反向间隙测量
伺服滑台反向间隙检查调整步骤
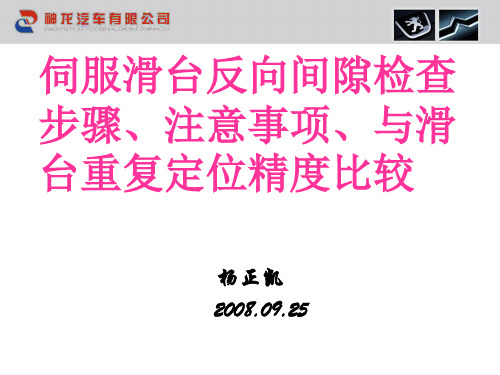
伺服滑台反向间隙
• 伺服滑台反向间隙: 伺服滑台反向间隙: • 由于机械传动系统的反向间隙,造 由于机械传动系统的反向间隙, 成伺服滑台在由正向运动转为反向 运动时形成的实际位移与理论位移 的差值。 的差值。
反向间隙的检测方法
• 反向间隙的检测方法: 反向间隙的检测方法: • 在所测滑台的行程内,预先向正向或 在所测滑台的行程内, 反向移动一段距离并以此位置为基准 再令向同一方向移动一段距离, 点,再令向同一方向移动一段距离, 然后再往相反方向移动相同的距离, 然后再往相反方向移动相同的距离, 测量停止位置与基准位置之差。 测量停止位置与基准位置之差。
操作示意简图如下图
O点
检查步骤
• 方法一: 方法一: • 1、先将滑台运行至大至为行程中段的位置,百分表座置 、先将滑台运行至大至为行程中段的位置, 于待测滑台的导轨上, 于待测滑台的导轨上,表头垂直置于滑台与运动方向垂直 的面上; 的面上; • 2、将数控系统置于手动方式,设定手动单步进给步长为 、将数控系统置于手动方式, 1mm,即每进给一次为移动 ,即每进给一次为移动1mm; ; • 3、百分表置零:如表头置于滑台左侧,令滑台向负方向 、百分表置零:如表头置于滑台左侧, 移动1mm,百分表指针旋转一圈,将表对零; 移动 ,百分表指针旋转一圈,将表对零; • 4、令滑台继续向负方向移动 、令滑台继续向负方向移动1mm,不动百分表,再令滑 ,不动百分表, 台向相反方向即正方向移动1mm,读取百分表与零的差 台向相反方向即正方向移动 , 值,即为反向间隙
反向间隙与重复定位精度的比较
• 伺服滑台反向间隙与滑台重复定位精度的 区别: 区别: • 重复定位精度反映的是反复运行同一指 令时, 令时,伺服滑台各次运行至终点位置的差 异程度而伺服滑台反向间隙反映的是滑台 每次作换向移动时空行程的大小。 每次作换向移动时空行程的大小。
反向间隙的测定及补偿 电子教材

反向间隙的测定及补偿任务内容反向间隙值的测定反向间隙的补偿在数控机床上,由于各坐标轴进给传动链上驱动部位(如伺服电动机) 的反向死区、各机械运动传动副的反向间隙等误差的存在,造成各坐标轴在由正向运动转为反向运动时形成反向偏差,通常称为反向间隙或失动量。
对于采用半闭环伺服系统的数控机床,反向间隙的存在会影响到机床的定位精度和重复定位精度,从而影响产品的加工精度。
若反向间隙太大,经常在加工中出现圆不够圆,方不够方的废品零件。
而FANUC半闭环数控则有相应的系统参数可实现较高精度的反向间隙补偿。
即可实现切削进给和快速进给两种加工模式下的反向间隙补偿功能,从而可以提高轮廓加工和定位加工的精度。
一、反向间隙值的测定在半闭环系统中,系统接收的实际值来自于电机编码器,轴在反向运行时指令值和实际值之间会相差一个反向间隙值,这个值就是反向间隙误差值。
在全闭环系统中,系统接收的实际值来自于光栅尺,实际值中已包含反向间隙,故不存在反向间隙误差。
反向间隙补偿在坐标轴处于任何方式时均有效。
当系统进行了双向螺距补偿时,双向螺距补偿的值已经包含了反向间隙,此时不需设置反向间隙的补偿值。
按以下步骤为例,说明测量切削进给方式下离机床参考点100mm 位置处的间隙量。
(1) 机床回参考点。
(2) 运行程序:G01X100F350;使机床以切削进给速度移动到测量点。
安装千分表,将刻度对0,此时机床状态如图1所示。
图 1 设定机床测量点的位置示意图(3) 运行程序:G01X 200F350,使机床以切削进给沿相同方向移动。
此时机床状态如图2所示。
图 2 机床沿X 轴正向移动100mm 后的位置示意图。
重复定位精度和反向间隙指导书

数控机床各数控轴重复定位精度和反向间隙一、重复定位精度1、定义重复定位精度是指机床滑板或大拖板在一定距离范围内(一般为200-300mm)往复运动7次千分表或激光干涉仪检测的精度。
取这7次的最大差值。
2、影响因素重复定位精度反映了伺服系统特性、进给系统的间隙与刚性以及摩擦特性等综合误差。
一般情况下,重复定位精度是呈正态分布的偶然性误差,它影响一批零件加工的一致性,是一个非常重要的精度指标。
它是影响机器能力指数CMK,工序能力指数CPK的重要因素。
3、相关标准GB/T18400.4-2010 与ISO标准相当。
300毫米长度上±0.0035JIS 日本标准DIN 德国标准二、重复定位精度和定位精度的区别。
定位精度指的是数控轴实际到达的位置和数控系统要求到达的位置误差。
比如要求一个轴走100 mm ,结果实际上它走了100.01 多出来的0.01 就是定位精度。
重复定位指的是同一个位置多次定位过去产生的误差。
比如要求一个轴走100 mm 结果第一次实际上他走了100.01 重复一次同样的动作他走了99.99 这之间的误差0.02 就是重复定位精度。
通常情况重复定位精度比定位精度要高的多。
单件生产(比如模具制造)要求机床具有较高的定位精度,大批量生产要求机床具有较高的重复定位精度三、重复定位精度的检测方法。
有两种,一种使用激光干涉仪,一种使用千分表。
介绍千分表检测重复定位精度。
1、选取数控轴经常使用的一段长度(200~300)毫米。
2、由作业指导员按下列要求编写一段小程序:1)设定坐标轴的起点2)坐标轴以工进速度(300米/分)往前走200或300毫米。
3)停住3秒。
(便于观察千分表)4)返回起点5)重复上述步骤共七次。
程序如下:(以X 轴为例)G91 X0G01 X300. F300G04 X3.G01 X0M993、作业指导员运行先单节运行小程序,确认程序无误。
4、保全工在停止的位置安装好千分表,并将千分表置零。
步距规测量滚珠丝杠反向间隙
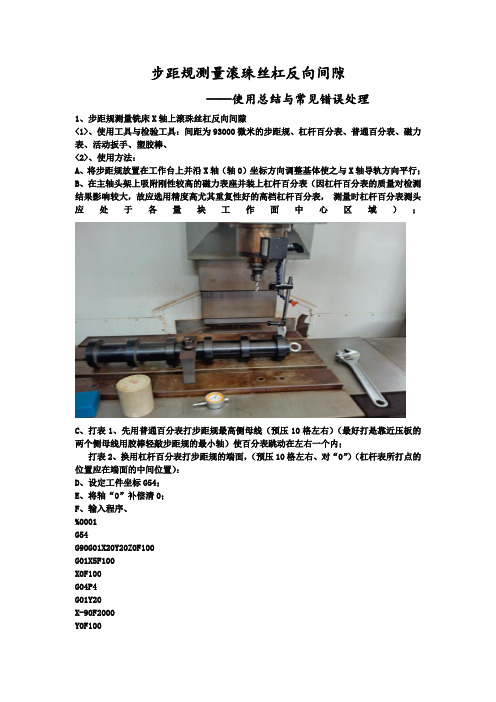
步距规测量滚珠丝杠反向间隙——使用总结与常见错误处理1、步距规测量铣床X轴上滚珠丝杠反向间隙<1>、使用工具与检验工具:间距为93000微米的步距规、杠杆百分表、普通百分表、磁力表、活动扳手、塑胶棒、<2>、使用方法:A、将步距规放置在工作台上并沿X轴(轴0)坐标方向调整基体使之与X轴导轨方向平行;B、在主轴头架上吸附刚性较高的磁力表座并装上杠杆百分表(因杠杆百分表的质量对检测结果影响较大,故应选用精度高尤其重复性好的高档杠杆百分表,测量时杠杆百分表测头应处于各量块工作面中心区域);C、打表1、先用普通百分表打步距规最高侧母线(预压10格左右)(最好打是靠近压板的两个侧母线用胶棒轻敲步距规的最小轴)使百分表跳动在左右一个内;打表2、换用杠杆百分表打步距规的端面,(预压10格左右、对“0”)(杠杆表所打点的位置应在端面的中间位置):D、设定工件坐标G54;E、将轴“0”补偿清0;F、输入程序、%0001G54G90G01X20Y20Z0F100G01X5F100X0F100G04P4G01Y20X-90F2000Y0F100X-93.005G04P4G01Y20F2000X-183Y0F100X-186.007G04P4G01X-276F2000Y0F100X-279.009G04P4G01Y20X-369F2000Y0F100X-372.09G04P4G01Y20X-390X-372.021Y0F100G04P4G01Y20X-279.009F2000Y0F100G04P4G01Y20F100X-186.007F2000Y0F100G04P5G01Y20F100X-93.005F2000Y0F100G04P4G01Y20F100X0F2000Y0F100G04P4M30或者输入程序:%0001 ;文件头:铣床X轴检测程序G92 X0 Y0 Z0 ;建立临时坐标WHILE[TRUE] ;循环次数不限,即死循环#1=P1 ;输入p1点尺寸#2=P2 ;输入p2点尺寸#3=P3 ;输入p3点尺寸#4=P4 ;输入p4点尺寸#5=P5 ;输入p5点尺寸G90 G01 X5 F2000 ;X轴正向移动5mmG01 Y15 F2000 ; Y轴正向移动15mm,将表头从步距规测量面上移开N05 X0 ;X轴负向移动5mm后返回测量位置,并消除反向间隙,此时测量系统清零G01 Y0 F300 ;Y轴负向移动5mm,让表头回到步距规测量面G04 P4 ;暂停3秒,记录表针读数G01 Y15 F2000X-#1 ;负向移动,使表头移动到(i=1,Pi=P1,下同)点Y0 F300G04 P4 ;暂停3秒,记录表针读数G01 Y15 F2000X-#2 ;负向移动,使表头移动到P2点Y0 F300G04 P4G01 Y15 F2000X-#3 ;负向移动,使表头移动到P3点Y0 F300G04 P4G01 Y15 F2000X-#4 ;负向移动,使表头移动到P4点Y0 F300G04 P4G01 Y15 F2000X-#5 ;负向移动,使表头移动到P5点Y0 F300G04 P4G01 Y15 F2000X-(#5+5) ;负向移动5mm(越程)X-#5 ;越程后正向移动至P5点Y0 F300G04 P4G01 Y15 F2000X-#4 ;正向移动到P4点Y0 F300G04 P4G01 Y15 F2000X-#3 ;正向移动到P3点Y0 F300G04 P4G01 Y15 F2000X-#2 ;正向移动到P2点Y0 F300G04 X3G01 Y15 F2000X-#1 ;正向移动到P1点Y0 F300G04 P4G01 Y15 F2000X0 ;正向移动到P0点Y0 F300G04 P4ENDWM02<3>、程序自检、单段运行(确保无误)、自动运行一次;<4>、测试数据及处理、第一点第二点第三点第四点第五点第一组0/-0.2 -0.7/-0.8 0/0 +0.1/0 -0.2/-0.4 第二组0/-0.5 -0.9/-0.9 0/0 +0.1/0 -0.2/-0.5 第三组-0.2/-0.4 -0.5/-0.9 0/0 0/0 -0.4/-0.4 第四组-0.1/-0.1 -0.7/-0.8 0/0 +0.3/+0.1 -0.4/-0.4 第五组-0.1/-0.5 -0.9/-0.8 0/0 +0.1/0 -0.2/-0.5 -0.08/-0.34 -0.74/-0.84 0/0 +0.12/+0.02 -0.28/-0.52 单向平均偏差双向……-0.21 -0.79 0 +0.07 -0.4反向偏差值-0.26 -0.1 0 +0.1 -0.24BiB=max【|Bi|】=0.26轴线反向差值轴线平均反向差值i B = 0.1<5>参数补偿、(轴补偿--轴0(X轴)--)反向间隙(微米)0(单向时为轴线平均偏差值)螺补类型(0-无,1-单向,2-双向,3,4-扩展) 2补偿点数 5参考点偏差号0补偿间隙93000偏差值(微米)[0] -4(-0.52-(-0.08)=-0.44)偏差值(微米)[1] 1(+0.02-(-0.08=+0.1))偏差值(微米)[2] 1 (0-(-0.08)=+0.08)偏差值(微米)[3] -8偏差值(微米)[4] -3偏差值(微米)[5] -2偏差值(微米)[6] 2偏差值(微米)[7] 1偏差值(微米)[8] -7偏差值(微米)[9] 0偏差值(微米)[10]<5>、保存、关机、重启、回参、重复上面<3>步骤、<6>、新测试数据、第一点第二点第三点第四点第五点0/0 +0.1/+0.1 -0.1/-0.1 +0.9/+0.5 0/-0.90/0 +0.1/0 -0.1/-0.1 +0.8/+0.5 0/-0.9<7>、分析测试结果、波动范围在1 以内、很合理、可以加工使用2、常见错误处理、A、开机回参报“超程”错误——原因、在回参之前、该轴一运动到极限位置、不能再执行该指令;B、运行程序报“超程”错误——原因、a、打表不合理、机床不能在有限的工作范围内执行该某句指令;b、程序起始点错误、C、“超程”报错解决方法——长按操作面板上的“超程解除”键(约10几秒)当按手动键有效时才松开、回参、2013-04-30s。
数控机床反向机械间隙的测量与补偿
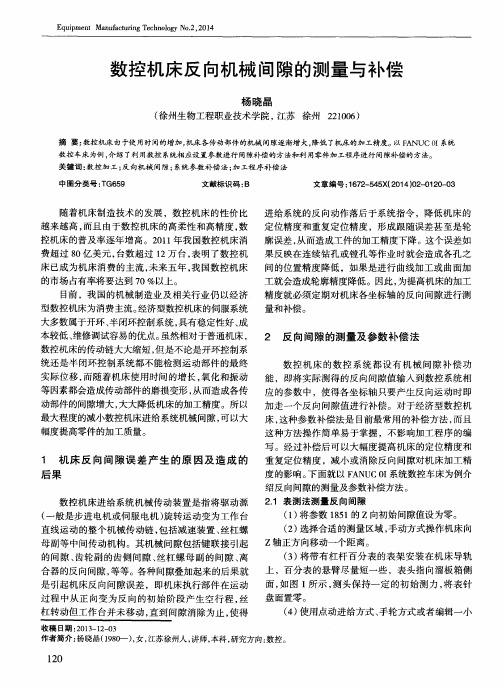
2 反 向间隙的测量及参数补偿法
数控 机床 的数 控 系统 都设 有机 械 间隙补偿 功 实际位移 , 而随着机床使用时间的增长 , 氧化和振动 能 ,即将实际测得 的反向间隙值输入到数控 系统相 等因素都会造成传动部件 的磨损变形 , 从而造成各传 应的参数 中,使得各坐标轴只要产生反向运动时 即 动部件的间隙增大 , 大大降低机床的加工精度 。所以 加走一个反向间隙值进行补偿。对 于经济型数控机 最大程度的减小数控机床进给系统机械间隙, 可 以大 床 , 这种参数补偿法是 目前最常用 的补偿方法 , 而且 幅度提高零件的加工质量 。 这种方法操作简单易于掌握 ,不影 响加工程序 的编 写 。经过补偿后可 以大幅度提高机床 的定位精度和 1 机 床 反 向间 隙误 差产 生 的原 因及造 成 的 重复定位精度 ,减小或消除反 向间隙对机床加工精
收 稿 日期 : 2 0 1 3 - 1 2 — 0 3
作者简介 : 杨晓晶( 1 9 8 o _ - ) , 女, 江苏徐州人 , 讲师 , 本科 , 研究方 向: 数控。
1 2 0
《 装备制造技术) ) 2 0 1 4 年第 2 期
段程序 , 操作机床向 z 轴负方 向移动 1 ~ 2 m m, 并读 间 隙 ; ( 6 ) 向下退刀 , 主轴停转 , 并测量 Q R段的长度 , 出百 分 表读 数 。 ( 5 ) 记录百分表读数 , 将理论移 动数值减 去实测 将编程值减去实测值 即为 z向反向间隙值 ; ( 7 ) x向反 向间隙的测量原理与 z向相同, 如图 移动距离即为反向间隙值 。 所示。先沿 一 x方向向上进刀 ,此时丝杠丝母 A _ x ( 6 ) 为提高测量 的精度 , 可以选取 z向工作行程 3 然 后 切 削一 段 阶梯 轴 , 在进行 Q R段 加 工 时 中的多个位置分别进行多次测量 ,计算 出最终的平 面接 触 , 均值作为反 向间隙值 , 输入到 1 8 5 1 的 z向参数 中。 恰巧是沿 + x方 向走刀 , 与进刀方 向相反 , 因此需 待 + x 面接触后 , 车刀才会开始切削 , 从而引 ( 7 ) x向传动 反 向间隙值 的测量与 z向传 动反 丝杠丝母 A 入 了 x 向反 向 间隙 ; 向间隙值 的测量方法相同。
数控机床反向间隙检测与补偿
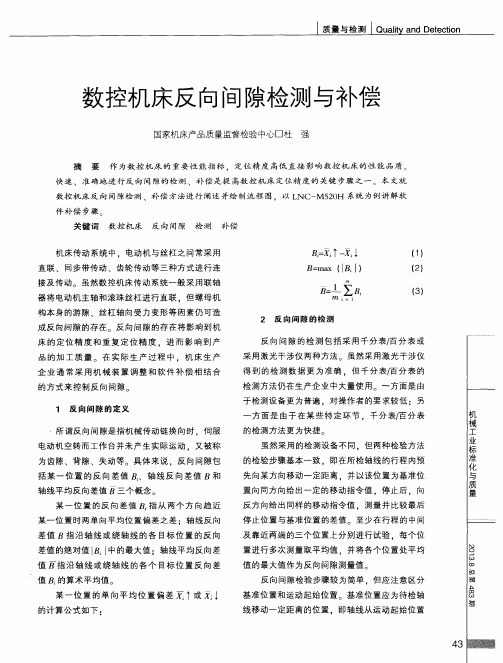
百 : ∑B
m : 1
构本 身的游 隙 、丝杠轴 向受 力变形等 因素仍 可造
成反 向间隙 的存在 反 向 间隙的存在 将影 响到机
2 反 向 间 隙 的检 测
床 的定 位 精 度 和 重 复 定位 精 度 .进 而 影 响到 产 品的 加 工质 量 。在 实 际 生产 过 程 中 ,机 床 生 产 企 业 通 常 采 用机 械 装 置 调 整和 软 件 补 偿相 结 合 的方 式来控 制反 向间 隙
经过机械 装置调整后 ,反 向间隙已符合机 床 组装 要求 。为 了进一 步减小反 向间隙 ,对数 控系 统进 行软件补偿是更 为方便 、快捷 的方式 。 根据实践 可知 ,反 向间隙的测 量值随着检 测 速 度 的不 同会 有 所 变化 。一 般 情况 。采 用 G0 1 切 削运 动速 度 的测量 值 比 G0 0快速运 动 速度 的
.
工 业 标 准
化
技 术人员在决定 采用何种检验 方法之前 ,应 根据机床 的具体 状况对反 向间 隙值进 行预判 。如 机 床传动机构 部装完毕或者 对丝杠施 加的预 紧力 调整之后 。反向间隙一般较 大。此 时对反 向间隙 的调 整属 于粗调 。强 调反 向 间隙值 的快速 检 出 ,
置 向同方 向给 出一定 的移 动指令值 ,停 止后 。向
某 一位 置 的 反 向差 值 指 从 两个 方 向趋 近
某一位 置 时两单 向平 均位置偏 差之 差 :轴 线反 向
反 方向给 出同样 的移动 指令值 .测量并 比较最后 停 止位置 与基 准位置 的差值 。至少在行 程的 中间 及 靠近 两端 的三 个位置 上分别进 行试验 .每个位 置进 行多次测量 取平均值 .并将 各个位 置处平均
数控机床的反向间隙测定及补偿参数设定

反向间隙是数控机床使用一段时间后必须要修整的技术参数,其测定及设定方法如下: 将百分表座吸附在工作台上,表头靠在正对主轴外圆面上,左右移动(X向是表头正对主轴侧面,前后移动)找到最高点。
先手轮方式选择Y向(X向)倍率选择X100;
朝正向连续移动三次(0.3mm)后记住当前百分表读数,然后反向移动一次(0.1mm )再读取当前百分表读数,两个值相减后被0.1mm相减得出的至即为当前的反向间隙值;
例如正向走是加表,三此后读数为0.56,反向一次后读数为0.47;那么实际还有反向间隙为:0.1-(0.56-0.48)=0.02mm;
所测得的反向间隙值减去0.01mm后乘1000(三菱是乘以2000)增加到参数中;
例如三菱系统(60S系列和70系列)2011当前值为48,上例测得反向间隙为0.02mm ,补偿时(0.02-0.01)*2000=20;那么2011的新的设定值为68;
设定好参数后最好按一次复位后机床关电后再上电,确保新参数生效。
系统反向间隙参数:
FAUNC(mate)MD:1851;1852;
三菱M64M70:2011;2012
SIEMENS808D828D840D:32450。
丝杠反向间隙实验
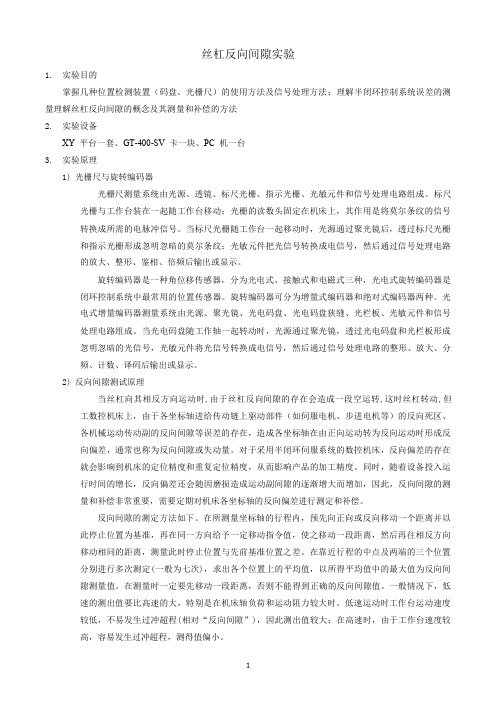
丝杠反向间隙实验1.实验目的掌握几种位置检测装置(码盘、光栅尺)的使用方法及信号处理方法;理解半闭环控制系统误差的测量理解丝杠反向间隙的概念及其测量和补偿的方法2.实验设备XY平台一套、GT-400-SV卡一块、PC机一台3.实验原理1)光栅尺与旋转编码器光栅尺测量系统由光源、透镜、标尺光栅、指示光栅、光敏元件和信号处理电路组成。
标尺光栅与工作台装在一起随工作台移动;光栅的读数头固定在机床上,其作用是将莫尔条纹的信号转换成所需的电脉冲信号。
当标尺光栅随工作台一起移动时,光源通过聚光镜后,透过标尺光栅和指示光栅形成忽明忽暗的莫尔条纹;光敏元件把光信号转换成电信号,然后通过信号处理电路的放大、整形、鉴相、倍频后输出或显示。
旋转编码器是一种角位移传感器,分为光电式、接触式和电磁式三种,光电式旋转编码器是闭环控制系统中最常用的位置传感器。
旋转编码器可分为增量式编码器和绝对式编码器两种。
光电式增量编码器测量系统由光源、聚光镜、光电码盘、光电码盘狭缝、光栏板、光敏元件和信号处理电路组成。
当光电码盘随工作轴一起转动时,光源通过聚光镜,透过光电码盘和光栏板形成忽明忽暗的光信号,光敏元件将光信号转换成电信号,然后通过信号处理电路的整形、放大、分频、计数、译码后输出或显示。
2)反向间隙测试原理当丝杠向其相反方向运动时,由于丝杠反向间隙的存在会造成一段空运转,这时丝杠转动,但工数控机床上,由于各坐标轴进给传动链上驱动部件(如伺服电机、步进电机等)的反向死区、各机械运动传动副的反向间隙等误差的存在,造成各坐标轴在由正向运动转为反向运动时形成反向偏差,通常也称为反向间隙或失动量。
对于采用半闭环伺服系统的数控机床,反向偏差的存在就会影响到机床的定位精度和重复定位精度,从而影响产品的加工精度。
同时,随着设备投入运行时间的增长,反向偏差还会随因磨损造成运动副间隙的逐渐增大而增加,因此,反向间隙的测量和补偿非常重要,需要定期对机床各坐标轴的反向偏差进行测定和补偿。
反向间隙[整理]
![反向间隙[整理]](https://img.taocdn.com/s3/m/142b411c78563c1ec5da50e2524de518964bd3f6.png)
反向间隙丝杆(丝杠)反向间隙又称丝杠背隙、丝杠间隙、丝杠失动量在数控机床的进给传动链中.齿轮传动、滚珠丝杠:螺母副等均存在反向间隙,这种厦向间隙的存在会造成机床丁作台反向运动时,伺服电动机空转而工作台实际不运动。
对于采用半闭环伺服系统的数控机球.反向问隙的存在会影响到机床的定位精度和重复定位精度,从而影响到产品的加工精度这就需要数挫系统提供反向间隙补偿功能,以便在加工过程中自动补偿一些有规律的误差,提高加工零件的精度。
并且随着数控机床使用时删的增长,反向间隙还会因磨损造成的运动副间隙的增大而逐渐增加,因此需定期对数控机床各坐标轴的反向问隙进行测定和补偿。
1.反向间隙补偿过程在数控系统无补偿的条件下,于机床测量行程范围内,在靠近行程的中点及两端的三个位置上分别进行多次测量,用千分表或百分表测量m各日标点位置P的平均反向间隙B.以所得平均值中的最大值为反向隙值B,并输人到数控系统反向间隙补偿参数中。
CNC系统在控制坐标轴反向运动时,自动先让该标轴反向运动,然后再按指令进行运动.即数控系统会控制伺服电动机多走一段距离,这段距离等等于反向间隙值B.从而补偿反向间隙。
需要指出的是这种方法只适合于半闭环数控系统.对于全闭环数控系统则不能采取以上补偿办法。
2.反向间隙补偿方法可使用激光干涉仪和百分表/千分表百分表/千分表方法:用手脉发生器移动相关轴,(将手脉倍率定为1×100的挡位,即每变化一步,电机进给0.1mm),配合百分表观察相关轴的运动情况。
在单向运动精度保持正常后作为起始点的正向运动,手脉每变化一步,机床该轴运动的实际距离d=d1=d2=d3…=0.1mm,说明电机运行良好,定位精度良好。
而返回机床实际运动位移的变化上,可以分为四个阶段:①机床运动距离d1>d=0.1mm(斜率大于1);②表现出为d=0.1mm>d2>d3(斜率小于1);③机床机构实际未移动,表现出最标准的反向间隙;④机床运动距离与手脉给定值相等(斜率等于1),恢复到机床的正常运动。
减速机 角传动精度测试方法
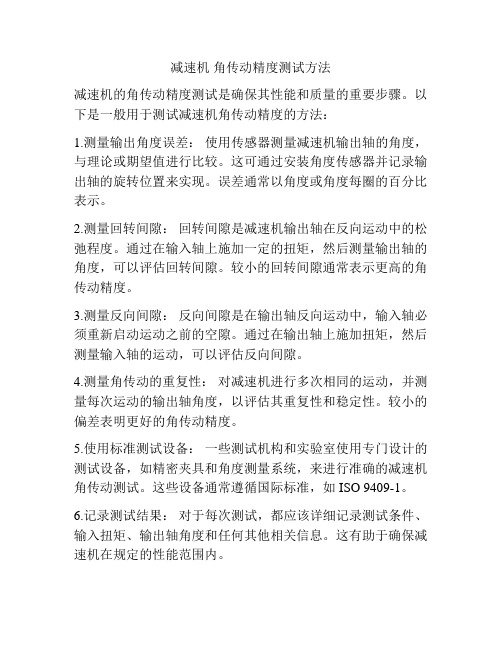
减速机角传动精度测试方法
减速机的角传动精度测试是确保其性能和质量的重要步骤。
以下是一般用于测试减速机角传动精度的方法:
1.测量输出角度误差:使用传感器测量减速机输出轴的角度,与理论或期望值进行比较。
这可通过安装角度传感器并记录输出轴的旋转位置来实现。
误差通常以角度或角度每圈的百分比表示。
2.测量回转间隙:回转间隙是减速机输出轴在反向运动中的松弛程度。
通过在输入轴上施加一定的扭矩,然后测量输出轴的角度,可以评估回转间隙。
较小的回转间隙通常表示更高的角传动精度。
3.测量反向间隙:反向间隙是在输出轴反向运动中,输入轴必须重新启动运动之前的空隙。
通过在输出轴上施加扭矩,然后测量输入轴的运动,可以评估反向间隙。
4.测量角传动的重复性:对减速机进行多次相同的运动,并测量每次运动的输出轴角度,以评估其重复性和稳定性。
较小的偏差表明更好的角传动精度。
5.使用标准测试设备:一些测试机构和实验室使用专门设计的测试设备,如精密夹具和角度测量系统,来进行准确的减速机角传动测试。
这些设备通常遵循国际标准,如ISO 9409-1。
6.记录测试结果:对于每次测试,都应该详细记录测试条件、输入扭矩、输出轴角度和任何其他相关信息。
这有助于确保减速机在规定的性能范围内。
在进行测试之前,建议参考减速机的制造商提供的技术规格和使用手册,以确保正确执行测试并满足相关的性能标准。
数控机床反向间隙的测量与补偿
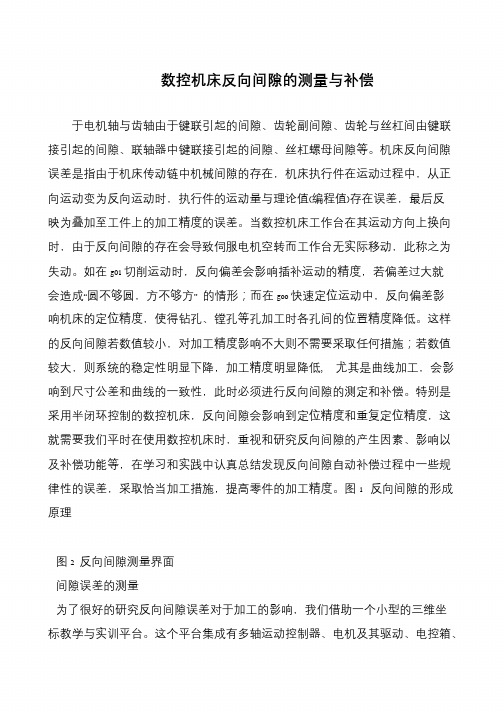
数控机床反向间隙的测量与补偿
于电机轴与齿轴由于键联引起的间隙、齿轮副间隙、齿轮与丝杠间由键联接引起的间隙、联轴器中键联接引起的间隙、丝杠螺母间隙等。
机床反向间隙误差是指由于机床传动链中机械间隙的存在,机床执行件在运动过程中,从正向运动变为反向运动时,执行件的运动量与理论值(编程值)存在误差,最后反
映为叠加至工件上的加工精度的误差。
当数控机床工作台在其运动方向上换向时,由于反向间隙的存在会导致伺服电机空转而工作台无实际移动,此称之为失动。
如在g01 切削运动时,反向偏差会影响插补运动的精度,若偏差过大就会造成“圆不够圆,方不够方”的情形;而在goo 快速定位运动中,反向偏差影响机床的定位精度,使得钻孔、镗孔等孔加工时各孔间的位置精度降低。
这样的反向间隙若数值较小,对加工精度影响不大则不需要采取任何措施;若数值较大,则系统的稳定性明显下降,加工精度明显降低, 尤其是曲线加工,会影响到尺寸公差和曲线的一致性,此时必须进行反向间隙的测定和补偿。
特别是采用半闭环控制的数控机床,反向间隙会影响到定位精度和重复定位精度,这就需要我们平时在使用数控机床时,重视和研究反向间隙的产生因素、影响以及补偿功能等,在学习和实践中认真总结发现反向间隙自动补偿过程中一些规律性的误差,采取恰当加工措施,提高零件的加工精度。
图1 反向间隙的形成原理
图2 反向间隙测量界面
间隙误差的测量
为了很好的研究反向间隙误差对于加工的影响,我们借助一个小型的三维坐标教学与实训平台。
这个平台集成有多轴运动控制器、电机及其驱动、电控箱、。
浅析数控机床反向间隙检测与控制
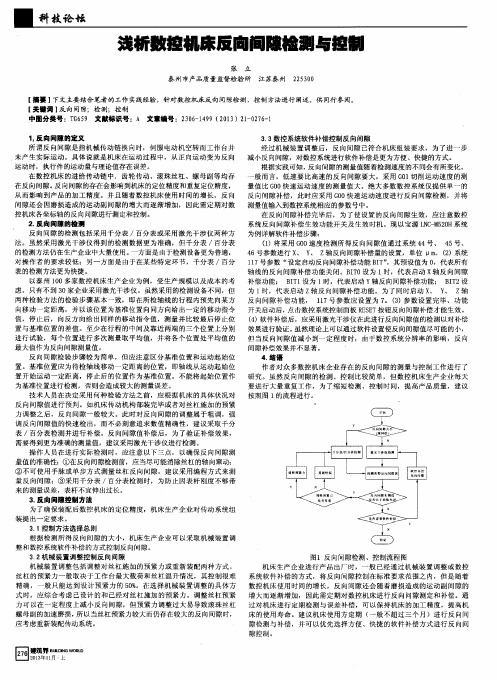
浅析数控机床反向问隙检测与控制
张 立
泰 州市产品质量监督 检验 所
江苏 笔者 的工作 实践经验 ,针对数控机床反 向间隙检测 、控制方法进行阐述。供 同行参 阅。 【 关键词 】 反向间隙;检 测;控制 中图分类号:T G 6 5 9 文献标识号 :h 文章编号 :2 3 0 6 — 1 4 9 9( 2 0 1 3 ) 2 1 — 0 2 7 6 - 1
1 . 反向间隙的定义 所谓反 向间隙是指机械传 动链换 向时,伺服 电动机空转而工 作台并 未产生 实际运动。具体说就 是机床在运动过程 中,从正 向运动变 为反 向 运动时 ,执行件的运 动量 与理论值存在误差。 在数控机 床的进给传动链 中.齿轮传动 、滚珠 丝杠、螺母 副等均存 在反 向间隙。反向间隙的存在会影响到机床的定位精度和重 复定位精度 , 从而影 响到产品 的加工精 度。并且随着数控机 床使用时 间的增 长,反 向 间隙还 会因磨损造成 的运 动副间 隙的增 大而逐渐增加 ,因此 需定期对数 控机床各坐标轴的反 向问隙进行测 定和控制 。 2 . 反向间隙的检测 反 向间隙的检测包括采用 千分表 /百分表 或采用激光干涉 仪两种方 法 。虽然采 用激光干涉 仪得到 的检测 数据更为准确 ,但千 分表 /百分表 的检测方法仍在生产企业中大量使用 。 一方面是 由于检测 设备更 为普遍 , 对操 作者的要求较低 :另一方面是 由于在某些特定环节 ,千分表 /百分 表 的检测方法更为快捷。 以泰州 1 0 0多家数控机床 生产企业 为例 ,受生产规模 以及 成本的考 虑 ,只有不到 3 O家企业采用激光干涉仪 。虽然采用 的检测设备不 同,但 两种检 验方法的检验步 骤基本一致 ,即在所 检轴线 的行程 内预先 向某方 向移动 一定距离 ,并 以该位置为基准位 置向同方 向给 出一定的移动指令 值 ,停 止后,向反方 向给 出同样 的移动 指令值,测量并 比较 最后停止位 置与基 准位置 的差值 。至少在行程 的中间及靠近两端 的三 个位置上分别 进行试 验,每个位置进 行多次测量取平 均值,并将各个位 置处平均值 的 最 大 值 作 为 反 向间 隙 测 量 值 。 反 向间隙检验步骤较 为简单 ,但应注 意区分基准位 置和运动起始位 置。基 准位置应为待检 轴线移动一 定距离的位置 ,即轴 线从运动起始位 置 开始运动一定距 离,停止后 的位 置作为基准位置 。不 能将起始位置 作 为基准位置进行检测 ,否则会造成较大的测量误差 。 技 术人员在决 定采 用何种检验方 法之前 ,应根据机床 的具体状况对 反向间隙值进行 预判。如机床传 动机 构部装完毕或 者对 丝杠施加 的预 紧 力调整之后 ,反 向间隙一般较 大。此 时对反 向间隙的调整属于粗 调,强 调反 向间 隙值 的快速检 出,而不 必刻意追求数值精 确性,建议采取干 分 表 /百分表检测 并进行补偿 。反向间隙值补偿后 ,为了验证补偿 效果, 需要得到更 为准确 的测量值 ,建议采用激光干涉 仪进行检测 。 操作人员在进 行实际检测 时,应 注意 以下三 点,以确保反 向间隙测 量值的准确 性:①在反向间隙检测前 ,应 当尽可能消除丝杠的轴 向窜动; ②不可使用 手脉或单步方 式测 量丝杠反 向间隙,建议采用编程 方式来测 量反 向间隙;③ 采用千分表 /百分表检测 时,为 防止因表杆刚度 不够带 来的测量误 差,表杆 不宜伸 出过长 。 3 . 反 向间隙控制方法 为了确保装配 后数控机床 的定位精度 ,机床 生产企业对传动 系统组 装 提 出一 定 要 求 。 3 . 1控 制 方 法选 择 总则 根据检测所 得反 向间隙的大小,机床生产企 业可 以采取机械 装置调 整和数控系统软件 补偿的方 式控制 反向间隙。 3 2机械装置调整控制反 向间隙 机 械 装 置调 整 包 括 调 整 对 丝 杠 施 加 的预 紧 力 或 重 新 装 配 两 种 方 式 。 丝杠 的预 紧力一般取决 于工作 台最大载荷 和丝杠温升情 况,其控制很难 精确 ,一般只能达 到设计预 紧力 的 5 0 9 6 。在 选择机械装 置调整 的具体方 式 时,应 综合考虑 已设计 的和 已经对丝杠 施加的预紧力 。调整 丝杠预紧 力可 以在 一定程度上减 小反 向间隙,但预 紧力调整过大 易导致滚珠丝杠 螺母副的加速磨损, 所 以当丝杠预紧力较大而仍存在较大的反向间隙时, 应考虑重新装配传动系统。
加工中心圆度误差的原因分析及调整方法【干货】
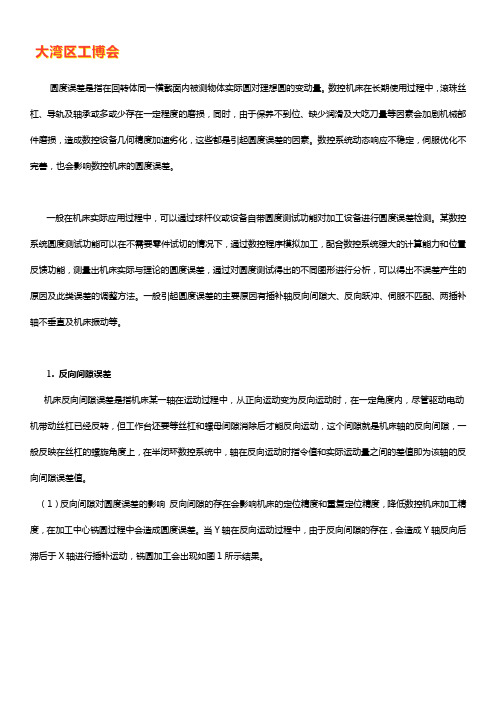
圆度误差是指在回转体同一横截面内被测物体实际圆对理想圆的变动量。
数控机床在长期使用过程中,滚珠丝杠、导轨及轴承或多或少存在一定程度的磨损,同时,由于保养不到位、缺少润滑及大吃刀量等因素会加剧机械部件磨损,造成数控设备几何精度加速劣化,这些都是引起圆度误差的因素。
数控系统动态响应不稳定,伺服优化不完善,也会影响数控机床的圆度误差。
一般在机床实际应用过程中,可以通过球杆仪或设备自带圆度测试功能对加工设备进行圆度误差检测。
某数控系统圆度测试功能可以在不需要零件试切的情况下,通过数控程序模拟加工,配合数控系统强大的计算能力和位置反馈功能,测量出机床实际与理论的圆度误差,通过对圆度测试得出的不同图形进行分析,可以得出不误差产生的原因及此类误差的调整方法。
一般引起圆度误差的主要原因有插补轴反向间隙大、反向跃冲、伺服不匹配、两插补轴不垂直及机床振动等。
1. 反向间隙误差机床反向间隙误差是指机床某一轴在运动过程中,从正向运动变为反向运动时,在一定角度内,尽管驱动电动机带动丝杠已经反转,但工作台还要等丝杠和螺母间隙消除后才能反向运动,这个间隙就是机床轴的反向间隙,一般反映在丝杠的螺旋角度上,在半闭环数控系统中,轴在反向运动时指令值和实际运动量之间的差值即为该轴的反向间隙误差值。
(1)反向间隙对圆度误差的影响反向间隙的存在会影响机床的定位精度和重复定位精度,降低数控机床加工精度,在加工中心铣圆过程中会造成圆度误差。
当Y轴在反向运动过程中,由于反向间隙的存在,会造成Y轴反向后滞后于X轴进行插补运动,铣圆加工会出现如图1所示结果。
图1 反向间隙造成的圆度误差(2)反向间隙测量与调整影响机床轴反向间隙误差的因素多种多样,从驱动电动机到运动部件之间所有的机械联接件都会存在间隙,电动机对丝杠的联轴结是否松动、滚珠丝杠制造误差、丝杠预紧是否过紧或过松、丝母与运动部件联接是否紧固,都是造成机床轴反向间隙的原因。
对于机械部分无法消除的间隙,需要在数控系统中对反向间隙进行补偿。
测量滚珠丝杠驱动的反向间隙手动测定

测量滚珠丝杠驱动的反向间隙手动测定
在三爪卡盘上或者夹钳上夹紧一个车过端面的圆形棒料。
2 在刀架上固定一个分辨率为1/1000的量表。
3 在夹紧的车削件上压表,直到测棒快接触到挡铁(进给f=200mm/min)。
4 滑台退回,直到量表的指针停在有效显示范围内(f=150mm/min)。
5 把表针对“0”。
6 滑台退回3mm(量表未压上)(f=150mm/min)。
7 滑台前进3mm,回到零位(f=150mm/min)。
8 在量表上读出显示值并记录(每个与“0”有出入的值即是反向间隙值)。
9 重复测量5次,求出平均值。
分别用G0和G1编程得出G0反向间隙和G1反向间隙值。
10 将计算出的平均值作为间隙补偿值输入系统参数#xx(G0间隙)和#xx(G1间隙)。
注: Mitsubishi T65 中,参数#xx和#xx的单位为<指令单位/2> ,即得出的反向间隙值
x2。
注意:如果X轴的反向间隙超过0、02mm,Z轴的反向间隙超过0、03mm,就应该由服务人员进行修正。
第 1 页共 1 页。
机床的反向间隙补偿原理

机床的反向间隙补偿原理机床的反向间隙补偿是为了解决机床加工过程中因为间隙导致的不精确问题而引入的一种补偿方法。
间隙是指机床在进行工件加工时,由于传动机构、结构松弛、刚度不足等原因而产生的相对位移,使得加工结果与期望值有一定的偏差。
反向间隙补偿的原理是通过测量间隙大小,然后在加工过程中对其进行补偿,以提高加工精度。
机床的反向间隙补偿原理可以分为以下几个步骤:1. 间隙检测:首先需要对机床的传动机构、结构松弛等进行检测,确定其间隙的大小和位置。
常用的方法有机械量规法、激光干涉法、振动法等。
通过这些方法可以准确测量出机床的间隙尺寸。
2. 补偿计算:根据测量得到的间隙尺寸,可以进行补偿计算。
具体的计算方法根据机床的不同类型和不同间隙特点而有所不同。
一般来说,可以根据间隙的大小和加工过程中的位置,以及工件的尺寸和形状,通过计算机算法来确定合适的补偿值。
3. 补偿控制:将计算得到的补偿值输入到机床的控制系统中,通过控制系统对机床的运动轴进行补偿控制。
具体的控制方式有闭环控制和开环控制两种。
闭环控制是指通过反馈信号对补偿值进行实时调整,以达到期望的加工精度。
开环控制是指根据预先设定的补偿值,直接对机床的运动轴进行控制。
4. 加工过程中的补偿:在机床进行工件加工时,补偿控制系统会自动对机床的运动轴进行补偿操作。
当机床的传动机构发生间隙时,补偿控制系统会根据预设的补偿值,使机床的运动轴根据补偿值进行调整,以使加工结果更加精确。
5. 精度验证:经过补偿操作后,需要进行加工结果的精度验证。
可以通过测量已加工工件的尺寸、形状等指标来进行验证。
如果验证结果与期望值相符,说明补偿效果良好;如果出现偏差,则需要重新调整补偿值。
综上所述,机床的反向间隙补偿原理是通过测量机床的间隙尺寸,并根据测量结果进行补偿计算和控制,以提高加工精度。
这种补偿方法可以有效地减小加工误差,提高工件的质量和精度,对于一些精密加工要求较高的行业具有重要的意义。
四轴反向间隙参数
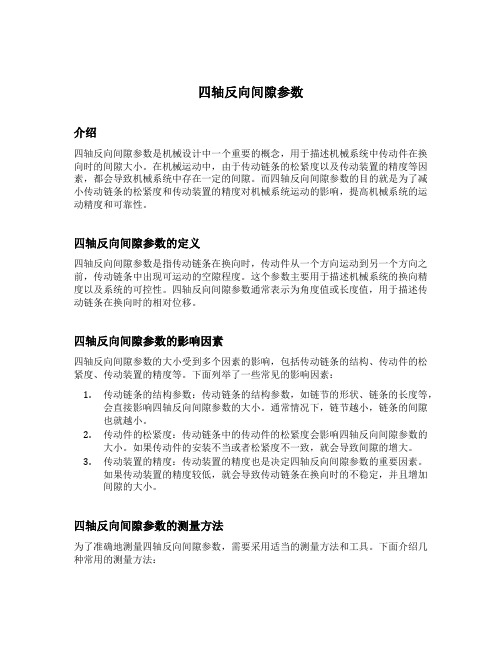
四轴反向间隙参数介绍四轴反向间隙参数是机械设计中一个重要的概念,用于描述机械系统中传动件在换向时的间隙大小。
在机械运动中,由于传动链条的松紧度以及传动装置的精度等因素,都会导致机械系统中存在一定的间隙。
而四轴反向间隙参数的目的就是为了减小传动链条的松紧度和传动装置的精度对机械系统运动的影响,提高机械系统的运动精度和可靠性。
四轴反向间隙参数的定义四轴反向间隙参数是指传动链条在换向时,传动件从一个方向运动到另一个方向之前,传动链条中出现可运动的空隙程度。
这个参数主要用于描述机械系统的换向精度以及系统的可控性。
四轴反向间隙参数通常表示为角度值或长度值,用于描述传动链条在换向时的相对位移。
四轴反向间隙参数的影响因素四轴反向间隙参数的大小受到多个因素的影响,包括传动链条的结构、传动件的松紧度、传动装置的精度等。
下面列举了一些常见的影响因素:1.传动链条的结构参数:传动链条的结构参数,如链节的形状、链条的长度等,会直接影响四轴反向间隙参数的大小。
通常情况下,链节越小,链条的间隙也就越小。
2.传动件的松紧度:传动链条中的传动件的松紧度会影响四轴反向间隙参数的大小。
如果传动件的安装不当或者松紧度不一致,就会导致间隙的增大。
3.传动装置的精度:传动装置的精度也是决定四轴反向间隙参数的重要因素。
如果传动装置的精度较低,就会导致传动链条在换向时的不稳定,并且增加间隙的大小。
四轴反向间隙参数的测量方法为了准确地测量四轴反向间隙参数,需要采用适当的测量方法和工具。
下面介绍几种常用的测量方法:1.针对角度值的测量方法:可以使用角度测量仪器,通过将测量仪器安装在传动链条上,测量传动件在换向时的角度变化,从而得到四轴反向间隙参数的角度值。
2.针对长度值的测量方法:可以使用测量卡尺或者游标卡尺等测量工具,测量传动链条在换向时传动件的相对位移,从而得到四轴反向间隙参数的长度值。
四轴反向间隙参数的优化方法为了减小四轴反向间隙参数的大小,提高机械系统的运动精度和可靠性,可以采取以下优化方法:1.优化传动链条的结构参数:合理设计传动链条的结构参数,如链节的形状、链条的长度等,可以减小传动链条中的间隙。
- 1、下载文档前请自行甄别文档内容的完整性,平台不提供额外的编辑、内容补充、找答案等附加服务。
- 2、"仅部分预览"的文档,不可在线预览部分如存在完整性等问题,可反馈申请退款(可完整预览的文档不适用该条件!)。
- 3、如文档侵犯您的权益,请联系客服反馈,我们会尽快为您处理(人工客服工作时间:9:00-18:30)。
数控机床反向间隙的测定方法
反向间隙的测定方法:在所测量坐标轴的行程内,预先向正向或反向移动一个距离并以此停止位置为基准,再在同一方向给予一定移动指令值,使之移动一段距离,然后再往相反方向移动相同的距离,测量停止位置与基准位置之差。
在靠近行程的中点及两端的三个位置分别进行多次测定(一般为七次),求出各个位置上的平均值,以所得平均值中的最大值为反向偏差测量值。
在测量时一定要先移动一段距离,否则不能得到正确的反向偏差值。
测量直线运动轴的反向偏差时,测量工具通常采有千分表或百分表,若条件允许,可使用双频激光干涉仪进行测量。
当采用千分表或百分表进行测量时,需要注意的是表座和表杆不要伸出过高过长,因为测量时由于悬臂较长,表座易受力移动,造成计数不准,补偿值也就不真实了。
若采用编程法实现测量,则能使测量过程变得更便捷更精确。
例如,在三坐标立式机床上测量X轴的反向偏差,可先将表压住主轴的圆柱表面,然后运行如下程序进行测量:
N10 G91 G01 X50 F1000;工作台右移
N20 X-50;工作台左移,消除传动间隙
N30 G04 X5;暂停以便观察
N40 Z50;Z轴抬高让开
N50 X-50:工作台左移
N60 X50:工作台右移复位
N70 Z-50:Z轴复位
N80 G04 X5:暂停以便观察
N90 M99;
需要注意的是,在工作台不同的运行速度下所测出的结果会有所不同。
一般情况下,低速的测出值要比高速的大,特别是在机床轴负荷和运动阻力较大时。
低速运动时工作台运动速度较低,不易发生过冲超程(相对“反向间隙”),因此测出值较大;在高速时,由于工作台速度较高,容易发生过冲超程,测得值偏小。
回转运动轴反向偏差量的测量方法与直线轴相同,只是用于检测的仪器不同而已。