Camworks的常见2.5轴加工操作流程
CAMworks 教程 CH3

NC程式 G4 1 刀具向右補正
4
開
開
未補正
關
未補正
關
有補正
圖3.33 粗加工NC定義對話框
Z軸提刀 退刀孔
粗切削 精切削 殘料加工 粗精切削
圖3.34 粗加工加工特徵選項 定義對話框
邊界內
以素材的頂端為第一刀的Z起始位置 以素材的頂端為第一刀的Z起始位置
圖3.11 島嶼特徵定義說明
中華大學 CAM實驗室
14
孔 1.特徵定義: 特徵輪廓必頇為封閉圓形。可由草圖、 邊、面定義特徵。 2.可使用的工法: 粗銑、輪廓銑削、中心鑽、鑽孔、搪 孔、鉸孔、錐孔、螺紋銑削。
圖3.12 孔特徵定義說明
中華大學 CAM實驗室
15
外槽穴 1.特徵定義: 介於素材邊界至島嶼周圍平坦區域。 可由草圖、邊、面定義特徵。 2.可使用的工法: 粗銑、輪廓銑削。
深孔啄鑽變化深度
刀具快速至X ,Y孔中心位置後 1. 快速移動至 Z 軸 R 高度 2. 進給切削指定的 q 量 3. 快速返回R高度以移除鑽屑 4. 快速至之前進給退出點位置 5. 切削進給 q 量 6. 重複3-5加工步驟直到孔底 7. 快速返回 R 高度
圖3.31 粗加工加工法定義對話框(8)
3-3-1
粗加工工法銑削加工
圖3.18~圖3.38說明粗加工工法各對話框的參數說明定 義圖。在此工法參數對話框中分別有以下子對話框。
刀具:選定此加工法的選用車削刀具型式及規格。 進給及切削速度(F/S):設定此加工法的切削率與進給速度。
粗加工工法:選定此加工法的加工方法及其相應的參數設定。 NC:設定應用此一工法時,其數控(NC)工具機的相關加工設定。 加工特徵選項:應用此一工法時,其下刀及提刀的相關加工設定。 進階:此加工時相關參數進階設定。 後處理:此加工法的後處理器相關參數設定。 最佳化:此加工法的切削路徑最佳化相關參數設定。
五轴雕刻机操作规程

五轴雕刻机是一种高精度的数控设备,操作规程如下:
1. 开机准备:
a. 检查电源和电气线路是否正常连接。
b. 检查机床各部位是否处于正常状态,如导轨、滑块、传动装置等。
c. 检查刀具和夹具是否安装正确。
2. 软件操作:
a. 启动电脑,并打开雕刻机控制软件。
b. 导入需要雕刻的文件,并进行相应的设置,如刀具路径、切削参数等。
c. 检查刀具路径是否与设计要求一致。
3. 定位和夹紧工件:
a. 将待加工的工件放置在工作台上,并进行定位。
b. 使用夹具将工件夹紧,确保工件不会移动或晃动。
4. 雕刻操作:
a. 根据设定的刀具路径,启动雕刻机进行加工。
b. 监控加工过程,确保刀具和工件之间的间隙适当,避免碰撞或切削不到位。
c. 定期检查刀具的磨损情况,及时更换或修复。
5. 加工完成:
a. 加工完成后,关闭雕刻机和电脑。
b. 清理加工区域,清除切屑和废料。
c. 对雕刻机进行日常维护,如清洁导轨、润滑滑块等。
注意事项:
- 操作人员应熟悉雕刻机的结构和工作原理,遵守操作规程,确保安全。
- 在操作过程中,应注意刀具和工件的相对位置,避免碰撞和损坏。
- 定期检查和维护雕刻机,保持其正常运行状态。
- 在操作过程中,如遇到异常情况或故障,应及时停机并寻求专业人员的帮助。
5轴基本操作流程8.14

精雕五轴设备操作步骤注意:五轴设备操作步骤要严格,操作人员要头脑灵活清晰,否则误操作轻者损毁工件,重者损坏机床、卡具。
一、打开控制软件EN3D,在路径“打开、选择、编辑”界面1、F1文件---打开要加工的文件。
2、F2选择---全部选择要加工的刀具路径。
3、编辑---指令---T指令,设置路径文件中所有刀具对应的刀号。
4、加工---进入加工界面二、在EN3D“加工”界面1、第一次进入EN3D加工界面,设备先进入各轴回原点界面,确保安全情况下让设备各轴回原点建立机床坐标系,进入加工界面。
2、装卡工件。
工件装卡要求:3、装卡刀具设置刀库装卡文件基准刀具(一般为第一把刀具或者粗加工刀具),对刀仪对刀设置刀长,并在F1-F3中设置基准刀长。
装卡其他所有刀具,对刀仪对刀设置刀长,并按前面(步骤一-3)所设置的对应刀号放入刀库。
4、设置工件原点调取基准刀具,(注:此时刀长补偿为0),设置F4工件原点(即程序对应的输出原点)的X、Y、Z、A、C(注:此时开启F8允许手工设置原点,X、Y通过分中或者卡具固定位置得到,Z 通过基准刀具微微接触毛坯表面设置或者通过固定Z向位置计算获得,A一般为0,C取决于卡具、工件装卡位置)。
5、多轴路经转换。
F10---CF5多轴路经转换器,在左侧输入步骤二-4中工件原点X、Y、Z 值,计算偏移值,多轴路经转换。
提示成功后点击确定。
6、计算工件原点F4工件原点中,关闭F8允许手工设置原点,X、Y、Z位置变灰色,点击下方CF2、CF3、CF4分别计算X、Y、Z。
(通过步骤6的操作后,工件原点XY 值为固定的数值)7、设置加工参数设置F2、F3、F5、F6、F7、F7- F8(1).F2进给速度。
进给速度显示为绿色时手动输入值有效,红色为程序控制模式,此时手动输入进给参数不起作用。
通过F2→F10进行转换控制模式。
(2).F3主轴转速。
手动与程控状态设置同上。
(3).F5微调深度。
设置时要看清图示是向上补偿还是向下补偿。
Solidworks集成软件CAMWorks 学习资料2轴铣削初级篇

2. 在快捷菜单上选择参数(Parameters)。
加工类型对话框上显示了机床(Machine)标签。默认的 加工类型是在工艺技术数据库中指定的。铣削(Mill)加工类型-mm 是在这本手册中加工 公制零件的默认加工类型。当您使用 CAWorks 加工您自己的零件,选择您需要加工零件的 加工类型。
机床是在工艺技术数据库中定义的。在使用 CAMWorks 加工零件之前,请确认您设定的机 床是您的设备中所有的。更多信息,请看第七章。
1-3 版权所有·南京东大软件工程有限公司
东大软件
CAMWorks
CAMWorks 加工树
CAMWorks 加工树提供一个对模型加工信息的概览。开始,CAMWorks 特征树只显示数控管理器 (NC Manager)、毛坯(Workspiece)、机床(Machine),以及回收站(Recycle Bin)项目。这颗 树随着数控程序生成、零件设置(Part Setups)和可加工特征的产生逐步得到扩大。树底的标签是 为了在 SolidWorks 树和 CAMWorks 树之间切换。
1-7 版权所有·南京东大软件工程有限公司
东大软件
在此练习中,您将通过用零件补偿的方式来定义毛坯。 1. 右击 CAMWorks 特征树中毛坯(Stock),在快捷菜单上选
择编辑定义(Edit Definition)。定义毛坯(Define Stock)对话 框将出现。
机床信息包括识别待加工零件的信息、如何进行加工,以及数控代码输出的格式。加工类型定 义的重要信息包括:
.加工类型类型-铣削或者车削:加工类型定义可以自动或者交互识别的可加工特征集合。 树上显示的图标区分当前的加工类型是铣削还是车削:
铣削
车削
CAMWORKS使用手册-part-05

免责声明(Disclaimer)几何公司(Geometric Technologies,Inc.)并没有担保,既没有明示也没有暗示关于本手册。
几何公司保留以它认为合适的方式来修订和完善产品的权利,修改本文所包含的信息规范不另行通知。
由于持续的产品开发,本手册的规格和功能描述更改恕不另行通知。
商标(Trademarks)以下和其他产品的名字和公司引用所有专有的商标注册或他们的各自的主人。
CAMWorks®是几何有限公司的注册商标。
SolidWorks®是达索系统公司下SolidWorks集团的注册商标。
FeatureManager™是DS SolidWorks和宾利系统公司共同拥有的一个商标。
所有其他品牌和名称都是他们的各自企业的财产。
目录第一章学习多轴加工基础 (4)多轴加工术语 (5)生成刀具轨迹和NC代码的步骤 (6)多轴加工1 (7)您将学习到 (7)定义机床和后置处理 (7)定义毛坯 (8)插入零件设置并定义多面特征 (9)生成一个操作计划并调整操作参数 (9)Slice Pattern(切片模式) (10)生成刀具轨迹并运行刀具轨迹模拟 (11)调整加工参数 (11)Cuts Across Curve Pattern(与曲线交叉切割模式) (11)定义刀具方向 (12)刀具轨迹后处理 (13)多轴加工2 (13)您将学习 (13)使用干涉检测选项 (14)控制刀具轨迹的始点和终点 (15)第二章学习关于多轴加工更多的知识 (17)多轴加工3 (18)您将学习 (18)在遭遇间隙时定义刀具运动 (19)使用带干涉检查的链接 (20)多轴加工4 (21)您将学习 (21)使用3轴加工倒扣区域 (21)多轴加工5 (25)您将学习 (25)改变加工参数来产生不同的结果 (25)多轴加工6 (27)您将学习 (27)采用曲面和干涉检查来简化加工 (28)索引 (31)第一章学习多轴加工基础CAMWorks多轴加工允许车间和生产设施大量地利用4/5轴机床加工以更大的生产力、设备灵活性和质量。
GibbsCAM2.5轴加工实例
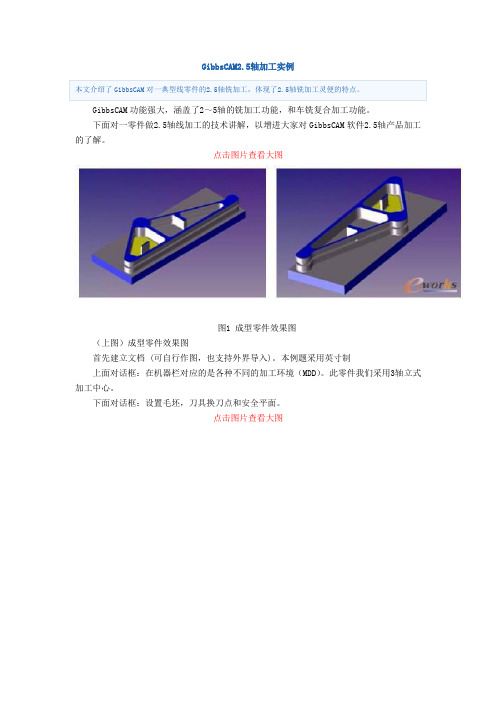
GibbsCAM2.5轴加工实例本文介绍了GibbsCAM对一典型线零件的2.5轴铣加工,体现了2.5轴铣加工灵便的特点。
GibbsCAM功能强大,涵盖了2~5轴的铣加工功能,和车铣复合加工功能。
下面对一零件做2.5轴线加工的技术讲解,以增进大家对GibbsCAM软件2.5轴产品加工的了解。
点击图片查看大图图1 成型零件效果图(上图)成型零件效果图首先建立文档 (可自行作图,也支持外界导入)。
本例题采用英寸制上面对话框:在机器栏对应的是各种不同的加工环境(MDD)。
此零件我们采用3轴立式加工中心。
下面对话框:设置毛坯,刀具换刀点和安全平面。
点击图片查看大图图2 设置毛坯,刀具换刀点和安全平面通过GibbsCAM的尺寸分析工具,我们可以确定要使用的刀具尺寸:点击图片查看大图图3 确定要使用的刀具尺寸打开刀具对话框,定义本次加工所要使用的刀具,分别定义粗铣刀T1:D1、T2:D0.7,精铣刀T4:D0.25和T5:T型刀D1点击图片查看大图图4 刀具对话框去除大余量外围毛坯:采用T1刀具,GibbsCAM有一个比较特别的功能,可以根据选取的刀具,通过划线画出走刀路线。
点击图片查看大图图5 走刀路线完成此步骤后,把轮廓策略和刀具拖至工序栏,便会自动弹出对话框,拾取所画走刀路线,点击线上圆环,确认切削位置。
在编程对话框,设置进刀距离0.1,切深-0.75,Z步距0.25,黑色和白色图标分别可以拖动,白色标记用来确定开始车削位置,黑色标记用来确定结束车削的位置,控制起来相当灵活。
点击图片查看大图图6 设置进刀距离走零件外轮廓:采用T1刀具,打开轮廓编程对话框,拾取轮廓线,点击线上外切圆环定义刀具外切,设置进刀距离0.1,余量0.015切深-0.75,Z步距0.75。
点击图片查看大图图7 走零件外轮廓轮廓精铣:采用T3刀具,只需把更换的刀具拖至工序栏,轮廓编程对话框会继承前面的程序参数,更改余量为0。
点击图片查看大图图8 轮廓精铣铣键槽:T5刀具,采用轮廓铣削方式,注意进刀,因为是T型刀,要防止过切,切深-0.4,一刀到位。
Solidcam2.5轴加工实例
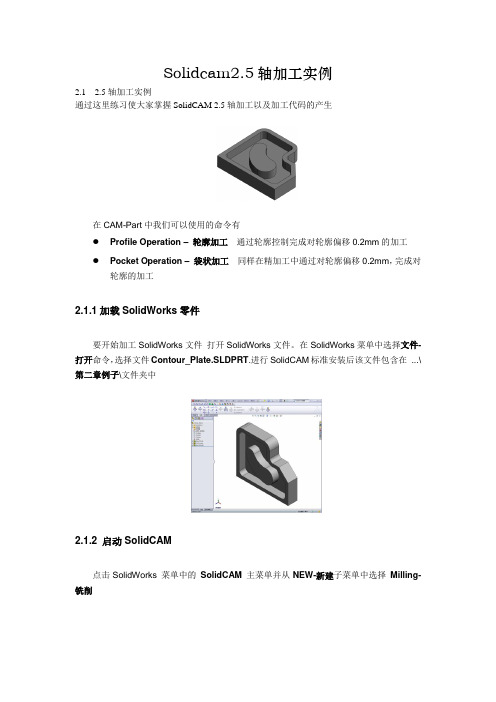
Solidcam2.5轴加工实例2.1 2.5轴加工实例通过这里练习使大家掌握SolidCAM 2.5轴加工以及加工代码的产生在CAM-Part中我们可以使用的命令有●Profile Operation –轮廓加工通过轮廓控制完成对轮廓偏移0.2mm的加工●Pocket Operation –袋状加工同样在精加工中通过对轮廓偏移0.2mm,完成对轮廓的加工2.1.1加载SolidWorks零件要开始加工SolidWorks文件打开SolidWorks文件。
在SolidWorks菜单中选择文件-打开命令,选择文件Contour_Plate.SLDPRT.进行SolidCAM标准安装后该文件包含在 ...\第二章例子\文件夹中2.1.2 启动SolidCAM点击SolidWorks 菜单中的SolidCAM 主菜单并从NEW-新建子菜单中选择Milling-铣削将会显示新的加工对话框在New Milling Part-新建CA M零件,对话框中定义CAM零件的细节默认的名称和SolidWorks 模型名称一致,您也可以更改默认名称mold_insert点击OK 确定2.1.3 定义坐标系选择Multi-sided CoordSys 多方向坐标系,并点击Define CoordSys 定义坐标系出现Milling Part data加工零件数据对话框选择下图黄色平面定义坐标系,CoordSys 坐标显示如下:选择完成确定坐标系的选项,坐标系将自动定义在实体的角落,Z轴自动会垂直我们所选取的平面。
2.1.4 定义切削位置更新下面参数:设置Tool start level加工开始高度为10设置Clearace level安全平面为7单击Part upper level 更新图形,选择实体顶面更新实体顶面的定义,您可以在Pick PartUpper对话框中看到Z-坐标。
单击按钮确认选择,坐标系对话框会再次自动显示出来。
CAMWorks2003 中文操作手册(铣床篇)
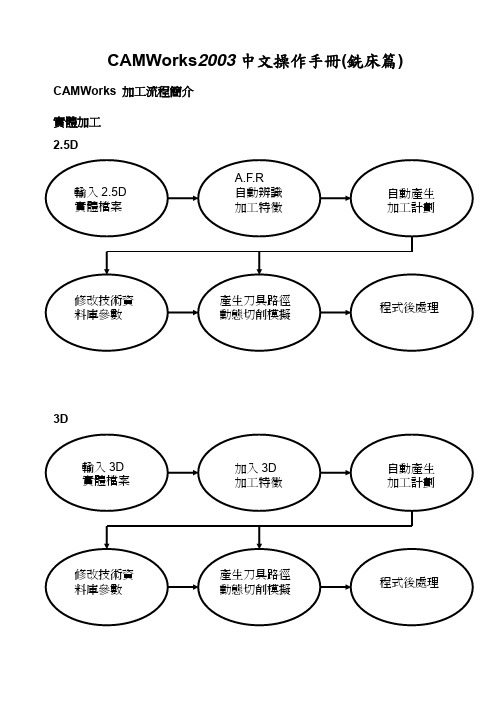
工法之殘料進行運算) §加工深度參數§ 模式:分為等距、精確及沿面等距,為降層進給量的定義模式,定義方式參考如下。
─等距、精確─ 底面預留量:指底部平面加工區域裕留量。 島嶼預留量:當對島嶼頂部加工選取時,可個別指定島嶼頂部之加工預留量。
此時在加工特徵管理員裡,我們可以看到系統自動辨識出之加工特徵。
3.如下圖所示,點選”自動產生加工計劃”。 此時在加工計劃管理員裡,我們可以看到系統依照各加工特徵自動產生出加工計劃。
3
4.點選”產生刀具路徑”。 此時系統會依據加工計劃的參數計算出刀具路徑。
5.點選”動態切削模擬”,或是在加工計劃總管中,在”加工面 2”上按滑鼠右鍵,點選”動態切 削模擬”。 ◎動態切削模擬
單節執行 按一次執行一次單步模擬。
5
開始模擬 點選後即執行持續模擬。
分段模擬 可選取模擬一次的分段單位。 尾端:模擬到加工尾端。 下一層:模擬至下一加工層。 下一加工法:一次模擬一條加
工法。 下一刀具:模擬至下次換刀停。
殘料分析 亦可稱為”誤差比對”,可比對 模擬結束後,與實際成品的誤 差比對,紅色區域代表”Over Cut(過切)”,藍色區域代表” Under Cut(殘料)。
§側壁參數§ 裕留量:側壁加工後裕留不加工部位,一般定義為殘留至成品面的厚度。 等距進給:單層加工時之水平進給量,單位為 mm。 刀徑倍率:同”等距進給”,但計算方式為刀具直徑百分比。 自動清除餘料:一般單層加工時,水平進給量若大於刀徑倍率 50%時,刀具路徑銳角轉角
處產生餘料時,自動產生清除餘料路徑(參考下圖)。
轴类零件加工工艺过程
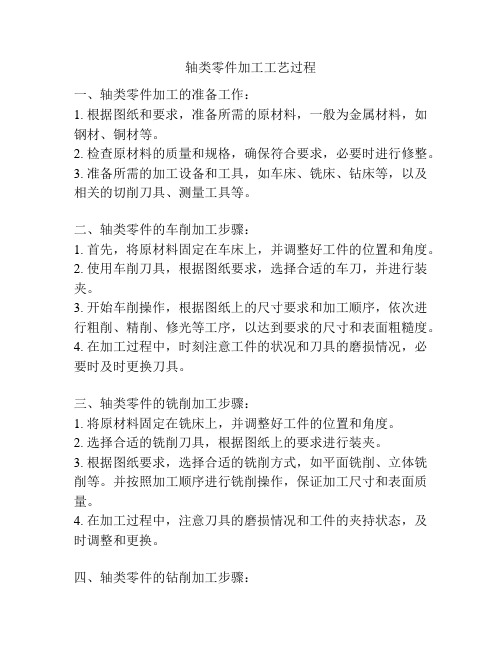
轴类零件加工工艺过程一、轴类零件加工的准备工作:1. 根据图纸和要求,准备所需的原材料,一般为金属材料,如钢材、铜材等。
2. 检查原材料的质量和规格,确保符合要求,必要时进行修整。
3. 准备所需的加工设备和工具,如车床、铣床、钻床等,以及相关的切削刀具、测量工具等。
二、轴类零件的车削加工步骤:1. 首先,将原材料固定在车床上,并调整好工件的位置和角度。
2. 使用车削刀具,根据图纸要求,选择合适的车刀,并进行装夹。
3. 开始车削操作,根据图纸上的尺寸要求和加工顺序,依次进行粗削、精削、修光等工序,以达到要求的尺寸和表面粗糙度。
4. 在加工过程中,时刻注意工件的状况和刀具的磨损情况,必要时及时更换刀具。
三、轴类零件的铣削加工步骤:1. 将原材料固定在铣床上,并调整好工件的位置和角度。
2. 选择合适的铣削刀具,根据图纸上的要求进行装夹。
3. 根据图纸要求,选择合适的铣削方式,如平面铣削、立体铣削等。
并按照加工顺序进行铣削操作,保证加工尺寸和表面质量。
4. 在加工过程中,注意刀具的磨损情况和工件的夹持状态,及时调整和更换。
四、轴类零件的钻削加工步骤:1. 将原材料固定在钻床上,并调整好工件的位置和角度。
2. 选择合适的钻孔刀具,根据图纸要求进行装夹。
3. 根据图纸上的孔径要求,选择合适的钻头,并进行设定,调整钻头的速度和进给量。
4. 开始钻削操作,根据图纸上的孔径位置进行钻孔,保证加工尺寸和孔壁的质量。
5. 在加工过程中,注意刀具的磨损情况和冷却液的使用,及时调整和更换。
五、轴类零件加工的后续工序:1. 进行工件的检验,包括尺寸测量、表面质量等,确保符合要求。
2. 进行必要的热处理、表面处理等工艺,以提高工件的性能和耐用度。
3. 进行最后的整理和打磨工作,使工件达到最终的要求。
4. 进行产品的包装和出库。
以上就是轴类零件加工的基本工艺过程,通过严格按照要求进行加工操作,可以确保加工出高质量的轴类零件。
加工过程中需要密切关注工件的状况和刀具的磨损情况,及时调整和更换,以保证加工质量和工艺效率。
camworks教程

camworks教程CamWorks是一个用于计算机辅助制造(CAM)的软件,可以与SolidWorks等CAD软件相结合使用。
下面是一个CamWorks教程的简要概述:1. 创建零件文件和工序:在CamWorks中,首先需要创建一个零件文件,并在文件中定义工序。
可以通过使用SolidWorks创建工艺特征来定义工序。
2. 创建加工特征:在CamWorks中,可以使用自动特征识别功能来创建加工特征。
该功能可以根据零件的几何形状自动识别出可能的加工特征,包括钻孔、铣削等。
3. 定义刀具库:在CamWorks中,需要定义一个刀具库来存储各种刀具的参数。
可以根据实际情况进行刀具库的设定,包括刀具的半径、长度、剖面等。
4. 设定加工策略:在CamWorks中,可以选择适当的加工策略来完成特定的加工任务。
可以设定粗加工和精加工参数,包括切削速度、进给速度、步距等。
5. 生成刀具路径:在CamWorks中,可以通过生成刀具路径来定义实际的加工路径。
可以根据需要进行多次加工路径的生成,以获得最佳的加工效果。
6. 模拟和验证:在CamWorks中,可以进行刀具路径的模拟和验证,以确保加工过程中没有碰撞和错误。
可以根据需要进行参数调整,以获得最佳的加工结果。
7. 输出NC代码:在CamWorks中,可以生成数控(NC)代码,以便将加工任务发送给数控机床进行实际加工。
可以根据需要选择合适的NC代码格式,包括ISO、G代码等。
请注意,以上教程仅为简要概述,具体实施步骤和操作细节可能因具体情况而有所不同。
建议在使用CamWorks之前,先参考CamWorks官方文档和教程,以获得更详细和准确的信息。
五轴操作规程免费下载
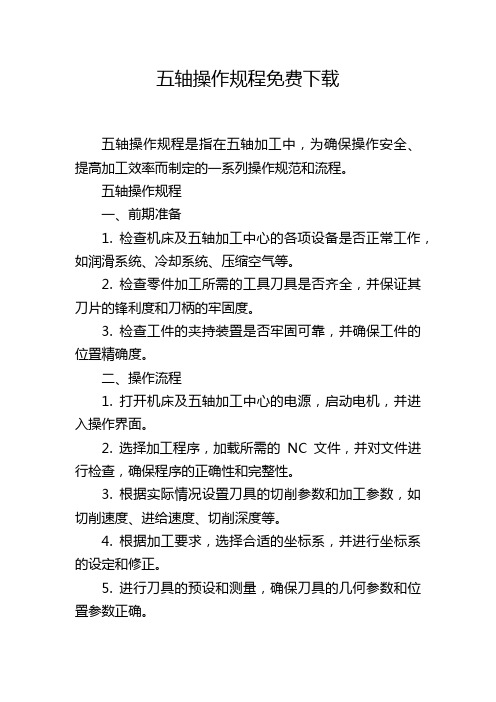
五轴操作规程免费下载五轴操作规程是指在五轴加工中,为确保操作安全、提高加工效率而制定的一系列操作规范和流程。
五轴操作规程一、前期准备1. 检查机床及五轴加工中心的各项设备是否正常工作,如润滑系统、冷却系统、压缩空气等。
2. 检查零件加工所需的工具刀具是否齐全,并保证其刀片的锋利度和刀柄的牢固度。
3. 检查工件的夹持装置是否牢固可靠,并确保工件的位置精确度。
二、操作流程1. 打开机床及五轴加工中心的电源,启动电机,并进入操作界面。
2. 选择加工程序,加载所需的NC文件,并对文件进行检查,确保程序的正确性和完整性。
3. 根据实际情况设置刀具的切削参数和加工参数,如切削速度、进给速度、切削深度等。
4. 根据加工要求,选择合适的坐标系,并进行坐标系的设定和修正。
5. 进行刀具的预设和测量,确保刀具的几何参数和位置参数正确。
6. 对机床进行五轴校准,保证加工轴与工件坐标系的一致性。
7. 启动自动加工模式,并进行加工前干涉检查,确保加工过程中不会发生碰撞等事故。
8. 按照设定的加工顺序和路径,进行加工操作。
三、操作注意事项1. 加工前要仔细检查工件和刀具的尺寸,确保加工精度和表面质量。
2. 在加工过程中,要随时观察加工状态,如加工速度、切削深度、进给速度等。
3. 发现异常情况时,要及时停机,并进行故障排除。
4. 加工结束后,要及时清理机床与工件,保持清洁。
5. 加工零件后,要进行尺寸测量和表面质量检查,确保加工结果符合要求。
四、操作安全措施1. 操作前要佩戴好防护眼镜和防护手套,确保人身安全。
2. 加工过程中要保持安全距离,避免发生意外事故。
3. 禁止在运转中触摸机床和工件,以免受伤。
4. 发现异常情况时,要及时报告上级或维修人员,并按照操作规程进行处理。
五、操作质量控制1. 操作过程中要保持稳定的加工状态,避免发生刀具故障和工件损坏。
2. 加工结束后要仔细检查加工零件的尺寸和表面质量,确保符合要求。
3. 对加工结果不合格的零件要进行重加工或调整,直至符合要求为止。
CNC 工具路径操作指南:使用 2.5 轴工具路径完成卡利普表面说明书
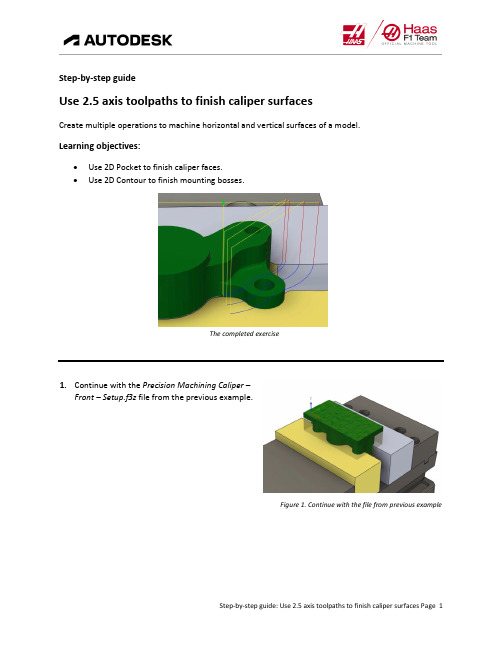
Step-by-step guideUse 2.5 axis toolpaths to finish caliper surfacesCreate multiple operations to machine horizontal and vertical surfaces of a model.Learning objectives:•Use 2D Pocket to finish caliper faces.•Use 2D Contour to finish mounting bosses.The completed exerciseFront – Setup.f3z file from the previous example.Figure 1. Continue with the file from previous example2.You’ll use a 2D Pocket operation to finish thecaliper’s side and top faces; click 2D> 2D Pocket.Figure 2. Create a 2D Pocket operation3.Click the dialog Select to choose the operation’stool. Navigate to the Documents> PrecisionMachining Caliper – Front – Setup tool libraryand choose Tool 8. This bull nose endmill willleave a small fillet between the vertical andhorizontal geometry.Figure 3. Choose the operation’s tool4.Continue to the Geometry tab and select thefive faces shown in the image on right.Figure 4. Select five faces5.Continue to the Passes tab and deactivate theStock to Leave option.Figure 5. Deactivate the Stock to Leave option6.Activate the Multiple Depths option, thenenter 0.02 inches into the MaximumRoughing Stepdown box. OK the dialog togenerate the toolpath preview.Figure 6. Adjust the Maximum Roughing Stepdown value7.Inspect the toolpath preview and notice thatthe material is removed using many passes.Figure 7. Inspect the toolpath preview8.Edit the operation and navigate to thePasses tab. Deactivate the Multiple Depthsoption, then OK the dialog.Figure 8. Deactivate the Multiple Depths option9.Inspect the toolpath preview and notice thateach section material is removed at a singledepth. However, notice the tool gouges thematerial. The modeled geometry is stickingout of the green in-process stock, whichindicates that too much material has beenremoved. Adjusting the lead-in or lead-outvalues would likely resolve this issue.Figure 9. Inspect the toolpath preview10.Edit the operation and navigate to theGeometry tab. Locate the two faces that arecausing the gouge issue and remove them.To remove them, select them in theselection box and click the box’s X.Figure 10. Remove the geometry11.After moving the two offending faces, onlythree faces should be selected. OK thedialog.Figure 11. Inspect the selected faces12.Inspect the toolpath preview and notice thegouge issue is resolved.Figure 12. Inspect the toolpath preview13.Create another new 2D Pocket operationand navigate to the Geometry tab. Selectone of the faces you removed in Step 10.Figure 13. Select a face14.Continue to the Linking tab and deactivatethe Same as Lead-In option. Enter 0.01inches into the Horizontal Lead-Out andLinear Lead-Out Distance boxes. OK thedialog to generate the toolpath preview.Figure 14. Adjust the lead-out values15.Navigate to the Passes tab and deactivatethe Stock to Leave option. OK the dialog.Figure 15. Deactivate the Stock to Leave option16.Inspect the toolpath preview and notice thegeometry is efficiently cut but the tool stillgouges the caliper body.Figure 16. Inspect the toolpath preview17.Select the 2D Pocket operation and right-click it. Choose the Delete option from themenu.Figure 17. Delete the new 2D Pocket operation18.A 2D Contour operation will replace the 2DPocket operation you deleted. Click 2D> 2DContour.Figure 18. Create a 2D Contour operation19.Navigate to the Geometry tab and select theedge shown in the image on the right. Alsoselect the corresponding edge on thecaliper’s other mounting tab.Figure 19. Select two edges20.Navigate to the Passes tab and activate theRoughing Passes option. Enter 0.22 inchesinto the Maximum Stepover box, thenincrease the Number of Stepovers value to3.Figure 20. Configure the roughing passes21.Continue to the Linking tab and deactivatethe Lead-In and Lead-Out options. OK thedialog to generate the toolpath preview.Figure 21. Deactivate the Lead-In and Lead-Out options22.Inspect the toolpath preview and notice thegeometry is correctly cut and does notgouge the caliper body. However, theoperation doesn’t cut the geometry themost efficiently because it is not modelaware. It spends a decent amount of timemachining open air.Figure 22. Inspect the toolpath preview23.Edit the 2D Contour operation and activatethe Stock Contours option. Choose theSelect option from the Geometry Selectionsmenu.Figure 23. Activate the Stock Contours option24.Choose the Outer loops option from theSelect dialog Loops section, then OK thedialog.Figure 24. Select the Outer loops optionStep-by-step guide: Use 2.5 axis toolpaths to finish caliper surfaces Page 1125. Inspect the toolpath preview and notice thatthe blue cutting lines don’t extend as far offthe mounting tab. This means the operation spends less time cutting open air. However,the changes cause a large gouge to thepiston bore area.Figure 25. Inspect the toolpath preview26.Edit the operation and deactivate the StockContours option. OK the dialog. Save the file.Figure 26. Deactivate the Stock Contours option。
CADCAMCAE技术课件-任务2 五轴联动曲线加工实例

目录
1 刻金字塔上的竖轴曲线 2 刻金字塔上的横轴曲线 3 程序输出
任务内容
一、刻金字塔上的竖轴曲线
1、单击[创建操作]命令,在出现的“创建工序”对话框上(见图1-21),“类型”选择为 “mill_multi_axis”;“子类型”选择为第一行第一个图标“可变轮廓铣”;其它选项如下设置: 程序:NC_PROGRAM 使用几何体:WORKPLECE 使用刀具:D1R0.5(2号球头铣刀) 使用方法:METHOD 名称:按照默认或者自己编一个名称即可。
图1-25“切削参数”对话框
任务内容
一、刻金字塔上的竖轴曲线
4)进给率和速度: 主轴速度:5000r/min 进给率:3000 其它参数可取默认值。
任务内容
一、刻金字塔上的竖轴曲线
5)生成刀具轨迹和仿真加工分别单击[生成]和[确认]命令来生成铣刀运行轨迹, 产生仿真切削过程,其刀具轨迹和仿真加工后的效果如图1-26所示。
全部设置如图1-22所示,完成上面的设置后,单击[应用]按钮,进入“可变轮廓铣”对话框。
任务内容
一、刻金字塔上的竖轴曲线
图1-21“创建工序”对话框
图1-22叶片精加工对话框
任务内容
一、刻金字塔上的竖轴曲线
可变轮廓铣对话框参数的设定: 1) 可变轮廓铣的驱动方法:如图1-23所示 方法:曲线/点
图1-28选择程序及仿真后的结果
任务内容
二、刻金字塔上的横轴曲线
1、单击[创建操作]命令,在出现的“创建工序”对话框上(见图1-27),“类型” 选择为“mill_multi_axis”;“子类型”选择为第一行第一个图标“可变轮廓铣”; 其它选项如下设置: 程序:NC_PROGRAM 使用几何体:WORKPLECE 使用刀具:D1R0.5(2号球头铣刀) 使用方法:METHOD 名称:按照默认或者自己编一个名称即可。
Solidcam2.5轴加工实例
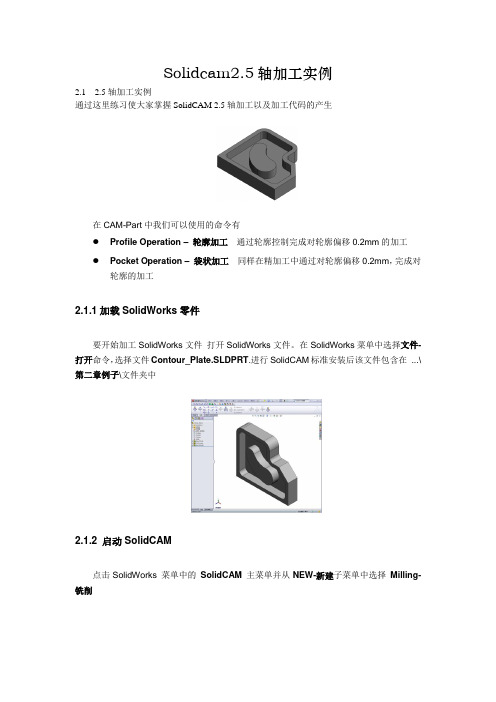
Solidcam2.5轴加工实例2.1 2.5轴加工实例通过这里练习使大家掌握SolidCAM 2.5轴加工以及加工代码的产生在CAM-Part中我们可以使用的命令有●Profile Operation –轮廓加工通过轮廓控制完成对轮廓偏移0.2mm的加工●Pocket Operation –袋状加工同样在精加工中通过对轮廓偏移0.2mm,完成对轮廓的加工2.1.1加载SolidWorks零件要开始加工SolidWorks文件打开SolidWorks文件。
在SolidWorks菜单中选择文件-打开命令,选择文件Contour_Plate.SLDPRT.进行SolidCAM标准安装后该文件包含在 ...\第二章例子\文件夹中2.1.2 启动SolidCAM点击SolidWorks 菜单中的SolidCAM 主菜单并从NEW-新建子菜单中选择Milling-铣削将会显示新的加工对话框在New Milling Part-新建CA M零件,对话框中定义CAM零件的细节默认的名称和SolidWorks 模型名称一致,您也可以更改默认名称mold_insert点击OK 确定2.1.3 定义坐标系选择Multi-sided CoordSys 多方向坐标系,并点击Define CoordSys 定义坐标系出现Milling Part data加工零件数据对话框选择下图黄色平面定义坐标系,CoordSys 坐标显示如下:选择完成确定坐标系的选项,坐标系将自动定义在实体的角落,Z轴自动会垂直我们所选取的平面。
2.1.4 定义切削位置更新下面参数:设置Tool start level加工开始高度为10设置Clearace level安全平面为7单击Part upper level 更新图形,选择实体顶面更新实体顶面的定义,您可以在Pick PartUpper对话框中看到Z-坐标。
单击按钮确认选择,坐标系对话框会再次自动显示出来。
CAXA 制造工程师五轴造型及加工
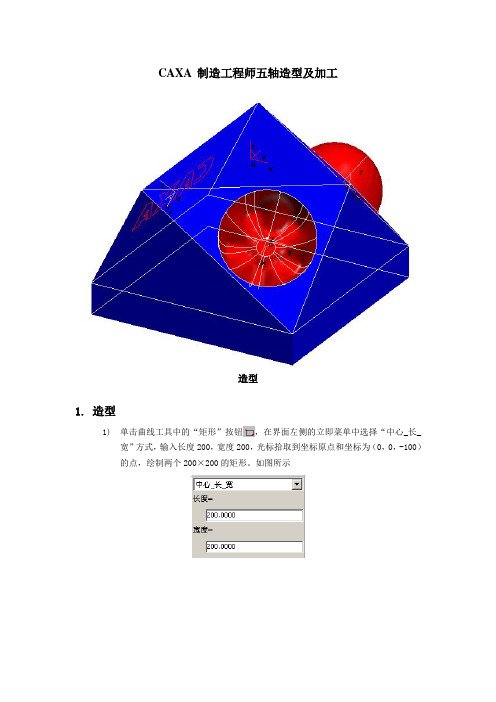
CAXA 制造工程师五轴造型及加工造型1.造型1)单击曲线工具中的“矩形”按钮,在界面左侧的立即菜单中选择“中心_长_宽”方式,输入长度200,宽度200,光标拾取到坐标原点和坐标为(0,0,-100)的点,绘制两个200×200的矩形。
如图所示2)单击曲线工具栏中的“等距线”按钮,在立即菜单中输入距离50,拾取上面矩形的最左面一条边,选择x正方向箭头为等距方向,生成距离为50的等距线,如图所示。
3)单击曲线工具栏中的“直线”按钮,选择“两点线”-“单个”-“非正交”,按图所示,进行连接,其中A,B,C三点为直线的中点。
4)单击曲线工具栏中的“删除”按钮。
剩余曲线如图所示5)单击曲线工具栏中的“点”按钮,选择“批量点”—“等分点”,段数为10 ,按软件提示,拾取曲线。
如图所示6)单击几何变换栏中的“平移”按钮,选择“两点”—“拷贝”—“非正交”。
按软件提示选取要平移的元素为三角形底边,点击右键,输入基点为底边中点,目标点为直线上的第四个点。
如图所示7)单击坐标系栏中的“创建坐标系”按钮,选择“三点”创建新的坐标系,坐标系原点为两直线的交点,第二点为三角形底边中点,第三点为平移后所得的直线的上端点,最后输入坐标系名称,得到新建坐标系。
如图所示8)单击曲线工具栏中的“删除”按钮。
多余曲线和点如图所示9)单击编辑栏中的“隐藏”,将所有线段隐藏起来。
10)按下【F7】键将绘图平面切换到XOZ平面。
11)单击曲线工具中的“矩形”按钮,在界面左侧的立即菜单中选择“中心_长_宽”方式,输入长度42.5,宽度37,光标拾取到坐标原点,绘制一个42.5×37的矩形。
12)单击几何变换工具栏中的“平移”按钮,在立即菜单中输入DX=21.25,DZ=-18.5,然后拾取矩形的四条边,单击鼠标右键确认,将矩形的左上角平移到原点(0,0,0)。
13)单击曲线工具栏中的“等距线”按钮,在立即菜单中输入距离3,拾取矩形的最上面一条边,选择向下箭头为等距方向,生成距离为3的等距线,如图所示。
轴加工工艺流程

轴加工的工艺流程一般分为以下几个步骤:
1.材料准备:选择符合要求的轴材料,进行检查和准备,包括截
断、切割、去毛刺、清洗等工序。
2.粗加工:将轴材料进行粗加工,包括车削、钻孔、铣削、刨削
等工序,依据轴的形状和尺寸要求进行,以保证轴的几何形状和表面粗糙度满足要求。
3.热处理:对轴进行热处理,包括淬火、回火、正火等工序,提
高轴的硬度、强度和耐磨性,以及改善轴的组织结构和性能。
4.精加工:对轴进行精加工,包括磨削、抛光、拉削、滚压等工
序,使轴的表面精度和光洁度达到要求,同时保证轴的尺寸精度和形状公差符合要求。
5.表面处理:对轴进行表面处理,包括喷涂、电镀、镀铬、喷砂
等工序,以提高轴的表面质量和防腐性能。
6.检验:对轴进行质量检验,包括尺寸测量、表面检查、硬度测
试等,以保证轴的质量符合要求。
7.包装:对轴进行包装,包括防潮、防锈、防震等措施,以确保
轴在运输和存储过程中不受损坏。
以上是轴加工的一般工艺流程,具体的步骤和顺序可能会根据轴的材料、形状和尺寸要求而有所不同。
五轴cnc操作方法

五轴cnc操作方法
五轴CNC操作方法要点如下:
1. 首先,确保操作者对CNC机床的基本构造、操作面板和操作软件有一定的了解和熟悉。
2. 确定加工任务和工件尺寸,根据工艺要求编写加工程序。
3. 打开CNC操作软件,导入或手动输入加工程序。
4. 在CNC操作软件中对加工程序进行编辑和优化,如调整切削速度、进给速度、切削路径等。
5. 设置刀具和工件的坐标系,确保刀具和工件的零点正确。
6. 将刀具安装在主轴上,确保刀具夹紧牢固并没有松动。
7. 将工件固定在工作台上,确保工件牢固并没有晃动。
8. 检查CNC机床的各项参数设置是否正确,如机床坐标系、刀具长度补偿、刀具半径补偿、安全距离等。
9. 启动CNC机床,初始化机床,并进行手动操作校对机床的各轴运动。
10. 进行自动运行模式,CNC机床按照加工程序中的指令进行自动加工。
11. 在加工过程中,及时观察机床各轴的运动状态和加工质量,如有异常情况及时停机检查并进行必要的调整。
12. 加工完成后,关闭CNC机床,保存加工程序和相关参数设置。
以上是五轴CNC操作方法的基本要点,具体操作还需要根据具体的机床型号和加工任务而定。
- 1、下载文档前请自行甄别文档内容的完整性,平台不提供额外的编辑、内容补充、找答案等附加服务。
- 2、"仅部分预览"的文档,不可在线预览部分如存在完整性等问题,可反馈申请退款(可完整预览的文档不适用该条件!)。
- 3、如文档侵犯您的权益,请联系客服反馈,我们会尽快为您处理(人工客服工作时间:9:00-18:30)。
Camworks常见2.5轴加工
Camworks可用于常见2.5轴加工,用来实现常见的轮廓铣,面铣,以及螺纹加工.
点击,在弹出的对话框中,选择我们事先设计好的零件,如图
通过对零件的分析,我们可
以看到,对于该零件,有三个
地方要加工,刷面,四个角铣
四个沉台,中间一个M48*3螺纹。
打开Camworks窗口,点击或者在左侧Camworks特征树里双击左侧在弹出的对话框中选择三轴机床,点击选择,然后点击刀具库,在可用刀具库中选择合适的刀具库点确定即可。
点击毛坯管理,系统会按照零件大小,自动设置毛坯大小,毛坯没有太大偏差,可以直接点选左上方的小勾来确定。
在定义好机床和毛坯以后,生成所要的操作可以通过自动和手动生成两种。
Camworks系统不同于其他软件的地方在于:Camworks不仅可以像其他软件一样手动选取并生成加工程序并且可以自动的捕捉并提取加工特征,来生成操作计划,虽然不能包分之百的达到我们的要求,但是大大的节省了编程的时间,在实际使用中非常使用。
在实际使用中,我们可以采取先自动后手动调整的方法。
对机床和毛坯设置好后,直接点击,这时候Camworks便会根据零件特征,来自动获取加工特征,然后在左侧的Camworks特征数
中显示出来及一个孔,四个矩形槽,虽然没有识
别出螺纹,但是后面可以通过手动插入来增加。
生成的加工特征基本上就是所需要的,这儿样可
以直接点击生成操作计划,点击Camworks操作
树,这时候就可以得到系统为我们生成的加工
操作。
,中心钻点眼,然后直径44钻头作中间
孔,然后铰孔,在后面分别是直径14的铣刀去粗铣和轮廓铣。
生成的策略使用的刀具在工艺数据库中可以对应设置。
铰孔是我们不需要的,我们可以删除。
同时缺少一个铣螺纹的操作,我们可以手动添加,点选新建2.5轴操作,在下面的选项中选择螺纹铣削或者在Camworks 特征树中,选中右键,选择新建孔加工操作中选择螺纹铣削,在弹出的对话框中设置刀具的直径和刀杆的直径,如果希望从上往下铣削,可以选择逆铣。
在生成了所有所需要的加工操作后,在刀具数据库没有设定的情况下,需要按自己需要逐一检查并调整刀具大小,加工深度已经每刀
的加工深度。
在所有都设置好后,点击或者点选零件铣削设置,
在弹出的小窗口中,选择第一个来生成刀具轨迹。
刀具轨迹生成后,所有的加工操作将由原来的粉色变为黑色,并且鼠标放在操作上,工件上将会自动呈现对应的刀具轨迹。
刀具轨迹生成后,可以通过模拟来直观的掌握实际加工情况,点选,在弹出的对话框中,可以选择单步模拟或者自动模拟,
点击播放按钮,加工情况便会逐一按照加工顺序来
逐步模拟。
模拟如果
没问题,我们点选后
置处理,选择保存地
址后,按照操作步骤,
最终就可以得到我
们所需要的加工程
序。
在对程序做简单
修改后便可以直接
导入机床加工了。