增产丙烯工艺技术进展
丙烯增产技术研究进展

蒸 汽裂解 增 产 丙 烯 主要 通 过 优 化 裂 解 原 料 , 优
提高 。另外 , 优化工艺参数 , 加强分离系统的工艺考 核, 减少 装置 损失 也可 达到 增产 丙烯 的 目的。
表 1 石科院裂解石脑 油模 拟实验产物分布
维普资讯
1 6
化 工科 技 市场
第3 0卷 第 7期
2 催化裂化增产技术
2 1 催化 剂添 加剂 .
使用 Z M一5含 量 高 的添加 剂 以 及经过 改进 的 F C S C
设备 , 操作条件温和, 蒸汽消耗量低 ,减压粗柴油为 、 原料 , 丙烯产率可达 1%( 8 质量分数 ) 。
旭化 成公 司 开发 的 O g 工 艺 ¨ 可从 石油 化 mea ,
维普资讯
第3 0卷 第 7期
20 0 7年 7月
化 工 科 技 市 场
CHEMI CAL TECHNOL OGY MARKET l 5
丙烯 增 产 技术 研 究 进展
苑 慧敏 赵春 晖 张永军 张 志 翔 张 宝军 王凤 荣 , , , , ,
.
p o p c e eo i g p o y e e n w o t u r wi g tc n lg , n rp s d s v rlp o ye e o t u —g o n e h o o r s e t d v lp n r p ln e up tg o n h oo y a d p o o e e e a r p ln u p t r w g t c n l- f o e i ge u h o b e eo e mp a ial n c i a is o g tt e d v lp d e h t l i h n . c y
C4烯烃催化裂解增产丙烯技术进展

摘!要!从热力学!反应机理等方面分析了 C4 烯烃催化裂解增产丙烯技术的特点" 介 绍 了 该 技 术 的 最 新 研 究 进 展#评述了 C4 烯烃催化裂解生产丙烯是高效利用烯烃资源的重要途径#认为应加快 开 发 具 有 我 国 自 主 知 识 产 权 的高效烯烃催化裂解增产丙烯的技术$ 关键词!C4 烯烃#丙烯#催化裂解#增产丙烯#反应机理#热力学 中图分类号!T@ Z Z 1. Z 1 +Z !!!文献标识码!A !!!文章编号!1000 6613 Z 005 1Z 1347 05
的分子筛具有较高的催化活性和选择性 并且其稳
定性也较高 7 在 # SAPO-34 ZS M-5 等 分 子 筛 上丁烯催化裂解的研究表明 大孔有利于双分子氢
转移反应 和 脱 氢 环 化- 芳 构 化 反 应 随 着 分 子 筛 孔 径减小 氢转移及芳构化反应明显受到抑制 丙烯
和乙烯的选择性明显升高 并且孔径越小 提高丙
1 低碳烯烃在 热 力 学 上 有 很 强 的 通 过 聚 合脱氢环化- 芳构化生成芳烃的倾向 例如 CZ !C5 烯 烃同芳烃 苯 二甲苯及三甲苯 构成的热力学系统
计算结果显示 在 Z 00 !6Z 0 范 围 内 芳 烃 的 质 量分数保持在 90 % 以上 乙烯 பைடு நூலகம் 丙 烯的 质 量 分数 均不足1 %
在异构化的同时主 要 通 过 二 聚 形 成 C8 中 间 体 然 后 C8 中间体再顺次裂解形成复杂的产物分布 3
对低碳烯 烃 裂 解 机 理 的 另 一 种 表 述 所 有 C4 以上的烯烃 丁烯 戊烯 己烯等 在催化剂上被
增产丙烯的技术进展

置 现 已扩 能到 9 2万 ta / 。表 l列 出 了 D C工 业装 C
子 筛 为 载 体 的镧 催 化 剂 。 实 验 室 验 证 试 验 表 明 ,
该 工 艺可 使 乙烯 和丙 烯 产 率达 到 6 % ,而 常规 的 1
技术 ,主要 有 :中国石化 石油 化工 研究 院 ( I P RP )
的深 度催 化 裂化 工 艺 ( C ,凯 洛 格 一 朗 路 特 D C) 布
(B K R) 公 司 的 Ma o n工 艺 、 S p re xf i u ef x工 艺 , l U P公 司 的 P t F C工 艺 ,鲁 姆 斯 公 司 的 S C O eoC r C
摘
要 :阐述各 国增产丙烯的技 术。提 出 D C、烯烃易位转化 、C C JC 烃选择裂解和 M O、MT T P工艺可 以推广应
用 .而丙 烷 脱 氢 工 艺 在 我 国 受 资 源 短 缺制 约 ,其 工 业 应 用 条 件不 具 备 。
关键词 :丙烯 ;制备 ;技术经济对 比;评论
条件 下操 作 ,而 F C装置 在 4 3 5 9℃ 、1 3 C 9~4 %- %
蒸汽 条 件 下操 作 。D C操 作 采 用 分 子筛 催 化 剂选 C
择性 地生 产丙烯 、乙烯 和 富芳烃 石 脑油 。 D C可 以 加 工 各 种 重 油 。 已 经 用 于 国 内外 C DC C工 业 装 置 的 原 料 包 括 :蜡 油 、加 氢 处 理 蜡
蒸 汽 裂解 为 5 %。30 0td装置 的可 行性 研究 指 0 0 /
出 ,操 作 可 在 约 6 0℃ 和 01 0 a压 力 下 进 5 . ̄ . MP 2
实现丙烯增产的利器:MAXOFIN?催化裂化技术

实现丙烯增产的利器:MAXOFIN™催化裂化技术满足市场对丙烯不断增长的需求目前,生产轻质烯烃的炼油厂和石化厂已经越来越难跟上市场对丙烯日益增长的需求了。
蒸汽裂解装置曾经能够通过副产丙烯的方法来满足这一需求,而现在,其供应已远远跟不上需求。
随着越来越多的蒸汽裂解装置采用乙烷为原料,副产的丙烯产量降低,市场对能大量生产丙烯同时副产乙烯较少的工艺的需求也在不断增加。
KBR的MAXOFIN催化裂化工艺恰好可以满足这种需求。
它将其成熟的的Orthoflow™同轴式催化裂化反应器与专有添加剂相结合,能用传统的FCC进料实现丙烯产量的最大化,同时减少乙烯副产品的产出。
更大的生产灵活性当今的炼油厂需要一种技术来帮助其满足市场需求。
KBR的MAXOFIN技术不但能从FCC原料中获得20%或更多的丙烯,同时还具备更大的生产灵活性。
当生产丙烯与生产油品收益差别较小时,MAXOFIN 也可以当作常规的FCC来操作,其生产的大部分产品为汽油。
而当市场对丙烯的需求相对较高时,该工艺可以相应减少汽油的产量,并使丙烯产量实现最大化。
当市场需要柴油和丙烯时,我们的MAXOFIN工艺可以在低转化率下运行主提升管反应器以维持油品收率。
主提升管中生成的轻石脑油及C4可以循环到第二提升管反应器中,在更加苛刻的条件下最大程度地转化为丙烯。
除了加工FCC自产的轻石脑油外,第二提升管也可以同时处理来自炼厂其它装置的石脑油及C4,如焦化石脑油及C4。
饱和石脑油,如直馏轻石脑油,也可以在MAXOFIN装置中进行转化,在提高丙烯收率的同时,直馏石脑油的辛烷值也有所提高。
需要考虑的经济因素在多产丙烯的操作模式下,石脑油的产量降低,但与常规的FCC装置相比,MAXOFIN催化裂化石脑油产品中的辛烷值及芳烃含量都大为增加。
除芳烃外,炼油厂也可以回收MAXOFIN工艺生成的乙烯作为高价值的石化产品原料,提高经济效益。
该工艺使炼厂可以对辛烷值较低的轻石脑油进行增值利用。
增产丙烯的催化裂化工艺进展

多产丙烯或扩大丙烯资源的技术 , 包括对传 统蒸 汽裂 解和催 化裂 化 技 术 的改 进 , 催 化 裂解 多产 如
丙烯 技术 、 催化 裂化 多产丙 烯技术 ; 与 乙烯 装置 可 或催 化裂 化 装 置 相 配 套 的技 术 , 烯 烃 易位 ( 如 即 乙烯 和丁 烯 歧化 技 术 ) C/ 馏 分转 化 技 术 ; 、 C 扩 大 丙烯资 源 的丙 烷 脱 氢 技 术 和 甲醇 制 烯 烃 技 术 等 。这些 技术 中 , 过催 化 裂 化 工艺 多 产 丙烯 技 通 术 更符合 国情 , 为此 , 笔者将 国内外催 化裂 化多 产 丙烯 工艺 进展综 述 如下 。
( % )羰 基醇 (% ) 。近年来 受丙 烯 衍 生物 需 4 、 9 等
求快速拉动的影响 , 全球丙烯需求年增长率大大 超过了乙烯 , 1 年丙烯需求增长率约为 5 , 2 1 0 % 将 达到 7 . M/ , 35 t 比乙烯高 出 0 5 a . 个百分点 , 同时 在 2 1-2 1 期 间 年平 均 增 长 速 度将 保 持 高 00 05年
化
工
EP T O E R CH 。 E
M Is C 三 A L
卷s 第期
2 11 D . . CC 工 艺
传 统 F C工艺 高 。 C
2 1 2 C P工 艺 . . P
1 催化 裂化 多产丙 烯技 术思路
2 1 国 内催化 裂化增 产丙 烯工艺 进展 . 国内相关 的增 产 丙 烯催 化 裂 催 化 裂 解 技 术有 : 以重 质油 为原 料多产 丙烯 的催化 裂解技 术 , 即深 度催 化裂化 技 术 ( C ; 产丙 烯 和 乙烯 的 D C) 多 催化 热裂 解技术 ( P ) 重 质 油接 触 裂解 ( C ) CP ; H C
增产丙烯的催化裂化工艺进展
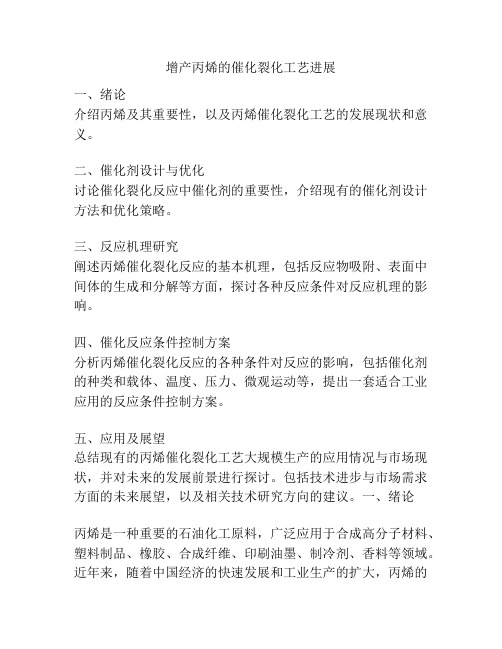
增产丙烯的催化裂化工艺进展一、绪论介绍丙烯及其重要性,以及丙烯催化裂化工艺的发展现状和意义。
二、催化剂设计与优化讨论催化裂化反应中催化剂的重要性,介绍现有的催化剂设计方法和优化策略。
三、反应机理研究阐述丙烯催化裂化反应的基本机理,包括反应物吸附、表面中间体的生成和分解等方面,探讨各种反应条件对反应机理的影响。
四、催化反应条件控制方案分析丙烯催化裂化反应的各种条件对反应的影响,包括催化剂的种类和载体、温度、压力、微观运动等,提出一套适合工业应用的反应条件控制方案。
五、应用及展望总结现有的丙烯催化裂化工艺大规模生产的应用情况与市场现状,并对未来的发展前景进行探讨。
包括技术进步与市场需求方面的未来展望,以及相关技术研究方向的建议。
一、绪论丙烯是一种重要的石油化工原料,广泛应用于合成高分子材料、塑料制品、橡胶、合成纤维、印刷油墨、制冷剂、香料等领域。
近年来,随着中国经济的快速发展和工业生产的扩大,丙烯的需求量越来越大,而传统的生产工艺存在低效、高能耗、低环保、低成本等问题。
因此,研究丙烯的高效生产工艺和技术具有重要的现实意义和应用价值。
催化裂化是一种重要的丙烯生产工艺,它通过在合适的催化剂存在下,将石油轻质油组分在高温下分解成丙烯等低碳烯烃和其他有机物,从而实现丙烯的高效生产。
催化裂化技术具有反应速率快、生产周期短、能源消耗低、环保性好等优点,是目前丙烯生产中最受关注和应用最广泛的工艺之一。
然而,由于催化剂的特殊性质和反应机理的复杂性,丙烯催化裂化工艺中存在着一系列技术瓶颈和难题,包括催化剂的设计、反应机理的解析、反应条件的控制等方面。
因此,探索和研究丙烯催化裂化工艺的基础理论、优化催化剂的组成和反应条件,对于提高工艺效率、提高丙烯产率和降低生产成本具有重要的现实意义和发展空间。
本文将在系统总结已有研究成果的基础上,探讨丙烯催化裂化工艺的主要技术问题和进展,包括催化剂设计与优化、反应机理研究、催化反应条件控制方案等方面。
增产丙烯的烯烃转化技术进展

近 年来 ,由于 丙烯 下 游 产 品链 的快 速发 展 和 丙 烯供 应量 的不 足 ,国外公 司 热衷 于 开 发新 的 增
反 应 生 成 丙 烯 , 反应 为平 衡 反应 。 该 因此 , C O T技 术 既可 以利 用 该 反应 由乙烯 和 丁 烯生 产丙 烯 , 又
可 以由丙烯 生 产 乙烯 和丁烯 。 反应 式 为 :
C2I C4 I4+ H8:= 2 C3 - ; 兰 H6+C5
南 非 Ssl 司开 发 了 一 种 由丁 烯 制 丙 烯 的 ao 公 技术 。 料 为 1 丁烯 、一 原 一 2 丁烯 或 其 混 合 物 , 化 剂 催
A BL m s 司 的 O T技 术将 乙烯转 化 为 B u mu 公 C 丙 烯[1 择性 近 10% , 丁烯 转化 为丙烯 的选 2的选 , 3 0 将 择性为 9 , 7% 丁烯 总 转化 率 为 8 5%~ 2%( 烯 进 9 丁 料 中正 丁烯质 量分 数 为 5 0%一 5%) 9 。进 料 中的 乙 烯 和 丁烯 可 来 自蒸 汽 裂解 装 置 和各 种 炼油 厂 的 生 产过 程 , 度也 可 不相 同 , 浓 丁烯也 可 来 自乙烯 二 聚
利 用催 化裂 化 产 物 中 乙烯 和丁烯 生 产 丙烯 ,为 我 国增 产丙烯 开 辟 了一 条新 的途 径 。 1 烯烃转 化技 术 烯 烃转 化技 术 属 于烃 类 转化 技 术 。 目前 , 世 全
界已经有 9 套烯烃歧化装置投产 ,这些烯烃歧化 装置或与蒸汽裂解装置联合 ,或与炼油厂回收丙 烯装置联合 。与蒸汽裂解装置结合可将丙烯/ 乙烯
多产丙烯的催化裂化工艺进展

增 产轻 质 烯 烃 , 尤其 是 丙 烯 。采 用 2台反应 器 和 1台共 用 的再生器 , 主裂解 原 料 在 高温 、 剂油 比 高 条件 下最 大 限度 地 生产 轻 质 烯 烃 , 压 反应 区用 低 以提高烯 烃度 。 通 常的 F C工 艺 提 高 轻 质 烯 烃 产 率 是 通 过 C 提高 反 应 温 度 和 催 化 剂 循 环 量 来 实 现 的 , 而 Pt F C工艺 通 过补加 特定 的择 形添加 剂使 一些 eo C r
丙烯 , 前以中国石油化工股份有限公司的深度 目
催 化裂 化 、 化 热裂解 工 艺和美 国 U P公 司的重 催 O 油催化 裂化 ( eo C 工艺 为代 表 。与 以减压 馏 Pt F C) r 分油 ( G 类 原料 的蒸 汽 裂解 装 置 相 比 , V O) 这些 为 炼 化 一体 化设 计 的技 术 可 以处 理重 质 原 料 , 于 由
炼 厂 回收丙烯 和 乙烯 的方法 难 以满足 市场 对丙烯
由美 国 U P公 司 开 发 的重 油 流 化 催 化 裂 化 O 工 艺 ( er lii d a l i rcig 简 称 P t Fudz C t y c akn , o e a t C P t F C) 艺可 以瓦 斯 油 和 减压 渣 油等 为 原 料 eo C 工 r
关键词 : 催化裂化 丙烯 技术 进展
中图 分 类 号 :Q 2 . 1 T 2 12 2 文 献 标识 码 : A 文章 编 号 : 17 6 4—19 (0 2 0 0 5 0 9 2 1 )2— 0 7—0 6
丙 烯是 产量 仅次 于 乙烯 的重要 基础 有机 化工 原料 , 主要 用于 生 产 聚 丙 烯 ( 占 5 % ) 丙 烯 腈 约 2 、 (2 ) 环 氧 丙 烷 ( % ) 异 丙 苯 ( % ) 异 丙 醇 1% 、 7 、 7 、 (%) 4 和羰 基 醇 (% ) 。近 年 来 受 丙 烯 衍 生 物 9 等
增产丙烯的技术进展(续)

维普资讯
・
工
20 0 6正
时 丁烯 一 l又 异 构 化 为 丁烯 一 2 。丁 烯 单 程 转 化 率 为 6 ~ 7 , O 5 丁烯转 化 为 丙烯 的选 择 性 大 于
乙烯 装置 也将 组 合 采 用 易 位 反 应 烯 烃 转 化 装 置 ,
( 接 20 上 0 5年第 4期 )
2 4 易位转化技术 .
烯 烃 易位 转化 通过 过 渡金 属化 合 物催化 剂使
乙烯 和丁 烯生 产 丙烯 , 应改 变碳 一碳 双键 , 室 反 在
可逆 反应 , 位 反应 可 将 乙烯 与 丁 烯 一 2反 应 生 易 成二 个分 子 的丙烯 。 易位 转化 与 石 脑 油 裂 解 相 组 合 , 可使 丙 烯 :
说 明 : 据 来源于鲁姆斯公 司。 数
.
鲁 姆 斯公 司 的 Tr lf i ei o n易位 转 化 工 艺 ( 称 又
烯烃相互转化 O T工艺) 30 -0 ℃和 3 O C 在 3  ̄4 0 , .~
35 a 操 作 , 用 钨 基 催 化 剂 的 固定 床 反 应 . MP 下 采
器 。催 化 剂 促使 乙烯 和 丁烯 一2转化 为丙烯 , 同
收稿 日期 :0 5 9 4 修 改 稿 返 回 日期 :0 5 1 — l 。 2 0 -0 -0 ; 2 0 — O 2 作者 简介 : 文 , ,9 9年 生 , 授 级 高 工 1 6 章 男 13 教 9 3年 毕 业 于 华 东 理 工 大 学 , 就 职 干 上 海 擎 督 信 息 科 技 公 司 , 事 石 油 化 工 现 从 和 化 工 信 息 调研 工 作 。
k/ t a丙 烯 装 置 , 定 进 料 中 含 8 正 丁 烯 , 假 6
我国丙烯生产技术最新进展

乙烯, 00 20 20- 0 5年 丙 烯 年 均 增 长 率 为
43 , .% 比乙烯 高 0 9个 百 分 点 。2 0 . 0 6年 世 界丙烯 生产 能力 达 到 74 62万 ta产 量 约 为 /, 64 86万 ta但 需 求 量 达 到 62 /, 90万 ta 预 /。 计到 21 00年世 界丙 烯 生 产 能力 将 达 到 9 6 40 万 ta 如 按 开 工 率 8 %计 , 量 约 为 8 2 /, 8 产 35 万 ta 需 求 预 计 将 达 82 /, 4 0万 ta 预 计 /, 20 -2 1 0 5 00年 , 世界 丙 烯 年均 需 求增 长 率 将
Mo , O, a Mg L z 3 C 0 , 2 5 3 0 Ni C O, O, a0 , e P 0 , 3
需求 的发展速 度也逐渐 超过 了 乙烯。2 0 03
年我 国丙烯 下游衍 生 物共 消费 丙烯 6 59万 1. t其 中 聚 丙烯 的 产 量 为 4 7万 t消耗 丙 烯 , 2 , 48万 t约 占全 国丙烯 表观 消 费量 的 7 .% 4 , 27
维普资讯
第3 7卷 9期 (07 20 )
国 内外 石 油化 工快 报
・ 1
・
综 述 ・
我 国丙 烯 生产 技术 最 新 进 展
孙 可 华
FCC工艺中提升增产丙烯助剂性能研究进展

化工进展Chemical Industry and Engineering Progress2022年第41卷第1期FCC 工艺中提升增产丙烯助剂性能研究进展吕鹏刚1,刘涛1,叶行2,黄校亮1,段宏昌1,谭争国1(1中国石油石油化工研究院兰州化工研究中心,甘肃兰州730060;2中国石油青海油田格尔木炼油厂,青海格尔木816099)摘要:流化催化裂化(FCC )是炼厂最重要的二次加工工艺,也是石油化工应用中丙烯的第二大来源。
随着丙烯需求消费的不断增长,在FCC 催化剂中添加增产丙烯助剂是一种灵活、高效提高丙烯收率的途径,其助剂主要由活性组分ZSM-5分子筛和基质组成。
本文主要从活性组分ZSM-5分子筛和基质两方面分别介绍目前阶段增产丙烯助剂的研究现状,通过对ZSM-5分子筛的改性来提升活性组分的性能,重点综述了调变分子筛的酸度、改善孔结构及粒度和提高水热稳定性;分析了基质孔结构和酸性的梯度分布对助剂在FCC 工艺中提高原料的转化、减少生焦和增产丙烯的重要作用。
最后指出在合成分子筛过程中引入改性元素,减少元素流失,提高改性元素的利用率,同时在助剂基质方面的研究仍有不足,开发低成本、大孔径和适宜酸度的高性能基质也是增产丙烯助剂未来的研究方向。
关键词:流化催化裂化(FCC );助剂;ZSM-5分子筛;基质;增产丙烯中图分类号:TE624.9文献标志码:A文章编号:1000-6613(2022)01-0210-11Advances in improving the performance of additives for increasingpropylene production in FCC processLYU Penggang 1,LIU Tao 1,YE Hang 2,HUANG Xiaoliang 1,DUAN Hongchang 1,TAN Zhengguo 1(1Lanzhou Petrochemical Research Center,Petrochemical Research Institute,PetroChina,Lanzhou 730060,Gansu,China;2Golmud Oil Refinery,Qinghai Oilfield,PetroChina,Golmud 816099,Qinghai,China)Abstract:Fluid catalytic cracking (FCC)is the most important secondary processing process inrefineries,and also the second largest source of propylene in petrochemical applications.Adding propylene production-increasing additives,mainly composed of active component ZSM-5zeolite and matrix,to FCC catalyst is a flexible and efficient method to increase propylene yield.In this paper,the research status of additives for increasing propylene production is introduced from two aspects of active component ZSM-5zeolite and matrix.The modification of ZSM-5zeolite is used to improve the performance of active component,which is by adjusting the acidity,improving pore structure and particle size,and improving hydrothermal stability of zeolite.The important effects of structure and acid gradient distribution of matrix in improving feedstock conversion,reducing coke formation and increasing propylene production in FCC process is analyzed.Finally,it is pointed out that introducing modification elements in the synthesis of zeolite can reduce the loss of elements,improve the utilization rate of modified elements.At the same time,there are still some deficiencies in the research of additive matrix.综述与专论DOI :10.16085/j.issn.1000-6613.2021-0175收稿日期:2021-01-25;修改稿日期:2021-04-11。
烯烃催化裂解增产丙烯技术进展

+ 6
典型原料 燃料气 7. 2 12. 0 13. 6 11. 6 乙烯 22. 5 22. 1 20 . 0 19. 8 丙烯 48. 2 43. 8 40 . 1 38. 7
M
� � 注 C 为 C 6 以上的烃组分
公司的 M O I 工
王红秋等 . 烯烃催化裂解增产丙烯技术进展 � � 57
图1
工艺流程示意
产品需求 量小的地 区 可 提高丙烯 和乙烯的产 量 �
同 时在几 乎不损 失辛
2006 年 12 月
技 术公司 的 25 0 产装 置 了 此外 KB 技术许 可 和 剂 在 5 00 6 00 公司的
工艺 � 首次 应用 于南 非 烷 值的前提 下降低汽 油混合物 料中的烯 烃含量
摘
要�
随着石化工业的快速发展 乙烯蒸汽裂解装 置和炼油厂催化裂化装置的 C 4 及 C 4 以上烯烃副产 物大
量增加 采用催化裂解工艺将其转化为丙烯和乙烯 且 丙烯乙烯质量比较高 不仅提高了副产物的附加值 而且 拓展 � � � 了低碳烯烃的原料来源 � 本文综述了烯烃催化裂解技术的特点 研究进展和工业应用情况 关键词 � 烯烃 催化裂解 丙烯 乙烯
表 � 烯烃催化 裂解技术 将较高 相对分 子质量 的富
典型原料的乙烯和丙烯等收率
% 丙烷 5. 3 6. 5 6. 6 7. 0 C+ 6 汽油 16. 8 15. 6 19. 7 22. 9
含烯 烃物料 ( 通常是 C 4 C8) 转化成丙 烯和乙烯 原 � 收率 料 通常 包括 石脑 油 裂解 装置 的 C4/ C5 馏分 和炼 油 厂 的 催化 裂 化 (FCC ) 轻 汽 油 焦 化轻 汽 油 等 前 已经开发的技术 有 美 国 K B R 公司的 S 工艺 法国 A 德国 L 的O 艺 工艺 和美国 U O P 公司 的 O CP 工艺 工 艺 日本 A 公司 美国 E 公 司的 P 目
增产丙烯工艺技术进展
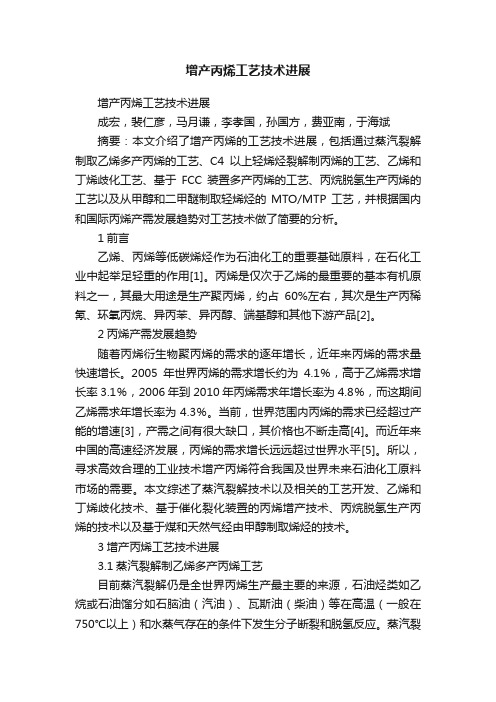
增产丙烯工艺技术进展增产丙烯工艺技术进展成宏,裴仁彦,马月谦,李孝国,孙国方,费亚南,于海斌摘要:本文介绍了增产丙烯的工艺技术进展,包括通过蒸汽裂解制取乙烯多产丙烯的工艺、C4以上轻烯烃裂解制丙烯的工艺、乙烯和丁烯歧化工艺、基于FCC装置多产丙烯的工艺、丙烷脱氢生产丙烯的工艺以及从甲醇和二甲醚制取轻烯烃的MTO/MTP工艺,并根据国内和国际丙烯产需发展趋势对工艺技术做了简要的分析。
1前言乙烯、丙烯等低碳烯烃作为石油化工的重要基础原料,在石化工业中起举足轻重的作用[1]。
丙烯是仅次于乙烯的最重要的基本有机原料之一,其最大用途是生产聚丙烯,约占60%左右,其次是生产丙稀氰、环氧丙烷、异丙苯、异丙醇、端基醇和其他下游产品[2]。
2丙烯产需发展趋势随着丙烯衍生物聚丙烯的需求的逐年增长,近年来丙烯的需求量快速增长。
2005年世界丙烯的需求增长约为4.1%,高于乙烯需求增长率3.1%,2006年到2010年丙烯需求年增长率为4.8%,而这期间乙烯需求年增长率为4.3%。
当前,世界范围内丙烯的需求已经超过产能的增速[3],产需之间有很大缺口,其价格也不断走高[4]。
而近年来中国的高速经济发展,丙烯的需求增长远远超过世界水平[5]。
所以,寻求高效合理的工业技术增产丙烯符合我国及世界未来石油化工原料市场的需要。
本文综述了蒸汽裂解技术以及相关的工艺开发、乙烯和丁烯歧化技术、基于催化裂化装置的丙烯增产技术、丙烷脱氢生产丙烯的技术以及基于煤和天然气经由甲醇制取烯烃的技术。
3增产丙烯工艺技术进展3.1蒸汽裂解制乙烯多产丙烯工艺目前蒸汽裂解仍是全世界丙烯生产最主要的来源,石油烃类如乙烷或石油馏分如石脑油(汽油)、瓦斯油(柴油)等在高温(一般在750℃以上)和水蒸气存在的条件下发生分子断裂和脱氢反应。
蒸汽裂解是吸热反应,通常在管式加热炉内进行:原料和水蒸气经预热后入加热炉炉管,被加热至750~900℃,发生裂解。
蒸汽裂解是生产乙烯的主要方法,同时多产丙烯等低分子烯烃,是强大的石油化学工业的基础[6]。
丙烯生产技术的研究进展

当代化工研究Modern Chemical Research155 2020•23科研开发丙烯生产技术的研究进展*张峰'韩伟'李永兵2温嵩'苟氽莲'车春霞'(1.兰州化工研究中心甘肃7300602.兰州石化公司石油化工厂甘肃730060)摘要:在文中对丙烯生产技术进行深入的分析,并且进一步阐述其发展情况,并且对各种不同的制取丙烯技术进行深入的说明.现阶段,丙烯生产时趋势是使裂解选择性得到有效的提升,并且使裂解深度也可以得到有效提升,使重质原料得到更好的处理,同时,还要探寻更多的丙烯原料.关键词:丙烯;蒸汽裂解;催化裂化;选择性;裂解深度中阖分类号:T文献标识码:AResearch Progress of Propylene Production TechnologyZhang Feng1,Han Wei1,Li Yongbing2,Wen He1,Gou Galian1,Che Chunxia1(nzhou Chemical Research Center,Gansu,7300602.Petrochemical Plant of Lanzhou Petrochemical Company,Gansu,730060)Abstract:This paper deeply analyzes the production technology of p ropylene,and f urther expounds its development,and deeply explains various technologies for preparing propylene.At present,the trend of p ropylene production has effectively improved the cracking selectivity and cracking depth,so that heavy raw materials can be better treated,and at the same time,more p ropylene raw materials should be explored.Key words:propylene;steam crackings catalytic crackings selectivity;cracking depth1.引言在工业化学中,丙烯有着重要的地位,可以推动国民生产的不断发展。
催化裂化生产丙烯工艺技术的新进展
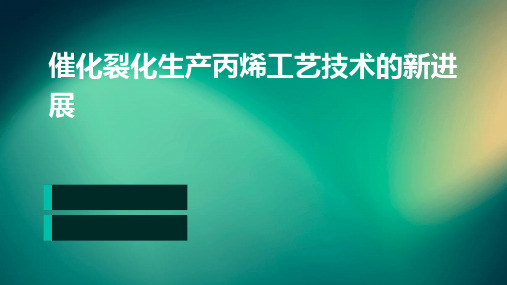
绿色生产与环境保护的考量
01
02
03
04
低碳排放
研发低碳排放的催化裂化技术 ,降低COx、SOx等温室气体
和有害气体的排放。
能耗降低
优化反应过程和能量回收利用 ,降低装置能耗,实现绿色节
能生产。
资源循环利用
开展催化剂再生和废弃物资源 化利用研究,减少固体废弃物
排放。
环境友好型催化剂
开发无毒、低污染的环境友好 型催化剂,降低对环境的负面
随着环保要求的提高和新能源的兴起,丙烯在生物降解塑料、燃料添加剂等方面的 应用也日益广泛。
02 催化裂化技术概述
催化裂化技术的原理
催化裂化是一种将重质烃类在催 化剂的作用下进行裂解,转化为 轻质烃类和烯烃的化学反应过程。
催化剂的存在可以降低裂化反应 的活化能,提高反应速率和选择
性。
裂化反应主要分为热裂化和催化 裂化两种类型,其中催化裂化具
04
提高丙烯收率的方法与技术的应用已取得一定成果,并在工业试验中 得到验证,为催化裂化生产丙烯的进一步发展提供了有力支持。
04 工业应用与实例分析
国内外工业应用的现状与趋势
国内现状
随着丙烯需求的不断增长,国内 催化裂化生产丙烯工艺技术得到 了广泛应用,技术水平不断提高 ,装置规模逐渐扩大。
国外趋势
研发更高效、选择性更 高的催化剂,提高丙烯 产率,降低副产物生成。
进一步探索适宜的反应 温度、压力和原料配比, 提高反应效率和稳定性。
开发新型的流化床和固 定床反应器,提高传热 和传质效率,降低能耗。
集成化与智能化
实现催化裂化装置的集 成化、智能化控制,提 高生产过程的自动化水
平。
提高丙烯产量的研究重点与难点
催化裂化生产丙烯工艺技术的新进展

5.1 38.8 32.3
>99 >85
16.5
-
中国石TP化I公集司团典炼型油调继合续汽教油育中心
组成,% DCC 汽油 重整油 异构化油
MTBE 直馏汽油 性质 密度,g/ml RON MON 芳烃含量,%
97#无铅汽油
1
2
85
65
-
15
5
6
6
8
4
6
0.7542
98.2 84.2 34.6
其中异丁烯
大庆 安庆 济南 济南
DCC-I DCC-I DCC-I DCC-II VGO+ VGO+ VGO+ VGO+ ATB CGO DAO DAO
545 550 564 530 3.7 3.5 5.3 1.8 23.0 18.6 19.2 14.4 17.3 13.8 13.2 11.4 6.9 5.7 5.2 4.8
重油裂化能力强 • 形成系列化、多品种,用于不同的原料和
目的产品
中国R石AG化催集化团剂炼功油能继结续构教示育意中心
积炭表面
汽油
积炭表面
原料 大分子
重油
中等分子
大孔活性基质表面
中孔 /通道 适宜的酸性表面
柴油
液化气+汽油 积炭表面
中等尺寸 饱和烃
复合分子筛 小孔 裂化表面
液化气+ 汽油
液化气
图2. 特殊结构和反应性能的催化剂
中国石化集团操炼作油参继数续教育中心
反应温度 剂油比 停留时间 反应压力 稀释蒸汽
FCC
基准 基准 基准 基准 基准
DCC
+0~50oC 1.5~2 倍
催化裂化增产丙烯的技术进展
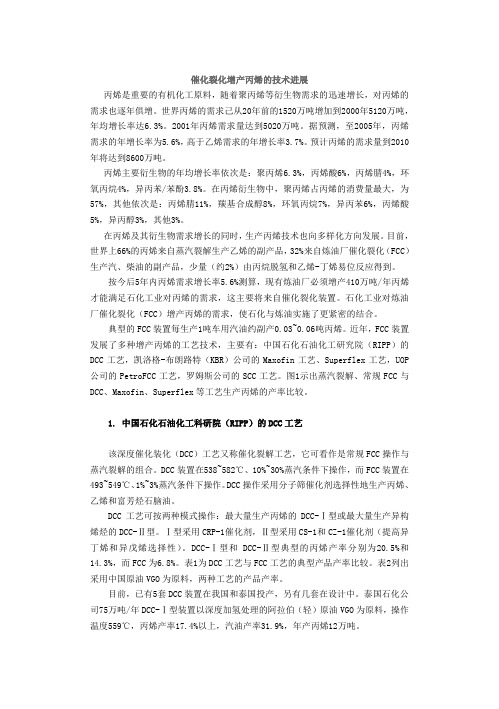
催化裂化增产丙烯的技术进展丙烯是重要的有机化工原料,随着聚丙烯等衍生物需求的迅速增长,对丙烯的需求也逐年俱增。
世界丙烯的需求己从20年前的1520万吨增加到2000年5120万吨,年均增长率达6.3%。
2001年丙烯需求量达到5020万吨。
据预测,至2005年,丙烯需求的年增长率为5.6%,高于乙烯需求的年增长率3.7%。
预计丙烯的需求量到2010年将达到8600万吨。
丙烯主要衍生物的年均增长率依次是:聚丙烯6.3%,丙烯酸6%,丙烯腈4%,环氧丙烷4%,异丙苯/苯酚3.8%。
在丙烯衍生物中,聚丙烯占丙烯的消费量最大,为57%,其他依次是:丙烯腈11%,羰基合成醇8%,环氧丙烷7%,异丙苯6%,丙烯酸5%,异丙醇3%,其他3%。
在丙烯及其衍生物需求增长的同时,生产丙烯技术也向多样化方向发展。
目前,世界上66%的丙烯来自蒸汽裂解生产乙烯的副产品,32%来自炼油厂催化裂化(FCC)生产汽、柴油的副产品,少量(约2%)由丙烷脱氢和乙烯-丁烯易位反应得到。
按今后5年内丙烯需求增长率5.6%测算,现有炼油厂必须增产410万吨/年丙烯才能满足石化工业对丙烯的需求,这主要将来自催化裂化装置。
石化工业对炼油厂催化裂化(FCC)增产丙烯的需求,使石化与炼油实施了更紧密的结合。
典型的FCC装置每生产1吨车用汽油约副产0.03~0.06吨丙烯。
近年,FCC装置发展了多种增产丙烯的工艺技术,主要有:中国石化石油化工研究院(RIPP)的DCC工艺,凯洛格-布朗路特(KBR)公司的Maxofin工艺、Superflex工艺,UOP 公司的PetroFCC工艺,罗姆斯公司的SCC工艺。
图1示出蒸汽裂解、常规FCC与DCC、Maxofin、Superflex等工艺生产丙烯的产率比较。
1. 中国石化石油化工科研院(RIPP)的DCC工艺该深度催化装化(DCC)工艺又称催化裂解工艺,它可看作是常规FCC操作与蒸汽裂解的组合。
DCC装置在538~582℃、10%~30%蒸汽条件下操作,而FCC装置在493~549℃、1%~3%蒸汽条件下操作。
- 1、下载文档前请自行甄别文档内容的完整性,平台不提供额外的编辑、内容补充、找答案等附加服务。
- 2、"仅部分预览"的文档,不可在线预览部分如存在完整性等问题,可反馈申请退款(可完整预览的文档不适用该条件!)。
- 3、如文档侵犯您的权益,请联系客服反馈,我们会尽快为您处理(人工客服工作时间:9:00-18:30)。
增产丙烯工艺技术进展成宏,裴仁彦,马月谦,李孝国,孙国方,费亚南,于海斌摘要:本文介绍了增产丙烯的工艺技术进展,包括通过蒸汽裂解制取乙烯多产丙烯的工艺、C4以上轻烯烃裂解制丙烯的工艺、乙烯和丁烯歧化工艺、基于FCC装置多产丙烯的工艺、丙烷脱氢生产丙烯的工艺以及从甲醇和二甲醚制取轻烯烃的MTO/MTP工艺,并根据国内和国际丙烯产需发展趋势对工艺技术做了简要的分析。
1前言乙烯、丙烯等低碳烯烃作为石油化工的重要基础原料,在石化工业中起举足轻重的作用[1]。
丙烯是仅次于乙烯的最重要的基本有机原料之一,其最大用途是生产聚丙烯,约占60%左右,其次是生产丙稀氰、环氧丙烷、异丙苯、异丙醇、端基醇和其他下游产品[2]。
2丙烯产需发展趋势随着丙烯衍生物聚丙烯的需求的逐年增长,近年来丙烯的需求量快速增长。
2005年世界丙烯的需求增长约为4.1%,高于乙烯需求增长率3.1%,2006年到2010年丙烯需求年增长率为4.8%,而这期间乙烯需求年增长率为4.3%。
当前,世界范围内丙烯的需求已经超过产能的增速[3],产需之间有很大缺口,其价格也不断走高[4]。
而近年来中国的高速经济发展,丙烯的需求增长远远超过世界水平[5]。
所以,寻求高效合理的工业技术增产丙烯符合我国及世界未来石油化工原料市场的需要。
本文综述了蒸汽裂解技术以及相关的工艺开发、乙烯和丁烯歧化技术、基于催化裂化装置的丙烯增产技术、丙烷脱氢生产丙烯的技术以及基于煤和天然气经由甲醇制取烯烃的技术。
3增产丙烯工艺技术进展3.1蒸汽裂解制乙烯多产丙烯工艺目前蒸汽裂解仍是全世界丙烯生产最主要的来源,石油烃类如乙烷或石油馏分如石脑油(汽油)、瓦斯油(柴油)等在高温(一般在750℃以上)和水蒸气存在的条件下发生分子断裂和脱氢反应。
蒸汽裂解是吸热反应,通常在管式加热炉内进行:原料和水蒸气经预热后入加热炉炉管,被加热至750~900℃,发生裂解。
蒸汽裂解是生产乙烯的主要方法,同时多产丙烯等低分子烯烃,是强大的石油化学工业的基础[6]。
在蒸汽裂解制乙烯过程中,不同原料和操作条件下丙烯的收率也不相同。
但总的来说,各种原料的丙烯产率随着原料分子量的增加而增大。
乙烯裂解装置规模趋向大型化、低成本化,并且近几年蒸汽裂解技术得到进一步提高。
比如,Lummus公司开发的乙烯工艺采用了短停留时间裂解炉、快速急冷换热器和在线清焦技术。
Shell公司采用等离子电力焊接工艺,在裂解炉管子内壁形成2~4 mm厚合金保护层,该炉管涂层技术延长裂解炉使用寿命,使反应炉管使用寿命由3~6年延长到6~10年。
美国Aemn表面技术公司(AST) 采用热扩散法在炉管内壁涂上特定的金属对裂解炉管内壁进行改性,金属涂层由两层组成,一层为铬/硅涂层,然后再在其上涂上铝/硅涂层,可抑制焦炭附着和炉管脆化,从而可将耐热温度从l000℃提高到1200℃,使乙烯和丙烯产率提高。
道化学公司推出CCA 500抗垢剂技术,使裂解炉运转时间延长2~8倍.同时提高了转化率和裂解深度。
3.2 C4以上烯烃裂解制丙烯工艺由于市场对丙烯衍生物产品持续的旺盛需求,与蒸汽裂解相配套的新工艺不断出现,传统的乙烯联产和炼厂回收丙烯方法已经难满足对丙烯日益增长的需求,一系列能多产丙烯的技术相继得以开发。
C4以上烯烃物流及轻裂解汽油是良好的转换成乙烯和丙烯的原料,轻烯烃裂解增产丙烯典型的代表性工艺有:MOI工艺,Propylur工艺及Superflex工艺。
3.2.1 MOI工艺烯烃互相转化(MOI)工艺为Mobil公司开发的、将蒸汽裂解的副产物(如C4, C5和轻裂解汽油)转化成丙烯和乙烯的技术,同时还可将炼厂新配方汽油中不理想的组分轻裂化石脑油转化成丙烯。
该工艺的关键是ZSM-5沸石催化剂,整个反应过程在一个单一连续再生的流化床反应器中进行,预热后的气相进料在反应区内与催化剂接触得到产品气,经过分离得到最终产品。
整个过程的操作温度和压力与催化裂化装置相似。
该工艺的催化剂活性通过不断抽出生焦催化剂并在流化床中用空气再生来保持。
再生后的催化剂将重新返回反应器并为进料提供部分预热。
3.2.2 Propylur工艺Propylur工艺由Lurgi公司开发,将C4/C5烯烃转换成丙烯和乙烯,该工艺合并在一套石脑油裂解装置中,可以使丙烯/乙烯产率比提高至1.0,蒸汽裂解装置中质量分数约为60%的C4C5馏分可以直按转化成丙烯。
该工艺的特点是在固定床反应器中采用了一种择形多相ZSM-5分子筛催化剂,反应器进料中加入了优选比例的蒸汽,在500 o C和0.1~0.2MPa条件下运行。
在Propylur装置的上游,对二烯烃组分进行加氢处理,可以减少结炭产生。
该工艺裂解条件十分温和,催化剂可以进行间断性进行再生,催化剂寿命超过1个月。
而且,蒸汽的加入可以提高反应物选择性,减少积炭和聚合物的生成,使用简单而廉价的卧式固定床绝热反应器即可。
该工艺的原料兼容性很好,无论烷烃、环烷烃、环烯烃还是芳烃都不会影响烯烃的转化,上述组分通过催化剂时只发生轻微的变化或完全没有改变。
到目前为止已有5种不同工业来源的原料在Lurgi公司中试装置上进行了验证,现正在开发工业化装置的流程,该工艺独家转让给了Linde公司。
典型的轻烯烃的总质量转化率为83%,通常生成42%丙烯、31%丁烯和10%乙烯。
塔底出来的C4C5物流部分循环回装置中可以提高丙烯收率。
3.2.3 Superflex工艺由Arco化学公司开发的Superflex工艺也是一项能提高丙烯收率的具有经济性的工艺,可将低值轻烃转化为丙烯,具有较高的转化率并对丙烯的选择性也最大。
它能处理轻烃如C4~C8石油馏分,理想的原料是从热裂解过程中副产的C4和C5馏分。
甲基叔丁基醚抽余油、芳烃装置的抽余液和富含烯烃的炼厂物流,如来自流化催化裂化装置、焦化装置或减粘裂化炉的石脑油,都可以作为Superflex工艺的原料来源。
Superflex系统由反应器/再生炉(转化器)、催化剂处理系统、空气压缩机、烟道气系统和原料/产品的热交换系统组成。
该工艺可得到高于40%的丙烯产率。
并且对轻烃的选择性较高,它几乎能将三分之二的原料转化成乙烯和丙烯。
3.3乙烯和丁烯歧化技术及工艺烯烃歧化(Olefin metathesis, Olefin disproportionation)又称烯烃复分解或烯烃易位反应。
它是通过烯烃碳-碳双键发生断裂并在分子间重新结合生成新产品的过程。
该技术就是利用乙烯和丁烯进行歧化生成丙烯的过程。
因有时丁烯市场低迷,石脑油裂解制乙烯的厂商对联产的C4馏分感到压力,而该技术可以在不降低石脑油裂解苛刻度的同时消化C4馏分,并增产丙烯。
目前已有以下几种代表性工艺。
OCT工艺烯烃转化技术(OCT)是Phillip公司开发的首套工业化的烯烃歧化工艺[7],可由乙烯二聚、异构化和歧化多个反应工序组成。
异构化的目的是将难以与乙烯发生歧化作用的1-丁烯异构为2-丁烯,并分离其中的异丁烯[8]。
乙烯二聚可弥补C4来源的不足。
在OCT工艺过程中,乙烯及循环乙烯与丁烯及循环丁烯混合并预热后,进入歧化固定床反应器,在氧化钨催化剂作用下,丁烯的转化率通常为60%~70%,丙烯选择性高于92%。
歧化反应器的产物被冷却和分馏,以除去未反应乙烯并循环利用。
乙烯塔塔底料被送入丙烯塔进行分离,分离出丁烯及更重的组分并循环利用,最终得到聚合级丙烯。
Meta-4工艺“Meta-4"歧化工艺由IFP公司开发[9],该工艺既可与蒸汽裂解装置相结合,也可利用炼厂FCC装置出来的C4馏分[10]。
“Meta-4"歧化工艺采取低温液相反应,使用担载在氧化铝上的铼系催化剂和液体反应介质逆向按触,在35o C下单程平衡转化率可达63%[11]。
催化剂连续再生使再生设备的尺寸较小,减少了催化剂存量。
低温下反应使催化剂上的积碳可更容易燃烧掉。
失活的催化剂从反应器底部卸出,提升至再生器再生后返回反应器顶部。
反应器底部的液体送到蒸馏段,脱乙烷塔内回收的乙烯再循环使用。
在脱丙烷塔内分离后得到聚合级丙烯。
没有反应的C4组分可循环至反应器再利用。
该工艺已在台湾省高雄的示范装置上运转了8600h,催化剂经过76次再生后仍保持非常优异的化学和物理性能,据称该催化剂至少可使用2年。
根据需要,该工艺可用在现有裂解炉上,开停工方便,投资回报率较高。
BASF C4烯烃歧化工艺BASF公司开发的烯烃歧化制丙烯技术[12][13][14],包括C4烯烃中的1-丁烯与2-丁烯反应生成丙烯和2-戊烯,2-戊烯与乙烯反应生成1-丁烯和丙烯两个步骤。
C4烯烃要经过脱除丁二烯和炔烃、异丁烯和含氧杂质,1-丁烯异构化为2-丁烯的C4烯烃精制过程。
国内相关研究国内也开展了歧化制丙烯的相关研究工作[15]。
大连化学物理研究所的乙烯与丁烯歧化制丙烯工艺主要采用钼基催化剂,碱金属或碱土金属为助剂进行改性,采用多种分子筛作载体,在乙烯与2-丁烯摩尔比1.5-3,60-70o C,1.0MPa条件下,丙烯选择性为90%-95%, 2-丁烯转化率在60%-90%,同时还研究了催化剂的预处理对反应性能的影响及反应后催化剂的再生条件[16]。
3.4 FCC装置多产丙烯工艺FCC装置是炼厂丙烯的主要来源。
这类技术多采用沸石分子筛或其他固体酸催化剂,工艺反应温度较低(550 o C~650 o C ),产物中丙烯占相当份额,所以此类工艺以生产丙烯为主,乙烯为辅,而且可增加芳烃选择性。
与FCC工艺相似,但反应条件更苛刻,所以对催化剂的稳定性提出了更高的要求。
多产丙烯的FCC工艺技术主要有SCC工艺、DCC工艺、Maxofin工艺和PetroFCC工艺等。
3.2.1 SCC技术ABB Lummus公司开发的SCC技术将高苛刻度FCC操作与石脑油组分选择性裂化和烯烃歧化技术组合在一起的成套技术。
将FCC催化剂与ZSM-5分子筛结合使用,采用进料喷嘴和直联式偶联旋风分离器使进料达到最大汽化速率,促进气相反应,减少焦炭和干气产率。
采用的石脑油选择性裂化技术,可从主进料喷嘴上游将石脑油或更轻组分选择注入提升管,缩短提升管停留时间。
该技术还结合OCT歧化技术,可使催化裂化产生的丁烯和乙烯通过歧化生成丙烯,从而进一步提高丙烯收率。
3.2.2 DCC工艺中国石化集团公司石油化工科学研究院开发的深度催化裂解技术(DCC),其流程类似于催化裂化工艺,以重减压柴油或脱沥青油为原料,生产低分子烯烃[17]。
DCC装置在538-582 o C, 10%~30%蒸汽条件下操作,可以有最大量丙烯(DCC-I型)和最大量异构烯烃(DCC-II)两种操作方案[18]。
前者以制取丙烯为主,兼产丁烯、乙烯和高辛烷值汽油组分。