DIN 1688-1-1998轻金属合金的铸件毛坯.砂模铸造.一般公差及加工余量.不适于新结构
铸造毛坯件检验规范
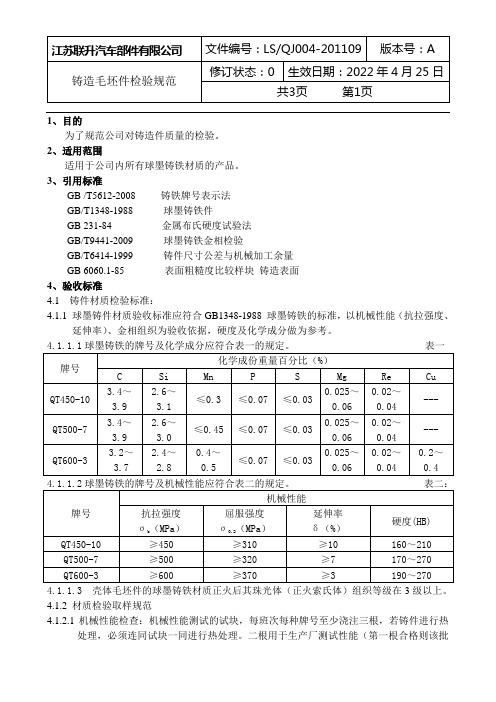
1、目的为了规范公司对铸造件质量的检验。
2、适用范围适用于公司内所有球墨铸铁材质的产品。
3、引用标准GB /T5612-2008 铸铁牌号表示法GB/T1348-1988 球墨铸铁件GB 231-84 金属布氏硬度试验法GB/T9441-2009 球墨铸铁金相检验GB/T6414-1999 铸件尺寸公差与机械加工余量GB 6060.1-85 表面粗糙度比较样块铸造表面4、验收标准4.1 铸件材质检验标准:4.1.1 球墨铸件材质验收标准应符合GB1348-1988 球墨铸铁的标准,以机械性能(抗拉强度、延伸率)、金相组织为验收依据,硬度及化学成分做为参考。
4.1.1.3 壳体毛坯件的球墨铸铁材质正火后其珠光体(正火索氏体)组织等级在3级以上。
4.1.2 材质检验取样规范4.1.2.1机械性能检查:机械性能测试的试块,每班次每种牌号至少浇注三根,若铸件进行热处理,必须连同试块一同进行热处理。
二根用于生产厂测试性能(第一根合格则该批次合格,余下试块(留有生产日期、包次标识)留存。
若第一根试块不合格,测试剩余二根,若第二根不合格则该批次产品全部报废,若第二根合格,应加试第三根,合格则判定该炉产品合格,若第三根不合格则该批次产品全部报废)。
材质检验报告(原档)保存期为5年。
4.1.2.2金相组织检查:球铁铸件从每包铁水的最后一型附铸金相试块或铸件本体进行金相检验,依次往前直到合格(或本包铁水所浇铸件检验完)为止。
附铸试块应能代表本体。
若试块不好,应对铸件本体破件进行检验。
若金相检验由问题,加倍抽查。
金相本体试块应按天分类以月为单位保存,保存期为6个月,检验报告保存期5年。
球化等级要求在3级以上,石墨大小要求为5~7级。
4.1.2.3化学成分检查:每天必须分析每炉铁水(炉前)及至少两炉铸件(炉后)的化学成分。
炉前主要化验C、Si和S,炉后所有元素全部化验。
每天第一炉溶清后必须检测C、Si、Mn、P和S,之后C、Si每炉化验检测。
DIN 1683-1第1 2 4 5页

工工序能够达到最佳状态,需采用的机加工余量可以降低到接近表 4 所列的一半值(如批量 生产时在客户和铸造厂间商定好的情况下)。减少后的数值请参差等级和机加工余量都选定时,等级 GTB 17 公差(GTB 17)和
表 6:现有图纸的线性尺寸极限偏差值
公
名义尺寸范围
差 ≤18 (18, (50, (180, (500, (1250,
等
50】 180】 500】 1250】 2500】
级
外 +3 +4
+7
+10
+15
+20
部
A 尺 -2 -2
-4
-5
-8
-10
寸
内 +2 +2
+4
+5
+8
+10
部
尺 -3 -4
-7
-10
-15
-20
寸
外 +2 +3.5 +5
+8
+11
+15
部 -1.5 -2
-3
-4
-6
-7.5
B尺
寸
内 +1.5 +2
+3
+4
+6
+7.5
部 -2 -3.5 -5
-8
-11
-15
尺
寸
(2500, 4000】
+27 -13 +13 -27
--
--
DIN 1685-1-1998 球墨铸铁件.一般公差,加工余量

表 3 机械加工余量
至 50
大于 50 至 120
大于 120 至
250
大于 250 至
500
大于 500 至 1000
机械加工余
2
2,5
3
3,5
4
量 BZ
2,5
3
4
5
7
大于 1000 至 2500
6
8
表 4 缩小的机械加工余量
表面在 名义尺寸范围
模型中 的位置
基于铸件整体 至 50
最大尺寸
底部 侧面 顶部
GTB 17 1,8 1,9
2 2,1 2,3 2,5 2,7 2,9 3,1 3,3 3,5 3,8 4,1 4,4 4,9 5,5
GTB
2
-
-
16 1,1 1,2 1,3 1,4 1,5 1,6 1,8 1,9
2,1 2,3 2,4 2,6 2,8
GTB
1
-
-
-
-
15 0,85 0,95
1,1 1,2 1,3 1,4 1,5 1,6 1,7 1,8 1,9
*) 不管表格中规定的值为何 铸件的线性尺寸的实际偏差无论如何均不得超出名义尺寸的 25 位) 该限制特别适用于粗实线线框中的偏差
大于 2000 至 2500
23
大于 2500 至 3150
25
大于 3150 至 4000
27
大于 4000 至 6300
33
大于 6300 至
10000
39
15 17 19 22 26
所引用的出版物的最后的版本
DIN 1680 1 粗铸件 通用公差和机加工公差 总则 DIN 1693 1 球墨铸铁 非合金 纯 及合金等级 DIN 7182 1 规格 偏差 公差及配合 基本概念 ISO 8062 1994 铸件 尺寸公差及机械加工余量 3 概念
压铸件毛坯质量检验标准 (规范)
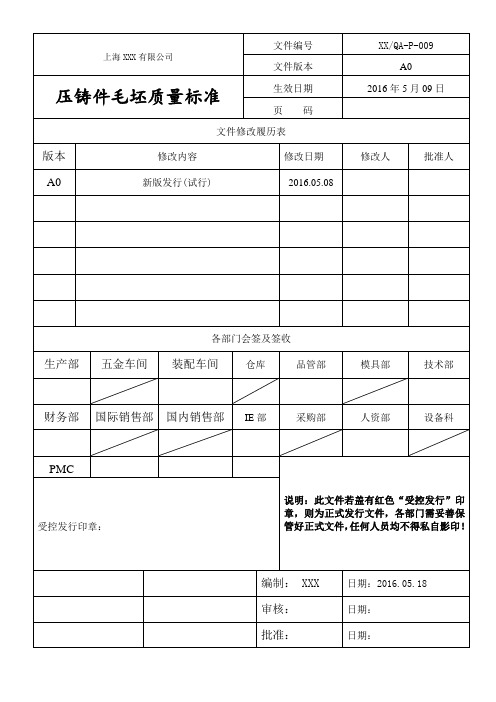
缺陷名称
缺陷范围
数值
备注
擦伤
深度(mm)
≤0.10
面积不超过总面积的百分数
5
凹陷
凹入深度(mm)
≤0.30
缺肉
深度(mm)
≤0.50
长度不大于(mm)
2
所在面上不允许超过的数量
2
离压铸件边缘距离(mm)
≥4
间距(mm)
≥10
网状毛刺
高度(mm)
≤0.2
2.1.2.4?压铸件的浇口、飞边、溢流口、隔皮、顶杆痕迹等应清理干净。但允许留有痕迹。
3.9?其它试验方法及检验规则按GB/T15114的规定执行。
4?压铸件的交付、包装、运输与储存
4.1?供方应提供需方一份检验证明,用来说明每批压铸件的检验符合本标准的规定。
4.2?合格压铸件交付时,必须附有检验合格证。其上应写明下列内容:产品名称、产品号、合金牌号、数量、交付状态、制造厂名。检验合格印记和交付时间。有特殊检验项目者,应在检验合格证上注明检验的条件和结果。
3.2?力学性能
3.2.1?力学性能的检验方法,检验频率和检验规则应符合GB/T15115的规定。
3.2.2?采用压铸件本体为试样时,切取部位的尺寸、测试形式由供需双方商定。
3.3?压铸件几何尺寸的检验可按检验批量抽检或按GB2828、GB2829的规定进行,检验结果应符合本标准3.3的规定。
3.4?压铸件表面质量的出厂检验应逐件检查,检验结果应符合本标准的规定。
L≤30
≤1.5
≤1.0
≤2
L>30
≤2.0
≤1.5
≤3
2.1.5.1?当加工孔直径?≤11 mm而L>50 mm时,过孔两端长10mm表面内不允许有孔穴。
德国标准DIN1688

±0.25
±0.3
±0.35
±0.4
±0.45
±0.55
±0.55
±0.6
-
-
-
-
GTA 13/5
大于50
小于等于500
非
本质
±0.32
±0.35
±0.4
±0.45
±0.5
±0.55
±0.6
±0.7
±0.7
±0.75
-
-
-
-
GTA 13/5
加上余量
GTA 13
本质
±0.14
±0.17
±0.2
800
大于
800
小于等于
1000
大于
1000
小于等于
1250
小于等于50
0.3
0.3
0.3
-
-
-
-
-
-
-
-
-
-
-
大于50
小于等于180
-
-
-
0.3
0.3
0.4
-
-
-
-
-
-
-
-
大于180
小于等于500
-
-
-
-
-
-
0.4
0.5
0.5
0.6
-
-
-
-
大于500
-
-
-
-
-
-
-
-
-
-
0.7
0.7
0.9
1.0
GTA 16
大于500
非本质
±0.55
±0.65
±0.7
德国标准翻译文本——DIN 1688 Teil 4轻合金粗铸件一般公差,机械加工余量
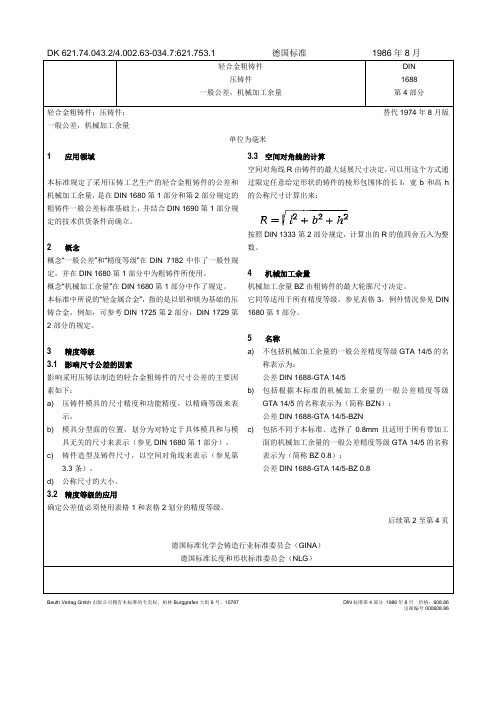
Beuth Verlag Gmbh出版公司拥有本标准的专卖权,柏林Burggrafen大街6号,10787 DIN标准第4部分1986年8月价格:608.86
出版编号000608.86
第2页DIN 1688第4部分
DIN 1688第4部分第3页
第4页DIN 1688 第4部分
参考标准
DIN 1333第2部分数据资料;四舍五入
DIN 1680第1部分粗铸件;一般公差和机械加工余量;一般性规定
DIN 1680第2部分粗铸件;一般公差系统
DIN 1690第1部分金属材料铸件技术供货条件;一般性条件
DIN 1725第2部分铝合金;铸造合金;砂型铸件;硬型铸件,压铸件,熔模铸件DIN 1729第2部分镁合金;铸造合金;砂型铸件,硬型铸件,压铸件
DIN 7182第1部分尺寸,偏差,公差与配合;基本概念
其他相关标准
DIN 1688第1部分轻合金粗铸件;砂型铸件;一般公差,机械加工余量
DIN 1688第3部分轻合金粗铸件;硬型铸件;一般公差,机械加工余量
前版
DIN 1688第4部分:08.74
修正
与1974年8月版相比,本版本进行了以下修正:
a) 采用了机械加工余量。
b) “自由公差”被“一般公差”替代,参见DIN 1680第1部分
c) 标题和应用领域作了相应的修正。
d) 正文在编辑上作了修改。
国际专利分类
B 22 B 17/00
B 22 B 21/00。
压铸件毛坯质量检验标准 (规范)
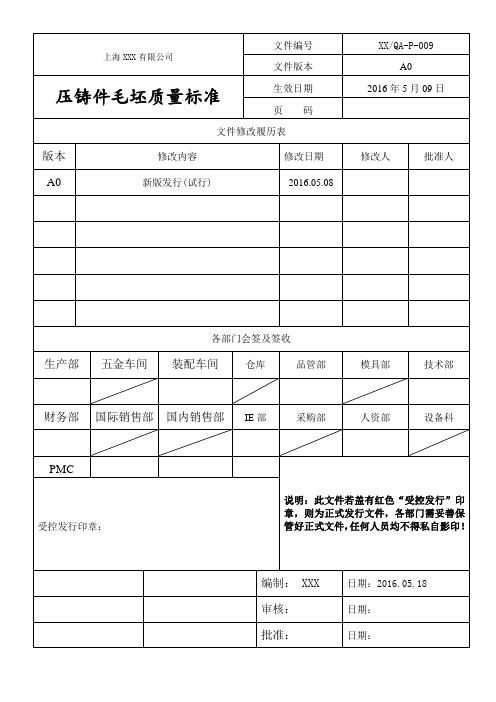
缺陷名称
缺陷范围
数值
备注
擦伤
深度(mm)
≤0.10
面积不超过总面积的百分数
5
凹陷
凹入深度(mm)
≤0.30
缺肉
深度(mm)
≤0.50
长度不大于(mm)
2
所在面上不允许超过的数量
2
离压铸件边缘距离(mm)
≥4
间距(mm)
≥10
网状毛刺
高度(mm)
≤0.2
2.1.2.4压铸件的浇口、飞边、溢流口、隔皮、顶杆痕迹等应清理干净。但允许留有痕迹。
2.1.6.2压铸件内部不允许有冷隔缺陷。
2.1.6.3压铸件内部允许有气孔、疏孔、夹杂等缺陷,但孔穴缺陷最大直径不超过壁厚的1/8,孔穴数量在任何剖面上不超过2个/cm2。
3.4.6.4重要压铸件的受力部位须进行解剖检查,符合表6中的规定。
表6压铸件指定解剖部位内部质量规定
孔穴平均直径mm
最多个数/cm2
2.技术要求
2.1压铸件质量要求
2.1.1压铸件应符合零件图样的规定。
2.1.2表面质量
2.1.2.1压铸件表面粗糙度应符合GB/T6060.1的规定。
2.1.2.2压铸件表面不允许有裂纹、欠铸、疏松、气泡和任何穿透性缺陷。
2.1.2.3压铸件表面允许有擦伤、凹陷、缺肉和网状毛刺等缺陷。但缺陷必须符合表1规定。
上海XXX有限公司
文件编号
XX/QA-P-009
文件版本
A0
压铸件毛坯质量标准
生效日期
2016年5月09日
页码
文件修改履历表
版本
修改内容
修改日期
修改人
铸件质量检验标准

铸件质量检验标准一、目的:为了确保外协毛坯铸件、采购毛坯铸件、标准铸件、成品铸件质量符合工艺、技术要求,为了满足产品特性,结合相关文件特制定本标准。
二、适用范围:本标准适用于我公司产品外协、采购、生产、装配过程中,全部铸件质量检验标准。
三、检验标准:3.1 铸件结构要符合设计要求或加工工艺要求。
无特殊要求时按铸件通用标准执行。
通用标准等级分为:交货验收技术条件标准;铸件质量分等通则(合格品、一等品、优等品)材质、检验方法;工艺和材料规格等一般性规则。
3.2 铸件成品检验。
铸件成品检验包括:铸件的内部质量检验和外观质量检验。
铸件内部质量检验包括:化学成分、机械性能等。
铸件外观质量检验包括:表面质量、粗糙度、铸件尺寸、重量等。
3.2.1 铸件内部质量检验①化学成分:表1②机械性能表23.2.2 铸件外观质量检验①表面质量检验。
机械加工生产一线人员在工艺过程中对铸造毛坯的检验主要是对其外观铸造缺陷(如有无砂眼、砂孔、疏松、浇不足、铸造裂纹等)的检验;以及毛坯加工余量是否满足加工要求的检验。
表3 铸件外观质量检验项目(GB6060.1-1997)②粗糙度检验。
表4 铸件表面粗糙度(Ra值μm)(GB6060.1-1997)③铸件尺寸检验。
主要一种是采用划线法检查毛坯的加工余量是否足够。
另一种方法是:用毛坯的参考基准面(也称工艺基准面)作为毛坯的检验基准面的相对测量法(需要测量相对基准面的尺寸及进行简单换算)。
表5 铸件尺寸公差数值(mm)(GBT 6414-1997)1)在等级CT1~CT15中对壁厚采用粗一级公差。
2)对于不超过16mm的尺寸,不采用CT13~CT16的一般公差,对于这些尺寸应标注个别公差。
3)等级CT16仅适用于一般公差规定为CT15的壁厚。
表6 单件、小批量生产的铸件公差等级(GBT 6414-1997)注:1)表中所列出的公差等级是小批量的或单件生产的砂型铸件通常能够达到的公差等级。
模胚加工公差及刀具使用指引4.22
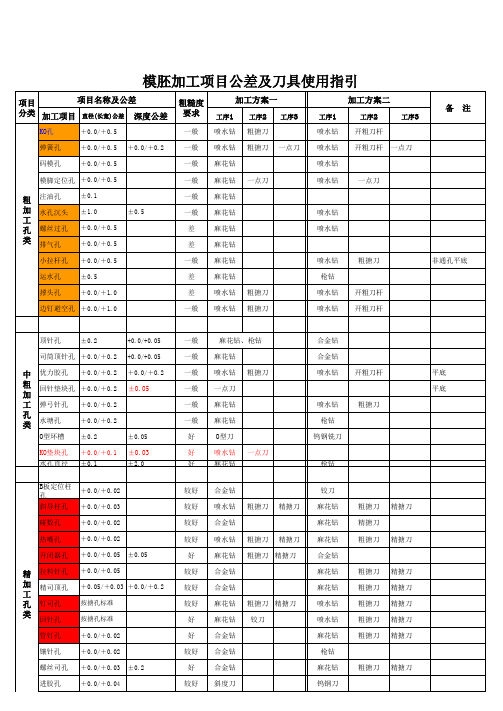
合金钻 合金钻 喷水钻 开粗刀杆 平底 平底 喷水钻 枪钻 钨钢铣刀 粗搪刀
司筒顶针孔 +0.0/+0.2
中 粗 加 工 孔 类
优力胶孔
+0.0/+0.2
回针垫块孔 +0.0/+0.2 弹弓针孔 水塘孔 O型环槽 KO垫块孔 水孔直径
+0.0/+0.2 +0.0/+0.2 ±0.2 +0.0/+0.1 ±0.1
一般 一般 一般 一般 差 一般 差 一般 一般
侧面U形槽 +0.0/+0.5 快速锁模位 ±0.1
基准/碰数槽 +0.0/+0.02
±0.5
较好 好 好 较好 较好
一点刀 T型刀 斜度刀 钨钢刀 钨钢刀 开粗刀 一点刀
钨钢刀
精 加 工 框 槽 类
T型槽高度 止口框
+0.0/+0.05 -0.02/-0.06
好 较差 差 差 差 差 差
粗铣加工 卡簧刀 旧钨钢刀 开粗刀 开粗刀 开粗刀 旧钨钢刀
加工中心加工
粗 加 工 框 槽 类
卡簧槽 排气槽 撬模槽 撬模角 码模槽 垃圾槽
一点刀 一点刀 一点刀 一点刀
V形槽 挡板槽 外形槽 斜顶槽
+0.0/+0.2 +0.0/+0.5 +0.0/+0.5 +0.0/+0.2 +0.05/-0.05 +0.0/+0.1 +0.05/-0.05 +0.05/-0.05 喷水钻 麻花钻 麻花钻 麻花钻 麻花钻 麻花钻 麻花钻 麻花钻 麻花钻 喷水钻 喷水钻
粗搪刀 粗搪刀 一点刀
喷水钻 喷水钻 喷水钻
开粗刀杆 开粗刀杆 一点刀
模脚定位孔 +0.0/+0.5
一点刀
喷水钻
一点刀
粗 加 工 孔 类
注油孔 水孔沉头 螺丝过孔 排气孔 小拉杆孔 运水孔 撑头孔
DIN1688
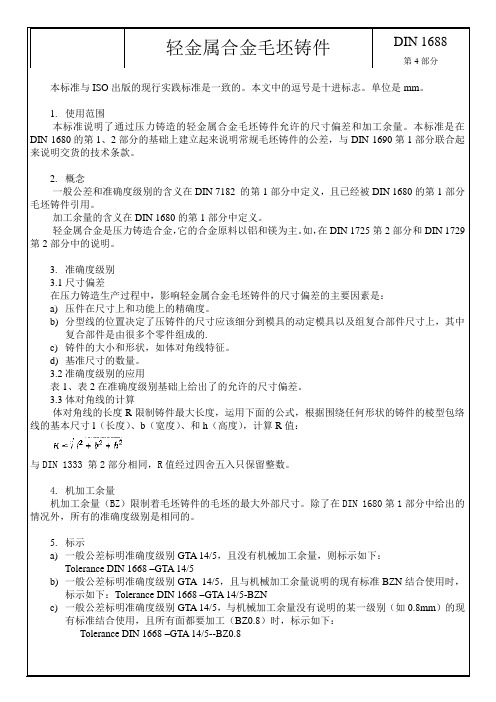
本标准与ISO 出版的现行实践标准是一致的。
本文中的逗号是十进标志。
单位是mm 。
1. 使用范围本标准说明了通过压力铸造的轻金属合金毛坯铸件允许的尺寸偏差和加工余量。
本标准是在DIN 1680的第1、2部分的基础上建立起来说明常规毛坯铸件的公差,与DIN 1690第1部分联合起来说明交货的技术条款。
2. 概念一般公差和准确度级别的含义在DIN 7182 的第1部分中定义,且已经被DIN 1680的第1部分毛坯铸件引用。
加工余量的含义在DIN 1680的第1部分中定义。
轻金属合金是压力铸造合金,它的合金原料以铝和镁为主。
如,在DIN 1725第2部分和DIN 1729第2部分中的说明。
3. 准确度级别 3.1尺寸偏差在压力铸造生产过程中,影响轻金属合金毛坯铸件的尺寸偏差的主要因素是: a) 压件在尺寸上和功能上的精确度。
b) 分型线的位置决定了压铸件的尺寸应该细分到模具的动定模具以及组复合部件尺寸上,其中复合部件是由很多个零件组成的.c) 铸件的大小和形状,如体对角线特征。
d) 基准尺寸的数量。
3.2准确度级别的应用表1、表2在准确度级别基础上给出了的允许的尺寸偏差。
3.3体对角线的计算体对角线的长度R 限制铸件最大长度,运用下面的公式,根据围绕任何形状的铸件的棱型包络线的基本尺寸l (长度)、b (宽度)、和h (高度),计算R 值:与DIN 1333 第2部分相同,R 值经过四舍五入只保留整数。
4. 机加工余量机加工余量(BZ )限制着毛坯铸件的毛坯的最大外部尺寸。
除了在DIN 1680第1部分中给出的情况外,所有的准确度级别是相同的。
5. 标示a) 一般公差标明准确度级别GTA 14/5,且没有机械加工余量,则标示如下:Tolerance DIN 1668 –GTA 14/5b) 一般公差标明准确度级别GTA 14/5,且与机械加工余量说明的现有标准BZN 结合使用时,标示如下:Tolerance DIN 1668 –GTA 14/5-BZNc) 一般公差标明准确度级别GTA 14/5,与机械加工余量没有说明的某一级别(如0.8mm )的现有标准结合使用,且所有面都要加工(BZ0.8)时,标示如下: Tolerance DIN 1668 –GTA 14/5--BZ0.8轻金属合金毛坯铸件DIN 1688第4部分表1:线性尺寸的允许偏差(长度、宽度、高度、中心线距离、直径、半径。
铸件标准

JB/ZQ4000.7-86 JB/ZQ4000.5-86 JB/ZQ400.3-86JB/ZQ4000.2-86JB/ZQ4000.7-86 JB/ZQ4000.5-86 JB/ZQ400.3-86 JB/ZQ4000.2-861、锻件通用技术要求(JB/ZQ4000.7-86)2、铸件通用技术要求(JB/ZQ4000.5-86)3、焊接件通用技术要求(JB/ZQ400.3-86)4、涂装通用技术条件(JB/ZQ4000.10-88)5、切削加工件通用技术要求(JB/ZQ4000.2-86)1、锻件通用技术要求(JB/ZQ4000.7-86)1.锻件上不应有白点,根据图样、工艺文件或订货技术要求的规定进行白点检查, 当发现有白点时,该批所有锻件必须经单个检查后,确定是否合格.2.锻件的力学性能试验,按图样、工艺文件或订货技术要求的规定可在纵向、切向和横向的试样上进行,试验的结果应符合JB/ZQ4287-86 (优质碳素结构钢)和JB/ZQ4288-86(合金结构钢)的规定.3.锻件根据其用途和工作条件,按试验种类分为:Ⅰ、Ⅱ、Ⅲ、Ⅳ和Ⅴ五组.每组锻件除Ⅰ组外,其必要的试验范围按下表规定.设计部门或订货单位对锻件力学性能有要求时,必须在图样或订货技术要求中注明.若未注明,则按Ⅰ组锻件处理.一、锻件组别:Ⅰ1.组别的基本标志1)检验特性: 不试验.2)组成批的条件: 同一钢号的锻件.二、锻件组别:Ⅱ1.组别的基本标志1)检验特性: 测定每批中锻件的硬度.2)组成批的条件:根据同一规范进行热处理的同一钢号的锻件.2.验收时的必要力学性能指标: HB3.试验方法1)力学性能: -2)硬度: 每批中试验5%,但不少于5件.三、锻件组别:Ⅲ1.组别的基本标志1)检验特性: 测定每一锻件的硬度.2)组成批的条件:共同进行热处理的同一钢号的锻件.2.验收时必要力学性能指标: HB3.试验方法:1)力学性能: -2)硬度: 每一锻件均受试验.四、锻件组别:Ⅳ1.组别的基本标志1)检验特性:测定每一锻件的硬度和每一批中的力学性能.2)组成批的条件:共同进行热处理的同一炉号的锻件.2.验收时的必要力学性能指标:σs或σb, δ5, ψ, αk3.试验方法1)力学性能: 试验数量.a.锻件重量在10kg以下,每批在300件以下者,试验2件;每批超过300件者,试验0.5%,但不少于2件.b.锻件重量超过10-20kg,每批在200件以下者,试验2件:每批超过200件者,试验1%,但不得少于2件.c.锻件重量超过20kg,每批超过150件以下者,试验2件;每批超过150者,试验1.5%,但不得少于3件.2)硬度:每一锻件均受试验,选择具有极限的毛坯作力学性能试验.五、锻件组别:Ⅴ1.组别的基本标志1)检验特性: 测定每一锻件的力学性能.2)组成批的条件: 每一锻件均单个验收.2.验收时的必要力学性能指标:σs或σb, δ5, ψ, αk3.试验方法1)力学性能: 每一锻件均受试验.2)硬度: 每一锻件均受试验.注:1.每批锻件由同一图号制造的锻件组成, 允许在同一批锻件中包括根据各种图号制造的外形尺寸近似的锻件.2.经订货单位同意, 允许把各种牌号钢制成的Ⅰ组锻件组成一批.3.对Ⅳ、Ⅴ组锻件验收时的必要力学性能指标σs和σb的选择,应在图样或订货技术要求中规定,如无规定,由制造厂工艺部门决定.4.锻件的验收规则和试验方法按标准要求进行.2、铸件通用技术要求(JB/ZQ4000.5-86)1.碳素铸钢应符合GB5678-85的规定;合金铸钢应符合JB/ZQ4297-86的规定,耐热铸钢应符合JB/ZQ4298的规定;不锈钢应符合JB/ZQ4299及JB/ZQ6009-84的规定.2.灰铸铁应符合GB5675-85的规定;球墨铸铁应符合JB/ZQ4302-86的规定,耐热铸铁应符合JB/ZQ4303-86的规定; 耐磨铸铁应符合JB/ZQ4303-86的规定.3.铸件尺寸公差等级分16级,见1-175 铸件尺寸公差.plb, 单件小批生产一般按1-176 小批单件毛坯尺寸公差.plb选用.公差带应对称于毛坯铸件基本尺寸配置,即公差的一半位于正侧,另一半位于负侧.有特殊要求时,公差带也可非对称配置,但应在图样上标注.4.铸件内、外圆角公差用1-175铸件尺寸公差.plb中公差值作为上限,使其下限为零;壁厚公差可比其它尺寸的一般公差降一级选用, 如图样上标明一般公差为CT10 级的话,则壁厚公差选用CT11级.5.特殊要求的公差, 应直接标注毛坯件基本尺寸的后面,如95±1.1. 特殊要求的公差可比一般公差高或低.一般情况下不能低于1-176 小批单件毛坯尺寸公差.plb规定的公差等级范围,当要求的公差超过该库规定的范围时, 则经有关方面协商后从1-175铸件尺寸公差.plb中选取.6.碳素钢和低合金钢(包括高锰钢)铸钢件缺陷的补焊按JB/ZQ4000.6-86(铸钢件补焊通用技术条件)规定执行.7.当铸件补焊处的焊缝深度超过壁厚20%或25mm时,补焊后均应进行适当的消除应力热处理.补焊大型缺陷时,焊缝金属量大,有必要时可在焊接到坡口的1/3-1/处时进行一次中间退火, 消除应力后再继续焊满坡口, 最后再做一次消除应力热处理.补焊大型或碳当量(碳当量的计算见本标准附录A)超过0.4%的铸钢件的缺陷时, 在补焊后应立即入炉进行消除应力的热处理.8.设计人员根据铸件的技术要求填写下表,并将此表贴在铸件图样的右上部.(铸件技术要求) :通用技术要求 JB/ZQ4000.5铸件尺寸公差要求 CT密封试验是/否耐压试验是/否注:表中空格中可补充其它技术要求.3、焊接件通用技术要求(JB/ZQ400.3-86)1.焊接结构件的长度尺寸公差见1-245c 尺寸和形位公差数值.plb,适用于焊接零件和焊接组件的长度尺寸. 焊接件的直线度.平面度和平行度公差见 1-245c 尺寸和形位公差数.plb,焊接结构件的尺寸公差与形位公差等级选用见1-245b 尺寸和形位公差等级.plb2.标注和未标注角度的偏差见1-246a 角度偏差.plb,角度偏差的公称尺寸以短边为基准边, 其长度从图样标明的基准点算起.3.喷丸处理的焊接件,为了防止钢丸钻入焊缝, 必须焊接内焊缝,并尽量避免内室和内腔.如果结构上必须有内室和内腔,则必须进行酸洗,以便达到表面除锈质量等级Be(见JB/ZQ4000.10-86附录A). 对此图样需作标注.4.由平炉钢制造的低碳钢结构件, 可在任何温度下进行焊接.但为了避免焊接过程产生裂纹及脆性断裂, 厚度较大的焊接件,焊削必须根据工艺要求,进行预热和缓冷. 板厚超过30mm的重要焊接结构,焊后应立即消除内应力,消除内应力采用550-600℃回火,或200℃局部低温回火.5.普通低合金结构钢制造的焊接件,必须按照焊接零件的碳当量和合金元素含量、零件的厚度、钢结构件的用途和要求进行焊前预热和焊后处理,见表1 .表1:钢号厚度mm 焊前预热℃焊后热处理温度℃09Mn2 不预热不处理09Mn2Si 不预热不处理09MnV 不预热不处理12Mn 不预热不处理16Mn ≤40不处理或600-650回火16MnRE >40 ≥ 100不处理或600-650回火14MnNb >40≥ 100不处理或600-650回火15MnV ≤32不预热不处理或560-590,630-650回火15MnTi >32 ≥ 100不处理或560-590,630-650回火14MnMoNb >32 ≥ 100不处理或560-590,630-650回火15MnVN ≤3215MnVTiRE >32 >10018MnMoVNb ≥ 150 600-650回火14MnMoV ≥ 150 600-650回火4MnMoVB ≥ 150在气温较低、焊接件厚度较大的情况下焊接的普通低合金结构,应按表2的规定预热.表2 :钢板厚度 mm 焊接气温℃预热温度℃≤16-10以下 100-15016-24 -5以下 100-15024-40 0以下任何温度>40 0以下任何温度6.有密闭内腔的焊接件,在热处理之前,应在中间隔板上适当的位置加工Φ10mm 孔,使其空腔与外界相通.需在外壁上钻孔的,在热处理后要重新堵上.7.焊缝射线探伤应符合GB3323-82的规定.要进行力学性能试验的焊接,应在图样或订货技术要求中注明.焊缝的力学性能试验种类、试样尺寸按GB2649-81-GB2656-81的规定,试样板焊后与工件经过相同的热处理,并事选经过外观无损探伤检查.8.焊件要进行密封性检验和耐压试验时,应按本标准要求进行.对耐压试验有要求时, 应在图样或订货要求中注明试验压力和试压时间.4、涂装通用技术条件(JB/ZQ4000.10-88)1.涂装前对物体的表面要求应符合本标准的规定.2.除锈后的金属表面与涂底漆的间隔时间不得大于 6h,酸洗处理表面与第一次涂底漆时间不少于 48h,但无论间隔时间多少,涂漆前表面不得有锈蚀或污染.3.铆接件相互接触的表面, 在联接前必须涂厚度30-40μm防锈漆.由于加工或焊接损坏的底漆,要重新涂装.4.不封闭的箱形结构内表面, 在组焊前必须涂厚度60-80μm防锈漆, 封闭的箱体结构件内表面不涂漆 .5.溜槽、漏斗、裙板内表面、平衡的重箱内表面、安全罩内表面、封闭箱且在运输过程中是敞开的内表面等,必须涂厚度60-80μm防锈漆.6.涂层的检查项目及方法应符合本标准的规定.5、切削加工件通用技术要求(JB/ZQ4000.2-86)1.铸钢件加工后,如发现有砂眼、缩孔、夹渣、裂缝等缺陷时,在不降低零件强度和使用性能的情况下, 按照铸钢件补焊通用技术条件(JB/ZQ4000.6-86)的规定补焊,并经检验合格.2.长度尺寸、圆角半径和倒角高度的未注公差见下表:长度尺寸未注公差 mm公称尺寸加工方法切削加工冷作成形0.5-3(≤) ±0.1 ±0.153-6 ±0.1 ±0.26-30 ±0.2 ±0.530-120 ±0.3 ±0.8120-400 ±0.5 ±1.2400-1000 ±0.8 ±21000-2000 ±1.2 ±32000-4000 ±2 ±44000-8000 ±3 ±58000-12000 ±4 ±612000-16000 ±5 ±716000-20000 ±6 ±8圆角半径、倒角高度未注公差 mm公称尺寸加工方法切削加工冷作成形0.5-3(≤) ±0.2 ±0.23-6 ±0.5 ±16-30 ±1 ±230-120 ±2 ±4120-400 ±4 ±8角度未注公差 mm短边公称尺寸加工方法切削加工正切值冷作成形正切值10(≤) ±1° 0.0175 ±1°30′ 0.026210-50 ±30′ 0.0087 ±50′ 0.014550-120 ±20′ 0.0058 ±25′ 0.0073120-400 ±10′ 0.0029 ±15′ 0.0044>400 ±5′ 0.0015 ±10′ 0.00293.未注形状公差应符合(GB1184-80)的要求,其中直线度,平面度不得低于该标准中规定的C级精度, 平行度未注公差应符合(GB1184-80)中第5条规定,垂直度和倾斜度未注公差,不得大于上表规定的角度公差; 同轴度、对称度不得大于GB1184-80表2规定的C级; 径向跳动和端面跳动应符合GB1184-80中第7条的规定.6、装配通用技术条件(JB/ZQ4000.9-86)1.外购材料与零部件应具有JB/ZQ4000.1-86<产品检验通用技术要求>中规定的检验报告与合格证.2.用于紧固机架,机座和压力容器压紧法兰的紧固件,在紧固后,螺钉或螺母的端面与被紧固零件间的倾斜不得大于1°.3.螺栓与螺母拧紧后,螺栓应露出螺母 2-4扣,不许露出过长或过短.4.各种密封毡圈、毡垫、石棉绳、皮碗等密封件装配前必须浸透油.钢纸板用热水泡软,紫铜垫作退火处理(加热至600-650℃后在水中冷却).5.d>4mm圆锥销与孔应进行着色检查,其接触率不得低于 50%.带螺尾圆锥销打入后,大端须沉入相关件2-3扣.6.钩头键与楔键装配后,工作面上的接触率应在70%以上 ,其不接触部分不得集中于一段. 装配后外露尺寸应为斜面长度的10-15%(不包括钩头).7.花键或齿形离合器的装配, 单齿分度加工的矩形花键或齿形离合器的工作面研合后,同时接触的齿数不得少于 2/3;接触率在齿长和齿高方向上均不得低于50%,研合时可用0.05mm的塞尺检查齿侧隙,塞尺不得插入全齿长.8.锥轴伸与轴孔配合表面接触应均匀, 着色研合检验时其接触率不得低于70%.9.各类联轴器技术要求及轴向(△X)、径向(△Y)与角向(△α)的许用补偿量,应符合有关联轴器标准的规定.10.轴承外圈与开式箱体或轴承座的各半圆孔间不准有"夹帮"现象,各半圆孔的"修帮"尺寸,不准超过下表规定的最大值.滚动轴承装配修帮尺寸 mm轴承外径D bmax hmax≤120 0.10 10120-260 0.15 15260-400 0.20 20>400 0.25 3011.采用润滑脂的轴承,装配后在轴承空腔内注入相当空腔容积65-80%的清洁润滑脂.12.轴承装在轴上后应靠紧轴肩,轴承内圈在常温状态经打击没有串动现象的情况下,圆锥滚子轴承和向心推力球轴承与轴肩的间隙不得大于0.05mm.其它轴承不得大于0.10mm.13.装配滚动轴承允许采用机油加热进行热装,油的温度不得超过100℃.14.在轴两端采用了径向间隙不可调的向心轴承(或滚针轴承、螺旋滚子轴承等), 而且轴的轴向位移又是以两端端盖限定时,必须留出间隙 C.如果没规定C的数值,通常可按 C=0.2-0.4mm规定,当温差变化较大或两轴承中心距较大时,间隙 C的数值可按下式计算:C=Lα△t+0.15式中:C─ 轴承外座圈与端盖间的间隙,mm.L─ 两轴承中心距,mm.α─ 轴材料的线膨胀系数(取α=12×10^(-6)△t─ 轴工作时温度与环境温度之差,℃ .0.15─ 轴膨胀后剩余的间隙 ,mm.15.单列圆锥滚子轴承、向心推力球轴承、双向推力球轴承向游隙按(表1)调整.双列和四列圆锥滚子轴承在装配时均应检查其轴向游隙,并应符合(表2)的要求.表1 : mm轴承内径向心推力球轴承向游隙单列圆锥滚子轴承向游隙双列推力球轴承向游隙轻系列中及重系列轻系列轻宽.中及中宽系列轻系列中及重系列≤30 0.02-0.06 0.03-0.09 0.03-0.10 0.04-0.11 0.03-0.08 0.05-0.1130-50 0.03-0.09 0.04-0.10 0.04-0.11 0.05-0.13 0.04-0.10 0.06-0.1250-80 0.04-0.10 0.05-0.12 0.05-0.13 0.06-0.15 0.05-0.12 0.07-0.1480-120 0.05-0.12 0.06-0.15 0.06-0.15 0.07-0.18 0.06-0.15 0.10-0.18120-150 0.06-0.15 0.07-0.18 0.07-0.18 0.08-0.20 - -150-180 0.07-0.18 0.08-0.20 0.09-0.20 0.10-0.22 - -180-200 0.09-0.20 0.10-0.22 0.12-0.22 0.14-0.24 - ->200-250 - - 0.18-0.30 0.18-0.30 - -表2: 双列、四列圆锥滚子轴承的轴向游隙 mm双列圆锥滚子轴承内径轴向游隙一般情况内圈比外圈温度高 25-30℃≤80 0.10-0.20 0.30-0.4080-180 0.15-0.25 0.40-0.50180-225 0.20-0.30 0.50-0.60225-315 0.30-0.40 0.70-0.80315-560 0.40-0.50 0.90-1.00四列圆锥滚子轴承内径轴向游隙120-180 0.15-0.25180-315 0.20-0.30315-400 0.25-0.35400-500 0.30-0.40500-630 0.30-0.40630-800 0.35-0.45800-1000 0.35-0.451000-1250 0.40-0.5016.滑动轴承上、下轴瓦的接合面要接触良好,无螺钉把紧的轴瓦接合面,用0.05mm和塞尺从外侧检查,在各处的塞入深度,都不得大于接合面的1/3.17.上、下轴瓦装配后其外圆应与相关轴承孔良好接触,如果图样或相关设计文件对接触率未作具体规定时,应按下表的规定执行.上下轴瓦外圆与相关轴承孔的接触要求项目接触要求上瓦下瓦接触角α:稀油润滑 130° 150°接触角α:油脂润滑 120° 140°α角内接触率 60% 70%瓦侧间隙 b,mm D≤200时,0.05mm塞尺不准塞入D>200时,0.10mm塞尺不准塞入18.轴瓦内孔刮研后,应与相关轴颈接触良好, 如图样或相关设计文件未作具体规定时,则按下表的规定执行.上下轴瓦内孔与相关轴颈的接触要求接触角αα角范围内接触点,点数/25×25mm^2稀油润滑油脂润滑轴转速r/min 轴瓦内径,mm≤180 180-360 360-500≤300 4 3 2300-500 5 4 3120° 90° 500-1000 6 5 4>1000 8 6 5注:受力较小的轴瓦、接触点可在25×25mm^2的面积上,按表中数值降低1个接触点.19.上、下轴瓦接触角α以外的部分均需刮出油楔(如下表所示C1),楔形从瓦口开始由最大逐步过渡到零,楔形最大值按下表中规定. 上、下轴瓦经刮研达要求并组装后,轴瓦内径与轴顶部处的间隙值C 应达到图样配合公差的中间值或接近上限值.上下轴瓦油楔尺寸油楔最大值C1)稀油润滑C1≈C油脂润滑距瓦两端面10-15mm范围内,C1≈C中间部位C1≈2C.注:C值为轴瓦的最大配合间隙.20.轴瓦中装固定销用的通孔,应在瓦口面与相关轴承孔的开合面保持平齐的情况下, 与其配钻铰. 固定销打入后,应与销孔紧密配合, 不得有松动现象,销子的端面应低于轴瓦内孔2-3mm.21.过盈配合零件在装配前必须对配合部位进行复检, 并做好记录.过盈量应符合图样或工艺文件的规定;与轴肩相靠的相头轮或环的端面,以及作为装配基准的轮缘端面,与孔的垂直度偏差应在图样规定的范围内.22.压装的轴和套允许在引入端制作导锥, 导锥的长度不准超过配合部位长度的15%,锥度各工厂自定.23.采用压力机压装时,应做好压力变化的记录,压力变化应当平稳,出现异常时就进行分析,不准有压坏零件配合表面的现象. 图样有最大压入力的要求时,应达到规定数值,不准过大或过小.24.压装完成后,在轴肩处必须靠紧,间隙不得大于0.10mm.25.热装薄环或轮缘时,在端面处应设置可靠的定位基准.热装后轴与环或轮毂与轮缘之间的中心不准出现互相偏斜现象.26.除铸铁轮毂与钢制轮缘在热装后可向轮毂内壁均匀浇冷水外,其余热装零件均应自然冷却,不准急冷.27.零件热装时,必须靠紧轴肩或其它相关端面.零件经过冷缩后, 零件与轴肩或其它相关端面的间隙在图样未做规定时,不得大于配合长度尺寸的1/1000.28.主动链轮和被动链轮齿的中心线应当重合. 其偏移误码差不得大于两链轮中心距2/1000.29.链条非工作边的下垂度,在图样没有具体规定时,按两链轮中心距的1-4.5%的规定.30.相关的两个平面需要互研时, 只能在两个平面各自按平板或平尺刮研接近合格后,方准两件互研.被刮研表面接触点在图样或相关设计文件无具体规定或以精磨代替刮研时,应符合下表规定.一般情况下的平面刮研接触点滑动速度接触面积,m^2≤0.20>0.20m/s 点数/25×25mm^2≤0.50 3 40.50-1.50 4 331.下列回转零件必须做静平衡试验:1).图样已给出不平衡力矩限值的零件;2).对于没有注明静平衡试验的回转零件,当Q.nmax>25时均需进行静平衡试验.式中Q为回转零件的质量,t;nmax为回转零件的最大转速,r/min.当nmax≤20r/min的以及锻造的全加工、全对称的回转零件不作静平衡试验.32.对于需要作平衡试验,但未规定平衡精度时,按 JB/ZZ4-86<<刚体转动件的平衡>>规定的平衡精度G18执行.33.所有铸造液压缸体等容器,如试压工序是安排在粗加工后进行的,而在精加工后表面又出现了气孔、裂纹、夹渣等缺陷时,则必须重新进行试压.34.所有钢板焊接的液压罐等容器,焊后应进行试压, 焊缝处经过切削加工时,则要重新试压.35.锻造或锻焊结构的液压缸等,要采用外观、超声波探伤、液压试验等方法,对承压的可靠性进行检验.36.探伤表面粗糙度应达到Ra3.2μm.37.承压母体试压与装配后的密封试压,如无特殊规定试验压力,一般为工作压力的1.5倍.38.零件母体承压可靠性的试压,保压15min(允许补压),母体各部不准有渗漏现象.39.装配件密封性试压,保压2min,不降压,且各密封处不准有渗漏现象.40.固定在机体上的管路,应按照JB/ZQ4000.8-86<<管道与容器焊接防锈通用技术要求>>的规定,进行清洗与防锈处理.。
铸件毛坯

铸造毛坯件的技术要求TT630-357(不适用于轮毂,下环和叶片毛坯)1.0应用范围这些技术要求应适应水轮机铸钢毛配件,并且与毛配件图纸要求提供的铸造毛配件的钢材相一致,初加工的20Л, 25Л, 35Л, 20ГСЛ, 08ГДНФЛ, 10Х12НДЛ, 06Х12Н3ДЛ, 08Х15Н4ДМЛ, 08Х13Н4ДМЛ等级钢。
2.0 一般要求3.1对于表1中材料的指定的化学成分允许的元素含量偏差列在表格2(Table2)。
3.2硫和磷的总含量不能超过0,050%.4.0热处理4.1热处理根据同购方协商一致的热处理规范4.2允许进行两次完全的重复热处理,回火次数不限。
5.0机械性能要求5.1最终热处理后(包括修复缺陷后回火)的毛坯件材料的机械性能和硬度应满足图表3要求图表3 ,5.2机械性能试验样本应从分离的铸件测试样本上取得,或者在铸件的测试带上取得。
对于铸件机械性能测定要求的测试带在毛坯图纸中被指出。
5.2.1. 单独的铸件试验样本从一组铸件中取样,这些铸件由相同的材料浇注并经过共同的热处理。
试验样本尺寸满足所有必要试验的需要包括重复试验需要的双倍数量试验样本。
对于1000Kg及以上的每个铸件应做为一个取样对象。
5.2.2. 在开始制造前,除非试验样本的尺寸在毛坯件图纸中没有被指出,否则试验样本在铸件上的位置和尺寸对于制造商和买方应是一样的并且和买方要求的一致。
试验样本在从铸件上取下前,制造商应在铸件上进行标记并且伴随铸件制造的全过程。
试验样本的尺寸应满足所有试验的需要,包括重复试验所需要的双倍数量样本。
制造商应提交给买方一份样本,这份样本需是已经过全部热处理,其中包括通过焊接进行缺陷处理后的回火处理。
5.3机械性能测试样本应按如下从测试样本上取样:如果壁厚至56mm,样本轴线应从表面深入14mm取样。
如果壁厚超过56mm,样本深度为样本厚度从表面算起的1/4深。
5.4机械性能测试的样本数量:1-拉伸试验,3-冲击试验或冲击弹性试验。
oeDIN1688-4(CHN)压铸件一般公差ni
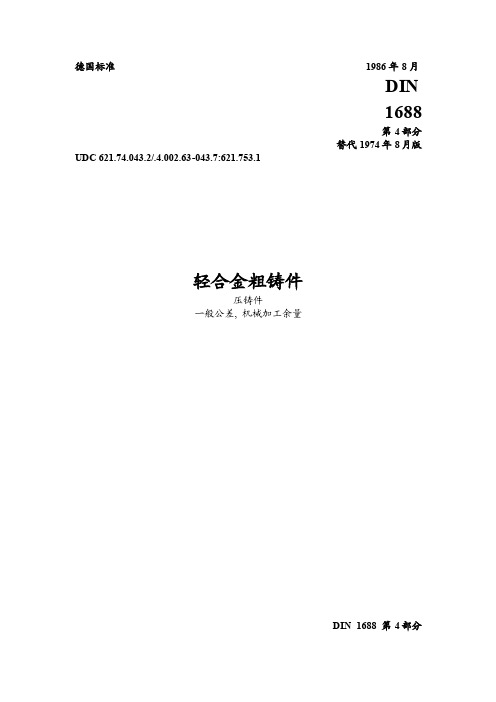
德国标准1986年8月DIN1688第4部分替代1974年8月版UDC 621.74.043.2/.4.002.63-043.7:621.753.1轻合金粗铸件压铸件一般公差, 机械加工余量DIN 1688 第4部分为了与国际标准化组织(ISO)标准的现行惯例保持一致,普遍使用逗号作为十进制标记.若有疑问,以德文原版为准.© 在事先没有得到德国标准协会(DIN)(柏林)允许的情况下,不得对本译本的任何部分进行复制.Beuth V erlag Gmbh出版公司(柏林)拥有德国标准(DIN-标准)之专卖权.英文版价格组06 出售品编号010606.87单位为毫米1应用领域本标准规定了用压力铸造法生产的轻合金粗铸件的允许偏差和机械加工余量.本标准技术规范以DIN 1680 第1部分和第2部分确定的关于粗铸件一般公差的原理为基础,与DIN 1690第1部分规定的技术交货条件一起使用.2概念概念“一般公差”和“精度等级”,与DIN 7182第1部分规定的相同, 已在DIN 1680第1部分粗铸件中使用.概念“机械加工余量” 在DIN 1680第1部分作了规定.基于本标准的目的, 轻合金是以铝和镁为基础的压铸合金, 例如, 见DIN 1725 第2部分和DIN 1729 第2部分的规定.3精度等级3.1尺寸偏差影响用压铸工艺生产的轻合金粗铸件的尺寸偏差的主要因素如下:a)作为精度等级的函数的压件尺寸和功能精度;b)分模线位置, 通过分模线尺寸再分成半模固有尺寸和由两个或多个压模构件组成的复合尺寸(见DIN 1680第1部分);c)通过体对角线来表现特征的铸件的形状或尺寸(见第3.3条);d)基本尺寸的大小.3.2精度等级的应用允许偏差技术规范必须以表1和表2给出的精度等级为基础.3.3体对角线计算体对角线长度R是铸件最大尺寸的函数,用下列公式根据任何给定形状的铸件的棱形包络面的长l,宽b和高h计算得出:R = l2 + b2 + h2按照DIN 1333 第2部分,为R获得的值必须四舍五入到整数.4机械加工余量机械加工余量BZ是粗铸件最大外部尺寸的函数,对于所有的精度等级都相同,DIN 1680第1部分给出的情况除外;见表3.5名称a)一般公差表示为精度等级GTA 14/5,无任何机械加工余量时,名称必须为公差DIN 1688 — GTA 14/5b)一般公差与现行标准规定的机械加工余量(BZN)一起使用时表示为精度等级GTA 14/5时,名称必须为公差DIN 1688 — GTA 14/5 — BZNc)一般公差与现行标准没有对该等级(如,0.8 mm)作规定的但适用于所有加工表面的加工公差(BZ 0.8)一起使用时表示为精度等级GTA 14/5,名称必须为公差DIN 1688 — GTA 14/5 — BZ 0.8参照标准DIN 1333 第2部分约整数DIN 1680第1部分粗铸件; 一般公差和机械加工余量; 总则DIN 1680 第2部分粗铸件;一般公差制度DIN 1690第1部分金属材料铸件技术交货条件; 一般条件DIN 1725 第2部分铝合金;铸造合金;砂型铸件,硬型铸件,压铸件,熔模铸件DIN 1729 第2部分镁合金;铸造合金; 砂型铸件,硬型铸件, 压铸件DIN 7182第1部分尺寸,偏差,公差与配合;基本概念其他相关标准DIN 1688第1部分轻合金粗铸件;砂型铸件;一般公差,机械加工余量DIN 1688 第3部分轻合金粗铸件;硬型铸件;一般公差,机械加工余量前版DIN 1688 第4部分: 08.74.修正与1974年8月版作比较,本版作了下列修正.a)首次使用了机械加工余量.b)对标题和应用领域作了修正.c)正文在编辑上作了修改.国际专利分类B 22 B 17/00B 22 B 21/00。
DIN1685-1_球墨铸铁件公差和加工余量
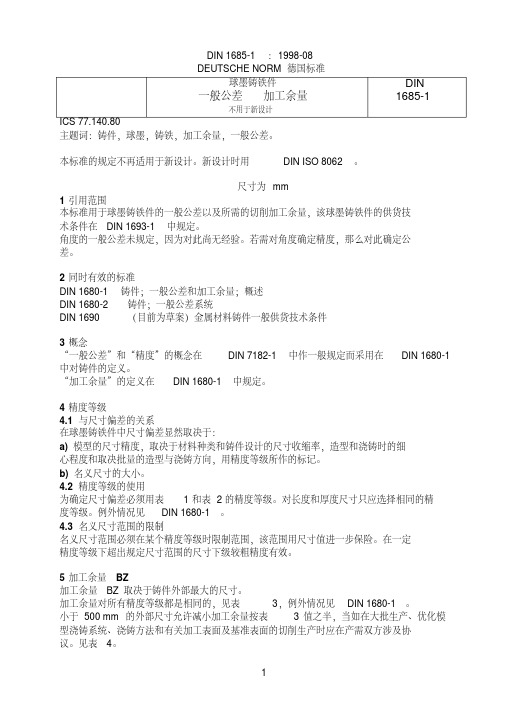
DIN 1685-1:1998-08 DEUTSCHE NORM 德国标准球墨铸铁件一般公差加工余量不用于新设计DIN 1685-1ICS 77.140.80主题词:铸件,球墨,铸铁,加工余量,一般公差。
本标准的规定不再适用于新设计。
新设计时用DIN ISO 8062。
尺寸为 mm1 引用范围本标准用于球墨铸铁件的一般公差以及所需的切削加工余量,该球墨铸铁件的供货技术条件在DIN 1693-1中规定。
角度的一般公差未规定,因为对此尚无经验。
若需对角度确定精度,那么对此确定公差。
2 同时有效的标准DIN 1680-1 铸件;一般公差和加工余量;概述DIN 1680-2 铸件;一般公差系统DIN 1690 (目前为草案)金属材料铸件一般供货技术条件3 概念“一般公差”和“精度”的概念在DIN 7182-1中作一般规定而采用在DIN 1680-1中对铸件的定义。
“加工余量”的定义在DIN 1680-1中规定。
4 精度等级4.1 与尺寸偏差的关系在球墨铸铁件中尺寸偏差显然取决于:a)模型的尺寸精度,取决于材料种类和铸件设计的尺寸收缩率,造型和浇铸时的细心程度和取决批量的造型与浇铸方向,用精度等级所作的标记。
b)名义尺寸的大小。
4.2 精度等级的使用为确定尺寸偏差必须用表1和表2的精度等级。
对长度和厚度尺寸只应选择相同的精度等级。
例外情况见DIN 1680-1。
4.3 名义尺寸范围的限制名义尺寸范围必须在某个精度等级时限制范围,该范围用尺寸值进一步保险。
在一定精度等级下超出规定尺寸范围的尺寸下级较粗精度有效。
5 加工余量BZ加工余量BZ取决于铸件外部最大的尺寸。
加工余量对所有精度等级都是相同的,见表3,例外情况见DIN 1680-1。
小于500 mm的外部尺寸允许减小加工余量按表 3 值之半,当如在大批生产、优化模型浇铸系统、浇铸方法和有关加工表面及基准表面的切削生产时应在产需双方涉及协议。
见表4。
DIN 1685-1:1998-08对铸件重量大于1000kg和/或壁厚大于50mm时加工余量也需在产需双方签订协议。
铸件其相应标准对照

铸件其相应标准对照1、熔模铸造碳素钢铸件产品符合GB 11352-89、JB/T 5100-91标准,满足ZG200-400、ZG230-450、ZG270-500、ZG310-570、ZG340-640及美标ASTM A 216GRWCB、ASTM A732 Grade 1A等牌号的成份及性能要求。
2、熔模铸造不锈钢、耐蚀钢、耐热钢铸件产品符合GB/T2100-2002epvISO 11972:1998、JB/T 5100-91标准要求,满足各类国标牌号及美标ASTM A743 GR CF-8、ASTM A743 CF8M 316SS、ASTM A 351 Gr.CF8M等牌号的成份及性能要求。
3、熔模铸造中低合金钢铸件产品符合GB/T11351-89、JB/T 5100-91标准要求,满足ZG42CrMo、ZG35CrMo、ZG28Cr2Si2MnMo、ZG40Mn、ZG50Mn2等各种牌号的成份及性能要求。
4、熔模铸造铜合金铸件产品符合GB/T13819-92、GB/1176-87、JB/T 5100-91标准,满足各类国标及美标ASTM B505 C93200、ASTM B 584 83800、ASTM B505 C84400、ASTM B 16 GR H02 BRASS C36000、ASTM B62 UNS C83600、ASTM B148 C95800等牌号的成份及性能要求。
5、熔模铸造铝合金铸件产品符合GB/T 1173-1995、JB/T 5100-91标准要求,满足各类牌号成份及性能要求。
6、砂型铸造各类铸件产品符合GB 6414-86、JB/T5105-91标准要求,满足各类国标及美标牌号成份及性能要求。
1 熔模铸造碳素钢铸件产品符合GB 11352-89、JB/T 5100-91标准,满足ZG200-400、ZG230-450、ZG270-500、ZG310-570、ZG340-640及美标ASTM A 216GRWCB、ASTM A732 Grade 1A等牌号的成份及性能要求。
- 1、下载文档前请自行甄别文档内容的完整性,平台不提供额外的编辑、内容补充、找答案等附加服务。
- 2、"仅部分预览"的文档,不可在线预览部分如存在完整性等问题,可反馈申请退款(可完整预览的文档不适用该条件!)。
- 3、如文档侵犯您的权益,请联系客服反馈,我们会尽快为您处理(人工客服工作时间:9:00-18:30)。
ICS 77.150.10; 77.150.20Descriptors:General tolerances, machining allowances, castings,light metal alloys.Gußrohteile aus Leichtmetallegierungen – Sandguß –Allgemeintoleranzen, Bearbeitungszugaben (Nicht für Neukonstruktionen)In keeping with current practice in standards published by the International Organization for Standardization (ISO), a comma has been used throughout as the decimal marker.Ref.No.DIN 1688-1:1998-08English price group 06Sales No.010611.98DEUTSCHE NORM August 19981688-1{Continued on pages 2 to 4.©No part of this translation may be reproduced without the prior permission of DIN Deutsches Institut für Normung e.V., Berlin.Beuth Verlag GmbH , D-10772Berlin, has the exclusive right of sale for German Standards (DIN-Normen).Translation by DIN-Sprachendienst.In case of doubt, the German-language original should be consulted as the authoritative text.Rough castings of light metal alloys producedby sand castingGeneral tolerances and machining allowances(For replacement purposes only)SupersedesOctober 1980 edition.Dimensions in mm1Scope and field of applicationThis standard specifies general tolerances and machining allowances for rough castings of aluminium and magnesium alloys produced by sand casting, which are subject to the technical delivery conditions laid down in DIN 1725-2 and DIN 1729-2.Users of this standard should note that it now only applies to castings used for repair and replacement purposes. New designs are covered by ISO 8062 : 1994.Owing to the lack of empirical data, general tolerances have not been specified here for angular dimensions.If angles are to meet accuracy requirements, these shall be indicated as individual tolerances.2Normative referencesThis standard incorporates, by dated or undated reference, provisions from other publications. These normative references are cited at the appropriate places in the text, and the titles of the publications are listed below. For dated references, subsequent amendments to or revisions of any of these publications apply to this standard only when incorporated in it by amendment or revision. For undated references, the latest edition of the publication referred to applies.DIN 1680-1Rough castings – General tolerances and machining allowances – General DIN 1680-2Rough castings – System of general tolerancesDIN 1725-2Aluminium casting alloys – Sand casting, gravity die casting, pressure die casting and investment castingDIN 1729-2Magnesium casting alloys – Sand casting, gravity die casting, pressure die casting DIN 7182-1Sizes, deviations, tolerances and fits – Basic conceptsISO 8062 : 1994Castings – System of dimensional tolerances and machining allowances3ConceptsSee DIN 7182-1 and DIN 1680-1 for the terms ‘general tolerances’ and ‘tolerance grade’, and DIN 1680-1for a definition of ‘machining allowance’.Page 2DIN 1688-1:1998-084Tolerance grades4.1Dimensional deviationsFor rough castings of light metal alloys produced by sand casting, dimensional deviations are largely dependent ona)the dimensional accuracy of the pattern, the care taken during moulding and casting, and the moulding and casting equipment used based on the batch size;b)the location of the parting line (i.e. dimensions are or are not influenced by the mould; cf. DIN 1680-1);c)the nominal sizes.4.2Application of tolerance gradesLimit deviations shall be specified on the basis of the tolerance grades given in tables 1 and 2. Linear dimensions and thickness shall be specified for the same grade; for exceptions see DIN 1680-1.4.3Nominal size rangesThe nominal size ranges shown in tables 1 and 2 for each tolerance grade have been selected on the basis of reliable measurement data.5Machining allowancesThe machining allowance, BZ , is a function of the largest external dimension of the casting and is the same for all tolerance grades (cf. table 3); see DIN 1680-1 for exceptions.For sizes up to 500 mm, machining allowances may be reduced to approximately half the values specified in table 3 if the pattern equipment, casting procedure and machining procedure with regard to clamping surfaces and datum surfaces have been optimized, for example, for series production, as agreed between the customer and the foundry. These reduced values are shown in table 4.6DesignationWhere both the tolerance grade and the machining allowance have been selected on the basis of this standard,the designation of a grade GTA 16/5 tolerance (GTA 16/5) in conjunction with a machining allowance of 3,5(BZ 3,5), for example, shall be designated as follows:Tolerance and machining allowance DIN 1688 – GTA 16/5 – BZ 3,5See DIN 1680-1 for other examples of designations.Table 1:Limit deviations for linear dimensions (length, width, height,centreline distance, diameter, radius)*)Tolerance gradeDimensionsinfluenced bymouldYes No Nominal size rangeYes No*)Irrespective of the values given in this table, the actual deviation of the linear dimensions of a casting shall in no case be greater than t 25 % of the nominal size, rounded to one decimal place. This restriction is of particular relevance when applying the deviations in the boxes enclosed by thick lines.Correspondsto tolerancegrade... as inDIN 1680-2Over up toOver up to Up to 50Over up to Over up to Over up to Over up to Over up to Over up to Over up to Over up to Over up to plus allowance,plus allowance ,Page 3DIN 1688-1:1998-087Indicating general tolerances on existing drawingsIf an existing drawing does NOT refer to the tolerance groups specified in the 1958 edition of this standard (which is no longer valid), then the tolerance grades given in tables 1 and 2 do not apply. It is recommended that a grade suitable for the casting in question be indicated on such drawings.If an existing drawing DOES refer to the previously valid tolerance groups, it is recommended that these be converted to the tolerance grades specified in tables 1 and 2 of the present standard. If this is not possible, the permissible limit deviations are to be taken from tables 5 and 6 below.Tables 5 and 6 do NOT apply to new drawings.Table 2:Limit deviations for thicknesses (wall, web or rib thicknesses)*)Tolerance gradeDimensions influenced bymouldNominal size rangeOverup toUp to 6Over 10Yes NoYes No*)Irrespective of the values given in this table, the actual deviation of the linear dimensions of a casting shall in no case be greater than t 25% of the nominal size, rounded to one decimal place.This restriction is of particular relevance when applying the deviations in the boxes enclosed by thick lines.The limit deviations specified in table 2 have not been derived from a specific tolerance series.Table 3:Machining allowances, BZTable 4:Reduced machining allowances, BZ (see clause 5)Nominal size range (based on the largest overall dimension of casting)Nominal size range (based on the largest overall dimension of casting)Machining allowance, BZMachining allowance, BZOverup toOver up toUp to 30Over up toOver up toOver up toOver up toOver up toOver up toOver up toUp to 30Overup toOver up toOver up toOver up toOver up toOver up toPage 4DIN 1688-1:1998-08Table 5:Limit deviations for linear dimensions on existing drawingsTable 6: Limit deviations for thicknesses on existing drawings8Indicating machining allowances on existing drawingsThe machining allowances specified in this standard only apply to drawings on which general tolerances in accordance with clause 4 and tables 1 and 2 of this standard are indicated.Previous editionsDIN 1688-1: 1958-04, 1974-08, 1980-10.AmendmentsAs compared with the October 1980 edition, the standard now applies only to castings used for replacement purposes.Other relevant standardDIN 1690-1Technical delivery conditions for castings of metallic materials – GeneralTolerancegroupNominal size rangeOver up toTolerancegroupNominal size rangeOver up toUp to 50Over up toOver up toOver up toOver up toOver up toOver up toOver up toOver up toOver up toUp to 6Over up to。