刍议汽轮机转子叶轮裂纹的超声检测方法
汽轮机叶片表面裂纹检查方法及影响因素

Research and Exploration |研究与探索•监测与诊断汽轮机叶片表面裂纹检查方法及影响因素王庆和(大庆石化公司检测公司,黑龙江大庆163H4)摘要:汽轮机的应用逐渐涉及到了多缸、多转子、大容量这几个方面,对叶片的强度有了更高的要求,汽轮机叶片的 工作环境越来的越恶劣。
伴随着汽轮机运转的时间越来越长、它的抗劳损能力和使用寿命都在不断地下降,经常会出现汽 轮机表面出现裂纹的现象。
本文介绍了当前主要用到的两种叶片裂纹检测方法及其影响因素。
关键词:汽轮机叶片;裂纹检查;探伤;方法选择中图分类号:T G484 文献标识码:A文章编号:1671-0711 (2017) 03 (下)-0072-02汽轮机在工作中出现表面裂纹有着多种原因,例如叶片的结构、材料、工作的频率、加工的工艺、运行的环境等原因都有可能造成汽轮机叶片表面的裂纹出现。
以下根据多年从事汽轮机的检修经验,对主要的两种检查方法以及影响进行分析研究。
1肉眼检查法1.1裂纹出现的位置(1 )冲动式叶轮机叶片。
发生裂纹的部位通常 在:叶片根部的轮槽里、叶片根部轮槽的上汽部分、叶片中部的表面、拉筋孔的位置、叶片的顶部的位置等,比如铆钉头、围带和自带覆环等部位,见图1。
图1(2 )反动式叶轮机叶片。
这种类型的叶片裂纹 通常出现在:外片靠上部分的出汽面、叶根上方的 2/3或者3/4位置以及叶片出气孔拉筋的部位,如 图2所示。
1.2肉眼检测的主要部位(1)冲动式机轮叶片。
这样叶片的叶轮机,应 该将检测重点放在出汽面的根部及自带覆环处和带覆环的部位,还应该重点的对出汽面的根部、拉筋 孔的横向面以及覆环铆钉孔等位置进行检查。
(2 )反动式机轮叶片。
出汽面的根部、从叶根 根部到2/3或者3/4处的出汽面的位置是这样的叶片的检查重点。
在进汽面的部分,一定要重点对低压转子末级叶片顶部镶焊的有司太立台金的硬化层进行检查。
(3)检查方法。
首先用喷砂的方法对汽转子进 行处理,然后将其放置在可以转动的搁架上,以便 在检查的时候能够旋转。
汽轮机转子枞树型叶根超声相控阵检测技术

汽轮机转子枞树型叶根超声相控阵检测技术汽轮机转子枞树型叶根超声相控阵检测技术是一种新型的检测技术,它利用超声相控阵进行检测,可以快速准确检测出汽轮机转子枞树型叶根的故障部位和质量状况。
它拥有传统检测技术所没有的特点,包括检测精度高,检测时间短,结果准确等优势。
超声相控阵检测技术的主体设备由一个枞树型叶片超声相控阵传感器组成,它拥有可编程及调节的检测模式,可以检测不同部件的故障,如枞树叶片断裂和缺陷,叶轮转子缺陷,枞树圆环、外轮板缺陷等。
检测后,枞树型叶片超声相控阵可生成检测报告,报告中详细说明了可能发生的缺陷类型及位置等内容,从而可以确定和缩短维修时间。
汽轮机一般焊维超声波探伤方法及评定标准

汽轮机一般焊维超声波探伤方法及评定标准下载提示:该文档是本店铺精心编制而成的,希望大家下载后,能够帮助大家解决实际问题。
文档下载后可定制修改,请根据实际需要进行调整和使用,谢谢!本店铺为大家提供各种类型的实用资料,如教育随笔、日记赏析、句子摘抄、古诗大全、经典美文、话题作文、工作总结、词语解析、文案摘录、其他资料等等,想了解不同资料格式和写法,敬请关注!Download tips: This document is carefully compiled by this editor. I hope that after you download it, it can help you solve practical problems. The document can be customized and modified after downloading, please adjust and use it according to actual needs, thank you! In addition, this shop provides you with various types of practical materials, such as educational essays, diary appreciation, sentence excerpts, ancient poems, classic articles, topic composition, work summary, word parsing, copy excerpts, other materials and so on, want to know different data formats and writing methods, please pay attention!汽轮机一般焊维超声波探伤方法及评定标准介绍汽轮机作为重要的能源转换设备,在使用过程中需要进行焊接维修以保持其性能和安全。
汽轮机、汽轮发电机转子和主轴锻件超声探伤方法(JB1581

JB 1581-85 汽轮机、汽轮发电机转子和主轴锻件超声探伤方法代替JB 1581-75本标准适用于JB 1265-72《电站汽轮机和船用汽轮机主轴、整体转子锻件技术条件》以及JB 1267-72《汽轮发电机转子锻件技术条件》中各类转子和主轴锻件的超声探伤.其它轴类锻件可参考使用.1 应用前提1.1 本标准采用2-2.5 兆赫的探测频率按照脉冲反射式原理在转子和主轴锻件的外圆表面用直探头进行接触法探伤探头的最大直径为28 毫米.必要时可使用其它行之有效的方法如变换探测频率、探头规格、增加探伤面等进行检查.1.2 从事转子和主轴锻件超声探伤的人员应持有关部门颁发的相应资格的证书并能正确理解和使用本标准.2 一般要求2.1 需探伤的转子和主轴锻件其外形应尽可能加工成简单的圆柱体形状避免出现妨碍探伤工作的锥体、沟槽、圆弧形过渡区等几何形状.表面粗糙度Ra 应不大于6.3 微米并且没有划伤、机加工留下的细、油漆或其它外来粘附物.2.2 锻造厂 从吵龀е柿慷 鞯超声探伤一般应在最终热处理之后进行如果必须在最终热处理之前加工出轮盘、沟槽、锥体等几何形状也允许采用加工这些几何形状之前的最后一次探伤结果作为评定锻件质量的依据.2.3 最终热处理之后为反映出厂质量而作的探伤必须在锻件的材质衰减系数不大于每米 4 分贝的情况下进行.2.4 材质衰减系数的测定应在被探部位的端部200-500 毫米轴向范围内无缺陷信号的圆周面上用2-2.5 兆赫的探测频率进行.2.5 锻件交货前未能进行探伤的部位交货后可由订货厂补作探伤其探伤结果也同样是评定锻件质量的依据.3 设备要求3.1 用于转子和主轴锻件探伤的探伤仪应至少具有1.25、2.5、5 赫三种探测频率或者数值相近的其它探频率.3.2 探伤仪应备有数值可按 1 分贝或 2 分贝间隔进行全量程调节、最大衰减量不低于50 分贝的衰减器.衰减器的精度应在任意12 分贝中误差不大于±1 分贝.3.3 在用2-2.5 兆赫、直径20 毫米的直探头探测CS-2 型试块上测距500 毫米、直径2 毫米平底孔时探伤装置的有效灵敏度余量应在平底孔的信号幅度等于示波屏垂直显示极限75的情况下不小于20 分贝.3.4 探伤仪的水平线性误差应不大于2垂直线性误差不大于5分辨力应不小于20 分贝最大灵敏度下的盲区应不大于20 毫米按ZBY230-84《A型脉冲反射式超声探伤仪通用技术条件》的规定测量.3.5 探头性能应按ZBY231-84《超声探伤用探头性能测试方法》的规定.4 参考试块4.1 在需要使用参试块调节扫描线比例和探伤灵敏度、绘制“距离-幅度”曲线和确定缺陷当量时应使用CS-2 型参考试块.CS-2 型参考试块的形状、尺寸、数量、材质、加工要求等见本标准的附录 A.4.2 本标准不限制使用与CS-2 型试块有等效作用的其它试块.5 探伤灵敏度5.1 用于转子和主轴锻件的探伤灵敏度应能有效地发现被检锻件中当量直径等于和大于 2 毫米的缺陷.为便于发现缺陷允许在寻找缺陷的扫查中使用高于规定数值的灵敏度但在发现缺陷之后进行的各项测定工作则必须在规定的灵敏度下进行.5.2 为了探伤灵敏度的需要应在扫描线上方等于屏高40-80的范围内事先选定一个平于扫描线的基准高度.5.3 当被探部位的厚度大于探头的三倍近场区时可任意选用底波调整法或试块调整或试块调整探伤灵敏度当被探部位的厚度等于或小于探头的三倍近场区时应采用试块调整法.5.4 底波调整法5.4.1 先用能足以显示材料组织的高灵敏度在锻件上找出无缺陷的部位.5.4.2 在符合 5.4.1 款要求的部位上把底波幅度调到等于基准高度.5.4.3 根据被探部位的厚度以及底面形状提高探伤仪增益至规定数值见 4 款和5 款.5.4.4 探测实心锻件时需提高的增益数值可用下式求得:式中Ma----需提高的增益倍数Da----被探部位的直径mmd----平底孔直径mm此处 d等于 2 mmλ----波长mmπ----圆周率即3.14159.5.4.5 探测有中心孔的锻件时需提高的增益数值呆用下式求得:式中Mr----需提高的增倍数T----被探部位的厚度mmDa----被探部位的外径mmDi----被探部位的内径mmd----平底孔直径mm此处d 等于2 mmλ----波长mmπ----圆周率即3.14159.5.5 试块调整法5.5.1 使用CS-2 型参考试块或具有等效作用的其它试块上测距等于或近于锻件厚度、直径2 毫米的平底孔进行调整.5.5.2 把符合 5.5.1 款要求的平底孔信号幅度调至等于基准高度.5.5.3 根据被探部位的直径提高探伤仪的增益至规定数值见5.5.4用以裣锻件圆弧面引起的声能损失.5.5.4 需提高的增益数值应从CS-R 型试块上测得. CS-R 型试块的形状、尺寸、数量、材质、加工要求等见本标准的附录B.6 扫描线的比例调节在调节扫描线的比例时应使第一次底波的前沿位置不超过示波屏水平显示极限的80以利观察第一次底波之后的某些信号情况.7 扫查要求7.1 探头在被探部位的移动速度不大于150 毫米/秒相邻两次扫查之间应有一定的重叠重叠宽度不小于扫查宽度的15.7.2 在同一个探伤面上应进行两次扫查并使两次扫查之间的扫查方向相垂直.7.3 在扫查过程中不但要注意观察底波之前有无缺陷信号而且要注意观察底波之后有无缺陷信号.7.4 如果遇到底波信号或其它非缺陷信号如探头反射信号波信号等发生明显降低或消失时应及时查明发生此种情况的原因.8 缺陷信号的分类8.1 密集缺陷信号:在边长50 毫米的立方体内数量不少于5 个当量直径不小于2 毫米的缺陷信号.8.2 分散缺陷信号:在边长50 毫米的立方体内数量少于5 个当量直径不小于2 毫米的缺陷信号.8.3 单个缺陷信号:间距大于50 毫米、当量直径不小于2 毫米的缺陷信号.8.4 连续缺陷信号:某个测距上当量直径不小于2 毫米幅度波动范围能在探头持续移动距离等于或大于30 毫米的区间内不大于2 分贝的缺陷信号.8.5 游动缺陷信号:探头在被探部位移动时信号前沿位置的移动距离相当于25毫米或25 毫米以上工件厚度的缺陷信号.9 缺陷的测量与记录9.1 探伤中遇到缺陷信号之后应根据缺陷信号的类别采用不同的方法对缺陷进行测定.9.2 当遇到单个或分散缺陷信号时应进行的测量工作:a. 缺陷的当量直径b. 缺陷在锻件上的位置.9.3 在实心锻件上遇到密集缺陷信号时应进行的测量工作:a. 缺陷的深度分布范围根据缺陷信号前沿在扫描线上的位置进行测量b. 缺陷的轴向分布范围根据探头中心声束扫查到缺陷的移动范围进行测定c. 缺陷的最大当量直径d. 缺陷密集区在锻件上的位置.9.4 在空心锻件上遇到密集缺陷信号时应进行的测量工作:a. 缺陷的深度分布范围根据缺陷信号前沿在扫描线上的位置进行测量b. 缺陷的轴向分布范围根据探头中心声束扫查到缺陷的移动范围进行测量c. 缺陷的周向分布范围测量方法与四、b 相同但必须根据被测部位的曲率对测量值进行和何修正d. 缺陷铁最大当量直径e. 缺陷密集区在锻件上的位置.9.5 当遇到连续缺陷信号时应进行的测量工作:a. 缺陷的指示长度和垂直于指示长度的缺陷宽度用半波高度测长法进行测量沿周向测量时应根据被测部位的曲率对测量值进行几何修正b. 缺陷的最大当量直径c. 缺陷在锻件上的位置.9.6 当遇到游动缺陷信号时应进行的测量工作:a. 信号的游动范围用相当于工件厚度的最小值和最大值两个数值表示b. 能探测到缺陷的探头周向移动范围弧长c. 缺陷信号幅度最大处的缺陷当量和缺陷位置d. 缺陷的轴向长度用半波高度测长法进行测量e. 缺陷在锻件上的位置..9.7 在根据缺陷信号幅度测量缺陷当量直径时应使用平底孔的“距离-幅度”关系进行修正.9.8 在由缺陷引起底波明显降低的部位应对底波的降低程度及明显降低的区域进行测量.9.9 对游动距离小于工件厚度25 毫米的缺陷信号可用四参数傻产法估判缺陷的位置和走向.注:四参数作图法是在能探测到缺陷的探头周向移动范围内建立多个测量点利用各个测量点上测到的缺陷测距缺陷信号幅度和底波幅度分析缺陷位置走向以及尺寸的一种作图方法.9.10 在需要制定缺陷性质时应根据缺陷的尺寸当量、长度、宽度等数量、形状、方位、分布状信号静态和动态的特征锻件材料的特性、冶炼、锻造、热处理等工艺因素综合分析给出参考意见.必要时还应采取其它检验方法协同验证.9.11 凡按9.2 至9.10 要求测量和制定的结果都应记录.10 探伤报告10.1 探伤完毕后应书写探伤报告.10.2 探伤报告应包括下列内容:a 锻件名称、图号、材料、尺寸简图、热处理状态.b. 锻件编号、炉号、产品命令号或工作号c. 委托单位、委托日期、委托编号d. 探伤条件e. 9.11 中规定记录的内容及缺陷分布图展开图f. 未探伤的部位及其原因g. 有参考价值的波形图h. 有必要说明的情况i. 探伤日期、探伤者的资格证号、探伤者和审核者的签名.附录ACS-2 型参考试块及其技术要求补充件A.1 CS-2 型参考试块为平面型试块由两种试块组成一种是没有平底孔的大平底试块另一种是底部有直甜-8 毫米平底孔的试块.A.2 试块总数66 块其中大平底试块11 块平底孔试块55 块.A.3 采用电炉或平炉熔炼的45 碳钢钢锭经锻压和正火处理后进行加工锻压比不小于3.A.4 用 5 兆赫、直径 1.6 毫米平底孔信号幅度等于屏高80的灵每度探测试块时示波屏上应当不出现缺陷信号信噪比不小于6 分贝试块中心轴线上的材质衰减系数不大于每米4 分贝.A.5 试块外形及各部份尺寸见表A1. 表A1 CS-2 型参考试块尺寸及外形序试块孔径d 外径D 参考图序试块孔径d 外径 D 参考图测距L1 高度L2 测距L1 高度L2号编号mm mm 号编号mm mm mm mm mm mm1 25/0 0 25 25 ≥35 a 34 150/4 4 150 175 ≥85 b2 25/2 2 25 50 ≥35 b 35 150/6 6 150 175 ≥85 b3 25/3 3 25 50 ≥35 b 36 150/8 8 150 175 ≥85 b4 25/4 4 25 50≥35 b 37 200/0 0 200 200 ≥100 a5 25/6 6 25 50 ≥35 b 38 200/2 2 200 225 ≥100 b6 25/88 25 50 ≥35 b 39 200/3 3 200 225 ≥100 b7 50/0 0 50 50 ≥50 a 40 200/4 4 200 225 ≥100b8 50/2 2 50 75 ≥50 b 41 200/6 6 200 225 ≥100 b9 50/3 350 75 ≥50 b 42 200/8 8 200 225 ≥100 b10 50/4 4 50 75 ≥50 b 43 250/0 0 250 250 ≥110 a11 50/6 6 50 75 ≥50 b 44 250/2 2 250 275 ≥110 b12 50/8 8 50 75 ≥50 b 45 250/3 3 250 275 ≥110 b13 75/0 0 75 75 ≥60 a 46 250/4 4 250 275 ≥110 b14 75/2 2 75 100 ≥60 b 47 250/6 6 250 275 ≥110 b1575/3 3 75 100 ≥60 b 48 250/8 8 250 275 ≥110 b16 75/4 4 75 100 ≥60 b 49 300/0 0 300 300 ≥120 a17 75/6 6 75 100 ≥60 b 50 300/2 2 300 325 ≥120 b18 75/8 8 75 100 ≥60 b 51 300/3 3 300 325 ≥120 b19 100/0 0 100 100 ≥70 a 52 300/4 4 300 325 ≥120 b20 100/2 2 100 125 ≥70 b 53 300/6 6 300 325 ≥120 b21 100/3 3 100 125 ≥70 b 54 300/8 8 300 325 ≥120 b22 100/4 4 100 125 ≥70 b 55 400/0 0 400 400 ≥140 a23 100/6 6 100 125 ≥70 b 56 400/2 2 400 425 ≥140 b24 100/8 8 100 125 ≥70 b 57 400/3 3 400 425 ≥140 b25 125/0 0 125 125 ≥80 a 58 400/4 4 400 425 ≥140 b26 125/2 2 125 150 ≥80 b 59 400/6 6 400 425 ≥140 b27 125/3 3 125 150 ≥80 b 60 400/8 8 400 425 ≥140 b28 125/4 4 125 150 ≥80 b 61 500/0 0 500 500 ≥155 a29 125/6 6 125 150 ≥80 b 62 500/2 2 500 525 ≥155 b30 125/8 8 125 150 ≥80 b 63 500/3 3 500 525 ≥155 b31 150/0 0 150 150 ≥85 a 64 500/4 4 500 525 ≥155 b32 150/2 2 150 175 ≥85 b 65 500/6 6 500 525 ≥155 b33 150/3 3 150 150 ≥85 b 66 500/8 8 500 525 ≥155 b附录BCS-R 型参考试块及其技术要求补充件B.1 CS-R 型参考试块为大平底试块用以测量探测面为凸形圆柱面的锻件探伤中因曲率不同而引起的声能损失.B.2 试块总数14 块其中 1 块的探测面为平面其余13 块为曲率不同的凸形圆柱面.B.3 采用电炉或平炉熔炼的45 碳钢钢锭经锻压和正火处理后进行加工锻压比不小于3B.4 用 5 兆赫1.6 平底孔信号幅度等于屏高80的灵敏度探测试块时示波屏上应当不出现缺陷信号信噪比不小于6 分贝试块中心轴线上的材质衰减系数不大于每米4 分贝.B.5 试块外形及各部分寸见表B1. 表B1 CS-R 参考试块尺寸及外形序试块编探测面R 参考图号号1 75/0 ---2 75/50 503 75/75 754 75/100 1005 75/125 1256 75/150 1507 75/200 2008 75/300 3009 75/400 4001075/500 50011 75/600 60012 75/700 70013 75/750 75014 75/800 800附加说明:本标准由上海材涎芯克 岢霾⒐榭诒颈曜加缮虾2牧涎芯克 涸鹌鸩?本标准主要起草人:徐立贤。
汽轮机叶轮轮缘小脚周向裂纹的超声检测

汽轮机叶轮轮缘小脚周向裂纹的超声检测
郑双武
【期刊名称】《无损检测》
【年(卷),期】1993(015)001
【总页数】2页(P14-15)
【作者】郑双武
【作者单位】无
【正文语种】中文
【中图分类】TG115.285
【相关文献】
1.刍议汽轮机转子叶轮裂纹的超声检测方法 [J], 陈玮俊
2.汽轮机叶轮轮缘反T型叶根槽裂纹的超声波探伤 [J], 李光彦;沙命余
3.300MW汽轮机叶轮轮缘小脚的超声波探伤 [J], 盛民
4.N75—90型汽轮机21级叶轮轮缘裂纹原因及处理 [J], 郭大辉;谢月芽
5.30万kW汽轮机叶轮轮缘小脚的超声波探伤 [J], 盛民
因版权原因,仅展示原文概要,查看原文内容请购买。
浅谈核电厂汽轮机低压转子叶片的缺陷检测技术

浅谈核电厂汽轮机低压转子叶片的缺陷检测技术发布时间:2022-01-20T10:09:55.681Z 来源:《中国科技人才》2021年第30期作者:余泽潭[导读] 核电厂的高效化运行,是维持社会正常运转的关键,因此只有消除各类设备的故障隐患,才能创造良好的经济效益及社会效益。
福建福清核电有限公司 350318摘要:核电厂的高效化运行,是维持社会正常运转的关键,因此只有消除各类设备的故障隐患,才能创造良好的经济效益及社会效益。
汽轮机低压转子是核电厂中的主要设备,在长期运行中会导致叶片部分出现缺陷,不仅会影响正常生产作业,严重时也会引发安全事故。
为此,应该做好叶片缺陷的全面检测,了解叶片的运行状态及变化趋势,以便在后续运维工作中实施针对性防控措施。
本文将对核电厂汽轮机低压转子叶片缺陷类型、特点和影响因素等加以分析,探索核电厂汽轮机低压转子叶片的缺陷检测技术,为实践工作提供参考。
关键词:核电厂;汽轮机低压转子;叶片缺陷;检测技术在我国现代化建设进程中,对于核电厂的依赖程度较高,也是决定社会经济发展命脉的关键环节,因此需要加强设备管控,以改善核电厂的整体运行环境。
汽轮机低压转子叶片会受到诸多外界因素的干扰,尤其是其运行环境十分复杂,包括了高温环境和腐蚀环境等,而且旋转离心力较大,因此会引发诸多缺陷故障问题,如果长期处于带病运行状态,则会对设备及人员安全形成威胁。
在科学技术水平不断提高的趋势下,应该引入更加先进的缺陷检测技术,采取事前控制、事中控制和事后控制相结合的方式,全面消除叶片的缺陷问题,避免酿成严重事故。
一、核电厂汽轮机低压转子叶片缺陷核电厂汽轮机低压转子叶片缺陷主要分为两大类,在设计生产中的缺陷和运行期间的缺陷。
对于设计工作的控制效果不佳,未能了解核电厂汽轮机低压转子的运行特点,导致结构设计不合理,在运行中则会提高缺陷出现的概率。
尤其是设计工作具有专业性特点,如果设计人员不了解材料学、流体力学等方面的专业理论,则会影响整体设计水平。
转轮叶片裂纹分析,检测及处理

转轮叶片裂纹分析,检测及处理作者:王磊来源:《中国新技术新产品》2009年第06期摘要:转轮是水轮机核心部件,转轮的叶片出现裂纹会严重威胁水电厂的安全运行。
通过对水轮机转轮叶片进行有限元计算分析,得出应力过于集中通常是叶片裂纹产生的主要原因,此外,叶片也存在设计、制造、运行方面的问题,为此,介绍了水轮机转轮叶片裂纹无损检测的常用方法和一般工艺。
关键词:水轮机;转轮叶片;应力;有限元;裂纹;无损检测引言水轮机转轮叶片裂纹的频繁产生,对机组安全运行构成很大威胁,也给电厂带来极大的经济损失,因此,分析裂纹产生原因,并对易产生裂纹部位进行无损探伤检查,对及时处理缺陷,消除事故隐患是十分必要的。
1 转轮裂纹及现象小浪底某台机组小修期间,发现转轮的13个叶片出水边接近上冠处有11个叶片出现裂纹(后经着色探伤,确定另两个叶片也有轻微裂纹),裂纹长度 100~400mm不等,大部分为贯穿(端面)型裂纹,所有裂纹形状相似,起始点在叶片负压面与出水端面交线上,距上冠约50mm,裂纹起始端与叶片出水边垂直,后端以不规则抛物线形向叶片中心延伸,其中有一个叶片同时出现沿焊缝方向的裂纹。
近期景洪1号机组也发现出水边靠近上冠部位以及靠近下环部位的裂纹,而且最近投产的大水电机组经常在转轮这些位置出现裂纹。
2 裂纹产生原因分析2.1 应力集中采用有限元计算分析得出,转轮在水压力及离心力的作用下,大应力区主要分布在转轮叶片周边上,按第三强度理论计算的相当应力沿叶片周边分布。
转轮叶片存在四个高应力区,他们的位置在叶片进水边正面(压力分布面)靠近上冠处;叶片出水边正面的中部;叶片出水边背面靠近上冠处;叶片与下环连接区内。
2.2铸造缺陷及焊接缺陷叶片原材料经加热模压,其中铸造气孔、铸造砂眼等在外部应力的作用下可能会成为裂纹源,造成裂纹的产生。
由于转轮叶片与上冠、下环的厚度相差大,在冷却过程中易产生缩孔、疏松等。
转轮上冠、下环与叶片均为马氏体不锈钢材料,焊条则是奥氏体不锈钢材料。
汽轮机叶轮键槽裂纹超声波探伤方法研究

24 汽轮机叶轮试块的研制 - 研制的超声波试块能满足下列要求 2 . 可以测试超声波探头入射点 : .1 4 242 可 以测试超声 波探 头的折射角 : .. 243 可 以调整仪器的扫描速度 : .- 244 具有 1 m线切割槽 的模拟裂纹 .. m
21 年 01
第 3 期 1
S IN E&T C N L G F R A I N CE C E H O O YI O M TO N
o电力与能源 0
科技信息
汽轮机叶轮键槽裂纹超声波探伤方法研究
喻 疆 宋绍河 张 昕 2 徐 俊成 2 f. 1中国水 利 电力物 资有 限公 司 中国 北 京 10 4 2甘肃 电 力科学研 究 院 0 0 5;. 甘肃 兰州 7 0 5 ) 3 0 0
图 1 图3
1 采用传统探伤方法探测时 . - 3 若发现可疑讯号 . 需将探头每 向前移 动 5 m记录 x 弧长) a r ( 的距离 , 反射当量 A(B 的数值 . d) 荧光屏 上 T距 ( 离) , 值 然后绘制 x —A、 —A曲线并综合几方 面的数值进行对裂纹 的 判定 。 目 我们往往是作性质判定. 前 并无认真地按断裂力学原理进行 寿命 评估 。 若发现裂纹 , 为安全运行需要将 叶轮拆下进行打磨 、 补焊或 更换 处理 。可见研制一种新的 、 的探伤方法是很有必要 的 简便 1 对 于 5 M 以下 的机组 . . 4 0W 末级叶轮往往轮盘间 隙过小 . 手持探头 操作 很难进行 , 给探伤和定位带来 一定的难度 . 也需 对传 统的探伤方 法进行改进 。鉴于 以上存在的问题 . 我们列题攻关 以寻求一种较 为简 便 的探伤方法和超声波试块
2 技术方案
根据 以上存在 的问题 , 我们从 以下几个方面进行攻关 :
汽轮机叶片超声波检验技术导则

汽轮机叶片超声波检验技术导则Technical guide for the ultrasonic testingof turbineblades2000-11-03 发布2001-01-01 实施中华人民共和国国家经济贸易委员会发布前言本标准是根据原电力工业部电力行业标准制、修订计划(技综[1996] 40号)的安排制定的。
运行中汽轮机叶片处于极复杂的应力状态,往往由于叶片(叶身和叶根)设计不合理,材料不符合要求,机加工质量不佳,组装工艺不良,运行工况变动等因素的影响造成叶片断裂事故。
对叶片尤其是叶根进行预防性检查是消除设备隐患,确保机组安全运行的重要手段。
长期以来,许多单位为了搞好这项工作,做了大量的试验研究。
尤其目前大量老机组仍然在超期服役,大容量新机组相继投运,叶片的断裂时有发生,本标准的制定为叶片无损检测提供了技术依据,同时提高了检测的准确性,尽可能避免和减少因误判而造成的不必要损失。
本标准附录A是标准的附录,附录B是提示的附录。
本标准由电力行业电站金属材料标准化技术委员会提出并归口。
本标准起草单位:国家电力公司热工研究院、西北电力试验研究院、江苏电力试验研究所、常熟电厂、甘肃电力试验研究所、台州电厂。
本标准主要起草人:吴前驱、白小云、于强、王世华、吴凯、张明非、徐大鹰。
本标准委托电力行业电站金属材料标准化技术委员会解释。
目次前百1范围2引用标准3术语4总则5仪器、探头和试块6检验技术条件选择7检验报告附录A(标准的附录)汽轮机叶片超声检验灵敏度及动态波形附录B(提示的附录)国产(125〜300)MW机组汽轮机叶片、叶根配置中华人民共和国电力行业标准汽轮机叶片超声波检验技术导则DL/T 714—2000 Technical guide for the ultrasonic testingof turbineblades1范围本导则规定了火电厂在役机组检修时,使用A型脉冲反射式超声波探伤仪,以单探头接触法为主进行汽轮机叶片(叶身及叶根)的超声波检验和判定方法。
整锻式汽轮机实心转子体超声波检验
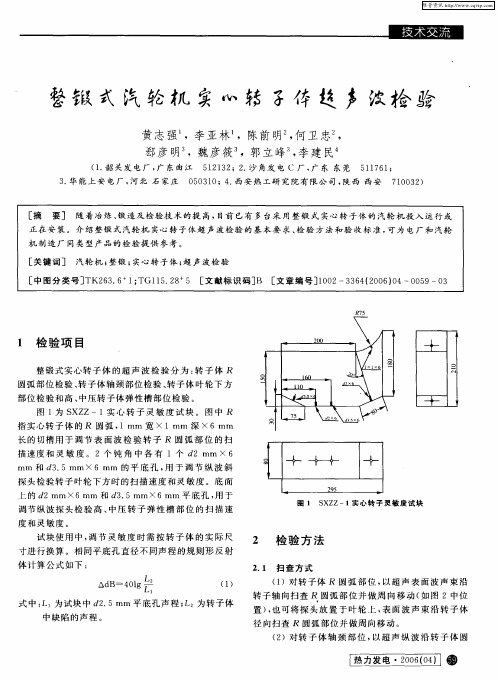
事 日 -1 I 珥 1 l - 叮Ⅱ
:
/ 一l 一 咖J 『
I! I I
一 。
I I I I
、
- 一
一
一
\ l I
图 3 实 心转 子体 高 、 中压 转 子 弹 性 槽 检 验 示 意
调节纵 波 探头 检 验 高 、 中压 转 子 弹性 槽 部 位 的扫 描 速
度和灵 敏 度 。 试 块使 用 中 , 节灵 敏 度 时需 按 转 子 体 的 实 际 尺 调 寸进 行换算 。相 同平底 孔直 径不 同声 程 的规 则形 反 射
体计算 公 式如 下 :
2 1 扫 查 方 式 .
mm 和 d . 3 5mm× 6mm 的平 底 孔 , 于 调 节 纵 波 斜 用
探 头检 验转 子 叶轮 下方 时的扫 描 速度 和灵 敏 度 。底 面
上 的 d ×6rm 和 d . 2mm n 3 5mm× 6mm 平 底 孔 , 于 用
图 1 S Z X Z一1 心 转 子 灵 敏 度 试 块 实
3 华 能上安 电厂 , 北 石 家庄 . 河
0 0 1 ; . 安 热 工 研 究 院 有 限 公 司 , 西 西 安 7 0 3 ) 5 30检验项 目
整锻 式实 心 转子 体 的 超 声 波 检 验 分 为 : 子 体 R 转 圆弧 部位 检验 、 子体 轴颈 部位 检验 、 转 转子 体 叶 轮下 方
维普资讯
罄考 汽 轮j m轱 孑铸 造 声汝检 验 段式 f 几实
黄 志 强 ,李 亚 林 ,陈前 明。 何 卫 忠。 , , 郄彦 明。 ,魏 彦 筱。 ,郭 立 峰。 李 建 民 ,
一种用于检测汽轮机转子叶片的超声表面波探头装置[实用新型专利]
![一种用于检测汽轮机转子叶片的超声表面波探头装置[实用新型专利]](https://img.taocdn.com/s3/m/94c24ca6b8d528ea81c758f5f61fb7360b4c2bfa.png)
专利名称:一种用于检测汽轮机转子叶片的超声表面波探头装置
专利类型:实用新型专利
发明人:王文涛,陈明,董鹏,高扬,王巍麟
申请号:CN202121941363.7
申请日:20210818
公开号:CN216350496U
公开日:
20220419
专利内容由知识产权出版社提供
摘要:本实用新型涉及一种用于检测汽轮机转子叶片的超声表面波探头装置,包括表面波探头、带有尺寸刻度和激光投影功能的激光投影卷尺,激光投影卷尺的一端安装在表面波探头的顶部,激光投影卷尺能伸展平直进行测量工作或者卷曲后进行收纳,激光投影卷尺伸展平直后,其零刻度线与表面波探头前端面齐平。
本超声表面波探头装置在进行检测工作时,将激光投影卷尺伸展平直,激光投影卷尺上的尺寸刻度能垂直向下正投影至叶片表面,手持表面波探头侧面,在对叶片进行超声波扫查时,即可实时观察距离尺寸,并与超声波探伤仪显示的异常波声程进行比对分析,对怀疑缺陷第一时间分析判断。
本实用新型安全可靠、操作简单。
申请人:华电电力科学研究院有限公司
地址:310030 浙江省杭州市西湖区西湖科技经济园西园一路10号
国籍:CN
代理机构:杭州天欣专利事务所(普通合伙)
代理人:陈红
更多信息请下载全文后查看。
某电厂汽轮机叶片裂纹的超声波横波检测

某电厂汽轮机叶片裂纹的超声波横波检测
摘要:该汽轮机,投运已30多年,步入老龄化阶段,汽轮机叶片处于复杂应力状态下工作,叶片常常因为设计、材质、加工精度、组装工艺等问题,随着时间的延长,产生裂纹,并不断扩展,本文运用了超声波横波检验方法,对该电厂汽轮机叶片裂纹进行检测。
关键词:汽轮机叶片、裂纹、超声波检测、横波
0前言
某发电厂2号机组,是前苏联列宁格勒金属工厂1972年生产的K-100/90-7型双缸凝汽式汽轮机组,功率100MW,1974年9月投产,截止2004年6月,累计运行时间20.4万h,期间已进行过11次大修。
低压转子24/29,25/30级叶片型号分别为1450/476,1147/749型,叶片总长分别为524mm,650mm,叶根长分别为92mm,105mm,根部下宽为35mm,32mm,对称1圈分别安装99片,102片,叶根为4叉型骑缝双铆孔叶根,叶根叉齿宽度为15mm。
1问题提出
该汽轮机,投运已30多年,步入老龄化阶段,汽轮机叶片处于复杂应力状态下工作,叶片常常因为设计、材质、加工精度、组装工艺等问题,随着时间的延长,产生裂纹,并不断扩展,严重地威胁着汽轮机运行的安全性,特别是长叶片叶根发生断裂,后果不堪设想。
传统检测方法,采用超声表面波检测次末级(24/29级)一侧叶根,如图1。
由于叶根水平面外露的宽度窄,对表面波探头入射点的要求非常苛刻,。
刍议汽轮机转子叶轮裂纹的超声检测方法
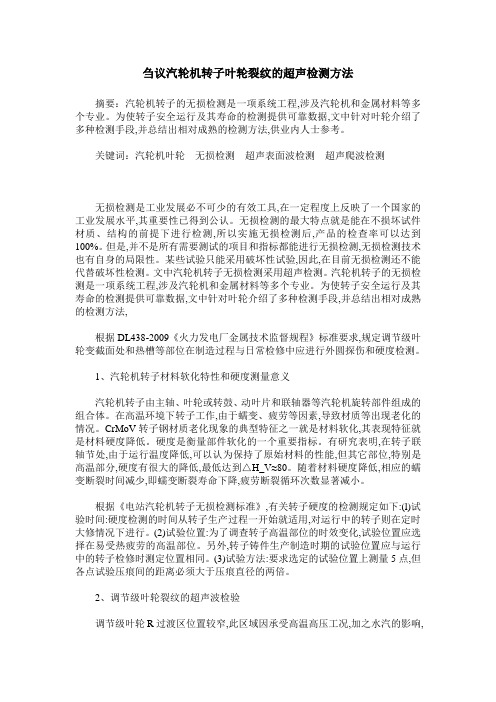
刍议汽轮机转子叶轮裂纹的超声检测方法摘要:汽轮机转子的无损检测是一项系统工程,涉及汽轮机和金属材料等多个专业。
为使转子安全运行及其寿命的检测提供可靠数据,文中针对叶轮介绍了多种检测手段,并总结出相对成熟的检测方法,供业内人士参考。
关键词:汽轮机叶轮无损检测超声表面波检测超声爬波检测无损检测是工业发展必不可少的有效工具,在一定程度上反映了一个国家的工业发展水平,其重要性已得到公认。
无损检测的最大特点就是能在不损坏试件材质、结构的前提下进行检测,所以实施无损检测后,产品的检查率可以达到100%。
但是,并不是所有需要测试的项目和指标都能进行无损检测,无损检测技术也有自身的局限性。
某些试验只能采用破坏性试验,因此,在目前无损检测还不能代替破坏性检测。
文中汽轮机转子无损检测采用超声检测。
汽轮机转子的无损检测是一项系统工程,涉及汽轮机和金属材料等多个专业。
为使转子安全运行及其寿命的检测提供可靠数据,文中针对叶轮介绍了多种检测手段,并总结出相对成熟的检测方法,根据DL438-2009《火力发电厂金属技术监督规程》标准要求,规定调节级叶轮变截面处和热槽等部位在制造过程与日常检修中应进行外圆探伤和硬度检测。
1、汽轮机转子材料软化特性和硬度测量意义汽轮机转子由主轴、叶轮或转鼓、动叶片和联轴器等汽轮机旋转部件组成的组合体。
在高温环境下转子工作,由于蠕变、疲劳等因素,导致材质等出现老化的情况。
CrMoV转子钢材质老化现象的典型特征之一就是材料软化,其表现特征就是材料硬度降低。
硬度是衡量部件软化的一个重要指标。
有研究表明,在转子联轴节处,由于运行温度降低,可以认为保持了原始材料的性能,但其它部位,特别是高温部分,硬度有很大的降低,最低达到△H_V≈80。
随着材料硬度降低,相应的蠕变断裂时间减少,即蠕变断裂寿命下降,疲劳断裂循环次数显著减小。
根据《电站汽轮机转子无损检测标准》,有关转子硬度的检测规定如下:(l)试验时间:硬度检测的时间从转子生产过程一开始就适用,对运行中的转子则在定时大修情况下进行。
汽轮机转子菌型叶根相控阵超声波检测的缺陷定量方法

汽轮机转子菌型叶根相控阵超声波检测的缺陷定量方法汪军【摘要】对核电站汽轮机中广泛使用的菌型类叶片叶根,采用相控阵超声波技术进行检测,分析了其定量检测结果。
通过比对常规超声检测的几类测长方法(-6,-12 dB相对灵敏度法和绝对灵敏度法)来确定适用于菌型叶根的长度测量方法。
通过对不同高度缺陷显示的特征分析,归纳出了菌型叶根的高度定量方法。
%This paper studied the imperfection sizing method using the advanced ultrasonic phased array inspection technology for the straddle tree bladeroots.Indication length measurement was determined by comparing several conventional indication sizing methods,such as 6dB drop technique,12dB drop technique,and complete drop technique.Appropriate indication height measurement was conducted by analyzing the characteristics of various indications with different heights.【期刊名称】《无损检测》【年(卷),期】2017(039)001【总页数】5页(P19-23)【关键词】相控阵;菌型叶根;长度测量;高度测量;缺陷定量【作者】汪军【作者单位】国核电站运行服务技术有限公司,上海 200233【正文语种】中文【中图分类】TG115.28汽轮机是核电站运行中的关键设备,属于在役检查中的重点检测对象,但是长期以来对汽轮机的叶片叶根的体积性缺陷检测十分困难。
- 1、下载文档前请自行甄别文档内容的完整性,平台不提供额外的编辑、内容补充、找答案等附加服务。
- 2、"仅部分预览"的文档,不可在线预览部分如存在完整性等问题,可反馈申请退款(可完整预览的文档不适用该条件!)。
- 3、如文档侵犯您的权益,请联系客服反馈,我们会尽快为您处理(人工客服工作时间:9:00-18:30)。
刍议汽轮机转子叶轮裂纹的超声检测方法
摘要:汽轮机转子的无损检测是一项系统工程,涉及汽轮机和金属材料等多个专业。
为使转子安全运行及其寿命的检测提供可靠数据,文中针对叶轮介绍了多种检测手段,并总结出相对成熟的检测方法,供业内人士参考。
关键词:汽轮机叶轮无损检测超声表面波检测超声爬波检测
无损检测是工业发展必不可少的有效工具,在一定程度上反映了一个国家的工业发展水平,其重要性已得到公认。
无损检测的最大特点就是能在不损坏试件材质、结构的前提下进行检测,所以实施无损检测后,产品的检查率可以达到100%。
但是,并不是所有需要测试的项目和指标都能进行无损检测,无损检测技术也有自身的局限性。
某些试验只能采用破坏性试验,因此,在目前无损检测还不能代替破坏性检测。
文中汽轮机转子无损检测采用超声检测。
汽轮机转子的无损检测是一项系统工程,涉及汽轮机和金属材料等多个专业。
为使转子安全运行及其寿命的检测提供可靠数据,文中针对叶轮介绍了多种检测手段,并总结出相对成熟的检测方法,
根据DL438-2009《火力发电厂金属技术监督规程》标准要求,规定调节级叶轮变截面处和热槽等部位在制造过程与日常检修中应进行外圆探伤和硬度检测。
1、汽轮机转子材料软化特性和硬度测量意义
汽轮机转子由主轴、叶轮或转鼓、动叶片和联轴器等汽轮机旋转部件组成的组合体。
在高温环境下转子工作,由于蠕变、疲劳等因素,导致材质等出现老化的情况。
CrMoV转子钢材质老化现象的典型特征之一就是材料软化,其表现特征就是材料硬度降低。
硬度是衡量部件软化的一个重要指标。
有研究表明,在转子联轴节处,由于运行温度降低,可以认为保持了原始材料的性能,但其它部位,特别是高温部分,硬度有很大的降低,最低达到△H_V≈80。
随着材料硬度降低,相应的蠕变断裂时间减少,即蠕变断裂寿命下降,疲劳断裂循环次数显著减小。
根据《电站汽轮机转子无损检测标准》,有关转子硬度的检测规定如下:(l)试验时间:硬度检测的时间从转子生产过程一开始就适用,对运行中的转子则在定时大修情况下进行。
(2)试验位置:为了调查转子高温部位的时效变化,试验位置应选择在易受热疲劳的高温部位。
另外,转子铸件生产制造时期的试验位置应与运行中的转子检修时测定位置相同。
(3)试验方法:要求选定的试验位置上测量5点,但各点试验压痕间的距离必须大于压痕直径的两倍。
2、调节级叶轮裂纹的超声波检验
调节级叶轮R过渡区位置较窄,此区域因承受高温高压工况,加之水汽的影响,
表面覆盖一层较厚的氧化皮,因而常用的渗透和磁粉检验受到限制。
分别采用超声表面波和超声爬波两种不同波形检测,对表面和近表面的裂纹或其它缺陷有较满意的效果。
2.1 超声表面波检测R过渡区缺陷
近表面缺陷检测时,表面波的能量集中于表面下两个波长之内,检测表面裂纹灵敏度极高,并且表面波的强度法和时延法可以较为准确地测定裂纹深度,如图l 所示。
但是,对于表面粗糙的工件,在堆焊层部位等会出现干扰杂波,使探测灵敏度大大下降。
表面波传播中遇到工件的棱边会产生反射波,如果棱边存在倒角,即可以更多能量通过圆弧面,调节级叶轮及过渡区表面波同样有较多能量通过,只有存在裂纹波时会发生强烈反射。
(1)表面波探伤时仪器时基线调整扫描速度调整方法与普通探头不一样,入射点按探头前沿计算。
调节时,将探头对准试块棱边,回波信号按水平距离调节成一定比例。
(2)探伤灵敏度调整探头对准直角棱边,调整棱边回波高度达到标准值(如满屏的80%),再增益21dB作为探伤灵敏度。
对于5MHz的探头,此灵敏度相当于发现0.1mm的裂纹。
2.2 超声爬波检测R过渡区缺陷
爬坡是指表面下纵波,它是纵波从第一介质的第一临界角附近的角度入射于第二介质时在第二介质中产生的表面下纵波。
在第二介质中,除了表面下纵波外还有其它波型。
前者以纵波速度传播,通常称其为“爬波”,相应的探头成为爬波探头。
图2为超声爬波检测调节级叶轮R过渡区裂纹,可探测最大深度)≥15mm,图3为利用爬波检测技术测量表面裂纹。
图2 超声爬波检测调节级叶轮R过渡区
图3 用爬波检测测量表面裂纹
(1)超声爬波探伤时仪器时基线调整扫描速度调整与表面波调整方法相似,亦可以当人工裂纹与探头前沿并齐时,使裂纹位于时基线20处,比例为1:1。
(2)探伤灵敏度调节根据裂纹试块上裂纹深度和裂纹反射波高成正比关系,选择0.5mm或更高增益作为探伤灵敏度。
3、调节级前后弹性槽(热槽)超声纵波检验
调节级前端存在弹性槽(热槽),常规的超声波检验探头无法实施。
为了实现外圆检测,可使用矩形晶片直人射纵波探头或00-40TR双晶探头放置在弹性槽内进行周向扫查。
灵敏度调节采用底波方法及试块方法,底波法无需再制作试块。
转子结构有中心孔和无中心孔实心转子两种。
实心转子圆柱体曲底面调节灵敏度时
的当量计算如下:
式中:——平底孔缺陷至探测面距离;
——铸件底面至探测面距离;
——材质衰减系数;
I——波长;
——平底孔缺陷的当量直径;
——中心孔圆柱面与平底孔缺陷的回波分贝差。
对于热槽内裂纹,常用表面检测方法(如渗透着色法、磁粉法)检测,由于存在矩形槽,很难实施常规的程序。
在实际操作时,采用点式涡流探伤方法不仅能检出缺陷,而且能测量出裂纹深度,是一种值得推广的方法。
4、寿命预测
某电厂汽轮机截止大修时累计运行123208h,启停336次。
大修时,发现汽轮机转子前轴封高温段1,2号弹性槽底部圆弧过度圆角处分别存在周向断续裂纹1条,深约2mm;周向连续裂纹2条,裂纹张口0.5-0.6mm,深约7mm。
在对转子钢30CrMoV进行材质分析时,发现1,2号弹性槽底及调节级前叶轮根部表面维氏硬度值由最初的203降到目前的1p
从表1结果看,到这次大修时,寿命总损耗达到86.391%,接近转子表面萌生裂纹程度,应对调节级前叶轮根部进行研磨处理,消除损伤表层,增加使用寿命。
如不作任何处理,继续运行2年,则寿命总损耗将达到109.718%,调节级前叶轮根部表面将出现裂纹。
若对调节级前叶轮根部进行研磨处理,可使表面硬度恢复到Hv=193,继续运行2年,寿命总损耗仅为13.755%。
因此,对转子表面进行研磨处理是必要的。
5、结语
汽轮机转子的无损检测是一项系统工程,涉及汽轮机和金属材料等多个专业。
只有按照DL 438一2009 标准要求,实施一系列有效措施后,才能提高机组运行的安全性和经济性。
坚持引进无损检测新技术,提高检侧可靠性。
根据检测需要,研制多种应用于现场的超声波换能器能促使新工艺得到广泛应用。