岩石爆破方案要点
爆破工程的专项方案

爆破工程的专项方案1. 项目背景爆破工程是利用爆炸能量将岩石或混凝土等硬质材料破碎或分离的一种施工方法。
在基础建设、矿山开采、隧道工程等领域都有广泛的应用。
本文将以某隧道工程爆破工程为例,详细介绍爆破工程的专项方案。
2. 爆破工程方案概述本项目为一条隧道工程,共计长2000米,宽15米,高12米。
地质条件为花岗岩和片岩交替分布,隧道深度在500米左右。
爆破工程主要是对隧道内部岩石进行爆破破碎,以便后续进行挖掘和支护。
3. 爆破工程前期准备3.1 地质勘察在爆破工程前,需要对隧道周边的地质条件进行详细勘察,了解岩石的种类、密度、裂缝等情况。
同时,还需进行地下水位的测定。
3.2 爆破方案设计根据地质勘察结果,确定爆破参数,包括爆炸药品种及用量、起爆序列、起爆时间等。
3.3 安全防护措施在爆破工程进行期间,需要设置爆破区域的限制线,并做好警戒工作,以确保周边人员和设施的安全。
4. 爆破工程具体方案4.1 爆破药品选择考虑到花岗岩和片岩的不同性质,我们选择使用不同种类的爆炸药品。
对于花岗岩,采用乳化炸药,以其爆炸速度快、能量高的特点;对于片岩,采用炸药捆包、炸药导爆管的方式进行爆破。
4.2 爆破参数确定在选择了适当的爆炸药品后,需要根据地质勘察结果,确定具体的爆破参数。
首先要确定爆破的钻孔深度和布孔距离,其次是合理设置爆破药量和装药方式。
同时,还要考虑到隧道内的地下水位,避免对地下水系统造成破坏。
4.3 起爆序列和起爆时间根据隧道的具体情况,确定起爆序列和起爆时间。
一般来说,需要先进行远端钻孔的爆破,然后再进行近端钻孔的爆破。
同时,要确保每个钻孔的起爆时间合理,以避免产生不均匀的爆炸效果。
4.4 安全防护措施在进行爆破工程时,需要在爆破区域周围设置警戒线,并由专人进行警戒工作。
同时,还需要对爆破现场进行视频监控,确保周边设施和人员的安全。
5. 爆破工程实施在做好前期准备工作后,可以开始进行爆破工程的实施。
预裂爆破方案
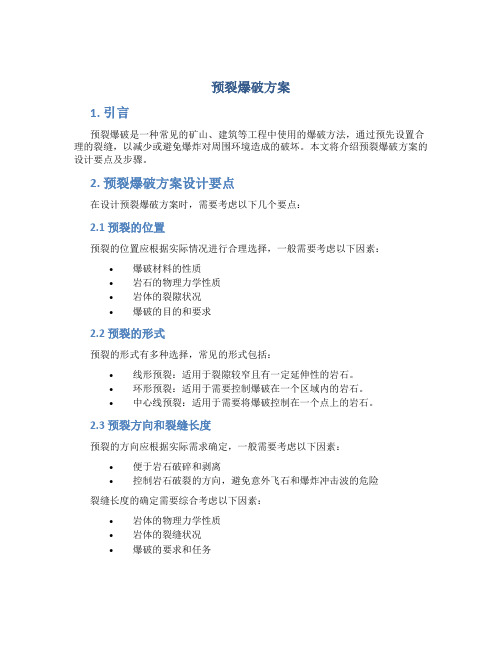
预裂爆破方案1. 引言预裂爆破是一种常见的矿山、建筑等工程中使用的爆破方法,通过预先设置合理的裂缝,以减少或避免爆炸对周围环境造成的破坏。
本文将介绍预裂爆破方案的设计要点及步骤。
2. 预裂爆破方案设计要点在设计预裂爆破方案时,需要考虑以下几个要点:2.1 预裂的位置预裂的位置应根据实际情况进行合理选择,一般需要考虑以下因素:•爆破材料的性质•岩石的物理力学性质•岩体的裂隙状况•爆破的目的和要求2.2 预裂的形式预裂的形式有多种选择,常见的形式包括:•线形预裂:适用于裂隙较窄且有一定延伸性的岩石。
•环形预裂:适用于需要控制爆破在一个区域内的岩石。
•中心线预裂:适用于需要将爆破控制在一个点上的岩石。
2.3 预裂方向和裂缝长度预裂的方向应根据实际需求确定,一般需要考虑以下因素:•便于岩石破碎和剥离•控制岩石破裂的方向,避免意外飞石和爆炸冲击波的危险裂缝长度的确定需要综合考虑以下因素:•岩体的物理力学性质•岩体的裂缝状况•爆破的要求和任务3. 预裂爆破方案设计步骤3.1 前期准备在设计预裂爆破方案之前,需要进行前期的准备工作,包括:•收集与岩石工程相关的资料和数据•进行现场勘察和实地调查,了解具体的地质情况和岩石特性•确定爆破的目的和要求•制定合理的工程计划和时间进度3.2 方案设计根据前期准备的结果,可以开始进行预裂爆破方案的设计:3.2.1 确定预裂的位置和形式根据岩体的特点和爆破的目标,选择适当的位置和形式进行预裂。
3.2.2 确定预裂方向和裂缝长度根据前期准备的数据和现场勘察结果,确定预裂的方向和裂缝长度。
3.2.3 选择合适的爆破材料根据岩体的物理力学性质和预裂的要求,选择适合的爆破材料。
3.2.4 设计合理的起爆序列根据岩体的裂隙状况和预裂的需要,设计合理的起爆序列,以达到预期的爆破效果。
3.3 方案评审和修改设计完预裂爆破方案后,需要进行方案评审和修改,主要包括:•经验技术人员对方案进行评审,提出修改意见和建议•根据评审结果,对方案进行修改和完善3.4 方案实施和监测在实施预裂爆破方案之前,需要进行必要的实施和监测工作,包括:•确保实施方案的安全性和可行性•监测预裂爆破的效果和影响•处理可能出现的意外情况和问题4. 结论预裂爆破方案是一种有效的控制爆破效果的方法,在岩石工程中得到广泛的应用。
隧道岩爆区施工方案
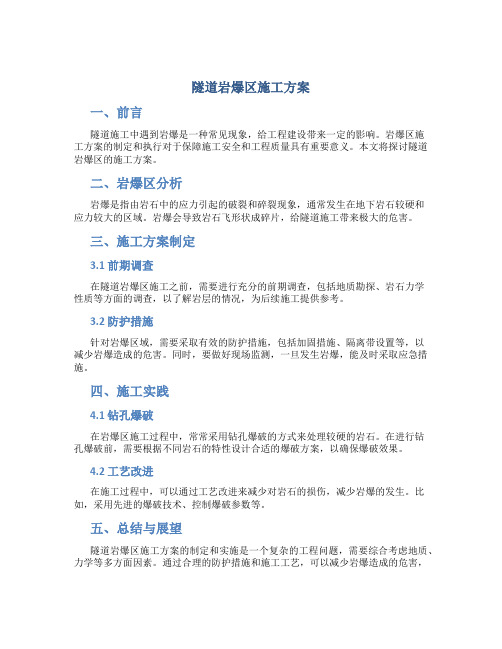
隧道岩爆区施工方案一、前言隧道施工中遇到岩爆是一种常见现象,给工程建设带来一定的影响。
岩爆区施工方案的制定和执行对于保障施工安全和工程质量具有重要意义。
本文将探讨隧道岩爆区的施工方案。
二、岩爆区分析岩爆是指由岩石中的应力引起的破裂和碎裂现象,通常发生在地下岩石较硬和应力较大的区域。
岩爆会导致岩石飞形状成碎片,给隧道施工带来极大的危害。
三、施工方案制定3.1 前期调查在隧道岩爆区施工之前,需要进行充分的前期调查,包括地质勘探、岩石力学性质等方面的调查,以了解岩层的情况,为后续施工提供参考。
3.2 防护措施针对岩爆区域,需要采取有效的防护措施,包括加固措施、隔离带设置等,以减少岩爆造成的危害。
同时,要做好现场监测,一旦发生岩爆,能及时采取应急措施。
四、施工实践4.1 钻孔爆破在岩爆区施工过程中,常常采用钻孔爆破的方式来处理较硬的岩石。
在进行钻孔爆破前,需要根据不同岩石的特性设计合适的爆破方案,以确保爆破效果。
4.2 工艺改进在施工过程中,可以通过工艺改进来减少对岩石的损伤,减少岩爆的发生。
比如,采用先进的爆破技术、控制爆破参数等。
五、总结与展望隧道岩爆区施工方案的制定和实施是一个复杂的工程问题,需要综合考虑地质、力学等多方面因素。
通过合理的防护措施和施工工艺,可以减少岩爆造成的危害,保障施工安全和工程质量。
未来,随着科技的发展,相信在这方面会有更多的创新和突破。
希望通过本文对隧道岩爆区施工方案的讨论能够引起更多从业者的关注和思考,共同努力提升施工质量,保障工程安全。
以上是本文的全部内容,谢谢阅读!。
爆破施工方案3

爆破施工方案3
在工程施工中,爆破技术是一种常用的手段,能够对岩石、土壤等硬质物体进
行有效地破碎和拆除,为工程施工提供了便捷有效的方式。
本文将就爆破施工方案
3进行详细介绍,包括施工前期准备、爆破设计、安全措施等内容。
1. 施工前期准备
在进行爆破施工之前,需要做好以下准备工作:
•审查施工区域周围的环境,确保没有人员和设施受到影响。
•对施工区域进行详细勘察,了解地质情况,确定爆破点位和方向。
•编制详细的爆破设计方案,包括装药量、起爆顺序等内容。
•安排专业人员进行爆破方面的指导和操作。
2. 爆破设计
针对爆破施工方案3,需要根据具体情况进行具体设计,以下是一般的爆破设
计要点:
•确定炸药的种类和数量,根据岩石硬度和爆破效果来选择。
•设计合适的装药方案,确保爆破效果均匀而又有效。
•制定合理的起爆顺序,防止空爆或炸药未能充分爆炸的情况发生。
•定期检查爆破设备和炸药,确保施工质量和安全。
3. 安全措施
在进行爆破施工时,安全至关重要,以下是一些常见的安全措施:
•对施工现场进行严格管控,确保周边区域不受影响。
•在爆破前做好警示标志,清场警报,以确保周边人员及时撤离。
•严格控制爆破设备的使用和操作,确保操作人员具备相关资质和经验。
•确保爆破后现场安全清理,消除爆炸余波,防止二次伤害发生。
结语
综上所述,爆破施工方案3是一项需要高度重视安全和技术要求的工程任务,
在施工前期准备、爆破设计和安全措施方面需严格执行相关规定,确保施工过程安全高效进行。
希望本文能对爆破施工方案3的实施提供一定的参考和帮助。
石方爆破专项施工方案..

石方爆破专项施工方案
一、背景介绍
石方爆破作为一种常见的工程施工方式,在岩石爆破前需要制定专项施工方案,以确保施工过程安全、高效。
本文将详细介绍石方爆破专项施工方案的制定及执行过程。
二、方案制定
2.1 施工前期准备
在进行石方爆破前,首先需要进行详细的勘察和测量,确定石方的类型、结构
及受力情况。
同时,需要对周边环境、人员和设备进行评估,制定应急预案。
2.2 方案设计
根据石方的具体情况,结合现场勘察结果,设计最佳的爆破参数,包括起爆顺序、装药方式等。
同时,需考虑爆破后石方的断面形态,确保施工效果达到预期。
2.3 安全措施
在施工过程中,安全始终是第一位的考虑因素。
需要严格执行作业许可制度,
设立爆破区域,并采取有效措施确保人员安全。
三、施工执行
3.1 装药
根据设计方案,按照爆破参数要求,对石方进行装药,确保装药均匀,爆破效
果最佳。
3.2 爆破
在确保安全的前提下,进行爆破操作。
严格控制爆炸能量,确保周边环境和设
备安全。
3.3 清理
爆破后,需对爆炸残留物进行清理,恢复原始状态,为后续施工做好准备。
四、施工总结
石方爆破专项施工方案的制定和执行是一项重要的工作,直接关系到施工过程中的安全性和效率。
通过科学合理的设计和严格的执行,可以有效降低风险,提高施工质量。
以上是石方爆破专项施工方案的简要介绍,欢迎对此提出任何意见和建议。
石方爆破专项施工方案(1)
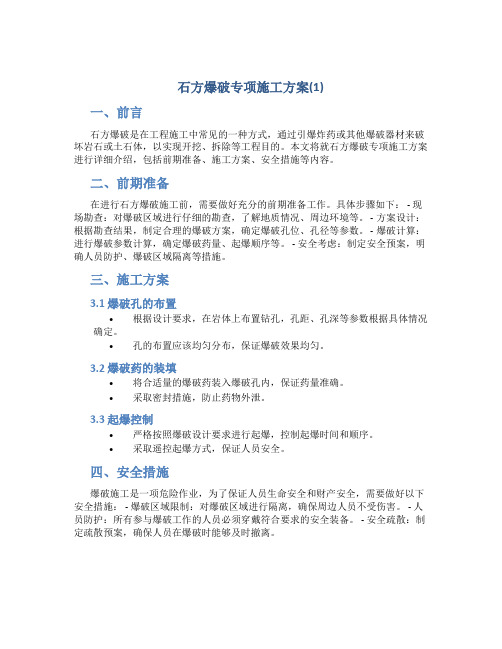
石方爆破专项施工方案(1)一、前言石方爆破是在工程施工中常见的一种方式,通过引爆炸药或其他爆破器材来破坏岩石或土石体,以实现开挖、拆除等工程目的。
本文将就石方爆破专项施工方案进行详细介绍,包括前期准备、施工方案、安全措施等内容。
二、前期准备在进行石方爆破施工前,需要做好充分的前期准备工作。
具体步骤如下: - 现场勘查:对爆破区域进行仔细的勘查,了解地质情况、周边环境等。
- 方案设计:根据勘查结果,制定合理的爆破方案,确定爆破孔位、孔径等参数。
- 爆破计算:进行爆破参数计算,确定爆破药量、起爆顺序等。
- 安全考虑:制定安全预案,明确人员防护、爆破区域隔离等措施。
三、施工方案3.1 爆破孔的布置•根据设计要求,在岩体上布置钻孔,孔距、孔深等参数根据具体情况确定。
•孔的布置应该均匀分布,保证爆破效果均匀。
3.2 爆破药的装填•将合适量的爆破药装入爆破孔内,保证药量准确。
•采取密封措施,防止药物外泄。
3.3 起爆控制•严格按照爆破设计要求进行起爆,控制起爆时间和顺序。
•采取遥控起爆方式,保证人员安全。
四、安全措施爆破施工是一项危险作业,为了保证人员生命安全和财产安全,需要做好以下安全措施: - 爆破区域限制:对爆破区域进行隔离,确保周边人员不受伤害。
- 人员防护:所有参与爆破工作的人员必须穿戴符合要求的安全装备。
- 安全疏散:制定疏散预案,确保人员在爆破时能够及时撤离。
五、总结石方爆破是一项常见的工程施工方式,在进行施工前需要做好详细的前期准备工作,制定科学合理的施工方案和严格的安全措施以确保施工过程安全有序进行。
只有做好全面的准备工作,才能高效完成爆破任务。
以上就是石方爆破专项施工方案的介绍,希望能为相关施工人员提供一些帮助。
硐石爆破施工方案1
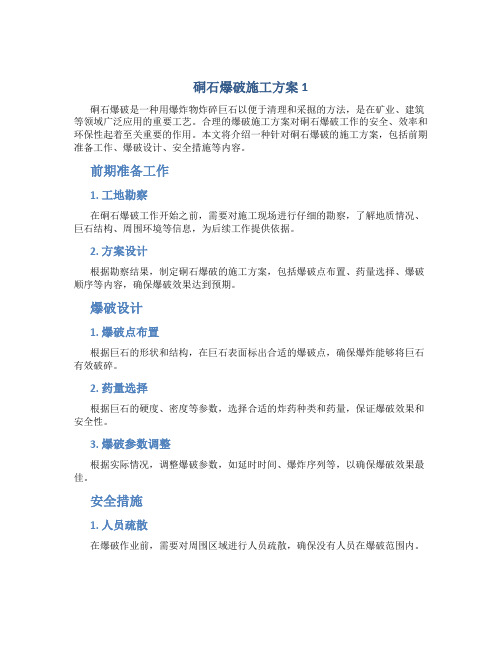
硐石爆破施工方案1
硐石爆破是一种用爆炸物炸碎巨石以便于清理和采掘的方法,是在矿业、建筑等领域广泛应用的重要工艺。
合理的爆破施工方案对硐石爆破工作的安全、效率和环保性起着至关重要的作用。
本文将介绍一种针对硐石爆破的施工方案,包括前期准备工作、爆破设计、安全措施等内容。
前期准备工作
1. 工地勘察
在硐石爆破工作开始之前,需要对施工现场进行仔细的勘察,了解地质情况、巨石结构、周围环境等信息,为后续工作提供依据。
2. 方案设计
根据勘察结果,制定硐石爆破的施工方案,包括爆破点布置、药量选择、爆破顺序等内容,确保爆破效果达到预期。
爆破设计
1. 爆破点布置
根据巨石的形状和结构,在巨石表面标出合适的爆破点,确保爆炸能够将巨石有效破碎。
2. 药量选择
根据巨石的硬度、密度等参数,选择合适的炸药种类和药量,保证爆破效果和安全性。
3. 爆破参数调整
根据实际情况,调整爆破参数,如延时时间、爆炸序列等,以确保爆破效果最佳。
安全措施
1. 人员疏散
在爆破作业前,需要对周围区域进行人员疏散,确保没有人员在爆破范围内。
2. 安全警示
在爆破前进行安全警示工作,确保所有工作人员了解爆破计划和安全注意事项。
3. 检查确认
在所有准备工作完成后,由专业人员对爆破方案进行检查确认,确保所有环节
符合安全要求。
结束语
硐石爆破是一项专业工作,施工方案的设计和执行至关重要,只有科学合理的
方案才能保证工作的安全、高效和顺利进行。
希望本文介绍的硐石爆破施工方案能够为相关工作者提供参考,促进硐石爆破工作的发展和进步。
石方爆破施工方案(全面)

石方爆破施工方案(全面)1. 施工前准备工作在进行石方爆破施工之前,需要进行全面的准备工作,包括但不限于以下几个方面:•勘察与测量:对工程地点进行详细的勘察与测量,确定石方的分布、结构及周边环境情况。
•安全评估:根据勘察结果制定安全评估报告,评估施工过程中可能存在的安全风险。
•施工方案制定:根据勘察结果和安全评估报告制定详细的石方爆破施工方案,包括爆破参数、爆破方式、爆破时间等内容。
2. 爆破设计石方爆破施工中的爆破设计是至关重要的环节,其主要包括以下几个方面:•爆破参数:确定合适的爆破参数,包括药量、装药方式、装药位置等,确保爆破效果达到预期目的。
•爆破方式:选择合适的爆破方式,包括平板爆破、逐排爆破等,根据石方情况和爆破效果需求进行选择。
•安全措施:制定详细的安全措施,保障施工人员和周边环境的安全。
3. 施工操作流程在进行石方爆破施工时,需按照以下操作流程进行:•清理工作面:清理石方表面杂物,确保爆破工作面干净整洁。
•布药:根据爆破设计方案,进行装药工作,保证药量和装药位置准确无误。
•引爆:按照爆破设计方案要求,进行引爆爆破药并观察爆破效果。
4. 爆破效果评估爆破施工结束后,需要进行爆破效果评估,主要包括以下几个方面:•碎石情况:评估石方的碎石情况,检查是否符合预期要求。
•施工安全:评估施工过程中的安全情况,检查是否存在安全隐患。
•环境影响:评估爆破对周边环境的影响,确保施工过程对环境的影响降至最低。
5. 总结与改进在石方爆破施工结束后,需要进行总结与改进工作,包括但不限于:•总结经验:总结本次施工经验教训,为今后的石方爆破施工提供参考。
•改进措施:提出改进措施和建议,完善施工方案,提高施工效率和安全性。
•记录与归档:对施工过程进行详细记录和归档,便于今后查阅和回顾。
以上是全面的石方爆破施工方案,希望能够对相关领域的从业者提供参考和帮助。
岩石爆破方案

1.爆破作业区域位置图
2.爆破设计图
本方案如有未尽事宜,可根据实际情况予以调整,并报请相关部门审批。
完。
第2篇
岩石爆破方案
一、前言
鉴于当前基础设施建设项目中对岩石爆破作业的需求,为确保爆破作业的安全、高效与环保,特制定本岩石爆破方案。本方案严格遵循《爆破作业安全管理条例》等相关法律法规,并结合项目具体情况进行编制。
1.爆破方法:根据工程特点,采用浅孔爆破法进行岩石爆破。
2.爆破工艺:包括钻孔、装药、堵塞、连线、起爆等环节。
五、爆破作业流程
1.钻孔:采用XX型钻机进行钻孔,孔径XXmm,孔深XXm,孔距XXm,排距XXm,按照设计要求进行布孔。
2.装药:选用XX型岩石乳化炸药,按照设计药量进行装药,装药结构为连续装药或间隔装药。
二、工程概述
1.工程地点:本项目位于XX省XX市XX区,地理环境复杂,岩石分布广泛。
2.工程规模:预计爆破岩石总量约为XX万立方米。
三、爆破目标与原则
1.目标:实现安全、高效、环保的岩石爆破,满足工程进度和质量要求。
2.原则:以人为本,安全第一;科学设计,优化爆破;保护环境,降低影响。
四、爆破方法与工艺
八、爆破作业时间安排
1.钻孔:XX天
2.装药:XX天
3.堵塞、连线:XX天
4.起爆:XX天
5.清理:XX天
九、质量保证措施
1.严格遵循爆破设计要求,确保爆破质量。
2.加强爆破作业过程控制,提高爆破效果。
3.及时对爆破效果进行评估,对存在的问题进行整改。
十、方案审批
本方案经项目相关部门审核,报请项目负责人批准后实施。
5.起爆:采用XX型起爆器进行起爆。
隧道工程岩石爆破拆除专项施工方案

隧道工程岩石爆破拆除专项施工方案1. 概述本文档旨在提供一份关于隧道工程岩石爆破拆除的专项施工方案。
该方案旨在确保安全、高效地进行岩石爆破拆除,以顺利推进隧道工程进展。
2. 施工目标本施工方案的主要目标如下:- 安全:确保施工过程中的人员和设备安全;- 高效:提高施工效率,减少工期;- 环保:采取环保措施,降低对周边环境的影响。
3. 施工步骤为了实现施工目标,我们将按照以下步骤执行岩石爆破拆除工作:3.1 前期准备工作在开始岩石爆破拆除工作之前,需要进行以下准备工作:- 确定爆破区域范围;- 进行现场勘察,了解地质情况;- 制定详细的爆破设计方案;- 确保所有参与施工的人员了解相关安全规范。
3.2 爆破准备在进行爆破拆除之前,需要进行以下准备工作:- 搭建爆破作业区域的临时围护结构,确保周边环境安全;- 安装监控设备,监测施工过程中的振动、噪音等参数;- 清理爆破区域内的杂物和不稳定物,确保安全;- 按照设计方案设置爆破孔。
3.3 爆破施工进行爆破拆除的主要步骤如下:- 加装爆破药包和导爆索,并按照设计方案设置引爆装置;- 撤离爆破区域内的人员和设备,确保安全;- 进行爆破作业;- 在爆破结束后,检查爆破区域,确保安全。
3.4 清理和检查爆破工作结束后,需要进行以下工作:- 清理爆破区域内产生的岩石碎片和杂物;- 检查爆破区域和围护结构的安全情况;- 总结施工过程中的经验教训,完善施工方案。
4. 安全措施在施工过程中,我们将采取以下安全措施:- 严格执行相关安全规范和操作规程;- 为施工人员提供必要的个人防护装备;- 对施工人员进行安全培训和技术指导;- 定期检查施工设备的安全状态。
5. 环保措施为保护环境,我们将采取以下措施:- 在施工区域周边设置防尘网和水幕;- 使用封闭式爆破装置,减少噪音和振动;- 清理施工区域内产生的废弃物,妥善处理。
以上所述即为本隧道工程岩石爆破拆除专项施工方案的基本内容,我们将根据实际情况进行具体实施,以确保施工过程的安全和顺利进行。
岩石爆破开挖施工方案

岩石爆破开挖施工方案背景介绍岩石爆破是一种常见的开挖施工方法,特别适用于需要快速击碎岩石并清除大量杂物的情况。
在建筑、挖掘和矿山等领域中广泛应用。
本文将详细介绍岩石爆破开挖施工方案。
施工准备工作施工人员和设备•钻孔机:用于钻取岩石孔,通常使用岩石钻机。
•炸药和引爆器:选择合适的炸药和引爆器,确保安全和高效的爆破作业。
•监测设备:安装地震仪等设备,监测爆破过程中的地震波情况。
•安全装备:包括安全帽、防护眼镜、防尘面罩等。
目标区域勘测在进行岩石爆破前,需要对目标区域进行细致的勘测,了解其地质、地下水位等情况。
了解目标区域的地质特征有助于制定爆破方案、确定钻孔位置和炸药数量等。
方案制定根据勘测结果,制定岩石爆破开挖施工方案。
方案应考虑以下因素:•安全性:确保施工过程中的人身和财产安全。
•高效性:以最小的投入达到预期开挖效果。
•环保性:尽量减少噪音、颗粒物和振动等对周围环境的影响。
施工过程钻孔根据爆破方案和地质勘测结果,在目标区域进行钻孔。
钻孔应根据地质条件和设计要求设置倾角和孔深。
钻孔直径通常为爆破材料直径的2-3倍,以确保充分装填炸药。
装药钻孔完成后,需要将炸药装入孔内。
装药的数量应根据岩石的抗压强度、岩石性质和开挖要求等因素进行合理评估。
装药时应做到均匀分布,以确保爆破效果的一致性。
引爆爆破前,应确保施工现场的安全,并与相关部门进行协调,确保周围区域的人员和设备不会受到影响。
引爆前,应检查引爆器和安全导线的连接情况,并进行必要的定时引爆设置。
爆破后,需要对残留岩石和炸药残渣进行清理。
同时,还需要检查爆破效果,确保开挖要求的达到。
环境监测在爆破过程中,应设置地震仪等监测设备,监测爆破所产生的地震波情况。
监测报告应及时上报,以便及时调整施工方案。
安全注意事项•施工前,应对施工现场进行安全检查,并向相关部门报备施工计划。
•施工人员应佩戴符合要求的安全装备。
•炸药应妥善保管,严禁在施工现场吸烟、使用明火等。
爆破实施方案

爆破实施方案一、前言爆破是一种常见的工程施工方法,通常用于拆除建筑物、岩石开采、地铁隧道开挖等工程中。
爆破实施方案是指在进行爆破作业时,为了保证作业安全和效果,需要提前制定的详细计划和措施。
下面将详细介绍爆破实施方案的内容和要点。
二、爆破实施方案的制定1. 工程概况分析在制定爆破实施方案之前,首先需要对工程进行详细的概况分析,包括爆破对象的材质、结构、周围环境等情况的调查和分析,以及对爆破后的效果和影响进行评估。
2. 爆破设计方案根据工程概况分析的结果,制定爆破设计方案,包括爆破参数的确定、爆破孔的布置、装药方案的选择等内容,确保爆破作业的安全和效果。
3. 安全措施制定爆破实施方案时,必须充分考虑安全因素,包括爆破现场的安全防护措施、人员的安全培训和防护装备、爆破作业的安全距离等,保障人员和设备的安全。
4. 环境保护措施爆破作业可能对周围环境产生影响,因此在制定爆破实施方案时,需要考虑环境保护措施,包括对周围建筑物、水体、土壤等环境的保护措施和监测方案。
5. 应急预案在爆破作业中,可能会出现意外情况,因此需要制定应急预案,包括对可能出现的意外情况进行分析和预测,以及相应的处置措施和救援方案。
三、爆破实施方案的执行1. 实施前准备在进行爆破作业之前,需要对爆破现场进行详细的检查和准备工作,包括检查爆破设备和装药材料的完好性、清理爆破现场、设置安全警戒线等。
2. 爆破作业根据爆破实施方案的要求,进行爆破孔的布置、装药、引爆等作业,确保爆破作业的安全和效果。
3. 爆破后处理爆破作业完成后,需要对爆破现场进行清理和检查,确保没有残留的爆破物和安全隐患,同时对周围环境进行监测和评估。
四、总结爆破实施方案是爆破作业的重要组成部分,它直接关系到爆破作业的安全和效果。
因此,在制定和执行爆破实施方案时,必须严格按照要求进行,确保爆破作业的安全、高效完成。
同时,需要不断总结和改进,提高爆破作业的质量和效率。
石方爆破施工方法
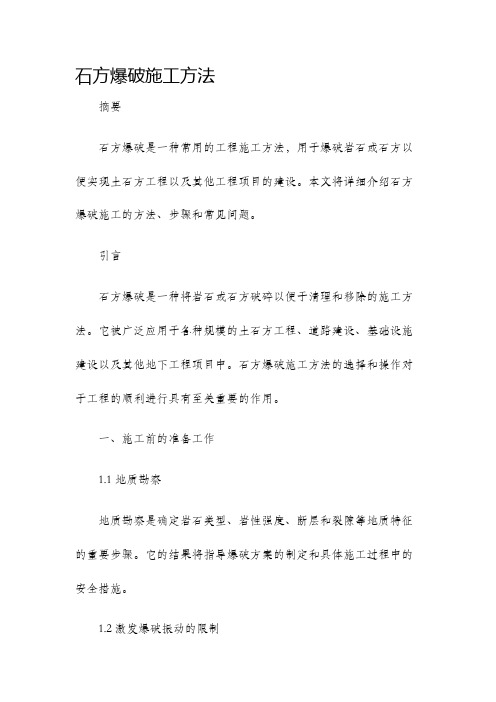
石方爆破施工方法摘要石方爆破是一种常用的工程施工方法,用于爆破岩石或石方以便实现土石方工程以及其他工程项目的建设。
本文将详细介绍石方爆破施工的方法、步骤和常见问题。
引言石方爆破是一种将岩石或石方破碎以便于清理和移除的施工方法。
它被广泛应用于各种规模的土石方工程、道路建设、基础设施建设以及其他地下工程项目中。
石方爆破施工方法的选择和操作对于工程的顺利进行具有至关重要的作用。
一、施工前的准备工作1.1 地质勘察地质勘察是确定岩石类型、岩性强度、断层和裂隙等地质特征的重要步骤。
它的结果将指导爆破方案的制定和具体施工过程中的安全措施。
1.2 激发爆破振动的限制根据相关法规和标准,需要确定炸药量、起爆点的位置以及相关的振动限制,以最大程度地减少对周边建筑物和环境的不良影响。
1.3 安全措施确保施工现场的安全是非常重要的。
施工前应对现场进行详细的安全评估,确保工作人员以及周围居民的人身安全。
二、石方爆破施工的基本步骤2.1 爆破设计根据地质勘察结果和工程要求,设计合适的爆破方案。
爆破方案将涉及炸药的选择、炸药的布置、起爆点的位置以及爆破的顺序等。
在设计过程中要注意控制破坏范围,确保对周围环境的影响最小化。
2.2 爆破设备的选择和布置根据爆破设计方案,选择合适的爆破设备。
爆破设备包括起爆器、导爆管、雷管等。
根据爆破设计,合理地布置爆破设备,确保爆破效果的最大化。
2.3 安全设施的设置在进行石方爆破施工时,必须设置符合安全要求的设施,如防护挡板、警示标识、遮挡网等。
这些设施将确保工作人员和周围环境的安全。
2.4 施工操作按照爆破设计方案进行施工操作。
这包括将炸药布置在岩石或石方内部的合适位置上、连接导爆管和雷管等操作。
2.5 立即启动爆破程序当施工操作完成后,立即启动爆破程序。
确保现场的人员全部撤离,并通过通知周围的居民和相关单位减少不必要的干扰。
三、常见问题及处理方法3.1 振动超限当爆破振动超过相关限制时,可能会对周围建筑物造成破坏。
岩石爆破施工工艺及方法

岩石爆破施工工艺及方法概述岩石爆破是一种常用的岩土工程施工方法,适用于岩石破碎、挖掘和开发等工作。
本文将介绍岩石爆破施工的基本工艺和方法。
工艺流程1. 岩石分析:在进行岩石爆破之前,需要对岩石进行详细的分析和评估。
分析包括岩石的硬度、脆性等特性,以确定适用于该岩石的爆破参数。
2. 爆破设计:根据岩石的分析结果,设计合适的爆破方案。
方案应包括爆破孔的布置、药量的确定、起爆顺序的规划等内容。
3. 施工准备:在开始爆破施工前,需要做好相应的准备工作。
包括清理施工现场、设置警示标志、排除安全隐患等。
4. 钻孔:按照爆破设计方案,在岩石中钻孔。
钻孔的位置、深度和直径应符合设计要求。
5. 装药:将爆破药物装入钻孔中。
根据设计方案,确定装药的种类、数量和方式。
6. 密封爆破孔:使用密封材料对爆破孔进行密封,以确保爆破效果。
7. 起爆:根据起爆顺序和方式,进行爆破操作。
起爆后,岩石会发生破碎和脱落。
8. 清理和处理:在爆破后,需对破碎的岩石进行清理和处理。
清理包括清除岩石碎片、清理作业现场等。
安全措施在进行岩石爆破施工时,需重视安全问题,并采取相应的措施来保障人员和设备的安全。
常见的安全措施包括:- 设置警示标志,提醒周围人员注意施工区域的危险性;- 使用合适的个人防护装备,如安全帽、护目镜、防护服等;- 严格遵守操作规程和安全操作要求,确保操作人员的安全;- 在施工现场设置消防设备,应对可能发生的火灾等事故。
结论岩石爆破施工是一种有效的岩土工程施工方法,能够满足岩石破碎、开发等需求。
在进行施工时,需要进行岩石分析、设计合适的爆破方案,并采取安全措施,以确保工程顺利进行。
*注意:以上内容仅供参考,具体施工时应根据实际情况进行细致分析和设计。
*。
岩石坑爆破施工方案范本(3篇)
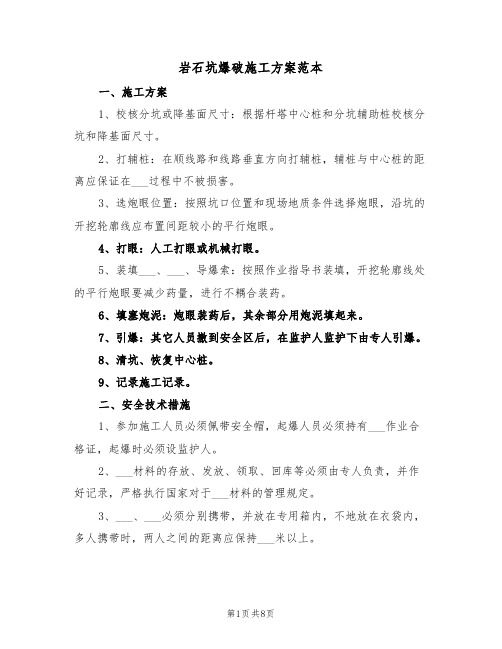
岩石坑爆破施工方案范本一、施工方案1、校核分坑或降基面尺寸:根据杆塔中心桩和分坑辅助桩校核分坑和降基面尺寸。
2、打辅桩:在顺线路和线路垂直方向打辅桩,辅桩与中心桩的距离应保证在___过程中不被损害。
3、选炮眼位置:按照坑口位置和现场地质条件选择炮眼,沿坑的开挖轮廓线应布置间距较小的平行炮眼。
4、打眼:人工打眼或机械打眼。
5、装填___、___、导爆索:按照作业指导书装填,开挖轮廓线处的平行炮眼要减少药量,进行不耦合装药。
6、填塞炮泥:炮眼装药后,其余部分用炮泥填起来。
7、引爆:其它人员撤到安全区后,在监护人监护下由专人引爆。
8、清坑、恢复中心桩。
9、记录施工记录。
二、安全技术措施1、参加施工人员必须佩带安全帽,起爆人员必须持有___作业合格证,起爆时必须设监护人。
2、___材料的存放、发放、领取、回库等必须由专人负责,并作好记录,严格执行国家对于___材料的管理规定。
3、___、___必须分别携带,并放在专用箱内,不地放在衣袋内,多人携带时,两人之间的距离应保持___米以上。
4、___在使用前,必须进行外观检查和燃速实验,燃速速度不得低于___秒/米,在同一次___中不得使用燃速不同的___。
5、人工打孔时,打锤人应在扶钎人的侧面,注意避免滑锤伤人。
6、利用凿岩机或风动机打孔时,操作人员应先检查设备是否完好,操作时应戴口罩和风镜。
7、向炮眼内装填___和___时,必须轻填轻送,不得用力积压药包,严禁用金属工具向炮眼内捣送___和___。
8、安全警戒范围:一般顺抛掷方向___米,逆抛掷方向___米。
9、起爆前必须把___物品全部拿出危险警戒区,除监护人和点炮人外,其他人必须撤到安全区,双方联系确认危险区内无人后方可引爆,点炮后点炮人和监护人必须马上撤到安全区。
10、装药和起爆必须由一人担任,严禁由两人操作。
11、发生哑炮数不清时,必须等___分钟后方可进场处理,处理哑炮严禁直接从炮孔内掏取___和___,重新打孔时,必须与原孔方向一致,其间距离孔深不得小于___米,浅孔不得小于0.3—___米。
石方爆破施工方案
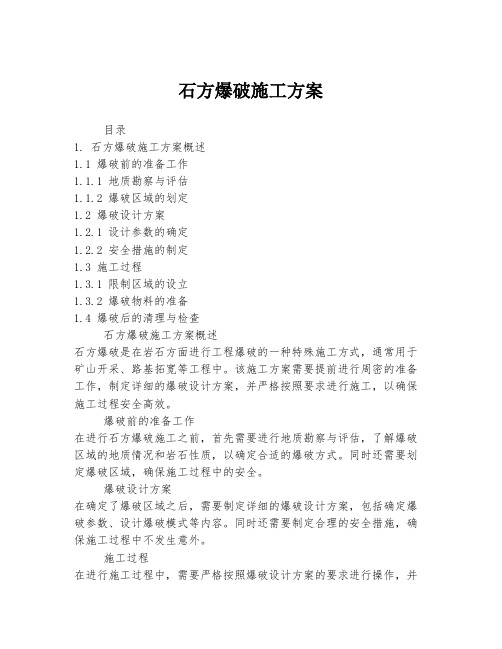
石方爆破施工方案
目录
1. 石方爆破施工方案概述
1.1 爆破前的准备工作
1.1.1 地质勘察与评估
1.1.2 爆破区域的划定
1.2 爆破设计方案
1.2.1 设计参数的确定
1.2.2 安全措施的制定
1.3 施工过程
1.3.1 限制区域的设立
1.3.2 爆破物料的准备
1.4 爆破后的清理与检查
石方爆破施工方案概述
石方爆破是在岩石方面进行工程爆破的一种特殊施工方式,通常用于矿山开采、路基拓宽等工程中。
该施工方案需要提前进行周密的准备工作,制定详细的爆破设计方案,并严格按照要求进行施工,以确保施工过程安全高效。
爆破前的准备工作
在进行石方爆破施工之前,首先需要进行地质勘察与评估,了解爆破区域的地质情况和岩石性质,以确定合适的爆破方式。
同时还需要划定爆破区域,确保施工过程中的安全。
爆破设计方案
在确定了爆破区域之后,需要制定详细的爆破设计方案,包括确定爆破参数、设计爆破模式等内容。
同时还需要制定合理的安全措施,确保施工过程中不发生意外。
施工过程
在进行施工过程中,需要严格按照爆破设计方案的要求进行操作,并
设立限制区域,确保施工现场的安全。
同时还需要提前准备好爆破物料,以保证爆破效果。
爆破后的清理与检查
爆破完成后,需要及时进行清理工作,清除爆破物料和碎石,确保施工现场的整洁。
同时还需要对爆破效果进行检查,确保施工达到预期效果。
岩石爆破施工的安全规范与注意事项
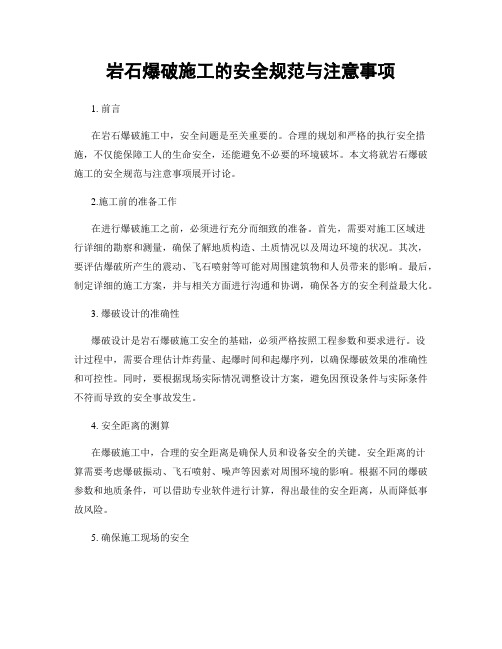
岩石爆破施工的安全规范与注意事项1. 前言在岩石爆破施工中,安全问题是至关重要的。
合理的规划和严格的执行安全措施,不仅能保障工人的生命安全,还能避免不必要的环境破坏。
本文将就岩石爆破施工的安全规范与注意事项展开讨论。
2.施工前的准备工作在进行爆破施工之前,必须进行充分而细致的准备。
首先,需要对施工区域进行详细的勘察和测量,确保了解地质构造、土质情况以及周边环境的状况。
其次,要评估爆破所产生的震动、飞石喷射等可能对周围建筑物和人员带来的影响。
最后,制定详细的施工方案,并与相关方面进行沟通和协调,确保各方的安全利益最大化。
3. 爆破设计的准确性爆破设计是岩石爆破施工安全的基础,必须严格按照工程参数和要求进行。
设计过程中,需要合理估计炸药量、起爆时间和起爆序列,以确保爆破效果的准确性和可控性。
同时,要根据现场实际情况调整设计方案,避免因预设条件与实际条件不符而导致的安全事故发生。
4. 安全距离的测算在爆破施工中,合理的安全距离是确保人员和设备安全的关键。
安全距离的计算需要考虑爆破振动、飞石喷射、噪声等因素对周围环境的影响。
根据不同的爆破参数和地质条件,可以借助专业软件进行计算,得出最佳的安全距离,从而降低事故风险。
5. 确保施工现场的安全施工现场的安全是岩石爆破施工的核心问题。
首先,应明确爆破区域的禁止进入区域,并设置明显的安全警示标识。
其次,要进行频繁而充分的施工区域巡视,确保作业人员遵守安全规范。
最后,要配备专业的安全人员,对施工现场进行全程监督和指导,及时发现和纠正不安全行为。
6. 严格执行安全操作规程在施工过程中,必须严格按照安全操作规程进行作业。
作业人员应接受专业培训,熟悉岩石爆破施工的操作流程和注意事项。
在操作中,要严格按照操作规程进行装药、引爆等工作,确保操作的准确性和安全性。
同时,要配备专业的监测设备,实时监测爆破振动、噪声等参数,及时采取相应的措施保证施工安全。
7. 爆破后的环境保护爆破施工对环境造成的影响不可忽视,必须采取措施保护生态环境。
岩石爆破方案

岩石爆破方案在矿山开采、道路建设等各种工程中,岩石爆破是一项非常重要的技术。
爆破可以快速、高效地将所需的岩石破碎,使工程进度得到迅速推进。
但是岩石爆破必须按照合适的方案进行,以确保操作的安全性和效果。
本文将针对该主题进行探讨。
一、评估目标岩石在进行岩石爆破之前,必须对目标岩石的物理特性和化学成分进行评估。
这包括岩石矿物成分、岩石的裂隙和孔洞情况、岩石密度、硬度等方面。
目标岩石的物理特性和化学成分将直接影响爆破的效果和安全性。
通过评估,可以制定适合该岩石的爆破方案,避免不必要的安全事故和损失。
二、选择合适的爆破器材整个爆破过程的效果和操作安全与所使用的爆破器材的选择紧密相关。
选择合适的爆破器材是确保岩石爆破成功的一个重要步骤。
选择爆破器材的方式取决于岩石的孔洞、裂隙、硬度和导爆性能等因素。
通常常使用的爆破器材有鱼雷、炸药、导火线、着火器和石灰石等材料。
三、制定爆破方案爆破方案是实现爆破目标的关键。
制定爆破方案时需要考虑许多因素,如爆破孔的位置、大小和深度、爆破器材的种类、爆破的时间和爆破序列等。
爆破方案应根据岩石的物理特性和化学成分进行制定,并尽可能减少破坏的影响。
四、布置爆破器材爆破器材的布置非常关键,必须在爆破前严格按照爆破方案进行。
爆破孔的布置需要考虑岩石的物理特性和化学成分,而且必须遵循原始的爆破设计。
同时,在爆破前需要对爆破现场进行详细的勘测,以保证爆破操作的安全性和测量精度。
在爆破操作中,作业人员必须严格遵守安全规定,以确保操作的安全性。
五、实施爆破爆破操作是整个岩石爆破过程的最后一步,是能否成功完成该项目的关键。
在实施爆破过程中,必须严格按照预定的爆破方案进行,以确保操作的安全性和效率。
在爆破后,必须对现场进行详细的勘测和清理,以确保安全以及减少环境污染。
综上所述,岩石爆破是工程中的重要工作,是实现工程建设的关键。
但是从评估目标岩石,选择合适的爆破器材,制定爆破方案等方面来看,合适的岩石爆破方案是必不可少的。
岩石坑爆破施工

岩石坑爆破施工1. 简介岩石坑爆破施工是一种常见的工程作业,用于破坏岩石表面、凿岩等工作。
本文将介绍岩石坑爆破施工的工艺流程、安全注意事项以及相关设备的使用方法。
2. 工艺流程岩石坑爆破施工的工艺流程主要包括以下几个步骤:2.1 前期准备在进行岩石坑爆破施工之前,需要进行充分的前期准备工作。
这包括调查、勘测、设计爆破方案以及确定爆破工序等。
2.2 岩石预处理岩石坑爆破施工之前,通常需要对岩石进行预处理。
这一步骤可以包括钻孔、破碎、凿岩等。
钻孔是将岩石表面打孔,以便后续的爆破操作;破碎是将大块的岩石打碎成适合后续处理的大小;凿岩是用凿子等工具将岩石表面凿制成所需的形状。
2.3 安装爆破装置安装爆破装置是岩石坑爆破施工的关键步骤。
爆破装置通常包括炸药、导爆索等。
在安装爆破装置之前,需要根据设计方案进行合理布局,并使用专业设备进行固定和连接。
2.4 岩石坑爆破岩石坑爆破是岩石坑爆破施工的核心工作。
在进行爆破之前,需要对现场进行安全检查,并保证人员安全撤离。
爆破操作包括引爆爆破装置、控制爆破的时间和力度等。
2.5 岩石坑处理岩石坑爆破之后,需要对岩石坑进行处理。
这包括清理爆破碎片、修复岩石表面等工作。
同时,还需要对爆破效果进行评估,以便后续工作的进行。
3. 安全注意事项在进行岩石坑爆破施工时,需要特别注意以下安全事项:3.1 人员安全岩石坑爆破施工过程中,人员的安全是最重要的。
施工人员必须经过专业培训,并佩戴个人防护装备。
在爆破操作前,必须确保现场没有其他人员,并按照操作规程进行撤离。
3.2 环境保护进行岩石坑爆破施工时,需要注意对环境的保护。
施工过程中产生的粉尘、碎片等应采取合适的措施进行收集和处理,以免对周围环境造成污染。
3.3 设备安全在进行岩石坑爆破施工时,必须使用经过检测和认证的专业设备。
施工人员需要对设备进行定期维护和保养,并保证设备的正常运行。
4. 相关设备的使用方法在岩石坑爆破施工中,有一些常用的设备需要正确使用。
- 1、下载文档前请自行甄别文档内容的完整性,平台不提供额外的编辑、内容补充、找答案等附加服务。
- 2、"仅部分预览"的文档,不可在线预览部分如存在完整性等问题,可反馈申请退款(可完整预览的文档不适用该条件!)。
- 3、如文档侵犯您的权益,请联系客服反馈,我们会尽快为您处理(人工客服工作时间:9:00-18:30)。
岩石爆破施工方案(1)爆破方案选择根据本露天矿采剥工艺,结合采装设备对岩石破碎块度、疏散度的要求,考虑到岩石的软硬程度,确定本矿山岩石层破碎方式为台阶松动爆破。
煤层顶板岩层厚度(即穿孔工作面到煤层的高度)若不足一个标准台阶高度,可采用小台阶爆破法处理,做到“分爆分采”,减少废石混入和降低贫化。
部分爆破区的炮孔穿透含水层,水孔装药应使用乳化炸药。
掘沟工程可根据掘沟高度即掘沟宽度单独进行爆破设计。
(2)标准台阶孔网参数设计(爆破对象为一般难爆岩石,达到爆破松动的效果,采用“经验法”设计)矿山生产标准台阶高度10m,本矿爆破岩石厚度3-8m,本设计采用爆破最大用药量,用8m计算,使用的穿孔设备时KY120型履带式露天潜孔钻机,穿孔直径d=120mm。
根据矿区岩层可爆性分析,结合类似矿山的爆破经验,炸药单耗kg。
施工过程中可根据不同爆破区的岩石硬度、初步确定为q=0.403m可爆性、岩石结构、层理发育程度的因素进行适当的调整,以期达到最佳爆破经济效果。
1)、孔径ø=110mm;2)、台阶高度H=8.0m3)、炮孔超深取h=1.5m4)、炮孔深度L=H+h=9.5m5)、填塞长度ho=3.0m6)、单孔装药量Q=qabWkg7)、实际单孔单耗q=0.43m8)、布孔方式:穿凿竖直孔,一般采用梅花形布孔方式。
a=5m b=5m Q后排=Q前排(1.1≈1.2)9)、总孔数n=5010)、药量数Q总=50×60=3.0T在采剥过程中由于开采的需要,有时采取低台阶爆破法,孔网及装药参数计算方法同上,即在保证爆破质量的前提下算出不同的孔网、装药参数,经设计计算得出不同条件下的参数如下表。
表1:经过计算调整后的低台阶爆破穿、爆参数成果表上表的参数可作为布孔和装药的参考,爆破施工中,对于不同的爆破区应根据岩石硬度,炮孔深度及爆破区周围的环境以及所选用的炸药特性调整照耀单耗、布置合理孔网、调整装药结构,以期达到理想的爆破效果。
(3)装药结构采用全孔径耦合装药结构,起爆药包放置在距底部装药长度的1/3处,用尾线长度7.0m的普通毫秒延期导爆管雷管(根据炮孔深度选用尾线长度)作为孔内激发雷管,深空内放置两发激发雷管,浅孔内放置一发激发雷管,使用多孔粒状铵油炸药时,用作起爆药包的乳化炸药不少于800g。
标准台阶爆破深孔装药结构见附图2图2 炮孔装药结构图(4) 填塞1、 结块的铵油炸药必须敲碎后放入孔内,防止堵塞炮孔,破碎药块只能用木棍、不能用铁器;乳化炸药在装入炮孔前一定要整理顺直,不得有压扁等迹象,防止炮孔堵塞。
2、 根据装入炮孔内的炸药量估计装药位置,发现装药位置偏差很大时立即停止装药,并报爆破技术人员处理。
3、 装药速度不宜过快,特别是水孔装药速度一定要慢,要保证乳化炸药沉入孔底。
4、 放置起爆药包时,雷管脚线要顺直,轻轻拉紧并贴在孔壁一侧,以避免脚线产生死弯而造成芯线折断、导爆管折断等,同时可减少炮棍捣坏脚线的机会。
5、 要采取措施,防止起爆线(或导爆管)掉入孔内。
6、 装药超量时采取的办法。
其一,装药为铵油炸药时往孔内倒入适量的水溶解炸药、降低装药高度、保证填塞长度符合设计要求;其二,装药为乳化炸药时采用炮棍等将炸药一节一节提出孔外,满足炮孔填塞长度。
处理过程中一定要注意雷管脚线(或导爆管)不得受到损伤,否则应在填塞前报爆破技术人员处理。
7、填塞过程中要防止导线、导爆管被砸断、砸破。
8、合理的填塞长度应能降低爆炸气体能量损失和尽可能增加钻孔装药量。
良好的填塞质量是尽量增加爆炸气体在孔内的作用时间和减少空气冲击波,噪声和个别飞散物的危害。
(5)安全分析与计算1)空气冲击波的影响本工程采用松动爆破方式,爆破震动和飞石距离时安全考虑的主导因素,空气冲击波危害不作为安全考虑的主要因素。
2 )由爆破震动确定最大同段齐爆药量爆破震动对建筑物造成的危害不容忽视,由构、建筑物最大容许震速确定最大同段齐爆药量,计算方法:爆破震动速度的控制标准和计算方法在〖爆破安全规程〗中由明确的规定,可按下表取值。
cm)建筑物地面质点最大允许振动速度V容(s具体计算方法:允许最大一次齐爆药量:a a K V R Q 3331上式中:安全距离R 以m 计,允许药量(最大单响爆破药量)Q1以kg 计,计算震速v 以s cm 计,公式中系数K a 的选取见下面的表格:按距离爆破区最近且抗震等级最差的建筑物允许地面质点最大震动速度反算最大一次齐爆药量:计算得出70米,质点振速为0.83小于1.0,符合安全标准要求。
上述由爆破震动确定的单响起爆药量式在取极端保守的参数条件下得出的,分析计算结构可知:爆破硬岩时同段齐爆药量控制在609kg以内,可使拒爆破区400m处的地面质点震速控制在1.0cm/s 以内,若爆破软岩,爆破震动会更小。
考虑到爆破区的地质条件:1、沉积岩在水平向上连续性好,对爆破震动波的传播有力,使得地震波在水平传播方向上衰减较为缓慢;2、地下采空区的存在,产生能力集中效应,使得地震波能量密度在水平传播方向上波衰减比正常地质条件下缓慢。
由于上述原因,对一次同段起爆药量在计算值的基础上进一步下调。
鉴于在爆破现场的多次实际观察,结合对爆破后的爆破震动分析,经归纳总结,本露天矿爆破的齐响齐爆药量以不超过300kg为宜。
3)由飞石安全距离的计算确定爆破安全警戒距离按照瑞典德唐尼克研究基金会总结的经验公式计算:Smax=15.8d=189.6md为孔径参照《爆破安全规程》(GB6722-2003)的相关规定,爆破安全警戒距离确定如下:爆破区位于避炮点高处时,人员安全警戒距离距爆破区边缘200m,设备安全距离不小于150m;爆破区位于避炮点地处时,人员安全警戒距离距爆破区边缘300m,设备安全距离不小于200m。
(6)爆破网络设计根据本次爆破的实际情况,为了最大限度地控制单段齐爆药量,本着“安全、高效、简单、可靠”的原则,结合现场使用爆破器材的情况及操作人员的技术熟练程度,确定采用“分区接力微差起爆网络”。
“分区接力微差起爆网络”的技术特点:1、合理分区也就是选择每个分区的合理宽度,选择合理的分区宽度是保证每个分区内各段别齐爆孔的总药量不超过300kg的前提;2、遵循顺序起爆的原则依次顺序起爆的意义如下:a、同一分区内自由面往后依次放置从低段到高段位的孔内延期雷管,确保同一分区内前爆孔为后爆孔创造自由面(即可降低爆破震动,同时提高爆破质量);b、先激发的分区纬相邻后激发的分区创造更多的侧向临空面;c、相邻分区顺序依次起爆可避免先爆分区最先激发炮孔产生的飞石破坏相邻分区的地表网络(分区接力微差起爆网络的技术关键是在先爆孔抛掷飞石不破坏地表网络前,起爆信号已达到孔内延期雷管)。
3、选择合理的雷管段别包括以下几个方面:a、分区接力雷管段别和接力区首段雷管段位的选择,确保起爆不跳段;b、分区内排间微差雷管段别的选择(排间微差间隔时间不低于40ms),将各段地震波分离开来。
实际情况:本次爆破网可根据爆破区的实际环境条件变动:1 、确定抵抗线方向为东2 、雷管布置总排数为2排,孔内首排为5,以此类推开始孔内分别为7、9,孔外延期管接力架用12、13,交叉使用,奇偶结合,达到减震。
3 、链接方法从一排到二排(7、9段)分为一区,以此反复,具体如图;4 、起爆顺序从北到南注:分区之间用双雷管连接(7)爆破施工应注意几点降震措施A、“分区接力微差起爆网络”能较好的解决控制爆破震动和一次爆破规模的矛盾问题,施工中应注意以下问题:1、控制一次爆破的排数,即控制一次采掘带宽度不超过六排炮孔为宜。
2、有条件可适当加大爆破长度,即一次采掘带长度不宜过小,这样,可提高一次穿爆规模,减少设备的频繁移动,减少扰民次数。
3、把握“分区接力微差起爆网络”的技术要点,艺术、合理的利用该技术,达到最终控制单响齐爆药量和微差时间间隔的,降低震动的目的。
B、合理布孔片面追求降低单耗的做法是不可取的,过小的单耗不仅增大爆破震动,同时也增加大块率。
实践证明,过小的单耗引起的二次破碎费用增加和采装效率所引起的单位成本增大量比降低单耗所省出的费用要高出不少。
总之,影响爆破震动强度、衰减快慢以及震动影响范围的因素很多,但将爆破震动的影响范围和强度控制到一定的范围内是完全可能的,只要我们依照“精心设计,精心组织施工”的爆破经验,把握好爆破施工的每一个环节,就会取得好的控制爆破结果,减少扰民情绪,造福社会,提高爆破企业的声誉。
(8)警戒与起爆1、警戒人员持红旗,配袖章,相邻两警戒岗哨应互相看见,以使相互联系2、路口设路障,指示牌。
3、警戒圈内人员及设备须在起爆前半小时撤离完毕,通往爆破区的个主要道路应设岗哨。
设备撤至距爆区150m外,人员警戒范围距爆破区边300m外。
附图5:预警信号(第一次信号):该信号发出后爆破警戒范围内开始清场工作;起爆信号(第二次信号):起爆信号应在确认人员,设备等全部撤离爆破警戒区,所有警戒人员到岗,具备安全起爆条件时发出。
起爆信号发出后,准许负责起爆的人员起爆;解除信号(第三次信号):安全等待时间(一般15min)过后,检查人员进入爆破警戒范围内检查,确认安全后,方可发出解除警戒信号。
在此之前岗哨不得撤离,不容许非检查人员进入爆破警戒范围。
各信号的发出要清晰、响亮,确保警戒范围内及周边的人员都能听到。
(9)爆破注意事项为确保爆破安全,爆破后由指挥部派专人进入现场检查,发现异常现象及时处理,安全保卫人员应严禁无关人员进入危险区,经检查确认安全后,向指挥长汇报,由指挥长下达解除警戒信号命令。
1)基本规定1.1)从事爆破及与有关的工作人员,必须进行安全知识教育并持证上岗;1.2 )工作过程中必须严格遵守《爆破安全规程》;1.3)必须使用爆破电桥测量电雷管电阻,不准用万用表或其他电工仪表代替专用爆破电桥;1.4 )起爆网络采用复式起爆网络1.5 )起爆站起爆电源开关应设专人看管,并锁好,起爆前起爆网络须始终属于短路状态;1.6 )一切准备完毕后,接上电源,由指挥长指挥起爆。
2)爆破后的检查2.1)爆破完后,派专人进入爆破区检查有无拒爆等不安全现象;2.2)如有盲炮等意外现象,立即设立局部警戒并采取相应措施解决。
(10)盲炮处理方案1 )处理盲炮必须遵守下列规定:A、发现盲炮或怀疑有盲炮,应立即报告并及时处理。
若不能及时处理,应在附近设有明显标志,并采取相应安全措施;B、难处理的盲炮,应指示爆破工作领导人,派有经验的爆破员处理;C、处理盲炮时,无关人员不准在场,应在危险区边界设警戒,危险区内禁止进行其他作业;D、盲炮处理后,应仔细检查爆堆,将残余的爆破器材收集起来,未判明爆堆有无残留的爆破器材前,应采取预防措施;2)处理深孔盲炮可采取下列方法:A、爆破网络未受破坏,最小抵抗线无变化者,可重新连线起爆;最小抵抗线有变化者,应验算安全距离,并加大警戒范围后,再连线起爆;B、在距盲炮孔口不小于10倍炮孔直径处另打平行孔装药起爆,爆破参数由爆破工作领导人确定;C、所用炸药为非抗水硝铵类炸药,孔壁完好者,可取出部分填塞物,向孔内灌水,使之失效,然后作进一步处理。