双头铺放轨迹后处理技术研究
双摆台五坐标铣削后置处理软件Star-Fpost研究
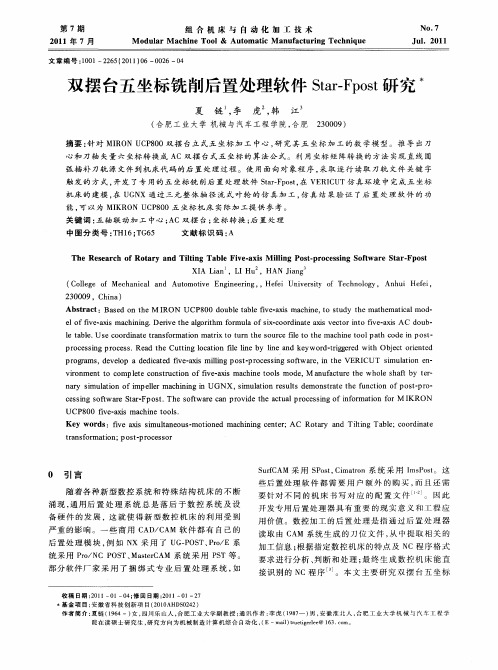
Ab ta t s r c :Ba e n t RON CP8 0 d u l a l v - xsm a hne t t d h a h m aia o ・ s d o heM I U 0 o b et b ef e a i c i , o s u y t em t e tc l i m d e ff - xsm a hii g D ei et e ag rt m o mul fsx c r i t xsve t ri t ve a sA C o b- lo ve a c n n . rv h lo ih f r i i a o i-oo dna ea c o o f - x i n i i d u
XI Lin A a ,L ,HAN i n IHu Ja g
( o ee o c ai lad A t oi n ier g , e iU i r t o eh ooy A h iH fi C l g fMeh nc n uo t e E gnei , H f n esy fT cn l , n u ee, l a m v n e v i g
第 7期 21 0 1年 7月
组 合 机 床 与 自 动 化 加 工 技 术
M o l r M a h ne To l& Aut m a i a uf t i c ni ue du a c i o o tc M n acurng Te h q
NO. 7
J 1 0 1 u .2 1
p o e s gp o es R a h tiglct n f el eb iea dk y r - igrdwi jc o i td r c si r c s . e d teCu t ai l i y l n e wod t g ee t Obe t r n e n n o o i n n r h e
涤纶长丝FDY卷绕机产生绊丝的原因探讨

的 导 丝器 ; 丝束 在 GR 2绕丝 圈数 由 6. 5圈 减 少 至 在压辊的摩擦力作用下易形成塌边或凸肚 。由于改
5. 5圈 ;调整了分丝辊 SR2 的 NESON 角 ,使丝束之 间分丝明显 。卷绕头上 、下拉杆由齿轮 、齿条式改为
造后丝饼数量要增加一倍 ,而卷绕头外观和卡盘轴 长度均没有变化 ,必然导致卷绕动程缩减 ,在此卷绕
行调整 ,两叶片和三叶片的磨损情况进行仔细检查
并择差更换 。
2. 5 横动电机
卷绕机在运行过程中 ,横动传动装置由横动电
机传动 ,横动电机的工作状况也是产生绊丝的原因
之一 。首先 ,由于双头改造后 ,拨叉由 8个大拨叉改
贵州电子科技职业学院2021年数控设备应用与维护论文题目
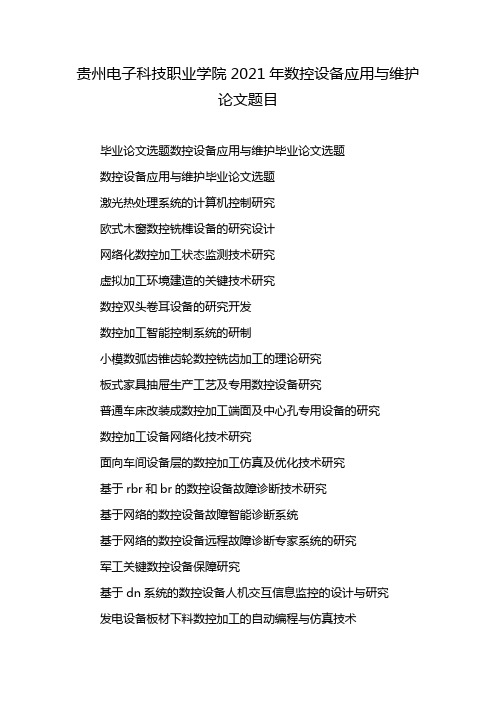
贵州电子科技职业学院2021年数控设备应用与维护论文题目毕业论文选题数控设备应用与维护毕业论文选题数控设备应用与维护毕业论文选题激光热处理系统的计算机控制研究欧式木窗数控铣榫设备的研究设计网络化数控加工状态监测技术研究虚拟加工环境建造的关键技术研究数控双头卷耳设备的研究开发数控加工智能控制系统的研制小模数弧齿锥齿轮数控铣齿加工的理论研究板式家具抽屉生产工艺及专用数控设备研究普通车床改装成数控加工端面及中心孔专用设备的研究数控加工设备网络化技术研究面向车间设备层的数控加工仿真及优化技术研究基于rbr和br的数控设备故障诊断技术研究基于网络的数控设备故障智能诊断系统基于网络的数控设备远程故障诊断专家系统的研究军工关键数控设备保障研究基于dn系统的数控设备人机交互信息监控的设计与研究发电设备板材下料数控加工的自动编程与仿真技术大直径筒体数控切管设备的研制可重构的数控设备远程诊断维护平台研究七坐标数控纤维铺放设备的控制系统及铺放头的研制车间设备集成控制系统中数控机床状态监测的研究数控设备产品质量监控系统设计塑性成形设备开放式数控系统及其关键技术研究数控激光加工教学实验设备的研究基于/s结构的数控设备网络化监控系统研究基于数控设备的制造资源重构的研究成批轮番生产方式下的数控设备组生产率研究基于pma球头立铣刀刃磨设备数控系统管理软件的开发研究数控设备管理信息系统的应用开发与研究应用于数控系统嵌入式1inux设备驱动程序的研究欧式木窗暗斜椎数控加工设备与仿真研究数控设备维修管理及其故障诊断系统研究m基于eb的数控设备管理及故障诊断系统的研究全自动数控u型钢辊弯设备控制系统的研制制锁设备专用数控系统研究。
自动铺带技术研究现状
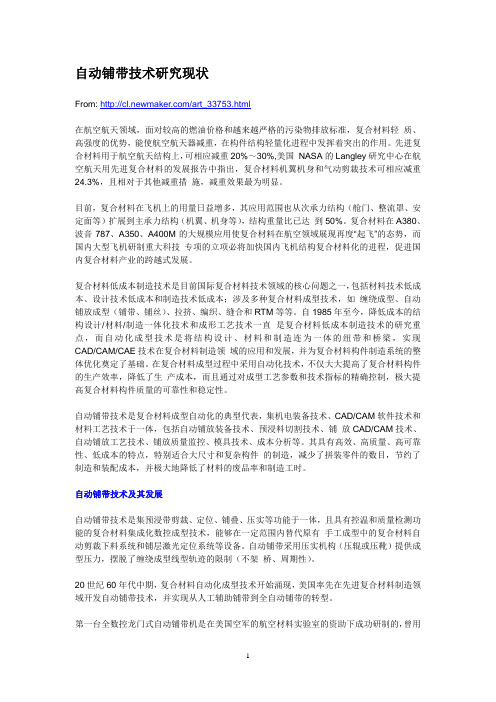
自动铺带技术研究现状From: /art_33753.html在航空航天领域,面对较高的燃油价格和越来越严格的污染物排放标准,复合材料轻质、高强度的优势,能使航空航天器减重,在构件结构轻量化进程中发挥着突出的作用。
先进复合材料用于航空航天结构上,可相应减重20%~30%,美国 NASA的Langley研究中心在航空航天用先进复合材料的发展报告中指出,复合材料机翼机身和气动剪裁技术可相应减重24.3%,且相对于其他减重措施,减重效果最为明显。
目前,复合材料在飞机上的用量日益增多,其应用范围也从次承力结构(舱门、整流罩、安定面等)扩展到主承力结构(机翼、机身等),结构重量比已达到50%。
复合材料在A380、波音787、A350、A400M的大规模应用使复合材料在航空领域展现再度“起飞”的态势,而国内大型飞机研制重大科技专项的立项必将加快国内飞机结构复合材料化的进程,促进国内复合材料产业的跨越式发展。
复合材料低成本制造技术是目前国际复合材料技术领域的核心问题之一,包括材料技术低成本、设计技术低成本和制造技术低成本;涉及多种复合材料成型技术,如缠绕成型、自动铺放成型(铺带、铺丝)、拉挤、编织、缝合和RTM等等。
自1985年至今,降低成本的结构设计/材料/制造一体化技术和成形工艺技术一直是复合材料低成本制造技术的研究重点,而自动化成型技术是将结构设计、材料和制造连为一体的纽带和桥梁,实现CAD/CAM/CAE技术在复合材料制造领域的应用和发展,并为复合材料构件制造系统的整体优化奠定了基础。
在复合材料成型过程中采用自动化技术,不仅大大提高了复合材料构件的生产效率,降低了生产成本,而且通过对成型工艺参数和技术指标的精确控制,极大提高复合材料构件质量的可靠性和稳定性。
自动铺带技术是复合材料成型自动化的典型代表,集机电装备技术、CAD/CAM软件技术和材料工艺技术于一体,包括自动铺放装备技术、预浸料切割技术、铺放CAD/CAM技术、自动铺放工艺技术、铺放质量监控、模具技术、成本分析等。
双头车床在生产实践中常用的排除故障方法

双头车床在生产实践中常用的排出故障方法双头车床在生产实践中常用的排出故障方法。
1、直观检查法直观检查法是维护和修理人员依据对故障发生时的各种光、声、味等异常现象的察看,确定故障范围,可将故障范围缩小到一个模块或一块电路板上,然后再进行排出。
一般包括:A、询问:向故障现场人员认真询问故障产生的过程、故障表象及故障后果等;B、目视:总体查看机床各部分工作状态是否处于正常状态,各电控装置有无报警指示,局部查看有无保险烧断,元器件烧焦、开裂、电线电缆脱落,各操作元件位置正确与否等等;C、触摸:在整机断电条件下可以通过触摸各紧要电路板的安装情形、各插头座的插接情形、各功率及信号导线的联接情形以及用手摸并轻摇元器件,尤其是大体积的阻容、半导体器件有无松动之感,以此可检查出一些断脚、虚焊、接触不良等故障;D、通电:是指为了检查有无冒烟、打火,有无异常声音、气味以及触摸有无过热电动机和元件存在而通电,一旦发觉立刻断电分析。
假如存在破坏性故障,必需排出后方可通电。
例:一台双头车床加工中心在运行一段时间后,CRT显示器蓦地显现无显示故障,而机床还可连续运转。
停机后再开又一切正常。
察看发觉,设备运转过程中,每当发生振动时故障就可能发生。
初步判定是元件接触不良。
当检查显示板时,CRT显示蓦地消失。
检查发觉有一晶振的两个引脚均虚焊松动。
重新焊接后,故障除去。
2、初始化复位法一般情况下,由于瞬时故障引起的系统报警,可用硬件复位或开关系统电源依次来清除故障。
若系统工作存贮区由于掉电、拨插线路板或电池欠压造成混乱,则必需对系统进行初始化清除,清除前应注意作好数据拷贝记录,若初始化后故障仍无法排出,则进行硬件诊断。
例:一台双头车床当按下自动运行键,微机拒不执行加工程序,也不显示故障自检提示,显示屏幕处于复位状态(只显示菜单)。
有时手动、编辑功能正常,检查用户程序、各种参数正确;有时因记忆电池失效,更换记忆电池等,系统显示某一方向尺寸超量或各方向的尺寸都超zui(显示尺寸超过机床实斤能加工的zui大尺寸或超过系统能够认可的zui大尺寸)。
摆头转台加工中心五轴联动加工的后置处理与仿真验证_吴海兵
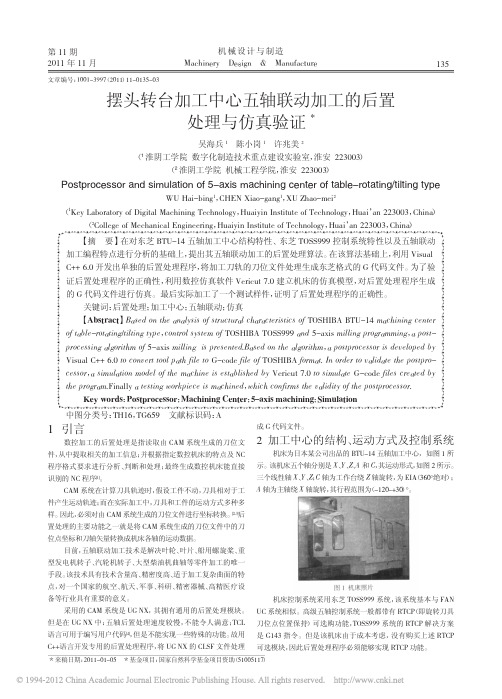
135
文章编号:1001-3997(2011)11-0135-03
摆头转台加工中心五轴联动加工的后置
处理与仿真验证 *
吴海兵 1 陈小岗 1 许兆美 2 (1 淮阴工学院 数字化制造技术重点建设实验室,淮安 223003)
(2 淮阴工学院 机械工程学院,淮安 223003)
Postprocessor and simulation of 5-axis machining center of table-rotating/tilting type
比如海德汉 iTNC530 的 M126 指令。机床控制系统没有内置的最
短距离旋转的指令,因此后置处理程序还要能够实现 C 轴最短距 离旋转功能。如上所述,C 轴旋转特性为 EIA(360°绝对),即 C 转角 的正负号定义旋转方向(正号逆时针旋转,符号顺时针旋转),C 转 角的绝对值定义绝对位置。3.2.2 计算出来的 C 角显然只确定了刀
手段。该技术具有技术含量高、精密度高、适于加工复杂曲面的特
点,对一个国家的航空、航天、军事、科研、精密器械、高精医疗设
图 1 机床照片
备等行业具有重要的意义。
机床控制系统采用东芝 TOSS999 系统,该系统基本与 FAN
采用的 CAM 系统是 UG NX,其拥有通用的后置处理模块。 UC 系统相似。高级五轴控制系统一般都带有 RTCP(即旋转刀具
中图分类号:TH16,TG659 文献标识码:A
1 引言
数控加工的后置处理是指读取由 CAM 系统生成的刀位文 件,从中提取相关的加工信息;并根据指定数控机床的特点及 NC 程序格式要求进行分析、判断和处理;最终生成数控机床能直接 识别的 NC 程序[1]。
CAM 系统在计算刀具轨迹时,假设工件不动,刀具相对于工
- 1、下载文档前请自行甄别文档内容的完整性,平台不提供额外的编辑、内容补充、找答案等附加服务。
- 2、"仅部分预览"的文档,不可在线预览部分如存在完整性等问题,可反馈申请退款(可完整预览的文档不适用该条件!)。
- 3、如文档侵犯您的权益,请联系客服反馈,我们会尽快为您处理(人工客服工作时间:9:00-18:30)。
DOI: 10.12677/ms.2017.79102 785
( ( (
) ) )
(1)
材料科学
王显峰 等
2 2 2 2 2 x0 + y0 + z0 = a2 ± a3 + d4
(
) + a + 2(a ±
2 2 1 2
2 2 a3 + d4 a1c2
Keywords
Automated Fiber Placement, Dual-Robot, Similar Rotation Component, Reachable Workspace, Trajectory Distribution
双头铺放轨迹后处理技术研究
王显峰,梁 涛,肖 军
南京航空航天大学复合材料工程自动化技术研究中心,江苏 南京
关键词
自动铺放,双工位,类转体,可达空间,轨迹分配
Copyright © 2017 by authors and Hans Publishers Inc. This work is licensed under the Creative Commons Attribution International License (CC BY). /licenses/by/4.0/
2 2
2.2. 铺丝头的干涉约束
图 1(a)中铺丝头姿态部分手腕长度为 215 mm,自身长度 685 mm,姿态部分总长为 900 mm。将整个 姿态部分近似为图 4(a)中所示区域进行简化计算,为了避免与地面和底座的干涉,运动空间与地面距离 需要设置 500 mm 的下限,还需要在机器人底座区域截取一个 650 mm × 900 mm 的矩形区域,如图 4(b) 所示,并将此区域带入到工作空间中,舍去重叠部分。
)
(2)
另外,将包络面根据 θ1 值的变化划分为若干层,使三维空间的包络面转化为二维空间的包络曲线进 行分析[18]。当 θ1 = 0 时,三维机构退化为 xoz 的二维平面机构,可以进一步简化运算。由于模具在铺放 过程中始终处于两个机器人的单侧位置,因此机器人不会出现背对模具的情况,可以舍去背部的包络空 间。综上,得到机器人可达空间的一条包络曲线,如图 3 所示。该包络曲线的表达式可以将各连杆参数 代入式(4)中得到。
P = 1P 2 : ( x − 350 ) + ( y − 675 )
2 2
(1150 +
2
412 + 10002
)
2
P2 P3 : ( x − ( 350 + 1150 ⋅ cos 5 ) ) + ( y − ( 675 + 1150 ⋅ sin 5 ) ) =412 + 10002
2
P3 P4 : ( x − 350 ) + ( y − 675 ) = 4722
王显峰 等
进行研究,提出了一个满足协调约束的轨迹预选机制。在确定了双机器人横向移动的配合方案后,以机 器人平台可达空间的限制作为约束条件,通过夹角控制对铺丝轨迹进行配对编码并验证。同时得到完整 模具的轨迹分配方案,将CAD软件生成的铺放信息转化成机器人角度的加工文件。文中模型证明所提方 法满足大型类回转体构件铺放生产的工艺要求,大大提高了铺放效率。
Open Access
1. 引言
多工位机器人协作系统已广泛应用在焊接领域,其具有设备成本较低、占用空间小,工作效率高, 运动灵活的特点。伴随复合材料在航空航天领域的广泛应用,自动铺丝技术已成为高性能复合材料复杂 构件的主流制造技术[1] [2] [3] [4], 使用机器人作为模块化铺放头的搭载平台的双头铺放系统可满足铺放 大型复材构件,兼顾复材构件的复杂度与高生产率铺放。但是由于复合材料构件形状复杂,这对多工位 铺丝机器人的铺丝轨迹分配、位姿协调控制提出了更高的要求。 相对于单个机器人系统而言,双机器人系统具有更高的灵活性和可靠性,能够完成更为复杂的任务 [5] [6]。 同时双机器人的协作任务也面临更为复杂的控制问题, 如双机器人系统的路径规划问题[7] [8] [9], 机器人之间的避碰问题[10] [11] [12]等。近年来国内外研究人员已提出许多有效的控制策略[13],主要包 括动力学控制和运动学控制两种方法,其中运动学协调控制是目前较实用的方法。早期研究更多的是通 过控制主机器人的位置而从机器人采用跟踪控制来协调其运动学约束关系的主/从控制方法[14]。后来, 针对较复杂任务中同时需要兼顾力与位置的协调,提出了一种混合力与位置的控制方法,通过分别控制 各机器人末端执行器的位置及外加力使其保持所需的运动约束关系[15]。 本文从铺放机器人协调空间约束 出发, 以较复杂的类转体构件的铺放成型为研究对象, 研究双机器人协调完成此类作业的运动规划问题, 提出在时间和空间上两个机器人协调运作的轨迹分配方法。 在 CAD 生成加工轨迹加工文件后, 以双机器 人系统的有效工作行程为动态约束进行轨迹再分配,降低后置处理难度。
Figure 3. A enveloping curve 图 3. 一条包络曲线
DOI: 10.12677/ms.2017.79102
786
材料科学
王显峰 等
3. 双头铺放轨迹分配策略
3.1. 两轨迹可铺放配对的判定
对于双头铺放系统而言,其铺放轨迹的分配是一个复杂的问题,主要涉及到双机器人有效工作行程 的限制。根据铺放任务的特定需求,施压气缸对压辊提供压力使其与铺放模具表面接触,为了使压力完 全均匀地作用于模具表面,一般情况下都是保证气缸的施压方向与机械臂末端坐标系的接近矢量同向。 由于这一特殊的末端姿态约束条件,在工作时必须保证实时铺放轨迹点模具处延伸面同时位于两侧机器 人腕点的可达包络空间内,图 5 所示。 具体计算步骤如下: (1) 原始轨迹信息的参考坐标系为 catia 数模的坐标系,该坐标系与机器人基坐标系各轴指向可能不 同。因此,在验证运算之前需要先对轨迹数据进行预处理,建立新的模具坐标系{B}(主轴坐标系)使得各 轴指向与机器人基坐标系保持一致, 坐标原点在模具回转轴线上。 将包络模型转化到主轴坐标系下表示, 简化位置关系的计算。设模具信息变换矩阵为 B I T ,对于空间某点 ( x, y , z ) ,该点在主轴坐标系下的坐标
Figudiagram 图 2. KUKA 机器人 D-H 连杆机构图
将 A4/A5/A6 三轴交点(第三杆末端)记为 P4org, 其位置仅与机器人前三个关节转角相关, 将点 P4org 的所有可达点的集合记为工作空间。
a2
x = a ± a2 + d 2 c c + a c 2 3 4 1 2 1 1 0 2 2 GP4 = y0 = a2 ± a3 + d4 s1c2 + a1 s1 z = a ± a2 + d 2 s 2 3 4 2 0
Research on Post-Processing Technique for Double-Heads Automated Placement
Xianfeng Wang, Tao Liang, Jun Xiao
R & D Center for Composites Industry Automation, NUAA, Nanjing Jiangsu Received: Dec. 3 , 2017; accepted: Dec. 19 , 2017; published: Dec. 28 , 2017
2. 双头铺放系统行程范围计算
2.1. 坐标系的建立及包络方程的求解
模块化的铺丝头与机器人通过法兰盘连接(图 1(a)),可以随时更换调试,能够更好地适应繁复的铺放 环境。图 1(b)中展示了由两台工业机器人组成的双工位铺放系统。 本文所采用的 KR 系列工业机器人结构示意,如图 2 所示,其后三关节轴线交于一点。判断模具是 否可铺首先要计算机器人的工作能力, 即末端执行器可达区域的最大范围曲面[16]。 机器人工作空间正问 题的求解方法一般有图解法、解析法和数值法三种。为了确定机器人工作空间旋转体的边界曲面和边界 曲线,本文基于曲面包络和包络叠加的计算方法[17],在解析法的基础上充分利用位姿解耦的特点,辅之 以图示求解简化运动包络的解析计算。
收稿日期:2017年12月3日;录用日期:2017年12月19日;发布日期:2017年12月28日
摘
要
为提升自动铺放装备工作效率并提高铺丝机工作的灵活度,对双机器人协同的类转体构件铺丝成型技术
文章引用: 王显峰, 梁涛, 肖军. 双头铺放轨迹后处理技术研究[J]. 材料科学, 2017, 7(9): 783-790. DOI: 10.12677/ms.2017.79102
rd th th
Abstract
In order to improve the rate and kinematic dexterity of automated fiber placement system technology, a dual-robot collaborative placement of similar rotation component is studied, and the method of primary trajectory that fits the constraints of coordination is put forward. After determination of the matching scheme for the longitudinal feed of the robot, the AFP trajectory is paired by the Angle control, under the constraint of the robot platform’s full reachable workspace. At the same time, the track distribution scheme of the complete mould is obtained, and the information generated by CAD software is transformed into the machining document of robot Angle. This paper proves that the proposed method meets the process requirements of the production of large class gyro member, which greatly improves the laying efficiency.