分解炉分级燃烧降氮脱硝技术的研究与应用.
水泥厂低氮燃烧及SNCR脱硝技术简介
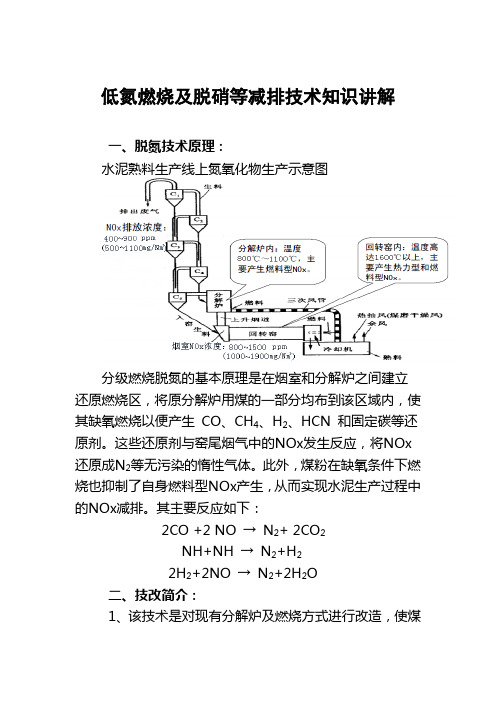
低氮燃烧及脱硝等减排技术知识讲解一、脱氮技术原理:水泥熟料生产线上氮氧化物生产示意图分级燃烧脱氮的基本原理是在烟室和分解炉之间建立还原燃烧区,将原分解炉用煤的一部分均布到该区域内,使其缺氧燃烧以便产生CO、CH4、H2、HCN 和固定碳等还原剂。
这些还原剂与窑尾烟气中的NOx发生反应,将NOx还原成N2等无污染的惰性气体。
此外,煤粉在缺氧条件下燃烧也抑制了自身燃料型NOx产生,从而实现水泥生产过程中的NOx减排。
其主要反应如下:2CO +2 NO →N2+ 2CO2NH+NH →N2+H22H2+2NO →N2+2H2O二、技改简介:1、该技术是对现有分解炉及燃烧方式进行改造,使煤粉在分解炉内分级燃烧,在分解炉锥部形成还原区,将窑内产生的NOx还原为N2,并抑制分解炉内NOx的生成。
根据池州海螺3#天津院设计的TDF分解炉结构,技改方案采用川崎公司窑尾新型燃烧器,并在分解炉锥部新增两个喂煤点,最大限度形成还原区,提高脱氮效率。
改造整体示意图2、窑尾缩口由圆形改成方形,高度改为1600mm,并设置跳台,防止分解炉塌料现象发生,通过在分解炉锥部增设喷煤点,在分解炉锥部形成还原区。
改造前锥部改造后锥部3、对窑尾烟室入炉烟气进行整流,将上升烟道改造成方形,同时,将上升烟道的直段延长,使窑内烟气入炉流场稳定,降低入炉风速。
其次在分解炉锥部设计脱氮还原区,将分解炉煤粉分4点、上下2层喂入,增加了燃烧空间。
在保证煤粉充分燃烧的同时,适当增加分解炉锥部的煤粉喂入比例,保证缺氧燃烧产生的还原气氛,从而在分解炉锥部区域形成一个“还原区”,部分生成的氮氧化物在该区域被还原分解,降低系统氮氧化物浓度。
改造前窑尾燃烧器改造后窑尾燃烧器三、SNCR脱硝技术基本原理SNCR选择性非催化还原是指无催化剂的作用下,在适合脱硝反应的“温度窗口”内喷入含有NHx基的还原剂将烟气中的氮氧化物还原为无害的氮气和水。
该项目技术采用炉内喷氨水(浓度20-25%)作为还原剂还原分解炉内烟气中的NOx。
几种工业脱硝技术简介

一、减排氮氧化物社会效益氮氧化物(NOx)是大气的主要污染物之一,包括NO、NO2、N2O、N2O3、N2O5等多种氮的氧化物,燃煤窑炉排放的NOx中绝大部分是NO。
NO的毒性不是很大,但是在大气中NO可以氧化生成NO2。
NO2比较稳定,其毒性是NO的4~5倍。
空气中NO2的含量在3.5×10-6(体积分数)持续1h,就开始对人体有影响;含量为(20~50)×10-6时,对人眼有刺激作用。
含量达到150×10-6时,对人体器官产生强烈的刺激作用。
此外,NOx还导致光化学烟雾和酸雨的形成。
由于大气的氧化性,NOx在大气中可形成硝酸(HNO3)和硝酸盐细颗粒物,同硫酸(H2SO4)和硫酸盐颗粒物一起,易加速区域性酸雨的恶化。
随着我国工业的持续发展,由氮氧化物等污染物引起的臭氧和细粒子污染问题日益突出,严重威胁着人民群众的身体健康,成为当前迫切需要解决的环境问题。
2011年全国人大审议通过了“十二五”规划纲要,提出将氮氧化物首次列入约束性指标体系,要求“十二五”期间工业氮氧化物排放减少10%,氮氧化物减排已经成为我国下一阶段污染治理和减排的重点。
二、水泥厂脱硝工艺选择目前,水泥窑NOx控制技术主要包括低氮燃烧器、分级燃烧法、非选择性催化还原法(SNCR)和选择性催化还原法(SCR)等,各控制技术的脱氮效率如下表所示:NOx控制技术低NOx燃烧器SCR分级燃烧SNCR脱氮效率10~15%85~90%25~30%50~70%1、低NOx燃烧器目前在国内已经有广泛应用,但其效果受窑工况影响较大,一般NOx 的排放量不能达到预期效果或效果不明显。
低氮燃烧器一般把一次风分成浓淡两股,浓相在内,更靠近火焰中心;淡相在外,贴近水冷壁。
浓相在内着火时,火焰温度相对较高,但是氧气比相对较少,故生成的氮氧化物的几率相对减少;淡相在外,氧气比相对较大,但由于距火焰高温区域较远,温度相对较低,故氮氧化物的生成也不会很多。
实例探讨低氮燃烧技术的应用

实例探讨低氮燃烧技术的应用近年来国务院及环保部相继出台了一系列严格的环保政策,要求燃煤发电机组在2014年7月1日后烟氣中NOx排放浓度不超过100mg/Nm3。
响应国家环保政策,我公司势必对6台燃煤机组实施进行烟气脱硝改造,为确保烟气脱硝装置投运后的NOx排放不超过100mg/Nm3,公司进行了认真调研,决定先对锅炉燃烧系统进行低氮改造,以实现炉膛出口NOx浓度不超过200mg/Nm3,为后期脱硝改造打下基础。
本文以#6机组为例介绍了我公司低氮燃烧改造过程。
1.分级燃烧技术的脱硝原理锅炉NOx的生成主要取决于燃烧区域的氧量和火焰温度,氧量越大或温度越高则NOx生成越多。
分级燃烧技术的原理就是在燃烧器前部加装浓淡分离器,并在燃烧器上部合理布置空气喷口(SOFA,俗称火上分)。
浓淡分离器使制粉系统喷入炉内的风粉混合物(一次风)分为浓淡两相,浓相在内,淡相在外。
浓相集中相对区域着火时,火焰温度虽高,但是氧量相对较少,故生成NOx的几率相对减少;淡相在外,氧量虽大,但由于距火焰集中区域较远,温度较低,故NOx 的生成也不会很多。
另外,在锅炉燃烧器上方布置SOFA喷口的目的,是为了在燃烧器上部构建充分的燃烧区域,使浓相缺氧燃烧后残留的可燃成份被再次充分燃烧,提升锅炉效率的同时减少炉膛结渣。
2.改造概况2.1概述江阴苏龙热电有限公司#6机组装机容量330MW,锅炉为亚临界、一次中间再热、控制循环汽包炉,单炉膛、Π型露天布置,全钢架悬吊结构,平衡通风,固态排渣,设计燃烧煤种为高挥发份烟煤,采用摆动式燃烧器、四角布置切圆燃烧方式,配用双进双出正压直吹式制粉系统。
2.2锅炉燃烧系统改造锅炉原设计采用单炉膛四角布置的摆动式直流燃烧器切圆燃烧方式,配以3台双进双出正压直吹式制粉系统,共有6层一次风喷嘴,其中4层运行即可带额定负荷。
燃烧器采用WR同轴一次风燃烧器,上部两层布置紧凑型OFA空气喷口。
本次改造采用大改方案,更换现有的全部主燃烧器,重新布置燃烧器一二次风射流方向;增加贴壁风喷口;在主燃烧器上部加装SOFA喷口,将原锅炉侧墙二次风风箱上取风引入SOFA喷口;主燃烧器区风箱风道、挡板风箱、风门执行器及摆动气缸等全部更换,以实现燃烧器改造后的可靠控制和精确配风,主要改造项目如下:2.2.1更换6层四角主燃烧器一二次风组件、风箱风道、挡板风箱及电气、热工附件;2.2.2在燃烧器组上方新增高位燃烬SOFA风风道、膨胀节、风箱、挡板风箱、喷口、风门执行器、摆动执行器;2.2.3主燃烧器区水冷壁管屏开孔、燃烬风区域水冷壁割断,由上海锅炉厂按照先要求重新设计制造水冷壁,采用弯管焊接方式进行恢复;2.2.4原油枪点火器、火焰检测器、微油燃烧器及油枪利旧,保护拆除恢复;2.2.5一次风管安装可调缩孔,根据动力场试验结论进行调整;2.2.6新增电气、仪表及控制设备,包括电源盘、控制柜、电缆等;2.2.7新增支吊架、楼梯平台、检修起吊设施、防腐、保温设计等相应附属设备。
浅谈分级燃烧与SNCR脱硝芜湖海螺

3.3 分级燃烧脱氮技术
空气分级燃烧
指将燃烧所需的空气( 三次风)分成两部分送入, 一部分送入第一级燃烧区内 ,使过剩空气系数α在0.8 左右,燃料先在缺氧富燃料 条件下燃烧,形成还原剂, 将NOx还原成N2等无污染的 惰性气体。另一部分空气输 入二级燃烧区内,保证燃料 的完全燃烧
缩口延长: 提高整流效果,形成稳定流场
增设跳台: 防止炉内局部塌料现象发生
缩小三次风管入风口截面积: 提高三次风入炉风速,增强旋流作用
4.4 分级燃烧操作控制思想
操作控制 思想
三次风挡板开度上调,由25% 40%,增大 三次风量,提高入炉旋流效应,避免边壁高 温现象;
506高温风机转速下调,由710rpm 680rpm, 严格控制预热器出口O2(1.0%左右),窑尾O2 (3.0%左右);
燃料分级燃烧
指在烟室和分解炉之间 建立还原燃烧区,将原分解 炉用燃料的一部分均布到该 区域内,使其缺氧燃烧以便 产生 CO、CH4、H2、HCN和固 定碳等还原剂。还原剂与窑 尾烟气中的NOx发生反应,将 NOx还原成N2等无污染的惰性 气体。此外,煤粉在缺氧条 件下燃烧也抑制了自身燃料 型NOx产生
做好系统漏风治理
3
避免煤粉在富氧下 燃烧,高温结皮,影响 脱硝效率分级燃烧正常 运行
4.7 分级燃烧改造应关注几个问题
三次风挡板
随着窑工况及煤质变化, 为匹配窑炉用风,保证分 级燃烧效果,三次风挡板 经常性调整
分煤比例
顾忌分解炉会出现结皮, 比例偏小控制;其实炉内 风煤料配合,保证三次风 旋流效应和缺氧燃烧才是 预防结皮的关键
水泥窑炉空气分级燃烧及SNCR烟气脱硝技术
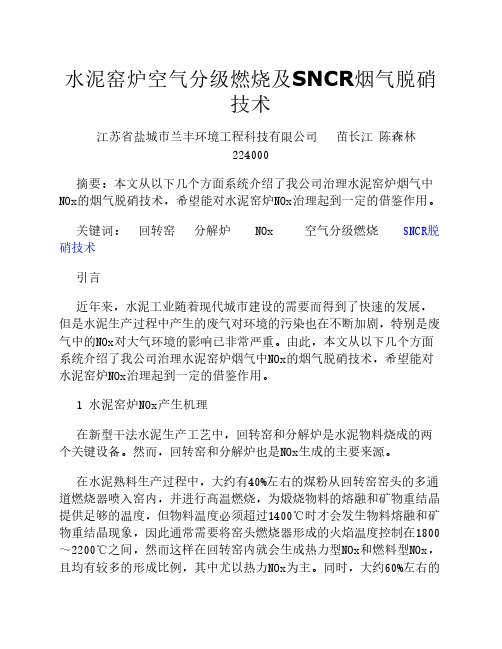
水泥窑炉空气分级燃烧及SNCR烟气脱硝技术江苏省盐城市兰丰环境工程科技有限公司 苗长江 陈森林224000摘要:本文从以下几个方面系统介绍了我公司治理水泥窑炉烟气中NOx的烟气脱硝技术,希望能对水泥窑炉NOx治理起到一定的借鉴作用。
关键词: 回转窑 分解炉 NOx 空气分级燃烧 SNCR脱硝技术引言近年来,水泥工业随着现代城市建设的需要而得到了快速的发展,但是水泥生产过程中产生的废气对环境的污染也在不断加剧,特别是废气中的NOx对大气环境的影响已非常严重。
由此,本文从以下几个方面系统介绍了我公司治理水泥窑炉烟气中NOx的烟气脱硝技术,希望能对水泥窑炉NOx治理起到一定的借鉴作用。
1 水泥窑炉NOx产生机理在新型干法水泥生产工艺中,回转窑和分解炉是水泥物料烧成的两个关键设备。
然而,回转窑和分解炉也是NOx生成的主要来源。
在水泥熟料生产过程中,大约有40%左右的煤粉从回转窑窑头的多通道燃烧器喷入窑内,并进行高温燃烧,为煅烧物料的熔融和矿物重结晶提供足够的温度,但物料温度必须超过1400℃时才会发生物料熔融和矿物重结晶现象,因此通常需要将窑头燃烧器形成的火焰温度控制在1800~2200℃之间,然而这样在回转窑内就会生成热力型NOx和燃料型NOx,且均有较多的形成比例,其中尤以热力NOx为主。
同时,大约60%左右的煤粉进入分解炉,炉内的温度一般在850~1100℃范围内,在此温度下,基本可以不考虑热力型NOx的形成,主要是燃料型NOx。
由此,本文系统介绍了我公司治理水泥窑炉烟气中NOx的空气分级燃烧及SNCR脱硝技术,希望能对水泥窑炉NOx治理起到一定帮助。
2 水泥窑炉空气分级燃烧技术2.1 基本原理水泥窑炉空气分级燃烧是目前最为普遍的降低NOx排放的燃烧技术之一。
其基本原理如图(一)所示:将燃烧所需的空气量分成两级送入,使第一级燃烧区内过量空气系数小于1,燃料先在缺氧的富燃料条件下燃烧,使得燃烧速度和温度降低,从而降低了热力型NOx的生成。
低氮燃烧炉内脱硝技术介绍

低氮燃烧炉内脱硝技术介绍低NOx燃烧方案NO系列低NOx燃烬风系统是LPAmina公司的核心技术,主要由\030、N050、N070三大方案组成。
低NOx系统基于空气分级原理,通过增加燃烬风系统降低NOx排放量,同时兼顾强化燃烧、进步燃烧效率,防止结渣、高温腐蚀,优化机组性能等。
我们针对不同客户情况,使用相应的燃烧布置方案。
尽可能的保存原结构,保持锅炉运行参数不发生变化,实现改造的有效性和经济性。
低NOx方案的制定以对机组的全面了解和正确分析为条件,它涉及对机组设计、运行的数据的广泛采集和对比验证,方案设计基于公道有效的机组信息,釆用计算流体力学模拟软件,并结合综合模拟试验,对机组改造前后的惜况进行比对,保证改造的有效性,经济性和可靠性。
针对不同锅炉的低NOx解决方案LPAmina根据客户需求提供一系列的低NOx解决方案。
在美国有25%的电厂采用了我们的技术, 应用在四角切圆、墙式燃炉和W火焰等形式的锅炉项U上,机组大小从50MW到1OOOMW。
我们的方案基于对整个燃烧系统的评估,通常会包括燃烧器改造、增加OFA或SOFA等,达到降低NOx,减少结渣,进步锅炉效率的目的。
四角切圆炉解决方案LPAmind提供三种方案帮助客户降低NOx。
N030方案保持原有风箱高度,压缩主燃烧区,尽可能利用原有OFA喷口。
如锅炉没有OFA喷口,就需要改造现有风箱,转移一部分空气到顶部喷口。
主风箱的顶二次风及上层煤粉喷口位置通常被用来安装新的OFA喷口。
在这种悄况下,主要是通过减少主燃烧区的氧气量达到减少燃料型NOx的LI的。
N050方案釆用了火上风(SOFA)技术。
在实验室和实际应用中均已证实:SOFA喷口与主燃烧区域间隔较远,能够很大程度上减少NOx的天生。
N030方案相对简单,由于它的OFA流量小,间隔主燃烧区近,降低NOx的能力有限,而N050方案,间隔增加,风量增加,减少NOx的能力也有较大的进步。
山于SOFA风与主燃烧区域分离,使得主燃烧区处于富燃料状态,这将有利于燃料型NOx 转化成N 2成分。
DD分解炉分级燃烧减排Nox的数值模拟及优化研究的开题报告

DD分解炉分级燃烧减排Nox的数值模拟及优化研究的开题报告1. 研究背景和意义随着环保意识日益提高,减少大气污染已成为各国的共同目标。
其中,NOx的减排至关重要,因为它是造成酸雨、臭氧等大气污染的重要成分之一。
DD分解炉是一种高温炉,用于生产多种金属材料,如钨、钽、铌等。
然而,DD分解炉在生产过程中会排放大量的NOx,给环境带来了严重的污染。
因此,研究DD分解炉的NOx减排技术具有重要的现实意义。
2. 研究目标和内容本研究旨在采用数值模拟方法,对DD分解炉NOx减排技术进行研究。
具体研究内容包括以下几个方面:(1)建立DD分解炉的数值模型,模拟其燃烧过程;(2)分析DD分解炉燃烧过程中NOx生成的机理;(3)探究DD分解炉NOx减排技术,比如SCR技术、SNCR技术等;(4)对减排技术进行数值模拟,优化减排效果。
3. 研究方法和技术路线本研究采用数值模拟方法,主要包括以下步骤:(1)建立DD分解炉的数值模型。
首先,收集DD分解炉的相关参数,如炉体形状、燃料类型、风速、温度等,建立数值模型;(2)模拟DD分解炉的燃烧过程,分析NOx生成的机理。
采用计算流体力学(CFD)方法,对DD分解炉的燃烧过程进行数值模拟,并分析NOx的生成机理;(3)探究DD分解炉的NOx减排技术,比如SCR技术、SNCR技术等。
对于不同的减排技术,分别对其原理、适用范围、优缺点等进行分析和比较;(4)对减排技术进行数值模拟,优化减排效果。
结合实验数据和数值模拟结果,优化减排技术,提高其减排效果。
4. 研究预期结果通过本研究,预计能够实现以下几个方面的结果:(1)建立DD分解炉的数值模型,模拟其燃烧过程;(2)分析DD分解炉燃烧过程中NOx生成的机理;(3)探究DD分解炉NOx减排技术,比如SCR技术、SNCR技术等;(4)对减排技术进行数值模拟,优化减排效果。
最终,本研究将提出有效的DD分解炉NOx减排技术,为解决大气污染问题提供一定的参考和帮助。
分级燃烧降低煤粉炉NOx排放的化学机理及影响因素
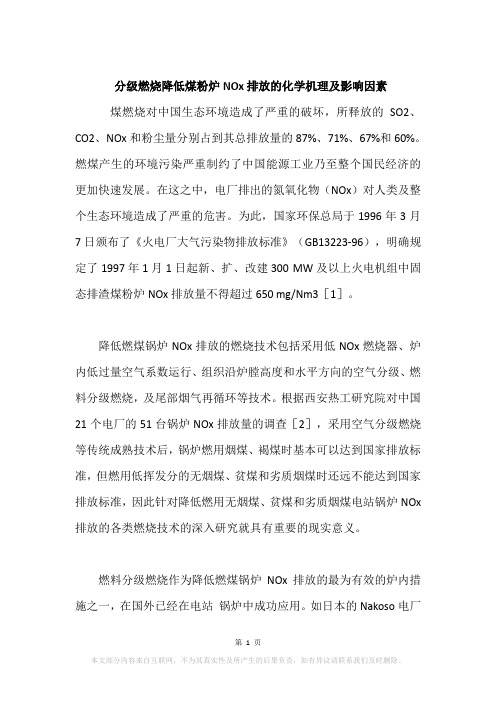
分级燃烧降低煤粉炉NOx排放的化学机理及影响因素煤燃烧对中国生态环境造成了严重的破坏,所释放的SO2、CO2、NOx和粉尘量分别占到其总排放量的87%、71%、67%和60%。
燃煤产生的环境污染严重制约了中国能源工业乃至整个国民经济的更加快速发展。
在这之中,电厂排出的氮氧化物(NOx)对人类及整个生态环境造成了严重的危害。
为此,国家环保总局于1996年3月7日颁布了《火电厂大气污染物排放标准》(GB13223-96),明确规定了1997年1月1日起新、扩、改建300 MW及以上火电机组中固态排渣煤粉炉NOx排放量不得超过650 mg/Nm3[1]。
降低燃煤锅炉NOx排放的燃烧技术包括采用低NOx燃烧器、炉内低过量空气系数运行、组织沿炉膛高度和水平方向的空气分级、燃料分级燃烧,及尾部烟气再循环等技术。
根据西安热工研究院对中国21个电厂的51台锅炉NOx排放量的调查[2],采用空气分级燃烧等传统成熟技术后,锅炉燃用烟煤、褐煤时基本可以达到国家排放标准,但燃用低挥发分的无烟煤、贫煤和劣质烟煤时还远不能达到国家排放标准,因此针对降低燃用无烟煤、贫煤和劣质烟煤电站锅炉NOx 排放的各类燃烧技术的深入研究就具有重要的现实意义。
燃料分级燃烧作为降低燃煤锅炉NOx排放的最为有效的炉内措施之一,在国外已经在电站锅炉中成功应用。
如日本的Nakoso电厂采用燃料分级燃烧后,NOx排放量降为120 mg/Nm 3;在美国的示范工程也取得了令人满意的结果,NOx的还原率为58%~77%。
主要探讨燃料分级燃烧降低NOx的化学反应机理,并对影响燃料分级燃烧降低NOx排放的各因素进行初步对比分析,以有利于进一步利用燃料分级燃烧降低中国燃煤锅炉的NOx排放水平,使大气质量得到改善。
1燃料分级燃烧对降低NOx的化学反应机理1.1燃料分级燃烧降低NOx的基本原理NOx在遇到烃根CHi、未完全燃烧产物CO、C和未完全燃烧中间产物HCN基团、NHi基团时,会被还原为N2。
水泥分解炉低氮燃烧过程数值模拟与优化研究

simulated actual value was 142.4 ppm. The optimization model has a good fit and can be
used for the preliminary analysis and prediction of NO concentration at the outlet of
furnace were simulated via the Fluent software. The effects of raw material angle, tertiary
air velocity and tertiary air temperature on combustion process and NO generation were
绪
论 .................................................................................................................... 1
1.1 研究背景 ................................................................................................................... 1
1.3.1 流场研究进展 .................................................................................................... 3
简析煤粉锅炉降氮脱硝技术选择及应用
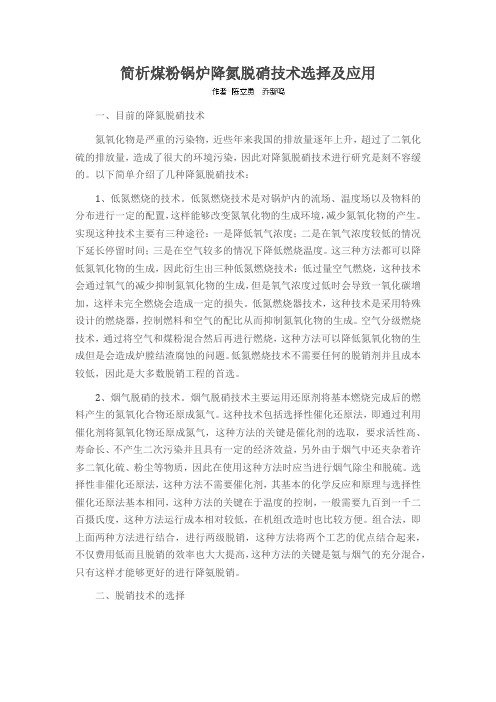
简析煤粉锅炉降氮脱硝技术选择及应用一、目前的降氮脱硝技术氮氧化物是严重的污染物,近些年来我国的排放量逐年上升,超过了二氧化硫的排放量,造成了很大的环境污染,因此对降氮脱硝技术进行研究是刻不容缓的。
以下简单介绍了几种降氮脱硝技术:1、低氮燃烧的技术。
低氮燃烧技术是对锅炉内的流场、温度场以及物料的分布进行一定的配置,这样能够改变氮氧化物的生成环境,减少氮氧化物的产生。
实现这种技术主要有三种途径:一是降低氧气浓度;二是在氧气浓度较低的情况下延长停留时间;三是在空气较多的情况下降低燃烧温度。
这三种方法都可以降低氮氧化物的生成,因此衍生出三种低氮燃烧技术:低过量空气燃烧,这种技术会通过氧气的减少抑制氮氧化物的生成,但是氧气浓度过低时会导致一氧化碳增加,这样未完全燃烧会造成一定的损失。
低氮燃烧器技术,这种技术是采用特殊设计的燃烧器,控制燃料和空气的配比从而抑制氮氧化物的生成。
空气分级燃烧技术,通过将空气和煤粉混合然后再进行燃烧,这种方法可以降低氮氧化物的生成但是会造成炉膛结渣腐蚀的问题。
低氮燃烧技术不需要任何的脱销剂并且成本较低,因此是大多数脱销工程的首选。
2、烟气脱硝的技术。
烟气脱硝技术主要运用还原剂将基本燃烧完成后的燃料产生的氮氧化合物还原成氮气。
这种技术包括选择性催化还原法,即通过利用催化剂将氮氧化物还原成氮气,这种方法的关键是催化剂的选取,要求活性高、寿命长、不产生二次污染并且具有一定的经济效益,另外由于烟气中还夹杂着许多二氧化硫、粉尘等物质,因此在使用这种方法时应当进行烟气除尘和脱硫。
选择性非催化还原法,这种方法不需要催化剂,其基本的化学反应和原理与选择性催化还原法基本相同,这种方法的关键在于温度的控制,一般需要九百到一千二百摄氏度,这种方法运行成本相对较低,在机组改造时也比较方便。
组合法,即上面两种方法进行结合,进行两级脱销,这种方法将两个工艺的优点结合起来,不仅费用低而且脱销的效率也大大提高,这种方法的关键是氨与烟气的充分混合,只有这样才能够更好的进行降氨脱销。
锅炉烟气脱硝技术的研究与应用
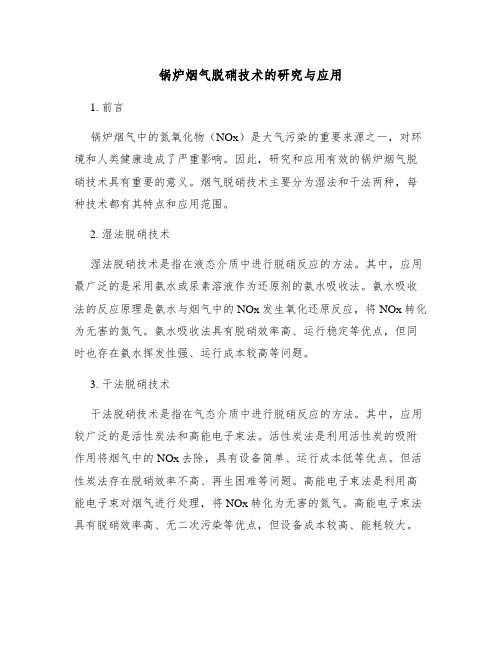
锅炉烟气脱硝技术的研究与应用1. 前言锅炉烟气中的氮氧化物(NOx)是大气污染的重要来源之一,对环境和人类健康造成了严重影响。
因此,研究和应用有效的锅炉烟气脱硝技术具有重要的意义。
烟气脱硝技术主要分为湿法和干法两种,每种技术都有其特点和应用范围。
2. 湿法脱硝技术湿法脱硝技术是指在液态介质中进行脱硝反应的方法。
其中,应用最广泛的是采用氨水或尿素溶液作为还原剂的氨水吸收法。
氨水吸收法的反应原理是氨水与烟气中的NOx发生氧化还原反应,将NOx转化为无害的氮气。
氨水吸收法具有脱硝效率高、运行稳定等优点,但同时也存在氨水挥发性强、运行成本较高等问题。
3. 干法脱硝技术干法脱硝技术是指在气态介质中进行脱硝反应的方法。
其中,应用较广泛的是活性炭法和高能电子束法。
活性炭法是利用活性炭的吸附作用将烟气中的NOx去除,具有设备简单、运行成本低等优点。
但活性炭法存在脱硝效率不高、再生困难等问题。
高能电子束法是利用高能电子束对烟气进行处理,将NOx转化为无害的氮气。
高能电子束法具有脱硝效率高、无二次污染等优点,但设备成本较高、能耗较大。
4. 结论锅炉烟气脱硝技术的研究与应用是为了减少烟气中的氮氧化物排放,保护和改善环境。
湿法脱硝技术中的氨水吸收法具有较高的脱硝效率和运行稳定性,但氨水挥发性和运行成本较高。
干法脱硝技术中的活性炭法设备简单、运行成本低,但脱硝效率不高;高能电子束法脱硝效率高、无二次污染,但设备成本较高、能耗较大。
因此,研究和应用锅炉烟气脱硝技术需要综合考虑脱硝效率、运行成本、设备投资和运行维护等多方面因素,选择适合实际情况的脱硝技术。
5. 先进的脱硝技术除了传统的湿法和干法脱硝技术,近年来还涌现了一些先进的脱硝技术。
其中包括催化剂法和等离子体法。
催化剂法是利用催化剂降低反应活化能,提高脱硝反应的速率和效率。
等离子体法是利用等离子体产生的高能电子和自由基对烟气中的NOx进行分解。
这些先进技术在一定程度上提高了脱硝效率,但多数仍处于实验室研究阶段,尚未大规模应用。
分解炉分级燃烧降氮脱硝技术的研究与应用

分解炉分级燃烧降氮脱硝技术的研究与应用谢胜【摘要】The combination of high temperature combustion technology of low NOx and decomposing furnace system with big cubage has the characteristics, such as the high heat efifciency, equality of decomposing furnace temperature, nitro-gen removal and denitration, low concentration of NOx emission. The paper introduces the application of high temperature&graded combustion technology in cement kiln, focusing on the application principle of graded combustion, nitrogen removal and denitration in decomposing furnace system and popularizing value.%低NOx高温燃烧技术与大容积分解炉系统有机结合,具有热效率高、分解炉温度分布均匀、降氮脱硝、NOx排放浓度低等特点。
文章介绍了高温分级燃烧技术在水泥窑中的应用,重点分析了分级燃烧、降氮脱硝在分解炉系统中的应用原理,以及推广的价值。
【期刊名称】《中国环保产业》【年(卷),期】2013(000)008【总页数】5页(P25-29)【关键词】水泥窑;分解炉;降氮脱硝;分级燃烧;低NOx燃烧技术【作者】谢胜【作者单位】广州市越德企业管理咨询有限公司,广州,510460【正文语种】中文【中图分类】X7011 前言氮氧化物的生成是燃烧反应的一部分:燃烧生成的氮氧化物主要是NO和NO2,统称为NOx。
分级燃烧降低燃煤污染物NO_x的实验研究

分级燃烧降低燃煤污染物NOx的实验研究向 军 苏 胜 胡 松 李培生 孙路石 高 鹏 石金明 孙学信 (华中科技大学煤燃烧国家重点实验室,湖北 武汉 430074) 摘要:采用空气分级和燃料分级方法,在实验室卧室炉上进行了降低燃煤污染物NOx的实验。
实验研究了两种煤在空气分级燃烧和燃料分级燃烧工况下,不同停留时间、燃烧区与还原区不同化学当量比及温度水平等因素对NOx还原性能的影响,获得不同工况下的脱硝效率,实验显示,利用分级燃烧可显著降低NOx排放量,采用空气分级燃烧降低氮氧化物还原率可达25%左右;实验中获得的再燃脱硝效率达到了50%以上,这证明利用气态碳氢燃料降低NOx排放量是切实可行的。
关键词:燃烧学;脱硝;分级燃烧;氮氧化物Experimental Research on Denitration by Using Staged Combustion XIANG Jun SU Sheng HU Song LI Pei-sheng SUN Lu-shi GAO Peng SUN Xue-xin (State Key Laboratory of Coal Combustion, Huazhong University of Science and Technology, Wuhan 430074)Abstract:A staged combustion experiment was carried out on a single-burner furnace to reduce the NOx production. The influence of residence time, combustion region stoichiometries and temperature level were studied on the experiment of staged combustion. The efficiency of NOx reduction has been provided. The results show that the staged combustion can reduce the emission of NOx effectively. The reduction of nitrogen oxide production is a bout 25% by using air staging combustion and 50% by using fuel staged combustion. The result also show that it is viable to reduce NOx emission by using gaseous hydrocarbon fuel.Key words:combustion theory; denitration; staged combustion; nitrogen oxide 近十多年来,有关煤燃烧中NOx的生成特性实验研究与机理分析的文献非常多,关于煤质、燃烧设备结构及燃烧工况对NOx的生成影响的研究也逐渐深化。
低氮分级燃烧技术介绍

低氮分级燃烧技术一.低NO x优化燃烧技术的分类及比较为了实现清洁燃烧,目前降低燃烧中NO、排放污染的技术措施可分为两大类:一类是炉内脱氮,另一类是尾部脱氮。
1.1炉内脱氮炉内脱氮就是采用各种燃烧技术手段来控制燃烧过程中NO x的生成,又称低NO x燃烧技术,下表给出了现有几种典型炉内脱氮技术的比较。
表2技术名称效果优点缺点低氧燃烧根据原来运行条件,最多降低20%投资最少导致飞灰含碳量增加降低投入运行的燃烧器数目15%—30% 投资低,易于锅炉改装有引起炉内腐蚀和结渣的可能,并导致飞灰含碳量增加空气分级燃烧(OFA)最多30% 投资低并不是对所有炉膛都适用,有可能引起炉内腐蚀和结渣,并降低燃烧效率低NO x燃烧器与空气分级燃烧相结合时可达60% 用于新的和改装的锅炉,中等投资,有运行经验结构比常规燃烧器复杂.烟气再循环(FGR)最多20% 能改善混合燃烧,中等投资增加再循环风机,使用不广泛燃料分级(再燃) 达到50% 适用于新的和改造现有锅炉,可减少已形成的NO X,中等投资可能需要增加第二种燃料,可能导致飞灰含碳量增加,运行经验较少1.2尾部脱氮尾部脱氮又称烟气净化技术,即把尾部烟气中已经生成的氮氧化物还原或吸附,从而降低NO x排放。
烟气脱氮的处理方法可分为:催化还原法、液体吸收法和吸附法三大类。
催化还原法是在催化剂作用下,利用还原剂将NO x还原为无害的N2。
这种方法虽然投资和运转费用高,且需消耗氨和燃料,但由于对NO x效率很高,设备紧凑,故在国外得到了广泛应用,催化还原法可分为选择性非催化还原法和选择性催化还原法相比,设备简单、运转资金少,是一种有吸引力的技术。
液体吸收法是用水或者其他溶液吸收烟气中的NO x。
该法工艺简单,能够以硝酸盐等形式回收N进行综合利用,但是吸收效率不高。
吸附法是用吸附剂对烟气中的NO x进行吸附,然后在一定条件下使被吸附的NO x脱附回收,同时吸附剂再生。
此法的NO x脱除率非常高,并且能回收利用。
炉内空气分级燃烧降低氮氧化物的技术应用

炉内空气分级燃烧降低氮氧化物的技术应用氮氧化物的排放量中70%来自于煤炭的直接燃烧,燃烧过程中产生的氮氧化物主要是NO和NO2(被通称为NOx),在绝大多数燃烧方式中,产生的NO占9o%以上,其余为NO2。
目前,控制氮氧化物排放的方法分为两大类:①低NOx燃烧技术--在燃烧过程中控制氮氧化物的生成;②烟气脱硝技术--使生成后的氮氧化物还原。
二、概述燃烧过程生成的NOX主要有热力型、燃料型及快速型3种,其中燃料型NO 占总生成量的60%一80%最高可达90%,热力型NOX在温度足够高时可达20%,快速型NOX占的比例最小。
燃料型NOX是燃料中的含氮化合物在燃烧过程中热分解后氧化而成的。
由于煤中含氮有机化合物的C—N较空气中N≡N的键能小得多更易形成NO。
燃料中的有机氮首先被热分解成HCN、NH3及CN等中间产物随挥发分一起析出,即所谓挥发分N,然后再被氧化成NO。
在通常的燃烧温度1200一l350℃,燃料中70%-90%的氮成为挥发分N,由此形成的N0 占燃料型NO 的60%一80%。
热力型NOX是由空气中的氮气高温氧化而成。
NOX的生成与氧原子的存在成正比,反应速度随温度的升高而加速,当煤粉炉中的温度升至1600℃时,热力型NOX可占到炉内NOX总量的25%一30%,这就是液态排渣炉的NOX比固态排渣炉高的原因。
大唐甘谷发电厂1、2锅炉烟气脱硝采用锅炉尾部布置脱硝装置采用液氨法制备脱硝还原剂,选择性催化还原法(SCR)作为脱硝方式;在脱硝系统设计煤种、锅炉BMCR工况、处理100%烟气量条件下,在入口NOx含量在500mg/Nm3时,设计脱硝总效率大于80%且出口NOx排放浓度小于100mg/Nm3,催化剂层数按2+1设置。
三、原运行方式存在的问题1.我厂采用液氨法制备脱硝还原剂,选择性催化还原法(SCR)作为脱硝方式;在此前正常锅炉运行方式下1号炉脱硝入口当氧化物A、B两侧平均值506.5mg/Nm3在经过尾部脱硝反应器后出口NOx排放浓度71.8mg/Nm3,此种运行方式液氨消耗量较大造成运行成本、运输成本增加。
分解炉梯度燃烧自脱硝技术的研究与工程应用
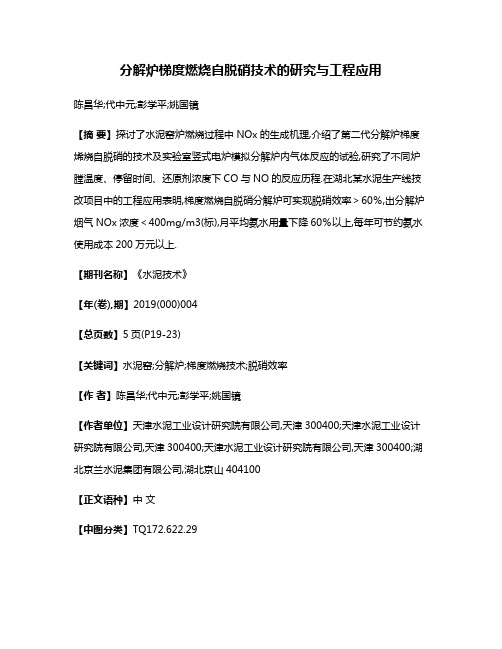
分解炉梯度燃烧自脱硝技术的研究与工程应用陈昌华;代中元;彭学平;姚国镜【摘要】探讨了水泥窑炉燃烧过程中NOx的生成机理,介绍了第二代分解炉梯度烯烧自脱硝的技术及实验室竖式电炉模拟分解炉内气体反应的试验,研究了不同炉膛温度、停留时间、还原剂浓度下CO与NO的反应历程.在湖北某水泥生产线技改项目中的工程应用表明,梯度燃烧自脱硝分解炉可实现脱硝效率>60%,出分解炉烟气NOx浓度<400mg/m3(标),月平均氨水用量下降60%以上,每年可节约氨水使用成本200万元以上.【期刊名称】《水泥技术》【年(卷),期】2019(000)004【总页数】5页(P19-23)【关键词】水泥窑;分解炉;梯度燃烧技术;脱硝效率【作者】陈昌华;代中元;彭学平;姚国镜【作者单位】天津水泥工业设计研究院有限公司,天津300400;天津水泥工业设计研究院有限公司,天津300400;天津水泥工业设计研究院有限公司,天津300400;湖北京兰水泥集团有限公司,湖北京山404100【正文语种】中文【中图分类】TQ172.622.291 引言为加快改善环境空气质量,中央和地方政府相继出台文件,严格控制大气污染物排放指标。
我国各行业大气污染物排放标准愈加严格,其中对水泥窑烟气排放的要求也进一步提升。
由于烟气NOx排放标准越来越严格,水泥厂烟气脱硝系统的氨水消耗量逐渐增多,水泥生产运行成本也随之增加。
工业氨水主要通过氨气水化来制备,而合成氨气的过程中会有大量的能耗,同时产生污染物排放,使用氨水脱硝不仅会增加水泥厂运行成本,也会产生二次污染。
利用水泥窑烧成系统特有的原料和煅烧工艺特点,进行分解炉自脱硝技术开发,降低烟气处置的本底浓度,可以从根本上减少污染物的排放,降低水泥企业的烟气治理成本。
1999年,天津水泥工业设计研究院有限公司率先开展了水泥窑降低NOx排放技术研发工作,并在该技术领域承担了国家“863”重大专项项目《水泥预分解窑系统降低氮氧化物的技术研究》和国家重大产业技术开发专项项目《降低水泥窑氮氧化物排放的关键技术开发》等国家级科研项目。
分级燃烧技术实现NO_(x)超低排放的应用实践

-56-CEM EtiT2021.N〇.2分级燃烧技术实现NO Y超低排放的应用实践蒋文伟\陶从喜\沈序辉\梁乾\何明海\苏军2(丨.平润水泥技术研发(广西)有限公氷广西|有宁530409;2.华润水泥(K治)丫f限公司.山W长治047500)摘要:本文介绍了降低N O,排放浓度的分级燃烧技术—分解炉梯度燃烧自脱硝技术原理,并结合其在5000t/d生产 线上的技术改造、调试及生产运行情况,阐述了应用分解炉梯度燃烧自脱硝的分级燃烧技术,可在不影响窑系统产质 量、煤耗的前提下,较大幅度地降低氨水消耗,并与S N C R系统组合脱硝确保实现NO,:?100mg/Nm3的超低排放要求 关键词:分解炉;梯度燃烧S脱硝;运行调试;N O,超低排放中图分类号:T Q172.622.26文献标识码:B文章编号:1002-9877(2021)02-0056-05DOI:10.13739/ki.c n l l-1899/tq.202丨.02.020〇引言氮氧化物(NO t.)是水泥工业主要的大气污染物,《水泥丁.业大气污染物排放标准》(GB 4915— 2013)规定NOA.的排放限值为400 mg/Nm3(重点地K 320 mg/Nm5)“十二.五”期间火电、钢铁T业全面 实施超低排放改造|l_21,NO,.执行50 mg/Nnr1的超低 排放标准;水泥行业的NO,.排放要求也日益严格,河 北、河南、山东、安徽等多个省市制定了地方标准,要求氮氧化物排放浓度达到彡100 mg/Nm\甚至 50 mg/Nm3的超低排放求随着氮氧化物排放指标的进一步降低,水泥厂 现有的SN CR脱硝系统运行成本激增,而且很难满足 环保控制要求,对水泥生产线进行相关的脱硝技术 改造和升级已成为水泥企业的重要下作。
分解炉梯 度燃烧自脱硝技术是一项改造T.作量少、对生产运 行成本影响小的脱硝技术,采用分解炉梯度燃烧自 脱硝技术,能够较大幅度地降低氮氧化物本底浓度、减少氨水消耗,并且与SN CR脱硝系统结合能够实现 100 mg/Nm3的超低排放要求本文以该技术在某5 000 t/d水泥生产线的应用情况进行相关介绍:1分解炉梯度燃烧自脱硝技术原理分解炉梯度燃烧A脱硝技术由燃料分级燃烧和 三次风分级燃烧组成燃料分级是将原分解炉用煤的一部分均布到分解炉锥部区域,在分解炉锥部空 间形成强贫氧燃烧区,强化C O、CH4、H2、H C N和碳 骸等形成这些具有还原性的化学物质与窑尾烟气中的NO、.发生反应,将其还原成N:三次风分级燃烧 是指将燃烧所需的三次风分成两级送入分解炉,使 第一级过剩空气系数a在0.7〜1.0左右,燃料先在贫氧 条件下燃烧,生成的C O与NO,.进行还原反应,以及燃料氮分解成中间产物(如N H、C N、HCN和NH.,.等)相 互作用或与氮氧化物还原分解,抑制燃料氮氧化物 的生成燃烧所需的剩余三次风(脱硝=次风)进人 二级燃烧区内,形成富氧燃烧fx:,保证燃料的完全燃 烧在富氧燃烧K, 一些中间产物被氧化生成氮氧 化物,但因温度相对常规燃烧较低,氮氧化物生成量 不大,因此,使得总的氮氧化物生成量明显降低13_5]。
水泥窑炉空气分级燃烧及SNCR烟气脱硝技术

水泥窑炉空气分级燃烧及SNCR烟气脱硝技术江苏省盐城市兰丰环境工程科技有限公司苗长江陈森林 224000摘要:本文从以下几个方面系统介绍了我公司治理水泥窑炉烟气中NOx的烟气脱硝技术,希望能对水泥窑炉NOx治理起到一定的借鉴作用。
关键词:回转窑分解炉 NOx 空气分级燃烧 SNCR脱硝技术引言近年来,水泥工业随着现代城市建设的需要而得到了快速的发展,但是水泥生产过程中产生的废气对环境的污染也在不断加剧,特别是废气中的NOx对大气环境的影响已非常严重。
由此,本文从以下几个方面系统介绍了我公司治理水泥窑炉烟气中NOx的烟气脱硝技术,希望能对水泥窑炉NOx治理起到一定的借鉴作用。
1 水泥窑炉NOx产生机理在新型干法水泥生产工艺中,回转窑和分解炉是水泥物料烧成的两个关键设备。
然而,回转窑和分解炉也是NOx生成的主要来源。
在水泥熟料生产过程中,大约有40%左右的煤粉从回转窑窑头的多通道燃烧器喷入窑内,并进行高温燃烧,为煅烧物料的熔融和矿物重结晶提供足够的温度,但物料温度必须超过1400℃时才会发生物料熔融和矿物重结晶现象,因此通常需要将窑头燃烧器形成的火焰温度控制在1800~2200℃之间,然而这样在回转窑内就会生成热力型NOx和燃料型NOx,且均有较多的形成比例,其中尤以热力NOx为主。
同时,大约60%左右的煤粉进入分解炉,炉内的温度一般在850~1100℃范围内,在此温度下,基本可以不考虑热力型NOx的形成,主要是燃料型NOx。
由此,本文系统介绍了我公司治理水泥窑炉烟气中NOx的空气分级燃烧及SNCR脱硝技术,希望能对水泥窑炉NOx治理起到一定帮助。
2 水泥窑炉空气分级燃烧技术2.1 基本原理水泥窑炉空气分级燃烧是目前最为普遍的降低NOx排放的燃烧技术之一。
其基本原理如图(一)所示:将燃烧所需的空气量分成两级送入,使第一级燃烧区内过量空气系数小于1,燃料先在缺氧的富燃料条件下燃烧,使得燃烧速度和温度降低,从而降低了热力型NOx的生成。
关于燃煤锅炉低氮燃烧与脱硝系统优化运行的探讨

关于燃煤锅炉低氮燃烧与脱硝系统优化运行的探讨工程采用的为空气分级燃烧的燃烧技术,这是一种广泛的、性能比较稳定且投资和运行成本较低的低氮燃烧技术,其能够很好完成锅炉的防渣工作,具备更宽的煤种适应性,并能够进一步提升锅炉的运行效率。
由于煤粉炉燃烧温度不超过1500℃,热力型NOx的生成量很少,所以可以忽略氮气的氧化。
燃料型NOx的快速形成主要集中于燃料的着火阶段,这时煤粉热解产生大量的挥发分。
如果氧气充足,它们将迅速生成NO;如果氧气不足,则氮气的形成得到强化,NO的形成受到抑制。
炉内空气分级燃烧就是根据这一原理,通过改变送风方式,控制炉内空气的分布,使煤在着火阶段缺氧,即在燃烧器出口和燃烧中心区域造成还原性气氛,从而降低NOx的生成量,未燃尽的炭粒将在炉膛上部的燃尽区与燃尽风混合并完全燃烧,其中燃尽风由主燃空气分流而来,并通过炉膛上部燃尽风喷口喷入燃尽区。
炉内空气分级燃烧的实现形式主要有两种,即轴向空气分级燃烧和径向空气分级燃烧。
1.4.1 轴向空气分级燃烧(OFA方式)。
将燃烧所需的空气分两部分送入炉膛:一部分为主二次风,约占总二次风量的70%~85%;另一部分为燃尽风(OFA,Over Fire Air),约占总二次风量的15%~30%。
因此,炉膛内的燃烧分成三个区域,即热解区、贫氧区和富氧区(见图1)。
上部燃尽风送入炉膛时,已经避开了高温火焰区,对未燃尽产物起完全燃烧的作用。
1.4.2 径向空气分级燃烧。
径向空气分级燃烧是在与烟气流垂直的炉膛断面上组织分级燃烧,它是通过将二次风射流部分偏向炉墙来实现的(见图2)。
径向分级燃烧不仅可以使主燃区处于还原性气氛从而降低NOx的排放量,还可使炉墙附近处于氧化性气氛,从而可以避免水冷壁的高温腐蚀以及因还原性气氛使灰熔点下降而导致的燃烧器附近的结渣。
对燃烧系统进行整体改造,对燃烧器应采用纵向的布置方式,从下到上分别为下二次风、下一次风、中下二次风、中一次风、中二次风、中上二次风、上一次风、三次风、上二次风、下燃尽风和上燃尽风。