弹箭制造工艺学
武器系统与工程专业

武器系统与工程专业培养目标武器系统与工程专业培养具备武器系统总体或其子系统技术以及相关民用工程技术等方面的基础理论知识和工程实践能力,能在国家有关部门、科研单位、高等学校、部队、企业和管理部门从事系统设计、技术开发、产品制造、实验测试和科技管理方面工作的高级工程技术人才。
培养要求武器系统与工程专业学生主要学习武器系统总体和其子系统技术以及相关民用工程技术方面的基本理论和基本知识,学习机械、电子、计算机、力学等知识,了解发射运载、探测识别、跟踪制导、火力与起爆控制、弹药工程与安全技术和地面武器机动系统等知识,受到系统设计、技术综合、产品研制、实验测试及工程管理方面的基本训练,具备系统分析与综合、工程设计与计算、计算机应用、试验检测等方面的基本能力。
专业特色武器系统与工程所属学科为国家级重点学科,拥有国家重点实验室,国家首批博士点和博士后流动站。
师资队伍实力雄厚,具有多个高水平的研究方向,在现代火炮发射理论与技术,外弹道理论及弹箭空气动力与增程技术,武器系统瞬态实验与仿真,火箭导弹发射理论与技术,新概念武器等研究方面具有明显的特色与优势,在国内同专业中处于领先地位。
主要课程武器系统工程、机电系统分析与设计、发射动力学、空气动力学、流体力学、弹道力学、水物理场理论、中近程探测与识别技术、现代控制理论、制导原理及系统、传感与动态检测技术、系统建模与仿真、弹药终点效应、冲击动力学、爆炸技术、安全工程学、物理化学、高分子材料与工程、火(炸)药合成、燃烧与爆炸物理学、火工烟火技术、地面武器机动系统分析与综合、液压与液力传动、车辆电子技术、导航与稳定理论、机械制造工艺学等。
就业方向在国家有关部门、科研院所、高等院校、部队、企业和管理部门从事武器系统设计、技术开发、产品制造实验测试和科技管理方面工作。
弹药制造工艺学

弹药制造工艺学
弹药制造工艺学是一门研究弹药制造过程和技术的学科。
它涉及到弹药设计、材料选择、加工工艺、质量控制等方面的知识。
弹药制造工艺学的主要内容包括:
1. 弹药设计:根据弹药的用途和要求,进行弹药的结构设计和性能设计。
2. 材料选择:选择适合弹药制造的材料,如金属、火药、炸药等。
3. 加工工艺:包括弹药的成型、加工、装配等工艺,如铸造、锻造、车削、铣削、磨削等。
4. 质量控制:对弹药制造过程中的各个环节进行质量控制,确保弹药的质量和安全性。
5. 测试与评估:对制造完成的弹药进行性能测试和评估,以确保其符合设计要求。
弹药制造工艺学的研究对于提高弹药的性能、质量和安全性具有重要意义。
同时,它也对于保障国家安全和军事战斗力具有重要作用。
需要注意的是,弹药制造涉及到危险化学品的使用和处理,需要严格遵守相关的安全规定和操作规程。
弹箭零件机械加工工艺规程的编制

5.1.4矩阵式键盘的软件结构
(1)判断键盘中有无键按下 将全部行线置低电平,列线置高电平,然
后检测列线的状态,只要有一列上的一页电下平一为页 返回
1.并行输出 如图5-8所示,这是一个由单片机上一的页 P下1一口页 返回
[任务5.2]LED数码显示器接口设 讨
5. 2. 3静态显示电路的软件结构
图5-8所示的并行输出的1位共阴LE D静态 显示电路比较简单,程序也不复杂。
5. 2. 4动态显示电路的结构及原理
动态显示就是逐位轮流点亮各位LE D显示 器(即扫描)。动态显示电路是单片机中应用 最为广泛的显示方式之一。适用于LE D显 示器较多的场合。电路如图5-10所示。
[任务5.4]步进电机控制
5. 4. 1概述
步进电机是机电控制中一种常用的执行机 构,它的用途是将电脉冲转化为角位移, 通俗地说:当步进驱动器接收到一个脉冲信 号,它就驱动步进电机按设定的方向转动 一个固定的角度(及步进角)。
下一页 返回
[任务5.4]步进电机控制
5.4.2永磁式步进电机的控制
什么特点? 4.独立式按键和矩阵式键盘的工作原理是
了什么?各有了什么特点? 5.修改前面的电子钟程序,以扩展系统的
功能,让系统具有定时功能,当时间 走到 预设定的时间时,电路将启动外设(用发光返回
图5-1独立式按键应用电路
返回
图5-2独立式按键处理流程图
返回
图5-3矩阵式键盘电路
返回
图5-6 4 x 4矩阵式键盘电路
第一章 制造弹箭零件用的材料及毛坯种类的选择

1.3 高密度材料
a. 碳化钨 制作方法:碳化钨弹芯由碳化钨粉等粉末 冶金方法加工而成,即配比后加润滑剂压 型、烧结,使其具有一定的强度和硬度。 (HRC≥55) 特点:密度大(19.3g/cm3),高强度、高 硬度;缺点韧性差,易发生断裂,长细比 不可太大。
b. 钨基合金材料 1.钨合金 特点:韧性比碳化钨好,密度大。 制作方法:钨-镍-铁微末混合后烧结,经真空 热处理和型锻,在经机械加工而成。 国内两种大口径钨合金性能水平为:σb= 1147MPa,1127MPa; σs=1107MPa, 1068MPa;A=11.4%,6.8%;Z=26%, 14.1%。
c. 铸铁 主要用途:迫击炮弹体。 1.刚性铸铁 原材料:优质原生铁和废钢。 废钢降低原生铁碳、硅量,获得珠光体基 体,使游离石墨呈细片状,提高力学性能。 刚性铸铁强度低,脆性大,弹体爆破后有效 破片数少。
2. 球墨铸铁 球铁是利用球化剂(镁、稀土元素或稀土镁 合金)对铁水进行炉前处理,以得到在铸态 呈球状或团状的游离石墨和致密的金属基 体,从而使铸铁具有较高的强度和一定的延 伸率。 球化处理:加球化剂使石墨呈球形析出。 孕育处理:加孕育剂——强烈促进石墨化, 防止产生白口组织。 基体组织:铁素体、珠光体及二者混合。 我国所使用的是稀土球铁。
3.聚碳酸脂 性能:高冲击韧性,成型精度高,尺寸稳定 性好,耐磨性好,工作温度范围宽(-100~ 130 ℃ )。 主要用途:验电器、片簧盖、电机底盖、弹 带、闭气环等。 4.氟塑料(含有氟原子的塑料总称) 聚四氟乙烯:极高的化学稳定性和耐高温、 低温能力以及极低的摩擦系数。“塑料王” 缺点:成型性较差,价格较贵。 主要用途:制作弹带。
2.钨基复合材料 制作方法: 英国以钨或铀为基相,以金属、合金或陶瓷 纤维、颗粒为增强相,采用高温烧结或浇注 制造; 德国用环氧树脂、丙烯酸酯等作黏结剂,将 高强度钨、钽或其它合金材料薄板卷制黏结 成复合弹芯; 美国研制液体烧结钨或钨合金的钨基复合弹 芯材料金属基体,增强材料可以是添加铪元 素碳化钨丝或其类似的金属丝。
弹药工程与爆炸技术专业介绍
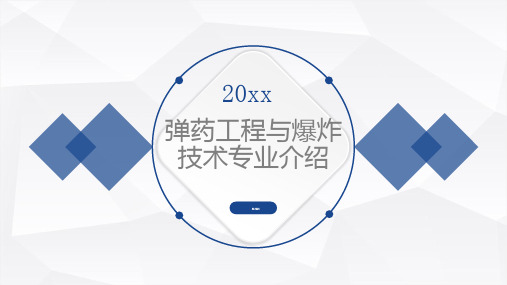
-
10
感谢您的欣赏
汇报人:XXXX
时间:20XX.7
专业定义
1
专业定义
2024/3/7
5
A
弹药工程与爆炸技术主要研究弹药工程、爆炸与安全技术以及民用工程爆破等方面的基本知识和技能,进行军用弹药工程或是民用爆破工程等
B
例如:手枪、炮弹等武器的弹药系统的分析设计,弹药威力的实验测试,建筑物拆除时爆破作业的设计等
核心课程
2
核心课程
兵器概论、弹箭空气动力学、弹道学、爆炸力学、弹丸设计理论、弹药终点效应、弹箭制造工艺学、固体火箭发动机原理、火箭弹设计、炸药装药技术、弹药现代设计方法、工业炸药、工程爆破技术基础、起爆器材、爆破安全技术与管理等
就业方向
3
就业方向
毕业生可以到中国兵器工业集团、中国兵器装备集团及中国航天工业集团等军工企业、民爆企业、机械制造和特种化工企业从事产品设计与制造工作、实验测试工作,同时面向军队、公安、爆破公司等部门从事安全管理和爆破技术工作,可在机械/化工制造行业从事机械/化工工艺设计、机械/化工产品制造方面的技术与管理工作来自弹药工程与爆炸技术专业介绍
20xx
-
2
目录
CONTENTS
专业定义
1
核心课程
2
就业方向
3
弹药工程与爆炸技术专业介绍
弹药工程与爆炸技术(Ammunition Engineering and Explosive Technology)是中国普通高等学校本科专业
培养具备化学、兵器科学与技术、化学工程与技术、力学等方面的基本理论和基础知识;接受炸药制造、工程爆破实践、爆炸安全管理技术和规范、爆炸测试方法和技术实验技能等方面的基本训练;具有从事爆炸物品生产技术与管理、工程爆破设计与施工及安全管理、爆破器材与爆破新技术研发等能力的复合型工程技术人才
76mm杀爆弹

76mm杀爆弹题目:76mm杀爆弹收口设计课程名称:弹箭制造工艺学专业:弹药工程与爆炸技术学号:姓名:指导教师:柳泽鑫能源与水利学院2017年 06月课程设计成绩评定表弹箭制造工艺课程设计任务书摘要热冲孔是大、中口径钢质弹体毛坯和火箭弹战斗部壳体毛坯的主要成型方法。
由于各类弹体结构上的不同,其热冲压工艺也有区别。
弹体结构一般可分为两种类型:一种是整体弹体,如地面榴弹和高射榴弹的弹体;另一种为带底螺的弹体,如后膛特种弹、半穿甲弹等。
本次设计的弹体为76mm杀爆弹,为整体弹体,基本的加工过程为下料→加热→预压型→冲孔→拔伸→冷却→粗加工→弹头部加热→收口→冷却→检验→精加工。
本文侧重方向为拔伸结束后的收口工艺过程以及模具的设计。
弹体收口的主要目的是得到合适的弹体弧形部,外弧形部是通过弹体模腔成型,而内弧形部则是靠收口过程自然成型。
模具设计是收口的关键收口时要预先将毛坯收口部加热至合适温度,以防止收口时金属因变形抗力大使得内部产生裂纹,导致发射时的危险。
由于收口时金属变形情况复杂,药室弧形部难以控制,影响因素较多,故为毛坯成型过程中的最难工序。
关键字:热冲孔;收口;模具设计目录摘要 (1)1完整工艺流程 (3)2收口前加工 (4)2.1定中心孔 (4)2.2药室机械加工 (5)2.3机械加工质量检验 (6)2.4弹体加热 (6)2.5收口 (8)2.5.1收口的基本过程与收口系数 (8)2.5.2收口方法 (8)2.5.3尺寸计算 (9)2.5.4收口后质量检验 (11)3收口模具设计 (12)3.1内形尺寸确定 (12)3.2外形尺寸确定 (13)3.3正料圈设计 (14)3.4热收口模具的材料、硬度及表面粗糙度 (15)计算结果分析 ............................................................................................. 错误!未定义书签。
2015年中国兵器集团校园招聘
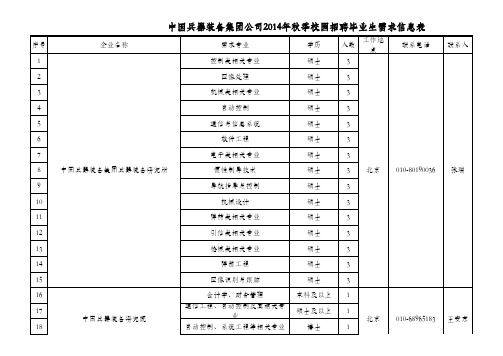
中国兵器装备集团公司2014年秋季校园招聘毕业生需求信息表
序号 162 163 164 165 166 167 168 169 170 171 172 173 174 175 176 177 178 179 重庆红宇精密工业有限责任公司 企业名称 重庆望江工业有限公司 需求专业 计算机网络或自动控制 导航制导与控制 传动液压 机电一体化 机械设计制造及其自动化 工业工程 计算机科学与技术 特种装备专业 特种能源 计算力学 工程力学 流体力学 材料学 计算机软件与理论 机械设计制造及其自动化 测控技术与仪器 软件工程 软件 学历 博士或硕士 硕士 本科 本科 本科 本科 本科 硕士研究生以 上 博士研究生 硕士研究生以 上 硕士研究生以 上 硕士研究生以 上 硕士研究生以 上 硕士研究生以 上 大学本科 大学本科 大学本科 硕士 人数 1 1 1 1 16 1 1 6 1 1 1 1 1 1 3 1 1 2 重庆 023-45585963 钱夏婵 工作地 点 重庆 联系电话 023-67110520 联系人 郭旭清
中国兵器装备集团公司2014年秋季校园招聘毕业生需求信息表
序号 72 73 74 75 76 77 78 79 80 81 82 83 84 85 86 87 88 89 四川华庆机械有限责任公司 成都光明光电股份有限公司 四川华川工业 有限公司 重庆长安工业(集团)有限责任公司 企业名称 需求专业 经济学 理论与应用化学 工程管理 探测与控制(电子引信) 探测与控制(机械引信) 特种能源与烟火技术 模具设计 安全工程或环境工程 光电技术 机械设计制造及自动化 人力资源管理学 财务管理或会计学 自动武器 计算机科学 应用化学 机械设计制造与自动化 工程管理 化学工程与工艺 学历 本科及以上 本科及以上 本科及以上 本硕 本硕 本硕 本硕 本硕 本科 博士 硕士及以上 本科及以上 本科及以上 本科及以上 本科及以上 本科及以上 本科及以上 本科及以上 人数 3 3 3 1 1 6 1 1 1 1 1 1 5 5 5 5 5 5 彭州 028-83452025 刘宗琴 成都 028-88456085 龙勇 成都 028-84612037 张国银 重庆 工作地 点 023-67418094 联系电话 刘霞 联系人
弹药工程与爆炸技术

弹药工程与爆炸技术专业培养目标:以满足军工和民爆企业需求为原则,以培养军工及民爆行业紧缺人才为特色,面向军工和民爆企业生产第一线,培养从事军工及民爆产品设计、制造以及技术管理等工作的高级应用型工程技术人才。
专业特色和基本要求:以军工及民爆行业为专业发展载体,以机械电子技术为基础,以弹箭产品制造技术及爆炸技术为特色,同时涵盖机械制造行业。
本专业的学生主要学习弹药工程技术、爆炸与安全技术以及机械工程与工程爆破方面的基础理论和基本知识、受到系统的产品设计与制造、技术开发、实验测试和科技管理等方面的基本训练,初步具备产品系统分析与综合设计、工程设计与制造、计算机应用、试验检测等方面的基本能力。
主要课程:高等数学、大学英语、工程力学、机械设计基础、电工与电子技术、计算机辅助设计与制造、机电一体化技术、动态测试技术、弹箭制造工艺学、弹药系统分析与设计、爆炸技术、终点效应、毕业设计等。
就业方向:本专业学生学习期满毕业后,主要面向军工企业和民爆企业就业,从事军工产品及民用爆破器材方面的技术开发和制造工作、实验测试工作、科技与安全质量管理工作,以及工程爆破等方面的工作,亦可在机械制造行业从事机械制造工艺方面的技术与管理工作。
2008级学生军训合影125毫米加农炮特种能源工程与烟火技术专业培养目标:以满足军工和民爆企业需求为原则,以培养军工及民爆行业紧缺人才为特色,面向军工和民爆企业生产第一线,培养从事含能材料产品设计与制造以及技术管理等工作的高级应用型工程技术人才。
专业特色和基本要求:以军工及民爆行业为专业发展载体,以化工技术为基础,以含能材料、火工产品制造技术及工程爆破技术为特色,同时涵盖化工产品制造行业。
本专业的学生主要学习特种能源工程技术、烟火技术、化学与化工技术以及工程爆破技术等方面的基础理论和基本知识、受到系统设计、技术开发、产品制造、实验测试和科技管理等方面的基本训练,初步具备产品系统分析与综合设计、工程设计与制造、计算机应用、试验检测等方面的基本能力。
巡飞弹的翼型选择及气动特性分析

巡飞弹的翼型选择及气动特性分析陶迎迎;郝永平;袁备;李曙光;谢天祥;李东辉【摘要】弹翼为巡飞弹提供大部分升力,为了研究选择高升力、高升阻比翼型的方法.利用CAD技术建立了3类圆头尖尾翼型的二维模型,运用GAMBIT进行网格划分,利用FLUENT软件进行动力学仿真,采集空气动力学数据对阻力系数、升力系数和升阻比进行了比较,对曲线存在的特殊点着重分析.结果表明,在满足高升力、高升阻比和飞行稳定的基础上,选择翼型FX-63-137为巡飞弹的最佳翼型.【期刊名称】《弹箭与制导学报》【年(卷),期】2016(036)001【总页数】4页(P129-131,139)【关键词】翼型;阻力系数;升力系数;升阻比【作者】陶迎迎;郝永平;袁备;李曙光;谢天祥;李东辉【作者单位】沈阳理工大学机械工程学院,沈阳110159;沈阳理工大学兵器科学技术研究中心,沈阳110159;沈阳理工大学机械工程学院,沈阳110159;沈阳理工大学兵器科学技术研究中心,沈阳110159;沈阳理工大学机械工程学院,沈阳110159;沈阳理工大学兵器科学技术研究中心,沈阳110159;沈阳理工大学机械工程学院,沈阳110159;沈阳理工大学兵器科学技术研究中心,沈阳110159;沈阳理工大学机械工程学院,沈阳110159;沈阳理工大学兵器科学技术研究中心,沈阳110159;沈阳理工大学机械工程学院,沈阳110159;沈阳理工大学兵器科学技术研究中心,沈阳110159【正文语种】中文【中图分类】TJ760.35纵观军事科技现状,未来主战场必将是高度信息化的战场,巡飞弹作为无人机与弹药技术有机结合的信息化武器,它不仅能够对敌实施精确、有效的打击,还能够承担战场侦察监视、战斗毁伤评估、通信以及无线电中继等单一或多项任务,必将成为弹药发展的重要趋势[1-2]。
巡飞弹是一种能在目标区上方进行“巡弋飞行”,“待机”执行多种作战任务的新概念弹药,长航时等高巡飞是其实现侦察和智能攻击作战使命的前提[2-3]。
期刊名称

期刊名称所在地类别分值安全与环境学报北京工业技术2半导体光电重庆工业技术2半导体技术石家庄工业技术2包装工程重庆工业技术2爆破武汉工业技术2爆破器材南京工业技术2北京服装学院学报北京工业技术2北京化工大学学报·自然科学版北京工业技术2北京交通大学学报北京工业技术2北京邮电大学学报北京工业技术2变压器沈阳工业技术2表面技术重庆工业技术2玻璃钢/复合材料北京工业技术2玻璃与搪瓷上海工业技术2材料开发与应用洛阳工业技术2材料科学技术学报(英文版)沈阳工业技术2材料科学与工艺哈尔滨工业技术2测井技术西安工业技术2测控技术北京工业技术2产业用纺织品上海工业技术2长安大学学报·建筑与环境科学版西安工业技术2长江科学院院报武汉工业技术2长沙交通学院学报长沙工业技术2车用发动机大同工业技术2成都信息工程学院学报成都工业技术2城市轨道交通研究上海工业技术2城市环境与城市生态天津工业技术2船舶上海工业技术2船舶工程上海工业技术2船舶力学无锡工业技术2船海工程武汉工业技术2纯碱工业大连工业技术2磁性材料及器件绵阳工业技术2大电机技术哈尔滨工业技术2大连海事大学学报大连工业技术2大连铁道学院学报大连工业技术2大庆石油地质与开发大庆工业技术2大庆石油学院学报大庆工业技术2弹箭与制导学报西安工业技术2弹性体吉林工业技术2导弹与航天运载技术北京工业技术2低温建筑技术哈尔滨工业技术2低压电器上海工业技术2电测与仪表哈尔滨工业技术2电池长沙工业技术2电瓷避雷器西安工业技术2电镀与环保上海工业技术2电镀与精饰天津工业技术2电镀与涂饰广州工业技术2电工电能新技术北京工业技术2电工技术杂志北京工业技术2电光与控制洛阳工业技术2电焊机成都工业技术2电机与控制学报哈尔滨工业技术2电加工与模具苏州工业技术2电力电子技术西安工业技术2电力建设北京工业技术2电力系统及其自动化学报天津工业技术2电力需求侧管理南京工业技术2电力自动化设备南京工业技术2电气传动天津工业技术2电气自动化上海工业技术2电声技术北京工业技术2电视技术北京工业技术2电线电缆上海工业技术2电汛技术成都工业技术2电站系统工程哈尔滨工业技术2电子测量技术北京工业技术2电子测量与仪器学报北京工业技术2电子产品世界北京工业技术2电子器件南京工业技术2电子元件与材料成都工业技术2锻压技术北京工业技术2锻压装备与制造技术济南工业技术2防灾减灾工程学报南京工业技术2纺织导报北京工业技术2纺织高校基础科学学报西安工业技术2纺织科学研究北京工业技术2纺织器材西安工业技术2飞航导弹北京工业技术2飞行力学西安工业技术2飞行器测控学报北京工业技术2分析仪器北京工业技术2粉煤灰综合利用石家庄工业技术2粉末冶金工业北京工业技术2风机技术沈阳工业技术2腐蚀与防护上海工业技术2钢铁钒钛攀枝花工业技术2港工技术天津工业技术2高电压技术武汉工业技术2高压电器西安工业技术2工程爆破北京工业技术2工程机械天津工业技术2工程勘察北京工业技术2工程抗震与加固改造北京工业技术2工程设计学报杭州工业技术2工程塑料应用济南工业技术2工程图学学报北京工业技术2工具技术成都工业技术2工矿自动化常州工业技术2工业催化西安工业技术2工业工程广州工业技术2工业工程与管理上海工业技术2工业锅炉上海工业技术2工业加热西安工业技术2工业建筑北京工业技术2工业炉天津工业技术2工业水处理天津工业技术2工业仪表与自动化装置西安工业技术2工业用水与废水合肥工业技术2公路北京工业技术2公路交通科技北京工业技术2功能材料与器件学报上海工业技术2固体火箭技术西安工业技术2光电子技术南京工业技术2光通信技术桂林工业技术2光通信研究武汉工业技术2光纤与电缆及其应用技术上海工业技术2光学技术北京工业技术2光学仪器上海工业技术2广播与电视技术北京工业技术2广东工业大学学报广州工业技术2广东造纸广东工业技术2贵金属昆明工业技术2贵州工业大学学报贵阳工业技术2桂林电子工业学院学报桂林工业技术2桂林工学院学报桂林工业技术2锅炉技术上海工业技术2国防大学学报北京工业技术2国际航空北京工业技术2哈尔滨工程大学学报哈尔滨工业技术2哈尔滨工程大学学报(英文版)哈尔滨工业技术2海湖盐与化工天津工业技术2海军工程大学学报武汉工业技术2含能材料绵阳工业技术2焊管宝鸡工业技术2焊接哈尔滨工业技术2焊接技术天津工业技术2航海技术上海工业技术2航空材料学报北京工业技术2航空工艺技术北京工业技术2航空计算技术西安工业技术2航空精密制造技术北京工业技术2航空维修与工程北京工业技术2航空制造技术北京工业技术2航天控制北京工业技术2合成材料老化与应用广州工业技术2合成树脂及塑料北京工业技术2合成纤维上海工业技术2合成纤维工业岳阳工业技术2合成橡胶工业兰州工业技术2合肥工业大学学报·自然科学版合肥工业技术2河北工业大学学报天津工业技术2河北工业科技石家庄工业技术2河北建筑科技学院学报·自然科学版邯郸工业技术2红外技术昆明工业技术2红外与激光工程天津工业技术2华北电力大学学报保定工业技术2华北电力技术北京工业技术2华北工学院学报太原工业技术2华东电力上海工业技术2华东公路合肥工业技术2华东交通大学学报南昌工业技术2华中建筑武汉工业技术2华中科技大学学报·城市科学版武汉工业技术2化肥工业上海工业技术2化工环保北京工业技术2化工机械兰州工业技术2化工科技吉林工业技术2化工矿物与加工连云港工业技术2化工新型材料北京工业技术2化工自动化及仪表兰州工业技术2化学工业与工程天津工业技术2化学建材上海工业技术2化学世界上海工业技术2化学与生物工程武汉工业技术2化学与粘合哈尔滨工业技术2环境保护科学沈阳工业技术2环境工程北京工业技术2环境监测管理与技术南京工业技术2环境科学与技术武汉工业技术2环境污染与防治杭州工业技术2黄金吉林工业技术2黄金科学技术兰州工业技术2混凝土沈阳工业技术2混凝土与水泥制品苏州工业技术2火工品西安工业技术2火力与指挥控制太原工业技术2火炮发射与控制学报西安工业技术2火灾科学合肥工业技术2火炸药学报西安工业技术2机车电传动株洲工业技术2机床与液压广州工业技术2机电工程杭州工业技术2机电一体化上海工业技术2机械传动郑州工业技术2机械工艺师北京工业技术2机械强度郑州工业技术2机械设计天津工业技术2机械设计与研究上海工业技术2机械设计与制造沈阳工业技术2机械设计与制造工程南京工业技术2机械与电子贵阳工业技术2机械制造上海工业技术2激光与光电子学进展上海工业技术2激光与红外北京工业技术2吉林大学学报·工学版长春工业技术2吉林大学学报·信息科学版长春工业技术2计量技术北京工业技术2计算机测量与控制北京工业技术2计算机仿真北京工业技术2计算机辅助工程上海工业技术2计算机工程与科学长沙工业技术2计算机工程与设计北京工业技术2计算机系统应用北京工业技术2计算机应用与软件上海工业技术2继电器许昌工业技术2建井技术北京工业技术2建筑材料学报上海工业技术2建筑电气成都工业技术2建筑机械北京工业技术2建筑机械化廊坊工业技术2建筑技术北京工业技术2建筑科学北京工业技术2舰船科学技术北京工业技术2江汉石油学院学报荆州工业技术2江苏工业学院学报常州工业技术2江苏科技大学学报·自然科学版镇江工业技术2交通与计算机武汉工业技术2交通运输工程学报西安工业技术2交通运输系统工程与信息北京工业技术2节能技术哈尔滨工业技术2节水灌溉武汉工业技术2洁净煤技术北京工业技术2结构工程师上海工业技术2金刚石与模料模具工程郑州工业技术2金属成形工艺重庆工业技术2金属功能材料北京工业技术2金属矿山马鞍山工业技术2精细石油化工天津工业技术2净水技术上海工业技术2聚氨酯工业南京工业技术2绝缘材料桂林工业技术2军械工程学院学报石家庄工业技术2勘察科学技术保定工业技术2空间结构杭州工业技术2空军工程大学学报·自然科学版西安工业技术2控制工程沈阳工业技术2矿产与地质桂林工业技术2矿产综合利用成都工业技术2矿山机械洛阳工业技术2矿山压力与顶板管理徐州工业技术2矿冶北京工业技术2矿冶工程长沙工业技术2矿业安全与环保重庆工业技术2矿业研究与开发长沙工业技术2兰州交通大学学报兰州工业技术2兰州理工大学学报兰州工业技术2理化检验·化学分册上海工业技术2理化检验·物理分册上海工业技术2炼钢武汉工业技术2炼铁武汉工业技术2炼油技术与工程洛阳工业技术2粮食与饲料工业武汉工业技术2粮油加工与食品机械北京工业技术2粮油食品科技北京工业技术2辽宁工程技术大学学报·自然科学版阜新工业技术2辽宁石油化工大学学报抚顺工业技术2流体机械合肥工业技术2硫酸工业南京工业技术2路基工程成都工业技术2氯碱工业葫芦岛工业技术2毛纺科技北京工业技术2煤化工太原工业技术2煤矿安全抚顺工业技术2煤矿机电上海工业技术2煤矿机械哈尔滨工业技术2煤气与热力天津工业技术2煤炭工程北京工业技术2煤炭科学技术北京工业技术2煤炭设计北京工业技术2棉防织技术西安工业技术2模具工业桂林工业技术2模具技术上海工业技术2木材工业北京工业技术2内燃机车大连工业技术2耐火材料洛阳工业技术2南昌航空工业学院学报·自然科学版南昌工业技术2南方冶金学院学报赣州工业技术2南京工业大学学报·自然科学版南京工业技术2南京邮电学院学报·自然科学版南京工业技术2酿酒哈尔滨工业技术2酿酒科技贵阳工业技术2农业环境科学学报天津工业技术2暖通空调北京工业技术2皮革科学与工程成都工业技术2起重运输机械北京工业技术2汽车技术长春工业技术2汽车与配件上海工业技术2汽轮机技术哈尔滨工业技术2桥梁建设武汉工业技术2青岛大学学报·工程技术版青岛工业技术2青岛建筑工程学院学报青岛工业技术2轻工机械杭州工业技术2轻合金加工技术哈尔滨工业技术2轻金属沈阳工业技术2燃料与化工鞍山工业技术2燃气轮机技术南京工业技术2燃烧科学与技术天津工业技术2热固性树脂天津工业技术2热加工工艺兴平工业技术2热科学与技术大连工业技术2热能动力工程哈尔滨工业技术2人民长江武汉工业技术2人民黄河郑州工业技术2人造板通讯北京工业技术2日用化学工业太原工业技术2润滑与密封广州工业技术2山东大学学报·工学版济南工业技术2山东建筑工程学院学报济南工业技术2陕西工学院学报·自然科学版汉中工业技术2上海纺织科技上海工业技术2上海海事大学学报上海工业技术2上海航天上海工业技术2上海金属上海工业技术2烧结球团长沙工业技术2深冷技术杭州工业技术2沈阳工业大学学报沈阳工业技术2沈阳工业学院学报沈阳工业技术2沈阳建筑工程学院学报·自然科学版沈阳工业技术2生态环境广州工业技术2声学技术上海工业技术2施工技术北京工业技术2石家庄铁道学院学报石家庄工业技术2石油工程建设天津工业技术2石油化工高等学校学报抚顺工业技术2石油化工设备兰州工业技术2石油化工设备技术北京工业技术2石油化工自动化兰州工业技术2石油机械荆州工业技术2石油矿场机械兰州工业技术2石油炼制与化工北京工业技术2石油物探南京工业技术2石油学报·石油加工北京工业技术2石油与天然气化工成都工业技术2石油钻采工艺任丘工业技术2石油钻探技术德州工业技术2时代建筑上海工业技术2实验技术与管理北京工业技术2实验室研究与探索上海工业技术2食品工业上海工业技术2食品工业科技北京工业技术2食品科技北京工业技术2食品研究与开发天津工业技术2食品与发酵工业北京工业技术2食品与机械长沙工业技术2世界建筑北京工业技术2世界军事北京工业技术2世界汽车天津工业技术2世界桥梁武汉工业技术2数据采集与处理南京工业技术2水泵技术沈阳工业技术2水电能源科学武汉工业技术2水电自动化与大坝监测南京工业技术2水力发电北京工业技术2水利水电技术北京工业技术2水利水电科技进展南京工业技术2水利水运工程学报南京工业技术2水利水运科学研究南京工业技术2水泥北京工业技术2水泥技术天津工业技术2水运工程北京工业技术2水资源保护南京工业技术2水资源与水工程学报咸阳工业技术2丝绸杭州工业技术2四川环境成都工业技术2四川建筑科学研究成都工业技术2四川水力发电成都工业技术2塑料北京工业技术2塑料工业成都工业技术2塑料科技大连工业技术2塑性工程学报北京工业技术2钛工业进展西安工业技术2炭素哈尔滨工业技术2炭素技术吉林工业技术2探测与控制学报西安工业技术2探矿工程(岩土钻掘工程)北京工业技术2陶瓷学报景德镇工业技术2特殊钢黄石工业技术2特种结构北京工业技术2天津工业大学学报天津工业技术2天津科技大学学报天津工业技术2天然气工业成都工业技术2铁道标准设计北京工业技术2铁道车辆青岛工业技术2铁道工程学报北京工业技术2铁道建筑北京工业技术2铁道科学与工程学报长沙工业技术2铁道通信信号北京工业技术2铁合金吉林工业技术2通信技术北京工业技术2同位素北京工业技术2涂料工业常州工业技术2微处理机沈阳工业技术2微电机西安工业技术2微电子学重庆工业技术2微电子学与计算机西安工业技术2微计算机信息北京工业技术2微计算机应用北京工业技术2微特电机上海工业技术2微细加工技术长沙工业技术2微型电脑应用上海工业技术2微型机与应用北京工业技术2微型计算机重庆工业技术2无机盐工业天津工业技术2无损检测上海工业技术2无锡轻工大学学报无锡工业技术2无线通信技术西安工业技术2武汉大学学报·工学版武汉工业技术2西安工程科技学院学报西安工业技术2西安工业学院学报西安工业技术2西安石油大学学报(自然科学版)西安工业技术2西南石油学院学报成都工业技术2稀土学报(英文版)北京工业技术2纤维素科学与技术广州工业技术2现代电力北京工业技术2现代防御技术北京工业技术2现代化工北京工业技术2现代科学仪器北京工业技术2现代雷达南京工业技术2现代塑料加工应用南京工业技术2现代隧道技术成都工业技术2现代仪器北京工业技术2现代制造工程北京工业技术2现代铸铁无锡工业技术2香料香精化妆品上海工业技术2湘潭矿业学院学报湘潭工业技术2橡胶工业北京工业技术2小型内燃机天津工业技术2小型内燃机与摩托车天津工业技术2新技术新工艺北京工业技术2新建筑武汉工业技术2新疆石油地质克拉玛依工业技术2新型建筑材料杭州工业技术2信息安全与通信保密北京工业技术2信息工程大学学报郑州工业技术2信息记录材料保定工业技术2蓄电池沈阳工业技术2选煤技术唐山工业技术2压力容器合肥工业技术2压缩机技术沈阳工业技术2烟草科技郑州工业技术2遥测遥控北京工业技术2遥感技术与应用兰州工业技术2冶金能源鞍山工业技术2冶金自动化北京工业技术2液压与气动北京工业技术2仪表技术与传感器沈阳工业技术2移动通信广州工业技术2印染上海工业技术2印染助剂常州工业技术2印刷技术北京工业技术2应用泛函分析学报北京工业技术2影视技术北京工业技术2影像科学与实践沈阳工业技术2硬质合金株州工业技术2油气储运廊坊工业技术2油气地质与采收率东营工业技术2油气田地面工程大庆工业技术2铀矿地质北京工业技术2铀矿冶北京工业技术2有机硅材料成都工业技术2有色金属北京工业技术2鱼雷技术西安工业技术2宇航计测技术北京工业技术2造船技术上海工业技术2噪声与振动控制上海工业技术2轧钢北京工业技术2粘接武汉工业技术2战术导弹技术北京工业技术2照明工程学报北京工业技术2照相机杭州工业技术2浙江工业大学学报杭州工业技术2浙江海洋学院学报·自然科学版舟山工业技术2浙江理工大学学报杭州工业技术2针织工业天津工业技术2真空沈阳工业技术2真空电子技术北京工业技术2振动测试与诊断南京工业技术2郑州大学学报·工学版郑州工业技术2郑州工程学院学报郑州工业技术2郑州轻工业学院学报·自然科学版郑州工业技术2纸和造纸都江堰工业技术2制冷学报北京工业技术2制造技术与机床北京工业技术2制造业自动化北京工业技术2中国安全科学学报北京工业技术2中国表面工程北京工业技术2中国电力北京工业技术2中国电业北京工业技术2中国调味品哈尔滨工业技术2中国非金属矿工业导刊北京工业技术2中国粉体技术济南工业技术2中国港湾建设天津工业技术2中国海上油气北京工业技术2中国海洋平台上海工业技术2中国航海上海工业技术2中国航天北京工业技术2中国航天(英文版)北京工业技术2中国环境监测北京工业技术2中国计量学院学报杭州工业技术2中国建材北京工业技术2中国胶粘剂上海工业技术2中国井矿盐自贡工业技术2中国军事科学自贡工业技术2中国矿业北京工业技术2中国煤炭北京工业技术2中国煤炭(英文版)北京工业技术2中国锰业长沙工业技术2中国民航学院学报天津工业技术2中国能源北京工业技术2中国酿造北京工业技术2中国农村水利水电武汉工业技术2中国皮革北京工业技术2中国乳品工业哈尔滨工业技术2中国社会保障北京工业技术2中国水土保持郑州工业技术2中国水运武汉工业技术2中国陶瓷景德镇工业技术2中国陶瓷工业景德镇工业技术2中国甜菜糖业哈尔滨工业技术2中国铁道科学北京工业技术2中国铁路北京工业技术2中国铁路(英文版)北京工业技术2中国钨业北京工业技术2中国医学计算机成像杂志上海工业技术2中国油脂西安工业技术2中国有色冶金北京工业技术2中国有线电视西安工业技术2中国园林北京工业技术2中国造纸北京工业技术2中国造纸学报北京工业技术2中国制造业信息化南京工业技术2中国铸造装备与技术济南工业技术2中华纸业济南工业技术2中南公路工程长沙工业技术2中外公路长沙工业技术2中小型电机上海工业技术2重庆环境科学重庆工业技术2重庆建筑大学学报重庆工业技术2重庆交通学院学报重庆工业技术2重庆邮电学院学报·自然科学版重庆工业技术2重型机械西安工业技术2轴承洛阳工业技术2筑路机械与施工机械化西安工业技术2铸造技术西安工业技术2装饰北京工业技术2自动化仪表上海工业技术2综合运输北京工业技术2组合机床与自动化加工技术大连工业技术2钻采工艺广汉工业技术2钻井液与完井液任丘工业技术2 NE MATHEMATICS NA基础科学2安徽大学学报·自然科学版合肥基础科学2安徽工业大学学报·自然科学版马鞍山基础科学2安徽理工大学学报·自然科学版淮南基础科学2安徽师范大学学报·自然科学版芜湖基础科学2氨基酸和生物资源武汉基础科学2逼近论及其应用(英文版)NA基础科学2测绘工程哈尔滨基础科学2测绘技术装备西安基础科学2测绘科学北京基础科学2测绘通报北京基础科学2测绘学院学报郑州基础科学2长安大学学报·自然科学版西安基础科学2长春理工大学学报长春基础科学2沉积与特提斯地质成都基础科学2纯粹数学与应用数学西宁基础科学2大学数学合肥基础科学2大学物理北京基础科学2弹道学报南京基础科学2地球信息科学北京基础科学2地图北京基础科学2地下空间与工程学报重庆基础科学2地震地磁观测与研究北京基础科学2地质力学学报北京基础科学2地质与资源沈阳基础科学2地质找矿论丛天津基础科学2东海海洋杭州基础科学2东华理工学院学报抚州基础科学2分子科学学报长春基础科学2福建师范大学学报·自然科学版福州基础科学2福州大学学报·自然科学版福州基础科学2甘肃科学学报兰州基础科学2工程地质学报北京基础科学2工业微生物上海基础科学2古地理学报北京基础科学2光谱实验室北京基础科学2广西大学学报·自然科学版南宁基础科学2。
弹药工程与爆炸技术

弹药工程与爆炸技术专业培育目标:以满足军工和民爆企业需求为原则,以培育军工及民爆行业紧缺人才为特色,面对军工和民爆企业生产第一线,培育从事军工及民爆产品设计、制造以及技术治理等工作的高级应用型工程技术人才。
专业特色和根本要求:以军工及民爆行业为专业进展载体,以机械电子技术为根底,以弹箭产品制造技术及爆炸技术为特色,同时涵盖机械制造行业。
本专业的学生主要学习弹药工程技术、爆炸与安全技术以及机械工程与工程爆破方面的根底理论和根本学问、受到系统的产品设计与制造、技术开发、试验测试和科技治理等方面的根本训练,初步具备产品系统分析与综合设计、工程设计与制造、计算机应用、试验检测等方面的根本力量。
主要课程:高等数学、大学英语、工程力学、机械设计根底、电工与电子技术、计算机关心设计与制造、机电一体化技术、动态测试技术、弹箭制造工艺学、弹药系统分析与设计、爆炸技术、终点效应、毕业设计等。
就业方向:本专业学生学习期满毕业后,主要面对军工企业和民爆企业就业,从事军工产品及民用爆破器材方面的技术开发和制造工作、试验测试工作、科技与安全质量治理工作,以及工程爆破等方面的工作,亦可在机械制造行业从事机械制造工艺方面的技术与治理工作。
2023 级学生军训合影125 毫米加农炮特种能源工程与烟火技术专业培育目标:以满足军工和民爆企业需求为原则,以培育军工及民爆行业紧缺人才为特色,面对军工和民爆企业生产第一线,培育从事含能材料产品设计与制造以及技术治理等工作的高级应用型工程技术人才。
专业特色和根本要求:以军工及民爆行业为专业进展载体,以化工技术为根底,以含能材料、火工产品制造技术及工程爆破技术为特色,同时涵盖化工产品制造行业。
本专业的学生主要学习特种能源工程技术、烟火技术、化学与化工技术以及工程爆破技术等方面的根底理论和根本学问、受到系统设计、技术开发、产品制造、试验测试和科技治理等方面的根本训练,初步具备产品系统分析与综合设计、工程设计与制造、计算机应用、试验检测等方面的根本力量。
弹药工程及爆炸技术-综合创新性实践-教学大纲
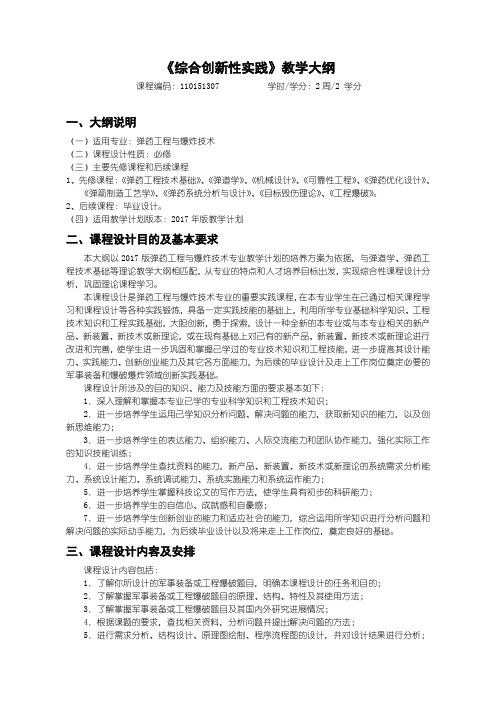
《综合创新性实践》教学大纲课程编码:110151307 学时/学分:2周/2 学分一、大纲说明(一)适用专业:弹药工程与爆炸技术(二)课程设计性质:必修(三)主要先修课程和后续课程1、先修课程:《弹药工程技术基础》、《弹道学》、《机械设计》、《可靠性工程》、《弹药优化设计》、《弹箭制造工艺学》、《弹药系统分析与设计》、《目标毁伤理论》、《工程爆破》。
2、后续课程:毕业设计。
(四)适用教学计划版本:2017年版教学计划二、课程设计目的及基本要求本大纲以2017版弹药工程与爆炸技术专业教学计划的培养方案为依据,与弹道学、弹药工程技术基础等理论教学大纲相匹配,从专业的特点和人才培养目标出发,实现综合性课程设计分析,巩固理论课程学习。
本课程设计是弹药工程与爆炸技术专业的重要实践课程,在本专业学生在已通过相关课程学习和课程设计等各种实践锻炼,具备一定实践技能的基础上,利用所学专业基础科学知识、工程技术知识和工程实践基础,大胆创新,勇于探索,设计一种全新的本专业或与本专业相关的新产品、新装置、新技术或新理论,或在现有基础上对已有的新产品、新装置、新技术或新理论进行改进和完善,使学生进一步巩固和掌握已学过的专业技术知识和工程技能,进一步提高其设计能力、实践能力、创新创业能力及其它各方面能力,为后续的毕业设计及走上工作岗位奠定必要的军事装备和爆破爆炸领域创新实践基础。
课程设计所涉及的目的知识、能力及技能方面的要求基本如下:1.深入理解和掌握本专业已学的专业科学知识和工程技术知识;2.进一步培养学生运用已学知识分析问题、解决问题的能力,获取新知识的能力,以及创新思维能力;3.进一步培养学生的表达能力、组织能力、人际交流能力和团队协作能力,强化实际工作的知识技能训练;4.进一步培养学生查找资料的能力,新产品、新装置、新技术或新理论的系统需求分析能力、系统设计能力、系统调试能力、系统实施能力和系统运作能力;5.进一步培养学生掌握科技论文的写作方法,使学生具有初步的科研能力;6.进一步培养学生的自信心、成就感和自豪感;7.进一步培养学生创新创业的能力和适应社会的能力,综合运用所学知识进行分析问题和解决问题的实际动手能力,为后续毕业设计以及将来走上工作岗位,奠定良好的基础。
弹箭制造工艺学习题

1.整体弹体的热变形工序有哪些?2.拔伸工序的作用?3.什么是压力加工的回弹现象?4.由体积不变规律得出的两条结论是什么?5.什么是最小阻力法则?6.Tresca和R.von mises准则的塑性条件各是什么?7.蓝脆区域有什么特点?8.什么是塑性和变形抗力?9.主应力图对金属的塑性和变形抗力有什么影响?10.什么是临界变形程度?11.已知冲孔后毛坯的内外径和方形截面坯料的圆角半径,如何确定D0?12.目前最佳的断料方法是什么?13.如何确定坯料的始冲温度和终冲温度?14.解释钢在加热过程中的氧化和脱碳现象?15.为什么钢在低温和高温阶段有不同的加热速度?16.什么是趋肤效应?17.为什么在冲孔前进行压型?18.简述弹体毛坯拔伸过程的受力状态?19.拔伸变形程度的三种描述方法是什么?20.怎样确定拔伸毛坯的各部分主要尺寸?21.拔伸时拔伸面积与拔伸冲头平均横截面积及拔伸毛坯平均环形横断面积应保持的关系是什么?22.收口系数的表达式是什么?23.收口毛坯的形状如何确定?1.冷挤压的基本变形方式有哪几种?2.冷挤压的优点有哪些?3.什么是反挤压?4.观察挤压成型时的方法有哪些?5.反挤杯形件的黏滞区有什么特点?6.什么是附加应力和残余应力?7.挤压力所需吨数的计算公式是什么?8.影响挤压力有哪些主要因素?9.解释工程材料中的一条线?10.冷挤压变形程度有哪些表示方法?11.简述模具几何形状对单位挤压力的影响?12.什么是许可变形程度?13.那种基本变形方式在相同变形程度下所需要的挤压力最大?在此种变形方式下,是否是变形程度越大,挤压力越大?14.冷挤压用的钢材有哪几种类型?15.简述化学成分对钢材冷挤压性能的影响?16.简述组织结构对钢材冷挤压性能的影响?17.冷挤压件的机械性能有什么特点?18.弹体爆破后的破片主要与什么有关?19.什么是蓝脆下料?20.常用钢质坯料冷挤压前的热处理方法有哪些?21.什么是磷化处理和皂化处理?22.获得冷挤压与热冲压弹体收口前毛坯的方法有什么不同?23.冷成型定心部的方法有哪几种?24.简述冷成型强化工序的安排?25.压型的主要目的有哪些?26.根据书中图例,简述大中、小口径弹体毛坯的工艺特点?1.弹体零件制造的冷冲压工序有哪三种?2.冷冲压的工艺特点是什么?3.平口剪床和斜口剪床适合剪裁的板料形状特点是什么?4.冲裁过程大致可以分为哪三个阶段?5.影响冲裁件质量的主要因素是什么?6.搭边的作用是什么?7.冲裁力计算公式的表达形式?8.画出弯曲成型时宽板和窄板的应力应变状态?9.什么是最小弯曲半径?材料允许的最小弯曲半径与哪些因素有关?10.中性层的位置如何确定?如何计算整个弯曲件的长度?11.弯曲件的回弹程度与材料的屈服强度和弹性模数有什么关系?12.描述拉伸过程中坯料的应力应变状态?13.解释材料拉伸过程中的起皱和破裂现象?14.拉伸过程中作用于筒壁的拉应力是哪几部分应力的总和?15.什么是拉伸系数?与哪些主要因素有关?拉伸系数过小会产生什么影响?16.什么情况下使用压边圈?17.对于圆筒件的进一步拉伸,材料的破裂发生在哪些阶段?18.拉伸力的计算公式是什么?19.药型罩成型具有哪些工艺特点?20.药型罩成型过程中退火的目的是什么?21.药型罩退火次数和温度会对药型罩的破甲性能产生什么影响?1.强力旋压按金属流动方向可分为哪几种?2.强力旋压具备那些特点?3.旋压较挤压弹体战斗部毛坯有那些优点?4.强力旋压药型罩具有哪些性能?5.材料经强力旋压后的组织有哪些变化?6.影响旋压件残余应力的主要因素有哪些?7.什么是应力腐蚀,与哪些因素有关?8.如何确定旋压的方向?9.壁厚减薄率及旋压次数如何确定?10.如何选择旋压毛坯?11.进给比是如何定义的?12.退让量和回弹量主要是由什么决定的?1.根据热处理的目的、要求及加热和冷却条件的不同,金属材料的热处理可分为哪几种?2.弹箭零件的热处理一般有哪两个方面的目的?3.122mm火箭弹燃烧室几种热处理工艺方法的目的是什么?4. 铝合金的淬火的概念是什么?5.解释铝合金淬火中的“过烧”现象?6.铝合金淬火冷却时应注意哪两点?7.解释自然时效和人工时效现象?8.解释铝合金时效中的过时效现象?9.热处理出现质量问题的主要原因有哪三种?1.确定弹箭零件用材料的依据是什么?2.制造弹箭零件用碳素结构钢按用途和性能可分为哪两种?3.深冲钢具有哪些特点?4.结合穿甲弹的使用性能说明其所用材料的特点?5.Cr、Ni、Mo、V元素在合金钢中的作用?6.结合火箭发动机的使用性能说明其所用材料的特点?7.刚性铸铁的性能?8.球墨铸铁的性能?9.何为球化处理与孕育处理?10.提高破片的两种途径事什么?11.制造弹箭零件用的有色金属材料有哪些?12.制造穿甲弹所采用的高密度材料有哪些?13.塑料按加工性能分为哪两类?14.塑料从使用角度可分为哪两类?15.什么是热塑性树脂?16.什么是热固性树脂?17.工程塑料与金属材料相比有哪些优点和缺点?18.常用的热塑性塑料有哪些,主要用途是什么?19.什么是玻璃钢?20.弹箭生产中常用的热固性塑料有哪些?21.什么是复合材料?22.复合材料两个基本组成相的作用?23.复合材料的特点?24.复合材料按结构可分为哪四类?25.复合材料按性能可分为哪两类?26.投产前钢材的检验主要有哪几种?27.弹箭零件毛坯的种类及特点?28.弹箭零件毛坯选择的原则是什么?1.拔伸的作用?2.结合拉伸试验图说明“回弹”现象?3.画出几种不同变形方式的变形力学简图?4.简要说明金属塑性变形和应用?5.塑性和变形抗力的概念?6.画出第一类硬化曲线并说明其上某一点切线的意义?7.变形温度对金属的塑性和变形抗力的影响?8.结合实例说明主应力图对塑性和变形抗力的影响?9.塑性变形对金属的组织和性能有哪些影响?10.结合图说明什么事临界变形程度?11.带圆角方形截面坯料具有哪些优点,如何确定其截面尺寸?12.单个原始坯料的重量应包括哪些?13.评定断料方法优劣的标志有哪些?14.生产中常用的断料方法有哪些?15.什么是过热与过烧?16.如何确定热冲压的温度范围?17.什么氧化和脱碳?18.针对不同的材料,如何确定加热速度和加热时间?19.按热能来源不同,加热方法可分为哪两类?20.感应加热原理及趋肤效应?21.冲孔前需做哪些准备工作?22.进入冲孔模冲孔的坯料加热不均匀会造成哪些后果?23.方形截料整个变形过程的4中变形方式是什么?24.何为滑动椎体?滑动椎体对冲孔压力——行程曲线有何影响?25.影响冲孔压力——行程曲线的因素有哪些?26.冲空前压型的方式有哪两种?27.画出弹体冲孔毛坯延伸时的受力分析,并分析弹体底部最可能被顶穿的时刻?28.毛坯拔伸变形程度有哪些表达式,推导多次拔伸的模数n的计算公式?29.如何确定拔伸毛坯形状和尺寸?30.提高弹体制造材料利用率需要改进的主要部位?31.如何确定冲孔毛坯形状和尺寸?32.为什么收口安排在粗加工之后?33.收口系数如何表示,结合收口受力情况说明收口系数过小会产生什么后果?34.收口系数许可极限值与哪些因素有关?35.如何确定收口的加热温度与加热长度?36.为什么说下模内收口较上模收口好?37.如何去顶收口毛坯形状和尺寸?。
弹箭制造工艺学
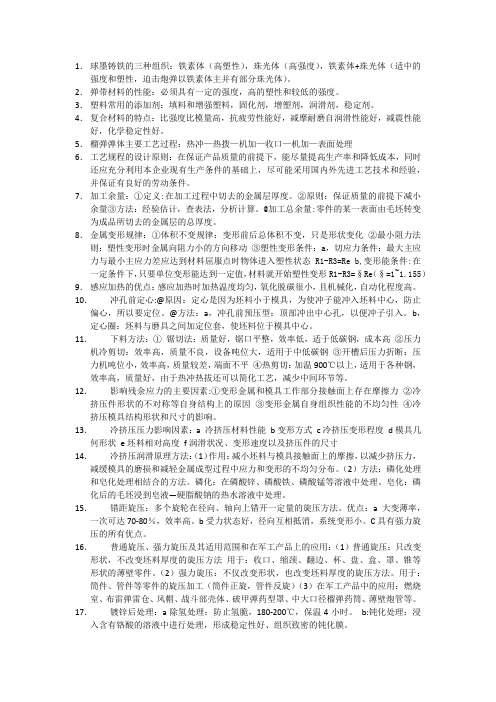
1.球墨铸铁的三种组织:铁素体(高塑性),珠光体(高强度),铁素体+珠光体(适中的强度和塑性,迫击炮弹以铁素体主并有部分珠光体)。
2.弹带材料的性能:必须具有一定的强度,高的塑性和较低的强度。
3.塑料常用的添加剂:填料和增强塑料,固化剂,增塑剂,润滑剂,稳定剂。
4.复合材料的特点:比强度比模量高,抗疲劳性能好,减摩耐磨自润滑性能好,减震性能好,化学稳定性好。
5.榴弹弹体主要工艺过程:热冲—热拨—机加—收口—机加—表面处理6.工艺规程的设计原则:在保证产品质量的前提下,能尽量提高生产率和降低成本,同时还应充分利用本企业现有生产条件的基础上,尽可能采用国内外先进工艺技术和经验,并保证有良好的劳动条件。
7.加工余量:①定义:在加工过程中切去的金属层厚度。
②原则:保证质量的前提下减小余量③方法:经验估计,查表法,分析计算。
@加工总余量:零件的某一表面由毛坯转变为成品所切去的金属层的总厚度。
8.金属变形规律:①体积不变规律:变形前后总体积不变,只是形状变化②最小阻力法则:塑性变形时金属向阻力小的方向移动③塑性变形条件:a,切应力条件:最大主应力与最小主应力差应达到材料屈服点时物体进入塑性状态R1-R3=Re b,变形能条件:在一定条件下,只要单位变形能达到一定值,材料就开始塑性变形R1-R3=§Re(§=1~1.155)9.感应加热的优点:感应加热时加热温度均匀,氧化脱碳很小,且机械化,自动化程度高。
10.冲孔前定心:@原因:定心是因为坯料小于模具,为使冲子能冲入坯料中心,防止偏心,所以要定位。
@方法:a,冲孔前预压型:顶部冲出中心孔,以便冲子引入。
b,定心圈:坯料与磨具之间加定位套,使坯料位于模具中心。
11.下料方法:①锯切法:质量好,锯口平整,效率低,适于低碳钢,成本高②压力机冷剪切:效率高,质量不良,设备吨位大,适用于中低碳钢③开槽后压力折断:压力机吨位小,效率高,质量较差,端面不平④热剪切:加温900℃以上,适用于各种钢,效率高,质量好,由于热冲热拔还可以简化工艺,减少中间环节等。
基于模型定义的弹箭三维计算机辅助工艺设计技术

第1 2期
四 川 兵 工 学 报
21 0 1年 1 2月
【 编委特稿 】
基 于模 型 定 义 的弹 箭 三 维计 算 机 辅 助 工艺 设 计 技 术
郝 博, 姜北北
10 5 ) 1 19
( 阳理工大学 机械工程学 院 , 阳 沈 沈
摘要 : 于模 型定 义的三维计算机辅 助工艺设计技术将 从根本上 改变 C P 基 A P流 程。该技术利 用 MB D规范参 数化 建
c u t  ̄w a o s h v n d mp ra tc n r u in o nr y e p n a i g ma e i o tn o t b t . i o
Ke y wor ds:3D —CAPP; MBD ; sg y l de in c c e
随着经济全球化 、 息一体 化地快 速发 展 , 其是 三维 信 尤 C D技术在制造业 的 日益普及和广泛应用 , A 人类应用 三维模 型表达设计意图成 为可 能。制造企业 为 了提高工 艺水 平和 效率 , 强市 场竞 争力 , 增 就必 须借 助于计算 机辅 助工艺 设计 (o p t ie r es ln i ,A P 。C P cm u r ddpo s pann C P ) A P作为设 计和 ea c g 制造 的中间环节 , 其研究 和开发 就显得 尤为 重要 , 但是 目前 并没 有在 世界 范 围 内出现 广 为普及 的 C P A P商 业化 软 件。
很多制造企业仍然采用二维加三维生产方式 , 相当一部 并且
分企业处于以二维为中心、 三维摸型为辅的管理方式, 使得
产品数 据传 递过 程复 杂 , 效率低 下 , 本高 昂 , 成 信息 利用 率
2018年版北大中文核心期刊目录(2017第八版,2018~2022适用) (第七编 工业技术)

学报 5. 自动化学报 6. 中国图象图形学报 7. 计算机工程与应用 8. 系统仿真学 报 9. 计算机工程 10.计算机集成制造系统 11.控制与决策 12. 小型微型计算机 TP 自动化技术, 计算机技术 系统 13.控制理论与应用 14.计算机应用研究 15.机器人 16. 中文信息学报 17. 计算机应用 18.信息与控制 19. 计算机科学 20.计算机测量与控制 21. 模式识 别与人工智能 22.计算机仿真 23. 计算机工程 与科学 24.遥感技术与应用 25. 传感器技术(改名为:传感器与微系统) 26. 计算机工程与设计 27.测控技术 28. 传 感技术学报 29.控制工程 30.微电子学与计算机 31.化工自动化及仪表 1. TQ0 一般性问题 高分子材料科学与工程 2. 化工学报 3. 高分子学报 4. 化工进展 5. 精细化
1.低温工程 2.制冷学报 1.真空科学与技术学报 2.真空
TB7 真空技术
TB9 计量学
1.计量学报 1. 岩矿测试 2.中国矿业大学学报 3.爆破 4.金属矿山 5. 矿山压力与顶板管理 (改名为:采矿与安全工程学报) 6.中国矿业 7.矿冶工程 8. 非金属矿 9. 学学报 1. 煤炭学报 2. 煤炭科学技术 3.煤矿安全 4. 煤田地质与勘探 5. 选煤技术 6.煤 炭工程 7.中国煤炭 8. 煤矿机械 9.煤矿开采 1. 质 石油勘探与开发 2. 石油学报 3. 天然气工业 4. 石油与天然气地 5. 石油化工 6. 石油实验地质 7. 石油大学学报.自然科学版(中国石油大 矿 业研究与开发 10. 矿业安全与环保 11.工程爆破 12. 矿山机械 13.西安科技大
1.食品科学 2.食品与发酵工业 3.食品工业科技 4. 中国油脂 5.中国粮油学 报 TS2 食品工业 6. 学 食品科技 7.食品与生物技术学报 8. 中国乳品工业 9. 食品工业 10. 茶叶科 11. 食品与机械 12.河南工业大学学报.自然科学版 13. 中国调味品
现代弹药技术的发展现状、趋势及其关键技术

3 )ME MS陀螺仪和加速度计技术 随着 国外制导 弹药特 别是 制导炮 弹发 展 的需求 不断 上
升, 制造体积更小 、 更耐 冲击 、 更可靠且适 于批量 生产 的微 机 械陀螺仪 正在称为 各 国研究 的热 点。微机 械陀 螺是 微 电子
与微 机械组结合 的微型振 动陀螺 , 是根 据受激振 动在有科 式
收 稿 日期 :02— 5—1 21 0 6 作者简 介 : 熊辉 (9 3 ) 男 , 17 一 , 工程师 , 主要从事弹箭武器系统装备研究 。
熊
22 2 精 确 打 击 弹 药技 术 ..
辉: 现代 弹药技 术 的发 展 现状 、 势及 其 关键 技 术 趋
4 )弹体姿态磁探测技术
器 , 发 展 最 积 极 、 活 跃 , 药装 备 与 技 术 的 发 展 处 在 新 一 其 最 弹 轮高峰期 , 正朝 着远 程 化 、 巧 化 、 用 途 ( 块 化 ) 高 效 能 、 灵 多 模 、 小 型 化 、 息化 和 网 络 化 方 向发 展 。 信 2 1 高 新 技 术 弹 药 .
1t增程技术 。例如 , 国 E G 美 R M弹 药和法 国超远程 “ 鹈 鹕” 弹, 炮 射程普遍达到 10k 0 m左右 。 2 )固冲发动机增程技术 用 于火 炮发射弹药增程 的固体 冲压发动机技术于 2 0世
纪7 0年 代末 开 始 研 究 。美 国 以 A F 射 增 程 弹 、 克 训 练 F S炮 坦 弹 和 S A K动 能 弹 为 应 用 背 景 展 开 了 应 用 研 究 , 23 m PR 在 0 m
基本原理是 , 弹丸在 快要爬 升到 弹道顶 点 时, 由控制 系
目前世界各 国正在发 展 的高新技 术 弹药主要 有 以下几 种: 末敏弹 , 导 炮 弹, 制 制导 与简 控 火箭 弹 , 飞 弹 , 巡 末修 弹 ( 如半主动激光制导炮弹 ) 弹道修正弹等 。 ,
兵器工程中、高级技术资格评审条件试行.doc

兵器工程中、高级技术资格评审条件试行兵器工程中、高级技术资格评审条件(试行)总则一、为客观公正地评价兵器工程专业技术人员的水平,鼓励多出成果,多出人才,促进兵器科技的进步和生产力的发展,结合兵器行业的特点,特制定本评审条件。
二、按照本评审条件经评审合格并获得相应专业技术资格证书者,表明具备相应的技术水平和能力,其职务与工资待遇由所在单位根据国家有关规定自行确定。
三、兵器工程中、高级技术资格的名称为工程师、高级工程师。
四、兵器工程分为五类专业,即坦克车辆专业、火炮枪械专业、弹箭专业、火炸药专业、光电火控专业。
下设二十四个分支专业。
五、各专业适用范围(一)坦克车辆专业本专业评审条件适用于从事坦克车辆(各种型号坦克、变形车辆、自行火炮、步兵战车、装甲车辆、军用发动机及附属系统、坦克特种装置等)研究、设计、制造(工艺)、试验、测试以及技术开发、科技信息、标准、新技术推广、维护、修理等工程技术人员。
坦克车辆专业的分支专业有四个1.坦克车辆及其军用发动机总体系统研究、设计。
2.坦克车辆及其军用发动机制造工艺。
3.坦克车辆特设装置。
4.坦克车辆装甲防护及材料。
(二)火炮枪械专业本专业评审条件适用于从事陆海空三军各种火炮系统(加农炮、榴弹炮、迫击炮、无后坐力炮、高射炮、坦克炮、自行炮、舰炮、火箭炮以及火焰喷射器)随动系统(各种自动、半自动操纵的电气、液压随动系统)和各种军用、民用枪械(手枪、步枪、冲锋枪、轻机枪、重机枪、大口径机枪、榴弹发射器、猎枪、小口径运动步枪、运动比赛用步枪、比赛用手枪)研究、设计、制造(工艺)、试验、测试以及技术开发、科技信息、标准、新技术推广、维护、修理等工程技术人员。
火包枪械专业的分支专业有三个1.火包、枪械设计。
2.武器随动系统。
3.火炮、枪械制造工艺。
(三)弹箭专业本专业评审条件适用于从事弹箭(包括各种炮弹、火箭弹、航空炸弹、深水炸弹、枪弹、救生弹、手榴弹、地雷、鱼雷、爆破器材及各种引信、火工品)和制导兵器(包括各种近程导弹及其发动机、战斗部、控制系统、稳定系统)研究、设计、制造(工艺)、包装、试验、测试以及技术开发、科技信息、标准、新技术推广、维护、修理等工程技术人员。
弹箭制造工艺
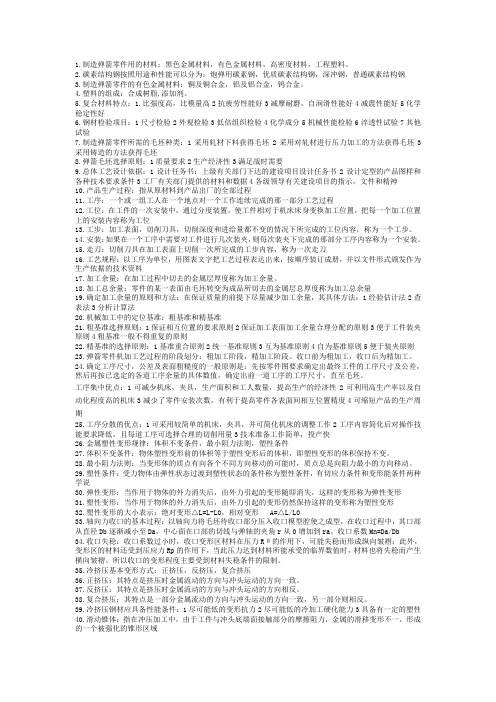
1.制造弹箭零件用的材料:黑色金属材料,有色金属材料,高密度材料,工程塑料。
2.碳素结构钢按照用途和性能可以分为:炮弹用碳素钢,优质碳素结构钢,深冲钢,普通碳素结构钢3.制造弹箭零件的有色金属材料:铜及铜合金,铝及铝合金,钨合金。
4.塑料的组成:合成树脂,添加剂。
5.复合材料特点:1.比强度高,比模量高2抗疲劳性能好3减摩耐磨,自润滑性能好4减震性能好5化学稳定性好6.钢材检验项目:1尺寸检验2外观检验3低倍组织检验4化学成分5机械性能检验6淬透性试验7其他试验7.制造弹箭零件所需的毛坯种类:1采用轧材下料获得毛坯2采用对轧材进行压力加工的方法获得毛坯3采用铸造的方法获得毛坯8.弹箭毛坯选择原则:1质量要求2生产经济性3满足战时需要9.总体工艺设计依据:1设计任务书:上级有关部门下达的建设项目设计任务书2设计定型的产品图样和各种技术要求条件3工厂有关部门提供的材料和数据4各级领导有关建设项目的指示,文件和精神10.产品生产过程:指从原材料到产品出厂的全部过程11.工序:一个或一组工人在一个地点对一个工作连续完成的那一部分工艺过程12.工位:在工件的一次安装中,通过分度装置,使工件相对于机床床身变换加工位置,把每一个加工位置上的安装内容称为工位13.工步:加工表面,切削刀具,切削深度和进给量都不变的情况下所完成的工位内容,称为一个工步。
14.安装:如果在一个工序中需要对工件进行几次装夹,则每次装夹下完成的那部分工序内容称为一个安装。
15.走刀:切削刀具在加工表面上切削一次所完成的工步内容,称为一次走刀16.工艺规程:以工序为单位,用图表文字把工艺过程表达出来,按顺序装订成册,并以文件形式颁发作为生产依据的技术资料17.加工余量:在加工过程中切去的金属层厚度称为加工余量。
18.加工总余量:零件的某一表面由毛坯转变为成品所切去的金属层总厚度称为加工总余量19.确定加工余量的原则和方法:在保证质量的前提下尽量减少加工余量,其具体方法:1经验估计法2查表法3分析计算法20.机械加工中的定位基准:粗基准和精基准21.粗基准选择原则:1保证相互位置的要求原则2保证加工表面加工余量合理分配的原则3便于工件装夹原则4粗基准一般不得重复的原则22.精基准的选择原则:1基准重合原则2统一基准原则3互为基准原则4自为基准原则5便于装夹原则23.弹箭零件机加工艺过程的阶段划分:粗加工阶段,精加工阶段。
弹箭制造工艺学

绪论本次毕业设计题目为编制152mm 杀爆弹弹丸加工工艺及工装。
编制工艺说明,进行下料尺寸、冲孔力、拔伸力、和收口力计算。
画出工艺框图,绘制工艺路线图表,编制工艺卡片,设计弹体粗加工外形、药室所用夹具和收口模具。
我国大口径弹体毛坯的生产,在8O年代以前多是沿用30~40年代的热冲老工艺,所用设备大部分为单工位水压机,公称压力一般均在2OO0~5O00kN范围内。
由于设备公称压力小,精度也较低,故冲压后毛坯壁厚差较大,造成材料利用率不高。
一般大口径弹体材料消耗率在50%~60%左右。
材料利用率的高低与工厂的设备条件、操作人员素质,管理水平以及制造水平有关。
在大口径弹体制造成本中,材料费约占生产成本的8O%左右,故要提高经济效益,实现弹体制造现代化,就必须从提高毛坯制造质量,提高材料利用率方面着手进行改造。
精化毛坯不仅直接关系到产品质量的提高、能源与材料的消耗以及综合生产效益,也关系到弹体切削加工先进设备的使用和先进工艺的实施。
本次毕业设计中力求精化弹体毛坯,采用目前较先进的热剪切下料工艺,加热采用大功率感应加热,预压型、冲孔与拔伸采用多工位组合冲压机,冷却采用可可控冷却设备以保证毛坯机械性能,收口前采用中频感应加热,增设有独立高压系统的高压水清除氧化皮装置,冲头和模具有自动喷涂润滑剂和冷却装置,毛坯实行100%自动化热检,白动剔除废品和打标记。
本文分三大部分。
第一部为弹体毛坯热冲压工艺,采用合理的下料方式和毛坯料的形状可以减少钢料的浪费,有效降低废料率。
热冲压分为预压型、冲孔、拔伸三道工序。
通过热冲压工序可以精化毛坯的外形,为以后的机械加工和收口提供余料小、尺寸合适的坯料,有效缩短工时,提高弹丸质量。
第二部分为弹体粗加工与收口工艺,包括切削外形余料和收口。
粗加工切削拔伸后毛坯外形和药室的余料,为精加工工序提供定位基准和装卡基准。
收口工序使弹丸头部得到设计要求的弧形。
第三部分为弹体精加工工艺,精车弧形,精车全形,修内弧等部位,并精车出定心部,车弹带槽和加工弹体口部螺纹。
- 1、下载文档前请自行甄别文档内容的完整性,平台不提供额外的编辑、内容补充、找答案等附加服务。
- 2、"仅部分预览"的文档,不可在线预览部分如存在完整性等问题,可反馈申请退款(可完整预览的文档不适用该条件!)。
- 3、如文档侵犯您的权益,请联系客服反馈,我们会尽快为您处理(人工客服工作时间:9:00-18:30)。
采用立式三模拔伸的方法,一般采用断续拔伸,即一个模圈拔伸后再进入模圈。模圈间距应保证在毛坯进入下一道拔伸模时,其端口刚好离开前一道拔伸模,这样可以减少毛坯出模卸载和入模加载时的冲击。
1.4.1拔伸后毛坯设计
拔伸后毛坯应依据收口前毛坯图进行设计,收口前毛坯是拔伸毛坯经粗加工后得到的,在收口前毛坯的粗加工部位考虑适当的加工余量,未加工部位保持尺寸不变,既得到收口后毛坯的形状与尺寸。在确定加工余量时,必须考虑毛坯制造所能达到的精度及表面可能出现的缺陷情况,在确保有足够余量的同时,尽量降低原材料的消耗。
高压水清除氧化皮的装置是一个箱型结构,一端进料,另一端出料,箱内四周布置喷嘴。喷嘴直径一般选用0.8-1mm,多数喷嘴与毛坯轴线的垂直面大约成15°角,部分喷嘴安装角与前后端面成45°角,以保证配料的六个面的氧化皮都能打掉。要避免喷射水流的互相干涉,喷嘴与配料表面间的距离可保持在200-300mm范围内,高压水压力一般为15-20MPa。
工艺流程如下:
原料进厂验收→长坯料感应加热→下料→清除氧化皮→精整对角线→预压型→冲孔→拔伸→热检→冷却→检验→喷砂→钻定心孔→粗车弹体→弹头部加热→药室加工→收口→热检→冷却→检验→修内弧形→精车全形→硬度及机械性能试验→精车定心部→车弹带槽→水压试验—弹体磁粉探伤→车口部螺纹→超声波探伤→内膛喷砂、喷漆→全面检验。
本文分三大部分。第一部为弹体毛坯热冲压工艺,采用合理的下料方式和毛坯料的形状可以减少钢料的浪费,有效降低废料率。热冲压分为预压型、冲孔、拔伸三道工序。通过热冲压工序可以精化毛坯的外形,为以后的机械加工和收口提供余料小、尺寸合适的坯料,有效缩短工时,提高弹丸质量。第二部分为弹体粗加工与收口工艺,包括切削外形余料和收口。粗加工切削拔伸后毛坯外形和药室的余料,为精加工工序提供定位基准和装卡基准。收口工序使弹丸头部得到设计要求的弧形。第三部分为弹体精加工工艺,精车弧形,精车全形,修内弧等部位,并精车出定心部,车弹带槽和加工弹体口部螺纹。
热剪切有关工艺参数:
热剪切的最佳剪切刀片间隙为0.5mm;
热剪切速度在3.7~5.1m/s范围,对剪切端部质量无大影响;
获得优质坯料的范围为:
低碳钢982~1232℃
申碳钢927~1175℃
高碳合金钢982~1093℃
对上述几种下料方式作简单对比,见下表1.2。表中数字越小性能越好。
表
下料方法 重量误差 断口耗料端面质量 弹体内 运料量 成本
式中s——方钢的横截面积(cm2);
ρ——钢的密度。
料长 =100× 69.1÷236.3÷7.85=37.25cm取 373mm
公差取5mm则下料毛坯尺寸为L= mm
1.2.2下料方式
生产中下料的方式有:开槽压力机折断法,锯切法,冷剪切法,热剪切法。
采用热剪切下料方法。锯切法虽端面质量较好,但材料的损耗和锯片的消耗量大且生产率低;压力机上冷剪切虽生产率高,但端面质量和端面平直度低;开槽折断法虽生产效率高,简易,但开槽折断后的断面质量较差,粗糙,多毛刺,端面不平直:这不仅影响冲孔毛坯质量,而且增加材料的耗材,必要时还需进行除毛刺的工作。热剪切法能排除几种现行断料方法所存在的缺点,并适用于各种弹体材料的一种新下料方法。热剪切断料工艺是目前一种良好的弹体下料方法,能获得优质的弹体毛坯。热剪切单个坯料的长度、质量偏差和断面平直度及端部质量都能达到较高的水平,剪切断面光洁、无氧化,无锯口损失,能显著提高弹体毛坯的内腔质量。又由于加热一热剪切一压力机同步联动,可大幅提高生产线效率。热剪切下料还具有简化工艺和减少中间材料运输等优点。在生产中应注意断面公差、弯曲度和扭曲度,增设自动称重、尺寸检测、自动剔除废品、自动送料装置和独立高压系统的高压水清除氧化皮装置。
1.3预压型和冲孔
增加预压型工序的好处是定心好,压型毛坯端面平整,有利于减小冲孔后毛坯的壁厚差。冲孔是热冲压成形的基本工序。若冲孔出现废品,如底部不饱满、设备型号壁厚差大等,则在拔伸工序中将无法弥补。
1.3.1预压型后毛坯设计
如图1.2所示,预压型后毛坯长度 是依据体积不变原则计算而得;因为预压型和冲孔在一台液压机上使用同一套模具,故直径D、D1、D2及长度 与冲孔毛坯的尺寸相同。为了便于坯料放入预压型模和定位,防止料歪,D应为方钢对角线长度,模具内径应略大于方钢加热后的对角线尺寸,预压型不正,会造成冲孔壁厚差过大。根据以上原则和冲孔后毛坯尺寸,D=Φ128mm, =Φ207.611mm, =Φ215.6mm, =36mm。体积不变下预压型毛坯的长度 =25mm。
腔质量
热剪切2121 1 1
圆锯切1 3 1 1 2 5
带锯切1 2 1 1 2 4
冷剪切2 1 2 2 2 2
切口折断3 1 3 3 3 3
1.2.3清除氧化皮
钢在火炉内加热的构成中,其表层金属与炉气中的水和氧气性气体进行化学反应生成氧化皮:氧化皮由三层组成,外层为三氧化二铁,中间层为四氧化三铁,金属与氧化层的交界处为氧化铁。
坯料应加热到125O℃;用一般感应加热,温差100℃加热时间约为15min。
表Hale Waihona Puke 温度ρ/( Ω)50Hz 500Hz 1000Hz
800 118 7.75 2.44 1.73
1000 122 7.85 4.53 1.76
12501288.04.641.80
1
A
图
1.2下料
1.2.1坯料长度设计
根据毛坯用料量,加适量消耗,按照体积不变计算长度。
图
冲孔的后续工序是拔伸,故内腔尾锥l部分,应与拔伸冲头尺寸相同或直径略大于拔伸冲头,以保证引入拔伸冲头和稳定的定位。此外还应考虑冲孔力,使金属向下流动,确保冲孔后毛坯外端尾锥部、定心桩、及端面充满模腔。
冲孔后毛坯主要尺寸为:外径 =215.6mm;d=98mm;L=310mm
冲孔力计算:影响冲孔力的因素较多,计算较为复杂,为简化计算,采用斯湟吉尔公式
d——冲孔模内径(指模口最薄处直径);
k——系数取0.2-0.25,推荐使用0.25
d取161.3mm,k取0.27.则D=215mm
冲孔模内工作表面和外斜度表面的粗糙度取Ra值为1.6μm
预压型和冲孔模具:
图
模具顶杆:
图1.8预压型和冲孔模具顶杆
预压型冲头:内平底冲头带有一个小冲头,如图1.7所示。
图
1.3.2冲孔后毛坯设计
在生产过程中,冲孔后毛坯是热状态下进行后读的拔伸工序,其形状、尺寸的确定,在满足拔伸要求的前提下,主要考虑冲孔工艺特性。弹体毛坯制造质量的优劣,很大程度上取决于冲孔,对产品质量特别是弹体毛坯的壁厚差尤为突出。设计冲孔毛坯时一般按热状态考虑,冲孔后毛坯的尺寸形状如图1.3所示。
1.1.2加热温度、时间
正确的加热应保证坯料达到所要求的始冲温度温度及坯料的连续、完整和温度均匀,在此前提下,尽量减少坯料的烧损和提高生产率。为满足上述要求,加热过程中必须控制加热温度、加热速度和加热时间。
根据生产经验,154mm× 154mm× 373mm坯料(D60钢)在加热炉中的加热参数可参考表1.1和图1.1。
图
1-
7-
图
1-
8-
1.3.4预压型和冲孔模具
冲孔模的壁厚影响到模具的寿命。如壁厚越薄,则模具易冷却,但强度低,易将模壁压在过水套的槽内,不易退模。如果模壁过厚,则不易冷却,寿命不高并浪费材料。为此模壁厚度可按经验公式计算:
D= …………………………………………….(1.4)
式中D——冲孔模外径(正锥模大头);
P=Fk =0.25 k ……………………………….(1.3)
式中P——冲孔力(kN);
F——冲孔冲头工作部分最大截面积( );
D——冲孔冲头工作部分最大直径(mm);
K——系数,有d/t=98/56.3的值确定(如图1.3),其中t为冲孔件壁厚;
——材料在冲孔温度下的强度极限,冲孔温度约为1100℃。
根据拔伸毛坯的用料重量,加上适量的消耗,按照体积不变原则计算出坯料下料的长度。
坯料实际用料重量计算如下:
...................................................(1.1)
式中Q——拔伸后毛坯重量
λ1——坯料加热时的火耗,油炉为2%~3%,燃气炉为1%~2%;
绪论
本次毕业设计题目为编制152mm杀爆弹弹丸加工工艺及工装。编制工艺说明,进行下料尺寸、冲孔力、拔伸力、和收口力计算。画出工艺框图,绘制工艺路线图表,编制工艺卡片,设计弹体粗加工外形、药室所用夹具和收口模具。我国大口径弹体毛坯的生产,在8O年代以前多是沿用30~40年代的热冲老工艺,所用设备大部分为单工位水压机,公称压力一般均在2OO0~5O00kN范围内。由于设备公称压力小,精度也较低,故冲压后毛坯壁厚差较大,造成材料利用率不高。一般大口径弹体材料消耗率在50%~60%左右。材料利用率的高低与工厂的设备条件、操作人员素质,管理水平以及制造水平有关。在大口径弹体制造成本中,材料费约占生产成本的8O%左右,故要提高经济效益,实现弹体制造现代化,就必须从提高毛坯制造质量,提高材料利用率方面着手进行改造。
λ2——断料的损耗。取1.5%.
然后运用Caxa制造工程师画出画出拔伸后毛坯的立体图,然后我们能得到毛坯的体积约为8163.4cm3,D60钢的密度为7.85g/cm3,得到拔伸后的毛坯重量Q=66.45kg。
则计算得到坯料实际用料重量Q0为69.1kg。
单个坯料长度计算如下:
L= /S﹒ρ(cm)…………………………………(1.2)
加热过程产生的氧化皮直接造成了金属的烧损,脱落在炉内的氧化皮对耐火砖炉子产生腐蚀作用,附着在坯料上的氧化皮会使热冲压模具的磨损加剧,同时可能被压入热冲压毛坯表面,降低毛坯的表面质量。因此,加热后的坯料,在冲压之前必须将氧化皮清除干净。
通常采用喷射高压水的方法清除氧化皮。由于喷射的时间短,坯料表面只有一层受到高压水的冷却,而坯料内部的热量又能很快地使其重新升温。用高压水清除氧化皮是一种最有效的方法。它利用于高压水的冲击力,又借助于氧化铁皮和钢遇冷收缩的不同,使它迅速脱落。不论面积大小,形状如何此方法均可采用,特别是紧贴的氧化皮,用其他方法难于清除时,只要水压足够,喷嘴大小角度喷水时间和水量合适,清除效果一般都很好。