CJTKC说明书-G1
冠景电动工具产品说明书

OWNER’S MANUAL & OPERATING INSTRUCTIONS12039 Smith Ave.Santa Fe Springs CA 90670USA / 1-877-338-0999SAVE THESE INSTRUCTIONS Important Safety Instructions are included in this manual.MADE IN CHINAREV 14001-20180821ATV/UTV Winch Kit4000 lb.WARNING: Cancer and Reproductive Harm – *We are always working to improve our products. Therefore, the enclosed product may differ slightly from the image on the cover.ENGLISH14001 INTRODUCTIONIntroductionCongratulations on your purchase of a Champion Power Equipment winch. CPE designs and builds winches to strict specifications. With proper use and maintenance, this winch will bring years of satisfying service.This BookletEvery effort has been made to ensure the accuracy and completeness of the information in this manual. We reserve the right to change, alter and/or improve the product and this document at any time without prior notice. AccessoriesChampion Power Equipment manufactures and sells accessories designed to help you get the most from your purchase. To find out more about our covers, tree savers, hooks, fairleads, etc., please visit our web site at:Record the model and serial numbers as well as date and place of purchase for future reference. Have this information available when ordering parts and when making technical or warranty inquiries.114001ENGLISHThis manual uses the following symbols to help differentiate between different kinds of information. The safety symbol is used with a key word to alert you to potential hazards in operating and owning power equipment.Follow all safety messages to avoid or reduce the risk of serious injury or death.MANUAL CONVENTIONS23ENGLISH 14001SAFETY RULES14001ENGLISHSAFETY RULES4ENGLISH14001Read this owner’s manual before operating your winch. Familiarize yourself with the location and function of the controls and features. Save this manual for future reference.(1) Motor – 1.4 HP 12V DC motor providespower to the planetary gear mechanism. (2) Braking System – Braking action isautomatically applied to the winch drumwhen the winch motor is stopped andthere is a load on the wire rope.(3) Winch Drum – The winch drum is thecylinder on which the wire rope is stored.It can feed or wind the rope depending onthe remote winch switch.(4) Planetary Gear System – The reductiongears convert the winch motor power intoextreme pulling forces. This system allowshigh torque while maintaining compactsize and light weight.(5) Free spooling Clutch – The clutch allowsthe operator to manually disengage “Out”the spooling drum from the gear train, freespool. Engaging the clutch “In” locks thewinch into the gear system.(6) Mount Assembly – Flatbed mountingchannel. (7) Roller Fairlead – When using the winch atan angle the roller fairlead acts to guidethe wire rope onto the drum and minimizesdamage to the wire rope from abrasion onthe winch mount or bumper.(8) Wire Rope – 7/32 in. x 49 ft. galvanizedaircraft cable designed specifically for loadcapacity of 4000 lb. (1814 kg).(9) Winch Connection Cables – Used toconnect the contactor to the winch motor. (10) Battery Connection Cables – Used toconnect the battery to the contactor. (11) Clevis Hook – Provides a means forconnecting the looped ends of cables toan anchor.(12) Strap – Used to assist cable feed.(13) Contactor/solenoid – Power from thevehicle battery flows through the weathersealed contactor/solenoid switch beforebeing directed to the winch motor.(14) Rocker Switch – Rocker switch withhandlebar mount for powering the rope inor out of your winch drum.CONTROLS AND FEATURES5614001 ENGLISHASSEMBLYAssembling the WinchThis CPE 4000 lb. (1814 kg) winch is designed with a bolt pattern that is standard in this class of winch. Many winch mounting kits are available that utilize this bolt pattern for the most popular UTVs and ATVs. If you cannot find a kit locally, contact CPE and we will provide you with the name of a dealer.1. Insert M10x20 bolts through the mountingchannel holes and attach the roller fairlead to the mounting channel with the M10 lockwashers and M10 nuts provided.2. Turn the winch upside down. Place themounting channel on the winch, making sure the winch is centered in the middle of it.3. Thread the M8x25 bolts through the M8 flatand lockers washers, and then thread through the mounting channel. Tighten the bolts. DO NOT over tighten.4. Turn winch right side up. Disengage theclutch by moving the Cam Ring to the “Out” position. Release the wire rope and pull through the roller fairlead.5. Attach the clevis hook to the cable, and thenhand strap to the clevis hook.Assembling the Winch Cont’d.Contactor/solenoid LocationFind a location for the contactor/solenoid. It is recommended that the contactor/solenoid be mounted close to the battery in a clean, drylocation. Make sure the location chosen allows for sufficient clearance from all metal components. Drill mounting holes if required. Once a location is found, DO NOT install the unit until all wiring is completed (see wiring section).Installing the Rocker Switch1. Decide which handlebar the rocker switch willbe mounted on. (The rocker switch is usually installed on the left handlebar).2. Use a piece of electrical tape (not provided)around the handlebar to help prevent rotation of the mount.3. Tighten the rocker switch in place. DO NOTover tighten or tighten/clamp over any hoses or cables.4. Once the rocker switch is mounted, the wirescan be routed back to where the contactor/solenoid is located.5. Make sure the handlebars have full range ofmotion and then secure the rocker switch’scable with the supplied cable ties.7ENGLISH 14001ASSEMBLYLeads default position.Leads rotated 90º7. Once all wiring is connected to the contactor/solenoid it can then be mounted using the supplied M6 hardware.8. Tighten the contactor/solenoid terminal nuts.DO NOT over tighten.9. Connect the black lead to the negative (–)terminal of the vehicle’s 12 volt battery.10. Place all terminal boots over terminals andsecure all cables with cable ties or electrical tape (not included).11. Check for proper drum rotation. Pull and turnthe clutch knob to the “OUT” position (free spooling). Pull out some cable from the drum, and then turn the clutch knob to the “IN” position to engage the gears. Press the cable out button on the rocker switch. If the drum is turning and releasing more cable, then your connections are accurate. If the drum is turning and collecting more cable then reverse the leads on the motor. Repeat and check rotation.1. Connect the yellow and blue cables to themotor terminals on the winch. (Yellow to the positive (+) terminal of the motor. Blue to the negative (-) terminal of the motor). Tighten the terminal nuts on the motor. DO NOT over tighten. Route the other ends to the contactor/solenoid location.2. Connect the yellow and blue cables to thecontactor/solenoid (yellow to yellow and blue to blue). DO NOT tighten nuts.3. Connect the red and black cables to thecontactor/solenoid (red to red andblack to black). DO NOT tighten nuts. Route the other ends to the vehicle’s battery.4. Connect the red lead to the positive (+)terminal of the vehicle’s 12 volt battery. 5. Connect the rocker switch to the contactor/solenoid (black to black and green to green).6. Splice the end of the red wire on the rockerswitch, to an ignition (keyed) controlled power source using the supplied wire tap.Wiring the Winch Cont’d.Wiring the WinchTest Winch OperationWhen testing the winch for correct connections and operation.1. Make sure there are no exposed terminals orwiring.2. Wiring to all components is correct.3. All loose wires are secured.4. Turn the vehicle ignition switch to the ONposition, but DO NOT start the vehicle.5. Check the winch for proper operation usingthe rocker switch. The wire rope should spool in and out in the direction indicated on the switch.With some applications the motor leads may need to be rotated to avoid interference with other components.14001ENGLISHASSEMBLY Wiring Diagram8ENGLISH14001 OPERATIONGeneral Tips for Safe OperationYour 14001 winch is rated at a 4000 lb. capacity in first layer (max) when spooling the first rope layer on the drum. Overloads can damage the winch, motor and/or wire rope. For loads over2,000 lb. (907 kg.) we recommend the use of the pulley block/snatch block to double the wire rope line. This will aid in two ways:(a) reduce the number or rope layers on the drum,as well as,(b) reduce the load on the wire rope by as muchas 50%.When doubling the line back to the vehicle,attach to the tow hook, frame or other load bearing part. The vehicle engine should be kept running during operation of the winch to minimize battery drain and maximize power and speed of the winch. If the winch is used for a considerable time with the engine off the battery may be drained and too weak to restart the engine.Get to know your winch before you actually need to use it. We recommend that you set up a few test runs to familiarize yourself with rigging techniques, the sounds your winch makes under various loads, the way the cable spools on the drum, etc. Inspect the wire rope and equipment before each use. A frayed or damaged rope shall be replaced immediately. Use only manufacturer’s identical replacement rope with the exact specifications. Inspect the winch installation and bolts to ensure that all bolts are tight before each operation. Store the remote control inside your vehicle in a place that it will not be damaged.Any winch that appears to be damaged in any way, is found to be worn, or operates abnormally MUST BE REMOVED FROM SERVICE UNTIL REPAIRED. It is recommended that the necessary repairsbe made by a manufacturer’s authorized repair facility.Pull only on areas of the vehicle as specified by the vehicle manufacturer. Only attachments and/ or adapters supplied by the manufacturer are to be used.Self RecoveryLocate a suitable anchor such as a strong tree trunkA roller fairlead (not included) will help guide the wire rope and to reduce binding on short side pulls. Do not winch from an acute angle as the wire rope will pile up on one side of the drumthe vehicle. Long pulls should be done with the wire rope at a 90° angle to the winch/vehicle.When pulling a heavy load, place a blanket or jacket In the event of a broken cable it will dampen the snap back. For additional protection open the hood of the vehicle. For pulls over 2,000 lb. (907 kg.), we recommend the use of the snatch block/ pulley block to double line the wire rope.914001ENGLISHOPERATIONWinching Techniques A-Z(a) Take time to assess your situation and planyour pull.(b) Put on gloves to protect your hands.(c) Disengage the clutch to allow free- spoolingand also save battery power.(d) Attach the hook strap to the clevis hook.(e) Pull out the wire rope to your desired anchorpoint using the hook strap.(f) Secure the clevis hook to the anchor point:Sling, chain or snatch block. Do not attachthe hook back onto the wire rope.(g) Engage the clutch.(h) Connect the remote control to the winch. Ifyou are going to control the winch from inside your vehicle then pass the remote through an open window to avoid the wires being pinched in the door.(i) Start your engine to ensure power is beingreplenished to the battery.(j) Power in the wire rope guiding the wire under tension to draw up the slack in the wire. Once the wire is under tension, stand clear. Neverstep over the wire rope.(k) Double check your anchors and make sure all connections are secure.(l) Inspect the wire rope. Make sure there are at least 5 wraps of wire rope around the winchdrum.(m) Drape a blanket or jacket over the wire rope approximately 5 to 6 feet from the hook.Open the hood for added protection.(n) Clear the area. Make sure all spectators stand clear and that no one is directly in front orbehind the vehicle or anchor point.(o) Begin winching. Be sure that the wire rope is winding evenly and tightly around thedrum. The vehicle that is being winched canbe slowly driven to add assistance to thewinching process. Avoid shock loads; keepthe wire rope under tension.Winching Techniques A-Z Cont’d.(p) The vehicle to be winched should be placed in neutral and the emergency brake released.Only release the brake pedal when under fulltension. Avoid shock loads to the winch. Thiscan damage the winch, rope and vehicle.(q) The winch is meant for intermittent use.Under full load with a single line rig do notpower in for more than a minute withoutletting the motor cool down for a few minutesand then resume the winching operation.(r) The winching operation is complete once the vehicle is on stable ground and is able todrive under its own power.(s) Secure the vehicle. Be sure to set the brakes and place the vehicle in park.(t) Release the tension on the wire rope. The winch is not meant to hold the vehicle forlong periods of time.(u) Disconnect the wire rope from the anchor. (v) Rewind the wire rope. Make sure that any wire already on the drum has spooled tightly andneatly. If not, draw out the wire and re-spoolfrom the point where the rope is tight.(w) Keep your hands clear of the winch drum and fairlead as the wire rope is being drawn in. (x) Secure the hook and hook strap.(y) Disconnect the remote control and store in a clean, dry place.(z) Clean and inspect connections and mounting hardware for next winching operation.1011ENGLISH 14001MAINTENANCEThe owner/operator is responsible for all periodic maintenance.LubricationAll moving parts within the Electric Winch having been Lubricated using high temperature lithium grease at the factory. No internal lubrication is required. Lubricate Cable Assembly periodically using a light penetrating oil.Cable Assembly ReplacementIt is recommended that any modifications be performed by a manufacturer’s authorized repair facility, and that only manufacturer-supplied parts be used.1. Move the clutch to the “Out” position.2. Extend Cable Assembly to its full length.Note how the existing cable is connected to the inside of the drum.3. Remove old Cable Assembly and attach newone.4. Retract Cable Assembly onto drum beingcareful not to allow kinking.Complete all scheduled maintenance in a timely manner. Correct any issue before operating the winch.1214001 ENGLISHSPECIFICATIONS– –– – – – – – – ––*If the motor becomes uncomfortably hot to the touch, stop winching immediately and let it cool down for 5 minutes. Do not pull for more than one minute at or near the rated load.**Electric winches are designed and made for intermittent use and should not be used in constant duty applications.ENGLISH14001 SPECIFICATIONSParts Diagram1314001ENGLISH14ENGLISH14001TROUBLESHOOTINGFor further technical support:Technical ServiceMon – Fri 8:30 AM – 5:00 PM (PST/PDT)Toll Free: 1-877-338-0999*******************************15WARRANTY*CHAMPION POWER EQUIPMENT2 YEAR LIMITED WARRANTYWarranty QualificationsTo register your product for warranty and FREE lifetime call center technical support please visit:https:///registerTo complete registration you will need to include a copy of the purchase receipt as proof of original purchase. Proof of purchase is required for warranty service. Please register within ten (10) days from date of purchase.Repair/Replacement WarrantyCPE warrants to the original purchaser that the mechanical and electrical components will be free of defects in material and workmanship for a period of two years (parts and labor) fromthe original date of purchase and 180 days (parts and labor) for commercial and industrial use. Transportation charges on product submitted for repair or replacement under this warranty are the sole responsibility of the purchaser. This warranty only applies to the original purchaser and is not transferable.Do Not Return The Unit To The Place Of PurchaseContact CPE’s Technical Service and CPE will troubleshoot any issue via phone or e-mail. If the problem is not corrected by this method, CPE will, at its option, authorize evaluation, repair or replacementof the defective part or component at a CPE Service Center. CPEwill provide you with a case number for warranty service. Please keep it for future reference. Repairs or replacements without prior authorization, or at an unauthorized repair facility, will not be covered by this warranty.Warranty ExclusionsThis warranty does not cover the following repairs and equipment: Normal WearProducts with mechanical and electrical components need periodic parts and service to perform well. This warranty does not cover repair when normal use has exhausted the life of a part or the equipment as a whole.Installation, Use and MaintenanceThis warranty will not apply to parts and/or labor if the product is deemed to have been misused, neglected, involved in an accident, abused, loaded beyond the product’s limits, modified, installed improperly or connected incorrectly to any electrical component. Normal maintenance is not covered by this warranty and is not required to be performed at a facility or by a person authorized by CPE.Other ExclusionsThis warranty excludes:–Cosmetic defects such as paint, decals, etc.–Wear items such as filter elements, o-rings, etc.–Accessory parts such as starting batteries, and storage covers.–Failures due to acts of God and other force majeure events beyond the manufacturer’s control.–Problems caused by parts that are not original Champion Power Equipment parts.When applicable, this warranty does not apply to products used for prime power in place of a utility.Limits of Implied Warranty and Consequential Damage Champion Power Equipment disclaims any obligation to coverany loss of time, use of this product, freight, or any incidentalor consequential claim by anyone from using this product. THIS WARRANTY AND THE ATTACHED U.S. EPA, CARB and/or ECCC EMISSION CONTROL SYSTEM WARRANTIES (WHEN APPLICABLE) ARE IN LIEU OF ALL OTHER WARRANTIES, EXPRESS OR IMPLIED, INCLUDING WARRANTIES OF MERCHANTABILITY OR FITNESS FOR A PARTICULAR PURPOSE.A unit provided as an exchange will be subject to the warranty of the original unit. The length of the warranty governing the exchanged unit will remain calculated by reference to the purchase date of the original unit.This warranty gives you certain legal rights which may change from state to state or province to province. Your state or province may also have other rights you may be entitled to that are not listed within this warranty.Contact InformationAddressChampion Power Equipment, Inc.Customer Service12039 Smith Ave.Santa Fe Springs, CA 90670 USACustomer ServiceMon – Fri 8:30 AM – 5:00 PM (PST/PDT)Toll Free: 1-877-338-0999*******************************Fax no.: 1-562-236-9429Technical ServiceMon – Fri 8:30 AM – 5:00 PM (PST/PDT)Toll Free: 1-877-338-0999*******************************24/7 Tech Support: 1-562-204-1188* E xcept as otherwise stipulated in any of the following enclosed Emission Control System Warranties (when applicable) for the Emission Control System: U.S. Environment Protection Agency (EPA), California Air Resources Board (CARB) and/or Environment and Climate Change Canada (ECCC).。
品牌C.K的电子塑料切割器产品说明书

C.K ECOTRONIC ESD - PRECISION SIDE CUTTERS
Item No. Description
A B CDE
Length Weight (mm) (g)
T3883 ESD Side Cutters – Micro 8 9.5 16 4 21 132
64
Blade Thickness (mm)
2
Blade Height at Tips (mm)
1.5
T3884
ESD Side Cutters - Micro, Reverse Cut
8
9.5 13 4 48
132
64
2
1.5
T3885 ESD Side Cutters - Slim
9 10 18 5 21 139
76
2.5
1.5
T3886
AB C D
E
mm mm mm mm mm
T3889 ESD Long Snipe Nose Pliers 49 12 6 1
2
T3890 ESD Short Snipe Nose Pliers 31 12 6 1 1.5
T3891 ESD Flat Nose Pliers3
31
3
2
T3892 ESD Snipe Nose Pliers (Bent) 39 12 6 1
• Special tool steel body, hardened for long-term performance
• Black oxidised finish for corrosion resistance and reduced glare
• Electro-static discharging handles - dissipative
高冠系统说明书

VVVF
广州市西奥电梯有限公司
102
JTK
轿顶急停
103 (无机房用)
KSK1
卡梯开关
103A KSK2
卡梯开关
103B
AK
轿厢急停
104
SJK
上极限开关
107
JSK
夹绳器开关
106
XSK
限速器开关
105
QK
安全钳开关
108 XJK
下极限开关
109 PSE
对重缓冲器开关
110
PSF
轿厢缓冲器开关
113
慢下
48 轿厢检修 49 轿顶检修
53
慢上
慢下
50 51
慢上
慢下
P1
上平层感应器
MQK
门区
P2
下平层感应器
SHK 低速上强迫换速开关
SHK1 高速上强迫换速开关
SXW 上限位
XHK 低速下强迫换速开关
XHK1 高速下强迫换速开关
XXW 下限位
YX1
YJ 安全回路检测
MX1
MSJ1
MX2
MSJ2
X16
6RD 3A
+
302
C1
300
EL10
轿顶插座
EN10
底坑插座
2RD 6A L2 3RD 6A L3
Q2
Q1
AC1
输入
AC2 电源 AC220V 应 急 照 明
380V
6RD 7RD 6A
KEG
8RD 3A 24V
0V 202
220VAC
12 3 相序
EL10
BK2 601 9RD 3A
KWG-1型可控硅控温柜使用说明书

KWG-1型可控硅控温柜使用说明书KWG-1型可控硅控温柜是本厂生产的Ltd型履带式加热器的配套产品,用于碳结钢及合金构件的焊前预热及焊后局部热处理,具有灵活、高效、实用、节能等特点。
可广泛用于电站、石油化工、锅炉、机械等行业的现场施工。
本产品还可以用于其它大型加热器(如电阻炉)的无级调压。
一、技术性能及使用条件1、工作环境温度:-20度~+40度相对温度:不大于85%海拔高度:不大于1000米2、电源三相四线交流380V±10%3、频率50HZ4、额定功率120KW5、最大输出电流200A6、输出电压0~220V7、调压方式三相单独无级调压8、温度控制范围0~1100度±0.5%9、控温点6点10、冷却方式风冷11、重量190Kg二、工作原理KWG-1型可控硅控温柜由主机、触发器、控温器三部分组成,主机由六只200A 大功率可控硅组成三相交流开关,触发器根据设定系统指令给出相应的脉冲信号分别触发可控硅,从而得到预想的功率输出。
控温器除了测量并记录六个测温点的温度之外还通过表面定值电接点以及由主控制的继电器对到温的加热器电源予以控制,从而达到控温效果。
设备框图如下:1、主机电源经主开关1ZD、电流互感器1~3LA、快速熔断器1~3RD到达可控硅,每一相正反并接的两只可控硅,依照触发角的不同向下输出0~220V的电压,输出经螺旋熔断器4~15RD接到输出端子上面。
可控硅输入并接的1~3C及1~3R用于吸收输入端的浪涌电压。
1)触发电源:稳压器的比较放大器由两个PNP小功率管组成的差分放大器构成,用以减小环境温度的影响,基准电压取自温度系数较小的标准稳压管2dW7B,取样电路由R7、W、R8组成。
由于负载变化或电源电压波动等缘故,比较放大器拾取输出电压的变化量放大后送至组合调态管基极以控制调态管的内阻,直到输出电压返回起始电位,电位器W可以调节输出电压,正常工作的稳定电源输出电压调态到20V左右。
JCB Access电动剪刀快速入门指南说明书
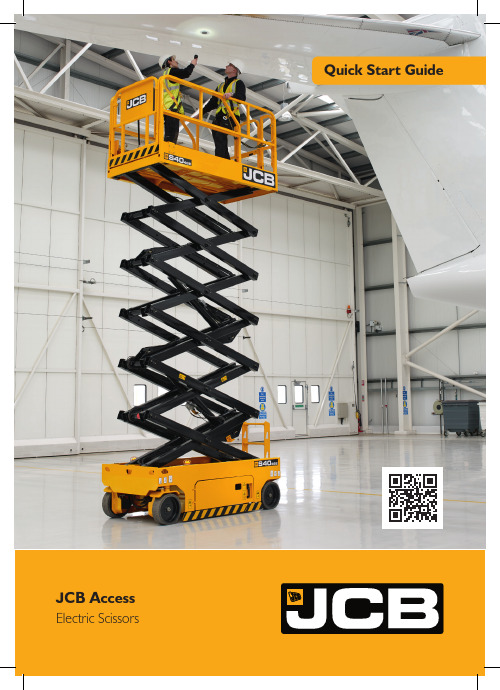
Quick Start Guide JCB AccessElectric Scissors1Operation Transporting the MachineAX – X axis distance Y – Y axis distanceourmeterlatform Raise / Lower Toggle Switchmergency Stopround Controls / Off / Platform Controls Key Switch Please see operator manual for full details./ R Steeringrigger Switch to enable operation attery Level / Fault Code Display latform / Drive Mode Buttonspeed Selectmergency Stoprake Release Lockrake Release PumpHow to Release BrakesEnsure machine can be controlled before releasing brakesPush in brake release lockPump brake release until feels solidCaution – machine is now un-brakedTo reapply pull the brake release lock back out or operate any control on the joystick4Switch Key Left Toggle SwitchTurn the key switch left to enable the ground controls. Use the toggle switch to raise or lower the platform as required.Note: If the platform raise/lower fails to operate, ensure the key switch is in the correct position and all of the emergency stops have been pulled to release.457Trigger & JoystickCradle Release Mode SelectOperate Machine Pull the trigger on the back of the joystick to enable operation.The cradle can be released from the platform by removing the bolt.If CH is shown on the platform controller, the key switch is in the wrong position. The switch must be on platform controls to use them. The machine will Choose from either lift/lower or drive mode. Do not attempt to operate prior to charge status being shown.Pressure SensorsPothole Protection SwitchLimit SwitchesOnly use the original charger installed to the machine with the original batteries. Charge the battery in a well ventilated place. Use an appropriate grounded industrial power supply with correct AC (alternating current) input voltage to charge.If at any time a fault occurs when charging, three battery charge LEDs will blink at the same time. Refer to the operators handbook immediately.AC harge Point C harger Viewing WindowThe flashing LED indicates the charge level. When all three LEDs are solid, the machine is fully charged.Code Description Reaction Instructions 01System intialisation fault Disables all motion Restart the machine 02System communication fault Disables all motion Restart the machine 03Invalid option setting fault Disables all motion Restart the machine 04Load sensing data faultWarning only Contact the dealer 12Chassis up or down switch ON at power-up faultDisable chassis control Contact the dealer 18Pothole guard fault Check pothole protection 31Pressure sensor 1 fault 32Angle sensor fault 36Limp mode42Platform left turn switch ON atpower-up message 43Platform right turn switch on atpower-up message 46Platform joystick enable switch on atpower-up fault 47Platform joystick not in neutral at power-upDiagnostic codes are shown on both the platform controller and through a viewing window on the hydraulic tray door.JCB Sales Limited, Rocester, Staffordshire, United Kingdom ST14 5JP Tel:+441889590312Email:***************** Download the very latest information on this product range at: All rights reserved. No part of this publication may be reproduced, stored in a retrieval system, or transmitted in any form or by any other means, electronic, mechanical, photocopying or otherwise, without prior permission from JCB Sales. All references in this publication to operating weights, sizes, capacities and other performance measurements are provided for guidance only and may vary dependant upon the exact specification of the machine. They should not therefore be relied upon in relation to suitability for a particular application.Guidance and advice should always be sought from your JCB Dealer’. JCB reserves the right to change specifications without notice. Illustrations and specifications shown mayinclude optional equipment and accessories.9818/3000。
CX-TGK01型电脑时间控制开关

CX-TGK01型微电脑时间控制开关使用说明书一、产品简介:CX-TGK01型微电脑时间控制开关,是一个以微电脑为核心,配合电子电路等组成的一个电源开关控制装置。
它可设定每天或一周内20次不同时间的开/关控制,还具有倒计时(延时关机)、随机、夏时制和12/24小时制转换功能。
本机内置一枚可充电镍氢电池作为备用电源,在脱离市电电源的情况下,仍可保持计时显示和储存的各项数据达6个月以上。
它采用输入输出接线形式,可以控制路灯、灯箱、电热水器、烘箱等各种安装位置固定的电器设备。
如和交流接触器串联后可控制大功率电器和三相电器设备。
您使用本产品后,各种电器将会根据您的要求实现自动开启和关闭。
二、技术参数:执行标准:GB/T14536.1-1998 GB/T14536.8-1996额定电压:220V ~50HZ额定电流:20A(阻性)工作温度:-10~55℃计时误差:<±2秒/天动作形式:1.B.S.U三、系统功能介绍:1.液晶全屏字符和外形尺寸,如右图所示:2. 本机在时钟状态下,按“模式”键可将工作状态设定为所需的方式。
设定顺序为:关自动开随机 Z Z(倒计时)关电源输出处于经常关闭状态。
自动电源输出处于执行编写的定时开/关程序状态。
开电源输出处于经常开启状态。
随机电源输出处于随机开启和关闭状态。
间隔时间为40~80分钟,开启时间为1~15分钟。
Z Z电源输出处于倒计时延时关机状态,最长时间为 2小时59分,最短为1分钟。
C按此键后系统将清除所有储存的数据,系统恢复到初始状态。
四、操作方法(一)、校正星期和时间:按“模式”键将定时器工作状态设定为“关”或“开”,在此状态下左手按住“时钟”键不放,右手按“星期”键,将星期调整为当前日期,调整好日期(星期)后再按“时”和“分”键将时钟调整为当前的标准时间。
(二)、设定倒计时(延时关机)工作状态:按“模式”键将工作状态切换至Z Z(倒计时)状态,电源输出即处于开启状态,屏幕显示如右图所示:在此状态下,按“时”或“分”键修改您所需要本机开启通电的时间,每按一次“时”或“分”键,时间将减少1小时或1分钟。
第一部分、TKGK-1产品使用说明
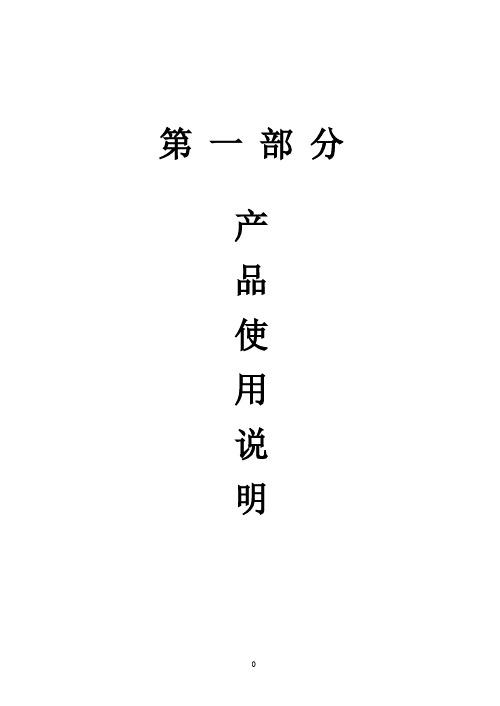
第一部分产品使用说明TKGK-1过程控制实验装置组成和各部分使用说明TKGK-1型过程控制实验装置是根据自动化专业及相关专业教学的特点,吸收了国外同类实验装置的特点和长处,经过精心设计,多次实验和反复论证,向广大师生推出一套全新的实验设备。
该设备可以满足《过程控制》、《自动化仪表》、《工程检测》、《计算机控制系统》等课程的教学实验。
整个系统结构紧凑、功能多样、使用方便,既能进行验证性、研究性实验,又能提供综合性实验。
本实验装置可满足本科、大专及中专等不同层次的教学实验要求,还可为科学研究开发提供实验手段。
本实验装置的控制信号及被控信号均采用IEC标准,即电压0~5V或1~5V,电流0~10mA或4~20mA。
实验系统供电要求为单相交流220V±10%,10A;外型尺寸为:167*164*73,重量:580Kg。
装置特点本实验装置具有以下特点:1、多种被控参数:温度、压力、流量、液位。
2、控制方式多样:位式控制、模拟PID控制、智能仪表控制、单片机控制、PLC控制、计算机控制等。
3、多种计算机控制软件:PROTOOL-CS组态软件、MCGS组态软件、本公司开发的上位机监控软件。
4、丰富的计算机控制算法:P、PI、PID、死区PID、积分分离、不完全积分、模糊控制、神元控制、基于SIMULINK的动态参数自适应补偿控制等。
5、开放的软件平台:在我们提供的软件平台上,学生既可以利用我们所提供的算法程序进行实验,又可以用自己编写的PLC程序、MATLAB算法程序等进行实验。
6、灵活多样的实验组合:可以很方便地对控制方式与被控参数进行不同组合,得到自己需要的单回路、多回路等多种控制系统。
系统组成TKGK-1型过程控制实验装置集多参数闭环控制为一体,它是由被控对象、调节器模块、执行器模块、变送器模块和单片机控制模块等组成,各模块间组合灵活,基本包含了目前所有的工业控制方式,涉及温度、压力、流量和液位等重要的过程控制参数。
KQC-C超载限制器使用说明书

超载限制器KQC-C使用说明书(Ⅵ)2013年2月版●使用前请仔细阅读本产品说明书●请妥善保管本产品说明书,以备查阅宁波柯力传感科技股份有限公司目录第一章概述 (2)第二章技术参数 (2)第三章安装连接 (3)第四章键盘功能介绍 (4)第五章操作方法 (5)第六章操作简要(开机操作即可使用) (6)第七章标定及参数设置 (8)第八章参数设置菜单说明 (11)第九章常见故障及解决方法 (12)附表 1 KQC-C超载限制器装箱清单 (13)第一章概述KQC-C型超载限制器是一种新型智能式重量过载保护器,通过设置的重量传感器测量装载物重量的变化,KQC-C仪表实时显示实际载荷,当载荷达到其额定载荷的设定值时,发出声光报警信号,并可给出开关量输出。
KQC-C型超载限制器体积较小,带有安装卡槽,并可外接小型显示板或大屏幕。
KQC-C型超载限制器具有结构合理、安装方便、调试操作简单、工作可靠、精度高等一系列优点。
采用单个传感器时可用于塔机、卷扬机等;采用两个传感器时可用于施工升降机。
带有标准卡槽,可安装于控制柜中。
第二章技术参数⏹工作电源:AC220V/50Hz;⏹综合误差:≤5%F.S.;⏹供桥电源:DC5V;⏹继电器输出触点容量:10A/250VAC;⏹输入信号范围:0mV--15mV;⏹最大净输入信号:≤15mV;⏹显示位数:4位;⏹大屏幕输出波特率600bps;⏹工作温度:-20℃-60℃;⏹仪表尺寸:115mm*90mm*72mm;⏹仪表重量:0.5kg⏹推荐预热时间:≥10min;第三章安装连接由于KQC-C型超载限制器采用了带有接线端子的工业机箱,因此安装极为简单。
在超载限制器的内部有6个接线端子,他们用来完成超载限制器的外部连接,如下表所示,具体接线如超载限制器上盖前后面贴提示说明所示。
接口编号连接备注1报警器正极报警器2报警器负极3220VAC火线220V电源4未用5220VAC零线6继电器常开端过载开关7继电器公共端8继电器常闭端9外接显示负极外接显示10外接显示信号11外接显示正极12传感器激励正13传感器信号正超载传感器114传感器信号负15传感器激励负16传感器激励正17传感器信号正超载传感器218传感器信号负19传感器激励负注:1、安装仪表时,请严格按照上盖前后面贴提示进行连接;接单个传感器时,另一路传感器接口须信号线短接;2、强制开关在正常情况下禁止使用,如遇特殊情况,超载后仍需继续工作,可打开强制开关。
CKS GT 系列封闭型超微型开关说明书

ToggleDimensions are shown: Inches (mm)Specifications and dimensions subject to changeGT SeriesSealed Ultraminiature Toggle SwitchesFeatures/Benefits • S ealed against solder and cleaningprocess contaminants •U ltraminiature size, smallestfootprint available• T hru-hole and surface mount models • H igh temperature materials (UL 94V-0)•R o HS co mpliant and co mpatibleTypical Applications• Hand-held telecommunications • Small instrumentationSpecificationsCONTACT RATING: 0.4 VA max. @ 20 V AC or DC max.MECHANICAL & ELECTRICAL LIFE: 40,000 make-and-breakcycles at full load.CONTACT RESISTANCE: Below 50 m Ω typ. initial @2-4 V DC, 100 mA.INSULATION RESISTANCE: 109 Ω min.DIELECTRIC STRENGTH: 500 Vrms min. @ sea level.OPERATING TEMPERATURE: –30ºC to 85ºC.SOLDERABILITY: Per MIL-STD-202F method 208D, orEIA RS-186E method 9 (1 hour steam aging).PACKAGING: Surface mount switches shipped in anti-statictape and reel packaging per EIA 481-3, see page F-47 for drawings and reel information. Tape and cover strip are conductive for use near statically sensitive components, consult Customer Service Center.MaterialsHOUSING AND BASE: Glass filled nylon 4/6, flame retardant,heat stabilized (UL 94V-0).ACTUATOR: Glass filled nylon 4/6, flame retardant, heat stabilized(UL 94V-0), with standard internal o-ring seal.SWITCH SUPPORT: Brass, tin plated.MOVABLE CONTACTS: Copper alloy, with gold plate overnickel plate.STATIONARY CONTACTS: Copper alloy, with gold plate overnickel plate.TERMINALS: Gold.TERMINAL SEAL: Epoxy. All terminals insert molded.NOTE: Specifications and materials listed above are for switches with standard options. For information on specific and custom switches, consult Customer Service Center.How To OrderOur easy build-a-switch concept allows you to mix and match options to create the switch you need. To order, select desired option from each category and place it in the appropriate box.4 Mar 22ToggleGT SeriesSealed Ultraminiature Toggle SwitchesEPOXY SEAL.170 DIA..015 TYP .(0,38).100(2,54).177(4,50).150(3,81).160(4,06).020 TYP .(0,51).100(2,54).066 DIA..063(1,60).228(5,79).130 TYP .(3,30)ACTUATOR SHOWN IN POS. 1TERMINAL NOS. FORREFERENCE ONLY GT12 MODELTERMINALS 1,3,4 & 6 ONLY1346.276(7,01)C&K MARKING ON OPPOSITE SIDE12346GT12-omit hole 2.PC MOUNTINGGT11MCBESPDT4 Mar 22Complete part numbers for GT Series Sealed Ultraminiature Toggle Switches are shown on following pages.123456C&K MARKING ON OPPOSITE SIDE1346ACTUATOR SHOWN IN POS. 1TERMINAL NOS. FOR REFERENCE ONLYGT22 MODELTERMINALS 1,3,4 & 6 ONLYEPOXY SEAL.170 DIA..015 TYP .(0,38).100(2,54).177(4,50).150(3,81).160(4,06).020 TYP .(0,51).100(2,54).066 DIA..063(1,60).228(5,79).130 TYP .(3,30).276(7,01)GT22-omit holes 2 & 5.PC MOUNTINGGT21MCBEDPDTT o g g l eGT SeriesSealed Ultraminiature Toggle SwitchesGT22 ModelsActuator ShownIn Pos. 1GT22-omit holes 2 & 5.PC MOUNTINGActuator ShownIn Pos. 1GT12 ModelsGT12-omit hole 2.PC MOUNTINGGT11MABE 4 Mar 22ToggleGT SeriesSealed Ultraminiature Toggle SwitchesGT12 ModelsActuator Shown In Pos. 1GT12omit hole 2.PC MOUNTINGGT11MV3BESPDTGT21MAVBE Vertical ActuationDPDTGT11MAVBE Vertical ActuationSPDTToggleDimensions are shown: Inches (mm)Specifications and dimensions subject to change GT SeriesSealed Ultraminiature Toggle SwitchesGT22 Models:1, 3, 4 & 6 terminals only.Actuator ShownIn Pos. 1PC MOUNTING(0,38) X (0,51).015 X .020 TY P..020 TY P.(0,51).200(5,08).053(1,35).050 TY P.(1,27).340(8,64).066 DIA..150(3,81).276(7,01).273(6,93).215(5,46)321TERM NOS. FO RREFEREN CE ONL YACTUA T OR SHO WN IN POS.1.100 TY P.(2,54)GT12 MODE LTERM S. 1 & 3 O NLY31EPO XYSEA L.109(2,77)PC MOUNTINGGT12-omit pad 2.GT11MSCBESPDTGT11MSABEHorizontalActuationSPDTGT21MV3BEDPDTStandard with tape & reel packaging, see page F-47.4 Mar 22ToggleDimensions are shown: Inches (mm)Specifications and dimensions subject to change4 Mar 22For part numbers GT11MSABE, GT12MSABE, GT13MSABEFor part numbers GT11MSCBE, GT12MSCBE, GT13MSCBE, GT21MSCBE, GT22MSCBE, GT23MSCBE,REEL INFORMATIONOUTSIDE DIAMETER 13.00 (330,0)PILOT HOLE .512 (13,0)QUANTITY PER REEL600REEL INFORMATIONOUTSIDE DIAMETER 13.00 (330,0)PILOT HOLE .512 (13,0)QUANTITY PER REEL200GT SeriesSealed Ultraminiature Toggle SwitchesActuator ShownIn Pos. 1GT22 ModelsGT22-omit pads 2 & 5.PC MOUNTINGStandard with tape & reel packagingGT21MSCBEDPDT。
XLJ-G1系列真空角阀商品说明书
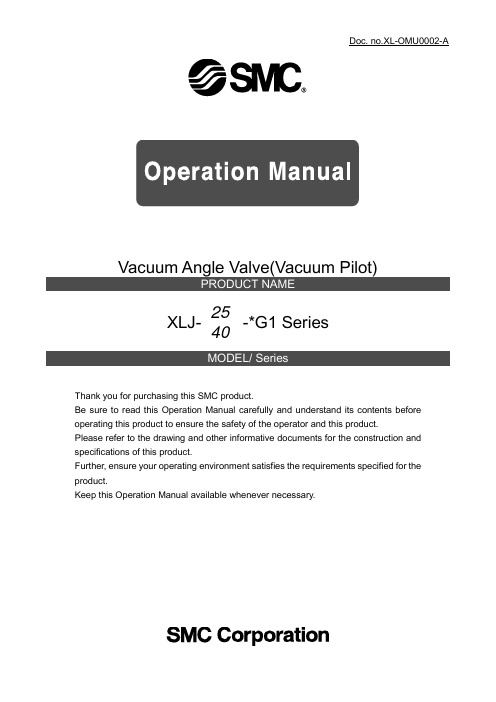
Doc. no.XL-OMU0002-AVacuum Angle Valve(Vacuum Pilot)XLJ- -*G1 SeriesThank you for purchasing this SMC product.Be sure to read this Operation Manual carefully and understand its contents before operating this product to ensure the safety of the operator and this product.Please refer to the drawing and other informative documents for the construction and specifications of this product.Further, ensure your operating environment satisfies the requirements specified for the product.Keep this Operation Manual available whenever necessary.2540Safety Instructions - - - - - - - - - - - - - - - - - - - - - - - - - - - - 2 1. Product Specific Precautions 1 - - - - - - - - - - - - - - - - - - - - - - - - - - - - 4(Precautions on Design, Selection, Mounting, Piping, Wiring, Maintenance) 2. Product Specific Precautions 2 - - - - - - - - - - - - - - - - - - - - - - - - - - - - 5(Maintenance parts)3. Specifications - - - - - - - - - - - - - - - - - - - - - - - - - - - - 64 Construction and Outer dimensions - - - - - - - - - - - - -- - - -- - - - - - - - - - - - 75. Period and scope of warranty - - - - - - - - - - - - - - - - - - - - - - - - - - - - 86. Parts replacement procedure - - - - - - - - - - - - - - - - - - - - - - - - - - - - 9Safety InstructionsThese safety instructions are intended to prevent hazardous situations and/or equipment damage. These instructions indicate the level of potential hazard with the labels of “Caution,” “Warning” or “Danger.”They are all important notes for safety and must be followed in addition to International Standards (ISO/IEC)*1), and other safety regulations.*1) ISO 4414: Pneumatic fluid power -- General rules relating to systems ISO 4413: Hydraulic fluid power -- General rules relating to systemsIEC 60204-1: Safety of machinery -- Electrical equipment of machines (Part 1: General requirements) ISO 10218-1992: Manipulating industrial robots -- SafetyCaution Caution indicates a hazard with a low level of risk which, if not avoided, could resultin minor or moderate injury. Warning Warning indicates a hazard with a medium level of risk which, if not avoided, could result in death or serious injury.DangerDanger indicates a hazard with a high level of risk which, if not avoided, will resultin death or serious injury .Warning 1. The compatibility of the product is the responsibility of the person who designs theequipment or decides its specifications.Since the product specified here is used under various operating conditions, its compatibility with specific equipment must be decided by the person who designs the equipment or decides its specifications based on necessary analysis and test results.The expected performance and safety assurance of the equipment will be the responsibility of the person who has determined its compatibility with the product.This person should also continuously review all specifications of the product referring to its latest catalog information, with a view to giving due consideration to any possibility of equipment failure when configuring the equipment.2. Only personnel with appropriate training should operate machinery and equipment.The product specified here may become unsafe if handled incorrectly.The assembly, operation and maintenance of machines or equipment including our products must be performed by an operator who is appropriately trained and experienced.3. Do not service or attempt to remove product and machinery/equipment until safety is confirmed.1.The inspection and maintenance of machinery/equipment should only be performed after measures to prevent falling or runaway of the driven objects have been confirmed.2.When the product is to be removed, confirm that the safety measures as mentioned above are implemented and the power from any appropriate source is cut, and read and understand the specific product precautions of all relevant products carefully.3.Before machinery/equipment is restarted, take measures to prevent unexpected operation and malfunction.4. Contact SMC beforehand and take special consideration of safety measures if the product is to be used in any of the following conditions.1. Conditions and environments outside of the given specifications, or use outdoors or in a place exposed to direct sunlight.2. Installation on equipment in conjunction with atomic energy, railways, air navigation, space, shipping, vehicles, military, medical treatment, combustion and recreation, or equipment in contact with food and beverages, emergency stop circuits, clutch and brake circuits in press applications, safety equipment or other applications unsuitable for the standard specifications described in the product catalog.3. An application which could have negative effects on people, property, or animals requiring special safety analysis.4. Use in an interlock circuit, which requires the provision of double interlock for possible failure by using a mechanical protective function, and periodical checks to confirm proper operation.Safety InstructionsCaution1. The product is provided for use in manufacturing industries.The product herein described is basically provided for peaceful use in manufacturing industries.If considering using the product in other industries, consult SMC beforehand and exchange specifications or a contract if necessary.If anything is unclear, contact your nearest sales branch.Limited warranty and Disclaimer/Compliance RequirementsThe product used is subject to the following “Limited warranty and Disclaimer” and “Compliance Requirements”.Read and accept them before using the product.Limited warranty and Disclaimer1. The warranty period of the product is 1 year in service or 1.5 years after the product is delivered,whichever is first.*2)Also, the product may have specified durability, running distance or replacement parts. Please consult your nearest sales branch.2. For any failure or damage reported within the warranty period which is clearly our responsibility, a replacement product or necessary parts will be provided.This limited warranty applies only to our product independently, and not to any other damage incurred due to the failure of the product.3. Prior to using SMC products, please read and understand the warranty terms and disclaimers noted in the specified catalog for the particular products.*2) Vacuum pads are excluded from this 1 year warranty.A vacuum pad is a consumable part, so it is warranted for a year after it is delivered.Also, even within the warranty period, the wear of a product due to the use of the vacuum pad orfailure due to the deterioration of rubber material are not covered by the limited warranty.Compliance Requirements1. The use of SMC products with production equipment for the manufacture of weapons of mass destruction (WMD) or any other weapon is strictly prohibited.2. The exports of SMC products or technology from one country to another are govemed by the relevant security laws and regulation of the countries involved in the transaction. Prior to the shipment of a SMC product to another country, assure that all local rules goveming that export are known and followed.Common Precautions 1Be sure to read before handling.DesignWarning●All models1. The material of the body and the bonnet is A6063, the other materials for vacuum is SUS304, brass, equivalent material to SUS405,and PPS, and the seal material is FKM. In addition, the seal material sliding part for vacuum is applied vacuum grease (Y-VAC2). Use fluids those are compatible with using materials after confirming.2. Fluctuation of each voltage should be +/- 10% or less.Selection●All models1. Keep within the specified range of the pilot pressure.2. Fluid containing foreign matters and oil will cause malfunction and sealing failure. Remove such things from the fluid.Mounting● All models1. In high humidity environments, keep the valve packed until the time of installation.2. Perform piping so that excessive force is not applied to the flange sections. When there is vibration from heavy objects or attachments, etc., fix piping so that vibration will not apply torque directly to the flange section. Piping and wiring1. Before mounting, clean the surface of the flange seal and the O-ring with ethanol, etc.2. There is an indentation of 0.1 to 0.2mm in order to protect the flange seal surface, and it should be handled so that the seal surface is not damaged in any way.3. This product has piping directionality. Check the vacuum pump side and the chamber side shown on the construction drawing.4. A wire for wiring should be 0.5 to 1.25mm 2 or more as reference.5. In addition, the wire shall not be applied excessive force.6.The power supply shall be operated together with the power supply for a vacuum pump.If the fluid or reaction product (deposit) may cause the valve to become unsafe, the valve should be disassembled, cleaned and re-assembled by an operator who has sufficient knowledge andexperience (e.g. a specialist).CautionCautionWarningCaution1. Replace the bonnet assembly when the valve is approaching the end of its service life.*For the endurance cycles, refer to Section 5 (page 8).2. If damage is suspected prior to the end of the service life, perform early maintenance.3. SMC specified parts should be used for service. Refer to the Construction / Maintenanceparts table.4. When removing the valve seal and external seal, take care not to damage the sealingsurfaces. When installing the valve seal and external seal, be sure that the O-ring is not twisted.Common Precautions 2 Be sure to read before handling Maintenance PartsSMC specified parts should be used for service.Refer to the construction drawing.1.Replace the bonnet assembly when changing the sealant material. Due to the differentmaterials used, changing only the seal may prove inadequate.Bonnet assemblyDescriptionConstruction no.Valve size25 40Bonnet assembly 1 XLJ25-30-*G1 XLJ40-30-*G1 External seal/ valve sealDescriptionConstruction no.Valve size25 40External seal 3 AS568-030V AS568-035VValve seal 2 B2401-V24V B2401-P42VNote 1) Refer to the Construction of for the construction numbers.Note 2) A voltage symbol (same as How to Order) is entered into the mark *CautionOpen valve) When the solenoid valve is energized (simultaneously with the vacuum pump), theatmospheric vent port is closed, and the channel of the bonnet and the top of the piston are opened. If the pressure at the vacuum pump side decreases, the pressure at the top of the piston also decreases via the channels of the shaft and the body. The pressure difference generated at that time makes the piston move upward. If the pressure decreases more, the channel of the shaft is closed, but the pressure at the top of the piston decreases much more via the channel of the bonnet, and it opens the valve.Close valve) When energizing to the solenoid valve is stopped (simultaneously with the vacuum pump),the channel of the bonnet is closed, and the atmospheric vent port and the top of the piston are opened. As the top of the piston gets atmospheric pressure via the atmospheric vent port, the valve is closed as the piston moves downward with the built-in spring. When the piston moves downward further, the channel of the shaft is opened, and it leads atmosphere to the vacuum pump side. Note) Valve response depends on the pump capability. Please check and use this valve.ModelXLJ-25-*G1XLJ-40-*G1Flange (valve) size 2540Actuating type Normally closed (vacuum pilot)FluidEvacuation with inert gasOperating temperature oC 5~40 Direction of exhaust Fixed Note 1Operating pressure Pa (abs) Atmospheric pressure to 1×10-2Conductance l/s Note 2 1245Operating power voltage 100VAC, 200VAC,110VAC,220VAC,230VAC,240VAC,24VDC,12VDCElectrical entry GrommetLeakagePa ・m 3/sInternal 1.3 x 10-8at ambient temperature, excluding gas penetrationExternal1.3 x 10-6at ambient temperature, excluding gas penetrationType of flangeKF(NW)Main materialBody and bonnet: aluminum alloy, Main parts: SUS304 and FKM Solenoid valve: brass, SUS304, equivalent to SUS405, PPS, and FKMSurface treatment for bodyOutside: hard anodized Inside: basis materialVacuum greaseFluorine type grease: Y-VAC2Weight kg0.951.5ON operation(simultaneously with pump) Note 3 Valve opens by vacuum pressure of pump side.. OFF operation(simultaneously with pump)Pump side opens to atmosphere after closing the valve.Note 1 See “Operation Description” and “Construction Drawing”.Note 2 The conductance is “molecular flow” measured with an elbow pipe which has the samedimension with each flange.Chamber sideOFF OFF ON Vacuum pump side4.A B DEACDimensions [mm]The guaranteed period covers the period which finishes the earliest among 0.5 million operating cycles [with our durability test conditions], 18 months after shipping from us, and 12 months after starting the use of the product at your place or your customer’s place.Note: The product durability is varied depending on the operating conditions (such as a use with large flow rate).If the specification is not kept, or any non-conformance derived from mounting or replace of a device, an assembly, or an O-ring at your place occurs, the guarantee cannot be applied.If any failure occurs due to our fault during the guaranteed period, we will guarantee the non-conformance by delivering a substitute in the worst case. However, responsibility of any damage which is led by the product failure is not taken by us.Result of durability test(with the circuit shown on the right) Internal/ external leakage and operation were checked by opening and closing a valve at room temperature.It was confirmed that this product Satisfied the specification up to0.5 million cycles.6-1. PrecautionsBe sure to follow [1. Precautions 1] when disassembling the product for maintenance. Along with the precautions above, comply with the following precautions too.Warning•If it is expected that product materials may get stuck to the product, ensure safety isassured before handling. It is recommended to wear gloves and a mask.•Pay attention to the handling of components according to the procedure in the next itemonwards. Do not apply excessive force or impact. This will not only damage the productbut also decrease its performance and life expectancy.•It is not possible to disassemble the bonnet assembly of this product. If the componentsand assembly are damaged, or damage is expected, exchange the bonnet assemblyitself.•Do not disassemble the parts that are not explained in this operation manual. Theperformance and life may decrease. Also, it may cause danger.Step 1 Step 2 Step 4 Step 5 Step 6 Apply ethanol to a clea (such as BENCOT) to wipe off dust on O-ring sur face, and place the O-ring on the Loosen the bolts gradually in numerical order (alternately) with bonnet assembly held.Apply ethanol to cloth (such as BENCOT) wi pe off dust on surface and the e seal.A (gas release)Remove the e xte rnal seal from the bod y. (Mind damage the bod y mounting surface.)ppl y et han ol t o a c l ea n c uc h as B E NCOT) t o wi pe offt on t h e e xt e rn al s eal s urf and t he b od y m ount i ng s urf hen, m ount t h e e xt er nal s eal.Loosen the bolts gradually innumerical order (alternately) withbonnet assembly held.Step 4 Step 5A 40 size added WU1st Printing :UX 4-14-1, Sotokanda, Chiyoda-ku, Tokyo 101-0021 JAPANTel: + 81 3 5207 8249 Fax: +81 3 5298 5362URL Note: Specifications are subject to change without prior notice and any obligation on the part of the manufacturer.© 2009 SMC Corporation All Rights Reserved。
cjt电气冲击式说明书
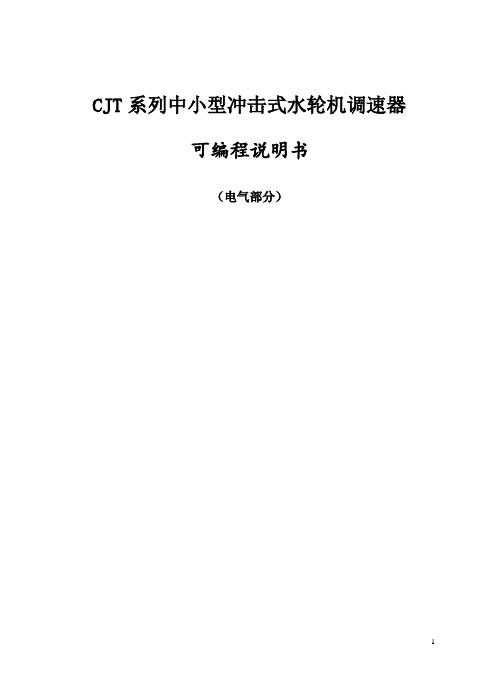
CJT系列中小型冲击式水轮机调速器可编程说明书(电气部分)第一章概述CJT系列中小型冲击式水轮机调速器是新一代冲击式水轮机电液调速器。
与传统的调速器不同,它采用折向器快速开启、关闭,喷针进行调节的控制方式,提高了调速系统的动态稳定性和调节品质。
该系列调速器电气部分采用三菱FX2N系列可编程。
整机工作可靠,性能优良,结构简单,运行方便。
1.1 功能和特点:1.1.1 调速器的主要功能·频率测量与调节:可测量机组和电网的频率,并实现机组频率的调节和控制。
·频率跟踪:当跟踪功能投入时,机组频率自动跟踪电网频率,可实现快速自动准同期并网。
·自动调整与分配负荷:机组并入电网,调速器将根据其整定的bp值和电网频差自动调整机组的出力。
·负荷调整:可接受上位机控制指令,实现发电自动控制功能(A.G.C)。
·开停机操作:接受中控室或上位机指令,实现开停机操作。
·手动操作:具有机械手动操作功能,并可无条件、无扰动地实现自动运行与手动操作的相互切换。
·能采集并显示调速系统的主要参数,如:机组频率、电网频率、喷针开度、折向器开度、调节输出值和调节器的整定参数等。
·可配置通讯单元,为电站微机监控系统联系提供标准、可靠的接口,能方便地实现与上位机的通讯。
1.1.2 本调速器具有如下主要特点·电气部分以可靠性极高的FX2N系列可编程序控制器为其硬件的主体,软件采用统一的时变参数控制策略,可适时辨识空载、并网和孤立运行等不同工况,可靠性高,稳定性好,带孤立负荷能力较强。
·频率测量部分采用了可编程内部测频,可靠性高,抗干扰能力强。
·用彩色液晶触摸屏作为人机界面,为运行人员提供了方便、准确、直观的操作环境。
·设有在线自诊断及处理功能,当系统故障时,调速器将自动转入手动工况运行,将负荷固定于故障前的状态。
·自动化程度高,调速器设有开机、停机、发电、调相、增减给定操作回路,只需给调速器相应的操作指令,调速器便能自动完成上述操作,减少了与水机自动回路的联系。
凯瑞吉咖啡机使用和保养指南说明书

Remove packing tape from brewer and plug into a grounded outlet.Place a large mug (12oz minimum) on the drip tray.Remove the water reservoir lid, then liftthe reservoir straight up to remove it.Starter Kit for instructions.Rinse reservoir with fresh water andfill to the MAX fill line.Replace water reservoir, making surethe lock tab engages with the brewer.Replace lid.NOTE:Do not use distilled water.Press power button — the green powerlight will illuminate.The brewer will automatically beginminutes. Once the heating sound stops,the brewer is ready.Do not insert a K-Cup® pod. Press theHOT WATER button. The five brewbuttons will blink. Press the small mug(8oz) button to start a cleansing brew.Pour the hot water into the sink.The one-time setup process is nowcomplete and you are ready to brew!NOTE:Between brew cycles, the brewer may take about aminute to reheat.135246Before You BrewBrew Your First CupSelect your brew size — for boldercoffee, press the STRONG button beforeselecting your brew size. The brew size andSTRONG button, if selected, will remainilluminated while brewing — about 1minute.For iced beverages, fill a 16oz plastictumbler with ice. Insert any K-Cup® pod,then press the ICED button.The brewer will be ready to brew another cup in about a minute.NOTE: For iced beverages, only use a plastic cup. Do not use glass.CAUTION:While brewing, there is extremely hot water in the K-Cup® pod holder. To avoidinjury, do not lift the handle during the brewing process.mug, remove the drip tray and place themug on the drip tray base. Lift the handleand place a K-Cup® pod in the K-Cup® podholder. Lower the handle completely to closethe lid.Do not remove the foil lid on the K-Cup® pod.High Altitude Brewing: While holding thebrewer handle up, push down slowly on theK-Cup® pod in the pod holder until the bottom of the K-Cup®pod is punctured by the exit needle.Plug & Place R inse & FillPower On Cleansing BrewPlace Mug & Pod Brew & Enjoy!Brewer FeaturesProgramming Brewer FeaturesStrong Brew increases the strength and bold taste of yourcoffee’s flavor. For bolder coffee, press the STRONG button and select your brew size.Iced Coffee: Brew hot over ice and enjoy cold. Makes full-flavored and delicious iced coffee .Hot Water on demand for instant soups and oatmeal.Smart Start heats then brews in one simple process. No need to wait for the brewer to heat before selecting brew size. Power on your brewer, add coffee, then select your brew size. The brewer will heat, then automatically begin brewing.Clock allows you to set an Auto On time.Temperature Control allows you to adjust the temperature from 187° – 192°.Auto On sets your brewer to turn on at a specific time. Auto Off automatically turns your brewer off 2 hours after the last brew for energy savings. You can also program your brewer to shut off in 15 minute increments after your last brew, or remain on all the time.High Altitude ensures your brewer works properly at higher altitudes (5,000 feet).NOTE: In High Altitude mode the temperature is not adjustable. If you attempt to adjust the temperature, the mountain icon will flash indicating that you are in high altitude mode.® brewer, use the settings button and . After the feature is programmed, press Clock: Press the settings button once and use the up and down arrows to select the correct hour. Press the settings button again and use the up and down arrows to select the correct minutes.Temperature Control: Press the settings button 3 times and use the up and down arrows to select your preferred temperature. Auto On: Press the settings button until a sun icon appears. Then use the up and down arrows to turn the Auto Onfunctionality “on.” Press the settings button again to set your preferred time, using the up and down arrows. Once you return to the home clock screen a sun icon will be present to let you know that the functionality is on.NOTE: You must set the clock to enable to Auto On functionality.Auto Off: Press the settings button and use the up and down arrows to set your preferred off time. Off time can be set from 15 minutes to 2 hours in 15 minute increments. A moon icon will appear on the screen to indicate your brewer is in Auto Off mode.To disable Auto Off, use the up and down arrows to turn the functionality “off.” The moon icon will no longer appear on the screen.To enable Auto Off, use the up and down arrows to turn the functionality “on.” The moon icon will appear on the screen.High Altitude: Press the settings button until you see the turn this setting on or off.NOTE: In high altitude mode the temperature is not adjustable. If you attempt to adjust the temperature, the mountain icon will flash indicating you are in high altitude mode.Brewer ExteriorKeep your Keurig® brewer looking its best by cleaning the exterior from time to time. Just clean with a damp, soapy, lint-free, non-abrasive cloth. Never immerse the brewer in water or other liquids.Drip TrayThe drip tray can hold up to 8 ounces of overflow and should be emptied and cleaned occasionally. To remove, slide it toward you, keeping it level to avoid spilling. Clean with a damp, soapy, lint-free, non-abrasive cloth.K-Cup® Pod HolderTo remove the K-Cup® pod holder from the brewer, lift the handle and grasp the top of the K-Cup® pod holder with one hand while pushing up on the bottom of the K-Cup® pod holder from underneath with the other until it releases. After cleaning, align the K-Cup® pod holder with the opening using the two front ribs as a guide and snap into place from the top.CAUTION: There are sharp needles that puncture the K-Cup® pod above the K-Cup® pod holder and in the bottom of the K-Cup® pod holder. To avoid risk of injury, do not put your fingers in the K-Cup® pod holder.Funnel The funnel can be removed from the K-Cup® pod holder by pulling on it until it pops off. To replace it, orient the snaps to the indent and just snap it back onto the K-Cup® pod holder.Regular cleaning keeps your brewer running smoothly. Always be sure to turn off and unplug your brewer before cleaning.Water Reservoir & Reservoir Lid The water reservoir lid and water reservoir should be cleanedperiodically with a damp, soapy, non-abrasive cloth. Rinse thereservoir thoroughly after cleaning. This will ensure that no cleaning solutions remain in the area as they may contaminate the water supply. After rinsing, fill the reservoir with clean water and return it to the brewer. Do not dry the inside of the water reservoir with a cloth as lint may remain. The water reservoir lid and water reservoir should not be put into the dishwasher.NOTE: If you are using a water filter inside the water reservoir, remove it before cleaning.Exit NeedleRemove the pod holder assembly and detach the funnel. Locate the exit needle on the inside bottom of the K-Cup® pod holder. Insert a straightened paper clip into the exit needle to loosen any coffee grounds.Entrance NeedleLift the brewer handle and locate the entrance needle on the underside of the lid. To clean the holes in the needle, hold the brewer handle in the upward position and with your other hand, carefully insert a straightened paper clip into all the holes. Gently move it around to loosen any coffee grounds. Lower the handle completely and run two water-only brew cycles. Do not insert a K-Cup® pod.TIP: Refer to for video instructions on cleaning the entrance/exit needles.TroubleshootingYou should descale your brewer every 3-6 months. Properly follow the descaling procedure.Depending on the mineral content of your water, calcium deposits or scale may build up in your brewer. Scale is non-toxic but if left unattended can hinder brewer performance. Regularly descaling your brewer every 3-6 months helpsmaintain the heating element, and other internal parts that come in contact with water. Calcium deposits may build up faster, making it necessary to descale more often. Descaling ProcedureBefore you begin, you will need a large ceramic mug, fresh water, Keurig® Descaling Solution, and access to a sink. Do not use a paper cup. Ensure that there is no beverage pod in the K-Cup® pod holder. Please allow approximately 45 minutes for the descaling procedure.Empty the water from the water reservoir. If using a Keurig® Water Filter, remove and set aside.STEP 1: Descaling Solution RinsePress the power button to power the brewer off.Pour the entire bottle of Keurig® Descaling Solution into an emptied water reservoir. Then fill the empty bottle with water and pour into the water reservoir. Press the power button to turn the brewer back on.Place a large mug on the drip tray and run a rinsing brew byselecting the hot water button and selecting the largest brew size.STEP 2: Descaling Rinse & RepeatRepeat the rinsing brew process until the add water light is illuminated. Do not use a K-Cup® pod. Let the brewer stand for at least 30 minutes while still on.After 30 minutes, discard any residual solution from the water reservoir and rinse thoroughly.STEP 3: Fresh Water RinseFill the water reservoir with fresh water to and not beyond the MAX fill line.Place a large mug on the drip tray and run a rinsing brew using the largest brew size. Do not use a K-Cup® pod. Pour the contents of the mug into the sink.Repeat brew process until you have completed at least 12 rinsing brews using the largest brew size. You may need to refill the water reservoir at least one time during this process.NOTE: The cleaning action of Keurig® Descaling Solution may result in a “foam” dispensed from the brewer. This is natural, as the solution is reacting with the scale inside. For a brewer that is heavily scaled, the brewer may not fill properly after the descaler is added. If this occurs, you may see only a small or no output dispensed, followed by the sound of air blowing out. If this occurs:• Turn off and unplug the brewer.• I f there is Keurig® Descaling Solution in the water reservoir, discard the contents, rinse the water reservoir thoroughly and refill with water.• P lug the brewer back in, power on, and repeat the Step 3 Fresh Water Rinse cycle. The brewer should begin to function normally as the solution is rinsed out and the scale is removed. If problem persists, allow brewer to sit unplugged for at least 30 minutes before continuing with the rinse.Grounds in Your CoffeeGrounds may have gathered in the exit or entrance needles and can be cleaned using a straightened paper clip or similar tool.• C lean the exit needle of the K-Cup® pod holder. Refer to the exit needle care instructions.• C lean the brewer entrance needle. Refer to the entrance needle care instructions.Brewer Will Not Brew• A fter placing the K-Cup® pod in the K-Cup® pod holder,make sure that the handle is pushed down securely and the brew buttons are flashing.• I f the add water light is illuminated, add water to the water reservoir. Fill to and not beyond the MAX fill line. Make sure the water reservoir is seated properly in its base. If the add water light continues to be illuminated even after refilling, contact Customer Service.• I f 4, 6, 8, 10, 12oz, and ICED button lights are all onsimultaneously, lift handle and remove K-Cup® pod (if present in the brewer). Close handle and place a large mug on the drip tray. Press the power button once. The brewer may dispense hot water.• I f 4, 6, 8, 10, 12oz lights all blink simultaneously, contact Customer Service.Brewing a Partial Cup• T he exit needle may be clogged. Refer to the exit needle care instructions.• T he water reservoir may have been removed duringbrewing. Replace the water reservoir and perform a rinsing brew without a K-Cup® pod.• T he brewer may need to be descaled. If you have repeated the descale procedure on your brewer two times and it is still only brewing a partial cup, contact Customer Service.Brewer Does Not Have Power or Shuts Off• Make sure that the power button has been turned on. • P lug brewer into its own grounded outlet. If the electriccircuit is overloaded with other appliances, your brewer may not function properly. The brewer should be operated on its own circuit, separate from other appliances.• For energy savings, your brewer is set to turn off automatically 2 hours after your last brew. You can program your brewer to automatically turn off in 15 minute increments by adjusting the settings.• I f the brewer still doesn’t have power, contact Customer Service.Adjustable Temperature Not WorkingThe temperature is not adjustable when set to High Altitude mode. When High Altitude mode is enabled, a mountain icon will be displayed on the screen. If you attempt to adjust the temperature, the mountain icon will flash indicating you are in high altitude mode.LIMITED ONE YEAR WARRANTYKeurig Green Mountain, Inc. (Keurig) warrants that your brewer will be free of defects in materials or workmanship under normal home use for one year from the date of purchase. It is recommended that you register your brewer on /new so that yourpurchase information will be stored in our system. Keurig will, at its option, repair or replace a defective brewer without charge upon its receipt of proof of the date of purchase. If a replacement brewer is necessary to service this warranty, the replacement brewer may be new or reconditioned. If a replacement brewer is sent, a new limited one year warranty will be applied to the replacement brewer.This warranty only applies to brewers operated in the United States and Canada. This warranty gives you specific legal rights, and you may also have other rights that vary from state to state and, in the case of Canada, from province to province.Only the use of Keurig® K-Cup® brand pods and accessories will guarantee the proper functioning and lifetime of your Keurig® brewer. Any damage to or malfunction of your brewer resulting from the use of non-Keurig® pods and accessories may not becovered by this warranty or may result in a service fee if the damage or malfunction is determined to be caused by such use.WHAT IS NOT COVERED BY THE LIMITED WARRANTY?THIS WARRANTY DOES NOT COVER CONSEQUENTIAL OR INCIDENTAL DAMAGES SUCH AS PROPERTY DAMAGE AND DOES NOT COVER INCIDENTAL COSTS AND EXPENSESRESULTING FROM ANY BREACH OF THIS WARRANTY , EVEN IF FORESEEABLE. Some states or provinces do not allow the exclusion or limitations of incidental or consequential damages, so the above limitation or exclusion may not apply to you depending on the state or province of purchase.Nor does this warranty cover damages caused by use of non-Keurig® pods or accessories, services performed by anyone other than Keurig or its authorized service providers, use of parts other than genuine Keurig® parts, or external causes such as abuse, misuse, inappropriate power supply, or acts of God.OTHER LIMITATIONSTHIS WARRANTY IS EXCLUSIVE AND IS IN LIEU OF ANYOTHER EXPRESS WARRANTY , WHETHER WRITTEN OR ORAL. IN ADDITION, KEURIG HEREBY SPECIFICALLY DISCLAIMS ALL OTHER WARRANTIES WITH RESPECT TO YOURK-ELITE™ BREWER, INCLUDING ANY IMPLIED WARRANTY OF MERCHANTABILITY OR FITNESS FOR ANY PARTICULAR PURPOSE. Some states or provinces do not allow disclaimers of such implied warranties or limitations on how long an implied warranty lasts, so the above limitation may not apply to you depending on the state or the province of purchase.HOW DO YOU OBTAIN WARRANTY SERVICE?Keurig® brewers are high-quality appliances and, with proper care, are intended to provide years of satisfying performance. However, should the need arise for warranty servicing, simply call Keurig Customer Service at our toll-free phone number 1.866.901.BREW (2739). Please do not return your brewer for servicing without first speaking to Keurig Customer Service to obtain a Return Materials Authorization (RMA) number. Keurig® brewers returned without an RMA number will be returned to the sender without servicing.WarrantyHelpful HintsWater quality varies greatly. If you notice an undesirable taste in your beverage (such as chlorine or mineral tastes), we recommend using bottled or filtered water. Do not use distilled water. You can also install a Keurig® Water Filter to help remove water impurities and improve beverage taste.ServiceBeyond these recommended cleaning and maintenance procedures, this brewer is not user serviceable. For service, please refer to the Warranty section of this guide.StorageEmpty the water reservoir before storing or transporting and take care to ensure that you store your brewer in a safe and frost-free environment. Please be sure to store your brewer in its upright position to avoid water leakage from the inner tank. If you store the brewer in a cold environment, you run the risk of water freezing inside the brewer and causing damage. When you prepare to use it after storage, werecommend rinsing the water reservoir with fresh water and running three rinsing brews without a K-Cup® pod.If you plan to move your brewer to a different location, turn the brewer off, unplug it, and empty the water reservoir. If your brewer has been in an environment below freezing, please be sure to let it warm to room temperature for at least 2 hours before using.Have Questions?We’re here to help. Visit forstep-by-step videos on cleaning, descaling, and more.Still Need Help? Give us a call at1-866-901-BREW (2739)Click or Call!Coffeehouse taste in your own home.FIND YOUR PERFECT PODWith over 70 brands and hundredsof varieties, find your match at/newB AC EH I JK L MG DFFor replacement parts, please visit DC0000001165 REV BA. Water Reservoir LidB. MAX Fill LineC. Water ReservoirD. Water Reservoir Lock Tab SlotE. Power CordF. HandleG. LidH. K-Cup® Pod Holder (H and I are the K-Cup® Pod Holder Assembly)I. FunnelJ. K-Cup® Pod Assembly Housing K. Drip Tray Plate L. Drip Tray M. Drip Tray Base。
维金Lite方向控制阀门值,G1 8,G1 4和G3 8说明书

3
Strategic Rationale
• To penetrate the global in-line valve market
• $100m addressable market
• Highly competitive product to address the in-line valve market in all regions of the world
• Overview • Specification • Design features • Options & accessories • Viking Lite & Xtreme – product differences
• Price & product positioning • Launch date • Summary
Viking Lite
Directional Control Valves
G1/8, G1/4 & G3/8 Body Ported
08 November 2019
Viking Lite
Table of contents
• Strategic rationale • Product information
Accessories
• Manifold bar - Anodised aluminium • Pressure bar - Anodised aluminium
10
Viking Lite
Table of contents
• Strategic rationale • Product information
Fasttrack磨刀器说明书

2ys.ohuarrptoeonlinlogo. ks
like
either of 3.
the
above
you
are
ready
to
sharpen.
Proceed
to
3. Should your blade make contact at the top or middle of the bevel or be very
n Mark and drill a line of pilot holes through the board
approximately 25mm in from the edge. Row of Fixing
n Screw and glue (if necessary) the
Screws
batten tight up against the board - wipe away the exces1s.glue.
The board can be any reasonable size providing the 4 x rubber feet of the base sit comfortably on it.
n Position the batten along the front of the vice facing edge.
1.1.
2. 2.
3.3.
SET-UP The back of the tool (the un-bevelled side) must be ground absolutely flat before sharpening. This process is imperative if a razor sharp finish is to be acher feet x4 C. Carriage x1 D. Carriage poppers x2 E. Diamond preparation stone 220 grit (black) x1 F. Diamond finishing stone 450 grit (white) x1 G. Cleaning block x1 H. Mounting screw No.8 x 1-1 / 4 ” x1
LGK说明书

LGK说明书用途及特点LGK系列逆变式空气等离子切割机属于一种全新设计的金属加工设备,采用了二十世纪末先进的绝缘栅大功率晶体管IGBT及脉冲宽度调制(PWM)软开关技术设计制造。
该系列切割机可以切割所有金属材料,特别适合于切割火焰切割法不能切割的高合金钢和有色金属。
该系列切割机具有理想的静外特性及良好的动态特性,具备高频引弧功能,特点如下: 电弧能量高度集中,稳定性好,切割力强。
切割速度快(是气割的3 – 5倍)。
切割成本低。
切口狭窄,光洁,整齐,接近于垂直。
工件变形小。
切割电流连续可调。
引弧容易。
操作非常方便。
重量轻,体积小,便于移动。
高效率,高功率因数,是一种高效节能设备。
噪音低,适应性强。
具有自锁,非自锁两种功能,适应长短割缝的不同要求,能减少工人的劳动强度。
便于组成自动切割设备。
该系列空气等离子切割机的制造符合标准GB15579.1-2004《弧焊设备第一部分:焊接电源》。
·2··3·避免切割弧光、飞溅及铁渣对人体的危害●请佩戴足够遮光度的保护眼镜。
弧光会引起眼部发炎。
●请使用切割用皮质保护手套、长袖衣服、帽子、护脚、围裙等保护用品,以免弧光、飞溅及铁渣灼伤、烫伤皮肤。
防止发生火灾、爆炸等事故●切割场所不得放置可燃物,飞溅和烫割缝会引发火灾。
●切割电缆与母材要连接紧固,否则会发热酿成火灾。
●请勿在可燃性气体中切割或在盛有可燃性物质的容器上切割,否则会引起爆炸。
●应准备灭火器,以防万一。
防止旋转运动部件伤人●请勿将手指、头发、衣服等靠近冷却风扇等旋转部件。
防止运动中切割机伤人●采用升降叉车或吊车搬运切割机时,人员不得在切割机下方及运动前方,防止切割机落下被砸伤。
●吊装时绳具应能承受足够的拉力,不得断裂。
绳具在吊钩处夹角不应大于30°。
·4·安装说明1.安装环境(1)应放在无阳光直射、防雨、湿度小、灰尘少的室内,周围空气温度范围为-10℃~+40℃。
CKS LC Series小型精确快速切换开关产品说明书

S n a p -a c t i n gDimensions are shown: Inch (mm)Features/Benefits •C ompact design • L ong life and high electrical capacity • Q uick connect, wire lead or PC mounting • W ide variety of actuator stylesTypical Applications• Motorized equipment • Sump pump• Thermostatic controlsSpecificationsCONTACT RATING: From low level* to 10.1 AMPS @ 250 V AC.ELECTRICAL LIFE: 100,000 cyclesINSULATION RESISTANCE: 1,000 M ohm min.DIELECTRIC STRENGTH: 1,000 Vrms min. @ sea level.OPERATING TEMPERATURE: –17ºF to 185ºF (–25ºC to 85ºC).OPERATING FORCE: From 142 to 170 grams at actuator button.Forces are less at free end of lever actuators; (see OPERATING FORCE and ACTUATOR option sections).MOUNTING: 2-56 screws, torque 2.3 in/lbs max.* Low Level=conditions where no arcing occurs during switching, i.e., 0.4 VA max. @ 20 V AC or DC max.NOTE: Specifications and materials listed above are for switches with standard options. For information on specific and custom switches, consult Customer Service center.MaterialsSWITCH HOUSING: Thermoplastic polyester or high temperaturethermoplastic (PTS) (UL 94V-0).ACTUATOR BUTTON: Thermoplastic polyester (UL 94V-0).SPRING: Copper alloy.PIVOT: Copper alloy.MOVABLE CONTACTS: Fine silver for ratings greater than 1 AMP@ 125 V AC. Fine silver with 24K gold plate for 1 AMP @ 125 V AC or less.STATIONARY CONTACTS: Fine silver welded on copper alloy for*********************************************on copper alloy for ratings less than 1 AMP @ 125 V AC.TERMINALS: Copper alloy.TERMINAL SEAL: Epoxy.Build-A-SwitchTo order, simply select desired option from each category and place in the appropriate box. For additional options not shown in catalog, consult Customer Service Center.SeriesLCSP, Mom.Operating Force GG 5 oz./142 grams GD 3.3 oz./94 grams GH 6 oz./170 grams Electrical RatingX1 UL 61058-1 (see chart)V6 UL 61058-1 (see chart)V7 UL 61058-1 (see chart)F5 UL 1054 (see chart)L9 UL 1054 (see chart)M1 UL 1054 (see chart)ActuatorP00 Pin plungerA10 .28” lever roller, high force A15 .51” lever roller, high force A20 .39” lever roller, low force A25 .61” lever roller, low force T10 .29” lever, high forceT13 .22” simulated roller, high force T15 .57” lever, high force T20 .38” lever, low forceT23 .32” simulated roller, low force T25 .67” lever, low forceTerminations E SolderH .110” quick connect J Wire leadL Left formed PC thru-hole R Right formed PC thru-hole S PC Thru-hole Circuitry C SPDT W SPST N.C.Y SPST N.O.Electrical LifeNONE 6,000 operationsU* Extended 100,000 operationsSealNONE (STD.) No seal E Epoxy seal* Extended operations only available on Electrical Rating options F5, L9 and M1UL61058-1Snap-actingELECTRICAL RATINGSMALL SIZE PRECISION SNAP-ACTING SWITCHESSP MOMENTARYNOTE: Operating force varies with actuator option, see ACTUATOR option section.Consult Customer Service Center for availability and delivery of nonstandard ratings.* Note: See Technical Data section of this catalog for RoHS compliant and compatible definition and specifications.S n a p -a c t i n gSnap-actingY SPST N.O. (Single Pole, Single Throw, Normally Open)W SPST N.C. (Single Pole, Single Throw, Normally Closed)C SPDT (Single Pole, Double Throw)ELECTRICAL LIFESEALNONE 6,000 OPERATIONSU EXTENDED 100,000 OPERATIONSE EPOXY SEALNONE NO SEAL。
凯尔基凉水机产品说明书
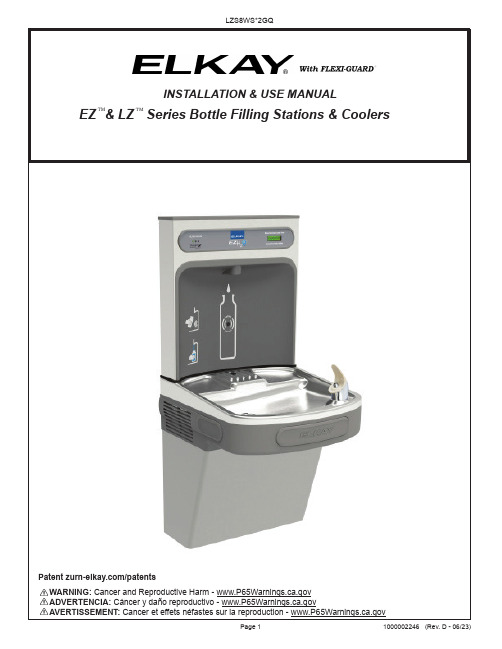
Page 11000002246 (Rev. D - 06/23)EZ & LZSeries Bottle Filling Stations & CoolersINSTALLATION & USE MANUALTM TM WARNING: Cancer and Reproductive Harm - ADVERTENCIA: Cáncer y daño reproductivo - AVERTISSEMENT: Cancer et effets néfastes sur la reproduction - Patent /patents1000002246 (Rev. D - 06/23)Page 2Page 31000002246 (Rev. D - 06/23)Page 41000002246 (Rev. D - 06/23)Page 51000002246 (Rev. D - 06/23)Bottle Filler Installation InstructionsRemove two (2) mounting screws with 5/32” Allen wrench holding top cover to Bottle Filler (See Fig. 5). Remove top cover. Note do not discard mounting screws, they will be needed to reinstall top cover.Remove wall mounting plate from Bottle Filler. Place wall plate against wall on top of basin. Center the wall plate side to side with the basin. Mark the six (6) mounting holes with a pencil (See Fig. 4).Remove wall mounting plate from wall. NOTE : Mounting plate MUST be supported securely. Add fixture support carrier if wall will not provide adequate support.Install wall mounting plate to wall using six (6) 7/16” obround mounting holes (mounting bolts not included) (See Fig. 4). Use appropriate fasteners for your wall type.Feed power cord & 3/8” water line through hole in tower/basin gasket (See Fig 6).Install gasket on bottom of bottle filler tower with gasket support bracket & (2) screws (See Fig 7).Lay Bottle Filler on water cooler basin and cut insulation from tube even with bottom of gasket, remove this insulation from the 3/8” tube, but do not discard. Feed the power cord and waterline through the hole on top of water cooler. NOTE: To prevent scratching the basin place a towel or soft cloth over the entire basin when working above it.With the power cord and waterline through hole on top of water cooler place Bottle Filler on the three (3) angled tabs protruding from the wall mounting plate installed on wall. Make sure round boss in gasket fits in hole of basin. (See Fig. 8).is installed on wall plate tabs, water line and power cord are installed properly, push top of Bottle Filler toward on Bottle Filler (See Fig. 5) with two mounting screws from step 1 above. Caution, do not over tighten screws.to the water line from bottle filler, connect Bottle Filler waterline inside of the water cooler by connecting the 3/8” water line to the tee. remove filter from carton, remove protective cap, attach filter to filter head by firmly inserting into head and rotating filterIf existing plumbing rough in locations (Drain, Water In, and Electric Supply) do not allow the filter to be mounted inside the cooler cabinet the filter can be installed horizontally below the unit. A retrofit kit is available to mount the filter beneath the cooler. for leaks and any leaks found corrected, plug Bottle Filler and unit into wall. Be sure to reinstall fuse to the circuit or the GREEN LED light should illuminate showing good filter status along with the LCD Bottle Counter.by placing cup, hand, or any opaque object in front of sensor area and verify water dispenses. Note: the first initial dispenses might have air in line which may cause a sputter. This will be eliminated once all air is purged from the line. Fig. 7Fig. 6BRACKET & SCREWSPage 61000002246 (Rev. D - 06/23)VERIFY CONTROL BOARD SOFTWARE 1) To verify the software program of the control board the unit will need to be shut down and restarted. The chiller (if present) does not need to be shut down and restarted.2) The units lower panel must be open to access the power cord and wall outlet.3) Shut down the unit by unplugging the power cord from the wall outlet. 4) R estart the unit by plugging the power cord back into the wall outlet.5) Upon start up, the bottle count display will show the software designation of BF11 or BF12.ACCESSING THE PROGRAMMING BUTTON1) T o access the program button, remove the top cover of the bottle- filler. Remove the two (2) screws holding top cover to bottle-filler with a 5/32” allen wrench. Remove top cover. Do not discardmounting screws, they will be needed to reinstall the top cove afterprogramming operations are completed. The programming button is located at the top right side of the unit on the control board. NOTE: When applicable, there is also an alternate reset button located on the lower part of the water cooler. After removing the bottom cover, the reset button will be located on the left side of the cooler, mounted on the side panel support.RESET THE FILTER MONITOR1) Instructions apply to filtered units only.2) Depress the program button for approximately 2 seconds untilthe display changes then release. The display will change andscroll through two messages:“RST FLTR” – Reset Filter Monitor“SETTINGS” – System Settings Sub MenuIf the program button is not pushed again the display will scrollthrough the two messages above for three cycles and then default back to bottle count and be back in run mode.3) When the display changes to “RST FLTR”, depress the buttonagain. The display will change to show “FLTR =”. Depress thebutton again and the display will show “FLTR =0”4) The Green LED should be illuminated indicating that the visualfilter monitor has been reset.SETTING RANGE OF THE IR SENSOR WHERE APPLICABLE 1) Depress the program button for approximately 2 seconds untilthe display changes then release. The display will change andscroll through two messages:“RST FLTR” – Reset Filter Status LED“SETTINGS” – System Settings Sub MenuIf the program button is not pushed again the display will scrollthrough the two messages above for three cycles and then default back to bottle count and be back in run mode.2) When the display changes to “SETTINGS”, depress the buttonagain. The display will change to show“RNG SET” - Range set for IR sensor.“UNIT TYP” - Type of unit (REFRIG or NON-RFRG)“FLT SIZE” - Select filter capacity“RST BCNT” - Reset bottle count3) W hen display shows “RNG SET” push program button once thedisplay will show current value (can be 1 – 10) e.g. “RNG = 3”.4) Once display shows current value push the program button toscroll through value of 1 – 10. Select the desired range setting,"1" being closest to sensor and "10" being farthest away.5) Once range is selected allow approximately 4 seconds to pass and then the display will go back to bottle counter and be in run mode.6) T est bottle filler by placing bottle or hand in front of sensor tomake sure water is dispensed.SETTING UNIT TYPE1) Depress the program button for approximately 2 seconds until the display changes then release. The display will change and scrollthrough two messages:“RST FLTR” – Reset Filter Status LED“SETTINGS” – System Settings Sub MenuIf the program button is not pushed again the display will scrollthrough the two messages above for three cycles and then default back to bottle count and be back in run mode.Continued from below:2) When the display changes to “SETTINGS”, depress the button again. The display will change to show “RNG SET” - Range set for IR sensor.“UNIT TYP” - Type of unit (REFRIG or NON-RFRG) “FLT SIZE” - Select filter capacity “RST BCNT” - Reset bottle count 3) W hen display shows “UNIT TYPE” push program button once the display will show current value. C an be REFRIG or NON-RFRG 4) Push button once to change value. Once value is s elected the display will show the new value. (Can be REFRIG or NON-RFRG) “REFRIG“ - stands for refrigerated product. In this setting the flow rate isestimated at 1.0 gallon per minute.“NON-RFRG“ - stands for nonrefrigerated product. In this setting the flow rate is estimated at 1.5 gallons per minute. Both “REFRIG“ and“NON-RFRG“ simulate 1 bottle equal to 20 oz.5) A llow approximately 4 seconds to pass and the display will return to bottle counter and be in run mode. RESETTING BOTTLE COUNT1) Depress the program button for approximately 2 seconds until the display changes then release. The display will change and scroll through two messages: “RST FLTR” – Reset Filter Status LED“SETTINGS” – System Settings Sub Menu If the program button is not pushed again the display will scroll through the two messages above for three cycles and then default back to bottle count and be back in run mode.2) When the display changes to “SETTINGS”, depress the button again. The display will change to show: “RNG SET”- Range set for IR sensor. “UNIT TYP” - Type of unit (REFRIG or NON-RFRG)“FLT SIZE” - Select filter capacity “RST BCNT” - Reset bottle count If the button is not pushed again the display will scroll through the four messages above for three cycles and return to run mode.3) W hen display shows “RST BCNT” push program button once the display will show current value, e.g. “0033183”.4) Once display shows current value push the program button once more to reset back to 0. The display will show BTLCT = 0 for approximately 2seconds and then return to run mode showing 00000000 bottles. NOTE: Once the bottle count is reset to zero there is no way to return to the previous bottle count.5) T esting the bottle counter: REFRIG units: Place bottle or hand in front of sensor for approximately 9 seconds to see bottle counter count 00000001, (This is based on filling a 20 oz. bottle).NON-RFRG units: Place bottle or hand in front of sensor for approximately 6 seconds to see bottle counter count 00000001, (This is based on filling a 20 oz bottle). SETTING FILTER CAPACITY 1) Depress the program button for approximately 2 seconds until the display changes then release. The display will change and scroll through two messages: “RST FLTR” – Reset Filter Status LED “SETTINGS” – System Settings Sub Menu If the program button is not pushed again the display will scroll through the two messages above for three cycles and then default back to bottle count and be back in run mode.2) When the display changes to “SETTINGS”, depress the button again. The display will change to show:“RNG SET“- Range set for IR sensor. “UNIT TYP“ - Type of unit (REFRIG or NON-RFRG) “FLT SIZE” - Select filter capacity “RST BCNT“ - Reset bottle countIf the button is not pushed again the display will scroll through the four messages above for three cycles and return to run mode.3) W hen display shows “FLT SIZE” push program button once. The display will show current value. Can be 3000GAL or 6000GAL.4) Push program button again to display the desired “FLT SIZE”. 5) Allow approximately 4 seconds to pass and the display will return tobottle counter and be in run mode.BF11 - BF12 PROGRAMSETTING THE CONTROL BOARDPage 71000002246 (Rev. D - 06/23)Page 81000002246 (Rev. D - 06/23)BUBBLER DETAILFig. 10NOTE:When installing replacement bubbler and pedestal, tighten nut only to hold parts snug in position. Do Not Overtighten.VANDAL RESISTANT BUBBLER DETAIL24Scan for trouble shooting and to sign up forauto replenishment of authentic Elkay filters.Page 91000002246 (Rev. D - 06/23)PRINTED IN U.S.A.FOR PARTS, CONTACT YOUR LOCAL DISTRIBUTOR OR CALL 1.800.834.4816REPAIR SERVICE INFORMATION TOLL FREE NUMBER 1.800.260.6640ELKAY MANUFACTURING COMPANY • 1333 BUTTERFIELD ROAD,SUITE 200 • DOWNERS GROVE, IL 60515 • 630.574.8484 • *INCLUDES RELAY & OVERLOAD. IF UNDERWARRANTY, REPLACE WITH SAME COMPRESSORUSED IN ORIGINAL ASSEMBLY.NOTE:All correspondence pertaining to any of the abovewater coolers or orders for repair parts MUST includeModel No. and Serial No. of cooler, name and part numberof replacement part.ITEM NO.28401C000000133736216C100000219456092C56229C66703C10000018771000004564100000457556073C98734C100000160098773C36066C000000024598776C000000025698778C98898C100000219598724C0000001144100000160297446C1000001791100000181235826C36004C000000133927416C27413CSee Filter TableHanger BracketBasin - Stainless SteelWiring - Front/Side Push BarCompr - Service PakTube - Poly (Cut To Length)Assy - Shroud - Upper (Front Side Push)DrierKit - Drain Replacement EZ (BF)(Brkt/Tube/Ftg/Clamp)Kit - Regulator w/Holder & NutKit - Solenoid Valve/Regulator AssyKit - Flexi Bubbler/“O”-Ring/NutKit - Pushbar (Front/Side) EZS TLKit - Pushbar (Front) EZS TLKit - Cold Control/ScrewsInternal Pwr CordKit - Fan Motor Assy/Blade/Mtr/Shroud/Screws/NutKit - Condenser/DrierKit- Compr Mtg Hdwe/Grommets/Clips/StudsKit - Heatx/DrierKit - Hardware (EZ)Kit - Elect/Relay/Overload/CoverKit - Evaporator AssemblyTee - 1/4” x 1/4” x 3/8”Kit - 75583C Elbow 5/16” x 1/4”Kit - VR Bubbler ShortKit - VR Bubbler Nipple W/GasketKit - Bottle Filler Drain (EZ)Power InletJumper Wire (White)Ferrule-Drain (BF)Wrapper - StainlessWrapper - Light GreyWater Filter Kit (When Provided)PART NO.DESCRIPTION123*456789101112131415161718192021222324252627282930NSNSBOTTLE FILLER REPLACEMENT PART KITSNSNSNSNS30NSNSNSNSITEM NO.PART NO.DESCRIPTION98631C98544C100000457498546C98547C98549C98551C98552C1000001813Kit - Electrical Package-220VKit - IR SensorKit - BF Solenoid Valve Replacement-220VKit - Aerator ReplacementKit - Top Cover ReplacementKit - Hardware & Waterway PartsKit - Filter Mounting CoverKit - Retro Filter MountingKit - Tower/Basin Gasket220V PARTS LISTNS = NOT SHOWNNS = NOT SHOWNPage 101000002246 (Rev. D - 06/23)。
Tesa Technology G-1 与 G-2 杆式直径测量指示器说明书

G-1L e v e r -t y p e D i a l T e s t I n d i c a t o r s42.5171.558.366.318.41.51.512.536.5358,546,4ø 1,51,65mm mm inN (± 15 %)Stem length, mm LCD, 5 digits + unit Display digit height 6 mmMax. perm. errors: f f Pre-span = 0,05 mm Repeatability: f Hysteresis :f L = 12,5 mm; max. 0,05 m/s L = 36,5 mm; max. 0,15 m/s Number of measure-ments per second: 9Zero-setting RS2323 V lithium battery, type CR2032Battery life > 4000 hoursOperating tempera-ture range: +5°C to + 40°C Degree of protec-tion: IP65 (IEC 529)EN 61326-173 g (L = 12,5 mm) 75 g (L = 36,5 mm)Supplied in a plastic case with:1 Insert with a2 mm dia.(No. 01860202)DIN 2270 NF E 11-053mm mm Ø, mm Insert, mm 018100050,8018100060,8018100070,5018100080,5018100090,2018100100,2S180016950,2TESATAST Standard ModelsDIN 2270 NF E 11-053Rotating dial Very low measuring force, see table.Movement with patented shock proof system Lever system with friction drive to prevent overload Accuracy: see table.Supplied in a plastic case together with: 1 Insert with a 2 mm dia. mm mm Ø, mm Insert, mm 018102040,8018102050,5018103040,2TESATAST Perpendicular Modelsmm mm Ø, mm Insert, mm 018110000,8018110010,2Same technical data as standard models, but equipped with a 2 mm dia. ruby ball tip No. 01860302.SWISSTAST Standard Models12,5M 1,4ø212,5M 1,4ø312,5M 1,4ø101860307Ball tip, mm Ball tip material mm 01860201018602020186020301860211M1,4 coupling threadTESATAST Measuring InsertsDIN 2270 NF E 11-053Technical data: see description for each productmm mm Ø, mm Insert, mm 0181001101810012018100130184010501840104018600080184020201860401mmmm 01860008Mounting rodFixing Shank0184040401840405mm018404060184040701840501Deviation range over partial Stylus insert with angular position of 12°all models interapiD 312 are designed to give a true reading when the angle between the stylus and the workpiece surface is 12° (fig. a).in any other measuring position, including parallel position of the stylus against the workpiece surface, measured readings have to be corrected accordingly (fig. B). please consult the instruction manual on this subject.–Safe reading thanks to secondary pointer totalling the number of revolutions made by the main pointer.–Bidirectional measuring with automatic reversal within the movement.–Pointer rotation direction is always constant due to automatic reversal effect. –Jewelled movement with rubies.–Ball-bearing lever system. Measuring insert swivelling through 210°. –Particularly robust due to full-metal construction.–Monobloc housing with mounting through dovetail clamping and a Ø 4 mm swivelling shank.mm mmØ, mm Insert, mm Rotating dial Very low measuring force: (see table for tolerance limits) Lever system with friction drive to prevent overload Accuracy: see table for tolerance limits Supplied in a plastic case with:1 with a Ø2 mm insert in hardenedmm mmØ, mm Insert, mm074111366 074111502 074111503 074111504 074111505INTERAPID 312 lever test indicators as listed in the table below:Technical data: seedescription for eachproductmmmmmm Ball tip, mm Ball tip material L mm M1,7 coupling threadmm0,01 13 30,01 13 30,01 26 3Total travel, mm μm μm μm Travel/ Ø, mm N Insert L1, DIN 2270 and factory standard Rotating dialContact points with tungsten carbide ball tips Friction lever system to prevent overloadSupplied in a plastic case, including: 1 contact point, 2 mm dia.220).Inspection report with a declaration of conformity≤ 0,3518 ≤ 0,3518 0 ÷ 50 ÷100≤ 0,2036 0 ÷ 50 ÷ 100≤ 0,2036 ≤ 0,3018 ≤ 0,3018 Total travel, mm μm μm μm Travel/ Ø, mm N Insert L1, mmTotal travel mm μm μm μm Ø, mm N Insert L1, 0,01130,01130,0113Total travel, mm μm μm μm Travel/ Ø, mm N Insert 0,011330,011330,012630,012630,002131,5DIN 2270 and factory standard Rotating dial Contact points with tungsten carbide ball tips Friction lever system to prevent overloadSupplied in a plastic storage case,in-cluding:1 contact point, No. 01840109Inspection report with a declaration of conformityBall tip, mm Ball tip material L1, mm L2, mm M1,6 coupling threadThe original inserts mounted on all indicators are fully interchangeble 0186601401850106sptStem Clamping length01860401mmmm01860008Mounting rod Fixing Shank0184040401840405mm01840406018404070184050101840105018401040186000801840202。
- 1、下载文档前请自行甄别文档内容的完整性,平台不提供额外的编辑、内容补充、找答案等附加服务。
- 2、"仅部分预览"的文档,不可在线预览部分如存在完整性等问题,可反馈申请退款(可完整预览的文档不适用该条件!)。
- 3、如文档侵犯您的权益,请联系客服反馈,我们会尽快为您处理(人工客服工作时间:9:00-18:30)。
CJTKC电动操作机构安装使用说明书0TK.466.5018泰开集团山东泰开隔离开关有限公司二〇一一年六月目录目录 (1)一、机构的主要特点 (2)二、CJTKC电动机构技术参数表: (3)三、使用环境条件 (3)四、结构和工作原理 (3)1、结构 (3)2、机构安装尺寸及外形尺寸 (4)3、工作原理 (6)五、安装和调试 (6)1、安装前检查 (6)2、调试步骤: (6)3、角度调节: (7)六、常见故障处理: (8)1、电动操作不动作 (8)2、接触器不动作或有异常声音 (8)七、储存: (8)八、注意事项 (8)九、随机文件 (9)十、订货须知 (9)CJTKC电动机构A相二次原理图(非汇控相) (10)CJTKC电动机构A相二次接线图(非汇控相) (11)CJTKC电动机构B相二次原理图(汇控相) (12)CJTKC电动机构B相二次原理图(汇控相) (13)CJTKC电动机构C相二次原理图(非汇控相) (14)CJTKC电动机构C相二次原理图(非汇控相) (15)附录:电动机构投运的条件 (16)CJTKC电动机操动机构是交流380V三相电动机驱动,通过蜗轮、蜗杆两级减速或齿轮及蜗轮、蜗杆三级传动的操动机构,可以用来驱动800kV及1100kV等电压等级的户外隔离开关和接地开关。
一、机构的主要特点1、适用性强:CJTKC电动机构可配用800kV及1100kV户外隔离开关和接地开关;2、CJTKC电动机构可靠性高:2.1传动系统操作平稳,冲击力小、自锁可靠、噪音低;2.2机构的限位装置可有效防止分、合到位后输出轴可能发生的继续转动,保证隔离开关(接地开关)不受损伤;2.3机构的联锁装置可以满足多种联锁及五防闭锁功能,能有效防止误操作;3、机构采用不锈钢板焊接而成,结构合理、外形美观,并具有有效的防锈、防腐功能。
4、箱盖采用凸台式机构,能有效的加固箱体;5、箱体与输出轴的密封采用油封及气体迷宫的双层密封结构,箱门的密封采用的是箱变折弯及气囊密封结构,能起到很好的防水、防尘效果,满足防护等级IP54的要求;凸台式顶盖机构防水机构6、机构整体机构简单,布局合理,零部件具有很强的互换性。
机构的正门和侧门可以在任意时候打开,方便的进行检查维护或更换零件;7、机构与隔离开关(接地开关)联结采用夹板式,不需焊接。
机构与传动杆的连接示意图二、C JTKC电动机构技术参数表:1、周围空气温度:-50℃—+50℃;2、海拔:3000m及以下;3、风压:不超过700Pa;4、地震烈度:不超过8度;5、污秽等级:不大于Ⅳ级;6、不适用于有易燃物质,爆炸危险,化学腐蚀及剧烈震动的场所;7、不适用于非水平安装的场所。
四、结构和工作原理1、结构传递给机构主轴,安装时借助于钢管连接使隔离开关或接地开关分合闸。
机构由电动机、机械减速传动系统、电气控制系统、加热系统、联锁装置及箱体组成。
1.1 电动机为三相交流异步电动机。
1.2根据电动机构所使用的位置不同,机械减速传动系统采用集成的双蜗轮蜗杆结构及齿轮及双蜗轮蜗杆结构进行减速,密封式结构,6007航空润滑脂。
具有操作平稳、冲击力小、噪音低、自锁可靠、外形美观、重量轻等优点。
1.3电气控制系统包括电源开关(低压断路器)、分合停控制按钮、接触器、电机保护器、远方就地选择开关、行程开关、温度湿度控制器、辅助开关、加热器、接线端子、照明灯、汇控分相选择开关(根据实际选择)。
如用户需要还可配置等其他电器元件,只需在合同中注明即可。
(a)辅助开关为F9型,供用户电气联锁及信号指示用,接点对数可按用户要求供应。
常规为10常开10常闭。
(b)为避免电动机因意外故障而过载烧坏,本机构装有低压断路器和电机保护器对电动机进行保护。
(c)为保证手动操作人员安全,本机构在装手柄处设有手动闭锁开关。
1.4 机构通过“联锁”接点,可以满足与其他设备的相互闭锁;1.5 为满足手动操作力的要求,在减速器原手动操作位置增加省力装置,有效降低手动操作力,提高现场调节的可操作性;1.6箱体为不锈钢焊接拉丝,采用三侧开门结构。
其外形美观、结构合理,具有可靠的防水、防尘、防腐及防锈蚀性。
对各种地域均能适应,与传统的铆接和螺栓连接结构相比,更为轻巧和美观。
2、机构安装尺寸及外形尺寸CJTKC电动机构的安装尺寸为250³300,详见外型及安装尺寸图。
3、工作原理CJTKC电动机构的控制原理图附后;3.1单相电气控制操作:首先,将机构手动摇至分合中间位置,将机构中“汇控、分相”旋钮指向“分相”,将“远方、就地”指向“就地”位置,然后接通三相电源,电动操作时,注意机构输出轴运动方向(或开关运动方向)与输入指令是否一致,如机构运动方向与要求相反,应立即按下停止按钮,更换电源进线相序,再次进行电动操作;3.2三相联动电气控制操作:在保证单相电动操作正确的情况下,将三相电动机构按照与单相操作时相同的相序接入电源,将A、B、C三相电动机构中的“汇控、分相”旋钮指向“汇控”,将“远方、就地”指向“就地”位置,接通电源,进行电动操作,如需停止,可直接按下B相机构中的“停止”按钮;在“就地”操作试验后,将“汇控、分相”旋钮指向“汇控”,“远方、就地”指向“远方”位置,然后进行后台汇控操作;五、安装和调试1、安装前检查为确保安全可靠运行,安装前应进行下列检查方可安装。
1.1 拆箱后检查机构外观是否完整,铭牌数据与订货要求是否相符。
1.2 检查机构箱内附件是否齐全,如手柄、合格证、说明书等。
1.3 用手柄进行数次空载分合操作,检查机构传动是否正常,行程开关和辅助开关切换是否正常。
1.4 接通电源,电动操作数次,检查机构动作是否正常。
注意:首次使用新电源进行电动操作前,应先将机构置于合、分中间位置。
再进行电动操作,检查输出轴选择方向是否正确,若不正确应立即按下“停止”按钮,在端子排处调节相序。
2、调试步骤:2.1在隔离开关(或接地开关)安装完毕后,将机构挂装在基础架上,先不要紧固机构背面的四个安装螺栓,然后用铅锤找好机构主轴和隔离开关(或接地开关)传动主轴使之同心,最后将安装螺栓固紧。
2.2 配好隔离开关转动主轴与机构输出轴之间的传动杆,用接头连接。
用手动操作机构,后使隔离开关(或接地开关)和机构都处于合闸终点位置,然后将紧固接头松开,手动将电动机构手动回转6—8圈,然后紧固接头螺栓,再进行操作几次,确保隔离开关(或接地开关)和机构分合正常。
2.3 按相应的接线图连接控制线,检查无误后接通电源进行电动试操作。
在电动操作前,应先将机构手摇至分合闸中间位置,拉下手动闭锁滑板,再按分、合闸按钮检查电动机旋转方向是否正确,若发现隔离开关(或接地开关)运动方向与指令不符,应立即切断电源,将三相电源任意二相互换一下,再重复以上过程,至转向正确。
电动连续操作分合数次,必须保证隔离开关(或接地开关)和机构分合动作正常,控制回路电气联锁、导电接触可靠,各有关连接部分无松动现象,机械传动平稳可靠,无异常声响。
2.4 电动操作完毕,检查各连接部位可靠拧紧,并作紧固标志。
2.5 检查控制回路联锁关系正确,加热、照明回路工作正常。
3、角度调节:当开关要求电动机构输出角度有变化时,可通过移动行程开关在扇形导轨中的位置进行调整,以达到调整电动机构输出角度的目的。
例如:如下图所示此时如需要增大输出角度,可以先将固定螺栓2松至扇形板1能自由转动,然后将扇形板1向行程止挡6处移动少量行程,使之行程止挡3的行程量增加,达到增大输出角度的目的;(注:允许最大调节量分合两侧各±5°)角度调节示意图下几点:4.1 有手柄操作机构,检查传动系统是否灵活,行程开关、辅助开关能否正常切换,分、合闸指示是否正确;4.2 连接部分,紧固件有无松动;4.3 控制回路、辅助开关、行程开关、接触器、电动机构保护器、空气开关等,电器元件有无损坏,接触是否良好;4.4 箱门的密封是否可靠、牢固。
六、常见故障处理:1、电动操作不动作可能原因:(1)电机电源或控制电源断相、电源没接通或与机构实际不符;(2)控制回路或电机回路不通;(3)接线头有松动,存在虚接;处理方式:(1)使用万用表检测电机电源、控制电源是否已经提供与机构铭牌标识相同的电源;(2)检查电机回路与控制回路是否断路①、试验时“联锁”及“五防”是否短接(需要接联锁时将短接线拆除);②、检查机构行程开关是否正常转换,“远方、就地”“汇控、分相”是否处于正确位置;(3)将虚接线压紧;2、接触器不动作或有异常声音可能原因:(1)接触器接线不良;(2)接触器触头或内部有异物;(3)控制回路短路;处理方式:(1)检查接触器接线是否存在虚接;(2)清理接触器触电和磁铁吸合接触面;(3)按照二次图纸及“电机检查”方式进行检查回路;七、储存:产品启封后如不立即安装或要长期存放时,须存放在干燥有遮蔽场所。
如储藏需要超过6个月,建议定期使用加热器给机构加热去潮。
八、注意事项1、当进行手动操作时,先将手动闭锁滑至露出手动操作孔,将手柄插入进行操作;拔出手柄将手动后,确保闭锁滑板回复至原位置时,方可进行电动(或远动)操作。
2、除调试及检查电动机操动机构外,严禁内门未关闭时操作电动机操动机构;3、为防止意外,现场在正门把手处必须加挂明锁;4、机构正常运行时,严禁用手直接触摸加热器,以防烫伤。
九、随机文件本机构采用木箱包装,机构本体、手柄及随机文件均装在一个箱内。
本机构一般随隔离开关成套供应,根据用户需求也可以单独供应,每台机构的随机文件见表。
十、订货须知订购CJTKC电动机操动机构时应注明以下内容:1、型号、规格和数量;1.1主轴输出转角及操作时间;1.2控制电压、电动机电压及电源性质;1.3辅助开关的触点对数(不指明时为只配辅助开关10开10闭);1.4是否配备其他特殊电器元件。
1.5是否采用三相汇控操作。
2、除以上各项外,用户若还有其它特殊要求,在订货时也应指明。
3、我公司电动操作机构除CJTKC以外,还配有用于110kV及以下产品的CJTKB电动机构、用于550kV以下、110kV以上的CJTKA电动机构;4、产品到货后,应及时进行验收,如发现有问题,应立即与我方联系,以便及时处理。
欢迎企业选购我厂产品,并热忱希望您对我企业的产品提出宝贵的意见和建议。
J D MJ D M附录:电动机构投运的条件电动机构投运所需要具备的条件包括:1、电机电源、控制电源与电动机构铭牌刻制的实际所需电源一致;2、电机电源相序正确,单相及三相联动时,机构能正确完成指令;3、电动机构“远方、就地”、“汇控、分相”电动操作均能正确完成工作指令;4、电动机构的手动闭锁位置闭合;5、端子排中“五防闭锁”、“联锁”两处预留端子,用户已经接入联锁线或已经短接;6、机构与隔离开关的连杆连接已经紧固;7、检查各位置紧固螺栓及其他固定件连接完成;8、检查其他相关设备;。