Moldex3D热浇道阀针速度控制仿真
Moldex3D软件

Moldex3D软件简介及其在模拟注塑中的应用Moldex3D是一款专业的注塑模拟软件,它通过数值计算和仿真技术,模拟出注塑过程中的流变性能、热力学性能和变形性能等,能够帮助企业更好地研发新产品、优化设计和生产工艺。
注塑模拟软件的作用在于减少实际操作过程中的试错成本,节省时间和成本。
因此,在制造业中应用广泛,尤其是在汽车、家电、电子等行业中得到了广泛的应用,下面将详细介绍的应用及其优势。
1.模拟出注塑过程中的流变性能在注塑过程中,材料的流变性能是非常关键的。
可以模拟出材料在注塑过程中的流动状态,以及热传递、凝固等关键过程,从而帮助企业更准确地确定注塑工艺参数,确保产品的设计成型度和力学性能达标。
2.优化模具设计可以对模具结构进行优化设计,通过模拟仿真,可以检测出模具结构的缺陷,并采取相应的优化措施。
同时,还可以预测产品的变形情况,进一步改进模具设计,从而提高整个生产流程的质量和效率。
3.节约成本通过的模拟仿真,企业可以避免实际操作中的试错成本,及时发现问题并进行改进,从而减少生产成本。
同时,还可以预测产品的缺陷,帮助企业尽早解决问题,避免后期返工和投诉。
4.提高产品质量通过的模拟仿真,企业可以在最短的时间内找到最佳的工艺参数和最适合的模具设计,确保产品的成型度和力学性能达到标准要求,从而提高产品质量和市场竞争力。
5.智能化生产可以与其他自动化设备相结合,实现生产过程的自动化和智能化。
通过与MES系统(制造执行系统)相集成,可以实现产量统计、在线监测等功能,从而提高生产效率和质量。
总的来说,可以模拟出产品的相关性能,包括材料流动、热传递、凝固变形等方面,对企业研发新产品、设计模具和生产工艺等都有很好的帮助。
其主要优势在于可以节约成本、提高产品质量和智能化生产,为制造业提供更有效的解决方案,帮助企业在市场中取得更大的竞争优势。
Moldex3D模流分析之热浇道模组准备分析

准备分析(Prepare Analysis)要使用进阶热浇道分析的功能,需要额外进阶热浇道分析模块的授权。
除了需要额外的授权之外,建立新项目、新组别、汇入网格档案与材料设定等流程与射出成型模拟完全相同。
应用项目(Application)显示功能1. 加工设置(Process Setting)进阶热浇道分析在加工精灵的设定中,冷却设定是唯一不同之处。
关于进阶热浇道分析,需设定加热线圈的加热方式及指定热浇道金属的材料性质。
在下图中,加热棒ID与感测节点ID可使用显示/隐藏功能(Show/Hide)显示与隐藏。
在热浇道系统中设定不同加热线圈的功率数值时,可以依显示的ID编号进行辨别。
组件ID此外,加热系统控制方式建议使用瞬时(Transient) 设定模式。
加热线圈可由温度或功率进行控制。
冷却设定加热棒设定提示:如果选择依据温度为加热方式,加热线圈的设定会以温度(°C)作为设定的条件。
同理,如果选择依据功率,加热线圈设定会以功率(W或W/cm2)作为设定的条件。
2. 进阶设定(Advanced Setting)模具嵌件与热浇道金属的温度设定能在模具嵌件初始温度(mold insert initial temperature)的设定页面中进行设定。
模具嵌入件初始温度设定关于热浇道金属,能在模具材料(mold metal material)的页面中设定属性,且需要的属性有密度、比热、热导系数、弹性模数、浦松比(Poisson ration)及线性热膨胀系数(CLTE)。
模具金属材料设定3. 计算参数(Computation Parameter)在下图中,计算参数的冷却(Cool) 页面中需选择进阶热浇道的选项,以执行进阶热浇道分析。
该选项若没勾选,则热浇道中的熔胶温度假设为不随时间变化。
如果没有组件被设定为热浇道金属,进阶热浇道的选项将会呈现灰色锁住的状态。
除瞬时与稳态冷却分析选项的默认值之外,用户也可设定全瞬时冷却分析的参数,以取得更精确的分析结果。
Moldex3D模流分析之仿真可制造性设计

仿真可制造性设计(Simulation DFM )仿真可制造性设计(sDFM)是一种辅助制造的功能。
它为产品设计提供相关的模具分析结果,使设计者可以减少手动验证每个模拟结果状态的时间。
sDFM 的过程分为三个阶段:sDFM Setting、sDFM Viewer 和sDFM Report。
•sDFM Setting允许使用者自定义验证标准格式。
验证标准包括验证项目、相关设计标准和制造中的关键因素。
用户可以设定标准以从提供的信息中查看分析项目。
•sDFM Viewer允许用户查看每个分析项目的验证状态。
用户可以右键单击SYNC UI树状菜单上的项目管理器(Project Manager)来操作sDFM Viewer,它使用自定义的验证标准显示自定义选择的分析项目列表和验证状态。
•sDFM Report功能在PowerPoint 中提供完整的标准内容和分析项目结果。
用户可以透过报告中的信息查看整个设计过程。
1. sDFM设定(Simulation DFM Setting)•右键单击项目管理员(Project Manager)并在目录中选择Simulation DFM Setting。
•选择Simulation DFM Setting设定后,开启Simulation DFM Setting模板列,可操作新增/编辑/删除及汇入/汇出检验模板。
•用户可以在Simulation DFM Setting 中选择验证项目。
在每个子项目下,必须的分析项目(带有注释必须)不能取消勾选。
例如:流动波前时间(Melt Front Time)是流动平衡(Filling Balance)子项中的必填项。
•单击分析项目,在规则设定(Rule Setting)栏将显示当前的验证标准,包括公式和相关参数。
•若分析项目需要手动检查,将会弹出提示讯息并锁定规则设定的字段。
•单击下拉式选单并选择结果类型。
若结果类型是自定义值(Custom Value),使用者可以在这种类型模式下设定值。
Moldex3D模流分析之Foam Injection Molding

为什么使用发泡射出成型模拟?
发泡射出成型如微细发泡及化学发泡剂(CBA)制程,适用于具有复杂几何和良好尺寸稳定性产品的大量生产,被广泛用于汽车、电子产品、建筑、户外产品等多种应用领域。
在发泡制程中的超临界流体(SCF)通常是使用N2或CO2两种气体与聚合物熔体混合在一起,产生单相聚合物/气体溶质,注入到模穴内,最后在产品中形成气泡。
而在CBA制程中,化学发泡剂与塑料颗粒混合在一起作为着色剂或添加剂使用,化学反应在料筒中完成,气体溶解在熔胶中,在充填阶段时气泡开始成长,同时在产品中开始释放,形成压力。
微细发泡成型原理
此项技术的好处是能有较低的射出压力、较低的温度、缩短周期时间、减少能源和材料的使用。
尽管以上优点,加入超临界流体会增加流动行为,材料形态及产品表面质量的复杂性,也因而局限了此制程的发展与接受度。
挑战
•气泡形成的数量、大小与分布都取决于成型条件的设定,直接影响产品的质量
•评估缝合线和包封问题,优化浇口数目和位置
•产品的几何设计有别于传统射出制程,因此设计经验无法直接套用
•潜在的表面质量问题
Moldex3D解决方案
•在熔胶注入到模穴后的充填阶段就开始模拟气泡成核与气泡成长
•计算气泡大小、数目、密度分布、体积收缩等结果,评估产品减重比率
•预测熔胶流动与气泡发展间的相互作用
•预测气泡结构对产品翘曲的影响,达到产品轻量化的目标
传统成型产品和发泡成型产品的尺寸稳定性与变形预测的比较应用产业
•电子
•汽车
•医疗
•消费性产品。
Moldex3D分析设定操作流程

Moldex3D分析设定操作流程一.新建档案及设置项目名称及贮存位置等操作步骤(页面设完后下一步直到完成)设定制程(利用传统射出成型)设定分析引擎(此项目选用3D实体分析引擎)其它的大体设定大体信息查看,完成分析项目成立新组别导入新的网格查看模具尺寸,模穴体积(cc数量,后续很常常利用的一项指标)等信息设置新的材质(假设是下拉菜单已有所需的材料能够选用,没有需新增)第一项紫色菜单是已加入的项目的材料第二项绿色菜单是用户利用过的材料第三项红色菜单是软件收积的材料库在材料库中找到所需材料右键加入项目此项目选用HIPS-POLYREXPH-888H查看材料的信息黏度MFI值(流动指数)-值越小越难流动(需在相同环境测试的值才能比较)比容Tg(玻璃转化温度点,塑胶在那个温度的时候会慢慢变软) 压力越大,比容越小,密度越大比热(塑胶吸热有速度) 鼠标停留在座标上,下面会显现相对应的温度及比热值热传导系数(塑胶的温度传递) 鼠标停留在座标上,下面会显现相对应的温度及热传导系数值了解机械性质材料内容非流动温度(也叫固化温度,塑胶冷却到此温度会固化) 密度查看完后关闭,下一步成立新的成型条件暂不了解模具的机台及成型压力等因素时选用CAE分析设定界面明白模具的机台可选射出机台设定界面(由多段设定/由射出时刻),本次项目选第二项射出机台设定界面(由多段设定)射出机台设定:假设是下拉菜单中已有所需机台,直接选用;假设是没有那么新增选择所需的机台型号如HC-600-S(S代表此型号机台的螺杆大小,S最小,M中等,L最大) 检视查看螺杆大小及机台压力螺杆越小,机台的压力越大,射出的流率(CC量)越小完成后确认加入自定资料库充填保压的设定流率的多段设定设为三段,第一段充填流道,此刻压力降小不让它速度过快产生高热第二段是产品的充填进程,能够让射出速度加速第三段是产品快充满时可降慢速度让压力减小第二段螺杆行程=产品CC量/(产品CC量+流道CC量)X螺杆总行程第三段螺杆行程=1/10 螺杆总行程设完后观看行程时刻合理性再确认射出压力多段设定射出压力操纵在机台的八成压力之内,不让机台进行极限运作VP切换(V是流率,充填P是压力,保压)VP切换指的是充填压力切换到保压压力此项暂选由充填体积的98%切换成保压压力保压时刻(分析时暂不确信保压时刻可设3秒,依照产品依体会判别)保压压力为参照充填终止压力啤机注塑时会有一个充填惯性,产品充填终止后假设是继续有持续的压力进行保压,产品可能会被显现毛边,变形等现象,因此充填终止切换到保压压力时应减小压力(充填压力七至八成),幸免过保压塑胶温度及模具温度台照材料内容里面冷却设定空气温度为啤机车间的室温,开模时刻(充填完成冷却时刻+开模+滑块及顶出等机械动作+合模的总时刻,模具开模后散发的热量会更多) 冷却时刻进行估算设各项指标进行估算密度,比热,热传导系数可在材料里面找出如比热光标停留在顶出温度上,下面会显示相应的值冷却进阶设定水路温度设成与模具温度一样选择相应的模具材质(此项目选项718H)了解和查对一些大体信息新建计算参数设定固化温度(非流动温度,在材料内容里面,HIPS非流动温度为117度)进行多个文件处置时可更改工作数(工作数不能超过授权数,也不能超过CPU数,如此项目不能超过2) 确认内容完成右键设定分析顺序选择完整分析-CFPCW(冷却,充填,保压,冷却,翘曲) ,贮存,开始分析有多个项目需一路分析时可用批次执行,选择所要分析的项目加入。
Moldex3D模流分析之热循环试验模拟预测热疲劳

简介温度循环试验(Thermal Cycling tests, TCT) 是一种于IC产业可靠度测试当中的重要测试项目之一。
用以测试产品于反复升降的环境温度下,是否能够在设计的周期内维持其质量。
TCT试验内容是将封装好的产品放入控温环境中,以每分钟5至15度的温度变化率使产品反复承受一连串的高低温变化。
最常见的破坏模式来自于产品内部组件因为热膨胀系数差异(CTE differences) 较大而反复受到产品内部组件交界面热应力与降温周期中累积的残余应力(residual stress)影响,最终造成组件间脱层、组件断裂或是最常见的锡裂(Solder crack)。
实务上,从组件产品设计、开模、封装到实际进行温度循环试验往往需要耗费大量的时间、人力以及物力。
因此,如何以计算机仿真温度循环试验,并将模拟中预测之热循环次数作为设计变更、设计优化的参考依据,进而加速整体流程及节省开发成本,就成为一个重要的议题。
热疲劳模型为了模拟热疲劳破坏(Thermal fatigue)现象,有许多研究提出热疲劳模型(Thermal fatigue model),可依照模型采用的物理量区分为三大类:应力(Stress base)、应变(Strain base) 以及能量(Energy base) 的模型。
其中又以基于应变的Coffin-Manson Model 最为广泛的被使用于预测较低循环周期的疲劳破坏(Wang et al 2017)。
Coffin-Manson Model 预测的循环周期模型为:此模型以材料延性疲劳参数(Fatigue ductility coefficient)、塑性应变量值(amplitude of plastic strain)与延性疲劳指数(Fatigue ductility exponent)以预测疲劳周期数。
延性疲劳指数可经由Modified Coffin-Manson Model:塑性应变模型热疲劳模型参数除了可由查表或实验取得的材料延性疲劳参数;以及经由欲模拟的热循环试验参数可得之周期平均温度与周期频率。
Moldex3D热流道阀浇口设定功能

7
True 3D CAE for Injection Molding
Shell設定
接著,在熱流道部分,點選欲設為閥澆口的點。點選MDXAttributeSetting 性設定界面出現於工作區視窗。 功能鍵,屬
點擊“Point Attribute” 下拉式表單,然後,請選按“Valve Gate Control Point”。 相同方法 定義其他點屬性為閥澆口。
改變閥式澆口的設定
12
True 3D CAE for Injection Molding
Solid設定
現在閥式澆口的屬性已改變成閥式澆口-1(Valve Gate 1),如下圖所示。
改變閥式澆口的屬性
使用者可以利用相同的方法設定閥式澆口2的實體網格,如下圖所示。
13
True 3D CAE for Injection Molding
14
True 3D CAE for Injection Molding
澆口閥設定-時間控制
時間點控制:指定改變澆口閥狀態的時間點。在整個週期,澆口閥的狀態可改變數次以配 合每個澆口的運用考量。 如,設定澆口閥-1從充填開始時就開啟,澆口閥-2在充填時間0.08sec開啟,其設定如圖 所示:
VG1
VG2
步驟4. 執行薄殼-充填(Shell-Flow)分析並檢查其結果,如下圖所示。很明顯地,當設定較 高的熔膠溫度,熔膠溫度較高所以較易充填模穴。因此,若模具為具多澆口和熱流道的系 統,利用不同的熔膠溫度控制,熔膠的充填行為將會大大不同。如圖所示。
不同的熔膠溫度設定:左邊控制器設為270 oC,右邊則為230oC
3
True 3D CAE for Injection Molding
Moldex3D分析设定操作技巧经过流程

Moldex3D 分析设定操作流程.巴•圜0如事 Q ・[[■!> 小@写目目|9国・・ §窟充日・俣 刚]厘❷秒"WA « V • A X M r a a "/回且■— 局面二盘94 Q ■ « ・ 自 81.新建档案及设置项目名称及储存位置等操作步骤(页面设完后下一步直到完成)■ =1 t| :| J琥 5 : iQliienW/Q^eifin 项目建立将园[miFro jecT2Da »0.,, V||案他&折x64RQ =篇6/<&-©中的-今£Moldex3D/€Desiqn 1s 目建立此精灵府至会常次唐建工新以口 项目宅费.HDHP 峋 F 疝。
口g 口7项口慢量.E..deyib 用『rtri 忖口他耳针汉E 国在目录铅有工作目录i 岫 唐口融仃口的机密做■step^ 期出世翘SKK 目一 力再击也比以WF 禹E ..漫隆型眄E ,,・下一沙迪,K眼前值?曲考 N 括八in”后卜弧 向&诩,4临门”小H伸ifj遇因心」工具口卷题」的猊明式画•■曲■■「34%利日,叱・寻〉海如甘后如・♦◎遂修H QH I曰_] •◎牙Ia s 8 a i9Ila."QCC工J基切氏小甑新栩t.1/三此灯四井后为自四周巨【玩虻陈口,船』加L.D□ IWU时在MHE】-麻.同日4113Hoi怨行楙*设定制程(使用传统射出成型)■ ahMiUM/M修与yr >M 网> 1JLA」匕一上百电1事□・际将•也=H C3占二与回1吨」■ ■四•』占■■■ •■•・旧旧n2] T占比扎口建3方值二司中后比更[映白算U出Ki &R白石可里归强强"中和号曲<> 下一例tii 2itcp d of b : tlBJU B F0)e£t 2fll>«IUiS2 r J■现曼与HFP3H后授率•咖丁库*以STF总手中中QM ffiV Fl制千十三才处回用黛此一后海好瞄便用『HF弓但笛已曾飞照畸布式,:邛于海海中jtftEfeB:空月I- mlL£ha顺耳点AJtfflT 砌博强奸桥力事工霸方花限般口恨+■idxmw*口y *里璃£曲网芈府但■小有h-n*同用置IMAGAIaaalQIsl*-eQI&l/#/*唐I〉舒|・■设定分析引擎(此项目选用3D实体分析引擎)其它的基本设定基本信息查看,完成*分析项目建立新组别0肛n股苛小*导入新的网格查看模具尺寸,模穴体积(cc 数量,后续很常用的一项指标)等信息」■ 密©为Ji 。
Moldex3D模流分析之Moldex3D仿真模面及实体水路分析

Moldex3D仿真模面加热温度预测更真实在射出成型制程中,高模温对提升产品表面质量有很大的帮助。
而感应加热为最常用的模面加热技术之一。
Moldex3D支持模面加热模拟,操作者可依需求分别选择加热公模或母模面,也可选择二者同时加热。
当模拟过程考虑模面加热,将可使分析结果更贴近实务情形。
以下为Moldex3D模拟模面加热之步骤。
步骤1:开启一个已建好实体网格的模型,根据需求,用户可选择加热公模或母模,或二者皆为加热区域。
在本案例中,选择公模侧为加热面。
如下图,虚线内为预热区域。
步骤2:生成感应加热(或其他加热方式)的区域实体网格(建议层数为5层以上)。
将此网格之属性设定为嵌件(mold insert)。
步骤3:在加工精灵中设定成型参数时,于冷却设定中点击模具嵌件初始温度。
步骤4:输入每一射出循环之模具初始温度。
务必在设定类型中选择感应加热。
如此一来,所设定的温度才会是每一射出循环之初始温度,而非第一射之初始温度。
设定完成后点击确定。
步骤5:在分析顺序设定中,务必选择瞬时分析(Ct);若选择周期平均冷却分析(C),则设定之嵌件初始温度将不会有作用。
完成后,点击开始分析。
分析完成后,在冷却结果中可观察到靠近公模侧在开始充填时有较高的温度。
Moldex3D 3D实体水路分析新增判断冷却效率指标为了达到较佳的冷却效率,一般希望冷却水路中的冷媒形成紊流,而雷诺数(Reynolds number) 的大小为形成紊流的依据(以圆形水路为例,雷诺数到达4000以上则形成完整的紊流)。
因此,雷诺数可做为判断冷却效率的重要依据。
Moldex3D 支持显示雷诺数在水路中的分布状况,提供使用者一个判断冷却效率的指标。
步骤1:在新项目中汇入一个水路的3D实体网格模型,并输入分析所需材料、成形及计算参数。
注:此例中为了突显雷诺数的效应,系故意在成型参数中将两条水路的设为不同的流率值。
步骤2:在计算参数(Computation Parameter) 中的冷却分析(Cool) 选单中,勾选执行冷却水路分析(Cooling channel analysis by),并选择进行冷却水管网络分析(Run cooling channel network analysis) 以启动进阶冷却水路分析。
用Moldex3D对副仪表盘热流道浇口时序的优化

用Moldex3D对副仪表盘热流道浇口时序的优化翟豪瑞;王小松;熊新;邹伏安;苏朔【摘要】Using Moldex3D mold flow analysis software ,a hot runner timing control valve pouring system of one car auxiliary instrument panel was designed . Optimizing the gate position effectively reduces and eliminates the weld marks of the car sub-instrument dial A/B surface and other parts ,and achieves the effect of spray-free . The test results show that there is no obvious weld mark on the surface of the car dashboard .%运用Moldex3D模流分析软件,设计了某汽车副仪表盘的热流道时序控制阀浇注系统.优化了浇口位置,从而有效地减少和消除了汽车副仪表盘A/B表面及其他部位的熔接痕,达到免喷涂的效果.试模结果表明,汽车仪表盘表面无明显熔接痕.【期刊名称】《现代塑料加工应用》【年(卷),期】2017(029)006【总页数】3页(P54-56)【关键词】熔接痕;Moldex3D软件;热流道;时序控制【作者】翟豪瑞;王小松;熊新;邹伏安;苏朔【作者单位】盐城工学院汽车工程学院 ,江苏盐城 ,224051;苏州洛世奇热流道科技有限公司 ,江苏苏州 ,215100;盐城工学院汽车工程学院 ,江苏盐城 ,224051;盐城工学院汽车工程学院 ,江苏盐城 ,224051;盐城工学院汽车工程学院 ,江苏盐城 ,224051【正文语种】中文由于汽车副仪表盘体积大、结构复杂等因素,采用传统的冷流道浇注系统注塑出来的产品熔接痕较多,严重影响其力学性能和外观质量,无法满足注塑工艺的要求[1]。
基于Moldex3D的微动开关浇口设计优化

设计与分析♦Sheji yu Fenxi基于Mo I dex3D的微动开关浇口设计优化韩国声1,"(1.贵州大学机械工程学院,贵州贵阳550000;2.黔东南民族职业技术学院,贵州凯里556000)摘要:基于Moldex3D模流分析软件,对某种微动开关壳体成型效果进行了仿真预测,并针对成型问题,找出了设计缺陷予以优化。
模具优化后,再次仿真分析确定,通过优化浇口位置及浇口形式,改善了保压效果以及成型材料纤维取问题,件程度降低。
后,件模流分析结果一致,证明Moldex3D模流分析软件实现了对成型过程的精确模拟及预测。
关键词:计算机仿真;模流分析;浇口设计;成型0引言成型工设计的进行塑件的及模具设计,再工模,善设计,过程成大,以优的设计,大大了成型工的。
,于计算机仿真技术的进,问题。
计算机仿真技术通过对成型过程的模,设计预测的成型效果,并确找出的以改善,成优设计,大了件,了件效。
成型的计算机仿真成型软件种,即台湾科盛出品的Moldex3D和美国Autodesk研发的moldflow。
其中,Moldex3D性价比较高,适合中小企业应用。
本文采用Moldex3D模流分析软件对件进行仿真预测分析。
#塑件产品分析本案例的塑件为一种微动开关壳体,选用PA66+GF50材料成型,该塑件结构如图1所示,塑件尺寸为23.8mm X14.2mm X 7.2mm,件平均壁厚为1.12mm,各部分厚均,两长边厚度差异尤明显,一侧厚度为2.35mm,另一侧厚度仅为0.76mm,极易现象。
作为一种开关按键,如过大,会因卡死丧失原功能,因此需严格控件。
图#塑件结构2初步设计方案成型效果及分析2.1初步设计方案成型效果该塑件初步设计方案如图2所示,模具选择一模两腔形式,平衡布置,选直径1.2mm的潜伏式浇口进胶,浇口位置选择件边厚厚一侧。
将设计导入Moldex3D软件进行模流仿真分析,成型条件设定如表1所示。
件分析果如图3所示,件边出现过度翘曲图2塑件初步设计方案表1成型条件设定充填时间/s保压时间/s熔体温度/?模具温度/@冷却时间/s 设定参数0.1133008510变形,较厚一侧最大位移为0.145mm,较薄一侧最大位移为0.138mm,沿位移较少,沿#位移多。
moldex3d所需的工艺参数

一、概述Moldex3D 是一款专业的注塑模流分析软件,可以帮助用户预测和优化注塑模流过程,提高产品质量,减少生产成本。
在使用这款软件进行注塑模流分析时,需要设置一些工艺参数,以确保分析的准确性和有效性。
本文将介绍 moldex3d 所需的工艺参数及其设置方法。
二、注塑机参数1. 射出压力:射出压力是指塑料材料在注塑机中由螺杆推动产生的压力,影响着塑料的射出速率和温度。
在进行模流分析时,需要准确设置射出压力,以保证模流模拟的真实性。
一般来说,根据实际生产中的数据及经验,设置合适的射出压力值。
2. 射出速度:射出速度是指塑料材料在注塑机中射出的速度,对产品的成型和表面质量有重要影响。
在进行模流分析时,需要根据实际情况来设置合适的射出速度,以确保模拟结果的准确性。
三、模具参数1. 冷却时间:冷却时间是指从注塑成型完成到模具完全冷却的时间。
在模流分析中,需要设置合理的冷却时间,以确保在模流模拟中考虑到了塑料充填后的冷却过程,并据此优化冷却系统。
2. 模具温度:模具温度是指模具在注塑过程中的温度,对产品的成型质量有很大影响。
在进行模流分析时,需要准确设置模具温度,以确保模拟结果的准确性。
四、材料参数1. 熔体指数:熔体指数是指树脂在一定温度下的流动性能,不同的熔体指数对产品的成型质量有很大的影响。
在进行模流分析时,需要根据实际情况设置合适的熔体指数值,以确保模拟结果的准确性。
2. 热性能:材料的热性能包括熔体温度、热传导系数等参数,对模流模拟结果的准确性和真实性有很大的影响。
在进行模流分析时,需要准确设置材料的热性能参数。
五、其他参数1. 其他参数:除了上述的参数外,还有很多其他的工艺参数会对模流模拟结果产生影响,比如模具设计、模具结构、射胶系统等方面的参数。
在使用 Moldex3D 进行模流分析时,需要综合考虑这些参数,并根据实际情况进行合理的设置。
六、总结Moldex3D 是一款功能强大的注塑模流分析软件,可以帮助用户准确预测和优化注塑过程,提高产品质量,降低生产成本。
基于Moldex3D 的MIM 注射仿真分析及烧结预报相关参数的计算

基于Moldex3D 的MIM 注射仿真分析及烧结预报相关参数的计算作者:王康来源:《智能制造》 2018年第2期鉴于相关课题MIM 工艺的烧结仿真预报软件开发的需要,本文基于Moldex3D 的PIM 分析模块对烧结标定阶段的两种试件进行注射分析,通过考察“填充- 保压- 冷却”阶段的注射性能以及适用于烧结分析相关参数的计算结果,经过仿真分析发现Moldex3D 计算结果对于后续的烧结仿真预报具有重要指导意义。
一、引言金属粉末注射成形工艺(Metal Powder Injection Molding)简称MIM,适用于制造形状复杂、高精密度和高性能材质的小型机械零件,是利用粉末冶金及塑胶射出成形之独具特色而发展出的一种新工艺。
MIM 工艺数值仿真的研究工作主要涉及到注射、脱脂和烧结三个工序,其中烧结是MIM 的关键工艺之一,因为零件在烧结过程中发生较大的收缩(一般为10% ~ 20%),这直接决定了产品的精度和性能。
针对本公司承担的项目课题“金属粉末注射成型烧结工艺仿真系统开发与试验研究(2016CX001)”中MIM 烧结预测算法的开发需要,鉴于该过程仿真准确性很大程度上受到注射成型质量的影响,其计算的主要初始参数(如烧结初始几何网格、密度分布以及粉末浓度分布等)均可由此得到,因此首先需要评估MIM 注射成型工艺的仿真分析工作,评价其对于烧结算法研究的指导意义。
二、标定模型设计及其注射方案根据试验条件限制和算法研究需要,本课题设计两种试件用于针对烧结过程不同方向的形变特征算法研究的试验标定,分别为数量若干的圆柱(高10mm,直径6mm)和长方体(长60mm,宽10mm,高3mm)标准试件。
注射粉末选择常用的铁镍合金(Fe 粉和Ni 粉混合,二者质量比为2Fe-2Ni),混合粉末的理论密度为7.888g/cm3,其平均粒径分别为Fe 粉5.6μm,Ni 粉2.18μm,装载量体积比为58%。
根据标定试件产品的形状特征,具体注射方案如图1 所示,分别选择针点式和侧边式浇口作为圆柱体和长方体试件的浇口方案。
用Moldex3D对副仪表盘热流道浇口时序的优化

收稿日期:2017-05-11;修改稿收到日期:2017-11-02㊂作者简介:翟豪瑞,讲师,研究方向为汽车零部件开发㊁材料成型及模具集成㊂E -m a i l :182********@163.c o m ㊂基金项目:江苏省六大高峰人才项目(X N Y Q C -005)㊂用M o l d e x 3D 对副仪表盘热流道浇口时序的优化翟豪瑞1 王小松2 熊新1 邹伏安1 苏朔1(1.盐城工学院汽车工程学院,江苏盐城,224051;2.苏州洛世奇热流道科技有限公司,江苏苏州,215100) 摘要:运用M o l d e x 3D 模流分析软件,设计了某汽车副仪表盘的热流道时序控制阀浇注系统㊂优化了浇口位置,从而有效地减少和消除了汽车副仪表盘A /B 表面及其他部位的熔接痕,达到免喷涂的效果㊂试模结果表明,汽车仪表盘表面无明显熔接痕㊂关键词: 熔接痕 M o l d e x 3D 软件 热流道 时序控制D O I :10.3969/j.i s s n .1004-3055.2017.06.015O p t i m i z a t i o no f H o tR u n n e r G a t eT i m eS e qu e n c eo f A u x i l i a r y I n s t r u m e n tP a n e lb y Mo l d e x 3D Z h a i H a o u i 1 W a n g X i a o s o n g 2 X i o n g Xi n 1 Z o u F u a n 1 S u S h u o 1(1.S c h o o lo f A u t o m o t i v e E n g i n e e r i n g ,Y a n c h e n g I n s t i t u t eo fT e c h n o l o g y ,Y a n c h e n g,J i a n g s u ,224051;2.S u z h o u R i c h r a y H o tR u n n e r T e c h n o l o g y L t d ,S u z h o u ,J i a n gs u ,215100)A b s t r a c t :U s i n g M o l d e x 3D m o l df l o w a n a l y s i ss o f t w a r e ,a h o tr u n n e rt i m i n g co n t r o l v a l v e p o u r i n g s y s t e m o fo n e c a ra u x i l i a r y i n s t r u m e n t p a n e l w a sd e s i g n e d .O p t i m i z i n g th e g a t e p o s i t i o ne f f e c t i v e l y r e d u c e sa n de l i m i n a t e st h e w e l d m a r k so f t h ec a rs u b -i n s t r u m e n t d i a lA /Bs u r f a c ea n do t h e r p a r t s ,a n da c h i e v e st h ee f f e c to fs p r a y -f r e e .T h et e s tr e s u l t s s h o w t h a tt h e r ei sn oo b v i o u s w e l d m a r ko nt h es u r f a c eo ft h ec a rd a s h b o a r d .K e y wo r d s :w e l dl i n e ;M o l d e x 3D ;h o tr u n n e r ;s e q u e n t i a lc o n t r o l 由于汽车副仪表盘体积大㊁结构复杂等因素,采用传统的冷流道浇注系统注塑出来的产品熔接痕较多,严重影响其力学性能和外观质量,无法满足注塑工艺的要求[1]㊂时序控制技术应用于热流道浇注系统,使注塑过程中各浇口流出的分支料流逐步推进,实现 动态供料”[2]㊂可较好地解决传统生产存在的模具型腔充填不均衡㊁熔接痕多等缺点,能够有效提高成型产品的表面质量[3]㊂下面采用M o l d e x 3D 模流分析软件,设计了某汽车副仪表盘的热流道时序控制阀浇注系统,并进行了试模试验㊂1 副仪表盘产品介绍副仪表盘外形尺寸为980mm×253mm×325mm ㊂有许多筋条㊁内孔㊁凸台㊁深腔等结构㊂产品壁厚分布在1.417~2.781mm ㊂作为汽车内饰件,该产品的成型表面质量要求高,图1标注的A /B 面需要达到免喷涂的效果,不允许出现明显的熔接痕,不允许进浇,且不能出现肉眼看见的色差㊂此产品采用的注塑原料聚丙烯,为金发公司生产的A B P -2036M ,该材料的塑化温度设定在200~240℃,一般设定为220℃㊂模具温度设定在30~60℃,一般设定为45℃㊂㊃45㊃图1 副仪表盘A/B面2原始方案的模流分析2.1M o l e x3D模流分析步骤将副仪表盘三维模型导入M o l d e x3D R14.0 D e s i g n e r软件进行有限元网格的划分,具体操作步骤为:汇入塑件几何㊁选定浇口位置㊁简单浇口变化㊁流道系统建立㊁汇出网格㊁设定进出水口㊁建立冷却系统㊁建立模座㊂网格划分采用第5等级进行划分,以.m d g格式存档[4]㊂M o l d e x3D R14.0分析软件自动判断出默认的工艺参数,再根据软件默认成型参数和实际经验进行调整㊂2.2 浇注系统的设计采用 热流道+冷流道”的形式进行设计,冷流道浇口采用针阀式点浇口进浇㊂热流道浇口设计为4个,进行时序的控制,冷流道浇口进浇点为7个㊂原始方案浇注系统设计如图2所示㊂图2 原始方案进浇系统热流道浇口进行时序控制首先开启浇口1,其他3个热流道阀浇口的开启型式采用流动波前进行控制,具体设置如图3所示㊂即当塑胶流动到图3选定的3个网格节点编号时,相应的热流道阀浇口将开启㊂图3 热流道浇口时序控制窗口2.3结果分析原始方案需要免喷涂的A /B面有较明显的熔接痕,而且其他部位熔接痕数目较多㊁较长熔接痕分布情况如图4所示,比较明显的熔接痕有4条㊂图4 熔接痕分布情况1号熔接痕在外观表面A/B面上,主要由于浇口3开启时间较早,造成浇口1,2注射出来的塑胶与浇口3注射出来的塑胶流动前沿相遇形成㊂2,3,4号熔接痕是由于制品中存在阻碍塑胶流动的结构,而引起塑胶分开再汇合而形成的,尤其是3号和4号熔接痕处在充填的末端,塑胶温度处在下降的过程中,所以熔接痕非常的明显㊂其他部位的熔接痕主要是由于制品壁厚不均,塑胶流动前沿填充时发生回流与原熔体流动方向发生汇聚所引起的㊂图5为原始方案充填的分析㊂图5 原始方案充填分析从图5的锁模力曲线可以发现当塑胶流动到选定网格节点的波前位置时,浇口1~4热流道浇口将逐一开启,锁模力会有一个下降又突然上升㊂㊃55㊃热流道进浇口的压力曲线,与锁模力曲线具有一一对应关系㊂填充过程塑胶流动受到的阻力随模具结构变化并且随温度下降明显上升,这时候的注塑压力必须足够大才能保证型腔被填满㊂因此这时的锁模力也随之不断上升,直至到达最大锁模力的时间点,这个时间点往往是V/P(速度/压力)切换时刻㊂3时序控制及热流道浇注系统的优化3.1 热流道浇注系统的优化原方案浇注口1~4设计的比较集中㊂1号熔接痕可以采取优化浇口3的开启时间进行消除㊂优化后的浇注系统如图6所示,只是在原方案的基础上改变1号进浇点的位置,其他进浇点不改变㊂图6 优化浇注系统方案3.2 结果分析从图7所示模流分析结果可以看出,汽车副仪表盘的A/B面熔接痕明显消除㊂图7 优化方案熔接痕分布情况锁模力和热流道进浇口的压力曲线,如图8所示㊂由图8观察发现,浇口1~4的开启时间比原方案合理,尤其是浇口2的开启时间明显滞后,这样将会让浇口1充填的塑胶进行充分的流动,而且浇口3和浇口4之间的开启时间符合流道口之间的长度分布,且浇口2~4的开启时间处在充填的中间,不会造成原方案的 头重脚轻”的情况㊂锁模力上升曲线非常的圆滑合理,没有出现图5锁模力曲线后段出现一个小小波浪的现象,说明充填过程非常的顺畅㊂图8 优化方案充填分析4试模验证和总结基于以上的优化分析,合作的企业进行模具的设计和开发,最终进行试模验证,实际生产的注塑产品如图9所示㊂图9 试模验证5 结论a) 基于M o l d e x3D成熟的模流分析软件,进行某汽车副仪表盘浇注系统的优化分析,可以减少不必要的试模修模次数㊂b) 在有限热嘴数量的前提下,时序控制热流道的使用基本能够消除较明显的熔接痕缺陷,有效地改善该产品的表面质量㊂c) 优化浇口位置,会解决充填过程中出现的 头重脚轻”的问题,而且会消除一些不易消除的熔接痕㊂参 考 文 献[1] 朱成兵,刘红.基于顺序阀技术的汽车仪表盘熔接痕分析与优化[J].现代塑料加工应用,2011,23(6):49-51. [2] 唐志玉.大型注塑模具设计技术原理与应用[M].北京:化学工业出版社,2004.[3] 王忠生.基于时序控制的大平板件熔接痕问题分析及工艺控制研究术[J].塑料工业,2016,44(6):65-68. [4] 翟豪瑞,葛晓宏,陶康.运用M o l d e x3D模流分析改善某空气滤清器成型的表面质量[J].模具工业,2016,42(3):50-54.㊃65㊃。
Moldex3D模流分析SYNC for SOLIDWORKS之指标工具
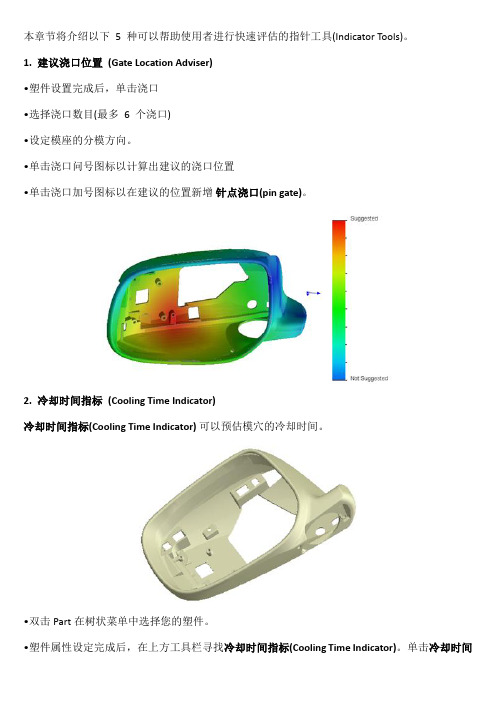
本章节将介绍以下 5 种可以帮助使用者进行快速评估的指针工具(Indicator Tools)。
1. 建议浇口位置(Gate Location Adviser)•塑件设置完成后,单击浇口•选择浇口数目(最多6 个浇口)•设定模座的分模方向。
•单击浇口问号图标以计算出建议的浇口位置•单击浇口加号图标以在建议的位置新增针点浇口(pin gate)。
2. 冷却时间指标(Cooling Time Indicator)冷却时间指标(Cooling Time Indicator)可以预估模穴的冷却时间。
•双击Part在树状菜单中选择您的塑件。
•塑件属性设定完成后,在上方工具栏寻找冷却时间指标(Cooling Time Indicator)。
单击冷却时间指针,系统会自动地预估冷却时间,并将结果显示在窗口上。
•左图中,需要更多冷却时间的塑件位置可以用色杆图标(color legend)分布来指示。
•同时,左侧会显示材料信息和参数设定。
预估冷却时间的计算是根据其相关信息;此外,使用者可以使用滑块手动地调整色杆图示(color legend)的上限和下限。
3. 流长比指标(Flow Length to Thickness Ratio Indicator)•完成浇口和进浇口设定后,单击流长比指标。
•拉动上限/下限的滑块以指定流长比的范围。
4. 凹痕指标(Sink Mark Indicator)凹痕指标(Sink Mark Indicator)可以预估凹痕(Sink Mark)的位置。
•使用此功能,用户必须完成塑件的属性设定,并确保流道和进浇口属性也都设定完成(至少各有一个属性)。
•属性设定完成后,单击凹痕指标图标,若其中一个属性( 塑件、流道和进浇口)尚未设定完成,图标将显示为灰色。
•单击凹痕指标图标,凹痕(Sink Mark)的结果就会显示在窗口上。
•凹痕(Sink Mark)通常出现在模穴的肋条或转角处。
•左侧将会显示参数设定。
Moldex3D模流分析之浇口贡献度、压力、温度、剪切应力、剪切率

浇口贡献度(Gate Contribution)浇口贡献度显示目前时间输出时射出塑料体积的效能,并以以百分比结果值显示浇口贡献度。
正常来说,必须取得平均的浇口贡献度,才能获得最佳的结果。
注:如果是有阀式浇口(Valve gate) 的情况,此结果项不会显示而用户须要透过粒子追踪(Particle Tracer) 结果来确认浇口贡献度。
压力(Pressure)压力结果显示目前时间输出时的塑料压力分布。
您可根据压力结果,执行以下动作并据此修改设计或分析设定:检查压力传动情况大小不恰当的流道、浇口和模穴厚度,会限制传动到模穴的射出压力。
此等限制会导致短射,因为驱动塑料熔体的力量是射出压力。
计算流道系统压力降要计算流道系统压力降,首先您需要知道在具备流道和没有具备流道时的最大压力。
(Max.Pressure with Runner) - (Max. Pressure without Runner) = (Pressure Drop in Runner)依据默认值,会在显示窗口显示流道。
所以,在彩色色杆显示的最大压力是具备流道的最大压力。
接下来在顶端工具栏单击显示/隐藏流道(Show/Hide runner) 隐藏流道。
彩色色杆的压力值将会瞬间更新。
取得两种不同的最大压力值并使用以上方程式,得出流道系统的压力降。
避免过保压和熔体毛边如前所述,您可利用流动波前时间结果检查是否发生过保压现象。
要更准确预测过保压,您可套用流动波前时间结果和压力结果。
检查可能发生过保压区域的压力值。
如果压力明显高于其他区域,该区域发生过保压的机率会变高。
温度(Temperature)温度结果显示了在显示区域当前时间点下的3D温度分布。
藉由温度结果判读, 可以判定塑件成品中的积热情形,或者冷却/加热效果是否符合设定与设计。
注:冷却阶段的温度结果显示于色杆上的最大最小值,参考的是目前显示的表面结果而非整个模型(使用检视工具时则会恢复一般的显示方式)。
Moldex3D 模型模拟 (一)

Moldex3D 模型模拟 (一)点击主页签上的材料或直接展开材料树形图,即可以为模型中的各个组件指定材料。
如果项目中没有需要的材料,可以在材料清单下选择汇入或从材料精灵中寻找,详细材料精灵的介绍,请参考前面仿真指南下的相关章节。
在模型页签分成不同区来帮助使用者建立完整的成型制程系统,其中包含了汇入与检查、流道系统及冷却系统。
经由模型页签的各式功能,用户可以简单的初步设计出成品及模具组件。
1.汇入和分析 (Import and Analysis)➢汇入几何 (Import Geometry)开始准备模型后,首先点击汇入几何 (Import Geometry)来汇入几何对象,而几何对象也能在主页签及工具页签汇入或创建。
点击汇入几何 (Import Geometry)来从其他地方汇入几何模型或点击汇入几何(自动修复) (Import Geometry (Auto Heal)) 来不仅汇入还进行几何自动修复。
注:自动修复(Auto Heal)功能可能会移除部分微小但重要的特征。
➢置换几何 (Swap Geometry)当执行过模拟后要设计变更时,一般也会需要设变的模型在进行过分析与比对验证。
此时,最好是能够让设变后的模型与原设计分析时的网格架构其差异最小化,而置换几何功能即可将原设计的撒点设置同步至新的类似模型上。
如须同步撒点,在已经完成至少原模型之撒点作为参考时,点击汇入几何下拉选单中的置换几何。
选择设计变更后的模型档案将其汇入,则原撒点信息会被映像到新的上面。
而后可以接续在模型上局部的变更撒点设置,而因为设变而无法同步到撒点的特征线也会标示为淡蓝色。
点击确认来完成新的撒点设置,而后则可以接续进行其他网格及分析工作。
➢检查几何 (Check Geometry)强烈建议在建构模型表面和实体网格前,使用几何检查功能,因为它对后续表面和实体网格的生成极为重要。
汇入产品模型后,点击 Check Geometry 检查几何缺陷,将会切将会切换到检查几何树并开启修复几何页签。
基于Moldex3D汽车中控台热流道及冷却水路的设计

基于Moldex3D汽车中控台热流道及冷却水路的设计王秀梅;邹栋坡;翟豪瑞;吴海东【摘要】选取蔚来汽车ES8中控台为设计对象,采取热流道浇注系统方案设计.该产品的材料为PP+20%CF,产品结构复杂、体积较大,成型工艺很难控制.为了验证热流道系统和冷却系统的合理性,在开发模具之前运用Moldex3D模流分析软件进行仿真分析,最终试模验证模流分析的准确性.为工艺参数的调试和采用预变形原理修模、试模提供了可靠的理论依据.【期刊名称】《汽车实用技术》【年(卷),期】2018(000)021【总页数】3页(P162-164)【关键词】碳纤增强;Moldex3D;热流道;冷却水路;翘曲变形【作者】王秀梅;邹栋坡;翟豪瑞;吴海东【作者单位】常州机电职业技术学院车辆工程(轨道交通)学院,江苏常州 213164;常州机电职业技术学院车辆工程(轨道交通)学院,江苏常州 213164;盐城工学院汽车工程学院,江苏盐城 224051;常州机电职业技术学院车辆工程(轨道交通)学院,江苏常州 213164【正文语种】中文【中图分类】U462热塑性复合材料以及其优秀性能广泛应用在汽车、航空航天、机械、电子等领域。
为新产品的开发提供各种可能。
主要在材料中增加不同百分比的玻璃纤维、碳纤维、芳纶纤维等一切可能的纤维品种,,增强其机械强度,该工程材料具有密度小、强度高、可塑性强、成型加工率高等特点[1-3]。
在汽车行业,碳纤维及其复合材料发挥着越来越重要的作用,从车身到发动机,碳纤维正在逐步取代金属材料,极大地提高了汽车的性能[4]。
其中采用玻纤增强材料极大的提高了汽车注塑件的强度寸稳定性,但纤维配向通常是引起塑件翘曲变形的主要原因[5-6]。
Moldex3D先进的三维BLM网格划分技术,为CAE模流分析提供了精准的前处理,可以实现熔体成型过程的动态仿真分析,为优化模具和塑件设计、优化成型工艺方案提供依据[7-8]。
本文提出了一种真实的三维数值方法,用于模拟热流道系统的性能。
- 1、下载文档前请自行甄别文档内容的完整性,平台不提供额外的编辑、内容补充、找答案等附加服务。
- 2、"仅部分预览"的文档,不可在线预览部分如存在完整性等问题,可反馈申请退款(可完整预览的文档不适用该条件!)。
- 3、如文档侵犯您的权益,请联系客服反馈,我们会尽快为您处理(人工客服工作时间:9:00-18:30)。
Science and technology project
科技专题
2016 年 3 月刊 塑料制造 71
Moldex3D热浇道阀针速度控制仿真
近年来,热浇道系统使用阀式浇口设计的比例持续成长,其应用领域也逐渐扩大中,从汽车、电子到医疗等产业都可以看到使用阀式热浇道系统的案例。
阀式浇口设计具备许多生产优势,浇口平整、不需要等待浇口固化等可以提升产品外观质量与有效缩短成型周期。
阀式浇口另一项重要的优势为可以结合时序控制技术来控制浇口开启时机,有效解决产品表面结合线问题。
然而时序控制技术也面临应用上的挑战。
随着射出成型的充填比例增加,射出压力也会跟着上升以符合充填流率,热流道内部会累积一定压力范围。
当关闭中的阀式浇口快速开启时,瞬间压力释放使融胶以高速进入模腔,这时会造成塑件表面发生质量不一的缺陷,如:流痕、光泽不均匀…等问题,对
产品良率产生严重影响。
协助热浇道使用者将时序控制技术的效益发挥至最大,达到提升塑件质量目标,热浇道厂商推出可对阀针开关浇口做速度控制的新解决方案,Moldex3D也因应市场的需求,在进阶热流道解决方案研发阀针作动速度控制仿真技术,让分析工程师可以从Moldex3D 中选择使用一般或进阶阀式浇口控制 (图1);若选择进阶阀式浇口模拟分析,设计者可以针对阀针上下作动的速度进行控制调整 (图2)。
从图3可以看到,浇口区域的速度场因为阀针的位置改变而产生变化,再搭配充填流动分析结果可以验证阀针速度控制对流动波前的影响和改善效果 (图4),确保表面流痕问题获得显著改善。
图1 Moldex3D 提供一般阀浇口分析(左)以及进阶阀式浇口控制
分析(右
)
图2 Moldex3D 仿真阀针移动速度控制的设定接口
Science and technology project 科技专题
72塑料制造 2016 年 3 月刊 图
3 阀针作动对浇口的速度场产生变化
左:多浇口、时序进浇设计容易产生流痕右:搭配阀针速度控制技术后,表面流痕问题获得显著改善
图4 利用Moldex3D仿真验证阀针速度控制技术
除此之外,在网格前处理阶段,Moldex3D使用者
可以藉由原本的网格编辑工具(图5),依照实际的阀式
浇口几何形状进行建模,包含:热流道几何、阀针几
何、行程距离、浇口控制编号…等等。
产品设计者不
需要进行几何简化,牺牲重要几何信息,透过真实三
维实体网格技术,Moldex3D模流分析完整考虑最真实
的阀式浇口设计,大幅提升模拟分析的准确度。
在成
型条件设定阶段,产品设计者还可以针对各别浇口群
组进行控制,例如:浇口初始状态(开或关)、阀针移
动速度、速度段数等,对于有阀式浇口进阶模拟需求
的使用者,是不可或缺的利器。
图5 Moldex3D 提供网格编辑工具,让使用者依照实际阀式浇口几何形状进行建模
Science and technology project
科技专题
2016 年 3 月刊 塑料制造 73
图
6 使用阀针作动功能进行浇口时序控制的案例
热浇道系统已经是塑料射出成型制程中不可或缺的重要设计之一,业界也仍持续投入研究资源发展更先进、更广范的应用。
透过Moldex3D仿真及验证阀针速度控制技术,热浇道使用者可以在实际开发前进行
设计验证和优化,降低塑件表面发生瑕疵的机会,将时序控制技术效益发挥至最大,确实为产品质量把
关。