挤压铝型材课程设计报告
挤压铝型材 截面设计
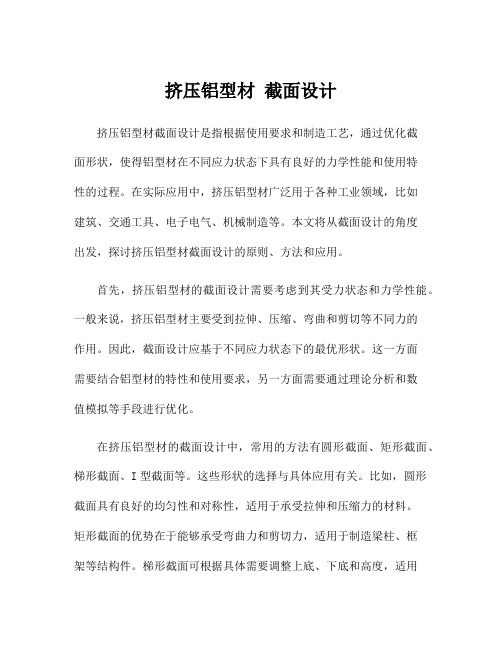
挤压铝型材截面设计挤压铝型材截面设计是指根据使用要求和制造工艺,通过优化截面形状,使得铝型材在不同应力状态下具有良好的力学性能和使用特性的过程。
在实际应用中,挤压铝型材广泛用于各种工业领域,比如建筑、交通工具、电子电气、机械制造等。
本文将从截面设计的角度出发,探讨挤压铝型材截面设计的原则、方法和应用。
首先,挤压铝型材的截面设计需要考虑到其受力状态和力学性能。
一般来说,挤压铝型材主要受到拉伸、压缩、弯曲和剪切等不同力的作用。
因此,截面设计应基于不同应力状态下的最优形状。
这一方面需要结合铝型材的特性和使用要求,另一方面需要通过理论分析和数值模拟等手段进行优化。
在挤压铝型材的截面设计中,常用的方法有圆形截面、矩形截面、梯形截面、I型截面等。
这些形状的选择与具体应用有关。
比如,圆形截面具有良好的均匀性和对称性,适用于承受拉伸和压缩力的材料。
矩形截面的优势在于能够承受弯曲力和剪切力,适用于制造梁柱、框架等结构件。
梯形截面可根据具体需要调整上底、下底和高度,适用于承受不同比例压缩力的结构。
I型截面则常用于承受大跨度梁的弯曲力。
此外,挤压铝型材的截面设计还需要考虑到材料的节能性能和强度。
对于建筑领域的铝型材来说,节能是一个重要指标。
截面设计可以通过减小型材的外壁厚度,增加空腔的使用,减轻铝材的重量,提高铝材的节能性能。
同时,合理的截面设计还能够提高铝材的屈服强度和抗拉强度。
在实际应用中,挤压铝型材的截面设计需要结合制造工艺和可加工性进行考虑。
为了实现设计要求,挤压铝型材的截面形状需要符合挤压成形的要求。
比如,截面的尺寸应尽量避免突变,避免内外壁厚度的突变,避免造成挤压后型材在成型过程中出现溶胀和折叠等问题。
总之,挤压铝型材截面设计是一个综合考虑材料特性、使用要求和制造工艺的过程。
通过充分理解材料的受力状态和力学性能,合理选择截面形状,并结合制造工艺进行设计优化,可以提高挤压铝型材的力学性能、可加工性和经济性。
铝型材挤压模具设计课件

铝型材挤压模具设计课件一、铝型材挤压工艺概述二、铝型材挤压模具结构三、铝型材挤压模具设计原则1.尺寸精度:铝型材挤压模具设计时要保证挤压后的铝型材尺寸精度。
模具的内芯设计需考虑材料的收缩率和强度,确保挤压后的铝型材尺寸准确。
2.结构合理:铝型材挤压模具设计时应尽量减小模具的重量和尺寸,提高模具的使用寿命。
同时,要增加模具的刚度和强度,确保在挤压过程中不会变形或断裂。
3.表面质量:铝型材挤压模具的表面光洁度直接影响到挤压后的铝型材表面质量。
因此,在设计模具壳和模具翼时应注意表面的光洁度,减少表面缺陷。
4.降低生产成本:铝型材挤压模具的设计应考虑降低生产成本。
例如,可以采用可更换模具芯片的设计来替换整个模具,从而降低维修和更换模具的成本。
四、铝型材挤压模具制造工艺1.材料选择:铝型材挤压模具一般选用高硬度、高强度的工具钢,如优质合金工具钢或高速工具钢等。
2.预先加工:将选定的工具钢进行粗加工,包括锻造、切割、拉伸等工艺,将模具的初始形状制作出来。
3.精密加工:通过数控加工等精密加工技术,对模具进行精细加工,包括车削、铣削、镗削、磨削等工艺,保证模具的尺寸精度和表面质量。
4.表面处理:对模具进行表面处理,如热处理、氮化等工艺,提高模具的硬度和耐磨性。
5.装配调试:将各个组成部分进行装配,并进行调试,保证模具的合理性和可靠性。
五、铝型材挤压模具的维护与保养1.清洁:定期对铝型材挤压模具进行清洁,除去铝屑和污垢,保持模具的清洁度。
2.润滑:对铝型材挤压模具的摩擦部位进行润滑,减少磨损和摩擦力,并延长模具的使用寿命。
3.定期检查:定期对铝型材挤压模具进行检查,发现问题及时修理,确保模具的正常使用。
4.储存:将不使用的铝型材挤压模具储存到干燥、防尘的环境中,避免受潮和污染。
六、铝型材挤压模具的发展趋势1.高精度:随着制造业对产品精度要求的提高,铝型材挤压模具的精度也将不断提高。
2.高效率:铝型材挤压模具的开发将更加注重提高生产效率和降低能耗。
铝的实训报告(3篇)

第1篇一、引言铝作为一种轻质、高强度、耐腐蚀的金属材料,广泛应用于航空航天、交通运输、建筑、电子电器等领域。
为了深入了解铝的性质、加工工艺和应用,我们开展了铝的实训项目。
本文将详细记录实训过程中的观察、实验结果和分析。
二、实训目的1. 了解铝的基本性质和分类;2. 掌握铝的加工工艺,如铸造、轧制、焊接等;3. 研究铝在各个领域的应用;4. 培养实践操作能力和分析问题能力。
三、实训内容1. 铝的基本性质和分类铝是一种银白色的轻金属,具有良好的导电性、导热性和耐腐蚀性。
铝的密度约为2.7g/cm³,仅为钢铁的1/3,且具有较好的机械性能。
铝的化学性质活泼,容易与氧气、水等反应。
铝的分类如下:(1)按纯度分类:工业纯铝、高纯铝、特殊纯铝;(2)按成分分类:变形铝合金、铸造铝合金、特种铝合金。
2. 铝的加工工艺(1)铸造:铝的铸造方法主要有砂型铸造、金属型铸造、压铸等。
铸造过程中,需要根据不同的要求选择合适的铸造方法、模具和浇注系统。
(2)轧制:铝的轧制方法主要有热轧和冷轧。
热轧主要用于生产厚板、中厚板等;冷轧主要用于生产薄板、带材等。
(3)焊接:铝的焊接方法主要有熔化极气体保护焊、氩弧焊、激光焊等。
焊接过程中,需要根据不同的要求选择合适的焊接方法、焊接参数和焊接材料。
3. 铝的应用(1)航空航天:铝及其合金在航空航天领域具有广泛的应用,如飞机蒙皮、发动机部件、结构件等。
(2)交通运输:铝及其合金在交通运输领域具有重要作用,如汽车、火车、船舶的轻量化、节能降耗。
(3)建筑:铝及其合金在建筑领域应用广泛,如门窗、幕墙、屋顶等。
(4)电子电器:铝及其合金在电子电器领域具有重要作用,如电子元件、散热器、机壳等。
四、实训过程及结果1. 铝的物理性质测试通过实验,我们得到了铝的密度、导电性、导热性等物理性质数据。
实验结果显示,铝的密度约为2.7g/cm³,导电性为3.77×10⁶S/m,导热性为237W/m·K。
铝型材挤压工艺设计

挤压一.操作规程:1.采用加温100℃/1小时的梯温形式,将盛锭筒加温至380℃---420℃。
2.根据作业计划单,选择适量的合适铝棒进棒炉加温至480℃---520℃,特殊的工业型材按规定的工艺温度执行。
3.根据作业计划单选定符合计划单的模具,加温至460℃---500℃,保温2---4小时。
4.启动挤压机冷却马达——油压马达。
5.根据计划单顺序,选定模具专用垫装在模座中,将模座锁定在挤压位置。
6.将盛定筒闭锁,将加热过的铝棒利用送料架升至料胆对齐位置。
7.主缸前进挤压8.挤压时刚起压速度要慢,中速挤压速度视出料口型材表面质量适当调整。
9.将模具编号、铝棒编号、主缸压力、出料速度等详细记入原始纪录。
二.工艺要求1.铝棒加热上机温度为:A平模:500℃---520℃ B.分流模:480℃---500℃ C.特殊工业材按特殊的工艺要求执行。
2.模具加温工艺:A.平模:460℃---480℃B.分流模:460℃---500℃3.盛定筒温度:380℃---420℃盛锭筒端面温度为280℃---360℃4.挤压出的料必须表面光滑,纵向压痕无手感,挤压纹细致均匀,无亮带、黑线、阴阳面平面间隙、角度偏差,切斜度按国标高精级。
5.挤压力:≤200㎏/cm26.料胆闭锁压力120㎏/cm2—150㎏/cm2。
7.液压油温度≤45℃8.型材流出速度一般控制在:5米/分钟---30米/分钟9.模具在炉内的时间:≤8小时10.每挤压80支棒-100支棒,必须用专用清缸垫清理一次料胆。
三.注意事项1、挤压时,如塞模,闷车时间不得超过5秒。
2、装模时,注意安全,防止螺丝滑脱砸伤脚。
3、出料时,严禁直线向出料口窥视。
4、装模上机前,必须检查中心位,挤压杆是否对中,开机前空载试机运行一次,确认无误正式开机。
5、测棒温,模温,盛锭筒温是否达到要求。
6、3—5支棒检查一次质量。
7、经常检查油温。
8、每支铝棒是否有炉号、合金牌号标示。
deform挤压模拟课程设计报告书
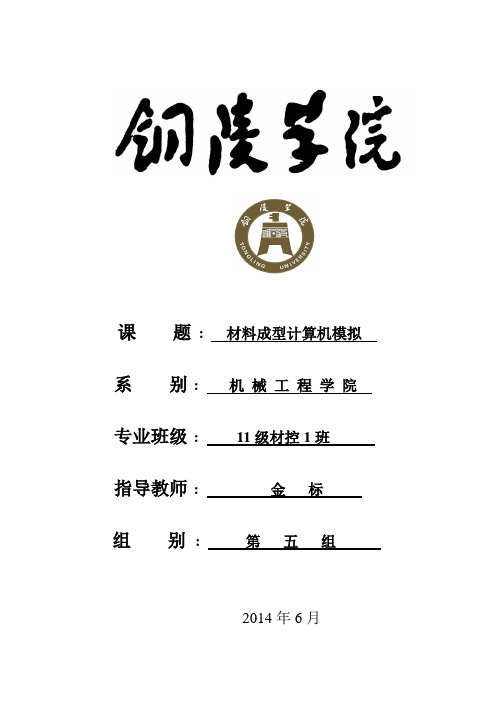
课题: 材料成型计算机模拟系别: 机械工程学院专业班级: 11级材控1班指导教师: 金标组别: 第五组2014年6月第一章课程设计容及任务分配.................................................................................................................. - 1 - 1.1 概述.......................................................................................................................................................... - 1 - 1.2 设计目的.................................................................................................................................................. - 1 - 1.3 设计容...................................................................................................................................................... - 1 - 1.4 设计要求.................................................................................................................................................. - 1 - 1.5 挤压方案任务分配.................................................................................................................................. - 2 - 第二章工艺参数.......................................................................................................................................... - 3 - 2.1 工艺参数的设计...................................................................................................................................... - 3 - 2.1.1 摩擦系数的确定.................................................................................................................................... - 3 - 2.1.2 挤压速度的确定.................................................................................................................................... - 3 - 2.1.3 工模具预热温度的确定........................................................................................................................ - 3 - 第三章模具尺寸的确定.............................................................................................................................. - 4 - 3.1 挤压工模具示意图.................................................................................................................................. - 4 - 3.2 模具尺寸的确定...................................................................................................................................... - 4 - 3.2.1挤压模结构尺寸的确定......................................................................................................................... - 4 - 3.2.2 挤压筒结构尺寸的确定...................................................................................................................... - 6 - 3.2.3 挤压垫的结构及尺寸确定.................................................................................................................... - 7 - 第四章实验模拟及数据提取分析............................................................................................................ - 8 - 4.1挤压工模具及工件的三维造型............................................................................................................... - 8 - 4.2 挤压模拟.................................................................................................................................................. - 8 - 4.3 后处理...................................................................................................................................................... - 9 - 4.4分析数据................................................................................................................................................... - 9 - 4.5 坯料温度对挤压力的影响.................................................................................................................... - 10 - 4.6 坯料预热温度对破坏系数的影响........................................................................................................ - 11 - 个人小结........................................................................................................................................................ - 12 - 参考文献........................................................................................................................................................ - 21 - 附表《塑性成型计算机模拟》课程设计成绩评定表第一章课程设计容及任务分配1.1 概述挤压是对放在容器(挤压筒)的金属坯料施加外力,使之从特定的模孔中流出,获得所需要断面形状和尺寸的一种塑性加工方法,有正挤压、反挤压、组合挤压、连续挤压、静液挤压等多种形式。
1450t全自动铝型材挤压机设计【毕业作品】

任务书设计题目:1450t全自动铝型材挤压机设计1.设计的主要任务及目标(1)主要任务:a:各个零件的设计 b:设计说明书 c:绘制各个零件图、液压系统图及电路控制图 d:电子资料一份(2)主要目标:通过对全自动铝型材挤压机的设计,以现在的市场实际需求出发,立足于企业目前的生产实际情况,研制全自动铝型材挤压机机械机构、液压系统以及电路控制实现全自动操作,更加有效的促使结构部件的整体化和合理化,提高结构的强度和耐用性,进而更有利于实现轻量化,节能化,以及减排高效化的最终目标。
2.设计的基本要求和内容(1)基本要求:机械结构:立论正确,文理通顺,简洁完整,技术用语准确,数据计算处理正确;设计合理,工艺可行;图表完备,绘图符合国家规范。
液压系统:合理计算工作压力,适当选取动力部分、执行部分以及辅助部分;绘制符合技术需求液压系统图。
电控系统:进行科学、合理的拟定电路设计图,选取合适的电路元件。
(2)内容:a:通过查阅相关的资料,确定铝型材挤压机机构总体布局及机构方案。
b:综合设计方案,并计算设计出合理的零件设计,选取合适的部分元件,完成铝型材挤压机设计的总装配图。
3.主要参考文献[1]《大型铝合金型材挤压技术与工模具优化设计》刘静安,谢建新主编;冶金工业出版社2003,6[2]《机械制图》左晓明王熊雯主编;高等教育出版社2009,4[3] 《机械设计手册》第四版成大先主编;化学工业出版社2002,1[4]《电气控制与PLC应用技术》崔继仁主编;中国电力出版社2010,2[5] 《铝型材挤压机使用说明书》佛山市业精机械制造有限公司4.进度安排1450t全自动铝型材挤压机设计摘要:1450t全自动铝型材挤压机是实现铝型材挤压加工的最主要设备。
铝型材挤压加工是利用金属塑性压力成形的一种重要方法。
其重要的特点是将金属锭坯一次加工成管、棒、型材完成在瞬息之间,几乎没有任何其他方法可以与之匹敌。
关键词:全自动,铝型材,挤压机,金属,坯锭,型材1450t automatic aluminum extrusion machine designAbstract:Automatic aluminum extrusion machine is 1450 t aluminum extrusion processing of the main equipment. Aluminum extrusion processing is the use of metal plastic pressure forming is a kind of important method. Its important characteristic is the metal ingot billet once completed processed into tubes, rods, profiles between instant, almost no other method can match.Keyword:full-automatic,Aluminium,Profile,Extrudingmachine,Metal,Billet,Proximate matter目录前言 (1)1 1450t全自动铝型材挤压机的工作原理 (2)1.1概述 (2)1.1.1主要技术参数与特点 (2)1.1.2工作原理与基本结构 (2)2 1450t全自动铝型材挤压机的机构系统的设计 (5)2.1盛锭筒的设计 (5)2.1.1盛锭筒的工作环境 (5)2.1.2盛锭筒的受力条件 (5)2.1.3盛锭筒的结构要素及特点 (5)2.1.4盛锭筒的加热方式 (6)2.1.5盛锭筒的结构尺寸设计 (6)2.1.6盛锭筒的强度校核 (8)2.2剪切机构的设计 (10)2.2.1剪切机构的工作环境以及受力条件 (10)2.2.2剪切机构的结构组成及特点 (10)2.2.3剪切力及刀片尺寸的计算 (11)2.2.4调整剪刀与模具之间的间隙 (12)2.3移模滑块机构 (12)2.3.1滑模移块机构的组成 (12)2.3.2移模滑块机构中的特征以及选用的模座 (13)2.4推棒机构 (14)2.4.1推棒机构中挤压杆的工作环境以及受力情况 (14)2.4.2推棒机构中挤压杆的结构及特点 (14)2.4.3推棒机构的计算 (15)2.4.4挤压垫片工作原理、结构形式以及优缺点 (16)2.5供锭机构 (18)2.5.1供锭机构的工作环境以及受力情况 (18)2.5.2供锭机构的结构以及特征 (19)2.6本章小结 (20)3 1450t全自动铝型材挤压机的液压系统的设计 (21)3.1机械机构液压缸的设计 (21)3.1.1主缸的主要零部件设计 (21)3.1.2副缸的主要零部件设计 (23)3.1.3盛锭筒油缸的主要零部件设计 (26)3.1.4剪刀油缸的主要零部件设计 (29)3.1.5方刀压余敲击油缸的主要零部件设计 (32)3.1.6滑模油缸的主要零部件设计 (35)3.1.7托料油缸的主要零部件设计 (38)3.1.8防尘圈压盖的设计 (40)3.1.9对液压缸设计的总结 (41)3.2拟定液压原理图 (42)3.2.1液压泵的配置 (42)3.2.2液压原理控制回路设计 (42)3.2.3液压阀的选择 (43)3.2.4系统性能验算 (44)3.2.5辅助元件的选择 (44)4 1450t全自动铝型材挤压机的电器系统的设计 (47)4.1电器控制系统设计 (47)4.1.1电器控制系统原理 (47)4.1.2电器控制系统设计 (47)4.1.3电器元件选择 (48)4.2 PLC系统硬件配置 (50)4.2.1简述PLC可编程控制器 (50)4.2.2PLC可编程控制器 (50)4.2.3PLC的硬态组件 (51)5 1450t全自动铝型材挤压机的机体外壳设计以及总装 (53)5.1主要结构设计 (53)5.1.1组合结构机架 (53)5.1.2三梁的设计 (55)5.1.3张力柱的强度计算 (57)5.1.4挤压机梁的强度计算 (59)5.2整体结构设计 (61)5.2.1机架结构类型 (61)毕业设计总结 (63)参考文献 (64)致谢 (65)前言机械制造及其自动化是一门研究机械制造理论、制造技术、自动化制造系统和先进制造模式的学科。
铝型材挤压过程数值模拟及模具设计的开题报告

铝型材挤压过程数值模拟及模具设计的开题报告一、选题背景及意义随着工业化进程的不断推进,各种金属制品的需求量也越来越大。
而铝型材作为一种轻薄高强、易加工的金属材料,因其良好的性能和应用范围而受到越来越广泛的关注。
铝型材的加工方法主要有挤压和拉拔两种方式。
其中,挤压工艺具有生产效率高、工艺适应性强、材料利用率高等优势,因此被广泛应用于铝型材的制造过程中。
在铝型材的挤压工艺中,模具是至关重要的关键环节。
模具的设计质量直接影响到铝型材的成型质量和生产效率。
现代科学技术的发展已经使得模拟计算成为了模具设计和制造过程中不可缺少的一环。
因此,通过数值模拟对铝型材的挤压工艺进行优化,同时结合合理的模具设计,能够有效地提高生产效率、降低造成工艺难度、并且保证铝型材的质量,具有非常重要的意义。
二、研究目的及任务本次研究的目的是为了通过数值模拟,优化铝型材挤压过程中的工艺参数,并结合合理的模具设计,提高铝型材的成型精度和生产效率。
具体任务包括:1、通过数值模拟,优化挤压过程中的主要工艺参数,如挤压速度、温度、润滑剂等。
2、设计适合挤压工艺要求的型材模具,确保型材的成型精度和生产效率。
3、在实际生产中对研究结果进行验证,同时不断进行优化和改进,提高铝型材的成型质量和生产效率。
三、研究方法本次研究的主要方法是数值模拟。
首先,需要对铝型材挤压过程的具体工艺流程和工艺参数进行分析和研究。
然后,通过建立铝型材挤压数值模型,模拟出整个挤压过程,并对模拟结果进行分析和评估,优化工艺参数,以达到最佳的挤压效果。
同时,结合数值模拟结果,设计出合理的型材模具,确保型材的成型精度和生产效率。
最后,在实际生产中进行验证,并不断优化改进,提高工艺效率和产品质量。
四、预期研究结果通过本次研究,预期达到以下几个方面的预期结果:1、建立完整的铝型材挤压数值模型,对挤压过程进行仿真模拟,得出挤压过程中的变形特征和影响因素。
2、优化挤压过程中的关键工艺参数,如挤压速度、温度、润滑剂等,以达到最佳的挤压效果。
铝型材挤压工艺及模具设计

铝型材挤压工艺及模具设计1. 挤压工艺铝型材挤压是一种利用压力对铝型材进行塑性变形的加工工艺。
其基本工艺是:铝棒坯料通过加热软化后,被压入模头,通过模头出口挤出成需要的截面形状。
铝型材挤压工艺的优点包括:高成形精度、高表面质量、操作简便,高生产效率等等。
2. 模具设计铝型材挤压的模具主要包括模头、辅助金属件、固定板、滑动板、胚料夹持装置等组成。
其中,模头是铝型材挤出的关键装置,包括卡箍板、模板、模板底部垫片、模座、模膜等部分。
模头的最重要的特点是不同形状的铝型材需要不同形状的模头;其次需要各个部位的设计匹配度高,精度要求高。
滑动板和固定板是模具的基础结构,他们需要耐压、耐磨,同时需要精度高、边缘无毛刺。
辅助金属件在滑动板、固定板及模头之间起到了加强固定的作用,除此之外还需要具有良好的导向功能。
2.2. 理论参数的确定合理的选择合适的挤压荷载能够很好的保证挤压过程中的质量,同时也能够最大限度的提高生产效率。
因此,在模具设计阶段,应尽可能的确定相应的理论参数。
此外,应还需根据压力、速度、保压时间等因素来确定合适的机器配置,以及最优的辅助系统。
为了达到最优的效果,这些参数需要经过实验验证。
2.3. 模具材料的选择对于铝型材挤压模具来说,常见的材料包括H13钢、特种合金钢、定向硅钢、硬质合金等材料。
如:H13钢:具有高的耐磨性、硬度和强度,适用于铝型材的大批量生产。
特种合金钢:高抗氧化性、高强度、高磨损性,这些特性使其适用于生产高性能和高质量的铝型材。
硬质合金:它具有高硬度和强度、高耐磨性和高耐蚀性,是生产大规模、高复杂度的模具的首选。
2.4. 设计注意事项在模具设计过程中还需要注意以下问题:1)要防止铝材在挤压过程中发生撕裂断裂,因此要注意模具底部的角度把控2)要避免孔洞过大过小,且要容易拆卸,之所以拆卸是为了清洁铝型材上残余物。
3)在设计过程中,要考虑铝型材的变形,保证材料截面和尺寸的均匀性。
4)在滑动板部位,还需要考虑降低铝型材与模具接触时所产生的不良效果,例如顶出口和顶料等问题。
挤压实验报告

挤压实验报告挤压实验报告一、引言挤压实验是一种常见的力学实验,通过对物体的挤压过程进行观察和分析,可以研究材料的力学性能和变形行为。
本实验旨在通过对某种材料的挤压实验,探究其力学性能和变形特点。
二、实验材料和设备本实验选用了一种常见的金属材料作为实验样品,具体材料名称不再赘述。
实验所需设备包括挤压机、测力计、计时器、显微镜等。
三、实验步骤1. 准备工作:将实验样品切割成适当的尺寸,并进行表面处理,确保表面光滑。
2. 装置调整:将实验样品放置在挤压机的工作台上,并调整挤压机的参数,如挤压速度、挤压力等。
3. 实验操作:启动挤压机,使其开始挤压实验样品。
同时,通过测力计测量挤压过程中的受力情况,并记录下来。
4. 观察记录:使用显微镜观察实验样品在挤压过程中的变形情况,并记录下来。
四、实验结果与分析通过对挤压实验的观察和记录,我们得到了一系列的实验数据。
根据这些数据,我们可以对实验样品的力学性能和变形特点进行分析。
首先,我们可以通过测力计的读数得到实验样品在挤压过程中所受的力大小。
通过对这些力的变化趋势进行分析,可以了解实验样品的变形行为。
例如,当实验样品受到较小的挤压力时,其变形较小,而当挤压力逐渐增大时,实验样品的变形也逐渐增大。
其次,通过显微镜观察实验样品的变形情况,我们可以了解其变形形态和变形程度。
例如,实验样品可能会出现拉伸、压缩、扭曲等不同形式的变形。
通过观察这些变形形态,可以进一步了解实验样品的力学性能。
在实验过程中,我们还可以观察到实验样品在挤压过程中的温度变化情况。
由于挤压过程中会产生摩擦热和变形热,导致实验样品的温度升高。
通过测量实验样品的温度变化,可以了解挤压过程中的能量转化情况。
根据实验结果和分析,我们可以得出一些结论。
例如,实验样品在挤压过程中呈现出一定的塑性变形特征,即在受力作用下能够发生可逆的形变。
同时,实验样品的变形程度与挤压力大小呈正相关关系,即挤压力越大,变形程度越大。
铝型材挤压模具设计
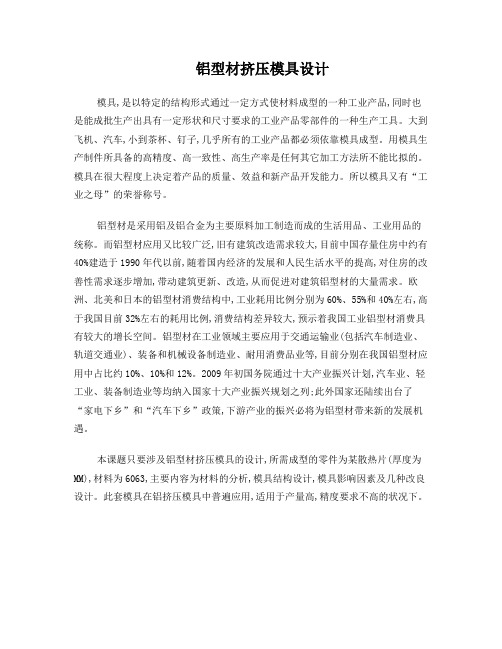
铝型材挤压模具设计模具,是以特定的结构形式通过一定方式使材料成型的一种工业产品,同时也是能成批生产出具有一定形状和尺寸要求的工业产品零部件的一种生产工具。
大到飞机、汽车,小到茶杯、钉子,几乎所有的工业产品都必须依靠模具成型。
用模具生产制件所具备的高精度、高一致性、高生产率是任何其它加工方法所不能比拟的。
模具在很大程度上决定着产品的质量、效益和新产品开发能力。
所以模具又有“工业之母”的荣誉称号。
铝型材是采用铝及铝合金为主要原料加工制造而成的生活用品、工业用品的统称。
而铝型材应用又比较广泛,旧有建筑改造需求较大,目前中国存量住房中约有40%建造于1990年代以前,随着国内经济的发展和人民生活水平的提高,对住房的改善性需求逐步增加,带动建筑更新、改造,从而促进对建筑铝型材的大量需求。
欧洲、北美和日本的铝型材消费结构中,工业耗用比例分别为60%、55%和40%左右,高于我国目前32%左右的耗用比例,消费结构差异较大,预示着我国工业铝型材消费具有较大的增长空间。
铝型材在工业领域主要应用于交通运输业(包括汽车制造业、轨道交通业)、装备和机械设备制造业、耐用消费品业等,目前分别在我国铝型材应用中占比约10%、10%和12%。
2009年初国务院通过十大产业振兴计划,汽车业、轻工业、装备制造业等均纳入国家十大产业振兴规划之列;此外国家还陆续出台了“家电下乡”和“汽车下乡”政策,下游产业的振兴必将为铝型材带来新的发展机遇。
本课题只要涉及铝型材挤压模具的设计,所需成型的零件为某散热片(厚度为MM),材料为6063,主要内容为材料的分析,模具结构设计,模具影响因素及几种改良设计。
此套模具在铝挤压模具中普遍应用,适用于产量高,精度要求不高的状况下。
铝合金型材实验报告

一、实验目的1. 探究铝合金型材的物理和机械性能。
2. 了解铝合金型材在工业应用中的导电性、导热性和抗腐蚀性。
3. 分析铝合金型材的加工性能和成型工艺。
二、实验原理铝合金型材是通过熔炼、铸造、挤压等工艺制成的,具有良好的导电性、导热性、抗腐蚀性和加工性能。
本实验主要针对铝合金型材的以下性能进行测试:1. 导电性:通过测量铝合金型材的电阻值,评估其导电性能。
2. 导热性:通过测量铝合金型材的导热系数,评估其导热性能。
3. 抗腐蚀性:通过浸泡实验,观察铝合金型材在特定腐蚀环境中的耐腐蚀性能。
4. 加工性能:通过模拟加工过程,评估铝合金型材的加工性能。
三、实验器材1. 铝合金型材样品2. 电阻测试仪3. 导热系数测试仪4. 浸泡实验箱5. 模拟加工设备6. 相关测试仪器和工具四、实验步骤1. 导电性测试:a. 使用电阻测试仪测量铝合金型材的电阻值。
b. 记录测试数据,分析导电性能。
2. 导热性测试:a. 使用导热系数测试仪测量铝合金型材的导热系数。
b. 记录测试数据,分析导热性能。
3. 抗腐蚀性测试:a. 将铝合金型材样品放入浸泡实验箱中。
b. 在特定腐蚀环境下浸泡一定时间。
c. 观察样品表面变化,评估耐腐蚀性能。
4. 加工性能测试:a. 使用模拟加工设备对铝合金型材进行切割、弯曲等加工操作。
b. 观察加工过程中的现象,评估加工性能。
五、实验结果与分析1. 导电性测试结果显示,铝合金型材的电阻值在0.1~0.5Ω之间,具有良好的导电性能。
2. 导热性测试结果显示,铝合金型材的导热系数在100~200W/(m·K)之间,具有良好的导热性能。
3. 抗腐蚀性测试结果显示,铝合金型材在浸泡实验中表现出良好的耐腐蚀性能,表面无明显腐蚀现象。
4. 加工性能测试结果显示,铝合金型材在切割、弯曲等加工过程中表现出良好的加工性能,无明显的加工缺陷。
六、结论1. 铝合金型材具有良好的导电性、导热性和抗腐蚀性能,适用于工业应用。
挤压铝型材 截面设计
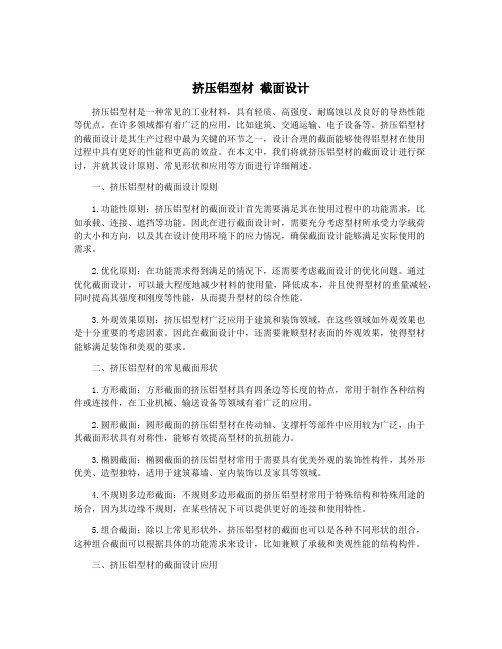
挤压铝型材截面设计挤压铝型材是一种常见的工业材料,具有轻质、高强度、耐腐蚀以及良好的导热性能等优点。
在许多领域都有着广泛的应用,比如建筑、交通运输、电子设备等。
挤压铝型材的截面设计是其生产过程中最为关键的环节之一,设计合理的截面能够使得铝型材在使用过程中具有更好的性能和更高的效益。
在本文中,我们将就挤压铝型材的截面设计进行探讨,并就其设计原则、常见形状和应用等方面进行详细阐述。
一、挤压铝型材的截面设计原则1.功能性原则:挤压铝型材的截面设计首先需要满足其在使用过程中的功能需求,比如承载、连接、遮挡等功能。
因此在进行截面设计时,需要充分考虑型材所承受力学载荷的大小和方向,以及其在设计使用环境下的应力情况,确保截面设计能够满足实际使用的需求。
2.优化原则:在功能需求得到满足的情况下,还需要考虑截面设计的优化问题。
通过优化截面设计,可以最大程度地减少材料的使用量,降低成本,并且使得型材的重量减轻,同时提高其强度和刚度等性能,从而提升型材的综合性能。
3.外观效果原则:挤压铝型材广泛应用于建筑和装饰领域,在这些领域如外观效果也是十分重要的考虑因素。
因此在截面设计中,还需要兼顾型材表面的外观效果,使得型材能够满足装饰和美观的要求。
二、挤压铝型材的常见截面形状1.方形截面:方形截面的挤压铝型材具有四条边等长度的特点,常用于制作各种结构件或连接件,在工业机械、输送设备等领域有着广泛的应用。
2.圆形截面:圆形截面的挤压铝型材在传动轴、支撑杆等部件中应用较为广泛,由于其截面形状具有对称性,能够有效提高型材的抗扭能力。
3.椭圆截面:椭圆截面的挤压铝型材常用于需要具有优美外观的装饰性构件,其外形优美、造型独特,适用于建筑幕墙、室内装饰以及家具等领域。
4.不规则多边形截面:不规则多边形截面的挤压铝型材常用于特殊结构和特殊用途的场合,因为其边缘不规则,在某些情况下可以提供更好的连接和使用特性。
5.组合截面:除以上常见形状外,挤压铝型材的截面也可以是各种不同形状的组合,这种组合截面可以根据具体的功能需求来设计,比如兼顾了承载和美观性能的结构构件。
- 1、下载文档前请自行甄别文档内容的完整性,平台不提供额外的编辑、内容补充、找答案等附加服务。
- 2、"仅部分预览"的文档,不可在线预览部分如存在完整性等问题,可反馈申请退款(可完整预览的文档不适用该条件!)。
- 3、如文档侵犯您的权益,请联系客服反馈,我们会尽快为您处理(人工客服工作时间:9:00-18:30)。
一. 题目: 铝合金型材挤压工艺及模具设计 二. 设计基本容: 设计一件实心型材制品和一件空心型材制品的工艺工艺过程及模具设计,包括挤压工艺参数,模具结构,制造工艺等要求 三. 完成后应缴的资料: 课程设计说明书一份 实心型材模零件图 空心型材模上模零件图 空心型材模下模零件图 空心型材模装配图 四. 设计完成期限: 2007年6月11日------2007年6月22日 指导老师_______签发日期___________ 教研室主任_______批准日期___________ 课程设计评语:
成绩: 设计指导教师_________ _____年_____月____日 目录 一、绪论………………………………………………………4
二、总设计过程概论…………………………………………7 2.1挤压工艺流程………………………………………7 2.2挤压工艺条件………………………………………7
三、实心型材模设计…………………………………………9 3.1所要设计的实心型材制品…………………………9 3.2选坯和选设备………………………………………10 3.3挤压力的计算………………………………………11 3.4实心型材模具体结构设计…………………………12 3.5. 实心模尺寸数据设计……………………………13
四、 空心型材模设计…………………………………………18 4.1所要设计的制品………………………………………18 4.2选坯和选设备…………………………………………18 4.3挤压力的计算…………………………………………19 4.4模组及模子外形尺寸确定……………………………20 4.5组合模相关参数的确定………………………………20 4.6 模子形尺寸的确定…………………………………23 4.7模孔工作带长度hg的确定……………………………24 4.8模芯的设计……………………………………………24 4.9上模凸台设计…………………………………………24 4.10定位销,螺钉………………………………………24 4.11模子强度校核………………………………………25 4.12零件图装配图………………………………………26
五、总结与体会……………………………………………….26 参考文献………………………………………………… 26 一.绪论 近20年来,随着建筑行业的高速发展,我国民用建筑铝型材工业也从无到有,从弱到强地迅猛前进。至今,省的建筑铝型材产品已约占全国的三分之二左右,铝型材的生产能力超过社会的需求,如何提高产品质量,降低成本是取得市场竞争胜利的关键环节。 铝合金型材具有强度高、重量轻、稳定性强、耐腐蚀性强、可塑性好、变形量小、无污染、无毒、防火性强,使用寿命长(可达50—100年),回收性好,可回炉重炼。6063合金中的主要合金元素为镁及硅,具有加工性能极佳,优良的可焊性,挤出性及电镀性,良好的抗腐蚀性,韧性,易于抛光,上包膜,阳极氧化效果优良,是典型的挤出合金,广泛应用于建筑型材,灌溉管材,供车辆,台架,家具,升降机,栅栏等用的管,棒,型材。多年来世界各国均采用6063铝合金(铝合金近百种)作为门窗框架。主要是为了该金属表面阳极氧化效果好,开始阳极氧化是白色,后进一步改变电解质才达到古铜色,这两种主体颜色在国用了十多年。 铝材在挤压过程中,如挤压模具不是很好或模具挤压铝材过多,铝材表面会产生挤压痕,用手可能触摸到铝材表面不平,因此,在现代化大生产中实施挤压加工技术,其成败的关键是模具,模具设计以及其质量,事关产品的质量,成本。 在挤压设计的过程中挤压工艺条件:应考虑挤压温度、挤压速度、润滑、模具(种类、形状、尺寸等)、切压余、淬火、冷却、切头切尾等多方面的因素。其中,选择挤压筒直径 D0 是一个最核心的问题,有以下的选择原则:1)保证产品表面质量原则;2)保证挤压模强度的原则;3)保证产品在质量的原则;4)经济上的优化原则-生产成本最低;成材率最大;产量最高。 这次的设计任务是设计一个实心型材和一个空心型材模,实心型材模采用单模,空心型材模采用分流组合模,挤压制品所有的材料是6063。由于其强度高,质量轻,加工性能好,在退火状态下,该合金有优良的耐蚀性及物理机械性能,是一种可以时效强化的AL-Mg-Si系合金,广泛应用于基础性建筑行业以及一些机械制造业。 其化学成分表示如下: 6063AL的成分: GB/T3190-1996: 表1:
牌号 Si Fe Cu Mn Mg Cr Zn Ti 其它元素 每种 总量
6063 0.2~0.6 ≤0.35 0.10 0.10 0.45~0.9 0.10 0.10 0.10 0.05 0.15
6063机械性能: (《铝合金及应用》)
表3:
常用挤压工具钢及其机械性能:
钢号 成分(%) 试验温度b 0.2 HB 热处理工艺 oC
/MPa /MPa /% /%
5CrMnMo 0.55C 1.51Mn 0.67Cr 0.26Mo 300 400 500 600 1150 1010 780 430 990 860 690 410 47 61 86 84 11.0 11.1 17.5 26.7 351 311 302 235
850 oC
油淬600oC
回火
3Cr2W8V 0.30C 0.23Cr 8.65W 0.29V 300 400 500 600 1520 1430 1280 1373 1363 15 5.6 8.3 429 429 405 325
1100 oC
在油中淬
火,550oC
回火
4Cr5MoSiV1 0.37C 4.74Cr 1.25Mo 1.05Si 1.11V 0.29Mn 400 450 500 550 600 1360 1300 1200 1050 825 1230 1135 1025 855 710 49 52 56 58 67 6 7 9 12 10 1050 oC
油淬第一次回火600oC
二.总设计过程概论 2.1挤压工艺流程: 铸锭加热→挤压→切压余→淬火→冷却→切头尾 或(切定尺 )→时效→表面处理→包装→出厂 2.2挤压工艺条件: 1).铸锭的加热温度 6063铝的最高允许加热温度为550℃,下限温度为320℃,为了保证制品的组织,性能,挤压时锭坯的加热温度不宜过高,应尽量降低挤压温度。 2).挤压筒的加热温度 模具的成分多为合金钢,由于导热性差,为避免产生热应力,挤压前挤压筒要预热,为保证挤压制品的质量,并且具有良好的挤压效应,挤压筒温度可取400℃~450℃。 3).挤压温度 热挤压时,加热温度一般是合金熔点绝对温度的0.75~0.95倍,本设计挤压温度为450℃~500℃,挤压过程温度控制在470℃左右。 4).挤压速度 考虑金属与合金的可挤压性,制品质量要求及设备的能力限制,本设计的挤压速度取0.7~0.8m/s。 5).工模具的润滑 因本设计采用热挤压,故不采用润滑。 6).模具 模具应具有足够的耐高温疲劳强度和硬度,较高的耐回火性及耐热性,足够的韧性,低的膨胀系数和良好的导热性,可加工性,及经济性,本设计采用4Cr5MoSiV1作为模具的材料,热处理的硬度为HRC40~47。 7).切压余 根据所选的设备而定。 8).淬火 本工艺过程中,制品挤出后可通过设置风扇对制品进行吹风来达到风淬的目的。 9).冷却 直接露置在空气中冷却,达到自然时效的目的。 10).切头尾 因头尾组织性能不均匀,为保证产品质量,本工艺过程统一去头尾各300mm。 三.实心型材模设计 3.1所要设计的实心型材制品: 本制品的形状和尺寸如下 图1:
牌号(XC311) 制品的截面积F制=212.9mm2
型材外接圆直径D外=43.86mm
现有设备: 表4: 3.2选坯和选设备: 根据加工围要求(F制≥F制min,及D外≤D外max)有500T、800T可选,按成材率最高的原则,进一步优化,计算列表: 表5:
设备吨位 500T 800T 1630T 挤压筒直径D0 Φ95 Φ125 Φ187 挤压截面积F0 7085 12266 27451 锭坯尺寸 DdⅹLd Φ90x270/320 Φ120X400/450 Φ178X540/600/660
冷床长 26m 32m 44m 填充系数 1.114 1.085 1.104 压余厚 20 25 30 最大挤压比 97.4 82 73.6
加工 围
最大外接圆直径 Φ65 Φ95 Φ147
挤一根最小制品断面积 F制min
72 150 372