5、唐钢第一钢轧厂铁水预处理(脱硫)工艺(封皮106)
KR法铁水预处理脱硫的生产实践浅析

211管理及其他M anagement and otherKR 法铁水预处理脱硫的生产实践浅析张振杰(南京钢铁股份有限公司板材事业部第一炼钢厂,江苏 南京 210035)摘 要:硫对于大部分钢种危害程度较高的一种元素,并且其通常情况下是以硫化物的形式存在于钢中。
在实际的应用过程中倘若钢内的硫含量过高,将会对钢材的加工以及使用方面造成极大程度的影响,因此对展开铁水预处理脱硫的意义重大。
本文主要针对南钢KR 机械搅拌法改造后铁水预处理脱硫的生产实践进行了有效的分析。
关键词:机械搅拌法;铁水;脱硫;生产中图分类号:TF704.3 文献标识码:A 文章编号:11-5004(2020)22-0211-2 收稿日期:2020-11作者简介:张振杰,男,生于1982年,汉族,河北衡水人,本科,工程师,研究方向:钢铁冶炼及其相关。
近些年来,铁水预处理脱硫技术得到了相对较快的发展,至今已出现了多种不同类型的工艺处理方法,然而在具体的应用过程中经常使用广泛的有喷吹法以及KR 搅拌法。
KR 搅拌法在进行铁水预处理脱硫的生产实践过程中消耗相对喷吹法较小,同时在处理的过程中有所产渣量相对较少,反应速度快和效率高等优势。
1 方案选型现阶段,铁水脱硫的主要手段在具体生产过程中经常采用的有以KR 法未代表的机械搅拌法以及喷吹法。
该两种脱硫方法在具体实践过程中,均有一定的优势与特点,从而使其能够在炼钢业内得到相对较为广的应用。
关于KR 法脱硫工艺与喷吹法脱硫工艺主要特点的比较。
(1)关于KR 脱硫法工艺由于其在脱硫的过程中动力条件相对较为充分因此该工艺具有相对较高的脱硫率,同时其重现性与稳定性相对较高。
然而因为喷吹脱硫工艺在具体的实施过程中其角度方面的制约还有脱硫剂不能下沉等方面因素的影响,在脱硫的过程中存在一定的死角区域,从而一定程度上影响铁水动力学条件,且经常出现回硫的情况以及对于脱硫剂的消耗相对较大等不足之处,由于该因素的存在使得喷吹脱硫工艺在重现性与稳定性方面与KR 脱硫法存在一定的差距。
唐钢一钢轧厂SPHC高效精炼的实践
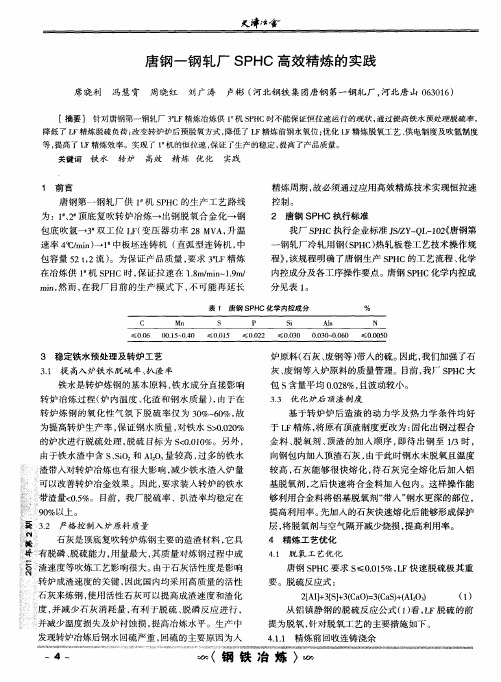
于 L 精炼 , F 将原有顶渣制度更 改为 : 固化 出钢过程合
金料 、 脱氧剂 、 顶渣 的加入顺序 , 即待 出钢 至 1 / , 3时 向钢包内加入顶渣石灰 , 由于此时钢水未脱氧且温度
由于铁水渣 中含 s s : A。, 、i 和 l 量较高 , O O 过多 的铁水 _ 渣带人对转炉冶炼也有很大影响 , 少铁水渣入炉量 。 减 l≯ l 可以改善转炉冶金效果。因此 , 要求装入转炉 的铁水
关键词
铁水
转 炉 高效
精 炼 优 化高效精炼技术 实现恒拉速
控制 。 2 唐钢 S H P G执行标准
唐钢第一钢轧厂供 1机 S H P C的生产 工艺路线
为 :1、 2 顶底 复吹转炉冶炼一 出钢 脱氧合 金化一 钢
包底吹氩一3 双工 位 L ( F 变压器 功率 2 V 升温 8M A, 速率 4Cm n一 1中板坯 连铸 机 ( 弧型连铸机 ,  ̄l i) 直 中
4 精 炼 工 艺 优化
41 脱 氧 工 艺 优 化 .
9 %以上 。 0 32 严 格 控 制入 炉原 料 质 量 .
l l 石灰是顶底复吹转炉炼钢主要 的造渣 材料 , 它具 廿鬈 有脱磷 、 脱硫能力 , 用量最大 , 其质量对炼 钢过程 中成
§ 渣速度等吹炼工艺影响很大。 由于石灰活性度是影响
我厂 S H P C执行企业标准 J/Y Q 一 0 < SZ — L 12 唐钢第 (
一
钢轧厂冷轧用钢 (P C) S H 热轧板卷 工艺技 术操作 规
包容量 5 , 流 ) 2t2 。为保证产 品质量 , 求 3 F 炼 要 # 精 L 在冶炼供 1机 S H P C时 , 保证拉速 在 18 / i~ .r . m n 1 r m 9d
一炼钢铁水预处理脱硫过程影响因素分析
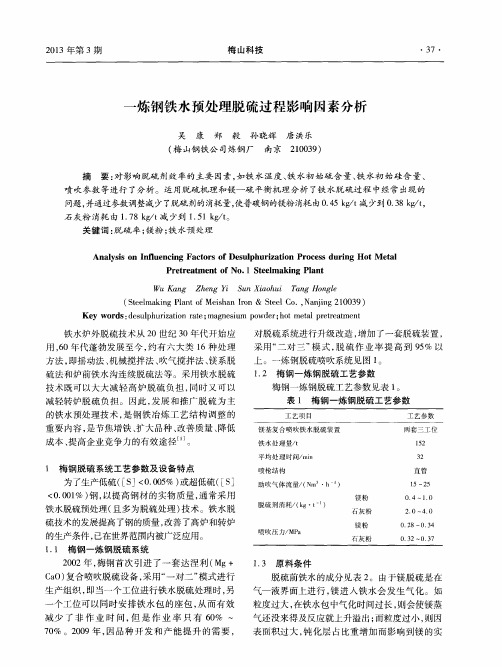
铁水炉外脱硫技术从 2 0世纪 3 0 年代开始应
用, 6 0年 代蓬 勃发 展至 今 , 约 有六 大 类 1 6种 处 理 方法 , 即摇 动法 、 机械 搅拌 法 、 吹气搅 拌 法 、 镁 系脱
对脱 硫 系统进 行升 级改 造 , 增 加 了一套 脱硫装 置 , 采用 “ 二对三” 模式 , 脱硫作业 率提高 到 9 5 % 以 上 。一炼 钢脱 硫喷 吹系 统见 图 1 。
A n a l y s i s o n I n l f u e n c i n g F a c t o r s o f D e s u l p h u r i z a t i 0 n P r o c e s s d u r i n g Ho t Me t a l
表 4 参数 设置 前后 脱硫 粉剂 消耗 指标
2 . 3 初始 硫含 量对 脱硫 剂效 率 的影 响
度较 快 。随着 硫 含量 的 降低 , 溶 解 的镁 占镁 量 的 比例 越来 越大 。从 铁 水 温 度 与脱 硫 剂 效 率 Ks 的 散点 图 ( 见图 3 ) 可 以看 出 , 由于铁 水 温度 高 时 , 在
脱硫 前铁 水 的成分 见 表 2 。 由于镁 脱 硫是 在 气一 液界 面上 进行 , 镁 进 入铁 水 会 发 生 气 化 。如
个工位可以同时安排铁水包的座包 , 从 而有效
减少 了非 作 业 时 间, 但 是 作 业 率 只有 6 0 % ~ 7 0 % 。2 0 0 9年 , 因 品种 开 发 和 产 能 提 升 的 需 要 ,
铁水预处理技术操作规程√

铁水预处理技术操作规程1、原料要求1.1 铁水条件铁水温度:T≥1250℃铁水硫含量:[S]≤0.140%处理铁水量:与转炉铁水装入量相符1.2 脱硫剂采用CaO系脱硫剂1.3 脱硫剂加入量范围处理前铁水s含量目标S 脱硫剂加入量(Kg/t铁)≤40 ≤20 4~4.5 ≤10 6.5-7.041~50 ≤40 3.0-3.5 ≤20 4.0~5.0 ≤10 6.0~6.551~60 ≤40 3.5-4.0 ≤20 6.0~6.5 ≤10 6.0~8.561~70 ≤40 3.5-4.5 ≤20 6.0~8.0 ≤10 7.5~9.071~80 ≤40 4.5-7.5≤20 7.5~9.0 ≤10 9.0~10.581~90 ≤40 5.5-7.0≤20 9.0~10.5 ≤10 10.0~12.591~100 ≤40 6.5-8.0≤20 10.5~11.5 ≤10 12.0~13.5101~110 ≤40 8.0-9.5≤20 11.5~12.5 ≤10 12.5~14.5>110 ≤40 ≥9.5≤20 13.0~14.5 ≤10 14.5~16.5注:(1)视脱硫剂理化指标上升、下降,可将前[S]减少或提高0.020%。
(2)前[S]≤0.045%时,可将前[S]提高0.005~0.010%。
(3)根据搅拌头状况、铁水带渣量的多少,脱硫剂加入量可适当调整。
(4)特殊情况(如:设备故障、生产节奏紧、前硫未及时分析出来等)脱硫剂加入量可按照上限硫含量进行处理。
2、扒渣作业2.1 启动液压电机,将罐倾翻至扒渣角度(以铁水不能溢出为准)。
2.2 接通扒渣扒电源选择手动或自动操作方法,确认各信号是否正常及各分功能紧停开关位置。
2.3 确认压缩空气入口压力≥0.4Mpa,小车前进端极限在零位,后退端极限在十位上。
2.4 调整大臂高度,试扒后再调整适宜高度。
2.5 当罐内渣块≥600kg(目测)时,原则上不能强行扒渣,应将铁水返回混铁炉。
铁水预处理脱硫分析
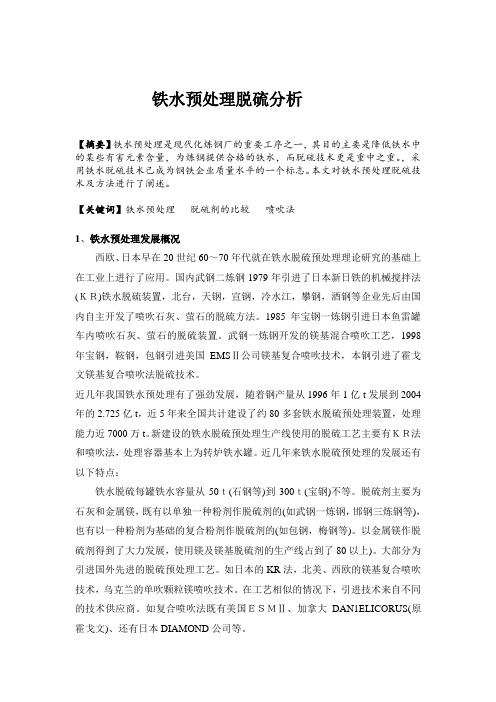
铁水预处理脱硫分析【摘要】铁水预处理是现代化炼钢厂的重要工序之一,其目的主要是降低铁水中的某些有害元素含量,为炼钢提供合格的铁水,而脱硫技术更是重中之重。
,采用铁水脱硫技术已成为钢铁企业质量水平的一个标志。
本文对铁水预处理脱硫技术及方法进行了阐述。
【关键词】铁水预处理脱硫剂的比较喷吹法1、铁水预处理发展概况西欧、日本早在20世纪60~70年代就在铁水脱硫预处理理论研究的基础上在工业上进行了应用。
国内武钢二炼钢1979年引进了日本新日铁的机械搅拌法(KR)铁水脱硫装置,北台,天钢,宣钢,冷水江,攀钢,酒钢等企业先后由国内自主开发了喷吹石灰、萤石的脱硫方法。
1985年宝钢一炼钢引进日本鱼雷罐车内喷吹石灰、萤石的脱硫装置。
武钢一炼钢开发的镁基混合喷吹工艺,1998年宝钢,鞍钢,包钢引进美国EMSⅡ公司镁基复合喷吹技术,本钢引进了霍戈文镁基复合喷吹法脱硫技术。
近几年我国铁水预处理有了强劲发展,随着钢产量从1996年1亿t发展到2004年的2.725亿t,近5年来全国共计建设了约80多套铁水脱硫预处理装置,处理能力近7000万t。
新建设的铁水脱硫预处理生产线使用的脱硫工艺主要有KR法和喷吹法,处理容器基本上为转炉铁水罐。
近几年来铁水脱硫预处理的发展还有以下特点:铁水脱硫每罐铁水容量从50t(石钢等)到300t(宝钢)不等。
脱硫剂主要为石灰和金属镁,既有以单独一种粉剂作脱硫剂的(如武钢一炼钢,邯钢三炼钢等),也有以一种粉剂为基础的复合粉剂作脱硫剂的(如包钢,梅钢等)。
以金属镁作脱硫剂得到了大力发展,使用镁及镁基脱硫剂的生产线占到了80以上)。
大部分为引进国外先进的脱硫预处理工艺。
如日本的KR法,北美、西欧的镁基复合喷吹技术,乌克兰的单吹颗粒镁喷吹技术。
在工艺相似的情况下,引进技术来自不同的技术供应商。
如复合喷吹法既有美国ESMⅡ、加拿大DAN1ELICORUS(原霍戈文)、还有日本DIAMOND公司等。
我国在早期引进国外先进技术的基础上改进的自主知识产权开发技术也在发挥着作用。
炼钢8步工艺流程

炼钢8步工艺流程
《炼钢8步工艺流程》
炼钢是一项重要的冶金工艺,用于生产高质量的钢材。
它需要经过一系列复杂的步骤才能完成。
以下是炼钢的典型8步工艺流程:
1. 预处理:原料是铁矿石和废钢,它们需要进行预处理,去除杂质和控制化学成分。
2. 熔炼:预处理后的原料被放入大型高炉中,通过高温熔炼达到融化状态。
3. 脱硫:在熔炼过程中,加入脱硫剂,以去除铁水中的硫和磷等杂质。
4. 脱氧:通过加入脱氧剂,去除铁水中的氧化物,提高钢的质量。
5. 合金化:根据生产需求,加入合金元素,如铬、镍和钛等,来调整钢的化学成分。
6. 精炼:在精炼炉中,对合金成分进行精密调整,以确保钢的质量和性能。
7. 结晶器:通过冷却处理,控制钢材的晶粒结构,使其获得理想的物理性能。
8. 成型:将高纯度的钢水倒入模具中,冷却后得到成品。
以上8步工艺流程是炼钢的基本工艺,每一步都至关重要,需要高度的技术和经验支持。
通过严格执行这些步骤,可以生产出高品质的钢材,满足各种工业领域的需求。
铁水预处理技术2

2013-7-22 铁水预处理技术 23
三种铁水预脱硅流程:
2013-7-22 铁水预处理技术 6
炉外脱硫的好处体现在:
高炉: 减轻脱硫负担,稳定、顺行、降低焦比
转炉:解放生产率,冶炼优质钢和合金钢 (高附加值钢种、低硫或极低硫钢)
预脱硫是目前实现全连铸、近终形连铸连轧和 热装热送新工艺的最经济、最可靠的技术保障。
企业:提高铁、钢、材系统的综合经济效益, 提高市场竞争能力。
铁水预处理技术
2013-7-22
12
(4) 镁 (Mg)系:
种类:
① 镁焦(Magcoke); ② 镁合金(MgFeSi); ③ 覆膜镁粒:其惰性保护膜占重量的3%~10%; ④ 覆膜混合镁粒:含Mg30%~80%,余为惰性物质。
镁的脱硫机理: 镁和[S]有很强亲合力,
[Mg ] + [S] ==== MgS(固) Mg(气) + [S] ==== MgS(固)
2013-7-22 铁水预处理技术 7
3)发展铁水预处理(脱硫)的必要性与紧迫性 是脱硫反应化学冶金学合理性的必要
高炉:动力学条件差,脱硫要付出代价 高炉脱硫:高炉温、焦比高、产量低 转炉:热力学条件不好,几乎无脱硫能力 炉外:可创造良好的热力学和动力学条件
是钢材市场竞争力紧迫性的必要 是企业工艺结构调整、产品发展需求的必要
8.3 铁水预处理脱硅
1 )铁水预脱硅发展背景及现状
常用铁水预处理技术

常用铁水预处理技术常用铁水预处理技术铁水预处理基础知识1、什么是铁水预处理?★铁水预处理指铁水兑人炼钢炉之前,为除去某些有害成份或回收某些有益成分的处理过程。
针对炼钢而言,主要是使铁水中硅、磷、硫含量降低到所要求的范围,以简化炼钢过程,提高钢的质量。
铁水预处理具体分为铁水炉外脱硅、脱磷和脱硫,有时脱磷和脱硫同时进行。
对于铁水含有特殊元素提纯精炼或资源综合利用而进行的提钒、提铌、提钨等预处理技术则称为特殊预处理。
2、什么是铁水“三脱”技术?★指铁水兑人炼钢炉之前,进行脱硫、脱硅、脱磷的预处理工艺过程。
3、铁水脱硫的目的是什么?★提高钢质、扩大品种和改善炼钢操作,提高钢的机械、工艺性能。
4、铁水脱硅的目的是什么?⑴减少转炉炼钢渣量、改善操作和提高炼钢经济指标。
硅是氧气转炉炼钢发热的元素,所以为了提高炼钢熔池温度和早化渣,往往希望铁水含硅高一些,但实践证明铁水含硅高时,为了保证转炉渣有较高的碱度,势必增加石灰消耗量,使渣量增多,冶炼时间延长,耗氧量增加,喷溅加剧,铁损增加,并给操作带来困难,从而降低炼钢生产率和增加生产成本。
铁水含硅量一般应控制在0.4%以下的水平。
(2)铁水预脱磷的需要脱硅是铁水预脱磷的先决条件。
铁水预脱磷要求脱磷反应区的氧位高,当加入氧化剂提高氧位时,硅首先就与氧作用而降低铁水中的氧位。
为此,脱磷首先要脱硅,脱磷前控制硅含量一般要求在0.15%以下。
5.铁水脱磷的目的是什么?(1)生产低磷钢、超低磷钢和不锈钢等工艺需要。
磷在钢中对性能的影响,除少数钢种为提高强度或耐大气腐蚀性,要求有一定含磷外,对大多数钢种是有害的,它降低钢的冲击韧性,尤其是低温冲击韧性;磷的枝晶偏析使板材产生带状组织,造成钢板各向异性。
随着新技术材料的发展,对某些品种钢要求磷含量≤0.01%(低磷钢) 或≤0.005%(超低磷钢) 。
用转炉工艺脱磷,虽然有较好的脱磷效果,但达到这种低磷的水平是难以完成的,如采取多次造渣操作,有可能达到,但都存在渣料消耗大,冶炼时间长,热损失大,金属收得率低等问题。
铁水预处理工艺

高效铁水预处理工艺开发新日铁公司君津制铁所采用将运送铁水的鱼雷罐车(TPC)作为精炼容器的ORP铁水预处理工艺,为大量生产高纯净钢奠定了基础。
然而,因从高炉出铁至转炉出钢的时间长,铁水处理中产生大量泡沫等问题限制了操作。
为此,该所一炼车间于1999投产了由KR(机械搅拌式脱S设备)和转炉型铁水P处理工艺(LD-ORP)组成的新工艺。
与原TPC型ORP工艺按在高炉出铁场脱Si、排除脱Si渣、喷粉脱P脱S的多段式分开处理不同,新工艺是在高炉出铁后到铁水包里采用KR工艺脱S,再用转炉的LD-O RP工艺脱Si脱P的2段式处理工艺,从而集中了处理场所并改善了炼钢物流。
而且,从热力学的观点重新配置了各种预处理反应,还分别采用了各种专用精炼容器的强搅拌(机械和全体搅拌)处理从而提高了精炼速度和效率。
整个工艺流程的产能为220t/炉次。
其中,KR的搅拌叶转速为100~120r?p?m(转/分),处理时间为9~11分钟;LD-ORP的顶吹氧最大为150Nm3;/小时?t,底吹CO2流量8 Nm3;/小时?t,处理时间8分钟。
较之原工艺,新流程缩短了各精炼工序时间,从而将从出铁~出钢的全程时间从原300~450分钟减少到240~350分钟,缩短了25%;还大幅度降低了铁水在运送中的温度,提高了设备周转率,降低了生产费用。
采用转炉渣对铁水脱P神户制钢?加古川制铁所从1999年开始,在铁水全量脱P处理中大量配用转炉炼钢熔渣,从而提高了脱P效率,缩短了脱P时间。
该厂的铁水预处理工艺流程为首先在高炉出铁场脱Si并除渣后,将铁水送往预处理站进行用转炉渣+生石灰(CaO)+铁矿石(FeO)的脱P处理,再用生石灰和碳化钙(CaC2)脱S。
转炉渣配合率与脱P处理后渣中游离CaO(即freeCaO简称f-CaO)密切相关,既提高转炉渣配合率将大大减少渣中f-CaO,当转炉渣配合率由0%提高到50%时,f-CaO由25%减少到5%左右。
铁水预处理工艺方法及原理

铁水预处理工艺方法及原理铁水预处理是指铁水兑入炼钢炉前对其进行脱除杂质元素的一种处理工艺。
常用的工艺方法有:铁沟散料法、铁水罐内喷吹法、铁水罐内机械搅拌法等。
(1)铁沟散料法:高炉出铁时,在铁沟内的铁水上散入工业纯碱(Na2CO3)或复合脱硫剂(由Na2CO3 、CaO、CaCO3、CaF2、C粉等配合而成),利用铁水流动时的冲击湍流运动使铁水与脱硫剂搅拌混合,促进脱硫反应,达到脱硫目的。
该法简便易行,但脱硫效率波动大(约为20—60%)、环境污染大、恢硫多。
已基本不用。
(2)铁水罐内喷吹法:如右图所示:在送去转炉的铁路线上设立喷吹脱硫站,喷枪的铁管外复合有耐火材料浇注料,可插入铁水内一定深度,以空气为载体,喷入粉状脱硫剂,进行脱硫,而后耙除脱硫渣,防止恢硫(脱硫渣如果不去掉,在后续过程中,脱硫渣中的硫又会返回铁水中,造成恢硫)。
由于该法使脱硫剂与铁水接触良好,脱硫效率较高,还可脱除部分硅和碳。
常用的脱硫剂:a、钝化石灰粉(不含钝化剂的石灰,存放时间稍长,吸水到一定程度,就会堵塞喷吹系统)。
优点:成本较低、脱硫效率较高。
缺点:环保较差、铁水温降较大。
b、复合脱硫剂(由Na2CO3 、CaO、CaCO3、CaF2、C粉等配合而成)。
优点:成本较低、脱硫效率较高、比钝化石灰粉较易耙渣。
缺点:环保较差、铁水温降较大。
c、钝化镁粒(金属镁粒需钝化,否则存放时易氧化,同时载体需改为氮气)。
金属镁粒喷入铁水后,会迅速气化,与铁水接触条件更好,脱硫率很高。
优点:脱硫率很高、喷吹设备和操作很简单、环保较好、铁水温降很小、脱硫渣量很小。
缺点:成本高。
d、钝化镁粒与钝化石灰混喷(结合了金属镁粒脱硫率很高和钝化石灰成本低的优点,还可根据铁水含硫量和所炼钢种,来调节钝化镁粒(0—100%)与钝化石灰的配比,从而达到最佳成本与脱硫率的配合。
优点:脱硫率很高且可调、环保较好、铁水温降较小、脱硫渣量较小、成本较低且可调。
缺点:喷吹设备投资较大、操作较复杂。
铁水预处理

一、铁水预处理概述
铁水预处理是指高炉铁水在进入炼钢炉之前预先脱除某 些杂质的预备处理过程。
分为普通铁水预处理和特殊铁水预处理两大类。
普通铁水预处理包括:铁水脱硫、铁水脱硅和铁水脱P。 特殊铁水预处理一般是针对铁水中含有的特殊元素进行 提纯精炼或资源综合利用,如铁水提钒、提铌、脱铬等 预处理工艺。
意大利 Taranto
0.01%占% 80.4 87.0 87.5
0.006%占% 36.4 240 4.7 48.8 240 4.9 62.5 240 5.3
12
喷Mg颗粒脱硫处理实绩
铁水罐容量(t) 铁水罐净空高度(mm) 喷吹罐容积(m3) 喷吹压力(Mpa) 喷吹流量(Nm3/min) 喷吹速度(kg/min) 处理前[S] Mg 单耗(kg/t) 温度降低(℃) 喷吹时间(min) [S]≤0.01% [S]≤0.005% [S]≤0.01% [S]≤0.005% [S]≤0.01% [S]≤0.005% 100 800 0.5×2 0.3~0.5 30~60 6~15 0.04% 0.2±0.05 0.46±0.03 10±1 12±1 5±1 7±1
搅拌能 低 高
氧气 比率 低 高
废钢比 低 高
建设投资 低 高
29
转炉脱磷主要目的:生产低磷、超低磷钢?
新日铁Matsumiya博士回答:
▪
[P]含量控制:
▪ ▪ 转炉脱磷处理后: 0.018~0.020%; 脱碳转炉出钢: 0.015~0.018%.
▪
采用转炉脱磷-脱碳工艺的主要目的:
1. 提高生产和工艺控制的稳定性;
T. Ueki, et al., The 10th Japan-China Symposium on Science and Technology of Iron and Steel, 2004, p116
炼钢厂铁水预处理一键脱硫控制系统

炼钢厂铁水预处理一键脱硫控制系统1 脱硫预处理组成与流程两个脱硫站共用一套氮气供应管路,即石灰和镁粉的储料仓。
为增加系统的灵活性,设置了一套共用的切换阀用于垂直(默认)和交叉(紧急备用)喷吹之间的选择。
喷吹系统、测温取样系统、铁包车、扒渣机和液压系统虽然每个站各自独立,但两站彼此又相同。
每个脱硫站均有两套独立的提升装置,一套用于脱硫喷枪的升降,另一套用于测温取样枪的升降。
为了获得更好的速度和位置控制,喷枪升降驱动装置采用变速调频电机驱动控制(vfd)。
铁水通过铁包车运至脱硫站。
铁包车直接接受原料跨450t天车吊运的铁水,而后从吊/座包位运至喷吹位进行喷吹、扒渣处理,当喷吹、扒渣完成后,再将铁水运至吊/座包位,由原料跨450t 天车从车上吊走处理好的铁水,完成一个脱硫周期。
铁水预处理工艺流程如图1。
2 远程i/o通讯主控台包含主控桌,主控桌包含有作为一台hmi和二级客户计算机的操作工作站。
himi显示用西门子wincc可扩充软件设计,并提供了脱硫和除尘系统设备的监控。
操作者报警将显示和公布在控制室的hmi上。
每个脱硫站将包括4个控制柜,每个控制柜均配有远程i/o通讯站,远程i/o模块通过一个profibus 网络与plc进行通讯。
plc 经过采用tcp/ip(工业以太网)协议的以太网与hmi进行通讯。
这种通讯方式在其配置和维护方面具有很大的适应性,并准许过程数据通过远程编程经过opc服务器进行存取。
脱硫站包括一套用oracle为数据库的二级系统。
它由一个位于计算机房的服务器和一个客户机组成。
服务器用于数据的储存和管理,客户机作为hmi使用。
3 一键喷吹系统优化每个站控制系统是由一台西门子s7-400系列可编程逻辑控制器(plc)和一台用于控制两个站共用部件s7-300plc组成。
每个plc 均有本地和远程数字和模拟i/o接口。
该系统也包括每个脱硫站的人机界面(hmi),人机界面位于主控制操作台上,若必要,每个人机界面均能控制两个站。
钢水脱硫新技术

钢水脱硫新技术由于在钢水加工过程中,硫元素的含量出现不断增长的趋势,同时市场上对金属的质量要求也在不断提升,在全球范围内,至少绝大多数的使用氧气顶吹转炉的钢铁厂对其中部分钢材进行了脱硫处理。
常规的钢水脱硫是把钢铁先进行转炉处理,然后再进行脱硫,这是后端脱硫,但是采用在金属进入到转炉中之前,先进行脱硫处理的前端脱硫方式更具经济性。
针对钢水脱硫过程,尽管有许多种方法可以使用,但是在大规模的商业使用上,有三种主要的脱硫方法:(1)机械搅拌脱硫法(KR):使用石灰作为反应试剂;(2)乌克兰(Desmag)颗粒镁喷吹技术或者镁粉单通道注塑工艺(MMI):将镁作为反应试剂;(3)多通道共同注塑工艺法:使用镁粉、石灰或者电石(或者三者同时使用)作为反应试剂。
反应试剂在这三种常用的钢水脱硫工艺中(KR、MMI和多通道混合共注塑法),常用的反应试剂有石灰、电石和镁粉等。
所有的反应过程都是基于如下的化学反应方程式:S(fe) + CaS →CaS + O(fe)(1)S(fe) + CaC2→CaS + 2C(fe)(2)S(fe) + Mg →MgS(3)上述三个反应式中,反应(3)的反应速率是反应(2)的速率的3倍,同时是反应(1)的速率的20倍。
这也就意味着,以镁粉作为反应试剂的时候,将会比用其他试剂的反应速率快很多。
在反应结束之后,反应产物之中会形成大量的CaS和MgS(它们的密度均比液态铁的密度低),这些产物将会上升到液态铁的表面,并形成渣层。
生产过程结束后,将这一层渣层清除,此时,硫元素将会从钢水中除去。
当MgS到达钢水表面的时候,这些产物将会接触到空气中的氧气,那么将会发生如下的反应过程:2MgS + O2→2MgO + 2S(4)此时,又有部分不受控制的硫元素再次溶解到液态铁水里面。
这就是所谓的再次硫化过程,可以通过两种方法来避免这种现象的产生——第一种,尽量避免空气和MgS的接触,但是这也将会导致一些实际问题的发生,(反应试剂的注入过程和灰渣的清理过程都应该惰性气体的氛围中进行)。
铁水预处理工艺技术操作规程
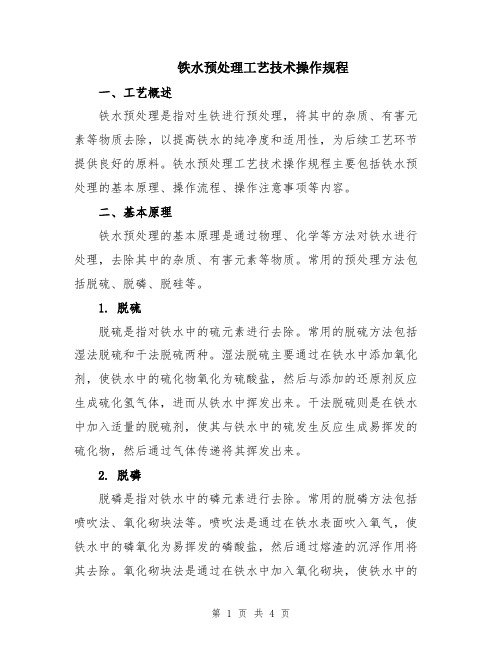
铁水预处理工艺技术操作规程一、工艺概述铁水预处理是指对生铁进行预处理,将其中的杂质、有害元素等物质去除,以提高铁水的纯净度和适用性,为后续工艺环节提供良好的原料。
铁水预处理工艺技术操作规程主要包括铁水预处理的基本原理、操作流程、操作注意事项等内容。
二、基本原理铁水预处理的基本原理是通过物理、化学等方法对铁水进行处理,去除其中的杂质、有害元素等物质。
常用的预处理方法包括脱硫、脱磷、脱硅等。
1. 脱硫脱硫是指对铁水中的硫元素进行去除。
常用的脱硫方法包括湿法脱硫和干法脱硫两种。
湿法脱硫主要通过在铁水中添加氧化剂,使铁水中的硫化物氧化为硫酸盐,然后与添加的还原剂反应生成硫化氢气体,进而从铁水中挥发出来。
干法脱硫则是在铁水中加入适量的脱硫剂,使其与铁水中的硫发生反应生成易挥发的硫化物,然后通过气体传递将其挥发出来。
2. 脱磷脱磷是指对铁水中的磷元素进行去除。
常用的脱磷方法包括喷吹法、氧化砌块法等。
喷吹法是通过在铁水表面吹入氧气,使铁水中的磷氧化为易挥发的磷酸盐,然后通过熔渣的沉浮作用将其去除。
氧化砌块法是通过在铁水中加入氧化砌块,使铁水中的磷与氧化砌块发生反应生成磷酸盐,然后通过熔渣的沉浮作用将其去除。
3. 脱硅脱硅是指对铁水中的硅元素进行去除。
常用的脱硅方法包括湿法脱硅和干法脱硅两种。
湿法脱硅主要是通过在铁水中加入足够量的碱性矿物,使硅与碱性矿物发生反应生成易挥发的硅酸盐,然后通过熔渣的沉浮作用将其去除。
干法脱硅则是在铁水中加入适量的脱硅剂,使其与铁水中的硅发生反应生成易挥发的硅化物,然后通过气体传递将其挥发出来。
三、操作流程铁水预处理的操作流程按照脱硫、脱磷、脱硅的顺序进行,具体步骤如下:1. 脱硫操作流程(1) 检查脱硫设备及周围环境的安全情况。
(2) 开始对铁水进行脱硫前,要先对铁水进行预热,使其温度达到预定的要求。
(3) 进行湿法脱硫时,在预热后的铁水中加入适当的氧化剂,并根据预定的脱硫时间进行搅拌。
天车称量系统在唐钢第一钢轧厂的应用
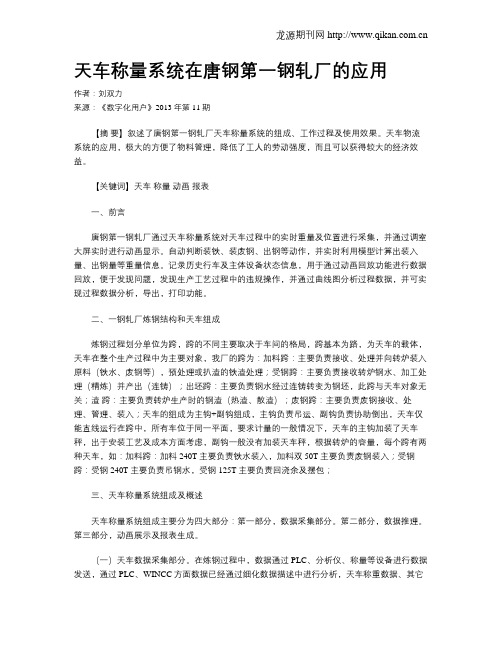
天车称量系统在唐钢第一钢轧厂的应用作者:刘双力来源:《数字化用户》2013年第11期【摘要】叙述了唐钢第一钢轧厂天车称量系统的组成、工作过程及使用效果。
天车物流系统的应用,极大的方便了物料管理,降低了工人的劳动强度,而且可以获得较大的经济效益。
【关键词】天车称量动画报表一、前言唐钢第一钢轧厂通过天车称量系统对天车过程中的实时重量及位置进行采集,并通过调室大屏实时进行动画显示。
自动判断装铁、装废钢、出钢等动作,并实时利用模型计算出装入量、出钢量等重量信息。
记录历史行车及主体设备状态信息,用于通过动画回放功能进行数据回放,便于发现问题,发现生产工艺过程中的违规操作,并通过曲线图分析过程数据,并可实现过程数据分析,导出,打印功能。
二、一钢轧厂炼钢结构和天车组成炼钢过程划分单位为跨,跨的不同主要取决于车间的格局,跨基本为路,为天车的载体,天车在整个生产过程中为主要对象,我厂的跨为:加料跨:主要负责接收、处理并向转炉装入原料(铁水、废钢等),预处理或扒渣的铁渣处理;受钢跨:主要负责接收转炉钢水、加工处理(精炼)并产出(连铸);出坯跨:主要负责钢水经过连铸转变为钢坯,此跨与天车对象无关;渣跨:主要负责转炉生产时的钢渣(热渣、散渣);废钢跨:主要负责废钢接收、处理、管理、装入;天车的组成为主钩+副钩组成,主钩负责吊运、副钩负责协助倒出,天车仅能直线运行在跨中,所有车位于同一平面,要求计量的一般情况下,天车的主钩加装了天车秤,出于安装工艺及成本方面考虑,副钩一般没有加装天车秤,根据转炉的容量,每个跨有两种天车,如:加料跨:加料240T主要负责铁水装入,加料双50T主要负责废钢装入;受钢跨:受钢240T主要负责吊钢水,受钢125T主要负责回浇余及摆包;三、天车称量系统组成及概述天车称量系统组成主要分为四大部分:第一部分,数据采集部分。
第二部分,数据推理。
第三部分,动画展示及报表生成。
(一)天车数据采集部分。
在炼钢过程中,数据通过PLC、分析仪、称量等设备进行数据发送,通过PLC、WINCC方面数据已经通过细化数据描述中进行分析,天车称重数据、其它数据库中数据则作为此次采数的重点分析项目,采集数据作为整个精细化管理系统的首要数据源入口,如何做到稳定、记录筛选并保存到数据库中则是整个采集系统的灵魂所在。
铁水预处理技术

铁水预处理技术1.概述铁水预处理技术从上个世纪六、七十年代发展起来到现在已经广泛地应用于各国,用于提高铁水质量,其技术也已经得到迅速的发展,目前可以用于铁水预处理的技术不下二、三十种。
铁水预处理工艺方法主要有:(1)机械搅拌法,有代表性的是日本开发的KR法;(2)吹气搅拌法,包括顶吹喷粉法和底吹法,目前顶吹喷粉法得到最广泛的应用,如ATH、TDS、IRSID、ISIDD等法;(3)喂丝法近年来开始得到应用。
铁水预处理的主要工艺目标是:(1)脱硫;(2)脱磷;(3)脱硅、磷、硫(俗称三脱);(4)其它。
从处理熔剂的选择来看有:主要是石灰系、碳化钙系、镁系三类脱硫剂,可以单独使用,可以复合应用,往往可以取得更好的冶金效果。
顶吹喷粉法近年发展了更多的工艺形成:产生了混合喷吹法和复合喷吹法以及分步喷吹法等。
从控制模型方面看:近年来更加重视建立较高精度的预处理粉剂喷吹量的控制模型。
还有一些不同的分类方法,但是无论怎样分类,每个企业选择的原则都是一样的,那就是从自己企业近期和长远规划来考虑,结合企业能力、产品目标、市场、经济效益等具体情况选择最适合自己的,最有利的方案。
本技术方案——从三个方面介绍科大三泰公司向用户推荐并可提供的技术装备:(1)铁水罐顶喷纯化镁脱硫;(2) 铁水罐采用镁加钙系脱硫剂分步或复合喷吹脱硫(即所谓混喷);(3) 铁水罐采用镁加钙系或者单纯钙系脱硫剂分步或者复合喷吹三脱(脱硫、脱磷、脱硅);是较高精度顶吹喷粉法;脱硫剂选用钝化镁粒或镁系的;喷吹工艺形式采用单系统喷吹或分步复合喷吹;为了提高镁的利用率,降低喷粉生产成本,同时达到目标硫数值,达到喷粉目的,采用具有较高精度的脱硫剂喷吹量的控制模型(可选择的和可即时调控的);采用高技术喷射器系统;带气化室的喷枪;采用PLC 全程程控和计算机操作等。
2.铁水预处理的热力学与动力学2.1 铁水脱硅1)脱硅反应[][]()22S i O S i O +=根据热力学原理不难看出,为了脱硅的同时碳不被氧化,脱硅应在低温下进行,最好不超过1500℃。
铁水预处理工艺技术操作规程
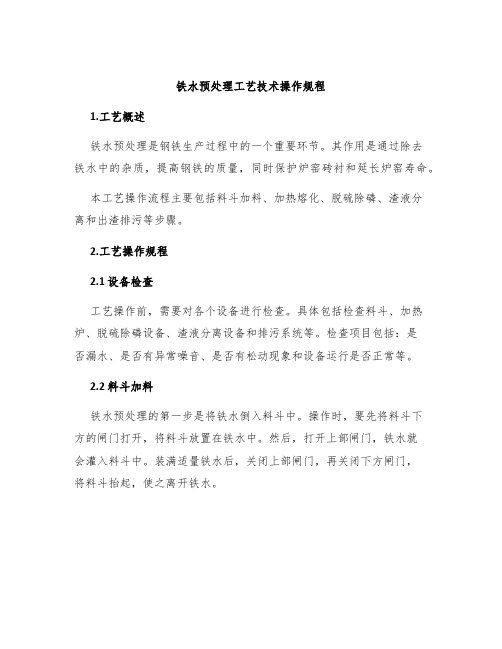
铁水预处理工艺技术操作规程1.工艺概述铁水预处理是钢铁生产过程中的一个重要环节。
其作用是通过除去铁水中的杂质,提高钢铁的质量,同时保护炉窑砖衬和延长炉窑寿命。
本工艺操作流程主要包括料斗加料、加热熔化、脱硫除磷、渣液分离和出渣排污等步骤。
2.工艺操作规程2.1 设备检查工艺操作前,需要对各个设备进行检查。
具体包括检查料斗、加热炉、脱硫除磷设备、渣液分离设备和排污系统等。
检查项目包括:是否漏水、是否有异常噪音、是否有松动现象和设备运行是否正常等。
2.2 料斗加料铁水预处理的第一步是将铁水倒入料斗中。
操作时,要先将料斗下方的闸门打开,将料斗放置在铁水中。
然后,打开上部闸门,铁水就会灌入料斗中。
装满适量铁水后,关闭上部闸门,再关闭下方闸门,将料斗抬起,使之离开铁水。
2.3 加热熔化装有铁水的料斗被送入加热炉中,加热至铁水完全熔化。
操作时,要按照设定的炉温和时间进行加热,在保证料斗不炸裂的前提下,确保铁水能够熔化。
2.4 脱硫除磷熔化后的铁水含有大量的硫和磷等杂质,需要进行脱除。
脱硫除磷设备是通过注入双氧水、氯化钙等化学试剂,将硫和磷等杂质转化为气体或沉淀,使其分离出铁水。
操作时,应按照设定的比例加入化学试剂,然后搅拌,进行反应,最后将杂质分离出来。
2.5 渣液分离经过脱硫除磷后的铁水含有较多的渣液,需要进行分离。
渣液分离设备通过旋转作用使铁水和渣分离,最终得到清洁的铁水,并将渣液排放到渣液仓中。
操作时,要按照设定的转速和时间进行分离。
分离后的渣液需要及时清理,以免影响下一次操作。
2.6 出渣排污渣液分离后,剩余的渣需要进行排出。
操作时,要先打开渣液仓下方的闸门,将渣排放到指定位置。
然后,关闭闸门,清理留在设备内的渣液和杂物。
排污作业应按照环保要求进行,不得将废渣氧化物和有害物质排到环境中。
3.注意事项1.操作人员应熟练掌握操作流程和设备使用知识,日常对设备进行检查和维护,确保设备运行正常;2.加热炉温度不要超过设定值,以免料斗炸裂;3.脱硫除磷过程中应严格按照试剂比例加入,并确保试剂质量合格;4.渣液分离设备应按照设定的转速和时间进行分离,不得过度或不足;5.排污作业应按照环保要求进行,废渣氧化物和有害物质不得排入环境中。
铁水预处理工艺技术操作规程

铁水预处理工艺技术操作规程一、概述铁水预处理是指将铁水中的杂质和其他有害成分去除,使之符合炼钢的要求,为后续的冶炼提供良好的原料。
本工艺技术操作规程旨在规范铁水预处理工艺的操作,确保工艺过程的安全、稳定和高效。
二、设备准备1. 对设备进行全面检查,确保设备正常运行和安全。
2. 检查各类阀门、泵等运行情况,清理设备表面积尘和杂物。
3. 清理储存区域,确保杂物不干扰工艺操作。
4. 做好易燃易爆物品的储存和管理工作。
三、工艺步骤1. 开启预处理设备的主电源,检查设备的电气连接情况。
2. 打开原料输入阀门,调整流量以保证输入量符合要求。
3. 打开设备排液阀门,排出设备内的污水。
4. 打开设备进水阀门,保证进水流量符合要求。
5. 根据铁水的成分和要求,在预处理设备中添加适量的矫正剂和脱氧剂。
6. 开启设备搅拌装置,调整搅拌速度,使其适应工艺要求。
7. 污水排出后,关闭排液阀门。
8. 检查设备运行情况,确保搅拌装置正常运转。
9. 根据实际情况,对设备进行调整和操作。
10. 当铁水成分符合要求时,关闭设备进水阀门,停止添加矫正剂和脱氧剂。
11. 根据生产计划和要求,调整设备停留时间。
12. 打开设备排渣阀门,将沉淀物排出设备。
13. 检查设备内部情况,清理设备表面积尘和杂物。
14. 根据需要,对设备进行维护和保养,确保设备的正常运行。
15. 关闭设备主电源,结束本次操作。
四、安全措施1. 操作人员必须经过相关培训,熟悉设备的操作规程和安全操作要求。
2. 操作人员必须佩戴符合规定的个人防护装备,如安全帽、防护服、防护眼镜等。
3. 在操作过程中,严禁吸烟和使用明火。
4. 严格控制矫正剂和脱氧剂的添加量,避免超量造成的安全隐患。
5. 发现设备异常情况或设备出现故障,应立即停止操作并报告维修人员处理。
6. 遇到突发情况需要停止操作时,应立即关闭设备主电源,并按照应急预案进行处理。
7. 在进行设备维护和保养时,必须切断设备的电源,并进行防护措施。
铁水预处理脱硫的优点

第一节铁水预脱硫的概念和优点铁水预处理,炼钢生产中主要是指铁水在进入转炉之前的脱硫处理。
广义的铁水预处理是指包括对铁水脱硫、脱硅、脱磷的三脱处理,另外还有特殊铁水的预处理,如含V铁水的提V 等。
铁水脱硫是二十世纪70年代发展起来的铁水处理工艺技术,它已成为现代钢铁企业优化工艺流程的重要组成部分。
铁水脱硫的主要优点如下:1.铁水中含有大量的硅、碳和锰等还原性的元素,在使用各种脱硫剂时,脱硫剂的烧损少,利用率高,有利于脱硫。
2.铁水中的碳、硅能大大提高铁水中硫的活度系数,改善脱硫的热力学条件,使硫较易脱致较低的水平。
3.铁水中含氧量较低,提高渣铁中硫的分配系数,有利于脱硫。
4.铁水处理温度低,使耐火材料及处理装置的寿命比较高。
5.铁水脱硫的费用低,如在高炉、转炉、炉外精炼装置中脱除一公斤硫,其费用分别是铁水脱硫的2.6、16.9和6.1倍。
6.铁水炉外脱硫的过程中铁水成份的变化,比炼钢或钢水炉外处理过程中钢水成份的变化对最终的钢种成份影响小。
采用铁水脱硫,不仅可以减轻高炉负担,降低焦比,减少渣量和提高生产率,也使转炉也不必为脱硫而采取大渣量高碱度操作,因为在转炉高氧化性炉渣条件下脱硫是相当困难的。
因此铁水脱硫已成为现代钢铁工业优化工艺流程的重要手段,是提高钢质量、扩大品种的主要措施。
早期的铁水脱硫方法有很多种:如将脱硫剂直接加在铁水罐罐底,靠出铁铁流的冲击形成混合而脱硫的铺撒法。
也有将脱硫剂加入装有铁水的铁水罐中,然后将铁水罐偏心旋转或正向反向交换旋转的摇包法。
之后逐步发展至今天采用的KR搅拌法及喷枪插入铁水中的喷吹法。
第二节常用脱硫剂及脱硫指标一、常用脱硫剂经过长期的生产实践,目前选用作为铁水脱硫剂的主要是Ca、Mg、Na等元素的单质或化合物,常用的脱硫剂主要有:Ca系:电石粉(CaC2)、石灰(CaO)、石灰石(CaCO3)等Mg系:金属Mg粉Na系:苏打(Na2CO3)二、常用脱硫剂反应特点1.电石粉碳化钙脱硫反应为用CaC2脱硫有如下特点:1)在高碳系铁水中,CaC2分解出的Ca离子与铁水中的硫有极强的亲和力。
- 1、下载文档前请自行甄别文档内容的完整性,平台不提供额外的编辑、内容补充、找答案等附加服务。
- 2、"仅部分预览"的文档,不可在线预览部分如存在完整性等问题,可反馈申请退款(可完整预览的文档不适用该条件!)。
- 3、如文档侵犯您的权益,请联系客服反馈,我们会尽快为您处理(人工客服工作时间:9:00-18:30)。
唐钢质量管理体系文件版本号:3 文件编号:JS/ZY—QL—106唐钢第一钢轧厂铁水预处理(脱硫)工艺操作规程(公司秘密)编制:张大勇审核:白连臣批准:持有者:管理编号:2009年02月01日发布2009年02月15日实施----------------------------------------------------------------唐山钢铁股份有限公司技术中心唐钢第一钢轧厂铁水预处理(脱硫)工艺操作规程文件编号:JS/ZY—QL—1061. 工艺流程铁水包进站↓氮气氮气测温取样→化验分析↓↓↓袋装颗粒镁→漏斗→装料罐→喷吹罐→喷枪→喷吹脱硫→烟气除尘↓测温取样→化验分析↓扒脱硫渣→渣罐↓铁水包出站2. 原材料技术条件2.1 颗粒镁金属镁含量≥92%球粒直径0.25-1.6mm,针状粒含量<10%燃点:1000℃、15秒2.2 压缩氮气纯度≥99.9%。
压力:0.8-1.0Mpa露点:-40℃。
含水量:≯0.15g/Nm33. 基本技术条件3.1脱硫前铁水温度:1250-1400℃3.2脱硫前包内铁水重量:140-160t3.3脱硫前包内渣化学成分组成:CaO:34-40%,SiO2:34-37%,MgO:6-10%,S:约1%,FeO:约1%3.4 脱硫前包内渣量:≤2%,渣层厚度>150mm时须扒渣。
3.5 铁水包参数及装满率参数3.5.1 从包底到上沿高:>3.7m3.5.2 熔池深度:>3.0m3.5.3 熔体上自由空间高度:430mm(装150t时)3.5.4 铁水包内径:>2.9m3.6 转炉工作参数:平均兑铁水量150t/炉,出钢频率40min/炉。
3.7 工业电压380/220V±7%,频率50HZ±2。
4. 工艺联锁4.1 铁水包车移动条件⑴脱硫站大门打开,铁水包车方可移动。
⑵脱硫喷枪、测温取样枪在高位,铁水包车方可移动。
⑶扒渣机在原始位置,铁水包车方可移动。
⑷脱硫室除尘阀打开,铁水包车才能通过主控台开到脱硫位;否则只能通过现场控制台操作。
⑸铁水包在垂直位,方可通过主控台操作移动铁水包车。
4.2喷枪架移动条件两喷枪在高位,喷枪架方准移动。
4.3 喷枪上下移动条件⑴喷枪对位即对准喷枪孔。
⑵得到把持器开信号。
⑶扒渣机在原始位。
⑷铁水包在垂直位,方可通过主控台控制喷枪。
4.4 喷枪供气流量达到120-160Nm3/h,喷吹罐中的压力不低于0.6Mpa,喷枪才能下降插到铁水中。
4.5 喷枪只有在最低位置或采用现场控制台控制,转子给料器才能供电。
4.6喷吹过程中,当喷吹罐中的压力降到0.45Mpa以下或供氮流量低于60Nm3/h时,喷枪自动报警提枪。
4.7喷吹罐中颗粒镁重量低于80kg,喷吹系统不具备预启动条件。
4.8在喷吹过程中,设置的颗粒镁量喷完或喷吹罐中颗粒镁重量为0kg时,喷枪自动提枪。
4.9当供氮管路中压力低于0.75Mpa时,喷吹系统不工作。
4.10除尘阀不打开,喷吹系统不工作。
4.11计量系统故障,上料及喷吹系统不工作。
4.12喷枪降到低位,把持器自动关闭;喷枪得到提枪指令,把持器自动打开。
4.13扒渣机操作条件⑴铁水包在竖直位置,扒渣机不能扒渣。
⑵喷枪、测温枪不在高位,扒渣机不能工作。
⑶渣罐车不在扒渣位,扒渣机不能工作。
4.14 铁水包倾翻条件⑴铁水包离开脱硫位,不能倾翻。
⑵渣罐车不在扒渣位,不能倾翻。
5. 颗粒镁的验收和存放5.1颗粒镁存放期(从生产至使用)不能超过6个月。
5.2运送到脱硫站的颗粒镁应由专人按如下标准验收。
5.2.1 检查质量保证书是否齐全,并签收磅单。
5.2.2 检查装有颗粒镁的料袋,以确保完好无损并且袋中无水分。
5.2.3 一旦料袋打开,脱硫工必须确认颗粒镁是否受潮。
5.2.4 抽查取样进行化学分析和物理指标检验(化学检验:含镁量;物理指标:粒度)。
5.3 生产倒运过程中出现的料袋破损,则应将颗粒镁倒入密闭容器中。
5.4对废弃的颗粒镁应系统的排除(扔入铁水包)。
禁止将颗粒镁排入下水管道,以免爆炸。
6. 装料罐装料6.1 装料前准备⑴打开漏斗盘。
⑵检查漏斗内料筛完好且无杂物,如有杂物则清理干净。
⑶确认漏斗下手动门已打开。
⑷确认阀50、阀51、阀52、阀53、阀54、阀55全部关闭。
6.2 装料操作⑴将现场控制台改为手动。
⑵打开阀50、再开阀51。
⑶用上料间的电葫芦吊运颗粒镁料袋到上料系统漏斗料筛上方,料袋下降时,戳穿袋底,再提升料袋到料筛上方(不超过50mm)将颗粒镁缓慢地卸到漏斗中。
⑷利用重力作用,颗粒镁自动从漏斗经管道流入装料罐。
⑸通过计量系统称重装置的读数和PC显示屏的显示数监视颗粒镁装入装料罐的上料情况,装料量不超过上限。
⑹上料完毕待漏斗和送料管中没有颗粒镁后,先关闭上料阀,再关闭除尘阀,盖上漏斗盖。
⑺将现场控制台开关选为自动。
6.3 装料罐上料过程注意事项⑴确认料袋下面和侧面没有杂物,以防卸料期间杂物落入装料罐。
⑵装料罐不能装料太多,以保证顺利上料和避免颗粒镁受潮。
7.喷吹罐转装7.1 向喷吹罐装料时,装入量不得超过最大料位7.2 转装条件⑴阀50、阀51关闭。
⑵现场控制台开关转为自动。
⑶阀60-1打开。
⑷工艺设备和自动化控制系统完好。
⑸供电系统,信号通讯,联锁机构处于正常状态。
⑹供氮管道压力:0.8-1.0Mpa。
⑺装料罐中压力:0.4-0.6Mpa 。
⑻操作台上指示灯和CRT显示屏正常。
⑼所有仪表阀件的功能正常。
⑽计量系统初始位置正常,具体如下:△除尘阀、进料阀、出料阀、输料阀、加压阀、辅输阀关闭。
△通向喷枪的喷料阀关闭。
△转子给料器断电。
△喷吹罐供氮管路上的阀关闭。
⑾装料罐中有足够的颗粒镁。
7.3转装操作将颗粒镁的用量输入计量机,在显示屏上选择“自动送料”,颗粒镁自动从装料罐输入计量系统。
送料时氮气输送量(输料阀前流量表显示)为150-400Nm3/h,颗粒镁输送量约40kg/min。
7.4 转装进行顺序⑴喷吹罐除尘阀打开,释放压力,排出含尘氮气。
⑵喷吹罐进料阀打开。
⑶关闭装料罐除尘阀。
⑷打开装料罐加压阀。
⑸增加装料罐压力到0.4-0.6Mpa。
⑹打开装料罐输料阀。
⑺用装料罐流量调节阀调节流量使输料阀前流量表显示为150-400Nm3/h。
⑻打开出料阀,将颗粒镁从装料罐经送料管道输送入喷吹罐。
7.5转装完成顺序⑴关闭装料罐出料阀,停止从装料罐出料。
⑵关闭装料罐加压阀,停止向装料罐供氮。
⑶打开装料罐减压阀,排气,降低压力。
⑷当装料罐中压力达到0.05Mpa时,打开除尘阀。
⑸当装料罐中压力达到0时,关闭减压阀及除尘阀。
⑹出料阀关闭后延时30-60秒,关闭输料阀,停止输料管道供氮。
⑺关闭喷吹罐进料阀。
⑻喷吹罐压力达到0Mpa时,关闭管道除尘阀。
7.6除尘排灰7.6.1 除尘漏斗仓中的料达到上位时,控制台上有报警信号显示,此时应及时将除尘灰清除。
7.6.2 除尘排灰条件:系统未进行送料及喷吹操作。
7.6.3 除尘排灰步骤⑴主控台发出排灰指令。
⑵现场控制台选手动。
⑶先打开除尘器下手动闸板。
⑷卸灰完毕,关闭除尘器下手动闸板,将现场控制台选自动。
8. 铁水脱硫8.1 喷吹前条件确认⑴喷吹罐内压力为0Mpa,通向喷吹罐氮气管路压力≥0.8Mpa⑵阀门气源压力≥0.8Mpa⑶除尘灰料位面正常⑷铁水包车、脱硫间大门、二次除尘阀、水冷盖、喷枪已由主控台控制⑸扒渣机在原始位⑹喷吹罐内镁重>80kg⑺把持器打开⑻除尘、进料、出料、输料、加压、辅输、喷料、流量调节阀及氮气阀关闭⑼转子给料器电机未接通⑽无设备故障及紧急事故信号8.2 喷吹前准备8.2.1 铁水准备⑴记录铁水重量。
⑵将铁水包吊运到脱硫站,座在铁水包车上。
⑶打开脱硫站大门,开铁水包车到脱硫位,降防溅罩,关闭脱硫站大门。
8.2.2 测初始温度、取初始样。
⑴装好测温取样头。
⑵测温取样枪降到所需深度,停留5-6秒测出温度,将枪提出。
⑶取下取样头,拿出试样。
⑷试样编号后送化验室,记录好化验分析结果。
8.2.3 打开二次除尘阀,接通气体净化系统。
8.2.4 选择喷枪号“A”或“B”,使其对位,打开氮风阀吹氮到氮封。
8.2.5 计算颗粒镁耗量:将铁水目标硫,初始硫,铁水温度,铁水量,颗粒镁吸收率(95%)输入计算机后,按计算机指令,此时计算机自动计算所需颗粒镁量,并将结果自动设置到自动控制系统中去。
注:自动控制系统出现故障时,可在在附表中查出推荐的颗粒镁消耗量,并按下式折成颗粒镁实际耗量(kg):实际耗量=(颗粒镁单耗×铁水量)÷颗粒镁吸收率。
8.2.6 上述工作完成后,可选择工作方式:“自动”或“手动”。
选手动时应按程序逐步进行。
选自动时,则通过设置,控制系统接通到各自的位置。
只有系统再次设定到初始位置后,才能将工艺控制方式从手动切换到自动。
8.3 喷吹脱硫在脱硫主画面上,按“开始”命令,则按设定的程序自动进行。
具体如下:⑴打开供氮阀、辅输阀和加压阀供气到转子给料器和喷吹罐,使喷吹罐中的压力达到初始压力0.6Mpa。
⑵下降喷枪从“高位”到铁水“上方位置”,打开喷料阀。
⑶当喷吹罐中压力达到0.6Mpa以后,打开输料阀向混合器供气,打开出料阀预备向喷枪中供镁,通过调节阀使混合器前供氮流量达到120-160Nm3/h。
⑷喷枪插入到铁水中到达最低位置,用夹持器将喷枪固定。
⑸延时10秒后,加压阀供气到“上限压力”后关闭,开启旋转供料器电机,以4kg/min 的速度向喷枪供镁,通过控制调节阀达到程序所要求的混合器前供氮量。
⑹缓慢提高供料机的旋转速度,使之达到程序规定的供镁量(应调节校准)喷溅较严重时,通过“镁提供量”窗口,调节供镁量。
⑺当供镁量距设定值2-3kg时,转子给料器驱动装置减速,将供镁速度降低到4kg/min。
同时调整混合器前供氮流量到120-140Nm3/h。
当供镁量距设定值0.1kg时,转子给料器驱动装置切断。
⑻打开固定喷枪的夹紧装置,提升喷枪到“铁水上方”的位置。
⑼关闭输料阀、辅输阀、供氮阀,将流量调节阀调到0%。
⑽喷吹罐内压力降到0.05-0.01Mpa时,关闭辅输阀、喷料阀及包盖供氮阀。
⑾打开除尘阀、使计量系统中被污染的气体排放到收集系统,卸压,当喷吹罐中的压力降至零时马上关闭除尘阀,喷枪上升到最高位置。
⑿脱硫结束进行测温取样,试样编号后送化验室,记录化验室通报的分析结果。
⒀测温取样完毕后按“扒渣”按钮,把铁水包车控制权移交给扒渣机控制台。
⒁如铁水含硫量未达到目标要求,应重新进行喷吹操作。
⒂将铁水最终含硫量、温度输入计算机,并将铁水全成分报炼钢主控室。
9. 铁水扒渣9.1扒渣控制台接到允许扒渣信号后,将控制方式切换为现场模式,接通扒渣和倾动铁水包的控制。
9.2将铁水包倾动一定的角度,移动扒渣机将渣子扒到渣罐中。