精馏工艺操作基本知识
精馏操作规程

精馏操作规程一、引言精馏操作是化工工艺中常用的分离技术之一,通过利用不同组分的沸点差异,将混合物分离为不同纯度的组分。
本文旨在提供一份详细的精馏操作规程,以确保操作的顺利进行和分离效果的最大化。
二、设备准备1. 精馏塔:选择适合工艺要求的精馏塔,确保其结构稳定、密封性良好,并具备足够的塔板数和塔板间距。
2. 加热设备:使用适当的加热方式,如蒸汽加热或电加热,确保温度控制精准。
3. 冷凝器:选择合适的冷凝器,以确保冷凝效果良好,避免组分的混合。
4. 泵和储液罐:根据需要配置泵和储液罐,以便于进料和收集产品。
三、操作步骤1. 开始操作前,确保所有设备已经检查并处于良好工作状态。
检查精馏塔的塔板、填料或板式换热器的清洁情况,并清除任何可能影响操作的杂质。
2. 将混合物加入精馏塔的进料管道中,并通过泵控制进料速度。
根据混合物的性质和组分,确定进料位置和速度,以确保塔板上的液相和气相充分接触。
3. 打开加热设备,逐渐升高温度。
根据混合物的沸点差异,调整加热功率和温度控制,确保塔板上的液相蒸发和气相冷凝。
4. 确保冷凝器的冷却水供应正常,并调整冷却水流量和温度,以保持冷凝器的冷却效果。
5. 监测塔顶和塔底的温度和压力,并根据需要进行调整。
温度和压力的变化可以反映出分离效果的变化,以便及时采取措施进行调整。
6. 根据需要,定期取样分析塔顶和塔底的组分,并根据分析结果调整操作参数。
如果需要收集不同纯度的产品,可以根据组分分布曲线进行操作调整。
7. 当达到预定的分离效果时,停止加热设备,并逐渐降低温度。
关闭进料泵,停止混合物的进料。
8. 将剩余的混合物排空,并清洗精馏塔和相关设备,以便于下一次操作。
四、安全注意事项1. 在操作过程中,严禁使用火源或其他易燃物品,以防止发生火灾或爆炸。
2. 操作人员应穿戴适当的个人防护装备,如防护眼镜、手套和防护服,以保护自身安全。
3. 注意操作区域的通风情况,确保室内空气流通,避免有害气体的积聚。
精馏操作

• 3、进料温度变化 进料温度降低 现象:塔底的轻组分会加多,而塔顶的产 品将更纯。 措施:要相应增加塔底的热负荷,减小塔 顶冷凝器的冷负荷。或者将进料位置上移。 进料温度升高, 现象:塔顶的重组分增加,塔底的产品较 纯。 措施:需要增大塔顶的冷凝负荷,降低塔 底的热负荷。或者将进料位置下移
• 4、进料组分变化 1、变重 现象:精馏段的负荷加重,重组分带到塔顶。 温度升高、塔压降低 措施:进料口往下改、加大回流比、加冷量 2、变轻 现象:提馏段的负荷加重,造成轻组分带到 塔底,温度降低、塔压升高 措施:进料口往上改、减小回流比、加热量
四氯乙烯 氟化氢 二氯三氟乙烷 1,2—二氯三氟乙烷 1—氯—1,2,2,2—四氟乙烷 1—氯—1,1,2,2四氟乙烷 五氟乙烷 三氟氯乙烷 1,1,1,2—四氟乙烷 1,1,2,2—四氟乙烷 五氟氯乙烷 六氟乙烷 三氟乙烷 氯化氢
1110 / 123 123a 124 124 a 125 133a 134a 134 115 116 143a /
136.48
-12.00 -10.22
120.03 118.58 102.00
-48.50 6.89 -26.50 -19.72
154.48 138.01 84.04 36.47
-38.7 -78.50 -47.61 -83.70
• 3、回流比
• 回流比是精馏段内液体回流与采出液量之 比。回流比大,分离效果好,产品质量高, 回流比过大,生产能力下降,能耗增加, 回流比对精馏操作影响很大,直接关系到 塔内物料浓度的改变和温度的分布,最终 反映在它的分离效率上。
• 4、压力降
• 塔压力降是衡量塔内气体负荷大小的主要 因素。在进料、出料保持平衡,回流比不 变的情况下,塔压差基本是不变的。当正 常的物料平衡遭到破坏,或塔内温度、压 力改变时,都会造成塔内上升蒸汽流速的 改变,塔液位的改变,引起塔压差的变化。 • PDI
精馏原理和流程

1-4精馏原理和流程1.掌握的内容:精馏分离过程原理及分析2.重点:精馏原理、精馏装置作用3.难点:精馏原理,部分气化和部分冷凝在实际精馏操作中有机结合的过程。
1.4.1 精馏原理精馏原理是根据图1-7所示的t-x-y图,在一定的压力下,通过多次部分气化和多次部分冷凝使混合液得以分离,以分别获得接近纯态的组分。
理论上多次部分气化在液相中可获得高纯度的难挥发组分,多次部分冷凝在气相中可获得高纯度的易挥发组分,但因产生大量中间组分而使产品量极少,且设备庞大。
工业生产中的精馏过程是在精馏塔中将部分气化过程和部分冷凝过程有机结合而实现操作的。
1.4.2 精馏装置流程一、精馏装置流程典型的精馏设备是连续精馏装置,包括精馏塔、冷凝器、再沸器等,如图1-8所示。
用于精馏的塔设备有两种,即板式塔和填料塔,但常采用的是板式塔。
连续精馏操作中,原料液连续送入精馏塔内,同时从塔顶和塔底连续得到产品(馏出液、釜残液),所以是一种定态操作过程。
二、精馏装置的作用精馏塔以加料板为界分为两段,精馏段和提馏段。
1.精馏段的作用加料板以上的塔段为精馏段,其作用是逐板增浓上升气相中易挥发组分的浓度。
2.提馏段的作用包括加料板在内的以下塔板为提馏段,其作用逐板提取下降的液相中易挥发组分。
3.塔板的作用塔板是供气液两相进行传质和传热的场所。
每一块塔板上气液两相进行双向传质,只要有足够的塔板数,就可以将混合液分离成两个较纯净的组分。
4.再沸器的作用其作用是提供一定流量的上升蒸气流。
5.冷凝器的作用其作用是提供塔顶液相产品并保证有适当的液相回流。
回流主要补充塔板上易挥发组分的浓度,是精馏连续定态进行的必要条件。
精馏是一种利用回流使混合液得到高纯度分离的蒸馏方法。
1-5两组分连续精馏的计算1.掌握的内容:(1)精馏塔物料衡算的应用。
(2)操作线方程和q线方程及其在x-y图上的作法和应用。
(3)理论板和实际板数的确定(逐板计算法和图解法)、塔高和塔径的计算。
精馏操作

精馏的原理和操作探讨学习精馏的原理——定义在一定压力下进行多次冷凝、蒸发,分离混合物的精馏操作称为精馏。
精馏塔的三大平衡:(1)物料平衡即F = D + W (进料=塔顶采出+塔底采出)对某一组分(轻组分):F xF=D xD+W xW操作中必须保证物料平衡,否则影响产品质量。
精馏设备的仪表必须设计为能使塔达到物料平衡,以便进行稳定的操作。
为了进行总体的进料平衡,塔顶和塔底的采出量必须进行适当的控制,进料物料不是做为塔顶产品采出,就是作为塔底产品采出。
通过调节阀控制(2)热量平衡QB + QF = QC + QD + QW + QLQB——再沸器加热剂带入的热量QF——进料带入热量QC——冷凝器冷却剂带出的热量QD——塔顶产品带出热量QW——塔底产品带出热量QL——散失于环境的热量操作中要保持热量的平衡,再沸器、冷凝器的负荷要满足要求,才能保持平稳操作。
再沸器和进料的热量输入必须转移到塔顶冷凝器。
如果试图使再沸器加热量输入和回流控制相互独立,那么该系统就不会稳定,因为热量不平衡。
(3)汽液相平衡在精馏塔板上温度较高的的气体和温度较低的液体相互接触时要进行传质、传热,其结果是气体部分冷凝,液相中重组分增加,而塔板上液体部分汽化,使汽相中轻组分浓度不断增加,当汽液相达到平衡时,其组分的组成不在随时间变化。
在精馏塔的连续操作过程中应做到物料平衡、气-液平衡和热量平衡,这3个平衡互相影响,互相制约。
借鉴R-134a一分塔的一些操作经验一、稳定几个参数包括进料温度、塔顶压力、回流量、回流温度,操作时尽量保持这几个参数的稳定,特别时塔顶的压力,其他三个参数可以作微调,或是从节能的角度考虑进行调节二、保持物料平衡根据操作经验和馏出口分析确定塔顶重关键组分的量和塔底轻关键组分的量,塔顶采出=进料量*进料中轻组分含量*(1+重关键组分含量)塔底采出=进料量*进料中重组分含量*(1+轻关键组分含量)或塔底采出=进料量—塔顶采出塔顶采出=进料量—塔底采出实际操作中根据塔顶和塔底馏分的质量要求确定计算方法,看那个的质量要求的比较严格,如果是塔顶产品的质量要求高,那么就通过塔顶采出=进料量*进料中轻组分含量*(1+重关键组分含量)计算塔顶采出量,在由塔底采出=进料量—塔顶采出计算塔底采出量,确定了物料平衡(以上为粗略计算,存在一定偏差,实际操作中还要参考产品质量和塔的压差)。
精馏塔常识

1,液泛?在精馏操作中,下层塔板上的液体涌至上层塔板,破坏了塔的正常操作,这种现象叫做液泛。
液泛形成的原因,主要是由于塔内上升蒸汽的速度过大,超过了最大允许速度所造成的。
另外在精馏操作中,也常常遇到液体负荷太大,使溢流管内液面上升,以至上下塔板的液体连在一起,破坏了塔的正常操作的现象,这也是液泛的一种形式。
以上两种现象都属于液泛,但引起的原因是不一样的。
2,雾沫夹带?雾沫夹带是指气体自下层塔板带至上层塔板的液体雾滴。
在传质过程中,大量雾沫夹带会使不应该上到塔顶的重组分带到产品中,从而降低产品的质量,同时会降低传质过程中的浓度差,只是塔板效率下降。
对于给定的塔来说,最大允许的雾沫夹带量就限定了气体的上升速度。
影响雾沫夹带量的因素很多,诸如塔板间距、空塔速度、堰高、液流速度及物料的物理化学性质等。
同时还必须指出:雾沫夹带量与捕集装置的结构也有很大的关系。
虽然影响雾沫夹带量的因素很多,但最主要的影响因素是空塔速度和两块塔板之间的气液分离空间。
对于固定的塔来说,雾沫夹带量主要随空塔速度的增大而增大。
但是,如果增大塔板间的距离,扩大分离空间,则相应提高空塔速度。
3,液体泄漏?俗称漏液,塔板上的液体从上升气体通道倒流入下层塔板的现象叫泄漏。
在精馏操作中,如上升气体所具有的能量不足以穿过塔板上的液层,甚至低于液层所具有的位能,这时就会托不住液体而产生泄漏。
空塔速度越低,泄漏越严重。
其结果是使一部分液体在塔板上没有和上升气体接触就流到下层塔板,不应留在液体中的低沸点组分没有蒸出去,致使塔板效率下降。
因此,塔板的适宜操作的最低空塔速度是由液体泄漏量所限制的,正常操作中要求塔板的泄漏量不得大于塔板上液体量的10%。
泄漏量的大小,亦是评价塔板性能的特性之一。
筛板、浮阀塔板和舌形塔板在塔内上升气速度小的情况下比较容易产生泄漏。
4,返混现象?在有降液管的塔板上,液体横过塔板与气体呈错流状态,液体中易挥发组分的浓度降沿着流动的方向逐渐下降。
精馏知识问答最新

甲醇精馏操作知识问答1、什么是沸点?答:某液体在一定压力作用下沸腾时的温度叫该液体在该压力下的沸点,如甲醇的沸点是64.5~64.7°C。
(1atm)2、什么叫汽化?答:物质由液相转化为气相的过程叫汽化。
3、什么叫冷凝?答:物质由气相转化为液相的过程叫冷凝。
4、什么叫回流?什么叫回流比?答:在精馏操作中,为了保证精馏的正常运行和产品质量,常把从塔顶采出馏分的一部作为产品,另一部分返回塔顶作为传质传热介质,这部分返回液体叫回流。
回流液体与作为产品采出的那部分的比值叫回流比。
常用R表示,R=L/D。
5、什么是最小回流比?答:为了保证产品和精馏操作的稳定,精馏的回流比不能低于某一规定值,该规定值即最小回流比。
6、什么叫全回流?答:在精馏操作中,把从塔顶采出的冷凝液作为回流液全部返回塔顶的操作叫全回流,R=无穷大,如预精馏塔。
7、填料塔与板式塔的比较答:(1)板式塔为逐级接触式气液传质设备,是最常用的气液传质设备之一。
传质机理:塔内液体依靠重力作用,由上层塔板的降液管流到下层塔板的受液盘,然后横向流过塔板,从另一侧的降液管流至下一层塔板。
溢流堰的作用是使塔板上保持一定厚度的液层。
气体则在压力差的推动下,自下而上穿过各层塔板的气体通道(泡罩、筛孔或浮阀等),分散成小股气流,鼓泡通过各层塔板的液层。
在塔板上,气液两相密切接触,进行热量和质量的交换。
在板式塔中,气液两相逐级接触,两相的组成沿塔高呈阶梯式变化,在正常操作下,液相为连续相,气相为分散相。
一般而论,板式塔的空塔速度较高,因而生产能力较大,塔板效率稳定,操作弹性大,且造价低,检修、清洗方便,故工业上应用较为广泛。
(2)填料塔是以塔内的填料作为气液两相间接触构件的传质设备。
填料塔的塔身是一直立式圆筒,底部装有填料支承板,填料以乱堆或整砌的方式放置在支承板上。
填料的上方安装填料压板,以防被上升气流吹动。
液体从塔顶经液体分布器喷淋到填料上,并沿填料表面流下。
精馏培训讲义PPT课件

目录
• 精馏技术简介 • 精馏流程与设备 • 精馏操作与控制 • 精馏分离效率与能耗分析 • 精馏安全与环保 • 精馏案例分析与实践
01 精馏技术简介
精馏的定义与原理
精馏的定义
精馏是一种利用混合物中各组分 挥发度的不同,通过加热、冷凝 、分馏等操作将液体混合物进行 分离的物理过程。
回收率
表示实际产品中目标组分 的比例,数值越高,目标 组分的回收效果越好。
热力学效率
反映精馏过程热力学有效 性的指标,数值越高,热 力学效率越高。
能耗分析的方法与意义
能耗分析方法
通过测量和计算精馏过程中的各种能 耗,如加热、冷却、压缩等,分析能 耗的分布和影响因素。
能耗分析意义
有助于优化精馏过程,降低能耗,提 高经济效益和环境可持续性。
精馏设备中的搅拌器、 泵等机械设备可能导致 夹击、割伤等事故。应 保持设备清洁,定期维 护保养,确保安全防护 装置完好。
精馏区域可能存在电气 安全隐患,如潮湿、腐 蚀等。应采用防爆、防 水等电气设备和电缆, 定期检查电气线路和设 备。
精馏过程的环保要求与处理方法
01 总结词
02 废气处理
03 废水处理
填料
填充在塔体内,增加接触面积 ,促进传热和传质。
塔板
设置在塔体内,形成不同的汽 液分离区域。
进料口和出料口
控制原料和产品的进入和流出 。
辅助设备
热源
提供加热所需的热量。
冷源
用于冷却回流液和产品。
泵
输送原料和产品。
仪表
监测温度、压力等参数。
精馏流程的优化与改进
控制进料速度和温度
调整进料速度和温度,提高分离效果。
04 噪声控制
精馏基础知识培训

精馏塔物料衡算
对稳定操作连续精馏塔,无论塔
V
顶的回流液量与塔釜的再沸蒸汽量多 D,xD
大,料液加入量必等于塔顶和塔釜所 F,zF
得产品量之和。
V L L,xD V' L'
总物料衡算 F D W
V'
L'
W,xW
易挥发组分物料衡算 FzF DxD WxW
图10-11 全塔物料衡算
例题:将 5000kg/h 含正戊烷 0.4( 摩尔分率 ) 的正戊烷 正己烷混合液在连续精馏塔内分离 , 馏出液含正戊烷 0.98, 釜液含正戊烷不高于 0.03。 求:馏出液、釜液的流量及塔顶易挥发组分的回收率。
萃取操作过程
萃取过程中,所选择的溶剂 称为萃取剂;混合液在溶解度 大的组分称为溶质,而不溶或
原料液
溶解度小的组分称为稀释剂。
经过混合、分离后形成两 层液相:萃取相和萃余相。萃 取剂提取了溶质成为萃取相, 分离出溶质的混合液成为萃余 相。
萃取剂回收
通常 ,萃取过程在高温下进行,萃取的结果是萃 取剂提取了溶质成为萃取相,分离出溶质的混合液 成为萃余相。萃取相的混合物,需要用精馏或解吸 等方法进行分离,得到溶质产品和溶剂(萃取剂), 萃取剂供循环使用。
2 、蒸馏分离的特点
( 1 )通过蒸馏操作,可以直接获得所需要的产品, 而吸收和萃取还需要如其它组分;
( 2 )蒸馏分离应用较广泛,历史悠久; ( 3 )能耗大,在生产过程中产生大量的气相或液相。
3 、蒸馏的分类
3 、蒸馏的分类
第二节 工作原理 平衡蒸馏
工作原理: 利用液体混合 物中各组分挥发性差异 ,以热能为媒介使其部 分汽化从而在汽相富集 轻组分、液相富集重组 分而分离的方法。
T8塔顶为萃余相,得到二类石油醚原料,塔底 为萃取相,进到T9塔。T9分离出粗苯(溶质)和萃 取剂(溶剂)。
精馏操作问答
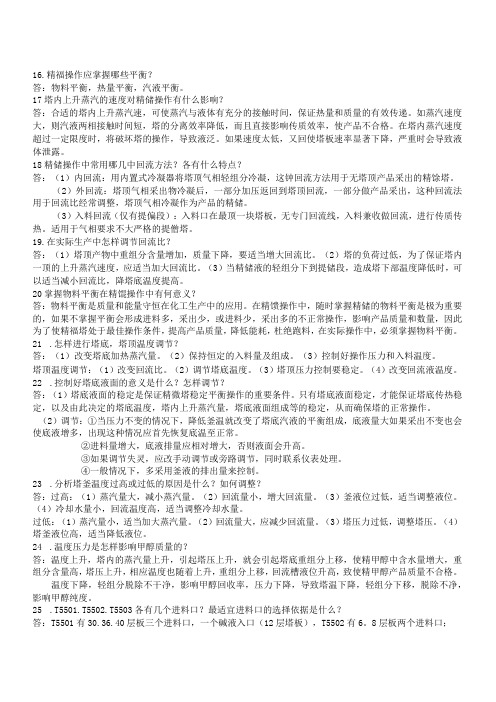
16.精福操作应掌握哪些平衡?答:物料平衡,热量平衡,汽液平衡。
17塔内上升蒸汽的速度对精储操作有什么影响?答:合适的塔内上升蒸汽速,可使蒸汽与液体有充分的接触时间,保证热量和质量的有效传递。
如蒸汽速度大,则汽液两相接触时间短,塔的分离效率降低,而且直接影响传质效率,使产品不合格。
在塔内蒸汽速度超过一定限度时,将破坏塔的操作,导致液泛。
如果速度太低,又回使塔板速率显著下降,严重时会导致液体泄露。
18精储操作中常用哪几中回流方法?各有什么特点?答:(1)内回流:用内置式冷凝器将塔顶气相轻组分冷凝,这钟回流方法用于无塔顶产品采出的精馀塔。
(2)外回流:塔顶气相采出物冷凝后,一部分加压返回到塔顶回流,一部分做产品采出,这种回流法用于回流比经常调整,塔顶气相冷凝作为产品的精储。
(3)入料回流(仅有提偏段):入料口在最顶一块塔板,无专门回流线,入料兼收做回流,进行传质传热。
适用于气相要求不大严格的提僧塔。
19.在实际生产中怎样调节回流比?答:(1)塔顶产物中重组分含量增加,质量下降,要适当增大回流比。
(2)塔的负荷过低,为了保证塔内一顶的上升蒸汽速度,应适当加大回流比。
(3)当精储液的轻组分下到提储段,造成塔下部温度降低时,可以适当减小回流比,降塔底温度提高。
20掌握物料平衡在精馄操作中有何意义?答:物料平衡是质量和能量守恒在化工生产中的应用。
在精馈操作中,随时掌握精储的物料平衡是极为重要的,如果不掌握平衡会形成进料多,采出少,或进料少,采出多的不正常操作,影响产品质量和数量,因此为了使精福塔处于最佳操作条件,提高产品质量,降低能耗,杜绝跑料,在实际操作中,必须掌握物料平衡。
21.怎样进行塔底,塔顶温度调节?答:(1)改变塔底加热蒸汽量。
(2)保持恒定的入料量及组成。
(3)控制好操作压力和入料温度。
塔顶温度调节:(1)改变回流比。
(2)调节塔底温度。
(3)塔顶压力控制要稳定。
(4)改变回流液温度。
22.控制好塔底液面的意义是什么?怎样调节?答:(1)塔底液面的稳定是保证精微塔稳定平衡操作的重要条件。
精馏工艺操作
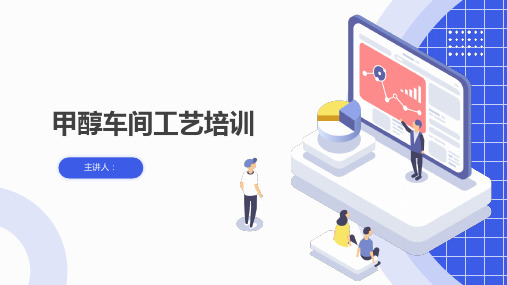
影响精馏操作的主要因素
五、操作压力的影响
塔的压力是精馏塔主要的控制指标之一。在精馏操作中,常常规定了操作压力的 调节范围。塔压波动过大,就会破坏全塔的气液平衡和物料平衡,使产品达不到所要 求的质量。
提高操作压力,可以相应地提高塔的生产能力,操作稳定。但在塔釜难挥发产品 中,易挥发组分含量增加。如果从塔顶得到产品,则可提高产品的质量和易挥发组分 的浓度。影响塔压变化的因素:塔顶温度,塔釜温度、进料组成、进料流量、回流量、 冷剂量、冷剂压力等的变化以及仪表故障、设备和管道的冻堵等。
1)减少塔顶采出量以增大回流比。
2)塔顶冷凝器为分凝器时,可增加塔顶冷剂的用量,以提高凝液量,增大回流比。
3)有回流液中间贮槽的强制回流,可暂时加大回流量,以提高回流比,但不得将 回流贮槽抽空。必须注意,在馏出液采出率D/F规定的条件下,借增加回流比R以提高 塔釜残液量的的方法并非总是有效。加大操作回流比意味着加大蒸发量与冷凝量,这 些数值还将受到塔釜及冷凝器的传热面的限制
精馏工艺流程
常压塔底液含有微量的甲醇和高沸点杂质,经回收塔进料泵加压, 由调节阀控制,由甲醇回收塔第24、26、30任一塔板进料至甲醇回收 塔。回收塔再沸器热源为低压蒸汽,塔釜温度由调节阀控制。回收塔塔 顶气体~81℃,经回收塔冷凝器降温至~40℃,液体进入回收塔回流槽, 再由回收塔回流泵抽出,部分由调节阀控制,送回至回收塔塔顶回流, 部分作为产品杂醇油,由调节阀控制,送至杂醇贮槽。回收塔侧线由塔 盘18、20、32、38任意采出的杂醇至冷却器冷却到~40℃后靠静压送 到杂醇贮槽。回收塔底的废水,经废水冷却器冷却后由废水泵送至事故 水池。
TWO
精馏工艺流程图
THREE
精馏工艺流程
从甲醇合成工段来的粗甲醇和稀醇水,(温度40℃,压力0.5MPa, 流量约40t/h)或由粗甲醇贮槽来粗甲醇,经粗甲醇预热器预热后,进 入(共3路进料,视情况选择进料板。进料板分别为14、20、24塔板) 预精馏塔。为中和预精馏塔底的少量酸及促进胺类和羰基物的分解,在 配碱槽配置5%-10%含量的NaOH碱液后放入碱液槽,经往复式计量泵 送入ME-40501管线,向预塔加入碱液约67.5㎏/h。
精馏工艺流程
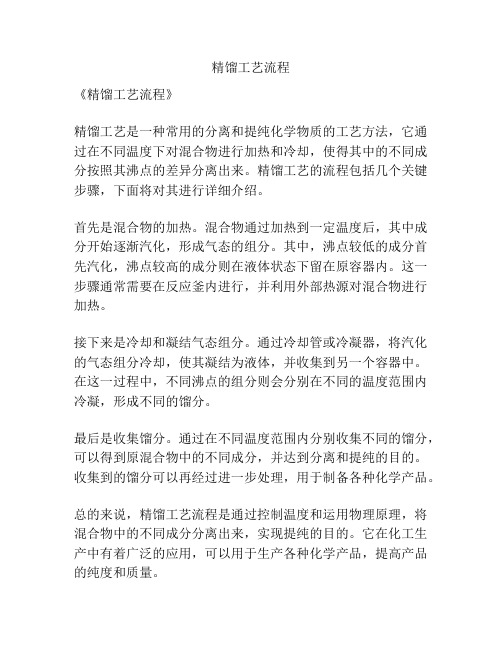
精馏工艺流程
《精馏工艺流程》
精馏工艺是一种常用的分离和提纯化学物质的工艺方法,它通过在不同温度下对混合物进行加热和冷却,使得其中的不同成分按照其沸点的差异分离出来。
精馏工艺的流程包括几个关键步骤,下面将对其进行详细介绍。
首先是混合物的加热。
混合物通过加热到一定温度后,其中成分开始逐渐汽化,形成气态的组分。
其中,沸点较低的成分首先汽化,沸点较高的成分则在液体状态下留在原容器内。
这一步骤通常需要在反应釜内进行,并利用外部热源对混合物进行加热。
接下来是冷却和凝结气态组分。
通过冷却管或冷凝器,将汽化的气态组分冷却,使其凝结为液体,并收集到另一个容器中。
在这一过程中,不同沸点的组分则会分别在不同的温度范围内冷凝,形成不同的馏分。
最后是收集馏分。
通过在不同温度范围内分别收集不同的馏分,可以得到原混合物中的不同成分,并达到分离和提纯的目的。
收集到的馏分可以再经过进一步处理,用于制备各种化学产品。
总的来说,精馏工艺流程是通过控制温度和运用物理原理,将混合物中的不同成分分离出来,实现提纯的目的。
它在化工生产中有着广泛的应用,可以用于生产各种化学产品,提高产品的纯度和质量。
《精馏基础知识》课件
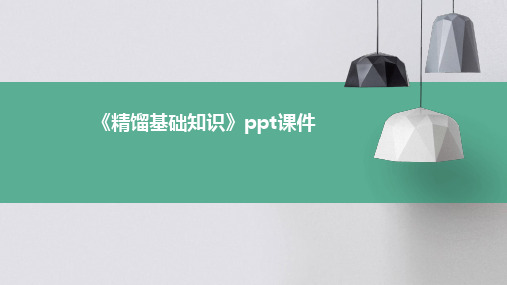
塔板或填料
提供气液接触面,促进气液传质 和传热。
进料口
将原料引入塔内的装置,位置根 据工艺要求而定。
塔底再沸器
加热塔底液体,使其部分汽化后 返回塔内,提供上升蒸汽。
塔顶冷凝器
将塔顶上升蒸汽冷凝成液体的装 置,以便进行液相收集和回流。
回流口
将部分塔顶冷凝液返回塔内的装 置,用于提供液相回流。
精馏塔操作参数设置
03
精馏塔结构与操作
精馏塔类型及特点
1 2
3
板式塔
气液接触良好,操作弹性大,塔板效率高,但结构复杂,造 价高。
填料塔
结构简单,造价低,压降小,但操作弹性小,效率相对较低 。
复合塔
结合板式塔和填料塔的优点,具有高效、低压降、大操作弹 性等特点。
精馏塔内部构件介绍
塔体
提供气液传质和传热的场所,通 常由钢板焊接而成。
精馏原理
基于溶液中不同组分相对挥发度的差异,通过加热使溶液部分汽化,然后使汽液两相进行充分接触,进行相际传 质,使易挥发组分不断从液相往气相中转移,而难挥发组分则从气相往液相中转移,从而在塔顶得到易挥发组分 的浓度较高的产品,在塔底得到难挥发组分的浓度较高的产品。
精馏分类及应用领域
精馏分类
根据操作方式的不同,精馏可分为连 续精馏和间歇精馏;根据压力的不同 ,可分为常压精馏、加压精馏和减压 精馏。
随着新能源和环保领域的快速发展,精馏 技术将在这些领域发挥重要作用,如用于 锂电池电解液的提纯、废气处理等。
THANKS
实验结果讨论与误差分析
实验结果展示
将实验结果以图表形式展示,便于直观比较和分析。
结果讨论
根据实验结果,讨论精馏过程的效率、产品质量等关键指标,以及 与理论预测的差异。
精馏工艺知识点总结

精馏工艺知识点总结精馏是一种用于分离和纯化混合物的方法,通过利用不同物质的沸点差异将混合物的组分进行分离。
精馏工艺在化工生产中被广泛应用,尤其是在石油化工和化学工业中。
以下是对精馏工艺的一些知识点的总结。
一、精馏原理精馏原理基于不同物质的沸点差异,利用热分解和凝华的原理使混合物的组分进行分离。
在精馏过程中,混合物被加热至沸点,然后蒸汽通过冷凝器冷却,生成液体,不同组分由于沸点不同,在冷却过程中会分别凝华,从而实现分离。
二、精馏设备1. 蒸馏塔:是精馏过程中最主要的设备,一般有塔筒、进料管、回流器、塔板等部件,用来将混合物通过加热进行分离与纯化。
2. 冷凝器:负责将蒸汽冷却成液体,促使混合物的凝华分离。
3. 凝结器:用于收集凝华液体,将不同组分分离收集。
三、常见的精馏工艺1. 原油精馏:利用石油中不同组分的沸点差异,进行分馏得到汽油、柴油、煤油等产品。
2. 酒精精制:利用酒精和水的沸点差,进行酒精的纯化。
3. 水的蒸馏:通过加热水使其沸腾,将水蒸汽分离冷凝得到纯净水。
四、精馏工艺的影响因素1. 混合物的成分:不同混合物的组分和沸点差异不同,对精馏过程影响很大。
2. 进料温度和压力:进料温度和压力的变化会直接影响精馏过程中的温度和压力变化,从而影响分离效果。
3. 冷凝器的温度及冷却效果:冷凝器冷却效果直接影响蒸汽的凝华时间,从而影响分离效果。
五、精馏工艺的优缺点1. 优点:(1)可以有效分离混合物中的各种组分,提高纯度和纯净度;(2)精馏过程自动化程度高,操作简单,易于控制;(3)可适用于各种混合物,广泛应用于石油化工、化学工业等领域。
2. 缺点:(1)能耗较高,需要大量能源和设备支持;(2)对进料质量要求较高,不适用于一些难以分离的混合物;(3)部分组分可能在精馏过程中发生化学反应,影响产品质量。
六、精馏工艺的应用1. 石油精馏:用于从原油中提炼出汽油、柴油、煤油等产品。
2. 化工原料的纯化:如酒精、醋酸、甘油等化工原料的纯化和分离。
精馏工艺操作基本知识

8、什么是显热?
纯物质在不发生相变和化学反应的条件下, 因温度的改变而吸收或放出的热量叫显热。
9什么是回流比
在精馏过程中,混合液加热后所产生的蒸汽由塔 顶蒸出,进入塔顶冷凝器。蒸汽在此冷凝(或部 分冷凝)成液体,将其一部分冷凝液返回塔顶沿 塔板下流,这部分液体叫做回流液;将另一部分 冷凝液(或未凝蒸汽)从塔顶采出,作为产品。 回流比就是回流液量与采出量的重量比,通常以 通常以R来表示,即 R=L/D 式中R-回流比 L-单位时间内塔顶回流液体量,公斤/小时。 D-单位时间内塔顶采储量,公斤/小时。
5.什么是泡点?
液体混合物在一定压力下加热到某一温度 时,液体中出现的第一个很小的气泡,即 刚开始沸腾时的温度叫该液体在指定压力 下的泡点温度,简称泡点。处于泡点温度 下的液体称为饱和液体,即精馏塔的釜温 温度。应该说明,这第一个很小的气泡, 也不是纯组分,它的组成也是有相平衡关 系决定的。
6、什么是沸点?
精馏塔的操作
1.精馏操作的影响因素有哪些?
除了设备问题以外,精馏操作过程的影响 因素主要有以下几个方面:塔的温度和压 力(包括塔顶、塔釜和某些有特殊意义的 塔板);进料状态;进料量;进料组成; 进料温度;塔内上升蒸汽速度和蒸发釜的 加热量;回流量;塔顶冷剂量;塔顶采出 量和塔底采出量。塔的操作就是按照塔顶 和塔底产品的组成要求来对这几个影响因 素进行调节。
11、什么是全回流?
在精馏操作中,把停止塔进料、塔釜出料 和塔顶出料,将塔顶冷凝液全部作为回流 液的操作,成为全回流。全回流操作,多 半用在精馏塔的开车初期,或用在生产不 正常时精馏塔的自生循环操作中。
12.什么是液泛?
在精馏操作中,下层塔板上的液体涌至上层塔板, 破坏了塔的正常操作,这种现象叫做液泛。 液泛形成的原因,主要是由于塔内上升蒸汽的速 度过大,超过了最大允许速度所造成的。另外在 精馏操作中,也常常遇到液体负荷太大,使溢流 管内液面上升,以至上下塔板的液体连在一起, 破坏了塔的正常操作的现象,这也是液泛的一种 形式。以上两种现象都属于液泛,但引起的原因 是不一样的。
化工萃取精馏工艺详解

化工萃取精馏工艺详解一、基本原理和流程萃取精馏是在被分离溶液中加入另一组分(称为溶剂或萃取剂),增大被分离组分的相对挥发度,因而能用精馏方法分离。
萃取剂的沸点比原溶液各组分的沸点均高,且不和被分离溶液各组分形成恒沸物。
二、萃取精馏的分类萃取精馏按照其操作方式可以分为两类,即连续萃取精馏和间歇萃取精馏。
1、连续萃取精馏连续萃取精馏过程中,进料、溶剂的加入及回收都是连续的。
连续萃取精馏一般采用双塔操作,第一个塔是萃取精馏塔,被分离的物料由塔的中部连续进入塔内,而溶剂则在靠近塔顶的部位连续加入。
在萃取精馏塔内易挥发组分由塔顶馏出,而难挥发组分和溶剂由塔底馏出并进入溶剂回收塔。
在溶剂回收塔内,可使难挥发组分与溶剂得以分离,难挥发组分由塔顶馏出,而溶剂由塔底馏出并循环回送至萃取精馏塔。
2、间歇萃取精馏间歇萃取精馏是近年来兴起的新的研究方向,由于间歇萃取精馏具有间歇精馏和萃取精馏的优点,近年来引起了一些学者的注意。
间歇萃取精馏比连续萃取精馏复杂的多,其流程及操作方法与连续萃取精馏不同。
例如,在0.1MPa压力下,苯的沸点为80.1℃,环己烷的沸点为80.73℃。
由这两种组分构成的溶液,很难用一般精馏方法分离。
若在该溶液中加入糠醛(沸点为161.7℃),则溶液中两组分的相对挥发度发生显著变化,如下表所示:对苯和环己烷混合液,可以选用糠醛为萃取剂,用萃取精馏法来分离,其流程如图4-7所示。
原料由萃取精馏塔中部加入,糠醛在原料入口以上接近塔顶的某块板加入,这样可以使绝对部分塔板上均能保持较高的溶剂浓度。
苯与糠醛从塔釜中排出并送入溶剂回收塔,在回收塔顶得到苯,塔顶得到回收的糠醛,糠醛回到萃取精馏塔回用。
萃取精馏流程中,萃取精馏塔是主要设备,它可以分为三段功能区域:提馏段,进料板以下的塔板,在此段中提馏回流液中的轻组分。
吸收段,进料与溶剂入口之间的塔板,在此段用溶剂吸收蒸汽中的重组分。
分离溶剂段,溶剂入口以上的若干块塔板,用以降低溶剂在馏出物中的浓度,提高产品纯度,减少溶剂损失。
精馏操作——精选推荐

精馏操作⼀、精馏操作(⼀)设备1、静设备⼀览表2、动设备⼀览表(⼆)⼯艺过程原槽内⽔和⼄醇的混合液,经原料泵输送⾄原料加热器中,预热后,由精馏塔中部进⼊精馏塔,进⾏分离。
⽓相由塔顶馏出,经冷凝器冷却后,进⼊冷凝液槽,经产品泵,⼀部分送⾄精馏塔上部第⼀块塔板做回流,另⼀部送⾄塔顶产品槽作为产品采出。
塔釜残液经塔底换热器冷却后送⾄残液槽。
(三)设备原理1、冷凝器:精馏塔分离后的⽓相物质经冷凝器冷却。
冷凝器进的是⽔,,冷凝器中⽔是下⼝进上⼝出,这样有利于热的⽓体通过玻璃管壁于冷⽔充分接触,冷凝效果更好。
2、再沸器:再沸器也称加热釜或重沸器,使被蒸馏液体⽓化的加热设备。
3、塔底换热器:通过热交换将加热或待冷却的介质与换热器⼯作介质进⾏热交换。
4、精馏塔:在⼀定压⼒下利⽤互溶液体混合物各组分沸点或饱和蒸汽压不同,使轻组分汽化,经多次部分液相汽化和部分⽓相冷凝,使⽓相中的轻组分和液相中的重组分浓度逐渐升⾼,从⽽实现分离。
精馏塔以进料塔为界,上部为精馏段,下部为提溜段,⼀定温度和压⼒的料液进⼊精馏塔后,轻组分在精馏段逐渐压缩,离开塔顶后全部冷凝进⼊回流罐,⼀部分作为塔顶产品,另⼀部分被送⼊塔内作为回流液,回流液的⽬的是补充塔顶上的轻组分,使塔板上的液体组成保持稳定,是精馏操作连续稳定的进⾏。
5、离⼼泵:依靠叶轮的不断运转,液体不断的被吸⼊和排出。
液体在离⼼泵中获得的机械能量最终静压能提⾼流速增⼤。
(四)注意事项1、开车前:对所有设备、阀门、仪表、电⽓、管道等按⼯艺流程图要求和专业技术要求进⾏检查。
2、开车时:确认各阀门是否正常开启关闭,观察⽣产过程中各⼯艺操作指标是否在正常范围内。
3、停车时:系统停⽌加料原料预热器停⽌加热,关闭原料液泵进出⼝阀,停原料泵。
根据塔内物料情况再沸器停⽌加热,塔顶温度下降时⽆冷凝液流出后,关闭塔顶冷凝器冷却⽔进⽔阀,停冷却⽔停回流泵,关泵进出⼝阀。
在物料冷却后开再沸器和预热器排污阀放出预热器及再沸器内物料,开塔底冷凝器排污阀,塔底产品槽排污阀,放出塔底冷凝器内物料、塔底产品槽内物料。
精馏操作
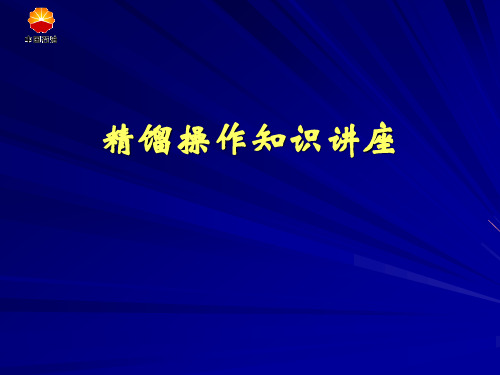
精馏过程中可能发生的问题
返混现象 :在有降液管的塔板上,液体横过塔板 与气体呈错流状态,液体中易挥发组分的浓度降 沿着流动的方向逐渐下降。但是当上升气体在塔 板上是液体形成涡流时,浓度高的液体和浓度低 的液体就混在一起,破坏了液体沿流动方向的浓 度变化,这种现象较做返混现象。 返混现象能导致分离效果的下降。 返混现象的发 生,受到很多因素的影响,如停留时间、液体流 动情况、流道的长度、塔板的水平度、水力梯度 等。
精馏塔的工艺形式主要有几种
A:要求从进料混合物中同时获得轻、重组 分,分馏塔必须包括精馏段和提馏段。这 种塔称为完整塔。 B:除要求得到塔顶和塔底产品外,还要从 塔的侧线抽出产品。必须采用由主塔和气 提塔组合的复合塔工艺形式。 C:只要求得到轻组分或重组分一个产品, 塔的形式采用只有精馏段或只有提馏段的 半截塔就可以了。
热量平衡
QB + QF = QC + QD + QW + QL QB——再沸器加热剂带入的热量 QF——进料带入热量 QC——冷凝器冷却剂带出的热量 QD——塔顶产品带出热量 QW——塔底产品带出热量 QL——散失于环境的热量 操作中要保持热量的平衡,再沸器、冷凝器的负荷要满足 要求,才能保持平稳操作。再沸器和进料的热量输入必须 转移到塔顶冷凝器。如果试图使再沸器热热量输入和回流 控制相互独立,那么该系统就不会稳定,因为热量不平衡。
上面是一个传统的精馏系统,塔底热量系统是固定的, 保证一定的回流比。灵敏板温度是塔顶产品的间接质 量指标,调节手段是改变回流量F1,用回流罐液面L1 的高低来控制塔顶产品的抽出量F2,这种方案是建立 在热平衡的关系上。回流量F1的给定值是由灵敏板温 度T给定的,当天气冷时,使回流温度降低,相应增加 了塔的内回流量并影响塔顶温度,此时由于塔顶温度 下降温度调节器将改变回流量F1的给定值,减少回流。 由于塔本身操作滞后及温度测量滞后,使这一变化缓 慢而波动,这一调整直到建立新的热量平衡为止。
精馏塔基本知识

没有利用组分浓度不高的中间产物,如y1’和xn,是收率低 的根本原因。为此,可将与原料浓度z相近的y1’蒸气和液 体xn回流至罐F,设计出如图所示的流程。
所示的流程即为精馏 过程,它可使混合物 得到有效分离,既可 保证高的产品纯度, 又能达到较高的收率。
流程中,每个容器都是气液平衡的接触级,每一级都有气 液两股进料。液相回流的轻组分浓度应高于该级条件下的 平衡液相浓度;而气相进料的轻组分浓度应低于该条件下 的平衡气相浓度. 进入每一级的气液相浓度是不平衡的,液相浓度比平衡浓 度高,气相浓度比平衡浓度低,这就产生了传质推动力, 使气液两相接触时液相中的轻组分蒸发,气相中的重组分 冷凝,气液相趋近于相平衡。因此,相间的浓度差别是精 馏的重要前提。
回流比R有若干种定义方法,较常用的定义为:塔顶回流量L 与塔顶产品量D之比(以mol/h计)。
回流比减小,理论塔板数增加。理论塔板数趋于无穷大时的 回流比称最小回流比
塔顶馏出物全部冷凝后回流,称全回流,对应的在某些特定情况下,可能需 要使用全回流,如塔的启动;塔的产品达不到纯度要求,进 行一段时间全回流,使塔迅速恢复正常工况;试验中测定各 层塔板分离效率等。
量。因而,天然气凝液进塔前所需的冷负荷和重沸器所需
的热负荷有紧密的联系,应做出折衷选择。
分馏塔
凝液与塔底产品换热后由塔的中部进塔,进料温 度与进塔处的塔温基本相等,使原料进塔时的闪 蒸量很小。塔顶气冷却后,使中间组分在回流罐 内冷凝、分离、冷凝液用泵送回塔内,并分布至 顶层塔板上。回流冷液体促使气流中的中间组分
塔底产品经重沸器加热后,所产生的蒸气返回塔底、产生气 相回流是提馏段工作的必要条件。若无气相回流,液体仅流 经各层接触级,液体内的重组分浓度也得不到提浓。
- 1、下载文档前请自行甄别文档内容的完整性,平台不提供额外的编辑、内容补充、找答案等附加服务。
- 2、"仅部分预览"的文档,不可在线预览部分如存在完整性等问题,可反馈申请退款(可完整预览的文档不适用该条件!)。
- 3、如文档侵犯您的权益,请联系客服反馈,我们会尽快为您处理(人工客服工作时间:9:00-18:30)。
精馏工艺操作基本知识
1、何为相和相平衡:
答:相就是指在系统中具有相同物理性质和化学性质的均匀部分,不同相之间往往有一个相界面,把不同的相分别开。
系统中相数的多少与物质的数量无关。
如水和冰混合在一起,水为液相,冰为固相。
一般情况下,物料在精馏塔内是气、液两相。
在一定的温度和压力下,如果物料系统中存在两个或两个以上的相,物料在各相的相对量以及物料中各组分在各个相中的浓度不随时间变化,我们称系统处于平衡状态。
平衡时,物质还是在不停地运动,但是,各个相的量和各组分在各项的浓度不随时间变化,当条件改变时,将建立起新的相平衡,因此相平衡是运动的、相对的,而不是静止的、绝对的。
比如:在精馏系统中,精馏塔板上温度较高的气体和温度较低的液体相互接触时,要进行传热、传质,其结果是气体部分冷凝,形成的液相中高沸点组分的浓度不断增加。
塔板上的液体部分气化,形成的气相中低沸点组分的浓度不断增加。
但是这个传热、传质过程并不是无止境的,当气液两相达到平衡时,其各组分的两相的组成就不再随时间变化了。
2、何为饱和蒸汽压?
答:在一定的温度下,与同种物质的液态(或固态)处于平衡状态的蒸汽所产生的压强叫饱和蒸汽压,它随温度的升高而增加。
众所周知,放在杯子里的水,会因不断蒸发变得愈来愈少。
如果把纯水放在一个密闭容器里,并抽走上方的空气,当水不断蒸发时,水面上方气相的压力,即水的蒸汽所具有的压力就不断增加。
但是,当温度一定时,气相压力
最中将稳定在一个固定的数值上,这时的压力称为水在该温度下的饱和蒸汽压。
应当注意的是,当气相压力的数值达到饱和蒸汽压力的数值是,液相的水分子仍然不断地气化,气相中的水分子也不断地冷凝成液体,只是由于水的气化速度等于水蒸汽的冷凝速度,液体量才没有减少,气体量也没有增加,气体和液体达到平衡状态。
所以,液态纯物质蒸汽所具有的压力为其饱和蒸汽压时,气液两相即达到了相平衡。
3、何为精馏,精馏的原理是什么?
答:把液体混合物进行多次部分汽化,同时又把产生的蒸汽多次部分冷凝,使混合物分离为所要求组分的操作过程称为精馏。
为什么把液体混合物进行多次部分汽化同时又多次部分冷凝,就能分离为纯或比较纯的组分呢?对于一次汽化,冷凝来说,由于液体混合物中所含的组分的沸点不同,当其在一定温度下部分汽化时,因低沸点物易于气化,故它在气相中的浓度较液相高,而液相中高沸点物的浓度较气相高。
这就改变了气液两相的组成。
当对部分汽化所得蒸汽进行部分冷凝时,因高沸点物易于冷凝,使冷凝液中高沸点物的浓度较气相高,而为冷凝气中低沸点物的浓度比冷凝液中要高。
这样经过一次部分汽化和部分冷凝,使混合液通过各组分浓度的改变得到了初步分离。
如果多次的这样进行下去,将最终在液相中留下的基本上是高沸点的组分,在气相中留下的基本上是低沸点的组分。
由此可见,多次部分汽化和多次部分冷凝同时进行,就可以将混合物分离为纯或比较纯的组分。
液体气化要吸收热量,气体冷凝要放出热量。
为了合理的利用热量,我
们可以把气体冷凝时放出的热量供给液体气化时使用,也就是使气液两相直接接触,在传热同时进行传质。
为了满足这一要求,在实践中,这种多次部分汽化伴随多次部分冷凝的过程是逆流作用的板式设备中进
行的。
所谓逆流,就是因液体受热而产生的温度较高的气体,自下而上地同塔顶因冷凝而产生的温度较低的回流液体(富含低沸点组分)作逆向流动。
塔内所发生的传热传质过程如下1)气液两相进行热的交换,利用部分汽化所得气体混合物中的热来加热部分冷凝所得的液体混合物;2)气液两相在热交换的同时进行质的交换。
温度较低的液体混合物被温度较高的气体混合物加热二部分汽化。
此时,因挥发能力的差异(低沸点物挥发能力强,高沸点物挥发能力差),低沸点物比高沸点物挥发多,结果表现为低沸点组分从液相转为气相,气相中易挥发组分增浓;同理,温度较高的气相混合物,因加热了温度较低的液体混合物,而使自己部分冷凝,同样因为挥发能力的差异,使高沸点组分从气相转为液相,液相中难挥发组分增浓。
精馏塔是由若干塔板组成的,塔的最上部称为塔顶,塔的最下部称为塔釜。
塔内的一块塔盘只进行一次部分汽化和部分冷凝,塔盘数愈多,部分汽化和部分冷凝的次数愈多,分离效果愈好。
通过整个精馏过程,最终由塔顶得到高纯度的易挥发组分,塔釜得到的基本上是难挥发的组分。
4、什么是露点?
答:把气体混合物在压力不变的条件下降温冷却,当冷却到某一温度时,产生的第一个微小的液滴,此温度叫做该混合物在指定压力下的露点温
度,简称露点。
处于露点温度下的气体称为饱和气体。
从精馏塔顶蒸出的气体温度,就是处在露点温度下。
值得注意的是:第一个野地不是纯组分,塔时露点温度下与气相平衡的液相,其组成有相平衡关系决定。
由此可见,不同组成的气体混合物,塔的露点是不同的。
5、什么是泡点?
答:液体混合物在一定压力下加热到某一温度时,液体中出现的第一个很小的气泡,即刚开始沸腾时的温度叫该液体在指定压力下的泡点温度,简称泡点。
处于泡点温度下的液体称为饱和液体,即精馏塔的釜温温度。
应该说明,这第一个很小的气泡,也不是纯组分,它的组成也是有相平衡关系决定的。
6、什么是沸点?
答:当纯液体物质的饱和蒸汽压等于外压时,液体就会沸腾,此时的温度叫做该液体在指定压力下的沸点。
纯物质的沸点是随外界压力的变化而改变的。
当外界压力增大时,沸点升高,外界压力降低时,沸点降低。
对于纯物质来说,在一定压力下,泡点、露点、沸点均为一个数值。
7什么是潜热?
答:单位重量的纯物质在相变(在没有化学反应的条件下,物质发生了相态的改变,称相变。
如水结成冰或水汽化成水蒸气等成为相变过程。
)过程吸收或放出的热叫潜热。
如1公斤水由液态受热变成水蒸气的过程中所吸收的热叫水的汽化潜热,常用单位为千卡/公斤。
值得注意的是,在相变时温度和压力都是不变的,否则不能称之为潜热。
因此,在说潜热数值时,要说明在什么温度什么压力下,进行何种相变过程。
如1公
斤水在760毫米汞柱压力,100摄氏度下汽化,汽化潜热为539.6千卡。
相反,在此条件下,水蒸汽冷凝释放出来的热,称为冷凝潜热,数值与上相等。
混合物的潜热可以实测或计算,其数值的大小除了和组分的性质有关外,还和组分的含量有关,不是一个固定的数值。
8、什么是显热?
答:纯物质在不发生相变和化学反应的条件下,因温度的改变而吸收或放出的热量叫显热。
9什么是回流比
答:在精馏过程中,混合液加热后所产生的蒸汽由塔顶蒸出,进入塔顶冷凝器。
蒸汽在此冷凝(或部分冷凝)成液体,将其一部分冷凝液返回塔顶沿塔板下流,这部分液体叫做回流液;将另一部分冷凝液(或未凝蒸汽)从塔顶采出,作为产品。
回流比就是回流液量与采出量的重量比,通常以通常以R来表示,即
R=L/D
式中R-回流比
L-单位时间内塔顶回流液体量,公斤/小时。
D-单位时间内塔顶采储量,公斤/小时。
10、什么是最小回流比?
答:在规定的分离精度要求下,即塔顶、塔釜采出的组成一定时,逐渐减少回流比,此时所谓的理论板数逐渐增加。
当回流比减少到某一数值时,所需的理论板数增加至无数多,这个回流比的数值,成为完成该项
预定分离任务的最小回流比。
通常操作时的实际回流比取为最小回流比的1.3~2倍。