冷轧带钢工艺技术
冷轧带钢生产工艺

冷轧带钢生产工艺
冷轧带钢是一种常见的金属材料,生产过程需要经过多个工艺步骤。
下面是一个主要的冷轧带钢生产工艺的简化描述:
1. 原料准备:根据冷轧带钢的规格要求,选取适当的钢材作为原料。
原料应具备良好的可塑性和延展性。
2. 热轧:将原料加热至高温,通常在1100-1250℃之间。
通过
热轧工艺,将原料加工成所需的形状和尺寸。
这一步骤主要是为了提高钢材的可塑性和延展性。
3. 酸洗:通过酸洗工艺,将热轧后的钢材表面涂覆的铁锈、氧化物等杂质去除。
酸洗可以使用硫酸、盐酸等酸性溶液。
4. 冷轧:将经过酸洗的钢材送入冷轧机进行冷轧加工。
冷轧是通过辊子将钢材压制成所需的规格和尺寸。
这一步骤主要是为了提高钢材的表面光洁度、尺寸精度和力学性能。
5. 钢带退火:为了减小冷轧带钢的硬度,提高其延展性和塑性,需要对冷轧后的钢带进行退火处理。
退火温度一般在600-800℃之间,持续一定时间。
6. 表面处理:为了提高冷轧带钢的防锈性能和美观度,通常需要进行表面处理。
常见的表面处理工艺包括镀锌、涂油等。
7. 剪切和卷绕:将经过表面处理的冷轧带钢按照规格要求进行剪切和卷绕,形成卷盘状的成品。
8. 检验和质量控制:对生产出的冷轧带钢进行质量检验,包括外观检查、尺寸测量、化学成分分析、力学性能测试等。
9. 包装和储存:将质量合格的冷轧带钢进行包装,并储存在合适的场所,以待出售或进一步加工使用。
以上是一个主要的冷轧带钢生产工艺的简化描述,具体工艺步骤和参数会根据不同的钢材和产品要求而有所差异。
板带生产工艺冷轧板带钢生产
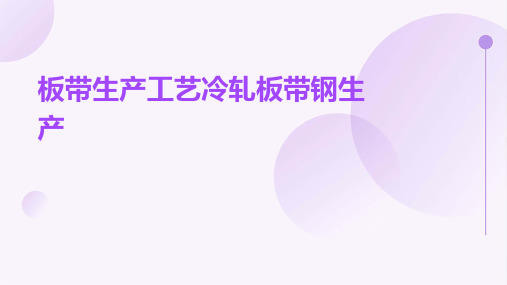
详细描述
冷轧板带钢的生产流程包括原料选择、加热、轧制、 冷却、精整等环节。原料选择是根据产品要求选择合 适的钢板;加热是为了使钢板软化,便于轧制;轧制 是利用轧机对钢板进行多次轧制,使其变薄、变长; 冷却是在轧制过程中对钢板进行快速冷却,使其内部 组织更加稳定;精整是对轧制后的钢板进行矫直、剪 切、表面处理等加工,以满足产品要求。
建立废水处理设施,对生产过程中产生的废水进行分类处理,
确保废水达标排放。
废气处理
03
对生产过程中产生的废气进行收集和处理,减少废气对环境的
影响。
资源利用与可持续发展
节能降耗
采用节能技术和设备,降低能源消耗,提高资源利用效率。
循环经济
实现废物的减量化、资源化和无害化处理,促进循环经济的发展 。
绿色产品开发
轧机设备主要包括工作辊、支撑辊和轧制力矩测量装置等部分。工作辊和支撑辊是轧机的核 心部件,负责将轧制力传递给钢板并进行塑性变形。轧制力矩测量装置则用于监测和控制轧 制过程中的力矩,以确保生产出的冷轧钢板厚度和性能符合要求。
为了确保轧制质量和生产效率,轧机设备需要定期进行维护和更换易损件,同时对设备参数 进行优化调整。
题发生。
生产过程质量控制
工艺参数控制
严格控制生产过程中的温度、压力、速度等工艺 参数,确保产品性能的稳定。
设备维护与检查
定期对生产设备进行检查和维护,确保设备处于 良好的工作状态。
过程监控与记录
对生产过程进行实时监控,并做好相关记录,以 便对产品质量的追溯和控制。
产品检验与质量评估
外观检验
对冷轧板带钢的表面质量进行 检验,确保产品表面无明显缺
轧制道次
根据带钢的材质和厚度要 求,确定合理的轧制道次 和每道次的压缩率。
毕业论文浅析冷轧带钢精整工艺及包装设备操作
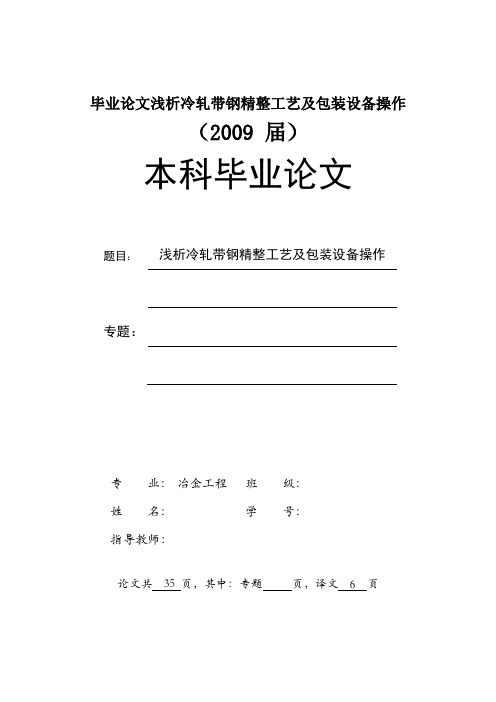
毕业论文浅析冷轧带钢精整工艺及包装设备操作(2009 届)本科毕业论文题目:浅析冷轧带钢精整工艺及包装设备操作专题:专业:冶金工程班级:姓名:学号:指导教师:论文共35 页,其中:专题页,译文 6 页浅析冷轧带钢精整工艺及包装设备操作摘要冷轧板带材产品是板带材生产的最终产品,而冷轧板带材的精整工艺是提高产品质量的重要途径,其作用已显得越来越突出。
冷轧厂中最后一道工序是精整,是保证产品质量的关键。
精整的目的,要紧在于操纵成品的力学性能和工艺性能,操纵成品的精确厚度和良好的板形以获得高质量性能和表面状态的成品。
精整成效的好坏就成为了产品质量的关键,因此我们有必要将整个精整工艺及设备进行简单的论述。
精整工序是使冷轧带钢成为交货状态产品的重要生产工艺过程,它由带钢平坦机组、横切机组、纵切机组、重卷机组等组成,各机组最后一个工序差不多上用打包机对产品进行打包验收完成最终的生产过程。
因此本文结合武钢冷轧薄板总厂精整车间生产体会,重点对冷轧板带材的包装设备钢带打捆机等进行研究,进而解决如何提高板带材包装质量的问题。
关键词:精整,钢带打捆机,冷轧带钢Analysis of cold-rolled steel finishing process and packagingequipmentAbstractCold rolled strip of plate and strip products are the final products of wood production, and cold rolled strip finishing the process is to improve the product quality of an important way, its role has become increasingly prominent. Cold Rolling Mill in the final process is finishing, is the key to ensure product quality. The finishing main purpose is to control the mechanical properties of finished product and process performance, precise control of the thickness of the finished product and a good shape to obtain high-quality performance and the finished surface. The quality of finishing the effect of product quality has become a key, so we need to finish the whole process and equipment exposition simple.Finishing process is to deliver a state of cold-rolled steel products to become an important production process, its formation by the strip units, cross-cutting units, longitudinal units, heavy units, such as volumes, each unit is the last process to use product packaging balers final acceptance of the production process. Therefore this paper WISCO precision cold-rolled sheet plant inter-vehicle production experience, with a focus on cold rolled strip steel packaging equipment, packaging machines, such as research, and resolve how to improve the quality of board with the problem of packaging material.Key words: Finishing, strip packaging machines, cold rolled strip名目1绪论 (1)1.1板带材精整的背景及目的 (1)1.2国内研究应用精整包装现状及有用意义 (1)1.3精整过程中包装重要性 (2)1.4研究内容 (3)2 冷轧板带材精整工艺及设备概述 (4)2.1武钢冷轧二分厂精整 (4)2.2平坦机组 (7)2.3纵剪重卷机组 (8)2.4横剪机组 (11)3 包装设备及工艺的研究 (13)3.1成品包装方式 (13)3.1.1成品包装的要求 (13)3.1.2包装的分类及工艺 (14)3.2包装使用设备的优化 (16)3.2.1打捆机的作用及使用现状 (16)3.3包装线部分单机的工艺流程及工艺参数(以武钢二冷轧1#包装生产线为参考) (17)3.3.1包装机组带卷包装的前提条件 (17)3.3.2工艺技术参数 (18)3.3.3产能参数 (18)3.4包装工艺流程概述(以武钢二冷轧1#包装生产线为参考) (19)3.5包装操作 (20)3.5.1操作模式 (20)3.5.2步进梁运输机 (23)3.5.3地辊台 (24)3.5.4包纸机 (24)3.5.5钢卷提升小车 (25)3.5.6包铁皮机 (25)3.6.7自动周向打捆机 (26)3.5.8自动眼向打捆机 (28)3.5.8自动打捆机平面图及设计图 (29)3.6包装中导致的产品缺陷分析 (30)结论 (31)致谢 (33)参考文献 (34)附录A (35)附录B (36)附录C (37)1 绪论1.1冷轧带钢精整的背景及目的在2004—2007年末全球经济一片繁荣的大环境下,中国钢铁钢铁工业经历了一个大进展的黄金期,全国各大钢铁集团纷纷扩大规模引进国际先进技术和设备,都在积极的进行钢铁产业结构升级,其中钢铁的板带比值迅速增长。
带钢冷轧生产工艺

带钢冷轧生产工艺
带钢冷轧生产工艺
一、引言
带钢冷轧生产工艺是一种广泛应用于钢铁制造的重要技术,它能够将热轧带钢通过一系列的加工工序,生产出具有高精度、高质量的冷轧带钢产品。
这种工艺具有产品尺寸精度高、表面质量好、性能优良等特点,广泛应用于汽车、家电、建筑、机械制造等领域。
本文将对带钢冷轧生产工艺进行详细介绍。
二、带钢冷轧生产工艺流程
带钢冷轧生产工艺主要包括以下步骤:原料准备、酸洗、轧制、退火、平整、精整和检查等。
1. 原料准备
原料准备是冷轧工艺的第一步,包括选择合适的原材料、进行表面处理和厚度调整等。
原料的品质和精度对最终产品的质量和性能有着至关重要的影响。
2. 酸洗
酸洗的目的是去除带钢表面的氧化皮和杂质,以确保轧制过程中的表面质量和性能。
酸洗后的带钢要进行清洗和干燥。
3. 轧制
轧制是冷轧生产的核心环节,通过多道次的轧制,使带钢的厚度、宽度和长度等参数达到要求。
在轧制过程中,要控制好温度、轧制速度和压下量等参数,以保证产品的质量和性能。
4. 退火
退火的目的是调整带钢的机械性能和消除加工硬化现象。
根据不同的产品要求,退火工艺可以选择在常温下进行或有保护气体的加热退火。
5. 平整
平整的目的是进一步调整带钢的表面质量、机械性能和厚度精度。
通过平整处理,可以改善带钢的板形和平整度,提高产品的使用性能。
6. 精整
精整包括剪切、矫直、标识和包装等工序,是产品出厂前的最后处理阶段。
精整的目的是确保产品的尺寸精度、表面质量和外观质量符合要求,便于运输和使用。
冷轧板带钢生产工艺

冷轧板带钢生产工艺冷轧板带钢是一种轧制工艺,通过将热轧板带钢进行再加工,使其在较低的温度下进行塑性变形,以获得更高的机械性能和更好的表面质量。
下面是冷轧板带钢的生产工艺。
冷轧板带钢的生产工艺主要包括原料处理、轧制、脱皮、退火和表面处理等环节。
首先是原料处理。
冷轧板带钢的主要原料是热轧板带钢,在生产过程中,需要对热轧板带钢进行拷边和切割,将其切割成适合冷轧的宽度和长度。
同时,为了进一步提高冷轧板带钢的表面质量,还需要对切割后的边缘进行修整和除锈处理。
接下来是轧制。
轧制是冷轧板带钢的核心工艺,主要通过轧机进行,将热轧板带钢在室温下进行塑性变形。
在轧制过程中,需要使用一系列的轧辊进行多道次的轧制,以逐步减小板带钢的厚度,并达到所需的规格要求。
轧制过程中,还需要控制好轧机的工作参数,如轧制力、轧制速度等,以保证产品的机械性能和尺寸精度。
轧制后,冷轧板带钢通常会出现脱皮现象,即表面有一层薄膜剥落。
为了去除脱皮层,常采用脱皮处理。
脱皮可通过刮刀脱皮或钢丝刷脱皮等方法进行。
脱皮后的冷轧板带钢还需要进行退火处理。
退火是为了消除轧制过程中的残余应力和晶粒变粗,使产品具有良好的塑性和韧性。
退火过程通常分为初始退火和终退火两个阶段,通过控制退火温度和保温时间,以达到所需的力学性能。
最后是表面处理。
冷轧板带钢经过退火后,表面通常会有氧化层和残留的油脂等物质,需要经过酸洗等表面处理工艺去除。
酸洗过程中,通常使用稀盐酸或硫酸等酸性溶液进行,以去除表面的铁锈和污垢,并使产品表面光洁度和外观质量得到保证。
以上就是冷轧板带钢的生产工艺,通过原料处理、轧制、脱皮、退火和表面处理等环节的有序进行,能够获得满足要求的优质冷轧板带钢产品。
冷轧带钢的生产工艺

冷轧带钢的生产工艺
冷轧带钢是一种重要的金属材料,广泛应用于汽车、电器、机械制造等行业。
其生产工艺主要包括原料准备、轧制、冷卷、退火等几个主要过程。
首先,原料准备是冷轧带钢的第一道工序。
原料一般采用热轧带钢,将其通过酸洗、清洗等工艺处理,去除表面的氧化铁皮、锈垢等杂质,使其表面光洁,以提高后续工序的质量。
接下来,原料经过轧制工序。
首先是将经过处理的原料带钢进入轧机,在辊缝中受到加热和压力作用,通过轧辊的旋转和带钢的传动,使其逐渐变薄、变形,并使其宽度、厚度等尺寸满足要求。
然后,冷卷是冷轧带钢生产工艺中的重要环节。
冷卷是指通过冷轧机对轧制后的带钢进行再次轧制,使其加工硬度增加,同时改善其机械性能,并获得所需尺寸的带钢。
最后,退火是冷轧带钢生产工艺中的最后一个环节。
退火是指通过加热带钢到一定温度,并进行保温一段时间,然后缓慢冷却,使其组织结构发生变化,消除冷加工应力,提高带钢的塑性、硬度和韧性。
除了以上几个主要的工序,冷轧带钢的生产还需要进行质检、修边、卷取、打包等工序,以确保最终产品的质量和外观。
总的来说,冷轧带钢的生产工艺是一个复杂的过程,需要通过
多个工序的组合来获得最终产品。
每个工序的操作都需要严格控制和精确操作,以保证冷轧带钢的质量和性能。
冷轧带钢生产工艺和精整工艺

第!章冷轧带钢生产工艺和精整工艺第一节冷轧带钢生产的工艺流程不锈钢冷轧带钢的生产是由!个以上的专业化机组完成的,见图"#$ #%。
热轧带钢首先在&’准备机组焊接引带,以减少冷轧不轧部分(头尾约())的消耗,并对带钢测长测厚,为冷轧做准备。
然后带钢在热轧带钢连续退火酸洗机组*+,上进行软化和去除氧化铁皮处理。
带钢在-./0辊或!"#$辊轧机上进行冷轧,在冷轧带钢连续退火酸洗机组!%&进行再结晶软化退火和酸洗。
成品冷轧带钢经平整机组’(&改善板形,提高表面光泽度,经纵切’)(钢卷交货)或横切!)机机组(单张板交货),完成冷轧带钢的生产。
图*+,+#不锈钢冷轧带钢生产工艺流程不锈钢除了铁素体不锈钢外,冷加工硬化率都非常高,一般为室温强度的$倍以上,为了对不锈钢进行冷轧,广泛使用$-辊整体机架的森吉米尔轧机或四柱分离式$-辊轧机或!"#$辊轧机。
多辊轧机工作辊径只有,./ #$-00,由于变形区面积小,相对总的变形抗力小,所以总变形率可达到1.2以上,可以生产-3#00薄规格产品,轧制速度可达1--04056。
在$-辊轧机中分离式轧机在通板中比较容易,不易伤害轧辊,同时检修方便。
!"#$辊轧机由于工作辊径较大,对提高轧速和轧机刚度(#7400)及降低热凸度有利,同时由于工作辊辊径范围大,因而可以采用小辊径生产薄规格产品。
这些轧机对厚度尺寸精度的控制能力都很强。
有预置88+%9!,对设定规格进行控制,有反馈8:+%9!,对厚度公差进行控制,对薄规格产品还设有张力%9!,秒流量%9!(:;’"%)。
另外有的工厂还采取了对轧制温度进行精确控制的措施。
因此带钢的厚度精度已达到<$3-!0的水平。
各种冷轧机的厚度控制精度和基本参数的比较见表*+,+#和表*+,+$。
表!"#"$新建的$%辊不锈钢冷轧机概要轧机参数日新制钢周南厂住友金属鹿岛厂川崎制铁千叶厂轧机速度(&·&’())**$***)**机组张力(+)%,$*-**工作辊!-*.$%*!/,.$!,(常用!)*.0,)辊直径(&&)中间辊!,*.$-*!%$*!/0.$%*支撑辊!%%*,!-*!,%*压下力(+),**$***$***轧机主电机(12)#***-!**钢卷宽度(&&)-**.$*,*0**.$!**-,*.$-**钢卷厚度(&&)来料*3$.%3*$3,.#3,$3*.)3*成品*3*,.*3-*3$.$3,*3%.,3,钢卷重量(+)$)%)!*生产日期(4)$0)0$00%$00$表!"#"%各种冷轧不锈钢宽板带(56$***&&)轧机的基本参数对比轧机典型型号森吉米尔%*辊轧机78%%5",#罗恩%*辊轧机29%*:"#*-"$!,*三菱$%辊轧机;8"$%<"$!,*日立<;-辊轧机=;>?=;#"$#**7型-辊轧机7"-"$/**机架形式零凸度整形机架四立柱分体式机架双牌坊闭口机架双牌坊闭口机架双牌坊闭口机架工作辊径直径(&&),)?/!3,-)?$**/,?$%*),?$%,$#*?%$*第一中间辊直径(&&)0-?$*,$$%?$!*$0,?%$*$,*?%$*!!,?#*,第二中间辊直径(&&)$/*?$/-%!%?%##支撑辊直径(&&)!**#*-3#,%*?,$),%)!?%),$#%*?$!%*$$,*?$%,*最大轧制带钢宽(&&)$!,*$!,*$!,*$$**$,,*辊缝开口度(&&)$%3/$,*.!**!**!**以上!**以上主传动轧辊数第二中间辊@#第二中间辊@#第二中间辊@%中间辊(或支撑辊)@%第二中间辊@%轧机刚度(1A·&&)-****约,,**约,****约#,***约#,***最大轧制力(1A))***$*,**$****$#***%****最大张力(1A),**,**,**#%*#**最大轧制度(&·&’())**)**)**)**—轧机典型型号森吉米尔!"辊轧机#$!!%&’(罗恩!"辊轧机)*!"+&(",&-.’"三菱-!辊轧机/$&-!0&-.’"日立0/,辊轧机1/231/(&-(""#型,辊轧机#&,&-4""道次最大压缩率(5)约!6约!4约!(约!(—轧程最大总压缩率(5)约6,约6(约6.约6.—!"世纪7"年代建设台数.!!’!’!-制造厂商西马克·德马克·82+,日立,9!+,):松德维·达涅利和:$;0<9=>联合三菱重工日立松德维注:"森吉米尔的最新机型为双牌坊闭口机架。
冷轧带钢工艺流程
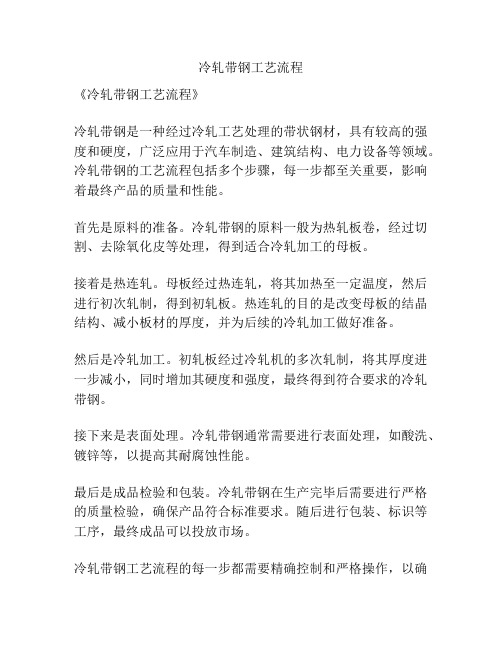
冷轧带钢工艺流程
《冷轧带钢工艺流程》
冷轧带钢是一种经过冷轧工艺处理的带状钢材,具有较高的强度和硬度,广泛应用于汽车制造、建筑结构、电力设备等领域。
冷轧带钢的工艺流程包括多个步骤,每一步都至关重要,影响着最终产品的质量和性能。
首先是原料的准备。
冷轧带钢的原料一般为热轧板卷,经过切割、去除氧化皮等处理,得到适合冷轧加工的母板。
接着是热连轧。
母板经过热连轧,将其加热至一定温度,然后进行初次轧制,得到初轧板。
热连轧的目的是改变母板的结晶结构、减小板材的厚度,并为后续的冷轧加工做好准备。
然后是冷轧加工。
初轧板经过冷轧机的多次轧制,将其厚度进一步减小,同时增加其硬度和强度,最终得到符合要求的冷轧带钢。
接下来是表面处理。
冷轧带钢通常需要进行表面处理,如酸洗、镀锌等,以提高其耐腐蚀性能。
最后是成品检验和包装。
冷轧带钢在生产完毕后需要进行严格的质量检验,确保产品符合标准要求。
随后进行包装、标识等工序,最终成品可以投放市场。
冷轧带钢工艺流程的每一步都需要精确控制和严格操作,以确
保最终产品具有优良的性能和质量。
随着钢铁行业的发展,冷轧带钢的工艺流程也在不断完善,以满足市场需求和环保要求。
冷轧带钢生产技术手册

冷轧带钢生产技术手册第一章:冷轧带钢生产概述1.什么叫冷轧,冷轧带钢有哪些优点金属在再结晶温度以下进行轧制变形叫做冷轧,一般指带钢不经加热而在室温直接进行轧制加工。
冷轧后的带钢可能烫手,但还是叫冷轧。
冷轧生产可提供大量高精确度和性能优良的钢板和带材,其最主要的特点是加工温度低,同热轧生产相比,它有以下优点:(1)冷轧带钢产品尺寸精确,厚度均匀,带钢厚度差一般不超过O.01-0.03mm或更小,完全可以符合高精度公差的要求。
(2)可获得热轧无法生产的极薄带材(最薄可达0.001mm以下)。
(3)冷轧产品表面质量优越,不存在热轧带钢常常出现的麻点、压入氧化铁皮等缺陷,并且可根据用户的要求,生产出不同表面粗糙度的带钢(光泽面或麻糙面等),以利于下道工序的加工。
(4)冷轧带钢具有很好的力学性能和工艺性能(如较高的强度、较低的屈服极限、良好的深冲性能等)。
(5)可实现高速轧制和全连续轧制,具有很高的生产率。
2.冷轧生产方法有哪几种冷轧板带钢生产方法分为单片轧制和成卷轧制两种方法。
(1)单片轧制。
单片轧制最早采用二辊式轧机,目前多用四辊式冷轧机。
四辊冷轧机按其轧辊运转方向可分为可逆式和不可逆式。
采用不可逆式四辊轧机进行单片生产时,轧制操作是由人工逐张将钢板喂入轧机,全垛钢板轧完一道次后,用吊车将板垛吊送到轧机前,进行下一道次的轧制,如此循环进行,直到轧成规定的成品尺寸时为止。
采用可逆式轧机时,则轧制操作有两种,一种是每一张钢板在轧机上往返轧制,直到轧制成最终的成品尺寸,然后再进行第二张钢板的轧制。
这种操作方法虽然压下调整操作频繁,但产品表面不易划伤,故实际生产中应用较多,特别是轧制单重和尺寸较大的钢板,均采用此法。
另一种是每张钢板逐张送入轧机,待全垛钢板轧完一道次后,再逐张返回轧制第二道次。
此种操作方法使轧制产品尺寸较均一,而且省去了轧辊反转和压下的调整时间,从而冷轧机产量较高,但板面之间有时可能造成划伤。
冷轧带钢生产技术

冷轧带钢生产技术冷轧带钢生产线技术解析1、了解带钢:带钢是相对于钢卷,由中小型生产线冷轧工艺轧制而成的带钢产品。
冷轧带钢的用途可谓广泛,根据后期的加工方式,可以分为如下类型:(1) 带式:如打包带、铠装电缆用带等;(2) 管式:如薄壁管(含家具用管)、复合管、缠绕管等;(3) 冷弯型材:如滑轨、龙骨、塑钢内衬、电缆桥架;(4) 压型钢板:如卷帘门板、钢结构建筑围护用墙板、屋面板等;(5) 冲压用板:如电池壳体、汽车用板、家电用板等。
冷轧的关键工序:一为酸洗、二为冷轧、三为热处理、四为平整。
酸洗是为了去除对冷轧有害的原料钢卷表面上的氧化铁皮;冷轧是生产冷轧板带钢的关键工序;热处理在冷轧工序中有二个作用,一是消除冷轧带钢的加工硬化和残余应力,软化金属,改善塑性,以便于进一步进行冷轧或其它加工;二是改善组织结构,产生所需要的晶粒大小和取向;平整是精整工序中十分重要的工序,它可以改善带钢的性能,提高钢板的成形性能,提高钢带的平直度及改善钢板的表面状态。
冷轧工艺的定义:轧制是将金属坯料通过一对旋转轧辊的间隙(各种形状),因受轧辊的压缩使材料截面减小,长度增加的压力加工方法,这是生产钢材最常用的生产方式,冷轧即是在常温下完成的轧制过程,其所使用的原料为热轧加工成的板带(卷)。
2、酸洗工艺带钢冷轧前必须酸洗,清洗其表面氧化铁皮,因为氧化铁皮在冷轧时会损坏轧辊表面,而导致带钢表面产生缺陷。
通常热轧带钢表面氧化铁皮通常是3层结构:外层为Fe2O3(三氧化二铁),中层为Fe304(四氧化三铁),内层为Fe0(氧化铁)。
先进的冷轧厂多采用高速运行的连续酸洗机组或推拉式酸洗。
以连续酸洗为例,是将带钢连续地通过几个酸洗槽进行酸洗。
为使作业线上过程连续,将前一个热轧带钢卷的尾部和后一个钢卷头部焊接起来,酸洗后带钢按需要的卷重、卷径切断带钢并收卷。
连续酸洗机组除完成清除带钢表面氧化铁皮的任务外,还有几个作用:(1) 用圆盘剪将带钢侧边剪齐。
冷轧带钢生产及工艺
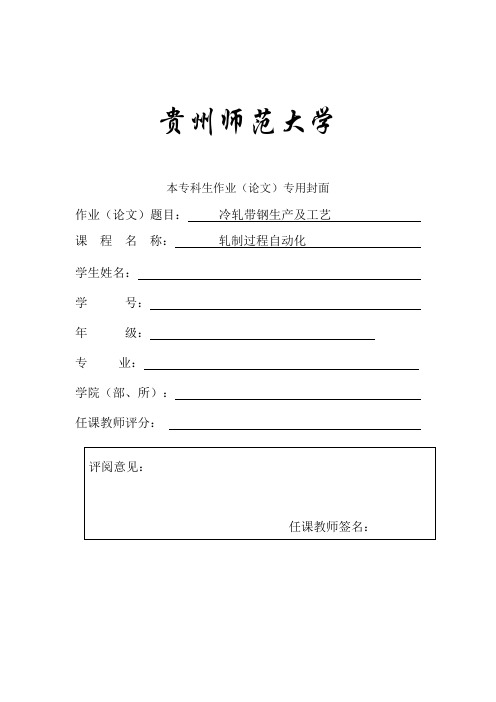
贵州师范大学本专科生作业(论文)专用封面作业(论文)题目:冷轧带钢生产及工艺课程名称:轧制过程自动化学生姓名:学号:年级:专业:学院(部、所):任课教师评分:冷轧带钢生产及工艺摘要:本文阐述了冷轧板带钢生产应用及新技术、新工艺,还有冷轧板带钢的生产工艺特点。
简要介绍了冷轧薄板带钢的生产工艺流程,根据市场需求和当今板带钢轧制最新设备。
关键词:冷轧带钢;轧制工艺;发展在相关学科和技术发展的基础上,冷轧技术发展迅速,面貌日新月异,逐渐形成了现代冷轧工艺。
经过几十年的发展,我国的冷轧事业不断地成长壮大,从只能生产建筑用材的产品发展成为能够生产高级汽车外板、高级家电板、高级包装材料和电工钢产品,无论产量,还是产品的规格品种多样化和质量,都有大幅提高。
一、冷轧带钢技术的特点当今现代冷轧工艺技术的特点和发展趋势基本可以归纳为如下几个方面:1.大力开发高精度轧制技术。
提高冷轧产品的精度,是用户的需要,也是冷轧技术发展的永恒目标。
产品的精度主要指产品的外形尺寸精度,它是社会主义市场经济发展的需要,也是作为产品的最基本条件。
2.以过程冶金理论为基础,以低合金钢为重点,提高产品的冶金质量,扩大品种。
轧制过程是赋予金属一定的尺寸和形状的过程,同时也是赋予金属材料一定组织和性能的过程。
轧材的最终组织性能取决于钢的化学成分、洁净度和均匀度,以及加工过程的热履历。
以物理冶金理论为基础,通过材料化学成分的优化和工艺制度的改进,已经大幅度提高了现有钢种的质量,并通过Nb、V、Ti微合金化开发出大批优良的新钢种。
3.提高连铸比,大力推广连铸连轧工艺及短流程技术。
采用连铸技术可以大幅度降低能耗,提高成材率,提高轧制产品的质量。
近年我国的连铸比大幅度提高,促进了相关轧制技术的发展,特别是连铸和轧制衔接技术的发展。
短流程是钢铁工业的发展方向,是目前国外竞相开发的热点。
尽管目前还存在各种各样的问题,短流程这个大趋势是绝对不会逆转的。
此外,半凝固态压力加工和薄带连续铸轧在将来一定会获得大的发展。
冷轧带钢生产工艺及设备
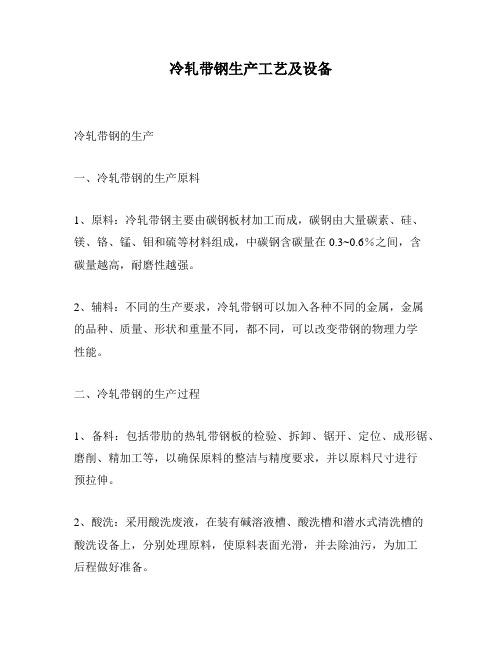
冷轧带钢生产工艺及设备冷轧带钢的生产一、冷轧带钢的生产原料1、原料:冷轧带钢主要由碳钢板材加工而成,碳钢由大量碳素、硅、镁、铬、锰、钼和硫等材料组成,中碳钢含碳量在0.3~0.6%之间,含碳量越高,耐磨性越强。
2、辅料:不同的生产要求,冷轧带钢可以加入各种不同的金属,金属的品种、质量、形状和重量不同,都不同,可以改变带钢的物理力学性能。
二、冷轧带钢的生产过程1、备料:包括带肋的热轧带钢板的检验、拆卸、锯开、定位、成形锯、磨削、精加工等,以确保原料的整洁与精度要求,并以原料尺寸进行预拉伸。
2、酸洗:采用酸洗废液,在装有碱溶液槽、酸洗槽和潜水式清洗槽的酸洗设备上,分别处理原料,使原料表面光滑,并去除油污,为加工后程做好准备。
3、退火:主要用于硬度调整,让带钢带变软以保证后续的加工过程。
4、轧制:经过退火处理带钢后,再进行轧制处理,主要有圆轧和平轧。
圆轧能使带钢表面形成桃形的品质结构,改进带钢的强度和韧性。
5、退火矫平:圆轧、丝条及钢棒等到达要求的尺寸时,需要进行退火矫平,以减少面积拉伸的变形,使其获得理想的宽度和尺寸。
6、清洗:清洗带钢表面的粗糙细节,使带钢表面更加美观、洁净、细腻,以及孔隙界面更易吸收油脂。
7、检测探伤:对冷轧带钢进行纵向和横向的检测,确保产品的完整性,以确保质量满足用户的要求。
三、冷轧带钢的生产设备1、热轧机:用于生产冷轧材料的主要机械,有独立轧辊组轧机、整体轧辊组热轧机、有轧辊组仿形轧机。
2、冷轧机:采用冷轧设备可以生产出高精度的冷轧材料,有平轧机、双辊轧机、圆轧机等,同时还有操作倒梁机来改变带钢纹波,增强工程使用性能。
3、酸洗机:一种由多个可调节的酸洗腔体组成的机械,用于酸洗和清洗冷轧带钢条,去除表面的污染物及油污。
4、球磨机:用于有效去除表面缺陷,修补表面缺陷,增加表面洁净度的装置。
四、冷轧带钢的生产管理1、产品技术管理:为了满足生产要求,需要进行产品技术管理,主要有研发、质量控制、交付、产品能力管理、成本核算、流程改善等。
冷轧带钢的轧制工艺制度

冷轧带钢的轧制工艺制度冷轧带钢是指将钢坯经过冷轧工艺加工而成的带状钢材。
冷轧带钢具有优良的表面质量、尺寸精度和机械性能,广泛应用于汽车制造、电气设备、建筑结构等领域。
下面是冷轧带钢的轧制工艺制度,详细介绍了冷轧带钢的轧制流程、设备要求、工艺参数等内容。
一、工艺流程1.原材料准备:选择合适的钢坯进行切割,并进行清洗去除表面污染物。
2.加热处理:将钢坯进行加热处理,提高其塑性和可塑性,便于后续的轧制加工。
3.轧制:采用冷轧机将加热处理的钢坯进行轧制,初轧得到初始带钢,经过多次轧制得到所需的规格和尺寸。
4.退火处理:对轧制后的带钢进行退火处理,消除内部应力,提高带钢的硬度、韧性和尺寸精度。
5.表面处理:对退火处理后的带钢进行除锈、清洗等处理,使其具有良好的表面质量。
6.成品制备:切割、卷取或剪切带钢,制备成所需的成品形式,如卷材、板材等。
二、设备要求1.冷轧机:冷轧机是冷轧带钢的主要设备,具有较大的轧制压力和辊系数量,能够实现多次轧制和调节带钢的厚度。
2.加热炉:加热炉用于对钢坯进行加热处理,通过控制加热温度和时间,提高钢材的塑性和可塑性。
3.退火炉:退火炉用于对轧制后的带钢进行退火处理,消除内部应力,改善带钢的硬度、韧性和尺寸精度。
4.表面处理设备:包括除锈机、清洗机等,用于清除带钢表面的污垢和氧化物,保证带钢表面的质量。
5.切割、卷取或剪切设备:用于将带钢制备成所需的成品形式,如卷材、板材等。
三、工艺参数1.加热温度:加热处理时的温度应根据不同的钢种和规格进行调节,一般在800℃到1200℃之间。
2.轧制温度:冷轧带钢的轧制温度一般在室温到300℃之间,根据不同的钢种和规格进行调节。
3.轧制压力:冷轧机的轧制压力应根据带钢的规格和厚度进行调整,以确保轧制质量和尺寸精度。
4.退火温度:退火处理时的温度应根据不同的钢种和规格进行调节,一般在500℃到800℃之间。
5.表面处理参数:包括除锈机的清理能力、清洗机的清洗时间和温度等,具体参数根据带钢表面的质量要求进行调节。
冷轧带钢生产工艺流程

冷轧带钢生产工艺流程
一、原料处理
1、原料检验:对原料进行检验,确保原料质量符合要求;
2、原料热处理:将原料进行热处理,改善材料的机械性能;
3、原料加工:将原料进行热轧、冷轧、拉伸、热处理等加工,以满足冷轧带钢的要求;
二、冷轧
1、冷轧机:将原料通过冷轧机进行冷轧,使其成为冷轧带钢;
2、冷轧设备:将冷轧机配备相应的冷轧设备,以确保冷轧带
钢的质量;
3、冷轧工艺:根据冷轧带钢的要求,选择合适的冷轧工艺,
以确保冷轧带钢的质量;
三、检验
1、定期检验:定期对冷轧带钢进行检验,确保其质量;
2、质量检验:对冷轧带钢进行质量检验,确保其质量符合要求;
3、报告检验:提交冷轧带钢的检验报告,以证明其质量符合
要求;
四、包装
1、包装材料:选择合适的包装材料,以防止冷轧带钢在运输
过程中受潮变形;
2、包装方式:根据冷轧带钢的规格,选择合适的包装方式,
以确保冷轧带钢在运输过程中的安全;
3、运输:按照客户的要求,将冷轧带钢运输到指定的目的地。
冷轧带钢生产工艺及设备pdf
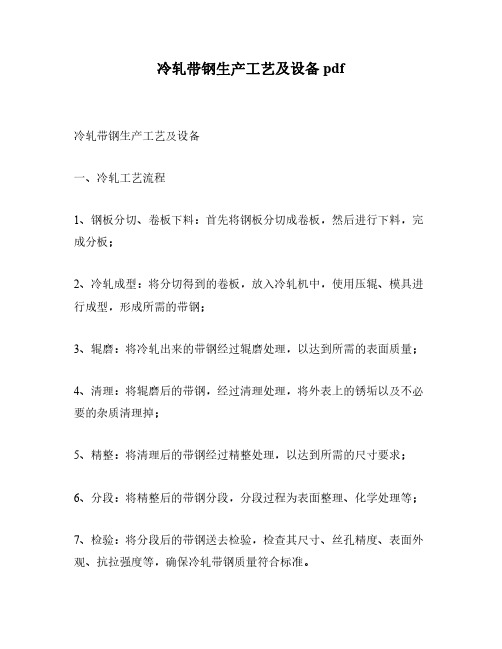
冷轧带钢生产工艺及设备pdf
冷轧带钢生产工艺及设备
一、冷轧工艺流程
1、钢板分切、卷板下料:首先将钢板分切成卷板,然后进行下料,完成分板;
2、冷轧成型:将分切得到的卷板,放入冷轧机中,使用压辊、模具进行成型,形成所需的带钢;
3、辊磨:将冷轧出来的带钢经过辊磨处理,以达到所需的表面质量;
4、清理:将辊磨后的带钢,经过清理处理,将外表上的锈垢以及不必要的杂质清理掉;
5、精整:将清理后的带钢经过精整处理,以达到所需的尺寸要求;
6、分段:将精整后的带钢分段,分段过程为表面整理、化学处理等;
7、检验:将分段后的带钢送去检验,检查其尺寸、丝孔精度、表面外观、抗拉强度等,确保冷轧带钢质量符合标准。
二、冷轧带钢生产设备
1、卷板机:用于分切钢板,得到所需尺寸的卷板;
2、冷轧机:用于冷轧成型,将卷板成型为所需的带钢;
3、辊磨机:用于处理带钢表面,以达到所需的表面质量;
4、清理机:用于清理成型带钢表面上的锈垢以及不必要的杂质,以达到所需的表面外观;
5、精整机:用于处理带钢尺寸,以达到所需的尺寸精度;
6、检验仪:用于查看冷轧后的带钢质量,确保其尺寸、丝孔精度、表面外观、抗拉强度等符合标准。
总之,冷轧带钢生产需要利用钢板分切、冷轧成型、辊磨、清理、精整、分段、检验等工艺流程,同时也需要卷板机、冷轧机、辊磨机、清理机、精整机、检验仪等一系列设备,以保证其质量符合标准且生产效率达标。
冷轧部分《冷轧带钢制工艺》大纲

《冷轧带钢轧制工艺》教学大纲编制陆品荣1.冷轧带钢产品有哪些特点冷轧带产品从外形特点讲A)形状扁平、横断面为矩形、B/h较大、 B)单位体积的表面截面积大。
冷轧板带产品从质量的特点讲有“尺寸准确板形好表面光洁度性能高”。
即 a)尺寸精度要求高,b)板形好。
c)表面质量好。
d)性能好2.冷轧带钢产品规格是怎样分类的?冷轧板带产品规格按厚度分中厚板、薄带钢、和极薄带钢《箔材》三类。
中厚板的板带厚度在4 .mm以上、薄板带的板带厚度一般在4.0 —— 0.2 mm,极薄板带的带钢厚度为0.2 mm以下。
3.冷轧带钢钢种有何分类?冷轧板带按钢种分类有:优质碳素钢、高碳钢(简称优钢)、低合金钢、硅钢、不锈钢、201不锈钢、202不锈钢、T10、40#钢、50#钢、60#钢65MN、铁素体1GR13---9GR13、SK4、SK5、纯铁、纯镍带、铜带、高温合金、精密合金、功能合金和复合钢带、涂锡。
镀锌板等等。
4.精密合金带钢怎样分类?有何用途?精密合金带钢按材料的理化特性和用途分为软磁合金、硬磁合金、弹性合金、膨胀合金、热敏双金属、电阻合金、热电偶材料等七大类。
其用途分别为:软磁合金的特点是磁导率高、广泛用于磁放大器、特殊变压器、磁屏敞、磁头等。
硬磁合金具有较高的矫顽力和剩余磁应值的材料,适用于制造电工仪表中的磁铁、电讯、电声、控制器件和磁分离器、磁滞马达的磁铁。
弹性合金按其性质可分高弹性和恒弹性二种,高弹性材料广泛用于制造精密机械和仪表中的膜片、膜盒、发条及其它弹性组件、恒弹性可用于制造各种频率组件。
膨胀合金分低膨胀合金和定膨胀两种,低膨胀合金用于制造精密仪器、仪表中的平衡轴轮、标准尺和谐振腔等,定膨胀合金用于制造与硬、软玻璃或陶瓷正配的封接部件。
热敏双金属当温度变化时发生定向弯曲、适用于制造继电器、专用温度计以及自控温度装置或自控电流装置中的敏感组件。
电阻合金是指那些具有较恒定的高电阻的合金,它广泛用于制造测量仪器仪表的电阻、电器回路中的精密电阻和电阻应变计。
精选带钢冷轧生产工艺

冷轧工艺流程
2.5 酸再生工艺流程: 废酸收集→废酸过滤→废酸预浓缩→培烧再生→再生酸收集
酸再生是将废酸液定量的送往酸再生装置再生成游离酸返回酸洗机组,同 时得到氧化铁粉的一个体系。
酸再生过程是一个化学过程,浓缩废酸通过喷枪以雾状喷入焙烧炉内,焙 烧炉通过两个喷嘴进行进行操作,操作期间煤气和空气流量自动控制,流 量由孔板和差压传感器测量并在显示屏上显示。
工序工艺流程
2.4.4罩式炉
最大外径:Φ1500mm 最小内径:Φ508㎜
宽度: 232~355㎜
厚度:0.3~2.0mm
最高工作温度:750℃ 设计最大装炉量 30吨
2.4.5车底炉
最大外径:Φ1500mm 最小内径:Φ508㎜
宽度: 232~355㎜
厚度:0.3~2.0mm
高炉煤气压力:0.02~0.04 Mpa 高炉煤气流量:760 M3/T
工序工艺流程
2.2.3.2冷轧时必须采用工艺润滑 我厂采用乳化液进行工艺润滑。(光退2~4﹪、其它1~3﹪) 乳化液主要由2%~10%的矿物油或植物油、乳化剂和水组成。 冷轧采用工艺润滑,主要作用是减小轧制变形区接触弧上的摩擦系数和摩力,
降低钢带的变形抗力【变形抗力:金属抵抗塑性变形的能力】,使轧制压力降低, 这样在已有的轧机能力条件下实现更大的压下,从而能轧制出更薄的钢带。 另一方面,钢带在变形时产生大量的热能,使带钢和轧辊温度升高。辊温升高 会改变辊缝形状,对钢带尺寸精度和板形产生影响。过高的辊温会引起工作辊淬 火层硬度降低,影响钢带表面质量和轧辊使用寿命。同时过高的辊温也会破坏乳 化液的润滑效果。
20.65T
20.65T
冷轧机组
20.45 T
5.0T
冷轧冷硬卷
冷轧高精度薄带钢生产工艺探析
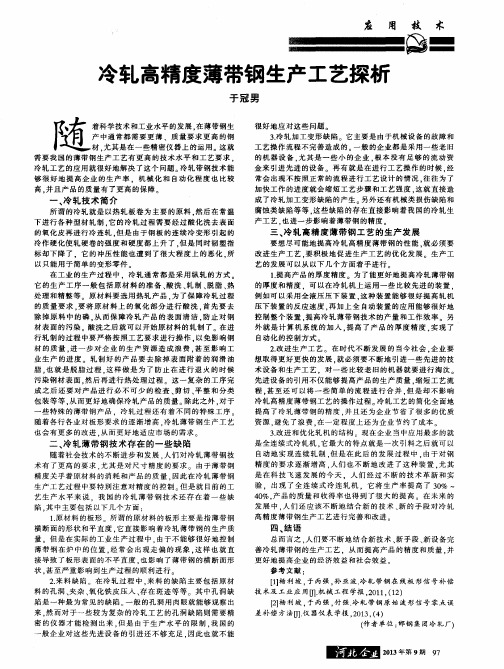
在 工 业 的 生 产 过 程 中 。冷 轧 通 常 都 是 采 用 纵 轧 的方 式 。
1 . 提 高 产 品 的厚 度 精 度 为 了能 更 好 地提 高冷 轧 薄 带 钢
的厚 度 和 精 度 ,可 以 在冷 轧机 上运 用一 些 比较 先 进 的装 置 . 例如可以: 果用 全 液压 压下 装 置 . 这 种 装 置 能 够 很 好 提 高 轧 机
除掉 原料中的磷 . 从 而 保 障冷 轧 产 品 的 表 面 清 洁 . 防 止 对 钢 材 表 面的 污 染 。酸洗 之 后 就 可 以开 始 原 材 料 的 轧 制 了 。在 进
控制整个装置 . 提 高 冷 轧 薄 带 钢 技 术 的 产 量 和 工 作 效 率 。另 外 就 是计 : 算机 系 统 的加 入 . 提高 了产品的厚度精 度 . 实 现 了 自动 化 的 控 制 方 式
一
想取得更好更快的发展 . 就 必 须 要 不 断 地 引 进 一 些 先 进 的 技 术 设 备 和 生 产 工 艺 ,对一 些 比 较 老 旧 的机 器 就 要 进 行 淘 汰 先 进 设 备 的 引 用 不仅 能够 提高 产 品 的生 产 质 量 . 缩 短 工 艺 流 程. 甚 至 还 可 以 将 一 些 简 单 的流 程 进 行 合 并 . 但 是 却 不 影 响 冷 轧 高 精 度 薄 带 钢 工 艺 的操 作 过 程 冷 轧 工艺 的简 化 全 面 地 提 高 了冷 轧 薄 带 钢 的 精度 . 并 且 还 为 企 业 节 省 了很 多 的 优 质 资源 , 避 免 了浪 费 . 在 一定 程 度 上 还 为 企 业 节 约 了成 本
3 . 改进 和优 化 轧 机 的结 构 现 在 企 业 当 中应 用 最 多 的 就 是全连续式冷轧机 . 它 最 大 的特 点 就 是 一 次 引 料 之 后 就 可 以
- 1、下载文档前请自行甄别文档内容的完整性,平台不提供额外的编辑、内容补充、找答案等附加服务。
- 2、"仅部分预览"的文档,不可在线预览部分如存在完整性等问题,可反馈申请退款(可完整预览的文档不适用该条件!)。
- 3、如文档侵犯您的权益,请联系客服反馈,我们会尽快为您处理(人工客服工作时间:9:00-18:30)。
180
4
精轧
可逆
0.6
680
2186
0.2
25
180
5
精轧
可逆
0.5
680
2623
0.1
17
180
四、工艺流程简述
1、酸洗:(原料)→放卷→矫直→剪切(头尾)→焊接→剥壳→储料→平整→酸洗→清洗→钝化→烘干→(上两连轧轧制)
4、精整:(退火)→平整(拉矫)→纵剪→涂油→包装→(入库)
精整的目的是进一步提高产品质量和规格,该工序包括平整、拉矫和纵剪。
平整的目的是通过大张力、小压下,来改善带钢的平直度、带材性能以及部分改变产品交货状态;拉矫是通过大张力的拉伸和矫直机的弯曲矫直,来消除带钢的残余应力和改善板型。本项目将平整和拉矫合为一台机组,退火后的钢卷吊放至开卷机,穿入入口S辊,经平整、弯曲、矫直后,进行收卷,过程中主要控制出口S辊速度以形成张力,在平整前段以张力控制为主,平整后段以设定延伸率的速度为主,以前后段张力实际值并经过对恒张力控制系统的调整,实现最终对延伸率的控制。
GB11253-89、GB716-91
汽车制造、机械制造、轻工、五金冲压和建筑
SPCC
JISG3141
ST12
DIN1623
2
优质碳素结构冷轧薄钢板(卷)和钢带
08Al、08F
GB710-88、GB3522-83
汽车制造、拖拉机、轻工普通冲压成型件、电器、五金
比例(%)
厚度
宽度
热卷
带钢
1
光亮
≥1.2
20-730
Q系列、SP系列、ST系列、SS400、16MnR
Q系列、08系列、SPHC
1
10
2
0.7~1.2
2
20
3
0.5~0.7
5
50
4
薄板
0.3~0.5
2
20
5
合计
10
说明:各种产品的实际比例,可根据市场变化作相应调整;客户有特殊要求的可按QB内控标准供货;产品综合成材率96%。
二、产品执行标准
序号
名称
品种
标准
应用
1
碳素结构钢冷轧薄钢板(卷)及钢带
Q195、Q215、Q235A
轧制过程中,两连轧机组各机架之间及第一架轧机与五辊前张力设备之间、第二架轧机与卷取机之间形成恒定的设定张力,张力值由2台张力称重仪测出。带钢厚度由同位素测厚仪测得,由电动涡轮—涡杆副根据指令手动完成压下或提升,以保证各机架间的连轧关系。轧制工艺润滑采用乳化液,乳化液由乳化液循环系统提供。用后的乳化液流经回流沟流向集液箱,经沉淀,由泵加压送出,过滤后用管道送至轧机处喷淋润滑。夏季气温较高时,乳化液经冷却塔降温后再循环使用。
136000
酸轧连线,酸洗后直接上四辊可逆轧机
1
粗轧
可逆
2.0
680
656
1.0
33
180
43300
2
粗轧
可逆
1.2
680 10ຫໍສະໝຸດ 3 0.8 40
180
3
中轧
可逆
0.8
680
1639
0.4
3、退火:装料→选择退火程序→密封夹紧→抽真空→冷泄漏检查→加热→均热保温→冷却→抽真空→出炉
退火的目的是消除塑性变形过程中的残余应力,改善其加工性能,项目选用钟罩式光亮退火炉进行钢带退火。对于不同的要处理的钢卷材料,必须选择或编制相应的退火程序。操作站可事先编制储存常用的退火程序,在正常生产时,操作站只要调出相应的退火工艺程序,传送给PLC,这个程序在PLC一直工作到下一个新的退火程序。
SPCD
JSG3141
ST14
DIN1623
3
深冲压用冷轧薄钢板和钢带
08Al、08F
GB5213-85
汽车制造和拖拉机制造、成型复杂冲压件、电器、五金
三、工艺流程
1、工艺流程
原料-(分条)-剥壳-酸洗-轧制-脱脂-退火-平整-拉矫-涂油-纵剪(横剪)-检验-包装-称重-标识-入库
热轧带钢由行车吊至放卷机液压移动小车上,启动小车,送料到开卷机,拉出带头引出并送进五辊矫直机,将钢带头部矫直后送入液压剪,切除带头(带尾),可切成45度角或平行剪切,然后将头尾对焊,送入剥壳机剥壳,剥壳后的钢带由两辊夹送机送入笼式储料仓,经过五辊平整后,进入酸洗槽酸洗。
酸洗的目的是为了去除热轧钢带表面的氧化铁皮。本项目采用盐酸酸洗方式,浓度为15%~25%,酸洗温度约65℃~90℃。酸洗槽为花岗岩,总长度为70m,内衬花岗岩石板,以增加耐磨性。为保证酸洗的质量与速度,酸液由耐酸泵、蒸汽加热装置至酸洗槽循环加热供应,酸洗槽中的酸液环流方向与带钢运行方向相反。当酸液中亚铁离子浓度大于120g/L 或酸浓度小于50g/L时,酸液作为废酸排入废酸中和池中。在实际生产中可在新配酸液中适量加入一定比例的废酸,以保证亚铁离子的浓度,这样有利于酸洗的速度,并且可以节约用酸量。另外,为避免在酸洗过程中产生酸雾和过酸洗,酸液中加入适量的缓蚀剂。酸洗后的带钢由挤干辊将酸液挤干。
平整后的钢带流入下道工序,进行纵剪分条。纵剪的目的是切边和分条。切边就是切去带钢边部有质量缺陷的部分,并保证整卷带钢的宽度一致,切边量为2~5mm;分条是为了将带钢纵向裁成所需宽度,满足客户需要的规格。对有特殊要求的带钢,在纵剪后还要进行表面涂油处理,以防锈。
涂油后的钢卷采用纤维包装,也可根据客户需求,采用涂层带进行精包装,包装好的钢卷进行称重,并贴上标识,然后入库,即为成品。
冷轧带钢工艺技术2011-05-19 09:50
年产10万吨冷轧中宽带钢项目工艺技术方案
一、产品方案:年产量为10万吨冷轧薄板,主要以SPCC、ST12和Q系列、08系列等钢种为主,产品厚度0.30-2.0mm,宽度≤730mm.
序号
产品名称
规格(mm)
品种
产量
(万吨)
2、轧制程序
轧制程序表(以冷卷产品规格7t、0.5x680xC为例,忽略宽展)
道次
生产方法
机架型式
轧件尺寸(mm)
压下量
轧制速度(m/min)
年产量(吨/年)
h
b
l
△h
△h%
0
酸洗
连续
3.0
680
470
/
/
30
清洗后的钢带经蒸气烘干炉烘干,烘干是通过蒸气加热、吹风,去除钢带表面残留的水渍和少量酸液。
2、轧制:(酸洗)→开卷→托辊→导卫→轧机→剪切→卷取→卸料→上卷→轧制→卷取→卸料→(退火)
轧制生产线上装置一套自动控制系统,该系统由主要由PLC执行控制。PLC用以完成带钢生产过程中的逻辑顺序控制、闭环控制、计算、通讯及过程I/O处理。