一种镀锌设备盐酸清洗缓蚀剂
热镀锌车间工艺操作规程

FEE有限公司镀锌车间工艺操作规程1、操作规程作为制造输电线路铁塔部件,金属结构件和微波通讯铁塔等使表面达到防腐要求为目的.2、本操作规程依照GB2694-81标准编制.3、各部件原材料必须是能形成符合标准的镀层.4、工艺流程镀前处理酸洗水洗助镀热浸镀锌冷却钝化后处理检验镀前处理操作规程酸洗前处理:1、酸洗之前操作工应检查被件表面是否有电焊药皮.小面积的处理后可进入酸洗池.面积较大的要报告上级处理.2、镀件表面有油腻和污渍,酸洗责任人有权决定镀件是否进入酸洗池.并报与上级处理.3、被镀件表面若有开裂和缺损的钢材放置在指定的位置.4、被镀件表面因原材料钢材锈蚀严重而产生大面积的麻点,酸洗责任人应阴止此料进入酸洗池,并报与上级处理.5、检查钢管镀件是否有开工艺孔.酸洗操作规程:1、严禁镀件过酸洗.2、采用盐酸进行酸洗,温度采用自然温度.3、酸洗液的配制,浓盐酸:水=2:1.配制方法为:先将定量的清水打入酸洗池,再将浓盐酸管伸入清水水面以下注入浓盐酸.配制时加入重量比例为0.1~0.4%的OP乳化剂和约0.2%的缓蚀剂马洛品六次甲基四胺以防止盐酸的挥发和工件的过酸洗.废酸洗液中可以加入一定量的NH4CL以增强氧化物的溶解.4、酸洗浓度为HCL4~17%,浓度低于4%用于镀件、返工件和退挂具上的锌层.严禁将返工件吊入新配制的盐酸中.5、酸洗的时间由酸洗责任人根据实际情况自己定夺,原则上按照生产上要求合理的安排酸洗次序.严禁将不同的材料如Q235与Q345混合在一起酸洗有缓蚀剂的条件下不存在这一问题.6、酸洗中镀件过密需要进行翻料操作,建议进行二次翻料操作.最后一次用高压水泵冲洗,入池前水断流后进入到酸池.7、根据不同镀件的规格穿上挂具.镀件厚度的规定:当不同规格的部件穿上挂具时,在下列规定下的镀件厚度范围内可以混合穿上挂具.镀件厚度4mm以下;厚度5~8mm;厚度9~11mm;厚度11mm以上混合穿上挂具.壁厚者应在下层.且应检查牢固情况是否在下道工序会产生脱落.长度的规定:当采用单头吊挂镀锌时,角钢下端头相对长度不得超过10cm.8、工件在装入挂具后,工件因放久发黄氧化的应放入新酸中起落几次后,用高压水泵冲洗干净后至流动的清水中水洗.断流后立刻进入助镀池.不得在空中久留.表面发黄的镀件严禁进入助镀池.应返回在新酸中放置30秒后重新冲洗后入助镀池.溶剂处理:1、助镀剂的成分,采用NH4CL和ZnCL2配制,NH4CL:180~300g/l,助镀剂的成分经过化验员化验合格后方可使用.其中酸度PH=5~7,亚铁离子浓度大于30g/l时作助镀液更新再生处理.2、助镀温度为55~80℃,助镀时间为30~120秒以上.3、助镀液中不允许有浑蚀物或悬浮杂质存在,否则采用助镀液循环过滤方法除去.4、烘干采用炉前自然温度,温度不得超过200~230℃,时间不得超过10min,颜色变黄应重新进入助镀池起落三次.热浸镀锌炉前操作规程:1、锌锅里加入的锌锭须经过化验符合GB470-1997中的有关规定才能加入.2、镀件浸锌时应平稳,稍慢,挂钩位置应能使部件避免扣灰或溅出锌液.3、镀件浸锌深度为100~900mm,并在浸锌后适当进行上下串动和摆动.4、浸锌时间以部件达到热平衡的时间为主.建议时间为5、浸镀温度以炉前实际操作经验决定,总体原则是按照顾客质量要求为准.6、镀件出锅时应及时除尽锌锅表面的溶剂层,以避免溶剂污染镀件.7、打捞锌渣操作:在停止生产半小时左右进行锌渣打捞工作,一般每周打捞两次.打捞温度控制在445~455℃左右.8、锌灰提炼操作:炉前操作去除锌灰后集在锌锅的一侧,用氯化铵提炼后用带孔的工具将锌灰舀起,禁止锌灰中夹带大量的锌.9、两头吊的炉前应斜起至最大的倾斜角,以使锌液能流出.10、镀件从锌液中吊入冷却池中,不得在锌锅上久留.应立即进行落锌工作,除锌工作一般在5~10秒左右.11、捞池工作:入锅前检查镀件的数量,起锅时若发现数量不对,应立即进行打捞工作.在镀锌时一旦发现镀件掉入锌锅,应立刻捞出,每天工作结束时,操作人员必须进行捞池工作.禁止向锌锅中倒入其它垃圾.12、于钢管焊接塔,为保证插缝处无积锌,建议从横截面积小的一端出锌.镀后处理操作规程:1、冷却方式:采用水冷却,里面加入适量的中性肥皂,以提高镀件光洁度.冷却时间以工件在水中不冒气泡为止.冷却温度以50~80℃为宜.2、钝化处理:钝化液浓度K2Cr2O7在3.0~3.5g/l之间,酸度PH=1.0~2.0之间,钝化时间3~8秒,温度30~40℃之间,钝化的杂物要经常性的处理,另外注意:钝化时掉进池子里面的工件必须马上捞出,避免过长时间而使得工件表面锌层腐蚀.另外,工件从钝化池吊也来以后,必须要在池子的正上方停留片刻,以保证工件表面的钝化液完全断流后,才能吊到后处理工作区.3、钝化后处理:钝化后的产品,经过检查,不合格的产品,按照GB2694-81标准和顾客满意目标确认是否能够补救,并采用相关的措施对其进行后处理工作.4、对于镀件表面点状漏镀等,采用补镀剂补救,发现镀件表面大面积漏镀的工件可以再重镀一次.5、对于工件表面或内侧积锌严重或锌渣太多的,必须通知行车工将其吊到炉前重新再“烫”一次.6、对于色差现象特别严重的工件一律采取返工.7、后处理人员在处理工件表面的滴瘤、毛刺时,切不可敲击,只能用锉刀将其锉平.8、后处理人员一定要注意螺栓孔的处理,特别是穿插销的螺栓孔的处理.9、经过质检员对工件表面光洁度、有无露铁、色差等检验合格,方可运到成品堆场.。
盐酸除锈最佳浓度的选择

盐酸除锈最佳浓度的选择发布日期:2013-09-24 浏览次数:1804 核心提示:国大多数去除钢铁表面的锈均采用盐酸除锈法,本文详细介绍了盐酸除锈的机理,最佳盐酸浓度控制与测定以及常温高效盐酸酸雾抑制缓蚀剂的应用。
1前言目前国太多数热程镀锌、渗锌、电镀锌、电镀多元合金.去除钢铁表面的锈蚀均采用盐酸除锈的方法。
由于强调生产,追求产量.使酸洗液一直处于较高的浓度,而忽视了酸洗液的最佳浓度的控制与维护许多厂家不知道控制酸洗液的浓度,而简单地采取每周更新一次酸液,有些则一年更新两次,有的甚至从来更新。
通常是倒掉一些酸洗液,漆加一些新酸洗谴。
造成盐酸耗量过高,增加生产成本,并对环境造成一定的污染。
因此.掌握与控制盐酸酸洗液的实用寿命具有一定的经济意义。
2盐酸除锈机理使用盐酸去除钢铁表面的铁锈时,一般认为有三种作用.即溶解、还原、少量氧化剥商作用。
而实际除锈机理远此上述复杂得多。
当钢铁与盐酸接触后.发生如下化学反应:(1)直接溶解作用(2)还原作用此还原反应,可加速溶解于盐酸溶液而成为可溶性FeCl2。
(3)少量剥离作用在上述反应中.第(1)、(2)化学反应进行得相当快。
对第(3)、(4)以及还原化学反应,通常要比(1)、(2)式幔得多。
(2)式析出的H2同时对难溶的黑色氧化皮起着冲裂和剥落的机械作用,提高了酸洗效率。
但往往由于钢铁制件基体在溶解时容易引起过腐蚀.而且析出台向基体部渗透扩散产生氢脆而降低了机械性能。
尤其是高瑞钢、弹性钢制件由于氢脆而造成报废。
从化学方程式(1)中可知.在一定温度下,要使这一反应持续地向右进行.必颁控制盐酸淮度和FeCl2含量。
随着酸洗不断进行.FeCl2在酸槽中含量将会越来越高.当达到饱和状态时,化学反应达到平衡状态.尽管延长酸洗时间技果也不太明显相反,在一定浓度下.FeC12不饱和,则酸渣仍具有裉强酸洗能力。
实践证明:酸洗建度快慢不仅考虑酸洗液的浓度,而重要的是决定于FeCl2,在该盐酸浓度下的饱和程度。
新型多用固体酸洗缓蚀剂

新型多用固体酸洗缓蚀剂赵丽萍,郑建国(天华化工机械及自动化研究设计院,兰州730060)摘 要:本研究采用腐蚀电化学弱极化测试、曲线拟合技术,测定腐蚀速率等腐蚀电化学参数,并以此方法进行配方筛选试验,最终以失重法进行评定,筛选出了缓蚀效果好、无毒、环保、低添加量的多用固体酸洗缓蚀剂CM-911,该缓蚀剂可用于十六种清洗碳钢、不锈钢、黄铜、紫铜、铝材设备水垢的清洗用酸。
关键词:CM -911;固体酸洗缓蚀剂;清洗;无毒;环保中图分类号:T G 174.42 文献标识码:A 文章编号:1005-748X(2007)10-0536-04A NEW TYPE OF SOLID PICKLING INHIBIT ORZHAO L-i ping,ZHENG Jian -guo(T ianhua Inst itute of chemica l M achinery and Auto mation,L anzho u 730060,China)Abstract:A new type o f solid pickling inhibito r CM-911w as develo ped,which had the featur es of ex cellentco rr osio n inhibition,nontox icit y,no env iro nmental contaminatio n,low dosage,and etc.CM -911could be used in sixteen kinds o f chemical cleaning agents,w hich co uld pickle the vessels made o f carbon steel,stainless steel,br ass,copper and aluminium.Key words:CM -911so lid inhibitor ;P ickling ;N ontox icity;Env iro nmental pr otectio n 随着化学清洗技术的迅速发展,酸洗缓蚀剂的市场不断扩大,并从原来单一酸种的缓蚀剂发展到多用酸洗缓蚀剂。
电力铁塔钢制件热镀锌生产优化工艺
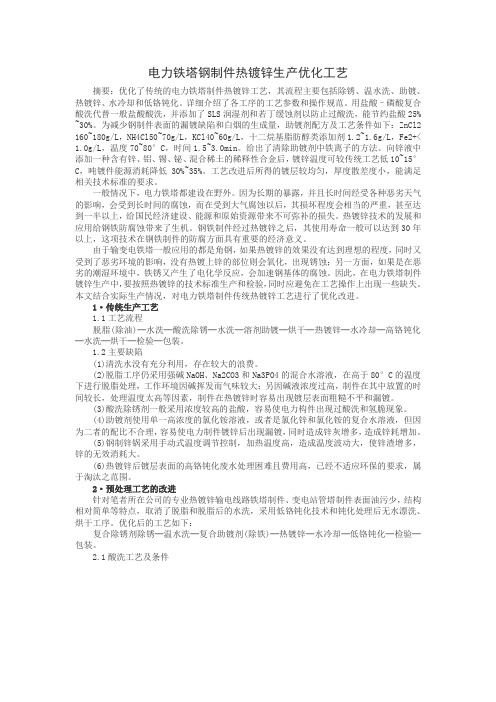
电力铁塔钢制件热镀锌生产优化工艺摘要:优化了传统的电力铁塔制件热镀锌工艺,其流程主要包括除锈、温水洗、助镀、热镀锌、水冷却和低铬钝化。
详细介绍了各工序的工艺参数和操作规范。
用盐酸–磷酸复合酸洗代替一般盐酸酸洗,并添加了SLS润湿剂和若丁缓蚀剂以防止过酸洗,能节约盐酸25% ~30%。
为减少钢制件表面的漏镀缺陷和白烟的生成量,助镀剂配方及工艺条件如下:ZnCl2 160~180g/L,NH4Cl50~70g/L,KCl40~60g/L,十二烷基脂肪醇类添加剂1.2~1.6g/L,Fe2+< 1.0g/L,温度70~80°C,时间1.5~3.0min。
给出了清除助镀剂中铁离子的方法。
向锌液中添加一种含有锌、铝、锡、铋、混合稀土的稀释性合金后,镀锌温度可较传统工艺低10~15°C,吨镀件能源消耗降低30%~35%。
工艺改进后所得的镀层较均匀,厚度散差度小,能满足相关技术标准的要求。
一般情况下,电力铁塔都建设在野外。
因为长期的暴露,并且长时间经受各种恶劣天气的影响,会受到长时间的腐蚀,而在受到大气腐蚀以后,其损坏程度会相当的严重,甚至达到一半以上,给国民经济建设、能源和原始资源带来不可弥补的损失。
热镀锌技术的发展和应用给钢铁防腐蚀带来了生机。
钢铁制件经过热镀锌之后,其使用寿命一般可以达到30年以上,这项技术在钢铁制件的防腐方面具有重要的经济意义。
由于输变电铁塔一般应用的都是角钢,如果热镀锌的效果没有达到理想的程度,同时又受到了恶劣环境的影响,没有热镀上锌的部位则会氧化,出现锈蚀;另一方面,如果是在恶劣的潮湿环境中,铁锈又产生了电化学反应,会加速钢基体的腐蚀。
因此,在电力铁塔制件镀锌生产中,要按照热镀锌的技术标准生产和检验,同时应避免在工艺操作上出现一些缺失。
本文结合实际生产情况,对电力铁塔制件传统热镀锌工艺进行了优化改进。
1·传统生产工艺1.1工艺流程脱脂(除油)─水洗─酸洗除锈─水洗─溶剂助镀─烘干─热镀锌─水冷却─高铬钝化─水洗─烘干─检验─包装。
氢脆

氢脆(或称氢损伤概念压力容器的氢脆(或称氢损伤)是指它的器壁受到氢的侵蚀,造成材料塑性和强度降低,并因此而导致的开裂或延迟性的脆性破坏。
高温高压的氢对钢的损伤主要是因为氢以原子状态渗入金属内,并在金属内部再结合成分子,产生很高的压力,严重时会导致表面鼓包或皱折;氢与钢中的碳结合,使钢脱碳,或使钢中的硫化物与氧化物还原。
氢的来源1)可以是设备中原来就存在的,例如,炼钢、焊接过程中的湿气在高温下被还原而生成氢,并溶解在液体金属中。
2)设备在电镀或酸洗时,钢表面被吸附的氢原子过饱和,使氢渗入钢中;3)使用后由介质中吸收进入的,例如在石油、化工容器中,就有许多介质中含氢或含混有硫化氢的杂质。
钢发生氢脆的特征1)表现在微观组织上。
它的腐蚀面常可见到钢的脱碳铁素体,氢脆层有沿着晶界扩展的腐蚀裂纹。
2)宏观上可以发现氢脆所产生的鼓包。
介质中含氢(或硫化氢)的容器是否会发生氢脆,主要决定于操作温度、氢的分压、作用时间和钢的化学成分。
温度越高、氢分压越突,碳钢的氢脆层就越深,发生氢脆破裂的时间也越短,其中温度尤其是重要因素。
3)钢的含碳量越高,在相同的温度和压力条件下,氢脆的倾向越严重。
4)一些没有基本技术要求的钢材在高温(例如焊接)条件下就容易产生氢脆。
例如Q235牌号的钢在焊接过程中,虽然焊接看起来很容易、很好,但是钢铁本身已经溢出了有害的氢破坏了钢铁的结晶组织,使得钢铁在这里变得脆弱,容易断裂,大大降低了钢铁在这个部位的强度5)氢脆是指,高强度钢在富氢环境(液体、气氛)中进行处理时,氢原子会向钢基体中渗透,使高强度钢出现塑性和韧性降低,甚至脆裂的现象称为氢脆。
如弹簧件电镀时,在除油、浸蚀、电镀工序中,均易发生基体或镀层渗氢。
其后果轻者镀层鼓泡、脱皮; 重者产生氢脆导致弹簧断裂避免氢脆的措施1)钢中添有铬、钛、钒等元素,可以阻止氢脆的产生2)出现氢脆的工件通过除氢处理(如加热等)也能消除氢脆;如电镀件的去氢都在200~240度的温度下,加热2~4小时可将绝大部分氢去除3)利用正火、时效等方法可进行去氢处理。
酸洗 碱洗缓蚀剂

多用酸洗缓蚀剂Lan-826本产品由化工部化机院清洗技术研究所生产,获中华人民共和国三等发明奖,被国家科委列为重点推广项目,在国内外处于领先地位。
当今国内销量最大,世界上用途最广的缓蚀剂.适用范围:● 配合用各种类酸清洗各种工业设备清除各种碳酸盐、硫酸盐、硅酸盐型等各种水垢用之添加剂.● 适用于碳钢、低合金钢、不锈钢、铜、铝、铜等金属设备及组合材质设备的酸洗。
● 适用于石油、化工、机械、冶金、电力、交通、制冷、生活等行业使用的各种换热设备的酸性清洗,如各种锅炉、冷却器、加热器、反应器、蒸发器、贮罐、上下水管道、冷冻机、压缩机等。
● 适用于各行业工业产品之酸性金属表面处理,以清除表面污垢、油污等污物防金属腐蚀.性能特点:● 多用:适用于Ø 盐酸Ø 硝酸Ø 氢氟酸Ø 磷酸Ø 硝酸—氢氟酸Ø 硫酸等各种无机酸Ø 加氨柠檬酸Ø 加氨柠檬酸—氟化氢铵Ø 氨基磺酸Ø 羟基乙酸Ø 羟基乙酸—甲酸—氟化氢铵Ø EDTAØ 草酸Ø 醋酸等有机酸Ø 有机酸及混合酸酸洗.是目前世界上用途最广的酸洗缓蚀剂。
● 高效:在各种化学清洗用酸中都具有优良的缓蚀效果,常用条件下金属腐蚀率小于1g/m²·h, 具有优良的抗酸洗渗氢和抑制Fe3+腐蚀的能力,酸洗时金属不产生孔蚀。
● 安全可靠: 不含氟化物,不含硫酸,不含磷酸, 不影响健康.● 经济价廉:用量小、费用低、操作简便、使用安全,特别是能避免误用缓蚀剂造成的危险。
主要成份:多元醇醚、聚乙二醇磷酯, 不含氟化物.物化性状:外观:淡黄色或茶色液体 pH值:≥7.0;密度:(20℃),g/cm³:≥ 0.96;可燃性:不燃;使用方法:● 根据需清洗设备构造、材质及水垢类型(清洗对象成份)选择合适的酸种和清洗工艺条件。
一种镀锌设备盐酸清洗缓蚀剂的研制与评价
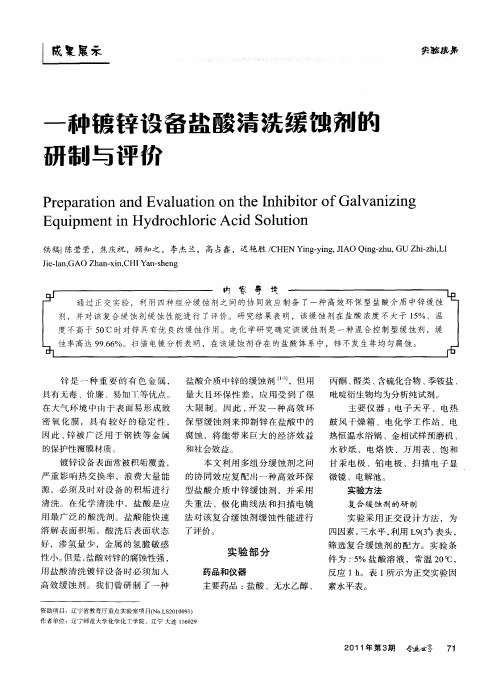
在一 定 温 度下 反 应 1 h后取 出锌 5 0mgL 0 / 。按 上述 比例将 四类化 锌腐蚀速 率加快 , 在 7 ℃ 以下 , 但 0
试 片 ,用蒸 馏水 冲洗后 ,用无 水 合 物 用 溶 剂 溶 解 ,得 到 复 合 缓 并 未发 现缓 蚀 剂失效 现 象 ,说 明
验 成
一
种锒 锌设 备 盐酸 清洗 缓 蚀剂 的
研 制 与 评 价
P e a ai n a dEv l ain o eI h b t ro l a ii g r p r t n au to nt n i i f o h o Gav n zn
Eq i m e ti u p n n Hyd o hl rcAc d S l to r c o i i u i n o
乙醇 和丙 酮处 理 ,再 用 电 吹风吹 蚀 剂 。
此 复 合 缓 蚀 剂 具 有 一 定 的 抗 温
表 2 正 交 实 验 结 果
面 光滑 后 ,用 蒸馏 水 冲洗 ,随后
蚀 剂后 不 同温度 下锌 的腐蚀 速率 。
实 验 温 度 分 别 为 2 、3 、4 、 0 0 0
5 、6 、7 ℃ 。 反 应 时 间 为 1h 0 0 0 。
用无 水 乙醇 和丙 酮脱脂 处 理 ; 干 实验结果如表 2 。
燥 后精 确 称重 。将两 片经 处理 的 素水 平表。 源自2 1 年第3 0 1 期
岔照对手 7 i
雾骝 成
表 1 正交实验因素水平表
蚀 速 率 下降 ,缓蚀 效 率提 高 ,当
缓 蚀 剂 的浓 度 增 大 到 一 定 程 度 后 .
1 , . C曲线 变 得 平 稳 ,缓 蚀 效 果 稳 定 。从 曲线 上 可见 ,缓蚀 剂浓 度 存 0 0m / l 2 0 gL时 即可 达 到很 好 的
盐酸除锈最佳浓度的选择
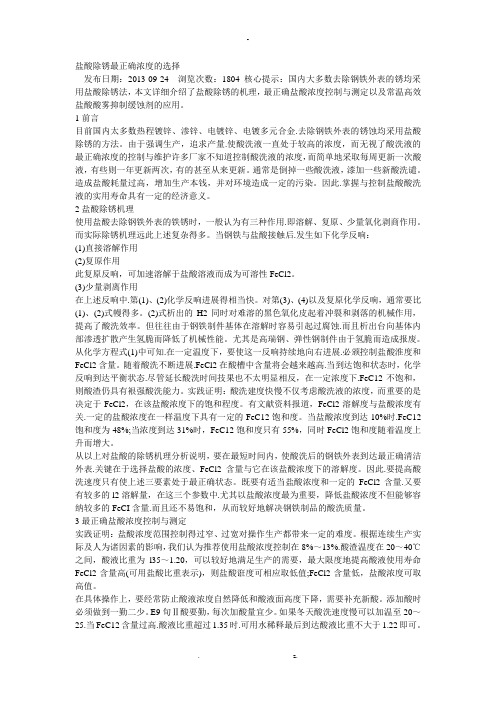
盐酸除锈最正确浓度的选择发布日期:2013-09-24 浏览次数:1804 核心提示:国内大多数去除钢铁外表的锈均采用盐酸除锈法,本文详细介绍了盐酸除锈的机理,最正确盐酸浓度控制与测定以及常温高效盐酸酸雾抑制缓蚀剂的应用。
1前言目前国内太多数热程镀锌、渗锌、电镀锌、电镀多元合金.去除钢铁外表的锈蚀均采用盐酸除锈的方法。
由于强调生产,追求产量.使酸洗液一直处于较高的浓度,而无视了酸洗液的最正确浓度的控制与维护许多厂家不知道控制酸洗液的浓度,而简单地采取每周更新一次酸液,有些则一年更新两次,有的甚至从来更新。
通常是倒掉一些酸洗液,漆加一些新酸洗谴。
造成盐酸耗量过高,增加生产本钱,并对环境造成一定的污染。
因此.掌握与控制盐酸酸洗液的实用寿命具有一定的经济意义。
2盐酸除锈机理使用盐酸去除钢铁外表的铁锈时,一般认为有三种作用.即溶解、复原、少量氧化剥商作用。
而实际除锈机理远此上述复杂得多。
当钢铁与盐酸接触后.发生如下化学反响:(1)直接溶解作用(2)复原作用此复原反响,可加速溶解于盐酸溶液而成为可溶性FeCl2。
(3)少量剥离作用在上述反响中.第(1)、(2)化学反响进展得相当快。
对第(3)、(4)以及复原化学反响,通常要比(1)、(2)式幔得多。
(2)式析出的H2同时对难溶的黑色氧化皮起着冲裂和剥落的机械作用,提高了酸洗效率。
但往往由于钢铁制件基体在溶解时容易引起过腐蚀.而且析出台向基体内部渗透扩散产生氢脆而降低了机械性能。
尤其是高瑞钢、弹性钢制件由于氢脆而造成报废。
从化学方程式(1)中可知.在一定温度下,要使这一反响持续地向右进展.必颁控制盐酸淮度和FeCl2含量。
随着酸洗不断进展.FeCl2在酸槽中含量将会越来越高.当到达饱和状态时,化学反响到达平衡状态.尽管延长酸洗时间技果也不太明显相反,在一定浓度下.FeC12不饱和,则酸渣仍具有裉强酸洗能力。
实践证明:酸洗建度快慢不仅考虑酸洗液的浓度,而重要的是决定于FeCl2,在该盐酸浓度下的饱和程度。
一种缓蚀剂对防锈添加剂抗盐雾性能的影响
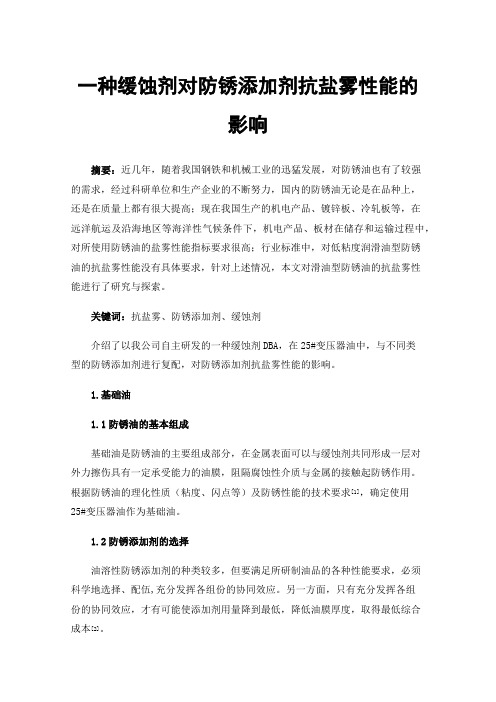
一种缓蚀剂对防锈添加剂抗盐雾性能的影响摘要:近几年,随着我国钢铁和机械工业的迅猛发展,对防锈油也有了较强的需求,经过科研单位和生产企业的不断努力,国内的防锈油无论是在品种上,还是在质量上都有很大提高;现在我国生产的机电产品、镀锌板、冷轧板等,在远洋航运及沿海地区等海洋性气候条件下,机电产品、板材在储存和运输过程中,对所使用防锈油的盐雾性能指标要求很高;行业标准中,对低粘度润滑油型防锈油的抗盐雾性能没有具体要求,针对上述情况,本文对滑油型防锈油的抗盐雾性能进行了研究与探索。
关键词:抗盐雾、防锈添加剂、缓蚀剂介绍了以我公司自主研发的一种缓蚀剂DBA,在25#变压器油中,与不同类型的防锈添加剂进行复配,对防锈添加剂抗盐雾性能的影响。
1.基础油1.1防锈油的基本组成基础油是防锈油的主要组成部分,在金属表面可以与缓蚀剂共同形成一层对外力擦伤具有一定承受能力的油膜,阻隔腐蚀性介质与金属的接触起防锈作用。
根据防锈油的理化性质(粘度、闪点等)及防锈性能的技术要求[1],确定使用25#变压器油作为基础油。
1.2防锈添加剂的选择油溶性防锈添加剂的种类较多,但要满足所研制油品的各种性能要求,必须科学地选择、配伍,充分发挥各组份的协同效应。
另一方面,只有充分发挥各组份的协同效应,才有可能使添加剂用量降到最低,降低油膜厚度,取得最低综合成本[2]。
1.3缓蚀剂DBA是我司自主研发的一款缓蚀剂,其具备油溶性好、成膜均匀、原料易得等条件。
在25#变压器油中,该缓蚀剂DBA与不同类型的防锈添加剂复配,通过反复试验,验证其对防锈添加剂抗盐雾性能的影响。
2性能试验及效果评价2.1试验方法试验材料:试验试片为10号钢,其尺寸为80×60×3~5mm。
防锈剂及基础油:防锈剂为工业级的石油磺酸钡(T701)、二壬基萘磺酸钡(T705)、N一油酰基氨酸十八胺(T711)、苯并三氮唑(T706)、山梨糖醇单油酸酯(司本一80)、羊毛酯镁皂、十二烯基丁二酸(T746)和十七烯基咪唑啉烯基丁二酸盐(T703)。
- 1、下载文档前请自行甄别文档内容的完整性,平台不提供额外的编辑、内容补充、找答案等附加服务。
- 2、"仅部分预览"的文档,不可在线预览部分如存在完整性等问题,可反馈申请退款(可完整预览的文档不适用该条件!)。
- 3、如文档侵犯您的权益,请联系客服反馈,我们会尽快为您处理(人工客服工作时间:9:00-18:30)。
!E$%$"6缓蚀剂'6盐酸""1;
参考文献
,!-!王 佳"邹爱美"李杰兰"等$盐酸介质中锌缓蚀剂的研 制,Q-$表面技术""%%&"#'!"$+#'7#($
,"-!王建国"王 佳"邹爱美"等$盐酸介质中锌缓蚀剂的电
化学研究,Q-$中国材料科技与设备""%%&"#!!$+(37 (-$ ,#-!焦庆祝"兰天丽"任晓英"等$型缓蚀剂和难溶垢清洗剂 ,Q-$清洗世界""%%-""'!!!$+#%7#&$
!1(' !'%% .
含%$"6复合 7%$-#& &$(1&b!%" (#$%! 1!&$% --$&&
缓蚀剂
由图1及表!可见"加入复合缓蚀剂后"腐蚀电 位变化不大"阴极和阳极 /?AO=斜率均发生明显变 化"说明该缓蚀剂属于混合控制型缓蚀剂&
添加缓蚀剂后"腐 蚀 电 流 密 度 !FE@UU$明 显 下 降" 由FE@UU计算缓蚀 效 率 可 达 --6 以 上"说 明 该 缓 蚀 剂 缓蚀效果良好&
测定了加入%$"6复合缓蚀剂时不同浓度的盐 酸溶液中锌 的 腐 蚀 速 率"结 果 见 图 #& 反 应 温 度 为
*!-%*
图1!缓蚀剂对锌极化曲线的影响
表"!图)拟合得到的腐蚀参数
ቤተ መጻሕፍቲ ባይዱ
无缓蚀剂
!E@UU
FE@UU
L
!*)E5"
7%$-(! "$%%-b!%'
"?
"E 缓蚀率
5L)XOE 5L)XOE 6
在'6的盐酸 溶 液 中"加 入 不 同 量 的 复 合 缓 蚀 剂"测定不同温度下锌的腐蚀速率&反应时间均为 !;"实验结果如图!所示&
"%8"反应时间为!;"盐酸浓度分别为!$'6%#6% '6%!%6%!'6%"%6&
图!!腐蚀速率与缓蚀剂浓度的关系
由图!可见"在一定温度下"随着缓蚀剂浓度的 增大"锌的腐蚀速率下降"缓蚀效率提高"当缓蚀剂 的浓度增大到一定程度后">:9 曲线变得平稳"缓蚀 效 果 稳 定& 从 曲 线 上 可 见"缓 蚀 剂 浓 度 在 "%%%5D)^时即可达到很好的缓蚀效果& #$,!温度对缓蚀性能的影响
.ABA<@C@D>;F>;8LNELA@Z@AYU]K@O+=AD@A/MI;>P<N>;@P.P@I3>NKD@>A
QJ*G fFCD,[;M"<+29 SFCD,RFCD"0ig;F,[;F"^JQFO,=?C"0*Gg;?C,aFC"<+JS?C,W;OCD
!^F?@CFCD9@U5?=iCFYOUWFPR"]?=F?C!!&%"-"<;FC?$
焦庆祝等+一种镀锌设备盐酸清洗缓蚀剂
#$2!扫描电镜分析 图'是锌腐蚀前后试片表面的扫描电镜照片& 对比腐蚀前后的锌试片的表面状态"未发现点
蚀'凹面(及条纹腐蚀'沟壑(&由此可见"该缓蚀剂
不会引起局部腐蚀& 综上所述"研制的镀锌设备盐酸清洗缓蚀剂的
缓蚀性能优良&
!
!?$未腐蚀
!>$%$"6缓蚀剂'6盐酸""; 图'!锌试片腐蚀前后表面扫描电镜形貌
本工作利用多组分缓蚀剂之间的协同效应复配 出一种高效环保型盐酸介质中锌缓蚀剂"并采用失 重法%极化曲线法和扫描电镜法对该复合缓蚀剂的 缓蚀性能进行了评价&
"!实验方法
"$"!药品和仪器 主要药品+盐酸%无水乙醇%丙酮%醛类%含硫化
合物%季铵盐%吡啶衍生物"均为分析纯试剂&主要 仪器+电子天平%电热鼓风干燥箱%电化学工作站%电 热恒温水浴锅%金相试样预磨机%水砂纸%电烙铁%万 用表%饱和 甘 汞 电 极%铂 电 极%扫 描 电 子 显 微 镜%电 解池& "$#!腐蚀速率测定
本实验采用失重法测定缓蚀剂的腐蚀速率和缓 蚀效率&具 体 如 下+将 规 格 为 #% 55b"% 55b
联系人焦庆祝"dF?@e[#!&#$E@5
%$"55 的锌试片用金相试样预磨机配以 &%%&% 3%%&的水砂纸打磨至表面光滑后"用蒸馏水冲洗" 随后用无水乙醇和丙酮脱脂处理#干燥后精确称重& 将两片经处理的锌试片悬于'%5=含有一定浓度复 合缓蚀剂的'6的盐酸溶液中"在一定温度下反应! ;后取出锌试片"用蒸馏水冲洗后"用无水乙醇和丙 酮处理"再用电吹风吹干"精确称重&取反应前后试 片质量差的平均值作为不同实验条件下锌试片的失 重量"计算腐蚀速率和缓蚀效率+
>$ !G% %G$)H*3 $ !!%>)>%$8!%%6 式中+G% 为试样腐蚀前的质量"D#G 为腐蚀并除去 腐蚀产物后试样的质量"D#H为试样表面积"5"#3为 反应时间";#> 为加入缓蚀 剂 后 试 样 的 腐 蚀 速 率#>% 为未加 缓 蚀 剂 时 试 样 的 腐 蚀 速 率# 为 缓 蚀 效 率"6& "$,!极化曲线测定 扫描速率为13% 5L)5FC"以饱和甘汞电极作 为参比电极"铂电极为辅助电极"锌电极!工作面积 !E5"$作为工作电极& "$)!扫描电镜观察 采用扫描电镜观察放大('%倍的锌表面扫描电 镜照片"考察点蚀及条纹腐蚀等非均匀腐蚀现象&
#!结果与讨论
#$"!复合缓蚀剂研制 采用正交设计方法筛选复合缓蚀剂的配方&实
验条件为+'6盐酸溶液"常温"%8"反应!;&由正 交实验结果分析得到缓蚀剂组分的最佳配比为+醛 类%吡啶衍生物%含硫化合物%季铵盐各'%%5D)^&
*!3-*
焦庆祝等+一种镀锌设备盐酸清洗缓蚀剂
按上述比例将四类化合物用溶剂溶解"得到复合缓 蚀剂& #$#!缓蚀剂浓度对缓蚀性能的影响
!!引 言
镀锌设备表面常被积垢覆盖"严重影响热交换 率"浪费大 量 能 源"必 须 及 时 对 设 备 的 积 垢 进 行 清 洗&在化学 清 洗 中"盐 酸 是 应 用 最 广 泛 的 酸 洗 剂& 盐酸能快速溶解表面积垢"酸洗后表面状态好"渗氢 量少"金属的氢脆敏感性小&但是"盐酸对锌的腐蚀 性强"用盐酸清洗镀锌设备时必须加入高效缓蚀剂& 曾经研制的一种盐酸介质中锌的缓蚀剂,!7#-用量大 且环保性差"应用受到了很大限制&因此"开发一种 高效环保型缓蚀剂来抑制锌在盐酸中的腐蚀"将具 有巨大的经济效益和社会效益&
温度是影响金属腐蚀速率的重要指标&测定了 '6的盐酸溶液中"加入%$"6的复合缓蚀剂后不同 温度下锌的 腐 蚀 速 率"结 果 见 图 "& 实 验 温 度 分 别 为"%8%#%8%1%8%'%8%&%8%(%8&反应时间为 !;&
图#!腐蚀速率与盐酸浓度的关系
由图#可见"随着酸浓度的增加"金属腐蚀速率 增大&盐酸浓度在!'6以内时"金属腐蚀速率变化 不大&盐酸浓度过高"则导致缓蚀剂失效& #$&!缓蚀剂的电化学测试
第#!卷增刊! "%!%年(月
腐蚀与防护
<GHHGIJG9 K :HG/2</JG9
L@=$#!!IMNN=O5OCP! QM=R"%!%
一种镀锌设备盐酸清洗缓蚀剂
焦庆祝陈莹莹顾知之李杰兰高占鑫迟艳胜
!辽宁师范大学化学化工学院"大连 !!&%"-$
摘!要通过正交实验"利用四种组分缓蚀剂之间的协同效应制备了一种高效环保型盐酸介质中的锌缓蚀剂"并对 该复合缓蚀剂的缓蚀性能进行了评价&研究结果表明"该缓蚀剂在盐酸浓度不大于!'6%温度不高于'% 8时对锌 具有优良的缓蚀作用&电化学研究确定该缓蚀剂是一种混合控制型缓蚀剂"缓蚀率高达--$&&6&扫描电镜分析表 明"在该缓蚀剂存在的盐酸体系中"锌不发生局部腐蚀& 关键词盐酸#锌#缓蚀剂#制备#性能 中图分类号/0!(1$1"!!!文献标识码*!!!文章编号!%%',(134"%!%增!,!3-,%#
.C?D;LPD+*;FD;=ROAAFEFOCP?CXOCYFU@C5OCP?=,AUFOCX=RFC;F>FP@UA@U[FCEFC;RXU@E;=@UFEW@=MPF@CB?WNUON?UOXMWFCD