铅焊料片式元件焊点的剪切试验方法
表面贴装焊点剪切力无合格判定标准的解析

表面贴装焊点剪切力无合格判定标准的解析发布时间:2022-08-29T01:30:36.513Z 来源:《科技新时代》2022年2期1月作者:杨绪瑶[导读] 在电子产品竞争日趋激烈的今天杨绪瑶连云港杰瑞电子有限公司江苏连云港222006摘要:在电子产品竞争日趋激烈的今天,产品质量水平不仅是企业技术和管理水平的标准,更与企业的生存和发展息息相关。
而随着元器件和PCB板的发展,SMT已成为电子组装的主流,提高产品质量已成为SMT生产中的最关键因素之一。
如何判断SMT器件焊点的可靠性,SMT工厂常常想用剪切力大小来评估。
但在整个电子制造行业中,包括国际电子工业联合会(IPC)在内的各个标准制定组织,并没有制定SMT焊接后器件的行业剪切力合格判断标准。
本文将从几个方面分析为什么行业中没有统一的器件剪切力合格判定标准,以及如何来判断SMT焊点质量是否合格。
关键词:表面贴装工艺、焊点、可靠性、标准、剪切力、合金层1、引言表面贴装工艺,又称表面贴装技术(SMT,Surface Mounted Technology的缩写),是一种无需在印制板上钻插装孔,而直接将表面组装元器件贴焊到印制线路板或其他基板表面的规定位置,用焊料使元器件与印制线路板之间构成机械和电气连接的电子组装技术。
表面贴装的最终目标是获得完美的焊点,即实现元器件与电路板之间机械和电气的完美连接。
焊点的可靠性就成为焦点关注的问题。
如何来判断焊点的可靠性是每位SMT从业人员所必须掌握的技能。
判断焊点的可靠性就需要参考相应的标准。
行业内通常想通过测试器件焊接后的剪切力值来判断焊点的可靠行。
然而,在整个电子组装行业中,有关于剪切力测试方法的标准,却没有判断剪切力值是否合格的标准。
国际电子工业联合会(IPC)作为著名的全球电子行业协会,其制定了涉及电子行业的涉及、制造和测试各个领域的标准,但依然没有焊点剪切力测试是否合格的标准。
本文就从几个专业技术角度来分析为什么整个电子组装行业没有统一的判断焊点剪切力是否合格的标准。
片式元件焊点剪切力比较实验研究

D c me t o e A A tceI : 0 13 7 2 1 0 .2 .4 o u n d : ril 10 .4 4l 00) 40 1 0 C D 5
1无铅化 带来 的转 变
伴随着无铅进程 的不 断深 入 ,与其相关 的诸多行 业都悄然发生着 变化 。几乎所有 的印制 电路板生产 厂 家都 为客户提供 了更多 的选 择, 印制电路板基 材 ( 普
Co a a i e S u y o e rS r n t fSM D mp r tv t d n Sh a t e g h o
S o -o g MAO S uqn UN Sh uh n . h -i
Ih n c u si t f pi , ieMeh nc n h sc, hn s cd m C a gh nI tueo t s F c a i a d y i C i e a e yo n t O c n s P s e A f S in e . h n c u 0 3 . h n l ce c s C a g h n 1 0 C ia 3 1
A s r c : h h n e f h d sr saei rd c ds c a ・ e n f cu eh sb e pe d T eman b ta t T ec a g so ei u t e r n o u e i el df ema u a t r a e ns r a . h i t n i t n e r po l s gla - e od r a ee b rt d i l i l bly po l , ei i y e p r n a i rbe r b msi u i df es l s r l o ae , n u n r i i r b ms rl bl x ei tt n po l e n n e r e a c d g ea i t e a i t me o ms
焊点质量检测方法

焊点质量检测方法1.1 目视检测目视检测时最常用的一种非破坏性检测方法,可用万能投影仪或10倍放大镜进行检测。
检测速度和精度与检测人员能力有关,评价可按照以下基准进行:(1)湿润状态钎料完全覆盖焊盘及引线的钎焊部位,接触角最好小于20°,通常以小于30°为标准,最大不超过60°。
(2)焊点外观钎料流动性好,表面完整且平滑光亮,无针孔、砂粒、裂纹、桥连和拉尖等微小缺陷。
(3)钎料量钎焊引线时,钎料轮廓薄且引线轮廓明显可见。
1.2 电气检测电气检测是产品在加载条件下通电,以检测是否满足所要求的规范。
它能有效地查出目视检测所不能发现的微小裂纹和桥连等。
检测时可使用各种电气测量仪,检测导通不良及在钎焊过程中引起的元器件热损坏。
前者是由微小裂纹、极细丝的锡蚀和松香粘附等引起,后者是由于过热使元器件失效或助焊剂分解气体引起元器件的腐蚀和变质等。
1.3 X-ray检测X-ray检测是利用X射线可穿透物质并在物质中有衰减的特性来发现缺陷,主要检测焊点内部缺陷,如BGA、CSP和FC焊点等。
目前X射线设备的X光束斑一般在1-5μm范围内,不能用来检测亚微米范围内的焊点微小开裂。
1.4 超声波检测超声波检测利用超声波束能透入金属材料的深处,由一截面进入另一截面时,在界面边缘发生反射的特点来检测焊点的缺陷。
来自焊点表面的超声波进入金属内部,遇到缺陷及焊点底部时就会发生反射现象,将反射波束收集到荧光屏上形成脉冲波形,根据波形的特点来判断缺陷的位置、大小和性质。
超声波检验具有灵敏度高、操作方便、检验速度快、成本低、对人体无害等优点,但是对缺陷进行定性和定量判定尚存在困难。
扫描超声波显微镜(C-SAM)主要利用高频超声(一般为100 MHz以上)在材料不连续的地方界面上反射产生的位相及振幅变化来成像,是用来检测元器件内部的分层、空洞和裂纹等一种有效方法。
采用微声像技术,通过超声换能器把超声脉冲发射到元件封装中,在表面和底板这一深度范围内,超声反馈回波信号以稍微不同的时间间隔到达转化器,经过处理就得到可视的内部图像,再通过选通回波信号,将成像限制在检测区域,得到缺陷图。
焊点检查方法

焊点检查方法1. 目测检查:对焊点进行目测检查,查看焊缝的形状,焊道的宽度和深度,焊缝表面是否平整,是否有气孔、裂纹和其他缺陷。
2. 触摸检查:用手指轻轻触摸焊点,感受其表面的凹凸不平,硬度和坚固程度,以此来初步判断焊接质量。
3. 声音检查:利用敲击焊点的方式,倾听焊点发出的声音,判断焊点的致密度和质量。
4. 温度检查:使用温度计对焊点进行温度检测,以确保焊接工艺是否符合标准要求,是否达到了正确的焊接温度。
5. 金相显微镜检查:采用金相显微镜对焊点进行放大观察,检查其金属组织、晶界和夹杂物等微观结构,以评估焊接质量。
6. X射线检查:利用X射线仪器对焊点进行检测,检查焊缝部位的结晶度、缺陷及杂质等问题。
7. 超声波检查:使用超声波探伤仪对焊点进行检测,通过声波的传播情况来评估焊接质量。
8. 磁粉探伤:对焊点表面喷洒磁粉,利用磁粉探伤设备来检测焊接部位是否存在裂纹、夹杂等缺陷。
9. 磁粉检测:在焊接区域表面喷洒磁粉,利用磁粉检测仪器观察是否有磁粉集聚,从而判断是否有裂纹或其他缺陷。
10. 高倍显微镜检查:利用高倍显微镜设备对焊点进行放大观察,检查焊接区域的细微缺陷和变形情况。
11. 发光检测:利用发光检测仪器对焊点进行检测,观察焊点会否产生辐射和发光现象,以判断焊接质量。
12. 流变学检测:通过流变学的测试方法,对焊点进行拉伸、压缩等力学性能测试,评估焊点的强度和韧性。
13. 电子探针分析:利用电子探针分析仪器,对焊点进行成分分析和元素探测,以评估焊接材料的质量和成分均匀性。
14. 硬度测试:使用硬度计对焊点进行硬度测试,评估焊接区域的硬度分布和焊接质量。
15. 电磁感应检测:利用电磁感应仪器对焊点进行检测,观察焊接区域的磁场分布情况,以判断焊点的致密性和质量。
16. 热处理检测:针对焊点进行热处理测试,检查焊接工艺是否符合热处理要求,以确保焊接质量稳定。
17. 电子束探伤:采用电子束探伤仪器,对焊接区域进行电子束探伤检测,评估焊点的结构完整性和质量。
焊接剪切试验
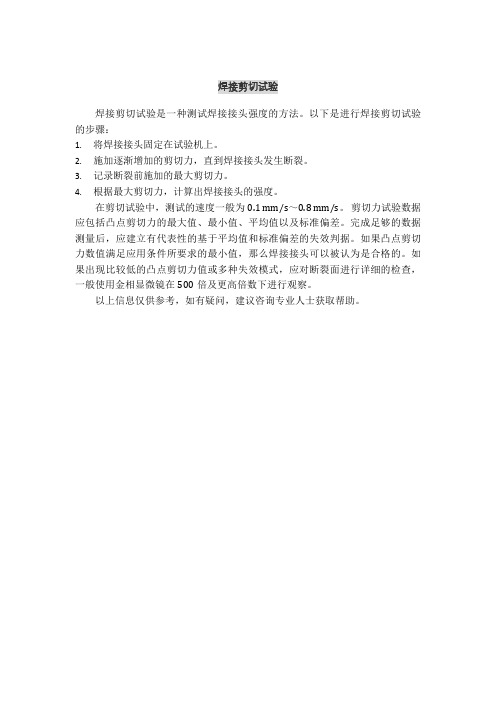
焊接剪切试验
焊接剪切试验是一种测试焊接接头强度的方法。
以下是进行焊接剪切试验的步骤:
1.将焊接接头固定在试验机上。
2.施加逐渐增加的剪切力,直到焊接接头发生断裂。
3.记录断裂前施加的最大剪切力。
4.根据最大剪切力,计算出焊接接头的强度。
在剪切试验中,测试的速度一般为0.1 mm/s~0.8 mm/s。
剪切力试验数据应包括凸点剪切力的最大值、最小值、平均值以及标准偏差。
完成足够的数据测量后,应建立有代表性的基于平均值和标准偏差的失效判据。
如果凸点剪切力数值满足应用条件所要求的最小值,那么焊接接头可以被认为是合格的。
如果出现比较低的凸点剪切力值或多种失效模式,应对断裂面进行详细的检查,一般使用金相显微镜在500倍及更高倍数下进行观察。
以上信息仅供参考,如有疑问,建议咨询专业人士获取帮助。
电子部品焊点切片实验
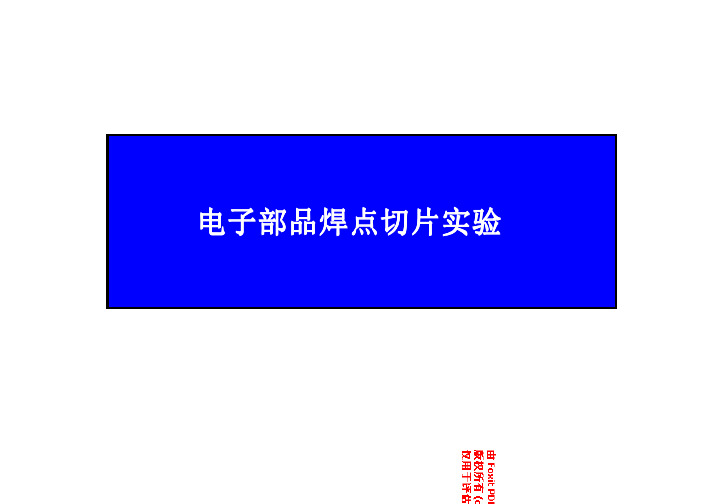
条件:
条件:
实物基板空基板
实物基板
空基板切割方向
元件电极情况完整
R13
选择需要进行测试的焊点选择需要进行测试的焊点,,通常每次切片针对一个焊点
两边焊接差异
QFP 的Lead
参考资料~焊点切片检查(断面检查)~
从基板上切割下有待分析的元件并将其周边磨平
固定元件
将硬化剂和元件一同放入在载体
中待中待55小时后固化
参考资料~焊点切片检查(断面检查)~)~切片制作切片制作
研磨
经过六次的研磨元件本体呈现透明状态
镀Pt
切片制作完成
参考资料~焊点切片检查(断面检查)~电子显微镜观察两边焊接差异QFP的Lead。
焊点破坏测量的方法

焊点破坏测量的方法焊点是连接电子设备和元器件的重要结构,其质量直接关系到设备的可靠性和稳定性。
在电子制造和维修过程中,经常需要对焊点进行质量评估和破坏测量。
下面将介绍几种常用的焊点破坏测量方法。
1. 目测观察法:这是最简单也是最常用的方法之一。
通过肉眼观察焊点的表面形态和颜色变化,可以初步判断焊点的质量。
合格的焊点通常具有光滑均匀的外观,颜色均匀且金属之间无明显缺陷。
而焊点表面不规则、颜色不均、露出明显的裂纹或孔洞等缺陷往往表示焊点质量存在问题。
2. 金相显微镜观察法:这种方法通过使用金相显微镜来观察焊点的显微形态和组织结构。
首先将焊点样本进行金相打磨和腐蚀处理,然后在金相显微镜下观察焊点的晶粒结构、夹杂物、缺陷和晶界等细节。
通过分析焊点的显微结构,可以评估焊点的可靠性和质量。
3. X射线检测法:X射线检测是一种非破坏性的测量方法,可以用于评估焊点的内部结构和缺陷情况。
在X射线机器的照射下,焊点会发生不同程度的透射和散射,通过检测X射线的衰减和散射情况,可以得出焊点的内部结构和缺陷信息。
这种方法可以检测焊点的脆性裂纹、孔洞、气泡等存在的问题。
4. 热冲击试验法:热冲击试验是一种用于模拟焊点在温度变化下的热应力情况的方法。
通过将焊点样品放置在高温和低温交替循环的环境中,观察焊点在热冲击过程中的变化。
如果焊点质量不合格,它可能会发生裂纹、开裂或脱落等现象。
这种方法可用于评估焊点在温度变化下的可靠性和耐久性。
总之,焊点破坏测量的方法多种多样,根据不同的需求和实际情况选择合适的方法进行评估和检测,可以有效提高焊接质量和设备的稳定性。
IPC-9701A 表面贴装锡焊件性能测试方法与鉴定要求
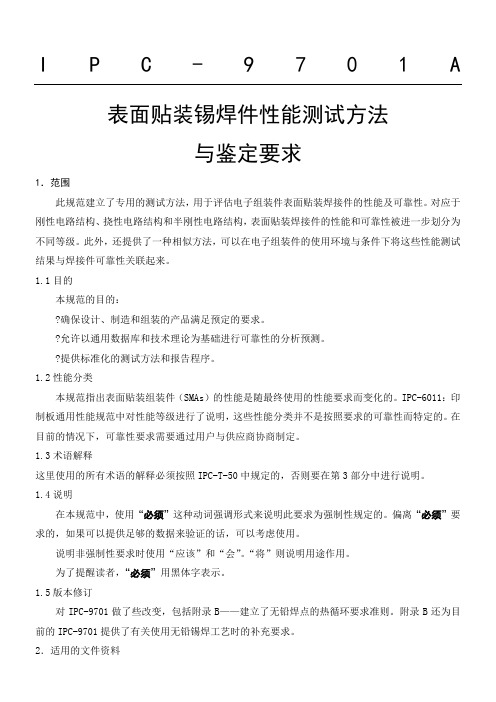
I P C-9701 A表面贴装锡焊件性能测试方法与鉴定要求1.范围此规范建立了专用的测试方法,用于评估电子组装件表面贴装焊接件的性能及可靠性。
对应于刚性电路结构、挠性电路结构和半刚性电路结构,表面贴装焊接件的性能和可靠性被进一步划分为不同等级。
此外,还提供了一种相似方法,可以在电子组装件的使用环境与条件下将这些性能测试结果与焊接件可靠性关联起来。
1.1目的本规范的目的:?确保设计、制造和组装的产品满足预定的要求。
?允许以通用数据库和技术理论为基础进行可靠性的分析预测。
?提供标准化的测试方法和报告程序。
1.2性能分类本规范指出表面贴装组装件(SMAs)的性能是随最终使用的性能要求而变化的。
IPC-6011:印制板通用性能规范中对性能等级进行了说明,这些性能分类并不是按照要求的可靠性而特定的。
在目前的情况下,可靠性要求需要通过用户与供应商协商制定。
1.3术语解释这里使用的所有术语的解释必须按照IPC-T-50中规定的,否则要在第3部分中进行说明。
1.4说明在本规范中,使用“必须”这种动词强调形式来说明此要求为强制性规定的。
偏离“必须”要求的,如果可以提供足够的数据来验证的话,可以考虑使用。
说明非强制性要求时使用“应该”和“会”。
“将”则说明用途作用。
为了提醒读者,“必须”用黑体字表示。
1.5版本修订对IPC-9701做了些改变,包括附录B——建立了无铅焊点的热循环要求准则。
附录B还为目前的IPC-9701提供了有关使用无铅锡焊工艺时的补充要求。
2.适用的文件资料下面是适用的文献标准以及这些文件的后续版本和修订部分,都属于本规范的内容。
下列文件标准分为IPC、联合工业标准、ITRI、EIA和其他。
2.1IPCIPC-T-50电子电路互连及封装的名词术语与定义IPC-D-279可靠的表面贴装技术印制板组装件的设计指南IPC-TM-650试验方法手册2.1.1手动微切片法2.4.1镀层附着力2.4.8覆金属箔板的剥离强度.1表面贴装焊接区的粘结强度(垂直拉伸方法)弯曲与扭转金属化孔的模拟返工.2热膨胀系数,应变计法2.5.7印制线路材料的介质耐电压,2.6.5多层印制线路板的物理(机械)震动试验2.6.7.2热冲击-刚性印制板2.6.8镀通孔的热应力冲击2.6.9刚性印制电路板振动试验IPC-SM-785表面贴装锡焊件加速可靠性试验指南IPC-S-816SMT工艺指南与检验单IPC-7711/21维修与返工指南IPC-9252无载印制板电气检测指南与要求IPC-9501电子元器件的PWB组装工艺模拟评估IPC-9502电子元器件的PWB组装锡焊工艺指南IPC-9504非集成电路元器件组装工艺模拟评估(预处理非集成电路元器件)2.2联合工业标准J-STD-001电气和电子组装件的焊接技术要求J-STD-002元器件引脚、端子、焊片、接线柱及导线可焊性试验J-STD-003印制板可焊性试验J-STD-020塑料集成电路表面贴装器件湿度/回流灵敏度分类2.3国际锡研究机构ITRIPub#580锡与锡合金的金相学ITRIPub#708电子元器件焊点冶金学2.4其它出版物2.4.1电子工业机构JESD22-A104-B“温度循环”(2000年7月)JESD22-B117“BGA焊球剪切”(2000年7月)2.4.2OEM工作组SJR-01第2版“焊点可靠性测试标准”(2001年2月)3.术语、定义及概念3.1概述为确保组装到电路板上的表面贴装电子元件焊点的可靠性,要求采用可靠性(DfR)设计步骤(见IP-D-279),在某些情况下通过试验验证使产品适用于特定产品类型和环境。
片式电阻电容元件焊点剪切强度试验研究
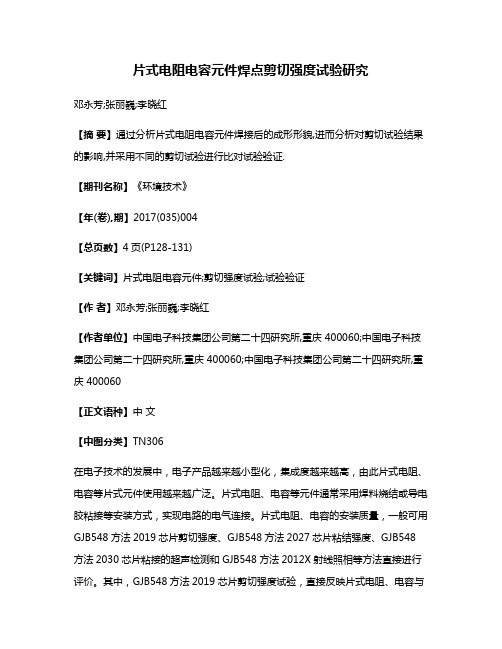
片式电阻电容元件焊点剪切强度试验研究邓永芳;张丽巍;李晓红【摘要】通过分析片式电阻电容元件焊接后的成形形貌,进而分析对剪切试验结果的影响,并采用不同的剪切试验进行比对试验验证.【期刊名称】《环境技术》【年(卷),期】2017(035)004【总页数】4页(P128-131)【关键词】片式电阻电容元件;剪切强度试验;试验验证【作者】邓永芳;张丽巍;李晓红【作者单位】中国电子科技集团公司第二十四研究所,重庆 400060;中国电子科技集团公司第二十四研究所,重庆 400060;中国电子科技集团公司第二十四研究所,重庆 400060【正文语种】中文【中图分类】TN306在电子技术的发展中,电子产品越来越小型化,集成度越来越高,由此片式电阻、电容等片式元件使用越来越广泛。
片式电阻、电容等元件通常采用焊料烧结或导电胶粘接等安装方式,实现电路的电气连接。
片式电阻、电容的安装质量,一般可用GJB548方法2019芯片剪切强度、GJB548方法2027芯片粘结强度、GJB548方法2030芯片粘接的超声检测和GJB548方法2012X射线照相等方法直接进行评价。
其中,GJB548方法2019芯片剪切强度试验,直接反映片式电阻、电容与基板间的烧接或粘接的质量,即反映电阻、电容端头金属化的质量,或者烧接或粘接工艺控制的质量,或者基板上电阻、电容安装区域金属化表面的质量。
如果烧接或粘接不良,会引起接触电阻增大,甚至开路,影响电路的参数性能。
因此,研究电阻、电容剪切强度试验方法对试验结果的影响十分重要和必要。
按GJB 548B-2005《微电子器件试验方法和程序》方法2011剪切强度试验,其工作原理如图1所示。
固定试验样品底座,接触工具把力均匀地加到电阻、电容的一条棱边(长边),使电阻、电容从基板上脱离。
记录电阻、电容从基板上脱离时所加力的大小及失效模式。
理想状态下,安装后的片式电阻、电容侧面与基板表面呈垂直状态。
实事上,受基板化自身厚度均匀性、基板金属层厚度均匀性或焊料熔化后厚度均匀性的影响,安装后的片式电阻、电容侧面不会与基板表面完全垂直,其典型形貌如图2所示。
2.焊点质量检测技术

电流较小,电极力较小
电流过大
电极力过大
因素复杂,如焊接规范 不当
电流过小
车身焊接技术培训课程
第 23 页
点焊超声无损检测
确定分析间隔 捕获极限值
缺陷门槛值 噪声门槛值
参考波形包含信息:
总厚度 最大回波数目 回波顺序衰减率
中间回波数目、位置以及相对振幅 中间回波的包络形状
车身焊接技术培训课程
第 24 页
其它
焊件表面质量 焊缝气密性 成分偏析 接头金属物相 接头残余应力 接头金属晶粒 度 断裂性质
表面接触电阻 测定 接头气密性试 验 电子探针、电 子显微镜检验 X射线衍射断 口分析
车身焊接技术培训课程
第6页
点焊质量检测与评价
焊点破坏性检测方法
焊点质量检测的传统方法为对焊点进行破坏性检测。
主要包括: ¾ 抽样进行破坏性撕裂或凿检; ¾ 破坏性拉剪测试焊点强度; ¾ 金相试验检测焊核微观组织
坏Sca焊nM点a信ste号r 的SysAt-e扫ms描显示(粘焊、 虚焊)
与好焊点相比粘焊有较低的衰减 通常上层板底面(中间)回波很明显
代Sca表nM有aste孔r S的ystAem-s扫描信号
有快速声衰减的信号(环状焊点)
点焊超声无损检测
点焊超声检 测回波波形 及回波特征 值数据库的 建立
1)超声波检测 2)其它检测方法 9 X射线检测 9 涡流检测 9 红外线检测
车身焊接技术培训课程
第5页
点焊质量检测与评价
目视检验
撕破试 验
破坏性试验
低倍试验
强度试 验
金相、化学成 无损试验 分分析
点、缝焊熔
电极压坑、局 点焊核心 核直径
焊点质量检测方法

焊点质量检测方法1.1 目视检测目视检测时最常用的一种非破坏性检测方法,可用万能投影仪或10倍放大镜进行检测。
检测速度和精度与检测人员能力有关,评价可按照以下基准进行:(1)湿润状态钎料完全覆盖焊盘及引线的钎焊部位,接触角最好小于20°,通常以小于30°为标准,最大不超过60°。
(2)焊点外观钎料流动性好,表面完整且平滑光亮,无针孔、砂粒、裂纹、桥连和拉尖等微小缺陷。
(3)钎料量钎焊引线时,钎料轮廓薄且引线轮廓明显可见。
1.2 电气检测电气检测是产品在加载条件下通电,以检测是否满足所要求的规范。
它能有效地查出目视检测所不能发现的微小裂纹和桥连等。
检测时可使用各种电气测量仪,检测导通不良及在钎焊过程中引起的元器件热损坏。
前者是由微小裂纹、极细丝的锡蚀和松香粘附等引起,后者是由于过热使元器件失效或助焊剂分解气体引起元器件的腐蚀和变质等。
1.3 X-ray检测X-ray检测是利用X射线可穿透物质并在物质中有衰减的特性来发现缺陷,主要检测焊点内部缺陷,如BGA、CSP和FC焊点等。
目前X射线设备的X光束斑一般在1-5μm范围内,不能用来检测亚微米范围内的焊点微小开裂。
1.4 超声波检测超声波检测利用超声波束能透入金属材料的深处,由一截面进入另一截面时,在界面边缘发生反射的特点来检测焊点的缺陷。
来自焊点表面的超声波进入金属内部,遇到缺陷及焊点底部时就会发生反射现象,将反射波束收集到荧光屏上形成脉冲波形,根据波形的特点来判断缺陷的位置、大小和性质。
超声波检验具有灵敏度高、操作方便、检验速度快、成本低、对人体无害等优点,但是对缺陷进行定性和定量判定尚存在困难。
扫描超声波显微镜(C-SAM)主要利用高频超声(一般为100 MHz以上)在材料不连续的地方界面上反射产生的位相及振幅变化来成像,是用来检测元器件内部的分层、空洞和裂纹等一种有效方法。
采用微声像技术,通过超声换能器把超声脉冲发射到元件封装中,在表面和底板这一深度范围内,超声反馈回波信号以稍微不同的时间间隔到达转化器,经过处理就得到可视的内部图像,再通过选通回波信号,将成像限制在检测区域,得到缺陷图。
焊点检验规范

1、特征:焊接成不平滑外表,严重时于线脚四周,产生皱折或裂缝。
2、影响性:焊点寿命较短,容易于使用一段时间后,开始产生焊接不良之现象,导致功能失效。
3、造成原因:焊点凝固时,受到不当震动(如输送皮带震动),焊接物(线脚、焊垫)氧化,润焊时间不足。
4、补救处置:排除焊接时之震动来源;检查线脚及焊垫之氧化状况,如氧化过于严重,可事先Dip 去除氧化、调整焊接速度,加长润焊时间。
针孔:1、特征:于焊点外表上产生如针孔般大小之孔洞2、影响性:外观不良且焊点强度较差3、造成原因:PWB含水气;零件线脚受污染(如硅油);倒通孔之空气受零件阻塞,不易逸出。
4、补救处置:PWB过炉前以80~100℃烘烤2~3小时;严格要求PWB在任何时间任何人都不得以手触碰PWB表面,以避免污染;变更零件脚成型方式,避免Coating落于孔内,或察看孔径与线径之搭配是否有风孔之现象。
1、特征:在不同线路上两个或两个以上之相邻焊点间,其焊垫上之焊锡产生相连现象。
2、影响性:严重影响电气特性,并造成零件严重损害3、造成原因:板面预热温度不足;输送带速度过快,润焊时间不足;助焊剂活化不足;板面吃锡高度过高;锡波表面氧化物过多;零件间距过近;板面过炉方向和锡波方向不配合。
4、补救处置:调高预热温度;调慢输送带速度,并以Profile确认板面温度;更新助焊剂;确认锡波高度为1/2板厚高清除锡槽表面氧化物;变更设计加大零件间距;确认过炉方向,以避免并列线脚同时过炉,或变更设计并列线脚同一方向过炉。
空焊:1、特征:零件线脚四周未与焊锡熔接及包覆2影响性:电路无法导通,电气功能无法显现,偶尔出现焊接不良,电气测试无法检测。
3、造成原因:助焊剂发泡不均匀,泡沫颗粒太大;助焊剂未能完全活化;零件设计过于密集,导致锡波阴影效应;PWB变形锡波过低或有搅流现象;零件脚受污染;PWB氧化、受污染或防焊漆沾附;过炉速度太快,焊锡时间太短。
4、补救处置:调整助焊剂发泡槽气压及定时清洗;调整预热温度与过炉速度之搭配;PWB Layout设计加开气孔;调整框架位置;锡波加高或清除锡渣及定期清理锡炉;更换零件或增加浸锡时间;去厨防焊油墨或更换PWB;调整过炉速度。
JIS-Z3139-2009点焊、凸焊、及缝焊部位的截面试验方法译文
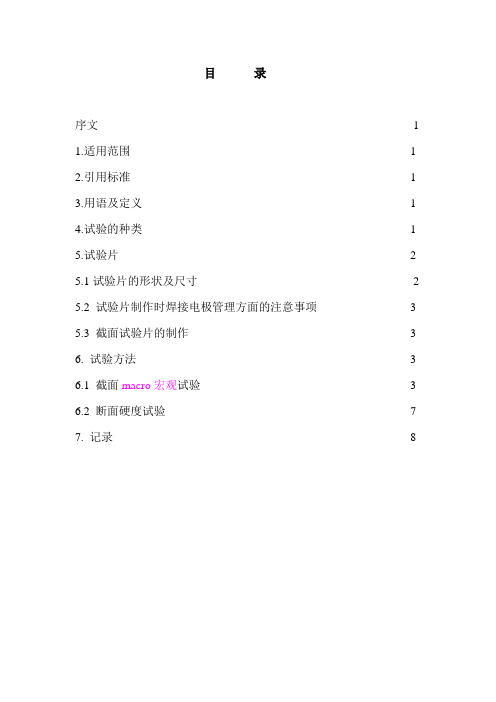
目录序文 11.适用范围 12.引用标准 13.用语及定义 14.试验的种类 15.试验片 2 5.1试验片的形状及尺寸 2 5.2 试验片制作时焊接电极管理方面的注意事项 35.3 截面试验片的制作 36. 试验方法 3 6.1 截面macro宏观试验 36.2 断面硬度试验77. 记录8Z 3139:2009前言本标准是依据工业标准化法第14条准用的第12条第1项之规定,应社团法人日本焊接协会(JWES)和财团法人日本标准协会(JSA)的申请,在原日本工业标准之基础上,经日本工业标准调查会的审议,由经济产业大臣修订的日本工业标准。
因此,JIS Z3139:1978 经修订由本标准替代。
本标准受著作权法的保护。
本标准的一部分,有可能与专利权、已公布的专利申请、实用新案权以及已公布的实用新案登记申请等有抵触之处,特敬请引起注意。
经济产业大臣和日本工业标准调查会对关于这样的专利权、已公布的专利申请、实用新案权以及已公布的实用新案登记申请等的确认,不负有责任。
日本工业标准JISZ 3139:2009 点焊、凸焊、及缝焊部位的截面试验方法序文本标准是在1978年发行的JIS Z 3139 “点焊焊接接头的截面试验方法”的基础上,根据我国国情进行了修订的版本,内容追加了截面硬度的试验方法。
1适用范围本标准适用于板厚为0.3mm--6.0mm的金属材料的点焊、凸焊及缝焊部位的截面试验方法的规定。
2引用标准本标准中所引用的标准如下,这些被引用的标准是构成本标准的一部分。
这些被引用的标准适用最新版本(含增补)。
JIS B 7725 维氏硬度试验----试验机的验证JIS Z 2244 维氏硬度试验----试验方法JIS Z 3001-1 焊接用语第1部:一般JIS Z 3001-2 焊接用语第1部:焊接方法JIS Z 3136 电阻点焊及凸焊接头的剪断试验之试片尺寸和试验方法3用语及定义本标准中使用的主要用语及定义除依据JIS Z 3001-1及JIS Z 3001-2之外,还作如下规定。
点焊试片测试指导书
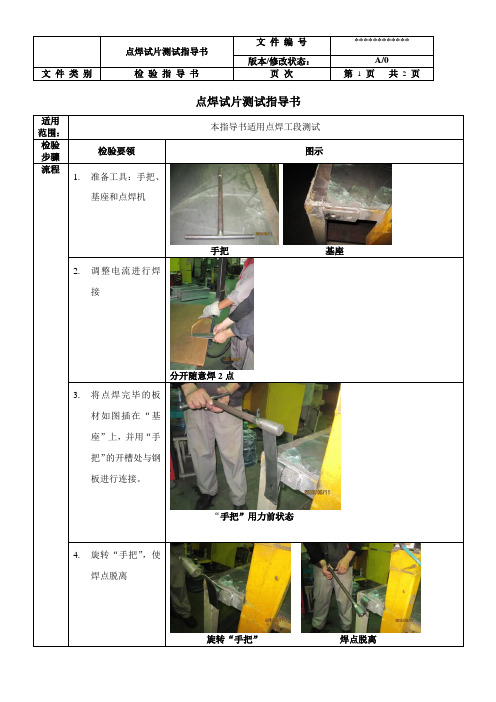
点焊试片测试指导书
适用
本指导书适用点焊工段测试
范围:
检验
检验要领图示
步骤
流程
1.准备工具:手把、
基座和点焊机
手把基座
2.调整电流进行焊
接
分开随意焊2点
3.将点焊完毕的板
材如图插在“基
座”上,并用“手
把”的开槽处与钢
板进行连接。
“手把”用力前状态
4.旋转“手把”,使
焊点脱离
旋转“手把”焊点脱离
5.焊点检测标准:焊
点剥离穿孔或基
板明显有凹坑—
适用于
0.5~2.0mm冷板。
√
合格:剥离通孔状态(如图)
不合格:没有剥离通孔现象
检测频率:首件检测,2.0厚板测试。
编制人: 审批人:日期:。
焊点质量检测
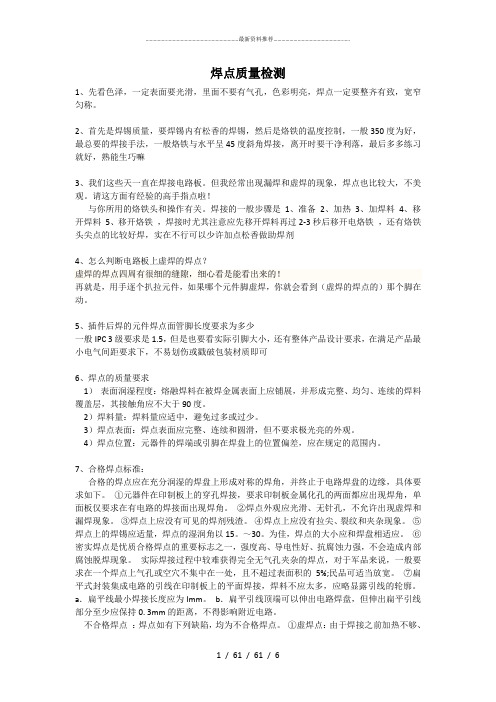
焊点质量检测1、先看色泽,一定表面要光滑,里面不要有气孔,色彩明亮,焊点一定要整齐有致,宽窄匀称。
2、首先是焊锡质量,要焊锡内有松香的焊锡,然后是烙铁的温度控制,一般350度为好,最总要的焊接手法,一般烙铁与水平呈45度斜角焊接,离开时要干净利落,最后多多练习就好,熟能生巧嘛3、我们这些天一直在焊接电路板。
但我经常出现漏焊和虚焊的现象,焊点也比较大,不美观。
请这方面有经验的高手指点啦!与你所用的烙铁头和操作有关。
焊接的一般步骤是1、准备2、加热3、加焊料4、移开焊料5、移开烙铁,焊接时尤其注意应先移开焊料再过2-3秒后移开电烙铁,还有烙铁头尖点的比较好焊,实在不行可以少许加点松香做助焊剂4、怎么判断电路板上虚焊的焊点?虚焊的焊点四周有很细的缝隙,细心看是能看出来的!再就是,用手逐个扒拉元件,如果哪个元件脚虚焊,你就会看到(虚焊的焊点的)那个脚在动。
5、插件后焊的元件焊点面管脚长度要求为多少一般IPC 3级要求是1.5,但是也要看实际引脚大小,还有整体产品设计要求,在满足产品最小电气间距要求下,不易划伤或戳破包装材质即可6、焊点的质量要求1)表面润湿程度:熔融焊料在被焊金属表面上应铺展,并形成完整、均匀、连续的焊料覆盖层,其接触角应不大于90度。
2)焊料量:焊料量应适中,避免过多或过少。
3)焊点表面:焊点表面应完整、连续和圆滑,但不要求极光亮的外观。
4)焊点位置:元器件的焊端或引脚在焊盘上的位置偏差,应在规定的范围内。
7、合格焊点标准:合格的焊点应在充分润湿的焊盘上形成对称的焊角,并终止于电路焊盘的边缘,具体要求如下。
①元器件在印制板上的穿孔焊接,要求印制板金属化孔的两面都应出现焊角,单面板仅要求在有电路的焊接面出现焊角。
②焊点外观应光滑、无针孔,不允许出现虚焊和漏焊现象。
③焊点上应没有可见的焊剂残渣。
④焊点上应没有拉尖、裂纹和夹杂现象。
⑤焊点上的焊锡应适量,焊点的湿润角以15。
~30。
为佳,焊点的大小应和焊盘相适应。
- 1、下载文档前请自行甄别文档内容的完整性,平台不提供额外的编辑、内容补充、找答案等附加服务。
- 2、"仅部分预览"的文档,不可在线预览部分如存在完整性等问题,可反馈申请退款(可完整预览的文档不适用该条件!)。
- 3、如文档侵犯您的权益,请联系客服反馈,我们会尽快为您处理(人工客服工作时间:9:00-18:30)。
铅焊料片式元件焊点的剪切试验方法
1.适用范围
这个标准主要针对电气机器、电子机器、通信机器等产品的布线连接和元器件连接(焊接)用无铅焊料所形成的焊点,对片式元件焊点剪切试验方法的规定。
2.引用标准
本标准的制定引用了以下标准的部分,这些标准均为当今适用性标准。
JIS Z 3197 焊接用助焊剂试验方法
JIS Z 3283 含树脂焊料
JIS Z 3284 焊锡膏
3.定义
这个标准使用的主要用语的定义,除了JIS Z 3197、JIS Z 3283和JIS Z 3284以外,还有下面二项。
a)无铅焊料,作为合金成分是不含有铅的"锡系焊料"的总称。
这里是对应电气、电子、通信机器等组装使用的"不含铅的焊料"。
b)片式元件,是适合表面贴装的超小型封装IC、电阻、电容、晶体管等单个型元件。
4.试验片由片式元件与焊接用基板组成,包含以下几个项目。
a)试验材料(基板和片式元件)的形状与尺寸。
b)试验材料的焊接方法。
C)试验片的热处理。
4.试验方法
试验方法有下面几项。
a)使用加压剪切试验装置(万能试验机)、将0.5mm的压头安装在剪切治具上。
b)将剪切治具垂直对准片式元件的中心位置,同时让焊接组装好的基板(试验片)固定在试验装置上。
剪切治具同片式元件的位置是否对准,可利用显微放大镜进行校正。
剪切治具同基板的间隙,规定在片式元件厚度的l/4以下。
但是,剪切治具和基板不能接触。
(参见图1)。
c)在对片式元件不形成冲击状态下,使用剪切治具一次接触,然后由剪切治具的移动作为施加载荷,
图1剪切试验方法测定概念图并开始测定。
(一次接触是剪切强度10%以下的力)。
剪切治具移动速度为5-30mm/min。
6.测定值的求得方法测定值的求得有以下二项。
a)将试验中的最大剪切负载作为测定值。
b)处用适合的观察装置观察剪切破坏位置与破坏界面,对破坏情况进行记录。
7.试验结果的记录试验结果的记录有以下内容。
a)试验的年、月、日。
b)试验场所。
C)试验片的名称、代号。
d)试验用基板焊盘与元件电极端子有无电镀、电镀的种类。
e)焊料种类。
f)助焊剂种类和焊接环境条件。
g)焊接方法(加热方法、预热温度、焊接温度、保持时间、加热.冷却速度等)。
h)焊点的剪切负载。
i)破断位置情况。