可视化技术在机床主轴误差分析中的应用研究
高精度数控刀具视觉检测算法研究及误差分析的开题报告
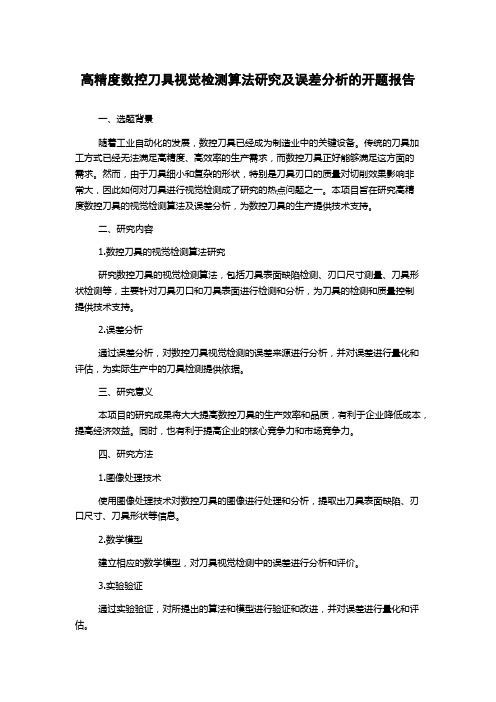
高精度数控刀具视觉检测算法研究及误差分析的开题报告一、选题背景随着工业自动化的发展,数控刀具已经成为制造业中的关键设备。
传统的刀具加工方式已经无法满足高精度、高效率的生产需求,而数控刀具正好能够满足这方面的需求。
然而,由于刀具细小和复杂的形状,特别是刀具刃口的质量对切削效果影响非常大,因此如何对刀具进行视觉检测成了研究的热点问题之一。
本项目旨在研究高精度数控刀具的视觉检测算法及误差分析,为数控刀具的生产提供技术支持。
二、研究内容1.数控刀具的视觉检测算法研究研究数控刀具的视觉检测算法,包括刀具表面缺陷检测、刃口尺寸测量、刀具形状检测等,主要针对刀具刃口和刀具表面进行检测和分析,为刀具的检测和质量控制提供技术支持。
2.误差分析通过误差分析,对数控刀具视觉检测的误差来源进行分析,并对误差进行量化和评估,为实际生产中的刀具检测提供依据。
三、研究意义本项目的研究成果将大大提高数控刀具的生产效率和品质,有利于企业降低成本,提高经济效益。
同时,也有利于提高企业的核心竞争力和市场竞争力。
四、研究方法1.图像处理技术使用图像处理技术对数控刀具的图像进行处理和分析,提取出刀具表面缺陷、刃口尺寸、刀具形状等信息。
2.数学模型建立相应的数学模型,对刀具视觉检测中的误差进行分析和评价。
3.实验验证通过实验验证,对所提出的算法和模型进行验证和改进,并对误差进行量化和评估。
五、预期成果1.数控刀具视觉检测算法。
2.误差分析模型。
3.数控刀具视觉检测系统。
4.数控刀具视觉检测的成果论文。
六、参考文献1.宋泓洋,张洪超. 基于机器视觉的刀具测量方法研究[J]. 机器人,2019,41(05):684-690.2.袁天坤. 刀具尺寸测量的机器视觉系统研究[J]. 神经计算机应用,2020,33(05):130-135.3.Deyang Qu, Cong Wang, Shuai Zhang,et al. Laser distance sensor based automated machine vision system for cutting tool wear and tool condition monitoring[J].Journal of Cleaner Production,2019,234:467-478.。
数控机床误差实时补偿技术及应用

数控机床误差实时补偿技术及应用数控机床误差实时补偿技术是一种通过测量和监控机床的误差,然后通过算法和控制系统来实时修正这些误差的技术。
它可以显著提高机床的加工精度和稳定性,使得加工的零件更加精确和一致。
下面将介绍数控机床误差实时补偿技术的原理、方法和应用。
数控机床误差实时补偿技术的原理是基于机床的误差源和误差特点进行建模,并通过控制系统实时调整机床的运动轨迹来补偿这些误差。
机床的误差主要包括几何误差、动态误差和热误差等。
几何误差是由机床结构、加工刀具和工件等因素引起的,例如导轨的尺寸偏差、传动装置的误差等。
动态误差是由机床运动过程中的惯性力、弹性变形等因素引起的,例如加工过程中的振动和共振等。
热误差是由于机床在工作过程中产生的热源,例如主轴的热膨胀和冷却液的温度变化等。
数控机床误差实时补偿技术的方法一般包括两个步骤:误差测量和误差补偿。
误差测量是通过传感器或测量仪器实时检测机床的误差,并将其反馈给控制系统。
常用的测量方法包括激光干涉法、电容法和光栅尺等。
误差补偿是在控制系统中根据误差测量结果进行数学建模和分析,并根据补偿算法调整控制指令,使得机床的运动轨迹达到期望的精度。
数控机床误差实时补偿技术在实际应用中具有广泛的应用领域。
首先,它可以应用于航空航天领域的高精度零件加工。
航空航天零件对精度和质量要求非常高,数控机床误差实时补偿技术可以有效提高加工精度,降低零件的尺寸偏差和表面光洁度,从而提高航空航天产品的性能和可靠性。
其次,它可以应用于汽车制造领域的模具加工。
模具制造对精度和一致性要求较高,数控机床误差实时补偿技术可以有效减少模具的尺寸和形状偏差,提高模具的加工质量和寿命。
此外,它还可以应用于医疗器械制造、光学仪器加工等领域。
总之,数控机床误差实时补偿技术是一种通过测量和监控机床的误差,并通过控制系统实时调整机床运动轨迹的技术。
它可以显著提高机床的加工精度和稳定性,广泛应用于航空航天、汽车制造、医疗器械等领域,为实现高精度和高质量的零件加工提供了重要的技术手段。
数控机床几何与热误差研究方法综述
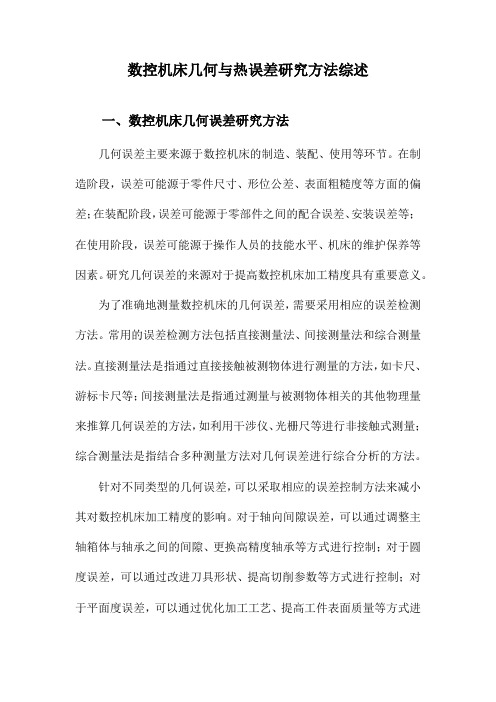
数控机床几何与热误差研究方法综述一、数控机床几何误差研究方法几何误差主要来源于数控机床的制造、装配、使用等环节。
在制造阶段,误差可能源于零件尺寸、形位公差、表面粗糙度等方面的偏差;在装配阶段,误差可能源于零部件之间的配合误差、安装误差等;在使用阶段,误差可能源于操作人员的技能水平、机床的维护保养等因素。
研究几何误差的来源对于提高数控机床加工精度具有重要意义。
为了准确地测量数控机床的几何误差,需要采用相应的误差检测方法。
常用的误差检测方法包括直接测量法、间接测量法和综合测量法。
直接测量法是指通过直接接触被测物体进行测量的方法,如卡尺、游标卡尺等;间接测量法是指通过测量与被测物体相关的其他物理量来推算几何误差的方法,如利用干涉仪、光栅尺等进行非接触式测量;综合测量法是指结合多种测量方法对几何误差进行综合分析的方法。
针对不同类型的几何误差,可以采取相应的误差控制方法来减小其对数控机床加工精度的影响。
对于轴向间隙误差,可以通过调整主轴箱体与轴承之间的间隙、更换高精度轴承等方式进行控制;对于圆度误差,可以通过改进刀具形状、提高切削参数等方式进行控制;对于平面度误差,可以通过优化加工工艺、提高工件表面质量等方式进行控制。
还可以采用补偿技术、自适应控制技术等方法对几何误差进行实时修正和调整。
数控机床几何误差的研究方法涉及多个学科领域,需要综合运用理论分析、实验研究和实际应用等多种手段。
通过对几何误差的研究和控制,可以有效提高数控机床的加工精度和稳定性,为现代制造业的发展提供有力支持。
1. 传统误差分析方法在数控机床几何与热误差研究中,传统误差分析方法主要包括有限元法、边界元法和接触单元法等。
这些方法主要通过对机床结构、刀具和工件的几何形状进行离散化处理,建立数学模型,然后通过求解线性方程组或非线性方程组来计算误差。
有限元法是一种将连续体分割为有限个单元,通过求解各单元上的微分方程组成的积分方程来描述整个系统的运动和变形过程的方法。
机械设计中的仿真与可视化技术应用

机械设计中的仿真与可视化技术应用仿真与可视化技术在机械设计领域中扮演着重要的角色,它们通过模拟和可视化的手段,能够帮助工程师更好地理解和分析设计方案,提高设计效率和产品质量。
本文将探讨机械设计中的仿真与可视化技术应用。
一、CAD软件计算机辅助设计(Computer-Aided Design,简称CAD)软件是机械设计中最基础也是最常用的工具之一。
CAD软件通过创建三维模型,让工程师可以直观地看到设计方案的外形和结构,快速修改和优化设计。
它也提供了相应的仿真功能,例如草图的约束和运动仿真等。
二、有限元分析有限元分析(Finite Element Analysis,简称FEA)是一种常用的仿真技术,它能够将复杂的物理问题离散化为简单的有限元单元,并通过求解有限元方程组,得到物体的应力、变形等物理特性。
在机械设计中,FEA可以通过模拟加载条件和不同材料参数,帮助工程师评估设计方案的结构强度和可靠性。
三、流体力学仿真流体力学仿真(Computational Fluid Dynamics,简称CFD)技术能够通过计算流体运动的方程,预测和分析流体的流动行为和特性。
在机械设计中,CFD可以用于优化流体传输设备和空气动力学设计。
通过仿真,工程师可以评估设计方案的流体流动情况,包括速度、压力和温度分布等。
四、刚体动力学仿真刚体动力学仿真(Rigid Body Dynamics,简称RBD)是一种模拟刚体运动和相互作用的技术。
在机械设计中,RBD可以用于分析机械系统的运动学和动力学性能,例如机构的速度、加速度、力和力矩等。
通过仿真,工程师可以对设计方案进行验证和改进,提高系统的性能和可靠性。
五、虚拟现实技术虚拟现实(Virtual Reality,简称VR)技术通过模拟真实场景和提供互动体验,让用户感受到身临其境的感觉。
在机械设计中,VR技术可以用于展示和评估设计方案,让用户在虚拟环境中与产品进行互动。
它不仅可以提供更直观的体验,还可以发现和解决设计中的问题,提高产品的用户友好性和市场竞争力。
机械系统的可视化与仿真技术研究

机械系统的可视化与仿真技术研究一、引言机械系统的可视化与仿真技术是一门涉及机械工程、计算机图形学和人机交互等多学科交叉的领域。
随着计算机技术的飞速发展,可视化和仿真技术在机械制造、维修和教育等领域的应用日益广泛。
本文旨在探讨机械系统的可视化与仿真技术的研究进展和应用前景。
二、机械系统的可视化技术机械系统的可视化技术主要基于计算机图形学和虚拟现实技术,通过三维模型、动画和交互界面等手段将机械系统的结构、运动和功能等信息直观呈现给用户。
可视化技术可以帮助用户更好地理解和分析机械系统,提高工作效率和决策准确性。
在机械系统的可视化技术中,三维建模是基础和关键环节。
通过对机械系统进行三维建模,可以准确地还原其外观和内部结构。
目前,常用的三维建模软件有SolidWorks、CATIA和AutoCAD等。
这些软件提供了丰富的建模工具和材质库,使得用户可以根据实际需求创建高质量的机械模型。
除了三维建模,纹理映射和光照模拟等技术也对机械系统的可视化效果起到重要作用。
纹理映射可以为机械模型添加细节和真实感,如表面纹理、颜色和透明度等。
光照模拟则可以模拟不同光源对机械系统的照明效果,使得可视化效果更加逼真和自然。
另外,交互界面是机械系统可视化的重要组成部分。
通过合理设计的交互界面,用户可以自由地浏览、操作和分析机械系统。
目前,常用的交互界面包括鼠标、键盘、触摸屏和虚拟现实设备等。
这些交互设备可以模拟真实的物理操作,提供更真实和沉浸式的用户体验。
三、机械系统的仿真技术机械系统的仿真技术是通过计算机模型和数值计算方法来模拟和预测机械系统的运动、力学和响应等行为。
仿真技术可以帮助用户快速评估和优化机械系统的设计和性能,并减少实际试验的时间和成本。
在机械系统的仿真技术中,刚体动力学和多体动力学是常用的数学模型。
刚体动力学可以用来描述机械系统的运动和力学行为,通过求解运动方程和约束方程可以得到系统的运动轨迹和受力情况。
多体动力学则可以描述机械系统中多个刚体之间的相互作用和力学行为,包括碰撞、摩擦和接触等。
数控加工过程的可视化研究
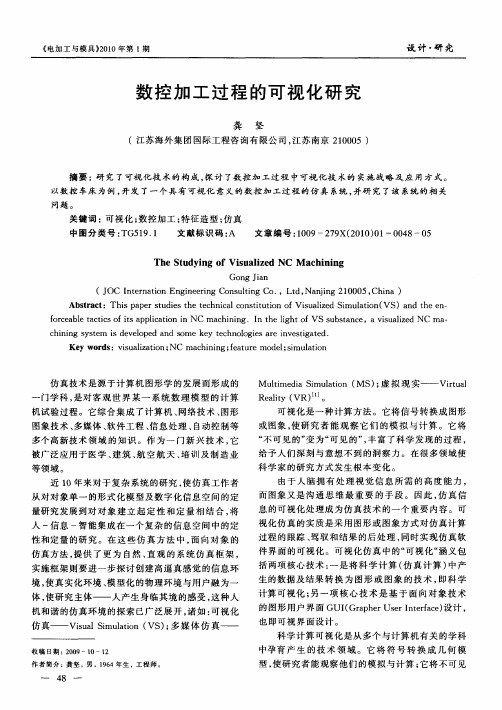
由于人 脑拥 有 处 理视 觉信 息 所需 的高 度能 力 ,
而 图象又 是沟 通思 维 最 重要 的手 段 。 因此 , 真信 仿
息 的可视 化处理 成为 仿真技 术 的一 个重要 内容 。可
人 一信 息 一智能集 成在 一个复 杂 的信 息空 间中的定
性 和定量 的研究 。在 这 些 仿 真方 法 中 , 向对象 的 面
以数 控车床 为例 , 开发 了一个具有 可视化 意义 的数控加 工过程 的仿 真 系统 , 并研 究 了该 系统 的相 关
问题 。
关键词 : 视化 ; 控加工 ; 可 数 特征造 型 ; 真 仿 中图分 类号 : G 1 . T 591 文 献标识码 : A 文章 编号 :0 9 7 X(0 0 O —0 4 10 —2 9 2 1 ) 1 0 8—0 5
视 化仿真 的实质 是采用 图形 或 图象 方式对 仿真计算
过 程 的跟 踪 、 驾驭 和结 果 的后处理 , 同时实 现仿真 软
仿真方法 , 提供 了更 为 自然 、 直观 的 系统 仿 真框 架 , 实施框架 则要进 一步探 讨创建 高逼真感 觉 的信息环 境, 使真 实化环境 、 模型 化 的物理 环境 与用户 融为一 体, 使研 究主体—— 人产 生身 临其境 的感受 , 这种人 机和谐 的仿真环 境 的探 索 已广 泛展 开 , 诸如 : 可视化 仿真—— Vi a Smuai V ) 多 媒 体仿 真— — s li l o u t n( S ;
的 图 形 用 户 界 面 G ( a h r e tr c) 计 , UIGrp e Usr nef e设 I a 也 即可视 界面设 计 。
科学 计算 可视化是 从多个 与计 算机有 关 的学 科 中孕育 产 生 的技 术 领 域 。 它将 符 号转 换 成 几 何 模
车床主轴轴颈精度的可视化分析方法
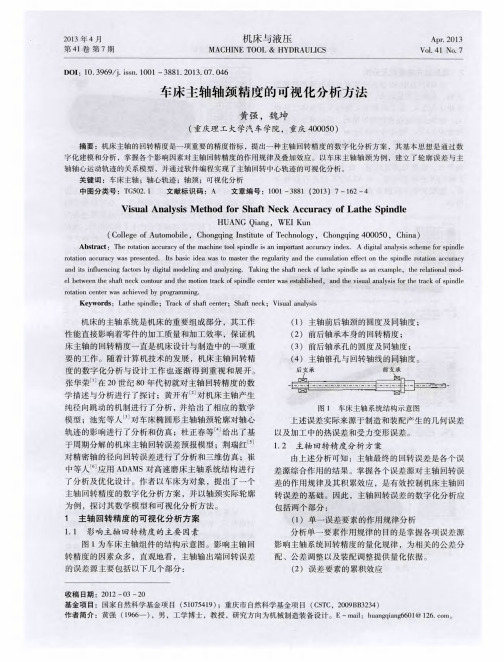
极值点 ,2个斜 率 无穷 大 点 。故在采点 密度较 大 的
情况下 ,第 i 个 接 触点 处 的斜率 k 为:
=
图 4 回转 中心 坐 标 系 的建 立
大 。这样 就得 到了 n 个 测量点到实际 回转 中心 的距离 值 r I = +△ r 。设第 一个采 样 点对应 的旋 转角度 为 0 ,第 i 个采样 点对应 的角度 是 0 ( i =1 ,2 ,3 ,… ,
图 2 车 床 主 轴 轴 颈 的 运 动 及 其 特 点
Q=∑ =∑ ( r i — R — a c o s 0 一 b s i n 0 ) = m i n
( 2 )
式 中 :Q是误差 函数 ,当误差 函数取最小值 时 ,最小 二乘圆的圆心坐标为 :
r
s i n
2
式 中 :占 ( 1 ,2 ,3 ,…,n )是 各 采样 点 到最 小 二 乘圆沿最小二乘 圆半径方 向的偏差 ;R是 最小二乘
< n3 < n4。
当点 n , 斜率 后 . 一 ∞时有 :
转中 l f , 与最 小二 乘 圆 l f , 的距 离 应远 小 于最 小二 乘 圆
半径 。
作者 以车床主轴 的轴颈轮廓 为例 ,探讨 其作 用规
律 分 析 的实 现 方 法 。
2 单一 支承 回转 精度 数 学模型 的 建立 2 . 1 轴颈轮 廓 与其 回转 中心 的 关 系
图 2为车床主轴轴颈 的运动 与特点示 意图。在 单
一
误差要 素分析 中 ,其 他误 差项被设置为零 ,此时 的 主轴 支承可视为滑动轴承 。车削加工 中主轴受力方 向
恒 定 ,所 以接触点为支承上 的一个 恒定点 A 。在这 种
机械可视化技术的研究与应用
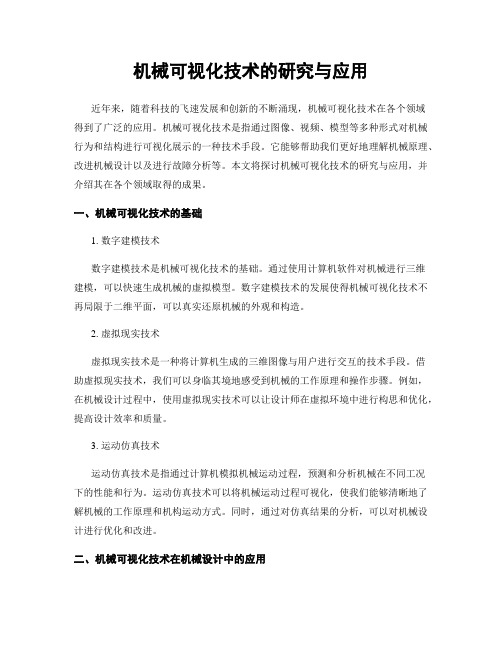
机械可视化技术的研究与应用近年来,随着科技的飞速发展和创新的不断涌现,机械可视化技术在各个领域得到了广泛的应用。
机械可视化技术是指通过图像、视频、模型等多种形式对机械行为和结构进行可视化展示的一种技术手段。
它能够帮助我们更好地理解机械原理、改进机械设计以及进行故障分析等。
本文将探讨机械可视化技术的研究与应用,并介绍其在各个领域取得的成果。
一、机械可视化技术的基础1. 数字建模技术数字建模技术是机械可视化技术的基础。
通过使用计算机软件对机械进行三维建模,可以快速生成机械的虚拟模型。
数字建模技术的发展使得机械可视化技术不再局限于二维平面,可以真实还原机械的外观和构造。
2. 虚拟现实技术虚拟现实技术是一种将计算机生成的三维图像与用户进行交互的技术手段。
借助虚拟现实技术,我们可以身临其境地感受到机械的工作原理和操作步骤。
例如,在机械设计过程中,使用虚拟现实技术可以让设计师在虚拟环境中进行构思和优化,提高设计效率和质量。
3. 运动仿真技术运动仿真技术是指通过计算机模拟机械运动过程,预测和分析机械在不同工况下的性能和行为。
运动仿真技术可以将机械运动过程可视化,使我们能够清晰地了解机械的工作原理和机构运动方式。
同时,通过对仿真结果的分析,可以对机械设计进行优化和改进。
二、机械可视化技术在机械设计中的应用机械可视化技术在机械设计过程中起到了重要的作用。
首先,通过对机械的三维建模和虚拟现实仿真,可以在设计阶段发现和解决问题,减少成本和风险。
其次,借助机械可视化技术,设计师可以直观地了解机械的工作原理和结构,有助于优化设计。
在机械设计领域,机械可视化技术已经广泛应用于汽车设计、航空航天设计、工业机器人设计等方面。
以汽车设计为例,通过机械可视化技术,设计师可以在虚拟环境中对汽车进行外观设计、车内布局等方面进行优化。
同时,通过运动仿真技术,可以模拟车辆在不同路况下的操控性能,为汽车改进和优化提供科学依据。
三、机械可视化技术在教育中的应用随着机械行业的发展,对机械人才的需求也越来越高。
机械工程中的可视化设计与优化分析研究
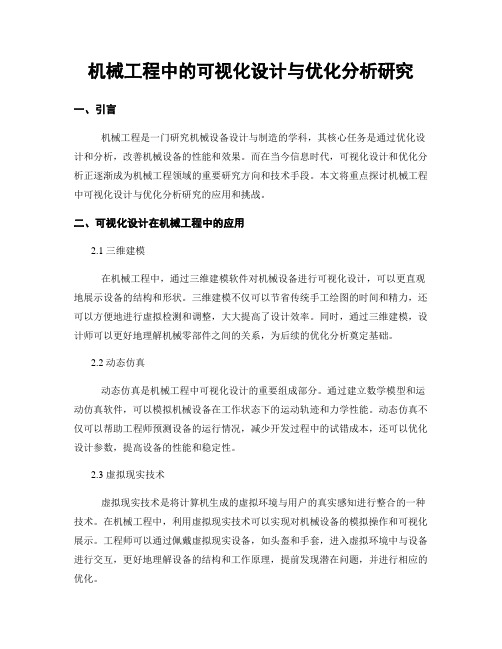
机械工程中的可视化设计与优化分析研究一、引言机械工程是一门研究机械设备设计与制造的学科,其核心任务是通过优化设计和分析,改善机械设备的性能和效果。
而在当今信息时代,可视化设计和优化分析正逐渐成为机械工程领域的重要研究方向和技术手段。
本文将重点探讨机械工程中可视化设计与优化分析研究的应用和挑战。
二、可视化设计在机械工程中的应用2.1 三维建模在机械工程中,通过三维建模软件对机械设备进行可视化设计,可以更直观地展示设备的结构和形状。
三维建模不仅可以节省传统手工绘图的时间和精力,还可以方便地进行虚拟检测和调整,大大提高了设计效率。
同时,通过三维建模,设计师可以更好地理解机械零部件之间的关系,为后续的优化分析奠定基础。
2.2 动态仿真动态仿真是机械工程中可视化设计的重要组成部分。
通过建立数学模型和运动仿真软件,可以模拟机械设备在工作状态下的运动轨迹和力学性能。
动态仿真不仅可以帮助工程师预测设备的运行情况,减少开发过程中的试错成本,还可以优化设计参数,提高设备的性能和稳定性。
2.3 虚拟现实技术虚拟现实技术是将计算机生成的虚拟环境与用户的真实感知进行整合的一种技术。
在机械工程中,利用虚拟现实技术可以实现对机械设备的模拟操作和可视化展示。
工程师可以通过佩戴虚拟现实设备,如头盔和手套,进入虚拟环境中与设备进行交互,更好地理解设备的结构和工作原理,提前发现潜在问题,并进行相应的优化。
三、优化分析在机械工程中的应用3.1 结构优化结构优化是指在保证机械设备稳定性和可靠性的前提下,通过调整零部件的材料、形状和连接方式等参数,使得设备的重量和体积最小化。
通过优化设计,可以降低设备的成本和能耗,并提高设备的运行效率。
3.2 流体优化在涉及流体传输的机械设备中,通过优化流道形状和流体流动参数,可以提高设备的传输效率和降低输运损耗。
流体优化可以通过数值模拟和实验验证相结合的方式进行,通过可视化的分析结果,可以直观地看到流体的流动过程和性能指标,为优化设计提供有力支持。
如何进行测量精度评定与可视化分析

如何进行测量精度评定与可视化分析在现代科技发展的背景下,测量精度评定与可视化分析成为了工程设计和研究领域中不可或缺的一环。
准确的测量和数据分析是保证产品质量和研究结果可信度的关键。
本文将介绍如何进行测量精度评定与可视化分析,并探讨其在不同领域的应用。
一、测量精度评定的方法测量精度评定是评估测量结果与真实值之间的接近程度。
常见的测量精度评定方法包括:1. 绝对误差评定:通过与已知的标准进行比较,计算出测量结果的绝对误差。
2. 相对误差评定:通过计算测量结果与预期结果之间的差异百分比来评估精度。
3. 重复性评定:通过进行多次重复测量,计算测量结果之间的差异,从而评估测量仪器的重复性。
4. 繁衍误差评定:通过对测量仪器的误差来源进行分析,探究造成误差的原因。
二、可视化分析的工具与方法可视化分析是将测量数据以可视化的方式呈现,以便更好地理解和分析数据。
以下是一些常用的可视化分析工具与方法。
1. 折线图:将时间、测量数值等作为x轴,将测量结果作为y轴,通过曲线的走势来展示测量数据的变化趋势。
2. 柱状图:适用于比较不同类别的测量结果,可以清晰地显示不同类别之间的差异。
3. 散点图:用于展示两个变量之间的关系,可以帮助发现数据中的模式和趋势。
4. 热力图:通过使用颜色编码来表示数据的密度和分布情况,可用于分析大数据集中的模式和异常。
5. 三维图形:可以展示三个或更多维度的数据,帮助理解更复杂的关系。
三、测量精度评定与可视化分析在工程设计中的应用测量精度评定和可视化分析在工程设计中具有广泛的应用。
如在建筑设计中,通过使用测量工具和可视化分析技术,可以测量和分析建筑物的尺寸、重量和形状,以确保设计的精确性和符合规范要求。
此外,在制造业中,测量精度评定和可视化分析也可以用于检测产品尺寸、模具精度等方面,从而保证产品质量和工艺流程的稳定性。
四、测量精度评定与可视化分析在科研领域中的应用测量精度评定和可视化分析在科研领域中也扮演着重要的角色。
基于人工智能的机床主轴故障诊断研究

基于人工智能的机床主轴故障诊断研究在制造业的心脏——机床中,主轴是其跳动的灵魂。
一旦这个灵魂出现故障,整个生产线就会陷入瘫痪,就像一场没有指挥的交响乐,乐手们各自为战,无法演奏出和谐美妙的旋律。
因此,对机床主轴的故障诊断显得尤为重要,它就像是医生对病人的诊断一样,准确而及时地发现问题并给出解决方案。
传统的故障诊断方法往往依赖于经验丰富的工程师,他们通过听、看、摸来判断机床的状态。
然而,这种方法就像是盲人摸象,只能了解局部情况,而且容易受到主观因素的影响。
随着科技的发展,人工智能技术如同一把锐利的钥匙,为我们打开了新世界的大门。
它能够从海量的数据中学习规律,像是一位拥有千里眼和顺风耳的超级侦探,能够迅速准确地定位问题所在。
人工智能在故障诊断中的应用,可以说是一场革命性的变革。
它不仅提高了诊断的准确性,还大大缩短了诊断时间。
例如,通过机器学习算法训练出的模型,可以在几分钟内完成原本需要数小时甚至数天才能完成的诊断工作。
这就像是用火箭代替了马车,将我们带入了一个高速高效的新时代。
然而,人工智能并非万能的。
它的应用也面临着一些挑战和问题。
首先,高质量的数据是人工智能发挥作用的基础。
如果输入的数据质量不高,那么输出的结果也难以令人满意。
这就像是用劣质食材做出的美食,无论厨师技艺多么高超,最终的味道也难以让人满意。
其次,人工智能的解释性问题也是一个重要的挑战。
很多时候,即使是专家也难以解释为什么模型会得出这样的结果。
这就像是黑箱操作,虽然能得到结果,但过程却充满了不确定性。
此外,人工智能的应用还可能带来一系列的社会影响。
例如,它可能会取代一部分传统的工作岗位,引发就业市场的动荡。
同时,过度依赖人工智能也可能让我们丧失一些基本的技能和判断力。
这就像是在自动驾驶汽车普及后,我们可能会忘记如何手动驾驶一样。
综上所述,基于人工智能的机床主轴故障诊断研究是一项充满前景和挑战的工作。
我们需要在享受其带来的便利的同时,也要警惕其可能带来的风险和问题。
数控机床整机动力学性能可视化分析与仿真
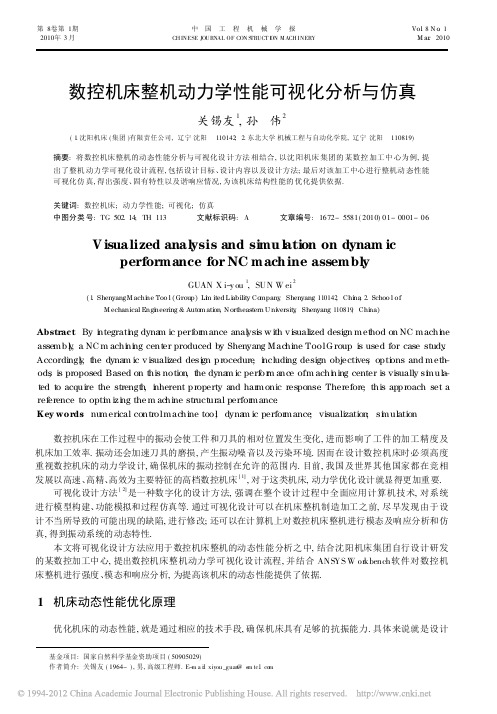
第8卷第1期2010年3月中 国 工 程 机 械 学 报CH INESE JOURNAL OF CON S TRUCT I ON MACH INERY Vo.l 8N o .1 M ar .2010基金项目:国家自然科学基金资助项目(50905029)作者简介:关锡友(1964-),男,高级工程师.E-m a i :l xiyou _guan @s m tc.l co m数控机床整机动力学性能可视化分析与仿真关锡友1,孙 伟2(1.沈阳机床(集团)有限责任公司,辽宁沈阳 110142; 2.东北大学机械工程与自动化学院,辽宁沈阳 110819)摘要:将数控机床整机的动态性能分析与可视化设计方法相结合,以沈阳机床集团的某数控加工中心为例,提出了整机动力学可视化设计流程,包括设计目标、设计内容以及设计方法;最后对该加工中心进行整机动态性能可视化仿真,得出强度、固有特性以及谐响应情况,为该机床结构性能的优化提供依据.关键词:数控机床;动力学性能;可视化;仿真中图分类号:TG 502.14;TH 113 文献标识码:A 文章编号:1672-5581(2010)01-0001-06V isualized anal ysis and si mu l ati on on dynam icperformance for NC machine assembl yGUAN X i-y ou 1,SUN W ei 2(1.Shenyang M achi ne Too l (Group)Li m ited L i ability Co mpany ,Shenyang 110142,Chi na ;2.Schoo l ofM echanical Engi neering &Auto m ati on ,N ortheastern U ni versity ,Shenyang 110819,Chi na)Abstract :By i n tegrati n g dyna m ic perf or m ance anal y sis w ith v isualized design m et hod on NC m achi n e assem bl y ,a NC m achi n i n g cent er produced by Shenyang M achine ToolG roup is used for case study .Accordingl y ,t he dynam ic v isualized des i g n procedure ,i n cluding design objectives ,opti o ns and m eth -ods ,is proposed .Based on t his notion ,t he dyna m ic perf or m ance ofm achi n ing center is visually s i m ula -t ed t o acquire the strengt h ,i n herent property and har m onic response .Therefore ,this approach set a ref erence to opti m iz i n g the m achine struct ural perfor m ance .Key words :nu m erical controlm achine too;l dyna m ic perfor m ance ;visualization ;s i m ulation数控机床在工作过程中的振动会使工件和刀具的相对位置发生变化,进而影响了工件的加工精度及机床加工效率.振动还会加速刀具的磨损,产生振动噪音以及污染环境.因而在设计数控机床时必须高度重视数控机床的动力学设计,确保机床的振动控制在允许的范围内.目前,我国及世界其他国家都在竞相发展以高速、高精、高效为主要特征的高档数控机床[1],对于这类机床,动力学优化设计就显得更加重要.可视化设计方法[2]是一种数字化的设计方法,强调在整个设计过程中全面应用计算机技术,对系统进行模型构建、功能模拟和过程仿真等.通过可视化设计可以在机床整机制造加工之前,尽早发现由于设计不当所导致的可能出现的缺陷,进行修改;还可以在计算机上对数控机床整机进行模态及响应分析和仿真,得到振动系统的动态特性.本文将可视化设计方法应用于数控机床整机的动态性能分析之中,结合沈阳机床集团自行设计研发的某数控加工中心,提出数控机床整机动力学可视化设计流程,并结合ANSYS W or kbench 软件对数控机床整机进行强度、模态和响应分析,为提高该机床的动态性能提供了依据.1 机床动态性能优化原理优化机床的动态性能,就是通过相应的技术手段,确保机床具有足够的抗振能力.具体来说就是设计中 国 工 程 机 械 学 报第8卷 出的机床具有抵抗受迫振动与自激振动的能力,能对工件进行稳定而精确的加工.机床对受迫振动的抗振能力主要在于避开共振,在设计时需要控制机床的固有频率远离激振频率.机床对自激振动的抗振能力,主要在于在切削颤振作用下机床抵抗再生颤振能力(或动态响应)的大小,目前公认的以稳定性极限切削宽度b li m 作为机床再生颤振的稳定性判据.对数控机床进行动态性能优化设计主要依据的原理包括模态分析、动响应分析.1.1 模态分析所谓模态分析法,是凭借振动系统的模态参数来对数控机床的动态性能进行分析、预测、评价和优化.而将振动系统的模态参数辨识出来是模态分析过程中的重要环节,辨识模态参数需要求解系统的特征向量和特征值(主振型和固有频率).为了对数控机床整机系统进行模态分析,必须将具有无限个自由度的机床离散成若干个质量集中的子结构,构建符合实际情况的机床动力学模型是对其进行模态分析的基础.具有n 个自由度的振动系统,其有阻尼的受迫振动运动方程为M X ##+C X #+K X =P (1)式中:M,C,K 分别为系统质量矩阵、阻尼矩阵和刚度矩阵;X 为位移响应向量;P 为激励力向量.振动系统的固有频率和主振型是系统的自然属性,必须通过研究无阻尼自由振动来求解.求出振动系统的固有频率得X 20和振幅列阵A .n 自由度振动系统就有n 个固有频率X 01,X 02,,,X 0n 以及n 个对应的主振型A (1),A (2),,,A(n ).1.2 动态响应振动系统在动态力P 作用下,处在受迫振动或自激振动或二者兼有的情况时,可以用模态分析方法来辨识振动系统的动态响应.随着振动系统阻尼情况的不同,分析处理系统动态响应的方法也不同,而机床系统的阻尼情况是很复杂的,通常是各种阻尼情况的综合(包括干摩擦阻尼、液体阻尼、粘性阻尼和结构阻尼等).它们所生成的阻尼力性质各不一样,由这些阻尼系数构成的阻尼矩阵无法用实模态矩阵来解耦.振型阻尼情况也称小阻尼情况.当系统的各阶模态阻尼比N r 较小(一般认为小于0.2),各阶固有频率不十分接近时,可以简便地略去模态阻尼矩阵中的非对角元素,成为对角矩阵,接触阻尼耦合.实践证明,这种简化方法可以获得很好的近似解.下面以振型阻尼为例,分析数控机床系统动态响应的求解方法[3].机床系统的模态方程为M Q ##+C Q #+K Q =Q(2)式中:Q 为模态矩阵.如果不存在耦合,就可以写出n 个独立方程,当第r 阶模态阻尼系数C r =2N r M r X 0时,模态方程为M r q ##r +2N r M r X 0q #r +K r q r =Q r ,r =1,2,,,n (3)式中:q r 为r 阶模态向量,根据此方程的解得出机床系统的模态交叉动柔度为P hj =E n r =1A (r )h A (r )j K r (1-K 2r +2N r K r )(4)式中:A (r )h ,A (r )j 分别为结构h ,j 的r 阶振幅;K r 为频率比.根据求出的第r 阶模态动柔度可以看出,机床系统动态响应的最主要的影响因素仍然是系统主振型和固有频率.因此可以看出,系统主振型和固有频率在机床整机系统动态性能优化中的重要作用,于是,研究数控机床整机系统的主振型和固有频率不但可以优化机床抵抗受迫振动的能力,同时也提高机床抵抗自激振动的水平.2 数控机床整机可视化设计数控机床是典型的机电一体化产品,采用传统的动力学设计方法,可概括为图1所示的设计流程.从图中可以看出,传统机床动力学设计方法以设计者为中心,设计者的水平影响机床的质量,设计过程出现的设计周期长、效率低、人力物力成本大、在反复加工装配过程中所产生无法预测误差等缺陷,已无法适应激烈的市场竞争,取而代之的是周期短、效率高、成本低以及获得高精度产品的设计方法.2第1期关锡友,等:数控机床整机动力学性能可视化分析与仿真图1 传统动力学设计方法流程图F i g .1 F lo w of trad iti onal dyna m ical design m et hod可视化设计方法以/可视0为手段,可以使设计者在产品加工出来之前看到产品各方面性能,进而对产品的缺陷进行修改、优化,大大缩短了设计周期,提高了生产效率.可视化设计的具体内容包括加工过程可视化、装配过程可视化、运动学可视化、动力学可视化、工作过程可视化和控制过程可视化六个方面.由于动态性能是数控机床在设计过程中所要考虑的重要指标,因此对数控机床整机进行动力学可视化分析,以获得振动系统的强度、固有频率、主振型和响应情况等指标,为提高数控机床的抗振能力提供依据.数控机床整机动力学可视化设计的内容首先是确定载荷分布并对整机强度进行验证,保证设计的模型在强度和刚度方面是满足设计要求的;其次是对数控机床整机模型进行模态分析,获得固有动态特性,这是优化机床动态性能的关键;最后在给定激励条件下确定系统的响应情况,流程如图2所示.图2 动力学可视化设计方法流程图F i g .2 Flo w of dyna m ical visual desi gn m et hod3 数控机床整机动态性能优化仿真研究要对数控机床整机动态性能进行研究,根据图2所示的动力学可视化流程,可以分成三大部分,创建数控机床整机动力学模型,对所创建的模型进行动力学可视化仿真,最后进行结果评价.3.1 创建数控机床整机动力学模型数控机床是集电子、机械、计算机、控制、传感器以及液压气动于一体的复杂的设备,对数控机床建模首先要对其进行适当的简化.本文建立的某数控加工中心模型包括床身、立柱、横梁、导轨、主轴箱以及传动轴等6部分,简化了螺栓和圆角,省略了电机.利用Pr o /E 软件完成实体建模,将模型导入到ANSYS W o r kbench(AW B ),A W B 会自动识别其几何特征、尺寸大小以及装配关系.对于数控加工中心这种复杂的模型结构且零部件较多的装配体,自动识别会发生错误,需要手动修正.对修正后的动力学模型进行前处理,包括定义材料属性、划分网格、对机床结合部的处理(定义接触类型)、添加边界条件和约束.模型中采用灰铸铁和结构钢两种材料,并且所有零部件的硬度属性都设置为柔性.模型的网格数量为79810,节点数为175858.由于本文着重对机床整机进行研究,因此所有的结合部接触类型都设定为固定接触.边界条件为机床底座的全约束,在机床主轴端面上加载一个集中力,同时添加惯性力.3.2 数控机床整机动力学可视化仿真3.2.1 强度校核从AWB 求解器得到的结果可以看出,机床整机大部分区域等效应力分布较为均匀,应力值低于5MPa .但是在机床导轨结合部位有应力集中的现象,最大应力值也出现在该部位,如图3所示.应力集中的原因主要是模型导轨过短,与支架接触面积过小,从实际角度出发,由于机床导轨制造误差,导轨表面微观不平度导致实际接触面积变小出现应力集中现象.通过对数控机床整机模型全变形云图的观察,如图4所示,整机在主轴箱位于最高处时,主轴处变形较大,变形量在0.03158~0.04734mm 之间,横梁部分次之,变形量在0.021053~0.031580mm 之间,底座与立柱的变形量最小,3中 国 工 程 机 械 学 报第8卷 基本在0.021mm 以下.机床变形的规律是从底座到主轴端处,变形量逐渐增大.机床底座受到全约束,主轴为自由端并且受载荷,这与悬臂梁结构受力变形情况相似.图3 数控机床模型应力最大处放大云图F ig .3 Extended figure of m axi mum 图4 机床模型静力分析全变形云图F ig .4 De f or m a tion of sta tic通过对模型的强度分析,得到关于机床强度和刚度的信息.机床整机等效强度均匀,但是在导轨结合处有应力集中现象,应改善导轨与其支架的连接结构,消解应力集中现象.3.2.2 模态分析本文研究的数控机床属于高速加工中心,最高工作转速可达到12000r #m i n -1,为了包含这一转速下的频率,所求解的固有频率阶数要比一般数控机床多,因此本文设置求解前10阶固有频率.将10阶固有频率及振型描述列于表1,并绘制10阶固有频率柱状图如图5所示.表1 模型10阶固有频率及振型描述Tab .1 Na tura l frequencies and v ibra tion m odes described of ten orders阶数固有频率/H z 振型描述145.41整机沿x 轴摆动256.54整机由上到下向前倾摆动396.94主轴部分与其他部分向前摆动,但振动方向相反4105.89机床整体绕y 轴扭转5167.10机床立柱部分沿着x 轴相对摆动,主轴部分左右摆动,顶端摆动幅度大于刀具端6170.25与第5阶振型接近7193.93立柱同向摆动8200.87立柱同向摆动,主轴部分左右摆动,其摆动幅度由中部向两端扩大9224.99主轴部分的摆动,摆动幅度很大,由中部向两端扩大10243.03立柱部分的相对摆动,摆动幅度很大从前10阶固有频率的结果来看,除了第4阶和第5阶固有频率有超过50H z 的频率差值,其他临阶图5 机床前10阶固有频率柱状图F i g .5 H istogra m of ten orders nat ural f requ e n cies固有频率值相差较小,而且5,6阶固有频率值还很接近.从固有频率柱状图中可以看出,机床前10阶固有频率基本上呈均匀上升趋势,这就使机床确定工作转速时很难避开共振区域.从振型图上看,第1阶振动位移较小,第2阶和第3阶位移接近并且较大,第4阶振动位移小,第5)9阶振动位移都很大,并且第5阶振动位移是最大的,第10阶振动位移不大,但是机床机身发生变形的面积大.针对本文研究的数控加工中心,要获得更好的动态性能,机床的稳定加工工作频率最好确定在第4阶固有频率和第5阶固有频率之间.3.2.3 谐响应分析任何持续的周期载荷将在结构系统中产生持续的周期响应(谐响应).数控机床在实际加工过程中,切削力及其他激励力以动载荷的形式周期性作用于结构.模态分析可以得到4第1期关锡友,等:数控机床整机动力学性能可视化分析与仿真 整机振型和固有频率,但这仅表示机床各部位的相对振动情况,而外力激励下各阶振型对机床振动大小的作用是不同的,因此对整机进行谐响应分析就能更清楚地看出在动态干扰激励下机床结构的抗振性能.谐响应分析能预测系统结构的持续动力特性,能够验证设计能否成功克服共振、疲劳及其他受迫振动引起的有害效果.在A W B 中选择谐响应分析模块,设定模型的工作转速为6000~12000r #m in -1,机床的工作频率为100~200H z .设定扫频范围为67~233H z ,频率点步长为80.在机床主轴外圆柱表面,分别插入100,133,167,200H z 时机床主轴全变型以及x,y,z 三个方向上的变形结果.数控机床模型在x,y ,z 方向的位移响应幅频曲线分别如图6所示.图6 数控机床在x,y,z 方向位移响应幅频曲线Fig .6 Cu rve of d isplace m en t a m p litude -frequ e n cy response a l ong x,y and z d irection s on NC m achine通过观察整机位移响应曲线,综合机床主轴在主要工作频率的位移响应数据(如表2所示),可以看出,在133H z ,即机床主轴工作转速在8000r #m i n -1时,主轴最大最小全变形量差值只有0.012742mm,说明机床在该频率工作下,主轴振动最小,适宜工作,这与模态分析的结论相一致.表2 主轴工作频率下位移谐响应Tab .2 D is p lace m ent ha r m onic response of spind le at w ork i ng frequency频率/H z极值全位移/mm 方向位移/mm x y z 100最小值0.291042.4237-0.40292-0.38904最大值0.546424.5264@10-2-0.28196-5.8834@10-2133最小值 2.1682@10-2-1.0688@10-2-2.9206@10-2-1.9615@10-2最大值 3.4424@10-24.9704@10-3-2.0186@10-2-3.2276@10-5167最小值 3.8425@10-3-0.13447-3.2456@10-2-3.175@10-2最大值0.137376.9857@10-2 3.2656@10-25.2029@10-2200最小值1.8544@10-25.3694@10-3-2.0106@10-2-5.0366@10-2最大值0.145370.141882.2195@10-23.6097@10-24 结论数控机床整机动态性能分析是机床抗振性和稳定性研究的基础,将可视化设计方法引入机床的动态性能研究对提高机床抗振性以及加工稳定性有重要意义.本文从理论分析出发,针对数控机床整机动力学5中国工程机械学报第8卷6可视化展开研究,主要工作包括:(1)分析并归纳了数控机床整机抗振性能的影响因素,明确了固有特性是影响机床受迫振动的关键因素;在均衡各阶模态中的能量分布和阻尼分配的情况下,降低各阶模态柔度,增大各阶模态阻尼比,可以提高机床抵抗自激振动的能力.(2)将可视化设计方法与机床整机动态性能分析相结合,提出了机床整机动力学可视化设计流程图,包括目标,内容以及方法.(3)以沈阳机床集团的某数控加工中心为例,按照本文提出的动力学可视化设计流程,对整机进行了强度、模态及谐响应仿真研究,得出了整机应力集中位置和适宜的工作转速为8000r#m i n-1.证明了可视化设计方法和流程的有效性,为机床的整机设计提供依据.参考文献:[1]夏伯雄.数控机床的产生、发展及其趋势[J].精密制造与自动化,2008(1):6-7.X I A B oxi ong.Th e devel opm ent trend and generati on ofNC m ach i ne tool[J].Preci s i on M anu f act u ri ng and Auto m ation,2008(1):6-7.[2]孙伟,任朝晖,于涛,等.现代机械可视优化设计方法研究[J].东北大学学报:自然科学版,2007,28(3):385-388.SUN W e,i REN Zhaohu,i YU Tao,et a.l The opti m i zati on m et hod ofm odern m ach i n ery v i sual des i gn[J].Jou rnal ofNortheastern Un i versity:Na-t u ral Science,2007,28(3):385-388.[3]GAR I TAONANDI A I,FERNANDES M H,ALBIZ URI J.Dyna m icm odel of a centerl ess grindi ng m ach i n e based on an updated FE m odel[J].In-tern ati on al Journa l ofM ach i ne Tool s&M anu fact u re,2008,48(7):832-840.#下期部分文章摘要预报#遥操作机器人位置反馈型H]双向伺服控制系统研究赵丁选,韩成浩针对目前遥操作机器人双向伺服控制策略中存在的主、从手间位置跟随性差,以及抓取刚性物体时主手所受反馈力冲击过大等问题,提出了一种位置反馈型H]双向伺服控制算法.同时,采用状态观测器消除操纵杆液压系统动态特性差异及系统的阻尼、摩擦力、惯性阻力等干扰因素.搭建二自由度同构型主从摇操作系统试验台,并进行了现场试验.结果表明,所提出的位置反馈型H]双向伺服控制策略能有效地改善高刚性操纵杆力觉临场感和主从位置跟随性,并能很好地解决反馈力瞬间冲击问题,为力觉临场感遥操作机器人走向实用化提供了宝贵经验和关键技术.。
机械装配系统可视化误差研究.
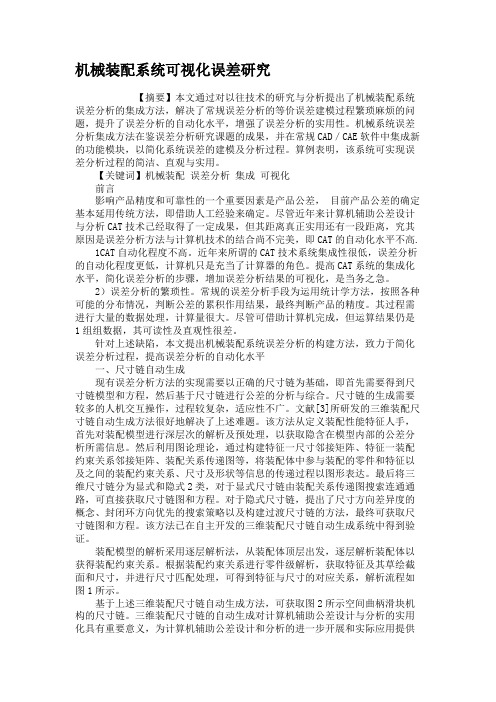
机械装配系统可视化误差研究【摘要】本文通过对以往技术的研究与分析提出了机械装配系统误差分析的集成方法,解决了常规误差分析的等价误差建模过程繁琐麻烦的问题,提升了误差分析的自动化水平,增强了误差分析的实用性。
机械系统误差分析集成方法在鉴误差分析研究课题的成果,并在常规CAD/CAE软件中集成新的功能模块,以简化系统误差的建模及分析过程。
算例表明,该系统可实现误差分析过程的简洁、直观与实用。
【关键词】机械装配误差分析集成可视化前言影响产品精度和可靠性的一个重要因素是产品公差,目前产品公差的确定基本延用传统方法,即借助人工经验来确定。
尽管近年来计算机辅助公差设计与分析CAT技术己经取得了一定成果,但其距离真正实用还有一段距离,究其原因是误差分析方法与计算机技术的结合尚不完美,即CAT的自动化水平不高.1CAT自动化程度不高。
近年来所谓的CAT技术系统集成性很低,误差分析的自动化程度更低,计算机只是充当了计算器的角色。
提高CAT系统的集成化水平,简化误差分析的步骤,增加误差分析结果的可视化,是当务之急。
2)误差分析的繁琐性。
常规的误差分析手段为运用统计学方法,按照各种可能的分布情况,判断公差的累积作用结果,最终判断产品的精度。
其过程需进行大量的数据处理,计算量很大。
尽管可借助计算机完成,但运算结果仍是1组组数据,其可读性及直观性很差。
针对上述缺陷,本文提出机械装配系统误差分析的构建方法,致力于简化误差分析过程,提高误差分析的自动化水平一、尺寸链自动生成现有误差分析方法的实现需要以正确的尺寸链为基础,即首先需要得到尺寸链模型和方程,然后基于尺寸链进行公差的分析与综合。
尺寸链的生成需要较多的人机交互操作,过程较复杂,适应性不广。
文献[3]所研发的三维装配尺寸链自动生成方法很好地解决了上述难题。
该方法从定义装配性能特征人手,首先对装配模型进行深层次的解析及预处理,以获取隐含在模型内部的公差分析所需信息。
然后利用图论理论,通过构建特征一尺寸邻接矩阵、特征一装配约束关系邻接矩阵、装配关系传递图等,将装配体中参与装配的零件和特征以及之间的装配约束关系、尺寸及形状等信息的传递过程以图形表达。
机械优化设计中可视化方法的研究的开题报告

机械优化设计中可视化方法的研究的开题报告一、选题背景及意义近年来,随着国家制造强国战略的推进,我国机械制造行业不断向智能化、高效化、专业化发展,各类机械设备的日益复杂化和实用化,也对机械优化设计提出了更高的要求。
同时,随着计算机技术、3D技术、虚拟现实技术等发展,机械优化设计中的可视化方法得到了广泛的应用和研究。
可视化直观地反映了机械设计的形态和结构,对于了解机械构造和性能、强化设计与审核、提高设计效率和质量等方面都有极大的帮助。
针对目前机械优化设计中可视化方法的研究现状和面临的问题,本文将设计一个机械件优化设计控制系统,研究其中的可视化方法,进行相关分析与探索,并提出相应的优化设计方案以期实现更好、更高效、更可靠的机械件优化设计。
二、选题目的与研究内容1.选题目的针对机械复杂结构与形态多变的现状,利用可视化方法设计一套机械件优化设计控制系统,解决机械优化设计面临的形态和性能等问题。
2.研究内容(1)机械件优化设计控制系统的构建;(2)机械件优化设计控制系统的可视化展示;(3)在控制系统上开发各种机械设计的优化方法;(4)优化结果的可视化展示与结果分析。
三、拟采用的研究方法(1)文献资料法:搜集机械件优化设计控制系统的相关文献、研究报告、参考书等,了解可视化方法在机械设计中的发展过程、应用情况和研究成果,为本研究提供理论基础和技术支持。
(2)实验研究法:采用实验方法进行可视化方法在机械件优化设计控制系统中的应用和验证,根据测试结果,不断改进优化设计控制系统,提高其可靠性和效率。
(3)网格优化法:采用网格优化方法,对机械件进行计算建模,并通过交互式操作实现对优化结果的可视化呈现,方便用户对优化结果进行分析和评估。
四、预期达到的研究目标(1)构建一套完整的机械件优化设计控制系统,实现机械件优化设计的自动化、智能化和质量化;(2)研究机械件优化设计中可视化方法的应用,为优化设计提供更直观、更具体的表现;(3)提高机械件优化设计的计算效率和精度,充分发挥机械优化设计的作用;(4)推动机械件优化设计的科学化和规范化,提升国内机械制造业的技术水平和创新能力。
【机械要点】JTEKT 机床主轴单元刚性测量系统——将主轴旋转中的特性可视化(附图)

JTEKT 机床主轴单元刚性测量系统——将主轴旋转中的特性可视化(附图) 捷太格特(JTEKT)通过利用电磁石的吸引力开发了新的主轴测量系统,不仅可以在主轴静止时测量,主轴旋转时也可以对其相关数值(刚性・固有值)进行测量,并可以对应所有的主轴姿势。
本系统是捷太格特最新的独创技术(※根据我司的调查),能通过定量把握出货时的预压状态、主轴特性,有助于提高主轴的可靠性,开发效率,以及使性能历时变化可视化。
将来,该系统的测量数据也将作为支持“主轴异常诊断”和“加工条件最优化”的工具被进一步活用于主轴的开发。
小于系统外观和概略图 【开发背景】 机床在日本被称为工作机械,意思是“制作其他机械的机械产品”,也被称为“工作母机”。
是作为支持日本制造业重要的基础产业而发展壮大的。
为了机床的进一步发展,作为决定机床性能最重要因素之一的主轴单元,其性能和可靠性的提高不可或缺,因此主轴单元中的轴承起到了很重要的作用。
“轴承的预压”是影响主轴性能的重要因素之一。
预压值越大主轴刚性越高,但有同时也有高速性、发热、寿命等方面的缺陷。
相反,预压值越小越有利于高速性、发热、寿命能方面的表现,但刚性就会较弱。
为了制作主轴性能公差小的主轴,缩小“预压的公差”是行之有效的方法。
一般对预压的管理项目进行测量都在主轴静止时进行,但是本来加工中的主轴就是处于高速旋转的状态,考虑对主轴性能的评估应该在旋转状态下实施,所以我们着手并开发了本系统。
【特点】 (1) 可以测量主轴静止时的刚性、固有值 (2) 可以测量旋转时的刚性、固有值 (3) 通过把握旋转中的刚性,有助于得出最优加工条件 利用电磁石的吸引力,对主轴前端安装的芯棒(类似的工具)用不同的频率加以振动(径向、轴向2个方向都可以加振)。
加振时通过感应器对实时的变位进行检测,静止时自不必说,旋转中的机床主轴特性(刚性・固有值)也可以测量出来。
位置误差部分项目的可视化理论及实现的开题报告

位置误差部分项目的可视化理论及实现的开题报告一、选题背景在现代科技高度发达的时代,人类对于位置信息的需求越来越广泛,如导航、物流、地图等应用场景中,位置误差是一个至关重要的问题。
根据不同应用场景,传感器、信号等探测手段的精度亦有所不同,位置误差的大小和形态可能也因此而各异。
如何对于不同误差场景进行可视化、分析和处理就成为一个重要研究课题。
二、研究目的本项目旨在研究现有的位置误差分析方法和技术,对于不同误差场景进行分析建模,实现相应的可视化算法,为用户提供统一的数据处理接口和数据交互方式,实现位置误差的可视化分析、展示和处理。
三、研究内容1. 各种位置误差类型的分析方法和建模技术2. 位置误差可视化的理论和算法3. 可视化算法的软件实现及数据交互接口设计四、实现方案本项目主要通过以下步骤来实现:1. 收集和整理各种位置误差场景和数据2. 基于现有的位置误差分析方法和技术,研究各种误差场景下的建模技术和算法3. 设计和实现可视化算法,包括误差数据的可视化展示、统计和分析4. 设计和实现数据交互接口,实现用户可自定义数据处理和交互操作5. 软件测试和性能优化五、预期成果本项目主要预期实现以下成果:1. 完成位置误差分析方法和技术的研究和整理2. 完成位置误差可视化算法的研究和实现3. 通过软件实现数据交互接口和数据的可视化展示和分析4. 完成测试和性能优化工作,使得软件能够稳定运行六、拟定计划和预算1. 计划和进度(1)项目启动和需求分析:2周(2)位置误差分析方法和技术的研究和整理:4周(3)位置误差可视化算法的研究和实现:6周(4)数据交互接口设计和实现:2周(5)软件测试和性能优化:2周(6)报告编写和汇报答辩:2周总共耗时18周2. 预算本项目预计需要购买软件和硬件设施等相关支出,预算为人民币50,000元。
七、研究方法本项目主要采用文献阅读和实验室测试相结合的产品研究方法,以实现研究目的和预期成果。
- 1、下载文档前请自行甄别文档内容的完整性,平台不提供额外的编辑、内容补充、找答案等附加服务。
- 2、"仅部分预览"的文档,不可在线预览部分如存在完整性等问题,可反馈申请退款(可完整预览的文档不适用该条件!)。
- 3、如文档侵犯您的权益,请联系客服反馈,我们会尽快为您处理(人工客服工作时间:9:00-18:30)。
沈阳机床 ( 团)设计研 究院 ( 集 辽宁 1 0 4 ) 刘启 伟 1 1 2 马 晓波 仇 建
随 着 计算 机 软 硬件 技 术 的 飞速 发 展 ,三维 可 视 化技 术 得 到 了越 来越 多的 应用 ,在 科研 及 工程 领 域 人 们 也 不 再 满 足 单 纯 的 文 字 叙 述 和 简 单 的二 维 图
图2 数据采集配置界面
硬件部分主要包括米铱公司出产的I2 0 数据 F 04
采 集 卡 2 ,每 块 4 通 道 ;5 激 光 三 角反 射 式 位 块 个 个 移 传 感 器 ,测 量 范 围为 2 ~2 mm ;5 控 制 器 、 4 6 个 1 2 V电 源 模 块 及 连 接 线 缆 和 1 工 控 机 等 , 个 4 台 图3 一通 道 硬件 连 接示 意 图。 为
l 配 墨 I 豢 8 I I 嚣 是 H 装坠及 骣 着 l 垦树 入 鏊 薯 I 堕I 装 树点 导 配 节 l 出 I
位 移传 感 器 的具 体 安装 方 式如 图4 所示 。
图5 T P 为S E 文件解析及零件网格化处理流程 ,在主
程 序 中将 接 收 到 的模 型 数据 流 进行 反 向解 析 ,即 可 建 立 装配 树 和3 模 型 。 维
…
图4 主轴误差测量装置安装示意 图
1 轴检 棒 2激 光位 移传 感 器 3支架 . 主 . .
兼 顾 了 系统 的 快 速 响 应 性 和 提 供 人 性 化 的界 面 等 优 点 。 图 1 系统 软 件 主 界 面 , 无需 切 换 到 其 他 窗 为 口 ,在 主 界 面 里 就 可 以 完 成 大 部 分 的 软 件 操 作 工 作 ,如 通 道颜 色 设 置 、采 样 时 间 、采样 数 据处 理 方
2 主轴误 差可视 化仿真系统 .
主轴误差可视 化仿真 系统包括建立可视 化模型 和误 差仿真两大部分 ,可视 化模型包括机床的3 D
模 型 和 安装 在 主 轴上 的 检 棒 ,机 床 模 型可 以 通过 导 入 设 计 人 员建 立的 C D 型 的 方 法实现 ,检 棒需 要 A 模
面 向对 象 的 3 D图形 和 可 视 化 类 库 ,主 要 用于 三 维 计 算 机 图形 学 、 图 像 处 理 和 可 视 化 ,能 够 对 标 量 场 、矢 量 场 以及 张量 场 数据 进 行 重建 。V K 有 丰 T 拥 富 的 数据 类 型 支持 ,可 以对 多 种数 据 进 行 处理 ,在 导 人大 量 模 型时 可 以使 用L D 示 技术 ,以提 高 系 O 显 统 的 响应 速 度和 显示 效 果 。 通 过 2 3 平 台 的 合 理 使 用 ,既 解 决 了机 床 3 个 D 维 模 型重 建 的 复杂 性 ,又提 高 了模 型的 显 示效 果 和 人 机 交互 性 ,充分 利 用 了两 大 平 台 的优 势 互补 性 。
式 、图像显示范围以及激光位移传感器的开关等 ,
给 实 际 的测试 工 作 带来 了很大 的 便利 性 。
表 ,对数据分析及处理上也提 出了更高的要求,动
态且 具 有交 互 功 能 的可 视化 技 术 走 进这 一 领域 。可 视 化 技 术 以其 独 有 的视 觉和 听 觉 感 受给 单 调 的数 据 分 析 及其 后 处理 带 来好 处 。
测 ),将可视化技术应 用于主轴误差分析 中,通过
导入机床模 型和将主轴误差以3 D的 方 式 显 示 , 可 以 从 机床 整 体 的 角度 来 审视 和 考量 误 差对 机 床 的影 响 ,收到 了以文 字 叙述 和 二 维 图表 所 无法 比拟 的效 果 ,对机 床 的性 能 分析 和 结 构优 化 起 到 了很 好 的参
ቤተ መጻሕፍቲ ባይዱ
根 据 硬 件 构 成 ,测 试 系 统 可 同时 进 行 5 道 的 通
数据采集工作 ,测量频率为每通道1k ,一般安 0 Hz
装 方式 为主 轴 轴 向一 个 ,其 他 两 个方 向各 两 个 ,可 同 时测 量 主 轴 、 Y 三 个 方 向的位 移 数据 ,通 过 、z
数据处理还可计算 出主轴在径向的倾斜角度,激光
包括主轴跳动检测 ( 包括轴 向和径 向)、主轴热变
形 检 测 、静 刚度 检 测等 项 目。通过 V K 发平 台 , T 开 本 文 结合 主 轴误 差 检 测 系统 ( 跳动 检 测和 热 变 形 检
图1 数据采集主界 面
图 2 软 件 配 置 界 面 , 可 以 进 行 硬 件 参 数 设 为 置 、通 道 设 置 等 操 作 ,所 有 参 数 都 将 保 存  ̄ X L IM J 配 置文 件 中 ,软件 启 动时 将 自动加 载 配 置文 件 。
考价 值 。
1 主轴误差测试系统 .
主轴误差测试系统采用沈阳机床 ( 集团)设计
研 究院 自行开 发 的 一套 测 试 装 置 ,测试 系统 包 括软
件和硬件两大部分。测试软件主要负责参数设置、
通道 设 置 以 及数 据 的实 时 显 示和 保 存等 工 作 ,采用
C+ 进 行 底 层开 发 ,以C 进 行上 层 界面 设 计 ,软 件 + #
机床 主轴 如 同 人的 手 臂 ,是 机 床 的关 键 部 件 , 主 轴 的性 能 将 直接 关 系 到机 床 的 最终 性 能 。对 机 床
主 轴 进 行误 差 测试 已经 成为 机 床性 能 检 验 、误 差 分 析 和 出厂 检 验 的 必须 工 作 。机 床 主轴 误 差测 试 一 般
5 4
, 痂
参 籼工 磊
能 ,编写 成一 个 动 态链 接库 供 主 程序 调 用 。 VT 是 目前 较 为成 熟 的3 K D显 示 平 台 ,VT K为 Vsai t nT oK t 写 ,是 一 个开 放 源码 的 、 i l a o o li u zi 的缩
图3 一通 道硬件连接示意 图