精馏塔精馏段温度串级系统方案
过程控制工程课程设计参考题目

过程控制工程课程设计参考题目(总5页)--本页仅作为文档封面,使用时请直接删除即可----内页可以根据需求调整合适字体及大小--14级过程控制课程设计题目1班课程设计参考题目:一、温度控制(单回路、串级、前馈—反馈、比值控制)(40)1、换热器出口温度单回路控制方案设计2、乳化物干燥器温度单回路控制方案设计3、精馏塔提馏段温度单回路控制方案设计4、管式加热炉出口温度单回路控制方案设计5、夹套式反应器温度单回路控制控制方案设计6、燃烧式工业窑炉温度单回路控制方案设计7、精馏塔精馏段温度单回路控制方案设计8、流化床反应器温度单回路控制方案设计9、管式热裂解反应器出口温度单回路控制方案设计10、发酵罐温度单回路控制方案设计11、换热器出口温度串级控制方案设计12、乳化物干燥器温度串级控制方案设计13、精馏塔提馏段温度串级控制方案设计14、管式加热炉出口温度串级控制方案设计15、夹套式反应器温度串级控制控制方案设计16、燃烧式工业窑炉温度串级控制方案设计17、精馏塔精馏段温度串级控制方案设计18、流化床反应器温度串级控制方案设计19、发酵罐温度串级控制方案设计20、管式热裂解反应器出口温度串级控制方案设计21、换热器出口温度前馈—反馈控制方案设计22、乳化物干燥器温度前馈—反馈控制方案设计23、精馏塔提馏段温度前馈—反馈控制方案设计24、管式加热炉出口温度前馈—反馈控制方案设计25、夹套式反应器温度前馈—反馈控制控制方案设计26、燃烧式工业窑炉温度前馈—反馈控制方案设计27、精馏塔精馏段温度前馈—反馈控制方案设计28、流化床反应器温度前馈—反馈控制方案设计29、发酵罐温度前馈—反馈控制方案设计30、管式热裂解反应器出口温度前馈—反馈控制方案设计31、换热器出口温度比值控制方案设计32、乳化物干燥器温度比值控制方案设计33、精馏塔提馏段温度比值控制方案设计34、管式加热炉出口温度比值控制方案设计35、夹套式反应器温度比值控制方案设计36、燃烧式工业窑炉温度比值控制方案设计37、精馏塔精馏段温度比值控制方案设计38、流化床反应器温度比值控制方案设计39、发酵罐温度比值控制方案设计40、管式热裂解反应器原料油与蒸汽流量比值控制方案设计41、锅炉出口蒸汽压力单回路控制方案设计42、锅炉出口蒸汽压力串级控制方案设计43、锅炉出口蒸汽压力前馈—反馈控制方案设计44、锅炉出口蒸汽压力比值控制方案设计45、炉膛负压单回路控制方案设计46、炉膛负压前馈—反馈控制方案设计47、离心泵压力定值控制方案设计2班课程设计参考题目:1、换热器出口温度单回路控制方案设计2、乳化物干燥器温度单回路控制方案设计3、精馏塔提馏段温度单回路控制方案设计4、管式加热炉出口温度单回路控制方案设计5、夹套式反应器温度单回路控制控制方案设计6、燃烧式工业窑炉温度单回路控制方案设计7、精馏塔精馏段温度单回路控制方案设计8、流化床反应器温度单回路控制方案设计9、管式热裂解反应器出口温度单回路控制方案设计10、发酵罐温度单回路控制方案设计11、换热器出口温度串级控制方案设计12、乳化物干燥器温度串级控制方案设计13、精馏塔提馏段温度串级控制方案设计14、管式加热炉出口温度串级控制方案设计15、夹套式反应器温度串级控制控制方案设计16、燃烧式工业窑炉温度串级控制方案设计17、精馏塔精馏段温度串级控制方案设计18、流化床反应器温度串级控制方案设计19、发酵罐温度串级控制方案设计20、管式热裂解反应器出口温度串级控制方案设计21、换热器出口温度前馈—反馈控制方案设计22、乳化物干燥器温度前馈—反馈控制方案设计23、精馏塔提馏段温度前馈—反馈控制方案设计24、管式加热炉出口温度前馈—反馈控制方案设计25、夹套式反应器温度前馈—反馈控制控制方案设计26、燃烧式工业窑炉温度前馈—反馈控制方案设计27、精馏塔精馏段温度前馈—反馈控制方案设计28、流化床反应器温度前馈—反馈控制方案设计29、发酵罐温度前馈—反馈控制方案设计30、管式热裂解反应器出口温度前馈—反馈控制方案设计31、换热器出口温度比值控制方案设计32、乳化物干燥器温度比值控制方案设计33、精馏塔提馏段温度比值控制方案设计34、管式加热炉出口温度比值控制方案设计35、夹套式反应器温度比值控制方案设计36、燃烧式工业窑炉温度比值控制方案设计37、精馏塔精馏段温度比值控制方案设计38、流化床反应器温度比值控制方案设计39、发酵罐温度比值控制方案设计40、管式热裂解反应器原料油与蒸汽流量比值控制方案设计41、锅炉出口蒸汽压力单回路控制方案设计42、锅炉出口蒸汽压力串级控制方案设计43、锅炉出口蒸汽压力前馈—反馈控制方案设计44、锅炉出口蒸汽压力比值控制方案设计45、炉膛负压单回路控制方案设计46、炉膛负压前馈—反馈控制方案设计47、离心泵压力定值控制方案设计课程设计教材及主要参考资料:1、戴连奎,《过程控制工程》,化学工业出版社,20122、杜维,《过程检测技术及仪表》,化学工业出版社,20013、姜培正,《过程流体机械》,化学工业出版社,20024、王毅,《过程装备控制技术与应用》,化学工业出版社,20015、厉玉鸣,《化工仪表及自动化》,化学工业出版社,2006一、课程设计教学目的及基本要求:1.课程设计的教学目的培养学生将理论知识应用到解决实际问题的能力,通过该课程的学生,可以很好地训练学生的实际动手能力和解决工程问题的能力,为学生从学校到工厂和技术部门提供前期的训练。
常用串级和分程控制(介绍)

概述
解决办法:再加入一个蒸汽流量控制系统,可控制 流量稳定。
FC
TC
问题:两套控制系统不能协调,甚至出现矛盾
温度控制系统要求增加或减小蒸汽流量,而流量控制 系统却只能根据事先的流量设定值进行定值控制。
概述
串级控制系统:两套控制系统的协调控制
FC
TC
特点:两个控制器,一个调节阀
- PID正反作用确定 . 先确定副控制器 调节阀选为气开型(故障关FC),特性为正作用; 流
量偏大时,阀门流通量应少, 对象特性为反作用; 所以 PID控制器应选正作用;
调节阀选为气关型(故障关FO),特性为反作用, PID控制器应选反作用;
串级控制系统
. 再确定主控制器 主控制器PID特性,不再需要考虑阀门特性和
一个控制器(主控制器)的输出送到另一个控制器 (副控制器)的给定,副控制器的输出送到控制阀ຫໍສະໝຸດ 述温度控制器流量控制器
控制阀
流量变送器
温度变送器
流量对象
温度对象
特点:两个闭环环路,内环和外环 内环:副环,副控制器、副对象、副变送器 (流量) 外环:主环,主控制器、主对象、主变送器 (温度)
概述
主环,定值控制系统,给定值由工艺设定,主控制
例:精馏塔提馏段温度控制系统 1)副环干扰 2)主环干扰
串级控制系统的特点
串级系统具有一定的自适应能力
自适应问题:控制器的参数往往是根据一定的控制对象设置的, 当控制对象特性发生变化时(非线性特性,操作条件变化、负 荷变化),原来好的控制器参数就变得不好了(不适应了) 串级系统中,副控制系统是随动系统,主控制器可根据操作条 件的变化,不断修改副控制器的给定值——自适应能力 “能力有限”,自适应控制(现代控制技术)
精馏塔温度控制

❖ 主变量:塔釜温度 副变量:再沸腾蒸汽进 口流量 主控制器:温度控制器
副控制器:流量控制器
工艺对象:精馏塔
化工仪表自动化PPT
苯+甲苯精馏
串级控制系统就是两只调节器串联起来工作,其中 一个调节器的输出作为另一个调节器的给定值的系 统。整个系统包括两个控制回路,主回路和副回路。 副回路由副变量检测变送、副调节器、
调节阀和副过程构成;主回路由主变量检测变送、 主调节器、副调节器、调节阀、副过程和动。二次扰动:作用在副被控 过 程上的,即包括在副回路范围内的扰动。
工艺要求:控制塔内 温度.
控制规律的选择
主控制器:PID 副控制器:P
系统方框图
检测变送
❖ 精馏塔的主要干扰因素 为进料状态,即进料流 量、进料组分、进料温 度或热焓
执行器
▪ 气开式 ▪ 正作用 ▪ 主调节器:反作用 ▪ 副调节器:反作用
温度调节器
精馏段或提馏段的某些塔 板上,温度变化量最为显 著。或者说,这些塔板的 温度对外界干扰因素的反 映最灵敏,故将这些塔板 称之为灵敏板。将感温元 件安置在灵敏板上可以较 早觉察精馏操作所受到的 干扰;而且灵敏板比较靠 近进料口,可在塔顶馏出 液组成尚未产生 变化之前 先感受到进料参数的变动 并即使采取调节手段,以 稳定馏出液的组成。
谢谢观赏
精馏塔精馏段温度串级系统
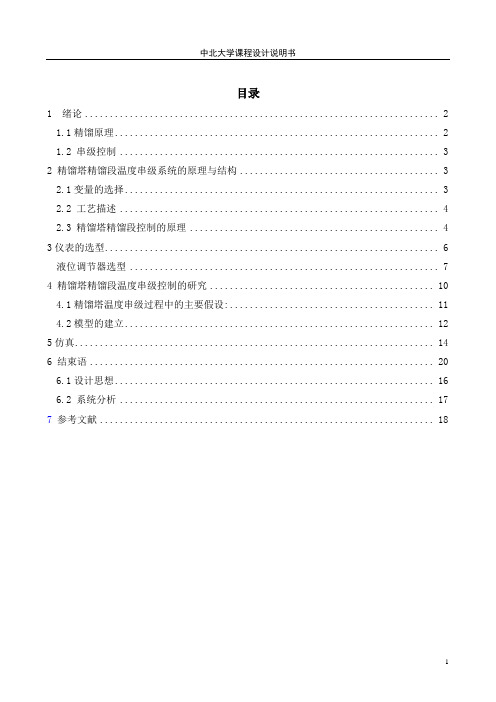
目录1 绪论 (2)1.1精馏原理 (2)1.2 串级控制 (3)2 精馏塔精馏段温度串级系统的原理与结构 (3)2.1变量的选择 (3)2.2 工艺描述 (4)2.3 精馏塔精馏段控制的原理 (4)3仪表的选型 (6)液位调节器选型 (7)4 精馏塔精馏段温度串级控制的研究 (10)4.1精馏塔温度串级过程中的主要假设: (11)4.2模型的建立 (12)5仿真 (14)6 结束语 (20)6.1设计思想 (16)6.2 系统分析 (17)7 参考文献 (18)1 绪论精馏是石油化工、炼油生产过程中的一个十分重要的环节,其目的是将混合物中各组分分离出来,达到规定的纯度。
精馏过程的实质就是迫使混合物的气、液两相在塔体中作逆向流动,利用混合液中各组分具有不同的挥发度,在互相接触的过程中,液相中的轻组分逐渐转入气相,而气相中的重组分则逐渐进入液相,从而实现液体混合物的分离。
一般精馏装置组成,如图1所示。
由精馏塔、再沸器、冷凝器、回流罐等设备[1]图 1 简单精馏控制示意图进料流量F 从精馏塔中段某一塔板上进入塔内,这块塔板称为进料板。
进料板将精馏塔分为上下两段,进料板以上部分称为精馏段,进料板以下部分称为提馏段。
溶液中组分的数目可以是两个或两个以上。
实际工业生产中,只有两个组分的溶液不多,大量需要分离的溶液往往是多组分溶液。
多组分溶液的精馏在基本原理方面和两组分溶液的精馏是一样的。
1.1精馏原理在恒定压力下,单组分液体在沸腾时虽然继续加热,其温度却保持不变,即单组分液体的沸点是恒定的。
对于两组分的理想溶液来说,在恒定压力下,其沸点却是可变的。
例如对于A、B 两种混合物的分馏,纯A 的沸点是140℃,纯B 的沸点是175℃。
如果两组分的混合比发生变化,混合溶液的沸点也随之发生变化,如图2中的液相曲线所示。
图 2设原溶液中A 占20%,B 占80%,此混合液的沸点是164.5℃,加热使混合液体沸腾。
这时,与液相共存的气相组分比是A 占45.8%,B 占54.2%。
串级控制系统的原理及设计

串级控制系统的原理及设计中应注意的问题摘要:介绍了串级控制系统的基本原理,性能和设计中应注意的几个问题。
关键词:内环;外环;增益;时间常数;对象;共振现象;积分饱和现象。
1、概述1.1串级控制系统介绍单回路控制系统只用一个调节器,调节器只有一个输入信号,即只有一个闭环,在大多数情况下,这种简单系统能够满足工艺生产的要求。
但是也有一些另外的情况,譬如调节对象的动态特性决定了它很难控制,而工艺对调节质量的要求又很高;或者对调节对象的控制任务要求特殊,则单回路控制系统就无能为力了。
另外,随着生产过程向着大型、连续和强化方向发展,对操作条件要求更加严格,参数间相互关系更加复杂,对控制系统的精度和功能提出许多新的要求,为此,需要在单回路的基础上,采取其他措施,组成复杂控制系统。
串级控制是改善调节过程的一种极为有效的方法,并且在实际中得到了广泛的应用。
我厂的生产过程自动控制系统中,串级控制系统是应用最为广泛的复杂控制系统。
1.2(简单控制系统)图1.1是精馏塔底部示意图,在再沸器中,用蒸汽加热塔釜液产生蒸汽,然后在塔釜中与下降物料流进行传质传热。
为了保证生产过程顺利进行,需要把提馏段温度t保持恒定。
为此,在蒸汽管路上装一个调节阀,用它来控制加热蒸汽流量。
从调节阀动作到温度t发生变化,需要相继通过很多热容积。
实践证明,加热蒸汽压力的波动对温度t的影响很大。
此外,还有来自液相加料方面的各种扰动,包括他的流量、温度和组分等,它们通过提馏段的传质传热过程,以及再沸器中的传热条件(塔釜温度、再沸器液面等),最后也影响到温度t。
当加热蒸汽压力较大时,如果采用图1.1所示的简单控制系统,调节质量一般都不能满足生产要求。
如果采用一个附加的蒸汽压力控制系统,把蒸汽压力的干扰克服在入塔前,这样也提高了温度调节的品质,但这样就需要增加一只调节阀并增加了蒸汽管路的压力损失,在经济上很不合理。
比较好的方法是采用串级控制,如图1.2所示。
精馏塔常用的一些控制方案

精馏塔常用的一些控制方案塔的作用是在同一个设备中进行质量和热量的交换,是石油化工装置非常重要的设备。
塔的型式有板式塔(泡罩塔、浮阀塔、栅板塔等)、填料塔(高效填料、常规填料、散装填料、规整填料等)、空塔。
塔由筒体和内件组成。
蒸馏塔由精馏段和提馏段组成,进料口以上是精馏段,进料口以下是提馏段。
精馏塔的控制方案主要从塔压、釜温、顶温、塔釜液面四个方面来说明:1.精馏操作中塔压的控制调节方法塔的压力是精馏塔主要的控制指标之一。
任何一个精馏塔的操作,都应当把塔压控制在规定的指标内,以相应地调节其它参数。
塔压波动过大,就会破坏全塔的物料平衡和气液平衡,使产品达不到所要求的质量。
所以,许多精馏塔都有其具体的措施,确保塔压稳定在适宜范周内。
对于加压塔的塔压,主要有以下三种调节方法(1)塔顶冷凝器为分凝器时,塔压一般是靠气相采出量来调节的,如图6-1所示。
在其它条件不变的情况下,气相采出量增大,塔压下降,气相采出量减小,塔压上升。
(2)塔顶冷凝器为全凝器时,塔压多是靠冷剂量的大小来调节,即相当于调节回流液温度,如图6-2所示。
在其它条件不变的前提下,加大冷剂量,则回流液的温度降低,塔压降低,若减少冷剂量,回流液温度上升,塔压上升。
(3)热旁通(浸没式)法调节塔压。
对于常压塔的压力控制,主要有以下三种方法(1)对塔顶压力在稳定性要求不高的情况下,无需安装压力控制系统,应当在精馏设备(冷凝器或回流罐)上设置一个通大气的管道,以保证塔内压力接近于大气压。
(2)对塔顶压力的稳定性要求较高或被分离的物料不能和空气接触时,塔顶压力的控制可采用加压塔塔压的控制方法,如图6-1、图6-2。
(3)用调节塔釜加热蒸汽量的方法来调节塔釜的气相压力,如图6-6所示。
2.精馏操作中塔釜温的控制调节方法釜温是由釜压和物料组成决定的。
精馏过程中,只有保持规定的釜温,才能确保产品质量。
因此釜温是精馏操作中重要的控制指标之一。
当釜温变化时,通常是用改变蒸发釜的加热蒸汽量,将釜温调节至正常,见图6-7a、图6-7b。
精馏塔提馏段温度控制系统.doc
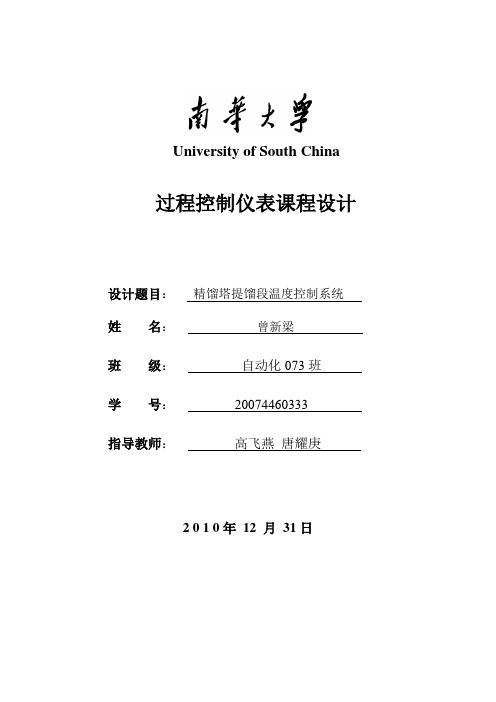
University of South China过程控制仪表课程设计设计题目:精馏塔提馏段温度控制系统**:***班级:自动化073班学号:***********指导教师:高飞燕唐耀庚2 0 1 0年12 月31日1、系统简介精馏操作是炼油、化工生产过程中的一个十分重要的环节。
精馏塔的控制直接影响到工厂的产品的质量、产量和能量的消耗,因此精馏塔的自动控制长期以来一直受到人们的高度重视。
精馏塔是一个多输入多输出的对象,它由很多级塔板组成,内在机理复杂,对控制要求又大多较高。
这些都给自动控制带来一定的困难。
同时各塔工艺结构特点有千差万别,这需要深入分析特性,结合具体塔的特点,进行自动控制方案设计和研究。
精馏塔的控制最终目标是:在保证产品质量的前提下,使回收率最高,能耗最小,或使总收益最大。
在这个情况为了更好实现精馏的目标就有了提馏段温度控制系统的产生。
按提馏段指标的控制方案:当塔釜液为主要产品时,常常按提馏段指标控制。
如果是液相进料,也常采用这类方案。
这是因为在液位相进料时,进料量的变化,首先影响到塔底产品浓度,塔顶或精馏段塔板上的温度不能很好地反映浓度的变化,所以采用提馏段控制温度比较及时。
另外如果对釜底出料的成分要求高于塔顶出料,塔顶或精馏段板上温度不能很好反映组分变化和实际操作回流比大于几倍最小回流比时,可采用提馏段控制。
提馏段温度是衡量质量指标的间接指标,而以改变再沸器加热量作为控手段的方案,就是提馏段温控。
2、设计方案及仪表选型2.1控制方案的确定图2-1是精馏塔底部示意图,在再沸器中,用蒸汽加热塔釜液产生蒸汽,然后在塔釜中与下降物料进行传热传质。
为了保证生产过程顺利进行,需要把提馏段温度θ。
保持恒定。
为此在蒸汽管路上装上一个调节阀,用它来控制加热蒸汽流量。
从调节阀的做到温度θ发生变化,需要相继通过很多热容积。
实践证明,加热蒸汽压力的波动对θ的影响很大。
此外,还有来自液相加料方面的各种干扰,包括它的流量、温度和组分等,它们通过提馏段的传质过程,以及再沸器中传热条件(塔釜温度、再沸器液面等),最后也影响到温度θ。
串级控制系统
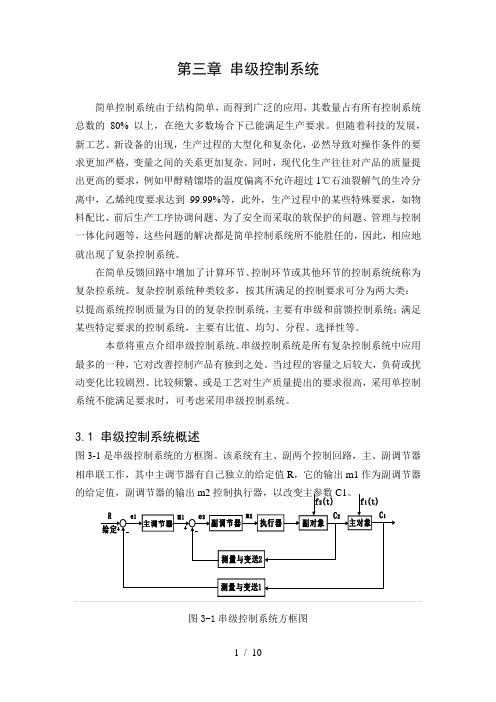
第三章串级控制系统简单控制系统由于结构简单,而得到广泛的应用,其数量占有所有控制系统总数的80% 以上,在绝大多数场合下已能满足生产要求。
但随着科技的发展,新工艺、新设备的出现,生产过程的大型化和复杂化,必然导致对操作条件的要求更加严格,变量之间的关系更加复杂。
同时,现代化生产往往对产品的质量提出更高的要求,例如甲醇精馏塔的温度偏离不允许超过1℃石油裂解气的生冷分离中,乙烯纯度要求达到99.99%等,此外,生产过程中的某些特殊要求,如物料配比、前后生产工序协调问题、为了安全而采取的软保护的问题、管理与控制一体化问题等,这些问题的解决都是简单控制系统所不能胜任的,因此,相应地就出现了复杂控制系统。
在简单反馈回路中增加了计算环节、控制环节或其他环节的控制系统统称为复杂控系统。
复杂控制系统种类较多,按其所满足的控制要求可分为两大类:以提高系统控制质量为目的的复杂控制系统,主要有串级和前馈控制系统;满足某些特定要求的控制系统,主要有比值、均匀、分程、选择性等。
本章将重点介绍串级控制系统。
串级控制系统是所有复杂控制系统中应用最多的一种,它对改善控制产品有独到之处。
当过程的容量之后较大,负荷或扰动变化比较剧烈、比较频繁、或是工艺对生产质量提出的要求很高,采用单控制系统不能满足要求时,可考虑采用串级控制系统。
3.1 串级控制系统概述图3-1串级控制系统方框图3.2 串级控制系统的特点串级控制系统从总体来看,仍然是一个定制控制系统,因此主变量在扰动作用下的过渡过程和简单定制控制系统的过渡过程具有相同的品质指标和类似的形式。
但是串级控制系统和简单控制系统相比,在结构上增加了一个与之相连的副回路,因此具有一系列特点。
由于副回路的存在,改善了过程的动态特性提高了系统的工作频率。
串级控制系统在结构上区别于接单控制系统的主要标志是用一个闭合的副回路代替了原来的一部分被控对象。
所以,也可以把整个副回路看作是主回路的一个环节,或把副回路称为等效副对象。
精馏塔精馏段温度串级系统方案
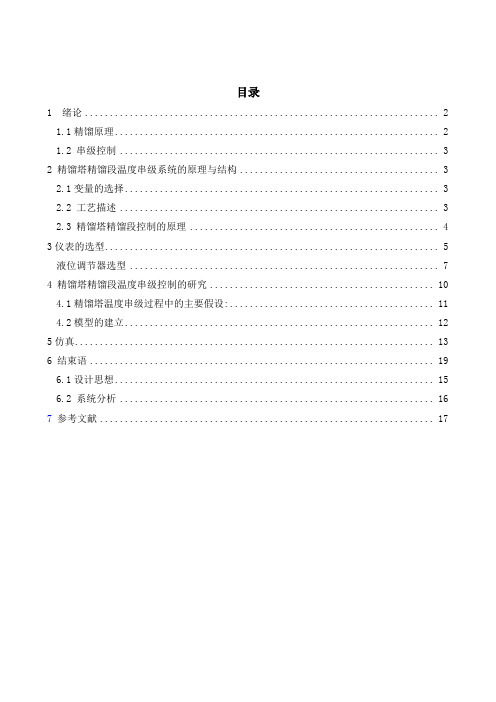
目录1 绪论 (2)1.1精馏原理 (2)1.2 串级控制 (3)2 精馏塔精馏段温度串级系统的原理与结构 (3)2.1变量的选择 (3)2.2 工艺描述 (3)2.3 精馏塔精馏段控制的原理 (4)3仪表的选型 (5)液位调节器选型 (7)4 精馏塔精馏段温度串级控制的研究 (10)4.1精馏塔温度串级过程中的主要假设: (11)4.2模型的建立 (12)5仿真 (13)6 结束语 (19)6.1设计思想 (15)6.2 系统分析 (16)7 参考文献 (17)1 绪论精馏是石油化工、炼油生产过程中的一个十分重要的环节,其目的是将混合物中各组分分离出来,达到规定的纯度。
精馏过程的实质就是迫使混合物的气、液两相在塔体中作逆向流动,利用混合液中各组分具有不同的挥发度,在互相接触的过程中,液相中的轻组分逐渐转入气相,而气相中的重组分则逐渐进入液相,从而实现液体混合物的分离。
一般精馏装置组成,如图1所示。
由精馏塔、再沸器、冷凝器、回流罐等设备[1]图 1 简单精馏控制示意图进料流量F 从精馏塔中段某一塔板上进入塔,这块塔板称为进料板。
进料板将精馏塔分为上下两段,进料板以上部分称为精馏段,进料板以下部分称为提馏段。
溶液中组分的数目可以是两个或两个以上。
实际工业生产中,只有两个组分的溶液不多,大量需要分离的溶液往往是多组分溶液。
多组分溶液的精馏在基本原理方面和两组分溶液的精馏是一样的。
1.1精馏原理在恒定压力下,单组分液体在沸腾时虽然继续加热,其温度却保持不变,即单组分液体的沸点是恒定的。
对于两组分的理想溶液来说,在恒定压力下,其沸点却是可变的。
例如对于A、B 两种混合物的分馏,纯A 的沸点是140℃,纯B 的沸点是175℃。
如果两组分的混合比发生变化,混合溶液的沸点也随之发生变化,如图2中的液相曲线所示。
图 2设原溶液中A 占20%,B 占80%,此混合液的沸点是164.5℃,加热使混合液体沸腾。
这时,与液相共存的气相组分比是A 占45.8%,B 占54.2%。
过程控制课程设计-精馏塔温度控制系统
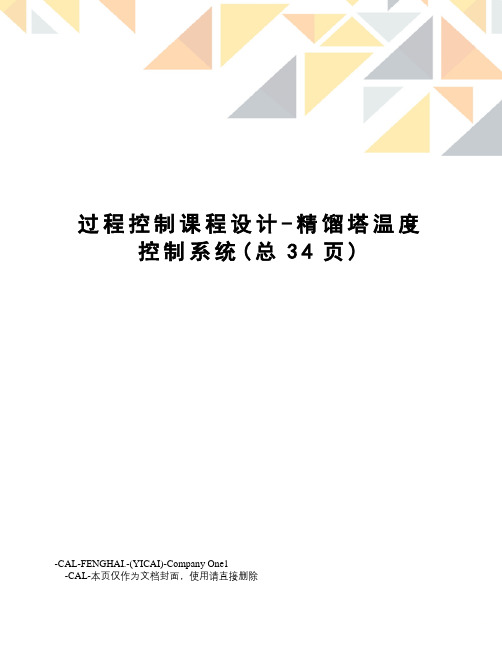
过程控制课程设计-精馏塔温度控制系统(总34页)-CAL-FENGHAI.-(YICAI)-Company One1-CAL-本页仅作为文档封面,使用请直接删除过程控制系统与仪表课程设计目录一、研究对象........................................................................................... 错误!未定义书签。
二、研究任务........................................................................................... 错误!未定义书签。
三、仿真研究要求 (4)四、传递函数计算 (5)五、控制方案........................................................................................... 错误!未定义书签。
1. 单回路反馈控制系统 (6)1) 控制方案的系统框图和工艺控制流程图............................... 错误!未定义书签。
2) PID参数整定 (7)3) 系统仿真................................................................................... 错误!未定义书签。
4) 对象特性变化后仿真 (12)2. Smith预估补偿控制系统 ................................................................ 错误!未定义书签。
1) 控制方案的系统框图和工艺控制流程图............................... 错误!未定义书签。
2) 控制系统方框图....................................................................... 错误!未定义书签。
串级调节对精馏塔塔釜温度的控制
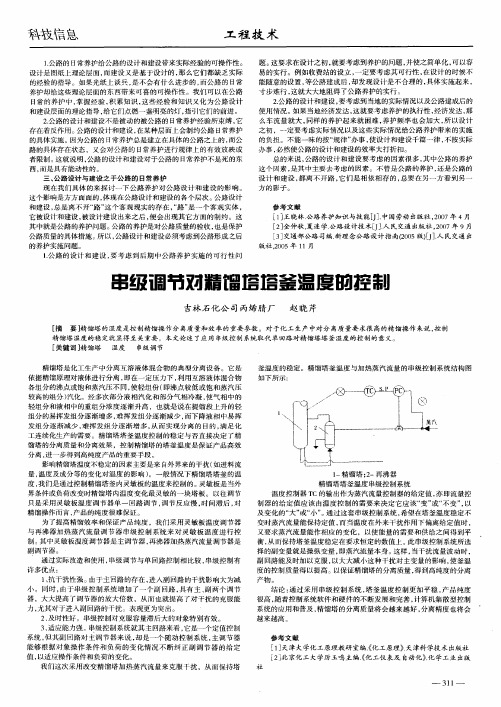
串 级 调 节 对 精 馏 塔 塔 釜 温 度 的 控 制
吉林 石化 公 司 丙烯腈厂 赵 晓 芹
[ 摘 要] 精馏塔的 温度是控制精馏操作分 离质量和效率 的重要 参数 。对于化工生产 中对 分离质量要求很高的精馏操作 来说 , 控制
精 馏 塔 温度 的稳 定就 显得 至 关重 要 。本 文 论 述 了应 用 串级 控 制 系统取 代 单 回路 对精 馏 塔 塔 釜 温度 的控 制 的意 义 。 [ 关键词 ] 精馏塔 温度 串级调 节
科技信息.
工 程 技 术
题。 这要求在设计之初 , 就要考虑到养护的问题 , 并使之简单化 , 以容 可 易 的实行 。例如收费站的设立 , 一定要考 虑其 可行性 , 在设计的时候不 能随意的设置 , 等公路建成后 , 却发现设计是 不合理 的 , 具体实施起来 , 寸步难行 , 这就大大地阻碍 了公路养护的实行 。 2公路 的设计和建设 , . 要考虑到当地的实际情 况以及公路建成后的 使用情况 。 如果当地经济发达 , 这就要考虑养护 的执行性 , 经济发达 , 那 么车流量 就大 , 同样 的养护起来 就困难 , 养护频 率也会加大 , 以设计 所 之初 ,一定要考虑实际情况 以及这些实际情 况给公路 养护带来 的实施 的负担。不能一味的按“ 规律” 办事 , 使设计和建设千篇 一律 , 不按实际 办事 , 必然使公路 的设计 和建设 的效率大 打折扣 。 总的来说 , 公路的设 计和建设要考虑 的因素很 多 , 中公路的养护 其 这个因素 , 是其中主要去考虑的 因素 。不管是公路 的养护 , 还是公路的 设计和建设 , 都离不开路 , 它们是相 依相存的 , 总要 在另一方看 到另一
方的影子。
1 . 公路的 日常养护给公路 的设计和建设带来实际经验的可操作性 。 设计是图纸上理论层 面, 而建设 又是基于设计 的 , 那么它们都缺乏实际 的经验的指导。如果光纸上谈兵 , 是不会有什 么进步的 , 而公路 的 日常 养护却给这些 理论层面 的东西带来可 喜的可操作 性 。我们可 以在公路
精馏塔提馏段的温度控制设计
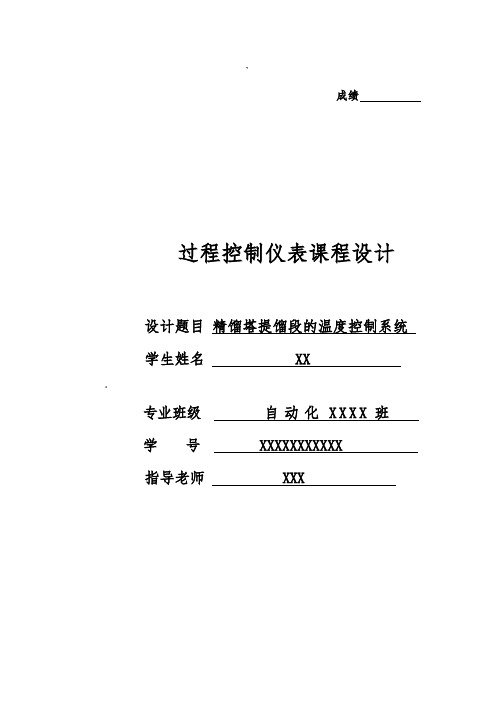
、成绩过程控制仪表课程设计设计题目精馏塔提馏段的温度控制系统学生姓名 XX ,专业班级自动化X X X X班学号 XXXXXXXXXXX指导老师 XXX2019年XX月XX日{《过程控制仪表》课程设计评分标准表姓名:XX 学号:XXXXXXXXX课程设计的最终成绩采取“优秀”、“良好”、“中等”、“及格”和“不及格”五级记分。
100-90分(优秀)、89-80(良好)、79-70(中等)、69-60(及格)、低于60(不及格)《过程控制仪表课程设计》任务书目录1.设计任务与要求 (1)设计任务 (1)设计要求 (1)2.系统简介 (1)3.设计方案及仪表选型 (2)控制方案的确定 (2)系统原理及方框图 (3)仪表选型 (4)4.系统仿真分析 (10)5.控制系统仪表配接图及说明 (13)6.仪表型号清单 (13)7.总结 (13)参考文献 (14)1.设计任务与要求设计任务过程控制仪表课程设计,是《自动化仪表与装置》课程中的后续课程,实践教学环节,也是一次全面的专业知识的运用和实践。
⑴巩固和深化所学课程的知识:通过课程设计,要求学生初步学会运用本门课程和其它相关课程的基本知识和方法,来解决工程实际中的具体的设计问题,检验学生对本门课程及相关课程内容的掌握的程度,以进一步巩固和深化所学课程的知识。
⑵培养学生的设计、实践能力:通过课程设计,从方案选择、设计计算到绘制图纸、编写设计说明书,可以培养学生对工程设计的独立工作能力,树立正确的设计思想,掌握自动控制系统中各环节使用仪表的基本方法和步骤,为以后从事工程设计打下良好的基础。
⑶使学生能熟悉和运用设计资料,学会查阅相关文献,如有关国家标准、手册、图册等,以完成作为工程技术人员在工程设计方面所必须的基本训练。
设计要求(1)编写过程控制仪表设计说明书。
内容包括:控制系统的简单介绍,工艺流程分析;各环节仪表的选型、仪表的工作原理及性能指标;控制系统的仿真分析;仪表间的配接说明。
精馏塔精馏段温度控制设计方案
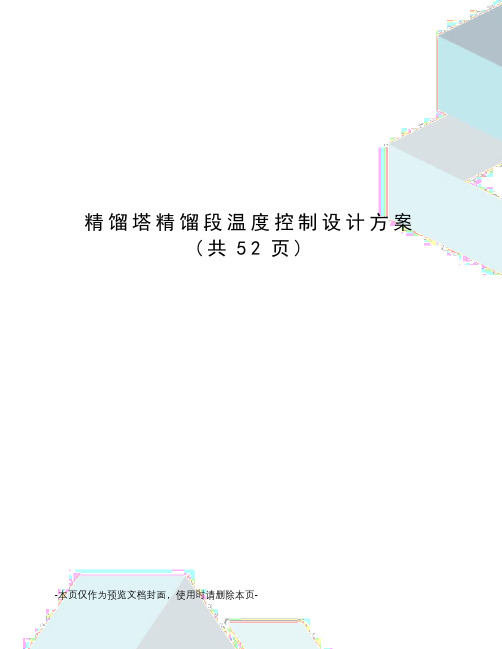
精馏塔精馏段温度控制设计方案(共52页)-本页仅作为预览文档封面,使用时请删除本页-精馏塔精馏段温度控制设计方案1.课题研究的背景和意义石油化工生产常需将液体混合物分离以达到提纯或回收有用组分的目的。
分离互溶液体混合物有许多种方法,精馏是在炼油、化工等众多生产过程中广泛应用的一个传质过程。
精馏过程通过反复的汽化与冷凝,使混合物料中的各组分分离,分别达到规定的纯度。
精馏塔的控制直接影响到产品质量、产量和能量消耗,因此精馏塔的自动控制问题长期以来一直受到人们的高度重视[1]。
精馏过程是由精馏装置来实现的,精馏装置一般是由精馏塔、再沸器(重沸器)、冷凝冷却器、回流罐及回流泵等组成。
实际生产过程中,精馏操作可分为间歇精馏和连续精馏两种。
石油化工等大型生产过程主要采用的连续精馏。
精馏塔是进行精馏的一种塔式汽液接触装置,又称为蒸馏塔。
有板式塔与填料塔两种主要类型。
根据操作方式又可分为连续精馏塔与间歇精馏塔。
蒸溜的原理是蒸气由塔底进入。
蒸发出的气相与下降液进行逆流接触,两相接触中,下降液中的易挥发(低沸点)组分不断地向气相中转移,气相中的难挥发(高沸点)组分不断地向下降液中转移,气相愈接近塔顶,其易挥发组分浓度愈高,而下降液愈接近塔底,其难挥发组分则愈富集,从而达到组分分离的目的。
由塔顶上升的气相进入冷凝器,冷凝的液体的一部分作为回流液返回塔顶进入精馏塔中,其余的部分则作为馏出液取出。
塔底流出的液体,其中的一部分送入再沸器,加热蒸发成气相返回塔中,另一部分液体作为釜残液取出。
精馏塔是一个多输入多输出的多变量过程,其内在机理复杂,动态响应迟缓,变量之间相互关联,不同的塔工艺结构差别很大,而工艺对控制提出的要求又较高,所以确定精馏塔的控制方案是一个极为重要的课题[1]。
2.课题研究的现状随着生产过程向着大型、连续和强化方面发展,对操作条件要求更加严格,参数间相互关系更加复杂,对控制系统的精度和功能提出许多新的要求,对能源消耗和环境污染也有明确的限制,采用传统的单回路PID控制往往不能达到控制要求,为此,需要在简单控制系统的基础上,采取其他设施,组成复杂控制系统,也称多回路控制系统。
过程控制工程-17精馏塔的控制ppt课件

精馏塔系统特点: MIMO系统、相互关联、机理复杂、动态响应迟缓 、能耗大 -〉控制要求高
17.1 概述
机理
F,zf
冷剂
LD L
D,xD V
热剂 二元精馏系统
LB 釜液,B,xB
17.1.1 精馏塔的基本关系
物料平衡、能量平衡 二元精馏系统
17.3 精馏塔被控变量的选择
压力补偿温度
温度控制恒定时,压力的微小波动,对产品的成分影 响很大
(1) 直接压力补偿
P Kp TT
KpO z=T-Kp+KpO
17.3 精馏塔被控变量的选择
(2) 温差控制 压力的变化,塔顶各板的温度同时变化,某两点温差控制, 可 消除压力影响,关键是温差的取值大小。
第17章
精馏塔的控制
17.1 概述 17.2 精馏塔的特性 17.3 精馏塔被控变量的选择 17.4 精馏塔的整体控制方案 17.5 精馏塔的新型控制方案
教学进程
17.1 概述
机理
利用混合物中各组分的挥发度(沸点)不同,或在 相同温度下,各组分的蒸汽分压不同,轻组分(液相 中)和重组分(汽相中)相互转移
● 间接指标——温差控制
在精密蒸馏时,要求产品纯度很高,组份之间的相对挥发度差异很小, 组份变化引起的温度变化有时比压力变化引起的温度变化还小,∴对 塔压控制要求很严格。
17.3 精馏塔被控变量的选择
温度点位置 ●塔顶分离物为产品时,温度放在塔顶——精馏段控制 ●塔底分离物为产品时,温度放在塔底——提馏段控制 ●有时为了兼顾塔顶、塔底产品,可以取进料板温度 ●塔顶温度受压力限制,变化很小,因而,有时取灵敏板温度
精馏塔提馏段串级控制系统设计1111111

目录引言 ··········································································错误!未定义书签。
第一章精馏塔的自动控制 ················································错误!未定义书签。
1.1 控制目的·······························································错误!未定义书签。
- 1、下载文档前请自行甄别文档内容的完整性,平台不提供额外的编辑、内容补充、找答案等附加服务。
- 2、"仅部分预览"的文档,不可在线预览部分如存在完整性等问题,可反馈申请退款(可完整预览的文档不适用该条件!)。
- 3、如文档侵犯您的权益,请联系客服反馈,我们会尽快为您处理(人工客服工作时间:9:00-18:30)。
目录1 绪论 (1)1.1精馏原理 (2)1.2 串级控制 (3)2 精馏塔精馏段温度串级系统的原理与结构 (3)2.1变量的选择 (3)2.2 工艺描述 (3)2.3 精馏塔精馏段控制的原理 (4)3仪表的选型 (5)液位调节器选型 (7)4 精馏塔精馏段温度串级控制的研究 (10)4.1精馏塔温度串级过程中的主要假设: (11)4.2模型的建立 (12)5仿真 (14)6 结束语 (17)6.1设计思想 (17)6.2 系统分析 (17)7 参考文献 (18)1 绪论精馏是石油化工、炼油生产过程中的一个十分重要的环节,其目的是将混合物中各组分分离出来,达到规定的纯度。
精馏过程的实质就是迫使混合物的气、液两相在塔体中作逆向流动,利用混合液中各组分具有不同的挥发度,在互相接触的过程中,液相中的轻组分逐渐转入气相,而气相中的重组分则逐渐进入液相,从而实现液体混合物的分离。
一般精馏装置组成,如图1所示。
由精馏塔、再沸器、冷凝器、回流罐等设备[1]图 1 简单精馏控制示意图进料流量F 从精馏塔中段某一塔板上进入塔,这块塔板称为进料板。
进料板将精馏塔分为上下两段,进料板以上部分称为精馏段,进料板以下部分称为提馏段。
溶液中组分的数目可以是两个或两个以上。
实际工业生产中,只有两个组分的溶液不多,大量需要分离的溶液往往是多组分溶液。
多组分溶液的精馏在基本原理方面和两组分溶液的精馏是一样的。
1.1精馏原理在恒定压力下,单组分液体在沸腾时虽然继续加热,其温度却保持不变,即单组分液体的沸点是恒定的。
对于两组分的理想溶液来说,在恒定压力下,其沸点却是可变的。
例如对于A、B 两种混合物的分馏,纯A 的沸点是140℃,纯B 的沸点是175℃。
如果两组分的混合比发生变化,混合溶液的沸点也随之发生变化,如图2中的液相曲线所示。
图 2设原溶液中 A 占20%,B 占80%,此混合液的沸点是164.5℃,加热使混合液体沸腾。
这时,与液相共存的气相组分比是A 占45.8%,B 占54.2%。
这些气体单独冷凝后所形成的混合液体中,A 占45.8%,B 占54.2%;如果使此冷凝后的混合液体沸腾,其沸点是154.5℃。
这时气相组分比又变成A 占73.5%,B 占26.5%,这样反复进行上述操作,不断蒸发和冷凝,最终出来。
就可将A 分离[2]1.2 串级控制串级控制是改善调节质量极为有效的方法,在过程控制中得到了广泛的应用。
对精馏塔精馏段温度串级控制系统引起出口温度的因素很多:被加热流量的和温度的扰动,压力的波动、热质的变化,回流量的扰动等,而对这些扰动单回路控制系统并不能把所有的干扰都包含进去,不能是出口温度稳定在要求的值上,为解决上述滞后时间和控制要求之间的矛盾,保持出口流量温度的恒定,可以通过温度串级控制系统来实现。
2 精馏塔精馏段温度串级系统的原理与结构单回路控制系统能解决工业过程自动化过程的大量参数定值控制问题。
对于多数复杂控制系统,如多输入多输出系统、大滞后系统和扰动较大的系统等简单控制系统就很难控制,控制要求。
串级控制系统在改善复杂控制系统的控制指标方面具有较无法满足控制系统的[3]大的优势。
2.1变量的选择被控变量的选择对于二元精馏塔,当塔压恒定时,温度与成分之间有一一对应的关系,因此,常用温度作为被控量。
对于多元精馏塔.由于石油化工过程中精馏产品大多数是碳氢化合物的同系物。
在一定塔压下,温度与成分之间仍有较好的对应关系。
误差较小。
因此。
绝大多数精馏塔当塔压恒定时采用温度作为间接质量指标。
操纵变量的选择精馏段的温度控制精馏段温度控制以精馏段产品的质量为控制目标.在恒压下根据温度检测点的位置不同。
有塔顶温度控制、灵敏板温度控制和中温控制等类型。
操纵变量可选择回流量或塔顶采出量。
而回流量L的动态响应快,温度稍有变化,即可通过调节回流量L加以精馏塔精馏段影响。
控制,能够很好的克服扰动对选择如图1所示在[]42.2 工艺描述影响精馏塔提馏段过程的因素是多方面的,而精镏段是在一定物料平衡和能量平衡的基础上进行操作的,分析精馏塔的无聊和能量平衡对制定精馏塔精馏段的控制至关重要。
关系。
精馏塔的基本[4]以二元简单精馏为例,介绍物料平衡和能量平衡的基本关系。
物料平衡: f B D Bz x D F x x -=- (2-1) D F增大,D x ,B x 减小。
式中 F ,D ,B ——进料、顶馏出液和底馏出液量;f z , B x , D x ——进料、顶馏出液和底馏出液中轻组分含量。
能量平衡:V ln F s β= (2-2) 式中分离度1x )x (1)D B B D x s x -=-(,s 增大,D x 增大,B x 减小。
说明塔系统分离效果增大β为塔特性因子,V 为上升蒸汽量,是有再沸器施加热量来提高的。
V F 增大,分离效果增大,能耗增大。
对于一个既定的塔,进料组分一定,D F 和V F一定,D x B x 完全确定。
分析精馏塔提馏段过程,本文对主回路采用串级控制系统,其主、副诃节器所起作用各有侧重。
主调节器起定值控制作用,且主控参数(提馏段温度)允许波动围很小,一般要求无余差,因此采用需要高精度的免疫PID 控制器;由于再沸器加热量的变化能够较快地反映在提馏段温度变化上,且能够通过阀门进行控制,因此选择回流罐的液位量控制作为串级控制的副控参数。
在串级控制中,副调节器起随动控制作用,且副控参数的调节也是为了保证主控参数的控制质量,可以有一定的余差,因此副调节器采用P 调节器。
由于进料量和进料温度对进料馏段温度影响较大。
2.3 精馏塔精馏段控制的原理我们的控制目的是使塔温保持恒定,现选用精馏段的温度, 与回流量来构成串级随动控制.如图3所示 图中TC 表示温度调节器,LC 表示量调节器液位调节器,TC 通常按PID 调节规律,流量调节器按P 调节规律。
当温度发生变化时,由主调节器( 温度调节器TC )进行控制,其输出作为副调节器(液位调节器LC )的给定值,最终控制阀门的开度,主控回路的输出作为副控回路设定值修正的依据,副控回路的输出作为真正的控制量作用于被控对象,液位一旦发生变化,副控回路及时地控制阀门的开度位置,较快地克服了液位的变化对出料温度的影响 如果液位是恒定的,只需测量实际温度,并使其与温度设定值相比较,利用二者的偏差控制管道上的阀门就能保持温度的恒定。
路中,以补偿过程的动态特性,使被控对象的滞后时间τ超前反映到控制器,有效地解决了大惯性环节的时间滞后问题,减少了系统的超调量,加速了系统的调节过程,另外,通过增大液位调节器的比例增益,系统的等效时间常数可以频率。
获得较小的数值,从而增加了副控回路的响应速度,提高了系统的工作[5]在这个计算机串级随动控制系统中,串级控制起到了及时检测系统中可能引起被控量发生变化的一些因素并加控制,阀位与流量得到了及时的调节,使塔温的控制达到了良好的控制效果,并且使系统具有一定的自适应能力,有效地解决了对象的等效纯滞后时间 很长的问题。
二次干扰为该系统的主要扰动,副控回路有效而快速地克服二次扰动的影响。
当扰动发生在副回路,例如液位发生波动引起精馏段的温度变化时,由于有副控回路的存在,液位调节器能及时地动作,快速消除了扰动的影响;当扰动发生在副控回路以外时,如物料、能量的转输变化引起提馏段的温度变化,温度调节器及时改变其输出信号,由副控回路去改影响。
变流量,克服了扰动[6]图3 精馏塔精馏段温度串级控制系统3仪表的选型过程控制系统一般都是负反馈控制系统,主要由被控对象、传感器和变送器、控制器和执行机构等四部分组成。
其中,传感器与变送器属于检测仪表,控制器和执行机构则属于控制仪表。
检测与控制仪表是过程控制系统的基本组成部分,是实现生产过程自动化必不可少的工具。
检测仪表将生产工艺参数变为电流信号或气压信号后,不仅要求由显示仪表显示或记录,让人们了解生产过程的情况,还需要将信号传送给控制仪表,对生产过程进行自动控制,使工艺参数符合预期要求。
检测仪表将生产过程中有关的工艺参数准确及时地测量出来,并转换为标准信号如0~10mA DC 电流信号,4~20mA DC 电流信号或20~100kPa示仪表。
的气压信号,送往控制仪表或显[7]温度控制(调节器)SR3-8I选型型表SR1/SR3/SR4 0.3级PID调节器选[8]温度变送器变送器如果由两个用来测量温差的传感器组成,输出信号与温差之间有一给定的连续函数关系。
故称为温度变送器。
变送器输出信号与温度变量之间有一给定的连续函数关系(通常为线性函数),早期生产的变送器其输出信号与温度传感器的电阻值(或电压值)之间呈线性函数关系。
标准化输出信号主要为0mA~10mA和4mA~20mA(或1V~5V)的直流电信号。
不排除具有特殊规定的其他标准化输出信号。
变送器有电动单元组合仪表系列的(DDZ-Ⅱ型、DDZ-Ⅲ型和DDZ-S型)和小型化模块式的,多功能智能型的。
前者均不带传感器,后两类变送器可以方便的与热电偶或热电阻组成带传感器的变送器。
所以在次选用DDZ-III型变送器。
热电偶温度变送器技术指标[9]冷端温度补偿:-15~+75℃输出电流:4~20mA输出回路供电:12~30VDC最小工作电压:12VDC负载电阻与供电电源的关系:负载电阻(包括引线电阻)=供电电源(V)-12(V)/0.02A ※综合参数标准精度:±0.2%温度漂移:基本误差/10℃热电阻引线补偿:±0.1%(0~10Ω)负载变化影响:±0.1%(允许负载围)电源变化影响:±0.1%(12~30V)开机响应时间:<1S(0~90%)工作环境温度:-20~+70℃防护等级:IP00/IP54(传感器防护等级决定)电磁兼容:符合IEC61000,EN61000液位调节器选型参数液位调节器主要[9]1、测量围:0—6000mm2、测量精度:±10mm3、介质密度:≥0.5g/cm4、工作压力:1.0 1.6 2.5MPa5、工作温度:80℃ 120℃ 200℃6、介质粘度:≤0.4Pa.s(对粘度大或低温易结晶介质要选用夹套型)7、测量界位比重差:0.15g/cm液位变[10]送器液位变送器是对压力变送器技术的延伸和发展,根据不同比重的液体在不同高度所产生压力成线性关系的原理,实现对水、油及糊状物的体积、液高、重量的准确测量和传送主要技术指标测量围:0.3~100m(由用户自选)精度:0.2、0.5、1.0级工作温度:-20~200℃输出信号:二线制4~20mADC电源电压:标准24VDC(12~36VDC)不灵敏区:≤±1.0%FS负载能力:0-600Ω相对温度:≤85%防护等级:IP68防爆标志:ExiaⅡCT4-6调节阀选型1 ) 阀型的选择调节阀阀型最好选择功能齐全、重量轻的全功能超轻型调节阀去代替其他调节阀产品,可简化选用期货产品因功能不齐全而担心选型不当 ( 如直行程类阀的防堵问题;切断与压差的关系等 ) 的麻烦。