隧道支护施工技术交底
隧道明洞施工安全技术交底模板

一、交底目的为确保隧道明洞施工过程中的安全,提高施工人员的安全意识,预防安全事故的发生,现将隧道明洞施工的安全技术要求进行交底。
二、施工概况1. 工程名称:[项目名称]2. 工程地点:[具体位置]3. 施工内容:隧道明洞开挖、支护、衬砌等。
三、安全技术要求1. 人员安全- 所有施工人员必须经过专业培训,持证上岗。
- 佩戴好安全帽、安全带、防尘口罩等个人防护用品。
- 禁止酒后作业、疲劳作业。
- 施工现场必须设置安全警示标志,明确警示内容。
2. 机械安全- 所有机械设备必须符合国家规定,并定期进行检修和维护。
- 操作人员必须熟悉机械设备性能和操作规程,严禁违规操作。
- 机械设备运行过程中,严禁人员进入危险区域。
3. 施工安全- 开挖前,必须进行地质勘察,了解地质情况,制定合理的施工方案。
- 隧道明洞开挖采用分层开挖,每层开挖深度不超过2m。
- 开挖过程中,必须设置临时支撑,确保边坡稳定。
- 隧道明洞支护采用锚杆、钢筋网、喷射混凝土等材料,确保支护质量。
- 隧道明洞衬砌采用模板、钢筋、混凝土等材料,确保衬砌质量。
4. 防护措施- 施工现场设置安全防护设施,如防护栏、安全网等。
- 隧道明洞进出口设置排水设施,防止水患。
- 隧道明洞施工过程中,必须进行监测,及时发现和处理安全隐患。
四、应急措施1. 火灾事故- 立即切断电源,使用灭火器、消防水等进行灭火。
- 疏散人员,确保人员安全。
2. 坍塌事故- 立即停止施工,设置警戒区域。
- 报告相关部门,采取抢险措施。
3. 中毒事故- 立即关闭通风系统,将中毒人员转移到空气新鲜的地方。
- 使用解毒药物进行救治。
五、交底总结通过本次安全技术交底,要求所有施工人员充分了解隧道明洞施工的安全技术要求,严格遵守操作规程,确保施工安全。
六、注意事项1. 施工过程中,必须密切关注现场安全状况,发现安全隐患立即报告。
2. 严格执行安全技术交底内容,不得擅自更改。
3. 定期对施工人员进行安全教育培训,提高安全意识。
隧道施工安全技术交底

隧道施工安全技术交底
为确保隧道施工期间的安全,保护工人的身体健康和财产安全,现就隧道施工安全技术进行交底:
一、现场管理
1. 施工现场应进行有效的封闭和警示,以确保工人的人身安全。
2. 工作场所必须保持清洁、有序,并对易滑倒、滑动、滚动、
坠落等危险地段进行封堵和标识。
3. 施工现场必须设置防止坍塌、滑坡、滑落和其他自然、人工
灾害的保护措施,并定期检查维护。
二、机械设备安全
1. 机械设备必须符合国家标准和规定,并定期进行保养和维护。
2. 员工必须经过技能培训和操作规程培训后方可操作设备,严
禁未经培训人员操作设备。
3. 设备检查前必须按要求进行试运行,确保正常无误后方可投
入使用。
三、电气安全
1. 电气设备必须符合国家标准和规定,并由专业人员安装和调试。
2. 必须对电气设备进行定期检查、试验和维护,消除安全隐患。
3. 工作时必须使用带有漏电保护装置的电器,并保持干燥。
四、防火安全
1. 施工现场必须具备灭火设施,做好防火措施,确保安全出口
畅通。
2. 施工现场禁止用明火进行作业,禁止吸烟等行为。
3. 原料和易燃物品应分类存储,注意防火,特别是易燃液体必
须用专业储罐储存。
以上是隧道施工安全技术交底内容,务必落实执行,确保施工
过程中的安全。
隧洞台车支护安全技术交底模板
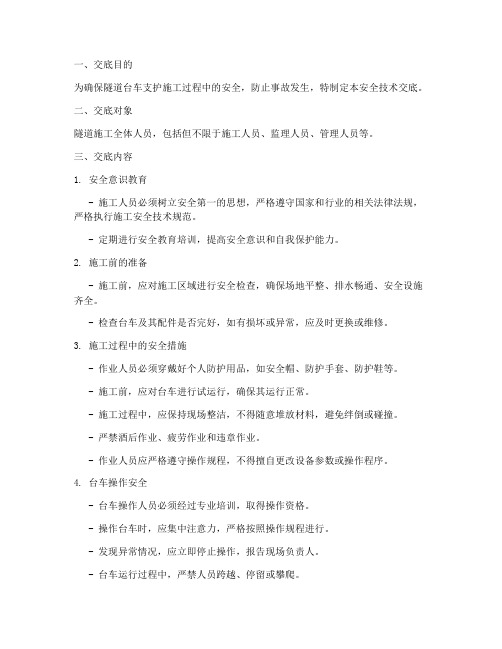
一、交底目的为确保隧道台车支护施工过程中的安全,防止事故发生,特制定本安全技术交底。
二、交底对象隧道施工全体人员,包括但不限于施工人员、监理人员、管理人员等。
三、交底内容1. 安全意识教育- 施工人员必须树立安全第一的思想,严格遵守国家和行业的相关法律法规,严格执行施工安全技术规范。
- 定期进行安全教育培训,提高安全意识和自我保护能力。
2. 施工前的准备- 施工前,应对施工区域进行安全检查,确保场地平整、排水畅通、安全设施齐全。
- 检查台车及其配件是否完好,如有损坏或异常,应及时更换或维修。
3. 施工过程中的安全措施- 作业人员必须穿戴好个人防护用品,如安全帽、防护手套、防护鞋等。
- 施工前,应对台车进行试运行,确保其运行正常。
- 施工过程中,应保持现场整洁,不得随意堆放材料,避免绊倒或碰撞。
- 严禁酒后作业、疲劳作业和违章作业。
- 作业人员应严格遵守操作规程,不得擅自更改设备参数或操作程序。
4. 台车操作安全- 台车操作人员必须经过专业培训,取得操作资格。
- 操作台车时,应集中注意力,严格按照操作规程进行。
- 发现异常情况,应立即停止操作,报告现场负责人。
- 台车运行过程中,严禁人员跨越、停留或攀爬。
5. 紧急情况处理- 发生火灾、触电、中毒等紧急情况时,应立即采取相应措施进行自救或互救。
- 紧急情况发生时,应迅速撤离危险区域,并报告现场负责人。
6. 安全检查与验收- 施工过程中,应定期进行安全检查,及时发现和消除安全隐患。
- 完成施工后,应对台车支护进行验收,确保其符合安全要求。
四、交底要求1. 施工单位应将本安全技术交底文件发放给所有施工人员,并组织学习。
2. 施工人员应认真学习并掌握本安全技术交底内容,确保在实际工作中严格执行。
3. 监理人员应对施工过程中的安全措施进行检查,确保施工安全。
五、附则本安全技术交底自发布之日起实施,如有未尽事宜,由施工单位负责解释。
注:以上模板仅供参考,具体内容应根据实际情况进行调整。
隧道施工支护安全技术交底
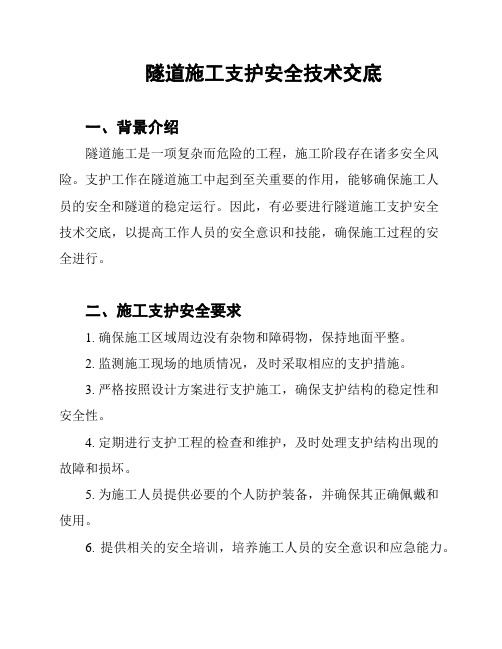
隧道施工支护安全技术交底一、背景介绍隧道施工是一项复杂而危险的工程,施工阶段存在诸多安全风险。
支护工作在隧道施工中起到至关重要的作用,能够确保施工人员的安全和隧道的稳定运行。
因此,有必要进行隧道施工支护安全技术交底,以提高工作人员的安全意识和技能,确保施工过程的安全进行。
二、施工支护安全要求1. 确保施工区域周边没有杂物和障碍物,保持地面平整。
2. 监测施工现场的地质情况,及时采取相应的支护措施。
3. 严格按照设计方案进行支护施工,确保支护结构的稳定性和安全性。
4. 定期进行支护工程的检查和维护,及时处理支护结构出现的故障和损坏。
5. 为施工人员提供必要的个人防护装备,并确保其正确佩戴和使用。
6. 提供相关的安全培训,培养施工人员的安全意识和应急能力。
三、施工支护安全措施1. 制定详细的施工计划,并确保施工人员理解并遵守。
2. 在施工现场设置明显的安全警示标志,指示施工区域和危险区域。
3. 使用适当的支护材料和设备,如钢架、钢筋网等。
4. 严格落实施工人员的管理制度,确保施工作业规范有序进行。
5. 安排专业人员进行监督和检查,及时发现和纠正施工中存在的安全问题。
四、应急预案和处置措施1. 制定全面的应急预案,包括应急措施、逃生路线等。
2. 在施工现场配备适当的应急设备和救援工具。
3. 组织定期的应急演练,提高施工人员的应急反应能力。
4. 发生事故时,及时报警并采取紧急救援措施,确保人员安全。
五、总结通过施工支护安全技术交底,可以提高施工人员的安全意识和技能,减少安全事故的发生。
同时,合理制定支护安全措施和应急预案,能够及时应对不可预见的情况,保障隧道施工的安全和顺利进行。
在施工过程中,我们每个人都要时刻关注安全,确保自己和他人的安全。
市政隧道工程施工技术交底(大全)
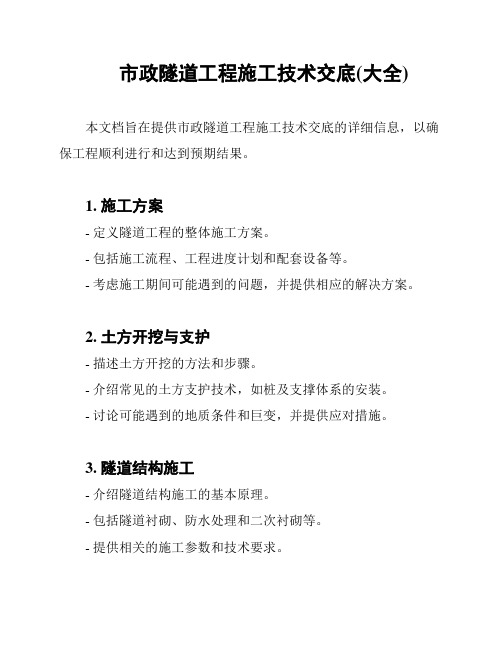
市政隧道工程施工技术交底(大全)
本文档旨在提供市政隧道工程施工技术交底的详细信息,以确保工程顺利进行和达到预期结果。
1. 施工方案
- 定义隧道工程的整体施工方案。
- 包括施工流程、工程进度计划和配套设备等。
- 考虑施工期间可能遇到的问题,并提供相应的解决方案。
2. 土方开挖与支护
- 描述土方开挖的方法和步骤。
- 介绍常见的土方支护技术,如桩及支撑体系的安装。
- 讨论可能遇到的地质条件和巨变,并提供应对措施。
3. 隧道结构施工
- 介绍隧道结构施工的基本原理。
- 包括隧道衬砌、防水处理和二次衬砌等。
- 提供相关的施工参数和技术要求。
4. 排水和通风系统
- 描述隧道工程中的排水和通风系统。
- 包括排水设施的设置和维护,以及通风系统的设计和安装。
- 强调系统的重要性和合理运行的必要性。
5. 施工安全措施
- 强调施工期间的安全措施。
- 包括工作人员的培训和个人保护装备的使用。
- 提供应急情况下的应对方案和紧急救援措施。
6. 施工质量控制
- 介绍施工期间的质量控制措施。
- 包括材料的验收、工程质量检测和施工过程中的监管等。
- 强调施工质量的重要性和符合规范的要求。
请注意,本文档只是市政隧道工程施工技术交底的概要,具体的施工细节和技术规范应根据实际情况进行进一步制定和实施。
> 以上为简要概述,详情请参阅实际工程相关文件。
隧道支护施工技术交底锚杆和喷射混凝土施工

隧道支护施工技术交底锚杆和喷射混凝土施工隧道支护施工技术交底:锚杆和喷射混凝土施工一、引言隧道工程是一项复杂而具有挑战性的工程,其在建设过程中需要采用多种支护措施来确保隧道的安全性和稳定性。
本文将重点介绍两种常用的隧道支护技术——锚杆和喷射混凝土施工技术,以及其在隧道工程中的应用。
二、锚杆施工技术1. 简介锚杆施工技术是一种常用的隧道支护措施,它通过将锚杆固定在围岩中,抵抗围岩的变形和破败,以实现隧道的稳定和安全。
2. 施工步骤(1)勘察与设计:在施工前,需进行现场勘察,确定围岩情况及锚杆的布置方式,然后设计锚杆的长度、直径和间距。
(2)预处理:在固定的位置,钻孔并清除孔内的泥土,以便于后续的锚杆灌浆。
(3)锚杆灌浆:将预先制作好的锚杆插入孔内,并进行灌浆。
灌浆材料应根据地质情况和设计要求选择合适的材料。
(4)质量检测:锚杆施工完成后,需进行质量检测,确保施工质量符合要求。
三、喷射混凝土施工技术1. 简介喷射混凝土施工技术是一种承重支护和衬砌技术,它通过将混凝土喷射到隧道围岩表面形成刚性支护结构,增加围岩的稳定性和承载能力。
2. 施工步骤(1)洞口准备:在喷射混凝土之前,需对洞口进行准备工作,包括清理洞口、布置钢筋和预埋件等。
(2)混凝土质量控制:混凝土质量需符合相关标准,包括配合比、强度等要求。
(3)喷射施工:采用喷射机将混凝土均匀喷射到围岩表面,形成均匀的混凝土衬砌层。
(4)表面处理:喷射完成后,对混凝土表面进行养护和处理,以保证施工质量。
四、锚杆和喷射混凝土施工技术在隧道工程中的应用1. 锚杆和喷射混凝土的协同应用在隧道工程中,锚杆和喷射混凝土往往会同时使用,以实现更好的支护效果。
锚杆可以增加围岩的稳定性,而喷射混凝土则可以提供刚性的支撑和保护。
2. 因地制宜的施工方案锚杆和喷射混凝土的具体施工方案需根据具体的地质情况和设计要求而定。
例如,在软弱围岩区域,可能需要更多的锚杆来提高支护效果;而在坚硬围岩区域,则可以减少锚杆数量,主要依靠喷射混凝土来提供支撑。
隧洞锚喷支护安全技术交底模板

一、适用范围本交底适用于隧道施工中锚喷支护作业,包括锚杆施工、钢筋网布设、喷射混凝土等工序。
二、交底内容1. 施工准备- 施工人员必须经过专业培训,掌握锚喷支护的基本知识和操作技能。
- 施工前应检查所有施工设备、材料是否符合要求,确保其安全、有效。
- 隧道地质情况分析,确定锚喷支护的设计参数和施工方案。
2. 安全技术要求- 进入施工现场人员必须佩戴安全帽、安全带等防护用品。
- 高空作业人员必须系好安全带,并采取防坠落措施。
- 施工现场应设置警示标志,明确危险区域。
- 施工机械操作人员必须熟悉机械性能,确保操作安全。
- 锚杆施工过程中,应注意锚杆方向和锚固深度,确保锚杆与围岩紧密结合。
- 钢筋网布设时,应确保网格尺寸准确,钢筋间距均匀。
3. 施工操作要点- 锚杆施工:- 根据设计要求,选择合适的锚杆材料和锚固方式。
- 使用风钻或钻机钻孔,孔径、孔深应符合设计要求。
- 锚杆插入孔内,并确保锚杆与围岩紧密结合。
- 使用锚杆锚固剂,确保锚杆锚固效果。
- 钢筋网布设:- 根据设计要求,选用合适的钢筋网材料和规格。
- 将钢筋网固定在锚杆上,确保钢筋网与锚杆垂直。
- 钢筋网应均匀分布,网格尺寸应符合设计要求。
- 喷射混凝土:- 选择合适的混凝土材料和配合比。
- 使用喷射机进行混凝土喷射,确保混凝土厚度均匀。
- 喷射过程中,应注意安全防护,防止混凝土飞溅。
4. 应急措施- 发生锚杆断裂、钢筋网损坏等情况时,应立即停止施工,并采取相应措施进行处理。
- 发生人员伤亡事故时,应立即启动应急预案,及时救治伤员,并报告相关部门。
三、注意事项1. 施工过程中,应密切关注围岩变化,如发现异常情况,应立即停止施工,并采取相应措施进行处理。
2. 施工现场应保持整洁,及时清理杂物,防止安全事故发生。
3. 施工人员应严格遵守操作规程,确保施工安全。
四、交底人及接受人- 交底人:项目技术负责人- 接受人:隧道施工全体人员五、交底时间- 日期:____年__月__日六、备注本交底内容仅供参考,具体施工方案应根据实际情况进行调整。
高速隧道维护安全技术交底模板

一、交底目的为确保高速隧道维护作业安全、高效进行,防止安全事故的发生,特进行安全技术交底。
本交底针对隧道维护作业中可能存在的安全隐患,对作业人员进行详细的安全技术指导。
二、交底对象隧道维护作业全体人员,包括施工、监理、管理人员。
三、交底内容1. 安全意识教育(1)加强安全意识,严格遵守国家有关安全生产法律法规和行业标准。
(2)树立“安全第一,预防为主,综合治理”的安全生产方针。
(3)增强自我保护意识,提高应急处置能力。
2. 隧道维护作业安全要求(1)隧道维护作业前,必须对作业区域进行全面的安全检查,确保无安全隐患。
(2)作业人员必须佩戴好安全帽、安全带、防尘口罩等个人防护用品。
(3)隧道内照明设施应保持完好,确保作业环境明亮。
(4)严禁酒后作业,严禁违章操作。
3. 具体作业安全措施(1)隧道内通风设备应保持正常运行,确保作业环境空气新鲜。
(2)隧道内作业时,必须保持通道畅通,不得堆放杂物。
(3)施工机械、工具应定期检查,确保安全可靠。
(4)高处作业时,必须使用安全带,并做好防坠落措施。
(5)隧道内作业时,严禁使用明火,防止火灾事故发生。
4. 应急处置措施(1)遇有突发事件,应立即停止作业,迅速撤离现场。
(2)发生火灾、触电、坍塌等事故时,应立即启动应急预案,采取有效措施进行处置。
(3)确保救援通道畅通,确保人员安全撤离。
5. 其他注意事项(1)作业人员应严格遵守劳动纪律,按时参加班前会,了解当天作业任务及安全注意事项。
(2)加强作业现场巡查,及时发现并消除安全隐患。
(3)加强作业人员的教育培训,提高安全技能。
四、交底方式1. 组织召开安全技术交底会议,对作业人员进行集中培训。
2. 制作安全技术交底记录表,确保交底内容完整、准确。
五、交底时间隧道维护作业开始前,由项目负责人组织进行安全技术交底。
六、交底责任人项目负责人为本次安全技术交底的第一责任人,负责组织、实施、监督和落实。
七、附则1. 本安全技术交底自发布之日起实施,有效期至隧道维护作业结束。
隧道施工技术交底

隧道施工技术交底引言隧道施工是指在地下或水下等特殊环境中进行的道路、铁路、管道等基础设施的建设工作。
隧道施工技术交底是指隧道施工过程中,施工团队向相关人员介绍和讲解施工技术要点和注意事项的活动。
本文将介绍隧道施工技术交底的目的、内容、形式和注意事项。
目的隧道施工技术交底的目的是确保参与施工工作的人员对隧道施工的要求、方法和安全注意事项有清楚的了解和掌握。
通过技术交底,可以提高施工人员的工作效率,减少施工中的错误和事故风险,确保施工进度和质量。
内容隧道施工技术交底的内容应包括以下方面:1. 施工过程和顺序在技术交底中,需要详细介绍整个隧道施工的过程和顺序。
包括隧道开挖、支护、内部结构施工等各个阶段的工作内容和流程。
同时,还需要介绍每个阶段的施工方法和工具的使用。
2. 安全注意事项安全是隧道施工中最重要的方面。
在技术交底中,应重点介绍各种安全注意事项,包括施工过程中的安全措施、防护装备的使用、事故应急处理等。
同时,需要讲解工作人员应具备的安全意识和自我保护能力。
3. 施工质量要求隧道施工的质量对工程的持久性和安全性有着重要影响。
在技术交底中,应介绍各种施工质量要求,包括尺寸精度、混凝土强度、钢筋工程质量等。
同时,还需要讲解质量验收的方法和标准。
4. 施工设备与材料技术交底还应包括施工所需的设备和材料介绍。
包括各种挖掘机械、支护设备、水泥、钢筋等。
需要介绍每种设备和材料的使用方法和注意事项,确保施工过程中的设备运行正常,材料质量符合要求。
5. 施工图纸和规范在技术交底中应着重介绍施工图纸和规范的使用和理解。
通过详细解读施工图纸和规范,可以避免因误解而导致的施工错误和质量问题。
形式隧道施工技术交底可以采用多种形式进行,常见的形式包括:1. 讲座会议通过组织讲座会议的形式,由专业的技术人员向参与施工的人员进行技术交底。
讲座会议可以结合实际案例,让参与者更好地理解和掌握施工技术要点和注意事项。
2. 培训课程可以通过组织专门的培训课程,对隧道施工技术进行系统的培训和讲解。
(完整版)地铁隧道支护技术交底

(完整版)地铁隧道支护技术交底一、支护技术的介绍地铁隧道的支护技术是确保地铁运营安全的重要环节。
支护技术包括地铁隧道的结构设计、材料选用、施工方法等方面,对于地铁隧道的稳定性和耐久性有着重要影响。
二、地铁隧道支护材料在地铁隧道的支护过程中,我们使用的是高强度钢材、钢筋混凝土、岩石锚杆等材料。
高强度钢材具有较高的抗拉强度和刚性,能够有效支撑隧道结构。
钢筋混凝土是一种常用的构造材料,具有优异的抗压和耐久性能。
岩石锚杆则可以增强土层或岩石的稳定性,防止隧道坍塌。
三、地铁隧道支护施工方法1. 开挖前支护:在进行地铁隧道开挖之前,我们通常会对周围土层进行支护。
支护方法包括钢筋网架、喷射混凝土预支护墙等。
这些支护措施可以有效地减少地下水的渗透,防止土层的塌方。
2. 地铁隧道衬砌:地铁隧道的衬砌是支撑和保护隧道内部结构的重要环节。
我们采用钢筋混凝土衬砌的方式,能够增强隧道的刚度和强度,保证乘客安全。
3. 地铁隧道封闭:隧道开挖完成后,需要进行封闭施工,以确保隧道的密闭性。
封闭施工通常采用预制块、注浆等方式,防止地下水和杂质渗入隧道。
四、地铁隧道支护技术的重要性地铁隧道支护技术的科学和有效应用,可以确保地铁隧道的稳定性、耐久性和安全性。
合理选择支护材料和施工方法,能够有效地减少隧道的损坏和维修成本,延长隧道的使用寿命。
地铁隧道的支护技术也是地铁建设与运营的关键环节,对于保障乘客的出行安全具有重要意义。
以上是地铁隧道支护技术的交底内容,请各工作人员认真研究并遵照执行。
编写人:[你的名字]日期:[日期]。
隧道洞口边坡支护技术交底

2、机具、材料准备
机具:13m3空压机、自落式搅拌机、湿式喷射机、注浆机、浆液搅拌机、YT28气腿式凿岩机、手推车、铁锹、台秤等。
材料:钢材、水泥、砂子、石子、速凝剂、炸药等已进行实验并符合相关要求。
交底单位
接收单位
交底人
接收人
年
月
日
施管表5
工程名称
分部工程
分项工程名称
(5)喷射砼
1、埋设好喷厚控制标志,本工程喷射砼厚度为100mm,夜间施工要保证作业区有足够照明,喷前要检查所有机械设备和管线,确保施工正常。对渗水面做好处理措施,备好处理材料,联系好仓面取样准备。
2、喷射混凝土应分段、分片依次进行,喷射顺序自下而上,避免回弹料覆盖未喷面。当分层(每层50mm)喷射时,后一层在前一层混凝土终凝后进行,若终凝1h以后再行喷射,应先用高压风水冲洗喷层面。
7、注浆完毕后,在浆液终凝前不得敲击、碰撞或施加任何其它荷载。
交底单位
接收单位
交底人
接收人
年
月
日
施管表5
工程名称
分部工程
分项工程名称
洞口边坡防护
交底内容:
(4)挂网片
本工程采用Φ6、间距150mm×150mm钢筋网在锚杆安装完毕后布设,施工时应严格按照设计间距先在加工场地制作好钢筋网片,钢筋网应点焊在锚杆头上并搭接100mm,使钢筋网在喷射砼时不易晃动。
交底单位
接收单位
交底人
接收人
年
月
日
施管表5
工程名称
分部工程
分项工程名称
洞口边坡防护
交底内容:
六、质量检测与标准
交底单位
接收单位
隧道工程安全技术交底

隧道工程安全技术交底引言概述:隧道工程是一项复杂而危险的工程,其施工和运营过程中必须严格遵守安全规范和技术要求。
隧道工程安全技术交底是指在施工和运营过程中,将相关的安全技术知识和要求向工作人员进行详细的说明和培训,以确保工作人员具备必要的安全意识和技能,从而保障隧道工程的安全运营。
本文将从四个方面详细阐述隧道工程安全技术交底的内容。
一、施工安全技术交底1.1 施工过程中的危险因素:详细介绍隧道施工过程中可能存在的危险因素,如地质条件、爆破作业、支护结构等,以及对应的安全措施和应急预案。
1.2 安全操作规程:明确施工人员在隧道工程施工过程中应遵守的安全操作规程,如穿戴个人防护装备、使用安全工具、正确操作机械设备等。
1.3 安全培训和考核:介绍施工人员接受安全培训的内容和方式,包括理论培训和实际操作培训,并强调安全考核的重要性。
二、通风安全技术交底2.1 隧道通风系统:详细介绍隧道通风系统的构成和工作原理,包括进风口、排风口、风机等设备的安装和调试要求。
2.2 烟气排放和防护措施:阐述在紧急情况下,如火灾发生时的烟气排放和人员疏散措施,以及防护设施的设置和使用方法。
2.3 通风系统的维护和检修:强调通风系统的定期维护和检修工作,包括清洁、更换滤网、检查电气设备等,以确保通风系统的正常运行。
三、电气安全技术交底3.1 电气设备安装要求:介绍隧道工程中常见的电气设备的安装要求,包括线路敷设、接地、防护等,确保电气设备的安全可靠。
3.2 电气设备的维护和检修:详细阐述电气设备的定期维护和检修工作,包括清洁、检查线路连接、更换老化部件等,以确保电气设备的正常运行。
3.3 紧急情况下的电气安全措施:强调在紧急情况下,如停电、火灾等情况下应采取的电气安全措施,包括切断电源、使用应急照明设备等,以保障人员的安全。
四、应急救援技术交底4.1 火灾应急救援:介绍隧道工程中可能发生的火灾情况下的应急救援措施,包括火灾报警、疏散逃生、灭火器材使用等。
高速隧道养护安全技术交底模板

一、交底目的为确保高速隧道养护作业的安全顺利进行,提高养护人员的安全意识,降低安全事故的发生,特制定本安全技术交底。
二、交底对象所有参与高速隧道养护作业的人员。
三、交底内容1. 安全意识教育(1)加强养护人员的安全教育,提高安全意识,确保作业过程中严格遵守各项安全操作规程。
(2)强化“安全第一,预防为主”的方针,将安全工作放在首位。
2. 现场环境检查(1)对隧道内外的环境进行全面检查,确保无安全隐患。
(2)检查隧道内照明、通风、排水等设施是否正常,确保满足养护作业需求。
3. 作业前的准备工作(1)对养护作业人员进行岗前培训,使其熟悉作业流程、安全操作规程及应急预案。
(2)对养护工具、设备进行检查,确保其安全可靠。
4. 养护作业安全操作规程(1)隧道内作业时,必须佩戴安全帽、安全带等防护用品。
(2)严禁酒后作业、疲劳作业,确保作业人员精神饱满。
(3)施工车辆、机械设备必须停放在指定区域,不得随意停放、掉头。
(4)作业过程中,必须保持通信畅通,确保信息传递及时、准确。
5. 特殊作业安全措施(1)高空作业时,必须采取防坠落措施,如使用安全带、安全绳等。
(2)有限空间作业时,必须进行气体检测,确保空气质量符合要求。
(3)隧道内施工时,必须采取防火、防爆措施,确保作业安全。
6. 事故应急预案(1)制定隧道养护作业事故应急预案,明确事故发生时的应急处理流程。
(2)定期组织应急演练,提高养护人员应对突发事件的能力。
7. 安全检查与考核(1)对养护作业现场进行定期安全检查,发现问题及时整改。
(2)对养护作业人员进行安全考核,确保其具备相应的安全技能。
四、交底要求1. 养护作业人员必须认真学习本安全技术交底,确保掌握各项安全操作规程。
2. 养护作业过程中,严格遵守各项安全操作规程,确保作业安全。
3. 养护作业负责人要加强对作业现场的安全管理,确保作业安全。
4. 发现安全隐患,及时上报并采取措施予以消除。
五、附则本安全技术交底自发布之日起实施,如有未尽事宜,由相关部门负责解释。
隧道施工作业安全技术交底

隧道施工作业安全技术交底隧道施工作业安全技术交底1. 交底目的为了确保隧道施工作业过程中的安全,减少事故的发生,保障施工人员的生命财产安全,特进行本次安全技术交底。
2. 作业内容本次施工作业涉及的内容包括:隧道开挖、支护、拱顶喷射混凝土施工、通风系统安装、电气设备安装等。
下面将对每一个作业环节进行详细说明:2.1 隧道开挖隧道开挖作业需要使用爆破、掘进机械等工具和设备,施工人员需要在作业前进行详细的安全交底。
具体的安全要求包括:熟悉工作地点、清理作业场地、设立明确的安全警示标志、使用标准化钻机进行开挖作业等。
2.2 支护工程支护工程包括刚性支撑和软性支撑两种,施工人员需要了解使用不同类型支护材料的方法和注意事项。
此外,需按照规定进行浇筑混凝土,加固支撑结构,确保施工过程中不发生坍塌等安全事故。
2.3 拱顶喷射混凝土施工在进行拱顶喷射混凝土施工过程中,施工人员需要掌握喷射混凝土机械的操作技巧,并严格遵守操作规程。
同时,需要配备足够的人员用于协助喷射作业,保证作业过程中的安全。
2.4 通风系统安装通风系统安装是确保隧道内空气流通、保证工作人员安全的重要环节。
施工人员需要按照设计要求进行通风系统的安装,安装过程中要注意检查通风设备的密封性温和流畅通情况。
2.5 电气设备安装在隧道施工过程中,还需要进行电气设备的安装工作。
施工人员需要对电气设备进行正确可靠的安装,确保电气设备运行安全可靠。
3. 附件本文档涉及的附件有:施工设备清单、施工图纸、工作方案、安全生产责任状等。
4. 法律名词及注释4.1 法律名词1:《中华人民共和国安全生产法》注释1:中华人民共和国安全生产法是指保护生产过程中参预劳务的人员的人身安全和生命财产安全的法律法规。
4.2 法律名词2:《隧道工程施工安全技术标准》注释2:隧道工程施工安全技术标准是指规定了隧道工程施工过程中必须遵守的安全要求和技术规范的标准文件。
-------------------------------------------------------隧道施工作业安全技术交底1. 交底目的为了确保隧道施工作业过程中的安全,减少事故的发生,保障施工人员的生命财产安全,特进行本次安全技术交底。
隧道施工技术交底

隧道施工技术交底前言隧道建设是重大基础设施建设的重要组成部分,隧道施工技术的成功应用,对于改善城市交通状况、提高交通运输效率、促进地区社会经济发展具有重要意义。
在隧道施工工程中,技术交底是工程质量保证的必要过程之一。
本文将详细介绍隧道施工技术交底流程、内容以及具体实施方法。
隧道施工技术交底流程1.技术人员准备:技术交底需要的人员主要包括:隧道施工现场技术负责人、专业技术人员、施工方案编制人员、安全生产专职人员等。
在技术交底前应做好人员配备、职责分工和工作计划等准备工作。
2.技术交底组织:为确保技术交底的顺利有序进行,应按照交底内容组织有关人员,明确技术交底时间、地点、人员和交底内容。
技术交底会议一般应当在施工前一天召开,确保全体参会人员到场,并进行工作布置,明确要求。
3.交底内容:隧道施工技术交底应包括施工质量和安全生产方面内容。
施工质量方面要包括着重说明施工方法、施工工艺、施工顺序、质量控制等具体工作;安全生产方面则要说明施工过程中的主要安全事项和注意事项,如防护措施、通风排烟、消防安全等。
4.讲解和记录:技术交底应当由技术负责人和专业技术人员进行讲解,并对需要特别强调的问题详细讲解。
同时应当视情况及时进行记录,尤其是重要问题和难点问题。
5.签字确认:技术交底结束后,所有参与人员均应进行签字确认,确认自己已经完全理解和认识技术交底内容,并同意在实际施工中认真遵守本次技术交底的各项要求。
隧道施工技术交底内容1.隧道及场地地质勘察和分析情况对于隧道施工而言,隧道及其周边地质情况是决定施工难度的关键因素。
在技术交底中应对隧道及场地地质勘察和分析结果进行详细的讲解,让人员了解洞体工程设计方案、施工过程中可能遇到的问题以及应对措施。
2.施工方案和施工工艺隧道的施工方案和施工工艺是决定施工质量的重要因素。
在技术交底中应对施工方案和施工工艺进行详细讲解,以确保所有参与施工的人员能够熟知和掌握施工方案、施工工艺、流程和方法。
隧道支护安全技术交底

隧道支护安全技术交底
介绍
本文档旨在对隧道支护工程中的安全技术进行交底,确保施工人员了解和遵守相关安全规定,以保障工程施工过程中的人员和设备安全。
隧道支护技术
隧道支护技术是指在隧道施工过程中采取的措施,用以保护隧道结构的稳定和工作面的安全。
常见的隧道支护技术包括:
1. 土壤改良:使用土工合成材料、灌浆、碎石等方法改良隧道周围的土壤,增加其承载能力和稳定性。
2. 锚杆支护:通过向隧道周围的岩石或土壤中灌注锚杆,增加隧道结构的支撑力和抗震能力。
3. 预应力支护:使用钢筋或钢缆对隧道结构进行预应力处理,增加其抗拉能力和稳定性。
4. 防水处理:采取防水涂层、排水系统等措施,防止地下水对隧道结构的侵蚀和渗透。
5. 隧道衬砌:在隧道内壁覆盖防护材料,增加其抗压能力和防腐蚀性能。
施工安全要求
为确保隧道支护工程施工过程中的人员和设备安全,以下安全要求需要得到严格遵守:
1. 确保施工现场清晰明了的安全标识,包括警示标识、安全通道、禁行区域等。
2. 按照施工规范和操作规程进行施工,严禁超负荷施工和未经授权的工作。
3. 组织施工人员进行必要的安全培训,并提供必要的个人防护装备。
4. 定期检查和维护施工设备,确保其正常运行和安全可靠。
5. 在施工过程中,保持与其他工种的良好沟通和协作,共同解决施工中的安全问题。
总结
隧道支护安全技术交底是确保隧道支护工程施工安全的重要环节。
通过采取适当的隧道支护技术,并遵守施工安全要求,可以有
效保护施工人员和设备的安全,同时确保隧道结构的稳定性和可靠性。
隧道工程技术交底6篇
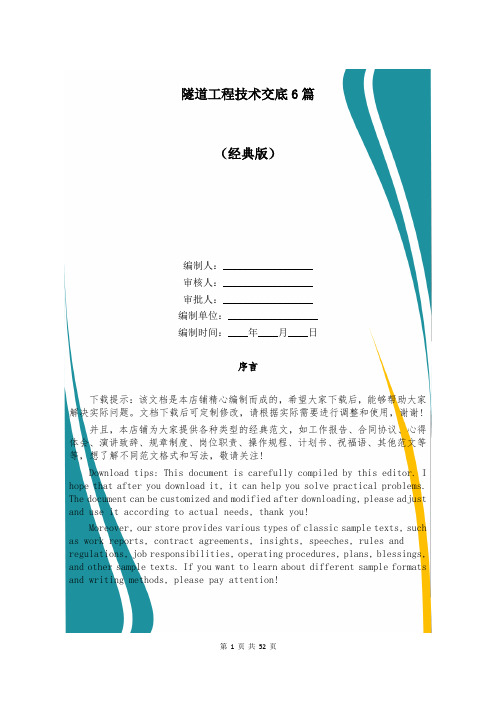
隧道工程技术交底6篇(经典版)编制人:__________________审核人:__________________审批人:__________________编制单位:__________________编制时间:____年____月____日序言下载提示:该文档是本店铺精心编制而成的,希望大家下载后,能够帮助大家解决实际问题。
文档下载后可定制修改,请根据实际需要进行调整和使用,谢谢!并且,本店铺为大家提供各种类型的经典范文,如工作报告、合同协议、心得体会、演讲致辞、规章制度、岗位职责、操作规程、计划书、祝福语、其他范文等等,想了解不同范文格式和写法,敬请关注!Download tips: This document is carefully compiled by this editor. I hope that after you download it, it can help you solve practical problems. The document can be customized and modified after downloading, please adjust and use it according to actual needs, thank you!Moreover, our store provides various types of classic sample texts, such as work reports, contract agreements, insights, speeches, rules and regulations, job responsibilities, operating procedures, plans, blessings, and other sample texts. If you want to learn about different sample formats and writing methods, please pay attention!隧道工程技术交底6篇【第1篇】隧道工程:施工安全技术交底一、洞口工程1、洞口工程施工应符合下列规定:(1)、洞口的路基及边、仰坡断面应自上而下开挖,一次将土石方工程做完,开挖人员不得上下重叠作业。
隧道工程初期支护施工安全技术交底

初期支护施工安全技术交底一、交底内容:1、初期支护施工安全技术交底二、安全要求:1、隧道各部开挖后,除围岩完整坚硬,以及设计文件中规定的不需支护外,都必须根据围岩情况、施工设计采取有效的支护。
2、施工期间,现场施工负责人应会同有关人员对支护各部定期进行检查。
在不良地质地段每班应设专人随时检查,当发现支护变形或损坏时,应立即整修和加固;当变形或损坏情况严重时,应先将施工人员撤离现场,再行加固。
3、洞内支护,宜随挖随支护,支护至开挖面的距离一般不得超过4m如遇石质破碎、风化严重和土质隧道时,应尽量缩小支护工作面。
当短期停工时,应将支撑直抵工作面。
4、不得将支撑立柱置于废碴或活动的石头上。
软弱围岩地段的立柱应加设垫板或垫梁,并加木楔塞紧。
7、钢支架安装,宜选用小型机具进行吊装,并应遵守本规程“起重吊装”的规定。
8、喷锚支护时,危石应先清除干净,脚手架应牢固可靠,喷射手应配戴防护用品;机械各部应完好正常,压力应保持在0.2MPa左右;注浆管喷嘴严禁对人放置。
9、当发现已喷锚区段的围岩有较大变形或锚杆失效时,应立即在该区段增设加强锚杆,其长度应不小于原锚杆长度的1.5倍。
如喷锚后发现围岩突变或围岩变形量超过设计允许值时,宜用钢支架支护。
10、当发现测量数据有不正常变化或突变,洞内或地表位移值大于允许位移值,洞内或地面出现裂缝以及喷层出现异常裂缝时,均应视为危险信号,必须立即通知作业人员撤离现场,待制定处理措施后才能继续施工。
安全技术交底主要包括两个方面的内容:一是在施工方案的基础上按照施工的要求,对施工方案进行细化和补充;二是要将操作者的安全注意事项讲清楚,保证作业人员的人身安全。
安全技术交底工作完毕后,所有参加交底的人员必须履行签字手续,施工负责人、生产班组、现场专职安全管理人员三方各留执一份,并纪录存档安全技术交底的作用。
安全技术交底的目的:在工程施工开工前,组织工程技术人员、施工管理人员和一线施工作业人员开展安全技术交底活动,把即将开展施工需要交待的施工工艺、工序、投入的机械设备、工程质量要求、施工过程中存在的危险因素、应对危险的安全技术措施、预防措施、应对突发事件危害的应急处置措施和救援行动需要注意的事项等进行交待。
隧道支护作业安全技术交底模板
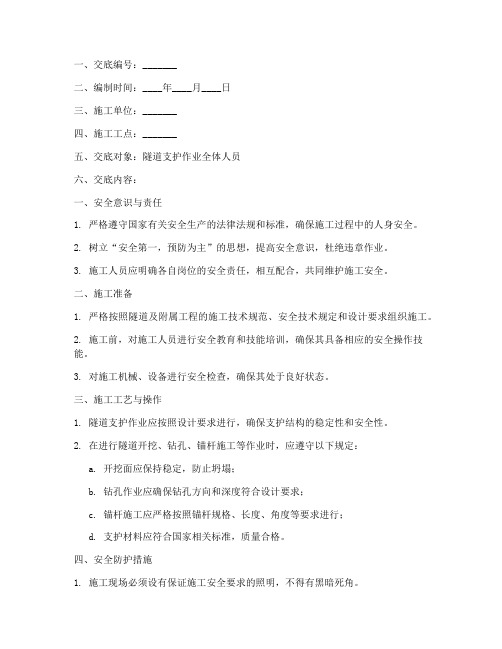
一、交底编号:_______二、编制时间:____年____月____日三、施工单位:_______四、施工工点:_______五、交底对象:隧道支护作业全体人员六、交底内容:一、安全意识与责任1. 严格遵守国家有关安全生产的法律法规和标准,确保施工过程中的人身安全。
2. 树立“安全第一,预防为主”的思想,提高安全意识,杜绝违章作业。
3. 施工人员应明确各自岗位的安全责任,相互配合,共同维护施工安全。
二、施工准备1. 严格按照隧道及附属工程的施工技术规范、安全技术规定和设计要求组织施工。
2. 施工前,对施工人员进行安全教育和技能培训,确保其具备相应的安全操作技能。
3. 对施工机械、设备进行安全检查,确保其处于良好状态。
三、施工工艺与操作1. 隧道支护作业应按照设计要求进行,确保支护结构的稳定性和安全性。
2. 在进行隧道开挖、钻孔、锚杆施工等作业时,应遵守以下规定:a. 开挖面应保持稳定,防止坍塌;b. 钻孔作业应确保钻孔方向和深度符合设计要求;c. 锚杆施工应严格按照锚杆规格、长度、角度等要求进行;d. 支护材料应符合国家相关标准,质量合格。
四、安全防护措施1. 施工现场必须设有保证施工安全要求的照明,不得有黑暗死角。
2. 进入施工现场的人员,按规定戴好安全帽,作业人员不得穿拖鞋、高跟鞋、硬底易滑鞋。
3. 两米以上高空作业配戴安全带,系好保险扣。
4. 严格执行现场临时用电线路安全规范,非电工严禁任意拉线接电。
5. 施工现场应设置安全警示标志,提醒施工人员注意安全。
五、应急处理1. 施工过程中,如发生安全事故,应立即启动应急预案,组织人员进行救援。
2. 事故发生后,应及时上报相关部门,做好事故调查和处理工作。
六、其他注意事项1. 施工人员应严格按照操作规程进行作业,不得擅自更改施工工艺。
2. 施工过程中,如发现安全隐患,应立即停止作业,并及时上报。
3. 施工结束后,对施工场地进行清理,确保不留安全隐患。
- 1、下载文档前请自行甄别文档内容的完整性,平台不提供额外的编辑、内容补充、找答案等附加服务。
- 2、"仅部分预览"的文档,不可在线预览部分如存在完整性等问题,可反馈申请退款(可完整预览的文档不适用该条件!)。
- 3、如文档侵犯您的权益,请联系客服反馈,我们会尽快为您处理(人工客服工作时间:9:00-18:30)。
隧道支护施工技术交底隧道锚喷支护施工技术交底一、适用范围适用于隧道施工。
二、施工工艺及操作要点1、超前支护A、小导管施工本隧道进出口Ⅱ类衬砌段由于岩体破碎,开挖时为了施工安全设有小导管注浆进行超前支护。
(1)小导管主要参数型号:φ42mm,壁厚4.0mm,无缝钢管;长度:4.5m;外插角:7°;环向间距:40cm;布置范围:拱部120°;搭接长度:>100cm。
(2) 小导管加工小导管前端10cm加工成尖形,以便插入,在管段中间部位钻四排φ8出浆孔,间距10cm,梅花型布置,后端预留30cm止浆段不钻孔;(3) 小导管施工小导管采用先钻孔后下钢管法施工,待喷射砼封闭岩面后,按照设计在拱部120°的范围内布设小导管,按照布孔位置用风动凿岩钻机先钻孔,使用高压风清孔,安设小导管,(或大锤)直接将小钢管打入岩层,并与预先埋设的钢架组合焊接在一起,后压注水泥浆。
(4)注浆施工参数①无水地段注单液浆(有水地段注双液浆)。
水泥浆水灰比为0.5:1~1:1。
注浆预加固后尽快开挖坑道;②注浆压力0.5~1MPa;③小导管注浆量计算:Q=πR2Lη式中:R—浆液扩散半径,取0.2m;L—小导管长度,取6m;η—岩体孔隙率,现场测定。
(5) 注浆压力控制注浆口最高压力严格控制在0.5Mpa(施工中可根据实际情况进行调整)以内,以防压裂工作面。
控制进浆速度,一般每根导管双液总进量控制在30L/min以内。
每根导管内注浆量由计算确定,若压力上升,流量减少,虽然注浆量未达到计算值,但孔口压力已达到0.5Mpa,结束注浆。
(6) 超前支护小导管施工工艺流程图超前小导管施工工艺流程图B、药卷锚杆施工本隧道中部Ⅲ类衬砌段由于岩体破碎,开挖时为了施工安全设有药卷锚杆进行超前支护。
(1) 药卷锚杆主要参数型号:φ22mm普通砂浆锚杆;长度:4.5m;外插角:7°;环向间距:40cm;布置范围:拱部90°;搭接长度:>100cm。
(2)锚杆孔施工药卷锚杆采用先钻孔后下锚杆法施工,待喷射砼封闭岩面后,按照设计在拱部90°的范围内布设药卷锚杆,按照布孔位置用风动凿岩钻机先钻孔,使用高压风清孔,安设药卷。
(3) 药卷锚杆安设药包随用随泡。
药包浸水前,先在其端头扎两个透气孔,然后竖直浸入水中约1~2分钟,待不冒气泡时,取出药包,按计算数量逐个依次装入孔内,第一节药包用木棍捅到孔底,装入药包到2/3孔深,再将锚杆插入,并缓慢转动以破碎药包,连续转动时间不少于1分钟,以保证充分搅拌均匀。
在搅动完毕后20分钟之后进行固定焊接药卷锚杆在已经安设好的格栅钢架上。
(4) 超前支护药卷锚杆施工工艺流程图药包锚杆施工程序框图2、初期支护(临时支护)A、φ25mm中空注浆锚杆施工(1)锚杆布置隧道初期支护锚杆按梅花型布置,Ⅱ型衬砌锚杆横向间距80cm,纵向间距为70cm。
Ⅲ型衬砌锚杆横向间距100cm ,纵向间距为90cm 。
单根锚杆长300cm 。
(2)锚杆施工采用风动凿岩钻机钻孔,高压风清孔,人工配合小型机具将锚杆插入。
注浆用注浆机进行,注浆压力控制在0.5~1Mpa ,并注意随时排除孔中空气。
(3)中空注浆锚杆施工工艺流程图如下:B 、挂钢筋网施工钢筋网使用Φ6.5盘条,Ⅱ类围岩网格为20㎝×20㎝,,Ⅲ类围岩网格为25㎝×25㎝,固结在锚杆端头上。
钢筋须调直除锈,按规定长度下料、安扎、焊、顺序堆放在工作面上使用。
钢筋网的铺设应设在锚杆施工后进行。
钢筋网应随喷射砼面的起伏进行铺设。
挂网在初喷砼及施作锚杆后进行。
钢筋网在洞外预制电焊成网片后安设,以节省挂网时间。
挂网时,钢筋网要紧贴岩面,网片间点焊搭接,并与邻近锚杆联接牢固。
网片的宽度据径向锚杆布置情况确定。
网片重量宜控制在100kg 左右,用在墙部的网片应上侧带钩,以方便挂设(如下图)。
中空注浆锚杆施工工艺框图初喷砼岩面钢 筋 网钢 筋 网C、工字钢(格栅)钢架施工(1)钢架加工制作:型钢钢架自行加工,洞外热弯预制。
按1:1 比例放样设立工作台。
按设计分节,垫板、螺栓联结。
加工做到尺寸准确,弧形圆顺。
格栅钢架节点焊接长度满足规范要求,焊接成型时,沿钢架两侧对称进行,格栅钢架主筋中心与轴线重合,连接孔位置准确。
钢架加工后先试拼,检查其平面翘曲和横断面误差。
钢架堆放和运输时不得损坏和变形。
(2)钢架安装:测量定位按设计位置现场测量定位。
首先测定出隧道中线,确定高程,然后再测定钢架的纵向位置;钢架平面必须与隧道中线垂直。
现场准备运至现场的单元钢架分单元堆码,安设前进行断面尺寸检查,及时处理欠挖侵入净空部分,保证钢架正确安设,安设拱脚或墙脚前,清除垫板下的松碴,将钢架置于原状岩石上,在软弱地段,采用垫钢板或槽钢的方法。
(3)钢架安设在初喷砼后进行,置于稳固地层上,超挖部分用混凝土回填。
安装时应备好风镐,随时剔除个别突出部位,保证钢架就位准确,受力可靠。
钢架与封闭砼之间紧贴,在安设过程中,当钢架与初喷混凝土面之间有较大间隙时安设垫块楔紧,垫块数量不少于10个,两排钢架间沿周边一般每隔1m用φ22纵向钢筋联接,形成纵向连接系。
拱脚高度不够时设置钢板调整,拱脚高度低于上半断面底线以下10cm。
钢架各单元之间用螺栓联接,不得以焊接代替。
钢架纵向间距符合设计,误差±100mm。
除纵向用钢筋连接外,与外露的锚杆头亦焊接牢固。
背部用混凝土垫块塞紧。
钢架落底接长应根据围岩条件沿隧道两侧交错进行,每次每侧接长1~3榀,如需立即封闭成环,则两侧同时进行,每次接长1榀。
拱部钢架与边墙钢架的连接采用螺栓,有困难时,也可采用焊接。
钢架安装后,即挂网、分层复喷混凝土,应先喷钢架处,然后喷钢架之间的砼,直至喷够设计厚度,将钢架完全覆盖2cm以上。
现场可用肉眼观察和锤击法进行检查。
(4)钢架安装施工程序框图钢架安装施工程序框图D、喷射砼施工(1)喷射砼的机具设备本隧道采用湿喷法。
喷射砼作业机具设备:砼喷射机、空气压缩机、搅拌机、上拌机具、供水设施。
(2)喷射砼的原材料和配合比1) 原材料:①水泥采用325#普硅水泥;②砂一般用坚硬耐久的中砂或粗砂,砂的含水率以5~7%为宜;③石子采用坚固耐久的碎石或卵石,粒径小于15㎜;④水:用洁净水;⑤速凝剂:采用BR型外加剂。
2) 配合比的选定:施工中选定,开始时采用1:1.98:2.02(3)喷射砼施工1) 场地布置:搅拌机一般布置在洞外,通过运输车运入洞内,然后给料于喷射机,同时应设晴雨棚,以控制砂石的含水率。
2) 清理工作面喷射砼,应认真检查开挖断面尺寸,欠挖者应予以凿除,修整断面,清理浮石及拱脚的虚碴等。
3) 喷射砼作业①混合料的备制a. 混合时,各种材料应按配合比准确称量;b. 采用强制式密封搅拌,时间不少于90秒;②机具就位机具安装在围岩稳定地段,保证输送线路通畅。
未上料前,先进行砼喷射机试运转:开启高压风及高压水,如喷嘴风压正常喷出的风水呈雾状,如喷嘴风压不足,可能出料口堵塞,如喷嘴不出风,则可能输料管堵塞。
有故障及时排除,待喷射机运转正常后才能进行喷射作业。
③喷射砼作业要点a、喷前应用高压风或高压水清洗岩面,将附着在岩面上的粉尘、硝屑冲洗干净,以保证砼与岩面粘结牢固。
若用高压水清洗会引起岩面软化时,只能用高压风清扫岩面杂物(视地质情况而定)。
b、严格掌握规定的速凝剂掺量,并添加均匀;c、喷射机工作风压一般控制在0.2~0.4MPa;d、喷射手严格控制水灰比,使喷层表面平整光滑,无干斑或滑移流淌现象;e、喷嘴的方向应与受喷岩面垂直,喷嘴与受喷岩面距离保持在0.6~1.0米范围;f、喷嘴移动轨迹应因地制宜,横条、竖条、圆圈等应交替使用,移动速度要慢,让砼“堆”起来,有了一定厚度再移开,然后逐块扩大其喷射范围;g、喷射顺序一般采用先下后上,先墙后拱;h、一次喷射厚度一般拱部为3~5㎝,边墙为6~8㎝;i、凹凸不平时应先将凹处喷平,按正常顺序喷射,以减少回弹;j、有钢筋网时,宜使喷嘴靠近钢筋,喷射角度也可适当偏一些,喷射砼应覆盖钢筋;k、有钢架时,钢架与围岩间隙必须以喷射砼充填密实,喷射砼应将钢架覆盖,并应由两侧拱脚向上喷射;l、喷完或间歇时,喷嘴应向低处放置,一工班结束,要拆开喷头,取出水环,用水清洗干净,疏通水眼,以备下一班使用。
喷完后,喷射机具均应清洗、保养,以保证机具处于完好状态。
④喷射砼的工艺参数:a、工作风压:一般为0.2~0.4MPa;b、喷射角度与喷射距离喷射料束与受喷面垂直时,回弹量最小;喷头与受喷面距离一般宜保持在0.6~1.0m;c、一次喷射砼的厚度:一般拱部为3~5㎝,边墙为6~8㎝;d、水灰比:喷射手应把水灰比控制在0.4~0.45,使喷层平整光滑,无干斑或滑移流淌现象;e、两次喷射的间隔:两层砼的喷射时间间隔太短,会由于前一层砼未达到强度而拉裂坠落,间隔时间过长,又会影响施工效率,较合理的间隔时间是前一层砼终凝,并达到一定强度后再复喷,一般可在20分钟以后进行。
f、养护(干燥处):喷射砼由于喷层内外部分干燥条件有异,必须进行养护,《规则》规定:喷射砼终凝后两小时起即开始养护,养护不得少于7天。
g、水压:喷头处水压控制在0.15~0.2MPa;h、速凝剂:掌握规定的掺量,并添加均匀。
4、需注意的问题①喷射机的合理使用启动喷射机时,应先送风再开机,并应在机械运转正常后送料,供料均匀连续。
作业结束时,先停止送料,待罐内余料喷完,再停机,然后关风。
停止喷射作业后,喷射机和输料管内的积料应及时清除干净,以避免混合料结块堵管。
②输料管堵塞问题堵管的一般原因不外乎以下几种:a、混合料中混入超规定粒径的石子、水泥硬块或其它杂物。
b、操作程序有误,如先开马达后送风,或砂子含水率过高,操作阀错开,致使高压风大量泄出,使工作室内风压急剧下降,也会引韦输料管堵塞。
c、如遇堵客,应立即关闭马达,随后关闭风源,并将软管拉直,然后以手锤敲击找到堵塞位置,可将风压开到0.3~0.4MPa,同时继续敲击堵塞部位,使其排除堵塞物而畅通。
排除堵管现象时,应注意喷嘴前方严禁站人,以免发生伤人事故。
③回弹问题影响回弹率的各种因素有:混合料配合比、水灰比、砂子含水率、工作风压、水压、喷射距离、喷射角度、操作方法及熟练程度等。
针对各种因素,采取相应的措施降低回弹率。
《规则》规定正常情况下的回弹率,一般拱部为20~30%,边墙为10~20%。
④粉尘问题a、控制砂石料含水率:当含水率控制在5~7%时,作业时的粉尘浓度可控制在15mg/m3以下;b、加强通风;c、加长拢料管:即在喷嘴水环到出口之间接一段0.5~1m长的管子,使干料与水混合后有一个充分湿润和混合的过程,这对降尘和提高砼质量都较为有利。