常减压蒸馏装置先进控制策略研究与应用
先进控制技术在常减压装置的应用
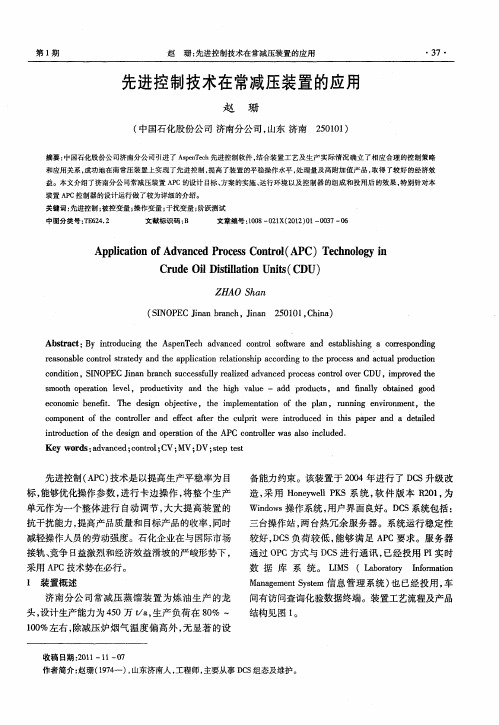
采用 A C技术势在必行。 P
l 装置概 述
数 据 库 系 统 。 LM (Lbr o I o ao IS ao t y n r tn ar fm i M ngm n Ss m信息 管理系统 ) 已经投用 , aae et y e t 也 车 间有访问查询化验数据终端。装置工艺流程及产品
c mp n n f t e c n o lr a d e e t atr t e c l r e e i t d c d i h s p p r a d a d ti d o o e t o o t l n f c fe u p i w r n r u e n t i a e n e al h r e h t o e i t d cin o e d s n p r t n o e AP o t l rwa l n l d d n o u t f e i a d o e a o ft C c nr l sa s i cu e . r o h t n g i h oe o Ke r s a v n e c n r l CV; y wo d : d a c d; o t ; o MV; V ;t p t s D s e t e
s ot prtn l e,pouti ad tehg a e— ad pout,ad f a otnd go m o oeao e l rdcv h i v i  ̄ n h ih vl u d rdc s n nl ba e od i  ̄ i
eoo i b nf .T e d s n ojc v ,te i pe n t n o h ln u nn n i n n ,te cn m c e e t h ei bet e h m l i g i met i fte pa ,rn ig e v omet h ao r
影响常减压蒸馏装置能耗的问题分析与节能对策

影响常减压蒸馏装置能耗的问题分析与节能对策
常减压蒸馏装置是一种高效节能的化工设备,广泛应用于石化、制药、化肥等行业的精馏过程中。
不过,其能耗问题一直是制约其进一步降低成本、提高效率的瓶颈。
首先,常减压蒸馏装置的能耗主要来源于两个方面:一是加热能耗,二是冷却能耗。
加热能耗主要来自于蒸汽加热沸腾液体的能量消耗,而冷却能耗则来自于冷凝物的冷却、回收能量的过程。
其次,常减压蒸馏装置能耗问题的解决需要从多方面入手,具体包括以下几点:
1. 优化加热系统。
通过采用高效的蒸汽加热设备、利用余热回收技术等方式,减少加热能耗。
同时,还可以考虑在提高加热效率的同时,降低操作压力,进一步优化系统。
2. 采用节能型材料。
在设备的建造和改造过程中,选用具有高热传导性能、低热容量的材料,减少传热过程中的能量损失。
3. 优化冷凝系统。
采用先进的冷凝技术,如催化反应冷凝、吸收冷凝等方式,提高冷凝效率,实现能量回收,降低冷却能耗。
此外,还可以考虑采用第二层蒸汽回收技术。
4. 加强操作管理。
合理调整操作参数,减少系统压力损失和能耗浪费,防止系统过于频繁的启停,减少系统能耗。
5. 合理选型。
在选择设备时,尽量选择压力损失小、传热效率高、耗能小的设备,减少系统能耗。
总之,常减压蒸馏装置的能耗问题不仅需要从技术改进入手,还需要加强操作管理、优化选型等多方面努力。
只有全面提升节能意识,实现能源利用的最佳效益,才能进一步提高设备的效率,降低生产成本,为企业发展注入新的动能。
常减压蒸馏装置的节能分析
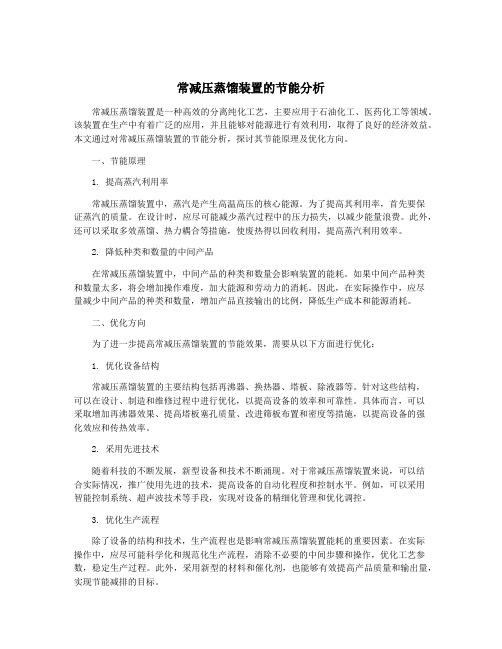
常减压蒸馏装置的节能分析常减压蒸馏装置是一种高效的分离纯化工艺,主要应用于石油化工、医药化工等领域。
该装置在生产中有着广泛的应用,并且能够对能源进行有效利用,取得了良好的经济效益。
本文通过对常减压蒸馏装置的节能分析,探讨其节能原理及优化方向。
一、节能原理1. 提高蒸汽利用率常减压蒸馏装置中,蒸汽是产生高温高压的核心能源。
为了提高其利用率,首先要保证蒸汽的质量。
在设计时,应尽可能减少蒸汽过程中的压力损失,以减少能量浪费。
此外,还可以采取多效蒸馏、热力耦合等措施,使废热得以回收利用,提高蒸汽利用效率。
2. 降低种类和数量的中间产品在常减压蒸馏装置中,中间产品的种类和数量会影响装置的能耗。
如果中间产品种类和数量太多,将会增加操作难度,加大能源和劳动力的消耗。
因此,在实际操作中,应尽量减少中间产品的种类和数量,增加产品直接输出的比例,降低生产成本和能源消耗。
二、优化方向为了进一步提高常减压蒸馏装置的节能效果,需要从以下方面进行优化:1. 优化设备结构常减压蒸馏装置的主要结构包括再沸器、换热器、塔板、除液器等。
针对这些结构,可以在设计、制造和维修过程中进行优化,以提高设备的效率和可靠性。
具体而言,可以采取增加再沸器效果、提高塔板塞孔质量、改进筛板布置和密度等措施,以提高设备的强化效应和传热效率。
2. 采用先进技术随着科技的不断发展,新型设备和技术不断涌现。
对于常减压蒸馏装置来说,可以结合实际情况,推广使用先进的技术,提高设备的自动化程度和控制水平。
例如,可以采用智能控制系统、超声波技术等手段,实现对设备的精细化管理和优化调控。
3. 优化生产流程除了设备的结构和技术,生产流程也是影响常减压蒸馏装置能耗的重要因素。
在实际操作中,应尽可能科学化和规范化生产流程,消除不必要的中间步骤和操作,优化工艺参数,稳定生产过程。
此外,采用新型的材料和催化剂,也能够有效提高产品质量和输出量,实现节能减排的目标。
三、结论综上所述,常减压蒸馏装置具有一定的节能优势,可以通过提高蒸汽利用率和降低中间产品种类和数量来实现节能减排的目标。
常减压蒸馏装置先进控制策略研究与应用
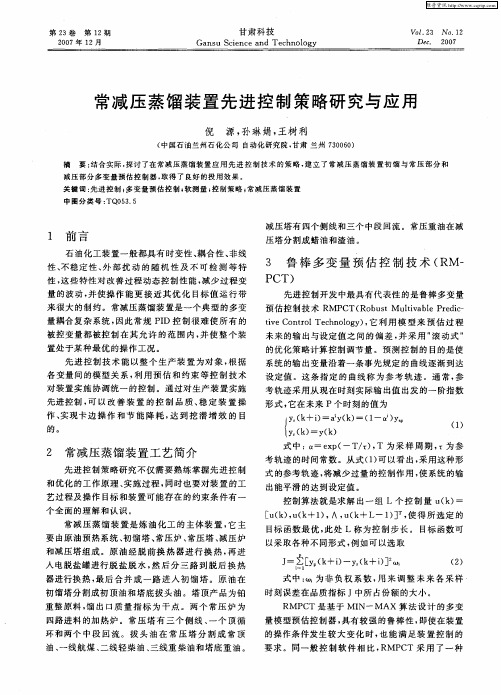
减压 部 分 多 变 量 预 估 控 制 器 , 得 了 良好 的 投 用 效 果 。 取
关 键 词 : 进 控 制 ; 变 量 预估 控 制 ; 先 多 软测 量 ; 制 策 略 ; 减 压 蒸 馏装 置 控 常
中 图分 类 号 : 0 3 5 TQ 5 .
减压塔有 四个侧线 和三个 中段 回流 。常压重油 在减
式 中 :i ∞ 为非 负 权 系数 , 来 调 整 未 来 各 采 样 用
时刻误差 在品质 指标 J中所 占份额 的大 小 。
R MP T是基 于 MI C N—MAX算 法设 计 的多 变
量 模型预 估控制 器 , 具有 较强 的鲁棒 性 , 即使在装 置
的操 作条件 发生较 大 变化 时 , 能 满 足装 置 控 制 的 也
个全 面的理 解和认 识 。 常减 压蒸 馏 装 置是 炼 油化 工 的 主体 装 置 , 主 它
式 的参考轨 迹 , 将减少 过量 的控制 作用 , 系统 的输 使
出能 平滑 的达 到设定 值 。
控制算法 就是求 解 出一 组 L个 控 制 量 U k 一 ()
[ ()u k ) ^, ( +L一 1] 使 得 所选 定 的 uk , (+1 , U k ) ,
维普资讯
第2卷 3
第 1 2期
甘肃 科技
Ga s inc nd Te h l gy n u Sce ea c no o
Z 3 N0 2 .2 .1 De . c 2 7 00
20 0 7年 1 2月
常减压 蒸 馏 装 置 先进 控 制 策 略研 究与 比, MP T 采 用 了 一种 R C
维普资讯
J 一∑[ k ) k )。 。 y( +i一Y( +i ∞ ]
先进控制技术在常减压装置上的开发与应用

夕 ) C (一 ) ∑c u —) ( ( = A p+ A B( f 5 k )
i =1
根据 输 出预测 值 再计 算 多变 量 预 测控 制 系统 的最 优控 制律 。
23 1 先 进 过 程 控 制软 件 应 用 介 绍 。.
S el h l 多变 量 优 化控 制器 (MOC 是 壳牌 全 球解 决 S p )
2 3 多变 量模 型预 测 控 制 .
上世 纪 8 0年 代以来 , S系统得 到了广泛应 用 , D 但
灰 箱 模 型 将 过 程 与 模 型 之 间 的 失 配 包 含 在 内 , 高 了控 提
制 器 的 鲁棒性 。在 控制 器 中引入 状 态变 量 来改 善对 大
《 动 技 与应 21 年 0 第5 自 化 术 用 0 1 第3 卷 期
工 业 控 制I 应 用 与
n s r on r l d Ap ia i n du ty C to an pl to s c
时 滞 过 程 的 预 测 精 度 。 例 如 , 常 压 塔 的 产 品 组 成 的 改 在 变 往 往 会 滞 后 于 塔 顶 灵 敏 板 的 温 度 。 使 用 灵 敏 板 温 度
流量的 影响耦 合严 重 , 常 波动较 大 。 通
x k+l =Ax k 4Bu k ( 、 ()- () ) 足 =C ( ) , ) x k (
其 中 : ∈ , e , ET, e y U I'A , e B , e C
() 1
,
不失一般性 , 假设矩 阵 是列满秩 的 , rn B m; 即 a k = 矩阵
2 1 工 艺 特 点
本装置 主要 由电脱盐 系统 、初 馏和常压 系统 、航煤
先进控制技术在常减压装置的应用

收稿 日期 : 0 7 0 — 5 2 0 — 7 2
作 者 简 介 : 琳 娟 (9 2 ) 女 ,9 5年 毕 业 于 石 油 大 学炼 制 孙 1 7一 , 1 9 工程 专 业 , 在 兰 州 石 化 公 司 自动 化 院 过 程 控 制 所 工 作 , 究 方 现 研
摘 要 :介绍了先进控制技术在兰州石化公 司 5Mta / 常减压装 置上的应用情况 , 阐述 了控制器 开发 过程的要点。通过采
用 多变 量 控 制 手 段 来 实 现 ] 艺控 制 目的 , 仅 提 高 了装 置 的运 行 平 稳 率 , 且 能 够 卡 边 进 行 操 作 , 到 了提 高 目标 产 品 收 率 和 不 而 达 装 置 节 能 降耗 的 目的 。
杂, 建立 精确 数学 模 型 非 常 困难 , 应 用预 估 控 制 而
技术 降低 了对 数学 模型精 度 的要求 , 利用现 场信 息 不 断反馈 修正模 型精 度 , 多变 量控 制技术应 用 于 使
石化 生产变 为可能 , 已成 为炼 化企 业 中普 遍推 广 现 的新技 术u 。2 0 ] 0 6年 , 州 石 化 公 司 自动 化 研 兰
向 :计 算 机应 用 、 油 工 业 先 进 过 程 控制 、 程 模 拟 。 炼 流
维普资讯
第 6期
孙琳娟等. 先进 控 制 技 术 在 常 减 装 置 的应 用
衡, 生产 波动 较 大 , 响产 品 质量 的合 格 率 , 时 , 影 同 伴 随着 原油性 质 的变 化 , 常压 塔 易 出现 泛 塔 、 塔 干
常减压蒸馏装置与设备分析

随着环保要求的日益严格,常减压蒸馏装置将面临更严峻的节能减排 挑战,需要不断开发和应用低能耗、低排放的新技术和新设备。
06
案例分析与实际操作
常减压蒸馏装置运行案例分析
案例一
装置启动过程中的参数调整
01
02
描述
在装置启动阶段,通过对温度、压力等关键参数的精细 调整,实现装置的平稳启动,提高产品质量的稳定性。
少能源浪费。
低排放技术
03
通过改进工艺流程和操作条件,减少装置废气、废水的排放,
实现绿色、环保生产。
设备自动化与智能化发展
1 2 3
自动化控制系统
常减压蒸馏装置引入先进的自动化控制系统,实 现生产过程的实时监测、自动调节,提高装置的 稳定性和安全性。
智能化诊断与预警
通过引入大数据、人工智能等技术,建立装置故 障诊断和预警模型,实现装置故障的及时发现和 处理,减少生产中断时间。
分析
阐述结焦形成的机理和危害,详细讲解预防措施的原理 和实施方法,提高装置的运行稳定性和寿命。
现场操作演示与实训
演示一
常减压蒸馏装置启动操作
内容
现场展示装置启动的全过程,包括参数设置、设备检查、 启动程序等,使学员全面了解装置启动的要点和注意事项 。
演示二
设备故障应急处理
内容
模拟设备故障场景,展示应急处理的操作流程和技巧,培 养学员应对突发情况的能力和冷静处理问题的心态。
装置的预防性维修与大修计划
预防性维修
根据设备的运行情况和历史故障数据,制定预防性维修计划,对 可能出现故障的部位进行提前维修和更换。
大修计划
根据设备的磨损情况和运行时间,制定大修计划,对装置进行全面 、系统的维修和更新,以确保装置的长周期稳定运行。
常减压蒸馏装置自动控制解决方案(精)
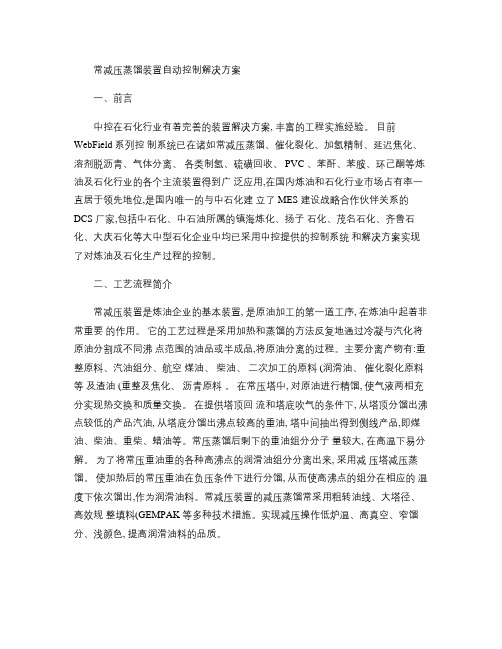
常减压蒸馏装置自动控制解决方案一、前言中控在石化行业有着完善的装置解决方案, 丰富的工程实施经验。
目前WebField 系列控制系统已在诸如常减压蒸馏、催化裂化、加氢精制、延迟焦化、溶剂脱沥青、气体分离、各类制氢、硫磺回收、 PVC 、苯酐、苯胺、环己酮等炼油及石化行业的各个主流装置得到广泛应用,在国内炼油和石化行业市场占有率一直居于领先地位,是国内唯一的与中石化建立了 MES 建设战略合作伙伴关系的DCS 厂家,包括中石化、中石油所属的镇海炼化、扬子石化、茂名石化、齐鲁石化、大庆石化等大中型石化企业中均已采用中控提供的控制系统和解决方案实现了对炼油及石化生产过程的控制。
二、工艺流程简介常减压装置是炼油企业的基本装置, 是原油加工的第一道工序, 在炼油中起着非常重要的作用。
它的工艺过程是采用加热和蒸馏的方法反复地通过冷凝与汽化将原油分割成不同沸点范围的油品或半成品,将原油分离的过程。
主要分离产物有:重整原料、汽油组分、航空煤油、柴油、二次加工的原料 (润滑油、催化裂化原料等及渣油 (重整及焦化、沥青原料。
在常压塔中, 对原油进行精馏, 使气液两相充分实现热交换和质量交换。
在提供塔顶回流和塔底吹气的条件下, 从塔顶分馏出沸点较低的产品汽油, 从塔底分馏出沸点较高的重油, 塔中间抽出得到侧线产品,即煤油、柴油、重柴、蜡油等。
常压蒸馏后剩下的重油组分分子量较大, 在高温下易分解。
为了将常压重油重的各种高沸点的润滑油组分分离出来, 采用减压塔减压蒸馏。
使加热后的常压重油在负压条件下进行分馏, 从而使高沸点的组分在相应的温度下依次馏出,作为润滑油料。
常减压装置的减压蒸馏常采用粗转油线、大塔径、高效规整填料(GEMPAK 等多种技术措施。
实现减压操作低炉温、高真空、窄馏分、浅颜色, 提高润滑油料的品质。
原油图 1 常减压装置工艺流程图三、控制方案3.1 装置关键控制常减压装置通常以常规单回路控制为主,辅以串级、均匀和切换等少量复杂控制。
250万t/年常减压蒸馏装置常压塔先进控制设计

250万t/年常减压蒸馏装置常压塔先进控制设计摘要玉门油田分公司炼油化工总厂曾建立过“250万t/年常减压蒸馏装置先进控制”项目,项目是由玉门油田分公司组织实施的中国石油天然气股份公司科研与技术开发项目。
在先进控制的应用中根据装置的特点和生产要求,精心设计阶跃测试计划,并保证测试的成功,从而为过程模型的辨识提供理想的数据。
本文通过对玉门油田分公司炼化总厂“250万t/年常减压蒸馏装置”中常压塔部分的先进控制设计的简述,包括常压塔先进控制系统功能设计,常压塔动态机理模型的建立及线性化模型的建立,呈现出先进控制在常减压装置中的具体建设和使用情况。
关键词先进控制;常压塔先进控制系统功能设计;常压塔动态机理模型;经济效益1 概述玉门油田分公司炼油化工总厂“250万t/年常减压蒸馏装置先进控制”项目是由玉门油田分公司炼油化工总厂组织实施的中国石油天然气股份公司科研与技术开发项目。
该项目计划在250万吨/年常减压蒸馏装置实施先进过程控制(APC)的应用,力争通过该项目的实施,提高装置产品质量控制水平、优化生产、降低能耗,提高玉门油田分公司炼油化工总厂自控水平。
玉门油田分公司炼油化工总厂选用Honeywell公司RMPCT先进控制技术、石油大学模型和工艺计算软测量技术,由石油大学(北京)自动化研究所进行工程实施及技术服务。
现以常压塔部分的先进控制设计为例,简述先进控制的设计。
2 总体控制目标1)提高装置运行平稳率,稳定工艺操作,延长设备寿命,在产品质量、装置能耗、产品收率等因素之间实现卡边操作,发挥装置最大潜力,提高经济效益;2)装置在处理量波动上有较大弹性,能够适应频繁的生产方案变化,避免生产波动,尽可能降低劳动强度,保证工艺平稳率在98%以上,保证装置能够达到三年一修的目标;3)使用先进控制技术后,能够更好的解决原油调和比例(性质)的变化对操作平稳性和产品质量目标的影响(原油调和方案:以吐哈原油为主,掺炼玉门、塔指油);4)在产品质量上可实现卡边操作,清晰分割侧线产品,尽可能提高产品收率和柴汽比,装置总收率提高1%以上;5)在不影响产品质量及收率的情况下,提高装置热回收率,使装置能耗降至10.4(千克标油/吨原油)以下;6)平稳加热炉操作,防止加热炉进料出现偏流现象,防止炉管结焦,降低燃料耗量,提高加热炉热效率,保证热效率在90%以上;7)能够适应常一线生产航煤、溶剂汽油、-35℃军柴,以及常二线生产液压油、不同凝固点柴油等生产方案的变化,并在不同方案下装置取得最大效益;8)实现常压塔的露点计算,防止常压塔的露点腐蚀;9)使用先进控制技术后,所有控制指标达到工艺控制目标的要求;10)使用先进控制技术后,装置可增效益400万元/年以上。
常减压蒸馏装置运行中存在的问题及对策

常减压蒸馏装置运行中存在的问题及对策常减压蒸馏装置是一种常用于石油化工行业的分离设备,它通过调整操作变量和运行参数,将原料中的组分按照沸点的不同进行分离和提纯。
然而,在常减压蒸馏装置的运行过程中,常常会出现一些问题和挑战,如产量下降、能耗增加、产品质量不稳定等。
本文将围绕这些问题展开讨论,并提出了对应的对策。
1. 产量下降问题在常减压蒸馏装置的运行过程中,如果产量出现下降,首先需要考虑的是原料供应是否稳定。
若供应不稳定,可以通过增加储备库容量或改善原料的供应情况来解决。
另外,还需要关注蒸馏塔内的操作变量。
可以调整回流比和加热器的负荷以提高产量。
还可以通过增加分馏塔的塔盘数目、优化进出料流程和改进塔内助剂的分布等方式来提高产量。
2. 能耗增加问题常减压蒸馏装置的运行过程中,能耗的增加也是一个常见的问题。
造成能耗增加的原因有很多,例如设备老化、设备损坏、操作不当等。
为了解决这个问题,首先需要对设备进行定期的检修和维护,确保设备处于良好的工作状态。
需要进行操作的优化。
可以调整冷凝器的温度和冷却水的流量来减少能耗。
另外,也可以考虑采用更加节能的技术和装置来替代现有的设备。
3. 产品质量不稳定问题常减压蒸馏装置的运行过程中,产品质量的不稳定性可能会成为一个问题。
这主要是由于原料中的杂质和组分之间的相互作用引起的。
为了解决这个问题,可以采取以下措施。
可以对原料进行预处理,例如采用适当的净化工艺来去除杂质。
可以调整分离过程中的操作变量,以达到所需的产品质量。
可以调整蒸馏塔的塔盘温度和压力,改变进料流量和回流比来优化产品的组分分离。
个人观点和理解:常减压蒸馏装置在石油化工的生产中起着重要的作用,但在实际运行中难免会遇到各种问题。
解决这些问题的关键在于科学合理的操作和优化。
通过合理调整操作变量、优化设备结构和改进工艺流程,可以提高产量、降低能耗和保持产品质量稳定。
还需要注重设备的维护和检修工作,确保设备处于良好的工作状态。
先进控制在常减压蒸馏装置的实施

2T O E M R FN R N I E R N E R L U E IE YE GN E IG
第3 7卷第 1 0期
自动捌
先 进控 制在 常减 压 蒸 馏 装 置 的 实施
成 。装置 的调 节 阀也相应 全部 更 新 , 上 D S改 加 C
控制软件 , 实施了先进控制。
1 装 置概 况
造, 使该装置完全具备了实施先进控制的条件 , 改
造于 20 05年 6 月底完成。
2 先 进控 制软 件 2 1 D pu 简介 . MC ls
常减压 蒸馏 装 置 18 95年 9月 由 中 国石 化 集 团洛 阳石油 化 工 工程 公 司设 计 , 18 于 97年 1 2月 建 成 ,9 8年 2月开 工 投产 。设 计 为 闪蒸 塔 和 常 18
为 了适应 加工 原油性 质 的变化 及产 品质 量升 级 的 需要 ,0 2年 5月 , 减 压 蒸 馏 装 置 换 热 流 程 进 20 对
该 装置 的先 进 控 制 采 用 美 国 A P N公 司的 SE D pu 软 件 。图 1 示 D pu 控制器 的软 件 MC ls 表 MC ls
张黎 明 姚 亮
1 西安石油大学 ( . 陕西省西安市 7 00 ) 10 0
2 中国石油化工股份有 限公 司洛阳分 公司( . 河南省洛 阳市 4 1 1 ) 7 0 2
摘 要: 介绍 了中国石油化工股份有限公司洛阳分公 司在 2 0 年对 常减压蒸馏装置实施先进控制的情况。该先 06 进控制采用 了美 国 A P N公 司的 D C l 先进控制软件 , SE M ps u 结合 生产装 置实际情况 , 设置 了三个 D C l 控制 器, M ps u 分别控制初馏塔 、 常压炉 、 常压塔。通过先进 控制 系统 的实施 , 实现 了稳定生产 : 常压炉操作平稳 , 温度偏差控制 在 ± 2℃ ; 加热炉热效率提 高 0 2 . 个百分点 ; 初馏塔塔底液位平 稳, 保持 在 4 % 一 0 ; 0 6 % 质量控制水 平明显提 高, 尤其
影响常减压蒸馏装置能耗的问题分析与节能对策

影响常减压蒸馏装置能耗的问题分析与节能对策常减压蒸馏装置在化工生产中起着非常重要的作用,它能够通过降低压力来蒸发和分离液体混合物,从而得到纯净的产品。
常减压蒸馏装置在使用过程中存在能耗较高的问题,这不仅增加了生产成本,也不利于环保。
对常减压蒸馏装置的能耗问题进行深入分析,并提出相应的节能对策,对于提高生产效率和降低能耗都具有重要意义。
一、常减压蒸馏装置能耗问题分析1. 设备运行能耗高常减压蒸馏装置在整个生产过程中需要通过加热使得混合物蒸发,并通过冷却器冷凝得到纯净的产品。
而加热和冷却过程都需要大量的能源支持,因此设备的运行能耗较高。
2. 设备设计不合理一些常减压蒸馏装置的设计存在结构紧凑、热交换面积小等问题,导致在蒸馏过程中对能源的利用率不高,一部分热能散失,造成了能耗的增加。
3. 控制方式不科学在实际操作中,一些企业为了追求产品的纯度和稳定性,会采用较为保守的操作控制方式,如调整较高的蒸发温度和急速的冷凝速度,这样会使得能耗增加。
二、节能对策1. 设备升级改造针对常减压蒸馏装置的设计不合理的问题,可以进行设备升级改造,增加热交换器的面积,提高能源的利用率。
通过优化设备的结构和调整设备的参数,减少能量的损失,降低能耗。
2. 优化控制策略在操作中采用科学合理的控制策略,如合理调整蒸发温度、冷凝速度等参数,使得设备在满足产品质量要求的实现更好的能耗控制。
3. 提高热能利用率采用余热回收技术,将设备蒸发所产生的热能进行回收再利用,用于加热进料液体或提供其他加热需求,从而降低设备总体能耗。
4. 完善设备管理建立健全的设备运行和维护管理制度,定期对设备进行检修和维护,保持设备的良好状态,减少运行中的能源浪费,进一步降低能耗。
5. 采用先进的节能技术利用先进的生产工艺和设备技术,如采用高效的换热器、蒸发器和冷凝器等设备,选用高效的燃料、提高能源利用效率,降低生产成本。
三、结语通过以上对常减压蒸馏装置能耗问题的分析和节能对策的提出,希望能够引起企业和生产工作者对能源的关注,并对设备的能耗问题予以重视。
蒸馏装置先进控制的实现
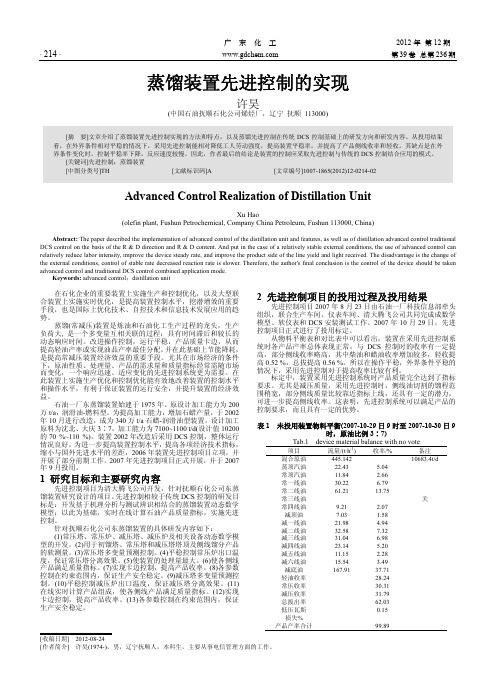
广东化工 2012年第12期· 214 · 第39卷总第236期蒸馏装置先进控制的实现许昊(中国石油抚顺石化公司烯烃厂,辽宁抚顺 113000)[摘要]文章介绍了蒸馏装置先进控制实现的方法和特点,以及蒸馏先进控制在传统DCS控制基础上的研发方向和研发内容。
从投用结果看,在外界条件相对平稳的情况下,采用先进控制能相对降低工人劳动强度,提高装置平稳率,并提高了产品侧线收率和轻收。
其缺点是在外界条件变化时,控制平稳率下降,反应速度较慢。
因此,作者最后的结论是装置的控制应采取先进控制与传统的DCS控制结合应用的模式。
[关键词]先进控制;蒸馏装置[中图分类号]TH [文献标识码]A [文章编号]1007-1865(2012)12-0214-02Advanced Control Realization of Distillation UnitXu Hao(olefin plant, Fushun Petrochemical, Company China Petroleum, Fushun 113000, China)Abstract: The paper described the implementation of advanced control of the distillation unit and features, as well as of distillation advanced control traditional DCS control on the basis of the R & D direction and R & D content. And put in the case of a relatively stable external conditions, the use of advanced control can relatively reduce labor intensity, improve the device steady rate, and improve the product side of the line yield and light received. The disadvantage is the change of the external conditions, control of stable rate decreased reaction rate is slower. Therefore, the author's final conclusion is the control of the device should be taken advanced control and traditional DCS control combined application mode.Keywords: advanced control;distillation unit在石化企业的重要装置上实施生产和控制优化,以及大型联合装置上实施实时优化,是提高装置控制水平,挖潜增效的重要手段,也是国际上优化技术、自控技术和信息技术发展应用的趋势。
先进控制技术在九江石化常减压装置的应用
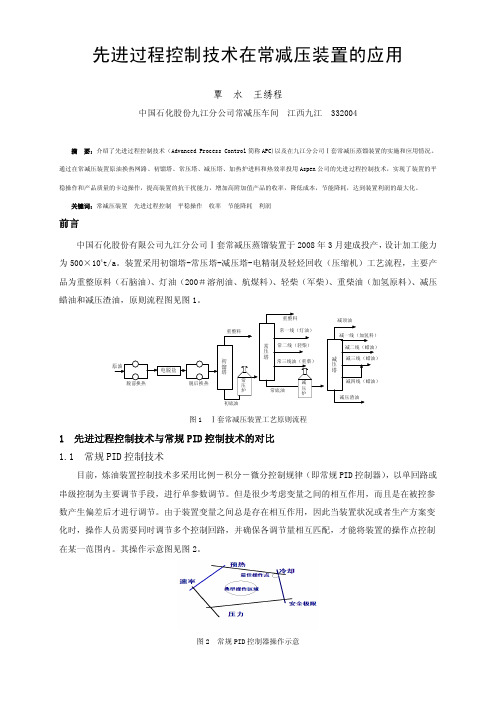
覃 水 王绣程
中国石化股份九江分公司常减压车间 江西九江 332004
摘 要:介绍了先进过程控制技术(Advanced Process Control 简称 APC)以及在九江分公司Ⅰ套常减压蒸馏装置的实施和应用情况。 通过在常减压装置原油换热网路、初馏塔、常压塔、减压塔、加热炉进料和热效率投用 Aspen 公司的先进过程控制技术,实现了装置的平 稳操作和产品质量的卡边操作,提高装置的抗干扰能力,增加高附加值产品的收率,降低成本,节能降耗,达到装置利润的最大化。
3.89 0.519 3.99 0.796 -52.96 13.63 -58.18 17.05 257.12 3.09 320.23 1.58 -0.912 1.004 -0.464 1.546 -0.292 1.312 0.417 0.601 1.305 0.844 59.3 7.701
DMC 投用后 平均值 方差
关键词:常减压装置 先进过程控制 平稳操作 收率 节能降耗 利润
前言
中国石化股份有限公司九江分公司Ⅰ套常减压蒸馏装置于 2008 年 3 月建成投产,设计加工能力 为 500×104t/a。装置采用初馏塔-常压塔-减压塔-电精制及轻烃回收(压缩机)工艺流程,主要产
品为重整原料(石脑油)、灯油(200#溶剂油、航煤料)、轻柴(军柴)、重柴油(加氢原料)、减压
蜡油和减压渣油,原则流程图见图 1。
原油 脱前换热
电脱盐
重整料
重整料 常一线(灯油)
脱后换热
初 馏 塔
常 压 炉
初底油
常 常二线(轻柴) 压 塔
常三线油(重柴)
减
常底油
压 炉
图 1 Ⅰ套常减压装置工艺原则流程
先进控制技术在常减压装置节能降耗方面的应用
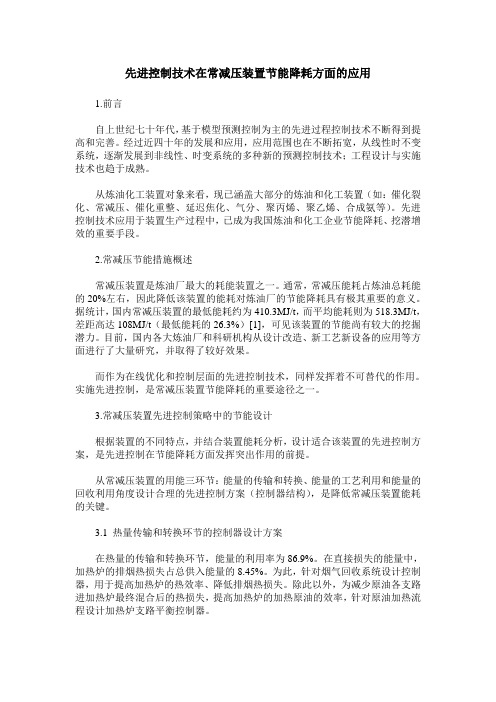
先进控制技术在常减压装置节能降耗方面的应用1.前言自上世纪七十年代,基于模型预测控制为主的先进过程控制技术不断得到提高和完善。
经过近四十年的发展和应用,应用范围也在不断拓宽,从线性时不变系统,逐渐发展到非线性、时变系统的多种新的预测控制技术;工程设计与实施技术也趋于成熟。
从炼油化工装置对象来看,现已涵盖大部分的炼油和化工装置(如:催化裂化、常减压、催化重整、延迟焦化、气分、聚丙烯、聚乙烯、合成氨等)。
先进控制技术应用于装置生产过程中,已成为我国炼油和化工企业节能降耗、挖潜增效的重要手段。
2.常减压节能措施概述常减压装置是炼油厂最大的耗能装置之一。
通常,常减压能耗占炼油总耗能的20%左右,因此降低该装置的能耗对炼油厂的节能降耗具有极其重要的意义。
据统计,国内常减压装置的最低能耗约为410.3MJ/t,而平均能耗则为518.3MJ/t,差距高达108MJ/t(最低能耗的26.3%)[1],可见该装置的节能尚有较大的挖掘潜力。
目前,国内各大炼油厂和科研机构从设计改造、新工艺新设备的应用等方面进行了大量研究,并取得了较好效果。
而作为在线优化和控制层面的先进控制技术,同样发挥着不可替代的作用。
实施先进控制,是常减压装置节能降耗的重要途径之一。
3.常减压装置先进控制策略中的节能设计根据装置的不同特点,并结合装置能耗分析,设计适合该装置的先进控制方案,是先进控制在节能降耗方面发挥突出作用的前提。
从常减压装置的用能三环节:能量的传输和转换、能量的工艺利用和能量的回收利用角度设计合理的先进控制方案(控制器结构),是降低常减压装置能耗的关键。
3.1 热量传输和转换环节的控制器设计方案在热量的传输和转换环节,能量的利用率为86.9%。
在直接损失的能量中,加热炉的排烟热损失占总供入能量的8.45%。
为此,针对烟气回收系统设计控制器,用于提高加热炉的热效率、降低排烟热损失。
除此以外,为减少原油各支路进加热炉最终混合后的热损失,提高加热炉的加热原油的效率,针对原油加热流程设计加热炉支路平衡控制器。
常减压装置先进控制关键技术分析

常减压装置先进控制关键技术分析摘要]:常减压装置在原油加工处于首要位置,同时在其过程中也是加工规模最大的工艺装置。
自动化技术在石油化工企业生产过程应用越来越广泛,先进控制已成为石油化工企业提高产品质量和扩大生产的重要手段。
本文在分析了常减压装置的控制方案相关技术,介绍鲁棒多变量预估控制原理,并研究了常压塔控制器的功能设计。
中国论文网 h[关键词]:炼油厂,常减压装置,先进控制,结束改革目前,石油化工企业对市场和生产环境的变化都表现出十分敏感的特性,以期获得最大的经济效益。
世界各国的经验表明,先进控制技术是提高企业的经济效益、降低生产成本、提高其在国际市场中的创新力、应变力、适应力和综合竞争力的主要技术手段之一。
常减压装置的主要任务是将原油分离成合格的产品或中间产品,是原油加工中重要的组成部分。
本文就炼油厂中的常减压装置的先进控制技术的一些关键技术进行分析。
1常减压装置的工艺简介常减压装置是炼油厂进行原油提炼的第一道工序,它的作用是从原油中提炼出各种燃料、润滑油、化工原料等产品。
其基本原理主要是利用加热、分馏等物理方法分割不同沸点范围的汽油,柴油、溶剂油、航空煤油和重油等二次加工原料和产品。
其特点是加工方法简单、成本低。
因此,在保证产品质量的前提下,其一次拔出率的高低将直接影响到炼油厂的整体经济效益。
常减压装置主要由原油电脱盐系统、原油换热系统、原油精馏系统和产品冷凝、冷却系统等几部分组成,其核心为原油精馏系统。
生产上利用原油中各组分的沸点不同,将原油加热到一定温度,送入常压精馏塔,在塔的进料段进行一次汽化。
汽化后,气相部分上升至塔的精馏段,液相部分下降至塔的提馏段,是此装置工艺原理。
2常减压装置先进控制关键技术分析2.1常减压装置的控制方案常减压装置控制系统的应用目的是平稳工艺操作,保证产品产量和质量。
要达到此目的就必须保证装置的物料、气液相和热量的三大平衡。
(1)常规控制方案常规控制方案是在经典控制理论的基础上形成的,在实际生产过程中,一般的常规控制回路主要由测量单元、以PID为基础建立的常规调节器、调节阀、检测元件和工艺对象等几部分组成。
关于对常减压蒸馏新技术的研究与探讨
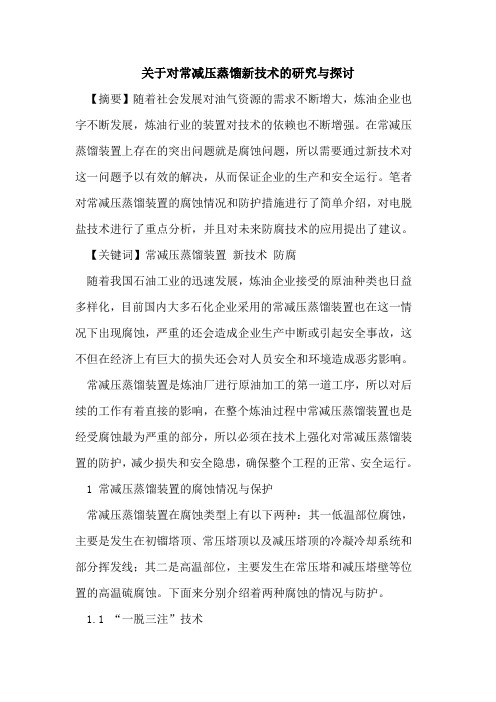
关于对常减压蒸馏新技术的研究与探讨【摘要】随着社会发展对油气资源的需求不断增大,炼油企业也字不断发展,炼油行业的装置对技术的依赖也不断增强。
在常减压蒸馏装置上存在的突出问题就是腐蚀问题,所以需要通过新技术对这一问题予以有效的解决,从而保证企业的生产和安全运行。
笔者对常减压蒸馏装置的腐蚀情况和防护措施进行了简单介绍,对电脱盐技术进行了重点分析,并且对未来防腐技术的应用提出了建议。
【关键词】常减压蒸馏装置新技术防腐随着我国石油工业的迅速发展,炼油企业接受的原油种类也日益多样化,目前国内大多石化企业采用的常减压蒸馏装置也在这一情况下出现腐蚀,严重的还会造成企业生产中断或引起安全事故,这不但在经济上有巨大的损失还会对人员安全和环境造成恶劣影响。
常减压蒸馏装置是炼油厂进行原油加工的第一道工序,所以对后续的工作有着直接的影响,在整个炼油过程中常减压蒸馏装置也是经受腐蚀最为严重的部分,所以必须在技术上强化对常减压蒸馏装置的防护,减少损失和安全隐患,确保整个工程的正常、安全运行。
1 常减压蒸馏装置的腐蚀情况与保护常减压蒸馏装置在腐蚀类型上有以下两种:其一低温部位腐蚀,主要是发生在初镏塔顶、常压塔顶以及减压塔顶的冷凝冷却系统和部分挥发线;其二是高温部位,主要发生在常压塔和减压塔壁等位置的高温硫腐蚀。
下面来分别介绍着两种腐蚀的情况与防护。
1.1 “一脱三注”技术低温部位的腐蚀主要来自于原油中的氯盐和硫化物通过加热生成的hc1和硫化氢,经过塔顶低温部位冷凝形成稀盐酸腐蚀环境,对常减压蒸馏装置造成坑蚀、沟槽、穿孔等腐蚀现象。
针对这一腐蚀防护的办法是以工艺技术——“一脱三注”为主,材料为辅。
“一脱三注”技术是对常减压蒸馏装置低温部位腐蚀最为有效的方法,包括原油电脱盐、注有机胺、注缓浊剂或注水。
这一技术旨在降低原油中的盐含量,从而控制hc1的产生,改变腐蚀环境状况,这一技术也能够在设备表明形成一层保护膜,能够有效阻止腐蚀物与设备表面的接触。
常减压蒸馏装置用能分析与探讨

依据热力学第一定律和热力学第二定律对装置进 行能量平衡和 平衡计算, 并对计算结果进行了分 析和探讨。 2 装置简介
装 置 设 计 原 油 处 理 能 力 5Mt/a, 采 用 “初 馏 — 常 压 蒸 馏 — 减 压 蒸 馏 ”工 艺 流 程 , 为 燃 料- 润 滑 油 型 常 减 压 蒸 馏 装 置 。初 馏 塔 、常 压 塔 采 用 操 作 弹 性 大 、效 率高的导向浮阀塔盘; 减压塔采用全填料, 以降低 全塔压降, 采用蒸汽与机械联合抽真空实现减压塔 真空度; 常压加热炉采用双室立管箱式炉设计, 减 压炉为卧管立式方箱炉, 设立两炉单独的烟气余热 回 收 系 统 , 两 炉 内 壁 保 温 采 用 HT- 1 高 温 辐 射 耐 火 涂 料 , 设 计 效 率 92%; 利 用 “窄 点 ”技 术 对 换 热 流 程 进 行 优 化 设 计 , 原 油 换 热 终 温 达 到 305℃; 对 机 泵 进 行了优化选型, 部分机泵采用电机调频技术, 以有 效 降 低 电 耗 。5Mt/a 常 减 压 蒸 馏 装 置 于 2003 年 8 月 建 成 投 产 , 至 2007 年 装 置 共 加 工 原 油 19.5Mt, 常 减 压 装 置 处 理 量 在 500 ̄645t/h 运 行 , 操 作 平 稳 , 产 品 质量稳定。 3 装置标定结果
无 效 动 力 8.83 散 热 损 失 2.96 烟 气 损 失 5.28 传 热 过 程 损 失 191.50
损 失 4.48 热 力 学 损 22.99
输 出 16.56 传 热 过 程 损 失 93.81
冷 却 排 弃 40.97
电 69.40 蒸 汽 17.06 燃 料 367.91 总 供 入 454.37 转换与传输
关于对常减压蒸馏新技术的研究与探讨

关于对常减压蒸馏新技术的研究与探讨摘要:石油资源对人类社会的发展起着举足轻重的作用,石油精制技术和精炼设备在技术上也取得了长足的进步。
本文分析了常减压蒸馏设备腐蚀的主要原因及种类,并提出了一些新的技术措施,以预防其腐蚀。
关键词:常减压;蒸馏技术;创新;分析引言随着我国石油行业的快速发展,炼油厂所能接收到的原油品种越来越多,目前国内大部分石化公司所使用的减压蒸馏设备都发生了这种腐蚀,甚至会导致生产中断或发生安全事故,不仅会给企业带来巨大的经济损失,而且会对环境和人身安全产生不利的影响。
常减压蒸馏设备是炼油厂生产原油的首要环节,它的存在对生产的影响很大,而常减压蒸馏设备又是整个生产过程中受到的腐蚀最大的一个环节,因此,为了降低事故的发生和安全风险,保证了项目的正常、安全运行。
常压蒸馏与减压蒸馏通常被称为常减压蒸馏,常减压蒸馏是一种物理过程。
常减压精馏工艺是原油生产的一个重要环节,但由于油田的类型和设备寿命的延长,其存在一定的腐蚀问题,不但影响了原油精炼的效率,而且还会造成各种程度的安全事故。
要彻底解决这个问题,必须避免常减压蒸馏装置的腐蚀,保证原油精炼的安全。
一、常减压蒸馏设备的腐蚀成因分析石油中的碳、氢、硫、氮、氧是其主要成分。
碳含量在83.0%~87.0%之间;其含氢量在11.0%~14.0%之间;在0.05%~8.0%的范围内,含0.05%~2.0%的氧气和0.02%~2.0%的含氮量。
虽然硫、氮、氧等元素含量很少,但仍然有很强的腐蚀性。
实践证明,常减压蒸馏设备发生腐蚀的原因有两个:①在塔顶和塔顶,都有凝结体系,也有挥发路线,所以这个位置的温度要低一些,因为在提取石油的时候,会有氯盐、硫化物等元素,这些元素会变成硫化氢和氯化氢,当它们通过低温的时候,会凝结成稀盐酸,所以很容易被腐蚀。
②常减压蒸馏设备的高温部位也是容易发生腐蚀的地方,高温会使原油中的硫化氢和其它硫化物与金属发生剧烈的反应,尤其是高温区域的环烷酸腐蚀。
- 1、下载文档前请自行甄别文档内容的完整性,平台不提供额外的编辑、内容补充、找答案等附加服务。
- 2、"仅部分预览"的文档,不可在线预览部分如存在完整性等问题,可反馈申请退款(可完整预览的文档不适用该条件!)。
- 3、如文档侵犯您的权益,请联系客服反馈,我们会尽快为您处理(人工客服工作时间:9:00-18:30)。
第23卷第12期2007年12月甘肃科技Gansu Science and T echnolo gyV ol.23N o.12D ec.2007常减压蒸馏装置先进控制策略研究与应用倪源,孙琳娟,王树利(中国石油兰州石化公司自动化研究院,甘肃兰州730060)摘要:结合实际,探讨了在常减压蒸馏装置应用先进控制技术的策略,建立了常减压蒸馏装置初馏与常压部分和减压部分多变量预估控制器,取得了良好的投用效果。
关键词:先进控制;多变量预估控制;软测量;控制策略;常减压蒸馏装置中图分类号:T Q053.51前言石油化工装置一般都具有时变性、耦合性、非线性、不稳定性、外部扰动的随机性及不可检测等特性,这些特性对改善过程动态控制性能,减少过程变量的波动,并使操作能更接近其优化目标值运行带来很大的制约。
常减压蒸馏装置是一个典型的多变量耦合复杂系统,因此常规PID控制很难使所有的被控变量都被控制在其允许的范围内,并使整个装置处于某种最优的操作工况。
先进控制技术能以整个生产装置为对象,根据各变量间的模型关系,利用预估和约束等控制技术对装置实施协调统一的控制。
通过对生产装置实施先进控制,可以改善装置的控制品质、稳定装置操作、实现卡边操作和节能降耗,达到挖潜增效的目的。
2常减压蒸馏装置工艺简介先进控制策略研究不仅需要熟练掌握先进控制和优化的工作原理、实施过程,同时也要对装置的工艺过程及操作目标和装置可能存在的约束条件有一个全面的理解和认识。
常减压蒸馏装置是炼油化工的主体装置,它主要由原油预热系统、初馏塔、常压炉、常压塔、减压炉和减压塔组成。
原油经脱前换热器进行换热,再进入电脱盐罐进行脱盐脱水,然后分三路到脱后换热器进行换热,最后合并成一路进入初馏塔。
原油在初馏塔分割成初顶油和塔底拔头油。
塔顶产品为铂重整原料,馏出口质量指标为干点。
两个常压炉为四路进料的加热炉。
常压塔有三个侧线、一个顶循环和两个中段回流。
拔头油在常压塔分割成常顶油、一线航煤、二线轻柴油、三线重柴油和塔底重油。
减压塔有四个侧线和三个中段回流。
常压重油在减压塔分割成蜡油和渣油。
3鲁棒多变量预估控制技术(RM-PCT)先进控制开发中最具有代表性的是鲁棒多变量预估控制技术RM PCT(Robust M ultiv able Predic-tive Contr ol T echno log y),它利用模型来预估过程未来的输出与设定值之间的偏差,并采用"滚动式"的优化策略计算控制调节量。
预测控制的目的是使系统的输出变量沿着一条事先规定的曲线逐渐到达设定值。
这条指定的曲线称为参考轨迹。
通常,参考轨迹采用从现在时刻实际输出值出发的一阶指数形式,它在未来P个时刻的值为y r(k+i)=a i y(k)=(1-A i)y spy r(k)=y(k)(1)式中:A=ex p(-T/S),T为采样周期,S为参考轨迹的时间常数。
从式(1)可以看出,采用这种形式的参考轨迹,将减少过量的控制作用,使系统的输出能平滑的达到设定值。
控制算法就是求解出一组L个控制量u(k)= [u(k),u(k+1),C,u(k+L-1)]T,使得所选定的目标函数最优,此处L称为控制步长。
目标函数可以采取各种不同形式,例如可以选取J=Epi=1[y p(k+i)-y r(k+i)]2X i(2)式中:X i为非负权系数,用来调整未来各采样时刻误差在品质指标J中所占份额的大小。
RM PCT是基于M IN-MAX算法设计的多变量模型预估控制器,具有较强的鲁棒性,即使在装置的操作条件发生较大变化时,也能满足装置控制的要求。
同一般控制软件相比,RM PCT采用了一种漏斗式的区域控制算法,即最优化的区域控制,力求以最小的控制作用获得最优的控制响应。
在控制过程中,漏斗控制区域自动以当前受控变量值为初值,以要求的闭环响应时间为长度张开漏斗,实施控制作用,使受控变量处于漏斗区域内,而当受控变量处于区域内时,控制器将不再采取进一步的控制作用,以提高整个控制系统的鲁棒性。
4先进控制策略研究进行常减压蒸馏装置先进控制策略研究,首先需要深刻理解工艺过程和现场操作条件,确定装置操作过程中的产品质量指标以及重要的工艺操作范围,同时还要理解操作过程中的各种约束条件。
其次,明确操作变量之间相互受影响的程度,如果选择的变量之间存在关联或者耦合关系,就必须在这些变量之间做出选择,否则会严重影响先进控制器的投用效果。
一个设计合理、具有良好控制性能和鲁棒性的先进控制器不一定是非常复杂的。
一般来说,常减压蒸馏装置进行先进控制器设计时,需要考虑实现下列具体目标:*为装置操作提供安全平稳的控制*优化操作,提高产品质量及合格率*满足产品质量指标的前提下,最大限度提高目的产品收率*控制加热炉支路出口温度极差最小*在满足装置的约束条件下,进行优化控制,以达到能量最大回收的目的4.1质量指标软测量技术在先进控制项目实施中,产品质量的软测量计算是一个难点。
一般的先进控制策略都是通过数据回归的方式或者基于物料平衡和能量平衡的纯机理建模方式来获取产品质量的数学模型,并应用于先进控制器中作为被控变量进行卡边操作。
但这两种建模方式对于软测量模型精度的要求非常高,在实际使用过程中,往往由于工艺操作条件变化等原因很难真正做到计算准确。
计算蒸馏塔各侧线产品质量指标采用/通用原油切割点计算方法0(Generalized Cutpo int Calcula-tion)是比较理想的一种软测量计算方法,这种方法基于蒸馏塔内的精馏机理,在进行软测量计算时以蒸馏塔的热平衡为推理计算的主要依据,这打破了传统的物料平衡与热平衡相结合的方式。
当原油性质发生变化时,GCC模型根据此时塔内的压力、温度等测量数据,可以很快地推算出新的原油的非线性实沸点馏程,进而计算各侧线产品质量指标,使得软测量计算模型的鲁棒性大大提高。
具体计算步骤如下:1、恩氏蒸馏曲线计算:GCC模型先假设石脑油与闪蒸段切割点之间的线性实沸点曲线,再利用塔的温度分布预算出非线性曲线,最终用非线性实沸点曲线结合GCC的内回流计算结果,估算出侧线物流恩氏蒸馏点。
2、闪点计算:应用侧线物流的非线性实沸点曲线,估算出该物流的泡点温度,并结合蒸汽量,最终计算出物流的闪点。
3、过汽化量模型:GCC根据全塔温度梯度以及闪蒸段的热平衡,估算出实时的过汽化量。
公式表示如下:侧线物流恩氏蒸馏点=f(切割点温度,内回流量)闪点=f(切割点温度,蒸汽量)4.2初馏/常压部分控制策略分析初馏塔/常压塔主要以各侧线产品质量指标为先进控制策略的主要控制目标,在实际的先进控制策略中是将软测量计算结果直接引入先进控制器中,以提高侧线产品质量合格率;同时,在保证侧线产品质量指标的前提下,通过对质量的卡边操作和对侧线抽出量的优化,最大限度地提高附加值产品的收率,增加装置的经济效益。
另外,在常压塔的先进控制策略中,我们将常一中、常二中回流量作为干扰变量进行设计,而并没有像常规设计一样作为操作变量,这是因为这两个变量对于常压塔全塔操作影响巨大,作为干扰变量进行前馈控制更符合操作习惯,实际应用效果更为理想。
对于常压塔底进行非线性液位控制,允许液位在某个范围内波动,当常压塔底液位越限时,根据其升高或降低的趋势调节塔底抽出量把塔底液位拉回到范围之内。
这种控制策略避免了对常压塔底抽出量或相应流量的频繁调节,减少了对下游操作的扰动。
常压塔底非线性液位控制的受控变量是常压塔底液位,操纵变量是减压炉四路进料流量。
对于常压炉,在保证加热炉总进料量不变的条件下,以温度均衡为原则,通过重新分配支路流量,使支路出口温差最小,从而达到防治偏流,延长加热炉炉管使用周期的目的。
它根据人工输入的处理量目标值,在支路流量有调节余地的条件下,按PID 算法逐步提降加热炉总进料量,使其最终达到目标值。
60甘肃科技第23卷常压塔过气化油流量很多装置都没有仪表指示,在我们的先进控制策略当中增加了这个量的软测量计算并将其作为优化控制目标,这样一方面可以在原油切换和产品方案切换过程中有效防止干板现象的发生,另一方面可以实现常压塔的优化控制,使得过气化油流量处于一个最合理的范围。
基于上述的先进控制策略,初馏/常压部分先进控制器如表1和表2。
表1初馏/常压先进控制器变量列表受控变量(CV)操作变量(M V)干扰变量(DV)初馏塔顶铂料干点初馏塔顶温度常一中流量常压塔顶汽油干点常压塔顶回流量常二中流量常一线抽出温度常压塔顶循流量初侧油流量常一线产品闪点常一线抽出流量常压塔进料量常一线产品98%点常二线抽出流量常二线产品95%点常三线抽出流量常三线产品95%点常一线热虹吸温度常压塔底过汽化量表2常压炉中间控制器变量列表受控变量(CV)操作变量(M V)常压炉一路进料出口温度常压炉一路进料流量常压炉二路进料出口温度常压炉二路进料流量常压炉三路进料出口温度常压炉二路进料流量常压炉四路进料出口温度常压炉二路进料流量常压炉总进料量4.3减压部分控制策略分析减压蒸馏单元的生产方案大部分是催料方案,控制起来比较容易,在生产润滑油方案时质量指标主要就是各侧线粘度、闪点和馏程。
同时,减压塔各侧线粘度的在线质量分析仪表运行稳定、可靠,完全可以取代人工化验分析,因此在进行先进控制策略研究中将粘度在线质量分析仪表信号值引入先进控制器中进行产品质量的在线闭环控制。
在减压先进控制策略中将减压塔顶温度和各侧线馏出口温度作为主要控制目标,为装置操作提供安全平稳的控制;同时将减二、三线产品粘度控制在给定范围内,进行产品质量的卡边控制。
这种策略兼顾了平稳操作和优化控制,是一种比较简单、易于实现的一种控制策略。
在先进控制器的控制下减压塔操作平稳,产品质量能够卡边,提高了润滑油的产量和质量。
减压加热炉支路平衡控制仅实现支路平衡功能,以温度均衡为原则,通过重新分配支路流量,使支路出口温差最小,从而达到延长炉管使用周期的目的。
它与常压塔底液位实现串级控制,共同操纵减压炉的四路流量。
在减压塔的先进控制策略中增加了换热终温的优化控制目标,以尽可能地利用减压塔各个侧线的高温热源,减少加热炉的能源消耗,使得装置总体热量回收效率提高,原油换热终温稳定在300e以上,降低了燃料消耗和电耗,使装置的能耗有较大幅度的降低。
基于这样的控制策略,减压部分先进控制器变量列表如表3和表4。
表3减压先进控制器变量列表受控变量(CV)操作变量(M V)干扰变量(DV)减压塔顶温度减顶回流量减压塔进料量减一线抽出温度减二线流量减压塔顶残压减二线抽出温度减三线流量减三线抽出温度减四线流量减四线抽出温度减一中流量减二线粘度减二中流量减三线粘度常一线热虹吸温度换热终温表4减压炉中间控制器变量列表受控变量(CV)操作变量(M V)干扰变量(DV)减压炉一路进料出口温度减压炉一路进料流量常压塔进料量减压炉二路进料出口温度减压炉二路进料流量减压炉三路进料出口温度减压炉二路进料流量减压炉四路进料出口温度减压炉二路进料流量常压塔底液位5结论先进控制器于2006年l2月在常减压蒸馏装置上开始投用,经过近半年的运行实践来看,取得了较好的效果,解决了原油性质变化对工艺平稳和产品质量目标的影响,软测量计算结果准确,实现了增产航煤、柴油的目的。