机械制造工艺学名词解释
机械制造工艺学概念

1,将原材料转变为成品的全过程称为生产过程。
2.机器的生产过程中,改变生产对象的形状、尺寸、相对位置和性质等使其成为成品或半成品的过程称为工艺过程。
3.将铸、锻件毛坯或钢材经机械加工方法,改变它们的形状、尺寸、表面质量,使其成为合格零件的过程,称为机械加工工艺过程。
4,机器产品在计划期内应生产的产品产量和进度计划称为该产品的生产纲领。
5,根据作用的不同,基准可分为设计基准和工艺基准两大类。
6,工艺基准包括工序基准、定位基准、测量基准和装配基准。
7,工件在机床上或夹具中进行加工时,用作定位的基准,称为定位基准。
8,将工件在机床上或夹具中定位、夹紧的过程称为装夹。
9,根据工件加工的不同技术要求,采取先定位后夹紧或在夹紧过程中同时实现定位的两种方式。
10,重复定位的后果是使工件定位不稳定,破坏一批工件位置的一致性,使工件或定位元件在夹紧力作用下产生变形,甚至使部分工件不能进行装夹。
11,平面定位的定位元件是:支承钉或支承板。
12,由于自位支承在结构上是活动或浮动的,虽然它们与工件定位表面可能是两点或三点接触,但实质只能起到一个定位支承点的作用。
13,工件装夹中,常用与圆孔表面的定位元件有定位销、刚性心轴和小锥度心轴。
14,长定位销限制四个不定度,短定位销则限制两个不定度。
15,定位误差,由基准位置误差和基准不重合误差两部分组成,但并不是在任何情况下这两部分都存在。
16,正确确定夹紧力,主要是正确确定夹紧力的方向、作用点和大小。
17,夹紧力的方向:1,垂直于主要定位基准面;2,有利于减小夹紧力;18,夹紧力的而大小必须适当,夹紧力过小,工件在夹具中的位置可能在加工过程中产生变动,破坏原有的定位。
夹紧力过大,不但会使工件和夹具产生过大的变形,对加工质量不利,而且还将造成人力、物力的浪费。
19,夹具中常用的夹紧机构有斜楔夹紧机构、螺旋夹紧机构、圆偏心夹紧机构,定心对中夹紧机构及联动夹紧机构。
20,定心对中常用机构:三爪卡盘。
机械制造工艺学,名词解释
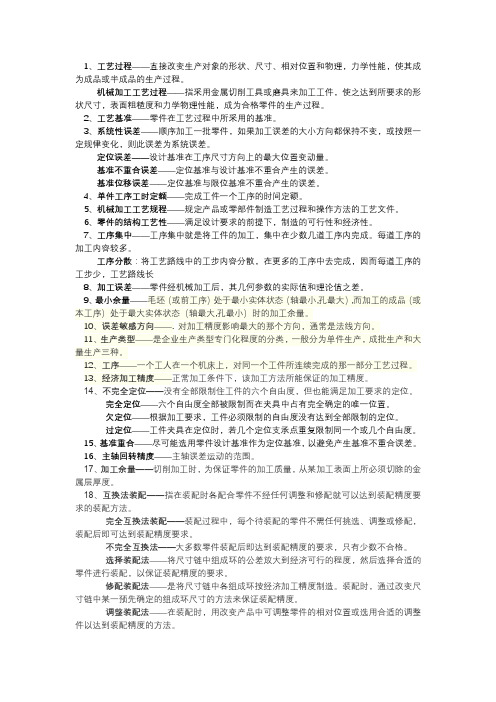
1、工艺过程——直接改变生产对象的形状、尺寸、相对位置和物理,力学性能,使其成为成品或半成品的生产过程。
机械加工工艺过程——指采用金属切削工具或磨具来加工工件,使之达到所要求的形状尺寸,表面粗糙度和力学物理性能,成为合格零件的生产过程。
2、工艺基准——零件在工艺过程中所采用的基准。
3、系统性误差——顺序加工一批零件,如果加工误差的大小方向都保持不变,或按照一定规律变化,则此误差为系统误差。
定位误差——设计基准在工序尺寸方向上的最大位置变动量。
基准不重合误差——定位基准与设计基准不重合产生的误差。
基准位移误差——定位基准与限位基准不重合产生的误差。
4、单件工序工时定额——完成工件一个工序的时间定额。
5、机械加工工艺规程——规定产品或零部件制造工艺过程和操作方法的工艺文件。
6、零件的结构工艺性——满足设计要求的前提下,制造的可行性和经济性。
7、工序集中——工序集中就是将工件的加工,集中在少数几道工序内完成。
每道工序的加工内容较多。
工序分散:将工艺路线中的工步内容分散,在更多的工序中去完成,因而每道工序的工步少,工艺路线长8、加工误差——零件经机械加工后,其几何参数的实际值和理论值之差。
9、最小余量——毛坯(或前工序)处于最小实体状态(轴最小,孔最大),而加工的成品(或本工序)处于最大实体状态(轴最大,孔最小)时的加工余量。
10、误差敏感方向——.对加工精度影响最大的那个方向,通常是法线方向。
11、生产类型——是企业生产类型专门化程度的分类,一般分为单件生产,成批生产和大量生产三种。
12、工序——一个工人在一个机床上,对同一个工件所连续完成的那一部分工艺过程。
13、经济加工精度——正常加工条件下,该加工方法所能保证的加工精度。
14、不完全定位——没有全部限制住工件的六个自由度,但也能满足加工要求的定位。
完全定位——六个自由度全部被限制而在夹具中占有完全确定的唯一位置。
欠定位——根据加工要求,工件必须限制的自由度没有达到全部限制的定位。
机械制造工艺学名词解释

机械制造工艺学名词解释机械制造工艺学是机械工程的一个重要分支,主要研究如何利用各种机械加工方法制造零件和构件。
这些加工方法和工艺都有一定的名词和术语,下面就针对一些常见的名词进行解释和说明。
1. CNC加工CNC加工是一种通过计算机数控系统控制加工机床进行加工的方法。
通过先设计出零件的CAD图纸,然后将图纸通过CAM软件转换成数控指令,再通过计算机控制加工机床进行精密加工。
CNC加工可以实现较高的精度和生产效率,被广泛应用于机械制造领域。
2. 挤压成型挤压成型是一种通过将金属材料加热至半固态状态,然后将其加压通过模具挤压成形的方法。
这种方法的主要优点是能够制造出长宽比较大的零件,而且精度和表面质量也比较高。
被广泛应用于汽车、航空等领域。
3. 焊接焊接是一种将两个或多个金属零件通过热力或压力的方法将它们融合在一起的加工方法。
焊接方式有很多种,包括电弧焊、气焊、激光焊等,每种方式都有其独特的优点和应用范围。
焊接广泛应用于制造行业中,特别是汽车、造船、航空等领域。
4. 精密切削精密切削是一种利用铣床、车床、磨床等机床进行高精度加工的方法。
在精密切削过程中,需要控制清晰的刀具跟踪和工艺参数,以实现最佳的加工效果。
精密切削广泛应用于制造行业中,特别是小型和高精度零件的制造。
5. 拉伸成型拉伸成型是一种将金属材料加热至塑性状态,然后通过模具拉伸成形的方法。
这种方法的优点是生产效率高,能够生产出成批的同型号零件。
被广泛应用于制造汽车、火车、自行车等用途的轮辋、镀锌板等。
6. 粉末冶金粉末冶金是一种通过将金属粉末复合、压缩、烘烤、烧结等工艺流程,将粉末压制成固形零件的方法。
这种方法的主要优点是能够生产出高强度和高耐磨性的零件。
被广泛应用于汽车、机械设备、电力设备等领域。
7. 压铸压铸是一种通过将熔化的金属或铝合金压入模具中成型的方法。
这种方法的特点是能够生产出高精度和高稳定性的零件,具有很高的制造效率。
被广泛应用于汽车、电器、通讯设备等制造领域。
机械制造工艺学名词解释

第一章1.1生产过程:是指从原材料变成成品的劳动过程的总和;包括原材料的采购、保管、生产准备工作、毛坯制造、零件机械加工和热处理、产品装配、调试、油封包装发运等;机械加工工艺过程:凡属直接改变生产对象形状、大小、性能及相对位置关系的过程;(包括:锻造、焊接、冲压、铸造、热处理、机械加工、特种加工、表面处理、装配)机械加工工艺规程:在现有的生产条件下,以最合理或者较合理的工艺过程,用文字按规定的表格形式书写的工艺文件;1.2.生产纲领:企业在计划期内应完成的产品数量及进度计划,包含了备品和废品;生产批量:指一次投入或者产出的同一产品数量单件生产:产品种类多、数量少、工作地点经常更换、加工对象很少重复;成批生产:各工作地点分批轮流制造几种不同的产品,加工对象周期性重复;大量生产:产品产量大,大多数工作地点按照一定的生产节拍重复进行某种零件的某一个加工内容,设备专业化程度很高;工件装夹:使工件在加工钱前相对于机床、刀具、夹具具有正确的位置,且在整个加工过程保持位置的准确可靠;包括工件的定位和夹紧;1.3.基准:用以确定生产对象几何要素间的几何关系所依据的点线面;包括设计基准和工艺基准;设计基准:工件在零件图上标注尺寸所采用的基准;工艺基准:工件在工艺过程中所采用的基准;包括:定位、工序、测量和装配基准工序基准:用以确定本工序被加工表面后的尺寸、现状、位置所采用的基准;定位基准:用以确定工件在机床上或者夹具中正确位置所采用的记住;测量基准:在加工中或者加工后,用以测量工件形状、尺寸和位置误差所采用的基准;装配基准:用以零件或者部件在产品上相对位置所采用的基准;工件定位:确定工件在机床或者夹具中占有正确位置的工艺过程;夹紧:将工件定位后的位置固定下来,使之在加工过程中相对于机床和刀具有正确的位置;六点定位原理:采用合理布置的六个支承点与工件的定位基准相接触,来限制工件的六个自由度;完全定位:工件的六个自由度被完全限制而在夹具中占有完全确定的位置;不完全定位:没有完全限制工件的六个自由度也能满足加工要求的定位;欠定位:根据加工要求,工件必须限制的自由度没有被完全的限制;过定位:采用的支承点重复限制了工件的同一个或几个自由度;1.4.装配:根据一定技术要求,通过校正、调整、平衡、配作、反复检验等一系列工作来保证产品质量的一个复杂工艺过程;机器的质量最终是通过装配来保证的;装配单元:零件、套件、组件、部件和机器;装配内容:根据一定技术要求,通过校正、调整、平衡、配作、反复检验等一系列工作来保证产品质量的一个复杂工艺过程;第二章2.1机械加工工艺规程作用:1.是生产准备工作的依据;2.是组织生产的指导性文件3.是新建和扩建工厂时的原始资料4.便于积累、交流和推广行之有效的生产经验;零件的结构工艺性:指在满足使用要求的前提下制造的可行性和经济性;包括:零件尺寸要合理和结构要合理;尺寸合理:(1)尺寸规格尽量标准化(2)尺寸标注要合理;结构合理:(1)结构应便于加工(2)便于测量(3)应有足够的刚度毛坯选择:(1)零件的材料及其力学性能(2)零件的机构形状和尺寸(3)生产类型(4)车间的生产能力(5)充分注意应用新工艺、新技术和新材料。
机械制造工艺学名词解释

三、解释概念(10分)1.经济精度在正常生产条件下即完好设备、适当夹具、必需刀具、一定的熟练工人,合理的工时定额下,某种加工方法所达到的公差等级和粗糙度。
2.工艺系统刚度垂直加工面的切削力FY与刀刃相对加工面在法线方向上的相对变形位移Y之比为工艺系统刚度K,即K=y Fy3.粗基准未加工面为定位基面的定位基准。
4.原理误差由于采用了近似的加工运动或近似的刀具形状而产生的误差。
1.基准统一(统一基准)原则零件在同一次安装中,方便地被加工多个表面,而且多个加工工序一致采用的一组定位基准。
2.工艺能力系数表示所要求加工的公差范围δ与实际工序加工误差(分散范围δ6)之比。
3.原理误差由于采用了近似的刀具形状和近似的加工运动而产生的误差。
4.过定位定位中工件的一个不定度同时被多个定位元件所限制的情况。
3.精基准已加工面为定位基准面的定位基准。
4.定位误差一批工件定位时,工序基准相对起始(调刀)基准在加工要求方向上的最大变动量。
1.机器零件表面质量的含义包括哪些内容?答:包含微观几何形状:粗糙度和波度。
物理机械性能变化:冷作硬化、金相组织变化、残余应力。
2.为何对车床床身导轨在水平面内的直线度要求高于在垂直面内的直线度要求,而对平面磨床的床身导轨要求却相反呢?答:因为车床床身导轨水平面内的直线度与加工表面的法线方向一致,有直线度误差,将直接影响到加工表面的形状精度,所以水平面内的直线度误差要求高于垂直面内的。
而平面磨床床身导轨在垂直面内的直线度与加工表面的法线方向一致,有直线度误差将直接影响到加工表面的形状精度,所以垂直面内的直线度要求高于水平面。
1.误差复映系数由于毛坯的制造误差等而使切削深度不均匀引起切削力变化,使弹性位移量也变化,使所加工的工件上产生了类似的加工误差。
2.装配尺寸链与装配技术要求有关的零部件因素(尺寸)与装配技术要求构成的封闭图形。
3.误差复映规律由于毛坯的误差而使切削深度不均匀,引起切削力变化而引起的弹性位移量变化,使所加工的工件产生了近似于毛坯误差的误差。
机械制造工艺学知识点总结(含名词解释)
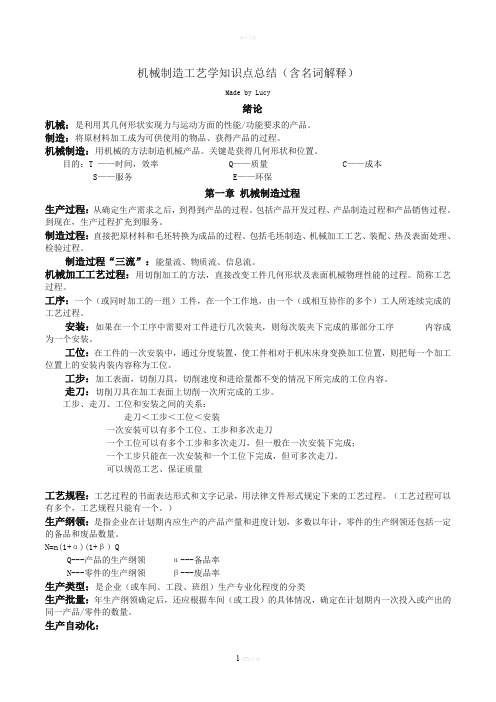
机械制造工艺学知识点总结(含名词解释)Made by Lucy绪论机械:是利用其几何形状实现力与运动方面的性能/功能要求的产品。
制造:将原材料加工成为可供使用的物品、获得产品的过程。
机械制造:用机械的方法制造机械产品。
关键是获得几何形状和位置。
目的:T ——时间,效率 Q——质量 C——成本S——服务 E——环保第一章机械制造过程生产过程:从确定生产需求之后,到得到产品的过程。
包括产品开发过程、产品制造过程和产品销售过程。
到现在,生产过程扩充到服务。
制造过程:直接把原材料和毛坯转换为成品的过程。
包括毛坯制造、机械加工工艺、装配、热及表面处理、检验过程。
制造过程“三流”:能量流、物质流、信息流。
机械加工工艺过程:用切削加工的方法,直接改变工件几何形状及表面机械物理性能的过程。
简称工艺过程。
工序:一个(或同时加工的一组)工件,在一个工作地,由一个(或相互协作的多个)工人所连续完成的工艺过程。
安装:如果在一个工序中需要对工件进行几次装夹,则每次装夹下完成的那部分工序内容成为一个安装。
工位:在工件的一次安装中,通过分度装置,使工件相对于机床床身变换加工位置,则把每一个加工位置上的安装内装内容称为工位。
工步:加工表面,切削刀具,切削速度和进给量都不变的情况下所完成的工位内容。
走刀:切削刀具在加工表面上切削一次所完成的工步。
工步、走刀、工位和安装之间的关系:走刀<工步<工位<安装一次安装可以有多个工位、工步和多次走刀一个工位可以有多个工步和多次走刀,但一般在一次安装下完成;一个工步只能在一次安装和一个工位下完成,但可多次走刀。
可以规范工艺、保证质量工艺规程:工艺过程的书面表达形式和文字记录,用法律文件形式规定下来的工艺过程。
(工艺过程可以有多个,工艺规程只能有一个。
)生产纲领:是指企业在计划期内应生产的产品产量和进度计划,多数以年计,零件的生产纲领还包括一定的备品和废品数量。
N=n(1+α)(1+β)QQ---产品的生产纲领α---备品率N---零件的生产纲领β---废品率生产类型:是企业(或车间、工段、班组)生产专业化程度的分类生产批量:年生产纲领确定后,还应根据车间(或工段)的具体情况,确定在计划期内一次投入或产出的同一产品/零件的数量。
机械制造工艺学

机械制造工艺学机械制造工艺学,是机械工程领域的一门基础学科,研究和探讨机械制造过程中的各种工艺方法和技术。
机械制造工艺学的发展和应用,对于提高机械制造效率、降低制造成本、改善产品质量具有重要意义。
一、机械制造工艺学的研究内容机械制造工艺学主要研究以下内容:1.材料与工艺:机械制造中所使用的材料种类繁多,如金属材料、非金属材料、复合材料等,而不同材料的加工工艺也不尽相同。
机械制造工艺学研究材料与工艺之间的关系,探究不同材料在不同工艺条件下的性能变化规律。
2.加工工艺:机械制造工艺学研究不同零件加工过程中涉及的各种方法和技术。
例如,钻孔、铣削、车削、磨削等传统加工工艺,以及激光切割、电火花加工等新兴加工工艺。
这些工艺的选择和应用,直接关系到产品的准确性、表面光洁度和加工效率。
3.工装夹具:机械制造工艺学研究工装夹具的设计和制造。
工装夹具是机械制造中的重要辅助工具,它们能够提高机械加工的精度和效率。
机械制造工艺学通过研究工装夹具的结构和使用方法,为机械制造过程提供支持和保障。
4.设备和工艺参数:机械制造工艺学研究机械制造过程中所需的各种设备和工艺参数。
例如,加工中所使用的机床、刀具、冷却液等设备,以及加工速度、切削速度、进给速度等工艺参数。
这些设备和参数的选择和配置,对于机械制造过程的效果有着重要影响。
二、机械制造工艺学的应用领域机械制造工艺学的研究成果广泛应用于以下领域:1.轿车制造:轿车制造是机械制造工艺学的重要应用领域之一。
轿车的制造涉及到各种形状复杂的零件加工和装配工艺,要求零件精度高、质量可靠。
机械制造工艺学的研究成果可以为轿车制造过程中的工艺选择和优化提供指导。
2.航空航天:航空航天领域对于零件的精度、强度和重量都有极高要求,同时也对工艺的可靠性和生产效率有较高需求。
机械制造工艺学的研究成果能够为航空航天领域的制造过程提供技术支持。
3.机械设备制造:机械设备制造涉及到各种类型的机械设备的加工和制造,这些设备的工艺要求和性能指标均不相同。
机械制造工艺学(简答,名词解释)

滚齿和插齿的区别:滚齿的运动精度高,插齿的齿形精度高,滚齿的生产率高,但模数小,齿圈薄的小齿轮,插齿效率高,滚齿通用性好,但按展成法加工齿轮距离较近的多联齿轮以及内齿轮,人字齿轮,齿轮带凸台齿轮只能用插齿加工齿形加工方法:成形法,铣齿,拉齿,成形磨齿展成法:滚齿,插齿,剃齿,磨齿,行齿细长轴:刚性差,热扩散性差,在切削热的作用下回产生相当大的线膨胀,加工时一次走刀所需时间长,增大几何形状误差(车刀住偏角大,是切削力减小。
改变走刀方向。
改进工件的装夹方法,采用中心架跟刀架。
改进刀具几何角度,入采用大前角减小切削热充分利用冷却液采用弹簧顶尖。
硬度高和耐磨性好的刀具)工件装夹(安装):即定位和加紧。
工件定位:采取一定的约束措施来限制自由度,通常可用约束点群来描述,而且一个自由度只需要一个约束点来限制。
六点定位原则:采用六个按一定规则布置的约束点来限制工件的六个自由度,实现完全定位。
完全定位:限制六个自由度。
不完全定位:仅限制1~5个自由度。
过定位:工件定位时,一个自由度同时被两个或两个以上的约束点所限制欠定位:在加工时根据被加工面的尺寸,形状和位置要求,应限制的自由度未被限制,即约束点不足。
定位:指确定工件在机床上或夹具中占有正确的位置的过程工件装夹有哪三种方法? 1.夹具中装夹;2.直接找正装夹;3.划线找正装夹夹紧力方向的选择原则: 1、夹紧力的作用方向应有利于工件的准确定位,而不破坏定位,为此一般要求主要夹紧力垂直指向定位面 2、夹紧力作用方向应尽量与工件刚度大的方向相一致,以减小工件夹紧变形 3、夹紧力作用方向应尽量与切削力、工件重力方向一致,以减小所需夹紧力夹紧力作用点选择原则:1、夹紧力作用点应正对支承元件所形成的支承面内,以保证工件已获得的定位不变 2、夹紧力作用点应处于刚性较好的部位以减小工件夹紧变形 3、夹紧力作用点应尽量靠近加工表面以减小切削力对工件造成的翻转力矩机床夹具的组成及功用?{机床夹具是在机床上装夹工件的一种装置.其作用是使工件相对于机床和刀具有一个正确位置.并在加工过程中保持这个位置不变。
机械制造工艺学

机械制造工艺学
机械制造工艺学是一门应用于机械制造的技术学科,主要研究加工工艺、工具和机床等工艺技术。
它涉及到材料特性、原理及机械制造工艺流程等方面,旨在帮助工程师们正确选择合适的加工工艺、设备、刀具和设备来制造出质量上乘的零件和产品。
机械制造工艺学包括加工工艺,即将原材料和半成品加工成最终产品的过程。
它包括传统加工工艺,如铣削、锯削、磨削、冲压、抛光等,以及现代加工工艺,如数控机床、激光切割、气体保护焊接等。
加工工艺的选择取决于产品的尺寸、精度、形状、表面质量、材料的特性和加工工艺的效率等因素。
机械制造工艺学还涉及机床设计、刀具设计和传动装置设计等内容。
机床设计旨在确定机床的尺寸、功能和结构,以保证满足加工要求。
刀具设计则是确定刀具的材料、形状和尺寸,以便满足不同类型加工的要求。
传动装置设计则是安装、操作和维护机床的过程。
《机械制造工艺学》名词解释(仅供参考)

时间定额:在一定的生产条件下,规定生产一件产品或完成一道工序所需消耗的时间。 磨削烧伤:对于已淬火的钢件,很高的磨削温度会使表面层的金相组织产生变化,表层金属硬度下降,工件表面呈氧化膜颜色。
自激振动:在机械加工过程中,在没有周期性外力作用下,有系统内部反馈产生的周期性震动。
冷作硬化:机械加工过程中产生的塑性变形使晶格扭曲,畸变,晶粒间产生滑移,晶粒被拉长使表面层金属的硬度增加。
工序:一个(或一组)工人在一个工作地点对一个(或同时对几个)工件连续完成的那一部分工艺过程。
机械加工工艺规程:规定产品或零部件机械加工工艺过程和操作方法等的工艺文件,是一切有关生产人员都应该严格执行,认真贯彻的纪律性文件。
工位:在工件的一次安装中,通过分度或(移位)装置,使工件相对于机床床身变换加工位置,则把每一个加工位置上的安装内容称为一个工位。
装配尺寸链:在机器的装配关系中,由相关零件的尺寸或相互位置关系所组成的封闭尺寸组合称为装配尺寸链。
定位误差:定位误差是由于工件在夹具上(或机床上)定位不准确而引起的加工误差。
机械加工工艺过程:是机械产品生产过程的一部分,是直接生产过程。其原意是指采用金属切削刀具或磨具来加工工件,使之达到所要求的形状、尺寸、相对位置和性质、表面粗糙度和力学物理性能,成为合格零件的生产过程。
安装:每次装甲下完成的那部分工序内容称为一个安装。
工步:加工表面、切削刀具、切削速度和进给量都不改变的情况下所完成的工位内容称为一个工步。
工序基准:在工序图上用来确定本工序所加工表面加工后的尺寸、形状和位置的基准。 定位基准:在加工时用于工件定位的基准,称为定。
封闭环:在零件加工或装配过程中间接获得或最后形成的环。
增环:该环的变动引起封闭环的同向变动。
复习资料-机械制造工艺学
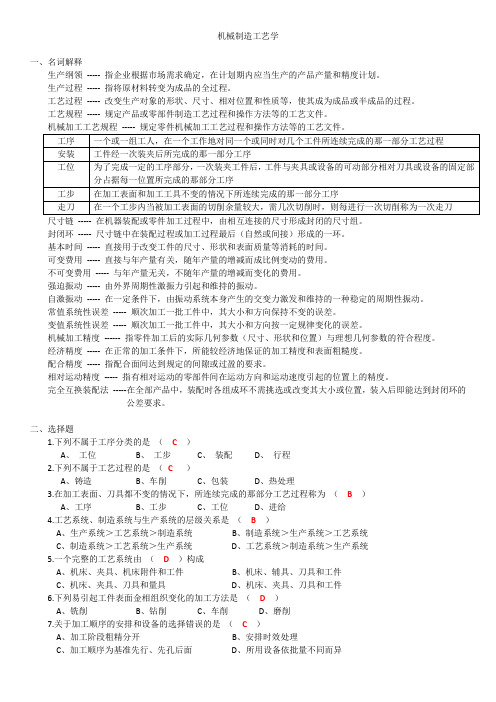
机械制造工艺学一、名词解释生产纲领-----指企业根据市场需求确定,在计划期内应当生产的产品产量和精度计划。
生产过程-----指将原材料转变为成品的全过程。
工艺过程-----改变生产对象的形状、尺寸、相对位置和性质等,使其成为成品或半成品的过程。
工艺规程-----规定产品或零部件制造工艺过程和操作方法等的工艺文件。
尺寸链-----在机器装配或零件加工过程中,由相互连接的尺寸形成封闭的尺寸组。
封闭环-----尺寸链中在装配过程或加工过程最后(自然或间接)形成的一环。
基本时间-----直接用于改变工件的尺寸、形状和表面质量等消耗的时间。
可变费用-----直接与年产量有关,随年产量的增减而成比例变动的费用。
不可变费用-----与年产量无关,不随年产量的增减而变化的费用。
强迫振动-----由外界周期性激振力引起和维持的振动。
自激振动-----在一定条件下,由振动系统本身产生的交变力激发和维持的一种稳定的周期性振动。
常值系统性误差-----顺次加工一批工件中,其大小和方向保持不变的误差。
变值系统性误差-----顺次加工一批工件中,其大小和方向按一定规律变化的误差。
机械加工精度------指零件加工后的实际几何参数(尺寸、形状和位置)与理想几何参数的符合程度。
经济精度-----在正常的加工条件下,所能较经济地保证的加工精度和表面粗糙度。
配合精度-----指配合面间达到规定的间隙或过盈的要求。
相对运动精度-----指有相对运动的零部件间在运动方向和运动速度引起的位置上的精度。
完全互换装配法-----在全部产品中,装配时各组成环不需挑选或改变其大小或位置,装入后即能达到封闭环的公差要求。
二、选择题1.下列不属于工序分类的是(C)A、工位B、工步C、装配D、行程2.下列不属于工艺过程的是(C)A、铸造B、车削C、包装D、热处理3.在加工表面、刀具都不变的情况下,所连续完成的那部分工艺过程称为(B)A、工序B、工步C、工位D、进给4.工艺系统、制造系统与生产系统的层级关系是( B )A、生产系统>工艺系统>制造系统B、制造系统>生产系统>工艺系统C、制造系统>工艺系统>生产系统D、工艺系统>制造系统>生产系统5.一个完整的工艺系统由( D )构成A、机床、夹具、机床附件和工件B、机床、辅具、刀具和工件C、机床、夹具、刀具和量具D、机床、夹具、刀具和工件6.下列易引起工件表面金相组织变化的加工方法是( D )A、铣削B、钻削C、车削D、磨削7.关于加工顺序的安排和设备的选择错误的是( C )A、加工阶段粗精分开B、安排时效处理C、加工顺序为基准先行、先孔后面D、所用设备依批量不同而异8.箱体平面的加工常用方法不包括(D)A、刨削B、铣削C、磨削D、车削9.属于几何误差的是( C )A、测量误差B、刀具磨损C、刀具误差D、工艺系统受热变形10.不能减少毛坯形状造成的误差复映规律的措施是( D )A、提高毛坯制造精度B、提高工艺系统刚度C、多次加工D、提高切削速度11.气缸盖的上下表面有很高的平行度要求,则精加工时可采用( C )A、精基准的基准重合原则B、精基准的自为基准原则C、精基准的互为基准原则D、精基准的基准统一原则12.车削细长轴,因工件刚度不足造成在工件轴向截面上的形状是(D)A、马鞍形B、梯形C、矩形D、腰鼓形13.磨淬火钢时,在工件表面上形成的瞬时高温将使表面金属产生的金相组织变化不包括( C )A、回火烧伤B、退火烧伤C、正火烧伤D、淬火烧伤14.对相互位置精度要求高的大孔孔系精加工(例如车床主轴箱箱体孔系精加工),应该采用的加工工艺是(C )A、钻削B、拉削C、镗削D、铰削15.齿轮的毛坯形式不包括( D )A、棒料B、锻件C、铸件D、焊件16.不属于外圆表面光整加工的是( A )A、砂带磨削B、滚压C、抛光D、珩磨17.机床导轨的精度要求极高,进行光整加工工序时,应符合(A)A、精基准的自为基准原则B、精基准的基准重合原则C、精基准的基准统一原则D、粗基准的保证加工余量均匀原则18.不属于获得尺寸精度的加工方法是( A )A、刀尖轨迹法B、试切法C、调整法D、主动观测法19.在零件选择精基准时,若应选择几个被加工表面(或几道工序)都能使用的定位基准为精基准称为(C )A、基准重合B、互为基准C、基准统一D、自为基准20.加工大型箱体零件上有数量较多、孔径较大、精度要求过高的孔时,一般使用下面的哪一种加工方法(D)A、钻削B、拉削C、铰削D、镗削21.查找装配图组成环的原则不包括(C)A、封闭原则B、环数最少原则C、单方向原则D、精确原则22.不属于获得形状精度加工方法的是( A )A、调整法B、成形法C、仿形法D、展成法23.单件零件生产的时间不包括( A )A、准终时间B、基本时间C、辅助时间D、布置场地时间24.在下列条件中,( C )是单件生产的工艺特征A、广泛使用专用设备B、有详细的工艺文件C、使用通用刀具和万能量具D、广泛用夹具进行安装定位25.轴类零件加工时最常用的定位基准是( C )A、端面B、外圆面C、中心孔D、端面和外圆面26.磨削淬火钢时,磨削区温度未超过淬火钢的相变温度,但已超过马氏体的转变温度,可能产生( B )A、淬火烧伤B、回火烧伤C、退火烧伤D、不烧伤27.机器的质量主要取决于机器设计的正确性、零件加工质量和( B )A、测试B、装配C、修理D、管理28.装配尺寸链的构成取决于( B )A、工艺过程方法B、零部件结构尺寸C、零件的数量D、加工方法29.高能束加工不包括( D )A、激光加工B、电子束加工C、离子束加工D、水射流加工30.非传统加工技术特点不包括( D )A、工具与工件不直接接触B、不主要依靠机械能C、使用的工具硬度一般小于被加工材料的硬度D、加工过程中不去除材料31.采用修配法装配时应正确选择( C )A、封闭环B、协调环C、补偿环D、公共环32.通过控制零件的加工误差来保证产品的装配精度的装配方法是( A )A、互换法B、选择法C、修配法D、调整法33.不属于装配工艺规程基本要求的是( B )A、保证装配质量B、提高零件质量C、提高生产率D、减少装配成本四、简答题1.制订工艺规程的步骤和内容有哪些?步骤:(1)熟悉和分析制订工艺规程的主要依据,确定零件的生产纲领和生产类型,进行零件的结构工艺性分析。
复习资料-机械制造工艺学

机械制造工艺学一、名词解释生产纲领-—-——指企业根据市场需求确定,在计划期内应当生产的产品产量和精度计划。
生产过程—————指将原材料转变为成品的全过程。
工艺过程——---改变生产对象的形状、尺寸、相对位置和性质等,使其成为成品或半成品的过程。
工艺规程-———-规定产品或零部件制造工艺过程和操作方法等的工艺文件。
尺寸链-—-——在机器装配或零件加工过程中,由相互连接的尺寸形成封闭的尺寸组。
封闭环——-——尺寸链中在装配过程或加工过程最后(自然或间接)形成的一环。
基本时间-———-直接用于改变工件的尺寸、形状和表面质量等消耗的时间。
可变费用—————直接与年产量有关,随年产量的增减而成比例变动的费用.不可变费用—-———与年产量无关,不随年产量的增减而变化的费用。
强迫振动—————由外界周期性激振力引起和维持的振动。
自激振动—-—--在一定条件下,由振动系统本身产生的交变力激发和维持的一种稳定的周期性振动.常值系统性误差-----顺次加工一批工件中,其大小和方向保持不变的误差。
变值系统性误差-————顺次加工一批工件中,其大小和方向按一定规律变化的误差。
机械加工精度—-———-指零件加工后的实际几何参数(尺寸、形状和位置)与理想几何参数的符合程度。
经济精度—---—在正常的加工条件下,所能较经济地保证的加工精度和表面粗糙度。
配合精度——-——指配合面间达到规定的间隙或过盈的要求.相对运动精度————-指有相对运动的零部件间在运动方向和运动速度引起的位置上的精度.完全互换装配法--———在全部产品中,装配时各组成环不需挑选或改变其大小或位置,装入后即能达到封闭环的公差要求.二、选择题1。
下列不属于工序分类的是(C)A、工位B、工步C、装配D、行程2。
下列不属于工艺过程的是(C)A、铸造B、车削C、包装D、热处理3。
在加工表面、刀具都不变的情况下,所连续完成的那部分工艺过程称为(B)A、工序B、工步C、工位D、进给4。
机械制造工艺学-
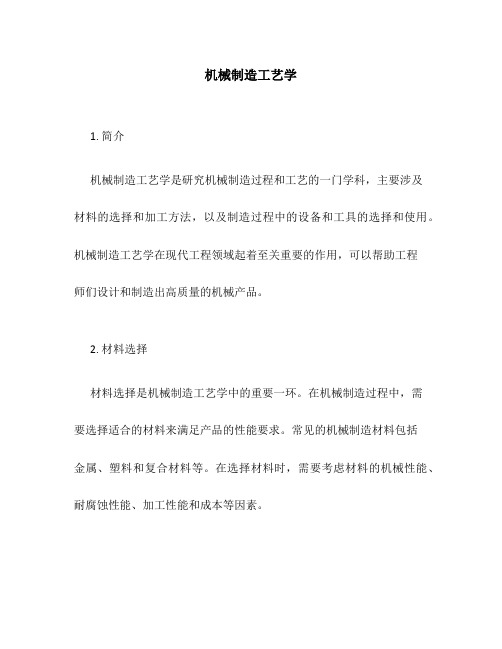
机械制造工艺学1. 简介机械制造工艺学是研究机械制造过程和工艺的一门学科,主要涉及材料的选择和加工方法,以及制造过程中的设备和工具的选择和使用。
机械制造工艺学在现代工程领域起着至关重要的作用,可以帮助工程师们设计和制造出高质量的机械产品。
2. 材料选择材料选择是机械制造工艺学中的重要一环。
在机械制造过程中,需要选择适合的材料来满足产品的性能要求。
常见的机械制造材料包括金属、塑料和复合材料等。
在选择材料时,需要考虑材料的机械性能、耐腐蚀性能、加工性能和成本等因素。
3. 加工方法机械制造工艺学中的加工方法是指将材料加工成所需形状和尺寸的过程。
常见的加工方法包括锻造、机械加工、焊接、注塑等。
不同的材料和产品要求需要采用不同的加工方法。
例如,对于金属材料,常使用的加工方法包括车削、铣削、钻削和磨削等;对于塑料材料,常使用的加工方法包括注塑、挤出和吹塑等。
4. 设备和工具选择在机械制造过程中,需要选择合适的设备和工具来进行加工。
设备和工具的选择直接影响到产品的加工质量和效率。
常见的机械制造设备包括车床、铣床、钻床、磨床等;常见的工具包括刀具、夹具、测量工具等。
在选择设备和工具时,需要考虑产品的加工要求、设备和工具的性能和成本等因素。
5. 制造过程控制制造过程控制是机械制造工艺学中的重要环节。
通过对制造过程进行控制,可以确保产品的质量和一致性。
常用的制造过程控制方法包括质量控制、工艺参数控制和设备状态监测等。
质量控制是通过检测和检验产品的特性来确保产品的质量;工艺参数控制是通过控制加工过程中的参数来确保产品的尺寸和形状精度;设备状态监测是通过监测设备的运行状态来确保设备的正常运行。
6. 制造工艺改进制造工艺改进是机械制造工艺学的重要研究内容之一。
通过改进制造工艺,可以提高产品的质量和生产效率。
常用的制造工艺改进方法包括工序优化、工艺参数优化和设备改进等。
工序优化是通过重新设计工艺流程来提高生产效率;工艺参数优化是通过调整加工过程中的参数来提高产品的质量和尺寸精度;设备改进是通过改进设备的结构和性能来提高生产效率和产品质量。
机械制造工艺学名词解释

1.生产过程:指把原材料转变为成品的全过程。
2.工艺过程:机器生产过程中,改变生产对象的形状、尺寸、相对位置和物理、力学性能等使其成为成品或半成品的过程。
3.热处理工艺过程:在热处理车间,对机器零件的半成品通过各种热处理方法,直接改变它们的材料性质的过程,称为热处理工艺过程。
4.装配工艺过程:将合格的机器零件和外购件,标准件装配成组件,部件和机器的过程,则称为装配工艺过程。
5.机械加工工艺过程:用机械加工方法逐步改变毛坯的形态,使其成为合格零件所进行的全部过程。
6.生产纲领:机器产品在计划期内应当生产的产品产量和进度计划称为该产品的生产纲领。
7.生产批量:指一次投入或产出的同一产品或零件的数量。
8.生产类型:单件生产、成批生产、大量生产(13年、14年)9.工艺规程:规定产品或零部件机械加工工艺过程和操作方法等的工艺文件。
10.机械加工工艺规程:规定产品或零部件机械加工工艺过程和操作方法等的工艺文件。
(14年)11.基准:在零件图上或实际的零件上,用来确定其它点、线、面的位置时所依据的点、线、面。
12.设计基准:零件工作图上用来确定其它点、线、面位置的基准。
13.工艺基准:加工、测量和装配过程中使用的基准。
(13年)14.工序基准:在工序图上用来确定本工序所加工表面加工后的位置尺寸和位置关系的基准。
15.定位基准:加工中用于定位的基准。
(14年)16.测量基准:工件测量时所用的基准。
17.装配基准:在装配时用来确定零件或部件在机器中的相对位置所采用的基准。
18.工件定位:采取一定的约束措施来限制自由度,通常可用约束点群来描述,而且一个自由度只需要一个约束点来限制。
19.定位:使工件在机床或夹具中占有正确的位置。
20.装夹:将工件在机床上或夹具中定位,夹紧的过程称为装夹。
21.定位误差:指由于工件定位造成的加工面相对工序基准的位置误差。
22.基准不重合误差:由于定位基准与工序基准不一致所引起的定位误差。
机械制造工艺学概念
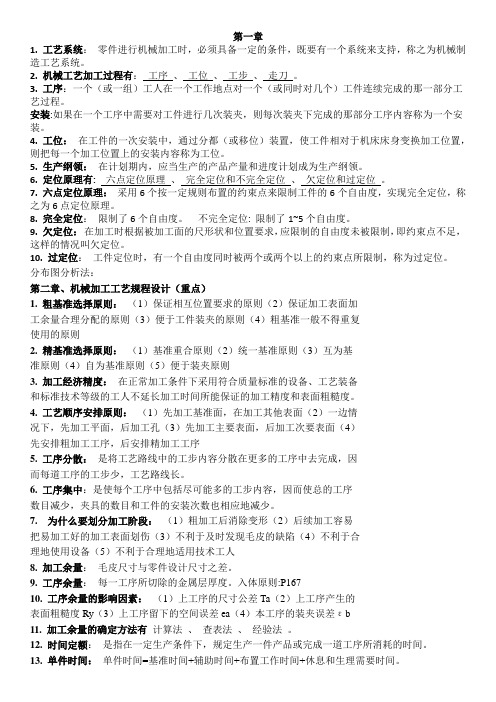
第一章1. 工艺系统:零件进行机械加工时,必须具备一定的条件,既要有一个系统来支持,称之为机械制造工艺系统。
2. 机械工艺加工过程有:工序、工位、工步、走刀。
3. 工序:一个(或一组)工人在一个工作地点对一个(或同时对几个)工件连续完成的那一部分工艺过程。
安装:如果在一个工序中需要对工件进行几次装夹,则每次装夹下完成的那部分工序内容称为一个安装。
4. 工位:在工件的一次安装中,通过分都(或移位)装置,使工件相对于机床床身变换加工位置,则把每一个加工位置上的安装内容称为工位。
5. 生产纲领:在计划期内,应当生产的产品产量和进度计划成为生产纲领。
6. 定位原理有:六点定位原理、完全定位和不完全定位、欠定位和过定位。
7. 六点定位原理:采用6个按一定规则布置的约束点来限制工件的6个自由度,实现完全定位,称之为6点定位原理。
8. 完全定位:限制了6个自由度。
不完全定位: 限制了1~5个自由度。
9. 欠定位:在加工时根据被加工面的尺形状和位置要求,应限制的自由度未被限制,即约束点不足,这样的情况叫欠定位。
10. 过定位:工件定位时,有一个自由度同时被两个或两个以上的约束点所限制,称为过定位。
分布图分析法:第二章、机械加工工艺规程设计(重点)1. 粗基准选择原则:(1)保证相互位置要求的原则(2)保证加工表面加工余量合理分配的原则(3)便于工件装夹的原则(4)粗基准一般不得重复使用的原则2. 精基准选择原则:(1)基准重合原则(2)统一基准原则(3)互为基准原则(4)自为基准原则(5)便于装夹原则3. 加工经济精度:在正常加工条件下采用符合质量标准的设备、工艺装备和标准技术等级的工人不延长加工时间所能保证的加工精度和表面粗糙度。
4. 工艺顺序安排原则:(1)先加工基准面,在加工其他表面(2)一边情况下,先加工平面,后加工孔(3)先加工主要表面,后加工次要表面(4)先安排粗加工工序,后安排精加工工序5. 工序分散:是将工艺路线中的工步内容分散在更多的工序中去完成,因而每道工序的工步少,工艺路线长。
机械制造工艺学名词解释
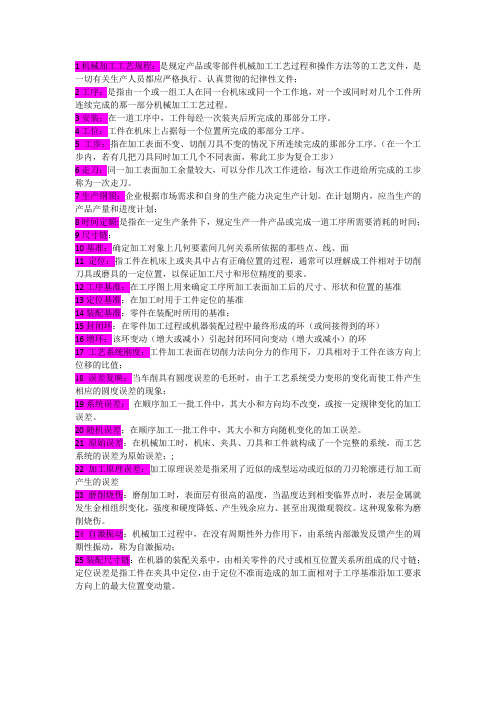
1机械加工工艺规程:是规定产品或零部件机械加工工艺过程和操作方法等的工艺文件,是一切有关生产人员都应严格执行、认真贯彻的纪律性文件;2工序:是指由一个或一组工人在同一台机床或同一个工作地,对一个或同时对几个工件所连续完成的那一部分机械加工工艺过程。
3安装:在一道工序中,工件每经一次装夹后所完成的那部分工序。
4工位:工件在机床上占据每一个位置所完成的那部分工序。
5工步:指在加工表面不变、切削刀具不变的情况下所连续完成的那部分工序。
(在一个工步内,若有几把刀具同时加工几个不同表面,称此工步为复合工步)6走刀:同一加工表面加工余量较大,可以分作几次工作进给,每次工作进给所完成的工步称为一次走刀。
7生产纲领:企业根据市场需求和自身的生产能力决定生产计划。
在计划期内,应当生产的产品产量和进度计划;8时间定额:是指在一定生产条件下,规定生产一件产品或完成一道工序所需要消耗的时间;9尺寸链:10基准:确定加工对象上几何要素间几何关系所依据的那些点、线、面11定位:指工件在机床上或夹具中占有正确位置的过程,通常可以理解成工件相对于切削刀具或磨具的一定位置,以保证加工尺寸和形位精度的要求。
12工序基准:在工序图上用来确定工序所加工表面加工后的尺寸、形状和位置的基准13定位基准:在加工时用于工件定位的基准14装配基准:零件在装配时所用的基准;15封闭环:在零件加工过程或机器装配过程中最终形成的环(或间接得到的环)16增环:该环变动(增大或减小)引起封闭环同向变动(增大或减小)的环17工艺系统刚度:工件加工表面在切削力法向分力的作用下,刀具相对于工件在该方向上位移的比值;18误差复映:当车削具有圆度误差的毛坯时,由于工艺系统受力变形的变化而使工件产生相应的圆度误差的现象;19系统误差:在顺序加工一批工件中,其大小和方向均不改变,或按一定规律变化的加工误差。
20随机误差:在顺序加工一批工件中,其大小和方向随机变化的加工误差。
机械制造技术名词解释

名词解释1刀具耐磨度:是一把新刃磨好的刀从开始切削直到磨损量达到磨钝标准为止的总切削时间,或者说是刀具两次刃磨之间的总切削时间。
2工艺基准:是在加工和装配过程中所采用的基准。
3精基准:能保证加工精度和装夹可靠方便。
4定位误差:一批工件按调整法加工时,因定位不准确而引起的加工误差。
5六点定位原理:适当分布的6个支承点限制工件的6个自由度的原理。
6经济粗糙度:是指在正常加工条件下(采用符合质量标准的设备,工艺装备和标准技术等级的工人,不延长加工时间)所能保证的加工精度。
7砂轮硬度:是指在磨削力作用下,磨粒从砂轮表面脱落的难易程度。
8材料的加工精度:指加工后所得到的零件的实际几何参数与理想几何参数的符合程度。
9工步:指加工表面,切削刀具,切削速度和进给量都保持不变的条件下所完成的那一部分工艺过程。
10机夹车刀:机夹车刀指用机械方法定位、夹紧刀片,通过刀片体外刃磨与安装倾斜后,综合形成刀具角度的车刀。
使用中刃口磨损后需进行重磨。
机夹车刀可用于加工外圆、端面、内孔,其中车槽车刀、螺纹车刀、刨刀方面应用较为广泛。
机夹车刀的优点在于避免焊接引起的缺陷,刀柄能多次使用,刀具几何参数设计选用灵活。
如采用集中刃磨,对提高刀具质量、方便管理、降低刀具费用等方面都有利。
特点:避免了焊接产生的应力,裂纹等缺陷,刀杆利用率高;刀片可集中刃磨获得所需参数,使用灵活方便。
11粗糙度:简答1工件精基准的选择原则?答:基准重合原则;基准统一原则;自为基准原则;互为基准原则;保证工件定位准确,夹紧可靠,操作方便原则。
2工件粗基准的选择原则?答:1为了保证加工面与不加工面之间的位置要求,应选不加工面为粗基准;2合理分配各加工面的余量;3尽量选用面积较大,平整光洁的表面做粗基准。
应避免选用有飞边,浇口,冒口或其他缺陷的表面做粗基准,以保证定位准确,夹紧可靠。
4粗基准一般不重复使用。
因为促进准比较粗糙,重复使用会产生很大的基准位置误差,影响加工精度,因此同一方向上的粗基准只能使用一次。
机械制造工艺学概念
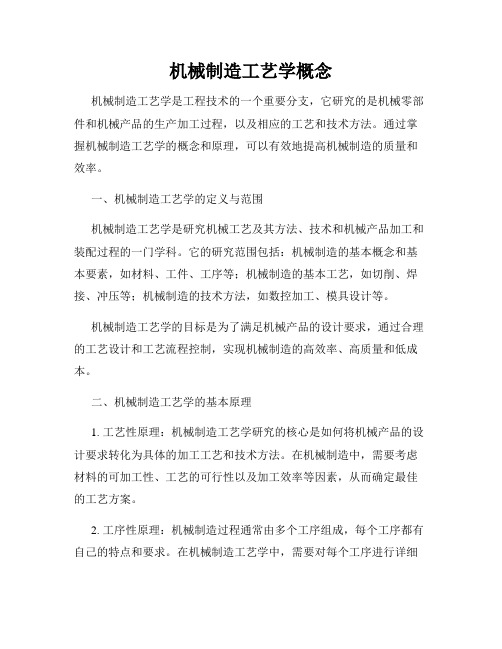
机械制造工艺学概念机械制造工艺学是工程技术的一个重要分支,它研究的是机械零部件和机械产品的生产加工过程,以及相应的工艺和技术方法。
通过掌握机械制造工艺学的概念和原理,可以有效地提高机械制造的质量和效率。
一、机械制造工艺学的定义与范围机械制造工艺学是研究机械工艺及其方法、技术和机械产品加工和装配过程的一门学科。
它的研究范围包括:机械制造的基本概念和基本要素,如材料、工件、工序等;机械制造的基本工艺,如切削、焊接、冲压等;机械制造的技术方法,如数控加工、模具设计等。
机械制造工艺学的目标是为了满足机械产品的设计要求,通过合理的工艺设计和工艺流程控制,实现机械制造的高效率、高质量和低成本。
二、机械制造工艺学的基本原理1. 工艺性原理:机械制造工艺学研究的核心是如何将机械产品的设计要求转化为具体的加工工艺和技术方法。
在机械制造中,需要考虑材料的可加工性、工艺的可行性以及加工效率等因素,从而确定最佳的工艺方案。
2. 工序性原理:机械制造过程通常由多个工序组成,每个工序都有自己的特点和要求。
在机械制造工艺学中,需要对每个工序进行详细的分析和设计,确保工序间的衔接和协调,从而保证整个制造过程的顺利进行。
3. 技术性原理:机械制造工艺学离不开现代机械制造技术的支持。
随着科技的不断发展,新的制造技术和方法层出不穷,机械制造工艺学需要与时俱进,不断引入新技术,提高制造效率和产品质量。
三、机械制造工艺学的应用机械制造工艺学的研究成果广泛应用于各个领域的机械制造中。
它不仅涉及传统的制造行业,如汽车制造、航空航天、机床制造等,还涉及到新兴的制造领域,如光学仪器、电子设备等。
在实践应用中,机械制造工艺学主要发挥以下几个方面的作用:1. 工艺设计与优化:机械制造工艺学可以根据机械产品的设计要求,设计出合理的工艺流程和工艺方法,并优化工艺参数,提高加工效率和产品质量。
2. 制造工艺控制:机械制造工艺学可以通过制定工艺规范和标准,对制造过程进行全面的控制和管理,确保产品的一致性和稳定性。
机械制造工艺学名词解释和简答题

1.机械加工工艺过程:对机械产品中的零件采用各种加工方法,直接用于改变毛坯的形状、尺寸、表面粗糙度以及力学物理性能,使之成为合格零件的全部劳动过程。
2生产纲领:计划期内,包括备品率和废品率在内的产量称为生产纲领。
3工艺规程:规定产品或零部件机械加工工艺过程和操作方法的工艺文件,是一切有关生产人员都应严格执行、认真贯彻的纪律性文件。
4加工余量:毛坯尺寸与零件设计尺寸之差称为加工总余量。
5六点定位原理:用来限制工件自由度的固定点称为定位支承点.用适当分布的六个支承点限制工件六个自由度的法则称为六点定位原理(六点定则)6.完全定位、不完全定位、欠定位、过定位完全定位:工件的六个自由度被完全限制的定位。
不完全定位:允许少于六点(1—5点)的定位。
欠定位:工件应限制的自由度未被限制的定位。
过定位:工件一个自由度被两个或以上支承点重复限制的定位。
7.加工精度、加工误差:加工精度:零件加工后的实际几何参数(尺寸、形状和表面间的相互位置)与理想几何参数的符合程度。
加工误差:加工后零件的实际几何参数(尺寸、形状和表面间的相互位置)对理想几何参数的偏离程度。
9误差复映:当车削具有圆度误差的毛坯时,由于工艺系统受力变形的变化而使工件产生相应的圆度误差,这种现象叫做误差复映。
10.表面粗糙度:表面粗糙度轮廓是加工表面的微观几何轮廓,其波长与波高比值一般小于50。
11.冷作硬化:机械加工过程中产生的塑性变形,使晶格扭曲、畸变,晶粒间产生滑移,晶粒被拉长,这些都会使表面层金属的硬度增加,统称为冷作硬化(或称为强化)。
12.工艺系统:在机械加工时,机床、夹具、刀具和工件就构成了一个完整的系统,称之为工艺系统。
13.工艺系统刚度:工艺系统抵抗变形的能力。
14.工序能力:工序处于稳定状态时,加工误差正常波动的幅度。
15.工序能力系数:表示工序能力等级,代表了工序能满足加工精度要求的程度。
16.自激振动:机械加工过程中,在没有周期性外力(相对于切削过程而言)作用下,由系统内部激发反馈产生的周期性振动,称为自激振动,简称颤振。
- 1、下载文档前请自行甄别文档内容的完整性,平台不提供额外的编辑、内容补充、找答案等附加服务。
- 2、"仅部分预览"的文档,不可在线预览部分如存在完整性等问题,可反馈申请退款(可完整预览的文档不适用该条件!)。
- 3、如文档侵犯您的权益,请联系客服反馈,我们会尽快为您处理(人工客服工作时间:9:00-18:30)。
1.生产过程:指把原材料转变为成品的全过程。
2.工艺过程:机器生产过程中,改变生产对象的形状、尺寸、相对位置和物理、力学性能等使其成为成
品或半成品的过程。
3.热处理工艺过程:在热处理车间,对机器零件的半成品通过各种热处理方法,直接改变它们的材料性
质的过程,称为热处理工艺过程。
4.装配工艺过程:将合格的机器零件和外购件,标准件装配成组件,部件和机器的过程,则称为装配工
艺过程。
5.机械加工工艺过程:用机械加工方法逐步改变毛坯的形态,使其成为合格零件所进行的全部过程。
6.生产纲领:机器产品在计划期内应当生产的产品产量和进度计划称为该产品的生产纲领。
7.生产批量:指一次投入或产出的同一产品或零件的数量。
8.生产类型:单件生产、成批生产、大量生产(13年、14年)
9.工艺规程:规定产品或零部件机械加工工艺过程和操作方法等的工艺文件。
10.机械加工工艺规程:规定产品或零部件机械加工工艺过程和操作方法等的工艺文件。
(14年)
11.基准:在零件图上或实际的零件上,用来确定其它点、线、面的位置时所依据的点、线、面。
12.设计基准:零件工作图上用来确定其它点、线、面位置的基准。
13.工艺基准:加工、测量和装配过程中使用的基准。
(13年)
14.工序基准:在工序图上用来确定本工序所加工表面加工后的位置尺寸和位置关系的基准。
15.定位基准:加工中用于定位的基准。
(14年)
16.测量基准:工件测量时所用的基准。
17.装配基准:在装配时用来确定零件或部件在机器中的相对位置所采用的基准。
18.工件定位:采取一定的约束措施来限制自由度,通常可用约束点群来描述,而且一个自由度只需要一
个约束点来限制。
19.定位:使工件在机床或夹具中占有正确的位置。
20.装夹:将工件在机床上或夹具中定位,夹紧的过程称为装夹。
21.定位误差:指由于工件定位造成的加工面相对工序基准的位置误差。
22.基准不重合误差:由于定位基准与工序基准不一致所引起的定位误差。
23.基准位置误差:由于工件的定位表面或夹具上的定位元件制作不准确引起的定位误差。
24.六点定位原理:用六个支承点来分别限制工件的六个自由度,从而使工件在空间得到确定定位的方法。
25.完全定位:工件的六个自由度完全被限制的定位。
(14年)
26.不完全定位:按加工要求,允许有一个或几个自由度不被限制的定位。
(13年)
27.欠定位:按加工要求,工件应限制的自由度未被限制的定位。
28.过定位:工件的同一个自由度被两个或两个以上支承点重复限制的定位。
29.工序:一个或一组工人,在一个工作地点,对一个或同时几个工件所连续完成的那部分工艺过程。
(13
年)
30.安装:工件在机床或夹具中定位并夹紧的过程。
31.工位:工件在一次安装后,工件与夹具或设备的可动部分一起相对于刀具或设备的固定部分所占据的
每一个位置上所完成的那一部分工艺过程。
32.工步:在加工表面、切削刀具和切削用量都不变的情况下,所连续完成的那部分工艺过程。
33.行程:有些工步,由于余量较大或其它原因,需要用同一刀具,对同一表面进行多次切削,这样刀具
对工件每切削一次就称为一次行程
34.走刀:攻坚的每一次切削称为一次走刀。
35.零件的结构工艺性:指所设计的零件在能满足使用要求的前提下制造的可行性和经济性。
(13年、14
年)
36.精基准:使用已经机械加工的表面作为定位基准。
37.粗基准:使用未经机械加工的表面作为定位基准。
38.基准统一原则:整个工艺过程或有关的几道工序采用同一个(或同一组)定位基准来定位。
39.基准重合:用设计基准作为精基准,以消除基准不重合误差。
(13年)
40.基准重合:用设计基准作为精基准,以消除基准不重合误差。
(13年)
41.工序分散:工序分散是将工件的加工分散在较多的工序内进行,因而每道工序的工步少,工艺路线长。
42.工序集中: 工序集中就是将工件的加工集中集中在少数几道工序内完成。
每道工序的加工内容较多。
(13年)
43.加工余量:零件在加工过程中,从加工表面上切除的金属层厚度。
44.工序余量:相邻两工序尺寸之差。
45.工序尺寸;各工序应保证的加工尺寸,通常为加工面至定位基准面之间的尺寸。
46.工艺尺寸:工艺尺寸是根据加工的需要,在工艺附图或工艺规程中所给出的尺寸。
47.环:把列入工艺尺寸链中的每一个工艺尺寸称为环。
48.封闭环:在零件加工过程中最后形成的一环称为封闭环。
49.组成环:在工艺尺寸链中对封闭环有影响的全部环称为组成环。
50.尺寸链:尺寸链是在机器装配或零件机械加工过程中,由若干个相互关联尺寸所形成的尺寸封闭形式。
51.工艺尺寸链:在工艺过程中,由同一零件上的与工艺相关的尺寸所形成的尺寸链。
(14年)
52.时间定额:是指在一定生产条件下,规定生产一件产品或完成一道工序所需消耗的时间。
(13年)
53.劳动生产率:一个工人在单位时间内生产出合格产品的数量,也可以用完成单件产品或单个工序所消
耗的劳动时间来衡量
54.工艺成本:
55.加工精度:零件加工后的实际几何参数(尺寸、形状和表面间的相互位置)与理想几何参数的符合程
度。
56.加工误差:加工后零件的实际几何参数(尺寸、形状和表面间的相互位置)对理想几何参数的偏离程
度。
(14年)
57.工艺系统:指在机械加工时,机床、夹具、刀具和工件构成的一个完整的系统。
58.原始误差:工艺系统的误差。
59.原理误差:即在加工中采用了近似的加工运动、近似的刀具轮廓和近似的加工方法而产生的原始误差。
60.试切法:通过试切——测量加工尺寸——调整刀具位置——试切的反复过程来获得距离尺寸精度
61.调整法:在成批,大量生产中,广泛采用试切法预先调整好刀具对工件的相对位置,并在一批零件的
加工过程中采用保持这种相对位置不变来获得所需要的零件尺寸。
62.经济加工精度:在正常加工条件下所能保证的加工精度和表面粗糙度。
(13年)
63.误差敏感方向:对加工精度影响最大的那个方向。
(13年)
64.误差复映:由于工艺系统受力变形的变化而使毛坯椭圆形状误差复映到加工后工件表面的现象(14年)
65.主轴回转误差:指主轴实际回转轴线相对于其理想回转轴线的漂移。
66.主轴回转精度:主轴实际回转精度线相对其理想回转精度线的相符程度。
67.导轨导向误差:指机床导轨副的运动件实际运动方向与理想运动方向之间的偏差值。
68.系统误差:在顺序加工一批工件中其加工误差的大小和方向都保持不变或者按一定规律变化,则称为
系统误差。
(13年)
69.随机误差:在顺序加工一批工件时,误差的大小和方向呈无规律变化着,称为随机误差。
(14年)
70.工艺系统刚度:工艺系统抵抗变形的能力。
71.机械加工表面质量:零件加工后的表面层状态
72.残余应力:由于切削力和切削热的综合作用,表面层金属晶格会发生不同程度的塑性变形或产生金相
组织的变化,使表层金属产生的应力。
73.自激振动:机械加工过程中,在没有周期性外力作用下,由系统内部激发反馈产生的周期性振动。
74.强迫振动:由于外界(相对于切削过程而言)周期性干扰力的作用而引起的振动。
75.装配:按规定的技术要求将零件或部件进行组配和连接,使之成为半成品或成品的工艺过程。
76.装配单元:为保证有效地进行装配工作,通常将机器划分为若干能进行独立装配的部分,成为装配单
元。
77.互换装配法:按互换程度的不同分为完全互换装配法和大数互换装配法。
(13年)
78.完全互换装配法:在全部产品中,装配时各组成不需挑选或改变其大小位置,装配后即能达到装配精
度的要求。
79.大数互换装配法:在绝大多数产品中,装配时各组成不需挑选或改变其大小位置,装配后即能达到装
配精度的要求。
80.修配装配法:是将尺寸链中各组成环按经济加工精度制造。
装配时,通过改变尺寸链中某一预先确定
的组成环尺寸的方法来保证装配精度。
(14年)
81.分组装配法:
82.调整装配法:在装配时,用改变产品中可调整零件的相对位置或选用合适的调整件以达到装配精度的
方法。
83.选择装配法:将尺寸链中组成环的公差放大到经济可行的程度,然后选择合适的零件进行装配,以保
证装配精度的要求。