19 高效优化粉磨节能技术
水泥粉磨节能降耗措施
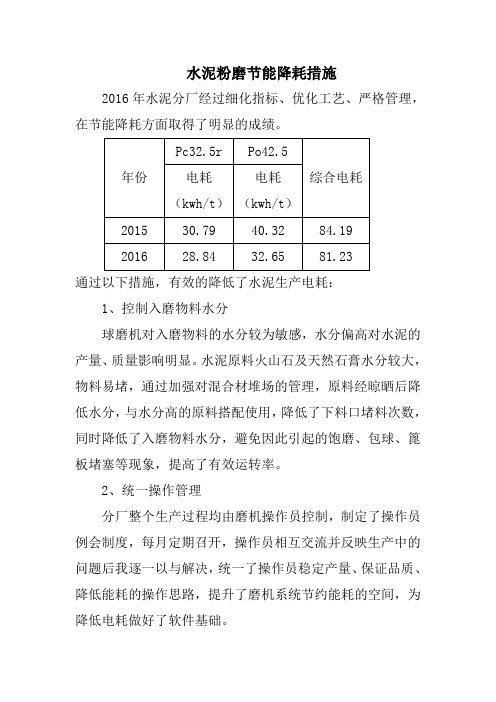
水泥粉磨节能降耗措施2016年水泥分厂经过细化指标、优化工艺、严格管理,在节能降耗方面取得了明显的成绩。
通过以下措施,有效的降低了水泥生产电耗:1、控制入磨物料水分球磨机对入磨物料的水分较为敏感,水分偏高对水泥的产量、质量影响明显。
水泥原料火山石及天然石膏水分较大,物料易堵,通过加强对混合材堆场的管理,原料经晾晒后降低水分,与水分高的原料搭配使用,降低了下料口堵料次数,同时降低了入磨物料水分,避免因此引起的饱磨、包球、篦板堵塞等现象,提高了有效运转率。
2、统一操作管理分厂整个生产过程均由磨机操作员控制,制定了操作员例会制度,每月定期召开,操作员相互交流并反映生产中的问题后我逐一以与解决,统一了操作员稳定产量、保证品质、降低能耗的操作思路,提升了磨机系统节约能耗的空间,为降低电耗做好了软件基础。
3、合理安排生产顺序水泥的生产设备通常都是大功率电机,启动及运行时负荷较大,如开机后不及时投料,水泥电耗将大幅上升。
通过优化巡检程序,缩短开机时间;生产任务量较小时,开一台磨机轮换磨制两个品种水泥,减少设备启停次数及空载时间,进而降低了电耗。
4、提高员工素质为保障生产顺利运行,通过培训、考试提高员工岗位知识,提升员工岗位技能,尽快解决生产中出现的问题,缩短故障时间,确保生产高效、稳定运行。
5、工艺管理2016年对两台磨机的钢球级配进行了调整,使钢球级配及填充率更适用于我厂物料,合理的钢球装载量也有利于降低水泥能耗。
定期检查隔仓板、篦板及选粉机叶片等磨损较大部位,适时修补、更换,提升了系统性能,进一步降低了水泥生产能耗及成本。
6、合理组织设备预维修结合生产供需情况,适时组织对磨机系统、包装系统的预维修工作,提前准备好备件、器材等所需材料,严格验收维修项目,确保开机后系统的运行质量。
每月对磨机故障停机次数及故障原因进行统计分析,采取措施、制定相关奖惩制度,减少故障停机次数,提升了设备运转率,进一步降低了工序电耗。
新型水泥预粉磨系统节能技术

一、技术名称:新型水泥预粉磨系统节能技术二、所属领域及适用范围:建材行业三、与该技术相关的能耗及碳排放现状目前,在国内建材、矿山等行业粉磨生产系统中,仍以球磨机作为研磨物料的主机,球磨机单机生产的能耗极高,达35~40kWh/t,消耗大量电耗。
同时,水泥生产中球磨机粉磨电耗约占水泥企业总用电量的70%,因此粉磨系统的节能改造是水泥企业节能减排的重点环节。
四、技术内容1.技术原理采用高效节能的料床粉磨原理,依靠油缸施加于磨辊的辊动及运行产生的剪切力,对料床中的物料产生高效的碾磨作业,再通过后续的节能低耗自流振动筛进行分级,使进球磨机的粒径控制在2mm以下,进料中0.08mm以下的细粉含量超过20%以上,并对后续球磨机内部衬板、隔仓及分仓长度和研磨体级配进行了优化改进,从而有效降低系统粉磨电耗,达到节能减排的目的。
2.关键技术(1)通过料床粉磨原理,对物料进行辊压和剪切作用,实现高效预粉磨,设备功率消耗少,做功有效作用率大大提高;(2)自流振动筛取代气流选粉设备,通过自身的重力、适量的振动和特殊的防堵结构,具有高效率的筛分功能和流动功能,且箱体不振动,对基础无要求,确保了入球磨机入磨粒度小于2mm;(3)根据物料经过自流振动筛的分级后的特性,优化了球磨机各仓的衬板形状和隔仓结构形式,并采用二仓结构并配合合理的研磨体级配,提高研磨效率,改善水泥颗粒分布,提高水泥比表面积,大大提高水泥产量,降低粉磨电耗。
3.工艺流程粉磨物料经过计量称计量配料后的混合料,通过斗提机进入预粉磨内进行粉磨作业,粉磨后的细物料进入自流振动筛实现分级,分级后大于2mm的粗物料通过斗提机返回预粉磨重新粉磨,分级后小于2mm的细物料进入球磨机研磨作业。
进入球磨机的物料经球磨机研磨后,达到成品要求后出磨,成品通过输送设备输入后面的成品库中。
具体设备结构图见图1,工艺流程图见图2。
图1 预粉磨结构图图2预粉磨技术工艺流程图五、主要技术指标(1)入球磨机物料粒度控制≤2mm,小于0.08mm细粉含量大于20%;(2)水泥粉磨系统电耗小于28kWh/t,吨成品粉磨电耗下降30%以上;(3)粉尘排放浓度小于30mg/Nm3。
现代水泥工业中高效节能的粉磨技术

●
Z H A O J i h ui , W A N G D o n g mi n , WA N G X ue g u a n g
( S c h o o l o f C h e m i c a 1 a n d E n v i r o n m e n t a 1 E n g i n e e r i n g ,C h i n a U n i v e r s i t y
浅论水泥粉磨站节能降耗的措施

浅论水泥粉磨站节能降耗的措施摘要:文章是针对水泥粉磨站节能降耗措施的探讨。
水泥粉磨的电耗在整个水泥生产过程中占据着相当大的比重,因此它是水泥生产中节能减排的重要环节。
粉磨站的节能降耗,要从改善传统的粉磨工艺和提高粉磨的效率抓起,同时也需要合理地安排生产工序,加强企业内部的管理和对节能减排的认识,从而实现产量、质量以及降耗三方面的共同提高。
关键词:水泥生产;粉磨站;节能降耗引言水泥的生产通常可以分为生料制备、熟料煅烧和水泥制成三个主要环节,而水泥粉磨站是从最后环节水泥制成阶段独立出来的一个成品制作单位。
在水泥生产中,企业往往在矿区附近建立水泥熟料生产线,而在靠近水泥销售的建筑市场周边建立水泥粉磨站,从而减少运输中的成本。
如果将熟料生产环节也建立在城市附近的话,根据每生产1吨熟料需要1.6吨的生料来计算,要增加60%的运输成本。
而如果将水泥粉磨站和熟料生产线一同建在矿区的话,则需要从城里运输生产材料到矿区,磨成水泥之后再运输到城市,同样增加了运输成本。
1目前我国数量最多的中小型水泥厂普遍采用的是球磨机一级圈流工艺来进行水泥粉磨,无论是球磨机还是选粉机,都存在着耗能高、产能低、产品质量差的弊端。
尽管一些水泥厂近年来都使用了新型的干法熟料工艺,但在粉磨的主机设备、系统工艺方面仍存在一些问题,如:(1)磨机的内部结构不合理,设置的单层隔仓板并没能有效地筛分物料,水泥颗粒分布范围也较宽,粉磨的工作效率低。
(2)有的物料的粒度大,但是磨机的长径比小,耐磨性不好,最终的直接后果就是需要耗费大量的时间来研磨物料,工作效率低下。
(3)选粉机工作效率低,不能筛选粒径在3~32μm之间的微粉[1]。
随着我国经济建设的不断发展,水泥的运用越来越广泛,任何类型的建筑工程中都离不开水泥。
而水泥的能耗又非常大,在能源紧缺的情况下,节约水泥的能耗,提高生产效率,减少生产中的浪费现象,无疑将会是未来水泥生产的重点方向。
2 水泥粉磨站节能降耗措施2.1 优化磨机的内部结构,设置具有选粉功能的高效强制筛分系统根据磨机存在的问题分析,我们发现,要想大幅度提高磨机的工作效率,最关键的就是要调整磨机的内部结构,改善其内部构造。
磨粉机的能耗和效率优化方法

磨粉机的能耗和效率优化方法磨粉机作为一种常用的工业设备,广泛应用于矿山、冶金、建材、化工等多个领域。
它的主要功能是将原料破碎、细磨成粉末状,以满足不同产品的制备需求。
然而,磨粉机的能耗问题一直是制约其发展和应用的重要因素之一。
如何有效地降低磨粉机的能耗,提高生产效率,成为了当前磨粉机研究的热点之一。
本文将介绍一些常见的磨粉机能耗和效率优化方法,以期为磨粉机的使用和改进提供一些有益的参考。
一、设备选型优化在磨粉机的能耗和效率优化过程中,合理的设备选型是至关重要的一步。
首先要根据生产工艺的要求确定所需磨粉机的型号和规格。
根据原料的性质、加工对象的颗粒度要求以及生产能力等多方面因素,选择适合的磨粉机设备。
同时,应考虑磨粉机的结构设计和制造工艺,选购具备高效、节能、耐磨、易维修等特点的设备。
通过合理的设备选型,可以明显降低磨粉机的能耗,提高其工作效率。
二、工艺优化改进工艺优化改进是磨粉机能耗和效率优化的关键环节。
在磨粉机的工作原理中,磨料和磨体的配比、磨料粒度的控制、磨机内部介质的优化等都会直接影响到磨粉机的能耗和效率。
因此,通过对磨粉机工艺流程的优化改进,可以实现能耗的降低和生产效率的提高。
其中,优化磨粉机的进料方式是一种常见的工艺改进方式。
传统的磨粉机多采用料罐、螺旋输送机等方式进行进料,但这种方式易造成物料的堆积和堵塞,降低了磨矿机的工作效率。
采用自动配料系统和定时进料系统,可以精确控制物料的进料量和进料时间,避免了物料的过量或不足,提高了磨粉机的工作效率。
此外,优化磨料和磨体的配比也是关键的工艺改进措施之一。
磨料和磨体的配比直接影响到磨粉机的研磨效果和能耗。
合理的配比可以提高磨粉机的工作效率,减少不必要的能量损耗。
因此,根据不同的生产工艺和产品要求,合理设置磨料和磨体的比例,是降低能耗、提高效率的重要手段之一。
三、优化设备运行管理除了设备选型和工艺改进,优化设备的运行管理也是降低磨粉机能耗和提高效率的重要方法之一。
浅述水泥粉磨系统节能降耗措施

浅述水泥粉磨系统节能降耗措施摘要:在水泥生产过程中,水泥粉磨是其中的一个重要环节,它是水泥生产中的最后一个环节,水泥粉磨质量的好坏,直接影响成品水泥质量的好坏及产量的高低;同时水泥粉磨环节又是电能消耗最多的环节,其电耗高高低直接影响着水泥生产的成本。
因此水泥粉磨环节效率的高低直接影响着企业效益的好坏。
本文在简要介绍不同粉磨系统优缺点的基拙上,提出了水泥粉磨系统节能降耗的措施。
关键词:水泥粉磨;节能;降耗随着经济的发展,能源供应紧张情况,环境污染压力不断加剧,这就对水泥生产提出了更高的要求。
水泥工业是我国工业领域中的能耗大户。
水泥行业能源消耗总量约占全国能源消耗总量的5%,是影响中国节能减排的重要行业之一。
水泥粉磨是水泥生产中最重要的环节,在水泥生产过程中,粉磨电耗约占水泥生产总电耗的65%-75% ,粉磨成本占生产总成本的35%左右。
因此,采取科学的方法降低粉磨系统能耗,提高粉磨效率,对水泥生产企业的降低成本,提高效益而言至关重要。
1、不同粉磨技术及设备能耗比较水泥粉磨是把电能转换成机械能,再把机械能转换成物料的表面能的过程。
当前粉磨水泥的形式有球磨机系统、辊压机预粉磨系统和辊磨(立磨)系统。
1.1球磨机系统。
水泥粉磨采用球磨机已有上百年历史,至今球磨机仍是水泥粉磨的主流设备,球磨机最大的特点就是研磨效率高,能把物料加工到350-450m2/kg比表面积,以满足高性能水泥的要求。
此系统主要有:球磨机+选粉机+收尘器+风机等组成圈流系统;球磨机+收尘器+风机等组成开流系统。
此系统工艺简单、运行效率高、混合均匀、颗粒形貌好,土建量较低,占地面积较小,投资相对较少。
缺点是电耗高,产量低等。
1.1辊压机预粉磨系统。
辊压机与球磨机组成的各种预粉磨系统(包括循环预粉磨、联合粉磨、半终粉磨等)已经成为水泥粉磨的主要方案,这是由于辊压机的粉磨效率约为球磨机的2倍左右,可以大幅度节电。
此系统电耗低,出磨水泥的温度较低,水泥强度均匀性比较好。
水泥粉磨系统节能优化技术改造探讨
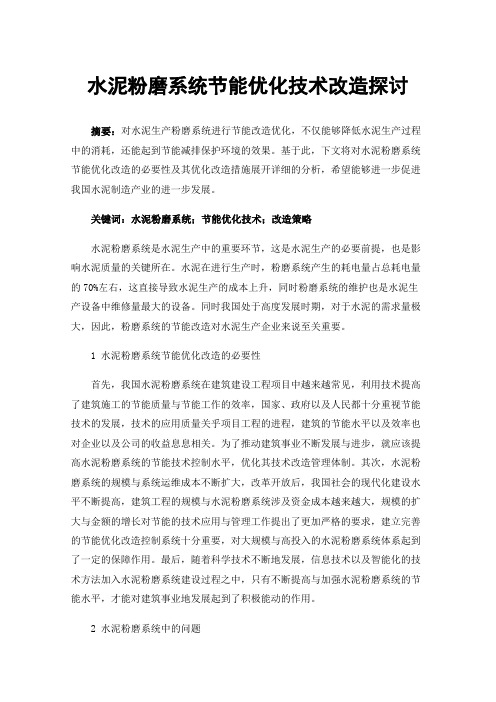
水泥粉磨系统节能优化技术改造探讨摘要:对水泥生产粉磨系统进行节能改造优化,不仅能够降低水泥生产过程中的消耗,还能起到节能减排保护环境的效果。
基于此,下文将对水泥粉磨系统节能优化改造的必要性及其优化改造措施展开详细的分析,希望能够进一步促进我国水泥制造产业的进一步发展。
关键词:水泥粉磨系统;节能优化技术;改造策略水泥粉磨系统是水泥生产中的重要环节,这是水泥生产的必要前提,也是影响水泥质量的关键所在。
水泥在进行生产时,粉磨系统产生的耗电量占总耗电量的70%左右,这直接导致水泥生产的成本上升,同时粉磨系统的维护也是水泥生产设备中维修量最大的设备。
同时我国处于高度发展时期,对于水泥的需求量极大,因此,粉磨系统的节能改造对水泥生产企业来说至关重要。
1 水泥粉磨系统节能优化改造的必要性首先,我国水泥粉磨系统在建筑建设工程项目中越来越常见,利用技术提高了建筑施工的节能质量与节能工作的效率,国家、政府以及人民都十分重视节能技术的发展,技术的应用质量关乎项目工程的进程,建筑的节能水平以及效率也对企业以及公司的收益息息相关。
为了推动建筑事业不断发展与进步,就应该提高水泥粉磨系统的节能技术控制水平,优化其技术改造管理体制。
其次,水泥粉磨系统的规模与系统运维成本不断扩大,改革开放后,我国社会的现代化建设水平不断提高,建筑工程的规模与水泥粉磨系统涉及资金成本越来越大,规模的扩大与金额的增长对节能的技术应用与管理工作提出了更加严格的要求,建立完善的节能优化改造控制系统十分重要,对大规模与高投入的水泥粉磨系统体系起到了一定的保障作用。
最后,随着科学技术不断地发展,信息技术以及智能化的技术方法加入水泥粉磨系统建设过程之中,只有不断提高与加强水泥粉磨系统的节能水平,才能对建筑事业地发展起到了积极能动的作用。
2 水泥粉磨系统中的问题2.1 设备小但是耗能高我国的水泥生产中使用的粉磨系统,其中小型粉磨机占的比例较大,因此水泥生产企业为了满足水泥生产需求,会大量购买相关的粉磨机,但是在实际的生产过程中粉磨机进行的产量远远低于设计产量,这直接造成了能源消耗的上升。
水泥联合粉磨系统的节能技术

水泥联合粉磨系统的节能技术摘要:在水泥生产过程中,粉磨消耗的电力约为65%。
提高水泥厂的工作效率,降低能耗,是目前各大水泥厂节能减排的首要目的。
本文对水泥联合粉磨系统的节能优越性进行了深入的剖析,采用了陶瓷磨料工艺代替了系统中的钢珠,并利用勃氏透气仪和负压筛法对其进行了相应的检测。
经实践证明,采用陶瓷磨料代替钢珠和降低磨机钢珠的加载量都能降低工艺能耗。
此外,在新建水泥生产线中,选择轧机和碾磨机时,应选用轧机与磨机的功率比为0.7。
关键词:水泥;粉磨系统;节能技术引言在水泥生产中,粉磨是其中的一个重要环节,它的能耗是最大的,占到了整个水泥生产的65%。
因此,提高水泥厂的工作效率,降低电力消耗,是水泥厂节能的关键。
陶瓷球密度低,质量轻,强度高,密度仅为钢珠的二分之一。
在同样的填充率下,磨机负载明显减小,从而降低了磨机的工作电流,从而降低了功率消耗。
这表明,在同样的充填速率下,采用陶瓷材料可以有效地节约电能,而降低负载也能达到同样的效果。
下面,对 TL公司生产的钢球进行了更换,并对其节能措施进行了分析,并对其与轧机的配合进行了探讨。
1实验方法公司采用水泥磨主机功率为3550kW和2×1200 kW的辊压机和2台高铬钢球。
通过对一条生产线上的钢珠更换为陶瓷磨料,对2条生产线上的钢球加料进行了试验和分析。
一条生产线的具体改装是:一仓的隔仓板向后移动1.25米,长度为3.75米,并对一仓的钢球进行了调整;把二号仓的有效长度减至8.75米,用陶瓷球代替钢珠。
二条生产线一、二仓的有效长度为2.5米,而二仓为10米,而钢珠的装载则从220吨降至177吨。
2改造实际效果一条生产线以 P. O42.5等级的水泥为主,用陶瓷磨料代替钢珠,连续生产约6个月。
2.1水泥的生产品质用陶瓷磨料代替后,其各项性能指标没有明显的改变,强度满足有关规范要求。
水泥的表面积和筛余量没有明显的改变,稠度的需水量变化都在正常范围之内,满足规范的要求;水泥的3天、28天的强度达到了规范的要求。
建材行业水泥粉磨节能技术改造案例-高压力料床粉碎技术-2019年节能技术应用案例

高压力料床粉碎技术
技术适用范围
适用于建材行业水泥粉磨领域。
技术原理及工艺
开发成套稳定料床的设备和装置(组合式分级机、“骑辊式”进料装置等)来解决入料中细粉含量较多时辊压机料床稳定性的问题,以增加辊压机的工作压力,从而提高其粉磨效率;同时通过对设备和系统的在线监测以及智能化控制保障设备和系统按照既定方式运行,实现水泥粉磨的高效率、低能耗、高品质的智能化生产。
工艺装备如下图:
技术指标
(1)粉磨单产电耗降低2 kW·h /t;
(2)水泥台产增加率10~20%;
(3)熟料用量减少0.5~1%。
技术功能特性
(1)先筛选后风选的高压力粉磨系统及其配套的组合式分级机、骑辊式进料装置,保证通过的物料都受到充分挤压,降低了系统能耗,同时也解决了边缘漏料和辊子端面磨损问题;
(2)辊压机粉磨智能控制系统实现生产过程无人智能优化控制,稳定产品质量,成品水泥质量波动幅值减小80% 以上。
应用案例
合肥东华建材水泥粉磨生产线“二代水泥”技术改造项目。
技术提供单位为合肥水泥研究设计院有限公司与中建材(合肥)粉体科技装备有限公司。
(1)用户用能情况简单说明
合肥东华建材集团股份有限公司两条120 万吨水泥粉磨生产线,技术改造前水泥粉磨台产为179.6 t/h,粉磨单产电耗为26.38 kW·h /t。
水泥粉磨节能降耗的技术措施

K e r s cme tgidn ; e eg o sraina dc nu t n rd cin; tc nc lmpo e n ; gidn i y wo d : e n r ig n rycn ev t n o smpi e u t n o o o eh ia rv me t i r igad n
占生产总成本 的 3 %左 右 , 磨 系统 维 修量 占全 厂 5 粉
设备 维修量 的 6 %, 此 , 磨 对 水 泥 生产 企 业 的 0 因 粉
效益 影响极大 。因此 大力 降低水 泥粉磨 过程 中的过
高能耗 , 我 国节 能减 排 具 有 重 要 意 义 。该 文从 3 对 个方面介 绍 水 泥 粉磨 中节 能 降 耗 的 重 要 的 技 术 措
i a o t6 % ~ 7 % .s th sv r o tn in f a c o r d c h o rc n u t n o e n r dn u o n s b u 5 5 o i a eyi mp ra t g ii n et e u et ep we o s mp i fc me t i i g i o rc u ・ s c o g n n ty n t i a e ,t e e a e i o tn e h i l a u e n s u h a h r p r g i d n e h i u ,s i t i i r v — r .I h sp p r h r r mp ra tt c n c a me s r me t ,s c st e p o e rn i g tc n q e ce i c mp o e n f me to rn n y t m ,a pia in o r dn i o r l e t eg a f n r y c n e v t n a d c n u t n r d c in n f i d g s se g i p l t f i i g ad t e i h o lo eg o s r a i n o mp i e u t . c o g n a z e o s o o
水泥粉磨节能降耗的技术措施

刘文增.采用分别粉磨工艺生产水泥的实践[J].水泥工程,2008(2):36-37.
梁尚杰.采用粉磨工艺降低矿渣水泥的生产成本[J].水泥工程,2006(6):35-37.
陈峭卉,杨军,陈应钦.新型水泥助磨剂的作用及机理研究[J].新型建筑材料,2006(6):47-49.
江朝华,蔡安兰,严生.高性能水泥助磨剂的研究[J].硅酸盐学报,2001(6):507-511.
4 结语
水泥粉磨电耗占水泥生产过程总电耗相当大的比重,是水泥生产节能减排中的一个重要环节。要求企业和科研人员重点研究开发和推广新的粉磨系统及技术,通过提高粉磨效率和合理使用助磨剂是水泥粉磨过程实现能耗降低的有效途径。
参考文献
马秋忠.2009年重点联系水泥企业生产运行回顾[J].中国建材,2010,(2):82-83.
国外公司推出的衬板有逐渐统一的趋势。一仓一般采用提升衬板即所谓的阶梯衬板,二仓则采用分级衬板。但这种分级衬板不是国内常见的锥形分级衬板或平衬板加锥形分级衬板,而是2种甚至3种衬板的组合或复合体。经过优化组合或复合,一种衬板可发挥不同形式衬板的优势,从而保证了最大限度地将能量输人装球区,并尽量消除磨内死区。
1979年日本小野田公司开发了O-Sepa选粉机,它不仅保留了旋风选粉机外循环的优点,而且采用笼型转子平面螺旋气流选粉原理,从而大幅度提高了选粉效率。以它为代表的笼式选粉机称之为高
效涡流选粉机,也被称为继离心式选粉机、旋风式选粉机之后的第三代选粉机。它的选粉效率一般在80%以上,与离心式或旋风式的选粉机相比,涡流式高效选粉机可提高磨机产量15%-40%,节电10%-20%,体积小、重量轻、布置灵活,产品可在300600澎/kg的比表面积内任意调节,系统负压操作,无粉尘污染。
水泥粉磨站节能降耗措施
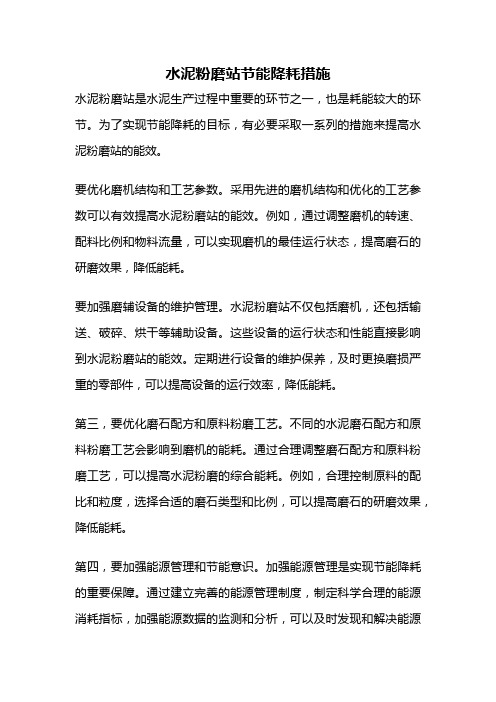
水泥粉磨站节能降耗措施水泥粉磨站是水泥生产过程中重要的环节之一,也是耗能较大的环节。
为了实现节能降耗的目标,有必要采取一系列的措施来提高水泥粉磨站的能效。
要优化磨机结构和工艺参数。
采用先进的磨机结构和优化的工艺参数可以有效提高水泥粉磨站的能效。
例如,通过调整磨机的转速、配料比例和物料流量,可以实现磨机的最佳运行状态,提高磨石的研磨效果,降低能耗。
要加强磨辅设备的维护管理。
水泥粉磨站不仅包括磨机,还包括输送、破碎、烘干等辅助设备。
这些设备的运行状态和性能直接影响到水泥粉磨站的能效。
定期进行设备的维护保养,及时更换磨损严重的零部件,可以提高设备的运行效率,降低能耗。
第三,要优化磨石配方和原料粉磨工艺。
不同的水泥磨石配方和原料粉磨工艺会影响到磨机的能耗。
通过合理调整磨石配方和原料粉磨工艺,可以提高水泥粉磨的综合能耗。
例如,合理控制原料的配比和粒度,选择合适的磨石类型和比例,可以提高磨石的研磨效果,降低能耗。
第四,要加强能源管理和节能意识。
加强能源管理是实现节能降耗的重要保障。
通过建立完善的能源管理制度,制定科学合理的能源消耗指标,加强能源数据的监测和分析,可以及时发现和解决能源浪费的问题,提高能源利用效率。
同时,要加强员工的节能意识培训,提高员工的节能意识,形成全员参与、共同节能的良好氛围。
第五,要加强技术创新和研发投入。
技术创新是实现节能降耗的根本途径。
通过加大研发投入,推动技术创新,引进先进的水泥磨石设备和工艺,可以有效提高水泥粉磨站的能效。
例如,引进高效节能的水泥磨石设备,采用先进的自动控制技术,可以降低能耗,提高生产效率。
水泥粉磨站节能降耗是一个系统工程,需要从磨机结构和工艺参数优化、磨辅设备维护管理、磨石配方和原料粉磨工艺优化、能源管理和节能意识加强、技术创新和研发投入等多个方面入手。
只有全面采取措施,才能实现水泥粉磨站的节能降耗目标,提高水泥生产的能效。
粉磨系统优化节能技术

粉磨系统优化节能技术1.我国水泥行业能耗现状水泥行业是一个高能耗工业。
在水泥生产中,破碎后的原料不仅要按一定的配比进行使用,而且必须将其粉磨到一定的细度,才能混合均匀,成为合格生料,并使煅烧过程中的物理化学反应得以顺利进行;水泥产品只有粉磨到一定的细度,才能在建筑施工使用中,发挥应有的强度和作用。
目前实现水泥行业粉磨物料的主要设备依然是球磨机。
球磨机1876年问世,1891年能够连续生产的球磨机投入工业中使用。
球磨机的筒体由钢板卷制而成,两端装有带空心轴的轴承座,一端进料一端出料,可以连续生产。
水平安装的筒体内装有不同形式的衬板和不同规格的研磨体,研磨体以钢球为最多;传动装置带动筒体旋转时,研磨体将物料磨成细粉,因此得名为:球磨机。
如果研磨体中有钢棒,则又称其为:棒磨机水泥行业内,不论这类粉磨设备研磨体的种类如何,都习惯地将“球磨机”作为它们的统称。
水泥行业每生产一吨水泥,需要粉磨各种物料三吨左右,粉磨电耗占水泥生产综合电耗的72%。
据有关部门统计的数据:我国2007年吨水泥平均耗电93.75kwh/t。
部分技术落后企业,吨水泥电耗甚至高达115kwh/t。
其中用于粉磨生料和粉磨水泥所用的电耗,约在67.5Kwh/t水泥(42.5级)。
2007年我国生产水泥13.6亿吨,平均按97.5kwh/吨水泥耗电计算,水泥行业年消耗约1326亿度电。
用于粉磨系统的电量约为1000亿度电。
虽然球磨机能量利用率很低仅有3%左右。
但球磨机的耐用性还是水泥行业的钟爱,我们看到一个企业有三台2.4*11M球磨机已经运行近50年,磨机本体,减速机,电机都很完好,还在发挥巨大的作用。
近年来有人倡导“无球磨机”水泥生产工艺,利用立磨以及挤压机终粉磨替代能耗高的球磨机工艺实现水泥生产过程的节能对于新建工艺生产线是可行的。
然而,我国水泥行业据不完全统计目前运行的球磨机多达两万多台!已经运行系统全部用立磨和挤压机终粉磨工艺来替代几乎在短期内是不可能的。
粉磨系统节能改造方案(一)

粉磨系统节能改造方案一、实施背景在产业结构改革的大背景下,节能减排已成为各行各业关注的焦点。
粉磨系统作为工业生产中的重要环节,其能耗占据了整个生产过程的很大比例。
因此,对粉磨系统进行节能改造,对于降低工业能耗、提高资源利用率、促进产业可持续发展具有重要意义。
二、工作原理粉磨系统的主要功能是将原料破碎并研磨成所需的细度,以供后续生产工艺使用。
改造前的粉磨系统通常采用球磨机进行研磨,这种研磨方式能耗较高,研磨效率较低。
本次节能改造方案采用立式辊磨机替代传统的球磨机,以提高研磨效率和降低能耗。
立式辊磨机的工作原理是:原料通过给料装置进入磨机,在磨机内部的研磨辊和研磨盘之间受到挤压和研磨作用,从而被破碎和研磨。
由于研磨辊和研磨盘之间的间隙可以调整,因此可以对原料进行精细研磨。
同时,立式辊磨机采用热风循环系统进行烘干,进一步降低能耗。
三、实施计划步骤1. 对现有粉磨系统进行评估,确定改造的可行性和必要性。
2. 设计立式辊磨机的规格和型号,确定各项技术参数。
3. 购置立式辊磨机及其配套设备,并进行安装和调试。
4. 对操作人员进行培训,确保他们掌握新设备的操作和维护技能。
5. 进行试运行,对改造效果进行评估,并根据评估结果进行调整和优化。
6. 正式投入运行,持续监控运行状况,确保设备稳定运行并达到预期的节能效果。
四、适用范围本节能改造方案适用于各类工业生产中的粉磨系统,尤其是高能耗的传统球磨机系统。
无论是冶金、建材、化工还是矿山等行业,只要涉及到原料的破碎和研磨工艺,都可以采用本方案进行节能改造。
五、创新要点1. 采用立式辊磨机替代传统的球磨机,提高研磨效率,降低能耗。
2. 引入热风循环系统,对原料进行烘干处理,进一步降低能耗。
3. 对原料进行精细研磨,提高原料的利用率和产品质量。
4. 优化整个粉磨系统的工艺流程,使生产更加高效、环保。
六、预期效果1. 节能效果:相比传统球磨机系统,立式辊磨机系统的能耗可降低30%-50%。
粉磨系统节能优化的措施及策略

粉磨系统节能优化的措施及策略在水泥生产中,近65%的电能消耗被原料和水泥的粉磨所占用,如何降低粉磨系统的电耗,已成为水泥生产节能降耗需要关注的重点环节。
利用先进技术,优化系统工艺、研发粉磨设备,降低粉磨电耗的各种措施,开始在水泥生产企业陆续采用。
1 生料粉磨系统1.1 生料粉磨采用的主要方式各企业生料粉磨采用的方式主要有两类:辊压机与磨机组成的各类粉磨系统,辊式磨粉磨系统。
目前都广泛应用在生料粉磨系统中。
(1)生料辊压机与磨机组成的各类粉磨系统工艺处理方式:利用辊压机进行预粉磨,辊压机与磨机系统进行联合粉磨,利用辊压机系统进行半终粉磨。
虽然各系统因工艺处理方式不同节能效果存在差异,但比未进行预粉磨处理的生料粉磨系统,电耗有了大幅度降低。
采用生料辊压机与磨机组成的粉磨系统,目前电耗一般在20~22kWh/t。
(2)生料辊式磨粉磨系统。
目前各大型水泥企业已广泛采用。
采用生料立磨粉磨系统,节能效果优于辊压机与磨机组成的粉磨系统,特别是大型立磨国产化以后,价格优势突显,已逐步取代进口设备,使用国产设备的企业逐渐增多。
采用生料辊式磨粉磨的终粉磨系统,粉磨电耗一般已达到17~19kWh/t 水平。
1.2 辊压机生料终粉磨系统目前有的企业已开始使用取消磨机,采用辊压机进行终粉磨的生料粉磨系统。
某厂采用G160-140 辊压机的生料终粉磨系统工艺布置见图1、系统设备配置见表1。
系统流程:物料由皮带机喂入V 型选粉机,与出辊压机的物料混合,经V 型选粉机进行首次选粉,细粉被带入动态转子式选粉机再进行二次选粉,通过两级分选后的细粉已满足细度要求,经旋风分离器收集后入库。
选出的粗料:首次选粉的通过提升机,二次选粉的直接接入辊压机的中间仓,经辊压机挤压后由提升机喂入V 型选粉机继续进行选粉。
窑尾废气是V 型选粉机的热风源,循环风机的循环风和V 型选粉机的冷风伐,用于调节入V 型选粉机的气体温度。
调节动态选粉机的转子转速、循环风机的排风和循环风量,可调整产品细度。
论水泥厂粉磨技术节能降耗措施

论水泥厂粉磨技术节能降耗措施发布时间:2021-06-24T13:42:56.200Z 来源:《建筑实践》2021年2月第6期作者:何立岷[导读] 在分析粉磨站工艺设备现状以及影响节能发展的因素基础上何立岷克州天山水泥有限责任公司?摘要:在分析粉磨站工艺设备现状以及影响节能发展的因素基础上,结合自身的水泥厂节能改造经验,多角度分析了现有粉磨技术的改造措施,最后论述了在此过程中如何优选耐磨材料,希望对于今后水泥厂粉磨技术节能化发展有所帮助。
关键词:水泥厂,粉磨系统,节能改造,降耗措施随着我国工业化进程的快速发展,水泥工业则是工业领域中能耗大户,而粉磨环节则是水泥生产中的总电耗的70%左右,其成本则是总成本的35%左右。
从这个角度来看,在推动水泥厂的节能改造发展的过程中,则应充分重视如何对于粉磨站的节能降耗等方面的工作,这样方可全面提升水泥企业的核心竞争力。
1 粉磨站工艺设备1.1 影响新型干法粉磨系统效能的设备当前,针对水泥厂中所采用的新型干法粉磨系统来说,系统效率主要受到熟料温度及细度、研磨体级配、粉磨工艺以及磨机通风等相关因素的影响,从这个角度来分析了如下的工艺设备情况。
(1)辊压机。
其和磨机构成了相应的预粉磨系统,能充分利用好机械自动化的优势,有效提升效率,降低成本,已经在诸多的水泥粉磨站中应用。
其中,采用辊压机系统系统后,能有效降低电耗25%左右,结合辊压机消耗功率的情况,能有效实现预期的节电要求。
(2)选粉机。
在水泥厂的应用环节,主要涉及到的选粉机有离心式选粉机、三分离选粉机以及旋风选粉机等,后结合实际的需求情况还涉及到相应的改造设备,能有效保障相应的产量要求。
这里主要采用高效选粉机的圈流球磨工艺,能实现水泥产品的温度以及细度的合理化控制,有效提升粉磨效率,具有良好的成品比较细的优势。
(3)磨机水泥磨机则是在系统工艺中最为重要的设备,主要涉及到如下两种设备。
一是,立式水泥磨。
这种类型设备在国外水泥工业中有着较为广泛的应用,德国、丹麦、日本等国家已经研发相应的立磨设备,并在应用实践中得到很好的应用效果。
水泥粉磨过程优化节能控制系统概述
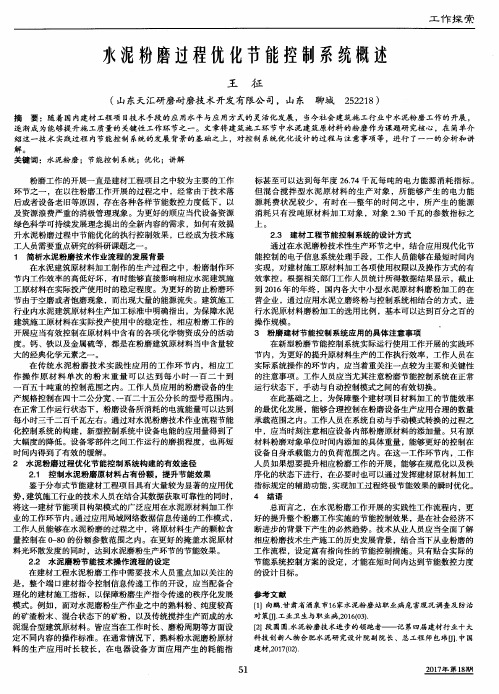
标甚 至可以达到 每年度 2 6 . 7 4千瓦每 吨的 电力 能源消耗 指标 。 但 混合 搅拌 型水泥 原材料 的生 产对象 ,所能 够产生 的 电力 能 源 耗费 状况 较少 ,有时在 一整年 的 时间之 中 ,所产 生 的能源 消 耗只有 没吨原 材料加工对 象 ,对象 2 . 3 0千 瓦的参数指标 之
4 结 语
势, 建筑施工行业 的技术人员在结合其数据获取可靠性 的同时 , 将 这一建材节能项 目构架模式 的广泛应用在水 泥原 材料 加工作 业 的工作环节 内。 通过应用局域 网络数据信息传递 的工作模式 , 工作人 员能够在水泥粉磨 的过程之 中 ,将原材料生 产的颗粒含 量 控制在 0 — 8 0的份额参数 范围之 内。在更 好 的掩 盖水泥原 材 料 光环 散发度的同时 ,达到水泥磨 粉生产环节的节能效果。 2 . 2 水泥磨 粉节能技术操作流程的设定 在建材工程水泥粉磨 工作 中需要技术人员重点加 以关 注的 是 ,整个 端 口建材指令控制信息传递工作 的开设 ,应 当配备 合 理化 的建材 施工指标 ,以保障粉磨生产指令传递 的秩序化 发展 模式 。例如 ,面对水 泥磨粉生产作业之 中的熟料粉 、纯度较 高 的矿渣粉末 、混合状态下的矿粉 ,以及传统搅拌生产而成 的水 泥混合 型建 筑原 材料。皆应当在工作时长 、磨粉周期等方 面设 定不 同内容 的操作标 准。在通常情况下 ,熟料粉水泥磨粉原材
一
通过在水泥磨粉技术性生产环 节之 中 ,结合应用 现代 化节 能控制 的电子信 息系统处 理手段 ,工作 人员能够在最短时间内 实现 ,对建材施 工原 材料 加工各项 使用 权限以及 操作 方式的有 效掌控 。根据相关部 门工作人 员统计所 得数 据结果显示 ,截止 到2 0 1 6年 的年终 ,国 内各 大中小型水 泥原材料磨 粉加工 的在 营企业 ,通过应用水 泥立磨终 粉与控制 系统 相结合 的方式 ,进 行水泥原材料磨粉加 工的选用 比例 ,基本 可以达到百 分之百的 操作规模 。 3 粉磨建材节能控制 系统应用的具体注意事项 在新 型粉磨节能控制系统实际运行使用工作开展 的实践环 节 内,为更好 的提升原材料生产 的工作执行效率 ,工作人员在 实际系统操作 的环节 内 ,应 当着重关注一点较为 主要 和关键性 的注意事项 。工作人员应 当尤其注意粉磨节 能控制系统在正 常 运行状态下 ,手动与 自动控制模式之间的有效切换 。 在此基础 之上 ,为保障整个建材项 目材料加工 的节能效率 的最优化发展 ,能够合理控制在粉磨设备生产应用合理 的数量 承载范 围之 内。工作人员在系统 自动与手动模式转换 的过程之 中 ,应当时刻注意相应设备 内部粉磨原材料 的添加量 。只有原 材料粉磨对象单位时 间内添加 的具体重量 ,能够更好 的控制在 设备 自身承载能力的负荷范 围之 内。在这一工作环节 内,工作 人员如果想要提升相应粉磨工作 的开展 ,能够在规范化 以及秩 序化的状态下进行 ,在必要时也可 以通过发挥建材原材料加工 指标 规定的辅助功能 , 实现加工过程终极节能效果的瞬时优化 。
19 高效优化粉磨节能技术

19 高效优化粉磨节能技术一、技术名称:高效优化粉磨节能技术二、适用范围:建材、矿山等行业 粉磨生产系统三、与该节能技术相关生产环节的能耗现状目前,我国建材、矿山、发电等行业粉磨生产系统仍以球磨机作为粉磨主机为主,物料的粉碎和研磨均在球磨机内完成。
粉磨生产系统电耗一直较高,球磨机的电能有效利用率只有1%-5%左右,效率非常低。
建材行业水泥生产是粉磨应用较普遍的领域,以水泥企业为例,其粉磨电耗约占水泥企业总电耗的2/3,球磨机系统吨水泥粉磨电耗(未加预粉磨系统)约35~42kWh/t,采用增加预粉碎系统后,吨水泥粉磨电耗可达到30kWh/t以下,节能效果显著。
四、技术内容1.技术原理采用高效冲击、挤压、碾压粉碎原理,配合适当的分级设备,使入磨物料粒度控制在3mm以下,并优化球磨机内部构造和研磨体级配方案,从而有效降低系统粉磨电耗。
2.关键技术(1)利用高效优化蓖式粉磨机预粉碎物料;充分利用冲击、挤压、碾压粉碎物料原理,构造科学合理,设备功率消耗低,电能有效利用率高。
(2)配套物料分级装置,确保入磨物料粒度小于3mm;(3)优化球磨机磨内构造和研磨体级配方案;优化改造球磨机内部构造,采用新型隔仓板、出料篦板、导料锥、盲板等,增加活化衬板,改造更能提高研磨体粉磨效果的衬板等。
根据入磨物料的易磨性和粒度大小优化调整球磨机研磨体级配方案,提高研磨体粉磨效率,改善水泥颗粒结构,提高水泥比表面积,从而提高水泥强度,同等水泥熟料质量,可增加混合材料的掺入量。
3.工艺流程粉磨物料经过计量称计量配料后,通过金属探测仪和除铁器除去金属杂质,进入物料分选设备进行分选,细颗粒物料(粒度≤3mm)进入球磨机进行研磨作业;粗颗粒物料(粒度>3mm)进入高效蓖式粉磨机进行破碎、粉磨,出高效蓖式粉磨机物料,再进入物料分选设备进行分选,分选后的细颗粒物料(粒度≤3mm)进入球磨机进行研磨作业,粗颗粒物料(粒度>3mm)返回高效蓖式粉磨机再进行粉碎。
水泥企业粉磨系统节能降耗的技术措施

水泥企业粉磨系统节能降耗的技术措施随着水泥行业产能的严重过剩,产品价格下跌,企业利润急剧下滑,企业的竞争也日趋严峻。
水泥生产企业在稳定提升产品质量、扩大市场占有率的前提下,如何有效降低成本、挖掘内部潜力,提升核心竞争力,其中节能降耗是一重要技术措施。
现将水泥粉磨企业的一些节能方案做简单阐述,希望能起到抛砖引玉的作用。
一.从电气角度节能的措施1. 合理选择供配电电压。
在额定电压允许情况下,提高引入的高压电压等级,是降低线损率的有效措施。
对于配电网,供电电压等级越高,线损就越低,而线损是随电压平方成反比而下降,新建项目将电压从6KV提高到10KV,一次投资略高,但运行成本将降低。
2. 变频节能设备的推广应用。
选用节能型变压器,合理选择变压器容量。
在确保变压器在安全和可靠的基础上,要选用损耗低的变压器。
S9系列节能变压器,其损耗值与S7系列相比,空载损耗可降低10%,负债损耗可降低10%。
近年来我国的变频调速节能设备不断取得技术突破,高压、低压不同电压等级的越来越大容量的节电设备开发成功。
这项技术可实现变频软启动,减少对电网的冲击,还可节电25%左右。
这项技术还广泛运用在交流电机的变频调速装置上,其节电效果要根据电机所拖动的不同类型负荷特性和调速范围而决定。
适用设备:离心风机,需要长期关小阀门进行调节的风机,如磨排风机、冷却风机等;罗茨风机,需要排放多余风的罗茨风机。
泵。
皮带机,为适应带负荷启动电机选型偏大,物料层薄的皮带机等。
3. 全方位地采用高、低压无功功率的就地补偿装置,包括自动调节的静电电容器组和进相机组的应用。
通过这些技术措施,大大改善水泥企业用电的功率因数,减少对无功功率的需求,从而减少输入电能的有功电能损失。
4. 注重低压电机全相控技术的推广运用。
这项节电技术可在拖动负荷轻载和重载时自动调整电动机的输出功率,使电机实现在最佳状态下运行,以达到最佳节电的目的。
此节电产品平均节电率为15%~55%。
- 1、下载文档前请自行甄别文档内容的完整性,平台不提供额外的编辑、内容补充、找答案等附加服务。
- 2、"仅部分预览"的文档,不可在线预览部分如存在完整性等问题,可反馈申请退款(可完整预览的文档不适用该条件!)。
- 3、如文档侵犯您的权益,请联系客服反馈,我们会尽快为您处理(人工客服工作时间:9:00-18:30)。
19 高效优化粉磨节能技术
一、技术名称:高效优化粉磨节能技术
二、适用范围:建材、矿山等行业 粉磨生产系统
三、与该节能技术相关生产环节的能耗现状
目前,我国建材、矿山、发电等行业粉磨生产系统仍以球磨机作为粉磨主机为主,物料的粉碎和研磨均在球磨机内完成。
粉磨生产系统电耗一直较高,球磨机的电能有效利用率只有1%-5%左右,效率非常低。
建材行业水泥生产是粉磨应用较普遍的领域,以水泥企业为例,其粉磨电耗约占水泥企业总电耗的2/3,球磨机系统吨水泥粉磨电耗(未加预粉磨系统)约35~42kWh/t,采用增加预粉碎系统后,吨水泥粉磨电耗可达到30kWh/t以下,节能效果显著。
四、技术内容
1.技术原理
采用高效冲击、挤压、碾压粉碎原理,配合适当的分级设备,使入磨物料粒度控制在3mm以下,并优化球磨机内部构造和研磨体级配方案,从而有效降低系统粉磨电耗。
2.关键技术
(1)利用高效优化蓖式粉磨机预粉碎物料;
充分利用冲击、挤压、碾压粉碎物料原理,构造科学合理,设备功率消耗低,电能有效利用率高。
(2)配套物料分级装置,确保入磨物料粒度小于3mm;
(3)优化球磨机磨内构造和研磨体级配方案;
优化改造球磨机内部构造,采用新型隔仓板、出料篦板、导料锥、盲板等,增加活化衬板,改造更能提高研磨体粉磨效果的衬板等。
根据入磨物料的易磨性和粒度大小优化调整球磨机研磨体级配方案,提高研磨体粉磨效率,改善水泥颗粒结构,提高水泥比表面积,从而提高水泥强度,同等水泥熟料质量,可增加混合材料的掺入量。
3.工艺流程
粉磨物料经过计量称计量配料后,通过金属探测仪和除铁器除去金属杂质,进入物料分选设备进行分选,细颗粒物料(粒度≤3mm)进入球磨机进行研磨作业;粗
颗粒物料(粒度>3mm)进入高效蓖式粉磨机进行破碎、粉磨,出高效蓖式粉磨机物料,再进入物料分选设备进行分选,分选后的细颗粒物料(粒度≤3mm)进入球磨机进行研磨作业,粗颗粒物料(粒度>3mm)返回高效蓖式粉磨机再进行粉碎。
进入球磨机的物料经球磨机研磨后,达到一定细度和比表面积要求,出磨后进入成品库。
该技术的工艺流程及主要设备结构见图1,图2。
图1高效优化粉磨技术流程图
图2 高效优化粉磨结构简图
五、主要技术指标
1.入磨物料粒度控制≤3mm;
2.吨成品粉磨电耗下降30%~40%;
3.成品比表面积提高5%以上;
4.水泥熟料掺加量减少5%以上;
5.粉磨系统机物料消耗降低30%以上。
六、技术应用情况
该技术已获得多项技术专利,且经过安徽省能源利用监测中心的节能效果认定。
目前,该技术和设备已在全国多家水泥制造、矿山企业粉磨生产线应用。
对水泥粉磨生产线进行技改,系统优化,使水泥磨机大幅提产,降低单位产品电耗,提高水泥比表面积,降低熟料掺加量,使企业产品更具市场竞争力。
七、典型用户及投资效益
典型用户:安徽聚龙新型节能建材有限公司、安徽宣城阳光水泥有限公司、江苏省张家港市金臣水泥有限公司、甘肃白银市银山水泥有限责任公司、广东开平容氏石英砂有限公司、河南新乡市东华水泥有限公司、浙江建德市虎城水泥有限公司等。
典型案例1
建设规模:MB32130水泥球磨机生产系统优化节能改造。
主要技改内容:采用先进的改进型细碎挤压粉磨专利技术和工艺设备,对磨机的粉磨系统进行改造,主要设备包括高效节能粉磨机、磨内活化衬板、隔仓板、出料篦板、筛板改造。
节能技改投资额470万元,建设期4个月。
每年可节能4107tce,年节能经济效益为935万元,投资回收期7个月。
典型案例2
建设规模:φ3.2×13m水泥磨1台,φ2.4×8m生料磨2台磨前预粉碎改造。
主要技改内容:采用先进的改进型细碎挤压粉磨专利技术和工艺设备,对磨机的粉磨系统进行改造,主要设备为高效节能粉磨机。
节能技改投资额510万元,建设期4个月。
每年可节能3865tce,年节能经济效益868万元,投资回收期8个月。
八、推广前景和节能潜力
目前,国内建材行业、矿山行业85%以上使用球磨机进行粉磨作业,球磨机生产系统大部分没有进行磨前预粉碎技改,市场前景广阔,节能潜力巨大。
预计到2015年,采用该技术改造或新建的生产线可达约300台套,形成的年节能能力约为123万tce。