车间作业管理系统循环图
作业活动清单

作业活动清单 It was last revised on January 2, 2021
作业活动清单部门(车间):南车间
作业活动清单部门(车间):南车间
作业活动清单部门(车间):北车间
作业活动清单部门(车间):北车间
作业活动清单部门(车间):锅炉车间
作业活动清单部门(车间):锅炉车间
作业活动清单部门(车间):质检科
作业活动清单部门(车间):仓库
作业活动清单部门(车间):维修班
作业活动清单部门(车间):司机
作业活动清单部门(车间):保卫科
作业活动清单部门(车间):人力资源部
作业活动清单部门(车间):工会
作业活动清单部门(车间):安全环保部
作业活动清单
作业活动清单部门(车间):供销部
作业活动清单部门(车间):生产技术部
作业活动清单部门(车间):财务科。
PDCA循环

II
既不重要 也不紧急
I
不重要 但紧急 IV
Байду номын сангаас
III
一些干扰的电话 一些信件报告 会议 许多迫在眉睫的事情 符合别人期望的事
忙碌琐碎的事 无关紧要的信件 电话 浪费时间 逃避性活动
紧急
紧急
二:合理制订计划
计划的周期性
为什么?你是企业管理者打算怎么做?
因为工人织布5000米是非常辛苦的,这个目标太难实现了,也就没有多 大的吸引力了,这个时候有没有目标就都一样了。 所以在工作量上对员工有要求,并且量是合理的,企业的管理就会比较 好。凡是没有工作量的要求的企业一定不会好,这就是目标的作用!
一:设立目标的好处及目标的制订
PDCA循环图
行动
再防发生
决定目的和目标
计划
生产管理 者的重点 是什么??
应急措施
决定达成目标的 方法
ACTION PLAN CHECK DO
检查原因 教育,训练
定期以结果检查
工作实施
检查
实行
总结
生产管理者一定要抓住计划、检查者两个环节,只有 这两个环节的都把握好了,才可能成为一个合格的管 理者,如果管理者每天都在做实施的工作,那就不是 一个称职的管理者,只是一个超级员工,因为如果管 理者去做实施的事情,就没有人做计划和检查的工作。
PDCA的八个步骤
CHECK DO PLAN
5. 实施行动计划
ACT
7. 标准化和进一步推广 8. 在下一个改进机会中重新使用PDCA循环
6. 评估结果,执行完成要检查(分析数据)
1. 分析现状,找出存在的质量问题 1.1 确认问题 1.2 收集和组织数据 1.3 设定目标和测量方法 2. 分析产生质量问题的各种原因或影响因素 3. 找出影响质量的主要因素 4. 制定措施,提出行动计划 4.1 寻找可能的解决方法 4.2 测试并选择 4.3 提出行动计划和相应的资源
精益生产(3-看板管理)
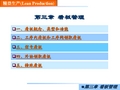
材料领取看板也称为材料准备看板、材料看板,如果领取 到挂着这张看板的物料箱,则摘下该看板送往上游工序, 领取看板指示数量的物料,相当于工序间领取看板。
精益生产(Lean Production)
2、信号看板的使用方法
冲压工序为例,说明信号看板的运行方法。 P45图3-23。
精益生产(Lean Production)
3、信号看板的位置计算
D L(1 ) N C N为三角看板的位臵,即订货点; D 为平均日需求量;L 为采购提前期; 为安全系数;C为盛放物料的容器。
工序内生产看板 工序间材料领取看板
D ( L T Ts ) N C
N为材料领取看板的位臵,即订货点;D为平均日需求 量;L为采购提前期; Ts为安全库存时间;C为盛放物 料的容器。
精益生产 (Lean Production) 3 、双看板工作系统 (P36图3-10)
依靠工序内生产看板和工序间领取看板分别来传递生产指令和搬运指令 的生产信息系统称为双看板系统。
双看板系统运行循环7步:
①后工序生产需求拉动物料配送人员带着工序间领取看板到前工序领取 零部件;
②到物料存放地将附在所领零部件容器内的工序内生产看板取下,并换 上领取看板; ③将工序内生产看板搬运到指定存放区域; ④换上领取看板的零部件传递到后工序,使用过程中被摘下; ⑤前工序,按照工序内看板摘下的顺序将看板放入工序内生产看板箱; ⑥按照看板要求进行生产; ⑦生产完成之后,附上工序内生产看板,转移到物料存放地,便于配送 人员随时领取。
看板的作用与功能
生产以及搬送的作业指令 防止过量生产和搬送 进行“目视管理”的工具 改善的工具
精益生产(Lean Production)
生产车间现场管理培训课件(PPT 44页)
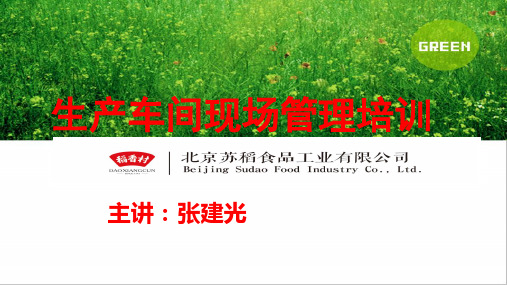
A
P
C
D
P(Plan) ——计划阶段 D(Do) ——执行阶段 C(Check)——检查阶段 A(Action)——处理阶段
三、生产现场的质量控制
1、在全面质量管理中使用PDCA循环法
阶段
步
骤
P 1、分析现状,找出问题 2、找出产生问题的原因或影响因素 3、找出原因中的主要原因 4、针对主要原因,制定解决问题的方案
一、优秀现场管理的标准和要求
一、优秀现场管理的标准和要求
3、现场管理六要素(5M1E分析法)
现场管理的六个要素即:人、机、料、法、环、测。 ----也称为5M1E分析法。
1) 人(Man):操作者对质量的认识、技术、身体状况等; 2) 机器(Machine):设备、测量仪器的精度和维护保养状况等; 3) 材料(Material):材料能否达到要求的性能等; 4) 方法(Method):生产工艺、设备选择、操作规程等; 5) 测量(Measurement):测量时采取的方法是否标准、正确; 6) 环境(Environment):工作现场的技术要求和清洁条件等; 由于这五个因素的英文名称的第一个字母是M和E,简称为5M1E。
D 5、按制定的计划认真执行 C 6、检查措施执行的效果 A 7、巩固提高,总结成功经验
8、把未解决或新出现的问题转入下一循环
主要方法和内容
调查表、分层法、排列图 因果图 排列图、相关图等 预期达到的目的(What) 在哪里执行措施(Where) 由谁来执行(Who) 何时开始和完成(When) 如何执行(How)
高企业经济效益。
二、现场管理的基本方法
(二)、作业标准化
3、标准的制定要求: 1)、目标指向:即遵循标准总是能保持生产出相同品
PMC运转流程图,职能,岗位职责,扮演角色
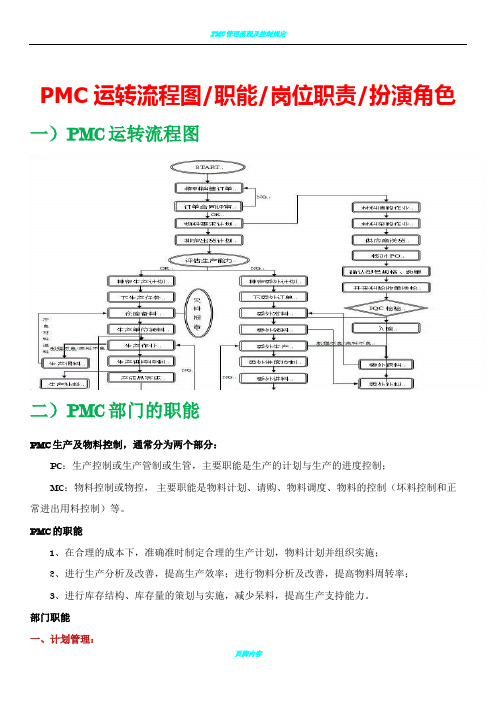
PMC运转流程图/职能/岗位职责/扮演角色一)PMC运转流程图二)PMC部门的职能PMC生产及物料控制,通常分为两个部分:PC:生产控制或生产管制或生管,主要职能是生产的计划与生产的进度控制;MC:物料控制或物控,主要职能是物料计划、请购、物料调度、物料的控制(坏料控制和正常进出用料控制)等。
PMC的职能1、在合理的成本下,准确准时制定合理的生产计划,物料计划并组织实施;2、进行生产分析及改善,提高生产效率;进行物料分析及改善,提高物料周转率;3、进行库存结构、库存量的策划与实施,减少呆料,提高生产支持能力。
部门职能一、计划管理:主导销售订单评审,对订单交期负责;编制生产计划和生产订单并组织生产;生产计划和生产订单情况跟进;生产协调会、周例会的组织与召开;进行产能负荷分析,调整生产计划;协调各部门的工作进度和衔接,对车间各工序时间和工作提出调整;生产计划、产品质量、数量及时间性统计,编制分析报告;准确及时统计计划物控各项数据尤其针对各机组、操作人工时效率和产品质量进行统计;提出各种分析报告,反馈统计信息。
二、物控管理:物料需求计划的制定与监督执行;配合产品开发部做好BOM、工艺路线的整理和编制;进行供应商交期统计和改善,有效进行材料跟进;生产过程中待料、退料、补料和借料以及订单改制的管理;呆废料定期处理;物料进、销、存的核实与控制;公司所有生产材料采购请购的预审;针对销售订单或生产进行物料使用状况统计和分析,为成本控制提供数据。
三、仓库管理:建立、完善仓库管理制度;准确统计库存,做到账物卡相符;做好仓库5s及物料标志等现场管理,且执行检查;做好合理安全库存、库存周期、有效期和边废料回收;不定期对重要材料进行抽盘。
直接考核指标生产订单完成率、总计划订单完成率、完成产值、超期14天订单量、停工待料工时、加班工时、仓库准时备货率、呆料金额、库存周转周期。
四、管理权限公司产品政策的参与权和知情权;生产计划及物料计划的编制执行和监督权、解释权;相关采购规则以及采购工作监督跟踪权;(进行交期、质量的有效控制)相关信息与资源的获取权及其他部门的协同权;特别是各生产车间或外协厂商生产进度监督与指导权;违规供应、采购的否决、制止权和处罚权(要求有所有A、B类材料采购预审权);物料管理的监控权;其他部门支援配合权。
亲和图、系统图、关联图法

4
第二章 品管新七大手法概述
5
第二章 品管新七大手法概述
三、品管新七大手法的特点:
▪ 整理语言资料的工具 ▪ 将语言情报用图形表示的方法 ▪ 引发思考,有效解决零乱问题; ▪ 充实计划; ▪ 防止遗漏、疏忽; ▪ 使有关人员了解; ▪ 促使有关人员的协助; ▪ 确实表达过程。 ▪ 管理工具,可以应用于QC以外的领域
7
第二章 品管新七大手法概述
五、使用新QC七大手法的时机与理由
❖ 解决问题时常发生没有数据或数据不足的情况 ❖ 管理活动强调PDCA循环,需要有充实的计划 ❖ 很多问题需所有相关人员共同解决,如何使他 们对问题理解、达成共识,并产生具体可执行方 案 ❖ QC领域中手法不足,无法有效解决更复杂的问 题,为适应将来更复杂的发展,需要有新QC手法 ❖ 图形思考使问题更易见、易懂,有利问题的解 决
25
第一节 亲和图
七、收集资料时应注意
搜集语言资料时,可以利用头脑风暴 法进行集体思考,利用共同参与、互相 激荡的方式,对于一个问题提供不同意 见或构想。进行时,宜延缓判断或避免 批评,应鼓励不同的想法,在寻求观念 上的整合或修正,如此一来不但可以提 高决策的创造力与品质,还可能出现意 想不到的解决方法
15
第一节 亲和图
四、亲和图特点
❖从混淆的状态中,采集语言资料,将其 整合以便发现问题; ❖打破现状,产生新思想; ❖掌握问题本质,让有关人员明确认识; ❖团体活动,对每个人的意见都采纳,提高全 员参与意识;
16
第一节 亲和图
五、亲和图类型 ❖个人亲和图
▪主要由一人来进行,重点放在资料的组 织上。
净化车间进出流程图

无尘车间管理制度目录1.0 无尘车间管理的目的2.0 无尘车间管理的原则3.0 适用范围4.0 术语5.0 管理程序5.1 无尘车间施工管理制度5.2 无尘车间洁净度定期检测制度/测量标准5.3 无尘车间人员管理制度5.4 无尘车间洁净服管理制度5.5 无尘车间物流/洁净室内设备及工器具管理制度5.6 无尘车间清洁、清扫和灭菌管理5.7 无尘车间洁净室安全管理6.0 版本更改记录1.0 无尘车间管理的目的半导体产品生产过程对车间有明确的洁净要求,为了满足生产工艺需要、保证产品质量、安全生产,必须对洁净室的环境、人员、物料、设备、生产过程等进行控制。
2.0 无尘车间管理的原则2.1进入洁净室的管理,包括对洁净室工作人员进入、物料进入、各类设备的搬入以及相关的设备、管线的维护管理,应做到不得将微粒、微生物带入洁净室。
2.2操作管理技术,对洁净室内人员用洁净工作服的制作、穿着和清洗;操作人员的移动和动作;室内设备及装修材料的选择和清扫、灭茵等,尽可能地减少、防止洁净室内尘粒、微生物的产生、滞留、繁殖等。
2.3严格各类设备、设施的维护管理,制定相应的操作规程,保证各类设备、设施按要求正常运转,包括净化空调系统、各类水气电系统、生产工艺设备和工器具(工装夹具)等。
以确保产品生产工艺要求和空气洁净度等级。
2.4清扫、灭菌管理,对洁净室内的各类设备、设施的清扫、灭茵以及方法、周期和检查作明确的规定,防止、捎除洁净室内尘粒、微生物的产生、滞留、繁殖。
2.5洁净室环境控制的内容包括:空气净化、洁净建筑、与产品直接接触的水或气体或化学品和生产设备、工器具等的污染物控制以及微振动、噪声、静电的控制、防止等。
3.0 适用范围半导体公司所有洁净生产区及洁净辅助间(包括人员净化用室、物料净化用室和相关生活用室等)、车间内管理区(包括部分办公、值班、管理和体息室等)和将来新建、改建、扩建的洁净厂房及其辅助用房。
4.0 术语洁净生产区是洁净厂房的主要部分,对洁净级别有明确规定的区域。
钣喷车间流程管理培训课件(PPT 47张)

例如:对钣金质量的过程加以严格的检验,可以减少喷漆工序的材料和 时间的消耗,避免浪费。 钣金的质量越好,刮涂原子灰的量就会越少,修理速度也就越快,反之 势必造成浪费。
25
钣喷快修流水线草案一(移动式)
调漆 房
工 具 范 例
⑺ ⑹
调 色房
⑻
⑼
⑽
⑾
待 修 工 位
喷漆快修流水线 拆件放置区
1
杜邦汽车修补漆
钣喷车间流程管理培训
2
如何才能使维修厂盈利 如何盈利?
开源(提高收入)
客源:新车捆绑,保险公司 推荐,使用各种营销手段,增 加服务种类,吸引客户。 质量:提高维修质量,提升 客户满意度和忠诚度 效率:提高交车速度及工作 效率、增加产值。
节流(降低成本)
降低工厂运营成本:能耗、 返工、浪费、设备,行政
对产品不满意
6
服务为什么那么重要?
愿意推荐同一家4S店给朋友的意愿
对产品满意
说明:回答 “ 绝对会 ” 及 “ 大概会 ”得比率。
21% 90%
对4S店服 务不满意 对4S店服 务满意
43% 0%
对产品不满意
7
修理厂钣喷业务的现状
修理厂每天面对的压力:
• • • • • 加班,加班,再加班。(返工现象——“旺丁不旺财”) 材料成本比例(材料与接车价比例)越来越高. 钣喷车间成为瓶颈(修补时间长、钣喷车间位置小、喷涂间数量
工 具 范 例
完成日期 责任人
7月30日 7月30日 8月30日 7月30日 8月30日
符亮 潘勇 李洪 符亮 潘勇
面漆
1
2 1
7月15日
李洪
7月20日 叶育超 7月15日 李洪