等静压成形工艺的优化研究
ptfe等静压成型工艺流程

ptfe等静压成型工艺流程PTFE是聚四氟乙烯的缩写,是一种具有优异性能的高分子材料。
静压成型工艺是一种常用的PTFE制造工艺,它通过将PTFE粉末在高温和高压的条件下进行成型,得到各种形状的制品。
本文将详细介绍PTFE静压成型的工艺流程和相关特点。
一、PTFE静压成型工艺流程PTFE静压成型的工艺流程主要包括粉末制备、预压、烧结和后处理等环节。
1. 粉末制备:首先需要将PTFE树脂经过研磨和分级,得到细小的PTFE粉末。
粉末的粒径和分布对最终制品的性能有很大影响,因此在粉末制备过程中需要严格控制粉末的质量和粒度。
2. 预压:将PTFE粉末放入模具中,然后施加一定的压力进行预压。
预压的目的是使粉末颗粒更加紧密地结合在一起,并排除空隙和气泡。
预压的压力一般在20~30MPa之间,时间根据制品的大小和形状而定。
3. 烧结:将预压得到的PTFE制品放入烧结炉中进行烧结。
烧结的温度和时间是影响制品性能的重要因素。
一般情况下,烧结温度为340~380℃,烧结时间约为1~2小时。
烧结过程中,PTFE粉末颗粒会融化并与周围颗粒结合,形成致密的结构。
4. 后处理:烧结后的PTFE制品需要进行后处理,主要包括冷却、修整和检测等步骤。
冷却是将烧结的制品从烧结炉中取出后放置在自然环境中进行冷却。
修整是对制品进行切割和修整,使其达到设计要求的形状和尺寸。
检测是对制品进行外观和性能的检测,确保制品质量符合要求。
二、PTFE静压成型的特点1. 良好的化学稳定性:PTFE具有优异的化学稳定性,可以耐受酸、碱和大部分有机溶剂的侵蚀。
2. 优异的耐高温性能:PTFE的使用温度范围广,可以在-200℃~260℃的温度下长期使用。
3. 低摩擦系数:PTFE具有极低的摩擦系数,在润滑条件下能够实现良好的自润滑效果。
4. 良好的绝缘性能:PTFE具有良好的绝缘性能,可以在高压和高频率下保持稳定的绝缘性能。
5. 良好的耐磨性:PTFE具有良好的耐磨性,可以在高速和高负载条件下长期使用。
陶瓷等静压成型工艺

标题:深入探究陶瓷等静压成型工艺引言:在现代工业领域,特别是在高性能材料制造中,陶瓷材料以其优异的耐高温、耐腐蚀和高硬度特性成为了重要的工程材料。
为了充分发挥陶瓷材料的性能,精确且高效的成型工艺显得尤为关键。
等静压成型技术(Isostatic Pressing Technology)便是制备高精度陶瓷制品的重要方法之一。
该技术以其均匀的压实效果和能够生产复杂形状零件的能力而受到重视。
一、等静压成型工艺概述等静压成型是一种利用流体或气体传递压力均匀的特性,使物料在各个方向上受到相等压力而成型的方法。
这种成型方式可以显著提高成型体的密度和结构的均匀性。
等静压成型分为两大类:冷等静压(CIP)和热等静压(HIP)。
二、冷等静压(CIP)冷等静压是在室温下将粉末置于橡胶或其他柔软模具中,然后将其放入密闭容器中施加等向静水压力,通过液体介质如油或水来传递压力,从而获得均匀压实的绿体。
CIP能够处理各种形状复杂和尺寸大的零件,常用于批量生产。
三、热等静压(HIP)热等静压则是在高温高压环境下对粉末或已烧结的陶瓷进行压制,旨在消除残留孔隙,提高材料的密度和强度。
这一过程通常需要使用惰性气体作为压力传递介质,如氩气或氮气。
HIP对于提升成品的力学性能特别有效。
四、等静压成型工艺流程以冷等静压为例,典型的成型流程包括:1. 粉末准备:选择合适的陶瓷粉末以及可能的添加剂(如粘结剂、塑化剂等),经过混合和研磨以得到均质的粉末。
2. 装模:将粉末填充进弹性模具中,并进行初步定位。
3. 压制:把装有粉末的模具置入等静压机中,通过液体介质传递高压力,使粉末在各个方向上均匀受压成型。
4. 脱模与固化:成型后从模具中取出成型体,并进行适当的固化处理。
5. 烧结:将固化后的成型体放入高温炉中,通过烧结使颗粒之间产生固相扩散,形成致密的陶瓷体。
6. 后处理:包括研磨、抛光等步骤以获得所需的最终形状和表面质量。
五、等静压成型的优势与挑战优势:1. 均匀压实:由于压力传递的均匀性,可以获得高度均一的密实度。
等静压成型概论范文

等静压成型概论范文等静压成型(Iso-static Pressing,简称IP)是一种材料加工方法,通常用于制备高密度的陶瓷、金属和复合材料。
其原理是将材料粉末放置在一个模具中,然后施加等静压力,使粉末颗粒之间形成高密度结构。
本文将探讨等静压成型的原理、工艺和应用。
等静压成型的原理基于物理学中的等静力理论。
当施加的静压力在三个方向上都相等时,即在各个方向上施加均匀的压力,材料粉末颗粒之间就会形成密实的接触,从而实现高密度结构。
相比于传统的压粉烧结方法,等静压成型能够实现更高的密度,减少气孔和缺陷的形成,从而提高材料的力学性能和其他性能指标。
等静压成型的工艺包括以下几个步骤。
首先,需要将所需材料制备成粉末形式。
这种粉末通常具有细小的颗粒尺寸和窄的颗粒大小分布,以提高材料的可塑性和流动性。
然后,将粉末放置在一个特殊设计的模具中,模具通常具有所需产品的形状和尺寸。
接下来,施加等静压力到模具中,以使粉末颗粒之间相互接触,并且形成高密度的结构。
最后,取出成型后的材料,进行烧结和热处理等后续工艺,以进一步提高材料的性能。
等静压成型的应用广泛。
在陶瓷领域,等静压成型常用于制备高硬度和耐磨材料,如陶瓷刀具和陶瓷球等。
在金属领域,等静压成型常用于制备复杂形状的零件,如汽车发动机部件和航空发动机零件等。
在复合材料领域,等静压成型通常用于制备高性能陶瓷基复合材料,如碳纤维增强陶瓷基复合材料,在航天、航空和能源领域具有广泛的应用前景。
尽管等静压成型具有许多优点,如能够实现高密度和形状复杂性等,但也存在一些限制。
首先,等静压成型通常需要经过多个工艺步骤,包括烧结和热处理等,从而增加了工艺复杂性和成本。
其次,等静压成型对模具的设计和制造要求较高,以确保施加的静压力能够均匀地传递到材料粉末中。
此外,由于等静压成型的原理限制,对于一些材料,如纤维增强复合材料,其工艺性能和力学性能需要进一步改善和优化。
总之,等静压成型是一种重要的材料加工方法,用于制备高密度的陶瓷、金属和复合材料。
等静压成形工艺的优化研究

的控 制提供依据 , 使 产品在达 到性 能要求 的 同时 , 提 高其 尺 寸 的可控 度 , 从而 提高产 品的合格 率 。同时 , 选择 合理
的成 形 压 力 以 降低 压 机 的损 耗 , 提高工作效 率。
粒径 ( m) 图 1 氧化 铝 造 粒 料 颗 粒 分 布 图
( 4 )粘 结 剂 : 1 . 2 %~ 1 . 5 %; ( 5 ) 粉料 松装密度 : 1 . 0 5 g / c m ; ( 6 ) 粉料 堆实密度 : 1 . 1 3 3 g / c m 。
将 会导致 真空管壳 尺寸 的浮动较 大 .从 而使得 尺寸超 出
公 差 。所 以 , 一套稳 定可控 的成形工 艺就显 得尤 为重要 。 本 实 验 主要 在 成 形 压 力 的 控 制 上 进 行 了研 究 ,并 分 析 了 成 形 压 力 和 保 压 时 间 对 烧 成 收缩 的 影 响 ,为 以 后 对 收 缩
并在 1 7 1 0 ℃的 推 板 窑 中 烧 成 。
3 6. 4 40 6 0 8 0 1 00 1 2 0
压力 ( MP a )
2 . 3 成形收缩 的测量 本 实验 采用 的橡 胶模 套 内径为 ‘ P : = 4 9 mm ,芯 棒外 径
图 2 成 形 收缩 与 压 力 的 关 系
压力 ( MP a )
图 3 烧 结 收 缩 与 压力 的关 系
纵 向烧成收缩= H d H G
( 3 )
26 昌 2.
、
2 . 5 烧成试 样密度 的测量
采用 排水法测定试 样的密度 。
船 2. 2 2
~
3 8- 4 缩 3 . O 、 2 . 2 试样 的制备
陶瓷等静压成型工艺

陶瓷等静压成型工艺稿子一嘿,朋友!今天咱们来聊聊陶瓷等静压成型工艺,这可真是个有趣的话题呢!你知道吗,陶瓷等静压成型工艺就像是给陶瓷一个超级舒适的“按摩”,让它们乖乖地变成我们想要的形状。
想象一下,把陶瓷粉末放进一个软软的模具里,然后从各个方向均匀地施加压力。
这压力可厉害了,就像无数双温柔又有力的手,把陶瓷粉末紧紧地压在一起,不留一点缝隙。
这样做出来的陶瓷,密度均匀,强度高,品质那叫一个棒!而且哦,这个工艺能做出各种形状复杂的陶瓷制品。
不管是圆圆的碗,还是奇形怪状的装饰品,都不在话下。
就像是魔法一样,能满足我们各种奇思妙想。
在操作的时候,可不能马虎。
得控制好压力的大小和时间,不然陶瓷可能就“发脾气”,做不出完美的样子啦。
怎么样,是不是觉得陶瓷等静压成型工艺很神奇?我反正是被它深深吸引了,每次看到那些精美的陶瓷制品,都会想到背后这个厉害的工艺。
稿子二亲,咱们来唠唠陶瓷等静压成型工艺哈!这工艺啊,就像是陶瓷世界里的一场奇妙冒险。
一开始,把那些细细的陶瓷粉末准备好,就像给小士兵们排好队。
然后呢,把它们放进专门的模具里,这时候好戏才开始!从四面八方来的压力,均匀又稳定,就好像给这些小粉末来了一场“团结大会”,让它们紧紧地抱在一起,变成一个结实的整体。
你别小看这压力,它可是有讲究的。
太大了,陶瓷可能会受不了;太小了,又达不到理想的效果。
所以啊,这得靠师傅们的经验和技巧,就像大厨掌握火候一样,要恰到好处。
等静压成型后的陶瓷,那可真是让人眼前一亮。
表面光滑细腻,内部结构也特别紧实,质量杠杠的!用这样的陶瓷做出来的东西,既美观又耐用。
而且哦,这个工艺还能让陶瓷变得更有创意。
可以做出各种独特的形状和设计,满足不同人的喜好。
感觉就像是陶瓷在这个工艺的帮助下,尽情地展现自己的魅力。
怎么样,是不是对陶瓷等静压成型工艺有了新的认识?我反正每次想到这个,都觉得太神奇啦!。
北航热等静压

北航热等静压热等静压技术是一种常用于航空航天领域的关键技术,主要应用于喷气发动机的涡轮叶片制造过程中。
北航作为中国航空航天领域的顶尖高校,一直在该领域做出了重要的贡献。
本文将围绕北航在热等静压技术方面的研究与应用进行探讨。
热等静压技术是一种通过热源加热,使得工件内部保持等静压的工艺方法。
在喷气发动机涡轮叶片制造过程中,涡轮叶片的内部结构复杂,由许多空腔和空隙构成。
热等静压技术通过加热空气,使其膨胀产生压力,从而使得工件内部的空腔与外部压力保持一致,确保了工件的成型质量和性能。
北航在热等静压技术方面的研究取得了显著的成果。
首先,北航研发了一套高精度的热等静压设备。
该设备采用先进的热控技术,能够精确控制加热温度和加热时间,保证了工件在加热过程中的稳定性和均匀性。
同时,该设备还具备高度自动化的特点,能够实现对工件的全程监控和控制,提高了生产效率和产品质量。
其次,北航在热等静压工艺参数的优化方面也做出了突出贡献。
热等静压工艺参数的优化对于提高产品质量和生产效率至关重要。
北航通过对不同工件的加热温度、加热时间和压力等参数进行系统研究和实验验证,建立了一套完善的参数优化模型。
这些研究成果不仅为热等静压工艺的应用提供了科学依据,还为工程实践中的工艺参数选择提供了参考和指导。
此外,北航还积极探索热等静压技术在其他领域的应用。
热等静压技术不仅在航空航天领域有着广泛的应用,还可以应用于汽车制造、船舶制造、石油化工等领域。
北航的研究人员结合不同领域的需求,探索并开发了适用于其他领域的热等静压技术解决方案。
这些研究成果的应用推广,为其他领域的工艺改进和产品质量提升提供了新的思路和方法。
总之,北航在热等静压技术方面的研究与应用取得了显著成果。
通过研发高精度的热等静压设备,优化工艺参数,探索多领域应用等方面的努力,北航为热等静压技术的发展和应用做出了重要贡献。
相信随着技术的不断进步和研究的深入,热等静压技术将在航空航天领域和其他领域发挥更加重要的作用,为工业制造带来更多的创新和突破。
等静压成型工艺参数对高纯石墨制品的影响研究
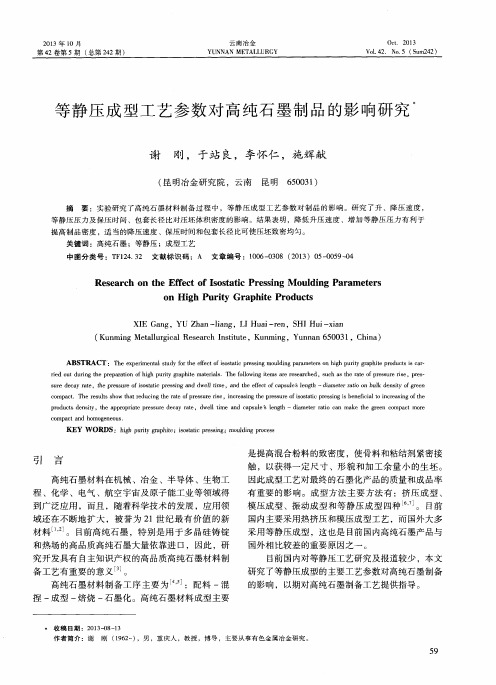
s l / r e d e c a y r a t e ,t h e p r e s s u r e o f i s o s t a t i e p r e s s i n g a n d d w e l l t i m e , a n d t h e e f f e c t o f c a p s u l e  ̄l e n g t h—d i a me t e r r a t i o O n b u l k d e n s i t y o f g r e e n
Re s e a r c h o n t h e Ef fe c t o f I s o s t a t i c Pr e s s i ng Mo ul d i n g Pa r a me t e r s
o n Hi g h Pu r i t y Gr a ph i t e Pr o d uc t s
提高制 品密度 ,适 当的降压速度 、保压时间和包套长径 比可使压坯致 密匀。
关 键 词 :高 纯 石 墨 ;等 静 压 ;成 型 工 艺 中 图分 类号 :T F 1 2 4 . 3 2 文 献 标 识 码 :A 文章 编 号 :1 0 0 6 - 0 3 0 8( 2 0 1 3 )0 5 — 0 0 5 9 - 0 4
c o mp a c t .Th e r e s u l t s s h o w t h a t r e d u c i n g t h e r a t e o f p r e s s u r e is r e,i n c r e a s i n g t h e p r e s s u r e o f i s o s t a t i c p r e s s i n g i s b e n e ic f i a l t o i n c r e a s i n g o f t h e p r o d u c t s d e n s i t y,t h e a p p r o p ia r t e p r e s s u r e d e c a y r a t e,d we l l t i me a n d c a p s u l e" s l e n g t h— d i a me t e r r a t i o c a n ma k e t h e re g e n c o mp a c t mo r e
什么是热等静压成型技术?

什么是热等静压成型技术?热等静压成型技术是一种先进的加工方法,广泛应用于航空航天、汽车制造、能源等领域。
它通过将粉末原料加热至高温并施加高压来制造坚固、高精度的零件和构件。
下面将从几个方面详细介绍热等静压成型技术的原理、应用以及未来发展趋势。
一、原理1.温度和压力控制:热等静压成型技术基于物质在高温和高压条件下的可塑性。
温度可使粉末原料变得可塑,而压力则能够使原料充分填充模具并形成所需形状。
2.粉末原料选择:热等静压成型技术通常使用金属粉末作为原料,包括铝、钢、镁等。
这些金属粉末具有良好的可塑性和热导性,适合于此类加工方法。
3.模具设计与制造:模具是热等静压成型技术的关键。
合理设计和制造模具可以保证零件的准确性和质量。
二、应用1.航空航天领域:热等静压成型技术可以制造出高精度、高强度的航空发动机零部件和复杂的涡轮叶片。
这些零件的制造过程需要满足严格的质量要求,而热等静压成型技术能够提供可靠的解决方案。
2.汽车制造领域:热等静压成型技术可用于制造各类发动机零件、底盘零件和传动系统部件。
相比传统的铸造和锻造工艺,它可以提供更高的准确性和性能。
3.能源领域:热等静压成型技术可以制造出耐高温和耐压的燃烧室和热交换器。
这些组件在火电厂、核电站等领域中发挥关键作用,因此需要具备优异的性能和可靠性。
三、未来发展趋势1.材料优化:随着科学技术的不断进步,研究人员将致力于开发新型的金属粉末材料,以满足更高的性能需求。
2.工艺改进:热等静压成型技术的工艺参数和设备将不断改进,以实现更高的加工效率和质量水平。
3.智能化应用:人工智能技术的兴起将为热等静压成型技术带来更多的应用机会,例如模具设计的优化和生产过程的自动化控制。
总结起来,热等静压成型技术是一种重要的先进加工方法,具有广泛的应用前景。
未来,随着材料和工艺的不断改进以及智能化技术的运用,热等静压成型技术将在各个领域发挥更加重要的作用。
等静压成形工艺的优化研究

等静压成形工艺的优化研究作者:薛志岗来源:《佛山陶瓷》2013年第05期摘要:本文研究了等静压成形工艺过程中氧化铝造粒粉料成形后的坯体相对密度和强度随着各成形参数的变化而变化的规律,并进一步研究了其对烧结收缩的影响。
实验表明:随着压力的增大,坯体密度逐渐提高,强度也相应增大;保压时间对坯体的相对密度影响不明显;在成形压力范围内,坯体相对密度对烧结之后的试样致密度影响不大。
关键词:等静压成形;相对密度;保压时间;烧结1 概述随着陶瓷工业和科学技术的发展,等静压成形工艺已成为陶瓷主要的成形工艺之一。
采用等静压成形工艺具有粉料受压均匀、坯体结构致密、强度高、烧成收缩小、产品不易变形,并且产品的含水率低、无需干燥,可直接入窑等优点。
陶瓷的成形,直接影响到后续的坯体加工质量、烧成制度和烧结后产品本身的结构性能。
随着科技的进步,对真空管壳尺寸的要求也越来越高,尤其是在真空管的成形过程中,由于其内径是一次成形。
烧成收缩的微小变化将会导致真空管壳尺寸的浮动较大,从而使得尺寸超出公差。
所以,一套稳定可控的成形工艺就显得尤为重要。
本实验主要在成形压力的控制上进行了研究,并分析了成形压力和保压时间对烧成收缩的影响,为以后对收缩的控制提供依据,使产品在达到性能要求的同时,提高其尺寸的可控度,从而提高产品的合格率。
同时,选择合理的成形压力以降低压机的损耗,提高工作效率。
2 实验内容2.1 原料的准备2.2 试样的制备将粉料进行等静压成形,考虑到现有的生产状况,成形压力选择为50MPa、60MPa、70MPa、80MPa、90MPa、100MPa、110MPa、120MPa,保压时间分别选取20s、40s、60s、80s、100s。
将成形的坯体经过车床加工制成形状为中空圆柱状试样,外径φ1为35mm左右,高度70mm左右,并在1710℃的推板窑中烧成。
2.3 成形收缩的测量2.4 烧成收缩的测量2.5 烧成试样密度的测量3 结果与分析3.1 成形压力对成形和烧成的影响本文以保压时间为20s的一组数据进行分析。
碳化硅等静压成型技术
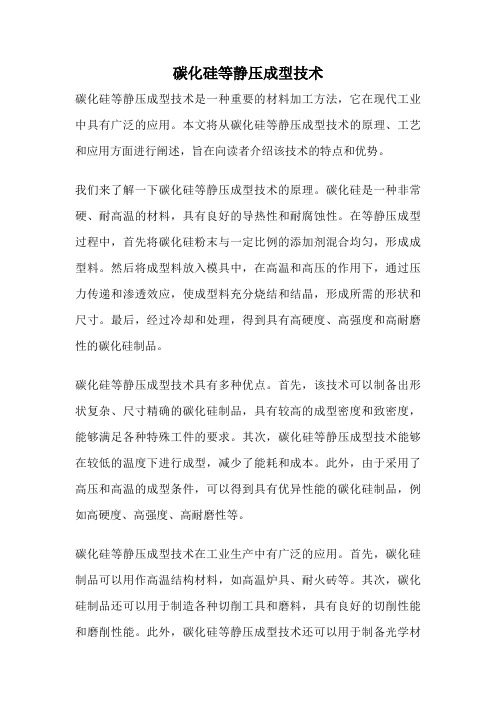
碳化硅等静压成型技术碳化硅等静压成型技术是一种重要的材料加工方法,它在现代工业中具有广泛的应用。
本文将从碳化硅等静压成型技术的原理、工艺和应用方面进行阐述,旨在向读者介绍该技术的特点和优势。
我们来了解一下碳化硅等静压成型技术的原理。
碳化硅是一种非常硬、耐高温的材料,具有良好的导热性和耐腐蚀性。
在等静压成型过程中,首先将碳化硅粉末与一定比例的添加剂混合均匀,形成成型料。
然后将成型料放入模具中,在高温和高压的作用下,通过压力传递和渗透效应,使成型料充分烧结和结晶,形成所需的形状和尺寸。
最后,经过冷却和处理,得到具有高硬度、高强度和高耐磨性的碳化硅制品。
碳化硅等静压成型技术具有多种优点。
首先,该技术可以制备出形状复杂、尺寸精确的碳化硅制品,具有较高的成型密度和致密度,能够满足各种特殊工件的要求。
其次,碳化硅等静压成型技术能够在较低的温度下进行成型,减少了能耗和成本。
此外,由于采用了高压和高温的成型条件,可以得到具有优异性能的碳化硅制品,例如高硬度、高强度、高耐磨性等。
碳化硅等静压成型技术在工业生产中有广泛的应用。
首先,碳化硅制品可以用作高温结构材料,如高温炉具、耐火砖等。
其次,碳化硅制品还可以用于制造各种切削工具和磨料,具有良好的切削性能和磨削性能。
此外,碳化硅等静压成型技术还可以用于制备光学材料、电子材料、陶瓷材料等,具有广阔的应用前景。
碳化硅等静压成型技术是一种重要的材料加工方法,具有独特的原理和优势。
通过该技术,可以制备出具有高硬度、高强度和高耐磨性的碳化硅制品,满足各种特殊工件的要求。
碳化硅等静压成型技术在高温结构材料、切削工具、磨料等领域具有广泛的应用,为现代工业的发展做出了重要贡献。
相信随着科技的不断进步和创新,碳化硅等静压成型技术将在未来发展中展现出更加广阔的应用前景。
响应曲面法优化各向同性石墨的冷等静压成型工艺
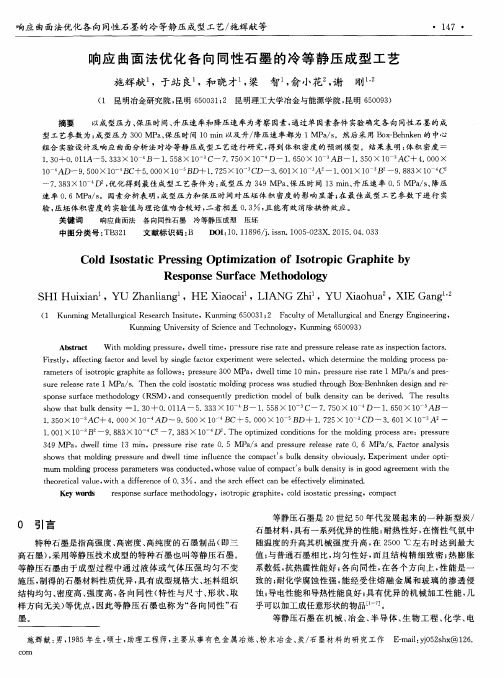
Co l d I s o s t a t i c Pr e s s i n g Op t i mi z a t i o n o f I s o t r o p i c Gr a ph i t e b y Re s po ns e S u r f a c e Me t h o d o l o g y
响应 曲面法优 化各 向 同性 石墨 的冷 等静 压成 型 工 艺/ 施 辉 献等
・1 4 7・
响 应 曲面 法 优化 各 向 同性石 墨 的冷等 静 压 成型 工艺
施辉献 ,于站 良 , 和 晓才 , 梁 智 , 俞 小花 , 谢 刚
( 1 昆明冶金研究 院 , 昆明 6 5 0 0 3 1 ; 2 昆明理工大学冶金 与能源学院 , 昆明 6 5 0 0 9 3 )
验, 压 坯体 积密度的 实验值与理论值 吻合较好 , 二者相 差 0 . 3 , 且能有效消除拱桥效应 。
关键 词 响应曲面法 各 向同性 石墨 冷等静压成 型 压坯
中 图分 类 号 : T B 3 2 1
文 献标 识 码 : B
D O I : 1 0 . 1 1 8 9 6 / j . i s s n . 1 0 0 5 — 0 2 3 X . 2 0 1 5 . 0 4 . 0 3 3
F i r s t l y,a f f e c t i n g f a c t o r a n d l e v e l b y s i n g l e f a c t o r e x p e r i me n t we r e s e l e c t e d ,wh i c h d e t e r mi n e t h e mo l d i n g p r o c e s s p a —
等静压成形工艺的优化

结合人工智能、机器学习等技术,开发智能化等静压成形技术,提 高生产效率和制品质量。
拓展多功能材料制备
研究等静压成形工艺在多功能材料制备方面的应用,为高性能复合材 料的制备提供技术支持。
THANKS
谢谢您的观看
脱模与后处理
脱去模具,对成形件 进行后处理如烧结、 热处理等。
设备和材料
等静压机
提供稳定、均匀的等静压 力,确保粉末在各个方向 上受到相同的压力。
模具材料
选择高强度、耐腐蚀、易 脱模的材料制作模具,如 金属、陶瓷等。
粉末材料
选择适当的粉末原料,如 金属粉末、陶瓷粉末等, 确保成形件的质量和性能 。
03
工艺参数对成形质量的影响
压力
压力大小
压力过大可能导致制品开裂,压 力过小则制品密度不足。
压力分布
不均匀的压力分布会导致制品变形 或开裂,需优化压力传递路径。
加压速度
加压速度过快可能引起制品开裂, 需控制加压速度。
温度
粉末温度
粉末温度过高会导致粘结剂失效,温度过低则影 响流动性。
模具温度
模具温度过高会引起制品粘模,温度过低则影响 制品脱模。
等静压成形工艺的优化
汇报人: 日期:
目录
• 引言 • 等静压成形工艺基础 • 工艺参数对成形质量的影响 • 优化方案的设计与实施 • 优化效果评估与讨论 • 结论与展望
01
引言
目的和背景
目的
阐述等静压成形工艺优化的重要性,分析现有工艺存在的问题,并提出相应的 解决方案。
背景
等静压成形工艺是一种广泛应用于陶瓷、粉末冶金、复合材料等领域的成形技 术,具有成形精度高、材料利用率高等优点。然而,在实际应用中,该工艺仍 存在一些问题,如成形效率低、成本高等,亟待优化。
面向航空航天难成形金属材料的热等静压工艺与性能研究
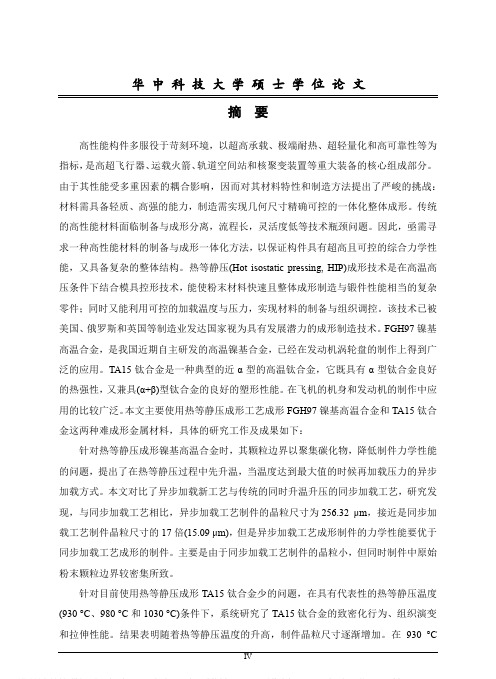
华中科技大学硕士学位论文摘要高性能构件多服役于苛刻环境,以超高承载、极端耐热、超轻量化和高可靠性等为指标,是高超飞行器、运载火箭、轨道空间站和核聚变装置等重大装备的核心组成部分。
由于其性能受多重因素的耦合影响,因而对其材料特性和制造方法提出了严峻的挑战:材料需具备轻质、高强的能力,制造需实现几何尺寸精确可控的一体化整体成形。
传统的高性能材料面临制备与成形分离,流程长,灵活度低等技术瓶颈问题。
因此,亟需寻求一种高性能材料的制备与成形一体化方法,以保证构件具有超高且可控的综合力学性能,又具备复杂的整体结构。
热等静压(Hot isostatic pressing, HIP)成形技术是在高温高压条件下结合模具控形技术,能使粉末材料快速且整体成形制造与锻件性能相当的复杂零件;同时又能利用可控的加载温度与压力,实现材料的制备与组织调控。
该技术已被美国、俄罗斯和英国等制造业发达国家视为具有发展潜力的成形制造技术。
FGH97镍基高温合金,是我国近期自主研发的高温镍基合金,已经在发动机涡轮盘的制作上得到广泛的应用。
TA15钛合金是一种典型的近α型的高温钛合金,它既具有α型钛合金良好的热强性,又兼具(α+β)型钛合金的良好的塑形性能。
在飞机的机身和发动机的制作中应用的比较广泛。
本文主要使用热等静压成形工艺成形FGH97镍基高温合金和TA15钛合金这两种难成形金属材料,具体的研究工作及成果如下:针对热等静压成形镍基高温合金时,其颗粒边界以聚集碳化物,降低制件力学性能的问题,提出了在热等静压过程中先升温,当温度达到最大值的时候再加载压力的异步加载方式。
本文对比了异步加载新工艺与传统的同时升温升压的同步加载工艺,研究发现,与同步加载工艺相比,异步加载工艺制件的晶粒尺寸为256.32 μm,接近是同步加载工艺制件晶粒尺寸的17倍(15.09 μm),但是异步加载工艺成形制件的力学性能要优于同步加载工艺成形的制件。
主要是由于同步加载工艺制件的晶粒小,但同时制件中原始粉末颗粒边界较密集所致。
复杂金属零件热等静压整体成形技术

复杂金属零件热等静压整体成形技术
复杂金属零件热等静压整体成形技术是一种通过热等静压成形工艺制造复杂金属零件的方法。
该技术的核心是在金属原料加热到合适温度后,将其置于模具中,在高压和高温下施加力量,使金属原料充分填充模具的空腔。
在这个过程中,金属原料的温度和压力会导致其变形和流动,最终形成所需的复杂形状。
与传统的机械加工方法相比,复杂金属零件热等静压整体成形技术具有以下优点:
1. 高精度和高表面质量:热等静压成形可以实现近净成形,减少后续加工的需求,从而提高成品的精度和表面质量。
2. 省材料和节能环保:热等静压成形技术可以将金属原料的利用率提高到90%以上,减少材料浪费。
同时,相对于传统的
机械加工方法,热等静压成形不需要大量削减金属材料,节约能源,并且减少了废弃物和废气的产生,对环境更友好。
3. 生产效率高:热等静压成形可以一次完成多个工序,减少了制造过程中的中间传递和安装时间,提高了生产效率。
4. 适用性广:热等静压成形技术适用于各种金属材料,包括钢、铁、铝等,能够制造出各种形状和尺寸的复杂零件。
总之,复杂金属零件热等静压整体成形技术是一种先进的制造
方法,具有高精度、高效率、高环保等优点,被广泛应用于航空航天、汽车、船舶等领域的零部件制造。
以液体静压为基础的高压成型技术分析

以液体静压为基础的高压成型技术分析随着科技的发展,各个行业都在不断探索与改进新的技术。
制造业中液体静压成型技术就是一种被广泛应用的高新技术。
这种技术通过利用高压油液推动金属板材变形,以满足产品对于形状、尺寸、性能等各方面的要求。
本文将从液体静压成型的基本概念、原理,以及优点等方面来对该技术进行分析。
一、基本概念液体静压成型技术(Hydrostatic Forming Technology)又称液压成型、液态冲击成型或压力成型,是一种利用高压油液来推动金属板材形成目标形状的成型技术。
这种技术广泛应用于航空、汽车、骨科、建筑等领域的产品生产中。
传统的冷冲压成型技术的局限性在于其不能对比较厚的材料进行成型,而液压成型技术则可以克服这种局限,成型厚度可以达到几百毫米。
二、原理在液态静压成型技术中,先将金属板材加工成凸台形状,并将其安置在硅胶板上方。
然后在凸台顶端装置一片板状的油囊,将油囊充满高压液体(通常为油)。
随后在凸台上端加上塑料膜,然后启动高压油泵,将高压油液注入油囊内。
这时,油囊内的压力就会逐渐升高,由于油囊的切线上的液体的力会作用在管子上,从而让管子形成所需要的凸缓形状。
整个成型过程中,凸台下的硅胶板要充满高压液体以保持均衡压力。
该过程的原理在于物理学中的伯努利原理。
泵抽出油液经过高压泵前经过油箱、空气旋流分离器、油箱回流阀,然后油液进入高压泵,在高压泵内部被压缩,经过高压泵出口进入高压阀体,进入行程液压泵中的柱塞式泵体,接着经过阀体,油液进入行程缸,以压力将成形件顶起并使之伸出打水滴状填充油囊的空间成形。
三、优点液态静压成型技术相对于传统的成型技术有如下的几个优点:1.变形效果好:该技术可以满足更复杂、精密、高强度的产品成型需求。
2.成型质量高:成型后的产品表面平整度好、无疤痕,无内部缺陷。
3.适用性广:该技术适用于各种类型的材料,比如金属、非金属、塑料等。
4.节约材料:该技术对材料的浪费较少,可以让生产成本更低。
等静压成形工艺的优化研究
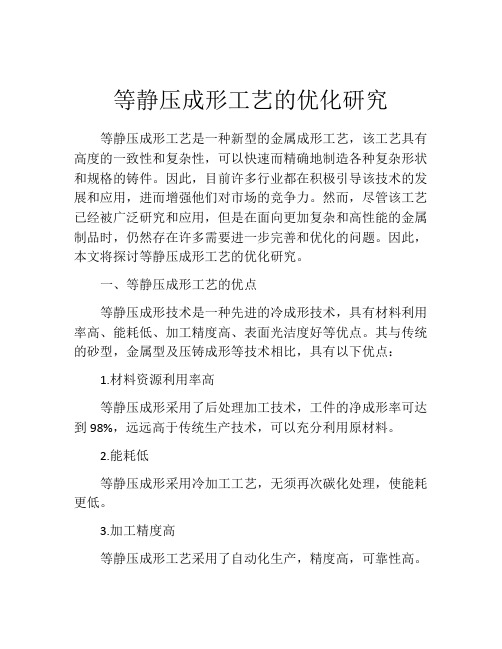
等静压成形工艺的优化研究等静压成形工艺是一种新型的金属成形工艺,该工艺具有高度的一致性和复杂性,可以快速而精确地制造各种复杂形状和规格的铸件。
因此,目前许多行业都在积极引导该技术的发展和应用,进而增强他们对市场的竞争力。
然而,尽管该工艺已经被广泛研究和应用,但是在面向更加复杂和高性能的金属制品时,仍然存在许多需要进一步完善和优化的问题。
因此,本文将探讨等静压成形工艺的优化研究。
一、等静压成形工艺的优点等静压成形技术是一种先进的冷成形技术,具有材料利用率高、能耗低、加工精度高、表面光洁度好等优点。
其与传统的砂型,金属型及压铸成形等技术相比,具有以下优点:1.材料资源利用率高等静压成形采用了后处理加工技术,工件的净成形率可达到98%,远远高于传统生产技术,可以充分利用原材料。
2.能耗低等静压成形采用冷加工工艺,无须再次碳化处理,使能耗更低。
3.加工精度高等静压成形工艺采用了自动化生产,精度高,可靠性高。
4.表面光洁度好等静压成形工艺可以制造高质量、表面光洁度高的零件和零件。
二、等静压成形工艺的应用及其制约因素:等静压成形技术可以生产大量的复杂零件,应用领域非常广泛,如航空航天、汽车工业、和机械制造等。
尽管有许多优点,该技术的应用仍存在一些制约因素:1.设备投入产量低,成本高目前等静压成形设备的生产成本较高,相应的设备投入产量也比较低。
2.生产效率低由于等静压成形工艺采用大型冷压机,其生产效率不高,无法追求高速生产的目标。
3.精度有限尽管等静压成形工艺的精度可达到很高,但是压制铸件还是存在一定误差。
4.轻微的变形等静压成形过程使用了大型压力,如果对材料的成形冲击过度,可能会导致轻微的变形或潜在缺陷,从而影响零件性能和寿命。
三、等静压成形工艺的优化研究为了避免等静压成形工艺的缺陷和限制,优化研究是非常必要的。
优化研究主要包括材料性能的提高、加工过程的优化、加工设备的更新和优化等方面。
近年来,由于机器人技术的发展,等静压成形的自动化程度不断提高,不断推动了该技术在机械制造等领域的普及和应用。
等静压成形

等静压成形等静压成形是一种先进的金属加工技术,它通过同时施加压力和温度来将金属粉末转化为具有高密度和精确形状的零件。
这种技术在各个工业领域中具有广泛应用,并在提高生产效率和产品质量方面发挥着重要作用。
等静压成形的基本原理是将金属粉末装入模具中,并在高压环境中施加压力。
同时,通过加热模具,使金属粉末在一定温度下具有一定的可塑性。
在压力和温度的共同作用下,金属粉末颗粒间产生变形,相互贴合,并形成一个致密的零件。
最后,通过冷却和固化过程,最终得到具有高密度和精确形状的零件。
等静压成形技术具有许多优点。
首先,由于金属粉末的一致性和可控性很高,所以可以制造出高精度的零件。
与传统的金属加工相比,等静压成形可以减少或消除后续加工工序,大大提高生产效率。
此外,这种技术还可以在一次成形中实现复杂形状的零件,减少了加工所需的时间和材料成本。
由于等静压成形过程中没有液态金属,因此不会出现表面氧化或污染等质量问题。
在实际应用中,等静压成形广泛用于汽车、航空航天、电子和医疗等行业。
例如,在汽车制造中,等静压成形可以实现发动机零部件、底盘组件和冷却系统的制造。
在航空航天领域,这种技术可以制造高强度的航空结构件和发动机部件。
而在电子和医疗器械领域,等静压成形可以制造高精度、复杂的连接器和导电零件。
要实现优质的等静压成形零件,工艺参数的选择至关重要。
首先,需要根据具体的材料性质和零件要求来确定适当的压力和温度。
压力过低可能导致零件密度不足,而过高的压力则会使零件变形或破裂。
温度过低可能无法使金属粉末达到足够的可塑性,而温度过高可能会引起过度蒸发或无法排除气体。
此外,模具设计和润滑剂的选择也对等静压成形的质量和效果有重要影响。
模具应具有合理的结构和适当的壁厚以确保零件形状的一致性和稳定性。
润滑剂的选择要考虑到对材料的影响以及生产环境的要求,以减少摩擦和磨损。
综上所述,等静压成形作为一种先进的金属加工技术,在提高生产效率和产品质量方面具有重要意义。
QC成果 提高冷等静压成型制品装料效率

小组成员 谭清华
性别 男
冯志源
男
李宗泰
男
李耐辉
男
李超群
男
孙洛峰
男
陆国栋
男
闫小丙
男
杨四江
男
中钢洛耐院
年龄 32
25
29
34 37 34 37 20
46
3年
出勤率
文化程度 职务/职称 硕士 工程师
硕士 助理工程师
本科 助理工程师
高中
班长
高中 高中
组员 组员
专科
组员
初中
组员
高中
组员
99%
小组分工 方案设计、撰写报告
中钢洛耐院
制表人:冯志源 时间:2013年6月25日
七、要因确认
1.培不培训完训制善力度度 不够
造粒料不合格
紧固件设计 不合理
配套工具不适用
5.加料方式 不合理
中钢洛耐院
确认标准:方便快捷、不漏料洒料、制品壁厚均匀
确认方法:现场调查、对比试验
确认人:李超群、陆国栋
确认时间: 2013.6.11∼2013.6.30
中钢集团洛阳耐火材料研究院有限公司
提高冷等静压成型制品装料效率
氧化物第一QC小组
中钢洛耐院
一、小组概况
小组名称
氧化物第一QC小组 成立时间
2013年3月
课题名称
提高冷等静压成型制品装料效率
课题类型
现场型
活动时间
2013.3~2014.2
活动次数
10次
发表人
谭清华
注册编号
LIRR 2013-02
接受QC教育时间
三、选题理由
中钢洛耐院
电真空陶瓷等静压成型模具的改进
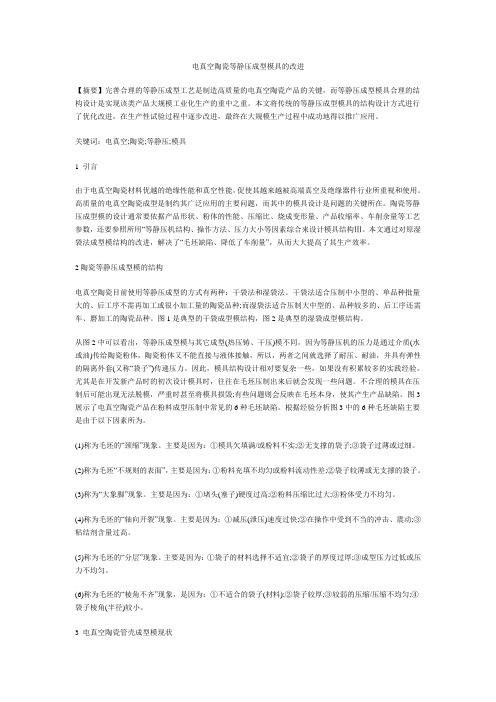
电真空陶瓷等静压成型模具的改进【摘要】完善合理的等静压成型工艺是制造高质量的电真空陶瓷产品的关键,而等静压成型模具合理的结构设计是实现该类产品大规模工业化生产的重中之重。
本文将传统的等静压成型模具的结构设计方式进行了优化改进,在生产性试验过程中逐步改进,最终在大规模生产过程中成功地得以推广应用。
关键词:电真空;陶瓷;等静压;模具1 引言由于电真空陶瓷材料优越的绝缘性能和真空性能,促使其越来越被高端真空及绝缘器件行业所重视和使用。
高质量的电真空陶瓷成型是制约其广泛应用的主要问题,而其中的模具设计是问题的关键所在。
陶瓷等静压成型模的设计通常要依据产品形状、粉体的性能、压缩比、烧成变形量、产品收缩率、车削余量等工艺参数,还要参照所用“等静压机结构、操作方法、压力大小等因素综合来设计模具结构Ⅲ。
本文通过对原湿袋法成型模结构的改进,解决了“毛坯缺陷、降低了车削量”,从而大大提高了其生产效率。
2陶瓷等静压成型模的结构电真空陶瓷目前使用等静压成型的方式有两种:干袋法和湿袋法。
干袋法适合压制中小型的、单品种批量大的、后工序不需再加工或很小加工量的陶瓷品种;而湿袋法适合压制大中型的、品种较多的、后工序还需车、磨加工的陶瓷品种。
图1是典型的干袋成型模结构,图2是典型的湿袋成型模结构。
从图2中可以看出,等静压成型模与其它成型(热压铸、干压)模不同,因为等静压机的压力是通过介质(水或油)传给陶瓷粉体,陶瓷粉体又不能直接与液体接触,所以,两者之间就选择了耐压、耐油,并具有弹性的隔离外套(又称“袋子”)传递压力。
因此,模具结构设计相对要复杂一些,如果没有积累较多的实践经验,尤其是在开发新产品时的初次设计模具时,往往在毛坯压制出来后就会发现一些问题。
不合理的模具在压制后可能出现无法脱模,严重时甚至将模具损毁;有些问题则会反映在毛坯本身,使其产生产品缺陷。
图3展示了电真空陶瓷产品在粉料成型压制中常见的6种毛坯缺陷。
根据经验分析图3中的6种毛坯缺陷主要是由于以下因素所为。
材料成型工艺论文

等静压成型摘要:介绍了等静压成型工艺的工艺原理、工艺特点、发展概况和前景,研究了研究了等静压成形过程中各种质量缺陷产生的原因和危害性,并提出了相应的预防措施,以提高产品的生产效率和产品质量。
关键词:等静压原理特点工艺缺陷预防措施1.简要介绍(1)等静压成型等静压成型是将待压试样置于高压容器中,利用液体介质不可压缩的性质和均匀传递压力的性质从各个方向对试样进行均匀加压,当液体介质通过压力泵注入压力容器时,根据流体力学原理,其压强大小不变且均匀地传递到各个方向。
此时高压容器中的粉料在各个方向上受到的压力是均匀的和大小一致的。
通过上述方法使瘠性粉料成型致密坯体的方法称为等静压法。
起(2)静压成型的过程等静压成型的过程包括1.初期成型压力较小时,粉体颗粒迁移和重堆积阶段。
2.中期压力提高,粉体局部流动和碎化阶段。
3.后期压力最大时,粉体体积压缩,排出气孔,达到致密化阶段。
(3)等静压成型的工艺特点静压成型的特点与等静压成型方法原理近似的是轴向压制成型。
轴向压制成型为单向或双向压力压制,粉料与模具的摩擦力较大,压力沿压制方向会产生压力损失,使坯体各部分的密度不均匀。
而等静压成型时液体介质传递的压力在各个方向上等是相等的。
弹性模具在受到液体介质压力时产生的变形传递到模具中的粉料,粉料与模具壁的摩擦力小,坯体受力均匀,密度分布均一,产品性能有很大提高。
与一般的钢模压制法相比还有下列优点。
1)具有凹形、空心等复杂形状的制件。
2)末提与弹性模具的相对移动很小,所以摩擦消耗也很小,单位压制压力比钢模压制成型时低。
3)属和非金属粉末,压坏密度分布均匀,对难容金属粉末及其化合物尤为有效。
4)密,强度较高,便于加工和运输。
(4)等静压成型的分类将预压好的坯料包封在弹性的塑料或橡胶模具内,密封后放入高压缸内,通过液体传递使坯体受压成型。
2)干式等静压:将弹性模具半固定,不浸泡在液体介质中,而是通过上下活塞密封。
压力泵将液体介质注入到高压缸和加压橡皮之间,通过液体和加压橡皮将压力传递使坯体受压成型。
- 1、下载文档前请自行甄别文档内容的完整性,平台不提供额外的编辑、内容补充、找答案等附加服务。
- 2、"仅部分预览"的文档,不可在线预览部分如存在完整性等问题,可反馈申请退款(可完整预览的文档不适用该条件!)。
- 3、如文档侵犯您的权益,请联系客服反馈,我们会尽快为您处理(人工客服工作时间:9:00-18:30)。
等静压成形工艺的优化研究
作者:薛志岗
来源:《佛山陶瓷》2013年第05期
摘要:本文研究了等静压成形工艺过程中氧化铝造粒粉料成形后的坯体相对密度和强度随着各成形参数的变化而变化的规律,并进一步研究了其对烧结收缩的影响。
实验表明:随着压力的增大,坯体密度逐渐提高,强度也相应增大;保压时间对坯体的相对密度影响不明显;在成形压力范围内,坯体相对密度对烧结之后的试样致密度影响不大。
关键词:等静压成形;相对密度;保压时间;烧结
1 概述
随着陶瓷工业和科学技术的发展,等静压成形工艺已成为陶瓷主要的成形工艺之一。
采用等静压成形工艺具有粉料受压均匀、坯体结构致密、强度高、烧成收缩小、产品不易变形,并且产品的含水率低、无需干燥,可直接入窑等优点。
陶瓷的成形,直接影响到后续的坯体加工质量、烧成制度和烧结后产品本身的结构性能。
随着科技的进步,对真空管壳尺寸的要求也越来越高,尤其是在真空管的成形过程中,由于其内径是一次成形。
烧成收缩的微小变化将会导致真空管壳尺寸的浮动较大,从而使得尺寸超出公差。
所以,一套稳定可控的成形工艺就显得尤为重要。
本实验主要在成形压力的控制上进行了研究,并分析了成形压力和保压时间对烧成收缩的影响,为以后对收缩的控制提供依据,使产品在达到性能要求的同时,提高其尺寸的可控度,从而提高产品的合格率。
同时,选择合理的成形压力以降低压机的损耗,提高工作效率。
2 实验内容
2.1 原料的准备
2.2 试样的制备
将粉料进行等静压成形,考虑到现有的生产状况,成形压力选择为50MPa、60MPa、
70MPa、80MPa、90MPa、100MPa、110MPa、120MPa,保压时间分别选取20s、40s、60s、80s、100s。
将成形的坯体经过车床加工制成形状为中空圆柱状试样,外径φ1为35mm左右,高度70mm左右,并在1710℃的推板窑中烧成。
2.3 成形收缩的测量
2.4 烧成收缩的测量
2.5 烧成试样密度的测量
3 结果与分析
3.1 成形压力对成形和烧成的影响
本文以保压时间为20s的一组数据进行分析。
图2为成形压力与成形收缩的关系图,图3为成形压力与烧成收缩的关系图,图4为坯体密度与压力的关系,图5为压力与烧结试样密度曲线。
由图2可知,随着压力的增大,成形收缩逐渐增大;压力从50MPa增大到120MPa时,横向线收缩率从36.6%增大到38.2%;当压力达到120MPa后继续增大,其收缩变化逐渐趋于平缓。
由图3可知,随着压力的增大,烧成收缩逐渐减小,压力从50MPa增大到120MPa,横向线收缩从16.3%减小到14.9%,收缩变化逐渐趋于平缓。
在50MPa~70MPa之间,成形收缩和烧成收缩变化较大,说明收缩对压力的变化比较敏感;在70MPa~100MPa之间,其收缩比50MPa~70MPa之间的要平缓,此时,坯体的强度也较好;在100MPa~120MPa之间,收缩已趋于水平,随着压力的增大,收缩的变化越来越小,此阶段的坯体强度最好。
由图4可知,从坯体密度的变化趋势也足以说明,当压力达到100MPa~120MPa之间时,坯体密度基本上不再增加[1]。
由图5可知,密度在3.75g/cm3~3.755g/cm3之间时,相对变化很小,且无规律。
说明在烧成时,由于试样摆放位置的差异,导致烧结性能也有差异,从而使其密度有所差异。
原因分析:由图4可知,随着压力的增大,坯体的密度变化较小,在50MPa~120MPa之间时,坯体密度变化仅为0.12g/cm3。
在现有的烧成制度下,较高的烧成温度有足够的驱动力,使试样达到致密化,可忽略坯体密度的微小差异而带来的改变[2]。
3.2 保压时间对成形和烧结的影响
本文选取成形压力为100MPa的一组试样数据为研究对象,其保压时间与烧结收缩的关系如图6所示。
由图6可知,随着压力的增大,烧成收缩的变化小于2‰,且无规律性,可以认为是试验过程中的误差造成的。
主要原因是,在实验过程中,所做的试样均为薄壁试样,因此,保压时间对其作用几乎可以忽略不计。
4 结论
(1)随着成形压力的增大,坯体的相对密度逐渐增大,曲线呈现阶梯性平缓趋势,在100MPa~120MPa处,坯体密度基本不再变。
(2)随着成形压力的增大,试样的烧成收缩逐渐变小,曲线呈现阶梯性平缓趋势,在100MPa~120MPa处,收缩基本不再变化。
(3)在50MPa~120MPa之间,试样烧结后的密度不随压力的增大而增大,说明压力的改变对产品最终的性能影响可以忽略不计。
因此,成形时对压力进行控制是可行的。
(4)对于薄壁产品,保压时间应尽可能短,以减少压机的损耗和能源的浪费。
参考文献
[1] 刘景林.在生产结构陶瓷工艺中冷态等静压成形方法的特点[J].耐火与石灰,2007,32(3):4.
[2] 施剑林.固相烧结-Ⅰ气孔显微结构模型及其热力学稳定性,致密化方程[J].硅酸盐学报,1997,25(5):499.。