薄片零件冲压机
机械设计中的冲压机设计
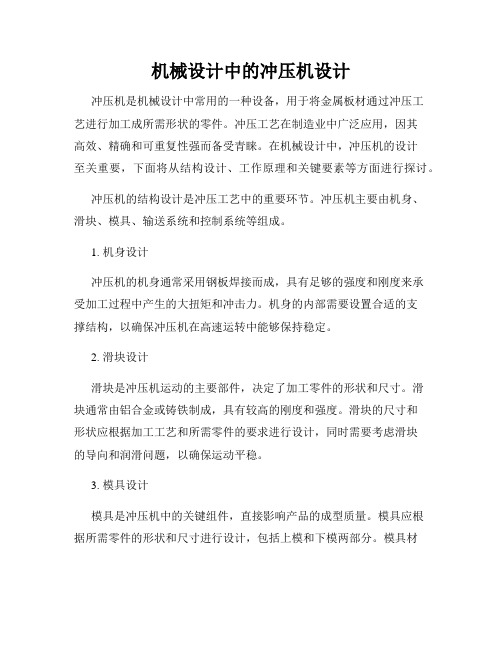
机械设计中的冲压机设计冲压机是机械设计中常用的一种设备,用于将金属板材通过冲压工艺进行加工成所需形状的零件。
冲压工艺在制造业中广泛应用,因其高效、精确和可重复性强而备受青睐。
在机械设计中,冲压机的设计至关重要,下面将从结构设计、工作原理和关键要素等方面进行探讨。
冲压机的结构设计是冲压工艺中的重要环节。
冲压机主要由机身、滑块、模具、输送系统和控制系统等组成。
1. 机身设计冲压机的机身通常采用钢板焊接而成,具有足够的强度和刚度来承受加工过程中产生的大扭矩和冲击力。
机身的内部需要设置合适的支撑结构,以确保冲压机在高速运转中能够保持稳定。
2. 滑块设计滑块是冲压机运动的主要部件,决定了加工零件的形状和尺寸。
滑块通常由铝合金或铸铁制成,具有较高的刚度和强度。
滑块的尺寸和形状应根据加工工艺和所需零件的要求进行设计,同时需要考虑滑块的导向和润滑问题,以确保运动平稳。
3. 模具设计模具是冲压机中的关键组件,直接影响产品的成型质量。
模具应根据所需零件的形状和尺寸进行设计,包括上模和下模两部分。
模具材料通常选用工具钢或硬质合金,以保证其硬度和耐磨性。
模具的结构设计应考虑到加工工艺、材料的变形以及模具的易用性等因素。
4. 输送系统设计冲压机的输送系统用于将金属板材自动送入模具中进行加工,并将成品零件排出。
输送系统通常包括进料装置、输送带和排料装置等。
进料装置的设计需要考虑金属板材的定位和定位精度,而输送带的设计要保证运动的平稳和精确。
5. 控制系统设计冲压机的控制系统负责控制机械的运动,包括滑块的上下运动、进料装置的定位和输送带的运动等。
控制系统可以采用PLC、伺服电机或液压系统等,具体的选择应根据冲压工艺的特点和要求进行设计。
冲压机设计中的关键要素是加工工艺和产品质量。
在设计过程中,需要考虑以下几个方面:1. 加工工艺冲压加工工艺包括模具设计、模具制造和模具试验等环节。
在设计冲压机时,需要充分了解所需加工零件的形状、材料和加工工艺,以便进行合理的结构设计。
薄壁零件冲压机结构设计

薄壁零件冲压机结构设计薄壁零件冲压机是一种专门用于加工薄壁零件的机器,其结构设计对于机器的性能和加工效率有着至关重要的影响。
本文将从机器的结构设计方面进行探讨,以期为读者提供一些有益的参考。
一、机器的整体结构设计薄壁零件冲压机的整体结构设计应该考虑到机器的稳定性和刚性,以确保机器在高速运转时不会出现晃动或变形等问题。
同时,机器的结构设计还应该考虑到机器的易于维护性和操作性,以方便用户进行维护和操作。
在机器的整体结构设计中,应该注意以下几点:1. 机器的底座应该采用厚实的钢板焊接而成,以确保机器的稳定性和刚性。
2. 机器的上下模板应该采用高强度的合金钢材料制造,以确保机器在高速运转时不会出现变形或破裂等问题。
3. 机器的传动系统应该采用高精度的齿轮传动或同步带传动,以确保机器的运转精度和稳定性。
4. 机器的液压系统应该采用高品质的液压元件和管路,以确保机器的液压系统的可靠性和稳定性。
二、机器的模具结构设计薄壁零件冲压机的模具结构设计是机器性能和加工效率的关键因素之一。
模具的结构设计应该考虑到以下几点:1. 模具的材料应该采用高强度的合金钢材料,以确保模具的耐磨性和耐用性。
2. 模具的结构应该简单、紧凑,以确保模具的加工精度和稳定性。
3. 模具的设计应该考虑到零件的加工工艺和加工要求,以确保零件的加工质量和精度。
4. 模具的调整和更换应该方便快捷,以提高机器的生产效率和经济效益。
三、机器的控制系统设计薄壁零件冲压机的控制系统设计是机器性能和加工效率的另一个关键因素。
控制系统的设计应该考虑到以下几点:1. 控制系统应该采用高性能的PLC控制器和触摸屏人机界面,以确保机器的控制精度和稳定性。
2. 控制系统应该具有多种自动化控制功能,如自动送料、自动定位、自动计数等,以提高机器的生产效率和经济效益。
3. 控制系统应该具有完善的故障诊断和报警功能,以方便用户进行故障排除和维护。
4. 控制系统应该具有良好的可扩展性和兼容性,以方便用户进行升级和改造。
冲压机的工作原理

冲压机的工作原理冲压机是一种工业生产中常用的设备,通常被用于车间中生产大批量金属工件,如汽车车身、电器外壳等。
与数控机床等其他设备不同的是,冲压机利用分段模具对冲压件进行成形,并在短时间内完成大批量加工,因而得到广泛应用。
冲压机的结构冲压机由机架、爪式进料机械手、分段模具、液压系统以及控制系统等组成,其整体结构紧凑且占地面积较小,能够在车间内灵活应用。
同时,冲压机通过进料机械手能够自动将金属板料送入分段模具之内,并通过液压系统完成过程中所需的范围内内、外轮廓、孔、凹凸形等多种不同形状的冲压加工过程。
整个冲压加工过程能够发挥出高效、精准、高品质的优势,从而满足工业生产中日益增长的需求。
冲压机的工作原理冲压机的工作原理主要表现在它的冲压工艺上,其原理简述如下:1. 选择模具。
根据目标工件的要求,采用对应的分段模具,包括形状、尺寸、材质、寿命等多个因素。
2. 放置金属板材。
将金属板材按照要求放置在机器上,一般由爪式进料机械手搬运。
3. 定位金属板料。
使用气压或机械定位,将金属板料固定在分段模具上,以确保冲压加工的稳定。
4. 冲压加工。
使用主缸压下凹模,将金属板料成型,然后使用剪切模将工件分割成各个部分。
由于主缸具有大的压力、速度等优势,不仅能够满足各种复杂形状的冲压件制作,而且能够达到高效、高精度的生产要求。
5. 完成工艺。
当冲压过程结束后,分段模具通过实现上下流动来脱模,同时放置位置将工件移出成品吊装设备,待后续加工。
总之,冲压机是一种利用分段模具和液压系统对金属板材进行成形的设备。
通过对板材的压制、剪切等作用,能够产生多种形状的工件,从而较好地满足了工业生产的要求。
在高效、高品质、大批量的加工过程中,冲压机的工作原理得到有效的应用,为工业制造业的发展赋予了更为前沿的技术支持。
冲压机的工作原理
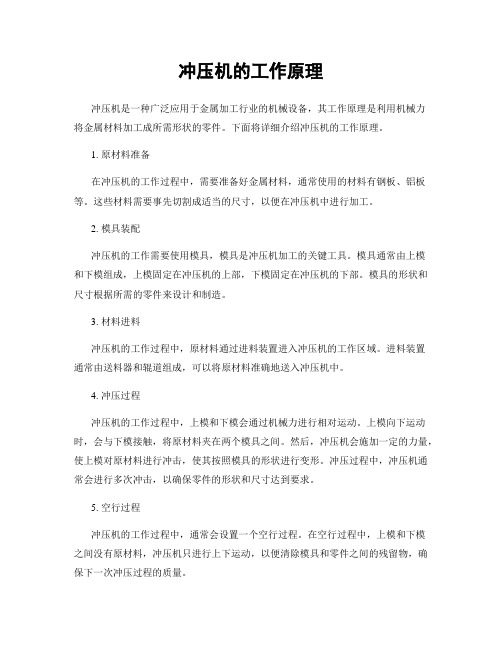
冲压机的工作原理冲压机是一种广泛应用于金属加工行业的机械设备,其工作原理是利用机械力将金属材料加工成所需形状的零件。
下面将详细介绍冲压机的工作原理。
1. 原材料准备在冲压机的工作过程中,需要准备好金属材料,通常使用的材料有钢板、铝板等。
这些材料需要事先切割成适当的尺寸,以便在冲压机中进行加工。
2. 模具装配冲压机的工作需要使用模具,模具是冲压机加工的关键工具。
模具通常由上模和下模组成,上模固定在冲压机的上部,下模固定在冲压机的下部。
模具的形状和尺寸根据所需的零件来设计和制造。
3. 材料进料冲压机的工作过程中,原材料通过进料装置进入冲压机的工作区域。
进料装置通常由送料器和辊道组成,可以将原材料准确地送入冲压机中。
4. 冲压过程冲压机的工作过程中,上模和下模会通过机械力进行相对运动。
上模向下运动时,会与下模接触,将原材料夹在两个模具之间。
然后,冲压机会施加一定的力量,使上模对原材料进行冲击,使其按照模具的形状进行变形。
冲压过程中,冲压机通常会进行多次冲击,以确保零件的形状和尺寸达到要求。
5. 空行过程冲压机的工作过程中,通常会设置一个空行过程。
在空行过程中,上模和下模之间没有原材料,冲压机只进行上下运动,以便清除模具和零件之间的残留物,确保下一次冲压过程的质量。
6. 退料冲压机的工作过程完成后,需要将加工好的零件从冲压机中取出。
通常使用退料装置将零件从下模中推出,然后通过传送带或其他方式将零件收集起来。
7. 整理和检验加工好的零件需要进行整理和检验。
整理是指将零件进行清洁和去除表面的毛刺等不良状况。
检验是指对零件的尺寸、形状和质量进行检查,确保其符合要求。
以上就是冲压机的工作原理的详细介绍。
冲压机通过模具和机械力的作用,将金属材料加工成所需的形状和尺寸。
冲压机在汽车制造、家电制造等行业都有广泛的应用,其工作原理的理解对于冲压机的操作和维护都具有重要意义。
冲压机的工艺参数
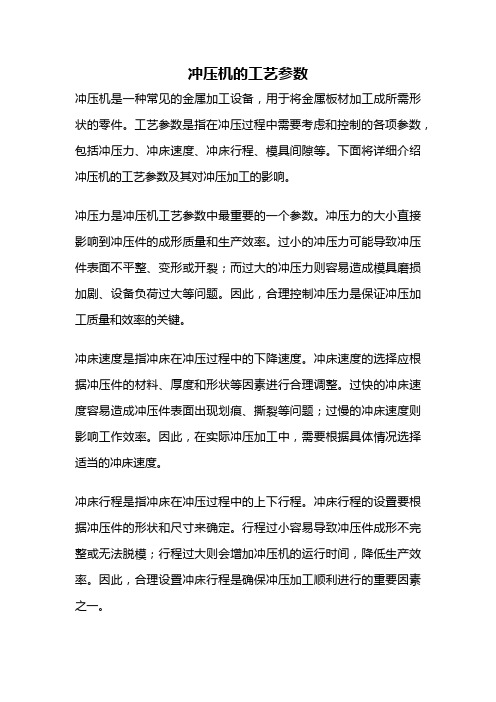
冲压机的工艺参数冲压机是一种常见的金属加工设备,用于将金属板材加工成所需形状的零件。
工艺参数是指在冲压过程中需要考虑和控制的各项参数,包括冲压力、冲床速度、冲床行程、模具间隙等。
下面将详细介绍冲压机的工艺参数及其对冲压加工的影响。
冲压力是冲压机工艺参数中最重要的一个参数。
冲压力的大小直接影响到冲压件的成形质量和生产效率。
过小的冲压力可能导致冲压件表面不平整、变形或开裂;而过大的冲压力则容易造成模具磨损加剧、设备负荷过大等问题。
因此,合理控制冲压力是保证冲压加工质量和效率的关键。
冲床速度是指冲床在冲压过程中的下降速度。
冲床速度的选择应根据冲压件的材料、厚度和形状等因素进行合理调整。
过快的冲床速度容易造成冲压件表面出现划痕、撕裂等问题;过慢的冲床速度则影响工作效率。
因此,在实际冲压加工中,需要根据具体情况选择适当的冲床速度。
冲床行程是指冲床在冲压过程中的上下行程。
冲床行程的设置要根据冲压件的形状和尺寸来确定。
行程过小容易导致冲压件成形不完整或无法脱模;行程过大则会增加冲压机的运行时间,降低生产效率。
因此,合理设置冲床行程是确保冲压加工顺利进行的重要因素之一。
模具间隙是指冲压模具之间的间隙大小。
模具间隙的大小直接影响到冲压件的尺寸精度和表面质量。
间隙过小容易导致冲压件变形、划伤等问题;间隙过大则会影响冲压件的尺寸精度。
因此,在冲压加工中,需要根据冲压件的形状和材料选择合适的模具间隙。
除了上述几个主要的工艺参数外,还有一些其他的工艺参数也需要考虑。
例如,冲压件的材料和厚度、冲压机的机床刚度和稳定性、模具的材料和硬度等都会对冲压加工产生一定的影响。
因此,在实际冲压加工中,需要综合考虑各项工艺参数,并进行合理调整,以获得满足要求的冲压件。
冲压机的工艺参数是决定冲压加工质量和效率的关键因素。
合理控制冲压力、冲床速度、冲床行程和模具间隙等工艺参数,可以确保冲压件的尺寸精度和表面质量,提高冲压加工的效率和稳定性。
冲压机原理
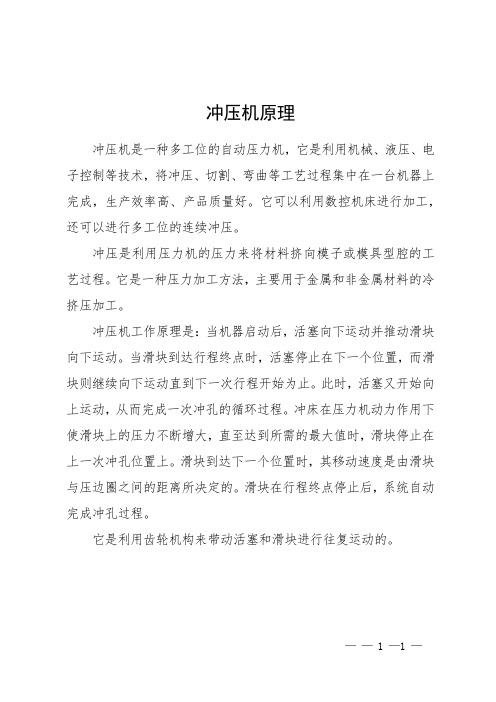
冲压机原理
冲压机是一种多工位的自动压力机,它是利用机械、液压、电子控制等技术,将冲压、切割、弯曲等工艺过程集中在一台机器上完成,生产效率高、产品质量好。
它可以利用数控机床进行加工,还可以进行多工位的连续冲压。
冲压是利用压力机的压力来将材料挤向模子或模具型腔的工艺过程。
它是一种压力加工方法,主要用于金属和非金属材料的冷挤压加工。
冲压机工作原理是:当机器启动后,活塞向下运动并推动滑块向下运动。
当滑块到达行程终点时,活塞停止在下一个位置,而滑块则继续向下运动直到下一次行程开始为止。
此时,活塞又开始向上运动,从而完成一次冲孔的循环过程。
冲床在压力机动力作用下使滑块上的压力不断增大,直至达到所需的最大值时,滑块停止在上一次冲孔位置上。
滑块到达下一个位置时,其移动速度是由滑块与压边圈之间的距离所决定的。
滑块在行程终点停止后,系统自动完成冲孔过程。
它是利用齿轮机构来带动活塞和滑块进行往复运动的。
—— 1 —1 —。
冲压机的工作原理
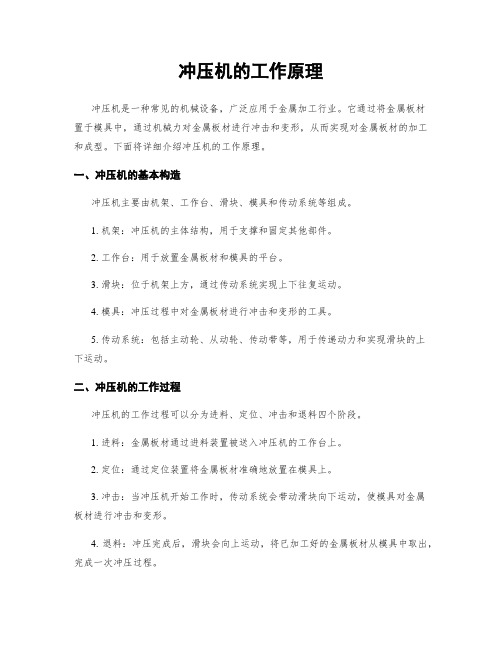
冲压机的工作原理冲压机是一种常见的机械设备,广泛应用于金属加工行业。
它通过将金属板材置于模具中,通过机械力对金属板材进行冲击和变形,从而实现对金属板材的加工和成型。
下面将详细介绍冲压机的工作原理。
一、冲压机的基本构造冲压机主要由机架、工作台、滑块、模具和传动系统等组成。
1. 机架:冲压机的主体结构,用于支撑和固定其他部件。
2. 工作台:用于放置金属板材和模具的平台。
3. 滑块:位于机架上方,通过传动系统实现上下往复运动。
4. 模具:冲压过程中对金属板材进行冲击和变形的工具。
5. 传动系统:包括主动轮、从动轮、传动带等,用于传递动力和实现滑块的上下运动。
二、冲压机的工作过程冲压机的工作过程可以分为进料、定位、冲击和退料四个阶段。
1. 进料:金属板材通过进料装置被送入冲压机的工作台上。
2. 定位:通过定位装置将金属板材准确地放置在模具上。
3. 冲击:当冲压机开始工作时,传动系统会带动滑块向下运动,使模具对金属板材进行冲击和变形。
4. 退料:冲压完成后,滑块会向上运动,将已加工好的金属板材从模具中取出,完成一次冲压过程。
三、冲压机的工作原理主要涉及力学和材料学的知识。
1. 力学原理:冲压机通过机械力对金属板材施加冲击和变形。
在冲击过程中,滑块下降时会受到阻力,阻力大小取决于金属板材的材料性质、厚度以及模具的几何形状等因素。
通过调整冲压机的参数,如冲程、冲次、冲击速度等,可以控制冲压的力度和变形程度。
2. 材料学原理:金属板材在冲压过程中会发生塑性变形。
当滑块对金属板材施加冲击力时,金属板材会受到应力的作用,产生塑性变形。
这种塑性变形可以使金属板材在模具的作用下得到所需的形状和尺寸。
四、冲压机的应用领域冲压机广泛应用于汽车创造、家电创造、航空航天、电子通信等行业。
它可以用于创造汽车车身、家电外壳、航空零部件、手机壳等各种金属制品。
冲压机具有高效、精确、稳定的特点,可以大规模生产高质量的金属制品。
总结:冲压机是一种通过机械力对金属板材进行冲击和变形的设备。
冲压机运行原理

冲压机运行原理冲压机是一种利用冲压工艺来加工金属材料的专用设备。
它通过应用压力将金属板材或带材加工成具有一定形状和尺寸的零件。
冲压机的运行原理是基于力学和液压原理。
冲压机主要由机架、传动系统、工作台、液压系统和控制系统组成。
1. 机架:冲压机的机架是支撑和固定冲压机各部件的基础结构。
它通常由钢板焊接而成,具有足够的刚度和强度,以承受冲压过程中的各种受力。
2. 传动系统:传动系统是冲压机的动力来源,它主要包括电机、减速机、连杆机构和滑块。
电机提供动力,减速机将电机的高速旋转转换为冲压机所需的低速高扭矩输出,连杆机构将旋转运动转换为往复直线运动,滑块则带动冲头进行冲压操作。
3. 工作台:工作台是冲压机上用于固定和支撑待加工材料的平台。
它通常由钢板制成,具有足够的平整度和稳固性,以确保冲压过程中材料的稳定定位。
4. 液压系统:液压系统是冲压机的重要组成部分,它通过应用液压力来提供冲压过程中所需的加工力。
液压系统由液压泵、液压缸、控制阀和油箱等组成。
液压泵将机械能转化为液压能,液压缸通过液压力将滑块下压,控制阀用于控制液压系统的工作压力和流量。
5. 控制系统:控制系统是冲压机的智能化部分,它通过电气传感器和控制器来实现对冲压过程的精确控制。
控制系统可以监测和调节冲压力、滑块行程、冲头速度等参数,以确保冲压过程的稳定和精度。
冲压机的运行原理可以简单概括为以下几个步骤:1. 材料进料:将待加工的金属板材或带材放置在工作台上,并通过夹具或卡板进行固定和定位。
2. 滑块下压:启动冲压机的电机和液压系统,液压泵将液压油送入液压缸,液压缸带动连杆机构,使滑块下压。
滑块下压的过程中,冲头与材料接触并施加一定的压力。
3. 冲压操作:当滑块下压到一定位置时,冲头开始对材料进行冲压操作。
冲头的形状和尺寸决定了最终加工件的形状和尺寸。
冲压过程中,冲头通过对材料施加压力,使其发生塑性变形,从而得到所需形状的零件。
4. 材料排出:完成冲压操作后,滑块开始向上运动,冲头与材料脱离接触。
冲压机工作原理及操作方法
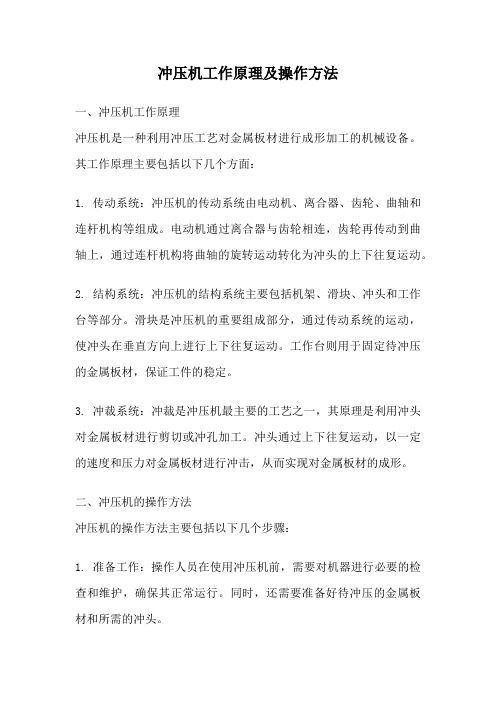
冲压机工作原理及操作方法一、冲压机工作原理冲压机是一种利用冲压工艺对金属板材进行成形加工的机械设备。
其工作原理主要包括以下几个方面:1. 传动系统:冲压机的传动系统由电动机、离合器、齿轮、曲轴和连杆机构等组成。
电动机通过离合器与齿轮相连,齿轮再传动到曲轴上,通过连杆机构将曲轴的旋转运动转化为冲头的上下往复运动。
2. 结构系统:冲压机的结构系统主要包括机架、滑块、冲头和工作台等部分。
滑块是冲压机的重要组成部分,通过传动系统的运动,使冲头在垂直方向上进行上下往复运动。
工作台则用于固定待冲压的金属板材,保证工件的稳定。
3. 冲裁系统:冲裁是冲压机最主要的工艺之一,其原理是利用冲头对金属板材进行剪切或冲孔加工。
冲头通过上下往复运动,以一定的速度和压力对金属板材进行冲击,从而实现对金属板材的成形。
二、冲压机的操作方法冲压机的操作方法主要包括以下几个步骤:1. 准备工作:操作人员在使用冲压机前,需要对机器进行必要的检查和维护,确保其正常运行。
同时,还需要准备好待冲压的金属板材和所需的冲头。
2. 调整冲头:根据工件的要求,选择合适的冲头,并将其安装在冲压机上。
同时,还需要根据工件的尺寸和形状,调整冲头的下行行程和上行行程,以确保冲压的准确性和稳定性。
3. 定位工件:将待冲压的金属板材放置在工作台上,并使用夹具或定位装置将其固定。
确保工件的位置准确无误,避免冲压过程中的偏移或变形。
4. 开始冲压:启动冲压机,通过操作控制台上的按钮或脚踏开关,使冲头开始上下往复运动。
在冲压过程中,操作人员需要密切观察冲压机的运行状态,确保冲压的平稳进行。
5. 完成冲压:当冲头完成对金属板材的冲击后,操作人员需要及时停止冲压机的运行,并将冲压好的工件取出。
同时,还需要对冲压机进行清洁和保养,以确保其正常运行和延长使用寿命。
三、注意事项在使用冲压机时,操作人员需要注意以下几个方面:1. 安全防护:操作人员在操作冲压机时,应佩戴好必要的安全防护用品,如手套、护目镜等。
冲压机工作原理及结构组成介绍【详细版】
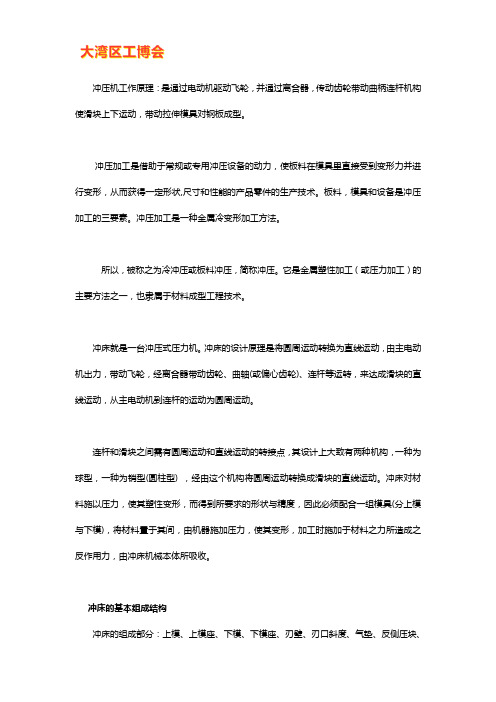
冲压机工作原理:是通过电动机驱动飞轮,并通过离合器,传动齿轮带动曲柄连杆机构使滑块上下运动,带动拉伸模具对钢板成型。
冲压加工是借助于常规或专用冲压设备的动力,使板料在模具里直接受到变形力并进行变形,从而获得一定形状,尺寸和性能的产品零件的生产技术。
板料,模具和设备是冲压加工的三要素。
冲压加工是一种金属冷变形加工方法。
所以,被称之为冷冲压或板料冲压,简称冲压。
它是金属塑性加工(或压力加工)的主要方法之一,也隶属于材料成型工程技术。
冲床就是一台冲压式压力机。
冲床的设计原理是将圆周运动转换为直线运动,由主电动机出力,带动飞轮,经离合器带动齿轮、曲轴(或偏心齿轮)、连杆等运转,来达成滑块的直线运动,从主电动机到连杆的运动为圆周运动。
连杆和滑块之间需有圆周运动和直线运动的转接点,其设计上大致有两种机构,一种为球型,一种为销型(圆柱型) ,经由这个机构将圆周运动转换成滑块的直线运动。
冲床对材料施以压力,使其塑性变形,而得到所要求的形状与精度,因此必须配合一组模具(分上模与下模),将材料置于其间,由机器施加压力,使其变形,加工时施加于材料之力所造成之反作用力,由冲床机械本体所吸收。
冲床的基本组成结构
冲床的组成部分:上模、上模座、下模、下模座、刃壁、刃口斜度、气垫、反侧压块、
导套、导板、导柱、导正销、导板模、导料板、导柱模架、冲模、凸模、凹模、防护板、压料板(圈)、压料筋、压料槛、承料板、连续模、侧刃、侧压板、顶杆、顶板、齿圈、限位套、限位柱、定位销(板)、固定板、固定卸料板、固定挡料销(板)、卸件器、卸料板、卸料螺钉、单工序模、废料切刀、组合冲模、始用挡料销(板)、拼块、挡块(板)、挡料销(板)、垫板等。
冲压机的工作原理
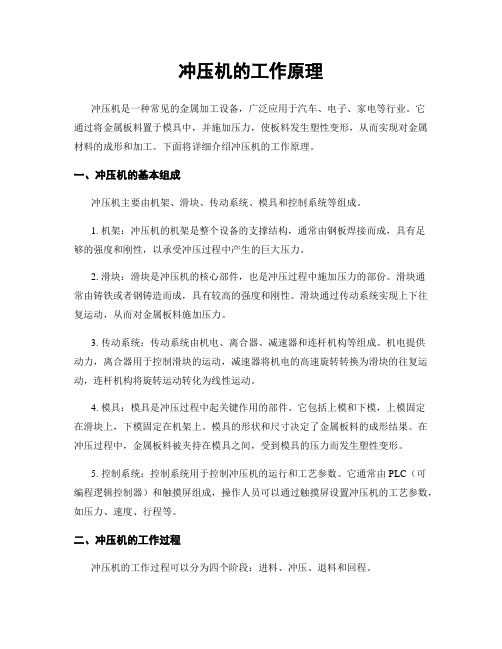
冲压机的工作原理冲压机是一种常见的金属加工设备,广泛应用于汽车、电子、家电等行业。
它通过将金属板料置于模具中,并施加压力,使板料发生塑性变形,从而实现对金属材料的成形和加工。
下面将详细介绍冲压机的工作原理。
一、冲压机的基本组成冲压机主要由机架、滑块、传动系统、模具和控制系统等组成。
1. 机架:冲压机的机架是整个设备的支撑结构,通常由钢板焊接而成,具有足够的强度和刚性,以承受冲压过程中产生的巨大压力。
2. 滑块:滑块是冲压机的核心部件,也是冲压过程中施加压力的部份。
滑块通常由铸铁或者钢铸造而成,具有较高的强度和刚性。
滑块通过传动系统实现上下往复运动,从而对金属板料施加压力。
3. 传动系统:传动系统由机电、离合器、减速器和连杆机构等组成。
机电提供动力,离合器用于控制滑块的运动,减速器将机电的高速旋转转换为滑块的往复运动,连杆机构将旋转运动转化为线性运动。
4. 模具:模具是冲压过程中起关键作用的部件。
它包括上模和下模,上模固定在滑块上,下模固定在机架上。
模具的形状和尺寸决定了金属板料的成形结果。
在冲压过程中,金属板料被夹持在模具之间,受到模具的压力而发生塑性变形。
5. 控制系统:控制系统用于控制冲压机的运行和工艺参数。
它通常由PLC(可编程逻辑控制器)和触摸屏组成,操作人员可以通过触摸屏设置冲压机的工艺参数,如压力、速度、行程等。
二、冲压机的工作过程冲压机的工作过程可以分为四个阶段:进料、冲压、退料和回程。
1. 进料:在进料阶段,金属板料被送入冲压机的进料装置中。
进料装置通常由送料器和送料辊组成,它们将金属板料送入模具之间,并确保板料的位置准确。
2. 冲压:在冲压阶段,滑块开始下行,并施加压力于金属板料上。
通过传动系统的作用,滑块以一定的速度下降,使上模与下模之间的距离减小,从而压缩金属板料。
金属板料受到模具的压力而发生塑性变形,成为所需的形状。
3. 退料:在冲压完成后,滑块开始上升,金属板料被释放出来。
冲压机的工作原理

冲压机的工作原理冲压机是一种常用的金属加工设备,广泛应用于汽车、电子、家电等行业中。
它通过将金属板材置于模具中,利用冲压机的工作原理将金属板材加工成所需的形状和尺寸。
冲压机的工作原理可以简单概括为:通过电动机驱动传动系统,使曲轴带动连杆和滑块运动,从而实现冲压过程。
具体来说,冲压机的工作原理包括以下几个关键步骤:1. 供料:金属板材经过剪切、切割等工艺处理后,通过供料系统送入冲压机的工作区域。
2. 定位:冲压机通过定位装置将金属板材准确地放置在模具上,确保冲压过程中的精度和稳定性。
3. 冲裁:冲压机通过下冲程将滑块带动的冲头对金属板材进行冲击,使其在模具的作用下发生塑性变形,从而完成冲裁过程。
4. 抽料:冲压过程中,模具通过抽料装置将冲裁后的零件从金属板材上抽离,为下一次冲压作准备。
5. 回程:冲压过程完成后,滑块通过回程装置回到起始位置,为下一次冲压作准备。
冲压机的工作原理中,关键的部件包括电动机、传动系统、滑块、模具等。
电动机提供动力,通过传动系统将动力传递给滑块,滑块通过连杆和曲轴的运动实现上下往复运动。
模具起到塑性变形的作用,将金属板材冲裁成所需的形状和尺寸。
冲压机的工作原理具有以下优点:1. 高效率:冲压机的工作速度快,可以实现高速连续冲压,提高生产效率。
2. 精度高:冲压机的工作精度高,可以满足精密零件的加工需求。
3. 适应性强:冲压机可以适应不同形状、尺寸和材质的金属板材加工,具有较强的通用性。
4. 自动化程度高:冲压机可以与自动化生产线配合使用,实现自动送料、自动冲裁等功能。
冲压机的工作原理在实际应用中有着广泛的应用,它不仅可以加工金属板材,还可以用于冲压成型、拉伸、弯曲等工艺。
冲压机的工作原理的理解和掌握对于操作人员的安全和生产效率具有重要意义,同时也为冲压机的维护和故障排除提供了基础。
总之,冲压机的工作原理是通过电动机驱动传动系统,使滑块带动的冲头对金属板材进行冲击,实现金属板材的塑性变形和冲裁。
冲压机原理及实际应用说明

冲压机原理及实际应用说明冲压机是一种用于将各种金属板材和线材加工成所需形状和尺寸的机械设备。
它是通过将金属板材或线材放置于模具中,并施加一定的压力和冲击力,使其在模具形状的作用下发生塑性变形,从而达到制作各种零部件和产品的目的。
冲压机的工作原理基本上可以分为以下几个步骤:1. 下料:冲压机通过上料机构将金属板材或线材送入冲床内,待冲床准备就绪后自动下料。
2. 切割:冲压机上的切断模具可以通过来回运动,将金属板材或线材切割成所需尺寸。
3. 冲压:冲压机的冲裁模具可以将金属板材或线材按照模具的设计形状进行冲裁,在冲压的过程中产生塑性变形。
4. 折弯:冲压机上的折弯模具可以将金属板材进行弯曲,以制作出所需形状的零部件。
5. 成型:冲压机上的成型模具可以将金属板材或线材按照模具的设计形状进行成型,制作出具有复杂结构的零部件。
冲压机的实际应用非常广泛,特别适合高速、精密、大批量的生产加工。
下面列举几个常见的应用领域:1. 汽车制造:冲压机是汽车制造中必不可少的工艺设备。
在汽车制造过程中,冲压机常用于制作车身零部件、车门、车顶等铁板件的冲裁、折弯和成型。
2. 家电制造:冲压机在家电制造过程中也有广泛应用。
例如,电视机中的金属外壳、冰箱中的金属板件等都是通过冲压机进行加工制作。
3. 机械制造:冲压机在机械制造领域中应用广泛,可以用于制作各种零部件,如轴承、销钉、螺栓等。
4. 电子设备制造:冲压机也被广泛应用于电子设备制造领域,如手机、平板电脑等设备中的金属壳体、按键等部件都可以通过冲压机进行加工。
总之,冲压机凭借其高效、精确、灵活的特点,在制造业中发挥着重要的作用。
通过不同的模具设计和制造,冲压机能够满足各种形状和尺寸的零部件的生产需求。
随着科技的不断发展,冲压机的自动化程度和加工精度也在不断提高,将进一步推动其在各个领域的应用。
冲压机的工作原理

冲压机的工作原理冲压机是一种用于对金属材料进行冲剪、弯曲、拉伸和拉拔等加工的机床。
其工作原理是将金属材料(如钢板、铝板等)放到冲压机的工作台上,通过冲压机的动作来对材料进行加工。
1.上料:将金属材料放置在冲压机的进料机构上。
进料机构将材料送入冲压机的工作台上。
2.定位:冲压机通过定位装置将材料定位到正确的位置上。
定位装置可以使材料在冲压机上得到准确的定位,保证加工质量。
3.下压:冲压机通过液压系统或机械传动装置下压,使冲头移向工作台。
在下压的同时,冲头还会带动冲针运动。
4.冲剪:冲头在下压的过程中,通过冲针对材料进行冲击,从而将材料冲剪成所需的形状。
冲头冲剪时会受到压力的影响,压力的大小可以根据加工需求进行调整。
5.弹起:当冲头完成冲剪后,液压系统或机械传动装置会将冲头弹起。
材料也会随之离开工作台。
6.卸料:完成冲剪后,冲压机会将加工完成的材料从工作台上卸下,进入下一个工序。
卸料可以通过传送带、人工或自动吹气等方式进行。
1.高效性:冲压机可以快速地对材料进行加工,加工效率高。
2.精度高:冲压机可以对材料进行精确的定位和加工,加工出的工件质量高。
3.可重复性好:冲压机的工作过程可以精确控制,使得加工过程稳定,加工结果可重复。
4.灵活性强:冲压机可以根据不同的加工要求进行调整,适应不同的加工需求。
5.自动化程度高:冲压机可以与自动送料系统和自动下料系统等配套使用,实现自动化生产。
总结起来,冲压机的工作原理是通过动作循环对金属材料进行加工,具有高效性、精度高、可重复性好、灵活性强和自动化程度高等特点。
冲压机广泛应用于汽车、家电、电子等行业中的金属加工过程中。
YT27-1000 10000千牛单动薄板冲压液压机
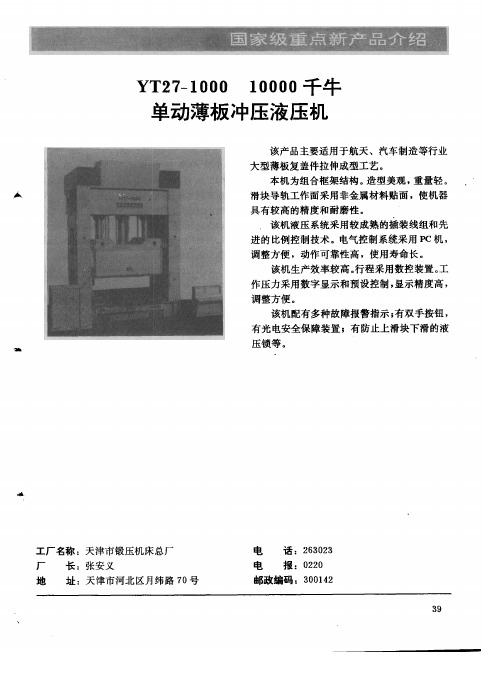
一
00 0
0000
千 牛
单 动 薄 板 冲 压 液 压 机
该 产 品主要 适用 于航 天
。 、
汽车制 造 等行业
。 ,
大型 薄板 复盖 件拉 伸成 型工 艺
本机 为组 合框架 结 构 造 型美观 滑块 导轨 工 作面采 用 非金属 材料 贴面 具 有较 高 的精 度 和 耐磨 性 进 的 比例控 制技 术 调 整方 便
,
。 。
重量 轻
,
。
使机 器
该 机液 压 系统采 用 较 成熟 的插 装 线组 和 先 电气控 制系统采 用
,
P c
。
机
。
,
动作 可靠 性高
。
使 用寿命 长
,
该机 生产效 率较 高 行 程 采用 数控装 置 工 作 压力采 用 数 字显示 和 预设控 制 显示 精 度高 调 整方便
。 ,
该机 配 有 多种 故 障报警 指示 ; 有双 手按 钮
。
,有 Βιβλιοθήκη 电安全 保障 装置 ; 有 防止上 滑块 下滑 的液 压锁等
工厂 名 称 厂 地 长 址
:
天津 市锻 压机床 总 厂 张安 义 天 津市河 北 区 月纬路 7 0 号
电 电
话 报
:
263 023
:
022 0
:
邮政 编码
3 00142
80吨气动冲床工作台参数
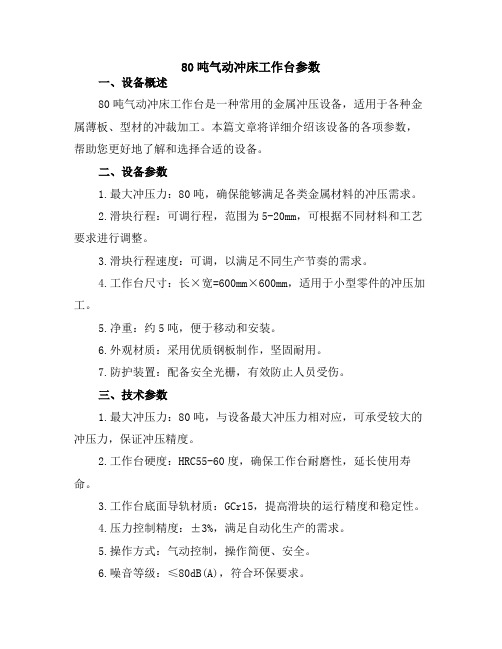
80吨气动冲床工作台参数一、设备概述80吨气动冲床工作台是一种常用的金属冲压设备,适用于各种金属薄板、型材的冲裁加工。
本篇文章将详细介绍该设备的各项参数,帮助您更好地了解和选择合适的设备。
二、设备参数1.最大冲压力:80吨,确保能够满足各类金属材料的冲压需求。
2.滑块行程:可调行程,范围为5-20mm,可根据不同材料和工艺要求进行调整。
3.滑块行程速度:可调,以满足不同生产节奏的需求。
4.工作台尺寸:长×宽=600mm×600mm,适用于小型零件的冲压加工。
5.净重:约5吨,便于移动和安装。
6.外观材质:采用优质钢板制作,坚固耐用。
7.防护装置:配备安全光栅,有效防止人员受伤。
三、技术参数1.最大冲压力:80吨,与设备最大冲压力相对应,可承受较大的冲压力,保证冲压精度。
2.工作台硬度:HRC55-60度,确保工作台耐磨性,延长使用寿命。
3.工作台底面导轨材质:GCr15,提高滑块的运行精度和稳定性。
4.压力控制精度:±3%,满足自动化生产的需求。
5.操作方式:气动控制,操作简便、安全。
6.噪音等级:≤80dB(A),符合环保要求。
四、适用范围该设备适用于各类小型金属零件的冲压加工,广泛应用于汽车零部件、家电、五金工具等行业。
具有生产效率高、精度准确等优点。
五、保养与维护为确保设备的正常运行,需要定期进行保养和维护,具体包括:1.定期检查各部件的磨损情况,及时更换易损件。
2.保持油润滑,定期对设备进行加油润滑。
3.定期清理工作台表面,保持设备清洁。
4.定期检查安全装置是否正常,确保安全操作。
六、总结总的来说,80吨气动冲床工作台是一款性能稳定、操作简便、适用范围广的金属冲压设备。
在选择和使用该设备时,需要充分了解其参数和技术要求,并做好日常保养和维护工作,以确保设备的正常运行和生产效率。
希望本文对大家有所帮助,祝大家工作顺利!。
冲压机的功能

冲压机的功能冲压机是一种常见的金属加工设备,广泛应用于各个行业。
它的主要功能是将金属材料通过一系列的工序,通过冲压模具的作用,进行成型、切割、弯曲等加工。
冲压机的主要功能之一是成型。
通过冲压机,可以将金属材料加工成各种形状。
例如,可以将平板材料冲压成帽子形状的零件,也可以将管材冲压成各种形状的螺纹接头。
冲压机通过冲压模具的作用,使得金属材料在一次或多次冲压过程中,逐渐形成所需的形状。
这种成型方式具有高效、精确的特点,可以满足不同形状零件的生产需求。
冲压机的功能还包括切割。
在金属加工过程中,常常需要对金属材料进行切割,以得到所需的尺寸和形状。
冲压机通过冲压模具的切割功能,可以将金属材料切割成各种形状的零件。
无论是直线切割,还是曲线切割,冲压机都能够满足要求。
切割精度高,速度快,可以大大提高生产效率。
冲压机还具有弯曲的功能。
在一些需要弯曲金属材料的场合,冲压机可以通过冲压模具的作用,将金属材料弯曲成所需的角度和形状。
无论是简单的弯曲,还是复杂的弯曲,冲压机都可以完成。
弯曲后的零件具有较高的强度和稳定性,适用于各种工程和制造领域。
冲压机的功能还包括拉伸、压缩、拉拔等。
通过冲压机,可以对金属材料进行各种形式的加工和变形,以满足不同的需求。
例如,可以将金属材料拉伸成细丝,也可以将金属材料压缩成薄板。
这些加工方式可以使金属材料的性能得到改善,满足特定的工程要求。
冲压机的功能不仅局限于金属加工,还可以用于其他材料的加工。
例如,可以用冲压机对塑料材料进行成型、切割、弯曲等加工。
冲压机通过更换适应不同材料的冲压模具,可以实现对各种材料的加工需求。
总的来说,冲压机是一种多功能的加工设备。
它可以通过冲压模具的作用,对金属和其他材料进行成型、切割、弯曲等加工,以满足各种工程和制造领域的需求。
冲压机具有高效、精确的特点,可以大大提高生产效率和产品质量。
在现代工业生产中,冲压机已经成为不可或缺的设备之一。
冲压机构的应用及原理图解
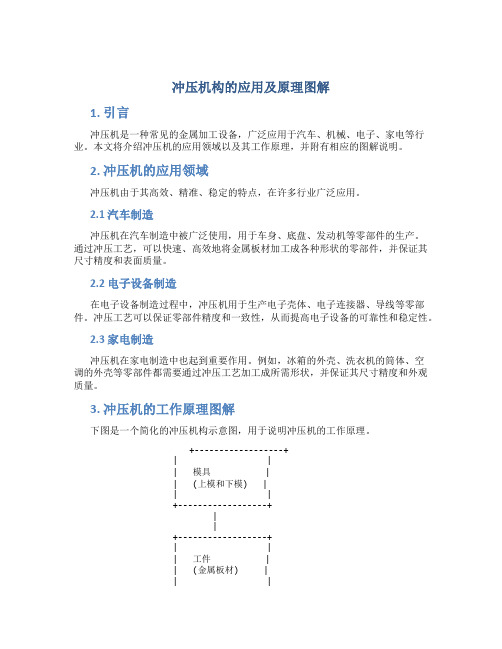
冲压机构的应用及原理图解1. 引言冲压机是一种常见的金属加工设备,广泛应用于汽车、机械、电子、家电等行业。
本文将介绍冲压机的应用领域以及其工作原理,并附有相应的图解说明。
2. 冲压机的应用领域冲压机由于其高效、精准、稳定的特点,在许多行业广泛应用。
2.1 汽车制造冲压机在汽车制造中被广泛使用,用于车身、底盘、发动机等零部件的生产。
通过冲压工艺,可以快速、高效地将金属板材加工成各种形状的零部件,并保证其尺寸精度和表面质量。
2.2 电子设备制造在电子设备制造过程中,冲压机用于生产电子壳体、电子连接器、导线等零部件。
冲压工艺可以保证零部件精度和一致性,从而提高电子设备的可靠性和稳定性。
2.3 家电制造冲压机在家电制造中也起到重要作用。
例如,冰箱的外壳、洗衣机的筒体、空调的外壳等零部件都需要通过冲压工艺加工成所需形状,并保证其尺寸精度和外观质量。
3. 冲压机的工作原理图解下图是一个简化的冲压机构示意图,用于说明冲压机的工作原理。
+------------------+| || 模具 || (上模和下模) || |+------------------+||+------------------+| || 工件 || (金属板材) || |+------------------+||+--------------------+| || 冲头 || (上冲头和下冲头) || |+--------------------+4. 冲压机的工作原理说明冲压机的工作原理是通过上模和下模加压,使得冲头对金属板材进行冲压加工。
冲压机的工作过程如下: 1. 工件放置在模具上,上模和下模夹紧工件。
2. 冲头向下移动,对金属板材进行冲击。
3. 当冲头施加足够的压力时,金属板材被冲剪下来,成为所需形状的零部件。
4. 移除冲压好的工件后,冲头向上移动,使得下一个工件能够放置在模具上。
冲压机的工作原理简单明了,通过不同的模具和冲头,可以加工出各种不同形状的零部件。
- 1、下载文档前请自行甄别文档内容的完整性,平台不提供额外的编辑、内容补充、找答案等附加服务。
- 2、"仅部分预览"的文档,不可在线预览部分如存在完整性等问题,可反馈申请退款(可完整预览的文档不适用该条件!)。
- 3、如文档侵犯您的权益,请联系客服反馈,我们会尽快为您处理(人工客服工作时间:9:00-18:30)。
薄片零件冲压机⏹薄壁零件冲压机的设计工作原理及加工过程◆薄壁零件冲压机是用于将具有良好拉伸延展性的薄壁金属板(如铝板)一次冲压成所规定形状的机械机构.它的主要加工过程如下:⏹将坯料送至待加工位置⏹下模固定在机架上,上模先以较大速度接近坯料,接着以近似匀速将坯料冲压拉延成形并将成品快速推出模腔,最后快速返回.原始数据及设计要求◆动力源为1400r/min的转动电动机◆冲压成型制品生产率约70件/min◆上模移动总行程为250mm,其拉延行程置于总行程末段,约为50mm◆上模行程速比系数K1=1.88;推杆行程速度系数K2 =1.4◆坯料输送最大距离200mm◆最小传动角45°三、传动系统方案设计⏹冲床传动系统如图3-1所示。
电动机转速经带传动、齿轮传动降低后驱动机器主轴运转。
原动机为三相交流异步电动机,其同步转速选为1400r/min,可选用如下型号:⏹电机型号额定功率(kw)额定转速(r/min)⏹Y112M-4 4 1440⏹ Y132S-4 5.5 1440⏹ Y132M-4 7.5 1440⏹ 由生产率可知主轴转速约为70r/min ,若电动机暂选为Y132S-4,则传动系统总传动比约为=20。
取带传动的传动比i b =2,则齿轮减速器的传动比i g =10,故可选用两级齿轮减速器。
图3-1 冲床传动系统● 执行机构运动方案设计及讨论⏹该冲压机械包含两个执行机构,即冲压机构和送料机构。
冲压机构的主动件是曲柄,从动件(执行构件)为滑块(上模),行程中有等速运动段(称工作段),并具有急回特性;机构还应有较好的动力特性。
要满足这些要求,用单一的基本机构如偏置曲柄滑块机构是难以实现的。
因此,需要将几个基本机构恰当地组合在一起来满足上述要求。
送料机构要求作间歇送进,比较简单。
实现上述要求的机构组合方案可以有许多种。
下面介绍几个较为合理的方案。
⏹齿轮—连杆冲压机构和凸轮—连杆送料机构⏹如图5—3所示,冲压机构采用了有两个自由度的双曲柄七杆机构,用齿轮副将其封闭为一个自由度。
恰当地选择点C的轨迹和确定构件尺寸,可保证机构具有急回运动和工作段近于匀速的特性,并使压力角尽可能小。
⏹送料机构是由凸轮机构和连杆机构串联组成的,按机构运动循环图可确定凸轮推程运动角和从动件的运动规律,使其能在预定时间将工件推送至待加工位置。
设计时,若使l OG<l OH,可减小凸轮尺寸。
◆4-1 冲床机构方案之一⏹ 2.六杆机构⏹冲压机构采用六杆机构,可保证机构具有急回特性和工作段近于匀速的特征,并使压力角尽可能小.用一般的四杆急回机构,虽可满足急回要求,但其工作行程的等速性能往往不好,采用六杆机构就可获得改善.⏹送料机构是由四杆机构组成,按机构的运动循环图确定主动件和从动件运动规律,则机构可在预定时间将工件送至待加工的位置.◆4-2 冲床机构方案之二⏹3.棘轮机构⏹冲压机构采用棘轮机构.棘轮和一四杆机构串联,上模上升时,摇杆顺时针摆动,并通过棘爪带动棘轮和工作抬顺时针转位.当上模下降进行冲压时,摇杆逆时针摆动,则棘爪在棘轮上滑动,工作台不动.凸轮送料机构的凸轮轴通过齿轮机构与曲柄轴相连,若按机构运动循环图确定凸轮转角及其从动件的运动规律,则机构可在预定时间将工件送至待加工位置.◆4-3 冲床机构方案之三⏹经过分析论证,方案1是三个方案中最为合理的方案,下面就对其进行设计。
八、传动件的设计 齿轮的设计传动齿轮设计高速级大小齿轮的设计:①材料选择:高速级小齿轮选用45#钢调质,齿面硬度为250HBS 。
高速级大齿轮选用45#钢正火,齿面硬度为220HBS 。
②查表得:lim 1550H Mpa σ= lim 2540H Mpa σ=。
查表得: 1.1H S = 1.3F S =。
故[]lim 115505001.1H H HMpaMpa S σσ=== []lim 225404901.1H H HMpaMpa S σσ===。
查表得:lim 1200F Mpa σ= lim 2150F Mpa σ=。
故[]lim 112001541.3F F FMpa Mpa S σσ=== []lim 221501151.3F F F MpaMpa S σσ===。
③按齿面接触强度设计:9级精度制造,查课本第164页表11-3得:载荷系数 1.2K =,取齿宽系数0.4a ϕ= 计算中心距:()[]()11122533335335 1.2 1.069101 4.631179.44900.4 4.63H a KT a u u σϕ⎛⎫⨯⨯⎛⎫≥+=+=⎪ ⎪⎪⨯⎝⎭⎝⎭考虑高速级大齿轮与低速级大齿轮相差不大取210a = 2.5m =则122168aZ Z m +==取129Z = 2139Z = 实际传动比:1394.7929=传动比误差:4.79 4.63100% 3.5%5%4.63-⨯=<。
齿宽:0.421084a b a ϕ==⨯=取284b =190b =高速级大齿轮:284b = 2139Z =高速级小齿轮:190b = 129Z = ④验算轮齿弯曲强度: 查表:1 2.6F Y = 2 2.2F Y = 按最小齿宽284b =计算:[]1111132222 1.2106.9 2.61043.584 2.529F F F KT Y Mpa bm Z σσ⨯⨯⨯⨯===<⨯⨯[]2212136.8F F F F F Y Mpa Y σσσ=⨯=< 所以安全。
⑤齿轮的圆周速度: 1129 2.5314.81.19/601000601000d nV m s ππ⨯⨯⨯===⨯⨯查表知选用9级的的精度是合适的。
低速级大小齿轮的设计:①材料:低速级小齿轮选用45#钢调质,齿面硬度为250HBS 。
低速级大齿轮选用45#钢正火,齿面硬度为220HBS 。
②查表得:lim 3550H Mpa σ= lim 4540H Mpa σ=。
查表得: 1.1H S = 1.3F S =。
故[]lim 335505001.1H H HMpaMpa S σσ=== []lim 445404901.1H H HMpaMpa S σσ===。
查表得:lim 3200F Mpa σ= lim 4150F Mpa σ=。
故[]lim 332001541.3F F FMpa Mpa S σσ=== []lim 441501151.3F F F MpaMpa S σσ===。
③按齿面接触强度设计:9级精度制造,查表得:载荷系数 1.2K =,取齿宽系数0.5ϕ= 计算中心距:()[]()22222333335335 1.2470.3101 3.561241.34900.4 3.56H KT a u u σϕ⎛⎫⨯⨯⎛⎫≥+=+= ⎪ ⎪⎪⨯⎝⎭⎝⎭取250a = 4m = 则 342125aZ Z m+==取327Z =498Z = 计算传动比误差:983.5627100% 1.9%5%3.56-⨯=<合适齿宽:0.5250125b a ϕ==⨯=则取4125b = ()34510130b b =+= 低速级大齿轮:4125b = 498Z = 低速级小齿轮:3130b = 327Z = ④验算轮齿弯曲强度: 查表得:3 2.65F Y =4 2.25F Y = 按最小齿宽4125b =计算:[]3333332222 1.21591.5 2.651047.9125427F F F KT Y Mpa bm Z σσ⨯⨯⨯⨯===<⨯⨯ []4234340.7F F F F F Y Mpa Y σσσ=⨯=<安全。
⑤齿轮的圆周速度:32274680.12/601000601000d n V m s ππ⨯⨯⨯===⨯⨯查表知选用9级的的精度是合适的。
九、轴的设计高速轴设计:①材料:选用45号钢调质处理。
查表取[]35Mpa τ= C=100。
②各轴段直径的确定: 1min 133 3.5210022.4314.8P d C n ≥== 又因为装小带轮的电动机轴径38d =,又因为高速轴第一段轴径装配大带轮,且()10.8 1.238d =⨯所以查手册第9页表1-16取136d =。
L 1=1.75d 1-3=60。
240d =因为大带轮要靠轴肩定位,且还要配合密封圈,所以查表取240d =,L 2=m+e+l+5=28+9+16+5=58。
3d 段装配轴承且32d d >,所以查表取345d =。
选用6009轴承。
L 3=B+3∆+2=16+10+2=28。
4d 段主要是定位轴承,取450d =。
L 4根据箱体内壁线确定后在确定。
5d 装配齿轮段直径:判断是不是作成齿轮轴: 41 2.52f d d e t m -=-<查表得:1 3.3t mm =得:e=5.9<6.25。
6d 段装配轴承所以6345d d == L 6= L 3=28。
2)、校核该轴和轴承:L 1=73 L 2=211 L 3=96作用在齿轮上的圆周力为:31122106.910294829 2.5t T F N d ⨯⨯===⨯径向力为2984201073r tF Ftg tg N =∂=⨯︒= 作用在轴1带轮上的外力:1132.8Q F F N == 求垂直面的支反力: 2112211107380073211r V l F F N l l ==⨯=++ 211073800273V r V F F F N =-=-= 求垂直弯矩,并绘制垂直弯矩图:⏹ 3222732111057.6.av v M F l N m -==⨯⨯=⏹ '311800731057.4.avv M F l N m -==⨯⨯= 求水平面的支承力: ◆ 由1122()H t F l l F l +=得 ◆ 21122112948219773211H t l F F l l ==⨯=++N ◆ 2129482197751H t H F F F =-=-=N 求并绘制水平面弯矩图:⏹ 31121977310158.2.aH H M F l N m -==⨯⨯=⏹ '32275121110158.4.aHH M F l N m -==⨯⨯= 求F 在支点产生的反力: ◆ 3112961132.8384.373211F l F F N l l ⨯===++ ◆ 21384.31132.81517.1F F F F F N =+=+= 求并绘制F 力产生的弯矩图:3231132.89610108.7F M Fl N -==⨯⨯='311384.3731027.7aFF M F l N -==⨯⨯= F 在a 处产生的弯矩:311384.3731027.7aF F M F l Nm -==⨯⨯= 求合成弯矩图:考虑最不利的情况,把'aF M 与22av aH M M +直接相加。