汽车内饰门低成本表面处理技术1211
汽车内饰主流的六大制造工艺的设计说明

汽车内饰主流的六大制造工艺的设计说明汽车内饰的制造工艺是指在生产过程中使用的技术和方法。
以下是汽车内饰主流的六大制造工艺的设计说明:1.注塑工艺:注塑工艺是汽车内饰制造中最常用的制造工艺之一、它通过将熔化的塑料材料注入金属模具中,然后用高压将其压实成型。
注塑工艺的优点是制作速度快、成本低、复杂的形状容易实现。
同时,注塑工艺还可以实现多种颜色和纹理效果的定制,满足消费者对个性化内饰的需求。
2.真皮工艺:真皮工艺是汽车内饰制造中高端豪华车型常用的制造工艺。
它使用动物皮革作为材料,在经过多道工序的处理后制成内饰面板。
真皮工艺的优点是具有独特的质感和舒适度,且更耐磨损。
然而,真皮工艺的制造成本较高,并且需要定期的保养和清洁。
3.木纹工艺:木纹工艺是一种将人造木材或真实木材应用于汽车内饰的工艺。
木纹工艺可以通过涂装或贴膜的方式实现。
其优点是能够给车内带来自然、温馨的氛围,提升整体质感。
同时,木纹材料也具备防火和防腐蚀的特性。
4.金属工艺:金属工艺是一种将金属材料制作成汽车内饰部件的工艺。
这种工艺可以通过冲压、焊接、打磨和抛光等方式实现。
金属工艺的优点是坚固耐用、外观美观,并且能够提供高质量的触感。
然而,金属工艺的加工难度较大,成本较高。
5.布艺工艺:布艺工艺是一种使用织物材料制作汽车内饰的方法。
布艺工艺可以通过织造、坯布定型、缝制等步骤来完成。
布艺工艺的优点是柔软舒适、透气性好,并且可以提供丰富多样的颜色和图案选择。
然而,布艺内饰容易吸尘和污染,需要定期清洗和保养。
6.涂装工艺:涂装工艺是一种使用涂料来改变汽车内饰表面颜色和质感的方法。
涂装工艺可以通过喷涂、刷涂、滚涂等方式来完成。
涂装工艺的优点是色彩鲜艳、外观平整,并且能够保护内饰表面不受损坏。
然而,涂装工艺的缺点是容易刮花和褪色,需要定期修补和保养。
汽车内饰的制造工艺在不同的车型和厂家中有所不同,每种工艺都有其适用的范围和特点。
汽车制造商通常会根据车辆定位、市场需求和成本考虑来选择适合的制造工艺,以确保内饰的质量和用户体验的提升。
汽车内饰主流的六大制造工艺
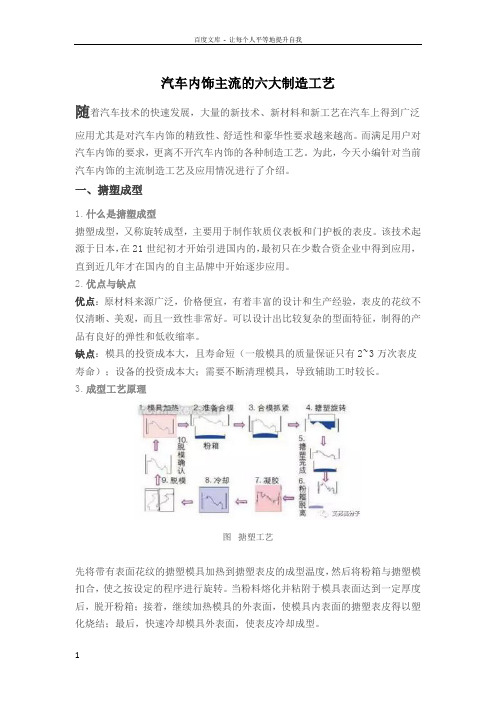
汽车内饰主流的六大制造工艺随着汽车技术的快速发展,大量的新技术、新材料和新工艺在汽车上得到广泛应用尤其是对汽车内饰的精致性、舒适性和豪华性要求越来越高。
而满足用户对汽车内饰的要求,更离不开汽车内饰的各种制造工艺。
为此,今天小编针对当前汽车内饰的主流制造工艺及应用情况进行了介绍。
一、搪塑成型1. 什么是搪塑成型搪塑成型,又称旋转成型,主要用于制作软质仪表板和门护板的表皮。
该技术起源于日本,在21世纪初才开始引进国内的,最初只在少数合资企业中得到应用,直到近几年才在国内的自主品牌中开始逐步应用。
2. 优点与缺点优点:原材料来源广泛,价格便宜,有着丰富的设计和生产经验,表皮的花纹不仅清晰、美观,而且一致性非常好。
可以设计出比较复杂的型面特征,制得的产品有良好的弹性和低收缩率。
缺点:模具的投资成本大,且寿命短(一般模具的质量保证只有2~3万次表皮寿命);设备的投资成本大;需要不断清理模具,导致辅助工时较长。
3. 成型工艺原理图搪塑工艺先将带有表面花纹的搪塑模具加热到搪塑表皮的成型温度,然后将粉箱与搪塑模扣合,使之按设定的程序进行旋转。
当粉料熔化并粘附于模具表面达到一定厚度后,脱开粉箱;接着,继续加热模具的外表面,使模具内表面的搪塑表皮得以塑化烧结;最后,快速冷却模具外表面,使表皮冷却成型。
二、PU(聚氨酯)喷涂PU喷涂工艺是近几年迅速发展起来的一种新的表皮成型工艺,主要用于仪表板的表皮和护板的表皮等。
1. 成型工艺图 PU喷涂表皮的生产流程PU喷涂是指先在表皮成型模表面喷上脱模剂,而后再喷涂模内漆(可根据产品需要喷涂不同颜色的模内漆),随后喷涂液态的PU原料(可通过喷涂机械手控制表皮的厚度),最后冷却起模。
2. 相比于搪塑工艺的优势第一部分搪塑工艺和PU喷涂工艺都是软质仪表板表皮的主要制作工艺,但相对于搪塑工艺而言,PU喷涂有许多优点,比如:可实现双色仪表板表面,使得造三、模内转印(IMD)1. 模内转印概念与应用模内转印是一种在成型过程中与装饰同步进行的工艺。
汽车内饰件油漆涂层标准
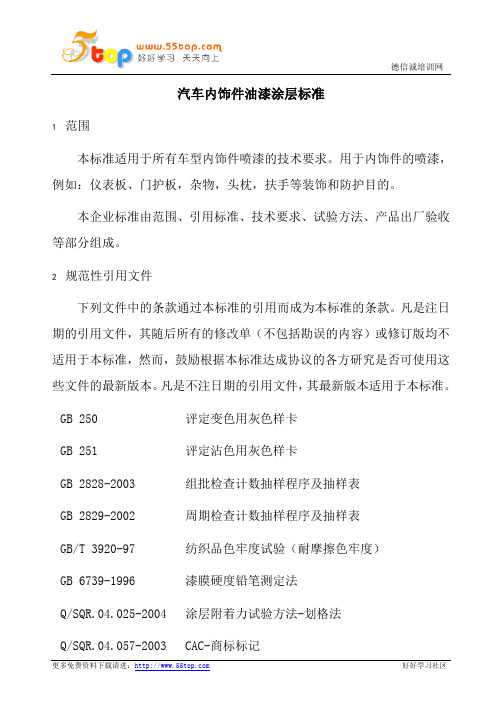
汽车内饰件油漆涂层标准1 范围本标准适用于所有车型内饰件喷漆的技术要求。
用于内饰件的喷漆,例如:仪表板、门护板,杂物,头枕,扶手等装饰和防护目的。
本企业标准由范围、引用标准、技术要求、试验方法、产品出厂验收等部分组成。
2 规范性引用文件下列文件中的条款通过本标准的引用而成为本标准的条款。
凡是注日期的引用文件,其随后所有的修改单(不包括勘误的内容)或修订版均不适用于本标准,然而,鼓励根据本标准达成协议的各方研究是否可使用这些文件的最新版本。
凡是不注日期的引用文件,其最新版本适用于本标准。
GB 250 评定变色用灰色样卡GB 251 评定沾色用灰色样卡GB 2828-2003 组批检查计数抽样程序及抽样表GB 2829-2002 周期检查计数抽样程序及抽样表GB/T 3920-97 纺织品色牢度试验(耐摩擦色牢度)GB 6739-1996 漆膜硬度铅笔测定法Q/SQR.04.025-2004 涂层附着力试验方法-划格法Q/SQR.04.057-2003 CAC-商标标记Q/SQR.04.058-2004 汽车零部件标记要求Q/SQR.04.065-2005 漆膜耐水试验方法Q/SQR.04.095-2004 塑料、织物氙弧灯连续照射试验Q/SQR.04.112-2003 产品包装标志要求Q/SQR.04.400-2005 涂层耐冲击试验方法DIN 50014 气候及技术引用标准气候3 术语内饰喷漆件:车身内部起装饰和防护作用的油漆件。
4 材料4.1材料和组成4.1.1 喷漆体按图纸或说明,或按照相应零部件标准要求;4.1.2 涂层体系漆基按图纸或说明;5 技术要求5.1 预处理在试验前,要放在正常气候条件下(空气温度为23℃,允许偏差在±1,空气湿度为50%和允许偏差在±3)24小时,做预处理。
5.2 外观喷漆件表面均匀,不允许有针孔、裂纹、流挂、条纹、叠层等缺陷。
喷漆表面的颜色和光泽必须与样品或色板一致。
木皮在汽车智能内饰表面透光性能研究

136AUTO TIMEAUTOMOBILE DESIGN | 汽车设计1 引言伴随着科技发展和智能驾驶技术的到来,为满足客户对汽车驾驶性和舒适性的需求,汽车的设计和研发不断朝着一体化和智能化发展[1-2]。
汽车内饰设计将成为汽车设计的关键,透光材料装饰也在越来越多地应用到汽车内饰表面中,从而提升优良的人车交互体验[3]。
真木材料因其具备的环保、轻量和可塑性强等特点,大量地应用与汽车内饰件中,并从单纯的装饰功能向智能集成方向发展[4]。
透光木皮具体效果是指在背部光源的作用下,将设计的图案、文字和LOGO 等清晰显示在汽车真木装饰件上。
本文针对透光表皮材质透光率低及表面图标显示不清晰等问题,以木皮为研究对象开展相应透光率实验及图标透光研究。
2 木皮透光率实验研究2.1 实验数据集本文分别选取黄杨木、枫木、樱桃木、法国梧桐木、柚木、雀眼木和欧椴木等木皮为研究对象,如图1所示。
木皮厚度为0.3mm —0.5m m ,木皮经过增白化学处理。
图1 木皮材料(a)黄杨木 (b)枫木 (c)樱桃木 (d)法国梧桐木(e)柚木 (f)雀眼木 (g)欧椴木2.2 实验设备和环境实验所用设备为KONICA MINOLTA 公司生产的型号为CS-2000分光辐射亮度计,使用CS-S10w 专业版数据处理软件控制CS-2000进行测量,实现透光率实验数据管理和分析。
所有实验都在无外界直接照射光源的密闭室内进行,室内温度保持在25±5℃,室内相对湿度控制在60%以下。
2.3 实验结果与分析透光率实验采用木皮在标准光源作用下的透光能力作为评价指标。
具体测量过程为:首先测量光源的亮度Lv 值及记录色度坐标x 、y 值;然后将木皮覆盖住光源,记录亮度Lv1值;最后通过计算得出木皮的透光率。
本研究通过设置不同的参数开展多轮实验并对实验结果比较分析。
实验一:喷漆前后色板木皮的透光率测试实验以PC/GF20材料为基材,使用汉高胶水将木皮集成到基材上,喷漆原料为T88棕色油漆。
汽车内饰塑料制品免喷涂技术探密

lications创新应用1!汽车内饰塑料制品免喷涂技术探密邓桂芳1引言近年来,低碳与环保的话题己不再新鲜,却仍然是国家和社会关注的重点,同时也是企业低 碳与环保行动进入实践的阶段。
对于汽车行业来 说,生产厂家的低碳之路,除了发展新能源技术 之外,工程塑料的应用也成为低碳的选择。
因为 塑料质轻,可以有效减轻车身重量,从而节省燃 油。
而且塑料具有较高的零件设计和造型自由度,因而受到汽车设计人员的青睐。
更重要的是,塑 料本身是可回收利用的,这样不仅节约了能源,还促进了环保和塑料循环经济的发展。
所以汽车 塑料零部件的回收利用是实现汽车产业可持续发 展的一个重要环节。
尤其是车用塑件免喷涂技术 能大量节省生产时间和成本,提高产品质量,增 长产品耐久性,最适宜应用在汽车、家电、通信 产品和日用品等外观上。
同时,此项技术也满足 了消费者对创意性及美感的需求。
车用塑件免喷 涂技术拥有广阔的市场前景,是目前国际上的热 门技术之一,每年以20%速度在递增,己成为当 今非常重要的研发课题。
2环保低碳推动车用塑件免喷涂技术的发 展成新趋向为使塑料制品获得各种色彩的外观效果,通 常需要采用喷涂的方法来实现。
常见一般用于汽车的塑料件,需要进行喷漆来达到如美观的哑光、高光或者闪烁等效果,以及保护基材实现耐侯,耐刮擦等功能。
但是,喷涂工艺的生产工序复杂,良品率低且成本高。
同时,该生产工艺不环保,产品的回收利用也较困难。
而对于那些直接成型的具有金属珠光效果的未喷涂外观件而言,其表面一般都带有难以消除的熔接线和流痕。
免去了喷漆的工艺,就免去了对环境的伤害,而且大大降低了制造本钱。
所以,免喷涂材料在源头上就考虑材料的回收利用和环保题目,是真正绿色设 计,绿色出产和出产绿色产品的新选择。
近年来,人们已不再满足于汽车内饰件的使用功能,对其外观的欣赏品味及绿色环保的要求越来越高。
由于以往那种先注塑汽车内饰件壳,然后再喷涂的方法,既不环保,质量也不稳定,众多国际国内知名厂商摒弃了老方法,转而采用一种新型成型工艺一一免喷涂高光无痕注塑成型技术。
低成本轻量化EPP材料在汽车内饰顶棚设计中的应用研究
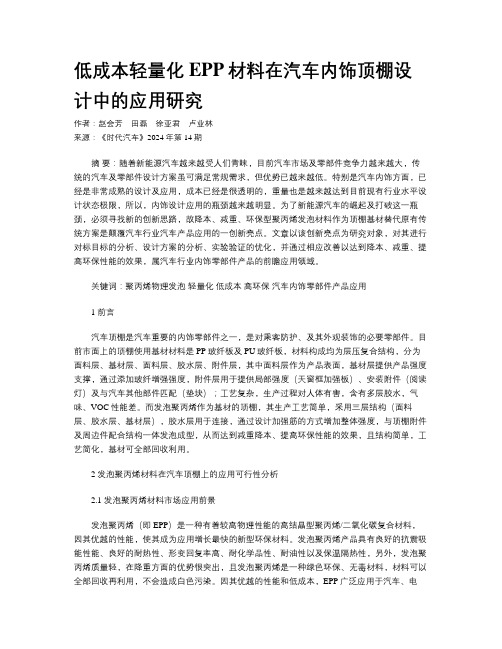
低成本轻量化EPP材料在汽车内饰顶棚设计中的应用研究作者:赵会芳田磊徐亚君卢业林来源:《时代汽车》2024年第14期摘要:随着新能源汽车越来越受人们青睐,目前汽车市场及零部件竞争力越来越大,传统的汽车及零部件设计方案虽可满足常规需求,但优势已越来越低。
特别是汽车内饰方面,已经是非常成熟的设计及应用,成本已经是很透明的,重量也是越来越达到目前现有行业水平设计状态极限,所以,内饰设计应用的瓶颈越来越明显。
为了新能源汽车的崛起及打破这一瓶颈,必须寻找新的创新思路,故降本、减重、环保型聚丙烯发泡材料作为顶棚基材替代原有传统方案是颠覆汽车行业汽车产品应用的一创新亮点。
文章以该创新亮点为研究对象,对其进行对标目标的分析、设计方案的分析、实验验证的优化,并通过相应改善以达到降本、减重、提高环保性能的效果,属汽车行业内饰零部件产品的前瞻应用领域。
关键词:聚丙烯物理发泡轻量化低成本高环保汽车内饰零部件产品应用1 前言汽车顶棚是汽车重要的内饰零部件之一,是对乘客防护、及其外观装饰的必要零部件。
目前市面上的顶棚使用基材材料是PP玻纤板及PU玻纤板,材料构成均为层压复合结构,分为面料层、基材层、面料层、胶水层、附件层,其中面料层作为产品表面,基材层提供产品强度支撑,通过添加玻纤增强强度,附件层用于提供局部强度(天窗框加强板)、安装附件(阅读灯)及与汽车其他部件匹配(垫块);工艺复杂,生产过程对人体有害,含有多层胶水,气味、VOC性能差。
而发泡聚丙烯作为基材的顶棚,其生产工艺简单,采用三层结构(面料层、胶水层、基材层),胶水层用于连接,通过设计加强筋的方式增加整体强度,与顶棚附件及周边件配合结构一体发泡成型,从而达到减重降本、提高环保性能的效果,且结构简单,工艺简化,基材可全部回收利用。
2 发泡聚丙烯材料在汽车顶棚上的应用可行性分析2.1 发泡聚丙烯材料市场应用前景发泡聚丙烯(即EPP)是一种有着较高物理性能的高结晶型聚丙烯/二氧化碳复合材料,因其优越的性能,使其成为应用增长最快的新型环保材料。
汽车内外饰常用工艺及新技术展望

汽车内外饰常用工艺及新技术展望引言随着汽车行业的不断发展,汽车内外饰工艺也在不断创新和改进。
汽车的内外饰设计不仅关乎汽车的外观美感,更直接影响到驾驶者和乘客的使用体验。
本文将介绍一些常用的汽车内外饰工艺,并展望未来可能出现的新技术。
一、汽车内饰常用工艺1.1 汽车座椅汽车座椅是汽车内饰中最重要的部分之一,它直接影响到驾驶者和乘客的舒适感和乘坐体验。
目前,常用的汽车座椅工艺包括皮革包裹、布料织物、合成革等。
这些材料都有其优点和缺点,如皮革包裹舒适度高但价格昂贵,布料织物相对便宜但不易清洁,合成革具有经济实惠和易清洁等优点。
未来,随着材料科技的进步,可能会出现更多新材料应用到汽车座椅上,如仿生材料、智能材料等,进一步提升座椅的舒适性和人性化设计。
1.2 汽车仪表盘汽车仪表盘是驾驶者与汽车的主要交互界面,它不仅需要提供车辆状态和驾驶信息,还需具备美观和易读性。
目前,常用的汽车仪表盘工艺包括液晶显示屏、LED背光、3D效果等。
这些技术使得仪表盘设计更加时尚和信息显示更加清晰。
未来,随着可穿戴设备和增强现实技术的发展,汽车仪表盘可能会进一步升级,具备更多智能化的功能,如智能语音助手、自适应亮度调节等。
1.3 汽车内饰照明汽车内饰照明是营造汽车内部氛围和提升驾乘舒适感的重要一环。
常用的汽车内饰照明工艺包括LED灯带、氛围灯等。
这些照明技术可以给汽车内部创造出不同色彩和亮度的氛围,增加车内的视觉效果和审美感。
未来,随着发光二极管技术的不断进步,可能会出现更多新的照明技术应用到汽车内饰上,如可调光、多彩变化等,进一步提升驾乘体验。
二、汽车外饰常用工艺2.1 汽车涂装汽车涂装是汽车外饰的重要一环,不仅可以保护车身,还能提升汽车的外观美感。
常用的汽车涂装工艺包括普通漆面、金属漆、水性漆等。
不同的涂装工艺可以给汽车带来不同的效果,如亮光、哑光等。
未来,随着环保意识的提高,水性漆等环保型涂料可能会逐渐取代传统有机溶剂漆,以减少对环境的污染。
轿车门内饰板总成技术条件
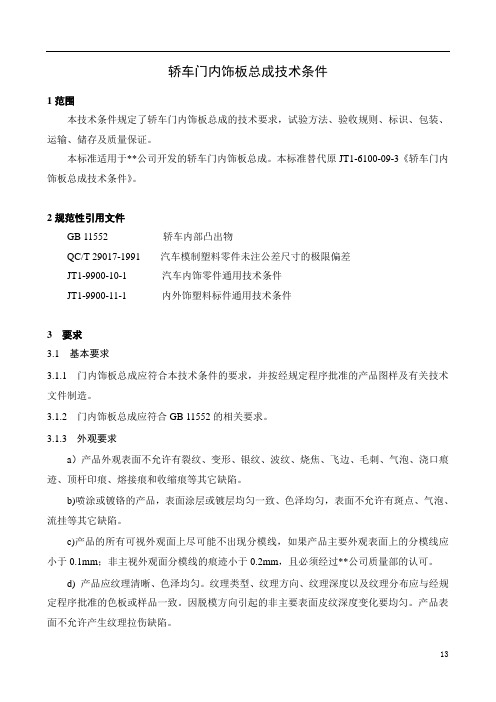
轿车门内饰板总成技术条件1范围本技术条件规定了轿车门内饰板总成的技术要求,试验方法、验收规则、标识、包装、运输、储存及质量保证。
本标准适用于**公司开发的轿车门内饰板总成。
本标准替代原JT1-6100-09-3《轿车门内饰板总成技术条件》。
2规范性引用文件GB 11552 轿车内部凸出物QC/T 29017-1991 汽车模制塑料零件未注公差尺寸的极限偏差JT1-9900-10-1 汽车内饰零件通用技术条件JT1-9900-11-1 内外饰塑料标件通用技术条件3 要求3.1 基本要求3.1.1 门内饰板总成应符合本技术条件的要求,并按经规定程序批准的产品图样及有关技术文件制造。
3.1.2 门内饰板总成应符合GB 11552的相关要求。
3.1.3 外观要求a)产品外观表面不允许有裂纹、变形、银纹、波纹、烧焦、飞边、毛刺、气泡、浇口痕迹、顶杆印痕、熔接痕和收缩痕等其它缺陷。
b)喷涂或镀铬的产品,表面涂层或镀层均匀一致、色泽均匀,表面不允许有斑点、气泡、流挂等其它缺陷。
c)产品的所有可视外观面上尽可能不出现分模线,如果产品主要外观表面上的分模线应小于0.1mm;非主视外观面分模线的痕迹小于0.2mm,且必须经过**公司质量部的认可。
d) 产品应纹理清晰、色泽均匀。
纹理类型、纹理方向、纹理深度以及纹理分布应与经规定程序批准的色板或样品一致。
因脱模方向引起的非主要表面皮纹深度变化要均匀。
产品表面不允许产生纹理拉伤缺陷。
3.1.4 门内饰板总成的尺寸应符合2D图纸及GD&T图纸等文件的规定。
在没有文件说明的情况下,应满足QC/T 29017-1991《汽车模制塑料零件未注公差尺寸的极限偏差》的要求。
3.2门内饰板总成性能门内饰板应满足表1的性能的要求。
4.试验方法4.1门饰板刚度加载区域:门内饰板最薄弱区域(由工程师指定);加载力:10N;加载面积;直径20mm;测量变形量区域应在加载点20mm范围内(图1);图1 门饰板刚度测试4.2车门内拉手刚度、强度将门饰板总成按照实际装车状态固定。
汽车塑料部件低成本解决方案与实例

汽车塑料部件低成本解决方案与实例摘要:本文主要介绍汽车塑料部件的低成本解决方案以及实例。
首先,我们将讨论低成本解决方案的重要性和应用场景。
然后,我们将详细介绍几种常见的汽车塑料部件低成本解决方案,并提供实际案例作为说明。
最后,我们将总结本文的主要观点和结论。
1.引言在汽车制造业中,降低成本是一项重要的任务。
汽车塑料部件作为汽车生产过程中不可或缺的组成部分,对于降低整车成本起着关键作用。
因此,寻找汽车塑料部件的低成本解决方案是汽车制造商和供应商的一项重要任务。
2.汽车塑料部件低成本解决方案的重要性和应用场景降低汽车塑料部件的成本对于提高汽车制造商的竞争力至关重要。
低成本解决方案可以帮助汽车制造商降低生产成本,提高利润率,并在市场上获得价格竞争优势。
此外,低成本解决方案还可以促进创新和技术发展,在设计和生产过程中寻找更有效和经济的方法。
3.1材料选择选择合适的塑料材料可以降低成本。
例如,汽车塑料部件可以采用更便宜的塑料材料,如聚丙烯或聚乙烯,而不是更昂贵的塑料材料,如聚酰胺。
此外,可以使用回收塑料材料,以降低原材料成本。
案例:一汽丰田在其车身部件中使用聚碳酸酯(PC)材料,代替传统的聚酰胺材料,降低了材料成本,并在汽车质量和性能方面没有降低。
3.2设计优化通过优化设计,可以降低汽车塑料部件的生产成本。
例如,可以减少零部件数量,简化生产工艺。
此外,可以通过优化零部件结构和形状,减少材料损耗。
案例:大众汽车将其汽车内饰件的设计进行优化,通过减少零部件数量和材料使用量,降低了生产成本。
3.3自动化生产采用自动化生产技术可以降低人工成本,提高生产效率。
例如,使用自动化机器人进行注塑成型过程,可以提高生产效率,并降低零部件的生产成本。
案例:特斯拉公司使用自动化生产技术生产其塑料零件,包括注塑成型和装配过程,从而实现了低成本生产。
4.结论汽车塑料部件的低成本解决方案对于降低汽车制造商的生产成本,提高市场竞争力至关重要。
汽车车门内饰板产品微发泡+气体反压工艺介绍
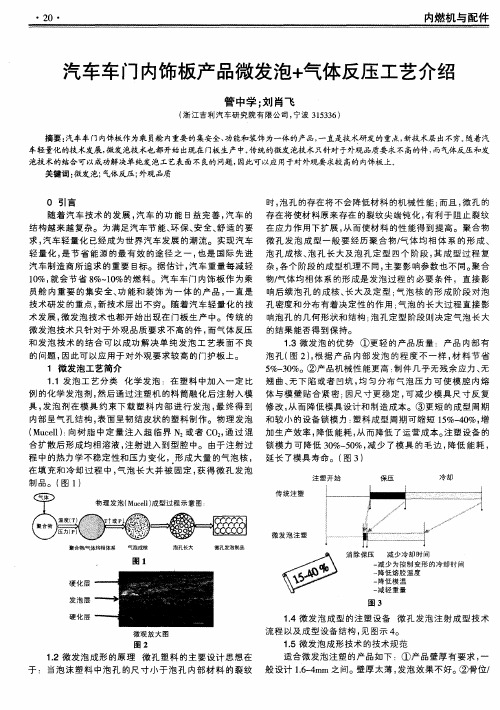
微 发泡技术只针对于外观品质 要求不高的件 , 而气体 反压 的结 果 能 否 得 到 保 持 。 和 发 泡 技 术 的 结 合 可 以成 功 解 决 单 纯 发 泡 工 艺 表 面 不 良 1 . 3微发泡 的优势 ① 更轻的产品质量 :产品 内部 有 的 问题 , 因此可以应用于对外观 要求较 高的门护板上。 1 微发 泡工艺简 介 泡孔 ( 图2 ) , 根 据产 品内部 发泡 的程 度不 一样 , 材 料节 省
合 扩 散 后 形 成均 相 溶液 , 注 射进 入 到 型 腔 中。 由于 注 射 过 锁 模 力 可 降 低 3 0 %一 5 0 %, 减 少了模具 的毛边 , 降低 能 耗 , 程 中 的热 力 学 不稳 定 性 和 压 力 变化 ,形 成 大 量 的气 泡核 , 延长 了模具寿命 。( 图3 ) 在 填充和冷却 过程 中, 气泡 长大并被 固定 , 获 得 徼 孔 发泡
0 引 言
时, 泡 孔 的存 在 将 不 会 降低 材 料 的机 械 性 能 ; 而且 , 微 孔 的
随 着 汽 车 技术 的发 展 , 汽 车 的 功 能 日益 完 善 , 汽 车 的 存 在 将 使 材 料原 来 存在 的 裂纹 尖 端 钝 化 , 有 利 于 阻止 裂纹 结构越来越复杂0为满足汽车节能、 环 保、 安全、 舒 适 的要 在 应 力 作 用 下 扩 展 , 从 而 使材 料 的性 能 得 到 提 高 。 聚 合 物 求, 汽 车 轻 量 化 已经 成 为 世 界 汽 车 发展 的 潮 流 。 实 现 汽 车 微 孔 发 泡 成 型 一 般 要 经 历 聚 合 物 / 气体均相 体 系的形 成、 轻量化 , 是 节 省 能 源 的 最 有 效 的途 径 之 一 , 也 是 国际 先 进 泡 孔 成核 、 泡 孔 长 大及 泡 孔 定 型 四 个 阶 段 , 其 成 型 过 程 复
基于六西格玛设计的汽车门饰板轻量化设计

066
AUTO DRIVING & SERVICE 2021 . 04
学术 | 制造研究
ACADEMIC
子类零件作为研究对象(图 1),研究对象的数量由 35 个缩小至 6 个 :左前门扶手、左前门内开拉手框盖板、左前门中饰板、左 前门上饰板、左前门杂物盒和左前门下饰板。
表 2 项目目标定义
车型
现有车型 美系对标车1
对标车 欧系对标车2 日系对标车3 目标值
质量/kg
3.402 3.68 2.360 2.258
产品表面 面密度=质量÷产品表面面
面积/㎡
积(/ kg/㎡)
1.725 1.978 1.453 1.290
1.97 1.86 1.79 1.75 ≤1.8
图 1 零件爆炸图和子零件重量排序
2.1.2 确定评价标准 通过相同零件行业对标分析发现,不同车型的门饰板总成质
2.1 识别阶段(I) 识别阶段主要通过运用“二八定律”缩小研究对象的范围,
以及开发“面密度”指标确定减重目标值。 2.1.1 确定研究对象
对正在开发项目进行筛选,根据“结构典型、工艺多样以及 方案可推广至其他零件”的原则,选定了某平台车型的门饰板产 品作为研究对象。门饰板下级子零件数量众多,共有 35 个,需 要进一步缩小研究对象范围。根据“二八定律”,推断出“20% 的子零件质量将占总成质量的 80%”。因此将子零件分类 14 个子 类,按质量由低到高进行排序。选取占总成质量 82% 的前 6 名
本文介绍了实际工作中的一个项目案例,通过采用美国供应 商学会总裁乔杜里先生的六西格玛设计流程(IDDOV,即识别、 定义、研发、优化和验证),运用六西格玛设计工具箱中的二八 定律、决策矩阵、质量屋、鱼骨图、普氏分析、数学建模以及参 数图等工具,对汽车内饰门饰板进行轻量化设计。
汽车内饰抗划伤的原理

汽车内饰抗划伤的原理
汽车内饰抗划伤的原理主要是基于材料的选择和表面处理。
首先,汽车内饰通常采用具有良好抗划伤性能的材料。
在材料的选择上,汽车内饰常常采用高强度且硬度较高的材料,如塑料、皮革和金属等。
这些材料具有出色的抗划伤性能,能够有效地防止因外力摩擦而产生的划痕和磨损。
其次,汽车内饰在表面处理上也起到了重要作用。
表面处理可以增加材料的硬度和耐磨性,提高其抗划伤性能。
常见的表面处理方法包括涂覆、喷涂和热压等。
涂覆可以形成一层坚硬的保护膜,有效地防止划痕和磨损。
喷涂可以在材料表面形成一层陶瓷式的保护涂层,具有更好的抗划伤性能。
而热压则可以改变材料的结构,使其表面更加坚硬和耐磨。
此外,汽车内饰中的一些部位还采用了特殊的加工工艺来增加抗划伤性能。
例如,在塑料材料中加入填充剂或纤维增强剂,使其硬度增加,从而提高抗划伤性能。
另外,一些汽车内饰件采用了仿生学设计原理,如皮革的纹路和金属的纹饰,可以有效地掩盖和分散划痕,减轻划痕对外观的影响。
总结起来,汽车内饰抗划伤的原理主要包括材料的选择、表面处理和特殊的加工工艺。
采用高强度且硬度较高的材料,并经过特殊的表面处理,可以在一定程度上提高汽车内饰的抗划伤性能。
此外,特殊的加工工艺和设计原理也能够有效地
减轻划痕对汽车内饰外观的影响。
这些措施的综合应用,使得汽车内饰能够长时间保持美观和整洁,增加乘客的舒适感受,提升汽车的整体品质。
bmw90010 -2 2020表面处理标准

bmw90010 -2 2020表面处理标准全文共四篇示例,供读者参考第一篇示例:BMW90010-2 2020表面处理标准旨在确保BMW生产的汽车在表面处理方面符合高品质标准,以提供客户满意的产品。
表面处理是汽车制造过程中至关重要的一环,它不仅决定了汽车外观的美观程度,还直接影响汽车零部件的质量和适用性。
BMW制定了严格的表面处理标准,以确保每一辆生产的汽车都符合要求。
BMW90010-2 2020表面处理标准主要涵盖了各种不同的汽车外观部件,包括车身、车门、引擎盖、保险杠等。
这些部件在生产过程中会经历一系列的表面处理工艺,如喷涂、涂覆、电镀等,这些工艺旨在保护汽车外观部件免受外部环境和日常使用的损坏。
根据BMW90010-2 2020表面处理标准,所有汽车外观部件在生产过程中必须严格按照BMW规定的工艺流程进行处理,以确保表面处理的质量。
这些工艺流程包括前处理、涂装、烘干以及检验等环节。
在前处理环节,外观部件需要经过除锈、磷化等处理,以确保油漆可以牢固附着在表面。
在涂装环节,外观部件需要经过底漆、面漆等多道喷涂工序,确保颜色均匀、色泽良好。
烘干环节则是用来固化油漆,使其达到最佳的耐磨性和耐候性。
除了工艺流程外,BMW90010-2 2020表面处理标准还规定了涂料的选择和质量要求。
根据不同的外观部件和环境要求,BMW指定了不同的涂料种类和品牌。
这些涂料必须符合一系列的物理性能和环境要求,如耐磨性、防腐性、光泽度等。
只有通过BMW认可的涂料才能在生产中使用,以确保外观部件的质量和耐久性。
BMW90010-2 2020表面处理标准还对外观部件的检验和质量控制提出了严格要求。
在生产过程中,外观部件需要经过多道质量检验,如外观检查、颜色检测、厚度检测等。
只有通过检验的外观部件才能进入下一道工序,确保生产出来的汽车外观部件符合BMW的标准。
第二篇示例:BMW 90010-2 2020表面处理标准是宝马公司严格执行的一份标准文档,规定了汽车表面处理工艺的要求和标准。
汽车车门内饰板产品微发泡和气体反压工艺介绍

汽车车门内饰板产品微发泡和气体反压工艺介绍摘要:汽车门板作为汽车的重要组成部分,一直是工作人员的关注焦点,他的主要作用在于保障乘车人员的生命安全,同时还具有一定的装饰作用。
为了适应轻量化技术发展的需求,微发泡技术在门板生产中的运用得到逐步扩大,发泡技术与气体反压两者的结合能够有效提升加工件的整体质量。
关键词:汽车车门内装饰;产品微发泡;气体反压工艺随着汽车技术的发展,以及汽车产品自身结构功能的日益丰富与完善,人们对产品质量以及节能、环保、安全等方面的标准要求也在逐步提升,这就需要技术的进步为生产工作的顺利开展提供支撑。
1.微发泡工艺简介1.1工艺分类发泡工艺是指在塑料中加入一定比例的化学发泡剂,用注塑机融化塑料后注入模具中,发泡剂由于受到模具的约束在模具内产生作用,从而获得表面呈出韧结皮状而内部有气孔的塑料制件。
物理发泡工艺是指注入超临界N2或者二氧化碳,再将混合形成的扩散溶液注入型腔中。
随着注入过程中压力与热力学不稳定性的不断变化,会产生出大量的气泡核,气泡在冷却与填充的过程中逐渐变大和固定,就形成了微孔发泡制品。
1.2发泡原理当泡沫塑料内部裂纹尺寸大于塑料泡孔时,泡孔不但不会降低材料的机械性能,还会使材料存在的裂纹尖端出现钝化,抑制裂纹在应力作用下的进一步发展趋势,相应的材料性能反而得到提升,这体现出了微孔塑料设计思想。
聚合物微孔发泡成型需要经历以下几个步骤,分别是聚合物或气体均相体系形成、泡孔成核、长大和定型。
不但过程复杂,而且成型机理存在差异,影响因素也不尽相同。
聚合物或均相体系形成对泡孔核的形成、长大和定型都产生影响,是发泡过程的必要条件。
气泡核的形成会影响气泡核分布与孔密度;气泡形状会影响气泡的形状与结构;气泡定型会对气泡长大的结果能否长久保持产生影响。
1.3微发泡优势产品内部的发泡程度不同,能够节约的材料也就不同。
微发泡的优势主要体现在质量能够降低质量。
1.3.1微发泡会使产品的机械性能得到提升,消除制件的残余应力,避免下陷或翘曲的情况。
基于高光无痕技术的汽车内饰件轻量化技术

基于高光无痕技术的汽车内饰件轻量化技术向良明;徐以国【摘要】Lightweight design and manufacture is an important direction in automobile development. This paper researched the lightweight method of interior part by using OptiStruct software and rapid heating and cooling molding technology. Taken the real sill plate trim as the research object, the application of this method reduced part weight by 19%. Taken the new part to do the strength test, dimension stability test and scratch and mar test, the results validated the superiority of the new Lightweight part. The study shows that, plastic parts performance is better than before and cost is lower, and also economic benefit is remarkable.%轻量化是汽车发展的重要方向,研究了汽车内饰件轻量化设计及成型方法.通过OptiStruct工具指导轻量化设计,通过高光无痕注塑成型技术提升零件的成型质量.以汽车后门槛饰板为研究对象,应用此方法成功的将汽重量降低19%以上,并通过强度、尺寸稳定性、外观、耐刮擦等试验,验证了轻量化之后的零件的优越性.研究结果表明:塑件在轻量化设计成型之后性能升高、成本降低,经济效益显著.【期刊名称】《轻工机械》【年(卷),期】2013(031)002【总页数】5页(P113-117)【关键词】注塑件;轻量化;汽车内饰;高光无痕【作者】向良明;徐以国【作者单位】泛亚汽车技术中心有限公司,上海201201【正文语种】中文【中图分类】TQ320.66随着国家绿色环保理念的展开,轻量化设计和生产已经成为汽车设计考虑的重要因素,内饰产品作为彰显汽车档次的重要工程,其设计和成型质量越来越受到关注。
化学微发泡注塑在汽车门内饰板的应用

化学微发泡注塑在汽车门内饰板的应用刘臻青【摘要】为了通过汽车内饰注塑零件的轻量化以降低整车燃油消耗,该文论述了化学微发泡注塑在汽车门内饰板中的应用.通过对化学微发泡注塑工艺原理的介绍及工程力学计算公式的运用,分析出减重目标及初始注塑壁厚,并在综合考虑减重目标、泡孔状态的稳定性及零件的性能后,确定出最为合适的发泡厚度和材料的弯曲模量.在满足刚度要求的基础上达到了轻量化的目的,最终将化学微发泡注塑工艺成功地应用在某量产车型门内饰板上,实现了23%的减重效果,取得了良好的经济和社会效益,为汽车内饰注塑零件的轻量化设计提供了参考.【期刊名称】《汽车工程师》【年(卷),期】2017(000)004【总页数】4页(P47-50)【关键词】化学微发泡注塑;汽车门内饰板;聚丙烯;轻量化;弯曲模量【作者】刘臻青【作者单位】泛亚汽车技术中心有限公司【正文语种】中文我国在2014年正式发布了乘用车燃料消耗量第四阶段强制性国家标准,根据标准要求,到2020年我国当年生产的乘用车平均燃料消耗量需降低到5.0L/100km。
除此之外欧盟、美国及日本等主要发达经济体也对汽车燃油消耗做出了更加严格的限制。
世界各大汽车制造企业为了应对新的标准纷纷加大了新能源车的研发,另一方面着力改善传统发动机的燃油利用效率。
根据美国能源署的统计,整车质量每下降10%燃油经济性提高5.1%,汽车的其他排放物也会相应降低。
所以塑料零件的轻量化成为减轻整车质量的重要组成部分,门内饰板作为重要的汽车内饰零件主要由塑料注塑工艺制造,成为塑料轻量化研究的重点。
文章论述了某车型采用化学微发泡工艺,通过门内饰板的注塑与发泡厚度的确认并考虑化学发泡注塑聚丙烯材料弯曲模量的性能要求,在满足门饰板刚度性能要求的前提下,实现了零件减重的目的。
1 化学微发泡注塑工艺过程目前国内外文献报道的微发泡聚合物材料加工主要采用物理发泡技术,而化学微发泡注塑工艺的研究报道很少。
微发泡注塑技术有降低锁模力、提高产品尺寸精度及缩短成型周期等诸多优势。
汽车内饰表面装饰工艺介绍

本文将针对汽车内饰表面装饰的几种主流工艺从技术、成本、环保性能等方面进行分析比较。
(文中“IMD”=IMR “INS”=IML/IMF)第一部分:水转印、IMD、INS工艺比较一、工艺描述1、水转印:将已成型的塑料基材压印浮在水面上的水溶性薄膜,转印薄膜上的花纹,再以透明面漆保护其花纹及对表面做光泽调节。
流程为转印-薄膜清除-烘干-喷面漆,如下图所示:2、INS(Film Insert Molding):将带有外观效果的INS薄膜预先吸塑/高压成型,把多余的膜边冲切,再把冲切好的薄膜壳片放置在注塑模具内进行注塑.流程为薄膜加热-高压空气成型(或者吸塑成型)-刀模裁切-已成型薄膜壳片放入模腔-合模,注塑成型-开模,完成总成件,如下图所示:3、IMD(In—Mold Decoration):带有外观效果的IMD薄膜(圈材)被安装在输膜机上,而输膜机则固定在注塑机上,在注塑开模时让薄膜输进模具中间,合模后让胶料注射,让薄膜贴覆在模具上同时与胶料成型。
流程为薄膜输送-薄膜定位,取模件-注塑成型-后处理,清理飞边,如下图所示:二、技术对比1、花纹包覆可行性方面水转印翻边高度(H)可让花纹包覆在300mm范围内不需要考虑R角(R)的锐度可以完全包覆圆柱形基材(如整体注塑方向盘)通过电铸模后加工工艺可对花纹拉伸严重部分加饰,修饰效果较佳可以对大型零件包覆(例如:SGM老别克新世纪IP 1。
3m长,内侧深度超过200mm;德国戴母勒奔驰Smart Car门板外饰整体通过水转印加饰)可以通过面漆工艺及底漆调节去控制最终产品表面光泽度、饱满度、花纹色泽及花纹层次的深度(而不需要重新开发薄膜,重新制版印刷)遇到零件形状变化大而花纹选择偏向有规则性的所谓技术性花纹,虽然包覆不受限制,但部分边角位置可能会出现花纹拉伸而导致外观上有花纹的规则性变弱的情况;但天然花纹(如木纹)的外观表现较佳INS(Film Insert Molding)翻边(H)极限约40mm,但同时R角(R)必须设计在10mm以上;而如果R角(R)在1mm以下,其翻边(H)只可以在5mm以下(而且要取决如零件的整体三维形状)R角考虑要很充分,与花纹包覆的翻边深度要经常做出让步及妥协三维形状变化大的零件,加工难度高,或不能把薄膜包覆完整花纹包覆不到地方(开口部分)可通过刀切露出基材原色,但如果基材上存在注塑缺陷或颜色无法满足外观设计(如金属效果),必须通过单模多片薄膜的insert工艺或电铸模后加工工艺完成(工艺难度增加)对大型零件包覆难度较高或质量难以控制在翻边及R角配合情况下(包覆可行性高),对包覆技术性花纹薄膜的最终外观效果较佳(但可能仍存在轻度花纹拉伸变形)IMD(In—mold Decoration)翻边(H)极限为5mm左右,同时其R角(R)也不能少于10mm由于IMD薄膜比INS薄膜更薄,翻边与R角的考虑与妥协要求更高一般只考虑对平面产品、翻边不大于1mm产品上用这工艺基本上很难做到产品上留下开口部分(如开关板)对大型零件包覆难度较高或质量难以控制对包覆技术性花纹(以上条件容许下)外观效果较佳,但由于薄膜很薄,天然花纹(如木纹)的外观效果则很差有关INS及IMD的定义解释:R角(R)和翻边(H) 的关系(只作参考*)INS:IMD:*每家薄膜供应商、每种外观花纹都有不同的厚度及规格,选择薄膜时必须同时综合考虑零件设计(R与H的关系)、花纹可变形程度及加工可行性等问题。
汽车门的涂装实施步骤
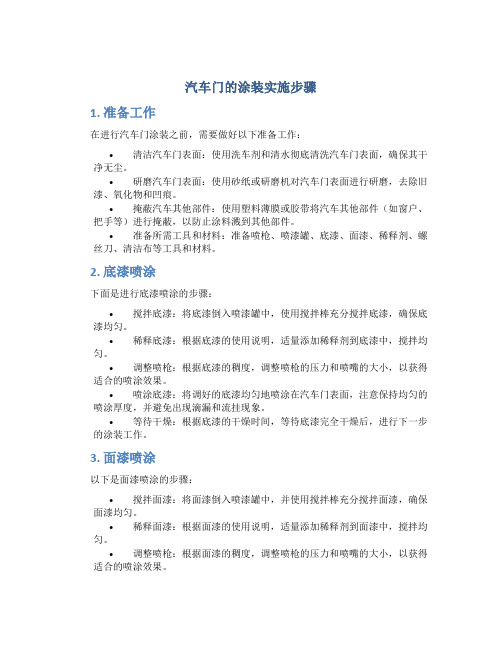
汽车门的涂装实施步骤1. 准备工作在进行汽车门涂装之前,需要做好以下准备工作:•清洁汽车门表面:使用洗车剂和清水彻底清洗汽车门表面,确保其干净无尘。
•研磨汽车门表面:使用砂纸或研磨机对汽车门表面进行研磨,去除旧漆、氧化物和凹痕。
•掩蔽汽车其他部件:使用塑料薄膜或胶带将汽车其他部件(如窗户、把手等)进行掩蔽,以防止涂料溅到其他部件。
•准备所需工具和材料:准备喷枪、喷漆罐、底漆、面漆、稀释剂、螺丝刀、清洁布等工具和材料。
2. 底漆喷涂下面是进行底漆喷涂的步骤:•搅拌底漆:将底漆倒入喷漆罐中,使用搅拌棒充分搅拌底漆,确保底漆均匀。
•稀释底漆:根据底漆的使用说明,适量添加稀释剂到底漆中,搅拌均匀。
•调整喷枪:根据底漆的稠度,调整喷枪的压力和喷嘴的大小,以获得适合的喷涂效果。
•喷涂底漆:将调好的底漆均匀地喷涂在汽车门表面,注意保持均匀的喷涂厚度,并避免出现滴漏和流挂现象。
•等待干燥:根据底漆的干燥时间,等待底漆完全干燥后,进行下一步的涂装工作。
3. 面漆喷涂以下是面漆喷涂的步骤:•搅拌面漆:将面漆倒入喷漆罐中,并使用搅拌棒充分搅拌面漆,确保面漆均匀。
•稀释面漆:根据面漆的使用说明,适量添加稀释剂到面漆中,搅拌均匀。
•调整喷枪:根据面漆的稠度,调整喷枪的压力和喷嘴的大小,以获得适合的喷涂效果。
•喷涂面漆:将调好的面漆均匀地喷涂在已干燥的底漆上,注意保持均匀的喷涂厚度,并避免出现滴漏和流挂现象。
•重复喷涂:根据需要,可以根据面漆的干燥时间进行多次喷涂,以获得更好的涂装效果。
•等待干燥:根据面漆的干燥时间,等待面漆完全干燥后,进行下一步的后续处理工作。
4. 后续处理在涂装完成后,还需要进行以下后续处理工作:•喷漆罐、喷枪清洗:使用稀释剂对喷漆罐、喷枪进行彻底清洗,以防止残留颜料引起堵塞。
•抛光处理:可以使用抛光机对已干燥的涂装表面进行抛光处理,使其更加光滑亮丽。
•去除掩蔽物:谨慎地去除用于掩盖其他部件的塑料薄膜或胶带,防止出现粘连现象。
- 1、下载文档前请自行甄别文档内容的完整性,平台不提供额外的编辑、内容补充、找答案等附加服务。
- 2、"仅部分预览"的文档,不可在线预览部分如存在完整性等问题,可反馈申请退款(可完整预览的文档不适用该条件!)。
- 3、如文档侵犯您的权益,请联系客服反馈,我们会尽快为您处理(人工客服工作时间:9:00-18:30)。
汽車內飾門低成本表面處理技術
(Door Linings Finished at Low Cost)
在使用旋轉模板的注射成型機中,採用PU(聚亞胺脂)工藝使得複合產品的全自動生產具有更好的柔性。
SkinForm成型工藝為在大尺寸熱塑性基材上涂上不同厚度、顏色、的PU層提供了可能,整個過程只需要一次裝夾,不需中間環節便可一步到位。
.
在K 2007 表面處理工藝展上展出的KM 2300-12000 MX型具有旋轉模板的注塑機(製造商:KraussMaffei技術公司,德國)第一次被用來生產大表面積的產品。
這種產品就是由汽車供應商Cadence 創新技術公司開發的汽車內飾門。
這種成型技術已經用於系列產品的生產。
汽車內飾門必須滿足很多應用要求。
當打開、關閉這門或上下車的時侯,相當高的力學載荷就會施加到汽車內飾門表面。
因此,其表面必須具有好的耐磨性能。
而且,汽車買主對汽車內部件的表面設計,令人愉悅性有更高的期望。
就審美而言,例如,這與不同區域的顏色方案,表面光度及連接處形狀的統一性有關。
爲了讓車主感覺更愉悅,內飾表面有明顯的柔和觸感和表面粒度是非常必要的。
汽車內飾門的其他生產工藝
至今,多種方法已被應用到汽車內飾門的生產上,在配置簡單的低檔汽車上,內飾門通常由注射模直接生產,而不考慮產品表面品質,後續也沒有額外的表面處理工序。
但另一方面,在高檔車上,為了提高表面品質內飾門在注射成型后還需要考慮進一步的表面處理。
為達到這一目的,生產中主要使用了三種方法,前兩種即噴漆或覆蓋薄膜,第三種方法有三層結構(即熱塑性塑料基材,表層和介入兩者之間的泡沫層),尤其是高品質的表面可以通過這種方法獲得。
上面所提到的表面處理方法都需要多步工藝,即注射成型后還需要進一步的處理步驟。
一方面增加了空間、機器及模具成本;另一方面,增加了相應的物流成本,例如,運輸、中間存儲成本。
如果僅次區域要進行表面處理(如車窗下方的扶手區),這種部件由兩個產品組成。
在這種情況下,因為兩個部件必須焊接在一起,成本就會增加。
而且這結構還會導致要處理產品的公差和連接處的形狀變化。
帶有旋轉模板的一站式成型工藝
由於PU(聚亞胺脂)塗層被應用到複合件注射成型機上,用這種由KraussMaffei開發的表面處理技術可大大簡化汽車內飾門的表面處理工藝。
(如圖一)
當熱塑性塑料基材成型后開模,中間的旋轉式模板繞竪直軸旋轉180度到第二工位并合模。
PU(聚亞胺脂)通過安裝在第二模腔上的混料噴頭直接注射出來。
成型完成后,旋轉式模盤及上面的模具旋轉90度,在這個位置成型品被送到雕刻機以除去產品上的溢料和料頭。
同時另就機械手會在模具上的某些區域涂上脫模劑。
圖一:具有旋轉式模板結構的生產單元
例子中的汽車內飾門的三個局部區域都涂有PU料,因此每個PU塗層區域在模具上都對用安裝有一個PU混料噴頭(如圖2)。
在輔助系統和轉換單元的作用下可通過計量系統單獨使用單一的混料噴頭。
三個區域的PU工藝成型總共至少需要60秒的成型週期。
圖二:動模側配有(在本例子中)三個PU混料噴頭
MK S/8 ULKP-2KVV+2K型多色混合噴頭的使用(製造商:KraussMaffei)允許要混合的多種顏色直接進料。
使用這種方法可實現顏色選擇的快速轉換,在一
個成型週期中生產出多色產品。
這種多色混合頭在射膠時也可進行無延期顏色變換。
這些技術在Roomster.汽車內飾門表面處理的應用上得到了驗證。
這種方法成型的技術優勢:
用這種工藝方法生產的PU面具有很強的抗刮傷性能和耐摩性,表面結構(如表面磨粒)可從模具型腔表面完整複製下來,且不會發生翹曲變形(如圖三)。
並且產品表面的柔軟度也可通過塗層厚度和選擇合適的材料得到改變。
圖三:這種工藝可進行表面磨粒的精密成型,且不會發生翹曲
而且這種工藝使得用戶在產品設計上有更大的選擇餘地,低黏度的PU在大面積和長流徑的產品上尤其具有優勢。
出於對材料成本效率的考慮,汽車內飾門的所有區域被做成薄壁結構。
然而有選擇的增加局部區域(拉汽車門扶手)的壁厚可獲得理想的觸感。
車門扣手上的彎曲和重疊區可通過注射模中的特殊分離技術獲得,低黏度的PU料需要非常精確的分離技術,這對模具體的製造提出了巨大的挑戰。
超過兩萬次的成型生產驗證了使用這種採用新型分模技術的模具有效性。
這些技術在PU 表面上的應用,直到今天或許都會覺得是不可想像的。
由於採用了具有很高的合模型力和高精度的合模單元,採用表面複合模具成型技術可生產出無飛邊的產品。
關於可獲得的連接寬度,根據目前的應用經驗可以預測,在未來的產品中,接近理想的無連接也是可以預見到的。
PU層可掩蓋熱塑性基材表面胡縮痕,迄今為止,這些縮痕都沒有得到很好的解決,因為在噴漆或貼膜后它們或許變得更加明顯。
在SkinForm工藝中,縮痕被蓋住不會影響外觀面胡品質。
因此在覆蓋有PU區域,設計者可添加大尺寸加強結構,以增加結構穩定性,而不用擔心縮痕影響產品表面品質(如圖四)。
圖四:PU層可掩蓋熱塑性基材表面胡縮痕
經濟上的優勢
相比于早期的成型工藝,注射成型和PU工藝相結合具有顯著的經濟優勢,產品的升級直接在基材注射成型后進行,這取消了此前生產具有光潔表面內飾門所所需要的而幾個生產單元。
由以前的多步生產整合到現在的一站式生產可降低中間產品的物流和儲存成本。
既然無飛邊的產品不需要進行再加工也就降低了成本。
高的生產精度和生產的可重複性減少聊廢品的產生及相關成本。
並且這種工藝良好的生產柔性,增加聊JIT(just in time)生產的可靠性。
在Cadence 創新技術公司,用上述提到的所有方法分別生產機車內飾門,使得該公司有條件對各種工藝的實際成本進行比較。
各種工藝經濟效益評估結果表明,運用Skin-Form工藝生產汽車內飾門的成本位於噴漆和表面貼膜之間。
(如圖五).試驗結果驗證了這種工藝的成本使用效率。
用PU塗層技術的產品表面附加值明顯超過噴漆面或貼模面,但不敵昂貴的三層結構表面處裡工藝。
(如圖六)
圖五:汽車內飾門表面各種成型方法成本比較
圖六:汽車內飾門各種表面處理方式的附加值比較
總結:
PU工藝和注射成型技術相結合降低了有高等級外觀面要求產品的生產成本,其他優點包括生產柔性好、精度高、可重複性工藝技術提高了產品的品質。