薄壁零件的加工实用工艺和夹具设计
薄壁易变形零件的夹具设计与改进

.
要 求
如 图 1 图 2所 示 , 、 4 个 圆形 凸 台 构 成 主 要 基 准面 A面 , 腰 形 凸 台 4个 构 成第 二基 准 面 B面 ,
2 加 工 工 艺 路 线
制定加 工 顺 序一 般遵 循 下列 原 则 :在一 次装 夹 中尽
程 决方案
E臣墨蜀 墨墨 工艺 / 工装 / 螺真 /诌断 / 柚■ / 维俺 / 改造
薄壁易 变形零件的 夹具设计与改 进
葛 菊 英 。 姚 建 方 。
( . 京 铁 道职 业 技 术 学 院 苏 州校 区 , 苏 苏 州 2 5 3 ;. 州 大 智 精 密 有 限 公 司 , 苏 苏 州 2 5 3 1 南 江 1 17 2苏 江 1 17)
1 零 件特 点
要 求 B 面 的 平 面度误 差 为 00 , 同时 相 .5
对 于 A 面 的
投影 仪 中 的盖 板是 薄壁 铝 压铸 件 , 构复 杂 , 件 刚 结 零 性 差 , 度弱 , 装 夹 中受 夹 紧 易变 形 , 易 保证 零 件 的 强 在 不 加 工质 量 。变形 l现翘 曲 , 叶 I 主要集 中在 中间 , 四周相 对 变
可能 完 成 大 部分 或 全 部工 序 ; 量 粗 、  ̄. 分 开 , 尽 精 12 1 3 先粗
后 精 ; 用 作精 加工 基 准 的表 面先 加 工 出来 ; 面后 孑 原 把 先 L
涂防锈 脂 , 再贴 二层 气相 防 锈纸 。
制 造 厂 已是 成 熟 的工 艺 技术 。但 对 一般 制造 厂 而言 仍然 进行 总结 , 供大 家借 鉴 。 大化及 麒麟 寺 机组 的镜 板投 入实
薄壁零件的加工特点及工艺分析

薄壁零件的加工特点及工艺分析机械加工肯定少不了薄壁零件的加工,而这类零件加工更需要仔细认真,所以了解其加工特点及工艺很有必要。
以下是店铺为你整理推荐薄壁零件的加工特点及工艺分析,希望你喜欢。
薄壁零件的加工特点1)易受力变形:因工件壁薄,在夹紧力的作用下容易产生变形,从而影响工件的尺寸精度和形状精度;(2)易受热变形:因工件较薄,切削热会引起工件热变形,使工件尺寸难于控制;(3)易振动变形:在切削力(特别是径向切削力)的作用下,容易产生振动和变形,影响工件的尺寸精度、形状、位置精度和表面粗糙度。
薄壁零件的加工工艺薄壁零件加工精度的容易受到多方面因素的影响,归纳起来主要有以下三方面:(1)受力变形;(2)受热变形;(3)振动变形。
如果采用传统的数控加工工艺,很难加工出符合精度要求的薄壁零件,甚至使薄壁产生破裂。
主要原因如下:(1)在粗加工时,切削量较大,在切削力、夹紧力、残余应力和切削热的作用下,会使薄壁产生一定程度的变形。
(2)半精加工和精加工时,随着材料的去除,工件的刚度已降至非常低,薄壁部分的变形会进一步加剧。
因此,根据薄壁零件的结构特点和加工精度要求,对于薄壁零件,应尽可能选择高速切削技术来加工。
采用高速切削技术,可有效地降低切削力和切削热,消除工件的残余应力,以提高薄壁零件的尺寸稳定性,同时要兼顾加工效率。
除采用高速切削技术外,薄壁零件的加工,还要合理安排加工顺序,尽可能保证内外轮廓线依次交叉切削加工。
以进一步消除工件变形带来的尺寸误差。
薄壁零件的加工举例1、工序的划分本任务划分为两道工序,共分(1)工序一:薄壁加工;(2)工序二:铣凸台和椭圆槽。
(3)工序三:孔加工。
其中工序一是难点。
划分2个工步,具体加工顺序如下:(1)选择φ10 mm双刃键槽铣刀粗加工薄壁内外轮廓线,刀补值选8.3mm,留出半精加工余量,深度方向分层切削,留0.2mm余量;(2)换φ10 mm 四刃立铣刀,采用高速切削技术半精加工薄壁内外轮廓线,刀补值选8.1 mm,深度方向分别留0.1mm余量;(3)用φ10 mm四刃立铣刀,采用高速切削技术,精加工薄壁两条轮廓线,并根据实际测量尺寸控制零件加工精度。
一种薄壁衬套的加工及夹具设计

厚 O4 nl最薄处 壁厚 01 .5l , n . 8mm。c ( 1 8 O ) / 1 . -O mm要 求与内 , 4 . 1 孔 同轴 度 00 i 零 件材料 为铍 青铜 C A12 来料 毛坯 为 .3h m, D 7, 中1 . t i 27o 的棒料 。 n 该零件为典 型的高精度 、 薄壁类零件 , 具有 薄壁 、 高精度 、 低刚性特点 。 加工 中最 需要解决 的问题 , 是控 制和减少变形。 成工 件 造
图 1 薄 壁零 件图
2 加 工需 考虑 的 主 要 因素
影 响薄壁衬套类零件 加工变形 的主要 因素 ,有工艺过程
3 工 艺路 线安 排
根据零件 的特点 , 毛坯外 圆余量 0 i, 计 了先 内后外 . ml 设 6 l
Байду номын сангаас
收稿 日期 :0 0-6 1 2 1- - 1 - 0 作者简介 : 王青成 ( 9 7 )男 , 1 7 一 , 河南光 山人 , 工程师 , 研究方 向: 机械加工 。
() 2 小锥 度芯轴一般 采用 1: 00 0或 1: 0 , 了降 1 0 50 0 为 低零件 的加 工难度 , 可根据其定 位孔精度制造 数种芯轴 , 这样
零件可 以分级/ r m- ;
fvvi - . ,  ̄I
( ) 内孔定位精加 工外形 时 , 3用 推荐采用用 小锥度 芯轴配
量; 然后 通过珩磨保证 内孔的尺寸和精度 。 配车 中(1. 1 .1
一
)
.
[: 二 [ : i 一
一
L …… 一 一一 ~
』
—
三 二
一 一
mm芯 轴后 , 套上零件 加工外 圆尺寸到设计要 求 , 最后 一道 车
浅谈薄壁零件加工的夹具设计与装夹

O 前 言
1 影 响 薄 壁零 件 加 工 精 度 的 因素
11 易 受 力 变 形 : 工 件 壁 薄 , 夹 紧 力 的 作 用 下 容 易 产 生 变 形 , . 因 在 从 而影 响工 件 的尺 寸 精 度 和 形 状 公 差 ; 1 易受 热变形 : 工件较单薄 , 削热 会引起工 件热变形 , 工件 _ 2 因 切 使 尺寸难于控制 : 13 易 振 动变 形 : 切 削 力 ( 别 是 粗 加 工 时 的切 削 力 ) 作 用 下 , - 在 特 的 容 易 产 生 振 动 和 变 形 。 接 影 响 工 件 的 尺 寸精 度 和表 面粗 糙 度 。 直
∞ O S 制静滠 皇 C 霞 ∞ 蛔 Z ∞ 墨 曩 魁
x 蹰嘲 。 8 辐 者 靠 郴 :x ’ 瞩
蕾盘
矗 哺礴 ∞ 毳 辅 30 蚺 礴
自x 觚
女 螂 ■ ≈ ■ t 戤
曩
_ {
挑
捌
3 夹具 设 计 与 装 夹
科技信息
O机械 与电子 0
S IN E&T C N L G N O M T O CE C E H O O YIF R A I N
21 年 01
第 2 期 1
浅谈薄壁零件加工的夹具设计与装夹
陈裕银 ( 东省 机械技 师 学院 广 东 广
广州
50 5 ) 1 4 0
【 要】 摘 针对影响批量薄壁零件加工的精度 因素 , 如何保 证薄壁 零件的k -精度 和批 量加 工的尺寸稳定 , y - 通过对 夹具设计与装夹 , 少多 减 次装 夹的累计误差 。 而达到薄壁零件加工的技术要求。 从 【 关键词 】 薄壁零件 ; 加工 ; 夹具设计与装夹
l 簟 I ’ ∞ ”麟 盘 姆 l● 如z x { . 哪
铝合金薄壁零件加工夹具设计

铝合金薄壁零件加工夹具设计摘要:随着经济的发展和社会的进步对我国的各行各业都产生了十分深远的影响,尤其是经济的发展在很大程度上带动了科技的发展,而科技的发展将直接带动铝合金薄壁零件加工技术的发展。
铝合金薄壁零件的应用十分广泛,为减少在加工期间的变形情况,本文对铝合金薄壁零件加工夹具的设计进行系统的探究。
关键词:铝合金;薄壁零件;加工;夹具薄壁零件在当前社会中是一件应用比较广泛的零件,尤其是在航天材料的制作方面,多能看到薄壁材料的身影。
但是薄壁材料本身的硬度比较小,在加工的过程中稍有不慎或者使用的器具不合规格便容易造成薄壁材料变形的情况。
如何有效的控制其变形一直是人们未曾彻底解决的问题。
基于此,本文对零件的夹具进行分析和研究,并且结合各项的测量数据来实现对夹具的改进。
1 铝合金薄壁零件加工过程中存在的问题某需要加工零件为长方体,长度为435mm,宽度为356mm,厚度为20mm,由铝合金制成。
加工要求其平面度为 0.06mm,粗糙度 Ral.6。
铝合金材料的韧性以及其本身的可塑性都比较好,但是在对其进行切割的过程中容易出现吸附现象,如在加工的过程中,已经被切掉的碎屑很容易吸附在刀具的刀刃上,从而形成一种比较聚集的碎屑“瘤”,而这种现象一旦形成之后将会很大程度上影响刀刃的使用情况,废屑不能够及时的排出并且很大程度上影响到加工材料的粗糙程度。
此外,在进行加工的过程中铝合金材料十分容易发生变热反应,而一旦变热之后便十分容易变形,从而产生且切削震动的现象,这种不正常的现象将对加工过程的本身产生很大的影响。
切削震动现象的发生不仅仅是会影响到加工完成之后的材料的质量,更会大大降低刀具本身和机床的使用效率和寿命。
2 夹具的设计的原则2.1如何设计夹具在进行夹具设计的过程中应满足以下几点要求:其加工的材料应具备足够的硬度,并且适当对其进行人工时效处理;在进行加紧处理时应注意其稳固程度;使用的过程要简洁方便;加工过程容易。
数控车床薄壁件加工技巧和方法

数控车床薄壁件加工技巧和方法一、概述薄壁件是指壁厚小于2mm的机械零件,具有重量轻、节省材料、结构紧凑等特点。
数控车床是现代加工制造业中应用广泛的设备,对于薄壁件的加工具有独特优势。
本文将重点介绍数控车床在薄壁件加工中的技巧和方法,以提高加工效率和产品质量。
二、材料选择与装夹方式1.材料选择:薄壁件常用的材料有铝合金、钛合金、不锈钢等,这些材料具有较好的塑性和切削性能。
在选择材料时,应充分考虑其物理性能和加工工艺性。
2.装夹方式:针对薄壁件易变形的特点,应采用合适的装夹方式,如真空吸附、专用夹具等,以保证工件在加工过程中保持稳定。
三、刀具选择与切削参数优化1.刀具选择:针对薄壁件的加工特点,应选用锋利、耐磨的刀具,如硬质合金刀具、涂层刀具等。
同时,刀具的几何参数对切削力、切削热等方面都有影响,应根据工件材料和加工要求进行合理选择。
2.切削参数优化:切削参数的合理选择对于薄壁件的加工至关重要。
应综合考虑切削深度、进给速度、切削速度等参数,以减小切削力、切削热对工件的影响,防止工件变形。
四、加工技巧1.轻切快走:在加工过程中,应采用轻切快走的加工方式,以减小切削力对工件的影响。
同时,合理使用切削液,降低切削温度。
2.分层加工:对于厚度较大的薄壁件,可以采用分层加工的方式,减小各层之间的切削力,避免工件变形。
3.工艺优化:在编制加工程序时,应充分考虑工件的形状、材料特性等因素,合理安排粗加工、半精加工和精加工的顺序,以提高加工效率和产品质量。
4.热处理:在加工过程中,可对工件进行适当的热处理,以提高其硬度和耐磨性。
同时,合理安排热处理工艺参数,防止工件变形或开裂。
5.检测与修正:在加工过程中,应定期检测工件的尺寸和形位公差,如有偏差应及时修正。
同时,对加工过程中出现的问题进行分析和总结,不断优化加工方法和工艺参数。
五、结论通过以上分析可知,数控车床在薄壁件加工中具有独特优势。
在实际生产中,应根据具体情况选择合适的材料、装夹方式、刀具和切削参数。
典型薄壁零件数控铣削加工工艺

典型薄壁零件数控铣削加工工艺典型薄壁零件指的是壁厚比较薄的机械零部件,其加工工艺要求高,因为薄壁零件具有易变形、易损坏等特点,所以数控铣削加工工艺尤为重要。
本文将介绍典型薄壁零件数控铣削加工的工艺流程、注意事项以及优化方案。
1. 零件设计和准备在进行数控铣削加工前,首先需要进行零件的设计和准备。
设计时需要根据零件的实际情况,合理确定加工工序、夹持方式和刀具选择。
在准备阶段,需要准备好数控铣床和相应的工具。
2. 夹持工件夹持工件是数控铣削加工的第一步,对于薄壁零件需要特别注意夹持方式。
通常采用夹具夹紧的方式,可以增加工件的稳固性,同时需要保证夹持力不会对薄壁零件造成变形。
3. 刀具选择和加工参数设定选择合适的刀具和加工参数对于数控铣削加工来说至关重要。
对于薄壁零件来说,需要选用合适的刀具和适当的进给速度、转速等加工参数,以减小切削力,降低对工件的影响。
4. 加工操作在进行数控铣削加工时,需要严格按照程序要求进行操作。
特别是在对薄壁零件进行加工时,需要小心谨慎,避免发生碰撞、振动等情况,以免对工件造成损坏。
5. 检测和修整加工完成后,需要对工件进行检测和修整。
特别是对于薄壁零件来说,需要注意检测工件的尺寸精度和表面质量,及时修整不合格的部分。
二、典型薄壁零件数控铣削加工的注意事项1. 选择合适的材料对于薄壁零件来说,材料的选择至关重要。
需要选择具有较好加工性能和机械性能的材料,以减小加工难度和提高工件的使用寿命。
4. 避免振动和冲击在进行数控铣削加工时,需要小心谨慎,避免对薄壁零件产生振动和冲击。
合理选择刀具和加工参数,以避免产生不必要的振动和冲击。
1. 刀具选用对于薄壁零件的数控铣削加工,需要选择具有良好刚性和稳定性的刀具,以减小切削力和振动。
同时应该根据工件的实际情况,选择不同的刀具类型以提高加工效率。
2. 加工参数优化在数控铣削加工时,需要根据薄壁零件的实际情况,合理选择进给速度、转速、切削深度等加工参数,以减小切削力,提高加工效率。
薄壁缸体零件加工工艺和夹具设计技术的研究

中图分类号 :H1 1 T 6
文献标识码 : A
文章编号 :6 1 7 8 (0 8 0 17 — 80 2 0 )5—04 0 0 5— 3
S u y o h r c si g Cr f n i sg i g o i l d r Co o e t t d n t e P o e sn a ta d J g Dei nn fTh n Cyi e mp n n s n
l ysi b r es gca n g e b ua l po si rfadj . m t e c n t i Ke od :rcsi r t i;ds r h c yW r spoes gca ;j n f g i ot uk t ;c
1 零 件 介 绍
前进档体伺服器缸体是某 公 司轿 车生产 中使用 的零
第 7卷第 5期
20 0 8年 1 0月
无 锡 职 业 技 术 学 院 学 报
J un lox s tt f I i Teh oo y
Vo . . 1 7 No 5
0c . 2 H8 t 0D
薄 壁 缸体 零 件 加 工 工 艺 和 夹 具 设 计 技 术 的研 究
CHEN i g, P n ZHENG e Zh n— pig n
( x stt o e n l y u i 1 1 1 C ia Wui ntue fTc o g ,W x 2 4 2 , hn ) I i h o
A s a t T ep oes gm to n gd s nn rc s o ti w l cl d r o yw r i rd c d ntepo es go b t c : h r si e da dj ei igpo es fhn a yi e d ee n o u e .I rc si f r c n h i g l n b t h n
薄壁零件的加工工艺和夹具设计

摘要:本文系统设计了薄壁零件的数控车削加工工艺。
通过探讨薄壁零件在加工中存在的易变形、零件尺寸精度、位置精度及表面粗糙度不易保证等技术问题,对加工难点进行分析,给出了加工工艺路线和加工方案,通过优化、完善夹具设计和切削参数,防止了薄壁零件加工变形、保证了较好的尺寸精度和位置精度,从而有效解决薄壁零件的车削加工难题。
由于薄壁零件刚性差、强度弱,在加工中极易变形,是零件的形位公差增大,不易保证零件的加工质量。
因此对薄壁零件的装夹,切削加工过程中刀具的合理选用及切削量的选择,提出了严格要求。
在普通车床上加工形状较复杂、有一定精度要求、且需要多把刀具进行加工的批量零件时,不仅需要频繁换刀和装夹,花费大量的人力和时间,而且加工出来的零件质量取决于加工人员的技术水平, 产品质量得不到充分的保证。
而运用数控车床,结合传统的加工工艺,不但能大大缩短加工时间、提高加工精度,而且成品率高、产品质量稳定。
所以,在运用数控机床加工过程中为保证被加工薄壁件的必要的精度,有同轴度要求的内外圆柱面或有垂直度要求的外圆与端面,尽可能在一次装夹中完成;需要编制其加工路线、合理的选择个阶段的加工参数并编写高质量的数控加工程序。
为完全保证零件的形位公差需要设计其装夹的夹具,为此,对零件图纸、零件加工及时效处理等方面都认真地进行了分析和研究。
图1-1由图1-1可看出,?64mm的外圆对?60mm的内孔的同轴度,?64的外圆的圆度和表面质量以及内孔尺寸精度的加工是该薄壁零件最主要的加工难点。
因为该零件刚性差、强度弱,在加工中极易变形,表面质量、垂直度及同轴度难以保证。
镗削内孔时应一次装夹中加工出来,以保证该零件的尺寸精度。
针对薄壁零件壁薄、刚性差、易变形的特点,可设计该薄壁零件专用夹具装夹,以保证零件的尺寸精度和形位公差达到图纸技术要求。
这些加工难点的存在,使得加工过程中刀具选择、加工工艺路线安排、工艺装夹方式确定等对于该零件是否合格非常关键。
薄壁类零件加工装夹技术研究
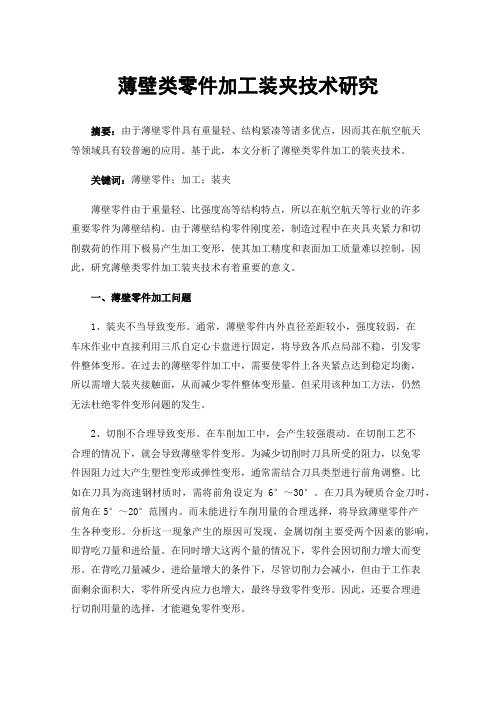
薄壁类零件加工装夹技术研究摘要:由于薄壁零件具有重量轻、结构紧凑等诸多优点,因而其在航空航天等领域具有较普遍的应用。
基于此,本文分析了薄壁类零件加工的装夹技术。
关键词:薄壁零件;加工;装夹薄壁零件由于重量轻、比强度高等结构特点,所以在航空航天等行业的许多重要零件为薄壁结构。
由于薄壁结构零件刚度差,制造过程中在夹具夹紧力和切削载荷的作用下极易产生加工变形,使其加工精度和表面加工质量难以控制,因此,研究薄壁类零件加工装夹技术有着重要的意义。
一、薄壁零件加工问题1、装夹不当导致变形。
通常,薄壁零件内外直径差距较小,强度较弱,在车床作业中直接利用三爪自定心卡盘进行固定,将导致各爪点局部不稳,引发零件整体变形。
在过去的薄壁零件加工中,需要使零件上各夹紧点达到稳定均衡,所以需增大装夹接触面,从而减少零件整体变形量。
但采用该种加工方法,仍然无法杜绝零件变形问题的发生。
2、切削不合理导致变形。
在车削加工中,会产生较强震动。
在切削工艺不合理的情况下,就会导致薄壁零件变形。
为减少切削时刀具所受的阻力,以免零件因阻力过大产生塑性变形或弹性变形,通常需结合刀具类型进行前角调整。
比如在刀具为高速钢材质时,需将前角设定为6°~30°。
在刀具为硬质合金刀时,前角在5°~20°范围内。
而未能进行车削用量的合理选择,将导致薄壁零件产生各种变形。
分析这一现象产生的原因可发现,金属切削主要受两个因素的影响,即背吃刀量和进给量。
在同时增大这两个量的情况下,零件会因切削力增大而变形。
在背吃刀量减少、进给量增大的条件下,尽管切削力会减小,但由于工作表面剩余面积大,零件所受内应力也增大,最终导致零件变形。
因此,还要合理进行切削用量的选择,才能避免零件变形。
3、刀具不合适导致变形。
薄壁零件在车削时,选取合理的刀具至关重要,尤其是对刀具几何角度的选择,不仅会影响切削力的大小,也会影响车削中产生的热变形程度,需关注的是,在薄壁零件的工作表面微观质量的把握也很重要。
毕业设计---薄壁类零件夹具设计

X X学院毕业设计说明书课题:薄壁类零件夹具子课题:同课题学生姓名:专业学生姓名班级学号指导教师完成日期目录摘要-------------------------------------------------3一、机床夹具概述----------------------------------------4二、审查零件图样的工艺性--------------------------------5三、毛坯的选择------------------------------------------5四、工艺过程设计----------------------------------------6五、确定机械加工余量及毛坯设计毛图----------------------8六、工序设计-------------------------------------------10七、夹具的设计-----------------------------------------13八、毕业设计小结 --------------------------------------24 致谢---------------------------------------------------25 参考文献-----------------------------------------------26摘要薄壁衬套是某型发动机火焰筒上的一个零件,加工难度较高。
材料为GH135,铁-镍基高温合金,此种合金具有良好的抗氧化性,有高的塑性和韧性,足够的热强性和良好的热疲劳性,是一种难加工材料。
并且是薄壁零件,当完成两外圆和内部形状加工之后,零件的壁较薄,受力差,因此要考虑其如何夹紧的问题。
为了加工出符合图样要求的零件,必须编制合理的工艺路线,并要求设计专用的夹具。
关键词:薄壁衬套、专用磨床夹具、专用钻模、铣槽夹具、铣弧形面夹具一机床夹具概述在机械制造中,用来固定加工对象,使这占有正确位置,以接受加工或检测的装置,统称为夹具。
薄壁类零件加工的工装设计与工艺设计

艺 和加工 方法 。正确 编制 工艺规 程 , 理安 排工序 , 合 使工 装设 计满 足使用 要求 。
2 工装 与工 艺 设 计
2 1 零件 的装夹 方式 与方 法 .
应 力塑 性 变形 和 比容 变化 引起 的体积 变形 两大类 。 某 厂某 型号 产 品 中加工 的是 大 口径 的变波束 平 板 天线 , 体结 构 由辐 射板 、 电板 、 5/ 主 馈 功 Y 和差 网络 等通过 盐浴 焊接 , 连接 波导 螺装 而成 , 显著 特点是 波 导腔体 叠 加 层 数 在 整 体 厚 度 不 到 3 r 内 达 到 五 0m a 体的零 件 壁厚 均 为 1 mm, 部 让 位 部 位 仅 为 局 05 m。腔体 尺寸精 密 。馈 网及 功率 分配 波 导 的分 .m 布与走 向设 计 变得 相 当 复杂 , 密 加 工 测量 比较 困 精 难 。再 有 天线 子 阵共 达 10多 个 , 0 天线 反 射 体 设 计
2 2 3 装 夹的有 效利 用 ..
提高了加工精度, 也降低 了后续钳工工序的工作量 。
参 考文 献 :
[ ] 王先逵 .机械 加工 工艺 手册 [ . 1 M] 机械 工业 出版 社 ,
20 . 0 7 ‘
装 夹 时采用 “ 哑铃 ” 面沉头 螺钉 装夹 , 除 了 双 去 压 板装 夹 , 以便 于零 件 的加 工 ; 而且 使 用 钢 丝 螺套 , 便 于螺纹 孔 的反 复使 用 ; 空 吸 附槽 增 加 了吸 附 面 真 积, 并且 减少 了真 空体 积 。
[ ] 崔 忠圻 .金 属 学与 热 处 理 [ . 2 M] 机械 工 业 出 版社 ,
】9 9 6.
具偏 差 , 并可实 现 对 薄 壁 工 件 的 加 工 。 由于 具有 这
薄壁零件车削加工的夹具改进与工艺调整方案分析

可把 原 来 车 内孔 和 车 外 圆 精 车 工 序 的两 套 拼 装 夹 具 合 并 成 一 套 专 用 夹 具 ,再 设计 两 套 压 板 ,这 样 夹 具 以工 件 的
2 9 7 . 5 。 mm 内孔 定位 , 以左 端 面 为 支 靠 面 , 并 让夹 具 外
一
圆直 径 小 于 3 3 3 . 5 . mm 。 2 . 调 整 车 削 加 工 工 艺 ( 1 ) 在 加 工 内孔 时 , 设 计 夹 具 由6点 支 靠 改 为 全 面 支 靠 。 可先 将 零 件 支 靠 面 磨 削 , 达 到 平 面 度 要 求 ,使 零 件 的 压 紧 面 和 定 位 面 配 合 稳 定 , 压 板 压 紧 零 件 受 力 均 匀 。在 加
l _ 2
一
/
、
●
、
‘
3 3 3 . 5 一 1 mm 留 余 量 0 . 6 mm, 尺 寸
.
5 ± 0 0 5
口
l mm 加 工 到 1 . 6 mm , 尺 寸 3 . 5± 0 . 0 5 mm@ H 工到3 . 7 mm
即可 。
一
-
U. 6 ● f 0 . 川
最 后 , 加 工 外 圆 尺 寸 3 3 3 . 5 _ o l , 3 4 6 06 。 此 时 , 由 于 其 他 尺 寸 已经 加 工 完 成 , 零 件 很 薄 ,而 且 形 位 公 差 精
一
度 要 求 高 ,就 一 定 要 使 用 较 小 的 进 给 量 和 较 锋 利 的 刀 具 进
1 !
j 5 ±0 0 5 0
]
薄壁零件的加工工艺处理和夹具设计

摘要:本文系统设计了薄壁零件的数控车削加工工艺。
通过探讨薄壁零件在加工中存在的易变形、零件尺寸精度、位置精度及表面粗糙度不易保证等技术问题,对加工难点进行分析,给出了加工工艺路线和加工方案,通过优化、完善夹具设计和切削参数,防止了薄壁零件加工变形、保证了较好的尺寸精度和位置精度,从而有效解决薄壁零件的车削加工难题。
由于薄壁零件刚性差、强度弱,在加工中极易变形,是零件的形位公差增大,不易保证零件的加工质量。
因此对薄壁零件的装夹,切削加工过程中刀具的合理选用及切削量的选择,提出了严格要求。
在普通车床上加工形状较复杂、有一定精度要求、且需要多把刀具进行加工的批量零件时,不仅需要频繁换刀和装夹,花费大量的人力和时间,而且加工出来的零件质量取决于加工人员的技术水平, 产品质量得不到充分的保证。
而运用数控车床,结合传统的加工工艺,不但能大大缩短加工时间、提高加工精度,而且成品率高、产品质量稳定。
所以,在运用数控机床加工过程中为保证被加工薄壁件的必要的精度,有同轴度要求的内外圆柱面或有垂直度要求的外圆与端面,尽可能在一次装夹中完成;需要编制其加工路线、合理的选择个阶段的加工参数并编写高质量的数控加工程序。
为完全保证零件的形位公差需要设计其装夹的夹具,为此,对零件图纸、零件加工及时效处理等方面都认真地进行了分析和研究。
图1-1由图1-1可看出,ø64mm的外圆对ø60mm的内孔的同轴度,ø64的外圆的圆度和表面质量以及内孔尺寸精度的加工是该薄壁零件最主要的加工难点。
因为该零件刚性差、强度弱,在加工中极易变形,表面质量、垂直度及同轴度难以保证。
镗削内孔时应一次装夹中加工出来,以保证该零件的尺寸精度。
针对薄壁零件壁薄、刚性差、易变形的特点,可设计该薄壁零件专用夹具装夹,以保证零件的尺寸精度和形位公差达到图纸技术要求。
这些加工难点的存在,使得加工过程中刀具选择、加工工艺路线安排、工艺装夹方式确定等对于该零件是否合格非常关键。
薄壁零件加工工艺及特点

薄壁零件加工工艺及特点1、工件分粗、精车阶段精车时,由于切削余量较大,夹紧力稍大些,变形也相应大些;精车时,夹紧力可稍小些,一方面夹紧变形小,另一方面精车时还可以消除粗车时因切削力过大而产生的变形。
2、合理选用道具的集合参数精车薄壁工件时,刀柄的刚度要求高,车刀的修光刃不易过长,一般取0.2—0.3mm,刃口要锋利。
3、增加装夹接触面采用开缝套筒或一些特制的软卡爪。
使接触面增大,让夹紧力均匀分布在工件上,从而使工件夹紧时不易产生变形。
4、应采用轴向夹紧夹具车薄壁工件时,工件靠轴向夹紧套螺纹套的端面实现轴向夹紧,由于夹紧力沿工件轴向分布,而工件轴向刚度大,不易产生夹紧变形。
5、增加工艺肋有些薄壁工件在其装夹部位特制几根工艺肋,以增强此处刚性,使夹紧力作用在工艺肋上,以减少工件的变形,加工完毕后,再去掉工艺肋。
6、充分浇注切削液通过充分浇注切削液,降低切削温度,减少工件热变形。
1、因工件壁薄,在夹紧力的作用下容易产生变形。
从而影响工件的尺寸精度和形状精度。
在夹紧力的作用下,会略微变成三边形,但车控后得到的是一个圆柱孔。
当松开卡爪,取下工件后,由于弹性恢复,外圆恢复成圆柱形,而内孔则变成弧形三边形。
若用内径千分尺测量时,各个方向直径相等,但已变形不是内圆柱面了,称之为等直径变形。
2、因工件较薄,切削热会引起工件热变形,从而使工件尺寸难于控制。
对于线膨胀系数较大的金属薄壁工件,如在一次安装中连续完成半精车和精车,由切削热引起工件的热变形,会对其尺寸精度产生极大影响,有时甚至会使工件卡死在夹具上。
3、在切削力特别是径向切削力的作用下,容易产生振动和变形,影响工件的尺寸精度、形状、位置精度和表面粗糙度。
由上述分析可知,薄壁零件的刚度低,是造成加工误差的内部因素,构成加工误差的外因,一方面,与机床本身的精度,刀具的性状有关。
另一方面,与零件所受外力有直接影响。
1、切削力的影响例如,在车床上或外圆磨床上加工长轴时,零件被装卡在两顶针之间。
薄壁工件的加工及装夹设计

薄壁工件的加工及装夹设计作者简介:姓名:章百明(1974.09--);性别:男,民族:汉,籍贯:安徽省太湖县人,学历:高中;现有职称:高级技师;研究方向:车工技能。
摘要:在当前的工业生产中,薄壁工件属于其中较为广泛应用的零件类型,对于这种零件来说,在具体的加工过程中,也具有一定的复杂性。
所以如果不能够妥善的处理,那么就会造成变形问题的出现,从而不利于零件的质量与精度的实现。
因此本文就对于薄壁工件的加工和装夹设计,作出了具体的分析,以供参考。
关键词:薄壁工件;加工;装夹;设计前言:对于薄壁工件而言,这种零件类型不仅自重较轻,而且从结构上来看,也较为紧凑,所以在对于零件的加工过程中,也提出了更高的要求。
在加工时,一个必要的加工操作就是切削。
在这一过程中,如果出现了振动问题,那么就会增加变形出现的几率。
所以,在具体的加工和装夹设计的过程中,也要能够掌握相应的技巧,提高整个加工的科学性,从而确保零件的质量。
1薄壁工件的加工技巧1.1 优化工艺流程在具体的加工过程中,会应用到各种类型的刀具,因此也会作用于工件之上。
所以针对实际的加工而言,要在最大程度上,减少装夹变形和切削过程中的力量,这样才能够防止变形问题的出现。
为了有效地切削材料,就要加大切削用量,同时还要施加一定的压紧力。
在这一过程中,要确保能够留出余量,以备后续的加工需要。
同时,也可以通过热处理的方法,这样就能够对于加工过程中所产生的残余应力,实现有效地消除,进一步的提高薄壁工件在加工过程中的精确度,不仅能够降低切削过程中所产生的热量和力量,同时还能提高加工质量,确保加工的进度。
1.2 完善加工工艺在具体的加工过程中,也会产生较大的摩擦力,所以就会出现较为严重的切削热。
在热力的影响之下,会导致产生受热不均的问题,因此不利于零件品质的实现。
而且在薄壁工件的加工过程中,所具有的加工效率以及变形的程度,都会受到走刀策略的直接影响。
因此就必须要能够科学的安排加工路径,让材料在切除的过程中具有对称性,同时还能够应用合理的走刀方式,做出相应的处理,确保能够均匀的施加力量,不断地降低在加工过程中工件的受力变化。
薄壁套零件的加工工艺分析与程序设计

图2六爪卡盘薄壁套零件的加工工艺分析与程序设计赵金凤(德州职业学院,山东德州253000)1薄壁套的工艺分析1.1薄壁套结构分析如图1所示为一薄壁套零件,生产类型为单件或小批量生产,无热处理工艺要求,薄壁套类零件孔壁较薄,该薄壁套结构简单,主要由内孔与外圆组成。
1.2薄壁套的工艺分析因薄壁套孔壁较薄,装夹过程中很容易变形,因此装夹难度较大,一般可采用以外圆定位和内孔定位夹紧的方法来完成。
1)以内孔定位。
该薄壁套的基准是准26+0.030mm 孔轴线,外圆、内孔精度及表面粗糙度要求较高;右端面与准26+0.030mm 孔轴线有垂直度要求,加工时应在一次装夹中完成;准300 -0.03mm 外圆既有圆度形位公差要求,又有同轴度要求,又因内孔存在阶台,无法一次装夹工件完成全部加工内容,因此可采取先加工完零件右端面及内孔,再使用芯轴或胀力芯轴装夹完成零件外圆加工的方法。
2)以外圆定位。
如果该薄壁套批量较大,基准是准300-0.03mm 的轴线,可以选择以外圆定位加工内孔,采用特制软卡爪、六爪卡盘(圆形包胎),如图2所示,夹持薄壁套,避免夹持变形,包胎选用轻、软材料,最好使用铜、铝制品,避免夹伤工件。
摘要:合理的数控加工工艺与加工程序是保证产品质量、提高生产效率的关键因素。
文中结合薄壁套的结构,分析加工工艺,设计加工程序,保证薄壁套的加工质量,同时也提高了加工效率。
关键词:薄壁套;加工工艺分析;程序设计中图分类号:TH 162文献标志码:A文章编号:1002-2333(2015)06-0070-02图1薄壁套零件41+0.0500.02准300-0.03准20+0.10准0.03 1.6C 140451.6A 0.02A3.2其余准26+0.03准380-0.1A作用也增强。
此外,在实际工程设计中,跨音速压气机的攻角设计是一个极其重要的参数,应当避免沿叶高局部正攻角过大,使得压气机局部槽道激波被推向上游从而引起整个压气机转子失速。
铝挤型散热片薄壁件加工工艺分析与夹具设计

115OCCUPATION2018 10技术与应用A PPLICATION编辑 姜学霞铝挤型散热片薄壁件加工工艺分析与夹具设计文/肖建章摘 要:本文主要讲述了铝挤型散热片薄壁件在CNC加工中的夹具设计。
在高精度、易变形的铝挤型散热片的加工中,在保证产品质量、精度的前提下,利用气动夹具装夹零件,操作方便,能大大地减轻劳动强度。
气动反应速度快,可以一次装夹多个零件,因而在生产过程中能缩短装夹、对零、拆卸工件等辅助工前时间,提高劳动生产率,实际生产中还可以实现一人多机,节省投资成本,实现快速盈利。
大批量的生产活动中还可以采用气动夹具通过电磁阀等电子元器件实现与设备联机实现自动化控制,进一步缩短加工过程中的辅助时间,使企业实现较大的盈利。
关键词:铝挤型散热片 夹具设计 气动装夹铝挤型散热片由于热传导能力强﹑密度小﹑价格便宜,所以得到了各大厂商的青睐,普遍装载在电脑CPU 、易发热电子元件的散热装置上,用途广泛。
图1所示为广州吉川机电装备有限公司加工的铝挤型散热片薄壁件,零件材料为AL 6063铸件薄体,加工量为5000个。
该零件的结构特点主要是由很多薄壁片组成,散热片厚度为1mm ,高度为6mm ,散热片不均匀地分布在最薄仅为2mm 厚的底板上,而且需要多面体加工,加工难度高。
按此加工本零件假如采用通用装夹的方式就容易出现变形、弯曲现象,且不能满足日常生产的效率。
为了解决此难题,本文结合企业大批量生产的加工要求,分析并设计一套基于数控加工工序分散的工艺方案及二道加工工序气动快速装置,从而有效提高工件的生产效率和加工精度,应用效果良好。
图1 铝挤型散热片零件图一、工艺分析1.零件加工工艺分析此散热片在购买时外形尺寸是为213.5mm × 117.5mm ,因此需要经过多个工序来完成。
工序一:裁剖,工序图如图2左图所示,采用普通夹具夹持即可。
工序二:CNC 铣裁切边,工序图如图2右图所示,采用普通夹具夹持即可。
薄壁零件的加工工艺

薄壁零件的加工工艺嘿,朋友!说起薄壁零件的加工工艺,这可真是个有趣又有挑战的事儿!你想想,薄壁零件就像个脆弱的小宝宝,稍微不小心,就容易受伤变形。
那怎么才能把这个“小宝宝”照顾好,让它乖乖地变成我们想要的样子呢?先来说说材料的选择吧。
这就好比给小宝宝选衣服,得选那种柔软又有韧性的布料,材料得有良好的力学性能,不然在加工过程中,它就容易“发脾气”,出各种问题。
比如说,如果选了太脆的材料,加工的时候一不小心就可能裂开,那可就糟糕啦!然后是刀具的选择。
这刀具就像是我们照顾薄壁零件的“小工具”,可不能马虎。
刀具得锋利,就像一把快刀能轻松地切开豆腐一样,这样在加工的时候才能减少切削力,降低零件变形的风险。
要是刀具不锋利,那加工起来就像用钝刀砍骨头,费劲不说,还容易把零件弄伤。
再说说切削参数。
这可太重要啦!切削速度、进给量和切削深度,就像是做饭时的火候、放盐量和加水的多少,得把握得恰到好处。
速度太快,零件会热得受不了,变形啦;进给量太大,零件会被“啃”得坑坑洼洼;切削深度太深,零件可能直接就“崩溃”了。
还有装夹方式呢!装夹就像给小宝宝系安全带,太紧了会勒得难受,太松了又不安全。
得选合适的夹具,均匀地施加夹紧力,不然零件会被夹得变形,那可就前功尽弃了。
加工顺序也有讲究哦!就像搭积木,得先搭好基础,再一层一层往上盖。
先加工容易变形的部位,再加工相对稳定的部分,这样才能保证零件的整体精度。
在加工过程中,冷却润滑也不能忽视。
这就好比大热天给小宝宝扇扇子、擦汗,能让零件保持冷静,减少热变形。
最后,别忘了加工后的处理。
就像给小宝宝洗完澡要擦干、穿好衣服一样,对加工好的薄壁零件进行去毛刺、抛光等处理,让它变得更加光滑漂亮。
总之,薄壁零件的加工工艺就像是一场精心策划的演出,每一个环节都要考虑周全,不能有丝毫的马虎。
只有这样,才能让薄壁零件这个“小宝宝”健康成长,变成我们理想中的样子!你说是不是这个理儿?。
薄壁套的加工工艺与夹具设计

本文采用有限元分析软件 ANSYS 对不同剪切间隙下 的钢管剪切过程进行了分析,采用接触类型单元处理模具 与钢管的贴合与分离,提高了准确性,并通过对分析结果 进行比较得出了剪切间隙与断面品质的关系。
参考文献:
[1] 齐克敏,丁 桦. 材料成 形工艺 学[M]. 北 京: 冶金工业出版 社,2006.
件变形大。因此要充分考虑如何装夹定位的问题。如果
采用常规方法装夹 工 件 及 切 削 加 工 ,将 会 受 到 轴 向 切 削
力和热变形的影响,工件会出现弯 曲 变 形,很 难 达 到 技
术要求。
b) 机械加工工艺
1) 用三爪卡盘装夹,找正工件。粗车零件各直径尺
寸留 1 mm 半精车和精车余量;
2)
·62·
http: ∥ZZHD. chinajournal. net. cn E-mail: ZZHD@ chainajournal. net. cn《机械制造与自动化》
- 1、下载文档前请自行甄别文档内容的完整性,平台不提供额外的编辑、内容补充、找答案等附加服务。
- 2、"仅部分预览"的文档,不可在线预览部分如存在完整性等问题,可反馈申请退款(可完整预览的文档不适用该条件!)。
- 3、如文档侵犯您的权益,请联系客服反馈,我们会尽快为您处理(人工客服工作时间:9:00-18:30)。
摘要:本文系统设计了薄壁零件的数控车削加工工艺。
通过探讨薄壁零件在加工中存在的易变形、零件尺寸精度、位置精度及表面粗糙度不易保证等技术问题,对加工难点进行分析,给出了加工工艺路线和加工方案,通过优化、完善夹具设计和切削参数,防止了薄壁零件加工变形、保证了较好的尺寸精度和位置精度,从而有效解决薄壁零件的车削加工难题。
由于薄壁零件刚性差、强度弱,在加工中极易变形,是零件的形位公差增大,不易保证零件的加工质量。
因此对薄壁零件的装夹,切削加工过程中刀具的合理选用及切削量的选择,提出了严格要求。
在普通车床上加工形状较复杂、有一定精度要求、且需要多把刀具进行加工的批量零件时,不仅需要频繁换刀和装夹,花费大量的人力和时间,而且加工出来的零件质量取决于加工人员的技术水平, 产品质量得不到充分的保证。
而运用数控车床,结合传统的加工工艺,不但能大大缩短加工时间、提高加工精度,而且成品率高、产品质量稳定。
所以,在运用数控机床加工过程中为保证被加工薄壁件的必要的精度,有同轴度要求的外圆柱面或有垂直度要求的外圆与端面,尽可能在一次装夹中完成;需要编制其加工路线、合理的选择个阶段的加工参数并编写高质量的数控加工程序。
为完全保证零件的形位公差需要设计其装夹的夹具,为此,对零件图纸、零件加工及时效处理等方面都认真地进行了分析和研究。
图1-1由图1-1可看出,ø64mm的外圆对ø60mm的孔的同轴度,ø64的外圆的圆度和表面质量以及孔尺寸精度的加工是该薄壁零件最主要的加工难点。
因为该零件刚性差、强度弱,在加工中极易变形,表面质量、垂直度及同轴度难以保证。
镗削孔时应一次装夹中加工出来,以保证该零件的尺寸精度。
针对薄壁零件壁薄、刚性差、易变形的特点,可设计该薄壁零件专用夹具装夹,以保证零件的尺寸精度和形位公差达到图纸技术要求。
这些加工难点的存在,使得加工过程中刀具选择、加工工艺路线安排、工艺装夹方式确定等对于该零件是否合格非常关键。
加工工艺分析与设计套类零件是用来支承旋转轴及轴上零件或用来导向的,该类零件的主要表面是孔和外圆,其主要技术要孔及外圆的尺寸以及圆度要求;外圆之间的同轴度要求;孔轴线与端面的垂直度要求。
薄壁套类零件壁厚很薄,径向刚度很弱,在加工过程中受切削力、切削热及夹紧力等因素的影响,极易变形,导致以上各项技术要求难以保证。
针对这些问题,本文对薄壁套类零件加工过程中装夹方法、切削用量、刀具几何角度等做了初步的探讨。
1.薄壁套类零件的加工分析(1)工件装夹方法薄壁类零件在加工过程中如果采用普通装夹方法,会因为产生很大的变形而无法保证加工精度。
如图1所示。
图1 套筒夹紧变形误差故薄壁类零件的装夹,一般应增大工件的支承面和夹压面积,或增加夹压点使之受力均匀,并减小夹压应力和接触应力,必要时可增设辅助支承,以增强工件的刚性。
具体措施如下:①采用工艺夹头装夹车削时在坯料上预留一定的夹持长度,在工件完成孔、外圆及端面的加工后切掉。
这样不但防止了工件产生太大变形,而且保证了孔、外圆及端面间的位置精度。
但这种方法在应用中有局限性而且会造成材料的浪费。
②增加夹压点或夹压面积通过增加夹压点或夹压面积减小零件的变形或使变形均匀化。
如:采用专用卡爪或开口过渡环装夹;采用液性塑料自定心夹头或弹簧夹头装夹;采用传力衬垫装夹等。
③变径向夹紧为轴向夹紧使夹紧力作用在刚度较大的轴向,避免了径向发生大的变形。
(2)切削用量的选择为减少工件振动和变形,应使工件所受切削力和切削热较小。
在切削过程中产生的切削力可以分解为三个分力:主切削力Fz、进给抗力Fx、吃刀抗力Fy。
切削力的经验公式为:其中吃刀抗力Fy作用在机床和工件刚度最差的方向上,容易引起切削振动和工件的弯曲变形,影响加工精度和工件表面质量。
切削热计算公式为:从以上两式中可以看出,切削用量应该选较小值,但考虑到生产率及加工塑性材料时避开积屑瘤的影响等,一般背吃刀量和进给量取较小值,而切削速度取较大值。
从式(2)中可以看出切削速度增大后产生的热量会增多,但同时工件与刀具的相对运动速度也提高,使热量来不及传到工件上而大部分被切屑带走,因此,对加工的影响并不会增大。
(3)刀具角度的选择加工薄壁类工件的刀具刃口要锋利,一般采用较大的前角和主偏角,但是不能太大,否则会因刀头体积的减小而引起强度、刚度下降,散热性能变差,最终影响加工精度。
刀具角度的取值与工件的形状、材质以及刀具自身的材料有关。
2加工工艺过程分析在薄壁套的加工中有两个主要因素影响加工精度:(1)薄壁套本身的刚度比较差,在外力(切削力、夹紧力)的作用下容易变形。
(2)薄壁套毛坯为d70x7的45号无缝钢管,孔的加工余量大,切削时会产生较大的残余应力,并引起应力的重新组合。
因此在安排工艺时,就需要把各主要表面的粗精加工工序分开。
这样,粗加工产生的误差和变形就可以通过半精加工和精加工予以修正,并逐步提高零件的精度和表面质量,最后达到零件的技术要求。
通过对该零件的基本情况及加工难点的分析,划分出薄壁套零件的加工阶段并制定出其加工工艺过程。
[6]2.1加工阶段的划分薄壁套的加工基本上分为三个阶段:(1)粗加工阶段。
主要包括粗车外圆和粗镗孔来去掉大部分余量。
(2)半精加工阶段。
主要完成零件一些次要表面的加工,并达到零件表面质量和未知精度的要求。
其次,采用半精车加工在精加工之前达到必要的精度和加工余量,从而为套外圆的精加工做准备。
(3)精加工阶段。
为保证薄壁套零件外圆表面质量达到图纸的技术要求,采用精车零件外圆最后达到所需的精度和粗糙度。
2.2定位基面的选择薄壁套是一典型薄壁零件,在外力作用下很容易产生变形,薄壁套孔与台阶孔表面的尺寸精度和位置精度的要求比较高,因此希望以一个统一基面定位来加工这些要求较高的表面。
实际加工中我们选择外圆表面和断面1作为加工定位基面。
采用外圆表面和断面1作为基面有以下优点:(1)用这种定位方法可以加工外圆表面、端面、孔。
且在一次装夹中完成精度要求较高的表面的加工,既提高了生产效率,又能保证各表面的尺寸精度和位置精度。
(2)以外圆作为定位基面一次装夹同时完成外圆和孔的加工,可以减小薄壁套的壁厚差,从而保证其壁厚均匀。
(3)所选定位基面与设计基准重合,可以避免因基准不重合而引起的定位误差,更好的保证精度。
2.2加工工艺过程薄壁套的尺寸精度、加工形位精度的要求比较高。
但薄壁套壁薄、刚性差,容易产生变形,这就给薄壁套零件机械加工带来了很多困难,必须予以充分重视。
薄壁套需要加工的表面有:外圆、孔及左右端面等。
各主要表面的工序安排如下:(1)外圆面:粗车、半精车、精车;(2)两端面;粗车、半精车、精车;考虑薄壁套零件需要加工的容不多,加工完成后就能达到待检状态,因此以一次安装加工作为一道工序。
该薄壁零件的数控加工工艺过程如表2-1所示。
表2-1 薄壁套机械加工工艺过程粗车断面1,且粗车孔加工到58mm长度尺寸45mm左右半精车孔至59mm工序一简图采用专用夹具装夹,加工到下列尺寸及技术条件:粗车外圆面至65mm,半精车外圆至64.4mm精车外圆至要求尺寸64mm工序四简图工件至于套筒加工精车孔到60mm工序五简图3加工工艺方案的设计3.1刀具的选择数控编程时,正确选择刀具是数控加工工艺中的重要容,其不仅影响机床的加工效率,而且直接影响加工质量。
选择刀具通常考虑工件材料、加工型面类型、切削用量,以及其他相关因素。
刀具选择总的原则是:既要求精度高、强度大、刚性好、耐用度高,又要求尺寸稳定,安装调整方便。
在满足加工要求的前提下,尽量选择较短的刀柄,以提高刀具的刚性。
在此原则上,综合考虑45钢材料的加工特点以及加工中振动和切削力引起的变形,薄壁套零件的加工刀具均选用机夹可转位车刀,切削刀具参数选择见表3-1。
表3-1刀具的参数选择3.2切削用量的确定数控编程中,必须确定每道工序的切削用量,并以指令的形式写入程序中。
切削用量包括主轴转速、背吃刀量及进给速度等。
其选择原则是保证零件加工精度和表面粗糙度,充分发挥刀具切削性能,保证合理的刀具耐用度,并充分发挥机床的性能,最大限度的提高生产率,降低成本。
由于此零件为薄壁零件,加工时,刚性较差,易产生振动,刀具的切削硬度又不足以满足加工需求,为此,在刀具和夹紧力相对固定的情况下,只能通过优化切削参数进行调整,以表面粗糙度计算公式:εr f R a 502⨯= (式3-1)(f——进给量, r——刀尖圆弧半径)为参考,切削用量选择见表3-2。
表3-2切削用量的选择3.3冷却与润滑用硬质合金车刀粗车45钢时,一般要用冷却润滑,但因切削用量较大,可用质量分数5%的乳化液。
精加工时由于45钢容易和氢起化学作用,使薄壁套零件表面产生很细的针孔,不宜采用水剂切削液。
为减少摩擦和粘刀,一般采用煤油或煤油加机油的混合。
[5]冷却液对零件冷却时切忌时有时无,以避免刀具出现冷热交变而产生破裂现象,必须连续、充分地浇注,以改善已加工表面的质量和提高刀具使用寿命。
同时工件不受切削热的影响而使它的加工尺寸和几何精度发生变化,保证了零件的加工质量表。
夹具设计1.在粗车和半精车薄壁套表面时,我选择的是在毛胚圆筒外面加上一个套筒进行夹紧,在这个套筒上是开了缝的,方便在三爪卡盘上能有效夹紧需要加工的薄壁套。
2.在半精车孔后,可以以孔为定位基准加工外圆,这时就应制作一个专用夹具—心轴。
2.1夹具设计总要求夹具通常安装在车床的主轴前端部,与主轴一起旋转。
由于夹具本身处于旋转状态,因而夹具在保证定位和夹紧的基本要求前提下,还必须有可靠的防松结构。
1)结构紧凑、悬伸短夹具是随主轴一起回转的,重心应尽可能靠近主轴端部,以减少惯性力和回转力矩。
夹具悬伸长度L与夹具体外径D之比应参照下列数值选取。
当D<150mm时,取L/D<1.25;当150mm<D<300mm时,取L/D<0.9;当D>300mm时,取L/D<0.60。
薄壁套夹具的外径是63mm,所以选择L/D<1.252)平衡、配重为避免回转时产生离心力而引起振动,对夹具应进行平衡。
平衡的方法有两种:设置配重块或加工减重孔。
配重块上应开有弧形槽或径向孔,以便调整配重块的位置。
3)夹紧机构应安全耐用夹紧点尽量选在工件直径最大处,夹紧力足够大,在切削过程中,不至于在离心力和惯性力作用下使夹紧松动。
夹具上尽可能避免带有尖角或凸出部分。
4)夹具与机床的联接要准确、可靠避免安装引起的加工误差。
2.2定位原件的设计要求加工回转面时,定位元件的结构和布置必须保证工件被加工面的轴线与车床主轴的旋转轴线重合。
2.3夹紧装置的设计要点夹紧机构必须产生足够的夹紧力,自锁性能要良好。
优先采用螺旋夹紧机构。
对于角铁式夹具,还应注意施力方式,防止引起夹具变形。