表面粗糙度的成因及其影响因素分析
浅论表面粗糙度及其影响因素

C OCCUPATION2013 0180案例ASES浅论表面粗糙度及其影响因素高瑞兰摘 要:本文简要介绍了表面粗糙度对机械零件使用性能的影响,强调要获得好的工件表面质量,就必须降低表面粗糙度,并简要列举了降低表面粗糙度的几种措施。
关键词:表面粗糙度 工作精度 配合性质 加工参数 切削液表面粗糙度是指零件加工表面具有的较小间距和峰谷所形成的微观几何形状误差。
表面粗糙度越小,零件表面越光滑。
在机械加工过程中,工件表面粗糙度的大小,是衡量工件表面质量的重要标志,对机械零件的使用性能具有很大影响。
一、工件表面粗糙度对机械零件使用性能的影响1.加剧零件的摩擦和磨损机器做功时,许多零件的表面之间存在着相互运动,相互运动将产生摩擦,进而导致磨损。
由于零件表面粗糙度的存在,当两个零件表面接触时,它们的接触面不是整个零件表面,而仅仅是两加工表面上许多突出小峰的顶端,从而导致实际接触面积只是理论面积的一部分,而加剧了零件的磨损。
并且表面越粗糙,接触面积越小,越易磨损,也就是零件的耐磨性越差。
但同时也要注意并不是表面越光滑越好,当表面粗糙度值超过一定值后,会由于表面过于光滑不利于润滑液的储存,且使接触表面之间的分子亲和力增大,甚至发生分子粘合,使摩擦阻力增大,从而进入一个急剧磨损阶段。
2.影响机器和仪器的工作精度工件的粗糙表面易于磨损,使配合间隙增大,从而使运动件灵敏度下降,影响机器和仪器的工作精度。
3.对配合性质造成影响在间隙配合中,如果零件的配合表面粗糙,就会使配合件很快磨损而增大配合间隙,改变配合性质,降低配合精度;在过盈配合中,如果零件的配合表面粗糙,则装配后配合表面的凸峰被挤平,配合件间的有效过盈量减小,降低配合件间的连接强度,从而影响配合的有效性。
4.对零件强度造成影响零件表面越粗糙,对应力集中越敏感,特别是在交变载荷作用下,产生的交变应力在工件表面微观不平度凹谷处易造成应力集中,从而形成细小裂纹,甚至使工件损坏。
关于表面粗糙度对机械零件使用性能的影响分析

关于表面粗糙度对机械零件使用性能的影响分析表面粗糙度是指在工作面上由于加工、磨削、切削等加工工艺所形成的一种微观形貌。
在机械零件中,表面粗糙度对零件的使用性能有着重要的影响。
粗糙度的大小会直接影响零件的摩擦、磨损、疲劳等性能,在工程设计中需要根据零件的实际使用情况来控制和选择合适的表面粗糙度,以确保零件的使用寿命和性能。
一、表面粗糙度的影响因素表面粗糙度是由材料的硬度、强度、加工工艺、刀具磨损等因素共同影响的。
在加工工艺中,切削刀具的尺寸、材料、刀具背角等都会对表面粗糙度产生影响。
在材料的硬度和强度上,材料硬度较高的话,在加工过程中产生的切削屑也就比较难削除,从而产生较大的表面粗糙度。
而加工工艺的参数设置不当也会直接影响到表面粗糙度,如切削速度、进给量、切削深度等都会对表面粗糙度的大小产生重要的影响。
二、表面粗糙度对机械零件使用性能的影响1. 摩擦阻力表面粗糙度的大小对零件摩擦阻力起着直接的影响。
通常来说,表面粗糙度越小,零件的摩擦阻力也就越小,这对于一些需要进行摩擦工作的机械零件来说是非常重要的。
在汽车发动机中的气缸套和活塞环之间的摩擦,要求表面粗糙度尽量小,以减小摩擦阻力,提高发动机的工作效率和性能。
2. 磨损表面粗糙度对机械零件的磨损也有着直接的影响。
通常情况下,表面粗糙度越大,零件的磨损也就越严重。
在机械零件运动过程中,表面粗糙度大会导致零件与零件之间产生过大的磨损,在严重的情况下会导致零件的失效。
对于一些需要长时间运转的机械零件来说,需要通过控制表面粗糙度来控制磨损的程度,延长零件的使用寿命。
3. 疲劳在一些需要长时间进行往复运动的机械零件中,表面粗糙度也会对零件的疲劳性能产生影响。
在往复运动中,表面粗糙度大会导致零件在应力集中区域产生较大的应力集中,从而降低零件的疲劳寿命。
而通过控制表面粗糙度,使零件表面平整度提高,表面裂纹的产生和扩展都得到一定的抑制,进而延长零件的使用寿命。
三、表面粗糙度的有效控制在实际的工程设计中,对于表面粗糙度需要进行有效的控制,以保证零件的使用性能。
表面粗糙度影响的因素及改善措施@
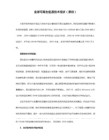
转速越高,单位时间内通过被磨表面的磨粒数越多,表面粗糙度值就越小。工件速度对表面粗糙度值的影响刚好与砂轮转速的影响相反。工件的速度增大,通过加工表面的磨粒数减少,因此表面粗糙度值增大。砂轮的纵向进给量小于砂轮的宽度时,工件表面将被重叠切削,而被磨次数越多,工件表面粗糙度值就越小。为提高磨削效率,通常在开始磨削时采用较大的径向进给量,而在磨削后期采用较小的径向进给量或无进给量磨削,以减小表面粗糙度值。
与切削机理有关的物理因素——刀瘤和鳞刺的影响
切削用量的影响
刀具材料的影响
刀瘤切削过程中切屑底层和前刀面发生冷焊的结果。
鳞刺的产生:切屑在前刀面上的摩擦和冷焊作用造成周期性的停留,代替刀具推挤切削层,造成切削层和工件之间出现撕裂现象。
①工件材料的影响
韧性材料:工件材料韧性愈好,金属塑性变形愈大,加工表面愈粗糙。故对中碳钢和低碳钢材料的工件,为改善切削性能,减小表面粗糙度,常在粗加工或精加工前安排正火或调质处理。 Βιβλιοθήκη 2磨削加工后表面粗糙度的形成
工件的磨削表面是由砂轮上大量磨粒刻划出无数极细的刻痕形成的,工件单位面积上通过的砂粒数越多,则刻痕越多,刻痕的等高性越好,表面粗糙度值越小。磨削速度比一般切削速度高得多,且磨粒大多数是负前角,切削刃又不锐利,大多数磨粒在磨削过程中只是对被加工表面挤压,没有切削作用。加工表面在多次挤压下出现沟槽与隆起,又由于磨削时的高温更加剧了塑性变形,故表面粗糙度值增大。
(4)工件材料太硬易磨粒磨钝→Ra↑太软易堵塞砂轮→Ra↑韧性太大热导率差会使磨粒早崩落→Ra ↑
(1)磨粒在砂轮上的分布越均匀、磨粒越细,刃口的等高性越好。则砂轮单位面积上参加磨削的磨粒越多,磨削表面上的刻痕就越细密均匀,表面粗糙度值就越小。
切削加工表面粗糙度的影响因素以及解决措施
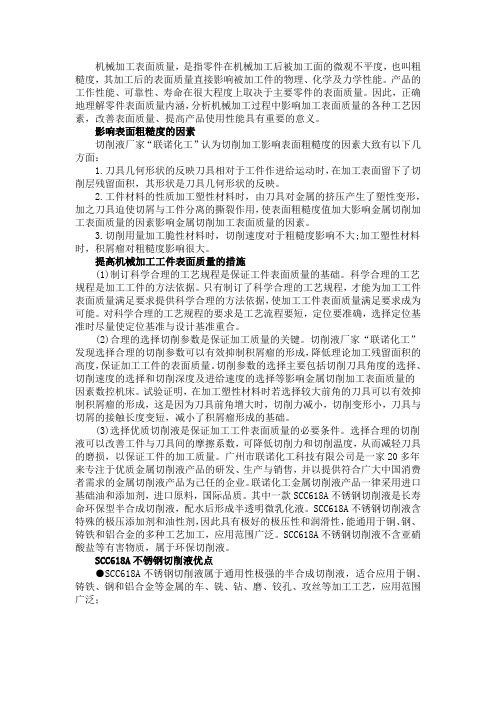
机械加工表面质量,是指零件在机械加工后被加工面的微观不平度,也叫粗糙度,其加工后的表面质量直接影响被加工件的物理、化学及力学性能。
产品的工作性能、可靠性、寿命在很大程度上取决于主要零件的表面质量。
因此,正确地理解零件表面质量内涵,分析机械加工过程中影响加工表面质量的各种工艺因素,改善表面质量、提高产品使用性能具有重要的意义。
影响表面粗糙度的因素切削液厂家“联诺化工”认为切削加工影响表面粗糙度的因素大致有以下几方面:1.刀具几何形状的反映刀具相对于工件作进给运动时,在加工表面留下了切削层残留面积,其形状是刀具几何形状的反映。
2.工件材料的性质加工塑性材料时,由刀具对金属的挤压产生了塑性变形,加之刀具迫使切屑与工件分离的撕裂作用,使表面粗糙度值加大影响金属切削加工表面质量的因素影响金属切削加工表面质量的因素。
3.切削用量加工脆性材料时,切削速度对于粗糙度影响不大;加工塑性材料时,积屑瘤对粗糙度影响很大。
提高机械加工工件表面质量的措施(1)制订科学合理的工艺规程是保证工件表面质量的基础。
科学合理的工艺规程是加工工件的方法依据。
只有制订了科学合理的工艺规程,才能为加工工件表面质量满足要求提供科学合理的方法依据,使加工工件表面质量满足要求成为可能。
对科学合理的工艺规程的要求是工艺流程要短,定位要准确,选择定位基准时尽量使定位基准与设计基准重合。
(2)合理的选择切削参数是保证加工质量的关键。
切削液厂家“联诺化工”发现选择合理的切削参数可以有效抑制积屑瘤的形成,降低理论加工残留面积的高度,保证加工工件的表面质量。
切削参数的选择主要包括切削刀具角度的选择、切削速度的选择和切削深度及进给速度的选择等影响金属切削加工表面质量的因素数控机床。
试验证明,在加工塑性材料时若选择较大前角的刀具可以有效抑制积屑瘤的形成,这是因为刀具前角增大时,切削力减小,切削变形小,刀具与切屑的接触长度变短,减小了积屑瘤形成的基础。
(3)选择优质切削液是保证加工工件表面质量的必要条件。
影响表面粗糙度的因素

.影响表面粗糙度的因素1.切削加工中影响表面粗糙度的因素1)?几何因素2)物理因素切削加工后表面粗糙度的实际轮廓形状一般都与由纯几何因素形成的理想轮廓有较大的差别。
这是由于存在与被加工材料的性质及切削机理有关的物理因素的缘故。
采用低切削速度加工塑性金属材料(如低碳钢、铬钢、不锈钢、高温合金、铝合金等)时,容易出现积屑瘤与鳞刺,使加工表面粗糙度严重恶化,成为影响加工表面质量的主要因素。
刀具与被加工材料的挤压与磨擦使金属材料发生塑性变形,也会增大表面粗糙度。
切削加工中的振动,使工件的表面粗糙度增大。
从物理因素看,降低表面粗糙度的主要措施是减少加工时的塑性变形,避免产生积屑瘤和鳞刺。
其主要影响因素有切削速度、被加工材料的性质、刀具的几何形状、材料性质和刃磨质量。
适当增大刀具的前角,可以降低被切削材料的塑性变形;降低刀具前刀面和后刀面的表面粗糙度可以抑制积屑瘤的生成;增大刀具后角,可以减少刀具和工件的摩擦;合理选择冷却润滑液,可以减少材料的变形和摩擦,降低切削区的温度;采取上述各项措施均有利于减小加工表面的粗糙度。
2.磨削中影响表面粗糙度的因素三.影响加工表面金属层物理力学性能的因素加工过程中,由于切削力和切削热的作用,工件表面金属层的物理力学性能会发生很大的变化,导致表面层金属和基体材料的性能有很大的差异。
其影响因素主要表现为三个方面。
1.表面层金属材料的加工硬化切削(磨削)过程中产生的塑性变形,会使表层金属的晶格发生畸变,晶粒间产生剪切滑移,晶粒被拉长,甚至破碎,从而使表层金属的硬度和强度提高,这种现象称为加工硬化。
加工硬化的程度取决于塑性变形的程度。
影响加工硬化的因素(1)?切削力越大,塑性变形越大,硬化程度也越大。
因此,当进给量、背吃刀量增大,刀具前角减小时,都会因切削力增大而使加工硬化程度增大。
(2)?切削温度越高,会使加工硬化作用减小。
如切削速度增大,会使切削温度升高,加工硬化程度将会减小。
影响磨削表面粗糙度的因素及改善措施

影响磨削表面粗糙度的因素及改善措施
1.磨削条件:
⑴提高砂轮速度ν或降低工件速度νω,使νω/ν的比值减小可获得较小数值的粗糙度
⑵采用较小的纵向进给量f a,减小f a/B的比值,使工件表面上某一点被磨的次数越多,则能获得较低数值的粗糙度
⑶径向进给量f r减小,能按一定比例降低的数值,例如磨削18CrNiW A时,若f r=0.02mm,R a=0.6μm;若f r=0.03mm,R a≈0.75μm。
最后进行5次以上的无进给光磨,可较好地改善表面粗糙度
⑷正确使用切削液的种类、配比、压力、流量和清洁度
⑸提高砂轮的平衡精度、磨床主轴的回转精度、工作台的运动平稳性及整个工艺系统的刚度,消减磨削时的振动,可使表面粗糙度大大改善
2.砂轮特性及修整:
⑴一般地说,砂轮粒度愈细,粗糙度数值就愈小,但超过80#时,则R a值的变化甚微
⑵应选择与工件材料亲和力小的磨料。
例如磨削高速钢时,宜选用白刚玉、单晶刚玉或绿碳化硅;磨削硬质合金时,则宜选用绿碳化硅或碳化硼。
一般地说碳化硅的磨料不适于加工钢材,但适于非铁金属Zn、Pb、Cu和非金属材料。
立方氮化硼为磨削不锈钢、高温合金和钛合金的好磨料
⑶磨具的硬度,工件材料软、粘时,应该选较硬的磨具;工件材料硬、脆时,应该选较软的磨具。
νω/ν愈大则磨具应硬些。
磨削难加工材料应选J~V的硬度
⑷采用直径较大的砂轮,增大砂轮宽度皆可降低表面粗糙度
⑸采用耐磨性好的金刚笔,合适的刃口形状和安装角度,当修整用量合适时(纵向进给量应小些),能使磨粒切削刃获得良好的等高性,降低表面粗糙度。
影响机械加工表面粗糙度

表面粗糙度不行的原因在哪?
影响机械加工表面粗糙度的因素
影响因素很多,主要是几何因素、物理因素和加工中工艺系 统的振动。
1、几何因素:减小进给量f,减小主、副偏角,增大刀尖圆角 半径,都能减小残留面积的高度H,也就减小了零件的表面粗 糙度。
2、物理因素: (1)切削力和摩擦力大,表面粗糙。 (2)积屑瘤的形成严重影响表面粗糙度提高。 (3)切屑在前刀面停留、挤拉、撕裂形成鳞刺导致表面粗糙。 措施:选择合适的切屑速度,改善材料的切削性能,选择正
尖刀切削时
H
f
cotr cotr
带圆角半径的刀切削时
H
f2
8r0
由公式可知,减小进给量f,减小主、副偏角,
增大刀尖圆角半径,都能减小残留面积的高度H,
也就减小了零件的表面粗糙度。
二、影响机械加工表面粗糙的物理因素
⒈切削力和摩擦力的影响
(刀刃圆角及后刀面挤压和摩擦材料,韧性材料材料发生塑性变形,Βιβλιοθήκη 性材料崩碎)00处不为零怎么办
球刀对刀对哪里?
⒉积屑瘤的影响(其形成、长大、脱落严重影响,看图,提高或降低切削速度,切削液,对材料进
行热处理)
⒊鳞刺的影响(切屑在前刀面产生周期停留、挤拉、撕裂,切削速度、切削深度、刀具的前角、工
件的材质和切削液。 )
从物理因素看、必须减少切削力引起的塑性变形,避免积屑瘤和鳞刺。 措施:选择合适的切屑速度,改善材料的切削性能,选择正确的切削液
确的切削液 3、振动使工艺系统的各种成形运动受到干扰和破坏,使加工
表面出现振纹,降低了零件的加工精度和增大表面粗糙度。
第二节 影响机械加工表面粗糙度的因素
影响因素很多,主要是几何因素、物理因素和加工中工艺系统的振动
影响表面粗糙度的因素

影响表面粗糙度的因素表面粗糙度是衡量已加工表面质量的重要标志之一,它对零件的耐磨性、耐腐蚀性、疲劳强度和配合性质都有很大影响。
但是,在加工中表面粗糙度影响因素有很多,为了达到良好的表面粗糙度,我们就来了解一下这些因素有哪些。
影响表面粗糙度的因素一、加工表面粗糙的原因1、残留面积:残留面积是刀具的主、副切削刃切削后,残留在已加工表面上的一些尚未被切去的面积。
2、鳞刺:用高速钢刀具低速或中速切削塑性金属材料时,如低碳钢、中碳钢、不锈钢、铝合金等,常在已加工表面上产生鱼鳞片状的毛刺,称为鳞刺。
出现鳞刺会显著增大已加工表面的表面粗糙度。
3、积屑瘤:在切削过程中,当产生积屑瘤时,其突出的部分能代替切削刃切入工件,在已加工表面上划出深浅不一的沟纹;当积屑瘤脱落时,部分积屑瘤碎片粘附在已加工表面上,形成细小毛刺,造成表面粗糙度增大。
4、振动:在切削加工时,由于工艺系统产生周期性振动,使已加工表面出现条痕或波纹痕迹,使表面粗糙度值明显增大。
二、影响表面粗糙度的因素凡影响残留面积、积屑瘤、鳞刺、振动的因素都影响加工表面粗糙度。
1、切削用量:进给量对残留面积的影响最大。
进给量减小,残留面积减小。
切削塑性金属时,当切削速度很低或很高时,表面粗糙度值较小。
这是因为低速时积屑瘤不易产生;切削速度较高时,塑性变形减小,可消除鳞刺的产生。
在切削脆性材料时,切削速度的影响较小,因为材料变形小,故表面粗糙度值也减小。
2、刀具几何参数:刀具的刀尖圆弧半径、主偏角和副偏角对残留面积和振动有较大的影响。
一般当刀尖圆弧半径增大,主偏角和副偏角减小时,表面粗糙度值小,但如果机床刚度低,刀尖圆弧半径过大或主偏角过小,会由于切削力增大而产生振动,使表面粗糙度值增大。
3、刀具材料:刀具材料不同,刃口圆弧半径的大小和保持锋利的时间是不同的。
高速钢刀具能刃磨得很锋利,但保持的时间较短,所以在低速切削时表面粗糙度值较小。
硬质合金刀具刃磨后刃口圆弧半径较大,在高速度下切削表面粗糙度值较小。
机械加工影响表面粗糙度的因素及应对措施

机械加工影响表面粗糙度的因素及措施!1、机械加工零件表面粗糙度的概述那么为了较好的提高零件的性能就需要减小零件表面粗糙度,其方法是针对影响零件粗糙度的因素而采取相应的措施,这样会取得更好的效果。
2、影响表面粗糙度的因素在零件的加工过程中会使得零件表面形成一定的粗糙程度,这非常不利于零件的正常使用。
影响零件表面粗糙度的因素有刀具几何形状的影响、积削瘤的影响、工件材料的影响、加工条件的影响以及振动的影响,下面将详述影响零件表面粗糙度的因素。
2.1刀具几何形状的影响刀具是用来切割零件的工具,在切割的过程中刀具与零件的接触最为充分,那么刀具对零件的表面粗糙度影响也最大,适当的增加刀具几何形状的前角可以在较大程度上减小零件表面粗糙度,但是过度增加刀具几何形状的前角反而会使得表面粗糙度增加。
这在实际的过程中很难进行控制,容易使得零件的表面粗糙度受到较大的影响。
当前角一定时,后角越大刀具就越锋利,也更加容易进行切割。
适当的增加后角可以减小刀面与零件表面的摩擦和挤压,这样就可以有效的减小零件的表面摩擦度。
但是后角过大时就会发生切削振动,从而使得零件的表面摩擦度增加。
但是适当的后角在实际操作中也很难进行把握,所以在实际的操作中容易使得零件的表面粗糙度增加。
此外刀具的前刀面与后刀面对零件的表面粗糙度也有一定的影响,如果刀具的前刀面和后刀面粗糙值较小,那么零件的表面粗糙度就越小。
因为刀具的前后刀面越光滑就越锋利,在切割的过程中就不容易产生缺口,从而使得零件的表面粗糙度减小。
由此可见刀具的几何形状对于零件表面粗糙度的大小有着非常重要的影响,所以在降低零件表面粗糙度的过程中药着重考虑这个影响因素。
2.2积削瘤的影响积削瘤所指的是在金属切削过程中,会有一些从工件上掉下来的金属冷焊并层积在前刀面上,这样就会形成一个非常坚硬的金属堆积物,这个金属堆积物的硬度是工件硬度的2~3倍,能够代替刀刃进行切削,但是在不断的切削过程中会逐渐掉落,这个金属堆积物所指的就是积削瘤。
机械零件表面质量影响粗糙度的原因

机械零件加工质量中,表面质量是衡量一个机械零件是否合格的重要指标之一。
而表面粗糙度则是衡量表面质量的指标。
粗糙度越高,表面质量越差,越容易造成机械设备的损坏。
那么,在机械零件的加工生产中,主要影响粗糙度的原因都有哪些呢?1、切削加工影响表面粗糙度因素在进行切削加工的时候,表面会留下切削层残留面积,其形状是刀具几何形状的的反应,想要减小残留面积的高度,可以减小进给量、主偏角、副偏角并增大刀尖圆弧半径。
除此之外,适当让刀具的前角增大,可以让塑性变形的程度减少,同时配合使用润滑液、提高刀具刃磨质量,还有助于减小切削时的塑性变形并抑制刀瘤、鳞刺的生成,对于减小表面粗糙度还是有一定帮助的。
2、工件材料的性质对塑性材料进行加工时,刀具会对金属产生挤压作用,出现塑性变形现象,在加上刀具会让切屑与工件产生撕裂作用,让金属的表面粗糙度变大,工件材料韧性越好,金属的塑性变形越大,加工表面就会越粗糙。
对脆性材料进行加工时,会产生碎粒切屑,这会在金属加工表面造成污染,留下麻点,让金属的表面粗糙度变大。
3、磨削加工影响表面粗糙度的因素磨削加工表面粗糙度的形成过程与切削加工表面粗糙度形成过程一样。
磨削加工表面粗糙度的形成,也是因为几何因素与表面金属的塑性变形来决定的。
影响磨削表面粗糙的主要因素有:(1)磨削加工中砂轮的粒度与硬度砂轮硬度的选择要根据产品表面精度要求来决定,应让磨粒钝化后及时脱落,露出新的磨粒后继续磨削。
砂轮粒度越细,单位面积上磨粒数越多。
(2)砂轮的修整由于磨削加工中,砂轮在磨削过程中会出现钝化,所以对砂轮应该进行及时修整,确保砂轮的微刃性和等高性。
(3)工件材质工件材料的硬度、塑性、韧性和导热性,对于表面粗糙度都会有一定的影响,工件硬度高,磨粒易钝化。
工件硬度低,砂轮容易阻塞,这些都会造成表面粗糙度增高。
磨削加工时,影响工件表面粗糙度的因素
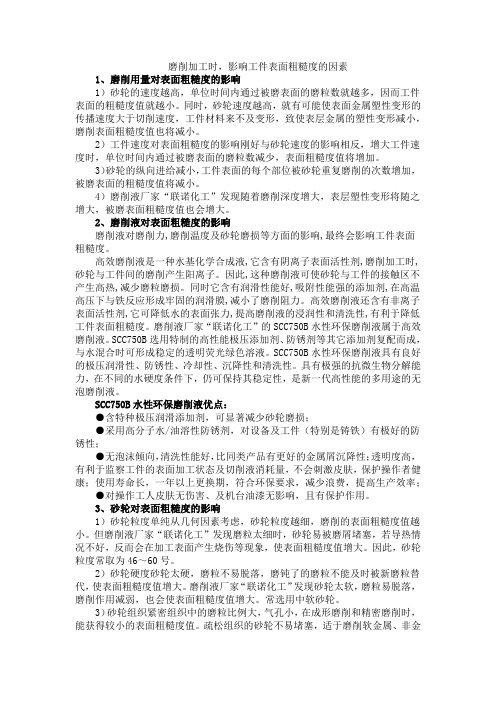
磨削加工时,影响工件表面粗糙度的因素1、磨削用量对表面粗糙度的影响1)砂轮的速度越高,单位时间内通过被磨表面的磨粒数就越多,因而工件表面的粗糙度值就越小。
同时,砂轮速度越高,就有可能使表面金属塑性变形的传播速度大于切削速度,工件材料来不及变形,致使表层金属的塑性变形减小,磨削表面粗糙度值也将减小。
2)工件速度对表面粗糙度的影响刚好与砂轮速度的影响相反,增大工件速度时,单位时间内通过被磨表面的磨粒数减少,表面粗糙度值将增加。
3)砂轮的纵向进给减小,工件表面的每个部位被砂轮重复磨削的次数增加,被磨表面的粗糙度值将减小。
4)磨削液厂家“联诺化工”发现随着磨削深度增大,表层塑性变形将随之增大,被磨表面粗糙度值也会增大。
2、磨削液对表面粗糙度的影响磨削液对磨削力,磨削温度及砂轮磨损等方面的影响,最终会影响工件表面粗糙度。
高效磨削液是一种水基化学合成液,它含有阴离子表面活性剂,磨削加工时,砂轮与工件间的磨削产生阳离子。
因此,这种磨削液可使砂轮与工件的接触区不产生高热,减少磨粒磨损。
同时它含有润滑性能好,吸附性能强的添加剂,在高温高压下与铁反应形成牢固的润滑膜,减小了磨削阻力。
高效磨削液还含有非离子表面活性剂,它可降低水的表面张力,提高磨削液的浸润性和清洗性,有利于降低工件表面粗糙度。
磨削液厂家“联诺化工”的SCC750B水性环保磨削液属于高效磨削液。
SCC750B选用特制的高性能极压添加剂、防锈剂等其它添加剂复配而成,与水混合时可形成稳定的透明荧光绿色溶液。
SCC750B水性环保磨削液具有良好的极压润滑性、防锈性、冷却性、沉降性和清洗性。
具有极强的抗微生物分解能力,在不同的水硬度条件下,仍可保持其稳定性,是新一代高性能的多用途的无泡磨削液。
SCC750B水性环保磨削液优点:●含特种极压润滑添加剂,可显著减少砂轮磨损;●采用高分子水/油溶性防锈剂,对设备及工件(特别是铸铁)有极好的防锈性;●无泡沫倾向,清洗性能好,比同类产品有更好的金属屑沉降性;透明度高,有利于监察工件的表面加工状态及切削液消耗量,不会刺激皮肤,保护操作者健康;使用寿命长,一年以上更换期,符合环保要求,减少浪费,提高生产效率;●对操作工人皮肤无伤害、及机台油漆无影响,且有保护作用。
影响表面粗糙度的因素

一.影响表面粗糙度的因素:(1)工件刚性差,加工表面粗糙度增大。
(2)刀具前角o γ为小值时,塑性变形增大,表面粗糙度也将增大。
过小的后角o α将增大摩擦,表面粗糙度也将增大。
刃倾角s λ为负,加工表面的表面粗糙度增大。
刀具材料软和刃磨质量差,刀具磨损,加工表面粗糙度增大。
(3)切削用量的影响1)切削塑性材料时,切削速度v 在一定的速度范围内(20~80m/min )易产生积屑瘤和鳞刺。
2)进给量f 大,加大了表面粗糙度值,或f 过小会增加刀具与工件表面的挤压次数,使塑性变形增大,反而加大了表面粗糙度值。
3)背吃刀量p α过小或大 ,在精密加工中加大了表面粗糙度值。
二.有锥度 : 车刀明显磨损,车刀松动,车刀架松动,尾座轴线与主轴轴线偏移三.圆度超差,圆柱度超差:主轴径向跳动大,刀具移动方向与主轴不平行,车刀磨损由于刀杆刚性差,产生“让刀”而使内孔成为锥孔,这时需降低切削用量重新镗孔。
镗孔刀磨损严重时,也会产生锥孔,这时需重磨车刀后再进行镗孔。
四.表面不光洁,有明显波纹或表面粗糙,有切痕,拉毛现象:①进给量过大;②铣削进给时,中途停顿,产生“深啃”;③铣刀安装不好,跳动过大,使铣削不平稳;④铣刀不锋利、已磨损五.平面不平整,出现凹下和凸起:①机床精度差或调整不当,②端铣时主轴与进给方向不垂直;③圆柱铣刀圆柱度不好六.槽的宽度尺寸不对:①键槽铣刀装夹不好,与主轴的同轴度差②铣刀已磨损③刀轴弯曲,铣刀摆差大七.槽底与工件轴线不平行:①工件装夹位置不准确,工件轴心线与工作台面不平行② 铣刀装夹不牢或铣削用量过大时,使铣刀被铣削力拉下八.键槽对称性不好:对刀不仔细,使偏差过大九.封闭槽的长度尺寸不对:①工作台自动进给关闭不及时②纵向工作台移动距离不对十.磨外圆断面不圆:①中心孔不圆,孔内有异物,两中心孔轴线不一致,顶尖与中心孔锥角不一致,顶尖未顶紧等;②用卡盘装夹工件时,头架主轴径向跳动太大;③砂轮主轴与轴承间间隙过大;④磨前工件断面不圆,而且工件刚性又差;⑤工件不平衡时,离心力作用,使较重的一边磨去多;⑥工件热处理后还存在部分内应力,磨削后内应力重新平衡而产生变形十一。
切削加工时表面粗糙度形成的原因及其影响因素

切削过程中如果有振动,表面粗糙度就会显著变大。振动是由于径向切削力Fr太大,或工件系统的的刚度小而引起的。
其他因素
副切削刃对残留面积的挤压,使残留面积向与进给相反方向变形,使残留面积顶部歪斜而产生毛刺,加大了表面粗糙度。过渡刃圆弧部分的切削厚度是变化的,近刀尖处的切削厚度很小。当进给量小于一定限度后,这部分的切削厚度小于刃口圆弧所能切下的最小厚度时,就有部分金属未能切除,就会使表面粗糙度增大。切削脆性材料时,产生崩碎切屑,切屑崩碎时的裂缝深人到已加工表面之下,使粗糙度增大。此外,排屑状况、机床设备的精度和刚度等,也会影响已加工表面的表面粗糙度。
工艺系ቤተ መጻሕፍቲ ባይዱ的精度和刚度
加工后的表面粗糙度要低,必须有高运动精度的机床和高刚度的工艺系统,有较强的抗振性,否则即使有很好的刀具,选择最佳的切削用量也很难获得高质量的加工表面。
3 降低表面粗糙度的措施
如果已加工表面的走刀痕迹比较清楚,说明影响表面粗糙度的主要因素是几何因素,就应该首先考虑减小残留面积高度。减小残留面积高度的方法,首先是改变刀具的几何参数,增大刀尖圆弧半径re和减小副偏角k'r。采用带有k'r=0的修光刃的刀具或宽刃精刨刀、精车刀是生产中降低加工表面粗糙度所采用的方法。不论是增大re、减小k'r,或用宽刃刀都要注意避免振动。减小进给量f,也能有效地减小残留面积高度,但减小进给量f会降低生产率,所以只有在改变刀具的几何参数后会引起振动或其它不良影响时才考虑减小进给量f。
当re→0时,残留面积是由主、副2条直线切削刃构成。此时 Rz= f ×1000
cotkr+k'r
刀具切削刃的粗糙度由于直接复映在加工表面上,所以刀具切削刃的粗糙度值,应低于加工表面要求的粗糙度值。
表面粗糙度及其影响因素
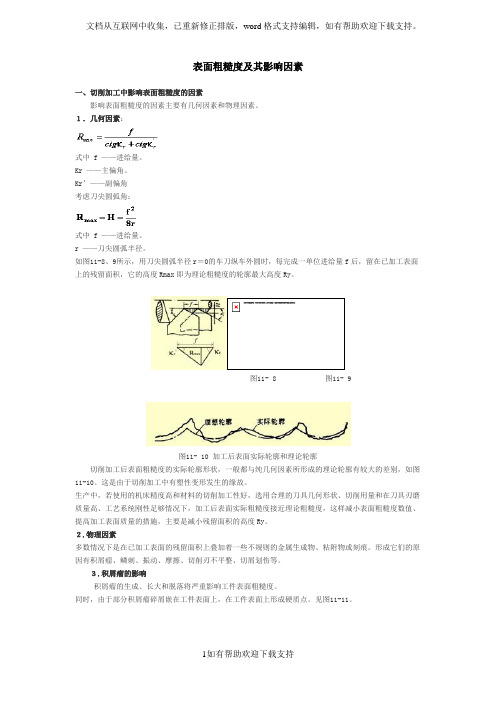
表面粗糙度及其影响因素一、切削加工中影响表面粗糙度的因素影响表面粗糙度的因素主要有几何因素和物理因素。
1.几何因素:式中 f ——进给量。
Kr ——主偏角。
Kr’——副偏角考虑刀尖圆弧角:式中 f ——进给量。
r ——刀尖圆弧半径。
如图11-8、9所示,用刀尖圆弧半径r=0的车刀纵车外圆时,每完成一单位进给量f后,留在已加工表面上的残留面积,它的高度Rmax即为理论粗糙度的轮廓最大高度Ry。
图11- 8 图11- 9图11- 10 加工后表面实际轮廓和理论轮廓切削加工后表面粗糙度的实际轮廓形状,一般都与纯几何因素所形成的理论轮廓有较大的差别,如图11-10。
这是由于切削加工中有塑性变形发生的缘故。
生产中,若使用的机床精度高和材料的切削加工性好,选用合理的刀具几何形状、切削用量和在刀具刃磨质量高、工艺系统刚性足够情况下,加工后表面实际粗糙度接近理论粗糙度,这样减小表面粗糙度数值、提高加工表面质量的措施,主要是减小残留面积的高度Ry。
2.物理因素多数情况下是在已加工表面的残留面积上叠加着一些不规则的金属生成物、粘附物或刻痕。
形成它们的原因有积屑瘤、鳞刺、振动、摩擦、切削刃不平整、切屑划伤等。
3.积屑瘤的影响积屑瘤的生成、长大和脱落将严重影响工件表面粗糙度。
同时,由于部分积屑瘤碎屑嵌在工件表面上,在工件表面上形成硬质点。
见图11-11。
图11- 11 图11- 12鳞刺的影响鳞刺的出现,使已加工表面更为粗糙不平。
鳞刺的形成分为:抹拭阶段:前一鳞刺已经形成,新鳞刺还未出现;而切屑沿着前刀面流出,切屑以刚切离的新鲜表面抹拭刀——屑摩擦面,将摩擦面上有润滑作用的吸附膜逐渐拭净,以致摩擦系数逐渐增大,并使刀具和切屑实际接触面积增大,为这两相摩擦材料的冷焊创造条件,如图11-12(a)。
导裂阶段:由于在第一阶段里,切屑将前刀面上的摩擦面抹拭干净,而前刀面与切屑之间又有巨大的压力作用着,于是切屑与刀具就发生冷焊现象,切屑便停留在前刀面上,暂时不再沿前刀面流出。
机械加工中影响表面粗糙度的因素及解决方法(附:进给量与粗糙度换算表)
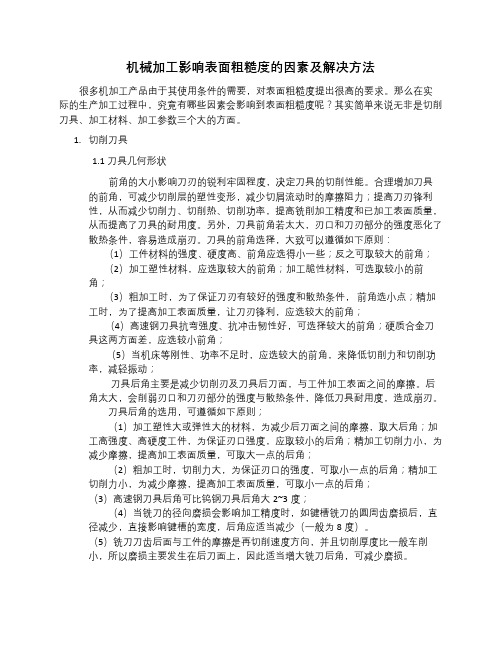
机械加工影响表面粗糙度的因素及解决方法很多机加工产品由于其使用条件的需要,对表面粗糙度提出很高的要求。
那么在实际的生产加工过程中,究竟有哪些因素会影响到表面粗糙度呢?其实简单来说无非是切削刀具、加工材料、加工参数三个大的方面。
1.切削刀具1.1刀具几何形状前角的大小影响刀刃的锐利牢固程度,决定刀具的切削性能。
合理增加刀具的前角,可减少切削层的塑性变形,减少切屑流动时的摩擦阻力;提高刀刃锋利性,从而减少切削力、切削热、切削功率,提高铣削加工精度和已加工表面质量,从而提高了刀具的耐用度。
另外,刀具前角若太大,刃口和刀刃部分的强度恶化了散热条件,容易造成崩刃。
刀具的前角选择,大致可以遵循如下原则:(1)工件材料的强度、硬度高、前角应选得小一些;反之可取较大的前角;(2)加工塑性材料,应选取较大的前角;加工脆性材料,可选取较小的前角;(3)粗加工时,为了保证刀刃有较好的强度和散热条件,前角选小点;精加工时,为了提高加工表面质量,让刀刃锋利,应选较大的前角;(4)高速钢刀具抗弯强度、抗冲击韧性好,可选择较大的前角;硬质合金刀具这两方面差,应选较小前角;(5)当机床等刚性、功率不足时,应选较大的前角,来降低切削力和切削功率,减轻振动;刀具后角主要是减少切削刃及刀具后刀面,与工件加工表面之间的摩擦。
后角太大,会削弱刃口和刀刃部分的强度与散热条件,降低刀具耐用度,造成崩刃。
刀具后角的选用,可遵循如下原则;(1)加工塑性大或弹性大的材料,为减少后刀面之间的摩擦,取大后角;加工高强度、高硬度工件,为保证刃口强度,应取较小的后角;精加工切削力小,为减少摩擦,提高加工表面质量,可取大一点的后角;(2)粗加工时,切削力大,为保证刃口的强度,可取小一点的后角;精加工切削力小,为减少摩擦,提高加工表面质量,可取小一点的后角;(3)高速钢刀具后角可比钨钢刀具后角大2~3度;(4)当铣刀的径向磨损会影响加工精度时,如键槽铣刀的圆周齿磨损后,直径减少,直接影响键槽的宽度,后角应适当减少(一般为8度)。
表面粗糙度的成因及其影响因素分析
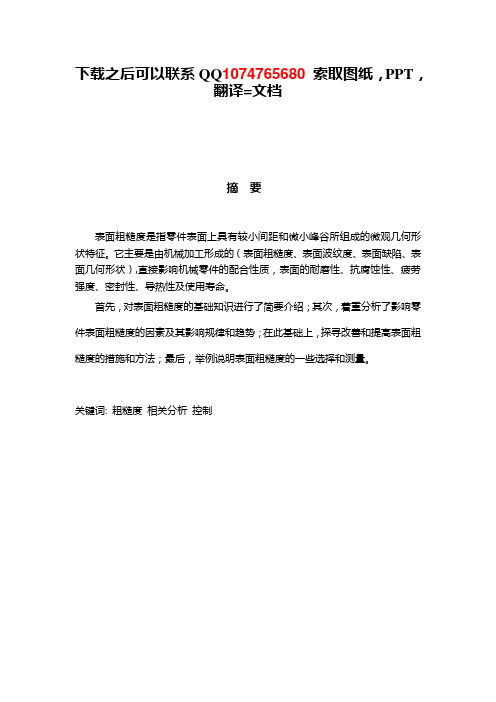
下载之后可以联系QQ1074765680索取图纸,PPT,翻译=文档摘要表面粗糙度是指零件表面上具有较小间距和微小峰谷所组成的微观几何形状特征。
它主要是由机械加工形成的(表面粗糙度、表面波纹度、表面缺陷、表面几何形状),直接影响机械零件的配合性质,表面的耐磨性、抗腐蚀性、疲劳强度、密封性、导热性及使用寿命。
首先,对表面粗糙度的基础知识进行了简要介绍;其次,着重分析了影响零件表面粗糙度的因素及其影响规律和趋势;在此基础上,探寻改善和提高表面粗糙度的措施和方法;最后,举例说明表面粗糙度的一些选择和测量。
关键词: 粗糙度相关分析控制Analysis of formation mechanism of surface roughness and it’sinfluence factorAbstractSurface roughness is the distance between the surface and has a smaller peak which consists of tiny micro-geometry characteristics. It is mainly formed by machining (surface roughness, surface waviness, surface defects, surface geometry), a direct impact on the nature of mechanical components with the surface of the wear resistance, corrosion resistance, fatigue strength, tightness, thermal conductivity and useful life.First, the basics of surface roughness have been briefed; Secondly, the focus on an analysis of the impact of parts of the surface roughness factors, and impact of laws and trends; On this basis, ways to improve and enhance the surface roughness of the measures and methods ; Finally, examples of surface roughness and measurement of the number of options.Keywords : Roughness, Relation Analysis, Control1目录1 绪论 (21)1.1表面粗糙度概述 (21)1.1.1表面粗糙度概念 (21)1.1.2表面粗糙度产生原因 (21)1.2表面粗糙度国内外研究现状 (21)1.3表面粗糙度研究的目的及意义 (22)2 表面粗糙度的影响因素分析 (22)2.1表面粗糙度的标准 (22)2.2表面粗糙度的因素 (23)2.2.1 刀具方面 (23)2.2.2切削条件 (24)2.3表面粗糙度的选择原则 (25)3 表面粗糙度的成因及其改善措施 (28)3.1控制目的 (28)3.2切削加工时表面粗糙度的成因与控制 (28)3.2.1形成原因 (28)3.2.2 控制措施 (31)4 结论 (33)谢辞 (34)参考文献 (35)21 绪论1.1表面粗糙度概述1.1.1表面粗糙度概念表面粗糙度[1]是指零件表面上具有较小间距和微小峰谷所组成的微观几何形状特征。
表面粗糙度的形成及控制探讨

表面粗糙度的形成及控制探讨文/许桂珍零件表面粗糙度是研究领域中最富有活力、对未来经济和社会发展有着十分重要影响的研究对象。
本文介绍表面粗糙度的基础知识,着重分析影响零件表面粗糙度的因素及其影响规律和趋势,并在此基础上,探寻改善表面粗糙度的措施和方法。
一、表面粗糙度的概念及形成原因表面粗糙度是指零件表面上具有较小间距和微小峰谷所组成的微观几何形状特征,它主要是由机械加工(表面粗糙度、表面波纹度、表面缺陷、表面几何形状)形成的,直接影响机械零件的配合性质,表面的耐磨性、抗腐蚀性、疲劳强度、密封性、导热性及使用寿命。
因此,表面粗糙度是评定机器和机械零件量的重要指标之一,是机械零件的加工和验收过程中一项必不可少的质量标准。
在加工过程中,刀具与制件表面之间的摩擦、切削或压制时的塑性变形以及工艺系统中高频振动等因素的作用,会使被加工表面产生微观几何变形。
二、表面粗糙度的影响因素1.表面粗糙度的标准GB/T1031—1995《表面粗糙度参数及其数值》规定,表面粗糙度参数首先从三项高度参数——轮廓算术平均偏差Ra、微观不平度十点高度Rz 和轮廓最大高度Ry中选取。
2.影响表面粗糙度的因素(1)刀具。
①刀具几何参数。
刀具几何参数中对表面粗糙度影响最大的是刀尖圆弧半径、副偏角和修光刃。
刀尖圆弧半径对表面粗糙度有很大影响:半径增大时,残留面积减小,另一方面,变形将增加。
副偏角越小,表面粗糙度越低,,减小副偏角,必须视机床系统的刚度而定。
②刀具的刃磨质量。
刀刃前、后刀面,切削刃本身的粗糙度直接影响被加工面的粗糙度。
一般来说,刀刃前、后刀面的粗糙度比加工面要求的粗糙度小l~2级。
③刀具的材料。
刀具材料与被加工材料金属分子的亲和力大时,被加工材料容易与刀具生成黏结积屑瘤和鳞刺,被黏结在刀刃上的金属与被加工表面分离时还会形成附加的粗糙度。
因此凡是黏结情况严重或摩擦严重的,表面粗糙度都大;反之,如果黏结和摩擦不严重的,表面粗糙度都小。
- 1、下载文档前请自行甄别文档内容的完整性,平台不提供额外的编辑、内容补充、找答案等附加服务。
- 2、"仅部分预览"的文档,不可在线预览部分如存在完整性等问题,可反馈申请退款(可完整预览的文档不适用该条件!)。
- 3、如文档侵犯您的权益,请联系客服反馈,我们会尽快为您处理(人工客服工作时间:9:00-18:30)。
下载之后可以联系QQ1074765680索取图纸,PPT,翻译=文档摘要表面粗糙度是指零件表面上具有较小间距和微小峰谷所组成的微观几何形状特征。
它主要是由机械加工形成的(表面粗糙度、表面波纹度、表面缺陷、表面几何形状),直接影响机械零件的配合性质,表面的耐磨性、抗腐蚀性、疲劳强度、密封性、导热性及使用寿命。
首先,对表面粗糙度的基础知识进行了简要介绍;其次,着重分析了影响零件表面粗糙度的因素及其影响规律和趋势;在此基础上,探寻改善和提高表面粗糙度的措施和方法;最后,举例说明表面粗糙度的一些选择和测量。
关键词: 粗糙度相关分析控制Analysis of formation mechanism of surface roughness and it’sinfluence factorAbstractSurface roughness is the distance between the surface and has a smaller peak which consists of tiny micro-geometry characteristics. It is mainly formed by machining (surface roughness, surface waviness, surface defects, surface geometry), a direct impact on the nature of mechanical components with the surface of the wear resistance, corrosion resistance, fatigue strength, tightness, thermal conductivity and useful life.First, the basics of surface roughness have been briefed; Secondly, the focus on an analysis of the impact of parts of the surface roughness factors, and impact of laws and trends; On this basis, ways to improve and enhance the surface roughness of the measures and methods ; Finally, examples of surface roughness and measurement of the number of options.Keywords : Roughness, Relation Analysis, Control1目录1 绪论 (21)1.1表面粗糙度概述 (21)1.1.1表面粗糙度概念 (21)1.1.2表面粗糙度产生原因 (21)1.2表面粗糙度国内外研究现状 (21)1.3表面粗糙度研究的目的及意义 (22)2 表面粗糙度的影响因素分析 (22)2.1表面粗糙度的标准 (22)2.2表面粗糙度的因素 (23)2.2.1 刀具方面 (23)2.2.2切削条件 (24)2.3表面粗糙度的选择原则 (25)3 表面粗糙度的成因及其改善措施 (28)3.1控制目的 (28)3.2切削加工时表面粗糙度的成因与控制 (28)3.2.1形成原因 (28)3.2.2 控制措施 (31)4 结论 (33)谢辞 (34)参考文献 (35)21 绪论1.1表面粗糙度概述1.1.1表面粗糙度概念表面粗糙度[1]是指零件表面上具有较小间距和微小峰谷所组成的微观几何形状特征。
它主要是由机械加工形成的(表面粗糙度、表面波纹度、表面缺陷、表面几何形状),直接影响机械零件的配合性质,表面的耐磨性、抗腐蚀性、疲劳强度、密封性、导热性及使用寿命。
[2]因此,表面粗糙度是评定机器和机械零件量的重要指标之一,是机械零件的生产、加工和验收过程中一项必不可少的质量标准。
1.1.2表面粗糙度产生原因在加工过程中,由于刀具与制件表面之间的摩擦、切削或压制时的塑性变形,以及工艺系统中高频振动等因素的作用,使被加工表面产生微观几何变形。
[3] 1.2表面粗糙度国内外研究现状从近年来国内外发表的有关粗糙度方面的论文来看,数量成指数地增加.这表明表面粗糙度测量和表征技术的研究一直处于上升趋势,一方面是由于商用仪器(如:STM、AFM和光学扫描干涉仪等)的发展以及计算机运算能力、控制技术的提高;另一方面是由于尖端技术、国防工业和精密工程等对零件的表面质量提出了越来越高的要求。
[4]表面粗糙度的表征参数都是在某一法向截面所截得的轮廓线上进行评定,只反映高度和横向距离之间的关系,属于‘二维’评定.当表面粗糙度在一小面积区域内评定时,还有纵向距离关系,这就属于‘三维’评定.近年来研制了许多三维表面微观形貌测量仪,才使得在局部表面上三维评定表面粗糙度成为可行,而且国际上方兴未艾. [5]最近,国内外在表征和研究表面粗糙度等方面越来越多地使用分形几何理论这一有力的数学工具。
研究表明很多种机加工表面呈现出随机性、多尺度性和自3仿射性,即具有分形的基本特征,因而使用分形几何来研究表面形貌将是合理地、有效地。
确定分形的重要参数有分形维数D和特征长度A,它们可以衡量机加工表面轮廓的不规则性,理论上不随取样长度变化和仪器分辨率变化,并能反映表面形貌本质的特征,能够提供传统的表面粗糙度评定参数(如Ra、Ry、Rz等)所不能提供的信息。
美国TopoMetrix公司生产的扫描探针显微镜(SPM)软件体系中,已将分形维数作为评价表面微观形貌的参数之一。
[6][7][8]随着超光滑表面的粗糙度数值接近纳米级甚至埃级,不同测量方法的测量结果不一致性对表面特征的评价影响越来越大。
为此,美国国家标准和技术研究院制作了一组尺寸范围从29nm一152um的标准台阶高度样块,其‘标准’值取决于本身的实际尺寸.另外还建立了一组高精度标准样块,其尺寸用三种不同的方法校准,如相移干涉显微镜、校准原子力显微镜(C一AFM)和高分辨力的触针式仪器。
如果用这些不同的方法测量台阶高度的精确值,能取得好的一致性,则样块台阶高度将作为精密校准的基准。
[9][10]1.3表面粗糙度研究的目的及意义随着现代化工业生产的不断发展,对产品的质量提出了越来越高的要求.如既要求产品具有长的和没有麻烦的使用寿命,又要利于能源的再利用和环境保护,保证产品的三个阶段.制造—使用—垃圾/再循环,协调发展.各制造商竞相生产具有优势性的零缺陷产品,以增强其市场的竞争能力,对零件表面的物理和几何性能提出了非常苛刻的要求.这就使仪器制造商生产性能更好、更全面,精度更高的检测设备。
在飞速发展的21世纪,信息、生物技术、能源、环境、先进制造技术和国防的高速发展必然会对零件表面粗糙度提出更高的要求,元器件的智能化、小型化、高集成、高密度存储和超快传输等要求材料的尺寸越来越小。
零件表面粗糙度无疑是研究领域中最富有活力、对未来经济和社会发展有着十分重要影响的研究对象。
[11]2表面粗糙度的影响因素分析2.1表面粗糙度的标准为了统一指标、统一方法和统一标准,各国都制定了相应的标准。
我国的表面粗糙度标准制定工作是从50年代开始的,经过几十年的研究发展,已由当初单纯解决图样标准的统一问题开始,逐步完善修订为现在的GB/T 1031《表面粗糙度参数及其数值》、GB/T 131《机械制图表面粗糙度符号、代号及其注法》、GB 3505《表面粗糙度术语表面及其参数》等系列标准,而成为我国重要的工业基础标准之一,并为其他产品标准及相关标准所引用。
GB/T 1031-1995(代替GB41031-83)规定了表面粗糙度的参数和数值系列,GB/T 131-93(代替GB 131-83)又规定了图样上表面粗糙度的标注方法及代号的含义,只要正确使用这些标准,表面粗糙度要求在图样上是十分清楚的。
但是在其他有关标准及一些技术文件中需要对零件作出表面粗糙度要求时,由于标准和技术文件的编写特点,大多采用文字叙述等加以规定。
这些表述如果不正确,会给理解和执行标准带来麻烦,同时影响到标准自身的质量。
[12]目前我国评定表面粗糙度的参数,根据《GB/T1031-1995表面粗糙度参数及其数值》规定,表面粗糙度参数首先从三项高度参数—轮廓算术平均偏差Ra、微观不平度十点高度Rz和轮廓最大高度Ry中选取。
根据表面功能的需要,在高度参数不能满足要求的情况下,可选用轮廓微观不平度的平均间距Sm、轮廓的单峰平均间距S和轮廓支承长度率Tp。
对表面粗糙度有要求的表面须给出高度参数值和评定时的取样长度。
间距参数Sm、S和形状特性参数Tp一般不单独使用,常作为补充参数与高度参数共同控制零件的表面粗糙度。
2.2表面粗糙度的因素2.2.1 刀具方面(1)刀具几何参数刀具几何参数中对表面粗糙度影响最大的是刀尖圆弧半径、副偏角和修光刃。
刀尖圆弧半径对表面粗糙度有很大影响:半径增大时,残留面积减小,另一方面变形将增加。
由于前一种变形影响较大,所以当刀尖圆弧半径增大时,表面粗糙度将降低。
因此在刚度允许的条件下.增大刀尖圆弧半径是降低表面粗糙度的好方法。
副偏角越小,表面粗糙度越低。
但减小副偏角容易引起振动,故减小副偏角,必须视机床系统的刚度而定。
当副偏角达到一定值时,再增大半径,也不会使表面粗糙度值增加。
采用一段长度稍大于进给量的修光刃是降低表面粗糙度的有效措施,利用增加修光刃来消除残留面积是实际加工工件中常常采用的方法。
前角对表面粗糙度没有直接的影响,对抑制积屑瘤和麟刺有利,可使刃口回弧半径减小,所以在中、低速范围内适当增大可有利于减小表面粗糙度。
(2)刀具的刃磨质量刀刃前、后刀面,切削刃本身的粗糙度值直接影响被加工面的粗糙度。
一般来说,刀刃前、后刀面的粗糙度比加工面要求的粗糙度小l一2级。
(3)刀具的材料刀具材料与被加工材料金属分子的亲和力大时,被加工材料容易与刀具而生5成粘结积屑瘤和鳞刺,且被粘结在刀刃上的金属与被加工表面分离时还会形成附加的粗糙度。
因此凡是粘结情况严重或摩擦严重的,表面粗糙度都大;反之如果粘结和摩擦不严重的,表面粗糙度都小。
2.2.2切削条件(1)切削速度加工塑性材料时,切削速度对积屑瘤和麟刺的影响非常显若。
切削速度较低易产生幼刺,低速至中速易形成积屑瘤,粗糙度也大。
避开这个速度区域,表面粗糙度值会减小。
加工脆性材料时.因为一般不会形成积屑瘤和鳞刺,所以切削速度对表面粗糙度无影响。
由此可见,用较高的切削速度,既可提高生产率,同时又可使加工表面粗糙度较小。