锂离子电池搅拌和涂布工艺及异常处理
锂电池制作过程中常见异常及解决方案

锂电池制作过程中常见异常及解决方案一、浆料异常及解决方案异常1:沉降,粘度变化大原因:浆料不稳定的原因是吸水,粘接剂少,未分散好;解决方法:调整原材料选型,主要是考虑比表,粘度等,调整搅伴工艺(主要转速,线速度,时间等),调整粘结剂用量,控制环境水分。
异常2:固含量低原因:消耗NMP多,主要原因是正极比表大,正极径小,搅伴时间长,粘接剂固含量低;解决方法:调整搅伴工艺(主要转速,线速度,时间等),调整正极选型,调整粘结剂选型。
异常3:难过筛原因:大颗粒,主要原因是正极大颗粒,正极粘度高,吸水团聚;解决方法:控制材料颗粒,降低浆料粘度,防止吸水。
异常4:无流动性,变果冻原因:吸水,主要原因是正极水分高,正极PH高,正极比表大,NMP水分高,环境湿度大,粘结剂水分高;解决方法:控制环境湿度,控制原材料水分,降低原材料PH值。
二、辊压前极片异常解决方案异常1:颗粒原因:主要原因是有颗粒或团聚,原材料大颗粒,浆料粘度高,浆料团聚;解决方案:减少材料大颗粒,降低浆料粘度,控制吸水;异常2:裂纹原因:是极片内NMP挥发慢,烘箱温度高,涂布速度快;解决方法:降低前段烘箱温度,降低涂布速度;异常3:气泡原因:浆料有气泡主要是因抽真空不彻底,搁置时间短,抽真空时搅伴速度过快;解决方法:延长抽真空时间,加入表面活性剂消泡;异常4:划痕原因:主要是浆料粘度高,来料大颗粒,浆料团聚,涂布刀口有干料;解决方法:减少材料大颗粒,降低浆料粘度,控制吸水;异常5:拖尾原因:主要是粘度偏高或粘度偏低;解决方法:调整粘度;异常6:质量不稳定原因:浆料不稳定的主要原因是浆料吸水,粘结剂胶水用量少,未分散好,涂布设备波动;解决方法:控制吸水,调整设备,调整粘度;三、辊压后极片异常及解决方案异常1:断片,脆片原因:使用压实过高的原因有烘烤时间长,温度高,粘结剂胶水变性,极片吸水;解决方法:降低压实,极片烘烤时间缩短;异常2:白点原因:极片内层NMP挥发慢的原因是烘箱温度高,涂布速度快;解决方法:控制吸水(原材料,环境);异常3:起皮,掉料原因:脱粉主要是材料水分敏感,极片存储环境湿度大;解决方法:控制吸水(原材料,环境);四、电芯异常及解决方案异常1:电芯工艺,电芯卷绕过松负极过量比设计不合理,安全系数低,正负未包裹正极,正负极片距离不均匀等原因;解决方法:控制卷绕工艺一致性,提高负极过量化,修改正负极片长度设计,优化电芯制作工艺;异常2:正极,混料过程不均匀,解决方法:控制浆料一致性及涂布一致性;异常3:负极,局部区域量少,浸润性差,压实过高或过低,颗粒太大,有效嵌锂面积小,材料配向性差或导电性差,面密度过高,混料不均匀,粘接剂锂电胶水上浮等问题;解决方法:控制浆料一致性及涂布一致性,优化负极过量比,控制原材料颗粒,优化负极配比,优化负极面密度,优化锂胶水粘合剂型号;异常4:电解液,电导率低,粘度大,SEI膜阻抗大,电解液中有气泡,SEI膜不均匀等问题;解决方法:提高电解液电导率,降低电解液粘度,优选成膜添加剂,控制电解气泡,控制化成工艺,保证成膜一致性;异常5:隔膜,孔隙率低,隔膜对电解液浸润性差,孔隙分布不均匀等问题;解决方法:优选孔隙率适合的隔膜,提高电解液的浸润性,控制隔膜来料,保证一致性;异常6:充电制度,充电电流大,充电温度低,截止电压高,电芯内温度分布不均匀等问题;解决方法:小电流化成,适当降低环境温度,适当降低充电截止电压,提高极片过流能力(宽极耳);五、电性能异常分析及解决方案异常1:平台低原因:电解液粘度大,电芯内阻大,放电电流大,环境温度低等问题;解决方法:电解液来料相关指标确认及优化,电芯内阻影响因素确认,控制环境温度及放电电流;异常2:容量低:原因:正极敷料量少,压实偏大,负极效率低,环境温度低,电芯吸水,电芯倍率差,电解液浸润性差等问题;解决方法:正极敷料量确认,正极压实及挥发确认,负极压实及首效确认,电芯倍率及测试环境温度等确认,拆解失效电池分板界面情况及影响因素;异常3:自放电大:原因:原材料杂质多,极片微粉多,极片分切毛刺大,隔膜孔隙率大等问题;解决方法:制程中各工序及设备控制,金属杂质来源查找并控制,各原材料的金属材质含量确认,隔膜及其他辅料性能确认;异常4:高温存储差:原因:电解液高温性能差,电芯水分含量偏高,正极残锂量高等问题;解决方法:电解液水分配方成分确认,电芯制程水分控制,正极残锂量确认;异常5:倍率差:原因:导电剂少,正极粘结性差,电芯内阻大,压实偏大,隔膜性能影响,电解液电导率低等问题;解决方法:配方及设计参数确认,电芯内阻相关因素确认,电芯制程的环境控制,拆解失效电池分析界面情况及影响因素;异常6:循环差:原因:负极析锂,过程吸水,隔膜透气性差,压实偏大,测试温度变化,注液量少,SEI膜成膜差等问题;解决方法:压实及注液量等影响因素确认,负极过量比优化,电芯倍率及测试环境温度等确认,拆解失效电池分析界面情况及影响因素;。
锂电池涂布工序
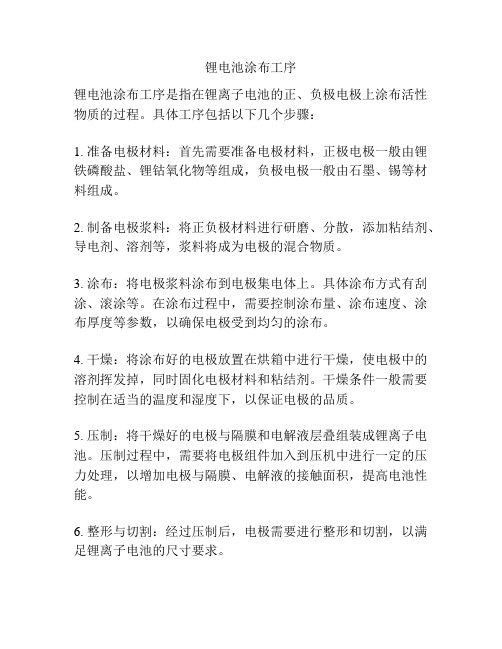
锂电池涂布工序
锂电池涂布工序是指在锂离子电池的正、负极电极上涂布活性物质的过程。
具体工序包括以下几个步骤:
1. 准备电极材料:首先需要准备电极材料,正极电极一般由锂铁磷酸盐、锂钴氧化物等组成,负极电极一般由石墨、锡等材料组成。
2. 制备电极浆料:将正负极材料进行研磨、分散,添加粘结剂、导电剂、溶剂等,浆料将成为电极的混合物质。
3. 涂布:将电极浆料涂布到电极集电体上。
具体涂布方式有刮涂、滚涂等。
在涂布过程中,需要控制涂布量、涂布速度、涂布厚度等参数,以确保电极受到均匀的涂布。
4. 干燥:将涂布好的电极放置在烘箱中进行干燥,使电极中的溶剂挥发掉,同时固化电极材料和粘结剂。
干燥条件一般需要控制在适当的温度和湿度下,以保证电极的品质。
5. 压制:将干燥好的电极与隔膜和电解液层叠组装成锂离子电池。
压制过程中,需要将电极组件加入到压机中进行一定的压力处理,以增加电极与隔膜、电解液的接触面积,提高电池性能。
6. 整形与切割:经过压制后,电极需要进行整形和切割,以满足锂离子电池的尺寸要求。
以上就是锂电池涂布工序的基本步骤,每个步骤的细节和操作要求会根据锂电池的型号和规格有所不同。
锂离子电池隔膜制造工艺
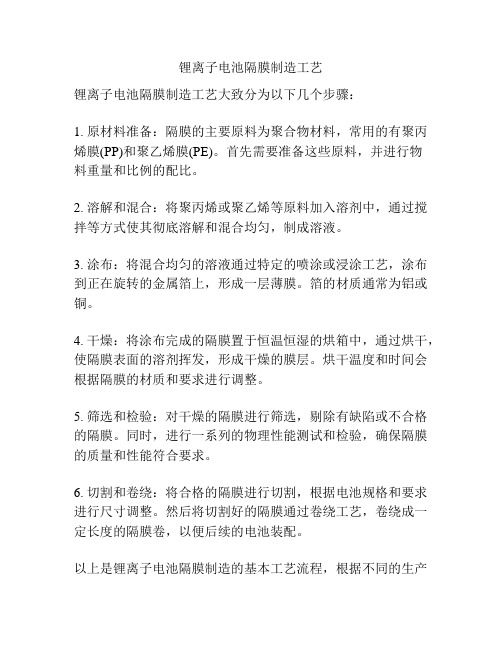
锂离子电池隔膜制造工艺
锂离子电池隔膜制造工艺大致分为以下几个步骤:
1. 原材料准备:隔膜的主要原料为聚合物材料,常用的有聚丙烯膜(PP)和聚乙烯膜(PE)。
首先需要准备这些原料,并进行物
料重量和比例的配比。
2. 溶解和混合:将聚丙烯或聚乙烯等原料加入溶剂中,通过搅拌等方式使其彻底溶解和混合均匀,制成溶液。
3. 涂布:将混合均匀的溶液通过特定的喷涂或浸涂工艺,涂布到正在旋转的金属箔上,形成一层薄膜。
箔的材质通常为铝或铜。
4. 干燥:将涂布完成的隔膜置于恒温恒湿的烘箱中,通过烘干,使隔膜表面的溶剂挥发,形成干燥的膜层。
烘干温度和时间会根据隔膜的材质和要求进行调整。
5. 筛选和检验:对干燥的隔膜进行筛选,剔除有缺陷或不合格的隔膜。
同时,进行一系列的物理性能测试和检验,确保隔膜的质量和性能符合要求。
6. 切割和卷绕:将合格的隔膜进行切割,根据电池规格和要求进行尺寸调整。
然后将切割好的隔膜通过卷绕工艺,卷绕成一定长度的隔膜卷,以便后续的电池装配。
以上是锂离子电池隔膜制造的基本工艺流程,根据不同的生产
工艺和要求,可能会有一些细节上的差异。
此外,隔膜的制造中还需要注意工艺参数、设备条件和环境条件等方面的控制,以确保隔膜的质量和稳定性。
锂离子电池原理常见不良项目及成因涂布方法汇总

锂离子电池原理常见不良项目及成因涂布方法汇总一、锂离子电池原理1.正极:通常采用锂化合物(如LiCoO2、LiFePO4)作为正极材料。
正极材料能嵌入或释放锂离子。
2.负极:通常采用石墨作为负极材料。
负极材料能嵌入或释放锂离子。
3.电解液:电解液是锂离子传输的介质,通常由有机溶剂和一种锂盐组成。
4.隔膜:隔膜起到隔离正负极的作用,防止短路。
在充电过程中,锂离子从正极材料中嵌出,经过电解液迁移到负极材料中嵌入。
在放电过程中,则反之。
正负极嵌入或嵌出锂离子的过程伴随着电子的流动,从而产生电能。
二、常见不良项目及成因1.容量衰减:锂离子电池的容量随着使用次数和充放电次数的增加而逐渐衰减。
这是由于正负极材料的脱钠和脱锂导致的。
2.电池发热:电池发热可能是由于不均匀的电池放电、充电导致的。
3.电池容量不匹配:电池组中的不同电池单体之间容量差异较大,导致一些单体的电压和容量迅速下降。
4.短路:短路可能是由于电池在使用过程中遭受外来损坏,引起正负极的直接连接。
以上这些不良项目的成因多是因为电池的设计不合理、材料不理想或使用环境不恰当等因素导致的。
三、涂布方法1.滚涂法:滚涂法是一种常用的涂布方法,通过将浆料涂刷在转动的滚筒上,然后将电极片从滚筒上剥离,完成正负极材料的涂布。
2.刮涂法:刮涂法是将浆料用刮刀均匀地涂抹在电极片上,然后通过烘干等工艺固化材料。
3.喷涂法:喷涂法是利用高速风切割浆料,将其喷射到电极片上,在快速干燥后,形成均匀的材料膜。
以上这些涂布方法各有优缺点,选用何种方法取决于电池设计的要求以及制造工艺的实际条件。
总结:锂离子电池是一种重要的电池类型,广泛应用于各个领域。
通过正负极的嵌入和嵌出实现充放电过程。
在使用过程中可能出现不良项目,如容量衰减、发热等,其成因多与设计、材料、使用环境等因素有关。
涂布方法有滚涂法、刮涂法和喷涂法等,选用何种方法需根据实际情况决定。
这些信息可以帮助我们更好地了解锂离子电池的原理和制造工艺。
锂离子电池正负极浆料搅拌工艺总结
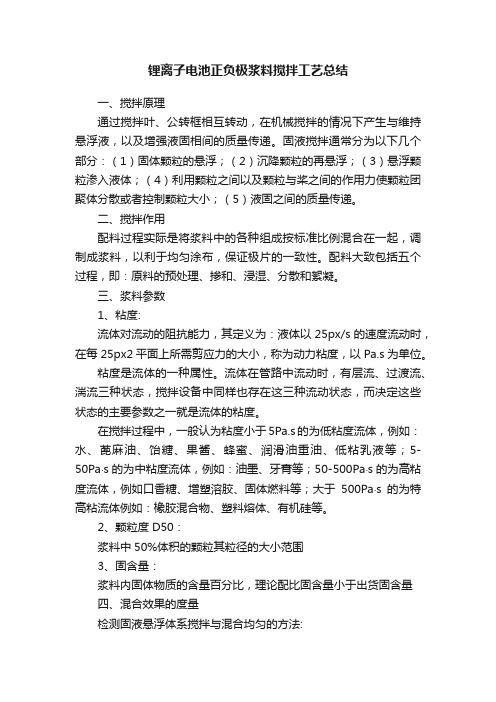
锂离子电池正负极浆料搅拌工艺总结一、搅拌原理通过搅拌叶、公转框相互转动,在机械搅拌的情况下产生与维持悬浮液,以及增强液固相间的质量传递。
固液搅拌通常分为以下几个部分:(1)固体颗粒的悬浮;(2)沉降颗粒的再悬浮;(3)悬浮颗粒渗入液体;(4)利用颗粒之间以及颗粒与桨之间的作用力使颗粒团聚体分散或者控制颗粒大小;(5)液固之间的质量传递。
二、搅拌作用配料过程实际是将浆料中的各种组成按标准比例混合在一起,调制成浆料,以利于均匀涂布,保证极片的一致性。
配料大致包括五个过程,即:原料的预处理、掺和、浸湿、分散和絮凝。
三、浆料参数1、粘度:流体对流动的阻抗能力,其定义为:液体以25px/s的速度流动时,在每25px2平面上所需剪应力的大小,称为动力粘度,以Pa.s为单位。
粘度是流体的一种属性。
流体在管路中流动时,有层流、过渡流、湍流三种状态,搅拌设备中同样也存在这三种流动状态,而决定这些状态的主要参数之一就是流体的粘度。
在搅拌过程中,一般认为粘度小于5Pa.s的为低粘度流体,例如:水、蓖麻油、饴糖、果酱、蜂蜜、润滑油重油、低粘乳液等;5-50Pa⋅s的为中粘度流体,例如:油墨、牙膏等;50-500Pa⋅s的为高粘度流体,例如口香糖、增塑溶胶、固体燃料等;大于500Pa⋅s的为特高粘流体例如:橡胶混合物、塑料熔体、有机硅等。
2、颗粒度D50:浆料中50%体积的颗粒其粒径的大小范围3、固含量:浆料内固体物质的含量百分比,理论配比固含量小于出货固含量四、混合效果的度量检测固液悬浮体系搅拌与混合均匀的方法:1、直接测量1)粘度法:从体系不同位置取样,用粘度计测量浆料的粘度;偏差越小,混合越均匀;2)颗粒度法:A,从体系不同位置取样,用颗粒度刮板仪观察浆料的颗粒度;粒度越接近原材料粉末大小,混合越均匀;B,从体系不同位置取样,用激光衍射颗粒度测试仪观察浆料的颗粒度;粒度分布越正态,大颗粒越小,混合越均匀;3)比重法:从体系不同位置取样,测量浆料的密度,偏差越小混合越均匀2、间接测量1)固含量法(宏观):从体系不同位置取样,经过适当的温度和时间的烘烤,测固体份的重量,偏差越小混合越均匀;2)SEM/EPMA(微观):从体系不同位置取样,涂布到基材上,烘干,用SEM(电子显微镜) /EPMA(电子探针)观察浆料干燥后膜片内颗粒或元素的分布;(体系固体份通常为导体材料)五、阳极搅拌工艺Conductive carbon black(导电碳黑):用做导电剂。
锂电池涂布工序常见故障和解决方法汇总

锂电池涂布工序是锂电池生产中非常关键的一环,涂布工序的质量直接影响着锂电池的性能和安全性。
然而,在实际生产过程中,涂布工序常常会出现各种故障,影响整个生产线的正常运转。
本文将就锂电池涂布工序常见的故障进行梳理和总结,并提供相应的解决方法,以期为从事锂电池生产的工程师和技术人员提供一定的参考和帮助。
1. 涂布机出现涂布不均匀情况1.1 可能原因:涂布刀片磨损不均匀,导致涂布厚度不均匀;涂布辊与输送辊之间的间隙不一致;涂布材料的粘度不一致。
1.2 解决方法:定期更换涂布刀片,保持其锋利度;调整涂布辊与输送辊的间隙,确保一致;加强涂布材料的粘度控制,确保一致。
2. 涂布机出现漏涂现象2.1 可能原因:涂布刀片损坏或安装不良;输送辊转速过快,导致涂布材料无法被充分涂覆;涂布材料的粘度过高,无法完全附着在电极上。
2.2 解决方法:检查涂布刀片的完好度并及时更换;适当调整输送辊的转速,确保涂布材料可以被充分涂覆;控制涂布材料的粘度,避免过高。
3. 涂布机出现起泡现象3.1 可能原因:涂布材料的挥发性成分过快,导致涂布过程中产生气泡;涂布刀片与电极间的间隙不一致,导致气体无法顺利逸出。
3.2 解决方法:调整涂布材料的挥发性成分,避免过快;确保涂布刀片与电极间的间隙一致,避免气泡产生。
4. 涂布机出现堵塞现象4.1 可能原因:涂布材料中有杂质,导致管道堵塞;输送辊转速过慢,无法及时排出涂布材料。
4.2 解决方法:加强涂布材料的过滤工作,确保无杂质;适当调整输送辊的转速,确保涂布材料能够顺利流动。
5. 涂布机出现电极破损现象5.1 可能原因:输送辊表面粗糙,易划伤电极;涂布刀片安装不稳,易引起电极损伤。
5.2 解决方法:定期对输送辊进行维护和更换,确保表面光滑;定期检查涂布刀片的安装情况,确保稳定可靠。
总结:通过对锂电池涂布工序常见故障和解决方法的梳理和总结,我们可以看到,涂布工序的质量受到多种因素的影响,需要全面而细致的管理和维护。
锂电浆料涂布瑕疵及改善方法
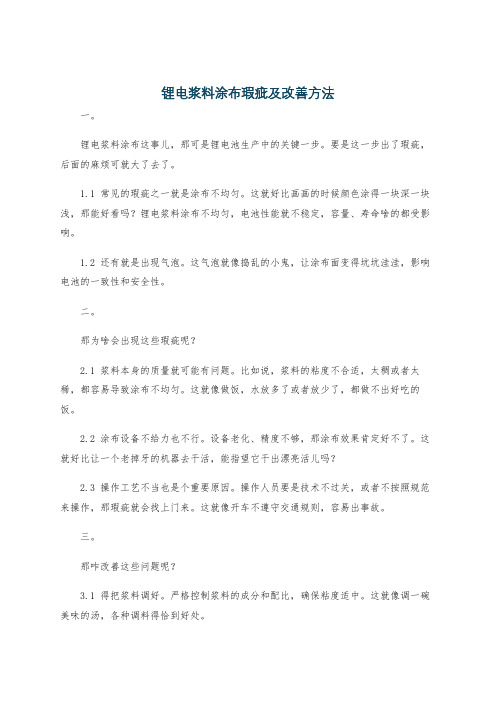
锂电浆料涂布瑕疵及改善方法
一。
锂电浆料涂布这事儿,那可是锂电池生产中的关键一步。
要是这一步出了瑕疵,后面的麻烦可就大了去了。
1.1 常见的瑕疵之一就是涂布不均匀。
这就好比画画的时候颜色涂得一块深一块浅,那能好看吗?锂电浆料涂布不均匀,电池性能就不稳定,容量、寿命啥的都受影响。
1.2 还有就是出现气泡。
这气泡就像捣乱的小鬼,让涂布面变得坑坑洼洼,影响电池的一致性和安全性。
二。
那为啥会出现这些瑕疵呢?
2.1 浆料本身的质量就可能有问题。
比如说,浆料的粘度不合适,太稠或者太稀,都容易导致涂布不均匀。
这就像做饭,水放多了或者放少了,都做不出好吃的饭。
2.2 涂布设备不给力也不行。
设备老化、精度不够,那涂布效果肯定好不了。
这就好比让一个老掉牙的机器去干活,能指望它干出漂亮活儿吗?
2.3 操作工艺不当也是个重要原因。
操作人员要是技术不过关,或者不按照规范来操作,那瑕疵就会找上门来。
这就像开车不遵守交通规则,容易出事故。
三。
那咋改善这些问题呢?
3.1 得把浆料调好。
严格控制浆料的成分和配比,确保粘度适中。
这就像调一碗美味的汤,各种调料得恰到好处。
3.2 设备要更新维护。
定期检查设备,有问题及时修,该换新的就换新的。
别心疼那点钱,不然因小失大。
锂电浆料涂布这事儿可不能马虎,得用心去做,才能做出高质量的锂电池,让咱们的新能源产业越来越好!。
锂离子电池的制浆与涂布关键影响因素

锂离子电池的制浆与涂布关键影响因素锂离子电池是目前最常用的二次电池,制浆与涂布工艺是锂离子电池制造过程中的两个关键步骤。
制浆是将正负极材料与电解质混合制成浆料,并通过特定的工艺流程形成电极片;涂布是将电极片通过涂覆技术涂布在导电膜上,形成电池的正负极。
影响锂离子电池制浆与涂布工艺的关键因素有以下几个方面:1.原材料选择:正负极材料是锂离子电池的核心材料,选择合适的原材料对电池的性能有重要影响。
首先,正负极材料的比容量和容量保持率应该高,以提高电池的能量密度和循环寿命;其次,正负极材料的颗粒粒径应均匀,以提高电池的充放电效率;再次,正负极材料应具有良好的化学稳定性和电化学性能。
2.制浆配方:制浆过程是将正负极材料与电解质混合制成浆料的过程,制浆配方的调整可以影响材料的分散性、可流动性和粘度等性质。
制浆配方需要合理控制正负极材料、电解质和溶剂的比例,以确保电解质的饱和度和粘度合适,并且避免产生过多的气泡和杂质。
3.浆料混合及分散工艺:混合和分散工艺对浆料的均匀性和粒径分布有重要影响。
通过机械搅拌、超声波处理、高压均质等方式,可以有效提高浆料的混合程度和颗粒的分散状态,以保证最终电极片的均匀性和性能。
4.涂布工艺参数:涂布过程是将浆料涂布在导电膜上的过程,涂布工艺参数的选择对电极片的厚度、颗粒分布、孔隙度等性能有重要影响。
主要的涂布参数包括浆料流量、刮涂速度、压力等,在涂布过程中需要根据实际情况进行合理的调整,以确保涂布均匀且不产生空隙或刮痕。
5.成型和烘干工艺:成型和烘干是将涂布好的电极片进行加工和固化的过程。
成型工艺可以通过压缩和模具设计来改变电极片的孔隙度和形状,以提高电池的性能。
而烘干过程则需要控制温度和湿度等参数,以确保电极片干燥充分且不出现变形等问题。
总之,锂离子电池的制浆与涂布工艺是锂离子电池制造过程中的两个关键环节。
原材料选择、制浆配方、浆料混合和分散工艺、涂布工艺参数以及成型和烘干工艺等因素的合理调控,可以改善电极片的性能,提高锂离子电池的容量、循环寿命和安全性能。
锂电池浆料搅拌工艺常见问题及解决措施
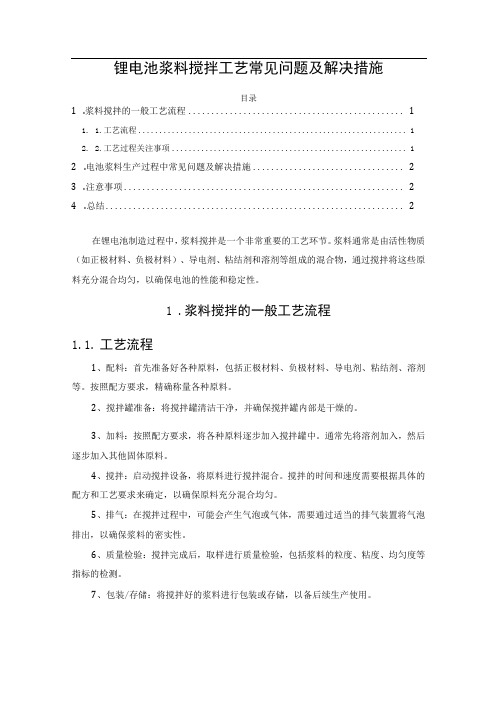
锂电池浆料搅拌工艺常见问题及解决措施目录1.浆料搅拌的一般工艺流程 (1)1. 1.工艺流程 (1)2. 2.工艺过程关注事项 (1)2.电池浆料生产过程中常见问题及解决措施 (2)3.注意事项 (2)4.总结 (2)在锂电池制造过程中,浆料搅拌是一个非常重要的工艺环节。
浆料通常是由活性物质(如正极材料、负极材料)、导电剂、粘结剂和溶剂等组成的混合物,通过搅拌将这些原料充分混合均匀,以确保电池的性能和稳定性。
1.浆料搅拌的一般工艺流程1.1.工艺流程1、配料:首先准备好各种原料,包括正极材料、负极材料、导电剂、粘结剂、溶剂等。
按照配方要求,精确称量各种原料。
2、搅拌罐准备:将搅拌罐清洁干净,并确保搅拌罐内部是干燥的。
3、加料:按照配方要求,将各种原料逐步加入搅拌罐中。
通常先将溶剂加入,然后逐步加入其他固体原料。
4、搅拌:启动搅拌设备,将原料进行搅拌混合。
搅拌的时间和速度需要根据具体的配方和工艺要求来确定,以确保原料充分混合均匀。
5、排气:在搅拌过程中,可能会产生气泡或气体,需要通过适当的排气装置将气泡排出,以确保浆料的密实性。
6、质量检验:搅拌完成后,取样进行质量检验,包括浆料的粒度、粘度、均匀度等指标的检测。
7、包装/存储:将搅拌好的浆料进行包装或存储,以备后续生产使用。
1.2.工艺过程关注事项确保搅拌设备的清洁和消毒,以防止交叉污染。
严格按照配方要求进行原料的称量和加入,避免误差。
控制搅拌时间和速度,确保原料充分混合均匀。
对搅拌后的浆料进行质量检验,确保符合产品要求。
2.电池浆料生产过程中常见问题及解决措施3.注意事项1、确保设备的连续操作能够满足产品质量和稳定性的要求。
2、确保封闭式系统的设计不会影响原料的顺畅投入,并定期清洁系统以防止堵塞。
3、确保选用的分散方法不会对产品质量造成负面影响。
4、清洗设备时要遵循正确的操作程序,以确保清洁彻底并避免交叉污染。
5、确保设备操作符合安全标准,避免使用有潜在危险的气体。
锂离子电池合浆涂布流程
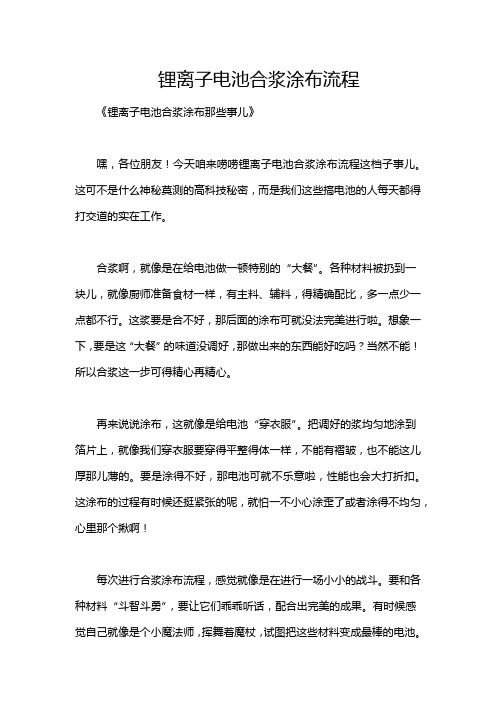
锂离子电池合浆涂布流程《锂离子电池合浆涂布那些事儿》嘿,各位朋友!今天咱来唠唠锂离子电池合浆涂布流程这档子事儿。
这可不是什么神秘莫测的高科技秘密,而是我们这些搞电池的人每天都得打交道的实在工作。
合浆啊,就像是在给电池做一顿特别的“大餐”。
各种材料被扔到一块儿,就像厨师准备食材一样,有主料、辅料,得精确配比,多一点少一点都不行。
这浆要是合不好,那后面的涂布可就没法完美进行啦。
想象一下,要是这“大餐”的味道没调好,那做出来的东西能好吃吗?当然不能!所以合浆这一步可得精心再精心。
再来说说涂布,这就像是给电池“穿衣服”。
把调好的浆均匀地涂到箔片上,就像我们穿衣服要穿得平整得体一样,不能有褶皱,也不能这儿厚那儿薄的。
要是涂得不好,那电池可就不乐意啦,性能也会大打折扣。
这涂布的过程有时候还挺紧张的呢,就怕一不小心涂歪了或者涂得不均匀,心里那个揪啊!每次进行合浆涂布流程,感觉就像是在进行一场小小的战斗。
要和各种材料“斗智斗勇”,要让它们乖乖听话,配合出完美的成果。
有时候感觉自己就像是个小魔法师,挥舞着魔杖,试图把这些材料变成最棒的电池。
不过话说回来,这中间也有好多乐趣呢!看着那浆在机器里翻滚,然后被均匀地涂到箔片上,就有一种莫名的成就感。
有时候还会和同事们比一比谁涂得更好,更均匀,就像比赛一样,特别有意思。
这锂离子电池合浆涂布流程虽然看起来挺复杂,但只要用心去做,还是能享受到其中的乐趣的。
咱就是要把这普通的工作变得有意思起来,让每一块电池都带着咱的心血和汗水,在未来发挥出它们的大作用。
总之呢,锂离子电池合浆涂布流程就是这么个既重要又有趣的事儿。
要是你也对这方面感兴趣,或者以后有机会接触到这工作,可一定要好好体验体验,说不定你也会和我一样,爱上这个看似普通却充满挑战和乐趣的过程呢!哈哈,好了,今天就先唠到这儿,下次再和你们分享其他有趣的事儿哟!。
锂电池涂布后的工艺要求
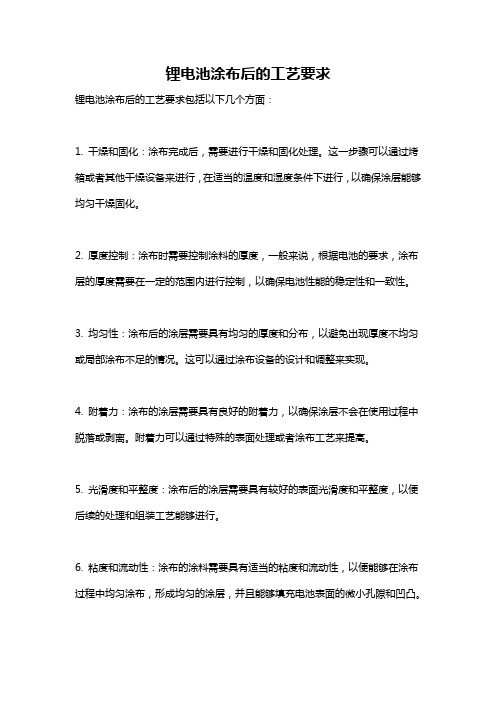
锂电池涂布后的工艺要求
锂电池涂布后的工艺要求包括以下几个方面:
1. 干燥和固化:涂布完成后,需要进行干燥和固化处理。
这一步骤可以通过烤箱或者其他干燥设备来进行,在适当的温度和湿度条件下进行,以确保涂层能够均匀干燥固化。
2. 厚度控制:涂布时需要控制涂料的厚度,一般来说,根据电池的要求,涂布层的厚度需要在一定的范围内进行控制,以确保电池性能的稳定性和一致性。
3. 均匀性:涂布后的涂层需要具有均匀的厚度和分布,以避免出现厚度不均匀或局部涂布不足的情况。
这可以通过涂布设备的设计和调整来实现。
4. 附着力:涂布的涂层需要具有良好的附着力,以确保涂层不会在使用过程中脱落或剥离。
附着力可以通过特殊的表面处理或者涂布工艺来提高。
5. 光滑度和平整度:涂布后的涂层需要具有较好的表面光滑度和平整度,以便后续的处理和组装工艺能够进行。
6. 粘度和流动性:涂布的涂料需要具有适当的粘度和流动性,以便能够在涂布过程中均匀涂布,形成均匀的涂层,并且能够填充电池表面的微小孔隙和凹凸。
7. 寿命和稳定性:涂布后的涂层需要具有良好的寿命和稳定性,以保证涂料在长期使用过程中不会发生变质或失效,影响电池的性能。
这可以通过选用合适的材料和添加剂,以及进行适当的贮存和包装来实现。
总之,锂电池涂布后的工艺要求涉及到干燥固化、厚度控制、均匀性、附着力、光滑度、粘度流动性、寿命稳定性等多个方面,需要通过合适的工艺和设备来进行控制和调整。
锂电涂布工艺

《锂电涂布工艺》
锂电涂布工艺在锂离子电池的生产中起着至关重要的作用。
锂电涂布是将电极浆料均匀地涂覆在集流体上的过程。
电极浆料通常由活性物质、导电剂、粘结剂和溶剂等组成。
集流体一般为铜箔(负极)和铝箔(正极)。
在涂布过程中,首先要确保浆料的质量稳定。
浆料的粘度、固含量等参数需要严格控制,以保证涂布的均匀性。
如果浆料太稀,可能会导致涂布厚度不均匀;如果浆料太稠,则可能会出现堵塞涂布设备的情况。
例如,有一家电池生产企业在生产过程中,由于浆料的粘度没有控制好,导致涂布后的电极出现厚度差异较大的问题,影响了电池的性能。
接着,选择合适的涂布方式也很关键。
目前常见的涂布方式有刮刀涂布、辊涂和喷涂等。
刮刀涂布适用于高精度的涂布要求,但设备成本较高;辊涂效率高,但对浆料的适应性相对较弱;喷涂则可以实现复杂形状的涂布,但可能会存在浪费浆料的情况。
企业需要根据自身的生产需求和产品特点选择合适的涂布方式。
涂布后的干燥过程也不容忽视。
干燥温度和时间需要合理控制,以确保电极中的溶剂充分挥发,同时避免活性物质的结构受到破坏。
如果干燥温度过高或时间过长,可能会导致电极开裂;如果干燥不充分,则会影响电池的性能和安全性。
总之,锂电涂布工艺是一个复杂而关键的环节,需要严格控制各个参数,确保涂布质量,从而提高锂离子电池的性能和可靠性。
锂电池制程异常案例分析
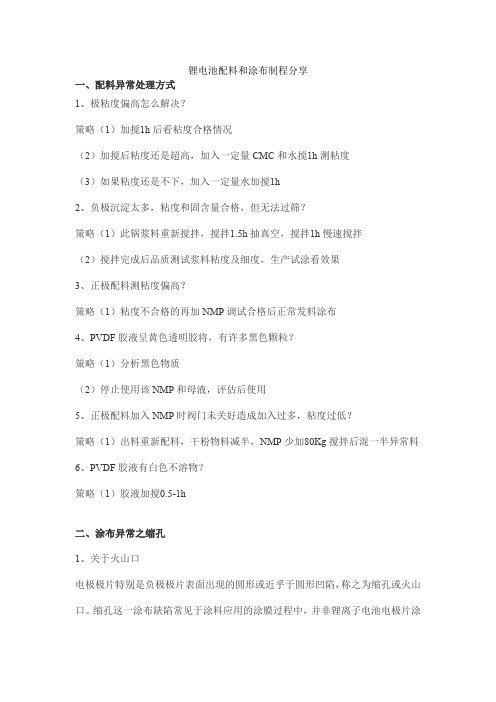
锂电池配料和涂布制程分享一、配料异常处理方式1、极粘度偏高怎么解决?策略(1)加搅1h后看粘度合格情况(2)加搅后粘度还是超高,加入一定量CMC和水搅1h测粘度(3)如果粘度还是不下,加入一定量水加搅1h2、负极沉淀太多,粘度和固含量合格,但无法过筛?策略(1)此锅浆料重新搅拌,搅拌1.5h抽真空,搅拌1h慢速搅拌(2)搅拌完成后品质测试浆料粘度及细度,生产试涂看效果3、正极配料测粘度偏高?策略(1)粘度不合格的再加NMP调试合格后正常发料涂布4、PVDF胶液呈黄色透明胶将,有许多黑色颗粒?策略(1)分析黑色物质(2)停止使用该NMP和母液,评估后使用5、正极配料加入NMP时阀门未关好造成加入过多,粘度过低?策略(1)出料重新配料,干粉物料减半,NMP少加80Kg搅拌后混一半异常料6、PVDF胶液有白色不溶物?策略(1)胶液加搅0.5-1h二、涂布异常之缩孔1、关于火山口电极极片特别是负极极片表面出现的圆形或近乎于圆形凹陷,称之为缩孔或火山口。
缩孔这一涂布缺陷常见于涂料应用的涂膜过程中,并非锂离子电池电极片涂布时特有的现象。
如下图2、缩孔的形成在涂布过程中可能会产生各种各样的缺陷,气泡、肥边、火山口、多边形凹陷、橘皮状等,缩孔是最常见的问题之一。
从根本上意义讲由于成膜时所产生的表面张力梯度造成的,这种现象称之为Maragoni效应。
材料间表面张力不匹配,是产生缩孔的主要诱因。
粘度、流动性以及干燥风速和烘箱温度等都可能改变表面张力及其作用过程,从而诱发缩孔的产生。
固化前可流动膜面中存在低表面张力的微粒(如粉体,油滴等),造成中央表面张力较低,流体以污染物为中心向四周迁移,最终形成边缘高于中心的圆形下陷(缩孔)。
3、缩孔的预防选用相容性好的分散剂或分散介质,减少涂料本体中低表面张力大颗粒(包括大液滴)的存在;添加疏水表面活性分散剂和溶剂等也可以控制缩孔的程度。
4、涂布缩孔解决方案1)材料表面结构的进一步改性通过对石墨材料表面进一步的改性,提高极性基团,提高其亲水性;2)调整粘合剂有效成分的分子结构通过调整粘合剂有效成分的分子结构,降低其极性基团的含量,有效降低LA型水性粘合剂产品的表面张力,提高其对石墨材料的润湿程度。
锂离子电池车间生产过程中常见涂布异常及处理方式
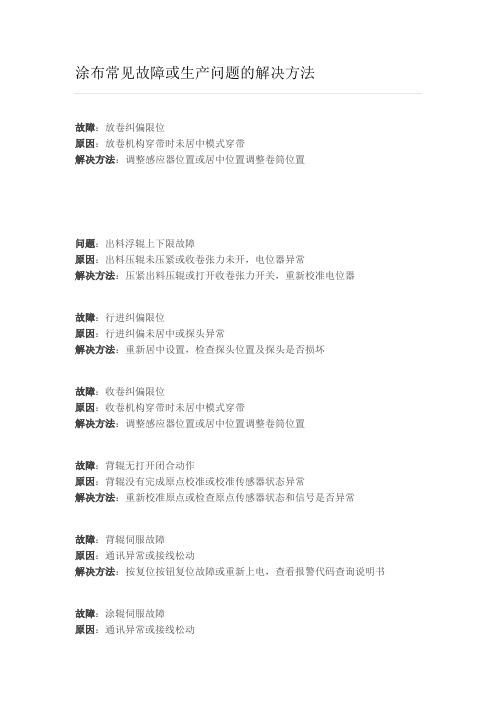
故障:放卷纠偏限位原因:放卷机构穿带时未居中模式穿带解决方法:调整感应器位置或居中位置调整卷筒位置问题:出料浮辊上下限故障原因:出料压辊未压紧或收卷张力未开,电位器异常解决方法:压紧出料压辊或打开收卷张力开关,重新校准电位器故障:行进纠偏限位原因:行进纠偏未居中或探头异常解决方法:重新居中设置,检查探头位置及探头是否损坏故障:收卷纠偏限位原因:收卷机构穿带时未居中模式穿带解决方法:调整感应器位置或居中位置调整卷筒位置故障:背辊无打开闭合动作原因:背辊没有完成原点校准或校准传感器状态异常解决方法:重新校准原点或检查原点传感器状态和信号是否异常故障:背辊伺服故障原因:通讯异常或接线松动解决方法:按复位按钮复位故障或重新上电,查看报警代码查询说明书故障:涂辊伺服故障原因:通讯异常或接线松动解决方法:按复位按钮复位故障或重新上电,查看报警代码查询说明书故障:第二面不间歇涂布原因:光纤故障解决方法:检查涂布参数或光纤信号是否异常故障:刮刀伺服故障原因:调刀伺服驱动器报警或传感器状态异常、设备急停解决方法:检查急停按钮或按复位按钮消除报警、重新校准刮刀辊原点并检查传感器状态是否异常故障:划痕原因:浆料颗粒引起或刮刀有缺口解决方法:塞尺清颗粒、检查刮刀故障:掉粉原因:a.过烘引起掉粉;b.车间湿度大、极片吸水;c.浆料粘接性差;d.浆料长时间未进行搅拌浆料解决方法:联系现场品质技术故障:面密度不够原因:a.液面高度落差大; b.走速 c.刀口解决办法:检查速度、刀口参数,保持一定的液位高度故障:颗粒较多原因:a.浆料本身所带或沉淀;b.单面涂布时辊轴造成;c.浆料长时间未搅拌(静止状态)解决办法:涂布前擦干净过辊、长时间浆料未用需要咨询品质技术是否搅拌故障:拖尾原因:浆料拖尾、背辊或涂辊间隙不平行、背辊弹开速度解决办法:调节间涂间隙参数、加大背辊弹开速度故障:正面错位原因:对齐有误差时未修正对齐参数解决方法:检查箔材有无打滑、清洗背辊,压住基准辊压辊、修正对齐参数故障:反面间涂呈平行状拖尾原因:涂背辊间距过小、过小或背辊弹开距离过小解决方法:调整涂背辊间距增加背辊弹开距离故障:头厚尾薄原因:头尾削薄参数未调好解决方法:调节头尾速度比及头尾起点距离故障:涂长、间歇过程变化原因:背辊表面有浆料、未压牵引胶辊,背辊与涂辊间隙太小过紧解决方法:清洁背辊表面、调整间涂参数,压上牵引、胶辊故障:极片上有明显裂痕原因:干燥速度过快、烘箱温度过高、烘烤时间过长解决方法:检查相关涂布参数是否符合工艺要求故障:运行时极片打皱原因:1、过辊之间平行度;2、背辊、过辊表面有严重浆料或水;3、箔带接头不良致两边张力不平衡;4、纠偏系统异常或未开启纠偏;5、张力过大或过小;6、背辊拉开行程间隙不一致;7、背辊的橡胶表面在使用时间较长后发生周期弹性形变解决方法:1、调整过辊平行度;2、及时处理背辊及过辊间异物;3、先调节机头的张力调节辊,待箔材平稳后再调整到原来状态;5、检查张力设定值、各传动辊、收放辊的转动是否灵活,及时处理不灵活辊;6、把间隙适当扩大,再慢慢缩小到合适位置;7、出现弹性形变严重时,更换新胶辊故障:边缘鼓边原因:档料板泡棉阻挡导致解决方法:安装挡料板时呈外八字即可或移动挡料板时由外向内移动即可故障:漏料原因:挡料板泡棉或刮料板安装不紧解决方法:刮料板间隙稍比图层厚度大10-20微米,压紧挡料板泡棉故障:收卷不齐原因:收卷轴未安装好、未充气、纠偏未开启或未开启收卷张力解决方法:安装固定好收卷轴、气胀轴充气、开启纠偏功能、收卷张力等故障:两边留白不均原因:挡料板安装位置、放卷纠偏未开启解决方法:移动挡料板、检查收卷纠偏故障:反面间涂无法追踪原因:光纤无感应输入或正面无间涂解决方法:检查光纤头的检测距离、光纤参数、正面涂布效果故障:纠偏不动作原因:光纤参数不对、纠偏开关未开解决方法:检查光纤参数是否合理(纠偏指示灯有无左右闪烁),纠偏开关是否开启故障:涂布时有大气泡方案:1、搅拌不均匀,试下浆料回锅重搅拌2、涂布管道或挤压头腔体内有气体残留。
锂电涂布丨涂布车间常见问题及解决方案
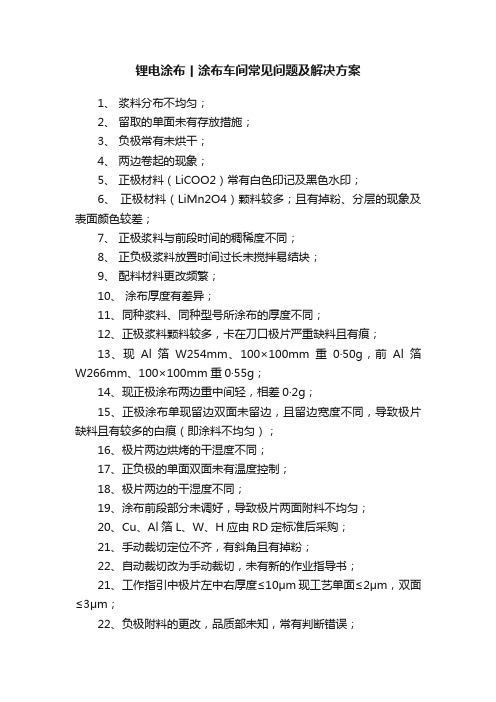
锂电涂布丨涂布车间常见问题及解决方案1、浆料分布不均匀;2、留取的单面未有存放措施;3、负极常有未烘干;4、两边卷起的现象;5、正极材料(LiCOO2)常有白色印记及黑色水印;6、正极材料(LiMn2O4)颗料较多;且有掉粉、分层的现象及表面颜色较差;7、正极浆料与前段时间的稠稀度不同;8、正负极浆料放置时间过长未搅拌易结块;9、配料材料更改频繁;10、涂布厚度有差异;11、同种浆料、同种型号所涂布的厚度不同;12、正极浆料颗料较多,卡在刀口极片严重缺料且有痕;13、现Al箔W254mm、100×100mm重0·50g,前Al箔W266mm、100×100mm重0·55g;14、现正极涂布两边重中间轻,相差0·2g;15、正极涂布单现留边双面未留边,且留边宽度不同,导致极片缺料且有较多的白痕(即涂料不均匀);16、极片两边烘烤的干湿度不同;17、正负极的单面双面未有温度控制;18、极片两边的干湿度不同;19、涂布前段部分未调好,导致极片两面附料不均匀;20、Cu、Al箔L、W、H应由RD定标准后采购;21、手动裁切定位不齐,有斜角且有掉粉;22、自动裁切改为手动裁切,未有新的作业指导书;21、工作指引中极片左中右厚度≤10μm现工艺单面≤2μm,双面≤3μm;22、负极附料的更改,品质部未知,常有判断错误;23、负极涂布双面温度无法升起(设125℃最多升至118℃);24、开窗后外面的温湿度对极片有影响吗;25、正、负单面涂布都是右边卷起,且正极收卷不齐易打皱;26、涂布机的温度与走速是成正比的,如何控制?未有标准;27、单面调机人员未带手套,留在Cu、Al上的手印(即汗渍),导致双面涂布后有明显的黑印迹;28、Al较窄不能留边,导致附在单面两干料,双面极易拉断且拉断次数较多,产生报废;29、涂布未有自检记录及习惯;30、刚停机,极片存放在烘箱中易掉粉;31、涂布完的极片未有明确规定如何存放;32、涂布后放Cu、Al箔位,未经其他部门认可已更换,且Cu、Al箔多次撞伤及两边松紧度不同;33、涂布机内辊轮未经常擦洗,易有干料附在极片上;34、加料未经常搅拌浆料稀稠不同,极片附料不均匀;35、同一大片分切后6小片,极片左中右厚度不稳定且重量在上中下限都有;36、加料最后的浆料(有干料、较稠、结块)对所涂极片都有影响;37、停机卡在刀口处的印记应切除,辊压后易断裂(正极);38、涂布工艺上所给的公差较大,能否缩小;39、涂布工艺两边附料不同,如063048 –ve单:1·7±0·05g双:3·41±0·05g ;083048 +ve单:3·74±0·08g双:7·48±0·15g ;40、未涂完的单面,用保鲜纸包后露置于空气中;41、Cu、Al箔未用后,露置于空气中且边缘未包;42、试机时所用碎布擦Cu、Al上浆料,对极片附为都有较多影响,且极片中有气泡(浆料);43、停机时,前段80mm处置于空气中,极片上浆料变色,有气泡;44、裁切大片定位不整齐,极片四角偏斜,不成直角,且切口处有毛剌及掉粉,手按片不稳定;45、RD规定涂布报废片回收,但放置空气中过久,+ve起泡-ve掉粉;46、未用电子称测量大片重量,也未规定多少时间分切小片测重;47、牵引极片受力不均,导致附料不均,试片调机应保留,经确认后方可执行;48、牵引Cu、Al箔的过程中,辅助转轴较多,箔两边受力不均;49、正极单面前加多一辊轮,负极未有;50、塞尺划痕,露基体极片较多;51、收卷越大,速度加速,应减慢,否则不能干;52、接带断带后,手拉附料不均匀(拉太快);53、负极拉完转拉正极时,极片存放烘箱过长;54、涂布机的保养未有当事人的审核;55、涂布机的排风扇未有见过清洗;56、裁切大片(手动)无设备操作、工位作业指导书,且工作台面太脏,极片易有±ve极粉到极片上;57、未调好机就涂布,造成两面附料不均匀。
锂电涂布工序简介

-2
C阀
B阀
大间隔位置阀门动作
10
涂布设备及工艺
2.5 间隔涂布异常及阀门调整
间隔带料
拉丝水印
原因分析: 1、GAP过大 2、模头有气体未排净 3、浆料粘度过高
解决措施: 1、减小GAP值 2、模头循环排气 3、降低下一批浆料粘度
漏箔
首不齐
原因分析: 1、起涂压力太小 2、首位置缩料
解决措施: 1、延迟回流阀打开时间 2、箔材烘干或电晕处理
一层烘箱
箔材面密度检测仪1
一面涂布头、供料系统
涂布面密度检测仪2
二面涂布 头、供料系
统
基材放卷
电晕处理
面密度 检测1
A面涂布
CCD检测
A面干燥
面密度 检测2
自动收卷
喷码标记
CCD检测
面密度 检测3
B面干燥
CCD检测
B面涂布
3
涂布过程简介
1.2 涂布控制参数
涂布的目的:将浆料涂覆在基材表面,得到面密度、尺寸、外观、极片性能合格的极片。
5
烘箱布置
前3坡度,后3 前3坡度,后5
水平
水平
全平
全平
全平
拱形,拱高 拱形,拱高 ≥200mm ≥600mm
6
托辊悬浮方式 前3主动辊托辊 前3主动辊托辊 前5托辊,后5 前3主动辊托辊 前4托辊,后6气
后2气浮
后5气浮
气浮烘箱
后5气浮
浮
全托辊
全托辊
7
热源
柴油加热导热油 天然气加热导热 天然气加热导
烘干过程及参数设定
3.6 NMP回收 转轮式NMP回收主要利用分子筛的物理吸附原理,具体工艺流程如右图所示:
- 1、下载文档前请自行甄别文档内容的完整性,平台不提供额外的编辑、内容补充、找答案等附加服务。
- 2、"仅部分预览"的文档,不可在线预览部分如存在完整性等问题,可反馈申请退款(可完整预览的文档不适用该条件!)。
- 3、如文档侵犯您的权益,请联系客服反馈,我们会尽快为您处理(人工客服工作时间:9:00-18:30)。
锂离子电池(含动力电池)搅拌和涂布工艺知识及异常处理新能源的锂离子电池发展很快,作为锂离子电池制造,每个工厂都在不断创新新的工艺,而这个工艺的发展速度很快,而真正核心的技术是新材料配方的应用和制作极片(涂布)过程中遇到问题的解决成为一个难点,而这个难点需要系统的知识才能解决,总结十几年的心得体会供大家学习。
主要内容有:
一、术语
二、正极材料
三、负极材料
四、陶瓷隔离膜材料
五、正极搅拌
六、负极搅拌
七、陶瓷隔离膜搅拌
八、正极涂布
九、负极涂布
十、陶瓷隔离膜tubu
十一、正极底涂印刷
一术语
1.1 粘度:粘度是指液体受外力作用移动时,分子间产生的内磨擦力的量度;单位是
mpa.s,我们测量粘度用旋转粘度计:包括一块平板和一块锥板样品粘度越大,扭矩越大。
扭矩检测器内设有一个可变电容器,其动片随着锥板转动,从而改变本身的电容数值。
这一电容变化反映出的扭簧扭矩即为被测样品的粘度,由仪表显示出来。
1.2 颗粒度:粒的大小。
通常球体颗粒的粒度用直径表示,立方体颗粒的粒度用边长表
示。
一般所说的粒度是指造粒后的二次粒子的粒度。
表示粒度特性的几个关键指标:D50/D90/D99
1.3 比表面积:单位重量的颗粒的表面积之和。
比表面积的单位为m2/kg或cm2/g。
比表
面积与粒度有一定的关系,粒度越细,比表面积越大,但这种关系并不一定是正比关系。
1.4 固含量:浆料中固体物质质量占总质量的百分比
1.5 透气度:严格来讲应该称为透气度或者透气量。
空气透过织物(PE及PTFE等等)
的性能。
以在规定的试样面积、压降和时间条件下,气流垂直通过试样的速率表示。
对于我们所做的陶瓷隔离膜,透气度越大,说明孔隙
率小。
1.6 公转:对我们搅拌来讲就是一个浆绕着另一个浆转动叫做公转
1.7 自转:是指物件自行旋转的运动,物件会沿著一条穿越身件本身的轴进行旋转,这
条轴被称为自转轴。
1.8 搅拌速度:每分钟搅拌的速度,单位是RPM
1.9 涂布重量:一般厂家是按照面密度来做,有的移50*100=500m2为单位,有的是以标
准的圆1540.25MM2的重量来做为标准单位设计和监控
1.10 压实密度:=面密度/(极片碾压后的厚度—集流体厚度) ,单位:g/cm3压实密度,
冷压后的不含基材的厚度
1.11 振实密度:在规定条件下容器中的粉末经振实后所测得的单位容积的质量,振实密度与
压实密度不成正比例关系
1.12 克容量:实际指的并不是“电池”的克容量,而是电池内部材料如:磷酸铁锂、钴酸锂、
锰酸锂、镍酸锂等等的克容量,每种材料的克容量是不相同的。
其单位为:mAh/g(毫安时每克)其定义可以理解为:每克锂电材料含多少mAh(毫安时)电量。
1.13 O verhang:阳极超出阴极的长度或宽度。