金属塑性变形物理本质
金属的塑性变形

滑移
滑移:在切应力作用下,晶体的一部分相对于另一部分沿着一
定的晶面(滑移面)和晶向(滑移方向)产生相对位移, 且不破坏晶体内部原子排列规律性的塑变方式。
τ
τ
a)未变形
bτ )弹性变形
τc)弹塑性变形
单晶体滑移变形示意图
d)塑性变形
孪生
孪生:晶体内的一部分原子(红色)相对另一部分原子沿某个
晶面转动,使未转动部分与转动部分的原子排列成镜面对称关系。
一、金属的可锻性(塑性加工性能)
定义:在锻造过程中,金属通过塑性加工而不开裂, 并获得合格零件的能力。 衡量指标:金属的塑性和变形抗力 塑性越高、变形抗力越低,可锻性越好。
二、影响金属可锻性的因素:
三个主要因素:金属的本质、加工条件、应力状态 1、金属的本质(内在因素): ①化学成分
➢ 碳钢:钢的含碳量越低,可锻性越好; ➢ 合金钢:合金元素含量越高,可锻性越差; ➢ 纯金属的可锻性优于合金。 ②金属组织
冷变形过程缺点:
①冷变形过程的加工硬化使金属的塑性变差,给进一步塑性变 形带来困难。 ②对加工坯料要求其表面干净、无氧化皮、平整。 ③加工硬化使金属变形处电阻升高,耐蚀性降低。
五、纤维组织及其利用
纤维组织(热加工流线):
塑性加工中,金属的晶粒形状和晶界分布的杂质沿变形方 向被拉长,呈纤维状。纤维组织不能热处理消除,只能通过锻 压改变其形状和方向。
纯金属或单相固溶体(奥氏体)的可锻性优于多相组织; 均匀细晶的可锻性优于粗晶组织和铸态柱状晶; 钢中存在网状二次渗碳体时可锻性下降。
影响金属可锻性的因素:
2、加工条件:
①变形温度 温度越高,金属塑性提高,
变形抗力降低,可锻性提高。
加热温度过高,产生缺陷: 过热:晶粒长大,使综合机械性能下降; 过烧:晶粒边界氧化或熔化 ,一击即碎; 脱碳:碳与环境气体反应,使表层含碳量减少; 严重氧化:表层与 氧反应,生成氧化物。
(金属塑性成形原理课件)第2讲塑性变形物理本质

存在着一系列缺陷: 点缺陷、线缺陷、 面缺陷
2020/10/4
10
Lesson Two
一些金属材料的实验屈服强度和理论屈服强度
材料
理论强度(G/30)/GPa 实验强度/MPa 理论强度/实验强度
银 铝 铜 镍 铁 钼 铌 镉 镁(柱面滑移) 钛(柱面滑移) 铍(基面滑移) 铍(柱面滑移)
2020/10/4
13
Lesson Two
肖脱基空位——只形成空位而不形成等量的间隙原子 弗兰克尔缺陷——同时形成等量的空位和间隙原子
2020/10/4
14
Lesson Two
在实际晶体中,点缺陷的形式可能更复杂。例 如,即使在金属晶体中,也可能存在两个、三个甚 至多个相邻的空位,分别称为双空位、三空位或空 位团。但由多个空位组成的空位团从能量上讲是不 稳定的,很容易沿某一方问“塌陷”成空位片(即 在某一原子面内有一个无原子的小区域)。同样,间 隙原子也未必都是单个原子,而是有可能m个原子均 匀分布在n个原子位置的范围内(m>n),形成所谓 “挤塞子”(crowdion)。
(1)表面:指所研究的金属材料系统与周围气相或液相介质的接触面。 (2)晶界、亚晶界:指多晶体材料内部,结构及成分相同,而位向不 同的两部分晶体之间的界面。 (3)相界:指晶体材料内部不仅位向不同,而且结构不同,甚至成分 也不同的两部分晶体之间的界面。在纯金属的同素异晶转变过程中出现 的相界面,其两侧仅结构不同;而合金相的相界两侧,除结构不同外, 往往成分也不相同。 此外,还有孪晶界、反相畴界,层错界、胞壁等等。
(1)对称倾侧晶界
对称倾侧晶界相当于两部分晶体,沿着平行于界面
的某一轴线,各自转过方向相反的θ/2而形成的。两晶 粒位向差为θ,如下图1所示。此晶界相当于两个晶粒的 对称面,它只有一个自由度θ。
第三章 金属塑性变形的物理基础
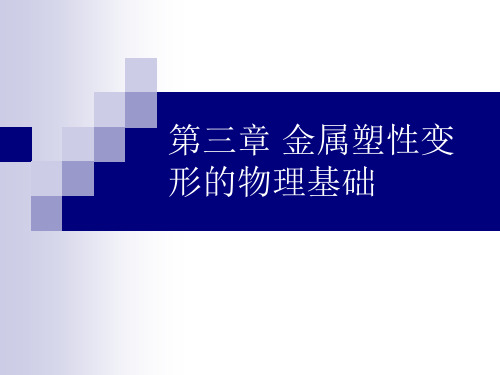
(1)塑性的基本概念
什么是塑性? 塑性是金属在外力作用下产生永久变形 而不破坏其完整性的能力。
塑性与柔软性的区别是什么? 塑性反映材料产生永久变形的能力。 柔软性反映材料抵抗变形的能力。
塑性与柔软性的对立统一
铅---------------塑性好,变形抗力小
不锈钢--------塑性好,但变形抗力高 白口铸铁----塑性差,变形抗力高
塑性指标的测量方法
拉伸试验法 压缩试验法 扭转试验法 轧制模拟试验法
拉伸试验法
Lh L0 100%
L0 F0 Fh 100%
F0
式中:L0——拉伸试样原始标距长度; Lh——拉伸试样破断后标距间的长度; F0——拉伸试样原始断面积; Fh——拉伸试样破断处的断面积
%
晶粒5 晶粒4 晶粒3
晶粒2
晶粒1
位置,mm
图5-6 多晶铝的几个晶粒各处的应变量。 垂直虚线是晶界,线上的数字为总变形量
四、合金的塑性变形
单相固溶体合金的变形 多相合金的变形
§3. 2 金属塑性加工中组织和性能变化 的基本规律
一、冷塑性变形时金属组织和性能的变化 二、热塑性变形时金属组织和性能的变化
2200
N/mm2
图4-6 正压力对摩擦系数的影响
0.5
μ
0.4
0.3
0.4
0.2 0.2
0.1
0
℃
200
400
600
800
图4-7 温度对钢的摩擦系数的影响
0
400
600
800 ℃
图4-8 温度对铜的摩擦系数的影响
测定摩擦系数的方法
夹钳轧制法 楔形件压缩法 塑性加工常用摩擦系数 圆环镦粗法
金属在塑性变形中的组织结构与性能变化

6 材料在塑性变形中的组织结构与性能变化本章仅将简要地介绍冷形变及其后的加热过程、以及热形变过程对金属和合金的组织结构与性能的影响的主要理论。
6.1 冷形变后金属组织结构和性能的变化金属和合金在低于再结晶温度进行压力加工时,通常就称为冷形变或冷加工。
钢在常温下进行的冷轧、冷拔、冷挤、冷冲等压力加工过程皆为冷形变过程。
在冷形变过程中组织和性能都会发生变化。
6.1.1 金属组织结构的变化金属塑性变形的物理实质基本上就是位错的运动,位错运动的结果就产生了塑性变形。
在位错的运动过程中,位错之间、位错与溶质原子、间隙位置原子以及空位之间、位错与第二相质点之间都会发生相互作用,引起位错的数量、分布和组态的变化。
从微观角度来看,这就是金属组织结构在塑性变形过程中或变形后的主要变化。
塑性变形对位错的数量、分布和组态的影响是和金属材料本身的性质以及变形温度、变形速度等外在条件有关的。
单晶体塑性变形时,随着变形量增加,位错增多,位错密度增加,运动位错在各种障碍前受阻,要继续运动需要增加应力,从而引起加工硬化。
变形到一定程度后产生交滑移,因而引起动态回复,这些塑性变形过程中的变化已是我们所熟知的,不再细述。
多晶体塑性变形时,随着变形量增加和单晶体变形一样,位错的密度要增加。
用测量电阻变化、储能变化的方法,或者用测量腐蚀坑的方法以及电镜直接观测的方法都可以出金属材料的位错密度。
退火状态的金属,典型的位错密度值是105~108 cm -2,而大变形后的典型数值是1010~1012cm -1。
通过实验得到的位错密度(ρ)同流变应力(σ)之间的关系是:21ρασGb = (6-1) 式中:a —等干0.2~0.3范围的常数;G —剪切弹性模量;b —柏氏矢量。
多晶体塑性变形时,因为各个晶粒取向不同,各晶粒的变形既相互阻碍又相互促进,变形量稍大就形成了位错胞状结构。
所谓胞状结构,是变形的各种晶粒中,被密集的位错缠给结区分许多个单个的小区域。
第二章 金属塑性变形的物理基础

26
锻造温度区间的制定
27
2、锻合内部缺陷 3、打碎并改善碳化物和非金属夹杂物在钢 中的分布 4、形成纤维组织 5、改善偏析
28
塑性变形过程中晶粒的变化
29
第三节 金属的超塑性变形
一、超塑性的概念和种类 概念:金属和合金具有的超常的均匀变形 能力。
大伸长率、无颈缩、低流动应力、易成形、无加工硬化
另一个取向,故晶界处原子排列处于过渡状态。
4、晶界不同于晶内性质:
3
一、变形机理
晶内变形 1、滑移 2、孪生 晶间变形 晶粒之间的相互转动和滑动 注意: 晶间变形的情况受温度的影响
4
1、滑移面和滑移方向的确定
确定滑移面:原子排 列密度最大的晶面 确定滑移方向:原子 排列密度最大的方向
5
金属的主要滑移方向、滑移面、滑移系
种类:
细晶超塑性:在一定的恒温下,在应变速率和晶粒度都满 足要求的条件下所呈现出的超塑性。 相变超塑性:具有相变或同素异构转变的金属,在其转变 温度附近以一定的频率反复加热、冷却。在外力的作用下 所呈现出的超塑性。
30
二、细晶超塑性变形的力学特征
无加工硬化
31
三、影响细晶超塑性的主要因素
应变速率
20
21
二、性能的变化 (力学性能) 加工硬化 成因:位错交互作用,难以运动 应用:强化(奥氏体钢) 避免:多次塑性加工中加入退火工序
22
第二节 金属热态下的塑性变形
热塑性变形:再结晶温度以上进行的塑性 变形 一、塑性变形时的软化过程 1、动态回复、动态再结晶 2、静态回复、静态再结晶、亚动钢中的碳和杂质元素的影响 碳 磷 硫 氮 氢 氧
37
2、合金元素对钢的塑性的影响 合金元素的加入,会使钢的塑性降低、变 形抗力提高 原因见课本p43
金属塑性成形原理期末复习
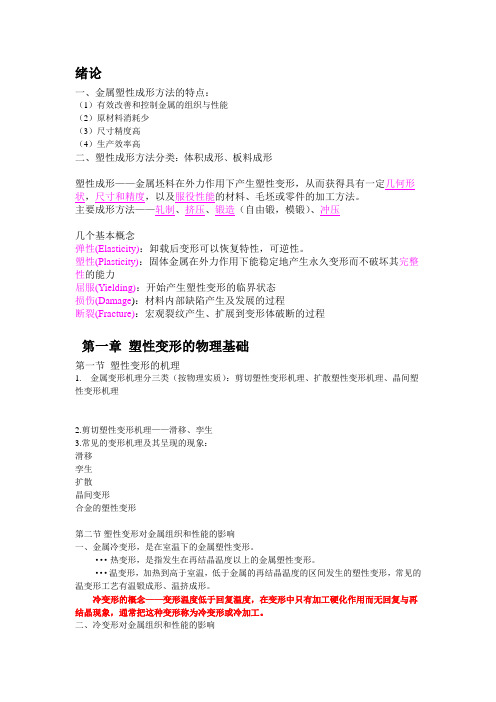
塑性指标:拉伸率δ和断面收缩率Ψ。 概 念: 金属在破坏前产生的最大
变形程度,即极限变形量。
H0 - Hk
塑性指标ε= ------------- ×100%(压缩法)
H0
塑性指标衡量金属塑性高低的指标。 塑性状态图及其应用 概念:表示金属塑性指标与变形温度及加载方式的关系曲线图形,简称塑性图。 应用:合理选择加工方法
静态回复 动态回复——主要通过位错的攀移、交滑移来实现。 2.再结晶
静态再结晶:利用金属变形余热发生 动态再结晶:热塑性变形过程中发生 亚动态再结晶:动态再结晶晶粒在热变形停止后的长大过程 (二)热塑性变形后金属组织和性能的变化 1.改善铸造组织,锻合内部缺陷 2.形成纤维组织 3 产生带状组织 超塑性的分类:恒温超塑性或第一类超塑性。
提高塑性的主要途径有以下几个方面: (1)控制化学成分、改善组织结构,提高材料的成分和组织的均匀性; (2)采用合适的变形温度—速度制度; (3)选用三向压应力较强的变形过程,减小变形的不均匀性,尽量造成均匀的变形状态; (4)避免加热和加工时周围介质的不良影响
第二节 金属的流动及其影响因素
第三节 金属塑性成形中的摩擦和润滑
几个基本概念 弹性(Elasticity):卸载后变形可以恢复特性,可逆性。 塑性(Plasticity):固体金属在外力作用下能稳定地产生永久变形而不破坏其完整 性的能力 屈服(Yielding):开始产生塑性变形的临界状态 损伤(Damage):材料内部缺陷产生及发展的过程 断裂(Fracture):宏观裂纹产生、扩展到变形体破断的过程
一般讲,如果变形速度大,有没有足够时间完成塑性变形,金属的变形抗力会提高,塑 性降低。变形速度对塑性的影响概括为变形速度的增大,金属和合金的变形抗力提高; 随变形速度提高,塑性变化的一般趋势如图;变形速度对锻压工艺也有广泛的影响。
金属塑性成形原理---第二章_金属塑性变形的物理基础
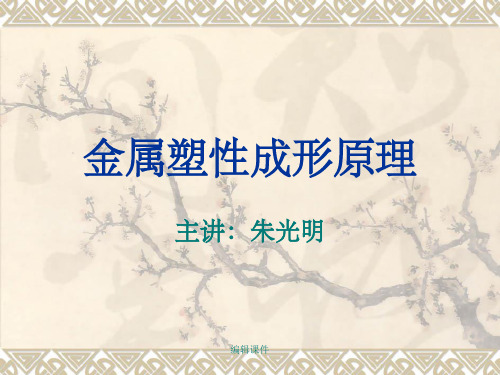
位错的攀移
❖ 螺型位错无攀移
❖ 正攀移——正刃型位错位错线上移
负刃型位错位错线下移
编辑课件
位错的交割
❖ 两根刃型位错线都在各自的滑移面上移动,
则在相遇后交截分别形成各界,形成割阶后
仍分别在各自的平面内运动。
❖ 刃型位错和螺型位错交割时,在各自的位错
线上形成刃型割阶,位错线也能继续滑移。
❖ 螺型位错和螺型位错交割时,相交后形成的
❖ 假设:理想晶体两排原子相距为a,同排原子间距
为b。原子在平衡位置时,能量处于最低的位置。
在外力τ作用下,原子偏离平衡位置时,能量上升,
原子能量随位置的变化为一余弦函数。
❖ 通过计算晶体的临界剪切应力,并与实际的临界
剪切应力进行比较,人们发现,理论计算的剪切
强度比实验所得到的剪切强度要高一千倍以上。
编辑课件
典型的晶胞结构
编辑课件
典型的晶胞结构
编辑课件
三种晶胞的晶格结构
编辑课件
一、塑性变形机理
实际金属的晶体结构
❖ 单晶体:各方向上的原子密度不同——各向
异性
❖ 多晶体:晶粒方向性互相抵消——各向同性
❖ 塑性成形所用的金属材料绝大多数为多晶
体,其变形过程比单晶体复杂的多。
编辑课件
多晶体塑性变形的分类
加工中,会使变形力显著增
加,对成形工件和模具都有
III.抛物线硬化阶段:
一定的损害作用;但利用金
与位错的交滑移过程有关,
θ3
随应变增加而降低,应力应变
属加工硬化的性质,对材料
曲线变为抛物线。
进行预处理,会使其力学性
能提高
编辑课件
2.2 金属热态下的塑性变形
大学金属工艺的金属塑性加工的相关问题的讲解
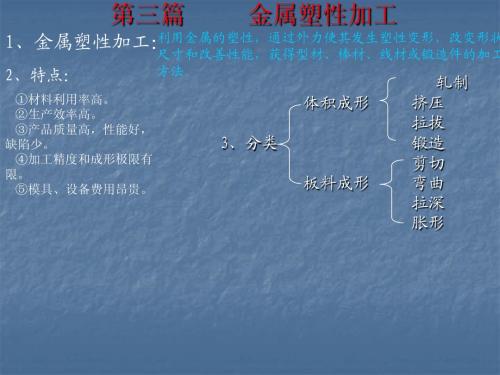
金属纤维组织
图3-6铸锭热变形前后的组织
纤维组织的特点
变形程度越大,纤维组织越明显。 常用锻造比γ表示变形程度。坯料拔长时的锻造比为: γ=F0/F 式中F0为坯料拔长前的横截面积;F为坯料拔长后的横截面积。 纤维组织使金属在性能上具有方向性。 纵向(平行于纤维方向)上的塑性、韧性提高, 横向(垂直于纤维方向)上的塑性、韧性则降低。 纤维组织的稳定性很高,不能用热处理或其它方法加以消除 不能用热处理或其它方法加以消除, 不能用热处理或其它方法加以消除 只有经过锻压使金属变形,才能改变其方向和形状。
知识点:
第二章
锻造
1、自由锻和模锻。 2、胎模锻。 3、余块、机械加工余量。 4、模锻--焊接成形。
锻造:在加压设备及工(模)具作用下,铸锭产生局部或全部的塑
性变形,以获得一定几何尺寸、形状和质量的锻件的加工方法。
第一节 锻造方法
一、自由锻
(1)、 (1)、自由锻是利用冲击力或压力使金属在上、下砧之间产生塑性变
位错移动:高位能的位错处原子, 位错移动 在比理论值小的切应力下滑移。从 一个位置滑移到另一个位置。
未变形
弹性变形
弹塑性变形
塑性变形
图3-2
位错运动引起塑性变形示意图
位 错 移 动 的 结 果: 塑 性 变 形。
晶内变形:金属由大量微小晶粒组成的 晶内变形 多晶体,由组成多晶体的许多单个晶粒 产生变形。其综合效果是塑性变形。 其综合效果是塑性变形。 其综合效果是塑性变形
A 锻造比: 锻造比:Y镦= A0 >1
拔长、镦粗、冲孔、弯曲、扭转、错移、 拔长、镦粗、冲孔、弯曲、扭转、错移、切割
使坯料高度减小,截面积增大的工序。 使坯料高度减小,截面积增大的工序。
2.金属塑性变形的物理本质

影响加工硬化曲线的因素
①晶体结构不同,曲线不同
②结构相同,层错能不同,曲线不同 扩展位错——由一个位错分解成两个半位错和
它们中间夹的层错带构成的位错组合
扩展位错的间距d d= KGb ε——层错能 ε↑,d ↓ 8 Cu ε= 40 erg/cm2 d可达20~30个原子间距 Al ε= 200 erg/cm2 ③温度 温度高,热激活容易,交滑移可提前进行, d仅为1~2个原子间距
5.复杂滑移
① 双滑移
——滑移在二个不同的滑移面和二个不同的
滑移方向上进行。
(a) 二个滑移系交替进行滑移。
滑移→晶体转动→不利方位→几何硬化 (b) 滑移阻力大 新旧滑移面互相切割,使变形阻力↑↑。
② 交滑移
——滑移在二个不同的滑移面和一个相 同的滑移方向 上进行。 (a)只有螺位错才能产生交滑移。 (b)交滑移能使受阻的位错重新开动,变形
一般低温、高速有利于孪生的产生。
三.塑性变形的其它机理
扩散机构:原子逐步从一个位置迁移到另
一个位置的过程。
1
非晶机构:原子流象粘滞性液体一样连续 流动。它是温度接近熔点的变 形机理。 晶块转动机构:此种机构会使晶界发生显
微破坏。
2
空位迁移过程
1
2.2 多晶体的塑性变形
一.多晶体变形的特点 1.变形不均匀 ①各晶粒的变形不均匀
二.加工硬化曲线(应力-应变曲线)
1.单晶体的加工硬化曲线(以面心立方晶体为例)
曲线分三段
曲线的斜率:加工硬化程度
加工硬化率
Ⅰ 易滑移阶段
滑移沿最有利的滑面和滑向进行。
1
硬化由位错塞积引起。
Ⅱ 线性硬化阶段
形成了多滑移,随ε↑,位错不断增殖,
材料加工成型理论第一章-金属塑性变形的物理本质

5. 割阶运动所引起的阻力
• 割阶运动所引起的阻力也就是形成点缺陷 引起的阻力。当带有割阶的位错滑移时, 如果割阶做的是非保守运动,则运动过程 中其后形成一连串的点缺陷。形成这些点 缺陷需要能量,这就相当于有反向的力阻 碍位错前进。形成这些点缺陷引起的阻力 为:
• 位错要运动,虽然很容易,但也必须至少克服点 阵阻力(派-纳力)对它的阻碍才能运动。
1.点阵阻力
• 位错向前运动,必须越过一个能量最大值的位置, 才能从一个低能的稳定位置过渡到另一个低能的 稳定位置。为此,就需要对位错施加足够的力以 供克服这一能垒所需要的能量,这个能垒就称为 派尔斯垒,克服这个能垒所需要的力就是派-纳力。
4. 位错切割穿过其滑移面的位错林所引起的阻力
• 位错林是指那些穿过运动位错所在滑移面的
位错。切割林位错所引起的阻力用
' s
表示,
是一种短程力。
• 热激活对于克服这个阻力是有很大作用的。
• 由于位错林的存在,必然存在应力场,林位
错的应力场对运动位错的阻力用
" s
表示,
该力是一种长程力,它对温度不敏感。
• 根据该理论可以估计出纯金属的理论屈服强度
m G / 2
• 一般金属晶体的理论屈服强度为103~104MPa 数量级。而实测纯金属单晶体大致为1MPa, 理论值是实际值的1000倍以上,说明把滑移 过程看成是整体刚性的移动与实际相差较远。
二、实际晶体屈服强度的构成
• 金属的理论屈服强度来源于金属的原子间的结合 力,它是金属原子间结合力大小的反映。而实际 晶体中存在各种晶体缺陷,如位错的存在,位错 易运动,因而不能充分发挥出原子间结合力的作 用,所以金属实际屈服强度远低于理论值。
材料成型基本原理总结

材料成型力学原理部分第十四章金属塑性变形的物理基础1、塑形成形:利用金属的塑性,使金属在外力作用下成形的一种加工方法,亦称金属塑性加工或金属压力加工。
2、金属塑性成形的优点:生产效率高、材料利用率高、组织性能亦改变、尺寸精度高。
3、塑性成形工艺:锻造、轧制、拉拔、挤压、冲裁、成型4、金属冷塑形变形的形式:1、晶内变形:滑移和孪生2、晶间变形:晶粒间发生相互滑动和转动5、加工硬化:在常温状态下,金属的流动应力随变形程度的增加而上升,为了使变形继续下去,就需要增加变形外力或变形功。
(指应变对时间的变化率)6、热塑性变形时金属组织和性能的变化1、改善晶粒组织2、锻合内部缺陷3、破碎并改善碳化物和非金属夹杂物在钢中的分布4、形成纤维组织5、改善偏析7、织构的理解:多晶体取向分布状态明显偏离随机分布的取向分布结构。
8、细化晶粒:1、晶粒越细小,利于变形方向的晶粒越多2、滑移从晶粒内发生止于晶界处,晶界越多变形抗力越大9、热塑性变形机理:晶内滑移、晶界滑移和扩散蠕变10、塑性:不可逆变形,表征金属的形变能力11、塑性指标:金属在破坏前产生的最大变形程度12、影响塑性的因素:1、化学成分和合金成分对金属塑性的影响2、组织状态对金属塑性的影响3、变形温度4、应变速率5、应力状态13、单位流动压力P:接触面上平均单位面积上的变形力14、碳和杂质元素的影响碳:其含量越高,塑性越差;磷:冷脆;硫:热脆性;氧:热脆性;氮:时效脆性、蓝脆、气孔;氢:氢脆、白点、气孔和冷裂纹等15、合金元素的影响:塑性降低硬度升高16、金属组织的影响(1)晶格类型(2)晶粒度(3)相组成(4)铸造组织17、变形温度对金属塑性的影响:对大多少金属而言,总的趋势是随着温度升高,塑性增加。
但是这种增加并不是线性的,在加热的某些温度区间,由于相态或晶界状态的变化而出现脆性区,使金属的塑性降低。
(蓝脆区和热脆区)18、变形抗力:指金属在发生塑性变形时,产生抵抗变形的能力一般用接触面上平均单位面积变形力来表示,又称单位面积上的流动压力19、质点的应力状态:变形体内某点任意截面上应力的大小和方向20、对变形抗力的影响因素:①化学成分:纯金属和合金②组织结构:组织状态、晶粒大小和相变③变形温度④变形程度:加工硬化⑤变形速度⑥应力状态21、金属的超塑性:细晶超塑性、相变超塑性第十五章应力分析1、研究塑性力学时的四个假设:①连续性假设:变形体不存在气孔等缺陷②匀质性假设:质点的组织、化学成分等相同③各向同性假设④体积不变假设2、质点:有质量但不存在体积或形状的点3、内力:在外力作用下,物体内各质点之间就会产生相互作用的力。
第四章金属材料的塑性变形与再结晶
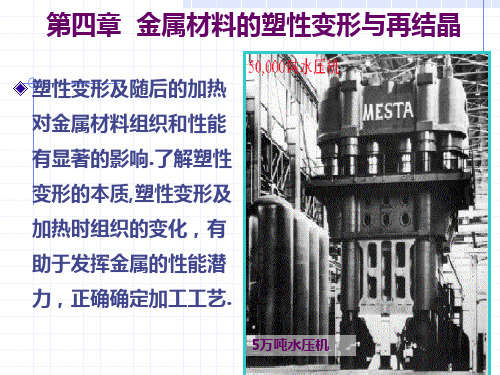
滑移方向上原子间距的 小于孪生方向上的原
整数倍,较大。
子间距,较小。
很大,总变形量大。
有限,总变形量小。
有一定的临界分切 压力 一般先发生滑移
所需临界分切应力远高于 滑移
滑移困难时发生
变形机制
全位错运动的结果 分位错运动的结果 34
(二) 多晶体金属的塑性变形
单个晶粒变形与单晶体相似,多晶体变形比单晶体复杂
① 晶界的特点:原子排列不规则;分布有大量缺陷
② 晶界对变形的影响:滑移、孪生多终止于晶界,极少穿 过。
35
当位错运动到晶界附近时,受到晶界的阻碍而堆积 起来,称位错的塞积。要使变形继续进行, 则必须增加 外力, 从而使金属的变形抗力提高。
36
晶界对塑性变形的影响
Cu-4.5Al合金晶 界的位错塞积
55
(4) 几何硬化:由晶粒转动引 起 由于加工硬化, 使已变形部 分发生硬化而停止变形, 而 未变形部分开始变形。没有 加工硬化, 金属就不会发生 均匀塑性变形。
未变形纯铁
加工硬化是强化金属的重要
手段之一,对于不能热处理
强化的金属和合金尤为重要
变形20%纯铁中的位错
56
2 对力学性能的影响
利弊
d. 孪生本身对金属塑性变形的贡献不大,但形成 的孪晶改变了晶体的位向,使新的滑移系开动, 间接对塑性变形有贡献。
33
总结
滑移
孪生
相同点
晶体位向
位移量 不 同 对塑变的贡献 点
变形应力
变形条件
1 切变;2 沿一定的晶面、晶向进行;3 不 改变结构。 不改变(对抛光面 改变,形成镜面对称关系 观察无重现性)。 (对抛光面观察有重现性)
1、晶粒取向和晶界对塑性变形的影响
金属塑性变形物理基础(ppt课件
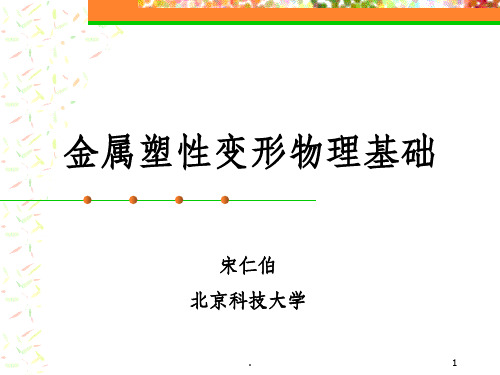
.
9
(2)晶体结构: 一个完整的晶粒或亚晶是由同类或不同比例的异类原子,按一 定规律结合在一起,并可以用严格的几何图案表达。 结构就是指原子集合体中各原子的组合状态。
金属和合金的典型结构模型: 面心立方晶体:Al、Ni、Cu、γ-Fe
.
5
前言
因此,为了达到有效的控制材料性能的目:
在现代缺陷理论的基础上,阐明金属塑 性变形的物理实质、变形机理、塑性变 形时材料的组织结构和性能变化的关系, 从而为合理地选择加工条件,保证塑性 变形过程的进行提供理论基础。
.
6
课程内容
1.金属材料的一般特性 2.金属塑性变形的物理本质 3.金属的塑性变形和强化 4.金属在塑性变形中的组织结构与性能变化
.
7
1.金属材料的一般特性
金属材料,尤其是钢铁材料: 由于本身具有比其它材料优越的综合性能; 由于在性能方面以及数量和质量方面蕴藏着巨大潜力; 对人类文明发挥着重要的作用。
决定金属材料性能的基本因素: 化学成分 --- 金属元素; “组织” 和“结构”-Biblioteka - 原子集合体的结构以及内部组织。
.
8
体心立方晶体:Cr、V、Mo、W、α-Fe、β-Ti
密排六方晶体:Zn、Mg、Be、α-Ti、α-Co
.
10
(3)结构缺陷:金属学中将原子组合的不规则性,统称 为结构缺陷,或晶体缺陷。
缺陷种类:
点缺陷:溶质原子,间隙原子,空位;
线缺陷:位错; 面缺陷:晶界,相界,层错,半位错…. 体缺陷:如固溶体中的偏聚区,孔洞….
样集中在一些滑移面上进行; 孪生比滑移困难一些,所以变形时首先发生滑移,当切应
第六章 金属材料性能与塑性变形
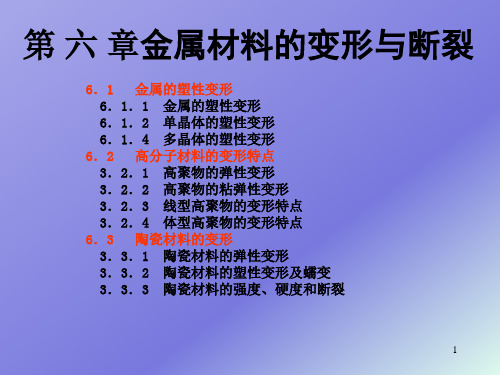
???
减震
恒力碟簧支吊架
第二节 弹性变形
1.2.5 滞弹性
(1)突然加载OA,产生瞬时应 变Oa ,而后产生附加应变Ah (2)快速卸载Be,产生瞬时应 变He 而后产生附加应变eO
滞弹性
在弹性范围内快速加载或卸载后,随时间延长产生附 加弹性应变的现象。
产生原因:可能与金属中点缺陷的移动有关。 在仪表和精密机械中,选用重要传感元件的材料时,需要考虑滞弹性问题。
P 载 荷 (N)
b
e p Pp s
(MPa) k
Pk
0
lk b (低碳钢的拉伸力-伸长曲线)
l
lu
l伸长 0 (mm)
p
b
k
u
(低碳钢的应力-应变曲线)
k
(%)
低碳钢的应力-应变曲线 (M Pa) b k
a
a′
0a段 aa ′段 a ′b段
弹性变形 阶段 塑性变形 阶段
但是,通常拉开n分之一个原子间距就发生了塑性变形——塑性变 形机理取代弹性变形
第二节 弹性变形
1.2.2 胡克定律
(一) 简单应力状态的胡克定律 1.单向拉伸
y
y
2.剪切和扭转
x z y
E
y
E
(1-1)
G
E G 3.E、G的关系 2(1 )
断口特征
第一节 应力-应变曲线
1.1.1 脆性材料的拉伸性能
在拉伸时只产生弹性变形,不产生或产生微量的塑性变形 强度高、塑性差的材料:玻璃、陶瓷、高强钢、铸铁
材料完全脆性的- 曲线
弹性变形阶段 应力-应变成正比
E G
第二章_金属塑性变形的物理基础

超塑性的特点
超塑性变形的一般特点: 1、大伸长率 2、无缩颈 3、低流动应力 4、易成形
采用超塑性成形工艺,可获得形状复杂和尺寸精确的锻件, 而变形力大大降低 。
超塑性成形实例
b 弥散强化
位错切过第二相粒子(表面能、错排能、 粒子阻碍位错运动)
四 塑性变形对金属组织和性能的影响
1 对组织结构的影响 (1) 形成纤维组织
晶粒拉长 杂质呈细带状或链状分布
H62黄铜挤压的带状组织
(2) 亚结构
变形量增大 位错缠结 位错胞 (大量位错缠结在胞壁,胞内位错密度低)
(3) 形变织构
四 塑性变形对金属组织和性能的影响
2 对力学性能的影响(加工硬化) (1)加工硬化(形变强化、冷作强化):随变形 量的增加,材料的强度、硬度升高而塑韧性下降 的现象。
2 对力学性能的影响(加工硬化)
强化金属的重要途径
利 提高材料使用安全性
(2)利弊
材料加工成型的保证
弊 变形阻力提高,动力消耗增大
孪生的特点
(1)孪生是一部分晶体沿孪晶面相对于另一部分晶体 作切变,切变时原子移动的距离是孪生方向原子间距的 分数倍;孪生是部分位错运动的结果;孪晶面两侧晶体 的位向不同,呈镜面对称;孪生是一种均匀的切变。
孪生的特点
(2)孪晶的萌生一般需 要较大的应力,但随后长 大所需的应力较小,其拉 伸曲线呈锯齿状。孪晶核 心大多是在晶体局部高应 力区形成。变形孪晶一般 呈片状。变形孪晶经常以 爆发方式形成,生成速率 较快。
位错密度越高,金属的强度、硬度越高。
S:位错线长度,V:体积,ρ:位错密度
金属塑性变形的物理基础

第二节金属热态下的塑性变形
01
02
03
04
第二节金属热态下的塑性变形 1.热塑性变形时软化过程
23% Option 1
30% Option 2
热塑性变形时软化过程
静态回复 在较低的温度下、或在较早阶段发生转变的过程称为静态回复。它是变形后的金属自发地向自由能降低的方向转变的过程。
静态再结晶 在再结晶温度以上,金属原子有更大的活动能力,会在原变形金属中重新形成新的无畸变等轴晶,并最终取代冷变形组织,此过程称为金属的静态再结晶。
01
02
03
04
05
06
3.合金的塑性变形
(一) 单相固溶体的塑性变形 2 固溶强化 (3)屈服和应变时效 现象:上下屈服点、屈服延伸(吕德斯带扩展)。 预变形和时效的影响:去载后立即加载不出现屈服现象;去载后放置一段时间或200℃加热后再加载出现屈服。这种现象叫做应变时效。 原因:柯氏气团的存在、破坏和重新形成。
在孪生变形时,所有平行于孪生面的原子平面都朝着一个方向移动。每一晶面移动距离的大小与它距孪生面的距离成正比。每一晶面与相邻晶面的相对移动恒等于点阵常数的若干分之一。
01
晶体以何种方式变形,取决于那张变形需要的切应力低。
02
常温下滑移切应力低于孪生,很低温度下,孪生低于滑移。
03
变形速度的增加可促使晶体的孪生化,如高速冲击。
热轧和热挤时,动、静态回复和再结晶的示意图。
图4-10 动、静回复和再结晶示意
热塑性变形机理
第二节金属热态下的塑性变形 2.热塑性变形的机理 变形机理主要有:晶内滑移、晶内孪生、晶界滑移和扩散蠕变。 一般来说,晶内滑移是最主要和常见的;孪生多在高温变形时发生,但对刘芳晶系金属,这种机理起重要作用。晶界滑移和扩散蠕变只在高温变形时才发挥作用。 (1)晶内滑移 热变形的主要机理仍然是晶内滑移。高温时原子间距加大,热振动和扩散速度增加,位错滑移、攀移、交滑移及节点脱锚比低温容易;滑移系增多,滑移灵便性提高,各晶粒之间变形更加协调;晶界对位错运动阻碍作用减弱。
塑性变形物理本质
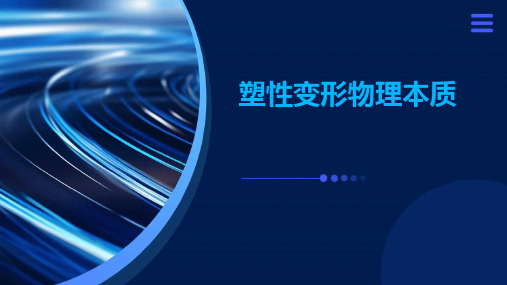
热效应与温度效应
总结词
热效应与温度效应是塑性变形过程中的两个重要物理 现象,它们对材料的变形行为和性能有显著影响。
详细描述
热效应是指在塑性变形过程中,由于机械功转化为热能 ,导致材料温度升高的现象。温度效应是指由于温度的 变化对材料的力学性能和变形行为的影响。在高温下, 材料的屈服极限和强度极限通常会降低,而塑性和韧性 则会增加。这主要是由于高温下原子活动能力增强,扩 散速度加快,促进了动态回复和再结晶过程。同时,温 度变化还会影响材料的热膨胀和热传导性能,进一步影 响材料的变形行为和性能。
作用。
在变形过程中,原子或分子的扩 散可以促进位错的运动和攀移,
从而影响塑性变形的行为。
扩散还可以导致晶体内部显微组 织的演变,如动态再结晶和晶粒 长大等,这些过程对塑性变形具
有重要影响。
微观结构的演变
塑性变形过程中,微观结构会发生变化,如晶粒尺寸、晶界形态和位错密度等。
这些微观结构的变化会影响材料的力学性能和塑性变形行为。
03
可以通过热处理、机械加工或振动等方法消除或减小残余应力
。
微观结构的损伤与演化
微观结构损伤的表现形式
塑性变形过程中,材料的微观结构会发生损伤,表现为晶 粒的变形、位错的增殖和缠结、相变以及新相的形成等。
微观结构演化规律
随着塑性变形的进行,微观结构会不断演化,材料的物理 和化学性质也会发生变化。
微观结构损伤与性能关系
加工硬化与软化
总结词
加工硬化与软化是塑性变形过程中的一对重要物理现象,它们共同决定了材料的变形行 为和最终性能。
详细描述
加工硬化是指随着塑性变形的增加,材料的屈服极限和强度极限逐渐提高,即材料逐渐 变硬、变强。这主要是由于位错密度的增加和晶界的强化作用。软化则是指材料在变形 过程中发生结构变化,导致屈服极限和强度极限降低的现象。它通常发生在高温或长时
金属的塑性变形

五、金属变形程度
常用锻造比表示 Y=F0/F F0表示变形前面积 F表示变形后面积
钢锭Y=2-3 合金钢Y=3-4 高速钢Y=5-12
六、冷、热变形比较
热变形特点:
(1)均匀、细化晶粒 (2)消除加工硬化
(3)高温、塑性好 (4)氧化严重
(5)精度差
(6)设备贵,维修费高
冷变形特点:
(1)不加热
(2)精度、表面质量好
单晶体的滑移
多晶体
二、冷变形后的金属组织与性能 塑Байду номын сангаас变形后:
(1)产生纤维组织,引起各向异性 (2)晶格扭曲 (3)晶粒间产生碎晶 使金属的强度、硬度增加,塑性、韧性 下降,即加工硬化。增加滑移阻力,使金 属形变强化
1.纤维组织 2.加工硬化 3.残余内应力
2.加工硬化(形变硬化、冷作硬化)
(3)硬度、强度高 (4)材料有方向性
(5)设备贵,存在残余应力,易产生裂纹。
§1-2 锻前加热与锻后冷却
一、锻造前加热目的及方法
目的: 提高金属塑性,降低变形抗力.易于锻造成形 并获得好的锻后组织.
按加热热源不同可分为:
1.火焰加热,燃料来源方便,炉子修造简单,加热费 用低适应范围广。用于各种大、中、小型坯料的加热。 劳动条件差,加热速度慢,加热质量难于控制。
§1-1 金属的塑性变形
压力加工:在外力作用下,使金属产生塑性变形,获得一定几 何形状、尺寸和力学性能毛坯,原材料或零件的加工方法。压 力加工有自由锻、模锻、板料冲压、轧制、挤压、拉拔等。
一、塑性变形实质 1、单晶体塑性变形 (1)当无外力,晶格正常排列。 (2)外力作用使原子离开平衡位置,晶格变形。 (3)当剪应力足够大,沿晶面移动一个或几个原子距离。 2、多晶体塑性变形 多晶体是多个位向不同变形总和。特点: (1)变形过程复杂。 (2)变形抗力比单晶体大的多。
- 1、下载文档前请自行甄别文档内容的完整性,平台不提供额外的编辑、内容补充、找答案等附加服务。
- 2、"仅部分预览"的文档,不可在线预览部分如存在完整性等问题,可反馈申请退款(可完整预览的文档不适用该条件!)。
- 3、如文档侵犯您的权益,请联系客服反馈,我们会尽快为您处理(人工客服工作时间:9:00-18:30)。
4 固态塑性变形物理本质材料经过加工成形使其具有需要的形状和性能,才体现出它的价值。
材料加工的目的就是两个:一是改变材料的形状,另一个是改善其性能。
塑性变形是既改变材料的形状,又改变材料的组织结构及相应性能的有效方法。
通过塑性变形可以有效地改变材料的性能,材料的性能又直接影响到工艺的进行。
金属材料的性能(包括使用性能和深加工性能)在使用条件一定时,是决定于成分和组织结构的。
在材料的化学成分一定的情况下,其组织结构是由加工工艺决定的,既通过冷、热加工、热处理和形变热处理可以在很大范围内改变金属材料的组织结构,从而改变材料的性能。
我们掌握了形变、相变、形变和相变相结合的过程中金属材料组织结构的变化规律,就可以利用这些规律,设计和优化加工工艺来获得满足性能要求所需要的组织结构。
有时为了充分发挥冷、热加工、热处理和形变热处理改变金属材料的组织结构的作用,也经常适当地调整化学成分,从而获得更好的效果。
这些知识是制定各种金属材料生产工艺的理论依据,为了达到有效的控制材料性能目的,我们首先要认识塑性加工过程中材料的组织及性能变化。
4.1 固态塑性变形机理材料塑性变形包括晶内变形和晶间变形。
通过各种位错运动而实现的晶内一部分相对于另一部分的剪切运动,这就是晶内变形。
剪切运动有不同的机理,其中最基本的形式是:滑移、孪生、形变带和扭折带。
在r T T 5.0>(r T 熔化温度)时,可能出现晶间变形。
当变形温度比晶体熔点低很多时,起控制作用的变形机理是滑移和孪生。
在高温塑性变形时,扩散机理起重要作用。
在金属和合金的塑性变形过程中,常常同时有几种机理起作用。
各种机理作用的情况受许多因素影响,例如:晶体结构、化学成分、相状态等材料的内在因素,及变形温度、变形速度、应力状态等外部条件的影响。
因此要研究和控制材料的变形过程,掌握基本的塑性变形机理很有必要。
4.1.1 滑移(1)点阵阻力晶内变形是晶体的一部分相对于另一部分的剪切变形,都是通过位错运动来实现的,所以研究基本的塑性变形机理就应研究相应的各种位错运动形式。
滑移是重要的切变机理之一。
虽说位错的滑移运动是很容易的,但是,它也必须至少克服点阵阻力对它的阻碍才能运动。
所谓点阵阻力也就是派一纳力。
当位错从一个低能的稳定位置过渡到另一个低能的稳定位置,必须越过一个能量最大值的位置,就需要对位错施加足够的力以供克服这一能垒所需要的能量,这个能垒就称为派尔斯垒,克服这个能垒所需要的力就是派一纳力。
派尔斯等作者,在经典的弹性介质假设和滑移面上原子的相互作用为原子相对位移的正弦函数假设的基础上,求出了单位长度位错的激活能△W (即派尔斯垒)和其临界切应力(派一纳力)p τ,按指数规律随面间距 a 和柏氏矢量 b 的比值a /b 而变化。
)/2e x p (2kb k Gb ππϖ-≈∆ (4-1) p τ≈)/2exp(2kb k G π- (4-2)上两式中,螺位错K=1,刃位错K=4-ν。
派一纳模型所给出的解仅在定性上是正确的。
p τ比理论切屈服应力m τ=π2G 小许多倍。
柏氏矢量b 值愈小,滑够面面间距a 愈大,则临界切应力p τ就愈小。
当a /b 稍有增加就对p τ产生强烈的影响。
因此,处于面间距最大的密排面上的小柏氏矢量的位借,其活动性最大,所以密排面就是易滑移面。
但要注意,派一纳力还和原子键类型及位错宽度有关,在此就不详细论述了。
(2) 滑移系统因为面间距a 越大、柏氏矢量越小时派一纳力越小。
因此,单晶体和多晶体中滑移变形都是沿着密排面和密排方向进行的。
这些密排面和密排方向就是滑移面和滑移方向。
滑移面和位于其上的滑移方向就构成了滑移系统。
面心立方晶体的滑移变形是沿着密排的八面体平面{111}上的密排方向<110>进行的。
四个取向不同的{111}平面中,每个平面上有3个完全位错的柏氏矢量a ﹤l10﹥/2的方向<110>,所以,可能的滑移系统为12。
见图4-1。
体心立方晶体的密排面是{110},滑移总是沿着密排方向<111>。
也观察到在{112}和{123}上发生滑移变形,但是滑移方向是衡定的,还是<111>方向。
这样,体心立方金属共有四十八个滑移系统,如图4-2。
图4-1 面心立方晶体的<110>{111} 图4-2 体心立方晶体中通过[111]的12个滑移系 方向的12个滑移面 滑移系的多少是影响金属塑性变形好坏的重要因素之一。
密排六方金属的滑移系统少,只有3个,因此,一般说来,它们的塑性低。
但是不能说具有48个滑移系统的体心立方金属的塑性一定比面心立方金属好,除了滑移系统多少外,还有夹杂对变形的影响、加工硬化的影响、屈服强度和断裂强度的高低等。
即使从滑移系统看,即使体心立方金属具有48个潜在的滑移系统,在实际的变形条件下,并不等于这么多滑移系统都同时动作。
4.1.2 孪晶孪晶也是一种常见的变形形式。
通过变形形成的孪晶称为形变孪晶或机械孪晶。
产生孪晶的过程称为孪生。
孪生是塑性变形的基本机理之一。
孪生是晶体的一部分相对于另一部分沿着一定的晶体学平面和方向产生的切变,那样的晶面就是孪生面,那样的晶向就是孪生方向。
但是,它和沿着滑移面上的滑移方向产生的相对切变不同,有它自己的特点。
由图4-3可见,孪生要改变晶体的取向。
从孪生后孪晶中原子排列情况可以看出,晶体切变后结构没有变化,但是取向发生了变化。
同时,由这个孪生过程可以看到孪生这种晶体的相对切变是沿孪生面逐层连续依次进行的,而不像滑移那样集中在一些滑移面上进行,且滑移时晶体取向不变。
图4-3 面心立方晶体的孪生过程●—切变前原子的位置○—切变后原子的位置在一般情况下,孪生比滑移困难一些所以变形时,首先发生滑移,当切应力升高到一定数值时,才出现孪生。
但像密排六方金属,由于滑够系统少,各滑移系相对于外力的取向都不利时,也可能在形变一开始就形成孪晶。
4.1.3 扩散塑性变形机理当材料在高温塑性变形时,扩散就起着重要的作用。
扩散作用是双重的。
一方面,它对剪切塑性变形机理可以有很大影响;另一方面扩散可以独立产生塑性流动。
扩散塑性变形机理包括:扩散-位错机理;溶质原子定向溶解机理;定向空位流机理。
扩散-位错机理:当温度较高具有扩散条件时,扩散过程从几个方面影响位错运动。
扩散对刃位错的攀移和螺位错的割阶运动产生影响。
特别是扩散对刃位错攀移速度的影响,在变形温度超过T5.0,变形物体承受中等或较高应力水平时,是扩散-位错机理控制着蠕r变变形过程的机理,也正是扩散-位错机理的速度控制着蠕变的速度。
有人也称为位错蠕变机理。
蠕变是弹性变形部分地转变为塑性变形的过程,也就是在应力恒定时,随着时间增长总变形量(弹性变形与塑性变形之和)增加的过程。
在蠕变过称中,蠕变速率不断增加,很快导致材料的最终断裂。
材料蠕变性能的变化反映了应变硬化和软化之间的相互作用的不断变化。
扩散对溶质气团对位错运动的限制作用,随着温度的变化而不同。
一般室温下,溶质原子的扩散速度很低,位错运动速度受扩散速度制约,位错被气团锚住了。
在大应力下出现了屈服效应现象。
温度较高,中等扩散速度下,位错不能摆脱气团包围,就出现了动态形变时效,发生蓝脆。
随着温度的升高,扩散可以减轻溶质气团对位错运动的限制作用。
气团的可动性增加了,材料的塑性得到改善。
溶质原子定向溶解机理:晶体没有受到力作用时,溶质原子在晶体中的分布是随机的,无序的。
如碳原子在а-F e铁中,加上弹性应力 (低于瞬时屈服应力的载荷)时,碳原子在棱边中点随机均匀分布的情况就破坏了,通过扩散,优先聚集在受拉的棱边,在晶体点阵的不同方向上产生了溶解碳原子能力的差别,称之为定向溶解。
这种择优分布的固溶体不可避免地伴随着晶体点阵和整个试样的变形,也就是产生了所谓的定向塑性变形。
应力松弛和弹性后效现象就是这种机理作用的结果。
在应力作用下,溶质原子产生定向溶解;去掉应力后,定向溶解的状态又要消失。
这种扩散引起的原子流动是可逆的。
定向空位流机理则是由扩散引起的不可逆的塑性流动机理。
除以上机理外,还有另一类变形机理,晶间滑动机理。
晶间滑动机理是综合的变形机理,它不是和晶内滑移、扩散塑性机理无关的。
它们之间互相协调。
因为,即使考虑在两个晶粒最简单的情况下,由于晶界一般说来不是平坦的平面,两晶粒沿晶界产生相对切变时,就必须拌随其他机理来协调。
对超塑性变形,大家的观点认为是晶间滑动机理。
4.2材料的屈服强度材料力学性能的屈服强度(广义讲流变应力)是材料各种性能中最重要的性能之一。
从使用金属材料的角度来看,大部分的工程构件和机器零件在服役过程中都可见许多塑性变形产生。
故屈服强度为其上限应力。
但从压力加工的角度来讲,要改变金属的形状和尺寸,使之成为性能和规格都符和需要的材料,必要的基本条件就是金属发生塑性变形,要在外力作用下屈服,要求外加应力至少要达到屈服强度。
所以它又是金属塑性加工时的下限力。
材料的屈服强度是指材料抵抗塑性变形的抗力。
定量地说,屈服强度是指材料发生塑性变形时的临界应力。
4.2.1理论屈服强度的估计位错理论出现之前,经典塑性变形理论认为,塑性变形的主要方式是:滑移是一部分晶体在滑移面上,沿着滑移方向,相对于另一部分晶体的刚性整体式地切变。
按照这个理论可以估计出纯金属的理论屈服强度。
金属的理论屈服强度来源于金属的原子间的结合力,它是金属原子间结合力大小的反映。
从金属的原子间结合力出发,推导出理论切屈服强度的τm≈G/2π的数值。
4.2.2 实际晶体屈服强度的构成推导出来的理论切屈服强度比实测数值高1000—10000倍,证明实际晶体的滑移过程不是刚性整体的移动,人们设想滑移是逐步进行的过程。
直到位错的存在最终得到证明,人们认识到,正因为实际晶体中存在着各种晶体缺陷,位错很容易运动,因而不能充分发挥原子间的结合力的作用,所以金属(特别是纯金属单晶体)实际屈服强度远低于理论值的。
实际晶体的屈服强度取决于什么呢?我们从各种塑性变形机理的分析中将看到,金属塑性变形的实质就是位错的运动(或者更全面严格地说就是晶体的缺陷运动,但位错运动是基本的,主要的)。
因此金属的实际屈服强度,即塑性变形实际所需要的临界力,就是产生一定切变量的位错运动所需要的应力。
4.2.2.1开动位错源所必须克服的阻力实际的金属晶体中存在大量的位错,就是经过充分退火的晶体中,位错也不会消失,金属塑性变形,要位错运动,首先就要求位错源工作,克服的位错源阻力为:τc =L Gb(4-3)式中 G —剪切模量;b —位错柏氏矢量;L —位错线长度。
这种抑制住位错源开动的阻力,也称为源硬化。
4.2.2.2点阵阻力位错在晶体点阵中从一个平衡位置移动到另一个平衡位置时,必须克服平衡位置之间的位垒ΔW ,为此所必须的应力就是点阵阻力或称派-纳力。