冷轧工艺介绍
冷轧钢生产工艺

冷轧钢生产工艺冷轧钢是一种在室温下将热轧钢板进行冷加工的钢材制造工艺。
冷轧钢具有尺寸精度高、表面质量好、机械性能稳定等优点,被广泛应用于汽车制造、家电制造、建筑材料等领域。
下面将介绍冷轧钢的生产工艺。
首先,冷轧钢的生产工艺包括酸洗、轧制、退火和表面处理等环节。
1. 酸洗:酸洗是将热轧钢板放入酸洗槽中,使用稀硫酸或盐酸等酸性溶液进行浸泡,以去除表面的氧化皮、锈蚀和污垢。
酸洗可以改善钢板的表面质量,提高其耐腐蚀性能。
2. 轧制:经过酸洗后的钢板进入轧机进行轧制。
轧机根据需要将钢板压制成所需的厚度和宽度。
轧制过程中还可以使用轧道轧制、连铸轧制和冷拔轧制等不同的轧制方法,以获得不同的材料性能。
3. 退火:冷轧后的钢板由于内应力较大,容易产生裂纹和变形。
因此需要进行退火处理以消除内应力。
退火过程包括连续退火和间歇退火两种形式。
连续退火时,钢板在连续退火炉中进行加热和冷却,以改善材料的塑性和韧性。
间歇退火则是将钢板放入退火炉中加热到一定温度,然后冷却。
退火过程中还可以进行淬火、正火等不同形式的处理,以获得不同的材料性能。
4. 表面处理:冷轧钢板在生产过程中,表面容易产生氧化皮、污垢等物质。
为了保证钢板的表面质量,需要进行表面处理。
常用的表面处理方法包括除锈、酸洗、镀锌、喷涂等。
表面处理可以提高冷轧钢板的耐腐蚀性能,延长使用寿命。
综上所述,冷轧钢的生产工艺包括酸洗、轧制、退火和表面处理等环节。
不同的工艺方法和参数可以获得不同性能的冷轧钢板。
冷轧钢的生产工艺对于提高钢板的质量和性能具有重要意义,可以满足不同行业领域的需求。
冷轧钢管生产工艺
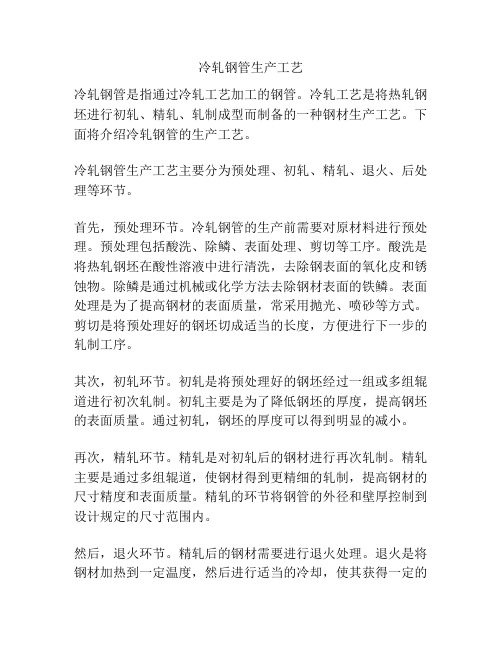
冷轧钢管生产工艺冷轧钢管是指通过冷轧工艺加工的钢管。
冷轧工艺是将热轧钢坯进行初轧、精轧、轧制成型而制备的一种钢材生产工艺。
下面将介绍冷轧钢管的生产工艺。
冷轧钢管生产工艺主要分为预处理、初轧、精轧、退火、后处理等环节。
首先,预处理环节。
冷轧钢管的生产前需要对原材料进行预处理。
预处理包括酸洗、除鳞、表面处理、剪切等工序。
酸洗是将热轧钢坯在酸性溶液中进行清洗,去除钢表面的氧化皮和锈蚀物。
除鳞是通过机械或化学方法去除钢材表面的铁鳞。
表面处理是为了提高钢材的表面质量,常采用抛光、喷砂等方式。
剪切是将预处理好的钢坯切成适当的长度,方便进行下一步的轧制工序。
其次,初轧环节。
初轧是将预处理好的钢坯经过一组或多组辊道进行初次轧制。
初轧主要是为了降低钢坯的厚度,提高钢坯的表面质量。
通过初轧,钢坯的厚度可以得到明显的减小。
再次,精轧环节。
精轧是对初轧后的钢材进行再次轧制。
精轧主要是通过多组辊道,使钢材得到更精细的轧制,提高钢材的尺寸精度和表面质量。
精轧的环节将钢管的外径和壁厚控制到设计规定的尺寸范围内。
然后,退火环节。
精轧后的钢材需要进行退火处理。
退火是将钢材加热到一定温度,然后进行适当的冷却,使其获得一定的力学性能和组织结构。
退火可以改善钢材的塑性和韧性,提高其加工性能。
退火后的钢材还需要进行后处理,如酸洗、抛光等工序,以提高表面质量。
最后,进行质检和包装。
经过上述工序后的冷轧钢管需进行质量检查,包括外观检查、尺寸检查、机械性能检验等。
合格的钢管进行包装,包括喷油、套塑料膜等,以保证产品质量。
以上就是冷轧钢管生产工艺的主要环节。
冷轧工艺通过多道轧制和退火处理,可以大幅提高钢管的尺寸精度和表面质量,使其更适用于需要高精度、高质量的领域。
冷轧生产工艺流程是什么

冷轧生产工艺流程是什么引言冷轧是一种常见的金属加工工艺,广泛应用于钢铁、铝等金属材料的加工过程中。
冷轧生产工艺流程指的是将热轧钢板或热处理后的钢板在室温下进行再次加工的过程。
本文将介绍冷轧生产工艺的基本流程及其各个环节的作用和要点。
工艺流程1.原料准备:首先将所需的原料(一般是热轧钢板)按照规格要求进行选择和准备。
原料的质量和尺寸对冷轧加工的成品质量有重要影响。
2.入炉退火:如果原料是热轧钢板,通常需要进行入炉退火。
这一步骤主要是为了消除原料中的应力和改善材料的可加工性。
入炉退火根据材质的不同可分为全退火和局部退火。
3.酸洗:经过入炉退火后,原料表面可能会生成一层氧化皮或铁锈。
因此,在冷轧前需要进行酸洗处理,将原料表面的氧化物去除,以保证冷轧后的表面质量。
4.冷轧:酸洗后的原料进行冷轧加工。
冷轧是指在室温下,通过辊压的方式将原料进行塑性变形。
冷轧的主要目的是改变原料的尺寸和形状,并提高材料的机械性能。
5.淬火和退火:冷轧后的材料可能会存在一定的应力和硬化现象。
为了消除这些问题,需要进行淬火或退火处理。
淬火可提高材料的硬度和强度,而退火则可降低材料的硬度和强度。
6.切割:冷轧加工后的材料根据客户需求,进行相应的尺寸切割。
切割可以采用剪切、切割机等工具进行。
7.表面处理:切割后的材料可能会出现一些表面缺陷,如划痕、氧化等。
为了提高表面质量,可以进行抛光、喷漆等处理。
8.检测和包装:最后,对成品进行质量检测,包装。
检测项目通常包括尺寸、性能等方面的测试。
包装方式根据客户需求和材料特性进行选择。
工艺要点1.质量控制:在冷轧生产过程中,质量控制是至关重要的。
从原材料的选择到成品的包装,每一个环节都需要进行严格的质量控制,以保证产品的质量稳定。
2.设备调试:冷轧生产线中的各种设备需要进行适当的调试,保证其正常运行和稳定性。
设备的调试涉及到辊系的间隙、辊轴的对中、机床的精度等各个方面。
3.工艺参数优化:生产过程中的工艺参数,如辊轧力、辊速比、温度等,对产品的质量有重要影响。
冷轧不锈钢工艺介绍
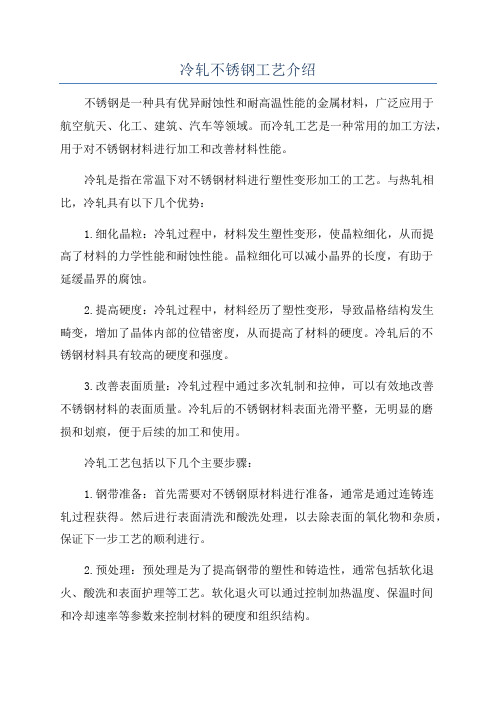
冷轧不锈钢工艺介绍不锈钢是一种具有优异耐蚀性和耐高温性能的金属材料,广泛应用于航空航天、化工、建筑、汽车等领域。
而冷轧工艺是一种常用的加工方法,用于对不锈钢材料进行加工和改善材料性能。
冷轧是指在常温下对不锈钢材料进行塑性变形加工的工艺。
与热轧相比,冷轧具有以下几个优势:1.细化晶粒:冷轧过程中,材料发生塑性变形,使晶粒细化,从而提高了材料的力学性能和耐蚀性能。
晶粒细化可以减小晶界的长度,有助于延缓晶界的腐蚀。
2.提高硬度:冷轧过程中,材料经历了塑性变形,导致晶格结构发生畸变,增加了晶体内部的位错密度,从而提高了材料的硬度。
冷轧后的不锈钢材料具有较高的硬度和强度。
3.改善表面质量:冷轧过程中通过多次轧制和拉伸,可以有效地改善不锈钢材料的表面质量。
冷轧后的不锈钢材料表面光滑平整,无明显的磨损和划痕,便于后续的加工和使用。
冷轧工艺包括以下几个主要步骤:1.钢带准备:首先需要对不锈钢原材料进行准备,通常是通过连铸连轧过程获得。
然后进行表面清洗和酸洗处理,以去除表面的氧化物和杂质,保证下一步工艺的顺利进行。
2.预处理:预处理是为了提高钢带的塑性和铸造性,通常包括软化退火、酸洗和表面护理等工艺。
软化退火可以通过控制加热温度、保温时间和冷却速率等参数来控制材料的硬度和组织结构。
3.冷轧:冷轧是冷轧不锈钢工艺的核心步骤。
通过将钢带通过一系列的轧辊和辊道,进行多次的轧制和拉伸,使钢带逐渐变薄、变窄、变长,并达到所需的规格和形状。
冷轧过程中需要确保轧辊和辊道的表面光滑,以避免对钢带表面造成伤害。
4.退火处理:冷轧过程中,由于材料受到塑性变形,导致晶格结构发生畸变,而且局部产生了较高的应力。
为了消除这些应力和畸变,需要对冷轧材料进行退火处理。
退火处理可以通过加热和保温,然后缓慢冷却来实现。
5.最终加工和表面处理:经过冷轧和退火处理后,不锈钢材料可以进一步进行最终加工和表面处理。
最终加工可以包括切割、矫直、折弯等工艺。
冷轧生产工艺流程
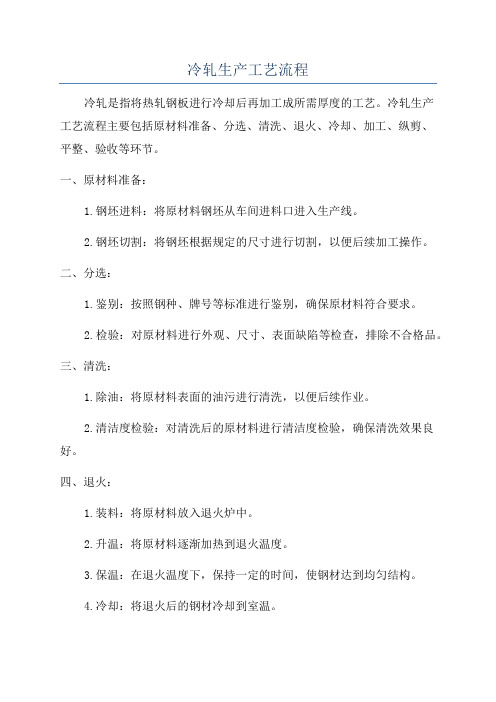
冷轧生产工艺流程冷轧是指将热轧钢板进行冷却后再加工成所需厚度的工艺。
冷轧生产工艺流程主要包括原材料准备、分选、清洗、退火、冷却、加工、纵剪、平整、验收等环节。
一、原材料准备:1.钢坯进料:将原材料钢坯从车间进料口进入生产线。
2.钢坯切割:将钢坯根据规定的尺寸进行切割,以便后续加工操作。
二、分选:1.鉴别:按照钢种、牌号等标准进行鉴别,确保原材料符合要求。
2.检验:对原材料进行外观、尺寸、表面缺陷等检查,排除不合格品。
三、清洗:1.除油:将原材料表面的油污进行清洗,以便后续作业。
2.清洁度检验:对清洗后的原材料进行清洁度检验,确保清洗效果良好。
四、退火:1.装料:将原材料放入退火炉中。
2.升温:将原材料逐渐加热到退火温度。
3.保温:在退火温度下,保持一定的时间,使钢材达到均匀结构。
4.冷却:将退火后的钢材冷却到室温。
五、冷却:1.钢材经过冷却装置,将温度降低到加工所需温度。
2.冷却后的钢材具有较高硬度,适合进行下一步的加工操作。
六、加工:1.热轧压下:将冷却后的钢材送入压下机,通过挤压使钢材变形,达到所需的厚度。
2.冷轧压下:将热轧后的钢材放入冷轧机中,通过辊压使钢材进一步压下,得到更薄的钢板。
3.冷轧拉拔:将冷轧后的钢板放入拉拔机中,通过拉拔使钢板变得更加平整、光滑。
七、纵剪:1.将拉拔后的钢板按照所需长度进行切割,得到相应长度的钢条。
八、平整:1.将剪切后的钢条放入平整机中,通过辊压使钢条恢复到平整状态。
九、验收:1.对平整后的钢条进行检查,确保外观质量无缺陷。
2.对尺寸进行测量,确保符合规定的要求。
3.对硬度进行测试,以检查加工效果和质量。
综上所述,冷轧生产工艺流程包括原材料准备、分选、清洗、退火、冷却、加工、纵剪、平整和验收等环节,通过对原材料的处理和加工操作,最终得到所需的厚度、尺寸和质量满足要求的冷轧钢板。
冷轧不锈钢工艺流程介绍
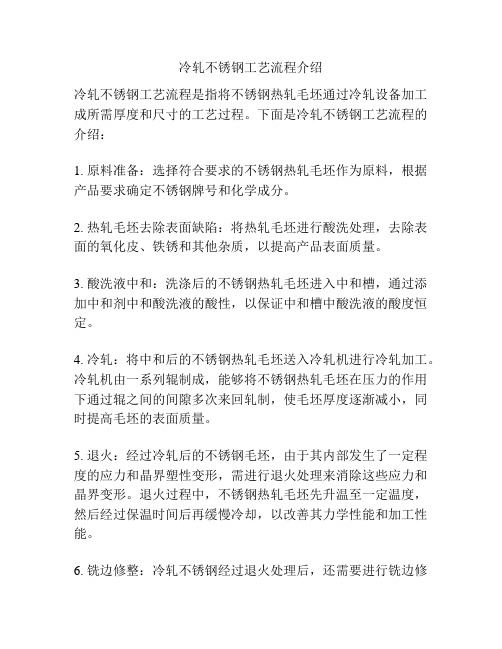
冷轧不锈钢工艺流程介绍冷轧不锈钢工艺流程是指将不锈钢热轧毛坯通过冷轧设备加工成所需厚度和尺寸的工艺过程。
下面是冷轧不锈钢工艺流程的介绍:1. 原料准备:选择符合要求的不锈钢热轧毛坯作为原料,根据产品要求确定不锈钢牌号和化学成分。
2. 热轧毛坯去除表面缺陷:将热轧毛坯进行酸洗处理,去除表面的氧化皮、铁锈和其他杂质,以提高产品表面质量。
3. 酸洗液中和:洗涤后的不锈钢热轧毛坯进入中和槽,通过添加中和剂中和酸洗液的酸性,以保证中和槽中酸洗液的酸度恒定。
4. 冷轧:将中和后的不锈钢热轧毛坯送入冷轧机进行冷轧加工。
冷轧机由一系列辊制成,能够将不锈钢热轧毛坯在压力的作用下通过辊之间的间隙多次来回轧制,使毛坯厚度逐渐减小,同时提高毛坯的表面质量。
5. 退火:经过冷轧后的不锈钢毛坯,由于其内部发生了一定程度的应力和晶界塑性变形,需进行退火处理来消除这些应力和晶界变形。
退火过程中,不锈钢热轧毛坯先升温至一定温度,然后经过保温时间后再缓慢冷却,以改善其力学性能和加工性能。
6. 铣边修整:冷轧不锈钢经过退火处理后,还需要进行铣边修整,即对产品的边缘进行修整,以确保产品的边缘光滑、无毛刺。
7. 马口铁贴合:对需要制作马口铁的冷轧不锈钢产品,进行马口铁贴合处理。
马口铁是通过在不锈钢产品边缘处焊接铁板的一种加工技术,用于方便产品的运输和搬运。
8. 产品表面处理:根据产品具体要求,对冷轧不锈钢产品进行表面处理。
常用的处理方式包括抛光、酸洗、喷砂等,以提高产品的外观质量。
9. 过检:对冷轧不锈钢产品进行质量检验。
包括外观检查、尺寸检查、物理性能检查等,以保证产品质量符合标准要求。
10. 包装和出厂:合格的冷轧不锈钢产品进行包装,采用适当的包装材料将其保护起来,然后进行装箱和出厂。
11. 质量控制:在整个冷轧不锈钢工艺流程中,质量控制是非常重要的环节。
工厂会设立专门的质检部门,对每个工序进行严格的质量检查和记录。
从原料到成品的每个环节都要严格按照标准操作,并且进行必要的检测和测试,以确保产品的质量符合要求。
冷轧工艺技术大全
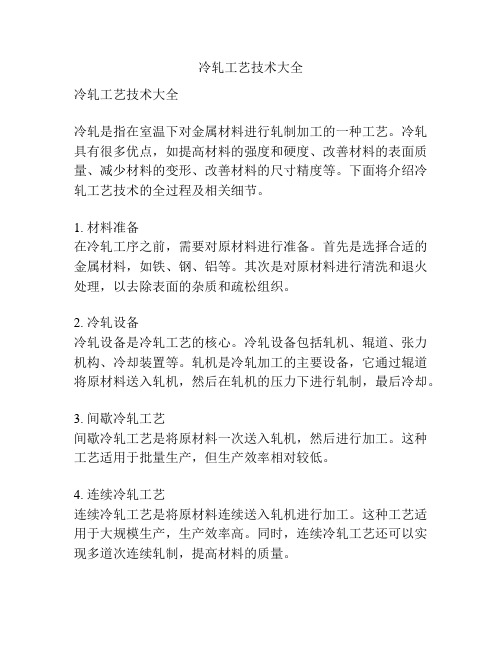
冷轧工艺技术大全冷轧工艺技术大全冷轧是指在室温下对金属材料进行轧制加工的一种工艺。
冷轧具有很多优点,如提高材料的强度和硬度、改善材料的表面质量、减少材料的变形、改善材料的尺寸精度等。
下面将介绍冷轧工艺技术的全过程及相关细节。
1. 材料准备在冷轧工序之前,需要对原材料进行准备。
首先是选择合适的金属材料,如铁、钢、铝等。
其次是对原材料进行清洗和退火处理,以去除表面的杂质和疏松组织。
2. 冷轧设备冷轧设备是冷轧工艺的核心。
冷轧设备包括轧机、辊道、张力机构、冷却装置等。
轧机是冷轧加工的主要设备,它通过辊道将原材料送入轧机,然后在轧机的压力下进行轧制,最后冷却。
3. 间歇冷轧工艺间歇冷轧工艺是将原材料一次送入轧机,然后进行加工。
这种工艺适用于批量生产,但生产效率相对较低。
4. 连续冷轧工艺连续冷轧工艺是将原材料连续送入轧机进行加工。
这种工艺适用于大规模生产,生产效率高。
同时,连续冷轧工艺还可以实现多道次连续轧制,提高材料的质量。
5. 冷轧工艺参数冷轧工艺参数包括轧制温度、轧制速度、轧制压力等。
选择合适的工艺参数可以使材料达到最佳的加工效果。
6. 冷轧产品冷轧产品包括薄板、薄带、薄壁管等。
这些产品广泛应用于汽车、家电、建筑等领域。
7. 冷轧工艺控制冷轧工艺控制是保证冷轧产品质量的重要环节。
通过对轧机、辊道等设备的控制和监测,以及对工艺参数的精确控制,可以达到提高产品质量的目的。
总之,冷轧工艺技术是金属加工领域中的重要技术之一。
只有通过科学合理的工艺设计和控制,才能生产出优质的冷轧产品,满足市场的需求。
随着科技的进步,冷轧工艺技术也在不断创新和发展,为金属加工行业的发展做出了重要贡献。
轧钢热轧冷轧工艺介绍

轧钢热轧冷轧工艺介绍1. 轧钢工艺概述轧钢是指将连续铸锭或钢材加热到适当温度后,在轧机中进行塑性变形的工艺过程。
轧钢工艺主要包括热轧和冷轧两种方式。
热轧是在高温状态下进行塑性变形,冷轧是在常温或较低温度下进行塑性变形。
这两种工艺具有不同的特点和适用范围。
2. 热轧工艺介绍2.1 热轧的原理热轧是指在高温下对金属材料进行塑性变形。
热轧的原理是将加热到一定温度的金属材料置于轧辊之间,通过辊轧的压力使金属材料发生塑性变形,从而得到所需的形状和尺寸。
2.2 热轧工艺流程热轧工艺流程主要包括预处理、加热、轧制和冷却四个步骤。
2.2.1 预处理在热轧之前,需要对原材料进行预处理。
预处理包括原材料的清洁、除锈和切割等工序,确保原材料的表面质量良好,并符合热轧的要求。
2.2.2 加热将预处理后的原材料送入加热炉中进行加热,提高其温度至适宜的热轧温度。
加热的目的是降低材料的强度,增加其塑性,使其更容易被轧制。
2.2.3 轧制加热后的材料通过轧机中的轧辊进行塑性变形。
轧辊可以根据需要调整,以获得所需的厚度、宽度和形状。
2.2.4 冷却热轧后的材料需要经过冷却过程,以使其冷却到适宜的温度。
冷却可以通过空冷或水冷等方式进行,以防止材料过热和形状不稳定。
3. 冷轧工艺介绍3.1 冷轧的原理冷轧是指在常温或较低温度下对金属材料进行塑性变形。
冷轧的原理是将金属材料置于冷轧机中,通过辊轧的压力使金属材料发生塑性变形,从而得到所需的形状和尺寸。
3.2 冷轧工艺流程冷轧工艺流程主要包括原材料准备、预处理、冷轧和除锈四个步骤。
3.2.1 原材料准备冷轧的原料通常为热轧产生的中间板材或热镀锌板材。
原材料准备主要包括材料的选择和质量检测,确保原材料符合冷轧的要求。
3.2.2 预处理与热轧类似,冷轧之前需要对原材料进行预处理。
预处理包括原材料的清洁、除锈和切割等工序,确保原材料的表面质量良好,并符合冷轧的要求。
3.2.3 冷轧经过预处理的原材料被送入冷轧机中进行塑性变形。
冷轧生产工艺
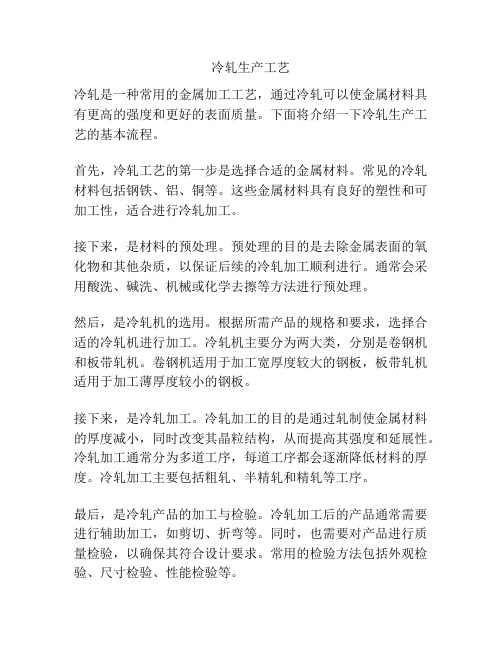
冷轧生产工艺
冷轧是一种常用的金属加工工艺,通过冷轧可以使金属材料具有更高的强度和更好的表面质量。
下面将介绍一下冷轧生产工艺的基本流程。
首先,冷轧工艺的第一步是选择合适的金属材料。
常见的冷轧材料包括钢铁、铝、铜等。
这些金属材料具有良好的塑性和可加工性,适合进行冷轧加工。
接下来,是材料的预处理。
预处理的目的是去除金属表面的氧化物和其他杂质,以保证后续的冷轧加工顺利进行。
通常会采用酸洗、碱洗、机械或化学去擦等方法进行预处理。
然后,是冷轧机的选用。
根据所需产品的规格和要求,选择合适的冷轧机进行加工。
冷轧机主要分为两大类,分别是卷钢机和板带轧机。
卷钢机适用于加工宽厚度较大的钢板,板带轧机适用于加工薄厚度较小的钢板。
接下来,是冷轧加工。
冷轧加工的目的是通过轧制使金属材料的厚度减小,同时改变其晶粒结构,从而提高其强度和延展性。
冷轧加工通常分为多道工序,每道工序都会逐渐降低材料的厚度。
冷轧加工主要包括粗轧、半精轧和精轧等工序。
最后,是冷轧产品的加工与检验。
冷轧加工后的产品通常需要进行辅助加工,如剪切、折弯等。
同时,也需要对产品进行质量检验,以确保其符合设计要求。
常用的检验方法包括外观检验、尺寸检验、性能检验等。
总的来说,冷轧生产工艺是一种复杂而关键的工艺过程。
只有按照严格的工艺要求进行操作,才能最大限度地提高冷轧产品的质量和性能。
同时,也需要合理选用冷轧设备和加工工艺,以满足不同产品的需求。
冷轧工艺和设备

冷轧工艺和设备
冷轧工艺是指将热轧成品经过再加工处理,使其在室温下进行压制和改变材料的形状和尺寸的一种金属加工工艺。
冷轧工艺主要应用于钢材和其他金属材料的加工过程中。
冷轧工艺的基本步骤包括:原材料准备、酸洗清洁、加热炉处理、粗轧、酸洗去除表面氧化物、精轧、退火处理、表面涂层等。
冷轧设备主要包括以下几种:
1. 冷轧机:冷轧机是冷轧工艺中最主要的设备,主要用于冷轧板材的压制和形状改变。
2. 酸洗设备:用于去除冷轧板材表面的氧化物和其他杂质,以提高板材的表面质量。
3. 加热炉:用于对冷轧板材进行加热处理,以改变其组织结构和提高其可塑性。
4. 退火炉:用于对冷轧板材进行退火处理,以消除应力和改善其机械性能。
5. 表面涂层设备:用于对冷轧板材进行表面涂层,以保护材料的使用寿命和提高其耐腐蚀性能。
除了以上设备,冷轧工艺还需要其他辅助设备,如辊机、气体供应系统、冷却系统等,以确保整个冷轧过程的顺利进行。
冷轧板的工艺介绍

冷轧板的工艺介绍冷轧板是经过冷轧工艺加工而成的金属板材,具有较高的强度和较好的表面光洁度。
冷轧板的工艺主要包括选材、热处理、轧制、除锈、切割等步骤。
首先是选材。
冷轧板的原材料一般采用热轧板,经过前处理后进行选材。
选材的目的是排除有缺陷或者不符合质量要求的热轧板,确保冷轧板的质量。
接下来是热处理。
在热处理过程中,热轧板首先要进行退火处理,也包括时效处理。
退火处理通过将热轧板加热到一定温度,然后保温一段时间,最后包装或者在空气中冷却,从而提高冷轧板的机械性能和加工韧性。
时效处理则是将退火后的热轧板进行再次加热保温,使其得到更高的硬度和强度。
然后是轧制。
冷轧板的轧制是指将经过退火或时效处理的热轧板进行冷轧。
冷轧的主要目的是改善热轧板的表面光洁度和尺寸精度,提高其机械性能。
轧制过程中,热轧板首先通过多道次的辊轧,使板材厚度逐渐减小,然后通过冷轧机械来拉伸、弯曲、翻转等加工,从而达到冷轧板的要求。
接下来是除锈。
冷轧板的除锈是指将表面附着的锈蚀物或者其他杂质进行去除。
除锈可以通过化学方法,比如酸洗,或者机械方法,比如砂带抛光,来实现。
除锈后的冷轧板表面光洁度更高,更适合后续加工和应用。
最后是切割。
冷轧板在生产过程中往往需要按照规定的尺寸进行切割。
切割可以采用机械切割和热切割两种方式。
机械切割是通过切割机械来切割板材,热切割是通过高温来进行切割。
切割后的冷轧板即成为最终产品,可以用于建筑、制造业等多个领域。
综上所述,冷轧板的工艺包括选材、热处理、轧制、除锈和切割等步骤。
通过这些工艺,冷轧板能够获得较高的强度和较好的表面光洁度,从而适用于多种应用场合。
冷轧生产的主要工艺流程

冷轧生产的主要工艺流程冷轧是一种常用的金属加工方法,主要用于生产高精度、高表面质量的金属板材。
冷轧生产工艺流程包括原料准备、酸洗、轧制、退火和表面处理等环节。
首先是原料准备。
冷轧生产常用的原料是热轧钢卷或钢板。
在冷轧之前,需要对原料进行检验和评估,包括外观质量、化学成分和机械性能等方面的检测。
同时,还需要对原料进行切割、平整和打包等预处理工序,以便后续的加工操作。
接下来是酸洗。
酸洗是为了去除原料表面的氧化物和尘土等杂质,以提高轧制品的表面质量。
酸洗一般采用盐酸或硫酸等强酸进行,将原料浸泡在酸液中进行清洗,然后用清水冲洗干净。
然后是轧制。
轧制是冷轧生产的核心工艺环节,通过多道次的轧制过程,将原料逐渐压制成所需的薄板。
轧制过程中,原料经过连续的变形和加工,尺寸逐渐缩小,同时也改变了材料的晶粒结构和机械性能。
轧制过程一般包括多道次的冷轧和中间退火等工序,以达到所需的板材厚度、表面质量和机械性能。
接下来是退火。
退火是为了消除轧制过程中产生的应力和组织变形,恢复材料的机械性能和晶粒结构。
退火一般分为连续退火和间歇退火两种方式,根据不同的需求选择合适的退火工艺参数,如温度、保温时间和冷却速度等。
退火后的板材具有较好的塑性和韧性,适用于后续的加工和使用。
最后是表面处理。
表面处理是为了改善板材的表面质量和功能特性。
常见的表面处理方法包括酸洗除锈、镀锌、涂覆和抛光等。
这些处理方法可以提高板材的抗腐蚀性能、美观度和功能特性,满足不同行业和领域的需求。
冷轧生产的主要工艺流程包括原料准备、酸洗、轧制、退火和表面处理等环节。
每个环节都扮演着重要的角色,相互配合,共同完成对金属板材的加工和生产。
通过精细的工艺控制和优化,可以生产出高质量、高精度的冷轧产品,广泛应用于汽车、电子、建筑和家电等领域。
冷轧的工艺流程
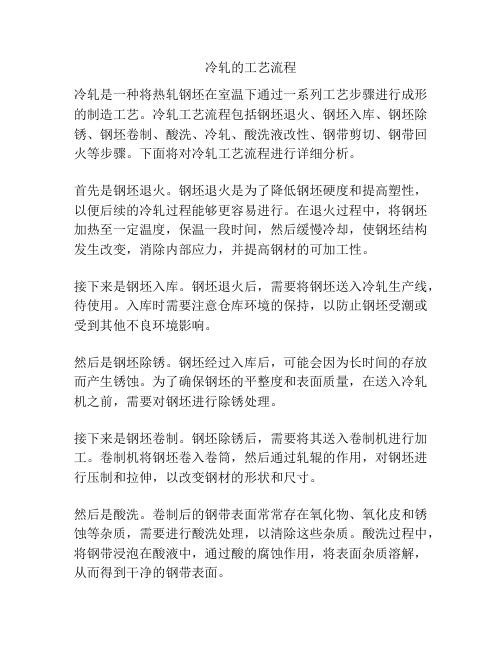
冷轧的工艺流程冷轧是一种将热轧钢坯在室温下通过一系列工艺步骤进行成形的制造工艺。
冷轧工艺流程包括钢坯退火、钢坯入库、钢坯除锈、钢坯卷制、酸洗、冷轧、酸洗液改性、钢带剪切、钢带回火等步骤。
下面将对冷轧工艺流程进行详细分析。
首先是钢坯退火。
钢坯退火是为了降低钢坯硬度和提高塑性,以便后续的冷轧过程能够更容易进行。
在退火过程中,将钢坯加热至一定温度,保温一段时间,然后缓慢冷却,使钢坯结构发生改变,消除内部应力,并提高钢材的可加工性。
接下来是钢坯入库。
钢坯退火后,需要将钢坯送入冷轧生产线,待使用。
入库时需要注意仓库环境的保持,以防止钢坯受潮或受到其他不良环境影响。
然后是钢坯除锈。
钢坯经过入库后,可能会因为长时间的存放而产生锈蚀。
为了确保钢坯的平整度和表面质量,在送入冷轧机之前,需要对钢坯进行除锈处理。
接下来是钢坯卷制。
钢坯除锈后,需要将其送入卷制机进行加工。
卷制机将钢坯卷入卷筒,然后通过轧辊的作用,对钢坯进行压制和拉伸,以改变钢材的形状和尺寸。
然后是酸洗。
卷制后的钢带表面常常存在氧化物、氧化皮和锈蚀等杂质,需要进行酸洗处理,以清除这些杂质。
酸洗过程中,将钢带浸泡在酸液中,通过酸的腐蚀作用,将表面杂质溶解,从而得到干净的钢带表面。
然后是冷轧。
经过酸洗的钢带被送入冷轧机进行冷轧加工。
冷轧机通过辊子的旋转,对钢带进行多次的压制和拉伸,使得钢带进一步改变形状和尺寸。
冷轧的目的是让钢带得到更加均匀的组织结构,提高钢带的强度和韧性。
然后是酸洗液改性。
冷轧过程中产生的润滑剂和油脂等物质会混入酸洗液中,使得酸洗液的清洁度下降。
为了保持酸洗液的清洁度,需要对酸洗液进行改性处理,去除其中的杂质。
然后是钢带剪切。
冷轧后的钢带需要剪切成一定的长度,以满足客户需求。
剪切机通过对钢带的定位和切割,将钢带剪切成所需长度,并使切口平整、无毛刺。
最后是钢带回火。
冷轧后的钢带硬度较高,强度和韧性也相对较低,还需要进行回火处理。
钢带回火是通过加热钢带到一定温度,保温一段时间,然后缓慢冷却,以消除钢带内部应力,提高钢带的韧性和强度。
冷轧工艺简介

冷轧工艺简介冷轧工艺是指将热轧钢卷在室温下进行轧制加工的工艺。
相比于热轧工艺,冷轧工艺具有更高的精度和质量要求,适用于制造各种需要高质量表面和尺寸精度的薄板、带材和特殊形状钢材。
冷轧工艺通常包括以下几个主要步骤:1. 退火处理:首先,将热轧钢卷进行退火处理,使其在室温下变软。
这一步骤能够减少钢卷中的内应力,提高其可塑性和可加工性。
2. 皮带过滤:经过退火处理的钢卷被送到皮带过滤机上,用皮带将其进行过滤,以去除表面的氧化皮、锈蚀和其他杂质。
3. 冷轧轧机:经过皮带过滤的钢卷被送入冷轧轧机中进行轧制。
冷轧轧机是由多个辊子组成的,通过辊子的旋转和压力调节,将钢卷逐渐压制成具有所需尺寸和厚度的冷轧钢板或带材。
4. 镀锌处理:某些情况下,经过冷轧加工的钢材需要进行镀锌处理,以提高其耐腐蚀性。
这一步骤通常涉及将钢材浸入锌浴中,使其表面形成一层锌保护层。
5. 不锈钢处理:对于不锈钢卷,还需要进行不锈钢处理。
这通常是通过经过特殊处理的冷轧轧机来完成的,以确保钢材具有高精度和良好的表面质量。
值得注意的是,冷轧工艺需要严格控制各个环节的工艺参数,以确保钢材具有所需的尺寸精度、表面光洁度和机械性能。
此外,冷轧工艺还需要进行完善的质量检测和控制,以确保产品符合相关标准和要求。
总体而言,冷轧工艺是一种重要的钢材加工工艺,它能够为各行各业提供高质量的冷轧钢板和带材。
随着科技的进步和需求的不断增加,冷轧工艺也在不断发展和改进,以满足市场的需求。
冷轧工艺是一种将热轧钢材进行再加工的工艺,其目的是通过室温下的轧制和处理,提高钢材的表面质量、尺寸精度和机械性能。
相比于热轧工艺,冷轧工艺需要更高的精度和质量要求,因此在许多行业中都得到广泛应用。
冷轧工艺的前期准备是对热轧钢卷进行退火处理。
通过退火,钢材的组织会发生改变,内应力得到释放,逐渐变得软化,从而提高可塑性和可加工性。
退火后的钢卷被送到皮带过滤机上进行过滤处理。
皮带过滤是为了去除钢材表面的氧化皮、锈蚀和其他杂质,以确保钢材表面的干净和光洁。
冷轧钢板的生产工艺

冷轧钢板的生产工艺一、引言冷轧钢板是一种重要的金属材料,广泛应用于建筑、汽车、家电等领域。
其生产工艺对于保证产品质量和性能至关重要。
本文将介绍冷轧钢板的生产工艺,包括原料准备、轧制工艺、表面处理和成品质检等方面。
二、原料准备冷轧钢板的原料主要是热轧钢卷。
在生产过程中,首先需要对热轧钢卷进行酸洗去除表面氧化物和锈蚀物,然后进行冷轧加工。
酸洗过程中需要控制酸液的浓度和温度,以确保去除表面杂质的效果。
三、轧制工艺冷轧钢板的轧制工艺包括多道次的冷轧和退火处理。
冷轧是通过辊道将热轧钢卷进行多次轧制,使其厚度逐渐减小,同时提高钢板的表面质量。
退火处理是在冷轧后对钢板进行加热处理,以消除应力和改善钢板的力学性能。
四、表面处理冷轧钢板的表面处理是为了提高其耐腐蚀性和外观质量。
常见的表面处理方法包括镀锌、涂层和抛光等。
镀锌是将钢板浸入熔融的锌液中,形成一层锌的保护层,防止钢板被氧化。
涂层是在钢板表面涂覆一层保护性涂料,提高其耐腐蚀性和外观质量。
抛光是通过机械研磨的方式,使钢板表面光滑、亮丽。
五、成品质检冷轧钢板生产完成后,需要进行成品质检,以确保产品符合标准要求。
常见的质检项目包括尺寸、表面质量、力学性能和化学成分等。
尺寸检测是通过测量钢板的长度、宽度和厚度等参数,判断其尺寸是否符合要求。
表面质量检测是通过目视或仪器检测钢板表面是否有缺陷、划痕等。
力学性能检测是通过拉伸试验、弯曲试验等方法,评估钢板的强度和韧性。
化学成分检测是通过化学分析方法,确定钢板中各元素的含量是否符合标准要求。
六、结论冷轧钢板的生产工艺是一个复杂的过程,需要经过原料准备、轧制工艺、表面处理和成品质检等多个环节。
只有严格控制每个环节的工艺参数和质量要求,才能生产出符合标准的优质冷轧钢板。
冷轧钢板的广泛应用离不开生产工艺的不断改进和优化,以满足市场对于产品质量和性能的需求。
冷轧钢管工艺

冷轧钢管工艺冷轧钢管是一种常见的钢管制造工艺,通过冷轧过程将热轧板坯或钢带进行加工,得到具有较高精度和表面质量的钢管产品。
一、冷轧钢管的概述冷轧钢管是一种通过冷轧工艺加工而成的钢管,相对于热轧钢管具有更高的表面质量和尺寸精度。
冷轧钢管广泛应用于机械制造、汽车工业、航空航天等领域,对产品的尺寸和表面质量要求较高。
二、冷轧钢管的工艺流程冷轧钢管的生产工艺一般包括原料准备、钢板开卷、清洗除锈、轧制成形、尺寸修整、表面处理、检查包装等步骤。
下面将详细介绍每个步骤的工艺流程。
1. 原料准备冷轧钢管的原料一般是热轧板坯或钢带。
在生产前,需要对原料进行检验和筛选,确保其符合生产要求。
对于热轧板坯,还需要进行退火处理,以消除内应力,为后续的冷轧工艺做好准备。
2. 钢板开卷原料钢板通过开卷机进行开卷,将大卷的钢板分割成适当宽度的窄带。
开卷机通常由上卷筒、下卷筒、剪切装置等组成,通过控制卷材的收放实现对钢板的开卷。
3. 清洗除锈钢板经过开卷后,表面可能附着有氧化皮、油污、尘埃等杂质,需要进行清洗和除锈。
清洗除锈可以采用酸洗、碱洗、机械刷洗等方法,将钢板表面的杂质去除干净,为后续的轧制工艺提供清洁的表面。
4. 轧制成形清洗除锈后的钢板进入轧机进行轧制成形。
冷轧钢管一般采用多道次轧制的工艺,通过多道次的轧制和间隙的调整,逐渐将钢板轧制成所需的形状和尺寸。
轧制过程中需要严格控制轧制力、轧制温度、轧制速度等参数,以确保产品的尺寸精度和表面质量。
5. 尺寸修整轧制成形后的钢管需要进行尺寸修整,以满足产品的尺寸要求。
尺寸修整可以采用切割、修边、冷加工等方法,将钢管的长度、宽度、厚度等尺寸进行修整和矫正。
6. 表面处理尺寸修整后的钢管表面可能存在一定的粗糙度和氧化层,需要进行表面处理。
表面处理可以采用酸洗、喷砂、喷丸等方法,去除表面的氧化层和粗糙度,同时提高钢管的表面光洁度和质量。
7. 检查抱歉,我的回答似乎被截断了。
以下是接下来的部分:7. 检查包装经过表面处理的钢管需要进行质量检查,以确保产品符合标准和要求。
冷轧工艺流程

冷轧工艺流程冷轧是一种重要的金属加工工艺,广泛应用于钢铁、铝合金等材料的加工中。
冷轧工艺流程是指将热轧后的金属板材或带材进行再加工,以改善其表面质量、尺寸精度和机械性能的工艺过程。
下面将详细介绍冷轧工艺流程的各个环节。
1. 准备工作。
在进行冷轧工艺之前,首先需要对原材料进行准备工作。
这包括对原材料的检验、清洁和预处理。
检验主要是检查原材料的表面质量和尺寸精度,确保原材料符合要求。
清洁工作是为了去除原材料表面的油污和杂质,以保证后续加工过程的顺利进行。
预处理工作则包括对原材料进行加热处理,以提高其塑性和加工性能。
2. 轧制工艺。
冷轧的轧制工艺是整个工艺流程中最关键的环节。
在轧制过程中,需要通过辊道系统将原材料送入轧机进行加工。
轧机通过对原材料进行压制和拉伸,使其发生塑性变形,从而改善其表面质量和尺寸精度。
在轧制过程中,需要根据不同的材料和加工要求选择合适的轧辊和轧制参数,以确保轧制效果的达到。
3. 钢板冷卷工艺。
在冷轧工艺中,钢板冷卷是一项重要的加工环节。
在钢板冷卷过程中,需要通过卷曲机将原材料进行卷曲,形成卷板或卷带。
在这个过程中,需要控制好卷曲张力和卷曲速度,以确保卷板或卷带的表面质量和尺寸精度。
4. 表面处理工艺。
在冷轧工艺流程中,表面处理是非常重要的一环。
通过对冷轧后的钢板或带材进行酸洗、磷化或涂层处理,可以改善其表面质量、耐腐蚀性能和涂装性能。
表面处理工艺的选择需要根据不同的材料和使用要求进行合理设计,以确保最终产品的质量和性能。
5. 成品检验。
冷轧工艺流程的最后一环是成品检验。
在成品检验过程中,需要对冷轧后的钢板或带材进行外观质量、尺寸精度和机械性能的检测,以确保产品符合标准要求。
只有通过严格的成品检验,才能保证冷轧产品的质量和可靠性。
总之,冷轧工艺流程是一个复杂而又关键的加工过程,需要在每一个环节都严格控制和管理,以确保最终产品的质量和性能。
只有通过不断的技术创新和工艺改进,才能适应市场的需求,满足客户的要求,推动整个行业的发展。
钛合金冷轧工艺

钛合金冷轧工艺钛合金是一种重要的结构材料,具有优良的机械性能和耐腐蚀性能。
冷轧是一种常用的钛合金加工工艺,可以有效提高钛合金的强度和塑性。
本文将介绍钛合金冷轧工艺的原理、方法和应用。
一、冷轧工艺原理冷轧是指将金属材料在室温下通过轧机进行塑性变形的加工工艺。
钛合金的冷轧工艺是将钛合金板材通过冷轧轧机进行轧制,使其在室温下发生塑性变形,从而改变钛合金的组织结构和性能。
冷轧可以使钛合金晶粒细化,提高材料的强度和塑性,并改善钛合金的表面质量。
二、冷轧工艺方法钛合金冷轧工艺可以分为多道次轧制和单道次轧制两种方法。
1. 多道次轧制多道次轧制是指将钛合金板材多次经过轧机进行轧制,每次轧制的压下量逐渐减小。
这种方法可以使钛合金板材充分发生塑性变形,细化晶粒,提高材料的强度和塑性。
多道次轧制还可以改善钛合金的表面质量,减少缺陷和氧化物的存在。
2. 单道次轧制单道次轧制是指将钛合金板材只经过一次轧制,轧制压下量较大。
这种方法可以快速提高钛合金板材的强度,但对于晶粒细化和表面质量的改善效果不如多道次轧制。
钛合金冷轧工艺广泛应用于航空、航天、船舶、化工等领域。
具体应用包括以下几个方面:1. 制造航空航天零部件:钛合金冷轧工艺可以使钛合金板材具有更高的强度和塑性,适用于制造航空航天零部件,如飞机机身、发动机外壳等。
2. 制造化工设备:钛合金具有优良的耐腐蚀性能,冷轧工艺可以进一步提高钛合金的耐腐蚀性能,适用于制造化工设备,如反应器、换热器等。
3. 制造海洋设备:钛合金冷轧工艺可以提高钛合金的抗海水腐蚀性能,适用于制造海洋设备,如海洋平台、潜水器等。
4. 制造医疗器械:钛合金具有生物相容性,冷轧工艺可以进一步提高钛合金的生物相容性,适用于制造医疗器械,如人工关节、牙科种植体等。
钛合金冷轧工艺是一种重要的加工工艺,可以提高钛合金的强度、塑性和耐腐蚀性能,广泛应用于航空、航天、船舶、化工和医疗器械等领域。
随着科技的不断进步,钛合金冷轧工艺将会得到更广泛的应用和发展。
冷轧板的工艺介绍

冷轧板的工艺介绍文章来源: 钢铁E站通简介冷轧是以热轧板卷为原料, 在常温下进行各种型材轧制与热轧相比, 冷轧厂的加工线比较分散, 冷轧产品重要有普通冷轧板、涂镀层板也就是镀锡板、镀锌板和彩涂板。
通过热轧厂送来的钢卷, 先要通过连续三次技术解决, 先要用盐酸除去氧化膜, 然后才干送到冷轧机组。
释义:20世纪末期, 欧洲各个发达国家率先研究开发冷轧堆前解决和冷轧堆染色, 并且通过数年实行经验证明, 冷轧堆前解决和冷轧堆染色它可引导印染公司走出困境, 提高公司在市场上的竞争力。
近年来, 我国在这一方面也有了长足的发展, 并且取得了可喜的成绩。
以下是冷轧工艺的相关内容。
1.轧机的形式二辊轧机, 四辊轧机, 多辊轧机。
各种新的轧机。
2.冷轧产品的优点: 厚度小, 精度高, 性能好品种多用途广, 表面质量高。
3.冷轧的特点:(1)可生产厚度更薄, 精度更高的板带钢。
(2)加工温度低, 轧制中产生加工硬化。
(3)采用工艺冷却和润滑。
(4)采用张力轧制。
4.采用工艺冷却和润滑的作用: 减小金属的变形抗力。
减少轧件的变形热, 冷却轧辊, 改善板形。
5.采用张力轧制的作用:(1)防止带钢在轧制中跑偏(2)改变应力状态,减少轧制力, 减小轧辊弹性压扁, 利于轧制更薄的产品(3)使带钢保证平直, 改善板形。
6、冷轧全连续轧制工艺流程:原料-预退火-酸轧-成品退火-平整-精整-包装-成品原料-酸轧-平整-精整-包装-成品原料-酸轧-成品退火-平整-精整-包装-成品原料-酸轧-包装-成品冷轧生产工艺流程圈7、板带钢的种类(按厚度分类)IT2 5 Hl弟中虬弊乎隅机t潺此最凯王黄墓tiflm酉,i T雄I3金苛*史用札切iH 豪卅沮#萱K谓其首箔材: 0.2mm以下薄板: 0.2-4.0mm 中板: 4-20mm 厚板:20-60mm 特厚板: 60mm 以上8、什么是钢材的产品标准:钢材的产品标准是生产单位和使用单位在交货和收货时的技术依据, 也是生产单位制定工艺和鉴定产品质量的重要依据。
铝板冷轧工艺流程简介

铝板冷轧工艺流程简介
铝板冷轧工艺流程是指将铝板通过轧制设备进行一系列的工艺处理,将其冷轧成所需厚度和规格的产品的过程。
下面是铝板冷轧工艺流程的简要介绍。
1. 材料准备:将原料铝板按照规定的尺寸和厚度进行切割和整平,保证材料的表面光滑,无划痕和变形。
2. 预处理:将铝板表面进行除油、除锈、除尘等处理,以确保后续工序的顺利进行。
3. 热处理:铝板在热处理炉中进行退火,使其获得适当的软化和再结晶,以改善其物理性能和加工性能。
4. 轧制:将预处理和热处理后的铝板送入轧机中进行冷轧。
冷轧是指在常温下对铝板进行轧制,通过轧制使铝板厚度逐渐减小,同时可以改善铝板的表面质量和机械性能。
5. 退火:冷轧后的铝板需要进行退火处理,使其恢复原有的物理性能和加工性能,并消除轧制应力。
6. 表面处理:对退火后的铝板进行清洗、抛光等处理,以改善其表面质量和光洁度。
7. 裁切:将轧制后的铝板按照规定的尺寸和长度进行裁切,以满足不同的应用需求。
8. 除尘、包装:将裁切后的铝板进行除尘处理,并进行包装,以保证产品的质量和外观。
以上就是铝板冷轧工艺流程的简要介绍。
铝板冷轧是一项复杂的工艺,需要经过多个步骤的精确操作和严格控制。
通过冷轧工艺可以获得高质量的铝板产品,广泛应用于汽车制造、航空航天、建筑装饰和电子电器等领域。
- 1、下载文档前请自行甄别文档内容的完整性,平台不提供额外的编辑、内容补充、找答案等附加服务。
- 2、"仅部分预览"的文档,不可在线预览部分如存在完整性等问题,可反馈申请退款(可完整预览的文档不适用该条件!)。
- 3、如文档侵犯您的权益,请联系客服反馈,我们会尽快为您处理(人工客服工作时间:9:00-18:30)。
冷轧情况汇报提纲各类冷轧产品(不包括特殊钢如不锈钢、取向硅钢片等)的主要工艺流程见图. 酸洗:热轧带钢在冷轧前必须酸洗以清除表面氧化铁皮.酸洗所用的介质基本上有二种:硫酸与盐酸.五、六十年代以前都采用硫酸,但硫酸酸洗的效果差,且环境污染严重,己逐渐淘汰而被盐酸替代.盐酸具有与氧化铁皮的化学反应速度快、生成的盐在水中溶解性强等优点.因而带钢表面洗得干净、效率高.酸洗机组有二种类型:推拉式酸洗机组及连续式酸洗机组.推拉式酸洗机组:它以单卷方式操作,设备比较简单,生产能力低,适合于产量在三十万吨左右的冷轧厂采用.国内益昌、海南、南京、及无锡等厂均配置了此类机组.连续式酸洗机组:在机组入口段将每个钢卷的头、尾焊接后连续不断地通过酸槽,因而生产效率高,大型连续酸洗机组工艺段的最高速度可达360米/分左右,年产量达200万吨以上,酸洗质量也好。
现代化冷轧厂一般都采用连续式机组.但设备复杂,自动化水平高,适合于在大型冷轧厂安装.武钢、宝钢、鞍钢、本钢等都选用了此类机组.连续机组入口段中的焊接机为本机组稳定生产及高速运行的关键设备,卷与卷之间焊缝质量的好坏还会影响下游工序的正常生产.当前以采用自动化程度高的闪光式电阻对焊机为主。
它适用于焊接低碳钢.近年来由于激光技术的发展,大功率激光发生器的研制成功,在一些机组中己采用激光焊机连接带钢.激光焊机具有焊缝质量高并能焊接除一般低碳钢以外的合金钢、不锈钢及硅钢等的特点。
中部酸洗工艺段有机械破鳞装置,酸洗槽,清洗槽,烘干装置等主要设备。
机械破鳞装置目前都用拉伸矫直机,在矫直机前后张力辊施加的强大张力下,经矫直机弯曲矫直使带钢延伸从而达到破碎带钢表面的氧化铁皮,因而可缩短酸洗的时间并改善带钢的平直度。
酸洗槽为机组的核心,以往的深槽结构及常规工艺己被各种新型酸槽结构及高效酸洗工艺所代替。
它们有紊流式、喷流式等々,其共同的特点是槽的深度一般都减少为200mm左右,且槽盖有内外二层,并提高酸液进入酸槽时的压力及改善进入时的方式,加快了酸液与带钢表面氧化铁皮所起的化学作用,并增加酸液的循环次数,更提高了酸洗效率。
因而缩短了酸洗时间,酸洗的质量也得到提高,相应可减少酸槽的长度,且由于酸槽的容积减小,浓度与温度的控制更精确,槽的密封性能也提高,改善了环境条件。
出口段的关键设备为园盘剪边机,以往常常是整条机组故障最多的设备之一,且刀具更换也比较频繁,严重影响机组生产能力的发挥。
因而现代化的机组都采用双刀头迥转式,可快速更换刀片.还有一些剪机更可自动按带钢的宽度及厚度调整开口度及刀片间隙。
带钢涂油机目前己开始使用静电式涂油机替代传统使用的辊涂式涂油机,不但可节省防锈油,而且涂层均匀。
冷轧冷轧机是整个冷轧厂的核心机组,也是保证带钢几何尺寸的精度及表面质量的主要工序。
根据工厂的生产规模及产品方案可选用不同的轧机组成.一般有二大类:即可逆与串列(连续).可逆式机组以往仅有一个机架,带钢在机组内往返轧制,生产效率低.按产品的厚度,宽度,及机组的速度,产量在几万至三十万吨左右.而串列式机组按产品品种及产量、质量的要求可由四至六个机架串列组成(目前普遍采用五个机架).带钢在机组内一次通过串列的轧机轧成所要求的厚度.因而生产效率高,一般产量视所生产的品种及机组速度,可从七、八十万到二百万吨左右不等.近年来冷轧板的用户.尤其是汽车及家电制造业等对钢板厚度的公差.平直度及表面质量等提出了愈来愈高的要求.为了满足用户的需求冷轧技术有了长足的进步.体现在以下几个方面:1.为了适应中等规模的生产,最近开发出双机架可逆式轧机.与单机架相比不但可节省投资,质量也得到改善.2.传统的串列式冷轧机也己从单卷轧制发展为无头的连续式轧制,并由单一的轧制而将前道酸洗工艺联结在一起的联合机组.单卷轧制的串列式冷轧机由于每个钢卷轧制时都要穿带.甩尾等操作.不但增加了生产的辅助时间,降低了设备的生产能力,而且由于在穿带与甩尾过程中带钢失去张力,降低速度,使带钢头尾的厚度公差及平直度等均难于得到控制而增加头尾不合格产品的长度,降低了成材率.而连续式冷轧机或酸洗冷轧联合机组则将前一个钢卷的尾部与后一个钢卷的头部焊接在一起而连续不断地送入冷轧机中轧制.只在焊缝通过轧机的瞬间才降低速度,因而能显著地提高成材率.连续式机组由于带钢不停歇地通过轧机,设备的生产能力也得到充分地发挥.此外,酸洗冷轧联合机组还因为省略了部分酸洗机组出口段及轧机入口的设备而节省占地面积及投资,降低了生产及设备维护费用.还由于取销了酸洗与冷轧二个工序之间的中间仑库,节省了厂房面积并缩短了生产周期.己普遍为近年来新建的冷轧厂所采用。
3.轧机的压下己由过去的电动的蜗轮蜗杆压下系统改为液压压下。
液压压下具有反应灵敏,压下速度快,有利于控制带钢的厚度。
因而不但近年来新建的冷轧机己普遍采用,一些七、八十年代建造的电动压下轧机也纷纷改建成液压压下。
4.为了改善带钢横断面的形状及平直度,开发了各种板形及平直度控制系统,可以归纳为以下几种类型:a)垂直面的弯辊系绕-工作辊及/或中间辊的正、负弯辊;b)水平面的工作辊弯辊系统;c)轧辊交叉系统-PC轧机;d)分级控制的支持辊-VC,DSR轧机;e)轴向移动园筒形轧辊系统-WRS轧机;f)轴向移边非园筒形轧辊系统-CVC,HC,UC轧机;g)轴向移动辊套;h)对轧辊进行热凸度控制-利用轧辊冷却系统在轧辊长度方向进行多段或多点喷射,调节轧辊凸度.5.轧辊表面质量的好坏直接影响带钢的表面质量,因而冷轧机组轧辊的更换十分频繁。
缩短换辊所需的时间,成为提高设备作业率的一项重要措施。
现代化的冷轧机组都配有快速换辊装置,在五分钟以内可以自动更换一对工作辊。
对于连续式轧机还可以不切断在机架内的带钢,而将带钢保留在机架内换辊,因而在换辊后可立即轧钢,不需要再逐架穿带而节省辅助时间,使生产能力提高。
6.完善轧辊冷却及润滑系统--轧辊冷却及润滑是保证轧机高速轧制及带钢表面质量的关键设施之一,它基本上有二种方式,直接式及循环式.直接式将一定浓度的轧制油喷在带钢上而用冷却水喷在轧辊及辊缝间冷却轧辊与带钢,用过的油与水一起排入地沟送至废水处理站处理后排走.一般用于高速轧制较薄的带钢如镀锡板等.而循环方式则将轧制油与水混合成乳化液喷在轧辊及辊缝中起到冷却及润滑双重作用,用过的乳化液收集后返面系统,经冷却过滤后循环使用.一般用于轧制较厚的冷轧板如汽车板等.近年来由于轧制油的发展,润滑性能好,油膜耐压强度,化学稳定性好,在循环系统中使用时不易氧化变质,而且具有良好的清洗性能不会加剧生锈,不产生油斑,容易用碱洗净,油的消耗低.因而一些新建的冷轧机都趋向于用循环方式.循环系统中还增设了磁过泸器及平床过泸器等设施,以提高油的过泸精度,保证带钢的表面质量及油的润滑性能。
并加强系统的自动化水平.自动控制乳化液的温度、浓度以及根据工艺需要控制及分配机架与轧辊各区段的流量。
7.冷轧机的主传动电机己由以往的直流电机发展到近年来的交流变频调速电机。
它的供电也己由传统的可控硅为当代的GTO,IGBT,IGCT等新型大功率整流元件所替代,并由全数字式系统控制。
因而传动系统的动态性能有很大的提高。
控制精度可达到很高的水平,一般速度控制精度可达到0.01%以下,力矩控制精度可达到1%.而且提高了系统的可靠性,调试简便,易于维护。
8.各种新型的检测元件如激光测速仪、板型测量仪、张力仪、测厚仪等的使用。
确保了轧机AGC (厚度自动控制)及AFC (平直度自动控制系统)精度的提高。
近年来新建的连轧机其厚度精度可达到1%以下,平直度小于10I.退火冷轧带钢材质的机械性能除了与上游冶炼、热轧有关外,在一定条件下与冷轧后的退火有密切关系。
带钢在冷轧后晶粒被破碎拉长,通过退火可以重新调整其内部织构而达到所要求的各种机械性能。
带钢退火基本上有二种方式一罩式退火及连续退火。
罩式退火由于有足够长的再结晶时间,可以获得软而深冲性能优良的带钢,适用于具有深冲性能低碳铝镇静钢的退火。
也可以通过在钢中加入适量Si、Mn、Ti 等强化元素制造高强度带钢。
其特点是设备比较简单,操作另活。
但存在退火周期长,钢卷内外温差大等缺点。
近年来己开发使用纯氢为保护气并加强氢气的循环。
使退火周期缩短,退火温度均匀等特点,且带钢表面的清洁度也得以提高。
因而仍普遍被采用。
对于进一步作电镀用的产品及表面清洁度要求较高的产品,一般在进入罩式炉退火前仍需在带钢清洗(脱脂)机组上先洗净带钢在冷轧时残留在表面的油污.连续退火有退火周期短及带钢性能均匀的特点。
但早期的连续退火机组由于加热和冷却速度都快,带钢的晶粒来不及长大且钢中的固溶碳未能充分析出,不能生产要求深冲性能的冷轧板,祗能用于生产相当于T4-T6调质度的镀锡用原板。
80年代以来,日本新日铁及日本钢管二家公司各自研究采取调整钢的成分和控制热轧的轧制、终轧和卷取温度,在退火时提高退火温度,使晶粒长大并急冷达到一定温度,经短时间的过时效处理后使固溶碳析出,从而生产出具有深冲性能的冷轧板。
近年来这一技术进一步得到发展,用连续退火不但能得到质软和r值高的钢板,并且还可生产出强度高和塑性好的高强度冷轧板,包括、固溶硬化、IF高强钢、双相钢及析出硬化型等。
这一技术目前由日本三家大公司掌握。
它们为新日铁的NSC-CAPL、日本钢管的CAL及川崎制铁的KM-CAL,它们各自拥有自己的从冶炼、连铸、热轧、冷轧到退火的一整套生产工艺和技术,但大体相似,不同点在于加热后的急冷(一次冷却)方法。
如新日铁从开发初期的喷气冷却(GJC )发展到高速喷气冷却(HJGC)、辊冷(RC)及气水冷却(AcC);日本钢管从早期的水淬冷却(WC)到辊冷(RC)以及辊冷加辅助喷气冷却;川崎制铁的辊气混合冷却等,其目的都是为了更好地控制冷却速度以获得所需的结晶组织,使带钢达到所要求的性能。
炉子的加热与均热段则采用新型的辐射管,可有效地对燃烧进行控制,降低辐射管表面温度峰值,而改善表面温度的分布,延长使用寿命,并降低废气中氮氧化合物(NOx)的含量,减少对环境的污染。
为提高炉子的热效率,还利用燃烧后废气中的余热对带钢进行予热.为了使炉内带钢在高速下稳定地运行.现代高速的连续退火炉在炉内还设有纠偏辊及带钢对中控制系统(CPC),炉辊采用交流马达单独传动,还分段设有张力辊,可根据各段不同的工况对炉内带钢的张力单独调节.炉辊还设有专门的热凸度控制装置,保持带钢在炉内平稳运行。
炉辊的表面喷涂有耐温陶瓷涂料,以防止辊子表面在高温下结瘤而产生粘结等现象而影响带钢表面质量,并可提高带钢与炉辊间的磨擦系数便于控制带钢在炉内的张力.连续退火机组的另一特点是将退火工序前的带钢清洗与退火后的平整及带钢检查等工序合并在机组内,成为联合机组。