轴承钢点状夹杂物成因及消除机理的探讨
钢中大颗粒夹杂物的产生及防止

1 主要设备兴澄钢铁公司滨江厂区采用全线从国外引进的100t超高功率电弧炉+LF(VD)+CCM(300mm×340mm)大方坯连铸工艺,电弧炉与连铸机的主要技术参数见表1,表2,表3。
非金属夹杂物对钢来说,是极其重要的质量指标。
降低大颗粒夹杂的生成,使钢中非金属夹杂物含量将低,从而提高了钢材的纯洁度。
因此,控制钢水中非金属夹杂物已经成为炼钢厂重点关注的问题。
2 钢包吹氩时氩气泡对夹杂物的浮选作用钢包吹氩条件下钢中固相夹杂物的去除主要依靠小气泡的浮选作用,即夹杂物与小气泡碰撞并粘附在气泡壁上,然后随着气泡上浮而去除。
对钢包吹氩去除夹杂物决定于吹入钢液中的气泡数量和气泡的尺寸,气泡尺寸越小,夹杂物被气泡俘获的概率越大,吹入钢液的气泡数量越多,去除夹杂物的数量就越多[1]。
3 钢包处理过程中钢包包龄对非金属夹杂物形成的影响钢包处理过程中钢包釉面层对形成非金属夹杂物的影响,在钢包处理工艺的各个环节以及从不同包龄的钢包中都取了钢样,在显微镜下对夹杂物的数量进行了统计,发现在钢水脱氧之前以及在钢包处理的末期,夹杂物的数量随着钢包包龄的增加而增加,在钢包使用超过一定炉次后,夹杂物的增加更为显著。
钢样中全氧含量与溶解氧含量之间存在的差异也进一步证明了这个结果。
在浇铸之前钢水中有两种类型的夹杂物,一种只包含成分接近于3C a O·A 1O 的氧化物溶体;另一种除包含该氧化物溶体之外还包含M g O 相。
该发现与另一项研究的结果相吻合,即在钢包釉面层的钢渣渗透层中同时存在3CaO ·A1O和Mg O。
得出的结论是,在钢包处理过程中,钢包釉面层是钢中非金属夹杂物的最重要来源。
4 连铸大方坯夹杂分析连铸坯中存在的非金属夹杂物是一种普遍现象,其来源有外来和内生夹杂两类,研究表明连铸坯中夹杂主要来源于外部,包括生产过程的各种渣,与高温熔体接触的耐火材料及钢液与空气接触的二次氧化产物。
此外,还受许多操作因素的影响。
钢中夹杂物的产生与去除途径

钢中夹杂物的产生与去除途径钢中夹杂物的产生与去除途径李振旭钢中夹杂物对钢质量的影响越来越受到重视,怎样减少钢中夹杂物对钢材性能的影响,各大院校、钢铁研究机构有很多研究成果及文献。
生产清洁钢有很多措施与手段,在此不作详细介绍,我想就电弧炉单设备冶炼,结合很多的文献作一下具体分析与验证。
钢中夹杂物的来源无非有两大类:一、外来夹杂。
二、内生夹杂。
外来夹杂是由原材料、炉渣、耐火材料等引起的。
如炼钢的废钢带入的泥沙、铅锌砷锑鉍等,出钢时钢液混渣,炉衬、出钢槽、盛钢桶等耐火材料的侵蚀、冲刷剥离等造成的。
内生的夹杂物是由脱氧产物、析出气体的反应产物构成的。
一般脱氧产物称为一次夹杂。
二次夹杂为钢液从浇注温度下降到液相线,由于温度下降气体的溶解度下降析出而产生的夹杂物。
三次夹杂是金属在固相线下由于结晶而产生的。
四次夹杂是结晶完成后到常温过程中由于发生组织转变而产生的。
由此可以看出钢中的夹杂物大部分是一次夹杂和二次夹杂。
外来夹杂通过现场管理及使用优质耐火材料是可以控制或减少的,三、四次夹杂是无法消除的,故此不做讨论。
重点讨论一二次夹杂的产生与去除。
钢在熔炼的过程中为了去除由原料带入的杂质及有害元素,往往采取氧化法冶炼。
利用碳氧沸腾来增加熔池的动能,通过一氧化碳的排出将熔于钢液中的气体及夹杂物去除,氧化以后钢液得到净化。
但当氧化结束以后,钢液中存在较多的溶解氧及氧化铁,这种钢液在浇注时会因气体含量高而引起冒涨而导致无法使用,那么就要对钢液进行脱氧操作。
目前脱氧主要有沉淀脱氧、扩散脱氧及两种方法结合的综合脱氧法。
硅铁、锰铁是目前最常用的脱氧剂,其他的有铝、硅铝铁、硅锰合金、硅钙合金、硅钙钡、硅铝钡、硅镁、镍镁合金混合稀土等等。
用于扩散脱氧的有碳粉、硅铁粉、硅钙粉、铝粉、碳化硅粉等。
作为沉淀脱氧剂的硅铁、锰铁等直接加入钢液,它的脱氧产物是SIO2和MnO,MnS等,用铝作为终脱氧剂脱氧其产物是AI2O3,其中一部分会上浮排除,当然还会有部分存在于钢液中,造成氧化物夹杂。
轴承钢夹杂物控制及成因分析

•搅拌时间与夹杂物数目及粒度分布
0.06
钢中夹杂物控制
夹 杂 物 数 目 ( mm 2 )
0.05 0.04 0.03 0.02 0.01 0 2.8-5.6 5.6-11.2 11.222.4 >22.4 长搅拌时间 短搅拌时间
夹杂物粒度( μ m)
图12
气体搅拌时间与夹杂物 数量及粒度分布的影响
[Ti]含量控制
出钢过程下渣量中Ti的还原: 出钢过程主要加入Al、C、Si、Mn、Cr。
[Ti]含量控制
在出钢温度下,只有 Al能还原渣中的Ti。 即出钢过程如果用 Al脱氧,则下渣中 的(TiO2) 能被Al 还原进入钢液。
图1 氧化物标准生成自由能随温度的变化
[Ti]含量控制
LF精炼过程(TiO2) 的还原 铝还原(TiO2)的反应: 4[Al]+3(TiO2)=3[Ti]+2(Al2O3) (2) 在1800oC高温下,碳还原TiO2的反应: (TiO2)+[C]=(TiO)+CO (3) (TiO2)+[C]=[TiC]+CO (4) 在>1850oC高温下,碳还原TiO2的反应: 2[C]+(TiO2)=[Ti]+2CO (5) 上述反应表明:如果在低温下,能先除去初炼炉的下渣 量,再用Al、C进行脱氧还原,就能减少(TiO2) 的 还原。
钢中夹杂物控制
浇注工艺参数控制 提高浇注系统用耐火材料的质量档次, 提高中包抗侵蚀、抗冲刷的能力,减少 外来夹杂物。 严格按工艺要求砌筑浇注系统,保证浇 注系统清洁、充分烘烤、干燥并保持至 浇注。
钢中夹杂物控制
浇注工艺参数控制 采用氩封保护浇注,防止二次氧化形成 大颗粒族状Al2O3夹杂物。
轴承钢点状夹杂物成因及消除机理的探讨
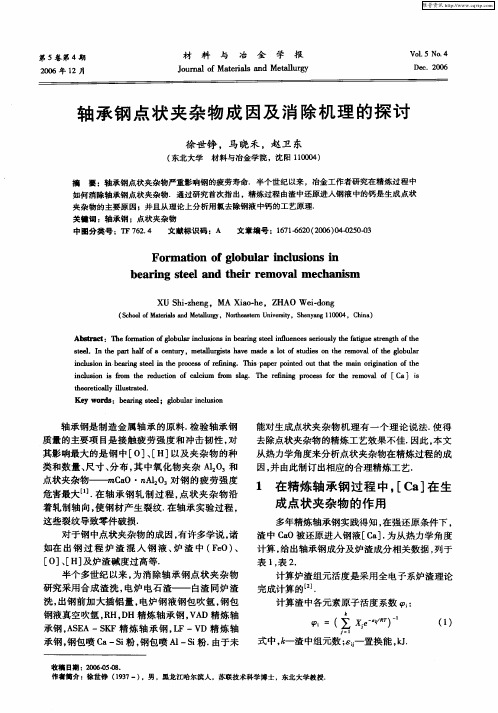
[ ][ ] O 、 H 及炉渣碱度过高等. 半个 多世 纪 以来 , 消 除轴 承 钢 点状 夹杂 物 为 研究采用合成渣洗 , 电炉电石渣—— 白渣同炉渣 洗, 出钢前 加 大 插 铝量 , 电炉 钢 液 钢包 吹 氩 , 钢包 钢 液真 空吹 氩 ,H, H 精炼 轴 承 钢 , A R D V D精 炼 轴 承 钢 ,S A—S F精 炼 轴 承 钢 ,F—V AE K L D精 炼 轴 承钢 , 钢包 喷 C a—s 粉 , i 钢包 喷 —s粉 . i 由于未
维普资讯
第 5卷 第 4期
2O O 6年 1 2月
材
料
与 冶 金
ห้องสมุดไป่ตู้
学
报
V L 5 No 4 o . De .2 0 c 06
J un l fMaeil n tl ry o ra trasa d Meal g o u
轴 承 钢 点 状 夹 杂 物 成 因及 消 除 机 理 的 探 讨
ic s n i f m h e ut n o M i f m l .T e r nn rcs frtermo ̄ o C ]i nl i s r te r c o fc c m r s g h e i poes o uo o d i u o a i f g h e v f[ a s
能对生 成点 状夹 杂 物 机 理 有 一个 理 论 说 法 . 得 使 去除点 状夹 杂物 的精 炼工 艺效 果不 佳 . 因此 。 本文 从热 力学角 度来 分析 点状 夹杂 物在 精炼 过 程 的成 因 , 由此 制订 出相 应 的合理 精炼 工艺 . 并
其影响最大的是钢 中[ ] [ 以及夹杂物的种 0 、 H] 类和数量 、 尺寸 、 分布, 中氧化物夹杂 A , 其 1 和 0 点 状夹 杂物— — , a ・ A , 钢 的 疲 劳 强 度 , O nl 对 I C 0 危害最大…. 在轴承钢轧制过 程 , 点状夹杂 物沿 着轧制轴 向, 使钢材产生裂纹. 在轴承实验过程 。 这些 裂纹 导致零 件破 损 . 对于 钢 中点状 夹杂 物 的成 因 , 许 多学说 , 有 诸
GCr15轴承钢夹杂物缺陷分析及改进
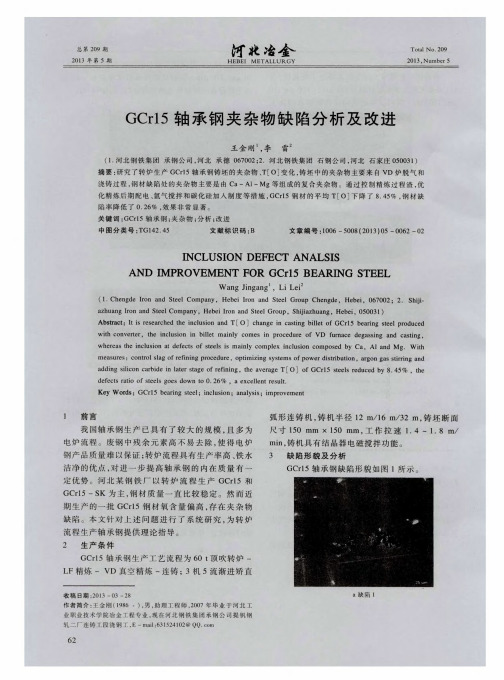
4 改 进 措 施
( 1 ) 加强 L F精炼过 程渣 控制 , 优 化精 炼后 期 配
在 工艺 优化前 后 分 别选 取 了多炉 钢 , 检 测 钢 材 中 的 T[ O] 。工艺优 化后 , 钢 材 中的平均 T[ 0] 下 降 了8 . 4 5 %, 由7 . 7 0×1 0 下降至 6 . 5×1 0~, 效 果
氩气 搅拌 和碳化 硅 加 入制 度 , 适 当 延 长 精 炼 终 点 小
( 4 ) 使用碱性低钛覆盖剂, 加 强 保 护 浇 铸 。及
电流时 间 , G C r l 5钢 材 的平 均 T [ 0] 下降了 8 . 4 5 %,
表 1 全 外矿 烧 结 的烧 结 矿 成 分 及 强 度 对 比
T a b .1 Co n t r a s t o f c o mp o s i t i o n a n d s  ̄e n g t h o f s i n t e r
由表 1 可 以看 出 : 石钢 2 8 0 m 烧 结 机 全 外 矿 烧 结 生产过 程 中 , 通 过采 取 多 项 措 施 , 烧结矿 中 F e O
显著 。
5 . 2 钢 材 的缺 陷 率 比较
电、 氩气搅 拌 和碳化 硅加入制 度 , 避免 V D 炉顶 渣 返
干; 适 当延 长精 炼终 点小 电流时 间 , 氩气 流量 中等 偏
低 控制 , 要 求精 炼终 点渣为玻 璃渣 且无 分层现 象 。 ( 2 ) 适 当控 制 钢 液 中的 铝 含 量 , 建议座包钢 中
A l s o l < 5 0 0×1 0 ~。加强 钢液 中的钙含 量控 制 , 禁 止 钙 处理 , 中包钙 含量 小于 1 0×1 0 ~。使用 含 ( Mg O) 较高( 6 % ~ 8 %) 的精炼 渣 系和高 质量 的耐火材 料 。
高级别轴承钢精炼过程中夹杂物的控制与研究

高级别轴承钢精炼过程中夹杂物的控制与研究摘要:为提升高级别轴承钢的精炼质量,延长轴承使用寿命,对钢精炼过程中的夹杂物进行控制与研究十分必要。
本文从高级别轴承钢和夹杂物的概念着手,全面分析了当前轴承钢精炼过程中夹杂物存在的情况,并对高级别轴承钢精炼过程中夹杂物的控制措施展开了详细阐述,以期为我国钢铁产业的发展做出一定贡献。
关键词:高级别轴承钢;精炼过程;夹杂物;控制与研究炉渣对钢水洁净度的影响很大,它的主要功能是:加强脱氧元素的吸附能力,避免钢水二次氧化。
在钢液的精炼过程中,熔渣内的多种物质对钢中的夹杂物具有很大的吸附和清除作用,因此有关部门利用轨钢LF精炼的废渣,对夹杂物的形态和分布的影响因素进行分析,并制定出一套完整的、高质量的钢精炼技术体系。
1.高级轴承钢及其夹杂物概述高级轴承钢在我国的工业生产和船舶制造等领域中得到了广泛应用。
由于其工作环境的特殊性和复杂性,相关行业对其质量的要求越来越高。
目前,国内常用的轴承钢包括高碳铬轴承钢、高温轴承钢、不锈轴承钢、渗碳轴承钢等,其应用范围因组织结构、成分、结构性能等性质而异[1]。
其中,高碳轴承钢是目前国内应用最广泛的一种。
1.轴承钢冶炼过程中的夹杂物控制问题2.1 钢液洁净度不足一般情况下,钢的含氧量不应超过10×10-4%,夹杂物的粒径也应小于15微米。
对于高品质产品,对氧含量和夹杂物的尺寸也有着更高的要求。
但实际生产中,这些要求难以满足钢铁冶炼的需要,导致钢液的清洁程度不足。
由于钢液中含有大量杂质,夹杂物的尺寸变大,从而降低了钢的整体质量。
2.2 精炼工艺有待改进国内轴承钢的质量问题主要是由于冶炼过程中存在大量的铝氧化物,如三氧化二铝和其他氧化物。
这些铝氧化物在精炼过程中没有及时上浮,导致轴承钢的组织均匀度下降,影响钢的整体质量。
在钢铁冶炼工艺和设备方面,受技术限制,国内轴承钢冶炼工艺与世界先进水平存在较大差距。
2.3 钢坯质量在线检测手段滞后钢坯的质量是制造优质钢材的重要前提。
前人对钢包内夹杂物的演变及去除机理

前人对钢包内夹杂物的演变及去除机理下载提示:该文档是本店铺精心编制而成的,希望大家下载后,能够帮助大家解决实际问题。
文档下载后可定制修改,请根据实际需要进行调整和使用,谢谢!本店铺为大家提供各种类型的实用资料,如教育随笔、日记赏析、句子摘抄、古诗大全、经典美文、话题作文、工作总结、词语解析、文案摘录、其他资料等等,想了解不同资料格式和写法,敬请关注!Download tips: This document is carefully compiled by this editor. I hope that after you download it, it can help you solve practical problems. The document can be customized and modified after downloading, please adjust and use it according to actual needs, thank you! In addition, this shop provides you with various types of practical materials, such as educational essays, diary appreciation, sentence excerpts, ancient poems, classic articles, topic composition, work summary, word parsing, copy excerpts, other materials and so on, want to know different data formats and writing methods, please pay attention!前人对钢包内夹杂物的演变及去除机理钢包内夹杂物的问题一直是钢铁冶炼过程中关注的重要方面。
减除轴承钢点状夹杂的新工艺

、
可
靠的 方 法
。
(余
力)
搜,
瓦二竺巴
带 氧化 渣 出钢
出钢 时加 硅铁合 金 化
。 、
1 钢包 吹 氢 两种方案都 在 出 钢 时 用铝 (
。
。
检 验 了 两 种方 案冶 炼 时 最终炉 渣 的 成 分
.
现行工 艺 的 渣 含 e F
.
6 4
55
、
.
93 C 0
2
.
a
、
4 3 、1 2 o
: ,
.
.
2 1 4 ~ 2 6 2 5 10 3 6 3 4~ 40 6 4C C
步 研究 夹 杂 物 的 成 因 和 减 除 方法 采 用 两 种 冶 炼 方案
,
在4 0
t电
一 种 方案 为 现 行 工 艺
,
采 用炉 渣 扩 散 脱 氧
,
,
钢 在 炉 中合 金 化
3 9 7。 ~
F
. .
,
另 一 方案 为在 炉
kg l )t 3 A 碑O :
、
中钢 和 渣 不 脱 氧
终脱氧
.
,
。
而 且成 分 为铝 镁 尖 晶 石 和 铝酸钙
,
从 夹杂物成分 和 出现 的时 间说明它 是
。
此 外夹杂 还 被 硫 化物 包 覆 冶炼 工 艺
说明 夹杂 是 早先 生 成 的
。
下 表 是 两 种方 案 成 品 材夹杂物 评 级 结 果
轧材 直径
炉数
平 硫化物
1 1 l 2
。
均
级
别
氧化物
1
1 1 1
轴承钢夹杂物控制技术研究
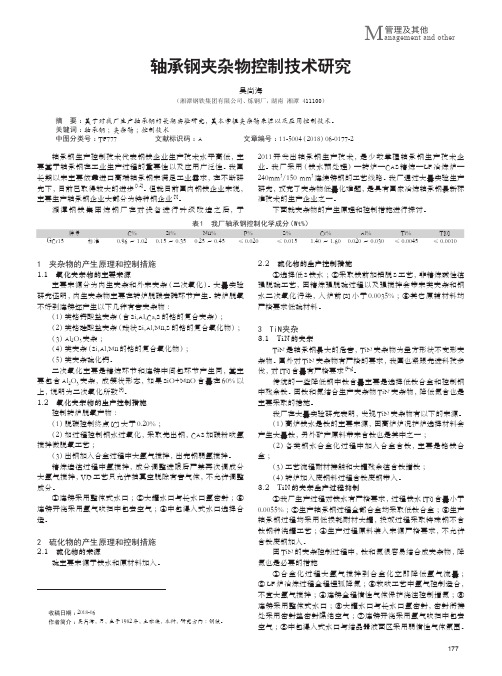
管理及其他M anagement and other 轴承钢夹杂物控制技术研究吴尚海(湘潭钢铁集团有限公司、炼钢厂,湖南 湘潭 411100)摘 要:基于对我厂生产轴承钢的长期实验研究,基本掌握夹杂物来源以及应用控制技术。
关键词:轴承钢;夹杂物;控制技术中图分类号:TF777 文献标识码:A 文章编号:11-5004(2018)06-0177-2轴承钢生产控制技术代表钢铁企业生产技术水平高低,主要基于轴承钢在工业生产过程的重要性以及应用广泛性。
我国长期以来主要依靠进口高端轴承钢来满足工业需求,在不断研究下,目前已取得较大的进步[1,2]。
但就目前国内钢铁企业来说,主要生产轴承钢企业大部分为特种钢企业[3]。
湘潭钢铁集团炼钢厂在对设备进行升级改造之后,于2011开发出轴承钢生产技术,是少数掌握轴承钢生产技术企业。
我厂采用(铁水预处理)—转炉—CAS精炼—LF冶炼炉—240mm3/150 mm3连续铸钢的工艺线路。
我厂通过大量实验生产研究,攻克了夹杂物低量化难题,是具有国家冶炼轴承钢最新标准技术的生产企业之一。
下面就夹杂物的产生原理和控制措施进行探讨。
表1 我厂轴承钢控制化学成分(Wt%)牌号C%Si%Mn%P%S%Cr%Al%Ti%T[0] GCr15标准0.96~1.020.15~0.350.25~0.45≤0.020≤0.015 1.40~1.600.020~0.030≤0.0045≤0.00101夹杂物的产生原理和控制措施1.1 氧化夹杂物的主要来源主要来源分为内生夹杂和外来夹杂(二次氧化)。
大量实验研究证明,内生夹杂物主要在转炉脱碳去磷环节产生。
转炉脱氧不好到连铸坯产生以下几种有害夹杂物:(1)类铬钙酸盐夹杂(含Si,Al,Ca,S的铬的复合夹杂);(2)类铬硅酸盐夹杂(球状Si,Al,Mn,S的铬的复合氧化物);(3)Al2O3夹杂;(4)类夹杂(Si,Al,Mn的铬的复合氧化物);(5)类夹杂硫化钙。
轴承钢中TiN夹杂的形成机理及控制措施
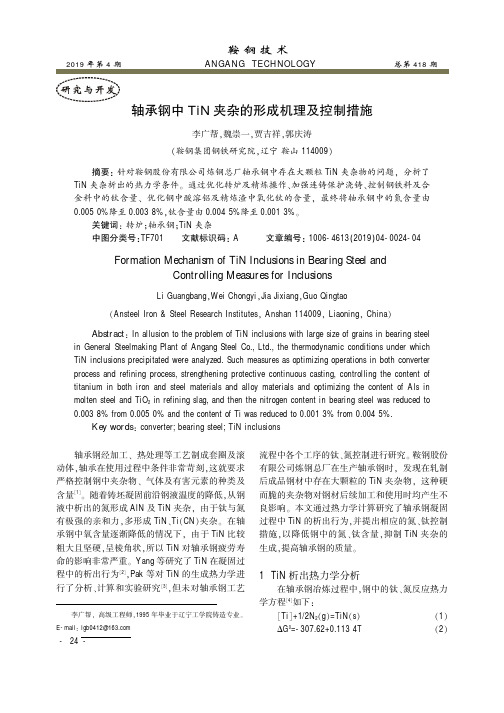
轴承钢经加工尧 热处理等工艺制成套圈及滚 动体袁轴承在使用过程中条件非常苛刻袁这就要求 严格控制钢中夹杂物尧 气体及有害元素的种类及 含量咱1暂遥 随着铸坯凝固前沿钢液温度的降低袁从钢 液中析出的氮形成 AlN 及 TiN 夹杂袁 由于钛与氮 有极强的亲和力袁多形成 TiN尧Ti渊CN冤夹杂遥 在轴 承钢中氧含量逐渐降低的情况下袁 由于 TiN 比较 粗大且坚硬袁呈棱角状袁所以 TiN 对轴承钢疲劳寿 命的影响非常严重遥 Yang 等研究了 TiN 在凝固过 程中的析出行为咱2暂袁Pak 等对 TiN 的生成热力学进 行了分析尧计算和实验研究咱3暂袁但未对轴承钢工艺
066.2 T
+4.773
1 TiN 析出热力学分析
在轴承钢冶炼过程中袁钢中的钛尧氮反应热力
学方程咱4暂如下院
咱Ti暂+1/2N2渊g冤=TiN渊s冤
渊1冤
驻G0=-307.62+0.113 4T
渊2冤
2019 年第 4 期
鞍钢技术
ANGANG TECHNOLOGY
总第 418 期
式 中 袁驻G0 为 标 准 自 由 能 袁kJ/mol曰 T 为 标 准 温
表 1 钢液中不同元素的相互作用系数渊1 873 K冤
元素 i C
元素 j
Si
Mn
P
S
Cr
Ti
-0.11 0.055
N
0.13 0.047 -0.02 0.045 0.007 -0.047
根据轴承钢的化学成分袁可以得到院
lg fTi =0.082袁lg fN=0.065,整理得院
轴承钢D类夹杂物来源分析及控制

高质量轴承钢提供必要 的理论依据 。 关键词 : 轴承钢 ; 夹杂物 ; 来 源
Re s e a r c h o n S o ur c e o f Ty pe D a n d Ds I nc l u s i o n s i n Be a r i ng s t e e l
f o r o p t i mi z i n g t h e p r o c e s s a n d s me l t i n g h i g h q u li a t y b e a r i n g s t e e 1 . Ke y Wo r d s : b e a r i n g s t e e l ;i n c l u s i o n;s o u r c e
f e a t u r e, me a n d i a me t e r , a mo u n t o f i n c l u s i o n s we r e a n a l y z e d,whi c h p r o v i d e s n e c e s s a r y t h e o r e t i c a l b a s i s
物、 带状碳化物及网状碳化物等 ) I 4 的不均匀性
都 有严 格要 求 。
轴承钢中 D类 D 类夹杂物是不变形夹杂物, 对轴承钢的疲 劳寿命极 为有害 , 在实 际生产 中应 采取手段控制该类夹杂物的产 生。目前某特钢采
用 转 炉一 L F —V D 一 软 吹一 C C流程 生 产轴 承钢 , 但 是存 在 D类 I ) s 类夹 杂 物 超标 的现 象 , 为 此 对其 轴 承钢 G C r l 5的生产 采用 夹杂 物 示踪 和系 统 取样
轴承钢的工作条件极为复杂 , 承受 着各种高 的交变应力 , 如拉力 、 压力 、 剪力和摩擦力等 , 为保
轴承钢点状夹杂物成因及消除机理的探讨

轴承钢点状夹杂物成因及消除机理的探讨
1 夹杂物成因
轴承钢点状夹杂物是指在轴承精锻件表面上存在的散落的一些硬
性物质,一般为硬质磨料、金属颗粒、研磨颗粒、合金残留物等。
一
般情况下,它们是在制造过程中被其他金属粒子进入轴承精锻件表面,或是由于轴承精锻的原料的杂质性导致的,也有可能是安装使得夹杂
物进入密封下的。
2 消除机理
夹杂物消除的主要方式有采用抛光、热处理、氣力清理和物理化
学处理等方式。
抛光是最常用的夹杂物消除方式,这种方法是采用彼此间准备磨
料把夹杂物磨掉,对夹杂物消除效果较好。
热处理是把轴承精锻件放入高温下,使夹杂物在高温下熔化,然
后把夹杂物去掉,这个方法使轴承精锻件得到跳漆和表面变深,达到
清理夹杂物的效果。
气力清理是采用压缩空气加水分子粒子以及其它微小纳米粒子对
轴承夹杂物进行清理,这种方法可以去除较大的硬质磨料以及漆料等
物质,效果也很明显。
物理化学处理是一种新型的夹杂物消除技术,它采用特制的药液,可以彻底清除夹杂物,物理化学处理不仅能够有效移除夹杂物,而且
还能够在表面形成一层防护膜,从而保护表面,使轴承更加耐久。
4 结论
轴承的精锻件表面点状夹杂物的形成很重要,主要是由于精锻原
料的杂质性、制造过程中的夹杂物进入等原因导致,也可能还有安装
的原因。
为了解决点状夹杂物的问题,还可以采用抛光、热处理、气
力清理以及物理化学处理等技术来清除夹杂物,达到良好的消除效果。
模铸轴承钢线材中心黑点产生机理及对策

模铸轴承钢线材中心黑点产生机理及对策
铸轴承钢线材中心黑点的产生一般主要是溶解气体中存在的有机物、矿物和有害尘埃等原因造成的,另外由于模具温度不正确以及模具材质不合适也可能导致产品中存在少量的残留物,而这些残留物在铸件冷却的过程中,施加了较强的压力,形成了黑点现象。
具体对策,在产品宜采用模具锻造,对温度、凝固度等应充分把握;同时应加强模具打磨,减少残留物的产生;而且在模具中适当放入抗氧化剂或者抗腐蚀剂等用以预防有害尘埃的侵入,从而达到减少铸件中黑点现象的目的。
轴承钢中TiN夹杂的形成机理及控制措施
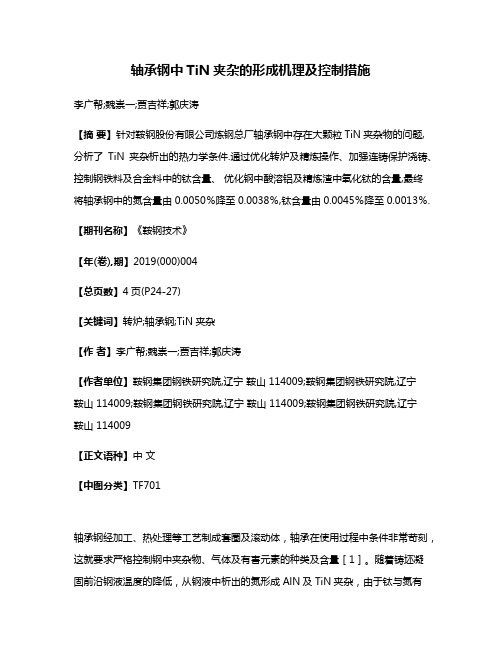
轴承钢中TiN夹杂的形成机理及控制措施李广帮;魏崇一;贾吉祥;郭庆涛【摘要】针对鞍钢股份有限公司炼钢总厂轴承钢中存在大颗粒TiN夹杂物的问题,分析了TiN夹杂析出的热力学条件.通过优化转炉及精炼操作、加强连铸保护浇铸、控制钢铁料及合金料中的钛含量、优化钢中酸溶铝及精炼渣中氧化钛的含量,最终将轴承钢中的氮含量由0.0050%降至0.0038%,钛含量由0.0045%降至0.0013%.【期刊名称】《鞍钢技术》【年(卷),期】2019(000)004【总页数】4页(P24-27)【关键词】转炉;轴承钢;TiN夹杂【作者】李广帮;魏崇一;贾吉祥;郭庆涛【作者单位】鞍钢集团钢铁研究院,辽宁鞍山 114009;鞍钢集团钢铁研究院,辽宁鞍山 114009;鞍钢集团钢铁研究院,辽宁鞍山 114009;鞍钢集团钢铁研究院,辽宁鞍山 114009【正文语种】中文【中图分类】TF701轴承钢经加工、热处理等工艺制成套圈及滚动体,轴承在使用过程中条件非常苛刻,这就要求严格控制钢中夹杂物、气体及有害元素的种类及含量[1]。
随着铸坯凝固前沿钢液温度的降低,从钢液中析出的氮形成AlN及TiN夹杂,由于钛与氮有极强的亲和力,多形成TiN、Ti(CN)夹杂。
在轴承钢中氧含量逐渐降低的情况下,由于TiN比较粗大且坚硬,呈棱角状,所以TiN对轴承钢疲劳寿命的影响非常严重。
Yang等研究了TiN在凝固过程中的析出行为[2],Pak等对TiN的生成热力学进行了分析、计算和实验研究[3],但未对轴承钢工艺流程中各个工序的钛、氮控制进行研究。
鞍钢股份有限公司炼钢总厂在生产轴承钢时,发现在轧制后成品钢材中存在大颗粒的TiN夹杂物,这种硬而脆的夹杂物对钢材后续加工和使用时均产生不良影响。
本文通过热力学计算研究了轴承钢凝固过程中TiN的析出行为,并提出相应的氮、钛控制措施,以降低钢中的氮、钛含量,抑制TiN夹杂的生成,提高轴承钢的质量。
1 TiN析出热力学分析在轴承钢冶炼过程中,钢中的钛、氮反应热力学方程[4]如下:式中,ΔG0为标准自由能,kJ/mol;T为标准温度,K。
轴承钢中钙铝酸盐夹杂物的形成及控制

渣中各成分中, CaF2 对夹杂物的形成作用也比 较大. 无论在铝含量高或者低的时候, 加入 CaF 2 都 生成 了 许多 MgO #Al2O3 夹 杂; 这 有 可 能是 CaF2 能侵蚀炉 衬, 使 M gO 入 钢 液 中, 从 而 有 利 于 M gO#A l2O3夹杂的生成, 如图 7 所示.
图 5 低 Al 钢中 Al 2O3 夹杂 Fig. 5 Al2O3 incl usi ons in low-Al steel
图 7 加 CaF2 钢中 MgO#Al2O3 夹杂 Fig. 7 MgO#Al2O3 incl usions in steel with CaF2
渣中 M gO 成分对钢中 M gO#A l2O 3 夹杂的生成 影响比较小. 在渣系中 MgO 含量最高的钢中, 由于 酸溶 A l 不高, 其中没有发现 MgO#Al2O3 和 MgO 夹 杂; 而在渣中 M gO 含量并不高的钢中, 由于酸溶 Al 比较高, 能发 现很 多的 Mg O #A l2O 3 和 MgO 夹杂 生成. 21213 [ Ca] 含量的影响
GCr15轴承钢中TiN复合夹杂物形成机理

GCr15轴承钢中TiN复合夹杂物形成机理田钱仁;马骞;尚德礼;雷洪;王国承【期刊名称】《辽宁科技大学学报》【年(卷),期】2018(041)003【摘要】在GCr15轴承钢扫描电镜观察中发现有两类复合TiN夹杂物,分别为:TiN-MnS和TiN-MgO-MgAl2O4-MnS.热力学计算表明,GCr15轴承钢中TiN 夹杂物在固液两相区析出,MnS在固相区析出,Mg元素部分来源于炉衬中MgO被钢液中溶解的碳侵蚀还原,[Mg]与[O]将已经形核的Al2O3改质为MgAl2O4.TiN-MgO-MgAl2O4-MnS的析出顺序依次为:MgAl2O4、MgO、TiN、MnS.MgO 可作为TiN的形核质点;MgAl2O4若作为MgO、TiN、MnS的形核质点,取决于其周围元素的类型以及析出温度.【总页数】7页(P173-179)【作者】田钱仁;马骞;尚德礼;雷洪;王国承【作者单位】辽宁科技大学材料与冶金学院,辽宁鞍山 114051;辽宁科技大学材料与冶金学院,辽宁鞍山 114051;鞍钢海洋装备用金属材料及其应用国家重点实验室,辽宁鞍山 114021;东北大学材料电磁过程研究教育部重点实验室,辽宁沈阳110004;辽宁科技大学材料与冶金学院,辽宁鞍山 114051;辽宁科技大学辽宁省化学冶金工程重点实验室,辽宁鞍山 114051【正文语种】中文【中图分类】TF769.2【相关文献】1.钢包软吹氩时间对GCr15轴承钢中夹杂物的影响 [J], 杨锋功;杨华峰;战东平;杨永坤;张慧书2.高碳抗疲劳应力钢TiN夹杂物形成机理及控制研究 [J], 金友林;杨丽珠;3.GCr15轴承钢中MnS-Al2O3复合夹杂物析出行为 [J], 赵洋;王国承;曹磊;田钱仁4.IF钢凝固过程中Al_2O_3-TiN复合夹杂物的形成机理 [J], 李志强;袁磊;刘涛;于景坤5.PMO对GCr15轴承钢连铸坯中MnS夹杂物的影响 [J], 朱雷敏;李莉娟;罗坤坤;李涛;翟启杰因版权原因,仅展示原文概要,查看原文内容请购买。
- 1、下载文档前请自行甄别文档内容的完整性,平台不提供额外的编辑、内容补充、找答案等附加服务。
- 2、"仅部分预览"的文档,不可在线预览部分如存在完整性等问题,可反馈申请退款(可完整预览的文档不适用该条件!)。
- 3、如文档侵犯您的权益,请联系客服反馈,我们会尽快为您处理(人工客服工作时间:9:00-18:30)。
第5卷第4期材 料 与 冶 金 学 报V ol 15N o 14 收稿日期:2006-05-08.作者简介:徐世铮(1937-),男,黑龙江哈尔滨人,苏联技术科学博士,东北大学教授.2006年12月Jour nal ofM ateria ls andM eta ll u rgyD ec .2006轴承钢点状夹杂物成因及消除机理的探讨徐世铮,马晓禾,赵卫东(东北大学 材料与冶金学院,沈阳110004)摘 要:轴承钢点状夹杂物严重影响钢的疲劳寿命.半个世纪以来,冶金工作者研究在精炼过程中如何消除轴承钢点状夹杂物.通过研究首次指出,精炼过程由渣中还原进入钢液中的钙是生成点状夹杂物的主要原因;并且从理论上分析用氯去除钢液中钙的工艺原理.关键词:轴承钢;点状夹杂物中图分类号:TF 76214 文献标识码:A 文章编号:1671-6620(2006)04-0250-03For mati on of globul ar incl usions i nbearing steel and their re m oval m echanis mXU Sh-i zheng ,MA X iao -he ,Z HAO W e-i dong(School ofM ateri als and M etall u rgy ,Northeastern Un ivers i ty ,Sh enyang 110004,Ch i n a)Ab stract :The for m ation of g l obu l ar i ncl usions i n bear i ng stee l i nfl uences seriously the fa tigue strength o f t he stee.l In t he pa rt ha lf o f a cen t ury ,m etall urg ists have m ade a l ot of st udies on the re m oval o f the globu l ar i nclusi on i n bear i ng stee l i n the process of refi n i ng .T his paper po i nted out t hat the m ain or i g i nati on o f t he i nclusi on i s fro m the reducti on of ca l c i u m from slag.The re fi ning process f o r the remova l o f [C a]is theo re ti ca lly ill ustra ted .K ey w ords :beari ng stee;l g l obu lar i ncl usion轴承钢是制造金属轴承的原料.检验轴承钢质量的主要项目是接触疲劳强度和冲击韧性,对其影响最大的是钢中[O ]、[H ]以及夹杂物的种类和数量、尺寸、分布,其中氧化物夹杂A l 2O 3和点状夹杂物)))m Ca O #n A l 2O 3对钢的疲劳强度危害最大[1].在轴承钢轧制过程,点状夹杂物沿着轧制轴向,使钢材产生裂纹.在轴承实验过程,这些裂纹导致零件破损.对于钢中点状夹杂物的成因,有许多学说,诸如在出钢过程炉渣混入钢液、炉渣中(Fe O )、[O]、[H ]及炉渣碱度过高等.半个多世纪以来,为消除轴承钢点状夹杂物研究采用合成渣洗,电炉电石渣)))白渣同炉渣洗,出钢前加大插铝量,电炉钢液钢包吹氩,钢包钢液真空吹氩,RH,DH 精炼轴承钢,VAD 精炼轴承钢,ASEA -SKF 精炼轴承钢,LF-VD 精炼轴承钢,钢包喷Ca-S i 粉,钢包喷A l-S i 粉.由于未能对生成点状夹杂物机理有一个理论说法.使得去除点状夹杂物的精炼工艺效果不佳.因此,本文从热力学角度来分析点状夹杂物在精炼过程的成因,并由此制订出相应的合理精炼工艺.1 在精炼轴承钢过程中,[Ca]在生成点状夹杂物的作用多年精炼轴承钢实践得知,在强还原条件下,渣中Ca O 被还原进入钢液[Ca].为从热力学角度计算,给出轴承钢成分及炉渣成分相关数据,列于表1,表2.计算炉渣组元活度是采用全电子系炉渣理论完成计算的[2].计算渣中各元素原子活度系数U i :U i =Ekj=1X j e-E ij/RT-1(1)式中,k )渣中组元数;E ij )置换能,kJ.计算出:U(A l)=21331;U(Ca)=21410.[A l]+3/4O2y(A l O115)l g K p=37790/T-81457K p1873=51025#1011k A l=X(A l)#U(A l)/A[A l]#p M A l/4O2(2) p3/4O2=X(A l)U(A l)/A[A l]#k A l=11044#10-11p O2=2128#10-10Pa,[O]=0100012%[C a]+1/2O2y(C a O)k(Ca)=X(Ca)#U(C a)/A[C a]#p M(Ca)/4O2(3)l g K p=37197/T-712K1873=4157#1012计算得出:a[Ca]=2#10-6,[Ca]=5#10-6%表1GC r15S M i n钢成分及相关数据Tab le1Composition and re lated data o f GCr15S M i n st ee lC S i M n C r P S Ca A l H O Fe质量分数/%1100015011001150010201010100201030100050100395193相对原子质量122855523132402811656摩尔分数4145@10-2917@10-3917@10-3116@10-2315@10-41166@10-4217@10-5519@10-41134@10-41101@10-40191f[i]113661174113501686112991139911251a[i]113360187113511029010026010420100061p*i /Pa116@10-76102@10-1518@10373131186@1052161@10226p i /Pa212@10-752718@10324418@1021126表2精炼轴承钢炉渣成分及相关数据Tab l e2Co m position o f slag and re la t ed da t aCaO S i O2M gO A l2O3F e O M nO CaF2S O质量分数/%4217817144141812012901760124315013摩尔分数Xi011920106901088010940100301001010210100201552 Mi242322由1873K降至1773K,氧分压由21281# 10-10Pa降至612#10-12Pa.则w[Ca]由5# 10-6%降至211#10-6%.得出钢液降温100e 时,钢中钙由于脱氧能力的提高,58%的[Ca]将与[O]反应生成CaO.其将在钢液内残留的刚玉或外来夹杂物这些现成表面上析出,形成m Ca O #n A l2O3.随钢液温度降低还有反应[H]y1/2 {H2}也将在上述现成表面上析出,而强化了液态点状夹杂物聚集长大.上述分析得出,要降低[C a],一是降低渣中(Ca O)的量,也就是降低炉渣碱度,但不能完全去除点状夹杂;另一种办法就是去除[Ca].2氯化法去除钢液中的钙采用氩气做载体,向钢液内吹入氩氯混合气体.当气泡上升至钢液表面,气泡与钢液相处于平衡状态,此时气泡内的总压力为110@105Pa.气泡内各组分的分压间关系为:E p M eCl+E p M e+p C l2+p A r=110@105Pa(4)因为氩不参与反应,初始气泡中p i C l2=110@105 -p A r,Pa.喷入钢液的氩氯气泡上浮达钢液表面时,气泡内将含有C l2、Ca、CaC l2、A l、A l C l3、C r、Cr C l3、M n、M nC l2、S i、Si C l4、C、CC l4、H2、H C l、Fe、Fe C l2.钢液中各元素与氯反应为:[Ca]+C l2y C a C l2(g)K1873=3184#1016[A l]+3/2C l2y A l C l3(g)K1873=6139#109[S i]+2C l4y S i C l4(g)K1873=3133@105[M n]+C l2y M nC l2(g)K1873=1105#106[C]+2C l2y CC l4(g)K1873=1146#106[H]+1/2C l2y H C l(g)K1873=3170#105[Fe]+C l2y FeC l2(g)K1873=6171#103将初始氯分压p i Cl定为310@104Pa情况下,平衡各分压计算值如表3:251第4期徐世铮等:轴承钢点状夹杂物成因及消除机理的探讨表3氯化产物平衡分压值Tab l e3Equ ili b rium pa rtia l p ressures of ch lo ride products Pap C l2pC a C l2pHC lpM nC l2pFeC l2pAlC l3pC r C l2pSiC l4219#10-10219#1041124#10-4119#10-6411#10-9110#10-9217#10-19由上表可见,钢液中各元素氯化次序为:Ca y H y M n y Fe y A l y C r y Si钙是优先氯化的元素,采用氯化去除是可行的.3精炼工艺参数的确定311加氯方式的选择氯化脱除钢液中钙的工艺,可在RH、DH、VAD、LF-VD精炼轴承钢过程中实施.为考虑首次工业性实验简便可行而选用SL钢包喷粉.312氯进入钢液的方式采用卤化物-氧化物合成粉剂[3](其成分见表4),用氩气做载体,经SL喷粉罐-喷枪,喷入钢包.表4合成粉剂成分Tab l e4Co m position o f compound powde r%CaO S i O2A l2O3M gO质量分数38~5812~157~127~11CaF2F eO CC l4质量分数5~7<0155~515粉剂粒度平均直径为01165mm.313卤化物配入量及卤化物合成粉剂用量计算按钢液中w[C a]=01002%计算[Ca]+C l2y C a C l2401m o l20015m o l每吨钢去除20g钙需015m o lC l2.采用CC l4分解生成C l2去除[Ca].炼钢温度下CC l4分解完全.每吨钢需用0125 m o lCC l4,即3815g,考虑到钢中其他元素氯化耗氯,配入50~60g CC l4/t为考虑,初始p i C l2为3#10-4Pa计,氩气用量为350~420L/.t在氧化物粉剂[3]中配入515%CC l4时,卤化物合成粉剂用量为1~111kg/.t若配入量为3%CC l4时,粉剂用量为117~2kg/.t供氩速度v A r=50~70L/m i n.钢液开喷温度为1600e时,吹毕温度为1520~1510e,可喷吹6~7m i n;喷吹时间依据出钢温度相应调整.314喷粉喉口临界速度从动力学角度出发,研究在炼钢温度条件下,为保证喷入钢液的气粉流中,粉剂不侵入钢液而导出粉剂在喷嘴喉口的临界速度v c.v c=8g(Q s/Q p-1)+12R/r Q p3(k Q s/Q p-1)1/2#(e R(Q s/Q p-1)-1)1/2(5)式中:Q s,Q p为钢液、粉剂密度,kg/m3;r为粉剂中平均粉粒半径,m;R为粉剂与钢液间界面张力, N/m;k为粉粒在钢液中阻力系数.将下列数据代入(5)式Q s=6800kg/m3,Q p=3410kg/m3,R=1152 N/m,k=113,得出临界速度:v c=(163138+01479r+1112#10-2/r)1/2,m/s(6) 4结语从热力学角度分析,在炼钢温度下当p O2[ 213#10-10Pa的条件下,促使渣中Ca O被还原成钙进入钢液中.精炼后随钢液温度降低,钢液中钙的脱氧能力提高,在w[C a]有01002%时,有58%的[Ca]参加脱氧反应生成初生C a O,又有反应2[H]y{H2},同时在钢液中现存夹杂物表面同时析出并长大,形成了m Ca O#n A l2O3点状夹杂物.热力学分析得出,用氯去除钢液中钙的可能性和合理性.对采用氯去除钢中钙的精炼工艺及相应的工艺参数进行了必要的理论分析和研究,为精炼工艺的制定提供依据.参考文献:[1] . . Å»¼À, . . Å»¼À. ¶ÀºѺĶǿÀ½À´ºÑϽ¶¼ÄÂÀ½½±³¼ºÃı½Î[M]. ºË±Ê¼À½±.1983.179-192. [2] . . º´ÀÂÑ¿. . . ¶½Ñ¿Éº¼À³. .¡. ÄÀ¾±Çº¿ . .À¿À¾±Â¶¿¼À. ¶Àºĺɶüº ÿÀ³Í½¶¼ÄÂÀÃı½¶Á½±³º½Î¿ÍÇ ÂÀȶÃÃÀ³[M]. ¶Ä±½½ÅÂĺÑ,Àü³±.1987.8-89.[3]徐世铮,刘沛环,刑玉录,等.喷射冶金用合成粉剂及其制造工艺:中国,8510031.1[P].1988.252材料与冶金学报第5卷。