协同仿真的一些资料
平台支撑下的仿真协同与设计优化

企业级材料数据管理(ANSYS Granta解决方案)
企业私有数据录入测试,研发,质量评估,设计, 仿真,供应商…
数据接口支持PLM, CAD, CAE系统
数据管理浏览,搜索 & 报告生成
数据分析可视化 & 辅助决策
流程管理
参考数据库金属,塑料,复合材料,陶瓷, 玻璃,涂料…
14
Ansys 综合解决方案打造仿真协同创新及设计优化平台
optimal performance parameters materials research and test calibration
仿真数据分析挖掘
Re-imagine simulation to model cause and effect to compute futureoutcomes with AI & deep learning baked in
仿真与试验协同
数据连续性
5
Minerva:以仿真流程与数据管理为核心,支持仿真协同创新
Workbench
Ansys Minerva
部署环境
On-Premise
Public Cloud
Private Cloud
Graphic Server
权限管理
门户
作业管理
工作区
业务管控
多物理场 仿真
项目管理
仿真报告
CAE
4
试做
试验
Redesign
CAE
试做
试验
Redesign
CAE
试做
试验
仿真验证
仿真早期介入,与需求管理、系统设计协同不同阶段仿真的连续性、协同、重用设计变更及仿真验证协同迭代仿真与试验验证对比协同
协同仿真是怎样炼成的
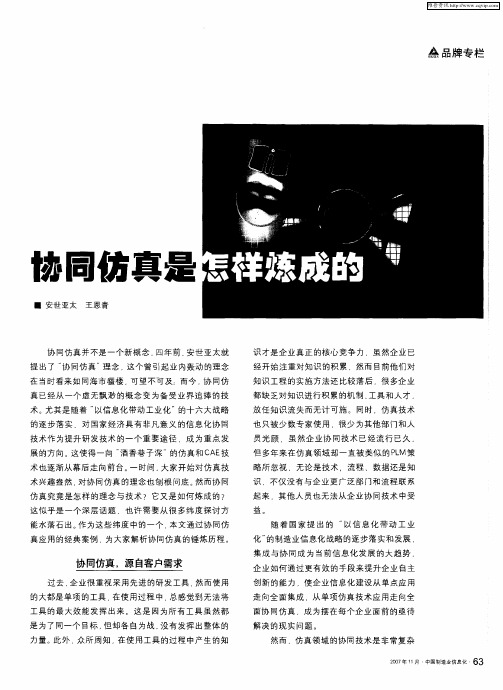
协 同仿真 ,源自客户需求
过去 业很 重视 采 用先 进 的研 发 工具 然 而使 用 企
的 大都是 单 项 的工 具 在使 用过 程 中 总感 觉 到无 法 将 工 具 的最 大效 能 发 挥 出来 。这 是 因 为所 有 工具 虽 然 都
企 业 如何 通过 更 有效 的手 段 来提 升企 业 自主
识 才是 企 业真 正 的核 心 竞争 力 ,虽 然企 业 已 经 开 始 注重 对知 识 的积 累 ,然而 目前 他 们对 知识 工程 的 实施 方 法还 比较 落 后 ,很 多企 业 都缺 乏对 知识 进 行积 累 的机 制 、 具和 人 才 , 工 放 任知 识 流 失而 无计 可 施 。 同时 ,仿 真 技术
快速 实 现不 同 类型 的飞 行器 设 计方 案优 化 流
程。
案例 三 :电子产 品 多学 科优 化
C E 电子 工业 方面 是 非 常重 要 的一部 A在
次 开 发 满 足 了客 户 提 出 的模 型 快 速 自动 简化 和 I— n hue os 求解 器 的可 视化 的有 限元 通用 前后 处 理需 求 。对
能 水落 石 出 。 为 这些 纬 度 中的一 个 , 文通 过协 同仿 作 本
真 应 用的经 典 案例 , 为大 家解 析协 同仿 真 的锤 炼历 程 。
随 着 国 家 提 出 的 以信 息 化 带 动 工 业
化” 的制 造 业信 息化 战 略 的逐 步落 实和 发 展 ,
集 成 与 协 同成 为 当前 信 息 化 发 展 的 大趋 势
PR E A具 备 行 业通 用 的技 术 , 以实 现 功能 上 的 交 可 钥匙 , 后 根据 不 同企 业 的特点 , 行 定制 服 务 。 然 进 该项
基于MATLABSIMULINK与FLUENT的协同仿真方法研究
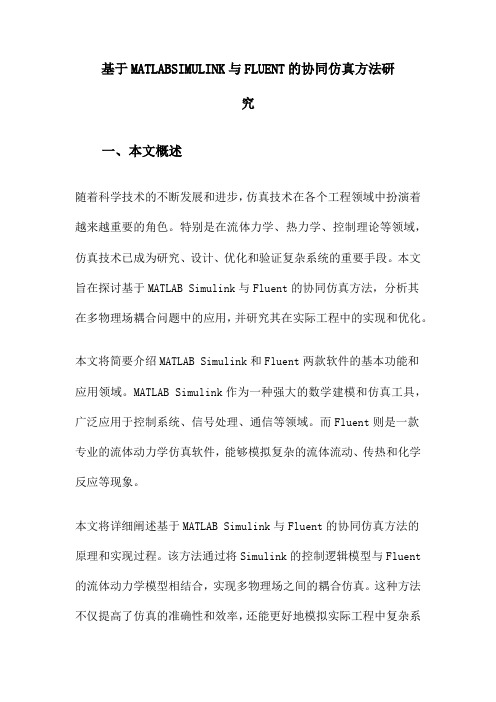
基于MATLABSIMULINK与FLUENT的协同仿真方法研究一、本文概述随着科学技术的不断发展和进步,仿真技术在各个工程领域中扮演着越来越重要的角色。
特别是在流体力学、热力学、控制理论等领域,仿真技术已成为研究、设计、优化和验证复杂系统的重要手段。
本文旨在探讨基于MATLAB Simulink与Fluent的协同仿真方法,分析其在多物理场耦合问题中的应用,并研究其在实际工程中的实现和优化。
本文将简要介绍MATLAB Simulink和Fluent两款软件的基本功能和应用领域。
MATLAB Simulink作为一种强大的数学建模和仿真工具,广泛应用于控制系统、信号处理、通信等领域。
而Fluent则是一款专业的流体动力学仿真软件,能够模拟复杂的流体流动、传热和化学反应等现象。
本文将详细阐述基于MATLAB Simulink与Fluent的协同仿真方法的原理和实现过程。
该方法通过将Simulink的控制逻辑模型与Fluent 的流体动力学模型相结合,实现多物理场之间的耦合仿真。
这种方法不仅提高了仿真的准确性和效率,还能更好地模拟实际工程中复杂系统的动态行为。
本文将通过具体案例,展示基于MATLAB Simulink与Fluent的协同仿真方法在实际工程中的应用。
通过对案例的详细分析和讨论,揭示该方法在解决实际问题中的优势和潜力,并为相关领域的研究和应用提供参考和借鉴。
本文旨在深入研究基于MATLAB Simulink与Fluent的协同仿真方法,探索其在多物理场耦合问题中的应用和优化策略,为相关领域的工程实践和技术创新提供有力支持。
二、MATLAB/SIMULINK简介MATLAB/Simulink是MathWorks公司开发的一款广泛应用于数学计算、算法开发、数据可视化以及数值计算的高级编程语言和交互式环境。
MATLAB以其高效的数值计算能力和丰富的函数库,在科学计算、工程设计和数据分析等领域具有广泛的应用。
用于SPICE电路的微控制器(MCU)协同仿真功能简介

用于SPICE电路的微控制器(MCU)协同仿真功能简介目录1.概览2.开始前的准备工作3.创建一个新的MCU工程4.输入源代码及添加其它工程5.放置并连接外围组件6.仿真您的电路7.调试您的源代码8.在活动工程之间切换9.更多资源概览NI Multisim MCU模块为Multisim软件增添了微控制器(microcontroller unit)协同仿真功能,从而使得您可以在使用SPICE建模的电路中加入一个可使用汇编语言或C语言进行编程的微控制器。
Multisim MCU模块使得学生、教师以及专业用户可以在熟悉的Multisim环境中以汇编语言或C语言对MCU进行编程。
这个MCU模块可与Multisim中任意一个虚拟仪器共同使用以实现一个完整的系统仿真,包括微控制器以及全部所连接的模拟和数字SPICE元件。
Multisim MCU模块支持Intel®/Atmel® 8051/8052和Microchip PIC16F84a芯片以及众多高级的外围器件,例如外部RAM和ROM、键盘、图形型和字符型液晶等等。
MCU模块充分利用了Multisim软件的教育平台功能从而使得它成为许多电子类课程的理想选择,例如数字电路、计算机体系结构、MCU编程、嵌入式系统控制、高级设计以及其他相关课程!开始前的准备工作本指南要求Multisim MCU模块已被激活或者处于有效的试用期内,而且建议您已对标准的NI Multisim软件环境有所了解。
附带的文档包括了完成此指南所需的全部文件。
但是,本指南只是说明了如何从零开始创建一个MCU模块工程,而没有解释源文件。
本指南中所使用的MCU工程是利用Microchip公司的PIC16F84芯片来演示一个简单的加碱计数器。
微控制器的端口A配置为输入并连接到两个开关,而端口B 则配置为输出并连接到一个7段显示器。
两个开关用以打开或关闭显示器以及改变计数方向。
7段显示器以十六进制显示了当前的计数器数值(0-F)。
系统工程中的协同设计与仿真研究

系统工程中的协同设计与仿真研究一、引言协同设计与仿真是系统工程发展的重要方向,其目的在于将多个设计模块相互连接、相互协作,从而提高系统设计效率和设计质量。
在工程实践中,协同设计与仿真可以有效地提升系统设计和开发效率,并降低成本和风险。
本文将就协同设计与仿真在系统工程中的应用研究进行探讨。
二、协同设计协同设计是指将信息和资源整合在一个平台上,使得设计团队内部和外部的成员能够相互协同工作,解决设计和开发中的问题。
在系统工程设计中,常用的协同设计软件如CATIA、SolidWorks和NX等。
1、CATIACATIA是由法国达索公司开发的一款CAD/CAM/CAE软件。
CATIA的协同设计功能旨在提供一个统一的设计平台,囊括了从概念设计到工艺设计的全过程。
CATIA的设计团队可以基于CATIA提供的协同设计环境进行团队交流、协作和控制。
2、SolidWorksSolidWorks是一种面向工程设计领域的CAD软件。
SolidWorks 的协同设计功能集成在其产品数据管理(PDM)模块中。
PDM可提供一种安全、便捷和可靠的数据存储系统,使得设计团队随时随地都可以对设计数据进行访问和共享。
3、NXNX是由西门子公司开发的一款强大的CAD/CAM软件。
NX的协同设计功能支持多种多样的工作方式,如实时协同、缓冲区协同等。
需要多个设计团队协作完成的项目,可以通过NX构建一个同步的设计平台,实现团队之间的无缝协作。
三、协同仿真协同仿真是指将仿真结果与实际设计进行无缝连接,从而能够综合考虑不同设计因素,逐步提高系统设计和开发的效率和质量。
下面我们看几种常用的协同仿真软件。
1、AnsysAnsys是一款基于有限元分析的仿真软件。
Ansys的协同仿真功能允许设计师在设计和分析过程中进行多因素、多阶段的综合仿真。
Ansys的仿真结果可作为设计的重要参考依据,以便设计师可以简化和改进设计。
2、SimulinkSimulink是一种基于MATLAB环境下的可视化仿真软件。
17、ANSYSWorkbench协同仿真环境中文培训资料

动力学分析简介M1-1M1-2动力学第一节: 定义和目的什么是动力学分析?•动力学分析是用来确定惯性(质量效应)和阻尼起重要作用时的结构或构件动力学特性的技术。
•“动力学特性”可能指的是下面的一种或几种类型:–振动特性-(结构振动方式和振动频率)–随时间变化载荷的效应(例如:对结构位移和应力的效应)–周期(振动)或随机载荷的效应M1-3总之,动力学分析有下列类型:Courtesy: NASA动力学动力学分析类型(接上页)•模态分析---确定结构的振动特性•瞬态动力学分析---计算结构对随时间变化载荷的响应•谐响应分析---确定结构对稳态简谐载荷的响应•谱分析---确定结构对地震载荷的响应•随机振动分析---确定结构对随机震动的影响M1-4动力学第三节: 基本概念和术语•通用运动方程•求解方法•建模要考虑的因素•质量矩阵•阻尼M1-5动力学-基本概念和术语运动方程•通用运动方程如下:[]{}[]{}[]{}(){}t F u K u C uM =++ •不同分析类型对应求解不同形式的方程–模态分析:设定F (t )为零,而矩阵[C] 通常被忽略;–谐响应分析:假设F (t )和u (t )都为谐函数,例如Xsin (ωt ),其中,X 是振幅,ω是单位为弧度/秒的频率;–瞬间动态分析:方程保持上述的形式。
其中:[M]= 结构质量矩阵[C]= 结构阻尼矩阵[K]= 结构刚度矩阵{F}= 随时间变化的载荷函数{u}= 节点位移矢量{ů}= 节点速度矢量{ü}= 节点加速度矢量M1-6动力学-基本概念和术语求解方法如何求解通用运动方程?•两种主要方法:–模态叠加法–直接积分法M1-7动力学-基本概念和术语求解方法(接上页)直接积分法•直接求解运动方程•在谐响应分析中,因为载荷和响应都假定为谐函数,所以运动方程是以干扰力频率的函数而不是时间的函数的形式写出并求解的•对于瞬态动力学,运动方程保持为时间的函数,并且可以通过显式或隐式的方法求解模态叠加法•确定结构的固有频率和模态,乘以正则化坐标,然后加起来用以计算位移解•可以用来处理瞬态动力学分析和谐响应分析•详见后面相关章节M1-8动力学-基本概念和术语求解方法(接上页)显式求解方法•也称为闭式求解法或预测求解法•不需要计算矩阵的逆•可轻松处理非线性问题(无收敛问题)•积分时间步Δt 必须很小,但求解速度很快(没有收敛问题)•对于短时间的瞬态分析有效,如用于波的传播,冲击载荷和高度非线性问题•当前时间点的位移{u}t 由包含时间点t-1的方程推导出来•有条件稳定: 如果Δt 超过结构最小周期的确定百分数,计算位移和速度将无限增加•ANSYS-LS/DYNA 就是使用这种方法,此处不作介绍隐式求解法•也称为开式求解法或修正求解法•要求矩阵的逆•非线性要求平衡迭代(存在收敛问题)•积分时间步Δt 可以较大,但因为有收敛问题而受到限制•除了Δt 必须很小的问题以外,对大多数问题都是有效的•当前时间点的位移{u}t 由包含时间点t 的方程推导出来•无条件稳定: Δt 的大小仅仅受精度条件控制, 无稳定性。
《hfss的协同仿真》课件
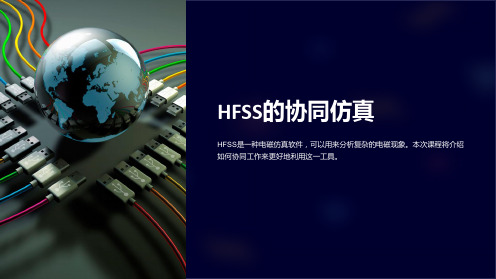
HFSS是一种电磁仿真软件,可以用来分析复杂的电磁现象。本次课程将介绍 如何协同工作来更好地利用这一工具。
什么是HFSS
功能强大
可以模拟各种电磁场问题,如天线、波导、传输线、滤波器等。非常适用于高频电路的设 计和分析。
广泛应用
HFSS被广泛应用于电子、通信、汽车、医疗器械等各个领域,帮助工程师快速解决问题。
电路仿真
利用HFSS进行天线系统和滤波器电路的仿 真,协同完成设计和测试,优化电路性能。
材料设计仿真
设计能够阻止辐射照射的防护材料,有效保 护人体健康。
医疗器械仿真
仿真手术过程中的操作流程和切割角度,提 高手术的准确率和安全性。
电子器件仿真
利用HFSS模拟电磁场分布情况,对市场上 的产品进行仿真并进行制造优化。
实验辅助
通过仿真实验来预测电磁场的行为,设计更加高效、精准。
HFSS的协同仿真特点
1
团队合作
多人同时参与一个项目,可以快速协同完成模拟、仿真等各个环节,大大提高了 效率。
2
多工程协同
不同部门之间的工程师可以通过HFSS协同工作,较好地解决了分布式工作组的 跨地域、跨部门的交流问题。
3
智能优化
HFSS可以自动进行仿真参数优化和智能设计,大大缩短仿真和设计时间,提高 了工作效率。
医学领域
例如医疗器械、放射治疗等, 帮助提高诊断的准确率和治 疗的安全性。
航空航天
可以模拟复杂的空气动力学 问题,为航空、航天领域的 研发带来了前所未有的便利。
结论与展望
HFSS协同仿真的出现,为产品和工程设计带来了新的理念和方法。随着技术 的发展,相信协同仿真将在更多领域创造价值。
多机协同控制系统的建模与仿真

多机协同控制系统的建模与仿真近年来,随着工业自动化水平的不断提高,越来越多的机器人和自动化设备投入使用,这些设备具有独立的智能控制系统,但在某些应用场景下,需要多个设备协同完成任务。
因此,多机协同控制系统的设计和建模成为了近年来的研究热点之一。
本文将介绍多机协同控制系统的建模和仿真方法。
一、多机系统的基本构成多机协同控制系统是由多个单独的控制系统组成,通过通信或其他方式协同工作,完成特定的任务。
在多机系统中,每个独立的控制系统都可以看做是一个子系统,这些子系统之间通过信号或数据交换实现协同工作。
为了更好地理解多机协同控制系统的构成,我们先来了解一下单独控制系统的基本构成。
单独的控制系统包括三部分:传感器、执行机构和控制器。
传感器用于测量某些物理量,如温度、速度、角度等,将测量值转换成电信号后发送给控制器。
控制器对传感器采集的信号进行处理,根据预设的控制策略产生控制指令,将指令发送给执行机构。
执行机构将接收到的指令转换成机械运动或能量输出,实现对被控制对象的控制。
对于多机协同控制系统,其基本构成与单独控制系统类似,包括传感器、执行机构和控制器,但可能会涉及到网络通信模块和协同控制模块的设计。
二、多机协同控制系统的建模方法多机协同控制系统的建模方法有多种,其中最常用的是基于状态空间法的建模方法。
状态空间法是系统建模和分析中广泛使用的一种数学方法,其核心思想是将系统的输入、输出和状态转移关系用数学方程描述出来,然后将它们转化为矩阵形式,方便进行分析和求解。
在多机协同控制系统中,整个系统可以看做是若干个子系统的集合,每个子系统都有自己的输入、输出和状态。
因此,对于多机协同控制系统的建模,通常先建立子系统的状态方程,然后构建整个系统的状态方程,最后进行仿真和分析。
三、多机协同控制系统的仿真方法多机协同控制系统的仿真方法有多种,其中最常用的是基于MATLAB/Simulink的仿真方法。
MATLAB/Simulink是广泛应用于系统建模与仿真的软件平台,其提供了丰富的工具箱和函数库,能够方便地进行系统建模和仿真。
HFSS的协同仿真讲解
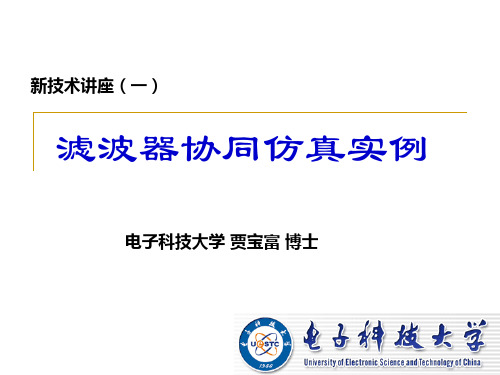
协同仿真定义设置
选择“Circuit”
Ansoft Designer Model
Port1
1:1
2:1
1:1
2:1
1:1
2:1
1:1
2:1
Port2 1:1
A=a B=b
2:1
1:1
A=a B=b
2:1
1:1
A=a B=b
2:1
A=a
A=a
A=a
B=b
B=b
B=b
Designer端口设置
Designer仿真设置
dB(S(Port2,Port1)) LinearFrequency
17.50
18.00
CST MWS模型
端口设置
扫频及对称性设置
基于模板的后处理设置
设置参数扫描并计算
导出ADS模型
在ADS中导入CST模型
在ADS中导入 CST模型(续)
在电路图中插入CST模型
电路图中放入波导
电路图中终端设置
仿真结果
Y1
0.00 -10.00 -20.00 -30.00 -40.00 -50.00 -60.00 -70.00 -80.00
14.50
15.00
15.50
XY Plot 1
16.00
F [GHz]
16.50
17.00
Circuit1 ANSOFT
Curve Info
dB(S(Port1,Port1)) LinearFrequency
-10.00
XY Plot 1
m1
m2
-20.00
-30.00
-40.00
-50.00
-60.00
emu软硬件协同仿真流程
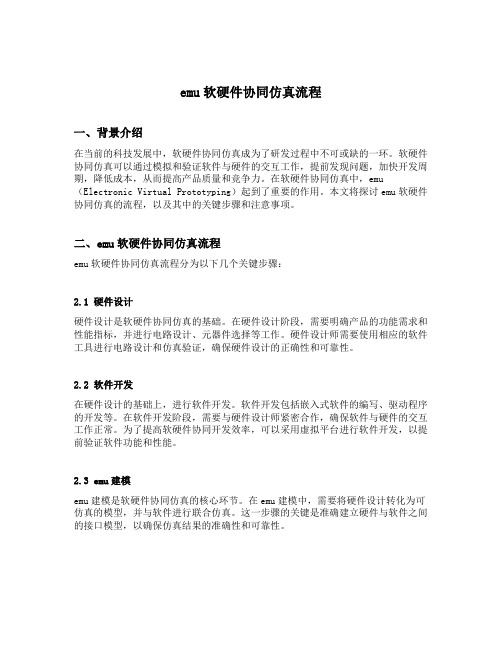
emu软硬件协同仿真流程一、背景介绍在当前的科技发展中,软硬件协同仿真成为了研发过程中不可或缺的一环。
软硬件协同仿真可以通过模拟和验证软件与硬件的交互工作,提前发现问题,加快开发周期,降低成本,从而提高产品质量和竞争力。
在软硬件协同仿真中,emu (Electronic Virtual Prototyping)起到了重要的作用。
本文将探讨emu软硬件协同仿真的流程,以及其中的关键步骤和注意事项。
二、emu软硬件协同仿真流程emu软硬件协同仿真流程分为以下几个关键步骤:2.1 硬件设计硬件设计是软硬件协同仿真的基础。
在硬件设计阶段,需要明确产品的功能需求和性能指标,并进行电路设计、元器件选择等工作。
硬件设计师需要使用相应的软件工具进行电路设计和仿真验证,确保硬件设计的正确性和可靠性。
2.2 软件开发在硬件设计的基础上,进行软件开发。
软件开发包括嵌入式软件的编写、驱动程序的开发等。
在软件开发阶段,需要与硬件设计师紧密合作,确保软件与硬件的交互工作正常。
为了提高软硬件协同开发效率,可以采用虚拟平台进行软件开发,以提前验证软件功能和性能。
2.3 emu建模emu建模是软硬件协同仿真的核心环节。
在emu建模中,需要将硬件设计转化为可仿真的模型,并与软件进行联合仿真。
这一步骤的关键是准确建立硬件与软件之间的接口模型,以确保仿真结果的准确性和可靠性。
2.4 emu仿真在emu建模完成后,可以进行真实的软硬件协同仿真。
通过emu仿真,可以模拟和验证软件与硬件的交互工作,发现潜在问题并进行修复。
在这一步骤中,需要根据实际需求和测试目标,设计合适的测试用例,并进行全面的测试。
2.5 结果分析与优化在emu仿真完成后,需要对仿真结果进行分析和优化。
通过对仿真结果的分析,可以找出性能瓶颈和问题所在,并采取相应的优化策略。
这一步骤的目的是提高软硬件协同系统的性能和可靠性,从而满足产品的功能需求和性能指标。
三、emu软硬件协同仿真流程的注意事项在进行emu软硬件协同仿真时,需要注意以下几点:3.1 良好的沟通与协作软硬件协同仿真需要硬件设计师和软件开发人员之间的良好沟通与协作。
多智能体系统的协同控制算法设计与仿真
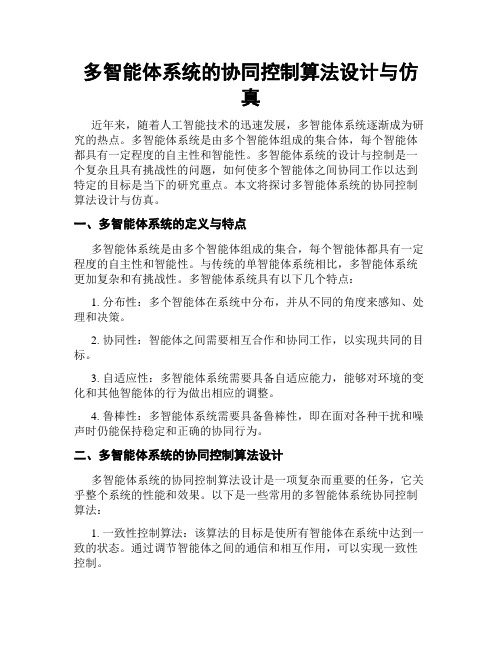
多智能体系统的协同控制算法设计与仿真近年来,随着人工智能技术的迅速发展,多智能体系统逐渐成为研究的热点。
多智能体系统是由多个智能体组成的集合体,每个智能体都具有一定程度的自主性和智能性。
多智能体系统的设计与控制是一个复杂且具有挑战性的问题,如何使多个智能体之间协同工作以达到特定的目标是当下的研究重点。
本文将探讨多智能体系统的协同控制算法设计与仿真。
一、多智能体系统的定义与特点多智能体系统是由多个智能体组成的集合,每个智能体都具有一定程度的自主性和智能性。
与传统的单智能体系统相比,多智能体系统更加复杂和有挑战性。
多智能体系统具有以下几个特点:1. 分布性:多个智能体在系统中分布,并从不同的角度来感知、处理和决策。
2. 协同性:智能体之间需要相互合作和协同工作,以实现共同的目标。
3. 自适应性:多智能体系统需要具备自适应能力,能够对环境的变化和其他智能体的行为做出相应的调整。
4. 鲁棒性:多智能体系统需要具备鲁棒性,即在面对各种干扰和噪声时仍能保持稳定和正确的协同行为。
二、多智能体系统的协同控制算法设计多智能体系统的协同控制算法设计是一项复杂而重要的任务,它关乎整个系统的性能和效果。
以下是一些常用的多智能体系统协同控制算法:1. 一致性控制算法:该算法的目标是使所有智能体在系统中达到一致的状态。
通过调节智能体之间的通信和相互作用,可以实现一致性控制。
2. 分工合作算法:该算法通过将系统任务进行分解和分配,使不同的智能体承担不同的责任和任务,以达到高效的协同工作。
3. 契约网络算法:该算法通过制定契约和规则来引导智能体的行为,以实现系统整体目标的最大化。
4. 强化学习算法:该算法利用奖励和惩罚机制来引导智能体的学习和决策,以达到最优的协同控制效果。
三、多智能体系统的协同控制算法仿真多智能体系统的协同控制算法仿真是研究多智能体系统性能和效果的重要手段。
通过仿真可以评估不同算法在各种情况下的性能,为实际系统的应用提供指导。
协同仿真是怎样炼成的

协同仿真是怎样炼成的协同仿真并不是一个新概念,四年前,安世亚太就提出了“协同仿真”理念,这个曾引起业内轰动的理念在当时看来如同海市蜃楼,可望不可及;而今,协同仿真已经从一个虚无飘渺的概念变为备受业界追捧的技术。
尤其是随着“以信息化带动工业化”的十六大战略的逐步落实,对国家经济具有非凡意义的信息化协同技术作为提升研发技术的一个重要途径,成为重点发展的方向。
这使得一向“酒香巷子深”的仿真和CAE技术也逐渐从幕后走向前台。
一时间,大家开始对仿真技术兴趣盎然,对协同仿真的理念也刨根问底。
然而协同仿真究竟是怎样的理念与技术?它又是如何炼成的?这似乎是一个深层话题,也许需要从很多纬度探讨方能水落石出。
作为这些纬度中的一个,本文通过协同仿真应用的经典案例,为大家解析协同仿真的锤炼历程。
协同仿真,源自客户需求过去,企业很重视采用先进的研发工具,然而使用的大都是单项的工具,在使用过程中,总感觉到无法将工具的最大效能发挥出来。
这是因为所有工具虽然都是为了同一个目标,但却各自为战,没有发挥出整体的力量。
此外,众所周知,在使用工具的过程中产生的知识才是企业真正的核心竞争力,虽然企业已经开始注重对知识的积累,然而目前他们对知识工程的实施方法还比较落后,很多企业都缺乏对知识进行积累的机制、工具和人才,放任知识流失而无计可施。
同时,仿真技术也只被少数专家使用,很少为其他部门和人员光顾,虽然企业协同技术已经流行已久,但多年来在仿真领域却一直被类似的PLM策略所忽视,无论是技术、流程、数据还是知识,不仅没有与企业更广泛部门和流程联系起来,其他人员也无法从企业协同技术中受益。
随着国家提出的“以信息化带动工业化”的制造业信息化战略的逐步落实和发展,集成与协同成为当前信息化发展的大趋势,企业如何通过更有效的手段来提升企业自主创新的能力,使企业信息化建设从单点应用走向全面集成,从单项仿真技术应用走向全面协同仿真,成为摆在每个企业面前的亟待解决的现实问题。
fmu联合仿真的实现原理

fmu联合仿真的实现原理FMU联合仿真的实现原理1. 引言在仿真领域,FMU(Functional Mock-up Unit)是一种常用的模型交换格式,它允许不同建模工具之间的模型互操作。
FMU联合仿真则是利用多个FMU实现系统级仿真的方法。
本文将从浅入深,介绍FMU 联合仿真的实现原理。
2. 什么是FMUFMU的定义FMU是一种用于描述仿真模型的标准文件格式,它包括模型的描述信息和模型的数学公式。
FMU具有可移植性和可重用性的特点,可以在不同的仿真环境中进行模型的交互和调用。
FMU的组成一个FMU文件由两部分组成:•模型描述文件():包含模型的结构、参数、变量和初始值等信息。
•模型二进制文件():包含模型的数学公式和仿真算法。
3. FMU联合仿真的概念FMU联合仿真是指将多个FMU集成到一个系统级仿真环境中,进行整体的仿真分析。
不同的FMU可以代表不同的子系统或组件,通过联合仿真,可以模拟整个系统的行为和性能。
4. FMU联合仿真的实现原理模型交互不同的FMU之间如何进行模型的交互是FMU联合仿真的关键。
一般而言,有两种主要的方法用于实现FMU之间的模型交互:•耦合方法:将不同FMU的接口连接起来,通过端口或信号进行数据交换。
这种方法适用于模型之间存在明确的依赖关系的情况。
•迭代方法:通过迭代计算的方式,将FMU的输出作为输入传递给其他FMU进行计算。
每轮迭代中,FMU之间的数据会不断更新,直到达到收敛条件。
这种方法适用于模型之间存在复杂的相互影响关系的情况。
仿真调度在FMU联合仿真过程中,需要对各个FMU的仿真时间进行调度,确保它们按照正确的时间步长进行计算。
常用的调度算法包括:•同步调度:所有FMU的仿真时间步长相同,按照相同的时间间隔进行计算。
•异步调度:不同FMU的仿真时间步长可以不同,根据各自的计算要求进行时间调度。
仿真协同在FMU联合仿真中,不同的FMU之间可能存在耦合和协同的关系。
面向多物理场耦合的分布式模型协同仿真技术研究

面向多物理场耦合的分布式模型协同仿真技术研究随着科技的发展,各种物理场耦合问题的研究日益增多,因此需要一种高效的技术来解决这些问题。
在这种情况下,分布式模型协同仿真技术就应运而生。
分布式模型协同仿真技术是指将多个仿真模型进行集成,从而达到对多物理场耦合问题进行分析的目的。
该技术旨在模拟不同的运动、物质流动、电磁场和热传导等多种方面的物理现象。
在使用分布式模型协同仿真技术时,需要使用高性能计算机和相应的软件来支持其中的运算。
这种技术的一个显著特点是,可以在全球范围内进行分布式计算,提高计算速度和精度。
此外,分布式模型协同仿真技术还具有其他许多优点。
它可以帮助研究人员更准确地预测物理场的行为,而且能够节省时间和成本。
使用分布式模型协同仿真技术,可以更好地了解多个物理场之间的相互作用,而且还可以提高研究人员对系统造成的影响的了解程度。
虽然分布式模型协同仿真技术的应用还比较有限,但它在一些领域的应用非常广泛。
例如,在机器人领域,这种技术可以帮助研究人员更好地了解机器人在各种环境中的行为,并优化它们的设计。
在材料科学领域,这种技术可以帮助研究人员更好地理解材料的结构和性能,从而提高材料的性能。
在生物医学领域,分布式模型协同仿真技术可以用于研究人员更好地理解生物体内的各种生理现象,并帮助找到更好的治疗方法。
总之,分布式模型协同仿真技术是一种非常有用的技术,可以在许多领域得到应用。
通过使用这种技术,研究人员可以更好地了解不同物理场之间的相互作用,并预测物理场的行为。
尽管该技术在某些领域已得到了广泛的应用,但在其他许多领域仍需要更多的研究。
相信随着技术的不断发展,这种技术的应用范围将会进一步扩大。
远程协同仿真调研分析报告

1.协同仿真概念协同仿真是一个复杂系统仿真方法,它支持处于不一样地点,基于不一样计算平台人员采取不用建模方法建立混合异构层次仿真模型并在分布环境上进行仿真运行。
协同仿真技术是基于优异建模技术,分布仿真技术和信息管理技术综合应用技术,是在各领域建模,仿真分析工具CAx/DFx技术基础上深入发展,是多学科协同技术。
协同仿真即包含时间轴上对产品全生命周期单点仿真分析,亦强调同一时间点上基于不一样人员/工具对同一产品对象在系统层面上联合仿真分析。
它支持“由上至下”复杂系统开发模式,是分布异地人员采取各领域专业设计,分析工具协同地开发复杂系统一条有效路径。
2.中国外远程协同仿真技术应用现实状况在国外,相关远程协同设计研究和应用起步较早。
80年代中期,麻省理工学院Paul Cashman等人就从事了这方面研究,并提出了计算机支持协同工作(Computer Support Cooperative Work ,CSCW)概念,近几年,伴随Internet技术快速发展,Wen-pal Lu等人则在研究CIM技术时提出利用广域网通信功效实施Tele-Manufacturing概念。
Eddy M.Rojas提出了以Web为中心工程合作设计环境。
G.Seliger等人提出一个将不一样企业工程师集成为虚拟增值小组进行复杂产品设计制造。
研究和开发快速成型(Rapid Proto-typing, RP)技术美国3D企业,已开始用Internet和用户联络,实现原型STL(Stereo-Lithograph)格式CAD文件传输,向用户提供网上报价服务和向用户汇报服务进展情况,降低了企业成本,提升了企业服务快捷程度。
在中国,相关这方面研究关键集中在高等院校。
同济大学和香港理工大学合作进行分散式网络生产系统(Dispersed Network Production System ,DNPS)研究,利用Internet所提供Email、WWW服务和浏览器、网页,实现了信息公布、文件传输等功效。
ANSYSWorkbench平台的协同仿真技术及应用
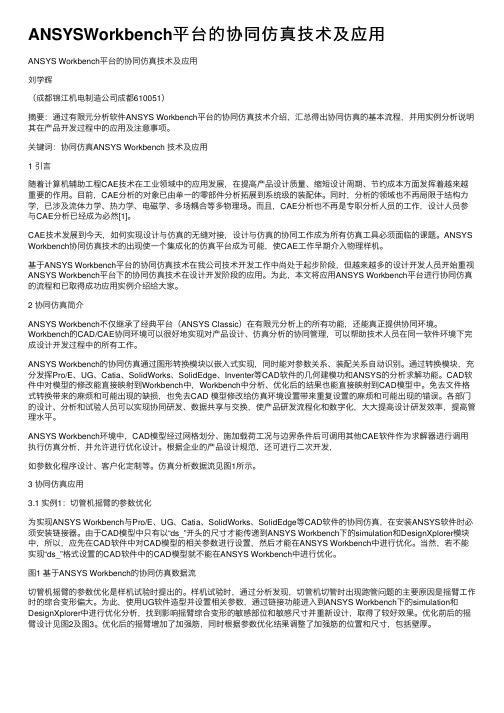
ANSYSWorkbench平台的协同仿真技术及应⽤ANSYS Workbench平台的协同仿真技术及应⽤刘学辉(成都锦江机电制造公司成都610051)摘要:通过有限元分析软件ANSYS Workbench平台的协同仿真技术介绍,汇总得出协同仿真的基本流程,并⽤实例分析说明其在产品开发过程中的应⽤及注意事项。
关键词:协同仿真ANSYS Workbench 技术及应⽤1 引⾔随着计算机辅助⼯程CAE技术在⼯业领域中的应⽤发展,在提⾼产品设计质量、缩短设计周期、节约成本⽅⾯发挥着越来越重要的作⽤。
⽬前,CAE分析的对象已由单⼀的零部件分析拓展到系统级的装配体。
同时,分析的领域也不再局限于结构⼒学,已涉及流体⼒学、热⼒学、电磁学、多场耦合等多物理场。
⽽且,CAE分析也不再是专职分析⼈员的⼯作,设计⼈员参与CAE分析已经成为必然[1]。
CAE技术发展到今天,如何实现设计与仿真的⽆缝对接,设计与仿真的协同⼯作成为所有仿真⼯具必须⾯临的课题。
ANSYS Workbench协同仿真技术的出现使⼀个集成化的仿真平台成为可能,使CAE⼯作早期介⼊物理样机。
基于ANSYS Workbench平台的协同仿真技术在我公司技术开发⼯作中尚处于起步阶段,但越来越多的设计开发⼈员开始重视ANSYS Workbench平台下的协同仿真技术在设计开发阶段的应⽤。
为此,本⽂将应⽤ANSYS Workbench平台进⾏协同仿真的流程和已取得成功应⽤实例介绍给⼤家。
2 协同仿真简介ANSYS Workbench不仅继承了经典平台(ANSYS Classic)在有限元分析上的所有功能,还能真正提供协同环境。
Workbench的CAD/CAE协同环境可以很好地实现对产品设计、仿真分析的协同管理,可以帮助技术⼈员在同⼀软件环境下完成设计开发过程中的所有⼯作。
ANSYS Workbench的协同仿真通过图形转换模块以嵌⼊式实现,同时能对参数关系、装配关系⾃动识别。
CosiMate协同仿真模式

CosiMate协同仿真模式同步CosiMate为各种系统的异构模型提供非常适合的同步方法。
确实,这些方法有如下益处:l 考虑到不同模拟语言的差异性及仿真工具的使用。
l 可以进行不同抽象层级之间的协同仿真。
当通过网络进行仿真时,CosiMate可以考虑到真正通信介质(网络实现)的固有限制。
当不同层级的不同系统的部分进行协同仿真时,通常需要添加适配器(主机访问控制方式),来确保不同层级之间模型的数据交互的兼容性。
它是一种确保在转换和仿真接口之间的数据传输的路由器。
同时使用同步和事件驱动模式,CosiMate为协同仿真提供非常强健稳定的同步模型。
此外,一些仿真工具需要基于时间的更强大同步模型来数据交互。
这种特点需要通过同步模式提供。
事件驱动协同仿真模式图1 事件驱动协同仿真模式在事件驱动的协同仿真模式下,路由器不会处理任何时间概念的事件,所以,整个系统并没有定义时间。
事件驱动通信模式允许事件驱动(如HDL仿真,UML模式)和/或顺序仿真。
(例如C代码)。
数据会很快通过通过CosiMate总线传输。
路由器验证从发送器到接收器传输的数据。
但是路由器并不检查接收器是否接收到有效数据。
因此,应该通过在应用层定义的协议来保证通信的一致性。
l 尽管如此,CosiMate API提供足够多的灵活性来支持各种通信协议。
事实上,在CosiMate软件界面上已经提供几种配置可供选择。
l 锁定输入端口:输入端口锁定包括仿真模型在内,直到一个事件通过第二个仿真利用CosiMate总线传输到第一个仿真模型时。
l 解锁输入端口:事件传输到解锁端口。
假定接收机配置正确能够在正确的时间里读取数据/事件。
注:从CosiMate总线到的信号也可以用于提醒仿真工具,传输一个或者多个事件。
l 锁定和解锁端口都可以使用未缓冲或缓冲的变量。
对于缓冲变量,一个FIFO(first input firsr output,先入先出)实例化及配置它的高度。
精益研发之协同仿真

精益研发之协同仿真作者:梅林涛精益研发是围绕企业研发活动来展开的,而研发离不开协同仿真技术的支持;同时,协同仿真也是精益研发不可或缺的一部分。
今天的仿真技术,已经由过去的单学科、单参数、事后验证以及无协同的CAE,发展到多学科、多参数、多场耦合、高性能计算的协同仿真环境,为企业的研发活动提供了更为广阔的空间。
作为精益研发平台的子平台,协同仿真平台(P E R A .S imu l a t i o n)将参与仿真过程的部门、人员、仿真工具、仿真模型、仿真数据、仿真流程、仿真项目等诸多方面实现协同的过程,将多学科、多场、多参数的问题耦合起来进行仿真,由此获得比各个单项CAE更为综合、准确的产品性能指标,有效提高了产品的技术含量。
同时,对于成本敏感型企业,通过仿真优化产品结构和重量,实现等寿命设计,降低研发成本。
协同仿真在精益研发中的作用企业产品研发是从客户需求域到功能域再到本身过程域的过程。
任何一款产品的研发,都是从需求分析开始,到概念设计、初步设计或方案设计,直到细节设计,一步步逐级展开。
精益研发的主流程也是遵循客户需求域→功能域→本身过程域的过程。
如图1所示。
图1 精益研发应用主流程协同仿真的过程遵循产品研发的过程,它将指标、任务逐级分解到子系统、部件、零件中,任务由不同部门和人员执行。
在研发过程中,企业涉及到众多研发活动,而这些活动都是围绕企业对产品本身的各项指标展开的,并扩展到精益研发主流程的各个阶段,分解到不同的人员、部门和专业当中。
从精益研发的主流程图上看到,仿真起重要的作用。
企业通过仿真可以对产品性能进行优化,提高产品性能,多方案比较,缩短仿真周期,对创新的多种方案进行定量分析,从而加快企业创新速度。
精益研发是一种以精益为目标、以精益研发总线为统筹、以精益样机为载体的研发方法。
精益研发总线,即以产品研发关键指标(性能、需求、质量、成本等)分解、分析和监控为特色的研发数据网络。
图2是安世亚太公司提出的通过“信息化看板”提升、表达和管理产品性能的新技术。
CAE-CAE协同仿真环境
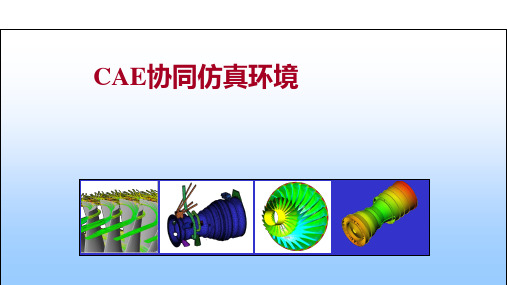
• 世界航空发动机预研以ANSYS为标准 分析平台
• 预研需要创新
– 实现创新的两个阶段 – 计算机辅助创新
• 创新有规律可循
– Triz:创新“灵感”秘密揭示 – 无折衷解决矛盾 – 产品发展的规律性预测
• 创新能力是可训练的
– 创新能力拓展平台 – 世界创新规律之集大成 – 通过各类训练提高创新能力
计算机辅助创新
计算技术辅助创新平台 创新能力拓展平台
航空发动机预研需要协同仿真环境
• 世界CAE核心技术大同小异 • 航空发动机预研需要协同仿真环境
CAE协同仿真环境
CAE核心分析技术
• 高速非线性分析
模态分析
鸟撞 分析
叶片包容
• 结构振动分析 高
• 机构运动学
温 蠕
变
• 热失效分析
疲 劳
• 高温蠕变疲劳分析
分 析
内流场 机构运动分析
模态分析
• 流体动力学分析
• 流/固/热耦合分析
应力分析
外流分析
流/固/热耦合
热分析
航空发动机预研中的尴尬现状
• ANSYS变分技术
– 深入计算核心,生成变分矩阵 – 只需一次求解即可得到优化结果 – 多目标优化及离散参数
设计优化
200 Parameters 2 weeks 2 hours
• ANSYS产品拆散形成组件(API) • 用户自己的程序形成API,与ANSYS的组件平等 • 用户根据需要取舍并重组这些功能组件 • Workbench是重新组合这些组件的专用平台
- 1、下载文档前请自行甄别文档内容的完整性,平台不提供额外的编辑、内容补充、找答案等附加服务。
- 2、"仅部分预览"的文档,不可在线预览部分如存在完整性等问题,可反馈申请退款(可完整预览的文档不适用该条件!)。
- 3、如文档侵犯您的权益,请联系客服反馈,我们会尽快为您处理(人工客服工作时间:9:00-18:30)。
现代中国制造业的发展主旋律是“以信息化带动工业化,以工业化促进信息化”。
产品研制过程的信息化瞄准“数字”和“协同”两个目标。
以日新月异的网络技术和计算机技术为基础,采用产品数字化虚拟研发技术,重组企业产品研发流程,大力推行并行工程,组建产品研发和制造的网络化虚拟环境。
现代制造业信息化主旋律将仿真带入了协同时代。
企业间产品协同开发的需求、仿真工作融入研发流程的呼吁,保存企业智力资产的渴求,都使我们无法不加快协同仿真技术发展的步伐。
CAE 仿真技术通过开发吻合研发流程的协同仿真平台,建立流畅的仿真通道,帮助企业打通从设计、仿真、试验、制造的全数字化生产线。
从而,企业可以非常方便地进行数字化工程的统筹规划,并在CAE 上的所有投入物有所值,物尽其用。
同时,在开发过程中,使企业的智力资产得到完美的融台。
传统的产品研制,都是以试验的方式对设计方法和产品进行验证,以确保产品的性能。
往往试验需要人为控制,对于环境、仪器、人员等条件要求非常高,需要资金、人员、设备等大量投入,有些大型试验风险很难以预测,产品的研制周期长,研制成本高。
CAE仿真技术的产生之后,可以通过CAE技术完成部分物理试验无法完成的产品性能分析工作。
但是仿真只是作为产品检验的手段,没有真正成为产品设计的一个必要阶段,只能在产品设计的后期,甚至产品试验过程或使用阶段发现问题之后才进行分析。
仿真不能对产品设计起到指导性作用,没有最大限度发挥自身价值。
目前,随着仿真技术的发展,仿真已经融入产品的设计过程,成为产品设计的一部分。
通过仿真不仅能在产品设计后期进行设计性能校核,同时在产品试验前期通过虚拟仿真模拟实验结果,指导产品物理试验,并在产品试验后期验证物
理试验结果,保证了试验准确度,大大降低了试验的成本。
但在企业产品研制仿真应用中期阶段,虚拟仿真仍然只是作为产品检验的工具对产品性能进行评估或指导物理试验,还不能完全取代物理样机试验。
随着仿真重要性不断加强,仿真已经被广泛的应用于汽车、航空、航天等行业。
这些行业的复杂产品仿真包括结构、流体、碰撞、振动噪声、成型分析等,涉及到多个学科的不同领域。
现有的仿真工具可以有效辅助某个功能单元的设计任务,能够解决大部分单学科的分析评估问题,却很难处理涉及多学科交互的复杂仿真问题,无法利用某一种仿真工具完成对多个学科的仿真。
传统的做法是分别从单个学科的角度出发对复杂产品进行处理,将涉及其他学科的子系统加以简化甚至完全忽略。
但由于复杂产品是一个统一的整体,各学科子系统之间有着不同程度的约束和交互。
如果只从某一个角度对其进行分析,忽略了学科之间的联系,势必将会造成系统整体性和相关性的丢失,降低仿真结果的可信度。
所以需要对多个不同学科领域的子系统所组成的整体系统进行相应的仿真分析,即进行多个领域的协同仿真,从而在产品设计阶段就可以对产品进行全面的评估和分析。
基于仿真技术在企业产品研制应用中的变革历程以及仿真在多学科多领域的应用,仿真技术必将应用到产品研发设计中的各个阶段,应用到更多的学科和领域当中。
在仿真技术的不断深化应下,数字化、协同化、知识化的协同仿真时代已经到来。
数字化、协同化、知识化的协同仿真平台是仿真技术发展不可逆转的趋势。
现代企业产品研制过程中,仿真在各个阶段都有着不同的应用,仿真的类型也越来越广泛,
因此为了提高产品的研制效率,仿真工作的效率提高显得尤为重要,提高仿真工作的效率,一方面需要能够在越来越广泛的仿真分析类型中实现协同,另一方面需要实现越来越多的人开展不同的仿真任务的协同。
广泛的仿真分析类型中,采用了多种的仿真分析软件(CAE 软件),各CAE 软件在核心功能上各有侧重,在解决问题的方式上各有特长。
但是没有一个CAE 软件可以包打天下,这是分析领域的广泛性决定的。
对于大型企业和设计院,即使对同一个部门,通常一种软件也无法涵盖所有分析需求。
企业内多种CAE 软件并存,为企业应用带来益处的同时也带来诸多烦恼。
企业产品设计分析工作带来多种零散的CAE 软件异构问题,导致该生产线上的操作人员在学习使用、技术交流、数据共享、多场耦合分析等方面的诸多问题,设计与仿真数据的不同源现象导致各种管理问题。
这些问题将严重阻碍企业信息化和数字化工程的顺利实施,降低企业的研发效率;因此仿真技术的集成在仿真效率的提高中显得尤为重要。
CAE 技术给工业产品研发带来了巨大经济效益,将基于物理样机试验的传统设计方法带入基于虚拟样机仿真的现代设计方法,大幅缩短产品研发周期,降低成本,提高企业竞争力。
因此,仿真技术的提高是提高企业研发质量的关键。
基于以上的现状,有必要对企业的仿真业务管理模式进行革新,加强仿真数据和流程的管理,构建特定的企业级仿真业务管理平台。
通过定制开发,企业可以在统一的平台下,实现企业仿真过程的协同化和标准化,管理仿真数据、流程、软件资源和任务调度工具,并能与设计、试验等外部系统集成,实现互联互通,形成协同研发环境。
对于标准化分析流程,进行封装应用软件,以重用最佳实践。
总之,协同仿真为企业带来了新的创新动力,推动产品研发走向成功。
企业建立协同的目标是,通过对产品研发流程中仿真环境的开发与实施,搭建一个集成多学科异构CAE 技术的仿真系统。
以协同仿真管理为核心,组建一个基于网络的产品研制虚拟仿真团队,基于产品虚拟仿真样机,实现产品研制的
并行仿真和异地仿真。
所有与仿真工作相关的人、技术、数据在这个统一环境中协同工作,各类数据之间的交流,传递和共享皆可在这个环境中完成。
协同仿真主旨和目的
主旨
∙将企业原本离散的CAE技术、流程、数据和知识综合起来,形成协同优势,使仿真作用最大化,充分发挥人员、工具、流程与数据的潜能,
完成以前无法完成的任务,最大化地支持复杂产品的创新与优化,提
升企业的竞争力。
目的
∙产品仿真业务中的项目、技术、流程、数据和知识等关键对象进行系统,有效的管理,实现产品仿真过程中人与人的协同、技术与技术的协同、
业务与业务的协同,通过集成各类研发工具和数据接口实现数据与工
具间的关联。
按照企业研发仿真流程,协同项目、部门、人员、学科、
软件工具、数据等信息形成统一的关联模型,实现对研发过程中所产
生的大量信息进行可塑性管理,并与企业其他系统进行无缝集成,共
同构成企业的研发管理系统。
∙通过对知识的封装,降低了仿真难度,使越来越多的人能够驾驭仿真技术,也能够使新手更早地进入高产能状态。
这样,仿真就不再是“黑
洞”,而能真正融入到企业协同的大环境中,进入产品生命周期的所
有环节,使更多的人愿意介入到仿真流程中来,从其成果中受益。
价值
∙协同仿真工作
通过仿真流程管理规范仿真任务执行,保证正确的数据传递到正确的仿真人员,并且使仿真人员工作目的更加明确,从而有效提高仿真工作的效率。
此外,仿真流程管理具有柔性扩展机制可将特定仿真流程固化,简化仿真过程,并能与企业现有应用系统进行集成。
∙仿真技术集成
通过仿真技术集成,各种工具软件集成到一个统一环境中,工程师不需要切换到各种工具界面环境,软件之间的数据传递自动完成,大大减少仿真工程师的非技术性劳动,提高工作效率。
能够将一些具体的、流程化的分析过程进行封装,实现仿真全过程的向导化和模板化。
∙协同仿真异地部署
通过异地部署,构建产品研发和制造的网络化环境。
协同仿真异地部署为时空上分散的仿真工作人员提供一个“面对面”的协同工作环境,实现不同区域的仿真数据共享,不仅改善相互间交流信息的方式,缩短传递信息
的途径,消除在时空上相互分割的障碍,而且节省工作时间和精力,提高工作质量和效率。
历史仿真数据的检索及重用
通过仿真数据管理,仿真产生的文件数据如仿真模型、各种仿真结果和报告等能够进行统一有效的管理,仿真人员都可在权限允许情况下共享仿真数据信息,实现仿真数据利用价值的最大化。