轴承钢棒材超快速冷却的试验研究
超快冷技术在轴承钢网状碳化物控制上的应用
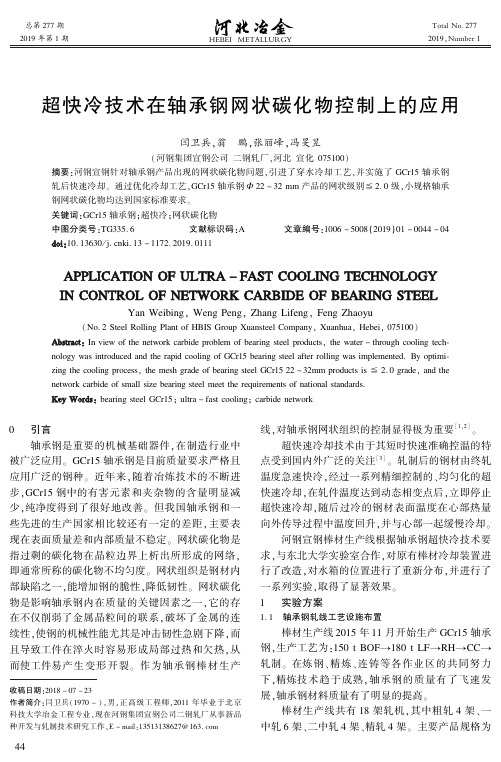
河北冶金 2019 年第 1 期
Φ 22 ~ Φ 70 mmꎮ 在线水箱有 4 套ꎬ每套水箱有 4 条不同内径的管道ꎬ可以根据不同的生产需求组合 运用ꎮ 水箱采用圆环喷射式冷却装置进行冷却ꎬ水 箱中冷却管和反水管靠调整环缝尺寸来控制进水 量ꎬ进入冷却器中的水经环形喷头以高速沿着钢材
轧后快速冷却ꎮ 通过优化冷却工艺ꎬGCr15 轴承钢 Φ 22 ~ 32 mm 产品的网状级别≦ 2. 0 级ꎬ小规格轴承
钢网状碳化物均达到国家标准要求ꎮ
关键词:GCr15 轴承钢ꎻ超快冷ꎻ网状碳化物
中图分类号:TG335. 6 文献标识码:A
文章编号:1006 - 5008(2019)01 - 0044 - 04
1. 1 轴承钢轧线工艺设施布置
棒材生产线 2015 年 11 月开始生产 GCr15 轴承 钢ꎬ生产工艺为:150 t BOF→180 t LF→RH→CC→ 轧制ꎮ 在炼钢、精炼、连铸等各作业区的共同努力 下ꎬ精炼技 术 趋 于 成 熟ꎬ 轴 承 钢 的 质 量 有 了 飞 速 发 展ꎬ轴承钢材料质量有了明显的提高ꎮ 棒材生产线共有 18 架轧机ꎬ其中粗轧 4 架、一 中轧 6 架、二中轧 4 架、精轧 4 架ꎮ 主要产品规格为
收稿日期:Байду номын сангаас018 - 07 - 23 作者简介:闫卫兵(1970 - ) ꎬ男ꎬ正高级工程师ꎬ2011 年毕业于北京 科技大学冶金工程专业ꎬ现在河钢集团宣钢公司二钢轧厂从事新品 种开发与轧制技术研究工作ꎬE - mail:13513138627@ 163. com
44
线ꎬ对轴承钢网状组织的控制显得极为重要[1ꎬ2] ꎮ 超快速冷却技术由于其短时快速准确控温的特 点受到国内外广泛的关注[3] ꎮ 轧制后的钢材由终轧 温度急速快冷ꎬ经过一系列精细控制的、均匀化的超 快速冷却ꎬ在轧件温度达到动态相变点后ꎬ立即停止 超快速冷却ꎬ随后过冷的钢材表面温度在心部热量 向外传导过程中温度回升ꎬ并与心部一起缓慢冷却ꎮ 河钢宣钢棒材生产线根据轴承钢超快冷技术要 求ꎬ与东北大学实验室合作ꎬ对原有棒材冷却装置进 行了改造ꎬ对水箱的位置进行了重新分布ꎬ并进行了 一系列实验ꎬ取得了显著效果ꎮ 1 实验方案
GCr15轴承钢轧制“穿水”冷却工艺的研究
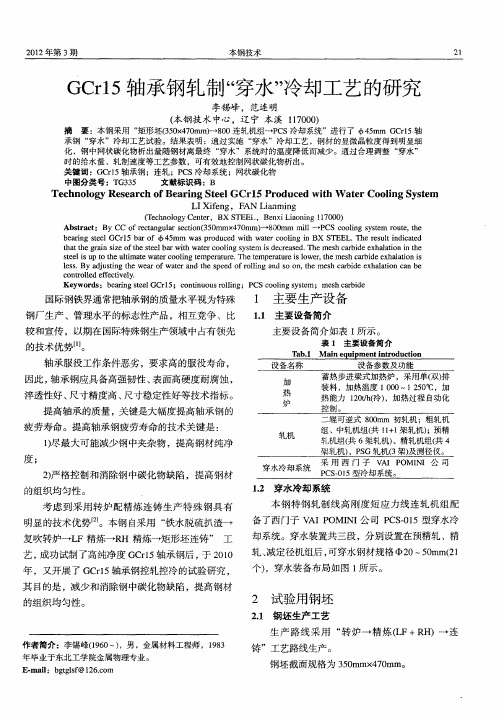
21 0 2年第 3 期
本钢技术
2 1
G r5 C l 轴承 钢轧 制“ 穿水 ” 冷却工艺 的研究
李锡峰 ,范连 明 ( 钢技 术 中心 ,辽 宁 本 溪 17 0 ) 本 1 0 0
摘 要 :本钢采用 “ 矩形坯(5 x 7 m - 8 0连轧机组一P s冷却系统”进行 了 4 m G r5轴 3 0 4 0 m)+ 0 c 5 m C l 承钢 “ 穿水 ”冷却 工艺试验 。结果表明 :通过实施 “ 穿水 ”冷却工艺 ,钢材 的显微晶粒度得到 明显细 化 ,钢 中网状 碳化物析出量随钢材离最终 “ 穿水 ”系统时 的温度降低而减少 。通过合理调整 “ 穿水” 时 的给 水量 、轧制 速度等工 艺参数 ,可有效地控制网状碳化物析出 。 关键词 : C 1 轴 承钢 ;连轧 ;P S冷却系统 ;网状碳化物 G r 5 C 中图分类 号 :T 3 G35 文献标识码 :B Te hn o y Re e r h fBe rng St e Cr 5 Pr d e t W a e o i y t m c ol g s a c o a i e l G l o uc d wih t r Co lng S s e
轴承钢快速冷却工艺介绍

RAL
控温轧制,由于较低终 P P的球团直径不仅与转变温
轧温度,少量再结晶发 生,奥氏体晶粒粗大
高温终轧,利于细化奥
球 团
度有关,还与奥氏体晶粒的 大小有关,随着转变温度降 低以及奥氏体晶粒细化而减
氏体晶粒
直 小,奥氏体晶粒细小,单位
在连续冷,P的转变温度越低, 片层间距越小,因为GCr15中 领先相M3C,由于形成温度降
GCr15轴承钢在轧后奥氏体状态下的冷却 过程中,二次碳化物在奥氏体晶界呈网状析 出。GCr15网状碳化物析出的温度范围一般 在700℃~900℃,大量析出碳化物温度为 700℃~850℃ 。
RAL 轧后快冷对网状碳化物影响
轧后实行快冷加快在网状碳化物析出温度区 间的冷却速度,避免在此区间停留,可以得到 分散细小的碳化物,达到破除网状碳化物的要 求,而且轧后快速冷却,过冷度增大,降低组 元的扩散系数,也会达到减小二次碳化物厚度 的作用。
RAL
应用
应用于宝钢特殊钢。
RAL
应用
RAL
应用
RAL
谢谢各位
RAL
轴承钢(GCr15)棒材连轧 快速冷却新工艺
轧制技术及连轧自动化国家重点实验室 东北大学
2007. 7. 20
RAL
1. 课题背景 2. 新型快冷工艺介绍 3. 结论
RAL 背景
网状碳化物析出直接影响轴承钢的质量。 我国的轴承钢质量还是有明显差距。过去
我们常说:“轴承钢质量有差距,主要是由于 设备落后”
目前有许多工厂宣称:”我厂拥有世界一 流的轧机”
RAL 现 状
控制网状碳化物析出常规的一种说法 是:采用控轧控冷工艺。
在生产中采用的方法是低温轧制 实际效果并不好:1)轧制不方便, 2)质量不稳定
高碳铬轴承钢棒材轧后控制冷却与快速球化工艺
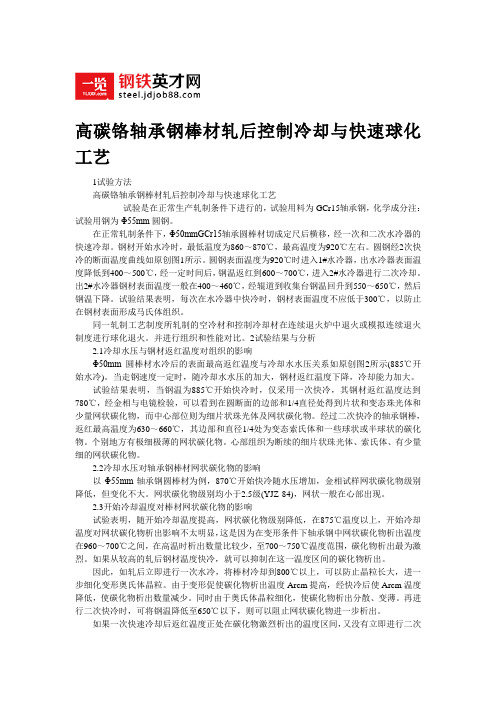
高碳铬轴承钢棒材轧后控制冷却与快速球化工艺1试验方法高碳铬轴承钢棒材轧后控制冷却与快速球化工艺试验是在正常生产轧制条件下进行的,试验用料为GCr15轴承钢,化学成分注:试验用钢为Φ55mm圆钢。
在正常轧制条件下,Φ50mmGCr15轴承圆棒材切成定尺后横移,经一次和二次水冷器的快速冷却。
钢材开始水冷时,最低温度为860~870℃,最高温度为920℃左右。
圆钢经2次快冷的断面温度曲线如原创图1所示。
圆钢表面温度为920℃时进入1#水冷器,出水冷器表面温度降低到400~500℃,经一定时间后,钢温返红到600~700℃,进入2#水冷器进行二次冷却。
出2#水冷器钢材表面温度一般在400~460℃,经辊道到收集台钢温回升到550~650℃,然后钢温下降。
试验结果表明,每次在水冷器中快冷时,钢材表面温度不应低于300℃,以防止在钢材表面形成马氏体组织。
同一轧制工艺制度所轧制的空冷材和控制冷却材在连续退火炉中退火或模拟连续退火制度进行球化退火。
并进行组织和性能对比。
2试验结果与分析2.1冷却水压与钢材返红温度对组织的影响Φ50mm圆棒材水冷后的表面最高返红温度与冷却水水压关系如原创图2所示(885℃开始水冷)。
当走钢速度一定时,随冷却水水压的加大,钢材返红温度下降,冷却能力加大。
试验结果表明,当钢温为885℃开始快冷时,仅采用一次快冷,其钢材返红温度达到780℃,经金相与电镜检验,可以看到在圆断面的边部和1/4直径处得到片状和变态珠光体和少量网状碳化物,而中心部位则为细片状珠光体及网状碳化物。
经过二次快冷的轴承钢棒,返红最高温度为630~660℃,其边部和直径1/4处为变态索氏体和一些球状或半球状的碳化物。
个别地方有极细极薄的网状碳化物。
心部组织为断续的细片状珠光体、索氏体、有少量细的网状碳化物。
2.2冷却水压对轴承钢棒材网状碳化物的影响以Φ55mm轴承钢圆棒材为例,870℃开始快冷随水压增加,金相试样网状碳化物级别降低,但变化不大。
以超快速冷却为核心的新一代技术

以超快速冷却为核心的新一代技术The New Generation TMCP with rhe KeyTechnology of Uletra Fast Cooling王国栋摘要针对传统TMCP技术采用“低温大压下”和“微合金化”的问题,利用连续轧制的大变形和应变积累,提出以超快速冷却技术为核心的新一代控制轧制和控制冷却技术的大变形和应变积累,提出以超快速冷却技术为核心的新一代控制轧制和控制冷却技术(NG-TMCP),描述了它的技术特征和材料特点,指出这是一项节省资源和能源,有利于材料循环利用,促进社会可持续发展的新技术。
1 TMCP技术及其特征控制轧制和控制冷却技术,即TMCP,是20世纪钢铁业最伟大的成就之一。
正是因为有了TMCP技术,钢铁业才能源源不断地向社会提供越来越优良的钢铁材料,支撑着人类社会的发展和进步。
控制轧制和控制冷却技术的目标是实现晶粒细化和细晶强化。
在控制轧制和控制冷却技术的发展历程中,人们首先认识到的是控制轧制,其核心思想是对奥氏体硬化状态的控制,即通过变形的奥氏体中积累大量的能量,力图在轧制过程中获得处于硬化状态的奥氏体,为后续的相变过程中实现晶粒细化做准备。
控制轧制的基本手段是“低温大压下”和添加微合金元素。
所谓“低温”是在接近相变点的温度进行变形,由于变形温度低,可以抑制奥氏体的再结晶,保持其硬化状态,“大压下”是指施加超出常规的大压下量,这样可以增加奥氏体内部储存的变形能,提高硬化奥氏体程度。
增加微合金元素,例如Nb,是为了提高奥氏体的再结晶温度,使奥氏体在比较高的温度即处于未再结晶区,因而可以增大奥氏体在未结晶区的变形量,实现奥氏体的硬化。
图1图1控制轧制和控制冷却为了突破控制轧制的限制,同时也是为了进一步强化钢材的性能,在控制轧制的基础上,又开发了控制冷却技术,控制冷却的核心思想,是对处于硬化状态奥氏体相变过程进行控制,以进一步细化铁素体晶粒,甚至通过相变强化得到贝氏体等强化相,进一步改善材料的性能。
超快速冷却棒材组织转变的元胞自动机模拟的开题报告

超快速冷却棒材组织转变的元胞自动机模拟的开题报告一、课题研究背景随着现代科技的不断发展,材料工程领域的研究成为了社会各方关注的焦点。
材料的性能和结构与其组织类型密切相关。
因此,利用计算机科学手段来研究材料的结构和性能是非常必要的。
超快速冷却(quenching)是实验室中常用的方法之一,通过快速降温来改变材料的性质和结构,这种方法在生产和制造中广泛应用。
超快速冷却棒材是目前一种热处理材料厂商广泛采用的产品,能实现对金属材料的高效处理。
超快速冷却棒的组织结构对材料的性能具有显著影响,而对组织结构的理解和研究主要依赖于实验研究。
然而,由于实验成本高昂、制约时间长等原因,需要寻找其他方法来研究组织转变的过程。
元胞自动机是一种基于离散时间和空间、局部交互和同步更新的计算模型,广泛应用于物理和生物系统、社会科学和工程技术等多个领域。
通过构建元胞自动机模型,可以模拟材料的结构和性能,从而研究材料的组织结构与性能之间的关系。
二、研究内容和目标本研究旨在基于元胞自动机模型,模拟超快速冷却棒材料的组织转变过程,并探究不同冷却速率、材料成分等因素对组织结构的影响。
具体来说,我们将从以下几个方面展开研究:1. 构建超快速冷却棒材料的元胞自动机模型。
2. 考虑材料的成分、结构和温度等因素,分析不同参数下元胞自动机模型的演化和组织结构的变化。
3. 比较不同冷却速率、材料成分等因素对超快速冷却棒材料的组织结构和性能的影响。
三、研究方法和步骤本研究采用元胞自动机模拟的方法,通过建立超快速冷却棒材料的元胞自动机模型,研究材料组织结构与性能之间的关系。
具体步骤如下:1. 收集超快速冷却棒材料的相关数据和实验结果,确定模型的基础参数,如材料的成分、结构和温度等因素。
2. 构建元胞自动机模型,确定元胞状态以及元胞间的交互规则。
根据元胞自动机模型的特点和实际情况,设计合适的模型结构。
3. 针对模型中的每个元胞,考虑其周围相邻元胞的状态和材料属性,根据设定的交互规则对其状态进行更新。
GCr15轴承钢高温变形后控冷工艺的研究
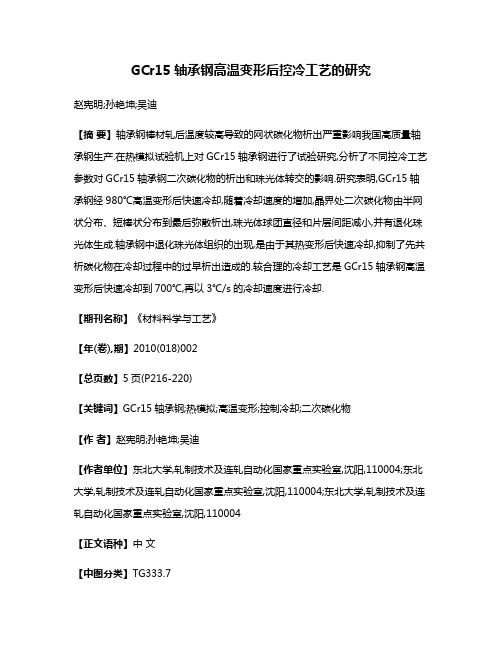
GCr15轴承钢高温变形后控冷工艺的研究赵宪明;孙艳坤;吴迪【摘要】轴承钢棒材轧后温度较高导致的网状碳化物析出严重影响我国高质量轴承钢生产.在热模拟试验机上对GCr15轴承钢进行了试验研究,分析了不同控冷工艺参数对GCr15轴承钢二次碳化物的析出和珠光体转交的影响.研究表明,GCr15轴承钢经980℃高温变形后快速冷却,随着冷却速度的增加,晶界处二次碳化物由半网状分布、短棒状分布到最后弥散析出,珠光体球团直径和片层间距减小,并有退化珠光体生成.轴承钢中退化珠光体组织的出现,是由于其热变形后快速冷却,抑制了先共析碳化物在冷却过程中的过早析出造成的.较合理的冷却工艺是GCr15轴承钢高温变形后快速冷却到700℃,再以3℃/s的冷却速度进行冷却.【期刊名称】《材料科学与工艺》【年(卷),期】2010(018)002【总页数】5页(P216-220)【关键词】GCr15轴承钢;热模拟;高温变形;控制冷却;二次碳化物【作者】赵宪明;孙艳坤;吴迪【作者单位】东北大学,轧制技术及连轧自动化国家重点实验室,沈阳,110004;东北大学,轧制技术及连轧自动化国家重点实验室,沈阳,110004;东北大学,轧制技术及连轧自动化国家重点实验室,沈阳,110004【正文语种】中文【中图分类】TG333.7轴承在机械产品和工程结构中应用十分广泛,轴承钢组织中碳化物的尺寸、形态和分布直接影响其接触疲劳强度和力学性能.GCr15轴承钢在轧后奥氏体状态下的冷却过程中,有二次碳化物析出,并在奥氏体晶界形成网状碳化物.如何降低网状碳化物级别,是热轧轴承钢急需解决的重大问题之一[1].钢材热变形后通过控制冷却可以改善其组织性能,细化奥氏体晶粒,抑制或延迟碳化物在冷却过程中的过早析出[2].近年来,在轴承钢生产领域,运用控轧控冷工艺解决网状碳化物严重析出问题已经开展了大量的工作,并取得一定的成果.轴承钢的轧后超快速冷却能够使碳化物微细、弥散析出[3].GCr15滚动轴承钢原始组织中碳化物的弥散均匀分布,直接提高其使用寿命 .本文以建立的CCT曲线为依据,对轴承钢热变形后不同冷却工艺进行模拟,分析了高温变形后冷却速度对轴承钢组织的影响,以期抑制轴承钢网状碳化物的析出,得到细小片层状珠光体组织.试验所用材料为由GCr15轴承钢棒材经过线切割制成Φ8 mm×15 mm圆棒,化学成分如表1所示.试验钢连续冷却转变曲线的测定和高温变形后快速冷却工艺模拟分别在Gleeble1500热模拟试验机和东北大学国家重点实验室自主研发的MMS-300多功能热力模拟试验机上进行,试样两端涂抹石墨粉以减少端部摩擦所造成的鼓肚效应.热模拟试验后将试样沿横向在靠近热电偶焊点处剖开,磨抛后采用4%硝酸酒精溶液腐蚀制成金相试样,组织观察在LEICA DMIRM多功能金相显微镜和FEI-Quanta 600扫描电镜上进行.对高温变形后不同冷速下的试样在1/2半径处进行布氏硬度试验.为了准确分析采用不同冷却速度对二次碳化物析出的影响,对热变形后不同冷却速度连续冷却到室温的试样进行淬-回火试验,经4%硝酸酒精溶液深腐蚀,挑选网状碳化物最严重区域,按照GB/T18254-2002进行网状评级.首先对GCr15钢进行CCT曲线的测定.将试样以10℃/s加热至奥氏体化温度1100℃,保温300 s后以10℃/s冷却至不同的变形温度,进行不同变形量单道次压缩变形,然后分别以不同连续冷却速度0.5、1、2、3、4、5、8、10、20、40、200℃/s冷却至室温.其中,变形温度(θ)和变形量(ε)分别为980℃和40%,变形速率为5/s,试验工艺如图1(a)所示.然后对其高温变形后快速冷却工艺进行模拟试验.将试样以10℃/s加热到1100℃,保温300 s后以10℃/s冷却至980℃,在980℃进行变形量为 40%的压缩变形,再以10℃/s的冷却速度冷却到700℃后,分别以不同冷却速度连续冷却到室温.具体试验工艺见图1(b).图2(a)为GCr15轴承钢980℃在40%变形条件下的CCT曲线.其中A、C、P分别代表奥氏体、碳化物和珠光体.对其高温变形后分别以1、3、5℃/s的冷却速度冷却室温,其冷却路径示意图见图2(b)中的粗线箭头.GCr15轴承钢高温变形后以10℃/s冷却到700℃,再分别以1、3、5℃/s冷却速度(v)冷却至室温的金相组织如图3所示.图3中,GCr15轴承钢高温变形后以10℃/s冷却到700℃,在接下来的冷却过程中,随着冷却速度的增加,晶界处二次碳化物析出减少.冷却速度为1℃/s时,呈网状连接的二次碳化物在晶界处仍隐约可见(图3(a));冷却速度增加到3℃/s时,晶界处仍有少量白色二次碳化物析出,但晶界处二次碳化物为短棒状,且网状结构已极大的减轻(图3(b));冷却速度达到5℃/s时由于冷却速度较快,在珠光体转变区域停留时间过短,残余奥氏体没有完全发生珠光体转变,室温组织如图3(c)所示,其中灰黑色基体组织为珠光体,灰白色块状组织为淬火马氏体和残留奥氏体组织,晶界处没有发现白色网状二次碳化物析出.图4为以不同冷却速度冷却到室温后对应的扫描电镜照片.图4中,GCr15钢高温变形后冷却速度为1℃/s时,扫描电镜下可以看到晶界处呈较为明显的网状分布的二次碳化物,而且,由于冷却速度相对较慢,珠光体球团直径和组织片层间距相对较大(图4(a));冷却速度为3℃/s时,不仅网状二次碳化物分布不再明显,而且,珠光体球团直径和片层间距相对减小(图4(b));冷却速度为5℃/s时,组织中已看不到网状二次碳化物,得到马氏体和珠光体的混晶组织(图4(c)).将上述的GCr15钢试样淬火-回火,其金相组织如图5所示.从图5可以看到,试验钢经淬-回火后深腐蚀,其组织为黑色回火马氏体及其上分布的白色二次碳化物.随着冷却速度变化,其基体上分布的白色碳化物数量和形状也发生变化.冷却速度1,3,5℃/s所对应的二次碳化物网状级别依次为4,2~3,1~2.热变形后以1℃/s连续冷却到室温,二次碳化物呈现不完整的网状分布,网状级别为4级;冷却速度为3℃/s时,由于冷却速度增加,二次碳化物析出量减少,网状趋势大大减弱,组织中二次碳化物已大部分呈断续的短棒状甚至点状,少部分由网状变为条状分布,评定级别应在2~3;冷却速度进一步增大达到5℃/s时,二次碳化物虽未完全弥散分布,但至多呈现点条状分布,完全看不到网状结构,网状级别在1~2级,达到标准.硬度测试表明,GCr15轴承钢980℃高温变形后分别以1℃/s冷却速度冷却,其布氏硬度最低,平均为HB354;以3℃/s冷却,其布氏硬度明显升高,平均为HB360;而以5℃/s冷却时,其布氏硬度最高,平均值达HB373.这是由于试样中晶界处二次碳化物随连续冷却速度增加依次从半网状、短棒状到弥散分布演化的结果.GCr15轴承钢属于过共析钢,由于碳含量较高,自奥氏体区连续冷却过程中,随着温度降低,将导致碳从过饱和奥氏体中析出,形成富铬的碳化物,即首先从奥氏体中析出先共析二次碳化物.通常,这种二次碳化物会优先在晶界上以仿晶界型网状形式排列形核长大[5].二次碳化物的析出主要取决于冷却速度,其析出的数量不仅与碳在奥氏体中的过饱和度有关,而且与碳化物形成元素在奥氏体中的扩散条件有关.轴承钢中C、Cr等元素的扩散受温度影响很大.这些元素沿奥氏体晶界的扩散速度远远大于晶内扩散速度(相差102~103倍),这也是二次碳化物多沿晶界析出,从而形成断续或者连续的网络状组织的原因.通过对CCT曲线分析可知,GCr15钢在热变形后的连续冷却过程中,二次碳化物析出主要温度区域为850~700℃,珠光体转变主要温度区域为750~500℃(图2).GCr15轴承钢在连续冷却过程中,当冷却速度缓慢时,由于晶界处缺陷多,C、Cr等碳化物形成元素在缓慢冷却过程中首先扩散到晶界处,在晶界处聚集长大、并置换铁形成Cr的合金碳化物,这些合金碳化物大量析出并连接成骨骼状紧密网状组织,形成网状碳化物.随着冷却速度增加,虽然仍然有C、Cr元素会向晶界处扩散并在晶界处聚集长大,但由于冷却速度增大,在二次碳化物析出区停留时间减小,C、Cr在高温区扩散时间减少,因此,晶界处析出的二次碳化物数量减少.试验钢高温变形后快速冷却至700℃以下,冷却速度足以快速通过二次碳化物析出温度区,然后减慢冷却,将使过冷奥氏体在珠光体转变温度区域完全发生珠光体转变.轴承钢晶界处二次碳化物随连续冷却速度增加而发生的形态变化,根据第二相强化理论,位错线以奥罗万模型绕过钢中的这种二次碳化物(第二相)质点,显然,随着相邻质点的间距减小,位错线的运动阻力增加,即质点的数量越多、越弥散,轴承钢的强度和硬度越高.当GCr15轴承钢试样以5℃/s冷却时,晶界处二次碳化物分布相对最为弥散(图5(c)),强度最高.由于硬度值是表征材料强度和韧性等一系列不同物理量组合的一种综合性能指标,因此,表现出了随冷却速度增加,试样中布氏硬度平均值增高的变化趋势.通常,过共析钢在发生珠光体转变前,会有先共析渗碳体的析出,即发生先共析转变.平衡状态下先共析碳化物的析出温度和成分范围表明,当过饱和奥氏体快速冷却到相变点以下的区域时,则会因同时对铁素体和渗碳体过饱和而直接进行珠光体转变[6].GCr15轴承钢高温变形后快速冷却至700℃以下,抑制了先共析碳化物的析出.由700℃至室温,以1℃/s冷却速度冷却,由于冷速相对较慢,钢在700℃以下相对较高的温度停留时间较长,发生先共析碳化物的析出,并在缓慢冷却过程中沿晶界处聚集长大并连接成网状形成网状碳化物,剩余奥氏体中含碳量则不断降低到共析点时才发生珠光体转变.由于碳化物在700℃以上的高温尚来不及析出,因此,碳化物网状结构并不十分明显.以3℃/s冷却时,由于冷速相对加快,过冷奥氏体在先共析碳化物析出区停留时间减少,虽然不能完全抑制先共析碳化物的网状析出,但先共析碳化物析出量明显减少,碳化物网状结构极大的减弱.以5℃/s冷却,由于冷速很快,阴影区浓度差值变大,则珠光体转变前先共析碳化物的析出及聚集长大非常困难,网状碳化物的析出被完全消除,GCr15钢由700℃被过冷到阴影区将同时析出铁素体和渗碳体,形成伪珠光体组织,达到了抑制网状碳化物析出的目的.上述网状碳化物析出的原理可以通过图2中的CCT曲线,在不同冷却速度条件下各相的析出过程得到合理的解释.GCr15轴承钢在980℃经40%的压缩变形,变形过程中所消耗的功,部分以形变储能形式存在,造成晶体点阵畸变和位错密度的增高,有利于C和Fe原子的晶体点阵重构,变形使能量升高,相变驱动力增大.同时,GCr15钢在700℃冷却速度加快,过冷度增大,亦使珠光体的相变驱动力增大.所以,珠光体的形核率增大.此外,变形在奥氏体中形成变形带,变形带可以起到分割奥氏体晶粒的作用,即奥氏体晶粒内部产生的变形带可以将奥氏体晶粒分割成几个小区域,因而增加了珠光体晶核的形核部位[7-8].变形对相变的加速作用还由于奥氏体晶界会发生应变集中,从而提高了晶界上珠光体晶核的形核率.因此,奥氏体向珠光体转变时珠光体晶核不仅可以在原奥氏体晶界上生成,而且可以在奥氏体晶粒内部生成,单位体积内晶界面积增大,达到了细化晶粒的目的,珠光体团尺寸变小.钢在700℃以不同冷却速度冷却,冷却速度增大,较低温度发生铁素体和渗碳体同时析出的伪共析反应.由于较大冷速使转变温度降低,碳原子扩散能力减小,不易进行较大距离迁移,渗碳体片和铁素体片逐渐变薄缩短.由于其长大速度减慢,珠光体团的轮廓也由块状逐渐变成扇形、团絮状等,珠光体球团直径和片层间距都更加细小,部分渗碳体片断开,呈短棒状或颗粒状.出现较为理想的退化珠光体组织.当然,冷却速度过大,虽然消除了网状碳化物,但在得到退化珠光体组织的同时,组织中同时也出现了马氏体,马氏体在使钢强化的同时损失了塑性,这是需要避免的.因此,GCr15轴承钢在700℃冷却时,应当严格控制其终冷温度,其冷却速度亦不易过大.高温变形后经过以3℃/s的较快冷却速度冷却,能够减小珠光体球团直径和珠光体片层间距,并基本消除网状碳化物,获得退化珠光体组织,因此,以3℃/s的冷却速度冷却应相对较为合适.GCr15轴承钢产品中存在大量碳化物.该钢高温变形后以10℃/s冷却到700℃以下,再以3℃/s冷却速度冷却,抑制了晶界处网状碳化物析出,热轧轴承钢基本能够得到细小的片层珠光体组织.1)GCr15轴承钢采用高温变形后以10℃/s冷却度速冷却至700℃以下,冷却速度足以快速通过二次碳化物析出温度区,能够有效地改善其组织形态,模拟试验取得了良好效果.2)GCr15轴承钢高温变形后快速冷却到700℃,再分别以不同冷却速度冷却.冷速较慢时,组织中仍含有网状碳化物;冷速过快,组织中淬火马氏体出现;当以3℃/s冷却速度冷却时,二次碳化物呈网状分布不再明显,而且,珠光体球团直径和组织片层间距相对减小,获得退化珠光体组织.因此,以3℃/s的冷却速度冷却相对较为合理.3)GCr15轴承钢中退化珠光体组织的出现,是由于其热变形后控制冷却,抑制了先共析碳化物在冷却过程中的过早析出,使其最终在基体组织中弥散析出,碳原子扩散能力低,无法进行较大距离迁移造成的.【相关文献】[1] WANG Y,YAN F G,WANG P.Finite element analysis of precision hard cutting using different cutting edge preparation[J].Applied Mechanics and Materials,2008,10-12:353-358.[2]刘宗昌.珠光体转变与退火[M].北京:化学工业出版社,2007.[3]王国栋,新一代TMCP的实践和工业应用举例[J].上海金属,2007,30:1-4.[4]郑逊昭,夏玉洲,陈文耀.GCr15轴承钢接触疲劳亚表面孔洞的形成[J].材料科学与工艺,1996,4 (3):29-33.[5]霍尼库姆R W K著.钢的显微组织和x`性能[M].北京:冶金工业出版社,1985.[6]胡光立,谢希文.钢的热处理[M].西安:西北工业大学出版社,2004.[7] UESUGI T.Recent development of bearing steel in japan transactions of the iron and steel[J].Institute of Japan,1988(11):893-899.[8]田村今男著.王国栋,刘振宇,熊尚武,译.高强度低合金钢的控制轧制与控制冷却[M].北京:冶金工业出版社,1992.。
轴承钢快速冷却工艺介绍
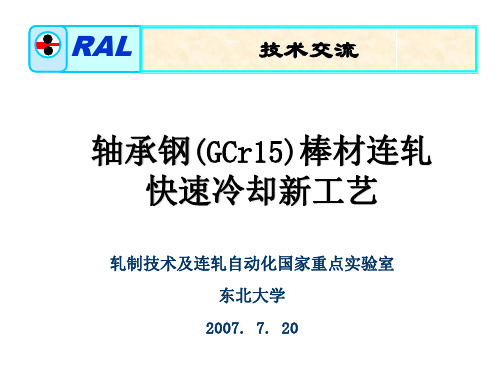
RAL
GCr15在轧后快速冷却时应严格注意形成” GCr15在轧后快速冷却时应严格注意形成” 在轧后快速冷却时应严格注意形成 淬火”,防止表面出现马氏体组织。 淬火” 防止表面出现马氏体组织。 也不能够使快速冷却穿水“返红” 也不能够使快速冷却穿水“返红”的温度超 过700℃,在高温区停留时间过长,使得碳化物 700℃,在高温区停留时间过长, 析出严重,从而达不到快速冷却的效果。 析出严重,从而达不到快速冷却的效果。
RAL
目前存在的问题
常规的控轧、 常规的控轧、控冷理论没有解释型钢 轧制(主要是连轧) 轧制(主要是连轧)中的现象 例如: 例如: 1)高速变形奥氏体的组织演变 2)变形温度升高时γ-α的演变 变形温度升高时γ
RAL
Fm/Fc
加工强化
1.6
细化晶粒软化
1.4 1.2 1
累积应变及未 再结晶强化
1
RAL
技术交流
轴承钢(GCr15)棒材连轧 快速冷却新工艺
轧制技术及连轧自动化国家重点实验室 东北大学 2007. 7. 20
RAL
1. 课题背景 2. 新型快冷工艺介承钢的质量。 网状碳化物析出直接影响轴承钢的质量。 我国的轴承钢质量还是有明显差距。 我国的轴承钢质量还是有明显差距。过去 我们常说: 轴承钢质量有差距, 我们常说:“轴承钢质量有差距,主要是由于 设备落后” 设备落后” 目前有许多工厂宣称: 目前有许多工厂宣称:”我厂拥有世界一 流的轧机” 流的轧机”
RAL
现
状
控制网状碳化物析出常规的一种说法 是:采用控轧控冷工艺。 采用控轧控冷工艺。 在生产中采用的方法是低温轧制 实际效果并不好: 实际效果并不好:1)轧制不方便, 轧制不方便, 2)质量不稳定
轴承钢棒材超快冷却的运用研究

轴承钢棒材超快冷却的运用研究针对生产轴承钢棒材产品出现的网状碳化物问题,以国内某厂棒材连轧生产线为依据,对GCr15轴承钢轧后进行快速控制冷却的温度场进行模拟研究,并运用于实际生产中,取得了较好的效果。
结合现场条件所能采用的各种冷却工艺,利用计算机模拟方法,对冷却工艺进行了优化分析,使得GCr15轴承钢φ20~60的产品的网状级别≤2.0级,解决了中小规格棒材轴承钢网状碳化物达不到标准要求的问题。
轴承钢在冷却过程中抑制网状碳化物的析出,是改善和提高GCr15轴承钢性能的必要条件。
网状碳化物的级别高会降低轴承的疲劳寿命,导致在轴承加工的研磨过程中产生磨裂(龟裂);网状碳化物严重,不但球化退火不能消除,甚至在以后的淬火过程中仍有保留,并易产生淬火裂纹或成为疲劳裂纹的发源地之一,作为轴承钢棒材生产线,对轴承钢网状的控制显得极其重要。
1 轧制设备与工艺某轧制棒材车间共有22架轧机,粗、中、预精轧各6架(共18架),精轧4架,其主要生产规格为φ20~90;在线水箱有4套,每个水箱有3条不同内径的管道,根据不同的生产规格可分别运用或组合运用。
水箱采用高压喷嘴水冷却方式,1#、2#、水箱各长7m,有9个喷嘴组成(其中6个正吹,2个反吹,一个气吹);3A、3B水箱各长5m(其中4个正吹,2个反吹,一个气吹)。
水压1.5~1.8MPa,每小时最大耗水量1180L。
2 轴承钢轧后超快速冷却分析和建模2.1 轧后快速冷却分析轧后控冷工艺的传热过程大体包括以下两个阶段:第一阶段为急冷段,钢材离开精轧机组在终轧温度下,尽快进入快速冷却装置,进行快速冷却。
这个阶段的传热按受迫对流沸腾鱼湍流受迫对流传热两种方式进行。
钢进入冷却器后,由于钢表面温度大大高于水的饱和温度,水温剧增至沸点并气化,在钢壁上形成动态蒸汽膜。
此时射流水以≥1.0MPa压力冲击钢表面,全面打碎蒸汽膜,钢外壁的移动又促进了沸腾过程的进行,这种传热过程具有很高的热流量,使传热系数激增。
《热轧钢板超快速冷却工艺的研究》范文

《热轧钢板超快速冷却工艺的研究》篇一一、引言热轧钢板作为重要的金属材料,在汽车制造、机械制造、桥梁建筑等多个领域都有着广泛的应用。
为了满足工业发展的需求,热轧钢板的性能提升变得尤为重要。
超快速冷却工艺作为一项先进的钢铁制造技术,能显著改善热轧钢板的性能,因而成为了近年来的研究热点。
本文将对热轧钢板超快速冷却工艺进行研究,以期为工业生产提供理论支持。
二、热轧钢板超快速冷却工艺概述热轧钢板超快速冷却工艺,即通过高效率的冷却设备和方法,将高温状态下的热轧钢板在极短时间内降低到常温,以改善钢板的组织结构,从而提高其机械性能、抗腐蚀性能等。
这种工艺在保证钢板质量的同时,还能提高生产效率,降低能耗。
三、热轧钢板超快速冷却工艺的研究内容1. 冷却速率对热轧钢板性能的影响本研究首先关注了冷却速率对热轧钢板性能的影响。
通过对比不同冷却速率下的钢板性能,我们发现,适当的超快速冷却可以显著提高钢板的强度和韧性,同时也能提高其抗腐蚀性能。
这主要是因为超快速冷却可以使得钢板的组织结构更加均匀、致密。
2. 冷却过程中组织结构的变化本研究还关注了超快速冷却过程中钢板组织结构的变化。
通过金相显微镜和电子显微镜观察发现,超快速冷却能够使得钢板的组织结构变得更加致密、晶粒更加细小。
这种组织结构的改变,使得钢板的机械性能和抗腐蚀性能得到了显著提升。
3. 工艺参数的优化为了进一步提高超快速冷却工艺的效果,我们还对工艺参数进行了优化。
通过调整冷却设备的参数、优化冷却介质的选择等措施,我们成功提高了冷却效率,同时保证了钢板的性能和质量。
四、研究方法本研究采用了理论分析、实验研究和数值模拟相结合的方法。
首先,我们通过查阅文献和资料,对超快速冷却工艺的原理和影响因素进行了理论分析。
然后,我们设计了实验方案,通过实验研究了不同条件下超快速冷却对热轧钢板性能的影响。
最后,我们还采用了数值模拟的方法,对实验结果进行了验证和预测。
五、结论通过对热轧钢板超快速冷却工艺的研究,我们得出以下结论:1. 超快速冷却工艺可以显著提高热轧钢板的性能,包括强度、韧性以及抗腐蚀性能等。
《热轧钢板超快速冷却工艺的研究》范文

《热轧钢板超快速冷却工艺的研究》篇一一、引言随着现代工业的快速发展,热轧钢板因其良好的力学性能和较高的生产效率,在汽车、建筑、机械制造等领域得到了广泛应用。
然而,传统的热轧钢板生产工艺中,冷却环节往往存在冷却速度慢、效率低下等问题,这在一定程度上限制了产品的性能和应用范围。
因此,研究热轧钢板超快速冷却工艺,对于提高产品质量、生产效率和降低成本具有重要意义。
二、热轧钢板超快速冷却工艺的必要性超快速冷却工艺是指通过采用先进的冷却技术和设备,使热轧钢板在极短的时间内完成冷却过程。
这种工艺的必要性主要体现在以下几个方面:1. 提高产品性能:超快速冷却可以显著提高钢板的强度、硬度和耐磨性,同时改善其韧性和抗疲劳性能。
2. 扩大应用范围:超快速冷却工艺可以生产出满足不同领域需求的高性能钢板,如汽车制造、航空航天等。
3. 降低成本:通过提高生产效率和降低能耗,超快速冷却工艺可以降低企业的生产成本。
三、热轧钢板超快速冷却工艺的研究内容1. 冷却设备的研发:研究开发高效、可靠的超快速冷却设备,如喷水式、喷气式等设备,以满足不同钢种和工艺需求。
2. 冷却速度的优化:通过调整冷却设备的参数和工艺流程,研究不同钢种的最佳冷却速度,以达到最佳的力学性能和微观组织结构。
3. 微观组织结构的研究:通过金相显微镜、电子显微镜等手段,研究超快速冷却过程中钢板的微观组织结构变化,为优化工艺提供理论依据。
4. 力学性能的测试与分析:对超快速冷却后的钢板进行拉伸、冲击、硬度等力学性能测试,分析其性能变化规律,为实际应用提供参考。
四、热轧钢板超快速冷却工艺的应用及前景1. 应用领域:热轧钢板超快速冷却工艺已广泛应用于汽车制造、建筑、机械制造等领域,取得了显著的成果。
2. 技术进步:随着科技的不断发展,超快速冷却技术将进一步改进和完善,提高冷却效率和效果,拓宽应用范围。
3. 发展趋势:未来,热轧钢板超快速冷却工艺将与智能化、自动化技术相结合,实现生产过程的智能化控制和优化,提高生产效率和产品质量。
《2024年热轧钢板超快速冷却工艺的研究》范文

《热轧钢板超快速冷却工艺的研究》篇一一、引言随着现代工业的快速发展,对钢材的需求与日俱增,特别是在机械制造、建筑桥梁、船舶制造等重要领域中,对热轧钢板的质量与性能提出了更高的要求。
为了满足市场对高强度、高韧性、高耐腐蚀性等特性的需求,热轧钢板的加工工艺成为了研究的热点。
其中,超快速冷却工艺作为一种新型的加工技术,对于提高热轧钢板的综合性能具有显著的效果。
本文旨在研究热轧钢板超快速冷却工艺,探讨其工艺特点、影响因素及优化措施。
二、热轧钢板超快速冷却工艺概述热轧钢板超快速冷却工艺是一种通过快速降低钢板温度,以改善其组织和性能的加工技术。
该工艺主要利用高压水或冷却气体等介质,在极短的时间内将钢板从高温状态冷却至室温,从而达到优化钢板组织和性能的目的。
超快速冷却工艺具有冷却速度快、组织细化、性能提升等优点,在提高钢材的强度、韧性、耐磨性等方面具有显著效果。
三、热轧钢板超快速冷却工艺的特点及影响因素1. 工艺特点:(1)冷却速度快:超快速冷却工艺的冷却速度可达每秒数百至数千摄氏度,远高于传统冷却工艺。
(2)组织细化:快速冷却使得钢板的组织得到细化,提高了材料的力学性能。
(3)性能提升:通过优化组织和性能,提高了钢板的强度、韧性、耐磨性等。
2. 影响因素:(1)冷却介质:不同的冷却介质对钢板的冷却效果和组织性能有显著影响。
(2)冷却速度:冷却速度是影响钢板组织和性能的关键因素。
(3)钢板成分与初始状态:钢板的化学成分及初始组织状态对超快速冷却工艺的效果也有重要影响。
四、热轧钢板超快速冷却工艺的优化措施为了进一步提高热轧钢板超快速冷却工艺的效果,可以采取以下优化措施:1. 优化冷却介质:选择合适的冷却介质,以提高钢板的冷却效果和组织性能。
2. 控制冷却速度:根据钢板的特点和性能要求,合理控制冷却速度。
3. 调整钢板成分与初始状态:通过调整钢板的化学成分和初始组织状态,以提高超快速冷却工艺的效果。
4. 引入智能控制技术:利用计算机技术和自动化控制技术,实现超快速冷却工艺的智能化控制,提高生产效率和产品质量。
《2024年热轧钢板超快速冷却工艺的研究》范文
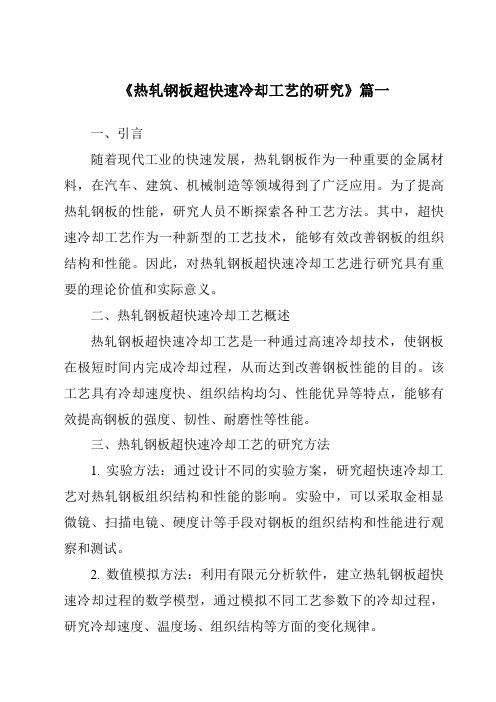
《热轧钢板超快速冷却工艺的研究》篇一一、引言随着现代工业的快速发展,热轧钢板作为一种重要的金属材料,在汽车、建筑、机械制造等领域得到了广泛应用。
为了提高热轧钢板的性能,研究人员不断探索各种工艺方法。
其中,超快速冷却工艺作为一种新型的工艺技术,能够有效改善钢板的组织结构和性能。
因此,对热轧钢板超快速冷却工艺进行研究具有重要的理论价值和实际意义。
二、热轧钢板超快速冷却工艺概述热轧钢板超快速冷却工艺是一种通过高速冷却技术,使钢板在极短时间内完成冷却过程,从而达到改善钢板性能的目的。
该工艺具有冷却速度快、组织结构均匀、性能优异等特点,能够有效提高钢板的强度、韧性、耐磨性等性能。
三、热轧钢板超快速冷却工艺的研究方法1. 实验方法:通过设计不同的实验方案,研究超快速冷却工艺对热轧钢板组织结构和性能的影响。
实验中,可以采取金相显微镜、扫描电镜、硬度计等手段对钢板的组织结构和性能进行观察和测试。
2. 数值模拟方法:利用有限元分析软件,建立热轧钢板超快速冷却过程的数学模型,通过模拟不同工艺参数下的冷却过程,研究冷却速度、温度场、组织结构等方面的变化规律。
3. 理论分析方法:结合金属学、材料科学等相关理论,分析超快速冷却工艺对热轧钢板组织结构和性能的影响机制,为优化工艺参数提供理论依据。
四、热轧钢板超快速冷却工艺的实验研究通过实验研究,我们发现超快速冷却工艺能够有效改善热轧钢板的组织结构和性能。
在实验中,我们采用了不同的冷却速度和温度制度,观察了钢板组织结构的变化规律。
结果表明,适当的超快速冷却工艺能够使钢板获得均匀细小的组织结构,提高钢板的强度和韧性。
此外,我们还研究了超快速冷却工艺对钢板耐磨性的影响,发现经过超快速冷却处理的钢板具有更好的耐磨性能。
五、热轧钢板超快速冷却工艺的优化与展望针对热轧钢板超快速冷却工艺,我们还需要进一步优化工艺参数,提高工艺的稳定性和可靠性。
未来,我们可以从以下几个方面进行研究和探索:1. 深入研究超快速冷却工艺对热轧钢板组织结构和性能的影响机制,为优化工艺参数提供更加准确的依据。
棒材轧后双线高效冷却系统的研制与应用

棒材轧后双线高效冷却系统的研制与应用1背景:棒材高效冷却系统的研制及其应用棒材热轧后的完整外观和内在质量以及它们在表面加工端处理有着十分重要的地位。
棒材表面的高效冷却也受到重视,因为冷却过程对棒材表面加工的品质有着极大的影响。
一般来说,冷却系统的设计主要考虑三个因素:一是冷却均匀,意味着棒材表面温度的均匀性要保证;二是冷却效率,要在有限的时间内,迅速地将棒材表面的温度降至最低;三是整个系统的空间占用面积要紧凑,既能节省设备空间,又省水、省电。
2研究基础高效节能的双线冷却系统,历来是热轧现场加工过程中的一大难题。
近年来,随着热轧技术的发展,双线高效冷却系统也逐渐得到重视。
双线冷却系统通常包括冷却管道和水供应系统,其空间利用率要求高,冷却管道必须完全包裹在棒材上,并能够有效传导热量,将热量传递到水供应系统,实现快速降温。
3研究方案本研究根据现代棒材快速转动热轧的工艺特点,主要采用的是双线高效冷却系统,重点研究了水供应、冷却管道和模拟分析等技术。
水供应系统可以有效利用棒材表面的冷却水,保证棒材表面快速降温,同时实现节能效果。
冷却管道采用宽度为80mm的双线结构,节省设备空间,同时减少设备的耗电量。
研究的模拟分析,较好的模拟了棒材轧后的表面冷却状态,得出了良好的冷却结果。
4运行结果研究表明,采用双线设计的高效冷却系统可以很好地满足棒材轧制过程中的冷却要求,充分发挥节能和节流的效果。
在研究试验中,实际操作中,仅在4.5m/min的轧制速度下,降温速率可以高达80°C/min,可获得稳定的冷却结果。
5结论本次研究研发的双线高效冷却系统解决了在表面加工过程中的冷却问题,既节能又高效。
本研究成果得到了广泛的应用,为工业提供可靠的冷却解决方案,使热轧技术更加可持续发展,受到社会各界的一致肯定。
- 1、下载文档前请自行甄别文档内容的完整性,平台不提供额外的编辑、内容补充、找答案等附加服务。
- 2、"仅部分预览"的文档,不可在线预览部分如存在完整性等问题,可反馈申请退款(可完整预览的文档不适用该条件!)。
- 3、如文档侵犯您的权益,请联系客服反馈,我们会尽快为您处理(人工客服工作时间:9:00-18:30)。
780 700
将冷却到室温后的棒材取中间部位制成试样 进行显微组织观察和显微硬度测试以及能谱线扫 描分析 ,并对其进行淬回火 (830 ℃ 保温 1 h 后油 淬 ,150 ℃ 回火 2 h) ,按照 JB/T1255 — 2001 标准 挑选网状 碳 化 物 最 严 重 区 域 进 行 网 状 碳 化 物 评
级[7
]
·
2 试验结果与分析
2 .1 超快速冷却对钢显微组织的影响 生产现场采用工艺 1 ,工艺 2 超快速冷却后
第 7 期 赵宪明等 : 轴承钢棒材超快速冷却的试验研究
949
的横断面 不 同 位 置 室 温 显 微 组 织 照 片 分 别 如 图 2 ,图 3 所示·
Commercial Test of Ultra-Fast Cooling for Bearing Steel Bar
ZHA O X ian-ming1 , S U N Y an-kun1 , W A NG Y ong-hong2
(1 .The State Key Laboratory of Rolling and Automation ,Northeastern University ,Shenyang 110004 ,China ;2 . Hebei Yongyang Iron and Steel Co .,Ltd .,Handan 057150 ,China .Correspondent :ZHAO Xian-ming ,E-mail : zhaoxm @ ral .neu .edu .cn)
足 ,造成轴承钢生产过程中经常出现网状碳化物 超标 ,严重影响其产品质量·在不改变原有热连轧 生产工艺的基础上 ,在连轧机后安装超快速冷却 系统 ,进行轴承钢棒材高温终轧后超快速冷却批 量工业化生产试验·通过高温终轧后超快速冷却 , 获得了具有理想组织 、性能 ,而其工艺能够为生产
现场所接受的轴承钢棒材产品·
对钢铁材料的整个热轧和轧后冷却过程进行 控轧控冷工艺技术 ,正在各种板材 、棒材以及型材 中广为应用[1 - 4] ·针对轴承钢棒材 ,采用新型控 冷方法 超快速冷却工艺 ,可以有效解决其在 终轧后冷却速度缓慢导致晶界处网状二次碳化物 的析出问题 ,改善其组织形态 ,细化高温奥氏体晶 粒[5 - 6]·这一新工艺不仅使二次碳化物在基体中 弥散析出 ,同时减小珠光体球团直径 ,细化珠光体 片层间距 ,得到断面上碳化物均匀分布的细小珠
的具体工艺参数如表 2 所示· 超快速冷却时三段水箱全部打开 ,总时间为
4 s ,水压为 0畅8 M Pa·其表面超快速冷却终冷温度 为 510 ℃ ,返红温度达到了 780 ℃ ;随着水压增加 到 1畅3 M Pa ,其表面超快速冷却终冷温度和返红 温度分别降低到 459 ,700 ℃ (工艺 1 ,工艺 2)·
%
C
Si
Mn
P
S
Cr
Ni
Cu
Mo
Ti
Al
1 .02 0 .22 0 .36 0 .11 0 .003 1 .48 0 .08 0 .15 0 .02 0 .002 0 .036
某特殊钢棒材厂原有的热连轧生产线上共有
22 架轧机 ,其中粗 、中 、预精轧各为 6 架 (共 18
架) ,精轧 4 架·连轧过程中轧制速度为 4畅5 m /s , 棒材经过连轧机组高温终轧后经过分段剪断再上 冷床进行缓冷·连轧机组后安装了 1 # ,2 # ,3 # 三 段超快速冷却器 ,冷却水箱的布置图如图 1 所示· 每套水箱有三条不同的内径管道 ,水箱采用高压 喷嘴水冷却方式 ,总供水量最大为 720 m3 /h ,每 段冷却器最大流量可达到 360 m3 /h·其中 1 # 水箱 长 8 m ,其中 5 个正吹 ,1 个反吹 ,1 个气吹 ;2 # , 3 # 水箱各长 5 m ,其中 4 个正吹 ,2 个反吹 ,1 个气 吹·3 # 水箱到冷床的距离为 22 m·水箱水压可以
(a) — 表面 ;(b) — 心部·
图 3 工艺 2 条件下显微组织 Fig .3 SEM images of the steel during schedule 2
(a) — 表面 ;(b) — 心部·
从图 2 中可以看到 ,矱30 mm 棒材经过工艺 1 超快速冷却后 ,棒材表面和心部组织为片层珠光 体和晶界处明显的白色网状二次碳化物·而经过 工艺 2 超快速冷却后 ,棒材表面部分和心部室温 显微组织均为细小的片层状珠光体 ,晶界处看不 到白色的网状二次碳化物析出(图 3)·此外 ,由于 心部冷却速度比表面低 ,虽然抑制了网状碳化物 的析出 ,珠光体球团直径和珠光体片层间距却都 比表面要大·将分别经过工艺 1 ,工艺 2 冷却到室 温后的 GCr15 棒材进行淬火 - 回火实验 ,进行二 次碳化物网状评级 ,其金相照片如图 4 所示·
表 2 工业试验中的具体参数
Table 2 Rolling parameters in commercial tests
工艺
矱
出炉温度 轧制速度 终轧温度 超快冷前温度 超快冷后温度 最高返红温度
编号 mm
℃
m·s - 1
℃
℃
℃
℃
1 2
30
1 150
4 .5
998
982 979
510 459
摘 要 : 在特殊钢棒材厂原有连轧生产线上 ,通过增设超快速冷却系统 ,对轴承钢棒材高温终轧后进行 超快速冷却工业试验·在连轧机组后增设三组超快速冷却系统·通过调节水压 、喷嘴孔大小以及开启水箱个 数 ,对 GCr15 轴承钢棒材进行高温终轧后超快速冷却·结果表明 :随着连续冷却速度增加 ,晶界处二次碳化物 中 C ,Cr 含量减小 ,珠光体球团直径和片层间距减小 ,显微硬度值增大·棒材断面不同位置的冷却速度均可以 达到抑制网状碳化物析出 、过冷奥氏体完全发生珠光体转变的冷却速度要求 ,网状碳化物级别小于 2 级 ,达到 轴承行业标准· 关 键 词 : 轴承钢棒材 ;超快速冷却 ;工业试验 ;冷却速度 ;网状碳化物 中图分类号 : TG 142 .41 文献标志码 : A 文章编号 : 1005-3026(2010)07-0947-06
1 试验材料及方法
在生产 现 场 工 业 化 批 量 试 生 产 的 轴 承 钢 为 矱30 mm 的 GCr15 钢棒材 ,其具体的化学成分如 表 1 所示·表 1 工业试验用钢的化Fra bibliotek成分(质量分数 )
Table 1 Chemical composition of the steel in commercial tests
Abstract : Commercial ultra-fast cooling industrialized tests were carried out after high temperature final rolling of the Cr15 bearing steel bar by installing three ultra-fast cooling systems in addition to the original continuous rolling line in a special steel plant . T he cooling rate w as controlled by readjusting water pressure , nozzle size and the number of turn-on taps of water tanks after high temperature deformation of steel bar . The results showed that the C and Cr contents at the grain boundaries of secondary carbides are reduced with the size of pearlite pellets and the pearlitic lamellar gaps both decreased but the micro-hardness increases along with the continuously increasing cooling rate .Moreover ,the cooling rate at anyplace on the cross section of the steel bar is available to restrain the precipitation of network carbides and transform all the overcooled austensites into pearlites .As a result ,the class of the network carbides is lower than the grade Ⅱ that is the professional standard . Key words : bearing steel bar ;ultra-fast cooling ;commercial test ;cooling rate ;network carbide
第31卷第7期 2010 年 7 月
东北大学学报 (自然科学版 ) Journal of Northeastern University (Natural Science)
Vol畅31 ,No .7 Jul . 2 0 1 0
轴承钢棒材超快速冷却的试验研究
赵宪明1 , 孙艳坤1 , 王永红2
(1 .东北大学 轧制技术及连轧自动化国家重点实验室 , 辽宁 沈阳 110004 ; 2 .河北永洋钢铁有限公司 , 河北 邯郸 057150)
光体组织· 轴承钢组织中碳化物的尺寸 、形态和分布直
接影响其使用寿命·通过实验室模拟轧制 、模拟冷 却以及理论分析表明 ,轴承钢轧后超快速冷却能 够使碳化物微细 、弥散析出[6] ·如能在生产现场 具体应用 ,将会具有重大的实际意义·