铝合金压铸件资料
压铸铝合金材料

压铸铝合金材料一、引言压铸铝合金是一种常见的金属材料,具有良好的流动性和成型性能,广泛应用于汽车、电子、航空航天等行业。
其中,ADC12是一种常见的压铸铝合金材料,具有优异的机械性能和耐腐蚀性能。
本文将对ADC12材料的组成、性能、加工工艺以及应用进行详细介绍。
二、ADC12材料的组成ADC12是由铝、硅、铜、铁、锰、镁等元素组成的铝合金。
其中,铝的含量在90%以上,硅的含量在9.6%-12.0%之间,铜的含量在0.5%以下,铁的含量在0.9%以下,锰的含量在0.3%以下,镁的含量在0.3%以下。
此外,还可以添加少量的锌、钛、铬等元素进行合金化处理。
三、ADC12材料的性能1.机械性能:ADC12材料具有较高的强度和硬度,拉伸强度高达290MPa,屈服强度高达220MPa,延伸率为3%以上。
同时,硬度达到80HB,具有良好的抗磨性和耐冲击性。
2.热物性能:ADC12材料具有良好的热导性和热膨胀性能,热导率为90W/(m·K),线性热膨胀系数为23.6×10-6/K。
3.化学性能:ADC12材料具有良好的耐腐蚀性能,抗蚀性能优于纯铝。
在常温下,可以耐受氧化性酸、弱碱以及一些有机溶剂的腐蚀。
4.加工性能:ADC12材料具有良好的流动性,可以通过压铸工艺进行加工。
同时,ADC12材料的热处理性能也较好,可以通过退火、固溶处理等工艺进行调整。
四、ADC12材料的加工工艺ADC12材料通常采用压铸工艺进行加工。
具体流程如下:1.原料准备:按照所需比例准备铝合金原料,包括铝、硅、铜、铁、锰、镁等元素。
2.熔炼:将铝合金原料放入炉中进行熔炼,熔炼温度通常在650-750°C之间。
3.发泡:在熔融的铝合金中通入发泡剂,使其膨胀成泡沫状。
4.浇铸:将膨胀后的铝合金液体倒入压铸模具中,进行铸造。
5.冷却:冷却后,将铝合金零件从模具中取出,进行后续的修整和加工。
五、ADC12材料的应用ADC12材料具有优异的机械性能和耐腐蚀性能,在汽车、电子、航空航天等行业得到广泛应用。
压铸件知识

1.壓鑄材料基本資料介紹
2.壓鑄件生產流程
合金材料
材料介紹
壓鑄件又稱鋁合金件,它主要成分是由以下元素組成:
鋁 Al
94% 以上
矽 Si
1% 以下
鐵 Fe
銅
錳
鎂
鋅
鎳
錫 Sn
鉛 Pb 雜 質
鈦 Ti 雜 質
Cu Mn Mg Zn Ni
0.8% 0.1% 0.4% 2.5% 0.4% 以下 以下 以下 至 至 0.6% 4.0%
下料
---把半成品從毛胚中沖出來
打磨
修毛邊
把部品上的毛邊剃除
整型
檢驗
檢驗重點: 1.檢查產品是否有拉 模、縮水、缺料、裂 紋等不良現象; 2.表面是否有毛邊殘 留、利邊、刮傷等現 象; 3.孔徑大小是否符合 要求; 4.產品是否有變形。
包裝
氣泡袋包裝,注意產品不可堆疊過 高,且需輕拿輕放
0.1% 0.1% 以下 以下
它具有良好的耐蝕性及延伸性(7.5%)
Hale Waihona Puke 型模具模具鋼材材質為:8407 它具有良好的耐高溫及抗強壓等特性
壓鑄件生產流程
壓鑄 下料 包裝 打磨 檢驗 修毛邊 整型
壓鑄
壓鑄成型條件: 1.熔爐溫度680正負20度。 2.模具溫度230正負20度。 3.射出速度為1.2m每秒。 4.高速二段為175m每秒。 5.射出壓力105KG每立方 厘米。 6.產品冷卻時間為1.5秒。
铝合金压铸件标准规范
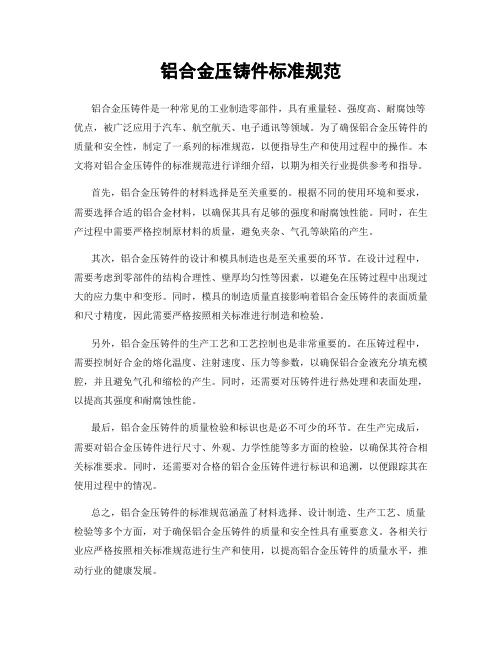
铝合金压铸件标准规范铝合金压铸件是一种常见的工业制造零部件,具有重量轻、强度高、耐腐蚀等优点,被广泛应用于汽车、航空航天、电子通讯等领域。
为了确保铝合金压铸件的质量和安全性,制定了一系列的标准规范,以便指导生产和使用过程中的操作。
本文将对铝合金压铸件的标准规范进行详细介绍,以期为相关行业提供参考和指导。
首先,铝合金压铸件的材料选择是至关重要的。
根据不同的使用环境和要求,需要选择合适的铝合金材料,以确保其具有足够的强度和耐腐蚀性能。
同时,在生产过程中需要严格控制原材料的质量,避免夹杂、气孔等缺陷的产生。
其次,铝合金压铸件的设计和模具制造也是至关重要的环节。
在设计过程中,需要考虑到零部件的结构合理性、壁厚均匀性等因素,以避免在压铸过程中出现过大的应力集中和变形。
同时,模具的制造质量直接影响着铝合金压铸件的表面质量和尺寸精度,因此需要严格按照相关标准进行制造和检验。
另外,铝合金压铸件的生产工艺和工艺控制也是非常重要的。
在压铸过程中,需要控制好合金的熔化温度、注射速度、压力等参数,以确保铝合金液充分填充模腔,并且避免气孔和缩松的产生。
同时,还需要对压铸件进行热处理和表面处理,以提高其强度和耐腐蚀性能。
最后,铝合金压铸件的质量检验和标识也是必不可少的环节。
在生产完成后,需要对铝合金压铸件进行尺寸、外观、力学性能等多方面的检验,以确保其符合相关标准要求。
同时,还需要对合格的铝合金压铸件进行标识和追溯,以便跟踪其在使用过程中的情况。
总之,铝合金压铸件的标准规范涵盖了材料选择、设计制造、生产工艺、质量检验等多个方面,对于确保铝合金压铸件的质量和安全性具有重要意义。
各相关行业应严格按照相关标准规范进行生产和使用,以提高铝合金压铸件的质量水平,推动行业的健康发展。
铝合金压铸件公差标准

铝合金压铸件公差标准铝合金压铸件是一种常见的工业零部件,其制造过程需要严格控制公差,以确保产品质量和性能。
在铝合金压铸件的生产过程中,公差标准是非常重要的,它直接影响着产品的精度和可靠性。
因此,制定和遵守铝合金压铸件公差标准对于保证产品质量和满足客户需求至关重要。
首先,铝合金压铸件的公差标准应该符合国家相关标准和行业规范。
在中国,铝合金压铸件的公差标准主要参照国家标准GB/T 15115-1994《压铸铝合金铸件尺寸公差》。
这一标准规定了铝合金压铸件的尺寸公差范围,包括线性尺寸、角度尺寸、曲面尺寸等方面的公差要求。
遵循国家标准可以保证铝合金压铸件的制造符合国家法律法规,同时也有利于产品在国际市场上的竞争力。
其次,铝合金压铸件的公差标准应该根据产品的具体要求和用途进行制定。
不同的铝合金压铸件在使用过程中会面临不同的工作环境和载荷条件,因此其公差标准也会有所不同。
例如,对于汽车发动机的铝合金压铸件,其公差标准需要更加严格,以确保零部件在高温、高压的工作环境下能够保持稳定的尺寸和形状。
而对于一般工业设备上使用的铝合金压铸件,其公差标准可以相对宽松一些。
因此,制定铝合金压铸件公差标准时,需要充分考虑产品的具体用途和工作条件。
另外,铝合金压铸件的公差标准还应该考虑到制造工艺的可行性和经济性。
过于严格的公差标准可能会导致生产成本的大幅增加,甚至影响产品的生产效率和良品率。
因此,在制定公差标准时,需要充分考虑到制造工艺的限制,尽量在保证产品质量的前提下,尽量减少公差范围,以降低生产成本,提高生产效率。
总的来说,铝合金压铸件的公差标准是确保产品质量和性能的重要保障,制定合理的公差标准对于提高产品质量、降低生产成本、满足客户需求具有重要意义。
因此,企业在制定和执行铝合金压铸件公差标准时,需要充分考虑国家标准、产品要求和制造工艺,以确保产品质量和生产效率的双重目标的实现。
铝合金压铸件材料

铝合金压铸件材料铝合金压铸件以其优异的性能和广泛的应用,在现代工业中占据了重要的地位。
在本文中,我们将对铝合金压铸件的材料进行详细的盘点,帮助您了解这一领域的最新发展。
一、铝合金的种类铝合金是铝与其它金属元素通过熔炼而成的合金。
根据主要添加的金属元素不同,铝合金可以分为多个种类,如铝镁合金、铝锌合金、铝硅合金等。
这些合金在压铸过程中表现出不同的物理和化学特性,使得铝合金压铸件具有多样化的性能。
二、铝合金压铸件的特点1.重量轻:铝合金的密度远低于钢铁和铜等金属,使得铝合金压铸件具有轻量化优势,可有效降低产品的重量。
2.耐腐蚀:铝合金表面能形成一层致密的氧化膜,具有良好的耐腐蚀性,适合于各种复杂环境的应用。
3.高强度:经过合理的合金设计和热处理工艺,铝合金压铸件可达到较高的强度和刚性,能够满足各种强度要求。
4.良好的铸造性能:铝合金熔点低,流动性好,易于实现压铸成型,且铸件表面光滑,减少后续加工量。
5.良好的导电性和导热性:铝合金具有良好的导电和导热性能,适用于电子元件、散热器等对导电和导热性能要求较高的领域。
三、铝合金压铸件的应用1.汽车工业:铝合金压铸件广泛应用于汽车领域,如发动机部件、底盘零件、车身结构件等,以实现汽车轻量化,提高燃油经济性和减排效果。
2.电子电器:铝合金压铸件用于制造电子元件、连接器、端子、散热器等部件,具有良好的导电、导热性能和耐腐蚀性。
3.建筑行业:铝合金压铸件如门窗、幕墙、栏杆等,具有美观、耐用、防火等特点,广泛应用于建筑领域。
4.五金工具:铝合金压铸件用于制造各种五金工具,如把手、支架、壳体等,具有良好的强度和耐腐蚀性。
5.家用电器:铝合金压铸件用于制造家用电器部件,如冰箱、洗衣机、空调等的外壳和内部结构件,具有良好的美观度和耐用性。
通过以上的介绍,相信您对铝合金压铸件的材料有了更深入的了解。
随着科技的不断发展,铝合金压铸件的性能和应用领域将不断拓展,为我们的生活和工作带来更多的便利和价值。
低压压铸铝合金件标准
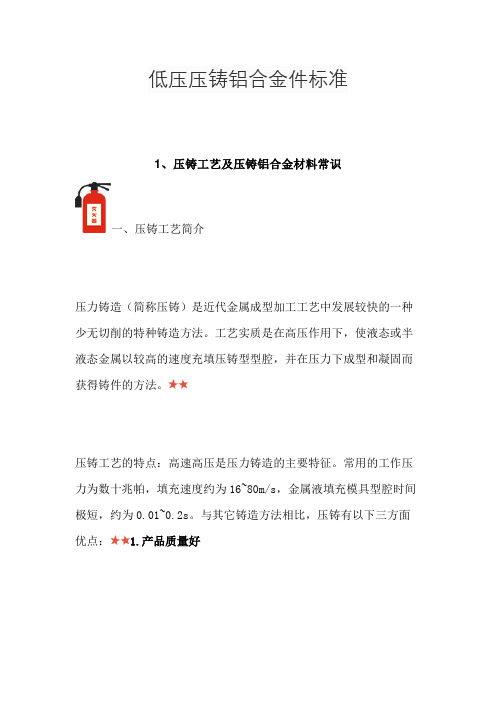
低压压铸铝合金件标准1、压铸工艺及压铸铝合金材料常识一、压铸工艺简介压力铸造(简称压铸)是近代金属成型加工工艺中发展较快的一种少无切削的特种铸造方法。
工艺实质是在高压作用下,使液态或半液态金属以较高的速度充填压铸型型腔,并在压力下成型和凝固而获得铸件的方法。
压铸工艺的特点:高速高压是压力铸造的主要特征。
常用的工作压力为数十兆帕,填充速度约为16~80m/s,金属液填充模具型腔时间极短,约为0.01~0.2s。
与其它铸造方法相比,压铸有以下三方面优点: 1.产品质量好铸件尺寸精度高,一般相当于6~7级,甚至可达4级;表面光洁度好,一般相当于5~8级;强度和硬度较高,强度一般比砂型铸造提高25~30%,但延伸率降低约70%;尺寸稳定,互换性好;可压铸薄壁复杂的铸件。
例如,当前锌合金压铸件最小壁厚可达0.3mm;铝合金铸件可达0.5mm;最小铸出孔径为0.7mm;最小螺距为0.75mm。
2.生产效率高机器生产率高,例如国产J1113型卧式冷空压铸机平均八小时可压铸600~700次,小型热室压铸机平均每八小时可压铸3000~7000次;压铸型寿命长,一付压铸型,压铸钟合金,寿命可达几十万次,甚至上百万次;易实现机械化和自动化。
3.经济效果优良由于压铸件尺寸精确,表泛光洁等优点。
一般不再进行机械加工而直接使用,或加工量很小,所以既提高了金属利用率,又减少了大量的加工设备和工时;铸件价格便易;可以采用组合压铸以其他金属或非金属材料。
既节省装配工时又节省金属。
压铸是最先进的金属成型方法之一,是实现少切屑,无切屑的有效途径,应用很广,发展很快。
目前压铸合金不再局限于有色金属的锌、铝、鎂和铜,而且也逐渐扩大用来压铸铸铁和铸钢件。
压铸件的尺寸和重量,取决于压铸机的功率。
由于压铸机的功率不断增大,铸件形尺寸可以从几毫米到1~2m;重量可以从几克到数十公斤。
国外可压铸直径为2m,重量为50kg的铝铸件。
二、压铸合金用于生产压铸件的金属材料有多为铝合金、纯铝、锌合金、铜合金、镁合金、铅合金、锡合金等有色金属,黑色金属很少采用。
铝合金压铸件的优点

铝合金压铸件的优点1. 强度高铝合金压铸件具有较高的强度。
铝合金相比于其他金属材料,具有较高的比强度和比刚度,这使得铝合金压铸件在承受高载荷和应力的情况下表现出色。
铝合金压铸件常用于制造汽车引擎和车身部件、飞机结构件等对强度要求高的领域。
2. 轻量化铝合金压铸件的密度较低,大约为铁的三分之一。
相对于其他金属材料,铝合金压铸件具有轻质化的特点,能够减少结构的自重。
在汽车、航空航天、电子产品等领域,使用铝合金压铸件可以使产品更加轻便,提升产品的性能和效率。
3. 成型性好铝合金压铸件具有良好的成型性,能够制造出复杂形状和精密尺寸的零件。
通过压铸工艺,铝合金可以在较短的时间内充分充填模具,实现尺寸精密度高、表面光滑度好的成型。
这种成型性优势使得铝合金压铸件在制造汽车发动机零件、家用电器外壳等产品时得到广泛应用。
4. 密封性好铝合金压铸件的表面质量好,能够实现较高的密封性。
铝合金压铸件在成型过程中,可以通过控制合金成分、优化工艺参数等方式,实现零件表面的致密性和抗氧化性的提升。
因此,铝合金压铸件常用于制造需要高密封性的产品,如汽车发动机缸盖、气门室盖等。
5. 导热性能好铝合金具有良好的导热性能,使得铝合金压铸件在导热要求较高的领域有广泛应用。
铝合金压铸件可以有效传导和分散热量,防止热点集中和局部温度过高。
因此,铝合金压铸件常用于制造散热器、电子设备外壳等产品。
6. 再生利用性高铝合金压铸件具有良好的可循环利用性。
铝合金可以经过再生循环,保持其原有的性能和质量。
铝合金压铸件可以通过熔化再铸的方式,将废旧件再次利用,减少资源消耗和环境污染。
这种再生利用性使得铝合金压铸件成为可持续发展的重要材料。
7. 耐腐蚀性好铝合金压铸件具有较好的耐腐蚀性。
铝合金与空气中的氧气反应生成致密的氧化铝,形成一层保护膜,防止铝继续被腐蚀。
在一些潮湿、腐蚀性环境中,使用铝合金压铸件可以有效延长产品的使用寿命,降低维护成本。
8. 表面处理性好铝合金压铸件表面易于进行各种处理。
汽车用铝合金压铸件

汽车用铝合金压铸件随着汽车工业的快速发展,铝合金压铸件作为一种重要的汽车零部件材料,正逐渐得到广泛应用。
本文将从铝合金压铸件的特点、应用领域、制造工艺以及未来发展趋势等方面进行介绍和分析。
铝合金压铸件是指通过压铸工艺将铝合金熔液注入到模具中,经过凝固和冷却后得到的零部件。
相比于传统的铸造工艺,铝合金压铸件具有以下几个显著的特点。
铝合金压铸件具有较高的强度和刚性。
铝合金本身具有良好的机械性能,经过压铸工艺后,其内部组织更加致密,结构更加均匀,因此能够获得更高的强度和刚性。
铝合金压铸件具有良好的表面质量和尺寸精度。
压铸工艺能够快速、高效地制造出形状复杂的零部件,且表面光洁度高,尺寸稳定性好,能够满足汽车工业对于外观和精度的要求。
铝合金压铸件具有较好的耐腐蚀性和耐热性。
铝合金具有良好的耐腐蚀性,能够适应汽车在各种恶劣环境下的使用要求。
而且铝合金具有较低的熔点和热膨胀系数,能够耐受高温条件下的使用,不易变形和破裂。
铝合金压铸件在汽车工业中有着广泛的应用。
首先,它被广泛应用于汽车车身和车身结构件。
汽车车身需要具备较高的强度和刚性,而铝合金压铸件能够满足这一要求。
其次,铝合金压铸件还广泛用于汽车发动机零部件,如缸盖、曲轴箱等。
铝合金的导热性能好,能够有效地散热,提高发动机的工作效率。
此外,铝合金压铸件还用于汽车悬挂系统、传动系统和制动系统等。
铝合金压铸件的制造工艺主要包括模具设计、合金熔炼、模具注液、凝固冷却、脱模清理等环节。
模具设计是关键,需要根据零部件的形状和尺寸来确定模具的结构和材料。
合金熔炼是将铝合金材料加热熔化,得到熔液的过程。
模具注液是将熔液注入到模具中,并保持一定的压力,使熔液充满整个模腔。
凝固冷却是指熔液在模具中逐渐冷却凝固,形成零部件的过程。
脱模清理是将凝固后的零部件从模具中取出,并进行除渣、修整等工艺处理。
未来,随着汽车工业的不断发展,铝合金压铸件在汽车领域的应用将会进一步扩大。
一方面,随着汽车整车质量的减轻和节能环保的要求,铝合金作为轻质材料将会得到更广泛的应用。
铝合金压铸培训资料

铝合金压铸培训资料铝合金压铸是一种常见的金属成型工艺,广泛应用于汽车、航空航天、电子等领域。
本文将介绍铝合金压铸的基本原理、工艺流程以及注意事项。
一、铝合金压铸基本原理铝合金压铸是指将熔化的铝合金注入压铸机的模具中,在高压下冷却固化成型的工艺。
其基本原理是利用压铸机的合模装置将熔化的铝合金注入模具中,通过高压力将铝液充满整个模腔,并在冷却过程中产生固化缩胀,最终得到所需的铝合金零件。
二、铝合金压铸工艺流程1. 模具准备:选择合适的压铸机和模具,根据产品设计要求制作模具,并进行必要的模具调试。
2. 材料准备:选择适合的铝合金材料,并按照配比准备好所需的铝合金料。
同时,将冷却水和切削液配置好。
3. 熔炼铝合金:将铝合金料加热熔化,控制好熔化温度和熔化时间,确保熔化的铝合金质量符合要求。
4. 注铸:将熔化的铝合金通过喷杆注入模具中,控制注铸时间和注铸速度,使得铝液充分填充整个模腔。
5. 冷却固化:铝液在注铸过程中受到冷却水的冷却,逐渐固化成型。
冷却固化时间根据具体工艺要求进行控制。
6. 脱模:经过冷却固化后的铝合金零件从模具中取出,注意避免零件变形或损坏。
7. 修整:对脱模后的铝合金零件进行去毛刺、抛光、修整等工艺处理,使其达到产品要求的表面粗糙度和尺寸精度。
8. 检验:对修整后的铝合金零件进行质量检验,包括外观检查、尺寸测量、力学性能测试等项目。
9. 表面处理:根据产品要求进行表面处理,如喷涂、氧化、电泳等工艺,提高零件的耐腐蚀性和美观度。
10. 包装出货:对完成质量检验合格的铝合金零件进行包装,并按照客户要求进行出货。
三、铝合金压铸注意事项1. 模具选择:根据产品设计要求选择合适的模具材料和结构,确保模具的强度和寿命。
2. 材料选择:根据产品性能要求选择合适的铝合金材料,避免因材料不合适导致的缺陷和失效。
3. 工艺参数控制:控制好注铸温度、注铸速度、冷却水温度等工艺参数,确保铝液充分填充模腔并冷却固化。
压铸铝合金材料
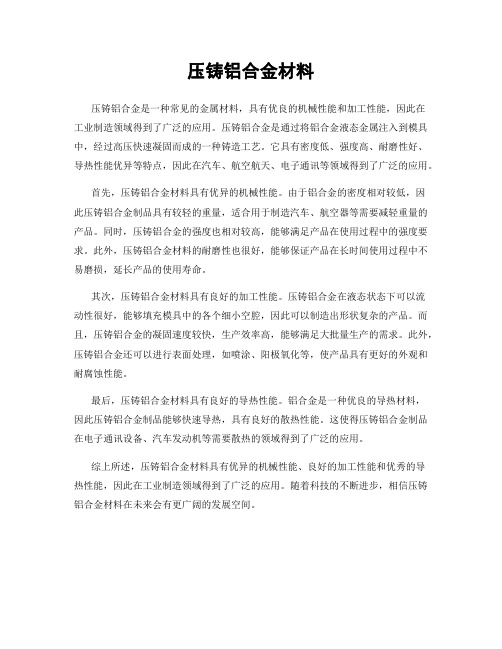
压铸铝合金材料
压铸铝合金是一种常见的金属材料,具有优良的机械性能和加工性能,因此在
工业制造领域得到了广泛的应用。
压铸铝合金是通过将铝合金液态金属注入到模具中,经过高压快速凝固而成的一种铸造工艺。
它具有密度低、强度高、耐磨性好、导热性能优异等特点,因此在汽车、航空航天、电子通讯等领域得到了广泛的应用。
首先,压铸铝合金材料具有优异的机械性能。
由于铝合金的密度相对较低,因
此压铸铝合金制品具有较轻的重量,适合用于制造汽车、航空器等需要减轻重量的产品。
同时,压铸铝合金的强度也相对较高,能够满足产品在使用过程中的强度要求。
此外,压铸铝合金材料的耐磨性也很好,能够保证产品在长时间使用过程中不易磨损,延长产品的使用寿命。
其次,压铸铝合金材料具有良好的加工性能。
压铸铝合金在液态状态下可以流
动性很好,能够填充模具中的各个细小空腔,因此可以制造出形状复杂的产品。
而且,压铸铝合金的凝固速度较快,生产效率高,能够满足大批量生产的需求。
此外,压铸铝合金还可以进行表面处理,如喷涂、阳极氧化等,使产品具有更好的外观和耐腐蚀性能。
最后,压铸铝合金材料具有良好的导热性能。
铝合金是一种优良的导热材料,
因此压铸铝合金制品能够快速导热,具有良好的散热性能。
这使得压铸铝合金制品在电子通讯设备、汽车发动机等需要散热的领域得到了广泛的应用。
综上所述,压铸铝合金材料具有优异的机械性能、良好的加工性能和优秀的导
热性能,因此在工业制造领域得到了广泛的应用。
随着科技的不断进步,相信压铸铝合金材料在未来会有更广阔的发展空间。
铝合金压铸件的标准
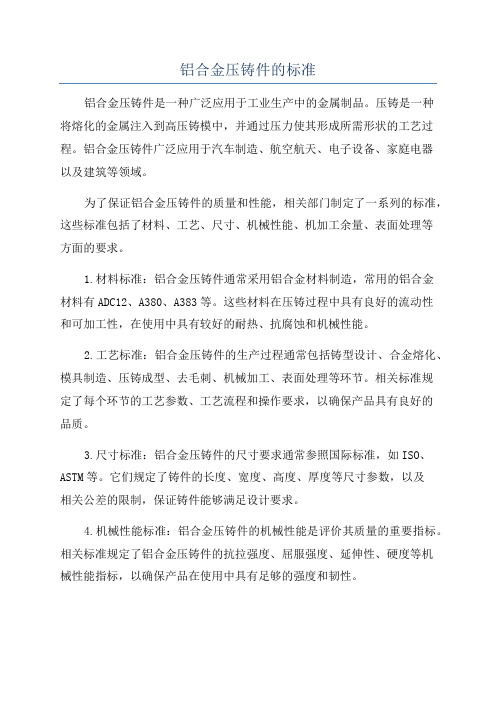
铝合金压铸件的标准铝合金压铸件是一种广泛应用于工业生产中的金属制品。
压铸是一种将熔化的金属注入到高压铸模中,并通过压力使其形成所需形状的工艺过程。
铝合金压铸件广泛应用于汽车制造、航空航天、电子设备、家庭电器以及建筑等领域。
为了保证铝合金压铸件的质量和性能,相关部门制定了一系列的标准,这些标准包括了材料、工艺、尺寸、机械性能、机加工余量、表面处理等方面的要求。
1.材料标准:铝合金压铸件通常采用铝合金材料制造,常用的铝合金材料有ADC12、A380、A383等。
这些材料在压铸过程中具有良好的流动性和可加工性,在使用中具有较好的耐热、抗腐蚀和机械性能。
2.工艺标准:铝合金压铸件的生产过程通常包括铸型设计、合金熔化、模具制造、压铸成型、去毛刺、机械加工、表面处理等环节。
相关标准规定了每个环节的工艺参数、工艺流程和操作要求,以确保产品具有良好的品质。
3.尺寸标准:铝合金压铸件的尺寸要求通常参照国际标准,如ISO、ASTM等。
它们规定了铸件的长度、宽度、高度、厚度等尺寸参数,以及相关公差的限制,保证铸件能够满足设计要求。
4.机械性能标准:铝合金压铸件的机械性能是评价其质量的重要指标。
相关标准规定了铝合金压铸件的抗拉强度、屈服强度、延伸性、硬度等机械性能指标,以确保产品在使用中具有足够的强度和韧性。
5.机加工余量标准:铝合金压铸件通常需要进行进一步的机械加工,比如铣削、切割、钻孔等。
相关标准规定了机加工余量的限制,以确保在机加工过程中不会影响铝合金压铸件的尺寸和性能。
6.表面处理标准:铝合金压铸件在生产后通常需要进行表面处理,以提高其耐腐蚀性、耐磨性和美观度。
常用的表面处理方法包括喷涂、阳极氧化、电泳涂装等。
相关标准规定了表面处理的方法、工艺和要求,以确保产品具有所需的表面性能。
总结起来,铝合金压铸件的标准涵盖了材料、工艺、尺寸、机械性能、机加工余量和表面处理等方面的要求,以确保产品的质量和性能。
这些标准不仅适用于压铸生产厂家,也为用户提供了选择和评估铝合金压铸件的指导依据。
压铸合金的分类及特点

压铸合金的分类及特点压铸合金是一种重要的材料,广泛应用于汽车、航空航天、电子、机械等行业。
根据不同的成分和特性,压铸合金可以分为多个不同的分类,每一类别都有其独特的特点和应用领域。
一、铝合金压铸件铝合金是最常见的压铸合金材料之一。
铝合金具有良好的铸造性能,可以通过压铸工艺制造复杂形状的零件。
铝合金压铸件的特点如下:1. 低密度:铝合金密度低,约为铁的1/3,具有轻量化的优势,适用于要求重量轻的产品。
2. 良好的导热性能:铝合金具有良好的导热性能,适用于需要散热或导电的应用。
3. 良好的机械性能:铝合金具有较高的强度和硬度,可以满足一些要求较高的应用。
4. 良好的耐腐蚀性:铝合金具有较好的耐腐蚀性,可以适应多种环境。
5. 可加工性好:铝合金易于加工,可实现高精度的加工要求。
二、镁合金压铸件镁合金是另一种常用的压铸合金材料。
与铝合金相比,镁合金具有更低的密度和更好的机械性能。
镁合金压铸件的特点如下:1. 轻质高强:镁合金密度较低,约为铝的2/3,具有较高的强度,适用于要求轻量化和高强度的产品。
2. 良好的刚性和耐冲击性:镁合金具有较好的刚性和耐冲击性,适用于要求高刚性和耐冲击的应用。
3. 良好的导电性和导热性:镁合金具有良好的导电性和导热性能,适用于需要散热或导电的应用。
4. 良好的耐腐蚀性:镁合金具有较好的耐腐蚀性,可以适应多种环境。
5. 难加工性:与铝合金相比,镁合金的加工性能较差,加工难度较大。
三、锌合金压铸件锌合金是常用的压铸合金材料之一,具有良好的流动性和耐腐蚀性。
锌合金压铸件的特点如下:1. 低熔点:锌合金的熔点较低,易于熔化和铸造。
2. 良好的流动性:锌合金具有良好的流动性,适用于制造复杂形状的零件。
3. 良好的耐腐蚀性:锌合金具有较好的耐腐蚀性,可以适应多种环境。
4. 良好的表面处理性能:锌合金可以通过多种表面处理方法进行处理,获得良好的表面质量和外观效果。
5. 低强度:锌合金的强度较低,适用于一些要求强度不高的应用。
铝合金压铸件五大特性

一、耐久性
铝的稳定性强、耐氧化,铝合金铸件不会生锈、耐腐蚀;表面采用静电粉末喷涂及氟碳涂料,制造出来的各种大型室内外装饰制品可长久保持不褪色。
二、可性
铝的延展性好,便于各种造型设计。有韧性,可反复循环使用,应用范围更为广泛。
三、安全性
经过各种严格的试验,保证铝制品对地震、风压、风化的抵抗强度。独特的铝合金铸造法使制造出的工作重量更轻,减轻搬运施工作业中的负担,减少危险发生。
四、创意性
纹饰由专业设计师专门设计,引领世界潮流。可根据业主喜好,另行设计纹饰,打造家居专属特权。
五、重量轻
铝的重量轻,安装和维护更为方便。
铝合金压铸件很久以来就在不断地发展,中国的铝合金压铸件行业取得了令人惊叹的发展,已发展为一个新兴产业。目前,工艺已成为汽车用铝合金成形工艺中应用最广泛的工艺之一。铝合金压铸类产品主要用于电子、汽车、电机、家电和一些通讯行业等,一些高性能、高精度、高韧性的优质铝合金产品也被用于大型飞机、船舶等要求比较高的行业中。主要的用途还是在一些器械的零件上。
铝合金压铸件的缺陷分析

铝合金压铸件的缺陷分析铝合金压铸件是指通过将铝合金熔化后注入铸模中,在高压下快速凝固而形成的铝合金制品。
它具有优异的机械性能、强度高、重量轻、加工性好等特点,因此广泛应用于汽车、航空航天、电子、建筑等领域。
然而,铝合金压铸件在制造过程中可能出现一些缺陷,影响其质量和性能。
下面将分析铝合金压铸件的常见缺陷及其原因:1.粘合缺陷:铝合金压铸件在注模过程中,由于铝液与铸模表面的接触面积较大,容易出现液态铝与模具表面产生粘合现象。
导致铸件表面出现明显的凹痕和粘合痕迹。
这种缺陷主要是由于铸造温度过高或模具表面粗糙度不足造成的。
2.空洞缺陷:空洞是指铸造件内部出现的孔洞。
空洞缺陷主要由于铝液在凝固过程中未完全填充铸型腔体,造成残留气体无法排出,从而形成气孔。
这种缺陷主要是由于铸造温度过低、注模速度过快、铝液中气体含量过高等原因造成的。
3.热裂缺陷:热裂是指铸造件在冷却过程中,由于内部应力超过材料的强度极限而产生的裂纹。
热裂缺陷主要由于铝合金压铸件在凝固过程中温度梯度过大、结晶过程不均匀等原因造成的。
4.气泡缺陷:气泡是指铝合金压铸件内部出现的气体聚集。
气泡缺陷主要由于熔铝中的氢气在凝固过程中无法完全排出,导致气泡形成。
这种缺陷主要是由于熔铝中氢气含量过高、注模速度过快、温度过高等原因造成的。
5.灰斑缺陷:灰斑是指铝合金压铸件表面出现的较大灰白色斑点。
灰斑缺陷主要由于模具表面氧化层未能完全清除、铝液中含有过多的杂质等原因造成的。
为减少这些缺陷的出现,可以采取以下措施:1.控制铸造温度,确保合金能够充分熔化并达到适宜的流动性,避免温度过高或过低产生缺陷。
2.提高模具表面的粗糙度,以增加与铝液的接触面积,减少粘合缺陷的发生。
3.控制注模速度,确保铝液完全填充铸模腔体,避免空洞和气泡的产生。
4.控制铸造过程中的温度梯度,确保均匀凝固,减少热裂缺陷的发生。
5.提高熔铝的纯净度,减少杂质的含量,避免灰斑的产生。
综上所述,铝合金压铸件的缺陷主要包括粘合缺陷、空洞缺陷、热裂缺陷、气泡缺陷和灰斑缺陷。
铝压铸件最小壁厚标准
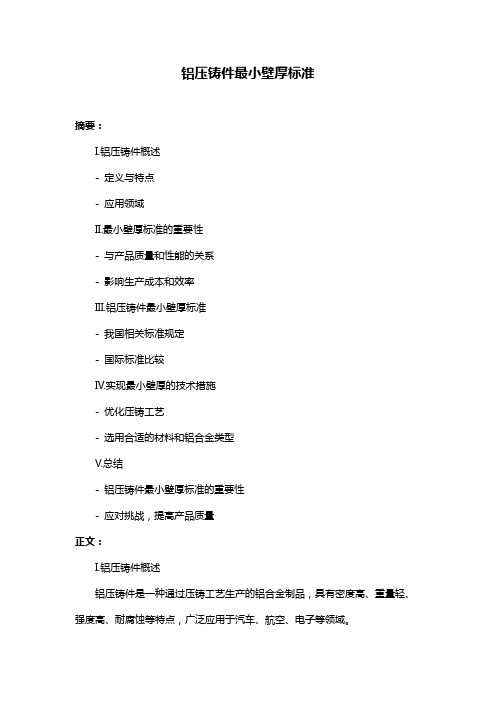
铝压铸件最小壁厚标准摘要:I.铝压铸件概述- 定义与特点- 应用领域II.最小壁厚标准的重要性- 与产品质量和性能的关系- 影响生产成本和效率III.铝压铸件最小壁厚标准- 我国相关标准规定- 国际标准比较IV.实现最小壁厚的技术措施- 优化压铸工艺- 选用合适的材料和铝合金类型V.总结- 铝压铸件最小壁厚标准的重要性- 应对挑战,提高产品质量正文:I.铝压铸件概述铝压铸件是一种通过压铸工艺生产的铝合金制品,具有密度高、重量轻、强度高、耐腐蚀等特点,广泛应用于汽车、航空、电子等领域。
II.最小壁厚标准的重要性铝压铸件的最小壁厚对于产品的质量和性能有着重要影响。
过薄的壁厚可能导致产品在使用过程中出现破裂、变形等安全隐患,而合适的壁厚不仅可以保证产品的使用寿命,还可以降低生产成本,提高生产效率。
III.铝压铸件最小壁厚标准我国对于铝压铸件最小壁厚的标准主要参考GB/T 15115-2008《铝及铝合金压铸件》标准,其中规定了各类铝及铝合金压铸件的最小壁厚要求。
在国际标准方面,主要参考ISO 3520-1998《铝及铝合金压铸件》和ASTM B85-2014《铝及铝合金压铸件标准规范》等,这些标准对于最小壁厚的规定也具有一定的参考价值。
IV.实现最小壁厚的技术措施要实现铝压铸件的最小壁厚,需要从压铸工艺和材料选择两方面进行优化。
首先,优化压铸工艺,如提高压铸压力、控制模具温度、采用局部加压等,以提高金属液的填充速度和充型完整性。
其次,选用合适的材料和铝合金类型,如采用高流动性、高塑性的铝合金材料,以降低最小壁厚的需求。
V.总结铝压铸件最小壁厚标准对于保证产品质量、性能及生产效率具有重要意义。
通过优化压铸工艺和选用合适的材料,可以实现最小壁厚的要求,从而满足生产需求。
铝合金压铸件

铝合金压铸件1 范围本标准规定了铝合金压铸件(以下简称压铸件)的材质、尺寸公差、角度公差、形位公差、工艺性要求和表面质量。
本标准适用于照相机、光学仪器等产品的铝合金压铸件。
2 规范性引用文件下列文件中的条款通过本标准的引用而成为本标准的条款。
凡是注明日期的引用文件,其随后所有的修改单(不包括勘误的内容)或修订版均不适用于本标准,然而,鼓励根据本标准达成协议的各方研究是否可使用这些文件的最新版本。
凡是不注日期的引用文件,其最新版本适用于本标准。
GB/T 6414—1999 铸件尺寸公差与机械加工余量GB/T 11334—1989 圆锥公差JIS H 5302—1990 压铸铝合金3 压铸铝合金3.1 压铸铝合金选用JIS H 5302—1990中的ADC10。
3.2 ADC10的化学成分表1给出。
其中铜的含量控制在不大于2.8 %。
a )抗拉强度σb :245 MPa;b )伸长率δ 5 :2 %;c )布氏硬度HBS(5/250/30):80。
4 铸件尺寸公差4.1 压铸件尺寸公差的代号、等级及数值压铸件尺寸公差的代号为CT。
尺寸公差等级选用GB/T6414—1999中的CT3 ~ CT8。
一般(未注)公差尺寸的公差等级基本规定为:照相机零件按CT6,其他产品零件按CT7。
尺寸公差数值表2给出。
4.2 壁厚尺寸公差壁厚尺寸公差一般比该压铸件的一般公差粗一级。
例如:一般公差规定为CT7,壁厚公差则为CT8。
当平均壁厚不大于1.2 mm时,壁厚尺寸公差则与一般公差同级,必要时,壁厚尺寸公差比一般公差精一级。
4.3 公差带的位置尺寸公差带应相对于基本尺寸对称分布,即尺寸公差的一半为正值,另一半取负值。
当有特殊要求时,也可采用非对称设置,此时应在图样上注明或在技术文件中规定。
对于有斜度要求的部位,其尺寸公差应沿斜面对称分布。
受分型面及型芯的影响而引起的固定增量和错型值,已包含在尺寸公差数值之内。
当需进一步限制错型值时,则应在图样上注明其允许的最大错型值。
压铸件
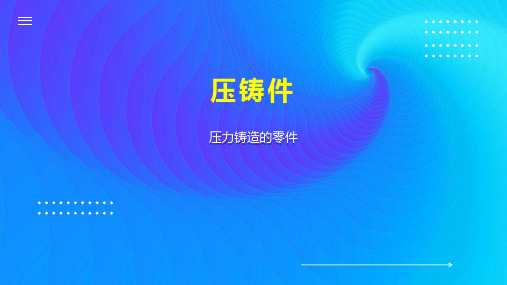
其他名称:缩凹、缩陷、憋气、塌边。
特征:铸件平滑表面上出现的凹瘪的部分,其表面呈自然冷却状态。
产生原因:1、铸件结构设计不合理,有局部厚实部位,产生热节。2、合金收缩率大。3、内浇口截面积太 小。4、比压低。5、模具温度太高。
排除措施:1、改善铸件结构,使壁厚稍为均匀,厚薄相差较大的连接处应逐步缓和过渡,消除热节。2、选 择收缩率小的合金。3、正确设置浇注系统,适当加大内浇口的截面积。4、增大压射力。5、适当调整模具热平 衡条件,采用温控装置以及冷却等。
其他名称:冷接(对接),水纹。
特征:温度较低的金属流互相对接但未熔合而出现的缝隙,呈不规则的线形,有穿透的和不穿透的两种,在 外力的作用下有发展的趋势。
产生原因:1、金属液浇注温度低或模具温度低。2、合金成分不符合标准,流动性差。3、金属液分股填充, 熔合不良。4、浇口不合理,流程太长。5、填充速度低或排气不良。6、比压偏低。
其他名称:空气孔、气眼。
特征:卷入压铸件内部的气体所形成的形状较为规则,表面较为光滑的孔洞。
产生原因:主要是包卷气体引起:1、浇口位置选择和导流形状不当,导致金属液进入型腔产生正面撞击和产 生旋涡。2、浇道形状设计不良。3、压室充满度不够。4、内浇口速度太高,产生湍流。5、排气不畅。6、模具 型腔位置太深。7、涂料过多,填充前未燃尽。8、炉料不干净,精炼不良。9、机械加工余量太大。
排除措施:1、适当提高浇注温度和模具温度。2、改变合金成分,提高流动性。3、改进浇注系统,加大内 浇口速度,改善填充条件。4、改善排溢条件,增大溢流量。5、提高压射速度,改善排气条件。6、提高比压。
其他名称:拉力、拉痕、粘模伤痕。
特征:顺着脱模方向,由于金属粘附,模具制造斜度太小而造成铸件表面的拉伤痕迹,严重时成为拉伤面。
铝合金压铸件耐压强度

铝合金压铸件耐压强度
铝合金压铸件是一种常见的金属制品,具有良好的强度和耐压性能。
它们被广泛应用于各个领域,如汽车制造、航空航天、机械设备等。
在这些应用中,铝合金压铸件的耐压强度是一个至关重要的指标。
铝合金压铸件的耐压强度是指它能够承受的最大压力。
这取决于许多因素,包括材料的选择、压铸工艺的控制、设计的合理性等。
首先,选择合适的铝合金材料对于提高压铸件的耐压强度至关重要。
常用的铝合金材料有ADC12、A380等,它们具有较高的强度和硬度,能够在高压下保持稳定的性能。
良好的压铸工艺能够保证铝合金压铸件的耐压强度。
压铸工艺包括模具设计、铝液的注入、冷却等环节。
合理的模具设计可以避免压铸件在注入过程中出现缺陷,如气孔、夹杂等。
同时,控制铝液的注入速度和温度可以确保铝合金的充填性和凝固性,从而提高压铸件的密实性和强度。
压铸件的设计也对其耐压强度有着重要影响。
合理的结构设计可以减少应力集中和变形,提高压铸件的抗压能力。
例如,在设计过程中可以通过增加壁厚、增加加强筋等方式来增加压铸件的强度。
同时,合理的设计也能够提高压铸件的使用寿命和安全性。
总的来说,铝合金压铸件的耐压强度是一个综合性能指标,需要在材料选择、压铸工艺和设计方面进行综合考虑和优化。
只有通过科
学的工艺和合理的设计,才能生产出具有良好耐压强度的铝合金压铸件,满足各个领域的需求。
- 1、下载文档前请自行甄别文档内容的完整性,平台不提供额外的编辑、内容补充、找答案等附加服务。
- 2、"仅部分预览"的文档,不可在线预览部分如存在完整性等问题,可反馈申请退款(可完整预览的文档不适用该条件!)。
- 3、如文档侵犯您的权益,请联系客服反馈,我们会尽快为您处理(人工客服工作时间:9:00-18:30)。
铝合金压铸件资料
ADC-12(相当国内的ZL104)是压铸铝合金牌号,为脆性材料,易崩裂。
性质类似铸铁,但有质轻和导热性好的优点。
主要用于做高档望远镜外壳,相机三脚架云台,发动机外壳等。
具体性能指标,可由铝合金压铸厂提供,或等我查资料后再告知。
在广东省南海市有大量生产厂家。
数码相机的铝合金外壳的壁厚多少合理?表面是如何处理的?有没有加工此类产品的厂家?壁厚:1.2~1.5mm,表面:铬酸皮膜后喷涂;
铝合金压铸件的内部裂痕怎样检测?
通过无损探伤来检测产品
1.超声波探伤
各类金属管材、板材、铸件、锻件和焊缝的超声波检测和超声波测厚.
当超声波在传播中遇到裂缝、空洞、离析等缺陷时,超声波的声速、振幅、频率等声学参数会因此改变。
根据仪器测量这些改变,可以判断缺陷的存在,并能确定其具体位置.
超声波脉冲(通常为1.5MHz)从探头射人被检测物体,如果其内部有缺陷,缺陷与材料之间便存在界面,则一部分人射的超声波在缺陷处被反射或折射,则原来单方向传播的超声能量有一部分被反射,通过此界面的能量就相应减少。
这时,在反射方向可以接到此缺陷处的反射波;在传播方向接收到的超声能量会小于正常值,这两种情况的出现都能证明缺陷的存在。
在探伤中,利用探头接收脉冲信号的性能也可检查出缺陷的位置及大小。
前者称为反射法,后者称为穿透法。
2.磁粉探伤
适宜于铁磁性材料如铸造、锻造和其它机加工部件的无损检测。
3.紫外线灯
价格低廉、可靠高和操作简单,各种管道的泄漏探查、涂镀层是否均匀的检验、杂质或污点的检测、半导体和生物领域、医疗、舞台特除艺术效果
4.射线探伤
射线探伤可以分为X射线、γ射线和高能射线探伤三种
X射线照相法探伤是利用射线在物质中的衰减规律和对某些物质产生的光化及荧光作用为基础进行探伤的。
从射线强度的角度看,当照射在工件上射线强度为J0,由于工件材料对射线的衰减,穿过工件的射线被减弱至Jc。
若工件存在缺陷时,因该点的射线透过的工件实际厚度减少,则穿过的射线强度Ja、Jb比没有缺陷的点的射线强度大一些。
从射线对底片的光化作用角度看,射线强的部分对底片的光化作用强烈,即感光量大。
感光量较大的底片经暗室处理后变得较黑。
因此,工件中的缺陷通过射线在底片上产生黑色的影迹,这就是射线探伤照相法的探伤原理。
铝合金压铸件的结构设计经验
1。
考虑壁厚的问题,厚度的差距过大会对填充带来影响
2。
考虑脱模问题,这点在压铸实际中非常重要,现实中往往回出现这样的问题,这比注塑脱模讨厌多了,所以拔模斜度的设置和动定模脱模力的计算要注意些,一般拔模斜度为1到3度,通常考虑到脱模的顺利性,外拔模要比内拔模的斜度要小些,外拔模也就1度,而内拔模要2~3度左右
3。
设计时考虑到模具设计的问题,如果有多个位置的抽心位,尽量的放两边,最好不要放在下位抽心,这样时间长了下抽心会容易出问题
4。
有些压铸件外观可能会有特殊的要求,如喷油、喷粉等,这时就要时结构避开重要外观位置便于设置浇口溢流槽5。
在结构上尽量的避免出现导致模具结构复杂的结构出现,如,不得不使用多个抽心或螺旋抽心等
6。
对于需进行表面加工的零件,注意,需要在零件设计时给适合的加工留量,不能太多,否则加工人员会骂你的,而且会把里面的气孔都暴露出来的,不能太少,否则粗精定位一加工,得,黑皮还没干掉,你就等再在模具上打火花了,那给多少呢,留量最好不要大于0。
8mm,这样加工出来的面基本看不到气孔的,因为有硬质层的保护。
7。
再有就是注意选料了,是用ADC12还是A380等,要看具体的要求了
8。
铝合金没有弹性,要做扣位只有和塑料配合。
9。
一般不能做深孔!在开模具时只做点孔,然后在后加工!
10。
如果是薄壁零件与不能太薄,而且一定要用加强肋,增加抗弯能力!由于铝铸件的温度要在800摄氏度左右!模具寿命一般比较短一般做如电机外壳的话只有80K左右就再见了!
1.压铸件的设计与塑胶件的设计比较相似,塑胶件的一些设计常规也适用于压铸件。
2.对于铝合金,模具所受温度和压力比塑胶的大很多,对设计的正确性要求特严。
即使很好的模具材料,一旦有焊接,模具就几乎无寿命可言。
锌合金跟塑胶差不多,模具寿命较好。
3.不能有凹的尖角,避免模具崩角。
4.压铸件的精度虽然比较高,但比塑胶差,而且拔模力比塑胶大,通常结构不能太复杂,必要时应将复杂的零件分解成两件或多件。
5.铝合金的螺孔通常模具只做锥坑,采用后加工。
对于要求严的配合部位通常留0.3mm的后加工量。
6.铝合金压铸易产生气孔,在外观上需加以考虑。
铝合金压铸件(含硅)表面做阳极氧化很难的,一般时间稍长回出现黑色。
铝合金压铸件不能做阳极氧化,可用喷油或喷塑。
常用的合金铝6061、7075,铸铝A356着色效果都不错的。
压铸件和阳极氧化之间没有必然的联系。
铸铝的种类很多,不一定要选硅铝合金(铸铝分Al-Si系、AL-Cu系、AL-Mg系、AL-Zn系等,还有参杂稀土元素的)。
即使选用硅铝合金,阳极氧化也并非不可行。
一般来说,合金铝中多多少少都含硅元素,比如6061含硅0.4~0.8%,7075含硅0.4%,这样的含硅量对合金阳极化影响是很小的(顺便说一句,铜含量对铝合金阳极氧化影响不大,但在硬质氧化、瓷质氧化时,铜、锰影响很大)。
但当合金中硅含量很大(>7%)时,对合金的阳极氧化就会有影响。
主要体现在氧化耗时较长,膜层显得灰暗等,这些问题通过工艺可以解决(比如不用直流、而用脉冲电流氧化),这就需要表面处理厂家有一定的技术能力。
所以,铸铝≠硅铝合金≠不能阳极氧化。
另外再说说着色的问题。
铝合金的阳极氧化和着色是两个不同的工序,这与钢铁的发蓝不同。
钢铁发蓝是氧化膜本身呈蓝色,而着色是在阳极氧化后立即进行,氧化膜本身是无色透明的。
铝合金用硫酸阳极化得到的氧化膜最适宜染色,现在比较多的使用有机染料着色,着色后再对氧化膜进行封闭处理。
另外也有用重金属盐电解着色的,但要按楼主的要求染成红色比较困难!
钢铁零件在含有磷酸溶液中进行化学处理,使钢铁表面生成一层难溶于水的保护膜的过程,叫做磷化处理!
它主要有以下特点:
1、磷化膜表面呈灰色或暗灰色。
2、磷化膜经填充、上油或涂漆处理,在大气条件下具有较好的抗腐蚀能力。
3、膜层的吸附能力强,常作为涂料的底层。
4、磷化膜具有较高的电绝缘性。
5、经磷化处理后,原金属的机械性能、强度、磁性等基本不变。
6、磷化膜有很好的润滑性能。
7、渗氮零件表面可以用磷化膜保护。
8、磷化膜的最大特点是能在钢铁的内表面及形状复杂的钢铁表面上获得保护膜。
9、膜层硬度和机械强度底,有一定的脆性。
钝化一般是指:为了提高镀锌层的防护性能和装饰性能,将镀件防入溶液中处理,使其表面形成一层化学稳定性较高的膜。
经钝化处理后能提高镀锌层的防护性能和表面光泽。
氧化一般分为:铝、铝合金和钢铁零件的氧化,只是所能达到的目的和所使用的溶液不同。