散热器盖压铸模设计
压铸模具设计范文

压铸模具设计范文压铸模具设计是指为了生产压铸件而设计的模具,其主要任务是将液态金属注入模具中,并在模具中冷却、凝固,最终得到所需形状的金属零件。
压铸模具设计的主要工作包括设计模具的结构、选材、计算模具的合理尺寸和形状等。
一、压铸模具结构设计1.模具整体结构设计:根据压铸件的形状和尺寸,确定模具的整体结构。
一般情况下,压铸模具采用上下模结构,上模为固定模,下模为活动模。
针对复杂形状的压铸件,可能需要设计多个滑模和拉杆。
2.模腔设计:根据压铸件的形状和尺寸,确定模腔的几何形状和尺寸。
模腔的设计应保证在模具关闭时,模腔中的液态金属能够充满整个腔体,并且在冷却凝固过程中,金属能够均匀收缩,避免产生缩孔和其他缺陷。
3.浇口和导流系统设计:浇口和导流系统的设计对于压铸件的质量和生产效率有着重要的影响。
浇口的设计应尽量避免金属的湍流流动,避免气泡的产生。
导流系统的设计应考虑金属的顺序填充和排气,以及冷却和凝固过程中的温度控制。
二、压铸模具选材压铸模具的选材应根据金属的性能和压铸工艺的要求来确定。
通常情况下,模具会选用高强度和耐磨损的合金钢作为材料,以保证模具的使用寿命和精度。
同时,还需要考虑模具的热传导性能,以确保压铸件能够快速冷却、凝固。
三、压铸模具尺寸和形状计算1.模具尺寸计算:模具尺寸的计算包括模腔尺寸、模板尺寸、滑模尺寸、导流系统尺寸等。
模具尺寸的计算需要考虑压铸件的最终尺寸、缩孔和收缩率等因素。
2.模具形状计算:模具的形状计算主要是指模腔内部的曲面和棱角的设计。
对于复杂形状的压铸件,需要使用CAD软件进行三维建模和形状优化,以确保模具的制造精度和压铸件的质量。
压铸模具设计需要充分考虑压铸件的形状和尺寸、材料的性能、压铸工艺要求等因素,通过合理的结构设计、选材和计算,能够提升压铸件的质量和生产效率。
在设计过程中,还需要考虑模具的制造难度和制造成本,以确保模具的可行性和经济性。
压铸铝散热器施工方案设计

压铸铝散热器施工方案设计一、方案背景随着电子设备的发展和智能化程度的提高,电子产品的散热问题愈发突出。
而在电子产品的散热方案中,压铸铝散热器由于其材料优势和制造工艺特点,成为了广泛应用的热管理解决方案之一。
本文旨在针对压铸铝散热器的施工方案进行设计。
二、施工流程1.原材料准备:选择合适的压铸铝材料,按照设计需求进行采购。
同时准备相应的模具和工艺设备。
2.模具制备:根据散热器的设计要求,制作相应的压铸模具。
模具制备完成后进行检查和调试,确保其正常可用。
3.材料熔化:将压铸铝材料加入铝熔炉中进行熔化,并根据需要添加合适的合金元素,以提升散热器的性能。
4.压铸过程:将熔化的铝液注入模具中,利用高压使其充分填充整个模具腔体,并形成预定的散热器形状。
5.除渣处理:待铝液冷却固化后,对散热器进行除渣处理,以去除表面的气孔和杂质,提高表面质量和散热性能。
6.表面处理:根据设计要求,对散热器进行表面处理,如喷涂、阳极氧化等,提升产品的外观和耐腐蚀性。
7.检验和测试:对加工完成的散热器进行检验和测试,确保其符合设计要求和性能指标。
三、施工注意事项1.模具设计:模具的合理设计对于散热器的质量和生产效率至关重要,要确保模具结构合理、软硬件配置适当以及模具寿命长。
2.材料选择:根据散热器的具体需求,选择合适的压铸铝材料和合金元素,以确保散热器具备良好的热导性和机械性能。
3.压铸工艺控制:在压铸过程中,需要控制好铝液的注入速度、温度和压力等参数,以保证散热器的成型质量。
4.除渣处理:除渣处理是确保散热器表面质量的关键步骤,需要选择适当的除渣方法和设备,严格按照工艺规范进行操作。
5.表面处理:表面处理工艺对于散热器的外观和耐腐蚀性能起着重要作用,要选择适当的处理方法,并注意控制处理时间和温度。
6.检验和测试:对散热器的检验和测试要严格按照相关标准进行,确保散热器满足设计要求和性能指标。
四、施工成本与效益压铸铝散热器的施工成本主要包括原材料采购、模具制备、设备投资和人工费用等方面。
压铸模具设计实例(散热器模具设计到试模整个流程分析)
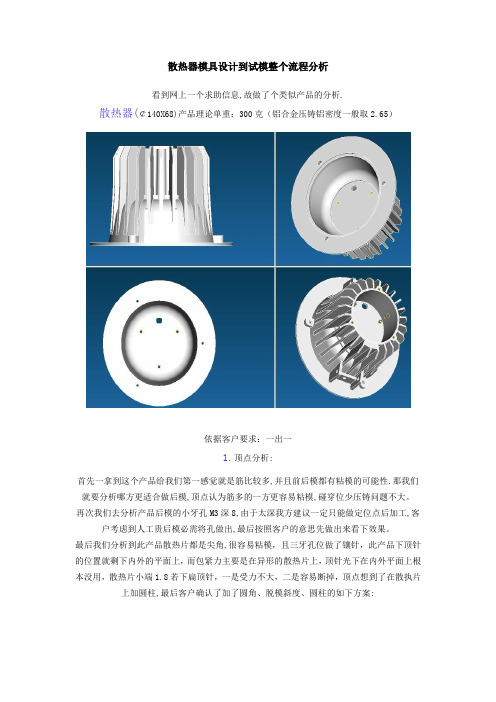
散热器模具设计到试模整个流程分析看到网上一个求助信息,故做了个类似产品的分析.散热器(¢140X68)产品理论单重:300克(铝合金压铸铝密度一般取2.65)依据客户要求:一出一1.顶点分析:首先一拿到这个产品给我们第一感觉就是筋比较多,并且前后模都有粘模的可能性.那我们就要分析哪方更适合做后模,顶点认为筋多的一方更容易粘模,碰穿位少压铸问题不大。
再次我们去分析产品后模的小牙孔M3深8,由于太深我方建议一定只能做定位点后加工,客户考虑到人工贵后模必需将孔做出,最后按照客户的意思先做出来看下效果。
最后我们分析到此产品散热片都是尖角,很容易粘模,且三牙孔位做了镶针,此产品下顶针的位置就剩下内外的平面上,而包紧力主要是在异形的散热片上,顶针光下在内外平面上根本没用,散热片小端1.8若下扁顶针,一是受力不大,二是容易断掉,顶点想到了在散执片上加圆柱,最后客户确认了加了圆角、脱模斜度、圆柱的如下方案:2.简易模具排位:分析些产品一出一,重量为300克,带流道渣包大概为600克左右.通过计算得出冲头应为¢50.我方建议模芯用上五H13电渣,普架为订普通模架.依据客户提供的成本控制得到如下简易排位:简易排位过程中,我们当然必需考虑模具的几处另类地方:首先分析此产品的形状,流道应放在前模,若如普通一样放在后模,则需反冲压力损失过大,前模则是顺冲低压快速填充产品.再次分析此模具的镶针及镶件,前模中间圆和三镶针太近,只能选择镶三镶针,后模中间圆和五镶针也是很近,但两者又必需都镶才好加工及粘模后好处理.那我们又不能按常理出牌了,顶点思维是将镶针镶通,镶件不镶通做反台阶,保证了整个模具的强度.3.客户确认简易排位及订料顶点与客户达成模具结构及尺寸的大体共识,马上要求客户订模芯及模架材料.在订料的过程中顶点有比较充足的时候设计出整套模具.4.模具设计的3D分模顶点依据排位,快速的将模具三维分出.达到如下图片效果:5.客户确认模具部件细节顶点考虑到每个企业,模具个别部件做法可能会有所差异,固需客户快速商看细节位置.6.顶点出详细的模具部件图顶点采用了最实用的标图方法,让一个生手看到图纸后都一目了然.绘出详细的组装图及散件图,一般还包括线割图和车床数.如下图所示:顶点会针求客户意愿,用客户的图框,还是用顶点自身的图框,顶点专门针对模具设计自创了非常实用的图框.7.整套模具的加工很明显只要稍微懂些加工的就知道,依据模具设计的2D及3D图,加工已经一目了然了.前模芯:电脑锣后线割配合镶针就好. 后模芯:车镶件后配到模芯,多个铜公打火花.结论就是此产品的型腔尺寸主要靠火花和电脑锣来保证.模芯和铜公做好后一定要测量重要尺寸.8.第一次试模情况顶点看过第一次试模后发现问题如下:未压的很满,后模镶针包紧力大.如顶点早期分析,后模五镶针太小太深,稍微加压就会难顶出。
压铸模具结构设计

压铸模具结构设计
1.铸件的形状和尺寸:根据铸件的形状和尺寸确定模具的结构,包括模具的上下模座、模具腔和底座等。
2.注塑系统设计:注塑系统是指将熔融金属注入模具腔中的系统。
注塑系统设计包括溢流口、进流口和排气口等。
3.冷却系统设计:冷却系统是指为了将熔融金属冷却成固态铸件而设计的系统。
冷却系统设计需要考虑冷却水的进出口位置和冷却通道的布置等。
4.驱动系统设计:驱动系统是指用于打开和关闭模具的系统。
驱动系统设计需要考虑模具的开合速度和力度等。
5.寿命和维护性设计:模具在使用过程中需要经受高温和高压力等作用,容易磨损和疲劳。
寿命和维护性设计需要考虑材料的选择和表面处理等。
6.系统集成设计:压铸模具结构设计需要和其他相关系统进行集成,包括压铸机械、控制系统和自动化系统等。
除了以上几个方面,压铸模具结构设计还需要考虑产品的特殊要求,如产品壁厚、孔洞和表面质量等。
在压铸模具结构设计的过程中,需要进行一系列的分析和计算,如强度分析、流动模拟和热处理分析等。
同时,还需要考虑生产工艺和经济效益等因素。
总之,压铸模具结构设计是一个综合性的工程问题,需要考虑多方面的因素,以满足产品的要求和工艺的需要。
压铸模设计 (有设计图纸)

压铸模设计(有设计图纸)有全套图纸摘要随着与国际接轨的脚步不断加快,市场竞争的日益加剧,人们已经越来越认识到产品质量、成本和新产品的开发能力的重要性。
而模具制造是整个链条中最基础的要素之一,模具制造技术现已成为衡量一个国家制造业水平高低的重要标志,并在很大程度上决定企业的生存空间。
虽然中国模具工业在过去十多年中取得了令人瞩目的发展,但许多方面与工业发达国家相比仍有较大的差距。
例如,CAD/CAE/CAM技术的普及率不高;许多先进的模具技术应用不够广泛等等,致使相当一部分大型、精密、复杂和长寿命模具依赖进口。
本说明书结合电梯踏板的模具设计系统地阐述了压铸与模锻技术的基本原理,分析了压铸与模锻工艺主要参数的确定方法,论述了压铸模与锻模主要零部件设计方法,并介绍了模具的加工制造及维修保养。
关键词:压铸模具加工制造维修保养有全套图纸有全套图纸ABSTRACTWith the nation of footstep join to the worldcontinuously ,market competition is turning worse ,people is already known the important of quality ,cost ,and the ability of develop new product . but the manufacturing to the molding is one of the most basal factors in the whole chain ,the molding tool manufacturing technique hasbecome to measure the important marking of a national manufacturing industry level now ,and decide the existence space of the business enterprise to a large extent .Although in the passed ten years of development ,the Chinese molding tool industry gain the harvest ,but compare to developed country westill have something to study .for example ,the universality rate of the technical of CAD/CAE/CAM is not high ;many of molding tool technique is not applied enough etc, caucus to import a larger number the complications and the longevity life molding tool .This manual systematically combined the molding tool to die-casting with the mold technical basic principle by introduce the design of the elevator pedal, analyze the method to make certain to the main parameter of die-casting and the mold craft, introduce the method to process and maintain .Keyword: Die-casting mould process maintain有全套图纸有全套图纸目录1 压铸工艺概论 (1)1.1 压铸生产过程和特点 (1)1.1.1 压铸生产过程 (1)1.1.2压铸特点 (1)1.2 压铸合金的基本要求和种类 (2)1.2.1对压铸合金的基本要求 (2)1.2.2压铸合金的种类 (2)1.3 压铸件的结构工艺性 (4)1.3.1壁厚 (4)1.3.2 铸孔 (4)1.3.3 铸造圆角和脱模斜有全套图纸有全套图纸度 (4)1.3.4 螺纹、齿轮和槽隙 (5)1.3.5 图案、文字和标志 (6)1.3.6 镶嵌件 (6)1.4 压铸主要工艺参数的选择与调整 (7)1.4.1压力 (7)1.4.2速度 (9)1.4.3温度 (10)1.4.4时间 (12)1.4.5涂料…………………………………………………………………12 2 压铸机…………………………………………………………………………142.1 压铸机的种类和工作原理 (14)2.1.1压铸机的型号和种类 (14)2.1.2压铸机结构形式和压铸过程 (13)2.1.3压铸机的主要技术参数 (18)3 踏板的压铸模具设计 (20)有全套图纸有全套图纸3.1压铸机的选用 (20)3.1.1锁模力计算 (20)3.1.2压室容量 (22)模距3.1.3 开离 (23)3.1.4 装模尺寸 (23)3.2浇铸系统和溢流、排气系统的设计 (23)3.2.1 内浇口的设计 (24)3.2.2 直浇道的设计 (26)3.2.3 横浇道的设计 (27)3.2.4溢流槽和排气槽的设计 (28)3.2.5动、定模导柱和导套的设计…………………………………………293.2.6模板的设计 (30)3.2.7 抽芯结构的设计 (34)3.2.8 推出机构的设计 (35)3.2.9模具厚度与动模座板行程的核算 (37)4 压铸模的技术要求及选材……………………………………………………有全套图纸有全套图纸 394.l 压铸模总装的技术要求 (39)4.1.1 压铸模装配图上需注明的技术要求 (39)4.1.2压铸模外形和安装部位的技术要求 (40)4.1.3 总体装配精度的技术要求 (41)4.2 结构零件的公差与配合 (41)4.2.1结构零件轴与孔朗配合和精度 (41)4.2.2 滑动零件的配合 (41)4.3 零件的表面粗糙度 (42)4.4 压铸模零件的材料选择及热处理要求 (43)4.4.1 压铸模所处的工作状况及对模具的影响 (43)4.4.2 影响压铸模寿命的因素及提高模具寿命的措施 (44)4.4.3 压铸模材料的选择和热处理……………………………………46 模具的加工制造及维修保养 (47)5.1 金属模具的加工制造……………………………………………………475.1.1 金属模县毛坯的获取方法 (47)5.1.2模样及铸有全套图纸有全套图纸型 (47)5.1.3 金属模具的机械加工 (50)5.2模具的快速制造 (60)5.2.1 快速成形技术的原理、主要方法及特点 (60)5.2.2 模具毛坯的快速制造方法 (62)5.3 铸造模具的维护保养 (64)5.3.1铸模的预防性维护保养 (64)5.3.2铸模的修复性维护 (65)5.3.3工装模具的清洗技术 (68)参考文献 (71)1 压铸工艺概论压力铸造是将熔融合金在高压、高速条件下充型,并在高压下冷却凝成形的精密铸造方法,简称比铸。
散热器挤压模设计
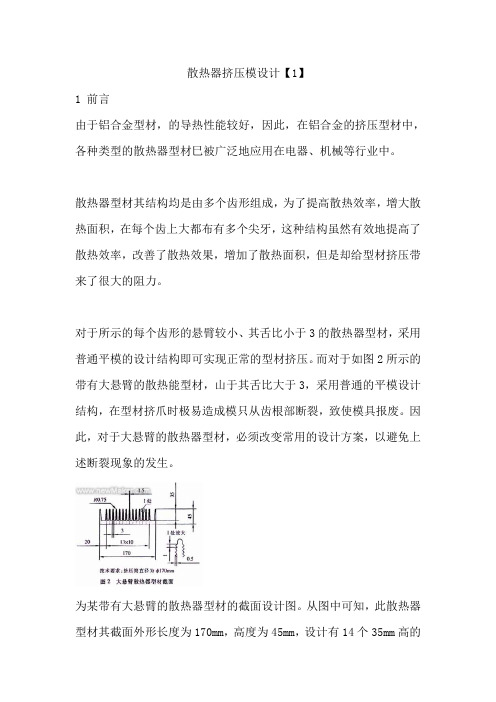
散热器挤压模设计【1】1 前言由于铝合金型材,的导热性能较好,因此,在铝合金的挤压型材中,各种类型的散热器型材巳被广泛地应用在电器、机械等行业中。
散热器型材其结构均是由多个齿形组成,为了提高散热效率,增大散热面积,在每个齿上大都布有多个尖牙,这种结构虽然有效地提高了散热效率,改善了散热效果,增加了散热面积,但是却给型材挤压带来了很大的阻力。
对于所示的每个齿形的悬臂较小、其舌比小于3的散热器型材,采用普通平模的设计结构即可实现正常的型材挤压。
而对于如图2所示的带有大悬臂的散热能型材,山于其舌比大于3,采用普通的平模设计结构,在型材挤爪时极易造成模只从齿根部断裂,致使模具报废。
因此,对于大悬臂的散热器型材,必须改变常用的设计方案,以避免上述断裂现象的发生。
为某带有大悬臂的散热器型材的截面设计图。
从图中可知,此散热器型材其截面外形长度为170mm,高度为45mm,设计有14个35mm高的齿形,两齿间距为1Omm,,在每个齿形的两侧布有0.5mm高,1mm间距的尖牙。
从其标注的尺寸上可计算出此散热器型材悬臂处舌比为:(45-10)/(10-3):4.69>3,在各齿间存在着危险断面。
特别是该截面的底部壁厚较厚(达1Omm),而齿部最薄处的壁厚仅有1.5mm,截面壁厚相差悬殊,更增大了危险断面的断裂系数。
另外,从图中的技术要求巾得知,挤压此型材的挤压筒内径仅为∮170mm,而此型材截面的外接圆直径却达∮175.8mm,大于挤压筒内径尺寸,要实现此型材的正常挤压难度极大。
3 模具设计3.1 结构分析这种大悬臂的散热器型材模具,如果选用普通平模的设计结构,由于其底部壁厚与齿部壁厚相差悬殊,而齿部又布有多个尖牙,使齿部的挤压阻力极大,致使危险断面的断裂系数增大,使模具的挤压寿命极大地降低。
为了使模具在挤压时模孔各部的流速均匀,挤压平稳,在设计其模具结构时,打破了实心型材大都采用平模形式的常规设计理念,将此型材模具设引成带有流口、分流桥的分流模的形式,与常规分流模不同的是:在此分流模的上模分流桥上,没有决定型材内孔尺寸的型芯部分,因此,称之为假分流模,如图3所示。
一种散热器的压铸模具[实用新型专利]
![一种散热器的压铸模具[实用新型专利]](https://img.taocdn.com/s3/m/17a762355022aaea988f0f05.png)
专利名称:一种散热器的压铸模具专利类型:实用新型专利
发明人:翁江辉
申请号:CN201420444970.6申请日:20140808
公开号:CN204018688U
公开日:
20141217
专利内容由知识产权出版社提供
摘要:本实用新型公开了一种散热器的压铸模具,包括上模框、上模芯、下模框和下模芯,其特征在于,所述上模芯、下模芯分别与对应的上模框、下模框相连,所述上模框与下模框相连,上下模芯形成散热器壳体的压铸型腔,所述上模框设有与压铸型腔相连通的分流锥,所述上模芯设有加热装置,所述下模框设有与下模芯相连的油压缸和与压铸型腔相连通的废渣槽,所述下模芯与下模框之间设有一段空隙,下模芯的上部设有与散热片相适配的压铸深槽。
本实用新型通过上模框、上模芯、下模框和下模芯及其连接结构的结合创新,提供一种结构简单,加工方便,成本低,局部温差小,铸件质量好和能够顺利脱模的散热器压铸模具。
申请人:宁波图冠精密模具有限公司
地址:315806 浙江省宁波市北仑大矸福托路26号
国籍:CN
代理机构:杭州杭诚专利事务所有限公司
代理人:尉伟敏
更多信息请下载全文后查看。
薄齿形散热片浇铸模设计方案

最厚的
部位 尽量用一个冒口同时补缩几个热
节;③在满足补缩作用的前提下,冒口
()
()
应尽可能设在加工面上,
以减少清整冒
口根部的工作量和降低能源消耗;
④冒
图
——活块结合面上开槽
()
排气系统图
——镶块与型腔的结合面上开槽
——排气缝
注:图 和图 中深色面为排气槽
口不应设在铸件受力大的部位,
处,
以便于安放浇冒口,使气体容易从型腔中排出。
不影响铸件的使用和外观。
浇注系统的设计
( )浇口杯。如图
内浇道设置应便于清理、打磨和去除浇注系统,
综上所述,该浇铸模的内浇道应该开在型腔的
所示,中型铸件的金属型浇
铸模都需要设计浇口杯,为了节省制型材料,可采用
个直角处。
( )温控系统的设计。如图 所示。由于合金熔
同时铸件厚实部分应置在浇注位置上方,以利于设置
冒口进行补缩。而该铸件为散热片,其工作面为薄齿
部分,
故铸件在型腔中的位置应该是齿形朝下。
性、操作方便。下面从不同角度,说明金属熔液引入
位置的选择原则。
对于结构复杂的铸件,应采用定向凝固与同时
凝固相结合的“较弱定向凝固”原则。即对每一个补
缩区按定向凝固的要求设置内浇道,对整个铸件则按
量化处理方法,最终得到图象的加工轮廓,利用
线切割软件对复杂图象进行矢
线切割软件对图象矢量化处理后生
成程序代码,然后通过线切割机床完成矢量图的加工,从而提高零件设计和加工效率。
关键词:矢量图;线切割;零件加工
中图分类号:
文献标识码:
Study Machining of Vector Graphics of the
电脑散热元件压铸成型工艺与模具设计
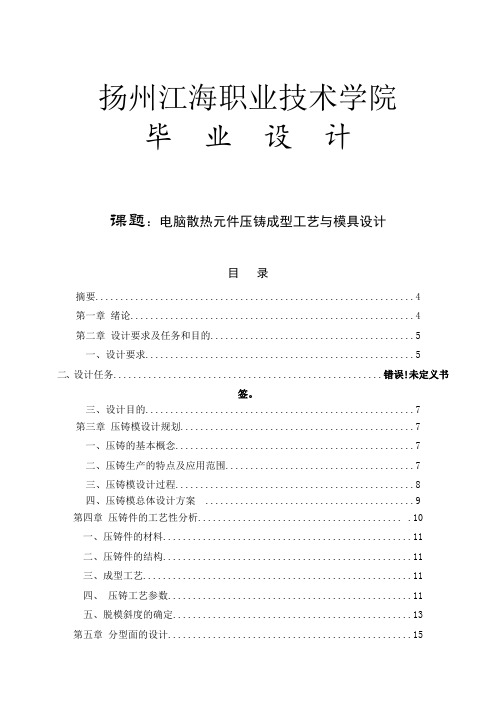
扬州江海职业技术学院毕业设计课题:电脑散热元件压铸成型工艺与模具设计目录摘要 (4)第一章绪论 (4)第二章设计要求及任务和目的 (5)一、设计要求 (5)二、设计任务......................................................错误!未定义书签。
三、设计目的 (7)第三章压铸模设计规划 (7)一、压铸的基本概念 (7)二、压铸生产的特点及应用范围 (7)三、压铸模设计过程 (8)四、压铸模总体设计方案 (9)第四章压铸件的工艺性分析......................................... .10一、压铸件的材料 (11)二、压铸件的结构 (11)三、成型工艺 (11)四、压铸工艺参数 (11)五、脱模斜度的确定 (13)第五章分型面的设计 (15)一、分型面的类型 (15)二、分型面的选择原则 (16)三、选择分型面 (16)第六章浇注系统及排溢系统的设计 (17)一、浇注系统设计 (17)二、溢流排溢系统的设计 (19)第七章压铸件成型零件设计 (21)一、成型零件结构形式分类 (22)二、镶块固定形式及适用范围 (22)三、型芯的固定形式 (22)四、成型零件尺寸的成型尺寸计算 (23)第八章推出机构的设计 (26)一、分类 (26)二、推出距离的计算 (26)三、推出部位的选择 (26)四、推出力的计算 (27)五、推杆的设计 (27)六、推出机构的复位和导向 (27)第九章模架的设计 (29)一、设计要求 (29)二、导向、支承与固定零件的设计 (29)第十章模具的装配 (31)第十一章压铸机的初选与校核 (34)一、压铸机的初选 (34)二、压铸机成型过程 (34)三、压铸机选择方法 (35)四、压铸机锁模力的计算 (35)五、压室容量及开模距离的校核 (36)第十二章模具的安装及调试 (37)一、模具安装在压铸机上要注意以下几方面: (37)二、试模与调模 (38)三、修模与检验 .. (38)第十三章全面审核投产制造 (41)一、模具的安装原则 (41)二、试模与模具合格的条件 (41)主要参考文献 (43)设计小结 (44)摘要压力铸造是目前成型有色金属铸件的重要成型工艺方法。
压铸模结构设计溢流与排气及加热冷却系统设计
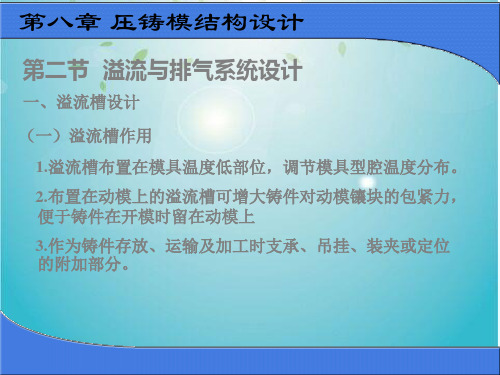
第八章 压铸模结构设计
第六节 加热与冷却系统设计
模具温度是影响铸件质量一个重要因素。如果在单位时间内 模具吸收的热量和散发的热量相等而达到一个平衡状态, 则称为模具的热平衡。
模具的温度控制是通过模具的加热和冷却系统来达到的。
加热冷却系统的主要作用:提高压铸件内部质量和表面质 量;稳定压铸件的尺寸精度;提高压铸机生产效率;降低
第六一节 加、热与溢冷却流系统槽设计设计
(6)需控制局部金属液流动状态以消除疵病的部位。
第六(节 加二热与)冷却溢系统流设计槽的设计要点
(三)溢流槽的容积和体积
第第八二章 节1压溢.铸流正模与结排确构气设系布计统设置计溢流槽在模具中的位置
加热模具的热源有煤气、喷灯、柴油喷枪、电阻加热器、电感应加热器和红外线加热器等。 第八章 压铸模结构设计 第六节 加热与冷却系统设计 模具的温度控制是通过模具的加热和冷却系统来达到的。 正确布置溢流槽在模具中的位置 第六节 加热与冷却系统设计 模具温度是影响铸件质量一个重要因素。 管状电热元件一般布置在动、定模套板、支撑板和座板上。 (5)内浇口两侧或金属液不能直接充填的部位。 溢流槽的溢流口总截面积应小于内浇口的总截面积。 第八章 压铸模结构设计 (3)是金属液最后充填的部位。 第八章 压铸模结构设计 (二)溢流槽的设计要点 第八章 压铸模结构设计 管状电热元件一般布置在动、定模套板、支撑板和座板上。 热管冷却法 热管的外壳为一密封管子,内壁衬以由吸水材料组成的虹吸管,在此虹吸管中可产生毛细管作用,内装低温时能气化的液 体。 一、模具加热方法
第八章 压铸模结构设计
第二节 溢流与排气系统设计
一、溢流槽设计 (二)溢流槽的设计要点
2.溢流槽的溢流口总截面积应小于内浇口的总截面积。 3.采用多个独立溢流槽比一个同等容积溢流槽,更易控制金 属液流动状态。 4.根据溢流槽的作用确定其容积。
- 1、下载文档前请自行甄别文档内容的完整性,平台不提供额外的编辑、内容补充、找答案等附加服务。
- 2、"仅部分预览"的文档,不可在线预览部分如存在完整性等问题,可反馈申请退款(可完整预览的文档不适用该条件!)。
- 3、如文档侵犯您的权益,请联系客服反馈,我们会尽快为您处理(人工客服工作时间:9:00-18:30)。
图3 铸件所选择 的正确 的料 流方 向 1.铸 口 2.横浇道
2 浇注 系统的设计
根据压铸模浇注系统 的设计原则 ,金属料流应顺 3 模具结构与总装设计
着散热片的方 向充填 ,以避免产生流痕 、冷 隔和散热
图4为模具 的总装结构示意图。模具 主要成型部
片部分形状充填不完整 。最终所选择 的浇注系统设 分 的工作零件采用镶件分别镶人动 、定模 内(定模镶
锻造效 率 。
5 参考文献
预锻和终锻模膛设计相辅相成 ,具有顺序成形模 …1 李 志广 .实现 锻件经济性 的七项原 则[J].锻压机械 ,2000,
锻 法的特点 :预锻成形具 有承前启后 的作 用 ,终 锻模
(4):28 30.
膛则 具有校正 与终 锻的作用 ,锻件 的氧化 皮小 、错 移 【2】 李 志广 ,郭建平 ,王刚.新 产 品锻件 开发 的优 化方案[J】.现
1 铸件 的成 型工艺性分析
统设计 时应充 分注意到金属 流体 在模具 内的流动 阻
该铸 件如图 1所示 ,是一结构组件 中的散热元件 力 ,尤其是铸件上部 l7片的片状结构处 的成型。压铸
单元 ,材料为 ADC12,铸件为椭 圆形 中空结构件 ,该铸 时 ,金属料流方 向如选 择不 当易造成冷 隔 、熔接强度
陷。结合企业生产实 际需求 、铸件的结构特点及模具 成型零件 的加 工精度 条件等 ,本压铸模采用 了 1模 1 腔的结构形式 。
椭圆形状中空结构件 的外缘为其最大轮廓 。故其 动 、定模间的水平分型面较易选择 ,即以铸件下端部的 大平面为模具的动 、定模间的分型面 ,如图2所示。
+
图 2 以 铸 件 大底 面 为 动 、定 模 I目的分 型 面
cmmctcom散热器盖压铸模设计姜伯军常州明顺电器有限公司江苏常州213015摘要介绍了散热器盖铸件的成型工艺分型面的选择浇注系统设计脱模方式设计对铸件质量的影响分析以及模具的总装结构设计
CMMC
曩
全球机床4S总部基地 网 址 :www cm m ct.com 。
心
散 热 器 盖 压 铸 模 设 计
件 的壁厚 较均匀 (壁厚 约为 2.5mm左右 )。在 浇注系 差 、铸件 内有气 包 、片 状处 不能 完 全成 型 等质 量 缺
寸与质量一致性好 ,相应 地改善 了锻造工 艺性 ,提高 格品率达 99% ,提高终锻模使用寿命 至少两倍 。
了锻件质量 ,提高 了终 锻锻模膛 的使用 寿命 ,提高 了
与质量 ,1998,(2):15 16.
①
性 。模锻 1火 次成形 ,打击次数少 ,操作 简单 ,锻件合
《模具制造)2Ol1年第 8期
·51·
S T L
淮 安仕 泰 隆 国 际工业 博 览城
全球 招 商热线 :051 7-86299999 I ̄ :www.stlep.com
图 1 散热器盖
量小 、残余 飞边毛刺小 、形状 、尺寸与质量一 致性好 ,
代模 具 ,2009,(3):45 8.
尺寸精度高 、锻造效率高和终锻模膛 的使用寿命高。 [3】 姚 泽坤.锻造 工艺学 与模具设 计【M].西安 :西北 工业大学
出版社 ,2005.
4 结束语
[4] 张 志文 .锻造工艺学【M】.北京 :机械工业出版社 ,1984. [5】 中国机械工程学 会锻压学会 .锻压 手册 ·锻造 (第 2版 )[M].
(1)改进模锻工艺和优化段模设计尤其是预锻模
北京:机械工业 出版社,2004.
设 计是有效改善锻造 工艺性 、确保开 闩板成 形 、提高 【6] 李 志广.锤锻模 平面锁扣 的结构设 计及其应 用『J].锻压技
锻件质量 、提 高锻件合格品率 、提高锻造效率 、提高锻
术 ,1996,(2):51~54.
Design of Die-Casting Die for the Radiator Cover
【Abstract]The radiator eover die—casting die process,the selection of the paaing line,design of
gating system,die design influence on the casting quality,as well as the die assembly structure design were introduced. Key words:the radiator cover;die-casting die design;structure analysis;gating system.
相一致 的导料结构方式设计 。在铸件成 型型腔 的三
成 型西6.5ram圆孔及 12mm台阶孔 的动模 型芯
面设置 了7个溢料气包。
(件 8、件 29)分别 以插人气动推管
《模具 制造 )2011年 第 8期
A —A
CMMC
量
全球机床 s总部基地 网 址 :WWW cm mct.com .
姜伯 军 常州明顺 电器有限公 司(江苏常 州 213015)
【摘要 】介绍 了散热器盖铸件 的成型工 艺,分型面的选择 ,浇注 系统设计 ,脱模 方式设计对 铸件质 量的影响分析 ,以及模具的总装结构设计。 关键词 :散热器盖;压铸模设计 ;结构分析 ;浇注系统 中图分类号 :TG244 文献标 识码 :B 文章编号 :201 1—06—19—248
模使用寿命和降低锻件成本 的有效方法 。
【7] 李志广.论热锻件图尺寸标注的合理原则fJ1.机械工业标
(2)开闩板成形 的锻造工艺 和锻模设计明显具有
准化 与质 量 ,1997,(6):25 26.
技术 上 的可行 性 、质 量上 的可靠性 和经 济上 的合理 【8] 李 志广.预锻热锻 件 图的设计 与绘制 [J].机械 工业标准化
计 如图3所示 。图 3所示主视图中浇 口套 内铸 口的分 件 7;动模镶件 32)的结构形式 ,以利 于模具工作及成
流锥 以圆弧导料 的结构形式设计 ,以使压铸 时加快料 型部位尺寸 的调整 ,也有利于易损部分零件 的修理 、
流的充盈速度 。图3所示俯视图中横浇道 以铸件圆弧 更换 、调 整 。