术的原理、分类、应用以及未来发展方向。
正文内容1. 键合技术原理1.1 金属键合技术原理金属键合技术是一种通过热压、焊接或化学反应等方式将两个金属材料永久性连接在一起的技术。
其原理主要基于金属材料的导电性和可塑性,在一定温度和压力下,金属材料之间的分子间力使得两者相互结合。
1.2 硅键合技术原理硅键合技术是应用于微电子封装领域的一种关键技术。
其原理基于硅材料在特定温度和压力下的化学反应,通过硅键合技术可以将芯片与载体物理上固定在一起,并且电连接的同时形成较强的机械支撑。
2. 键合技术分类2.1 金属键合技术分类金属键合技术可以进一步分为焊接、压合和电极化学键合等几类。
焊接是通过热源将两个金属材料熔接在一起,而压合是通过压力将两个金属材料加工成密封形状,并形成固态连接。
电极化学键合则是通过电流和化学反应将两个金属材料连接在一起。
2.2 硅键合技术分类硅键合技术主要可以分为金属键合和焊接键合两类。
金属键合是通过金属材料在高温下的化学反应将芯片与载体连接在一起,而焊接键合则是通过焊料在高温下熔化并冷却形成连接。
3. 键合技术应用3.1 集成电路封装键合技术在集成电路封装中发挥着至关重要的作用。
通过键合技术,可以将芯片与封装基板连接在一起,实现电连接和信号传递,同时提供机械支撑。
不同的键合技术可以适用于不同的封装器件,如BGA、CSP、COB等。
3.2 光电子器件制备光电子器件是利用光与电之间的相互关系进行信息处理和传输的设备。
键合技术在光电子器件制备中起到重要的作用。
例如,在激光器的制备过程中,通过键合技术可以将激光芯片与泵浦源键合在一起,实现光的放大和产生。
而在光通信领域,键合技术也被用于激光二极管和光纤的连接。
soi键合机原理
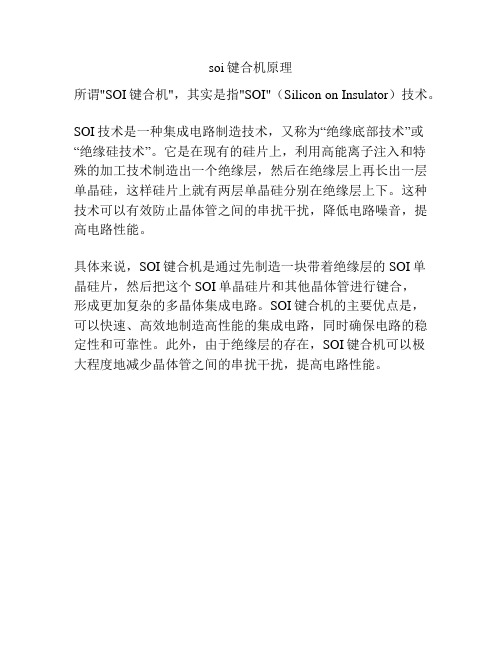
soi键合机原理
所谓"SOI键合机",其实是指"SOI"(Silicon on Insulator)技术。
SOI技术是一种集成电路制造技术,又称为“绝缘底部技术”或“绝缘硅技术”。
它是在现有的硅片上,利用高能离子注入和特
殊的加工技术制造出一个绝缘层,然后在绝缘层上再长出一层单晶硅,这样硅片上就有两层单晶硅分别在绝缘层上下。
这种技术可以有效防止晶体管之间的串扰干扰,降低电路噪音,提高电路性能。
具体来说,SOI键合机是通过先制造一块带着绝缘层的SOI单
晶硅片,然后把这个SOI单晶硅片和其他晶体管进行键合,
形成更加复杂的多晶体集成电路。
SOI键合机的主要优点是,
可以快速、高效地制造高性能的集成电路,同时确保电路的稳定性和可靠性。
此外,由于绝缘层的存在,SOI键合机可以极
大程度地减少晶体管之间的串扰干扰,提高电路性能。
- 1、下载文档前请自行甄别文档内容的完整性,平台不提供额外的编辑、内容补充、找答案等附加服务。
- 2、"仅部分预览"的文档,不可在线预览部分如存在完整性等问题,可反馈申请退款(可完整预览的文档不适用该条件!)。
- 3、如文档侵犯您的权益,请联系客服反馈,我们会尽快为您处理(人工客服工作时间:9:00-18:30)。
传感器与微系统(Transducer and Microsystem Technologies)2019年第38卷第6期DOI:10.13873/J.1000—9787(2019)06—0056—03表面有微结构的硅片键合技术张栋鹏,蔡安江,周嘉玮,翟彦昭(西安建筑科技大学陕西省纳米材料与技术重点实验室,陕西西安710055)摘要:针对表面带有微结构硅晶圆的封装展开研究,以采用Ti/Au作为金属过渡层的硅—硅共晶键合为对象,提出一种表面带有微结构的硅—硅共晶键合工艺,以亲水湿法表面活化处理降低硅片表面杂质含量,以微装配平台与键合机控制键合环境及温度来保证键合精度与键合强度,使用恒温炉进行低温退火,解决键合对硅晶圆表面平整度和洁净度要求极高,环境要求苛刻的问题。
高低温循环测试试验与既定拉力破坏性试验结果表明:提出的工艺在保证了封装组件封装强度的同时,具有工艺温度低、容易实现图形化、应力匹配度高等优点。
关键词:晶片键合;带有微结构硅晶圆;共晶键合中图分类号:TP212文献标识码:A文章编号:1000—9787(2019)06—0056—03Bonding technology of silicon wafer withmicro-structure on surfaceZHANG Dongpeng,CAI Anjiang,ZHOU Jiawei,ZHAI Yanzhao(Shaanxi Key Laboratory of Nano Materials and Technology,Xi’an University of Architecture&Technology,Xi’an710055,China)Abstract:A novel Si-Si wafer bonding method is presented to achieve micro-structured surface silicon waferpackage.Ti/Au is chosen as metal transition layer to ensure the bonding force.Hydrophilic wet method is used forsurface treatment and to reduce the surface impurity content,micro assembly platform and bonding machine areused to control the bonding environment and temperature to ensure both precision and strength of bonding.Siliconwafer is annealed by using constant temperature furnace.This method can achieve bonding with low level siliconwafer surface and the degree of cleanliness requirements,harsh environmental requirements.The results of highand low temperature cycle test and the established tensile failure test show that this method ensures the strength ofthe packaging module,and has the advantages of low process temperature,easy realization of graphics and highdegree of stress matching.Keywords:wafer bonding;micro-structured surface silicon wafer;eutectic bonding0引言封装技术对微机电系统(micro-electro-mechanical system,MEMS)器件尺寸及功能的影响巨大,已成为MEMS 技术发展和实用化的关键技术[1]。
实现封装的技术手段很多,其中较关键的工艺步骤就是键合工艺。
随着MEMS 技术的发展,越来越多的器件封装需要用到表面带有微结构的硅片键合,然而MEMS器件封装一般采用硅—硅直接键合(silicon directly bonding,SDB)技术[2]。
由于表面有微结构的硅片界面已经受到极大的损伤,其平整度和光滑度远远达不到SDB的要求,要进行复杂的抛光处理,这大大加大了工艺的复杂性和降低了器件的成品率[3]。
Abouie M等人[4]针对金—硅共晶键合过程中凹坑对键收稿日期:2018—03—14合质量的影响展开研究,提出一种以非晶硅为基材的金—硅共晶键合工艺以减少凹坑的形成,但非晶硅的实际应用限制较大。
康兴华等人[5]加工了简单的多层硅—硅结构,但不涉及对准问题,实际应用的价值较小。
陈颖慧等人[6]以金—硅共晶键合技术对MEMS器件进行了圆片级封装[6],其键合强度可以达到36MPa,但键合面积以及键合密封性不太理想,不适用一些敏感器件的封装处理。
袁星等人[7]对带有微结构的硅—硅直接键合进行了研究,但其硅片不涉及光刻、深刻蚀、清洗等对硅片表面质量影响较大的工艺,故其键合工艺限制较大。
目前关于晶片键合的研究很多,工艺日渐成熟,但是对于表面带有微结构的硅片键合研究很少,键合效果很差。
65第6期张栋鹏,等:表面有微结构的硅片键合技术本文针对表面带有微结构硅晶圆的封装问题,提出一种基于采用Ti /Au 作为金属过渡层的硅—硅共晶键合的键合工艺,实现表面带有微结构硅晶圆之间的键合,解决键合对硅晶圆表面要求极高,环境要求苛刻的问题。
1键合试验1.1键合理论共晶键合[8,9]是利用某些共晶合金熔融温度较低的特点,以其作为中间键合介质层,通过加热熔融产生金属—半导体共晶相来实现。
因此,中间介质层的选取可以很大程度影响共晶键合的工艺以及键合质量。
中间金属键合介质层种类很多,通常有铝、金、钛、铬、铅—锡等。
虽然金—硅共熔温度不是最低(363ħ)的,但其共晶体的一种成分即为预键合材料硅本身,可以降低键合工艺难度,且其液相粘结性好,故本文采用金—硅合金共晶相作为中间键合介质层进行表面有微结构的硅—硅共晶键合技术的研究。
而金层与硅衬底的结合力较弱,故还要加入钛金属作为黏结层增强金层与硅衬底的结合力,同时钛也具有阻挡扩散层的作用,可以阻止金向硅中扩散[10,11]。
表面带有微结构硅晶圆的界面已受到极大的损伤,其表面粗糙度远高于抛光硅片(Ra <0.5nm ),有时甚至可以达到1μm 以上。
金硅共晶键合时将金薄膜置于欲键合的两硅片之间,加热至稍高于金—硅共晶点的温度,即363ħ,金硅混合物从预键合的硅片中夺取硅原子,达到硅在金硅二相系(其中硅含量为19%)中的饱和状态,冷却后形成良好的键合[12,13]。
而光刻、深刻蚀、清洗等工艺带来的杂质对于金硅二相系的形成有很大的影响。
以表面粗糙度极高且有杂质的硅晶圆完成键合,达到既定的键合质量成为研究重点。
1.2试验方案本文采用封装组件的上下板与中间可动件为材料进行双面溅金键合试验,通过不断改善表面清洗及处理工艺和预键合工艺,实现表面有微结构的硅—硅键合,确定合适的键合工艺参数,为后续的工艺优化与改良打下基础。
设计的键合主要流程如图1所示。
图1硅—硅键合主要工艺流程1.2.1表面清洗和亲水处理硅—硅键合表面清洗和处理方法分为亲水处理与疏水处理两种,本文采用亲水处理方法,其工艺较简单:1)丙酮超声清洗5min ,去离子水清洗,氮气吹干;2)120ħ浓硫酸双氧水混合(SPM )溶液(浓H 2SO 4ʒH 2O 2=3ʒ1)浸泡处理10min ,去离子水清洗,氮气吹干;3)70ħ氨水双氧水混合(RCAI )溶液(NH 4OHʒH 2O 2=1ʒ1)浸泡处理15min ,去离子水清洗,氮气吹干。
1.2.2预键合1)在预键合表面溅射一层30nmTi 薄膜,再溅射一层200nmAu 薄膜,溅射完成后如图2所示。
图2溅射完成后预键合晶片2)将预键合晶片与中间可动件(图3)在微装配平台上进行预装配(图4)。
图3中间可动件图4预装配示意3)将预装配好的组件紧贴在一起放入键合台上,设定压力为40kPa ,加热至363ħ,保温10min ,随后加热至380ħ,保温15min ,自然降温。
1.2.3退火处理将预键合好的Si 片在氮气的保护下进行快速退火处理,退火温度为300ħ,退火时间为15min 。
2结果分析显微镜下可以观测到有些样片上下板之间有间隙,原因为从微装配平台转移至键合台的过程可能导致结构对准出现偏差,影响键合效果。
取其中5片进行检测,在既定拉力下均未分开,加大拉力进行破坏性检测,得到破损的键合面(图5)。
由图可以看出实验样品存在的键合类型有两种:1)在金—硅界面发生的共晶键合金—硅界面在高于其共晶温度363ħ时生成金硅化合75传感器与微系统第38卷图5破损的键合面物。
该过程对金、硅的质量比例要求极其严格,硅含量略微偏离19%,其共晶温度就立刻上升。
2)在互相接触的金—金界面发生的热压键合在对金层施加一定的压力和温度时,金层发生流动、互融,从而形成键合。
该过程对金的纯度要求较高,即当金层发生氧化就会影响键合质量。
将剩余5片置入恒温炉中进行高低温循环测试,随后在既定拉力下进行检测,样片均未分开。
破坏性测试后,可观测到样片键合率在10%左右,低于标准水平。
3结论1)由既定拉力测试高低温循环测试结果可以看出,该键合工艺在满足实际应用所需键合强度的同时,解决了键合对硅晶圆表面平整度和洁净度要求极高、对环境要求苛刻的问题。
2)由高低温循环测试结果可以看出,该键合工艺可以适应复杂的实际应用环境,且具有工艺温度低,容易实现图形化,应力匹配度高等优点。
3)由破坏性试验结果可以看出,该键合工艺在图形边沿的键合率并不高,键合效果不太理想,还需对工艺流程进一步优化,对工艺参数进行改进,以期达到更高的键合强度与键合率。
参考文献:[1]TEE T Y,FAN X J,LAI Y S.Advances in wafer level packaging (WLP)[J].MicroelectronicsReliability,2010,50(4):479-480.[2]TONG Q Y.Low temperature wafer direct bonding[J].J MEMS,1994,31:29-35.[3]CHENG Y T,LIN L W.Localized silicon fusion and eutectic bonding for MEMS fabrication and packaging[J].J MEMS,2000,9:3-8.[4]ABOUIE M,LIU Q,IVEY D G.Eutectic and solid-state wafer bonding of silicon with gold[J].Materials Science&Enginee-ring B,2012,177(20):1748-1758.[5]康兴华.多层硅直接键合技术的研究[D].南京:东南大学,2011.[6]陈颖慧,施志贵,郑英彬,等.金—硅共晶键合技术及其应用[J].纳米技术与精密工程,2015(1):69-73.[7]袁星,陶智,李海旺,等.从双层到多层带有微结构的硅硅直接键合技术研究[J].航空动力学报,2016,31(11):2628-2634.[8]王翔,张大成,李婷,等.压阻加速度计的Au-Si共晶键合[J].半导体学报,2003,24(3):332-335.[9]张东梅,丁桂甫,汪红,等.MEMS器件气密性封装的低温共晶键合工艺研究[J].传感器与微系统,2006,25(1):82-84.[10]TONG Q Y.Low temperature wafer direct bonding[J].Journal of Microelectromechanical Systems,1994,3(1):29-35.[11]WOLFFENBUTTELRF.Low-temperature intermediate Au-Si wafer bonding eutectic or silicide bond[J].Sensors and ActuatorsA:Physical,1997,62(1/2/3):680-686.[12]JING ER,XIONG B,WANG Y L.The interface of Au/Si eutec-tic bonding studied by IRmicroscope[J].Materials Letters,2010,64(7):827-829.[13]陈继超,赵湛,杜利东,等.利用银锡共晶键合技术的MEMS 压力传感器气密封装[J].纳米技术与精密工程,2013,11(2):174-178.作者简介:张栋鹏(1994-),男,硕士,主要研究方向为微纳执行器件,E—mail:296387731@qq.com。