基于低周热疲劳试验条件的活塞寿命预测研究
金属低周热疲劳试验方法 标准
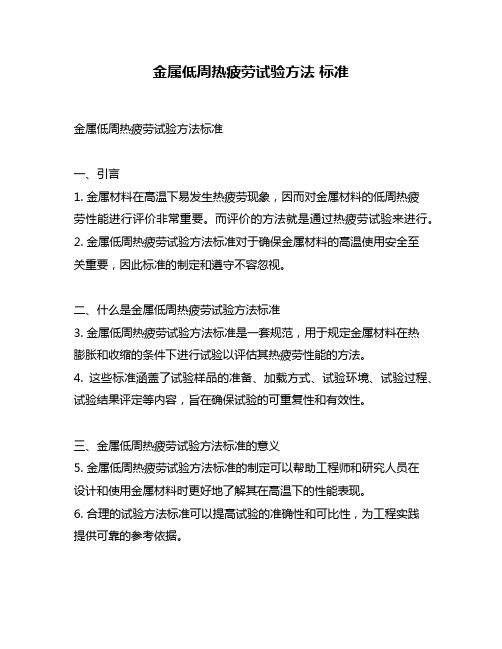
金属低周热疲劳试验方法标准金属低周热疲劳试验方法标准一、引言1. 金属材料在高温下易发生热疲劳现象,因而对金属材料的低周热疲劳性能进行评价非常重要。
而评价的方法就是通过热疲劳试验来进行。
2. 金属低周热疲劳试验方法标准对于确保金属材料的高温使用安全至关重要,因此标准的制定和遵守不容忽视。
二、什么是金属低周热疲劳试验方法标准3. 金属低周热疲劳试验方法标准是一套规范,用于规定金属材料在热膨胀和收缩的条件下进行试验以评估其热疲劳性能的方法。
4. 这些标准涵盖了试验样品的准备、加载方式、试验环境、试验过程、试验结果评定等内容,旨在确保试验的可重复性和有效性。
三、金属低周热疲劳试验方法标准的意义5. 金属低周热疲劳试验方法标准的制定可以帮助工程师和研究人员在设计和使用金属材料时更好地了解其在高温下的性能表现。
6. 合理的试验方法标准可以提高试验的准确性和可比性,为工程实践提供可靠的参考依据。
四、金属低周热疲劳试验方法标准的分类7. 目前,国际上的金属低周热疲劳试验方法标准主要分为两类,一类是基于高温蠕变试验的方法标准,另一类是基于高温振动试验的方法标准。
8. 这两种方法标准都有各自的特点和适用范围,工程师和研究人员需要根据具体情况选择合适的试验方法标准。
五、金属低周热疲劳试验方法标准的实施9. 实施金属低周热疲劳试验方法标准需要严格按照标准规定的试验条件和程序进行,并且需要保证试验设备的精度和稳定性。
10. 对试验结果的评定也需要按照标准的要求进行,才能得到可靠的试验数据和评价结果。
六、个人观点和理解11. 在实际工作中,我认为金属低周热疲劳试验方法标准的制定和实施对于确保金属材料在高温环境下的安全可靠运行至关重要。
12. 合理的试验方法标准可以帮助工程师更好地选用材料、设计结构,并且可以为新材料的研发提供重要参考。
七、总结13. 金属低周热疲劳试验方法标准的制定和实施对于金属材料的高温使用具有重要意义,需要得到工程师和研究人员的高度重视和遵守。
一种预测高低周复合疲劳寿命的新方法
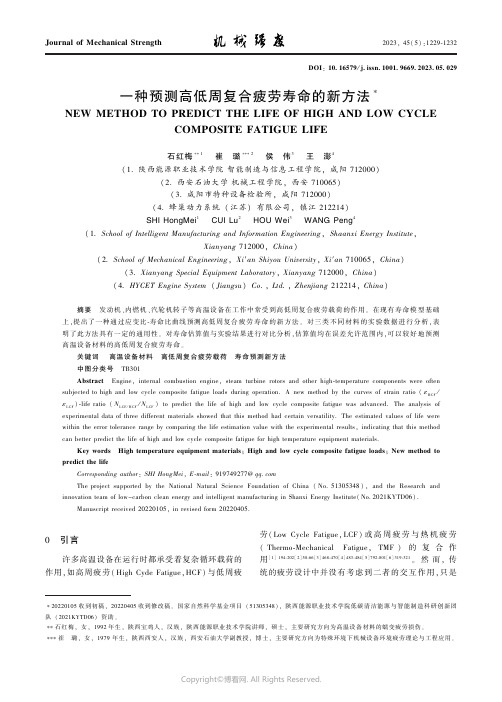
Journal of Mechanical Strength2023,45(5):1229-1232DOI :10.16579/j.issn.1001.9669.2023.05.029∗20220105收到初稿,20220405收到修改稿㊂国家自然科学基金项目(51305348),陕西能源职业技术学院低碳清洁能源与智能制造科研创新团队(2021KYTD06)资助㊂∗∗石红梅,女,1992年生,陕西宝鸡人,汉族,陕西能源职业技术学院讲师,硕士,主要研究方向为高温设备材料的蠕变疲劳损伤㊂∗∗∗崔㊀璐,女,1979年生,陕西西安人,汉族,西安石油大学副教授,博士,主要研究方向为特殊环境下机械设备环境疲劳理论与工程应用㊂一种预测高低周复合疲劳寿命的新方法∗NEW METHOD TO PREDICT THE LIFE OF HIGH AND LOW CYCLECOMPOSITE FATIGUE LIFE石红梅∗∗1㊀崔㊀璐∗∗∗2㊀侯㊀伟3㊀王㊀澎4(1.陕西能源职业技术学院智能制造与信息工程学院,咸阳712000)(2.西安石油大学机械工程学院,西安710065)(3.咸阳市特种设备检验所,咸阳712000)(4.蜂巢动力系统(江苏)有限公司,镇江212214)SHI HongMei 1㊀CUI Lu 2㊀HOU Wei 3㊀WANG Peng 4(1.School of Intelligent Manufacturing and Information Engineering ,Shaanxi Energy Institute ,Xianyang 712000,China )(2.School of Mechanical Engineering ,Xiᶄan Shiyou University ,Xiᶄan 710065,China )(3.Xianyang Special Equipment Laboratory ,Xianyang 712000,China )(4.HYCET Engine System (Jiangsu )Co.,Ltd.,Zhenjiang 212214,China )摘要㊀发动机㊁内燃机㊁汽轮机转子等高温设备在工作中常受到高低周复合疲劳载荷的作用㊂在现有寿命模型基础上,提出了一种通过应变比-寿命比曲线预测高低周复合疲劳寿命的新方法㊂对三类不同材料的实验数据进行分析,表明了此方法具有一定的通用性㊂对寿命估算值与实验结果进行对比分析,估算值均在误差允许范围内,可以较好地预测高温设备材料的高低周复合疲劳寿命㊂关键词㊀高温设备材料㊀高低周复合疲劳载荷㊀寿命预测新方法中图分类号㊀TB301㊀㊀Abstract ㊀Engine,internal combustion engine,steam turbine rotors and other high-temperature components were oftensubjected to high and low cycle composite fatigue loads during operation.A new method by the curves of strain ratio (εHCF /εLCF )-life ratio (N LCF /HCF /N LCF )to predict the life of high and low cycle composite fatigue was advanced.The analysis of experimental data of three different materials showed that this method had certain versatility.The estimated values of life were within the error tolerance range by comparing the life estimation value with the experimental results,indicating that this methodcan better predict the life of high and low cycle composite fatigue for high temperature equipment materials.Key words㊀High temperature equipment materials ;High and low cycle composite fatigue loads ;New method topredict the lifeCorresponding author :SHI HongMei ,E-mail :919749277@The project supported by the National Natural Science Foundation of China (No.51305348),and the Research andinnovation team of low -carbon clean energy and intelligent manufacturing in Shanxi Energy Institute(No.2021KYTD06).Manuscript received 20220105,in revised form 20220405.0㊀引言㊀㊀许多高温设备在运行时都承受着复杂循环载荷的作用,如高周疲劳(High Cyde Fatigue,HCF)与低周疲劳(Low Cycle Fatigue,LCF)或高周疲劳与热机疲劳(Thermo-MechanicalFatigue,TMF )的复合作用[1]194-202[2]58-66[3]468-470[4]483-484[5]792-801[6]319-321㊂然而,传统的疲劳设计中并没有考虑到二者的交互作用,只是㊀1230㊀机㊀㊀械㊀㊀强㊀㊀度2023年㊀单独研究了两种疲劳失效形式㊂随着高温设备运行工况越来越复杂,进一步研究表明很多高温设备的疲劳寿命和高周疲劳载荷的附加有很大关系;随着高周疲劳载荷应变幅的增大,材料的疲劳寿命飞速降低[7-8]㊂因此,研究高温设备材料在高低周复合疲劳载荷下的寿命模型,成为了该领域的研究重点㊂对于高低周复合疲劳寿命模型的研究,较成熟的是裂纹扩展模型和累积损伤模型[9]629-632㊂基于裂纹扩展的机制模型认为叠加的高周疲劳载荷会增加裂纹扩展速率,减少构件的疲劳寿命,经实验验证可以较好地预测材料的疲劳寿命㊂赵振华等[9]629-632提出了线性和非线性疲劳损伤累积模型,其中非线性损伤累积模型研究了高低周复合循环比和应力(应变)幅比的关系,故而估算精度较好㊂这两种模型虽然得到了广泛的应用,但都只是将高低周疲劳载荷对材料寿命的影响进行了纯粹地叠加,而没有考虑二者的交互作用㊂因此,本文分析了高低周疲劳载荷对几种高温设备材料寿命的影响,提出一种预测高低周复合疲劳寿命的新方法㊂1㊀分析方法1.1㊀基础模型㊀㊀SCHWEIZER C等[1]194-202为了描述高低周复合载荷下疲劳裂纹的扩展行为,提出了以裂纹增长速率(d a/d N)和循环裂纹尖端位移(ΔCTOD)的相关性而展开的机制制型:d ad N block=d ad N total+ðblock d a d N HCF式中,d a/d N|block为高低周复合载荷下的裂纹增长速率;d a/d N|total为低周载荷下的裂纹增长速率;ðblock (d a/d N|HCF)为高周载荷下的裂纹增长速率㊂文中以汽轮机转子10%Cr钢为实验材料,分别进行了低周载荷和高低周复合载荷下的疲劳实验,得到了裂纹长度和循环周期的曲线,如图1所示㊂如此,已知裂纹长度,就可预测试件在该载荷下的循环周期(寿命)㊂而且此模型的预测结果和实验结果吻合度较好,可以很好地描述高低周复合载荷下疲劳裂纹的扩展行为㊂1.2㊀演化方法㊀㊀由图1可知,载荷加载初期,裂纹扩展很慢;当循环周期达到1500后,裂纹扩展速率加快,表现为裂纹长度迅速增大,而且高低周复合载荷下裂纹的扩展速率远大于纯低周疲劳载荷;裂纹长度增大到一定值时不再变化,循环周期趋于固定值,说明此时试件已经断图1㊀10%Cr钢在不同载荷下裂纹长度与循环周期的关系Fig.1㊀Relationship between crack length and life cycle of10%Cr steel under different loads裂,相对应的循环周期可以表示为试件的实验寿命㊂㊀㊀因为高周疲劳载荷的附加会大大降低材料的复合疲劳寿命,所以可推算得材料的高低周复合疲劳寿命与纯低周疲劳寿命之比(N LCF/HCF/N LCF)小于1,且大于0㊂受上述基础模型的启发,以10%Cr钢实验数据为例,做出高周应变-寿命比(εHCF-N LCF/HCF/N LCF)和高低周应变比-寿命比(εHCF/εLCF-N LCF/HCF/N LCF)两种曲线[10],如图2所示㊂图2㊀10%Cr钢的应变-寿命比和应变比-寿命比曲线Fig.2㊀Fitting curve that the strain-life ratio and the ratioby strain-life of10%Cr steel经曲线拟合,发现应变比-寿命比曲线的变化趋势更明显,拟合度较高㊂因此,提出可通过应变比-寿命比曲线来预测高温设备材料的复合疲劳寿命㊂此方法计算简单,其是否具有较高的准确度和通用性,需要大量的数据验证㊂㊀第45卷第5期石红梅等:一种预测高低周复合疲劳寿命的新方法1231㊀㊀2㊀方法验证2.1㊀实验数据分析㊀㊀铸造铝合金一般用于汽车发动机的汽缸盖㊁机体和活塞等部件,而这些部件往往遭受着复杂的热疲劳与机械疲劳载荷[3]468-470[4]483-484[5]792-801㊂钴基合金材料一般用于航空发动机或燃气涡轮机的燃烧室,而燃烧室在工作时既承受着由温度变化引起的热机疲劳载荷,也承受着由机械振动引起的高周疲劳载荷[6]319-321㊂球墨铸铁材料常用于内燃机的高温设备,尤其是汽缸盖部件[2]58-66㊂这些高温设备工作时不但遭受着由频繁启停机引起的低周疲劳载荷,而且承受着由点火压力和机械惯性振动引起的高周疲劳载荷㊂本文摘取以上三类材料在复合疲劳载荷下的实验数据,并对这三类不同材料在不同实验条件下的实验数据进行了分析,得到了其应变比-寿命比曲线,如图3所示㊂图3㊀不同材料的应变比-寿命比曲线Fig.3㊀Fitting curve that the ratio by strain-lifeof different materials由图3可知,所有数据的变化趋势一致,都是幂函数关系,且与10%Cr钢材料的应变比-寿命比曲线变化趋势一致㊂2.2㊀论证分析㊀㊀由以上不同材料的数据分析,可以得到如下结论: 1)虽然以上几种材料在组成成分上差别较大,但其大多都用在燃气涡轮机和航空发动机的燃烧室或燃烧器及汽车发动机的汽缸盖㊁机体和活塞等部件上,而这些高温部件在工作时不仅承受着由温度变化引起的热机疲劳载荷或者低周疲劳载荷,还承受着由机械振动及燃烧压力引起的高周疲劳载荷㊂这与10%Cr钢材料工作时的受力情况基本相同,故这几种材料具有可比性和代表性㊂2)同种材料,实验工况(温度㊁频率等)不同,其应变比-寿命比曲线计算值几乎在同一条曲线上,曲线变化趋势一致;不同材料,实验条件各不相同,但其应变比(εHCF/εLCF)-寿命比(N LCF/HCF/N LCF)曲线的变化趋势也相同㊂所有曲线都和10%Cr钢材料的曲线变化趋势一致,材料的应变比-寿命比呈幂函数变化关系㊂3)从数据分析的角度看,应变比-寿命比曲线反映的其实还是应变幅与疲劳寿命之间的关系,只不过将此关系用应变比-寿命比的数学关系反映出来了,更适合表达高周复合疲劳载荷下高低周应变福与疲劳寿命之间的关系㊂在疲劳实验中,当实验温度确定,在同样的应变幅下,同材料的疲劳寿命基本稳定在一定范围数值下,而应变比-寿命比曲线反应的含义与此实验现象是一致的,即应变幅值是决定疲劳寿命的最主要因素㊂因此,通过应变比(εHCF/εLCF)-寿命比(N LCF/HCF/ N LCF)曲线预测高温设备材料的高低周复合疲劳寿命时,具有一定的适用性㊂3㊀寿命估算㊀㊀10%Cr钢的应变比-寿命比计算值和对应的拟合曲线如图2(b)所示㊂图中黑色实心方块是根据实验数据计算的结果,平滑曲线是根据计算值在Origin中非线性拟合得到的曲线㊂在双对数坐标下,应变比与寿命比之间呈幂函数关系,拟合相似度为0.9777㊂得到这条拟合曲线后,已知实验条件(高低周载荷应变幅)和材料在纯低周载荷下的疲劳寿命,就可估算出材料在高低周复合载荷下的疲劳寿命㊂图4所示为通过拟合曲线估算的高低周复合疲劳寿命和实验结果的误差分析㊂由图4可知,此方法的计算精度在两倍误差范围内,且误差分布均匀㊂因此,该方法可以较好地估算高低周复合载荷下高温设备材料的疲劳寿命㊂图4㊀疲劳寿命估算值与实验值的比较Fig.4㊀Comparison of estimated and experimental values of fatigue life 4㊀结论与展望㊀㊀发动机㊁内燃机㊁汽轮机转子等高温部件在工作中常受到高低周复合疲劳载荷的作用,本文在现有寿命模型基础上,提出了一种预测高低周复合疲劳寿命的新方法㊂此方法通过应变比和寿命比反映了高低周疲劳载荷的交互作用,两者在双对数坐标下呈幂函数关系,三类不同材料的应变比-寿命比曲线表明此关系成立㊂文中还通过此关系估算了10%Cr钢的复合疲劳㊀1232㊀机㊀㊀械㊀㊀强㊀㊀度2023年㊀寿命,并与实验结果进行了对比,均在误差允许范围内,进而表明此方法可以估算高温设备材料的复合疲劳寿命㊂高低周复合疲劳参数复杂,影响因素众多,其中,温度和应变幅是最主要的影响因素㊂本文中得到的应变比-寿命比曲线是暂时忽略了温度的影响而得到的,通过实验数据的分析,不同温度下应变比-寿命比曲线的趋势基本是一致的㊂由此说明,此关系具有一定适用性,可以利用此关系估算高低周复合疲劳寿命㊂但为了更精确地预测疲劳寿命,可在后期通过实验及资料收集,得到更多实验数据,进行温度修正,使此关系能更精准地预测高温设备材料的复合疲劳寿命㊂参考文献(References)[1]㊀SCHWEIZER C,SEIFERT T,NIEWEG B,et al.Mechanisms andmodelling of fatigue crack growth under combined low and high cyclefatigue loading[J].International Journal of Fatigue,2011(33):194-202.[2]㊀METZGER M,NIEWEG B,SCHWEIZER C,et al.Lifetimeprediction of cast iron materials under combined thermomechanicalfatigue and high cycle fatigue loading using a mechanism-basedmodel[J].International Journal of Fatigue,2013(53):58-66. [3]㊀BECK T,LOEHE D,LUFT J,et al.Damage mechanisms of cast Al-Si-Mg alloys under superimposed thermal-mechanical fatigue andhigh-cycle fatigue loading[J].Materials Science and Engineering:A,2007,468/469/470:184-192.[4]㊀BECK T,HENNE I,LOEHE D.Lifetime of cast AlSi6Cu4undersuperimposed thermal mechanical fatigue and high-cycle fatigueloading[J].Materials Science and Engineering:A,2008,483/484:382-386.[5]㊀ZHENG X,ENGLER-PINTO C C,SU X,et al.Modeling of fatiguedamage under superimposed high-cycle and low-cycle fatigue loadingfor a cast aluminum alloy[J].Materials Science&Engineering A,2013(560):792-801.[6]㊀MOALLA M,LANG K-H,LOEHE D.Effect of superimposed highcycle fatigue loadings on the out-of-phase thermal-mechanical fatiguebehaviour of CoCr22Ni22W14[J].Materials Science andEngineering:A,2001:319/320/321:647-651.[7]㊀崔㊀璐,康文泉,吴㊀鹏,等.高低周复合疲劳工况下汽轮机转子钢寿命模型[J].科学技术与工程,2021,21(9):3612-3617.CUI Lu,KANG WenQuan,WU Peng,et al.Life model of steamturbine rotor steel under combined high and low cycle fatigueconditions[J].Science Technology and Engineering,2021,21(9):3612-3617(In Chinese).[8]㊀崔㊀璐,石红梅,李㊀臻,等.先进汽轮机转子材料蠕变疲劳损伤研究新进展[J].机械强度,2018,40(2):449-454.CUI Lu,SHI HongMei,LI Zhen,et al.Research on hightemperature and low cycle fatigue performance of ultra-supercriticalsteam turbine high and intermediate pressure rotor steel[A].Journalof Mechanical Strength,2013(7):51-52(In Chinese). [9]㊀赵振华,陈㊀伟,吴铁鹰.高低周复合载荷下的钛合金疲劳寿命估算[J].机械强度,2011,33(4):629-632.ZHAO ZhenHua,CHEN Wei,WU TieYing.Fatigue life estimationof titanium alloys under high and low cycle compound loads[J].Journal of Mechanical Strength,2011,33(4):629-632(InChinese).[10]㊀石红梅.复杂蠕变疲劳载荷对超超临界汽轮机转子钢寿命的影响[D].西安:西安石油大学,2017:42-46.SHI HongMei.The influence of complex creep fatigue loading on lifeof ultra supercritical steam turbine rotor steel[D].Xiᶄan:XiᶄanShiyou University,2017:42-46(In Chinese).。
基于机器学习的机械零部件剩余寿命预测方法研究

基于机器学习的机械零部件剩余寿命预测方法研究近年来,随着工业化进程的加快,工业设备的维修与管理成为工业生产中不可或缺的一环。
机械零部件的剩余寿命预测一直是工业设备维护中的难题之一。
然而,借助机器学习的方法,我们可以通过对大量真实数据的分析和建模来解决这个问题。
首先,我们需要收集大量关于机械零部件的性能数据,这些数据通常包括温度、振动、电流、压力等信息。
同时,还应该记录机械零部件的使用时间和维护记录等相关信息。
这些数据将成为我们训练机器学习模型的依据。
接下来,我们可以使用监督学习算法来建立剩余寿命预测模型。
监督学习算法常用的有决策树、支持向量机和神经网络等。
这些算法通过学习历史数据中的模式和规律,将输入特征与剩余寿命之间的关系建立起来。
在模型训练过程中,我们需要将数据集分为训练集和测试集,以验证模型的准确性和稳定性。
在模型建立完成后,我们可以利用模型对未来的机械零部件的剩余寿命进行预测。
这样一来,我们就可以根据预测结果来制定合理的维修和更换计划,以降低设备故障率和生产停机时间。
同时,还可以优化维护成本,提高设备利用率。
此外,为了进一步提高预测准确性,我们可以结合其他技术手段和模型优化方法。
例如,可以采用特征工程的方法来提取更有意义的特征,去除冗余和无关的特征,从而提高模型的表现。
还可以引入深度学习算法,利用更复杂的神经网络结构来实现更精确的剩余寿命预测。
同时,在数据采集和模型建立过程中,我们还需要注意解决一些常见的问题和难题。
例如,数据质量问题可能会导致模型的不准确性,因此我们需要采取一系列的数据清洗和预处理措施。
此外,由于机械零部件的使用环境和工况条件多变,我们还需要考虑对模型进行动态调整和更新,以适应实际应用场景的变化。
总之,基于机器学习的机械零部件剩余寿命预测方法为工业设备维护和管理提供了新的思路和工具。
通过建立预测模型,我们可以更加准确地预测机械零部件的寿命,提前进行维修和更换,从而减少故障风险,提高生产效率和设备利用率。
蠕变—热疲劳可靠寿命预测的若干问题研究

蠕变—热疲劳可靠寿命预测的若干问题研究一、本文概述本文旨在深入研究蠕变与热疲劳对材料可靠寿命的影响,并探讨相关的预测方法。
蠕变是指在恒定温度和应力作用下,材料随时间发生的不可逆变形,而热疲劳则是由材料在循环热负荷下产生的内部损伤。
这两种现象在诸多工程领域,如航空航天、能源、化工等都有着广泛的应用背景。
本文将首先概述蠕变和热疲劳的基本概念、产生机理及其对材料性能的影响。
随后,我们将深入探讨现有可靠寿命预测模型的优缺点,并重点分析影响蠕变和热疲劳寿命的关键因素,如材料属性、环境条件和载荷谱等。
在此基础上,我们将研究并提出改进的寿命预测模型,以提高预测的准确性和可靠性。
本文还将关注蠕变与热疲劳交互作用对材料性能的影响,探讨在复杂工况下如何综合考虑这两种因素进行寿命预测。
我们将通过理论分析和实验研究相结合的方法,揭示蠕变与热疲劳交互作用的机理,为建立更加完善的寿命预测模型提供理论基础。
我们将总结本文的主要研究成果,并展望未来的研究方向。
本文的研究不仅有助于推动蠕变与热疲劳理论的发展,也将为工程实践提供更加准确、可靠的寿命预测方法,对于提高设备的安全性和经济性具有重要意义。
二、蠕变与热疲劳的交互作用机制蠕变与热疲劳是材料在高温环境下常见的两种失效模式,它们各自独立存在时,对材料性能的影响已经相当显著。
然而,当蠕变与热疲劳共同作用时,它们的交互作用机制将变得更为复杂。
这种交互作用不仅影响材料的力学行为,还对其疲劳寿命产生显著影响。
蠕变是指材料在持续高温和应力作用下,随时间发生的缓慢塑性变形。
蠕变过程中,材料的微观结构会发生变化,如晶界滑移、位错运动等,导致材料性能的逐渐退化。
热疲劳则是指材料在周期性温度变化下,由于热应力的反复作用而产生的疲劳损伤。
热疲劳过程中,材料的热膨胀系数、导热率等热物理性能会发生变化,进而影响其力学性能和疲劳寿命。
蠕变与热疲劳的交互作用主要体现在以下几个方面:蠕变过程中产生的塑性变形会改变材料的应力分布,从而影响热疲劳过程中的应力集中和裂纹萌生。
航空航天工程中的材料失效与寿命预测
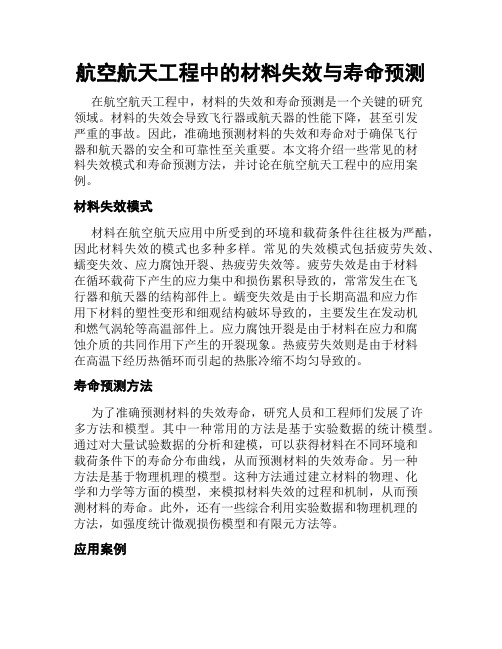
航空航天工程中的材料失效与寿命预测在航空航天工程中,材料的失效和寿命预测是一个关键的研究领域。
材料的失效会导致飞行器或航天器的性能下降,甚至引发严重的事故。
因此,准确地预测材料的失效和寿命对于确保飞行器和航天器的安全和可靠性至关重要。
本文将介绍一些常见的材料失效模式和寿命预测方法,并讨论在航空航天工程中的应用案例。
材料失效模式材料在航空航天应用中所受到的环境和载荷条件往往极为严酷,因此材料失效的模式也多种多样。
常见的失效模式包括疲劳失效、蠕变失效、应力腐蚀开裂、热疲劳失效等。
疲劳失效是由于材料在循环载荷下产生的应力集中和损伤累积导致的,常常发生在飞行器和航天器的结构部件上。
蠕变失效是由于长期高温和应力作用下材料的塑性变形和细观结构破坏导致的,主要发生在发动机和燃气涡轮等高温部件上。
应力腐蚀开裂是由于材料在应力和腐蚀介质的共同作用下产生的开裂现象。
热疲劳失效则是由于材料在高温下经历热循环而引起的热胀冷缩不均匀导致的。
寿命预测方法为了准确预测材料的失效寿命,研究人员和工程师们发展了许多方法和模型。
其中一种常用的方法是基于实验数据的统计模型。
通过对大量试验数据的分析和建模,可以获得材料在不同环境和载荷条件下的寿命分布曲线,从而预测材料的失效寿命。
另一种方法是基于物理机理的模型。
这种方法通过建立材料的物理、化学和力学等方面的模型,来模拟材料失效的过程和机制,从而预测材料的寿命。
此外,还有一些综合利用实验数据和物理机理的方法,如强度统计微观损伤模型和有限元方法等。
应用案例航空航天工程中的材料失效和寿命预测在许多领域都有广泛的应用。
以飞行器为例,发动机是一个至关重要的部件,其材料的失效可能导致严重的事故。
因此,对发动机材料的失效和寿命进行准确预测是非常重要的。
研究人员通过对发动机材料的疲劳、蠕变和热疲劳等失效模式进行研究,并结合统计模型和物理机理模型,成功预测了发动机材料的寿命。
类似地,对于航天器的结构部件,研究人员也开展了大量的研究工作,以预测材料的失效和寿命。
基于能量法的缸盖低周热疲劳寿命预测

基于能量法的缸盖低周热疲劳寿命预测张亚鲁;胡玉平;李国祥【摘要】用材料在低周载荷下形成的滞回能量作为预测结构高温低周疲劳寿命的损伤参量,通过对发动机缸盖材料施加循环热负荷,获得材料基于能量法的低周寿命预测模型参数;采用有限元分析方法对发动机单缸进行典型工况分析,并根据发动机启停循环中温度和应力的变化规律,结合子模型技术获得单个工作循环内缸盖火力面区域的温度场和应力场;对缸盖火力面附近区域进行循环加载,得到迟滞回线,评估其低周疲劳寿命.结果表明,在缸盖火力面进-排气门之间的鼻梁区低周疲劳寿命较短.【期刊名称】《内燃机与动力装置》【年(卷),期】2018(035)003【总页数】6页(P17-22)【关键词】气缸盖;能量法;有限元;低周疲劳;迟滞回线;子模型【作者】张亚鲁;胡玉平;李国祥【作者单位】山东大学能源与动力工程学院,山东济南250061;山东大学能源与动力工程学院,山东济南250061;山东大学能源与动力工程学院,山东济南250061【正文语种】中文【中图分类】TK423.2气缸盖是发动机结构中所受负荷最复杂、最高的零部件之一。
随着内燃机功率的提高、设计轻量化和涡轮增压等技术的应用,对气缸盖的强度和疲劳寿命都提出了更高的要求。
发动机实际工作过程中,工况复杂多变,气缸盖所受温度变化剧烈,尤其是在燃气直接接触的火力面区域,会产生较大的循环热负荷,产生低周疲劳损伤。
气缸盖火力面的低周疲劳寿命成为发动机可靠性设计的重要考虑因素[1-3]。
近年来,对于内燃机零部件低周疲劳寿命的评估和研究主要从循环热负荷加载试验与有限元仿真计算预测两方面着手。
试验方法一般采用实体发动机,对其进行启停循环加载来模拟低周疲劳失效过程,评价是否满足可靠性要求,并寻找可靠性低的区域,准确度高,但是试验周期长、成本高。
仿真方法一般根据Manson-Coffin低周疲劳寿命预测理论,采用有限元方法,对受热件的低周疲劳寿命进行预测分析,周期短、成本低,但是目前软件中选择塑性应变幅作为低周寿命评价参量,跟高温低周疲劳失效的本质有所偏离,故预测精度较低[4-6]。
机械零部件的疲劳寿命预测研究

机械零部件的疲劳寿命预测研究现代机械工程的发展离不开复杂的机械零部件。
然而,长期以来,机械零部件的疲劳寿命一直是制约机械设备可靠性的重要因素之一。
疲劳寿命预测研究的发展,旨在提前预测零部件的寿命,以便在出现问题之前采取相应的措施维护机械设备。
本文将介绍机械零部件疲劳寿命预测的研究方法,并探讨其在实际应用中的挑战。
研究方法机械零部件的疲劳寿命预测主要依靠材料力学学科的知识和疲劳寿命评估方法。
首先,需要对材料的静态和动态力学性能进行全面的测试和分析。
通过加载试验,可以获得材料的强度、韧性和变形特性等参数。
此外,需要考虑材料的应力-应变响应、断裂韧性和应力强度因子等因素,以建立与材料特性相关的寿命预测模型。
然后,结合实际工况下的载荷、温度和环境等因素,使用数值仿真或试验验证的方法,对机械零部件的疲劳寿命进行预测。
挑战机械零部件的疲劳寿命预测研究面临着一些挑战。
首先,不同材料在不同工况下的疲劳寿命预测模型可能存在差异。
因此,需要根据具体情况选择适用的预测模型,并进行合理的修正和验证。
其次,由于疲劳寿命与工况参数的复杂关联,模型的建立和参数确定较为困难。
需要采用准确可靠的试验手段对参数进行获取和修正。
此外,实际工况下存在多种复杂载荷作用和多路疲劳载荷的叠加,这对疲劳寿命预测的准确性提出了更高的要求。
未来发展方向为了提高机械零部件疲劳寿命预测的准确性和可靠性,需要在以下几个方面进行深入研究。
首先,开展多尺度材料模型的建立,考虑材料的内部结构和微观变形行为。
其次,加强对极端工况下疲劳寿命的预测。
例如,高温、低温等特殊环境下对机械零部件疲劳寿命的影响需要更深入的研究和验证。
此外,结合大数据和人工智能技术,开展机械零部件疲劳寿命预测模型的优化和自动化方法研究。
结语机械零部件的疲劳寿命预测研究旨在提前预测零部件的寿命,以便及时采取维护和修复措施,确保机械设备的可靠运行。
通过研究方法的不断创新和改进,预测模型的不断优化,我们可以更准确地预测机械零部件的疲劳寿命。
疲劳寿命预测方法的研究现状与发展

基于物理模型的预测方法是通过建立描述材料疲劳行为的物理模型来进行预 测。这些模型通常基于材料的微观结构和失效机制,并考虑了诸如应力集中、裂 纹扩展、材料强化等因素。基于物理模型的预测方法通常比基于经验和实验的方 法更准确,但需要更深入的材料科学知识。
4、基于统计的预测方法
基于统计的预测方法是通过分析大量实验数据来建立统计模型,从而预测材 料的疲劳寿命。这种方法通常考虑了诸如材料成分、加工条件、环境因素等对疲 劳性能的影响。基于统计的预测方法在处理复杂多变的数据时可能更具优势,但 也可能受到数据质量和数量等因素的影响。
2、人工智能与机器学习
人工智能和机器学习技术在许多领域都取得了显著的进展,包括疲劳寿命预 测。这些技术可以通过对大量数据进行学习和分析,建立更加准确和高效的预测 模型。未来,人工智能和机器学习将在疲劳寿命预测中发挥更大的作用,提高预 测的准确性和效率。
3、跨学科合作与交叉融合
疲劳寿命预测涉及到材料科学、机械工程、物理学等多个学科领域的知识。 未来,跨学科合作与交叉融合将成为疲劳寿命预测的重要发展趋势。通过不同学 科领域的专家共同合作,可以更深入地理解材料的疲劳行为,提出更加有效的预 测方法。
疲劳寿命预测方法的研究现状 与发展
01 一、引言
目录
02
二、疲劳寿命预测方 法的研究现状
03
三、疲劳寿命预测方 法的发展趋势
04 四、结论
05 参考内容
一、引言
疲劳寿命预测是材料科学、机械工程和相关领域中的一项重要研究内容。它 涉及到对材料或结构在循环载荷作用下的失效行为进行预测和评估。疲劳寿命预 测方法对于提高机械部件的可靠性和安全性,优化产品设计,降低维修和更换成 本等方面具有重要意义。本次演示将综述疲劳寿命预测方法的研究现状,并探讨 其行疲劳试验来获取材料的疲劳性能数据。这些 数据可以用于建立数学模型,从而预测材料的疲劳寿命。这种方法通常比基于经 验的方法更准确,但需要大量的时间和资源来执行实验。此外,实验结果可能受 到实验条件和试样制备等因素的影响。
20g 高温低周疲劳试验评定

试验温度为*"+ , 。试验采用应变控 过程中! 9!:, 制方式, 用拉;压加载方式, 试验频率为 ! <=, 应变比 温 度 和 应 变 相 位 相 同, 应变波形为三角 " > ? 8 $, 波, 加热设备为电阻炉。按照金属材料高温强度理 论, 这些试验条件比较苛刻, 高温低周疲劳试验条件 与焦炭塔的实际情况比较接近, 所预测的剩余寿命 偏于安全。
高温低周疲劳中恒应变 ! %A 在整个试验中恒定 其中 ! 且! %A ? ! %> I ! %B, %> 为弹性应变。将通过 试验得出的数据 (表 !) 按最小二乘法回归整理得到 以下关系式: 母材 焊缝
%B # C !
! %A # C
) . 5+) !
? $3 . *( ? $ . $)! + ? ) . )!" (4 ? ) . )$+ 5(
关键词:焦炭塔;低周疲劳试验;评定;剩余寿命 中图分类号: 23 +!"4+ 文献标识码:5
$%#&’()*+),-(.,) /01 232/) 4-(%#.) ()5( -55)55%6# (&) ,)5%7.-/ /%4)(%*) 04 !"# 208%6# (01),
657 89:$,-;,,8<5=> >?@$/?, AB=> 2:-;$C:; (D:-@;:;, E;:FGHI:.J @/ KG.H@LG?C M 69GC:N-L 2GN9;@L@,J,O?I9?; ’’&""’, 69:;-)
燃气轮机热端部件寿命的等效运行时间分析
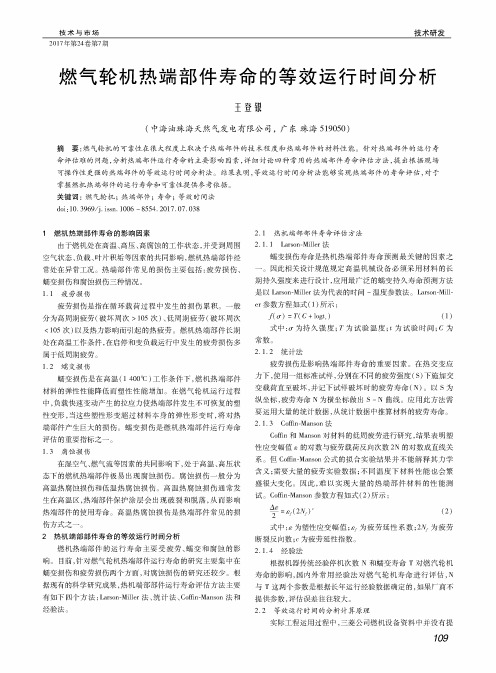
2017年第24卷第7期技术与市场技术研发燃气轮机热端部件寿命的等效运行时间分析王登银(中海油珠海天然气发电有限公司,广东珠海519050)摘要:燃气轮机的可靠性在很大程度上取决于热端部件的技术程度和热端部件的材料性能。
针对热端部件的运行寿 命评估难的问题,分析热端部件运行寿命的主要影响因素,详细讨论四种常用的热端部件寿命评估方法,提出根据现场 可操作性更强的热端部件的等效运行时间分析法。
结果表明,等效运行时间分析法能够实现热端部件的寿命评估,对于 掌握燃机热端部件的运行寿命和可靠性提供参考依据。
关键词:燃气轮机;热端部件;寿命;等效时间法doi:10. 3969/j.issn.1006 - 8554. 2017.07.0381燃机热端部件寿命的影响因素由于燃机处在高温、高压、高腐蚀的工作状态,并受到周围 空气状态、负载、叶片积垢等因素的共同影响,燃机热端部件经 常处在异常工况。
热端部件常见的损伤主要包括:疲劳损伤、蠕变损伤和腐蚀损伤三种情况。
1.1疲劳损伤疲劳损伤是指在循环载荷过程中发生的损伤累积。
一般 分为高周期疲劳(破坏周次>105次)、低周期疲劳(破坏周次 <105次)以及热力影响而引起的热疲劳。
燃机热端部件长期 处在高温工作条件,在启停和变负载运行中发生的疲劳损伤多 属于低周期疲劳。
1.2蠕变损伤蠕变损伤是在高温(1 400T)工作条件下,燃机热端部件 材料的弹性性能降低而塑性性能增加。
在燃气轮机运行过程 中,负载快速变动产生的拉应力使热端部件发生不可恢复的塑 性变形,当这些塑性形变超过材料本身的弹性形变时,将对热 端部件产生巨大的损伤。
蠕变损伤是燃机热端部件运行寿命 评估的重要指标之一。
1.3腐蚀损伤在湿空气、燃气流等因素的共同影响下,处于高温、高压状 态下的燃机热端部件极易出现腐蚀损伤。
腐蚀损伤一般分为 高温热腐蚀损伤和低温热腐蚀损伤。
高温热腐蚀损伤通常发 生在高温区,热端部件保护涂层会出现破裂和脱落,从而影响 热端部件的使用寿命。
基于虚拟疲劳试验的铁路车辆焊接结构疲劳寿命预测

基于虚拟疲劳试验的铁路车辆焊接结构疲劳寿命预测一、本文概述随着铁路行业的快速发展,车辆的安全性和可靠性越来越受到人们的关注。
焊接结构作为铁路车辆的重要组成部分,其疲劳寿命的预测和评估对于确保车辆运行安全具有重要意义。
传统的疲劳试验方法由于周期长、成本高、对试验条件要求严格等限制,已无法满足现代铁路车辆研发的需求。
基于虚拟疲劳试验的铁路车辆焊接结构疲劳寿命预测方法应运而生,成为了当前研究的热点。
本文旨在探讨基于虚拟疲劳试验的铁路车辆焊接结构疲劳寿命预测方法。
文章将介绍虚拟疲劳试验的基本原理和关键技术,包括有限元分析、疲劳损伤累积理论等。
将详细阐述如何利用虚拟疲劳试验对铁路车辆焊接结构进行疲劳寿命预测,包括模型的建立、加载条件的设定、疲劳寿命的计算等步骤。
文章还将对虚拟疲劳试验的准确性和可靠性进行评估,并与传统疲劳试验结果进行对比分析。
文章将总结虚拟疲劳试验在铁路车辆焊接结构疲劳寿命预测中的应用前景,并提出相应的建议和改进措施。
通过本文的研究,旨在为铁路车辆焊接结构的疲劳寿命预测提供一种新的、高效的方法,为铁路车辆的安全性和可靠性提供有力保障。
也为相关领域的研究提供参考和借鉴。
二、虚拟疲劳试验技术概述虚拟疲劳试验技术是一种基于计算机模拟和数值分析的方法,旨在预测和评估铁路车辆焊接结构的疲劳寿命。
该技术结合了有限元分析(FEA)、多体动力学仿真、疲劳损伤累积理论和数据处理技术等手段,通过构建高度逼真的虚拟模型来模拟实际工作环境中的载荷条件和应力分布。
在虚拟疲劳试验中,首先需要根据实际车辆的结构特点、材料属性和焊接工艺等建立精确的有限元模型。
通过多体动力学仿真模拟车辆在不同运行条件下的动力学行为,获取各关键部位的动态载荷历程。
利用疲劳分析软件对这些载荷历程进行处理,计算各部位的应力响应和疲劳损伤累积情况。
基于疲劳损伤累积理论,预测结构的疲劳寿命,并找出潜在的疲劳薄弱环节。
虚拟疲劳试验技术具有成本低、周期短、可重复性好等优点,能够在产品设计阶段就进行疲劳性能的预测和优化,从而有效提高铁路车辆焊接结构的安全性和可靠性。
基于缺陷材料建模的疲劳寿命预测研究

基于缺陷材料建模的疲劳寿命预测研究疲劳寿命是指材料在不断受力循环下,能够承受多少循环次数后疲劳断裂的能力,是评价材料耐久性和机械性能的一个重要指标。
而在实际应用过程中,材料疲劳断裂的原因往往与内在缺陷有关。
因此,基于缺陷材料建模的疲劳寿命预测研究具有重要的理论意义和实际应用价值。
一、缺陷形态建模在构建缺陷模型时,首先需要确定材料的缺陷形态。
常见的材料缺陷形态包括孔洞、夹杂和裂纹等。
这些缺陷形态在不同的载荷下会呈现出不同的形态和演化特征,因此在建模时需要尽可能准确地描述这些特征。
例如,对于裂纹缺陷,可以采用有限元方法或数值分析方法,结合外加载荷和材料的应力应变特性,建立一个裂纹扩展模型,模拟裂纹在不同载荷下的扩展过程。
二、缺陷材料损伤模型缺陷模型的建立为接下来的材料损伤模型提供了关键参数。
在材料损伤模型中,通常会考虑到以下几个方面的因素:1.缺陷形态和分布:不同形态和分布的缺陷对材料的损伤程度不同,因此需要考虑其影响因素。
2.应力水平和载荷历程:在实际应用过程中,材料所承受的应力水平和载荷历程不同,直接影响到其疲劳寿命。
3.环境和温度:环境和温度是材料损伤的外在因素,对材料的损伤程度也具有重要影响。
基于这些因素,可以建立一个综合考虑缺陷形态和载荷等因素的材料损伤模型,并预测材料在不同条件下的疲劳寿命。
三、模型验证和应用基于缺陷材料建模的疲劳寿命预测模型需要经过实验验证,以确定其预测准确性和可靠性。
在实验中,可以通过对不同形态、大小和分布的缺陷样本进行循环载荷实验,对预测模型的预测结果进行比对验证。
预测模型的应用范围广泛,主要应用于工程结构和材料的设计和评估工作中。
例如,对于航空发动机、汽车发动机等高负荷结构件的设计过程中,可以利用这种预测模型来预计其疲劳寿命,从而进行结构材料选型和设计优化。
总之,基于缺陷材料建模的疲劳寿命预测研究,是材料科学领域中的重要研究方向,也是实现材料高效设计和评估的关键手段。
航空发动机结构疲劳分析与寿命预测研究

航空发动机结构疲劳分析与寿命预测研究引言:航空发动机作为飞机的核心部件, 承担着将燃油能转化为机械能的重要任务。
在航空工程中,航空发动机的安全性和可靠性是最基本的要求之一。
因此,对航空发动机的结构疲劳特性进行分析和寿命预测就显得尤为重要。
本文将对航空发动机结构疲劳分析和寿命预测的研究进行探讨及分析。
一、航空发动机结构疲劳分析方法1. 应力分析法为了分析航空发动机在工作过程中受到的应力情况,可以使用有限元法对其结构进行数值模拟。
通过确定结构中各个关键部位的应力分布情况,可以判断关键部位是否有可能出现疲劳破坏。
这种方法对于快速评估结构的疲劳寿命以及发动机设计的优化具有重要意义。
2. 超声波无损检测法超声波无损检测是一种常用的检测方法,可用于航空发动机的结构健康监测。
通过高频的超声波脉冲,可以探测到发动机结构中的缺陷、裂纹等问题。
这种方法具有快速、非破坏性的特点,可以提前发现发动机结构的隐患,从而采取相应的维修和改进措施。
二、航空发动机结构疲劳寿命的预测方法1. Miner理论Miner理论是一种经验性的方法,根据发动机结构在工作过程中的载荷谱和材料疲劳损伤曲线,通过累积损伤值的计算,对结构的疲劳寿命进行预测。
这种方法的优点是简单易行,但缺点是没有考虑结构在不同工况下的动态特性。
2. 基于飞行数据的预测方法这种方法是根据实际的飞行数据来预测航空发动机的结构疲劳寿命。
通过对飞行过程中的加速度、温度、振动等数据的监测和分析,可以得到发动机在实际使用中的负荷情况,从而有效地预测疲劳寿命。
这种方法更加准确,但需要大量的实际数据支持。
三、航空发动机结构疲劳分析与寿命预测的应用1. 优化设计和改进通过对航空发动机结构疲劳分析和寿命预测的研究,可以及时发现和解决发动机结构的缺陷和问题,进而对其进行优化设计和改进。
这将有助于提高发动机的安全性、可靠性和性能。
2. 维修策略制定在航空发动机的使用过程中,经常会遇到一些疲劳裂纹的问题,通过结构疲劳分析和寿命预测,可以预先判断出哪些部位可能会出现疲劳破坏,并制定相应的维修策略。
1.375-12UNJF-3A_外螺纹疲劳寿命预估与试验

1 疲劳考核部位确定
1.1 螺纹牙型 与粗牙螺纹相比,细牙螺纹特点如下所示。1)螺纹的
螺距小,在相同的螺纹长度下旋入的牙数多。2)螺纹的牙
纹齿的分布几乎不受螺旋升角的影响,所产生的应力集中可
以忽略不计。螺纹旋升角度 φ 如公式(1)所示。
长螺栓 1.375-12UNJF-3A 外螺纹为滚压螺纹,与其他
在轴向拉 - 拉低循环疲劳载荷作用下,外螺纹低循环疲
加工方法相比,滚压可以提高螺纹的抗拉强度,有利于降低 螺纹加工工艺对力学性能的影响。为提高螺纹抗疲劳强度, 外螺纹牙底采用加大半径的牙底圆弧,牙底为连续、光滑的 曲线,牙型如图 1 所示。与长螺栓外螺纹相配套的螺母内螺 纹类型为 1.375-12UNJF-3B,螺纹的材料均为优质 GH4169 合金。
如公式(3)所示。
σmax=(2×FN×σb)/(KSu×KN+Ks×Kc×σb)
(3)
式中 :FN 为 10N 循环时的零 - 平均疲劳强度,如公式(4)
所示。
FN=F6·(F3/F6)2-x/3
(4)
式中 :x=log10N ;假设 F3=0.9×σb,F6=0.5×σb。
Ks 为 10N 循环时的疲劳分散系数,4<N<5 时,如公式
3max d 3min d
30°
最小实体牙型 Rmax=0.18042P Rmin=0.15011P
图 1 外螺纹牙型图
在轴向拉 - 拉疲劳载荷作用下,长螺栓外螺纹的螺距增大, 32.233mm,螺距 P 为 2.117mm,牙底圆弧半径 R 为 0.318mm,
螺母内螺纹的螺距变小,靠近螺母下部的螺纹受力比螺母上 部大 [2],外螺纹先于内螺纹发生疲劳破坏。
热作模具热疲劳寿命评估及预测方法的研究进展

热作模具热疲劳寿命评估及预测方法的研究进展苏楠;陈明和【摘要】热作模具服役过程中存在温度及机械载荷的循环变化,产生变形及失效的机理复杂,故热作模具热疲劳寿命的评估预测是模具应用研究的难点.结合现有研究成果,介绍了热应力疲劳研究中可用于热作模具热疲劳寿命评估及预测的方法,从唯象寿命模型和损伤累积模型两个角度分别阐述了热作模具热机械疲劳寿命的研究,并对热作模具热疲劳寿命预测的发展趋势进行了展望.【期刊名称】《中国机械工程》【年(卷),期】2019(030)011【总页数】8页(P1378-1385)【关键词】热疲劳寿命;热作模具;热应力疲劳;热机械疲劳【作者】苏楠;陈明和【作者单位】南京航空航天大学机电学院,南京,210016;南京航空航天大学机电学院,南京,210016【正文语种】中文【中图分类】TG142.450 引言随着科学技术和工业进程的飞速发展,高强材料的应用越来越广泛,对应用于高强材料成形的热作模具的需求和要求也越来越高[1]。
在服役过程中,热作模具(如热锻模、热冲压模、压铸模和热挤压模等)在高温、高压、高应力等恶劣工作条件下受到热循环和载荷循环的共同作用,从而产生热疲劳裂纹直至破坏失效[2]。
热作模具的热疲劳寿命直接影响热作模具的服役寿命,研究其热疲劳寿命评估及预测方法对模具工业的发展具有重要的工程和经济意义。
热疲劳研究的历史可追溯到1838年,Duhamel研究发现,物体在不均匀加热时会产生热应力,直至1976年,SPERA等[3]才对热疲劳研究做出了详尽的基础解释和分类,将其主要分为热应力疲劳与热机械疲劳两个研究方向。
20世纪50年代Manson-Coffin公式[4-5](以下简称“M-C公式”)被提出后,热疲劳研究得到了从定性分析到定量研究的质的飞跃。
国内外研究方向从简单的破坏分析逐渐过渡到裂纹萌生、扩展过程的研究,通常通过试验测量材料的热疲劳损伤因子,并利用数学模型表征应力应变-寿命关系,构建寿命预测模型来估算材料或构件的寿命。
基于热循环模式的加速寿命试验 ppt课件

PPT课件
20
模型分析
合成因子:
AF
KTC
U
KTC T
160 8.28
20
失效率计算 合成加速因子:
样本数k=40台,测试时间T=250h;
PPT课件
21
思考题 1 在规定单元时间的条件下如何确定样本数量和测试时间 2 加速寿命试验前有哪些必须的准备工作
PPT课件
22
PPT课件
16
模型分析
Norris-Landzberg模型 Norris-Landzberg模型说明了温度漂移,高温极限,还有涉及应力松弛的铅轴 承焊接合金的由时间决定的热机行为.此模型解释了完全根据经验的观察:在 低频热循环时延长的停留时间,加速了疲劳损坏,引起了高风险焊接互连的早 期失效;
PPT课件
17
模型分析 Norris-Landzberg加速因子的标准公式为:
测试条件:-10~+65°C,每天循环8次; △T=75℃ Tmax=273+65=338k f=8 使用条件:每天循环1次,△T=13℃ Tmax=273+55=328k f=1 Norris-Landzberg加速因子AF:
序进应力加速寿命试验
序进应力加速寿命试验可近似看作步进应力的每级应力差很小的极限情况, 进行这种试验需专门程序控制, 故很少采用
PPT课件
5
3 基于热循环模式的加速寿命试验
名词解释 试验模型 应力分析 效果评析
PPT课件
6
名词解释 MTBF
是指相邻两次故障之间的平均工作时间,也称为平均故障间隔。它仅适用于可 维修产品。同时也规定产品在总的使用阶段累计工作时间与故障次数的比值为 MTBF
基于热机耦合的柴油机活塞热应力及疲劳寿命分析

基于热机耦合的柴油机活塞热应力及疲劳寿命分析许广举;李铭迪;赵洋;陈庆樟;李学智【摘要】通过建立活塞裙部型线、活塞优化后的燃烧室及内冷油道等的有限元模型,采用PERMAS软件计算了优化后的活塞在标定工况下的温度场和热机耦合应力,分析了活塞的疲劳寿命,并测量了800h热冲击试验后,活塞环槽、活塞外圆尺寸等尺寸和型线的变化情况.结果表明:活塞高温区域主要分布在活塞顶部,最高温度约为301℃,在活塞材料许用范围内;第一环槽的表面平均温度为194℃,低于润滑油结焦温度230℃;增加了20%喷油量时,活塞的表面温度仍可满足设计要求.在活塞受到热机耦合作用时,活塞向主推力面方向倾斜,主推力面受力较大,约为44N/mm2,活塞销座表面最大应力值区域主要分布在后端销孔上侧,约为98N/mm2,应力值均在许用范围内.活塞疲劳寿命最低的部位在活塞燃烧室底部及燃烧室喉口,理论寿命分别为6.9和7.7,800h热冲击试验后,活塞环槽、销孔、活塞环槽底径、活塞外援尺寸等尺寸变化均较小,活塞外圆型线和椭圆型线变化不大,能够满足使用要求.%A finite element model of a piston including its skirt profile, optimized combustion chamber and oil gallery was established to investigate its temperature field, thermal stress and fatigue life at the rated condition by means of the finite element software PERMAS.Besides that, the sizes of the piston ring grooves and skirt profile were measured after a thermal shock test for 800h.The analysis results show that high temperature areas are mainly found at top of the piston, with the maximum temperature reaching about 301℃, and the mean temperature reaching 194℃ is found in the top ring insert, much lo wer than 230℃ for oil coking.So they are all acceptable even when the fuel injection quantity is increased by 20%.Thepiston inclines to the thrusting side under the coupled thermo-mechanical force, and the thrusting side bears a stress of 44N/mm2.The peak stress of about 98N/mm2 in piston pin bore is found at the rear end of the bore and they all are acceptable.The lowest piston fatigue life occurs at the bottom and bowl rim of the combustion chamber, and their theoretical service lives are 6.9 and 7.7 respectively, and the sizes of piston ring grooves and skirt profile have a little change after the 800h test, satisfying the requirements of use.【期刊名称】《内燃机工程》【年(卷),期】2017(038)002【总页数】6页(P96-100,106)【关键词】柴油机;活塞;热负荷;疲劳寿命;有限元分析【作者】许广举;李铭迪;赵洋;陈庆樟;李学智【作者单位】常熟理工学院汽车工程学院,常熟 215500;常熟理工学院汽车工程学院,常熟 215500;常熟理工学院汽车工程学院,常熟 215500;常熟理工学院汽车工程学院,常熟 215500;常熟理工学院汽车工程学院,常熟 215500【正文语种】中文【中图分类】TK423.33活塞是柴油机重要的零部件之一,与连杆、曲轴等形成曲柄连杆机构,将活塞的往复运动输出为旋转运动[1]。
基于Sehitoglu 模型的发动机气缸盖热机疲劳寿命预测

JournalofMechanicalStrength2021ꎬ43(5):1184 ̄1190DOI:10 16579/j.issn.1001 9669 2021 05 023∗20200907收到初稿ꎬ20201107收到修改稿ꎮ国防科技重点实验室基金项目(6142212190307)资助ꎮ∗∗邹萍萍ꎬ女ꎬ1987年8月ꎬ江西抚州人ꎬ汉族ꎬ江铃汽车股份有限公司工程师ꎬ硕士ꎬ主要研究方向为发动机缸盖疲劳强度与寿命研究ꎮ∗∗∗景国玺(通信作者)ꎬ男ꎬ1984年1月ꎬ甘肃会宁人ꎬ河北工业大学机械工程学院教授ꎬ博士ꎬ主要从事发动机结构疲劳强度研究工作ꎮ基于Sehitoglu模型的发动机气缸盖热机疲劳寿命预测∗THERMAL ̄MECHANICALFATIGUEPREDICTIONOFENGINECYLINDERHEADBASEDONTHESEHITOGLUMODEL邹萍萍∗∗1㊀景国玺∗∗∗2ꎬ3㊀曾小春1㊀骆旭薇1㊀袁晓军1㊀魏㊀涛1㊀林宇星1(1.江铃汽车股份有限公司动力总成开发部ꎬ南昌330001)(2.河北工业大学机械工程学院ꎬ天津300400)(3.天津市新能源汽车动力传动与安全技术重点实验室ꎬ天津300400)ZOUPingPing1㊀JINGGuoXi2ꎬ3㊀ZENGXiaoChun1㊀LUOXuWei1㊀YUANXiaoJun1㊀WEITao1㊀LINYuXing1(1.PowertrainEngineeringDepartmentꎬJianglingMotorsCorporationꎬLimitedꎬNanchang330001ꎬChina)(2.SchoolofMechanicalEngineeringꎬHebeiUniversityofTechnologyꎬTianjin300400ꎬChina)(3.TianjinKeylaboratoryofPowerTransmissionandSafetyTechnologyforNewEnergyVehiclesꎬTianjin300400ꎬChina)摘要㊀以某发动机气缸盖为研究对象ꎬ开展了气缸盖本体材料力学性能测试与表征㊁气缸盖热机疲劳寿命预测研究工作ꎮ采用流固耦合方法ꎬ获得了准确的气缸盖热边界和温度场结果ꎬ温度场计算值与实测结果相符合ꎮ依照整机热冲击试验规范ꎬ采用Sehitoglu模型对缸盖的热机疲劳寿命进行了预测ꎬ仿真结果显示ꎬ缸盖最低寿命出现在第二缸火力面排气侧鼻梁区ꎬ主要由环境损伤引起ꎬ最低寿命为6860次ꎬ满足设计要求ꎬ该气缸盖顺利通过整机热机疲劳台架试验考核ꎮ关键词㊀发动机㊀气缸盖㊀热机疲劳㊀寿命预测中图分类号㊀TK422Abstract㊀Theresearchworkwascarriedoutonthemechanicalperformancetestingandcharacterizationofanenginecylinderheadmaterialꎬandthepredictionofthecylinderheadthermalenginefatiguelife.Thefluid ̄solidcouplingmethodwasusedtoobtainaccurateresultsofthethermalboundaryandtemperaturefieldofthecylinderhead.Thecalculatedtemperaturefieldisconsistentwiththemeasuredresults.AccordingtothethermalshocktestspecificationsofthewholemachineꎬtheSehitoglumodelwasusedtopredictthethermalfatiguelifeofthecylinderhead.Thesimulationresultsshowthattheminimumlifeofthecylinderheadoccursinthenosebridgeareaontheexhaustsideofthesecondcylinderfiresurfaceꎬwhichismainlycausedbyenvironmentaldamage.Theservicelifeis6860ꎬwhichmeetsthedesignrequirements.Atthesametimeꎬthecylinderheadhassuccessfullypassedtheheatenginefatiguebenchtestofthewholemachine.Keywords㊀InternalcombustionengineꎻCylinderheadꎻThermalmechanicalfatigueꎻLifepredictionCorrespondingauthor:JINGGuoXiꎬE ̄mail:okjgx@163.comꎬTel:+86 ̄22 ̄60435125ꎬFax:+86 ̄22 ̄60435125TheprojectsupportedbytheFundofNationalDefenseScienceandTechnologyKeyLaboratory(No.6142212190307).Manuscriptreceived20200907ꎬinrevisedform20201107.㊀㊀引言近年来ꎬ随着排放法规日益严格和对轻量化设计的需求ꎬ发动机强化程度越来越高ꎮ随着发动机功率密度增加ꎬ气缸盖等结构件热机械负荷突出ꎬ疲劳寿命问题已成为研究的热点[1]1 ̄12[2 ̄3]和发动机产品研制过程中的拦路虎[4]ꎮ发动机气缸盖设计开发必须满足高周机械疲劳和低周热机械疲劳(ThermalMechanicalFatigueꎬTMFꎬ简称热机疲劳)设计要求[5]ꎮ针对气缸盖高周疲劳评估㊀第43卷第5期邹萍萍等:基于Sehitoglu模型的发动机气缸盖热机疲劳寿命预测1185㊀㊀问题ꎬ国内外已开展较为广泛的研究[6 ̄8]ꎬ为缸盖疲劳强度评估提供了重要依据ꎮ由于低周热机疲劳损伤机理复杂ꎬ热机疲劳寿命预测问题是当前研究的难点和焦点[1]1 ̄12[9]ꎮ国内采用总应变法㊁修正的能量法等方法对气缸盖低周疲劳寿命进行了预测ꎬ获得了热冲击载荷下气缸盖火力面损伤结果ꎮ由于气缸盖鼻梁区呈现典型的反相位热机疲劳载荷特性ꎬ常规低周疲劳寿命预测模型精度较低ꎬ目前ꎬSehitoglu模型[10]1769 ̄1783被行业认为精度高最权威的TMF模型ꎬ本论文将以该理论模型为依据进行气缸盖材料热机疲劳性能测试与表征及热机疲劳寿命预测研究ꎮ1㊀热机疲劳分析流程气缸盖热机疲劳寿命预测流程见图1所示ꎬ主要包括材料力学性能测试与表征㊁低周循环载荷条件下温度和应力应变行为分析和热机疲劳寿命评估等方面ꎮ测试气缸盖铸铝材料不同温度下导热率ꎬ为温度场预测提供材料边界ꎻ开展材料低周疲劳试验ꎬ获取材料弹塑性本构模型参数ꎬ为气缸盖热机耦合应力有限元分析提供边界ꎻ开展不同温度和相位条件下材料热机疲劳试验和蠕变试验等ꎬ获得材料应力应变行为与热机疲劳寿命之间的关系ꎬ进而构建Sehitoglu热机疲劳寿命预测模型和完成模型参数识别ꎮ采用AVL ̄Boost软件建立整机一维热力学仿真模型ꎬ得到发动机在怠速㊁额定功率负荷下进排气道气体温度㊁质量流量等参数ꎬ为三维缸内燃烧分析提供计算边界ꎮ然后ꎬ通过AVL ̄Fire软件进行缸内燃烧分析和缸体缸盖水套分析计算ꎬ并将燃烧和水侧换热边界映射至有限元模型ꎬ采用Abaqus软件对气缸盖进行温度场分析ꎬ通过多轮次耦合计算使得温度结果趋于稳定ꎬ并与实测结果相符合ꎮ依照整机热冲击试验规范ꎬ建立基于材料弹塑性非线性的有限元分析模型ꎬ获得怠速 ̄额定转速交变工况条件下气缸盖应力应变行为ꎬ进而基于Sehitoglu模型实现气缸盖热机疲劳损伤和寿命预测ꎮ图1㊀气缸盖热机疲劳寿命评估流程Fig.1㊀ThecylinderheadTMFlifeevaluationprocess2㊀热机疲劳损伤模型本文采用Sehitoglu模型[10]1769 ̄1783ꎬ该模型考虑机械疲劳㊁环境效应和蠕变三种不同的损伤机制ꎮ疲劳(机械)损伤主要指由室温条件下应变幅主导的疲劳损伤ꎬ高温条件下的损伤主要包括环境损伤和蠕变损伤ꎮ总损伤与机械损伤㊁环境损伤和蠕变损伤之间的关系见公式(1)ꎬ寿命关系式描述见公式(2)ꎮDTMF=Dfat+Denv+Dcreep(1)式中ꎬDTMF为总损伤ꎬDfat为机械疲劳损伤ꎬDenv为环境损伤ꎬDcreep为蠕变损伤ꎮ1/Ntotalf=1/Nfatf+1/Nenvf+1/Ncreepf(2)式中ꎬNtotalf为总寿命ꎬNfatf为机械寿命ꎬNenvf为环境寿命ꎬNcreepf为蠕变寿命ꎮ在热机疲劳循环中ꎬ采用应变 ̄寿命方法来描述疲劳行为ꎬ疲劳寿命采用Manson ̄Coffin方程来描述㊀1186㊀机㊀㊀械㊀㊀强㊀㊀度2021年㊀εmech2=εemech2+εplmech2=σᶄfE(2Nfatf)b+εᶄf(2Nfatf)c(3)式中ꎬΔεmech的机械应变幅ꎬσᶄf为疲劳强度系数ꎬE为弹性模量ꎬb为疲劳强度指数ꎬεᶄf为疲劳延展性系数ꎬc为疲劳延展性指数ꎮ这些参数通过室温条件下应变寿命试验来确定ꎮ环境损伤主要认为在环境温度影响下氧化等现象诱导裂纹扩展ꎬ不断将新鲜的金属材料暴露在环境中ꎬ环境损伤寿命可描述为1Nenvf=hcrδoBΦoxKeffpéëêêùûúú-1/β2Δεmech()2/β()+1ε mech1-α/β()(4)式中ꎬhcr为临界氧化层厚度ꎬδ0㊁α㊁β和B均为材料常数ꎬε mech为机械应变速率ꎬKeffp为有效氧化系数ꎬΦox为环境损伤相位调整系数ꎮ考虑载荷作用历程ꎬ蠕变寿命描述如下1Ncreepf=ΦcreepʏAe-ΔH/RT()α1σ+α2σHKæèçöø÷mdt(5)式中ꎬσ-是有效应力ꎬσH是流体静力学应力ꎬK是拖拉压力ꎬα1和α2是应力作用系数ꎬ表示在拉伸和压缩过程中发生损伤的相对量ꎬΦcreep是蠕变损伤相位调整系数ꎬA和m是材料常数ꎬt是时间ꎮ3㊀气缸盖材料力学性能测试与表征为获得热机疲劳模型材料参数ꎬ设计了一系列低周应变寿命曲线试验和热机疲劳试验ꎬ试验过程分别见图2和图3ꎬ典型试验载荷见图4所示ꎮ低周疲劳试验基于Instron8801疲劳试验机开展ꎬ应变比为-1ꎬ测试温度包括室温㊁150ħ㊁200ħ㊁250ħ和300ħꎬ测试应变速率为1%/sꎮ另外ꎬ在250ħ和300ħ下设计低应变速率0 1%/s下应变寿命试验ꎬ以考虑蠕变对疲劳寿命的影响ꎮ通过低周应变疲劳寿命试验得到的塑性应变与应力关系见图5ꎬ低周疲劳试验结果见图6ꎮ材料TMF测试基于MTS810热机疲劳试验机进行ꎬ测试最高上限温度包括200ħ㊁250ħ和300ħꎬ每种温度考虑两种不同相位和约束系数ꎬ采用电感器加热方式加热ꎬ加热速率约为8ħ/sꎬ冷却使用压缩空气ꎬ最大温度保温60sꎬ截止寿命选定为3000次ꎮ图7为温度载荷100ħ~200ħꎬ约束比为1ꎬ下缸盖材料同相位TMF试验结果ꎬ图7a为不同循环下总应变㊁机械应变和热应变变化曲线ꎬ图7b为第二个㊁中值寿命和最后一个循环对应的应力应变滞后回环ꎬ图7b和图7c分别为中值寿命对应循环内温度和应变与时间的变化曲线ꎮ图2㊀材料低周疲劳测试装置Fig.2㊀Lowcyclefatiguetestdevicet图3㊀材料TMF测试装置Fig.3㊀TMFtestdevice基于上述低周疲劳试验和热机疲劳实验结果ꎬ以中值寿命循环应力应变为载荷输入和Sehitoglu模型为依托ꎬ以试验寿命为目标ꎬ采用多目标优化算法进行材料参数多目标优化和识别ꎬ模型计算结果和实测对比见图8所示ꎬ在69个试验结果中ꎬ90%以上预测结果在3倍误差带范围之内ꎮ4㊀热机疲劳寿命预测4 1㊀缸内燃烧换热边界确定本文缸盖热分析工作中缸内燃烧侧边界采用缸内燃烧数值模拟方法获得ꎮ缸内燃烧分析的湍流模型采用k ̄ζ ̄f模型ꎬ壁面传热采用StandardWallFunction模型ꎬPoisson方程求解采用Simple数值方法ꎮ对于三维缸内燃烧分析ꎬ喷雾模型中ꎬ破碎模型采用Wave模型ꎬ蒸发模型采用Dukowicz模型ꎬ壁面油膜模型采用Walljet1模型ꎬ燃烧模型采用Ecfm ̄3Z模型ꎮCFD ̄FEA燃气侧耦合交接面包括缸盖火力面㊁进排气门㊁进排气道和缸孔内侧ꎮ通过缸内3D燃烧分析获得燃气温度和换热系数ꎬ并将内流场温度和换热系数边界映射到缸盖三维FEA模型上ꎮ额定工况下CFD ̄FEA耦合单缸的燃气侧在一个发动机循环周期内平均温度和换热系数如图9㊁图10所示ꎬ其他三缸燃气测的温度和换热系数采用与第一缸相同的CFD结果ꎮ从图9可以看出ꎬ缸盖火力面温㊀第43卷第5期邹萍萍等:基于Sehitoglu模型的发动机气缸盖热机疲劳寿命预测1187㊀㊀图4㊀材料疲劳试验载荷形式示意图Fig.4㊀Schematicdiagramofmaterialfatiguetestloadform图5㊀塑性应变 ̄应力关系曲线Fig.5㊀Plasticstrain ̄stresscurves图6㊀应变 ̄寿命曲线Fig.6㊀Strain ̄lifecurves度分布很不均匀ꎬ与燃烧过程密切相关ꎮ4 2㊀水套流动换热边界确定水套的主要作用是吸收气缸盖燃烧产生的热量ꎬ确保气缸盖不会因为温度过高而出现故障ꎮ同时ꎬ气缸盖的热负荷也取决于温度分布的均匀性ꎬ温度梯度越大ꎬ气缸盖热负荷越高ꎮCFD ̄FEA耦合水冷边界主要是指缸体和缸盖的水套壁面ꎮ与三维燃烧CFD分析相似ꎬ三维水套分析发动机额定工况和怠速工况两个点ꎬ为FEA温度场分析的水冷边界提供壁面温度和换热系数ꎮ经三个轮次CFD ̄FEA耦合计算ꎬ缸体缸盖水套近壁面的温度和对流换热系数趋于稳定ꎮ缸体缸盖水套最终速度和对流换热系数分布如图11㊁图12所示ꎬ流速越高的区域对应的换热系数也越大ꎬ带走的热量越多ꎮ4 3㊀温度场分析与试验对标缸盖温度场分析CAE模型见图13ꎬ模型网格总数约410万ꎬ缸盖材料导热率结果采用实测值ꎮ缸内燃烧和冷却水腔换热边界由前述CFD结果提供ꎮ额定工况下机油温度为140ħꎬ怠速工况为100ħꎬ换热系数为l30W/(m2 K)ꎮ额定工况下缸盖温度分布如图14所示ꎬ结果显示缸盖火力面温度明显高于其他区域ꎮ受进气和排气温㊀1188㊀机㊀㊀械㊀㊀强㊀㊀度2021年㊀图7㊀TMF试验结果Fig.7㊀TMFtestresults图8㊀实测值和模型预测值对比Fig.8㊀Comparisonoftestandpredictedresults图9㊀额定工况燃气侧温度分布Fig.9㊀Gastemperaturedistributionatratedcondition度的影响ꎬ缸盖排气侧结构温度高于进气侧ꎬ整个模型最高温度出现在第二缸排气侧鼻梁区ꎬ最高温度为203ħꎮ为验证仿真分析的准确性ꎬ本文采用硬度塞法对发动机额定工况下各缸温度进行了试验测试ꎮ每缸布图10㊀额定工况燃气侧换热系数分布Fig.10㊀Gasheattransfercoefficientdistributionatratedcondition图11㊀额定工况下水套速度分布Fig.11㊀Velocitydistributionofcoolantwateratratedcondition置了12个测试点ꎬ四缸测点均采用相同的布置形式ꎬ各点分布位置如图15所示ꎮ四缸各测点温度测试平均值和仿真对比果如图16所示ꎬ结果表明仿真计算温度与测试温度趋势一致ꎬ相对误差基本在5%范围以内ꎮ4 4㊀气缸盖热机疲劳寿命预测气缸盖热机疲劳损伤发生部位主要位于火力面气㊀第43卷第5期邹萍萍等:基于Sehitoglu模型的发动机气缸盖热机疲劳寿命预测1189㊀㊀图12㊀额定工况下水套换热系数分布Fig.12㊀Heattransfercoefficientdistributionofcoolantwateratratedcondition图13㊀温度场分析CAE模型Fig.13㊀FEAmodel图14㊀缸盖的温度场Fig.14㊀Temperaturedistributionofcylinderhead图15㊀温度测点布置Fig.15㊀Temperaturetestpointsarrangement门之间的鼻梁区域ꎬ同时由于整体模型自由度数量巨大ꎬ模型考虑温度和材料弹塑性等非线性特性ꎬ为节约计算成本ꎬ热机疲劳计算过程采用子模型方法ꎬ即整机模型采用线弹性模型计算ꎬ然后用整机模型位移结果作为边界驱动子模型进行详细计算ꎬ缸盖全局模型和子模型网格见图17所示ꎬ有限元分析工况依照整机耐久试验确定ꎮ图16㊀额定工况测试温度与仿真值对比Fig.16㊀Comparisonoftestandcalculatedtemperatureatratedcondition图17㊀缸盖热机疲劳分析子模型Fig.17㊀CylinderheadsubmodelofTMFanalysis气缸盖第二缸热机疲劳损伤计算结果见图18ꎬ结果表明环境损伤在总热机疲劳损伤中占据主导作用ꎬ机械疲劳次之ꎮ由图19的缸盖热机疲劳寿命结果可知ꎬ缸盖最低疲劳寿命为6860次ꎬ出现在第二缸进气和排气门之间的鼻梁区ꎬ各缸火力面疲劳寿命均符合低周疲劳耐久试验规范要求6000次ꎮ5㊀气缸盖热机疲劳耐久试验验证整机热机疲劳耐久试验主要是考核气缸盖因温度变化引起应变所产生的低周疲劳ꎬ整个试验在某一发动机台架上进行ꎮ循环工况主要由怠速工况点和额定功率点两个工况交替运行组成ꎬ一个循环运行280sꎬ按试验要求总共运行6000个循环ꎮ试验完成后拆机ꎬ经观测气缸盖表面没有发现热机疲劳裂纹ꎬ该气缸盖顺利通过试验考核ꎮ6㊀结论本文对某发动机气缸盖热机疲劳特性进行了研究ꎬ主要结论如下:1)从气缸盖本体取样开展了材料低周疲劳性能㊁热机疲劳性能等测试ꎬ并基于Sehitoglu热机疲劳模型进行了预测ꎬ相对实验寿命ꎬ90%以上预测结果在3倍误差带范围内ꎻ2)根据缸盖火力面的测试温度和仿真温度对比㊀1190㊀机㊀㊀械㊀㊀强㊀㊀度2021年㊀图18㊀第二缸火力面热机疲劳损伤分布Fig.18㊀TMFdamagedistributionofthesecondcylinder图19㊀缸盖热机疲劳寿命Fig.19㊀CylinderheadTMFlifedistribution可知ꎬ缸盖仿真分析温度与实测温度分布趋势基本一致ꎬ证明采用该耦合分析方法获得仿真分析结果能够较准确地反映缸盖的实际温度分布情况ꎻ3)通过缸盖热机疲劳分析可知ꎬ环境损伤是引起缸盖热机疲劳的主要因素ꎬ缸盖热机疲劳寿命均满足设计要求ꎬ且顺利通过了整机热机疲劳试验ꎮ参考文献(References)[1]㊀ElanghovanNꎬStefanEꎬJohanAMꎬetal.EffectoftemperatureondeformationandfatiguebehaviourofA356 ̄T7castaluminiumalloysusedinhighspecificpowericenginecylinderheads[J].Materialsꎬ2020ꎬ13(5):1 ̄12.[2]㊀MartinWꎬAndreasMSꎬMarionEꎬetal.ThermomechanicalfatigueoflostfoamcastAl ̄Sicylinderheads ̄assessmentofcrackoriginbasedontheevaluationofporedistribution[J].Metalsꎬ2019ꎬ9(821):1 ̄14.[3]㊀张全中ꎬ魏志明ꎬ刘长振ꎬ等.高承载铝质气缸盖优化设计研究[J].机械强度ꎬ2015(3):493 ̄497.ZHANGQuanZhongꎬWEIZhiMingꎬLIUChangZhenꎬetal.Optimizationdesignofhighloadaluminumcylinderhead[J].JournalofMechanicalStrengthꎬ2015(3):493 ̄497(InChinese).[4]㊀GuoXJꎬMengXZꎬShenQꎬetal.Investigationintodieselenginecylinderheadfailure[J].EngineeringFailureAnalysisꎬ2018:90.[5]㊀景国玺ꎬ张树勇ꎬ付文清ꎬ等.高强化柴油机铸铁缸盖承载特性研究[J].车用发动机ꎬ2017(1):42 ̄48.JINGGuoXiꎬZHANGShuYongꎬFUWenQingꎬetal.Loadingcharacteristicsofcastironcylinderheadforhigh ̄strengtheneddieselengine[J].VehicleEngineꎬ2017(1):42 ̄48(InChinese).[6]㊀罗㊀通ꎬ冯文荣ꎬ黄㊀波ꎬ等.反求重构的气缸盖冷却水腔的CFD分析与优化[J].机械强度ꎬ2015(3):199 ̄204.LUOTongꎬFENGWenRongꎬHUANGBoꎬetal.CFDanalysisandoptimizationofcylinderheadcoolingwatercavityreconstructedbyreverseengineering[J].JournalofMechanicalStrengthꎬ2015(3):199 ̄204(InChinese).[7]㊀丛㊀林ꎬ于㊀群ꎬ何敬宇ꎬ等.6S50MC ̄C柴油机气缸盖的疲劳仿真[J].大连海事大学学报ꎬ2013ꎬ39(4):82 ̄85.CONGLinꎬYUQunꎬHEJingYUꎬetal.Fatigueanalysisof6S50MC ̄Cdieselengine[J].JournalofDalianMaritimeUniversityꎬ2013ꎬ39(4):82 ̄85(InChinese).[8]㊀ChenXꎬBrewerTꎬSeverCꎬetal.Cylinderheaddesignprocesstoimprovehighcyclefatigueperformance[Z].SAETechnicalPaperꎬ2017:2017 ̄01 ̄1085.[9]㊀SeverCꎬBrewerTꎬEeleySꎬetal.Cylinderheadthermo ̄mechanicalfatigueriskassessmentundercustomerusage[Z].SAETechnicalPaperꎬ2017:2017 ̄01 ̄1086.[10]㊀NeuRWꎬSehitogluH.Thermomechanicalfatigueꎬoxidationandcreep:PartII.Lifeprediction[J].MetallurgicalTransactionsAꎬ1989ꎬ20(9):1769 ̄1783.。
- 1、下载文档前请自行甄别文档内容的完整性,平台不提供额外的编辑、内容补充、找答案等附加服务。
- 2、"仅部分预览"的文档,不可在线预览部分如存在完整性等问题,可反馈申请退款(可完整预览的文档不适用该条件!)。
- 3、如文档侵犯您的权益,请联系客服反馈,我们会尽快为您处理(人工客服工作时间:9:00-18:30)。
万方数据
122胡定云等:基于低周热疲劳试验条件的活塞寿命预测研究第2期表1活塞材料热属性
图2活塞的网格
2.2,2边界条件
活塞的低周热疲劳试验,是通过激光把活塞加热到特定的温度分布,激光卸载时配合通水、通气强制冷却方式加速活塞的热疲劳。
三个环形区域为激光加载区域,如图3所示。
预热时Ⅸ域1—3的热流密度分别为203.1啪,m2、2.52W/m2,687,9w^n2,以后每次加热的热流密度为预热时的1.5倍,试验中活塞区域3的加热预设温度为300。
C,冷却预设温度为170"C,加热时间为210s,强制冷却时间为lOs。
活塞有限无数值仿真寿命预测与活塞激光热负荷的热边界条件一致,为了量化其边界条件,采用有限元迭代反求方法闭,求出各边界的具体热物性参数,如表2所示。
图3激光加载位鼍示意图
表2活塞热边界条件
3模拟结果和讨论
活塞顶面激光加载区域3内某特征点的温度变化,如图4所示。
冷却过程中,该点温度在通水通气条件下迅速冷却,下降速率是先快后慢(下凹分布);加热过程中,其温度上升,上升速率是先快后慢(上凸分布),这与试验结果(如图7)及文献1"31的观点一致。
活塞内腔某特征点的Von-mise应力变化,如图5所示。
其应力在冷却过程中急剧变化,应力先增大后减小,极值约为240MPa;在加热过程中应力先减小至冷却前的状态并保持至加热结束,最终应力约为20MPa。
将有限元计算结果导入到FE—Fatigue软件中使用其E—N法计算出活塞寿命分布,寿命分布,如图6所示。
活塞破坏位置在冷却油道与活塞内腔过渡圆角处,循环寿命为18.2次。
£300.
芒
§250.
盘
200.
150.
50.100.150.200.
Time(s)
图4特征点温度变化曲线
Time(s)
图5特征点Von—raise应力变化曲线
图6活器疲劳寿命分布
4试验验证
采用和数值模拟相同的热边界条件在激光热负荷试验台上做活塞低周热疲劳试验,监测点温度变化,如图7所示。
活塞经过26次循环出现可监测裂纹,起始裂纹位置在活塞冷却油腔进油道口处,如图8所示。
软件预测与疲劳试验活塞最危险区域一致,预测的绝对寿命与试验存在一些误差,这是由于热疲劳本身的复杂性及材料的分散性造成的。
02004006008001000
Time(s)
图7试验监测点温度变化曲线
图8活塞起始裂纹位置
珊瑚瑚瑚瑚瑚姗啪姗
万方数据
万方数据。